- 您的位置:
- 标准下载网 >>
- 标准分类 >>
- 铁路运输行业标准(TB) >>
- TB/T 3136-2006 机车车辆不落轮车床技术条件
标准号:
TB/T 3136-2006
标准名称:
机车车辆不落轮车床技术条件
标准类别:
铁路运输行业标准(TB)
标准状态:
现行出版语种:
简体中文下载格式:
.zip .pdf下载大小:
3.72 MB

点击下载
标准简介:
TB/T 3136-2006.Technical specification for underfloor wheel sets lathe of locomotive and rolling stock.
1范围
TB/T 3136规定了机车车辆不落轮车床的技术要求、试验方法、精度检验、检验规则等。
TB/T 3136适用于铁路机车、车辆、动车组等轨道列车不落轮检修轮对时切削加工车轮轮缘及踏面的不落轮车床(以下简称车床)。
2规范性引用文件
下列文件中的条款通过本标准的引用而成为本标准的条款。凡是注日期的引用文件,其随后所有的修改单(不包括勘误的内容)或修订版均不适用于本标准然而,鼓励根据本标准达成协议的各方研究是否可使用这些文件的最新版本。凡是不注日期的引用文件,其最新版本适用于本标准。
GB/T 3766- 2001 液压系统通 用技术条件(eqv ISO 4413:1998)
GB 5226.1- -2002 机械安全 机械电气设备第 1部分:通用技术条件(IDT IEC 60204-1:2000)
GB/T 7344- -1997 交流伺服电动机通 用技术条件
GB/T 7935- -2005 液压元件通用技术条件
GB/T 9061金属切削机床 通 用技术条件
GB 15760金属切削机床 安全防护通用技术条件
GB/T 16439-1996交流伺服 系统通用技术条件
GB/T 16769-1997金属切削机床 噪声声 压级测量方法
GB/T 17162-1997 机床速度 和进给量
GB/T 17421.1-1998 机床检验通则第1部分:在无负荷或精加工条件下机床的几何精度(eqvISO 230-1 : 1996)
GB/T 17421.2-2000 机床检验通则 第 2部分:数控轴线的定位精度和重复定位精度的确定(eqv ISO 230-2: 1997)
GB/T 17587.3-1998 滚珠丝杠副第3部份:验收条件和验收检验
JB/T 3997-1994金属切削机床灰铸铁件技术条件
JB/T 6105-1992数控机床液压泵站 技术条件
JB/T 8356.1-1996机床包装 技术条件

部分标准内容:
中华人民共和国铁道行业标准
