- 您的位置:
- 标准下载网 >>
- 标准分类 >>
- 铁路运输行业标准(TB) >>
- TB/T 1718.2-2017 机车车辆轮对组装第2部分:车辆
标准号:
TB/T 1718.2-2017
标准名称:
机车车辆轮对组装第2部分:车辆
标准类别:
铁路运输行业标准(TB)
标准状态:
现行出版语种:
简体中文下载格式:
.zip .pdf下载大小:
3.40 MB

点击下载
标准简介:
TB/T 1718.2-2017.Wheelsets assembly for locomotive and rolling stock-Part 2: Railway rolling stock.
1范围
TB/T 1718.2规定了车辆轮对零部件技术要求、轮对组装技术要求、检验、标记、涂装与防护。
TB/T 1718.2适用于铁道车辆最高运行速度小于或等于200km/h的新制车轮..新制车轴和新制制动盘的组装。
TB/T 1718.2不适用于动力轨道车辆轮对组装和注油压装轮对组装。
2规范性引用文件
下列文件对于本文件的应用是必不可少的。凡是注日期的引用文件,仅注日期的版本适用于本文件。凡是不注日期的引用文件,其最新版本(包括所有的修改单)适用于本文件。
TB/T 1010铁道 车辆轮对及轴承型式与基本尺寸
TB/T 1013碳素 钢铸钢车轮
TB/T 2708铁路快速客 车辗钢整体车轮技术条件
TB/T 2817铁道 车辆用辗钢整体车轮技术条件
TB/T 2945铁道 车辆用LZ50钢车轴及钢坯技术条件
TB/T2980机车车辆用制动盘
3零部件技术要 求
3.1总则
车轴、车轮.制动盘应符合按规定程序审批的产品图样及技术文件的要求。
3.2车轴
3.2.1车轴应符合 TB/T 1010 ,TB/T 2945或相应的技术文件的要求。
3.2.2轮座( 盘座)的终加工可以采用磨削或滚压工艺。采用滚压工艺作为终加工时,轮座(盘座)终车削加工表面粗糙度Ra上限值为3.2 μm后方可进行滚压加工。轮座(盘座)经磨削或滚压加工后表面粗糙度Ra上限值为1.6 μm,圆度公差为0.02 mm, 货车轮座(盘座)的圆柱度公差为0.05 mm,客车轮座(盘座)的圆柱度公差为0.015 mm,客车轮座(盘座)的跳动为0.03 mm。其大端应在内侧。

部分标准内容:
中华人民共和国铁道行业标准
TB/T1718.2—2017
代替TB/T1718—2003和部分代替TB/T2562—1995机车车辆轮对组装
第2部分:车辆
Wheelsets assembly for locomotive and rolling stock --Part2:Railwayrolling stock
2017-05-06发布
国家铁路局发布
2017-12-01实施
规范性引用文件
零部件技术要求…
4轮对组装技术要求
4.1基本要求
4.2车轮(制动盘)与车轴压装
4.3车轮和车轴的热装
成品轮对
5检验
标记、涂装与防护
附录A(规范性附录)
轮对组装压装力曲线及说明
TB/T1718.2—2017
TB/T1718.2—2017
TB/T1718《机车车辆轮对组装》分为三个部分:第1部分:机车;
一第2部分:车辆:
一第3部分:动车组。
本部分为TB/T1718的第2部分。
本部分按照CB/T1.1一2009给出的规则起草。本部分代替TB/T1718—2003《铁道车辆轮对组装技术条件》和部分代替TB/T2562—1995《铁道客车用车轮静平衡、轮对动平衡试验方法》。本部分以TB/T1718一2003为主,纳人了TB/T25621995中的最高运行速度小于或等于200km/h轮对动不平衡的内容。与TB/T1718一2003相比,本部分主要技术变化如下:
