- 您的位置:
- 标准下载网 >>
- 标准分类 >>
- 汽车行业标准(QC) >>
- QC/T 311-2018 汽车液压制动主缸性能要求及台架试验方法
标准号:
QC/T 311-2018
标准名称:
汽车液压制动主缸性能要求及台架试验方法
标准类别:
汽车行业标准(QC)
标准状态:
现行出版语种:
简体中文下载格式:
.zip .pdf下载大小:
1.86 MB

点击下载
标准简介:
QC/T 311-2018.Performance requirements and bench test methods of motor vehicle brake master cylinder.
1范围
1.1 QC/T 311规定了汽车液压制动主缸总成的术语和定义、产品分类、性能要求、试验装置和试验方法。
1.2 QC/T 311适用于汽车用串联双腔液压制动主缸总成(以下简称“制动主缸"),其他型式的制动主缸可参照执行。
2规范性引用文件
下列文件对于本文件的应用是必不可少的。凡是注日期的引用文件,仅注日期的版本适用于本文件。凡是不注日期的引用文件,其最新版本(包括所有的修改单)适用于本文件。
GB/T 10125- -2012 人造气氛腐蚀试验 盐雾试验
3术语和定义
下列术语和定义适用于本标准。
1供液腔fuid supply cavity
通过供液孔与储液罐相通的腔(参见图1、图2)。在制动解除的瞬间向制动腔供给制动液。
3.2制动腔brake service cavity
通过排液孔或残留阀与制动回路相通的腔(参见图工、图2)。在制动过程中制动腔内建立起的液压与其相连接的回路内的液压相同。
3.3补偿孔compensating hole
缸体(或活塞)上.制动腔 与供液腔(或储液罐)连通的孔(参见图1)。在解除制动状态下向制动腔补偿制动液和将多余的制动液返回供液腔。
3.4中心阀center valve
在活塞上,位于制动腔与供液腔之间的阀(参见图2)。在制动状态下,切断制动腔和供液腔的通道和向制动腔补偿制动液;在解除制动状态下,向制动腔补偿制动液和将多余的制动液返回供液腔。

部分标准内容:
中华人民共和国汽车行业标准
QC/T311—2018
代替QC/T311—2008
汽车液压制动主缸性能要求及
台架试验方法
Performance requirements and bench test methods ofmotorvehiclebrakemastercylinder仅供参阅
2018-07-04发布
2019-01-01实施
中华人民共和国工业和信息化部发布
范围·
2规范性引用文件
3术语和定义··
4产品分类·
性能要求
6试验装置
样品和样品安装