TB/T3136—2006
机车车辆不落轮车床技术条件
Technical specification for underfloor wheel sets latheof locomotive and rolling stock2006-08-07发布
2007-01-01实施
中华人民共和国铁道部发布
规范性引用文件
技术要求
试验方法
精度检验
检验规则
附录A(资料性附录)
不落轮车床试验记录格式
TB/T3136—2006
TB/T3136-2006
本标准由铁道部经济规划研究院提出并归口。本标准起草单位:铁道部经济规划研究院、广汉快速铁路设备有限公司。本标准起草人:张逸凡、孙新、刘复川、邓家才、张纯福、桑翠江、曾勇、赵桂荣。1范围
机车车辆不落轮车床技术条件
TB/T3136—2006
本标准规定了机车车辆不落轮车床的技术要求、试验方法、精度检验、检验规则等。本标准适用于铁路机车、车辆、动车组等轨道列车不落轮检修轮对时切削加工车轮轮缘及踏面的不落轮车床(以下简称车床)。
2规范性引用文件
下列文件中的条款通过本标准的引用而成为本标准的条款。凡是注日期的引用文件,其随后所有的修改单(不包括勘误的内容)或修订版均不适用于本标准,然而,鼓励根据本标准达成协议的各方研究是否可使用这些文件的最新版本。凡是不注日期的引用文件,其最新版本适用于本标准。GB/T3766—2001液压系统通用技术条件(eqvISO4413:1998)GB5226.1—2002机械安全机械电气设备第1部分:通用技术条件(IDTIEC60204-1:2000)GB/T7344一1997交流伺服电动机通用技术条件5液压元件通用技术条件
GB/T7935—2005
GB/T9061金属切削机床通用技术条件GB15760金属切削机床安全防护通用技术条件GB/T16439—1996交流伺服系统通用技术条件GB/T16769—1997
金属切削机床噪声声压级测量方法GB/T17162—1997机床速度和进给量GB/T17421.1-1998机床检验通则ISO 230-1:1996)
第1部分:在无负荷或精加工条件下机床的几何精度(eqvGB/T17421.2-2000机床检验通则第2部分:数控轴线的定位精度和重复定位精度的确定(eqvISO230-2:1997)
GB/T17587.3—1998滚珠丝杠副第3部份:验收条件和验收检验JB/T3997-1994金属切削机床灰铸铁件技术条件JB/T6105—1992
数控机床液压泵站技术条件
JB/T8356.11996机床包装技术条件JB/T8832—2001
机床数控系统通用技术条件
JB/T9871—1999