一修改了同一车轴组装的铸钢车轮轮辋宽度差(见表1,2003年版的表1):一删除了盘毂孔加工后的圆度、圆柱度和表面粗糙度的要求(见2003年版的4.3.6);删除了轮毂孔与轮毂外侧端面的过渡圆弧半径的要求(见2003年版的4.3.7);修改了车轮、制动盘静不平衡位置的要求(见4.1.3,2003年版的表3);增加了轮座(盘座)表面及轮毂孔(盘毂孔)内径面可涂抹矿物油的要求(见4.2.1):一增加了轮对组装后轮轴有效突悬量的要求(见4.2.5);一增加了LZ45CrV钢车轴的压装力的要求(见表2):修改了轮对压装后,如压装压力曲线不合格,第二次组装的要求(见4.2.8、A.2.6,2003年版的4.4.7、A.2.6):
修改了注油压退的要求(见4.2.10,2003年版的4.6);一增加了车轮和车轴热装的要求(见4.3);修改了轮对组装后要求(见表3,2003年版的表3);一增加了轮对组装后的动不平衡规定(见4.4.3);删除了压装曲线保存期管理性内容(见2003年版的4.4.4,A.2.7)。本部分由中车戚墅堰机车车辆工艺研究所有限公司归口。本部分起草单位:中国铁道科学研究院标准计量研究所、中车戚墅堰机车车辆工艺研究所有限公司、中车长春轨道客车股份有限公司、中车青岛四方车辆研究所有限公司、中车长江车辆有限公司、中国铁道科学研究院金属及化学研究所。本部分主要起草人:高俊莉、蒋田芳、赵文学、刁克军、胡宏伟、张澎湃、马作为。本部分代替标准的历次版本发布情况:TB/T1718—1987TB/T1718—1991、TB/T1718—2003。Ⅱ
1范围
机车车辆轮对组装
第2部分:车辆
TB/T1718.2-2017
TB/T1718本部分规定了车辆轮对零部件技术要求、轮对组装技术要求、检验、标记、涂装与防护。
本部分适用于铁道车辆最高运行速度小于或等于200km/h的新制车轮、新制车轴和新制制动盘的组装。
本部分不适用于动力轨道车辆轮对组装和注油压装轮对组装。2规范性引用文件
下列文件对于本文件的应用是必不可少的。凡是注日期的引用文件,仅注日期的版本适用于本文件。凡是不注日期的引用文件,其最新版本(包括所有的修改单)适用于本文件。TB/T1010铁道车辆轮对及轴承型式与基本尺寸TB/T1013
碳素钢铸钢车轮
TB/T2708
铁路快速客车辗钢整体车轮技术条件TB/T2817
铁道车辆用辗钢整体车轮技术条件TB/T2945
铁道车辆用LZ50钢车轴及钢坏技术条件TB/T2980
机车车辆用制动盘
3零部件技术要求
3.1总则
车轴、车轮、制动盘应符合按规定程序审批的产品图样及技术文件的要求。3.2车轴
3.2.1车轴应符合TB/T1010、TB/T2945或相应的技术文件的要求。3.2.2轮座(盘座)的终加工可以采用磨削或滚压工艺。采用滚压工艺作为终加工时,轮座(盘座)终车削加工表面粗糙度Ra上限值为3.2μm后方可进行滚压加工。轮座(盘座)经磨削或滚压加工后表面粗糙度Ra上限值为1.6μm,圆度公差为0.02mm,货车轮座(盘座)的圆柱度公差为0.05mm,客车轮座(盘座)的圆柱度公差为0.015mm,客车轮座(盘座)的跳动为0.03mm。其大端应在内侧。
3.3车轮
3.3.1车轮应符合TB/T1010,TB/T1013、TB/T2817、TB/T2708或相应的技术文件的要求。3.3.2轮毂孔加工后的圆度公差为0.02mm,圆柱度公差为0.05mm,且大端应在内侧;轮毂孔内径表面粗糙度Ra上限值为6.3μm。3.3.3当图纸未规定时,轮毂孔加工后,轮毂孔与轮毂内侧端面的过渡圆弧半径为3mm。3.4制动盘
制动盘应符合TB/T2980或相应的技术文件的要求。1
TB/T1718.2—2017
4轮对组装技术要求
4.1基本要求
4.1.1同一车轴上应组装同型号、同材质、同厂家生产的车轮及同型号、同材质、同厂家生产的制动盘。
同一车轴上组装的两个车轮轮辋宽度差应符合表1的规定。表1
最高运行速度!
