- 您的位置:
- 标准下载网 >>
- 标准分类 >>
- 机械行业标准(JB) >>
- JB/T 5000.4-2007 重型机械通用技术条件 第4部分:铸铁件
标准号:
JB/T 5000.4-2007
标准名称:
重型机械通用技术条件 第4部分:铸铁件
标准类别:
机械行业标准(JB)
标准状态:
现行-
发布日期:
2007-08-28 -
实施日期:
2008-02-01 出版语种:
简体中文下载格式:
.rar.pdf下载大小:
726.59 KB
标准ICS号:
机械制造>>无屑加工设备>>25.120.20轧制、挤压和拉制设备中标分类号:
冶金>>冶金机械设备>>H90冶金机械设备综合
替代情况:
替代JB/T 5000.4-1998

点击下载
标准简介:
标准下载解压密码:www.bzxz.net
本部分适用于重型机械中用砂型或导热型相仿的铸型中铸造的灰铸铁件和耐热铸铁件。JB/T 5000的本部分规定了铸铁件技术的要求、试验方法、检验规则、标志与证明。 JB/T 5000.4-2007 重型机械通用技术条件 第4部分:铸铁件 JB/T5000.4-2007

部分标准内容:
ICS25.120.20
备案号:21698—2007
中华人民共和国机械行业标准
JB/T5000.4—2007
代替JB/T5000.4—1998
重型机械通用技术条件
第4部分:铸铁件
Heavy mechanical general techniques and standardsPart4:Ironcating
2007-08-28发布
2008-02-01实施
中华人民共和国国家发展和改革委员会发布前言,
1范围..
2规范性引用文件.
3技术要求
3.1铸铁件牌号、化学成分和力学性能3.2尺寸公差及公差带的分布
错型(错箱)
3.4加工余量
铸件的几何形状、尺寸
铸件的热处理,
铸件重量公差
铸件的冒口切割余量及其处理方法表面质量要求,
3.10铸件的补焊.
喷丸、涂底漆
试验方法,
检验规则
检验权利和检验地点
批量的划定
试验次数、试验结果的评定和复验5.4几何形状和尺寸
铸件表面质量.
试验的有效性
5.7铸铁件的理化检查
6标志与证明.
附录A(规范性附录)铸铁件的理化检验.图1尺寸公差与极限尺寸
图2倾斜部位的尺寸公差带,
图3最大错型
图4铸铁圆环
表1铸铁件尺寸公差:
内圆角..
表3起模斜度.
表4铸件加工余量
表5铸铁圆环毛坏尺寸
表6铸件的冒口切割余量
表7在100mmx100mm范围内允许的凹坑大小表8铸件非加工表面粗糙度..
表A.1铸铁件的理化检测项目
JB/T5000.4—2007
JB/T5000《重型机械通用技术条件》分为15部分:第1部分:产品检验;
第2部分:火焰切割件;
第3部分:焊接件;
第4部分:铸铁件;
一第5部分:有色金属铸件;
第6部分:铸钢件;
第7部分:铸钢件补焊;
第8部分:锻件;
-第9部分:切削加工件;
第10部分:装配;
第11部分:配管:
第12部分:涂装:
第13部分:包装;
第14部分:铸钢件无损检测;
第15部分:锻钢件无损检测。
本部分为JB/T5000的第4部分。
本部分代替JB/T5000.4--1998《重型机械通用技术条件铸铁件》。本部分与JB/T5000.4-1998相比,主要变化如下:一对表1中黑框推荐的小批和单件生产铸铁件的尺寸公差等级进行调整。JB/T5000.4—2007
-3.2.4条增加“为减少产生裂纹的危险,内圆角根据工件壁厚应保证表2中的最小值”增加3.2.5起模斜度。
增加3.9.6.3铸件表面粗糙度不含3.9.3和3.9.4允许的缺陷。本部分的附录A是规范性附录。
本部分由中国机械工业联合会提出。本部分由机械工业治金设备标准化技术委员会归口。本部分负责起草单位:第一重型机械集团公司。本部分参加起草单位:西安重型机械研究所。本部分主要起草人:段秀明、李剑平。本部分所代替标准的历次版本发布情况:JB/T5000.4—1998。