JB/T9872—1999
JB/T9873—1999
JB/T9874—1999
JB/T9875—1999
JB/T9877—1999
JB/T10051—1999
金属切削机床精度分级
金属切削机床机械加工件通用技术条件金属切削机床焊接件通用技术条件金属切削机床装配通用技术条件随机技术文件的编制
金属切削机床
金属切削机床清洁度的测定
金属切削机床液压系统通用技术条件JB/T102692001
JB/T10270—2001
数控机床直流主轴驱动单元通用技术条件数控机床直流伺服驱动单元通用技术条件数控机床直流主轴电动机通用技术条件JB/T10271--2001
TB/T3136—2006
JB/T10272—2001
数控机床直流伺服电动机通用技术条件JB/T10273—2001
数控机床交流主轴电动机通用技术条件数控机床交流伺服电动机通用技术条件JB/T10274—-2001
JB/T10275—2001
数控机床交流主轴驱动单元通用技术条件JB/T10276—2001数控机床交流伺服驱动单元通用技术条件3技术要求
3.1一般要求
3.1.1车床应符合本标准,并应按经规定程序批准的技术文件设计和制造。3.1.2车床的设计制造应符合GB/T9061、GB/T17162—1997的规定。3.1.3车床的精度分级应按JB/T9871一1999中绝对精度等级V级所对应的机床相对精度等级,选用普通级精度P级。
3.1.4车床的机械结构及数控系统的基本组成3.1.4.1车床的机械结构可由以下部分组成:基础件:床身、底座、驱动滚轮架等机床主体机架;车轮组件驱动系统;
-车轮组件定位夹持装置;
刀架;
车轮型面加工测量与定位装置;轨道系统;
辅助装置:液压、气动、润滑、冷却、防护、吸尘、断屑及切屑输送装置等;特殊功能装置:精度检测、监控装置等。3.1.4.2车床的数控系统应由以下部分组成:计算机CNC控制系统;
可编程序控制器PLC;
伺服驱动单元;
伺服驱动电动机。
3.1.5车床的铸件、机械加工件、焊接件应分别符合JB/T3997—1994、JB/T9872—1999、JB/T9873—1999的有关规定。
3.1.6车床的数控系统应符合GB/T17421.2—2000、JB/T8832—2001的规定。3.1.7车床的电气系统应符合GB5226.1—2002的有关规定。3.1.8车床的液压系统应符合GB/T3766—2001、GB/T7935-2005、JB/T6105—1992、JB/T10051—1999的有关规定。