车轮轮辋宽度差
≤120
120160
速度大于120km/h或盘形轮对车辆的轮对静不平衡位置应符合以下规定:两车轮残余静不平衡位置相位差为180°±5°;两制动盘残余静不平衡位置相位差为180°±5°;同侧车轮与制动盘残余不平衡相位差为180°±5°:160200
制动盘静不平衡位置与车轮静不平衡位置应位于同一平面(通过车轴中心线的同一平面)。d)
轮对组装时,轮毂孔(盘毂孔)、轮座(盘座)及相关量具宜在相同环境下同温8h后进行测量、4.1.4
选配和组装。
4.1.5轮毂孔(盘毂孔)和轮座(盘座)的直径应在规定尺寸范围内,并且同一车轴上两端的轮座直径差不应大于3mm,盘座直径差不应大于2mm。4.1.6轮座与轮毂孔应采取过盈配合,过盈量为轮座直径的0.08%~0.15%。4.2车轮(制动盘)与车轴压装
4.2.1轮对压装前,轮座(盘座)表面及轮毂孔(盘毂孔)内径面应洁净,均匀涂抹植物油或矿物脂(不应采用桐油)。
4.2.2压装车轮(制动盘)时,车轴纵向中心线与压力机活塞中心线一致,并平行压入。4.2.3轮对(制动盘)压装时应采取保护措施,防止轴颈碰伤及轴颈端部墩粗。4.2.4轮轴组装最终压力按轮毂孔直径计算,每100mm的压装力应符合表2的规定。轮轴组装过程的突悬部分不计人压装曲线,压装压力曲线图和过盈量应记录并保存,压力机自动记录器所记录的压装压力曲线图,应符合轮对组装压装力曲线及说明(见附录A)。表2
车轴类型
40钢车轴
50钢车轴
LZ45CrV钢车轴
最小压装力
单位为千牛
最大压装力
4.2.5轮对组装后,车轮内侧与车轴轮座间应有一定的有效突悬量,轮轴有效突悬量宜为2mm3mm,见图1。