试验方法
馆藏文本
仅供参阅
QC/T311—2018
QC/T311—2018
本标准按GB/T1.1一2009《标准化工作导则第1部分:标准的结构和编写》给出的规则起草。本标准代替QC/T3112008《汽车液压制动主缸性能要求及台架试验方法》,与QC/T311一2008相比,主要技术变化如下:一修改了“补偿孔”“中心阀”“最大行程”“初始建压行程”等术语的定义(见3.3、3.43.10、3.11,2008年版的3.3、3.4、3.7、3.8);增加了“补偿孔式制动主缸”“中心阀式制动主缸”“柱塞式制动主缸”等术语和定义(见3.6、3.7、3.8)
取消了基本要求(见2008年版的5.1);修改了残留阀的评价指标(见5.1,2008年版的5.2.1);修改了密封性的评价指标及试验方法(见5.2、8.2、2008年版的5.2.2、7.2.2);修改了初始建压行程的评价指标及试验方法(见5.3、8.3,2008年版的5.2.3、7.2.3)修改了排量的评价指标(见5.5,2008年版的5.2.5)—增加了制动主缸的流量的性能要求及试验方法(见5.8、8.8);增加了耐压强度的性能要求及试验方法(见5.10、8.10):修改了工作耐久性的评价指标及试验方法,增加了ABS工作模式耐久性的试验方法(见5.11、8.11.2008年版的5.2.9、72.9):修改了振动性能的评价指标及试验方法(见5.12、8.12、2008年版的5.2.10、7.2.10);删除了清洁度的性能要求及试验方法(见2008年版的5.2.11、7.2.11):修改了耐盐雾腐蚀性的评价指标及试验方法(见5.13、8.13,2008年版的5.2.12、7.2.12);修改了液压测试部分的试验装置原理图(见6.1.5.1,2008年版的6.1.5);一增加了流量测量装置示意图(见6.1.5.2):将对样品和样品安装的要求作为独立一章列出(见第7章,2008年版的7.1):一修改了输出功能的试验方法(见8.4,2008年版的7.2.4)本标准由全国汽车标准化技术委员会(SAC/TC114)提出并归I1。本标准主要起草单位:吉林东光奥威汽车制动系统有限公司、上海汽车制动系统有限公司、中国第一汽车股份有限公司技术中心、泛亚汽车技术中心有限公司、上海大众汽车有限公司、中国第一汽车股份有限公司天津技术开发分公司、博世汽车部件(苏州)有限公司、浙江亚太机电股份有限公司、浙江万安科技股份有限公司、吉林东光集团。本标准主要起草人:张玉海、葛宏、李欣、齐钢、魏宏、车绵、郑文汇、黄国兴、侯宗岗、徐鑫。
本标准所代替标准的历次版本发布情况为:-ZB/TT24—1990;
-QC/T311-1999;
-QCT311-2008。
1范围