3.1.9车床的装配应符合JB/T98741999的有关规定。3.1.10车床的随机技术文件应符合JB/T9875--1999的有关规定。3.1.11车床的包装应符合JB/T8356.1-1996的有关规定。3.2安全卫生
3.2.1梯子、走台应设防滑板、栏杆等防护装置。紧急停车开关应设置合理、工作可靠。3.2.2
车床应设有联锁保护、声光报警等安全装置。3.2.3
车床外露易磨损部位应设防护罩。3.2.4
车床应有防止切屑飞溅的安全挡板及切屑收集、断屑和输送装置。3.2.5
车床的噪声应按GB/T16769—1997的规定执行。3.2.6
3.2.7车床的安全防护应符合GB15760的要求。3.3主要零件加工质量
3.3.1床身、床鞍、立柱、主变速箱体等重要零件粗加工后,应进行时效处理。TB/T3136—2006
3.3.2床身与床鞍、床鞍与滑板等导轨副应采取耐磨措施(热处理和精密磨削),如采用钢材嵌人式导轨,硬度不应小于60HRC。
3.3.3传动系统采用的滚珠丝杠副应符合GB/T17587.3—1998的规定。3.3.4部件非加工面应进行防腐处理。3.3.5驱动滚轮应符合以下要求:-驱动滚轮圆跳动不应超过0.06mm;驱动滚轮全跳动不应超过0.08mm;-驱动滚轮同轴度不应超过$0.08mm;-驱动滚轮圆度误差不应超过0.04mm;-驱动滚轮轮廊差不应超过0.5mm;车床一侧两个驱动滚轮相互间直径偏差不应超过0.5mm;3.4车轮组件驱动系统
3.4.1车轮组件驱动系统采用机械摩擦传动。3.4.2驱动系统采用的交直流主轴驱动单元应分别符合JB/T10269—2001、JB/T10275—2001的有关规定。
3.4.3驱动系统采用的交直流主轴电动机应分别符合JB/T10271—2001、JB/T10273—2001的有关规定。
驱动系统的主轴组件、皮带轮出厂前应进行平衡试验。3.4.5驱动系统应有可靠的轴向和径向定位装置。3.4.6驱动滚轮架应能及时补偿加工后轮径变小引起的垂直方向位移量,且驱动滚轮应能在加工过程中与车轮稳定接触。
3.4.7车床的控制系统如采用电子滑动测控器装置,应能监测驱动滚轮和车轮之间产生的滑动现象,如切削速度改变较大,应自动降低进给量,调整到原状态,发生故障时,应自动停车。3.5车轮组件定位夹持装置
3.5.1车床在定位夹紧时,应保证对车轮组件的测量和切削刀具参考点位置不变。3.5.2定位夹持方式可分为:
外轴箱定位;
-内轴箱定位;
外部夹持;
一内部夹持。
3.5.3定位夹持装置应能满足机车、车辆、动车组车轮组件的定位夹紧及加工精度要求。3.5.4车轮组件的轴向定位装置,应有足够的制审力,防止加工过程中的轴向位移。3.6伺服进给系统bZxz.net