4.2.6制动盘毂与盘座的压装过盈量及最终压力应符合产品图样和技术文件。制动盘压装压力曲线和过盈量记录应保存。
4.2.7在压装过程中,自动记录器的压力表与压力曲线的压力值应一致,如不一致时,以压力曲线的压力值为准,允许压力曲线数值小于压力表数值,但相差不应大于49kN。2
TB/T1718.2—2017
轮对压装后,如压装压力曲线不合格,不应将退下的原车轮与原车轴进行第二次压装,在原车4.2.8
轴、车轮表面无损伤的情况下,可重新选配其他车轮、车轴进行压装。分解后有拉伤的车轮、车轴应重新加工,清除缺陷后方可使用。4.2.9
有注油孔车轮组装后车轮上的注油孔应配有防松油堵。车轮
有效突悬量
图1轮轴有效突悬量
有注油孔车轮退轮应采用注油压退方式。车轮退卸时使用带有分级保压功能的超高压注油泵进行分级保压,40MPa到80MPa分别保压1min~2min,至100MPa~130MPa油液渗出,再实施退卸。4.3车轮和车轴的热装
过盈量应符合4.1.6的规定。
热装应在整体车轮加热后进行,车轮加热温度为220℃~240℃,恒温时间宜为180min~4.3.2%
210mino
热装的车轮应加工注油孔及注油槽。轮轴热装后内侧距及轮位差可采用超高压注油方式进行轴向调整。热装轮轴达到相同温度或热装轮轴轴向调整48h后,应进行压力试验。组装应能经得住30s的轴向力F,且车轮与车轴间没有任何位移。当装配长度符合公式(1)时,试验压力F见公式(2)。0.8dm
装配长度的数值,单位为毫米(mm);车轴的轮座直径的名义值,单位为毫米(mm):压力试验的轴向力的数值,单位为千牛(kN)。试验时压力应从0缓慢提升至力F,压力作用在车轮轮毂处。4.4成品轮对