1范围
JB/T5000.4--2007
重型机械通用技术条件第4部分:铸铁件JB/T5000的本部分规定了铸铁件的技术要求、试验方法、检验规则、标志与证明。本部分适用于重型机械中用砂型或导热性与砂型相仿的铸型中铸造的灰铸铁件、球墨铸铁件和耐热铸铁件。
2规范性引用文件
下列文件中的条款通过JB/T5000的本部分的引用而成为本部分的条款。凡是注明日期的引用文件,其随后所有的修改单(不包括勘误的内容)或修订版均不适用于本部分,然而,鼓励根据本部分达成协议的各方研究是否可使用这些文件的最新版本。凡是不注日期的引用文件,其最新版本适用于本部分。
GB/T1348球墨铸铁件
GB/T6060.1表面粗糙度比较样块铸造表面(GB/T6060.1--1997,eqVISO2632-3:1979)GB/T6414
铸件尺寸公差与机械加工余量(GB/T6414—1999,eqvISO8062:1994)GB/T9437
耐热铸铁件
GB/T9439
灰铸铁件
GB/T11351铸件重量公差
JB/T5000.12重型机械用技术条件第12部分:涂装3技术要求
3.1铸铁件牌号、化学成分和力学性能3.1.1灰铸铁件的牌号和力学性能应符合GB/T9439的规定,化学成分由供方自行决定,但应达到GB/T9439规定的牌号及相应的力学性能指标。如需方对化学成分有特殊要求时由供需双方商定。3.1.2球墨铸铁件的牌号和力学性能应符合GB/T1348的规定,化学成分由供方自行决定,但应达到GB/T1348规定的牌号及相应的力学性能指标。如需方对化学成分有特殊要求时由供需双方商定。
3.1.3耐热铸铁件的牌号、化学成分和力学性能应符合GB/T9437的规定。3.2尺寸公差及公差带的分布
3.2.1铸件尺寸公差应符合GB/T6414的规定,常用等级代号与公差见表1。同一铸件应选用同一种公差等级,公差等级按毛坏铸件基本尺寸选取。3.2.2铸件尺寸公差带应相对于毛坏铸件基本尺寸对称分布,即公差的一半位于基本尺寸之上,另一半位于基本尺寸之下(见图1)。有特殊要求时,公差带也可以不对称分布,但应在图样上标注或技术文件中规定。
毛坏铸件基本尺寸包括必要的机械加工余量(见图1),分为下列三种情况:a)图样中标注的两个非机械加工面间尺寸;b)图样中标注的非机械加工内外径、圆角和圆弧;c)图样中标注的机械加工尺寸加上加工余量(见图1)。JB/T5000.4-2007
毛坏铸件基本尺寸
>25~40
>40~63
>63100
>100~160
>160~250
>250~400
>400~630
>630~1000
>1000~1600
>1600~2500
>2500~4000
>4000~6300
>6300~10000
注1:尺寸公差不包括起模斜度。表1铸铁件尺寸公差
公差等级
单位:mm
注2:图样及技术文件未作规定时,小批和单件生产铸铁件的尺寸公差等级按黑框推荐的等级选取;成批和大量生产铸铁件的尺寸公差等级相应提高两级毛坏铸件基本尺寸
加工后尺寸
加工余量
铸件公差/2
最小极限尺寸
最大极限尺寸
图1尺寸公差与极限尺寸
加工余盘
铸件公差/2
铸件有倾斜的部位,其尺寸公差带应沿倾斜面对称分布(见图2)。2
铸件尺寸公差带
图2倾斜部位的尺寸公差带
JB/T5000.4—2007
3.2.3除非另有规定,壁厚尺寸公差等级可降一级选用。例如:如果图样上标注的一般尺寸公差为CT12,则壁厚尺寸公差为CT13。3.2.4非机械加工铸造内、外圆角或圆弧其最小极限尺寸为图样标注尺寸,最大极限尺寸为图样标注尺寸加表1中公差值。
为减少产生裂纹的危险,内圆角根据工件壁厚应保证表2中的最小值。表2内圆角
单位:mm
最小内圆角
3.2.5起模斜度:
>10~30
0.33×壁厚