3.6.1伺服进给系统采用的交直流伺服驱动单元应分别符合GB/T16439—1996、JB/T10270—2001JB/T10276—2001的有关规定。
3.6.2伺服进给系统采用的交直流伺服电动机应分别符合GB/T7344—1997、JB/T10272—2001、JB/T10274—2001的要求。
3.6.3伺服进给系统应保证刀架在进给过程中不出现爬行、位移精度不够、失控等现象。3.7刀架
3.7.1刀架与刀架底座导轨的设计应考虑导轨的导向精度、刀具受力、排屑等因素。3
TB/T3136--2006
3.7.2刀架和刀具的强度应能保证切削加工正常进行。3.7.3刀架的传动系统精度应满足车轮加工的技术要求。3.8车轮型面加工测量与定位装置测量装置应采用自动测量方式,实现车刀的自动定位,并应具备如下功能;-轮径检测;
-轮缘厚度检测;
-轮缘高度检测;
磨耗量检测;
踏面跳动检测;
-轮缘内侧跳动检测;
内侧距测量。
3.9车床通道坐标
车床应建立左、右两个坐标通道,以确定车轮型面加工测量与定位的基准,并进行控制调整加工过程中车轮轴线平行于车床的水平轴线,通道坐标由计算机CNC系统控制,通道坐标X轴与车床刀架径向轨迹运动平行或重合,通道坐标乙轴与车床刀架轴向轨迹运动平行或重合。左右通道坐标如图1所示。X
左通道坐标
1一刀具;
2刀架X向:
3刀架Z向:
4一机床主体。
3.10数控系统
右通道坐标
3.10.1数控系统应采用计算机CNC控制系统和可编程逻辑控制器PLC结合控制车床的切削加工。3.10.2数控系统的软件应具备以下功能:一测量计算车轮磨损型面的数据;一对比名义值确定新的车轮型面,选择最佳进给量;4
一人机对话方式,选择最佳加工程序:一控制调整加工过程中车轮轴线平行于车床的水平轴线;一设置故障的自动诊断、检测、查询及处理程序,并具备安全报警显示功能;一加工前、后检测数据的浏览、输出、打印功能;一加工前,后检测数据的网络传输及远程联网管理功能。TB/T3136—2006
3.10.3数控系统应具备较强的抗干扰能力,易于操作、运行可靠,并能保证车轮的加工精度。3.11轨道系统
车床轨道系统应具有对机车,车辆、动车组不同轴位轮对加工的纵向定位提示功能。3.12清洁度要求
车床的液压系统液压油清洁度检测所含脏物(杂质)不应超过200mg/L,润滑系统润滑油清洁度检测所含脏物(杂质)不应超过400mg/L,检测方法应符合JB/T9877—1999的规定。4试验方法
4.1空运转试验
4.1.1温升试验
车床在不切削状态下空运转,使主轴运转从低速逐步到高速,在最高转速时运转时间不应少于1h,当主轴轴承达到稳定温度后,检查其温度不应大于70℃,温升不应大于40℃。4.1.2一般功能试验