4.4.1轮对组装后应符合表3的规定。表3
≤120km/h
同一轮对两车轮直径差
轮位差
内侧距
1353mm±2mmbzxZ.net
120km/h1353mm±2mm
...(1)
160km/h
TB/T1718.2—2017
盘位差
轮对内侧距任意三处相差
两车轮滚动圆相对于轴中心线径向圆跳动两车轮轮辋内侧面相对于轴中心线端面圆跳动
注:表中为最高运行速度。
货车轮对可不检测。
表3(续)
≤120km/h
≤2mm
120km/h<≤160km/h
≤2mm
4.4.2轮对组装后轮对两踏面间的电阻不应大于0.0102。160km/h<≤200km/h
≤2mm
4.4.3轮对组装后的动不平衡应符合表4的规定。如轮对的残余动不平衡量不符合表4的规定,应用减重法进行轮对动平衡校正,其减重法应符合TB/T2708的规定。表4
最高运行速度
120160
160200
5检验
动不平衡量
5.1轮对组装前及组装过程中应按第3章和4.1~4.3的规定进行检查。5.2轮对组装后应按表1、表3和表4内容进行检查。5.3大于120km/h的轮对或盘形轮对组装后进行动平衡试验时,试验应在专用的轮对动平衡试验机上进行,旋转速度不应低于235r/min。5.4轮对需在绝缘状态下进行检验,用轮对电阻检测仪测量轮对两踏面间的电阻,其电阻值应符合4.4.2的规定。
5.5各项检验中,任何一项不符合规定要求时,均为不合格品。6标记、涂装与防护
6.1标记
轮对组装后应在轴端面按有关规定刻打组装责任单位标记、组装年月日等钢印。6.2涂装与防护
轮对经检验合格,在人库和发货前,应进行如下处理:a)下列部位应涂防腐剂:
轴颈、防尘板座及其附近的加工部位;轮毂的内外端面;