铸件的起模斜度满足了铸件和铸模、模型和铸模之间的相互分离要求,由此造成的与毛坏铸件公称形状相比的尺寸和形状变化不记人公差范围。起模斜度相对于毛坏铸件基本尺寸对称分布。推荐的起模斜度见表3。
表3起模斜度
高度mm
起模斜度
高度mm
起模斜度
>18~30
>500~630>630~800
>30~50
>50~80
>1000~
注:高度180~250以上的“起模斜度”是宽度之差。3.3错型(错箱)
>250~315>315~400|>400~500
>80~180>180~250
>1250~
>1600~
>2000~
>2500~
>3150~
除非另有规定,错型值应处在表1所规定的公差范围内(见图3)。当需要进一步限制错型时,应在图样上注明最大错型值。
JB/T5000.4—2007
3.4加工余量
最大错型
最大错型
最小极限尺寸
最大极限尺寸
图3最大错型
最大错型
除非另有规定,要求的机械加工余量适用于整个毛坏铸件,即对所有需机械加工的表面只规定一个值,且该值应根据最终机械加工后成品铸件的最大外形尺寸,在表4中按相应的尺寸范围选取。铸件某一部位在铸态下的最大尺寸应不超过成品尺寸与要求的加工余量及铸造总公差之和(见图1)。当采用斜度时,由斜度引起的铸件最大尺寸变化应另外考虑,如图2所示。3.4.1加工余量是指一个面的加工余量,数值见表4。个旋转体或两个面需加工的表面总加工余量应按表4的2倍计算。
表4铸件加工余量
单位:mm
加工余量
铸件最大尺寸
≤180
>180~500
>500~800
>800~1250
>1250~1600
>1600~2500
>2500~3150
>3150~6300
>6300~10000
小批和单件生产
底面和侧面单个面
注1:机械加工余量不包括起模斜度。孔和顶面加量
注2:“铸件最大尺寸”是指铸件最终机械加工后的最大轮廓尺寸。3.4.2加工余量按铸件最大尺寸选取。成批和大量生产
底面和侧面单个面
孔和顶面加量
3.4.3对于有二次加工(指粗加工后返回铸造车间精整修或二次时效后精加工)的铸件,其加工余量为表4的1.2倍~1.5倍。
3.4.4铸件毛坏尺寸计算示例(见表5)。铸铁圆环(单件生产)见图4。
铸件尺寸公差等级CT12。
铸铁圆环最大尺寸@1000mm,每个面加工余量按表4。表5铸铁圆环毛坏尺寸
加工件公称尺寸
加工余量
注:铸件毛坏尺寸不包括起模斜度。金Www.bzxZ.net
3.5铸件的几何形状、尺寸
尺寸公差
JB/T5000.4—2007
单位:mm
铸件毛坏尺寸
最小尺寸
图4铸铁圆环
铸件的几何形状、尺寸应符合图样或订货技术条件的要求。3.6铸件的热处理
最大尺寸
对铸件有人工时效处理(低温退火)或其他热处理要求时,应在图样或订货技术文件中注明。3.7
铸件重量公差
铸件重量公差按GB/T11351规定执行。当铸件的重量公差作为验收依据时,应在图样或技术文件中注明。
3.8铸件的冒口切割余量及其处理方法3.8.1
铸件的冒口切割余量按表6。
表6铸件的冒口切割余量
单位:mm
冒口残留
最大凸起值
冒口根部最大尺寸
≤6060~100>100~200>200~300>300~400>400~500>500~600>600~800>800~1000>10005
不得超过该处加工余量的1/2,最小要有3mm~5mm的机械加工余量。当铸件置口设置在非加工面上时,应刨磨修平达到表面质量要求。3.8.2
3.8.3铸件冒口一般应在热处理前去除。3.9表面质量要求
3.9.1铸件上的型砂、芯砂、芯骨、多肉、粘砂、夹砂等应铲磨平整,清理干净。3.9.2对错型、凸台铸偏等应给予修正,达到圆滑过渡,以保证外观质量。32
3.9.3铸件表面铸造缺陷,在不影响使用性能的情况下,经清理后符合下列情况者允许存在:a)加工面上的缺陷,经加工应能除去;b)铸件非加工外表面凹坑不得超过表7的规定。50
JB/T5000.4—2007