利用按键、开关或人工操纵对车床点动进行功能试验,检验各部分动作的灵活性和功能的可靠性,应进行以下试验:
a)点动单步移动滑座、溜板、滑板等;b)驱动系统功能试验,进行驱动滚轮装置的升降,定位、返回,在驱动工位驱动滚轮任选一种转速进行启动、运转、停止(包括制动)的连续操纵试验,试验不少于7次;c)进给系统任选一种进给速度或进给量,按启动、进给和停止作连续操纵,在X、Z坐标的全部行程做工作进给和快速进给试验,正,反向操纵不少于7次:d)液压、润滑、冷却系统的密封、润滑、冷却性能试验,要求调整方便、动作灵活、润滑良好、冷却充分,各系统无渗漏现象:
e)各种指示灯、数控装置的显示控制等功能试验:f)安全、保险、防护装置功能试验。4.1.3主运动进给运动试验
主运动进给运动应进行以下试验:a)驱动滚轮做低、中、高速的变换试验,转速的实测值与名义值之差不超过10%;b)在Z、X轴的全部行程上,做低、中、高进给速度的变换试验,进给速度的实测值与名义值之差不超过5%。
4.1.4数控系统功能试验
数控系统应进行以下功能试验:a)用数控装置的程序指令进行主运动和进给运动的功能变换试验;b)试验进给坐标的超程,手动数据的输入、位置显示、回基准点、程序序号的指示和检索、程序暂停、程序删除、加工程序、刀具位置补偿、间隙补偿等功能。4.1.5空运转功率试验(抽查)
主运动空运转功率试验应符合GB/T9061的规定。4.1.6整机连续空运转试验
按车轮轮缘及踏面形状加工的仿型程序和车床全部功能的运转状态做连续16h空运转试验,每个5
TB/T3136—2006
循环时间不超过15min,每个循环之间停止时间不应超过1min,整个运转过程不应发生故障。空运转试验记录格式参见附录A。
4.2负荷试验
4.2.1负荷试验应包括:
a)承载工件最大重量的运转试验(抽查):b)主传动系统最大扭矩、最大切削抗力试验;c)主传动系统最大功率试验抽查)。4.2.2负荷试验方法应按GB/T9061的规定执行,记录格式参见附录A。4.3返回基准点试验
溜板或滑板分别在X轴(或Z轴)上的任意位置快速返回基准点,测量其实际停止位置,进行5次返回基准点试验,Z轴、X轴基准点误差分别计算,误差以5次测量的最大差值计。允许误差Z轴不应大于0.01mm,x轴不应大于0.005mm。4.4测量装置重复精度检验
安装在刀架定位盘上的测量头反复伸出并返回多次,检验测量轮端面与检验轮内侧面的距离,重复定位允许误差不应大于0.05mm。5精度检验
5.1检验车床应按本标准的规定并应符合GB/T17421.1—1998、GB/T17421.2-2000中的有关要求。