汽车液压制动主缸性能要求及台架试验方法QC/T311—2018
1.1本标准规定了汽车液压制动主缸总成的术语和定义、产品分类、性能要求、试验装置和试验方法。
1.2本标准适用于汽车用串联双腔液压制动主缸总成(以下简称“制动主缸”)、其他型式的制动主缸可参照执行。
2规范性引用文件
下列文件对于本文件的应用是必不可少的。凡是注日期的引用文件,仅注日期的版本适用于本文件。凡是不注日期的引用文件,其最新版本(包括所有的修改单)适用于本文件。GB/T10125—2012人造气氛腐蚀试验盐雾试验3术语和定义
下列术语和定义适用于本标准。藏蔽文本
fluid supply cavity
供液腔
通过供液孔与储液罐相通的腔(参见图1、图2)。在制动解除的瞬间向制动腔供给制动液。3.2
brake servicecavity
制动腔
通过排液孔或残留阀与制动回路相通的腔(参见图1图2)在制动过程中制动腔内建立起
的液压与其相连接的回路内的液压相同。3.3
补偿孔compensatinghole
缸体(或活塞)上制动腔与供液腔(或储液罐)连通的孔(参见图1)。在解除制动状态下向制动腔补偿制动液和将多余的制动液返回供液腔。3.4
中心阀centervalve
在活塞上,位于制动腔与供液腔之间的阀(参见图2)。在制动状态下,切断制动腔和供液腔的通道和向制动腔补偿制动液;在解除制动状态下,向制动腔补偿制动液和将多余的制动液返回供液腔。
残留阀residual valve
位于制动腔与制动回路之间的阀(参见图!)。在制动解除时使制动回路中仍保持一定的残留压力。
QC/T311—2018
安装尺寸
1一缸体:2一副皮碗:3一第一活塞:4一第一供液孔:5一供液孔:6—补偿孔:7—第一制动腔:8一第二供液腔:9连接套:10第二供液孔:11一补偿孔:12—第二制动腔:13第二排液孔:14第二活塞:15一第一排液孔;16—管座:17残留阀总成:18一第一供液腔图1液压制动主缸典型结构
补偿孔式bzxZ.net
安装尺寸
1一第一活塞:2弹黄挡圈;3限位环;16
5-0型密封图:6一第一控制销:7、13一主皮碗:刷皮碗:5
8一第一供液孔:9一第二副皮碗:10—连接套:11一第二供液孔:12一第二控制销:14-缸体:15一第一供液腔;16一第一中心阀:17一第一制动腔:18一第一排液孔:19一第二供液腔:20第二活寒:21-第二中心阀:22—第二排液孔;23一第二制动腔图2液压制动主缸典型结构中心阀式3.6
补偿孔式制动主缸brakemastercylinderwitheompensatinghole带有补偿孔的制动主缸(参见图1)。2