与其他零部件安装配合及需要的部位:4
车轴轴身;
一车轮辐板内外侧面;
轴端面及轴端螺纹孔部位。
车轮踏面、轮缘和轮辋内、外侧面部位不应涂防腐剂。轴颈部分应使用有效的防护方式进行防护,确保不发生锈蚀和碰伤TB/T1718.2—2017
TB/T1718.2—2017
A.1轮对组装压装力曲线理论长度附录A
(规范性附录)
轮对组装压装力曲线及说明
轮对组装压装力曲线理论长度计算见公式(A.1)。L=(S+A-K-)Xi
式中:
L——轮对组装压装力曲线理论长度;S—一车轮轮毂孔长度;
A一一伸出于轮毂孔外端之轮座长度:K一轮座前端锥形引人段长度;
T——车轮轮毂孔内侧之圆弧半径;.(A.1)
i一压力指示器之传达系数,即指示器圆简行程比活塞冲程之缩短系数,根据各厂压力指示器构造决定。
A.2轮对组装压装力曲线图
A.2.1压装力曲线图应均勾平稳上升,其曲线投影长度不小于理论长度的80%,起点陡升不应超过98kN,全部曲线不应有跳动。由于注油沟槽导致的压装曲线局部压力下降不考虑。A.2.2曲线中部不应有下降,平直线长度不应超过该曲线投影长度的10%,平直线的两端均应圆滑过渡。A.2.3曲线末端平直线长度不应超过该曲线投影长度的15%。曲线末端下降的长度不应超过该曲线投影长度的10%,压装力的下降值不应超过按该轮毂孔直径计算的最大压装力的5%,如曲线末端平直和下降同时存在,而压装力下降数值又不超过规定时,其合并长度不应超过该曲线投影长度的15%。A.2.4曲线的最高点压力,不应大于按该轮毂孔直径计算的最大压装力数值,曲线终点的最小压装力,不应小于按该轮毂孔直径计算的最小压装力数值。