铸件重量
凹坑尺寸和数量
表7在100mm×100mm范围内允许的凹坑大小≤2000kg
Φ2mm~g3mm,深2mm,三个
注1:重量不大于2000kg的铸件,不大于2mm的散存坑不计。注2:重量大于2000kg的铸件,不大于3mm的散存凹坑不计。3.9.4铸件非加工表面的皱褶,深度小于2mm,间距应大于100mm。3.9.5铸件不允许存在的缺陷:
a)影响铸件使用性能的铸造缺陷,如裂纹、冷隔、缩孔、夹渣等;>2000kg
3mm~6mm,深3mm,三个
b)重要的螺纹孔、滚动元件的工作面、滚轮的踏面等表面的铸造缺陷;c)非加工表面导致泄漏的缺陷:d)在订货文件中注明的其他重要工作面上的缺陷。3.9.6铸件非加工表面的粗糙度的要求3.9.6.1铸件非加工表面的粗糙度应符合表8的规定。表8铸件非加工表面粗糙度
单位:μm
手工干型
Rg≤50
机器干型
R≤50
3.9.6.2铸件表面粗糙度以GB/T6060.1规定的比较样块或自制的比较样件对比检查。比较样件由供需双方协商选定和确定。铸件表面有80%面积不低于比较样块时,则认为合格。铸件表面经检验人员确认不低于比较样件时也认为合格。3.9.6.3铸件表面粗糙度不含3.9.3和3.9.4允许的缺陷。3.9.7铸件如喷丸处理则表面粗糙度以喷丸处理后为准。3.10铸件的补焊
3.10.1铸件在保证使用性能和外观质量的情况下,经技术检验部门同意及需方认可才能进行补焊。3.10.2补焊时必须将补焊部位清理干净、露出母材,以保证补焊质量。补焊时应根据铸件的材质、形状、结构和使用要求等制订可靠的补焊工艺并在补焊过程中严格执行。3.10.3精度稳定性要求较高,且在补焊过程中有可能产生较大应力的铸件应进行消除应力处理,但冷加工后发现的缺陷采用铸308焊条补焊的除外。3.11喷丸、涂底漆
3.11.1机器产品铸件的非加工表面均需喷丸处理或滚筒清理处理,达到清洁度Sa21/2级的要求。喷丸粒度应满足铸件表面质量要求。3.11.2铸件在最后喷丸处理后6h内即应涂底漆。涂底漆时,铸件本身温度和环境温度不得低于涂漆允许的温度。涂漆前,铸件上的粉尘等物应用无油无水压缩空气或吸尘器清理干净。3.11.3有关涂漆的要求按JB/T5000.12的规定。4试验方法
4.1灰铸铁件试验方法应符合GB/T9439的规定。4.2球墨铸铁件试验方法应符合GB/T1348的规定。4.3耐热铸铁件试验方法应符合GB/T9437的规定。5检验规则
5.1检验权利和检验地点
JB/T5000.4—2007
5.1.1铸件应由供方技术检验部门检验和验收。需方有权对铸件进行检验。需方要求参加供方检验时,双方应商定提交检验的日期。若需方在商定的时间未能到场,供方可自行检验,并将检验结果提交需方。5.1.2除供需双方商定只能在需方检验外,最终检验一般在供方进行。供需双方对铸件质量发生争议时,检验可在双方商定的第三方进行。5.2批量的划定
5.2.1由同一包铁水浇注的铸件为一个批量。5.2.2每一批铸件的最大重量为清铲完重2000kg的铸件。经供需双方同意,批量的重量可以变动。5.2.3如果一个铸件的重量大于或等于2000kg时,就单成为一个批量。5.2.4当连续不断地熔化大量同一一牌号的铁水时,以2h内所浇注的铸件为一个批量。5.3试验次数、试验结果的评定和复验5.3.1检验抗拉强度或冲击值时,每批至少取一根抗拉试样或一组(三根)冲击试样进行试验。试验结果符合要求,则该批铸件为合格;如果试验结果达不到要求,再用双倍同批试样进行复验。5.3.2当复验结果都达到要求时,则该批铸件为合格;如果复验中有1/2达不到要求时,则该批铸件为不合格。
若因热处理不当造成不合格时,允许再次热处理,但重复热处理的次数不得超过两次。5.3.3耐热铸铁件每一批铸件应进行一次化学成分的分析,若化学成分不合格,允许用双倍同批试样重新复验一次,试样全合格时为合格。5.3.4,铸件以铸态供货时,如果性能达不到要求,经需方同意,供方可将铸件和其代表的试块进行热处理后重新试验。