中心阀式制动主缸brakemastercylinderwithcentervalve带有中心阀的制动主缸(参见图2)。柱塞式制动主缸plungerbrakemastercylinder密封圈安装在缸体上的制动主缸(参见图3)12
安装尺寸
QC/T311—2018
1一缸体:2第二制动腔:3一第活塞:4一主皮碗:5连接套:6第二供液礼:7一第一制动腔:8-第供波孔:9-钢珠:10-刷皮碗;11一第一活塞:12-一第二活簧:13一第二排液孔:14一小垫过:15一第一活寒简:16—一第一排液孔:17—一弹简限位座图3液压制动主缸典型结构
最高工作液压
maximumservicepressu
供参阅
设计规定的最高使用液压。
最大行程maximumstroke
制动主缸的第一活塞从安装尺寸到终止位置的位移量,3.11
初始建压行程initialpressure-buildingtravel柱塞式
制动主缸在安装尺寸状态下,制动腔的液压达到0.IMPa时,第一活塞所移动的位移。4产品分类
制动主缸产品按工作环境温度分A类、B类、C类三种,见表1。表1制动主缸按工作环境温度分类种
A类(安装在驾驶室内)
B类(安装在发动机舱内,但离发动机较远)C类(安装在发动机舱内,但离发动机较近)工作环境温度
-40~+80℃
-40~+100℃
-40~~+120℃
QC/T311—2018
5性能要求
5.1残留阀性能
残留阀的开启压力不应大于0.05MPa:残留压力应满足设计要求。5.2密封性
5.2.1真空密封性
对采用真空注油的车辆使用的制动主缸,其压力升高值不应大于0.3kPa。5.2.2气压密封性
5.2.2.1制动主缸各制动腔的气压降不应大于3kPa。5.2.2.2在施加0.5MPa气压过程中,制动主缸和储液罐(仅对自带储液罐样品)不应出现空气泄漏现象,制动主缸自带的储液罐不应出现影响功能的变形。5.2.3液压密封性
制动主缸各制动腔在不同试验压力下的压力降不应大于表2规定值或按供需双方商定的要求:制动主缸排液孔螺纹不应出现滑丝和损坏。表2液压密封性技术要求
试验压力
最高工作液工
最高工作液压/MPa
S15、520
仅供参间
5.3初始建压行程
压力降/MPa
M,类车辆用制动主缸的初始建压行程不应大于2.5mm:其他类车辆用制动主缸的初始建压行程不应大于4mm。
5.4输出功能
一个制动腔失效后,制动主缸的另一个制动腔仍能建立起最高工作液压。5.5排量
制动主缸各制动腔的排量不应小于设计值。5.6无负载回程时间
制动主缸第-活塞无负载回程时间不应大于0.5s5.7压差性能
缓加压压差试验时,制动主缸两制动腔的压力差不应大于0.3MPa:急加压压差试验时,制动主缸两制动腔的压力差不应大于0.5MPa4
5.8流量
制动主缸各制动腔的流量应满足设计要求。5.9压力冲击