A.2.5曲线开始上升的一点与终点处的一点(按该轮毂孔直径计算的最小压装力数值的一点)连成一直线,压装曲线应全部在此直线以上。A.2.6轮对压装后,如压装压力曲线不合格,不应将退下的原车轮与原车轴进行第二次压装,在原车轴表面无损伤的情况下,可重新选配其他车轮进行压装,每次压装的压力曲线合并保存。A.2.7每个轮对的压装力曲线图填写下列内容:轴型、轴号、组装责任单位代号、左右侧别、车轮制造标记、轮座直径及轮毂孔直径(或配合过盈量)、最终压装力、压装年月日等。A.2.8车轮压装压力曲线图例见图A.1~图A.20。1470
良好曲线(L/L≥80%)
合格曲线(陡升T≤98kN)
合格曲线(末段平直线1/L。≤15%)La
合格曲线(末段下降T/Tmx≤5%,LsL。≤10%)L
TB/T1718.2—2017
合格曲线[末段平直线与下降(1+l,)/L。≤15%,T,/T<5%]图A.5
合格曲线(中间低凹)
TB/T1718.2—2017
合格曲线(中间平直线12/L,≤10%)图A.8
合格曲线(最小压装力T≥Tmin)合格曲线(最大压装力T≤T..)不合格曲线(各段平直线长总和/L>20%)Ln
不合格曲线(曲线短L/L<80%)
不合格曲线(陡升超过T>98kN)Lo
不合格曲线(末段平直线长1/L。>15%)Lo
不合格曲线(末段下降线长1L。>10%)L
TB/T1718.2—2017
不合格曲线[末段平直线和下降线长超过(L,+L)/L。>15%]图A.16
不合格曲线(中间凹下)
小提示:此标准内容仅展示完整标准里的部分截取内容,若需要完整标准请到上方自行免费下载完整标准文档。

标准图片预览:
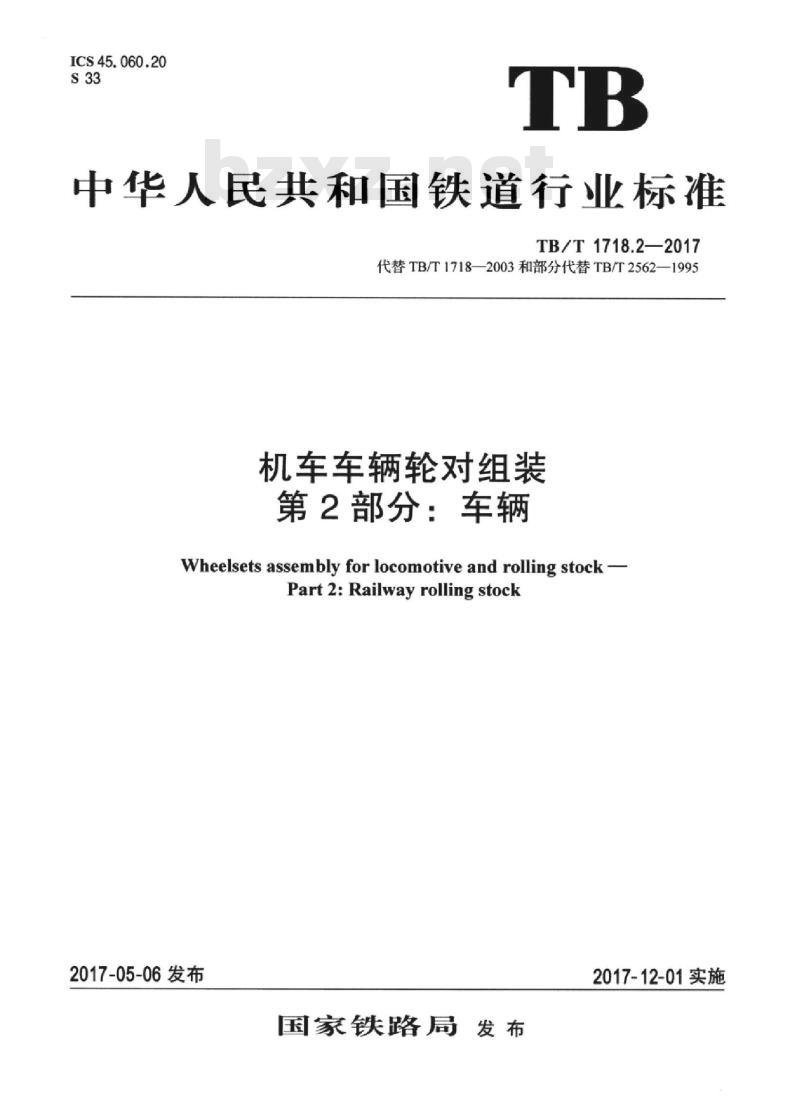