5.2车床的几何精度检验应按表1的规定进行。表1几何精度检验
检验项目
纵向导
轨水平平
面内的直
充允差
检验方法
检验工具参照GB/T17421.1的
有关条文
在全程上精密水平仪
测量:
专用角形桥
a)左导板
b)右导
横向导在全程上
轨的平行测量:
a)左导
b)右导
5.2.1.2.2.1
纵向导轨水平平面
内的直线度,将水平仪
纵向放置在专用角形
桥板上,等距离移动桥
板,每次移动距离小于
或等于250mm,在导
轨的两端和中间至少
三个位置上进行检验。
误差以水平仪读数
的最大代数差值计
5.4.1.2.2.2
横向导轨的平行度,
将水平仪横向放置在
专用角形桥板上,等距
离移动专用角形桥板。
误差以水平仪读数
的最大代数差值计
表1(续)
检验项目
TB/T3136—2006
检验方法
检验工具参照GB/T17421.1的
有关条文
在全程上检验轮
左、右大
溜板(Z测量:
等高V形铁
向)移动轨
a)左刀于分表
迹对检验架0.03
轮轴线的
平行度
左、右小
溜板X
在全程上检验轮
摩高益块
a)左刀传用角尺
向移动轨
迹对检验架0.02
千分表
轮轴线的
垂直度
5.3车床的工作精度检验应按图2、图3,表2的规定进行。橡触段
表2工作精度检验
检验项目
图2车轮轮廓形状误差
图2滚动圆“D\的圆度误差
图3同一轮对组件上两个车轮的直径偏差图3车轮内侧端面的端面跳动
图3车轮踏面的径向跳动
车轮踏面的表面粗糙度
b)右刀
检验方法
用轮缘踏面样板及塞尺检验
用百分表检验
用专用量具检验
用百分表检验
用百分表检验
比较样块检验
5.4.2.2.3
把检验轮通过等高
V形铁放在车床的基
推面上,在大溜板上设
置带磁力表座的干分
表,移动大溜板进行检
误差以千分表的最
大读数计
5.5.1.2.5
溜板两导轨
动小滴
吴差以千分表的最
大读数计
E≤0.3,F<0.2
R。的上限值为12.5μm
TB/T3136-2006
5.4验收之前应调整好车床的安装水平及与精度性能有关的机构,如车床上方安装输人轨道(含活动轨道),两轨顶面平行度允差为2mm。车床床身的水平允差为0.06mm/m。车床床身纵向轴线与车床上方安装轨道的对称中心线的夹角为90°,允差为5。车床具体的安装要求(包括基础)应由制造厂提供。
6检验规则
6.1出厂检验
6.1.1车床出厂前应按本标准的规定进行检验,经厂质量检验部门确认合格后,方可出厂。6.1.2制造厂应向用户提供传感器的精度等级、误差、检定周期等资料。6.1.3出厂检验的试验项目应按本标第4章、第5章的有关规定进行。6.2型式检验
6.2.1车床符合下列情况之一时,应进行型式检验:新产品定型时;