QC/T311—2018
经压力冲击试验后,制动主缸应无影响功能的变形和损坏:试验压力为制动主缸最高工作液压的密封性应满足表2的要求;若制动主缸自带储液罐,则压力冲击试验后不应有制动液从储液罐中溢出。
5.10耐压强度
经耐压试验后,制动主缸应无变形、泄漏等异常现象,其液压密封性应满足5.2.3的要求。5.11工作耐久性
试验过程中,制动主缸各处应无泄漏和任何异常现象,活塞应动作灵活;试验后,液压密封性应满足5.2.3的要求;若自带储液罐,则工作耐久性试验过程中不应有制动液从储液罐中溢出,试验后,储液罐与制动主缸的连接部位不应出现松动现象。5.12振动性能
5.12.1在振动性能试验过程中,不应有制动液从储液罐中溢出:试验后.储液罐与制动主缸的连接部位不应出现松动现象,不应有影响功能的变形和损坏。5.12.2与试验前相比,残留的紧力矩应大于50%5.13耐盐雾腐蚀性
经耐盐雾腐蚀性试验后,制动主缸应满足表3的要求。表面处理
铸铝缸体
6试验装置
表3耐腐蚀性技术要求
技术要
在任意100cm范围内不应右5cm以上的下列缺陷:a)有色铬酸盐的明显生成物:
b)光洋铬酸盐以及黑色处理物的锈蚀不应有下列缺陷:
a)有色铬酸盐的明显生成物:
b)光泽铬酸盐以及黑色处理物的诱蚀在任意100cm范固内不应有一个以上直径大于2mm的腐蚀物,不应产生膨胀、剥落以及涂膜软化
外询任意100cm范围内不应产生直径大于2mm的魔仙物,离使总面积不应超过5cm6.1制动主缸试验装置
6.1.1驱动装置
驱动装置的推杆头部应与实车样品推杆头部尺寸规格一致,推杆与制动主缸轴线的初始夹角不应大于2°。驱动装置能够单次地、周期性地推动样品的活塞,样品的活塞可以移动到最大行程位置,推动的距离可调整并可在任意位置固定不动,推动时样品建压的速率可以调整。单次推动样品的活塞时,在样品的制动腔中能够建立起样品的最高工作液压、最高工作液压的130%,可以保证样品的活塞在不同推动位置时不受其他限制而迅速回位:周期性地推动样品的活塞时,推动频率、升压时间、保压时间、降压时间、停顿时间等可以调整。5
QC/T311—2018
6.1.2负载装置
负载装置能够模拟制动器中液压制动轮缸的工作状态,可按要求调整加载压力和样品行程的关系,负载装置中的可运动部件可以根据需要锁住不动。6.1.3测量装置
6.1.3.1用于测量压力、位移、排量、流量、力矩、长度的仪器或仪表的有效测量数值均应大于需要测量的值,测量的相对误差不应超过+1%:但可采用1.5级的压力表监测工作耐久性试验的压力值。
6.1.3.2测时仪测量样品无负载回程时间的相对误差不应超过+5%。6.1.3.3进行初始建压行程、输出功能、无负载回程时间、液压密封性和压差性能的测量时,测试回路总有效容积为135~150mL。6.1.3.4进行真空密封性、气压密封性试验时,测试回路的总有效容积为450~500mL。6.1.4连接管路