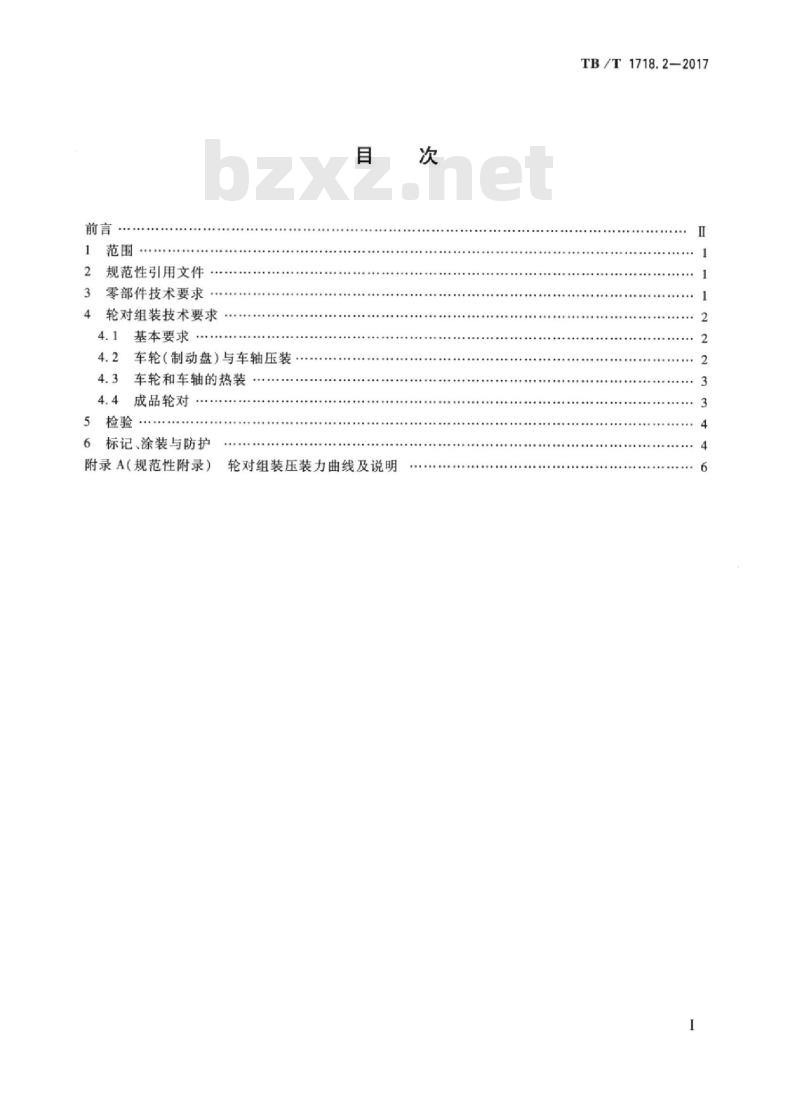
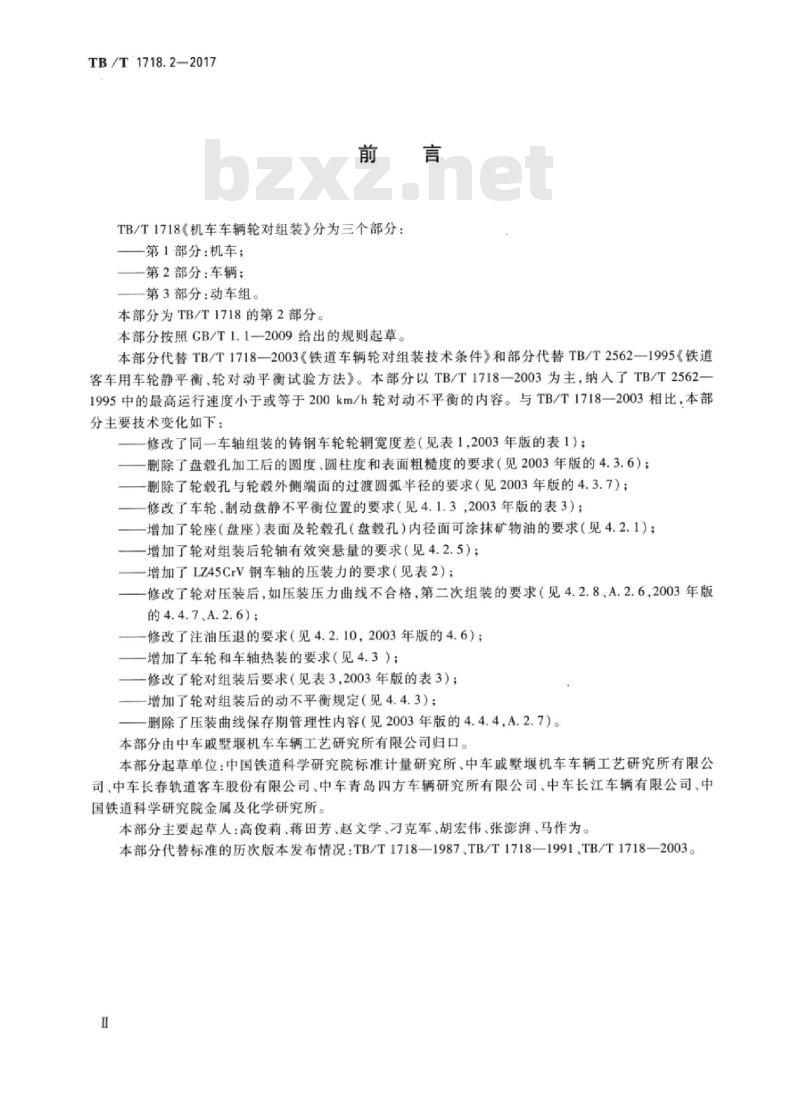
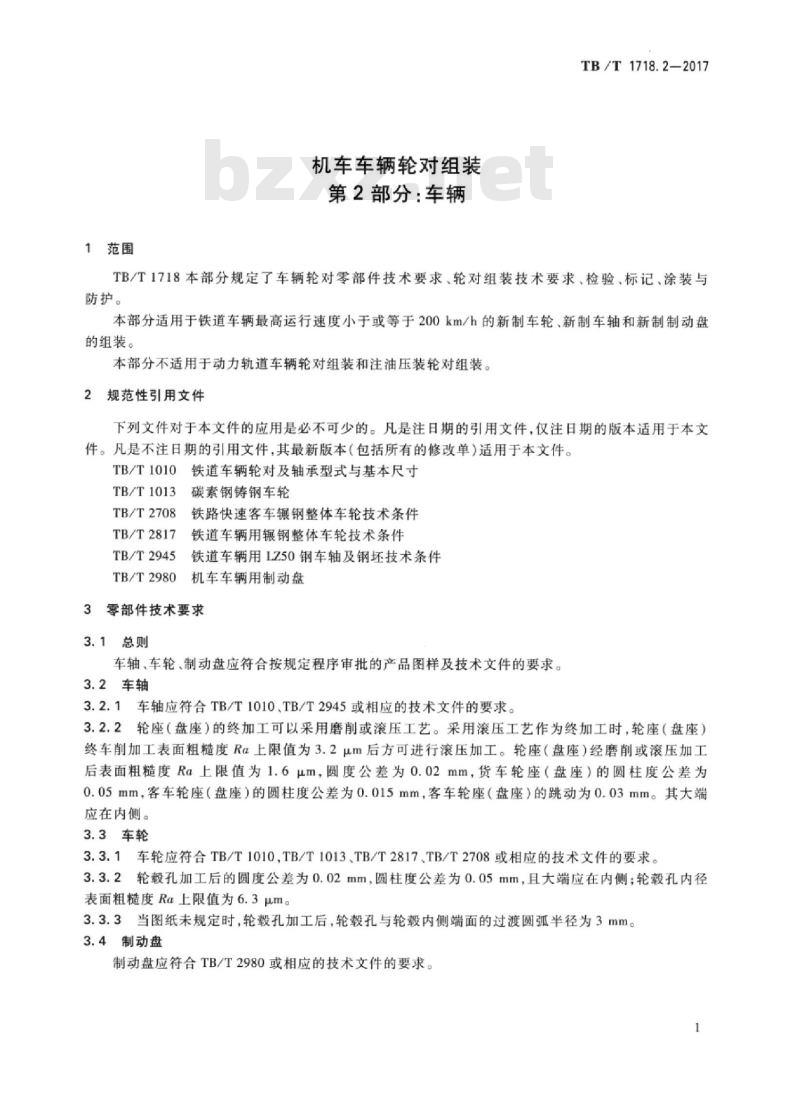
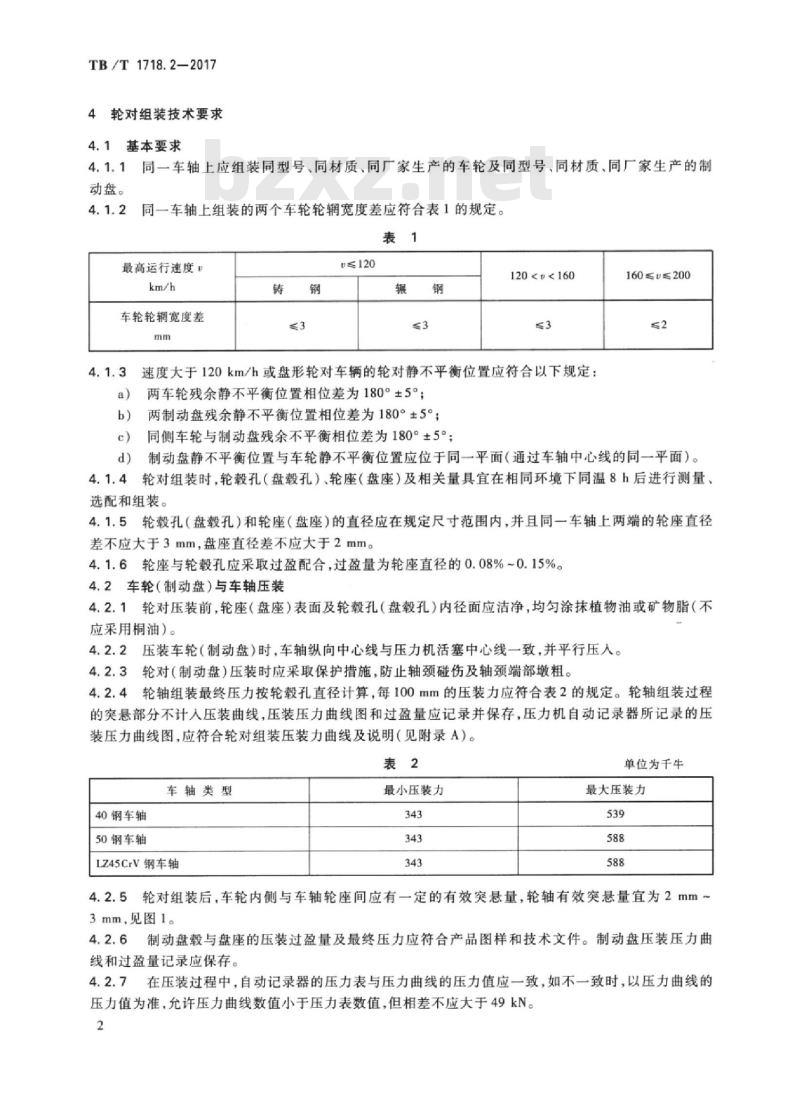
- 热门标准
- TB铁路运输标准
- TB10122-2008 铁路路堑边坡光面(预裂)爆破技术规程
- TB/T1760-1986 客车门锁技术条件
- TB/T2563-1995 内燃机车用柴油机机体清洁度测定方法
- TB/T1632.4-2005 钢轨焊接 第4部分:气压焊接
- TB/T2599-1996 细长钢管内壁涂塑技术条件
- TB/T2769.9-1997 重型轨道车试验方法动力学性能试验方法及评定标准
- TB/T3170-2007 货车车钩、钩尾框采购和验收技术条件
- TB/T2521-1995 电力机车平波电抗器装车后温升与电感值试验计算方法
- TB/T2820.1-1997 铁路桥隧建筑物劣化评定标准钢梁
- TB/T2336-93 铁路行李、包裹运输包装技术条件
- TB/T1869.4-2013 铁路信号用变压器第4部分:25 Hz系列轨道变压器
- TB/T2472-93D ●S型道口闪光器
- TB/T3416.3-2015 动车组编码标识系统第3部分:安装地点与位置的标识
- TB/T3264-2011 动车司机座椅
- TB10441-2008 铁路建设项目现场管理规范
- 行业新闻
网站备案号:湘ICP备2023016450号-1