一产品长期停产、重新投产时。合同有规定时。
6.2.2产品应符合本标准和相关标准的规定,其中试验项目应包括所有抽查试验项目。8
附录A
(资料性附录)
不落轮车床试验记录格式
主运动系统空运转试验记录格式A.1
主运动系统空运转试验记录格式运转时间
主轴转速
规定值
实测值
2进给系统空运转试验记录格式
进给系统空运转试验记录格式
试验项目
进给量或进给速度
指令值
mm/t或m/min
主传动系统最大扭矩、最大切削抗力试验记录格式空载功率
TB/T3136-2006
输功率
实测值
mm/t或m/min
主传动系统最大扭矩、最大切削抗力试验记录格式试件
主轴转速
切削条件
切削速度
切削深度
进给量
电压电流输人功率
空载功率
切削功率
小提示:此标准内容仅展示完整标准里的部分截取内容,若需要完整标准请到上方自行免费下载完整标准文档。

标准图片预览:
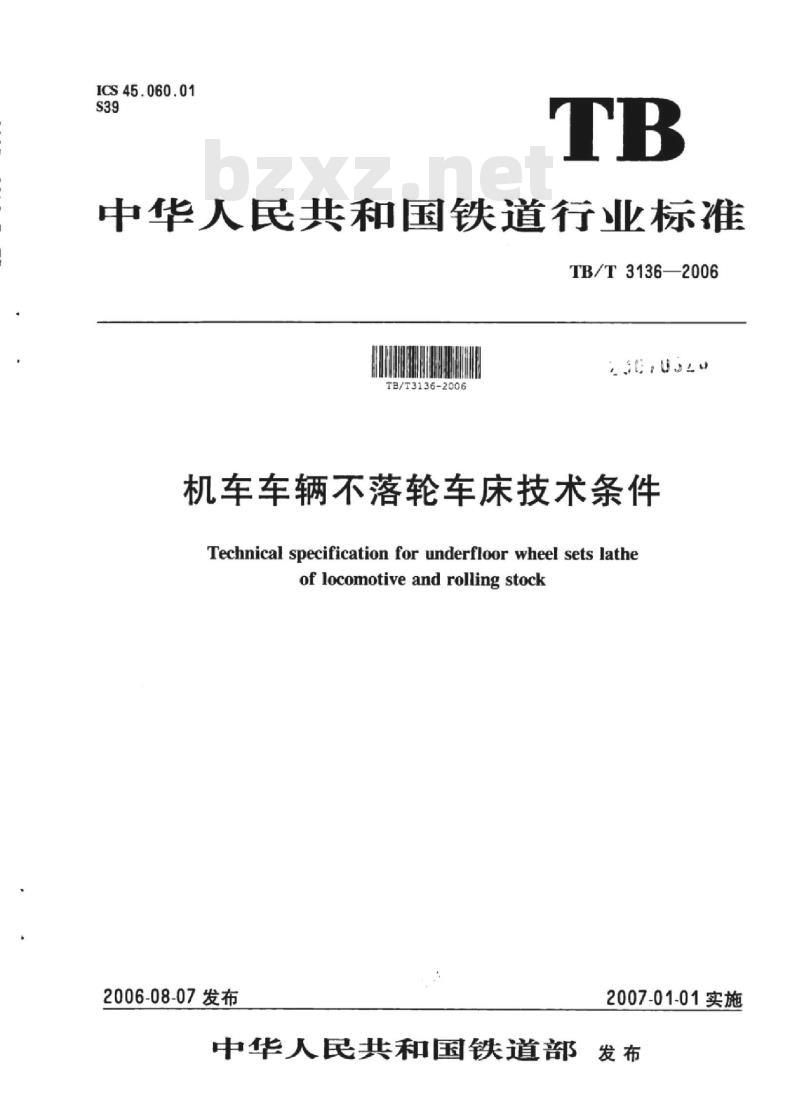
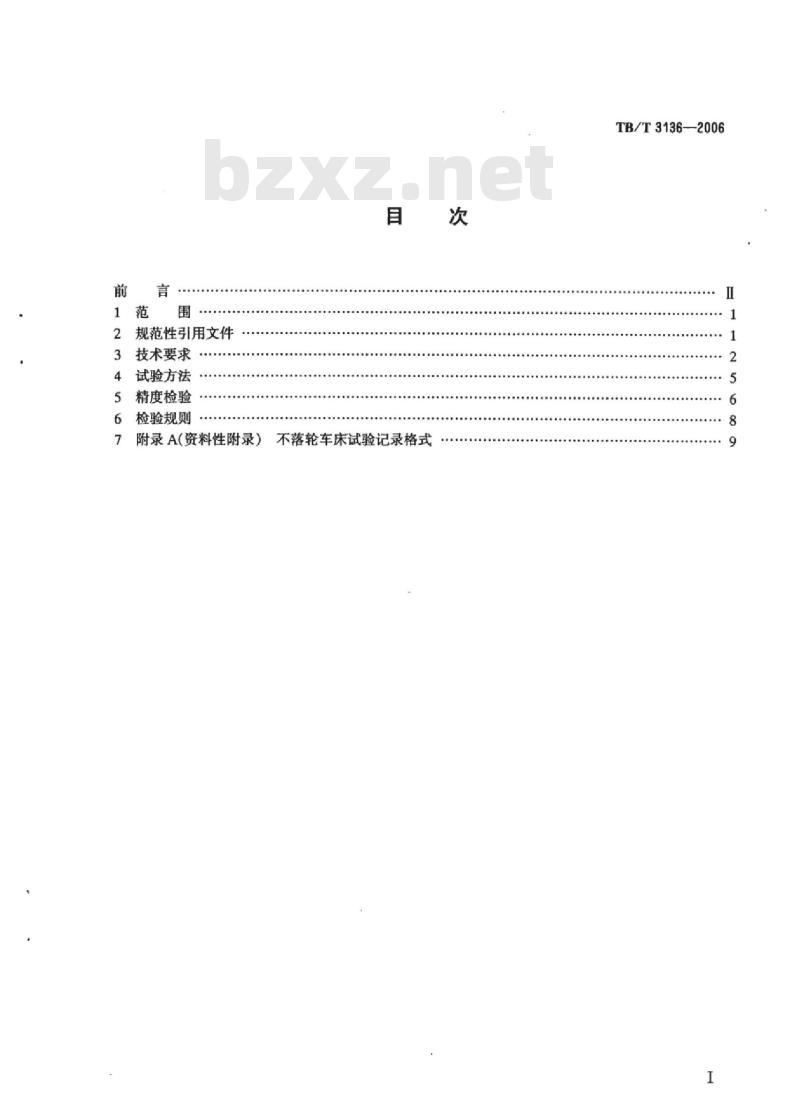
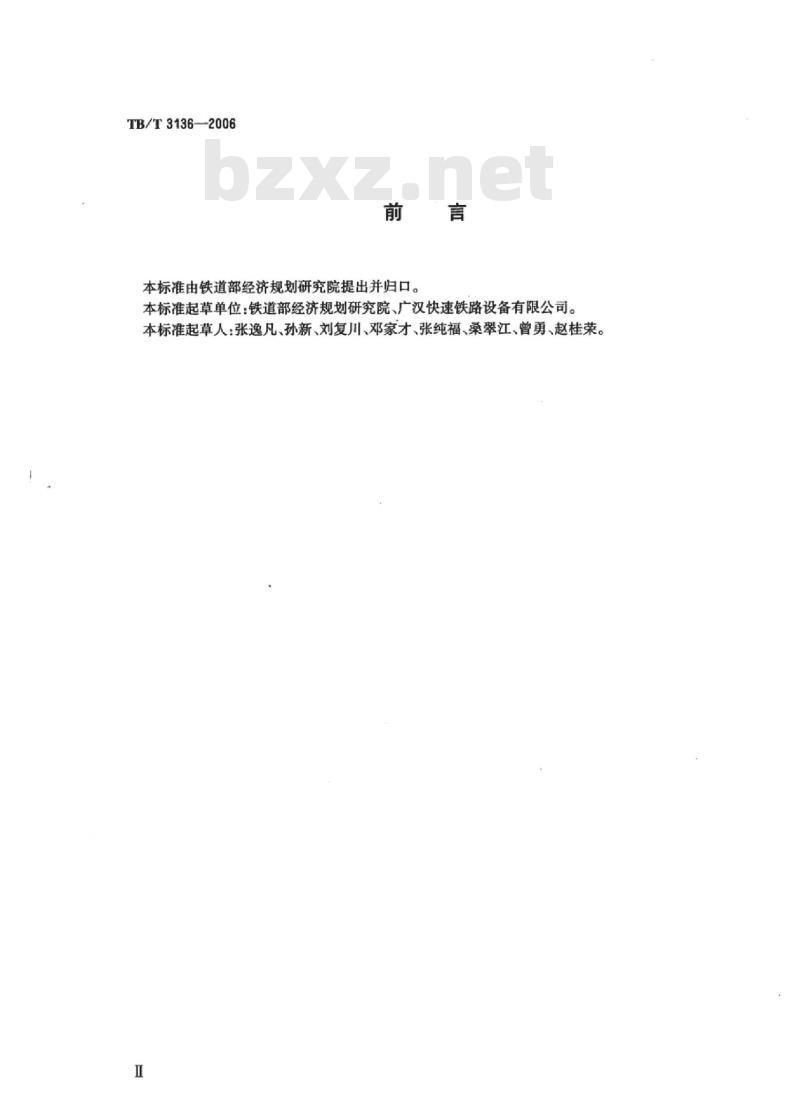
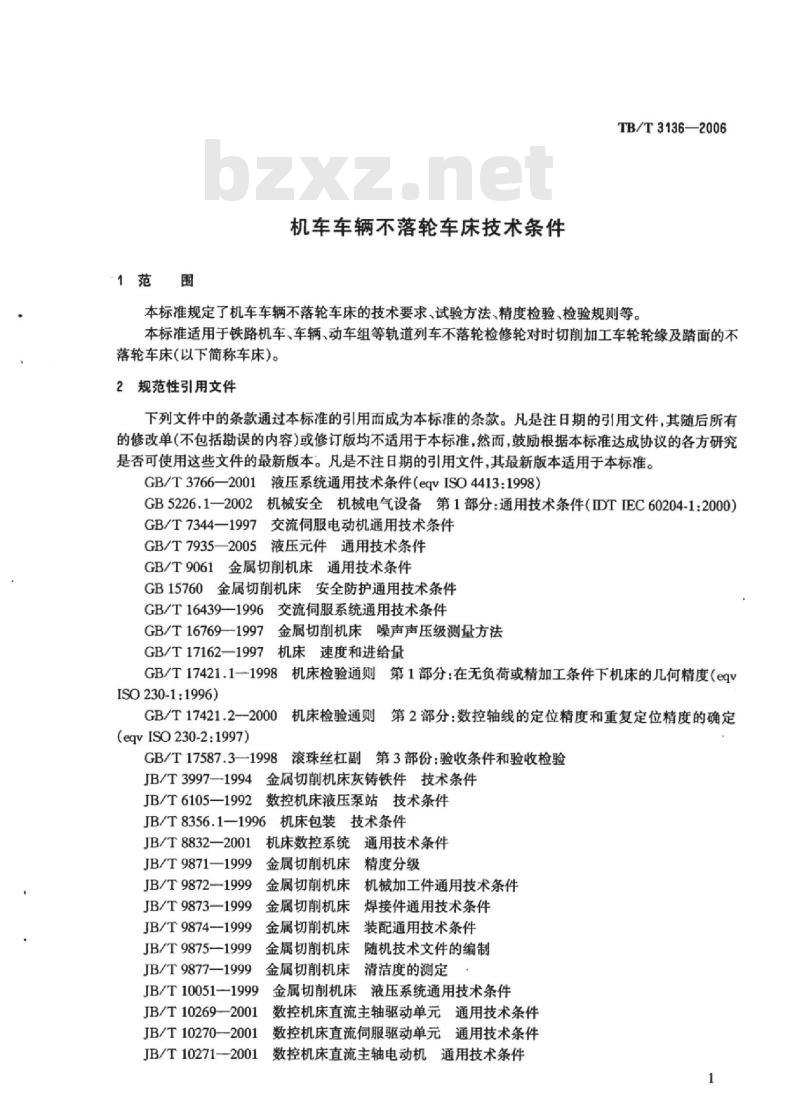
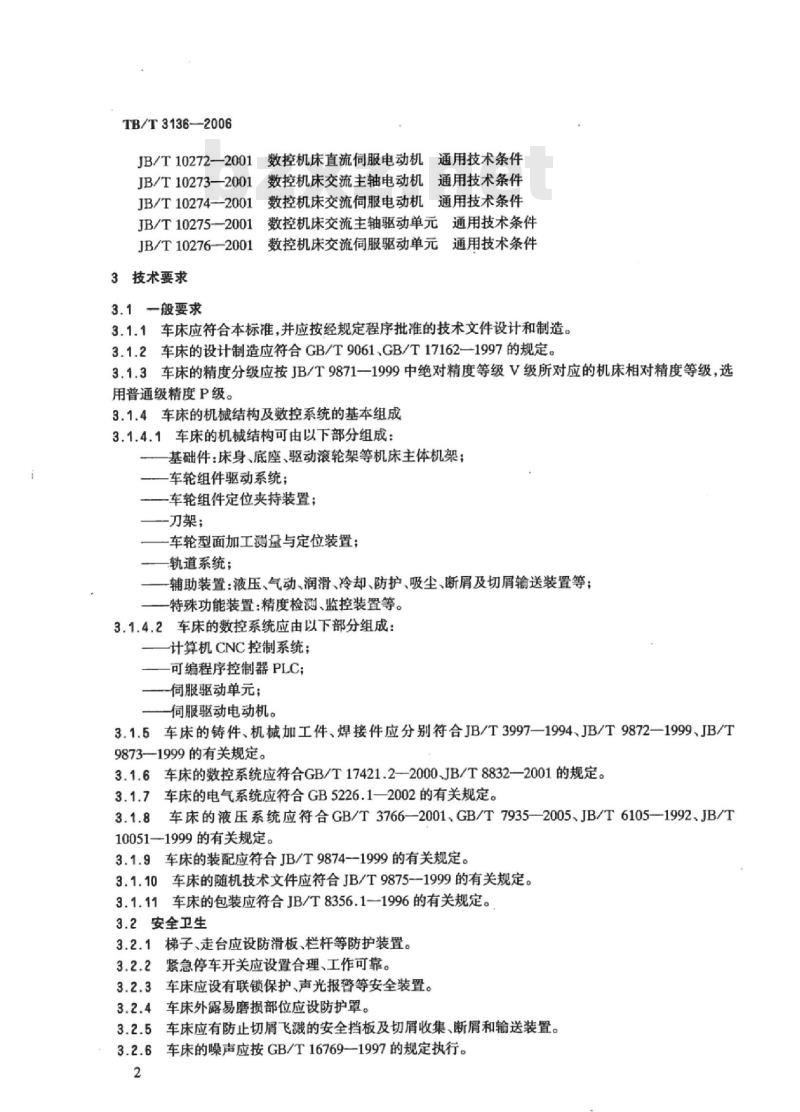
- 其它标准
- 热门标准
- TB铁路运输标准
- TB10122-2008 铁路路堑边坡光面(预裂)爆破技术规程
- TB/T1760-1986 客车门锁技术条件
- TB/T2563-1995 内燃机车用柴油机机体清洁度测定方法
- TB/T1632.4-2005 钢轨焊接 第4部分:气压焊接
- TB/T2599-1996 细长钢管内壁涂塑技术条件
- TB/T2769.9-1997 重型轨道车试验方法动力学性能试验方法及评定标准
- TB/T3170-2007 货车车钩、钩尾框采购和验收技术条件
- TB/T2521-1995 电力机车平波电抗器装车后温升与电感值试验计算方法
- TB/T2820.1-1997 铁路桥隧建筑物劣化评定标准钢梁
- TB/T2336-93 铁路行李、包裹运输包装技术条件
- TB/T1869.4-2013 铁路信号用变压器第4部分:25 Hz系列轨道变压器
- TB/T2472-93D ●S型道口闪光器
- TB/T3416.3-2015 动车组编码标识系统第3部分:安装地点与位置的标识
- TB/T3269-2011 铁道货车弹性旁承
- TB/T3264-2011 动车司机座椅
- 行业新闻
网站备案号:湘ICP备2023016450号-1