样品与负载装置、压力测量装置、流量测量装置、排量测量装置、各种截止阀之间的连接采用制动用金属管和/或软管连接(或按供需双方商定的连接方式连接),连接的测试回路中不应产生节流现象。
6.1.5试验装置原理图
6.1.5.1液压测试部分的试验装置原理图参见图4。馆藏实本
仪供参闵目
1-驱动装置:2一推杆:3一力传感器:4样品支架:5一储液罐:6—样品:7一高低温试验箱:8、10、12、14、16、18、20、22、23、24截止阀:9、15—排量测量装置:11.17—压力传感器:13.19-压力表:21、25一负载装置;26一位移测量装置:27—位移传感器:28一测时仪图4液压测试部分的试验装置原理图6
2流量测量装置示意图参见图5。安装尺寸
QG/T311-—2018
1-驱动装置:2-推杆:3-样品支架:4样品:5-油管:6-截止阀:7一三通接头:8--液压泵:9-流量计:10-真空传感器
图5流量测量装置示意图
6.2高低温试验箱
高低温试验箱的实际温度与设定温度的误差不应超过±2℃,高低温试验箱应有连接气管、液压管的通道,并且该通道应有隔热,隔湿的密封措施,高低温试验箱内应有足够安装驱动装置、样品及连接气管、液压管的空间。6.3振动试验设备
振动设备的振动波形应能提供正弦波,加速度波形失真不应超过25%,频率误差不应超过仅供参阅
±1%。
6.4盐雾试验箱
盐雾试验箱内实际温度与设定温度的误差不应超过±1C;盐雾沉降速度应符合GB/T10125-2012中的中性盐零试验的相关规定。7样品和样品安装
7.1试验用制动液应与实车使用的制动液相同或由供需双方商定。7.2除另有规定外,样品试验时的初始状态应处于安装尺寸(在规定真空状态下,真空助力器与制动主缸之间的装配尺寸即为安装尺寸),试验环境温度为室温。7.3除另有规定外,应按设计规定的力矩(或供需双方商定)连接到测试回路,安装状态应模拟实车安装状态。
7.4工作耐久性、振动性能、输出功能试验,样品应与相匹配的助力器一起进行试验,7.5试验中,若样品自带储液罐,制动液应加注到储液罐最高刻度线位置。7.6液压试验时应在试验前排净样品及系统内的空气。7.7样品数量、试验项月和试验顺序宜根据不同的试验目的按表4进行。QC/T311—2018
试验顷序
试验项目
残留闷性能
密封性
初始建压行程
输出功能
无负载回程时间
乐差性能
乐力冲击
耐压强度
工作耐久性
振动性能
耐盐雾腐蚀性
“*”表示要进行试验的项目
试验方法
8.1残留裙性能
表4试验项目和试验顺序
样品瑞号
表示不进行武验的项目
8.1.1将样品的供液孔时气源接通,向供液孔逐渐通人气压不大于0.10MPa的气体,记录排液孔有气体流出时,供液孔输人的最低气压值(残留阀的开启压力)。8.1.2将样品的排液孔与气源接通,向排液孔逐渐通入气压不大于0.15MPa的气体,记录补偿孔有气体流出时排液孔输人的最低气压值(残留阀的残留压力)。8.2密封性
8.2.1真空密封性
8.2.1.1关闭样品排液孔,两供液孔连通后与真空源相连(若样品自带储液罐,则真空源直接与储液罐的加液口相连)。
8.2.1.2将系统抽真空至绝对压力(250±50)Pa(或由供需双方商定的压力)后切断真空源,立即记录此后5s内测试系统内的压力升高值。气压密封性
将样品与驱动装置连接到测试回路用驱动装置的推杆将样品的活塞推动到超过样品的初始建压行程。将样品的排液孔与气源相连,调节气源压力为(502)kPa,然后切断气源。稳压3~5s后,测量此后10s内样品各制动腔的压力降。8.2.2.5驱动装置的推杆回到原始位置。QC/T311—2018
8.2.2.6将样品的排液孔堵死,供液孔与气源相连,若样品自带储液罐,则气源与储液罐加液口相连。
调节气源压力为(0.5±0.05)MPa,保持10s,观察样品及自带的储液罐有无空气外泄现象,储液罐有无影响功能的变形。8.2.3液压密封性
8.2.3.1将样品与负载装置、压力测量装置连接到测试回路。8.2.3.2用与样品排液孔相匹配的螺纹连接器或实车连接件与样品的排液孔连接,力矩升高时的紧速度约为3r/min,拧紧力矩为设计值下限(或供需双方商定的拧紧力矩)。8.2.3.3用驱动装置的推杆推动样品的活塞,在样品的制动腔中建立起样品的最高工作液压,保持推杆位置不变,稳压3~5s后,测量此后30s内样品各制动腔的压力降。8.2.3.4用驱动装置的推杆推动样品的活塞,在样品的制动腔中建立起样品最高工作液压的130%,保持推杆位置不变,稳压3~5s后,测量此后5s内样品各制动腔的压力降。8.2.3.5试验结束后,拆除螺纹连接器,检查排液孔的连接螺纹是否有滑丝和损坏。8.3初始建压行程
8.3.1在样品排液孔连接压力测量装置,其总容积不应大于50mL。8.3.2以(0.2±0.1)mm/s的速度推动样品的活塞,分别记录样品各制动腔液压为0.1MPa时第一活塞移动的位移量。
8.4输出功能
8.4.1将样品与负载装置、压力测量装置连接到测试回路8.4.2以(3±1)mm/s的速度推进样品的活塞运动,在测试回路中建立起样品的最高工作液压后返回,至少进行5次。
8.4.3分别模拟样品的一个制动腔失效(排液孔通大气)后,观察另一个制动腔是否能够建立起样品的最高工作液压,
文供参悦
8.5排量
8.5.1将样品与驱动装置、排量测量装置连接到测试回路。8.5.2使样品内充满制动液,关闭样品的排液孔。8.5.3打开排液孔,同时以(3±1)mm/s的速度推动样品的活塞达到最大行程位置,关闭样品的排液孔,然后活塞返回到初始位置,测量此过程中各排液孔的排量。此过程为1个测量周期,共进行3个周期的测量,2个测量周期之问时间间隔为10s。8.5.4记录3个周期的各腔排量,取3个周期测量值的平均值作为样品的各腔排量测量值。8.6无负载回程时间
8.6.1将样品与驱动装置、负载装置、测时仪连接到测试回路。8.6.2使样品和负载装置内充满制动液。8.6.3将样品的活塞推动到最大行程位置后(不建立压力)、关闭样品的排液孔。8.6.4迅速撤销推杆的推力,记录样品的第一活塞在不受其他限制的条件下完全返回原位的时间。8.7压差性能
8.7.1缓加压压差
8.7.1.1将样品与负载装置、压力测量装置连接到测试回路。9
小提示:此标准内容仅展示完整标准里的部分截取内容,若需要完整标准请到上方自行免费下载完整标准文档。

标准图片预览:
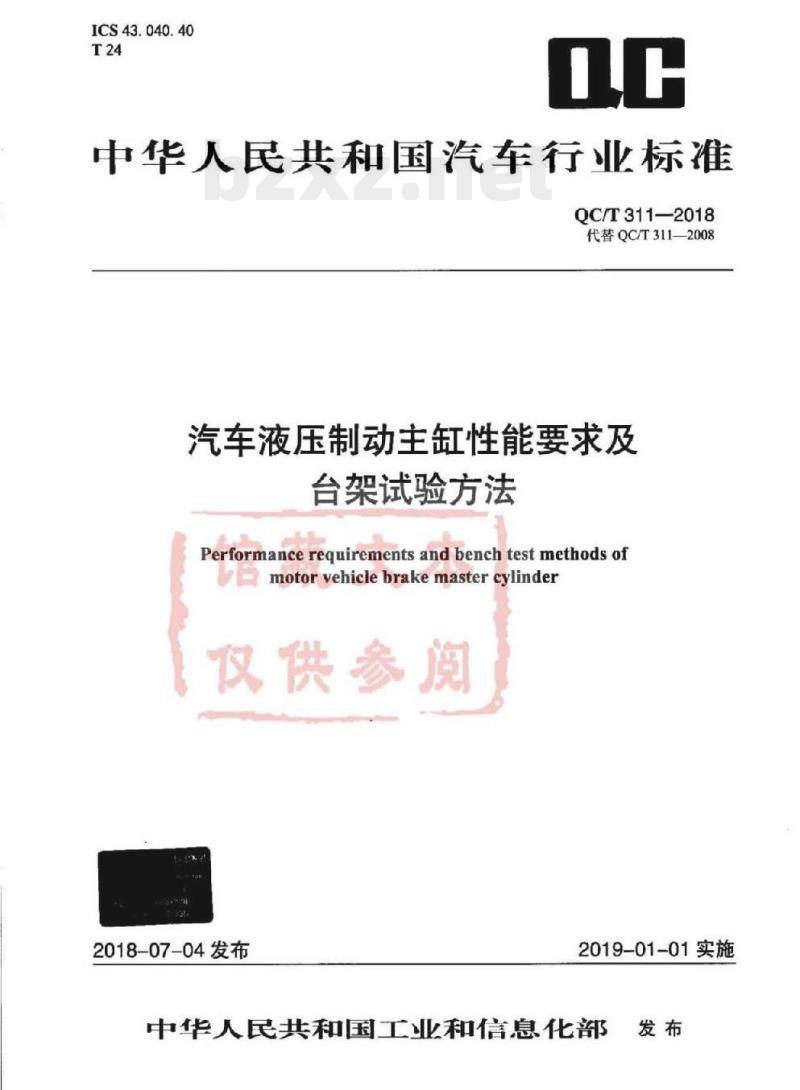
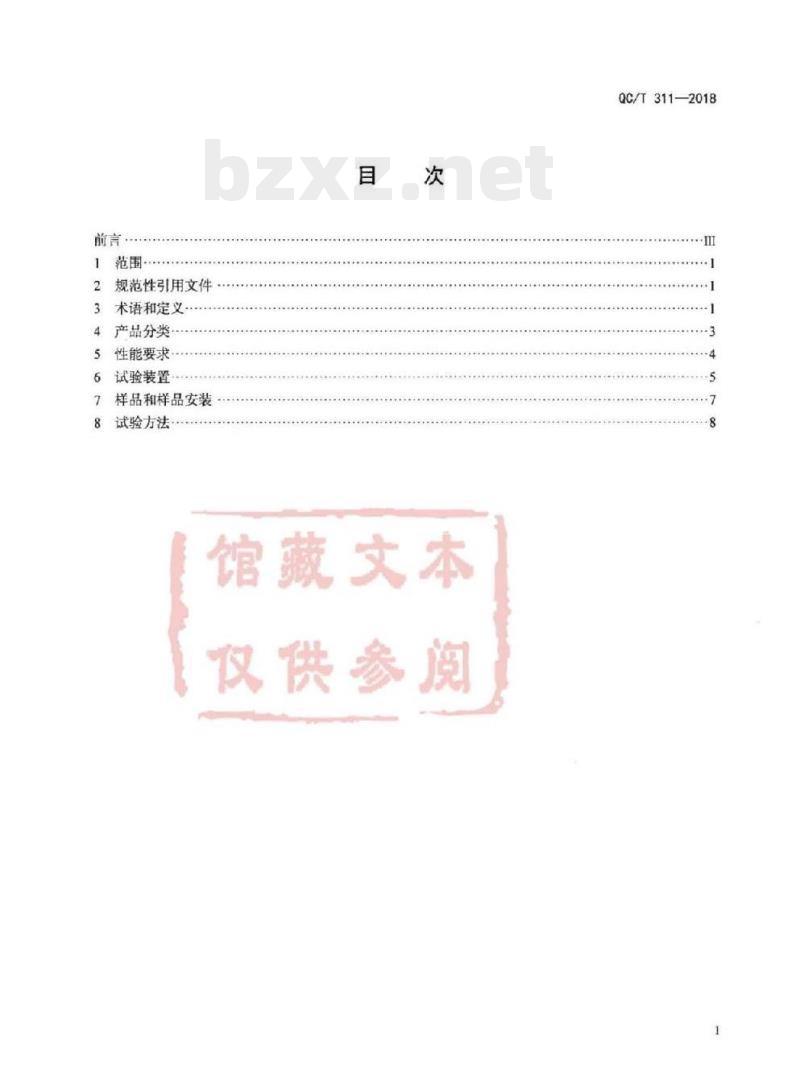
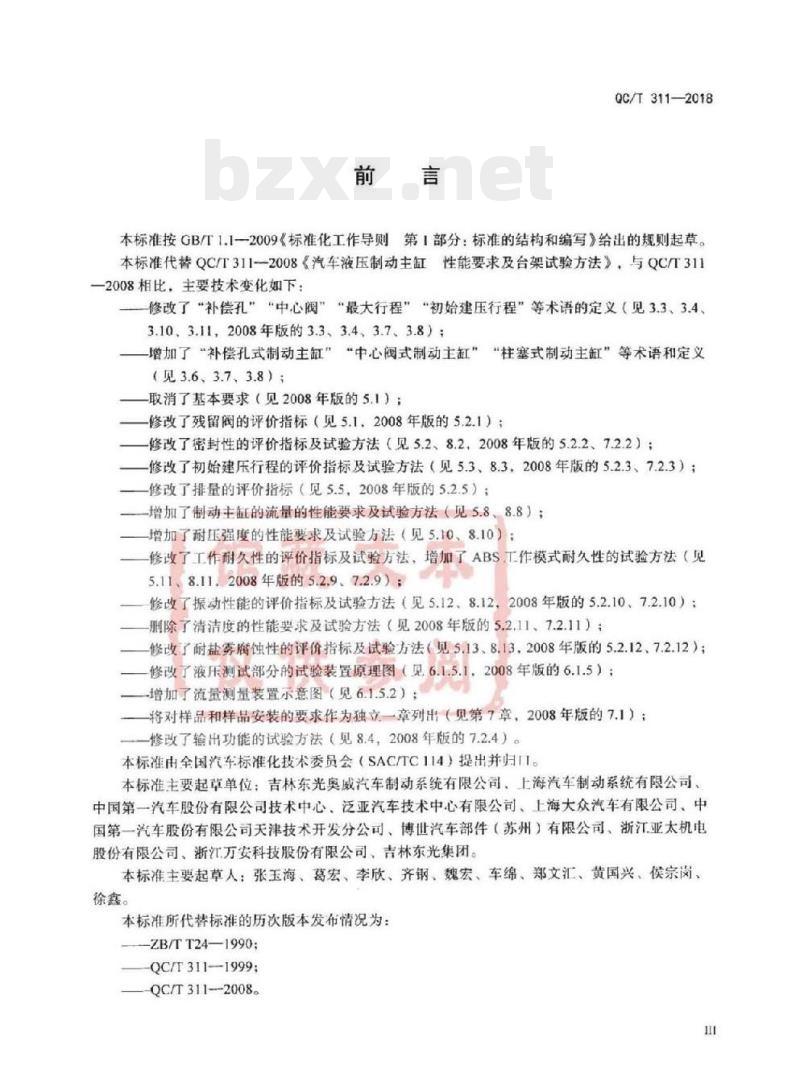
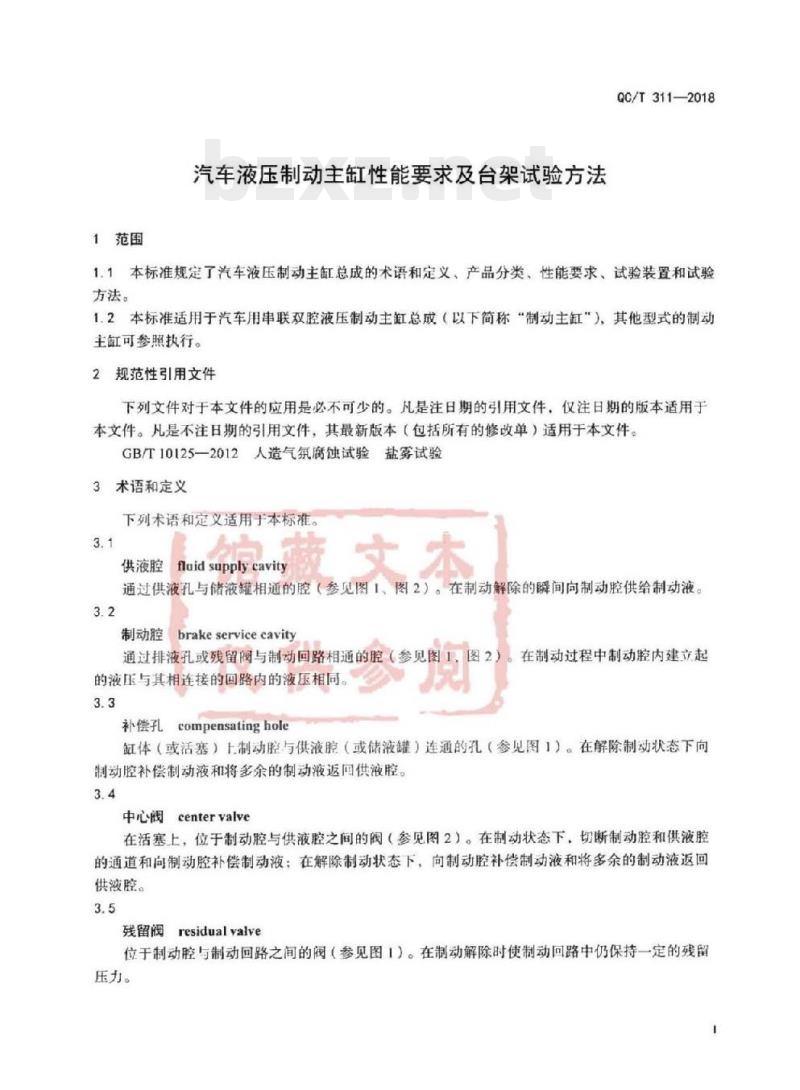
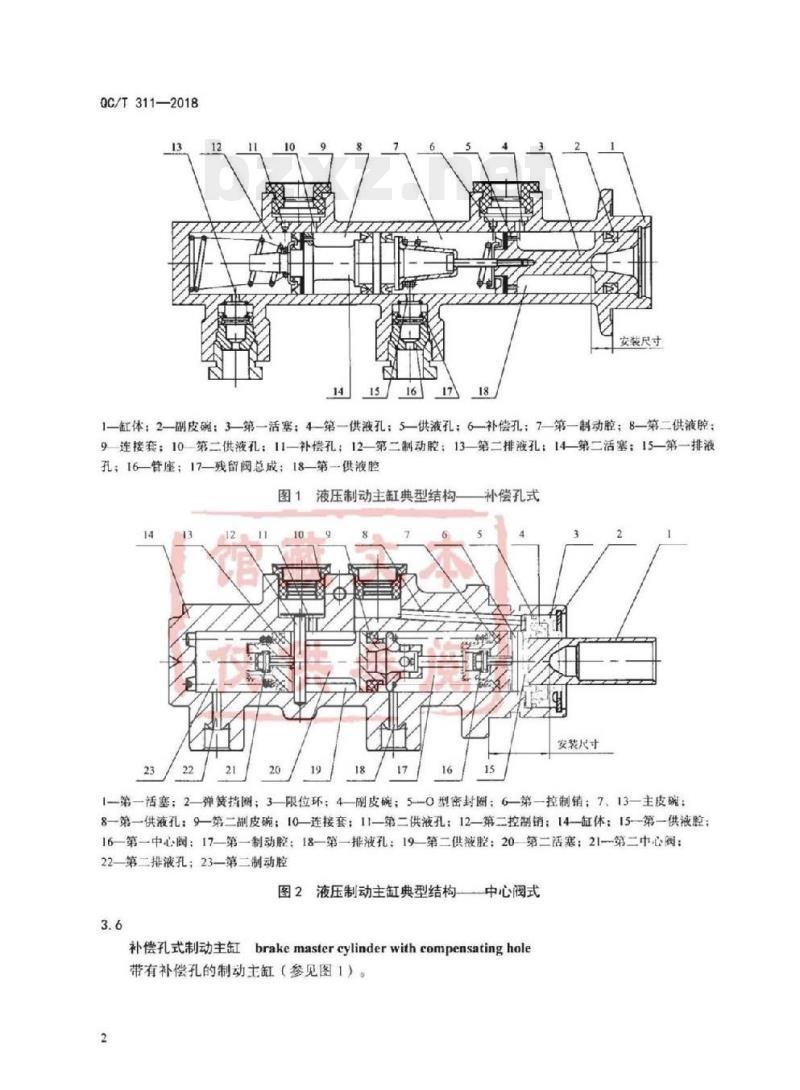
- 其它标准
- 热门标准
- QC汽车标准
- QC/T882-2011 开口夹
- QC/T772-2006 汽车用柴油滤清器试验方法
- QC/T35-1992 汽车与挂车气压控制装置台架试验方法
- QC/T1068-2017 电动汽车用异步驱动电机系统
- QC/T29105.4-1992 专用汽车液压系统液压油固体污染度测试方法显 微镜颗粒计数法
- QC/T228.2-1997 摩托车和轻便摩托车操纵拉索钢丝绳
- QC/T629——2021 汽车遮阳板
- QC/T932-2012 道路运输液体危险货物罐式车辆紧急切断阀
- QC/T29115-2013 摩托车和轻便摩托车产品质量检验规程
- QC/T1028-2016 汽车真空单向阀性能要求及试验方法
- QC/T861-2011 盲孔平头六角铆螺母
- QC/T29102-92 汽车化油器质量分等
- QC/T29106-2014 汽车电线束技术条件
- QC/T817-2009 摩托车和轻便摩托车簧片阀式二次空气补给机构耐久性要求与试验方法
- QC/T881-2011 塑料用焊接螺柱
- 行业新闻
网站备案号:湘ICP备2023016450号-1