5.4几何形状和尺寸
首批铸件和重要铸件,应按图样规定逐件检查几何形状和尺寸。一般铸件及用保证尺寸稳定性方法生产出来的铸件可以抽查,抽查的方法按双方商定的方式进行。5.5铸件表面质量
按3.9要求验收。
5.6试验的有效性
如果不是由于铸件本身的质量问题,而是由于下列原因之一造成试验结果不符合要求时,则该试验无效。
a)试样在试验机上的装卡不当或试验机的操作不当;b)试样有铸造缺陷或试样切削加工不当:c)拉伸试样在标距外断裂;
d)试样拉伸、冲击后在断口上有铸造缺陷。5.7铸铁件的理化检查
铸铁件的理化检查项目见附录A。6标志与证明
6.1重要或单独订货的铸件上应有制造厂的标志。6.2标志的位置、尺寸和方法应由供需双方商定,但要注意不使铸件质量受到损伤。6.3出厂铸件应附有供方检验部门签章的质量证明书,质量证明书应包括下列内容:a)制造厂名或工厂标志:
b)零件号或订货合同号;
c)材料牌号;
d)主要检验结果。
JB/T5000.4--2007
铸铁件的理化检验项目见表A.1。附录A
(规范性附录)
铸铁件的理化检验
铸铁件的理化检验项目
灰铸铁
球墨铸铁
耐热铸铁
化学成分
注:“+”为必检项目,“”
抗拉强度
为抽检项目。
力学性能
仲长率
冲击韧度
中华人民共和国
机械行业标准
重型机械通用技术条件
第4部分:铸铁件
JB/T5000.4—2007
机械工业出版社出版发行
北京市百万庄大街22号
邮政编码:100037
210mm×297mm?0.75印张·21千字2008年2月第1版第1次印刷
书号:15111:8673
网址:http://cmpbook.com(010)88379779
编辑部电话:
直销中心电话:(010)88379693封面无防伪标均为盗版
版权专有
侵权必究
200000
小提示:此标准内容仅展示完整标准里的部分截取内容,若需要完整标准请到上方自行免费下载完整标准文档。
备案号:21698—2007
中华人民共和国机械行业标准
JB/T5000.4—2007
代替JB/T5000.4—1998
重型机械通用技术条件
第4部分:铸铁件
Heavy mechanical general techniques and standardsPart4:Ironcating
2007-08-28发布
2008-02-01实施
中华人民共和国国家发展和改革委员会发布前言,
1范围..
2规范性引用文件.
3技术要求
3.1铸铁件牌号、化学成分和力学性能3.2尺寸公差及公差带的分布
错型(错箱)
3.4加工余量
铸件的几何形状、尺寸
铸件的热处理,
铸件重量公差
铸件的冒口切割余量及其处理方法表面质量要求,
3.10铸件的补焊.
喷丸、涂底漆
试验方法,
检验规则
检验权利和检验地点
批量的划定
试验次数、试验结果的评定和复验5.4几何形状和尺寸
铸件表面质量.
试验的有效性
5.7铸铁件的理化检查
6标志与证明.
附录A(规范性附录)铸铁件的理化检验.图1尺寸公差与极限尺寸
图2倾斜部位的尺寸公差带,
图3最大错型
图4铸铁圆环
表1铸铁件尺寸公差:
内圆角..
表3起模斜度.
表4铸件加工余量
表5铸铁圆环毛坏尺寸
表6铸件的冒口切割余量
表7在100mmx100mm范围内允许的凹坑大小表8铸件非加工表面粗糙度..
表A.1铸铁件的理化检测项目
JB/T5000.4—2007
JB/T5000《重型机械通用技术条件》分为15部分:第1部分:产品检验;
第2部分:火焰切割件;
第3部分:焊接件;
第4部分:铸铁件;
一第5部分:有色金属铸件;
第6部分:铸钢件;
第7部分:铸钢件补焊;
第8部分:锻件;
-第9部分:切削加工件;
第10部分:装配;
第11部分:配管:
第12部分:涂装:
第13部分:包装;
第14部分:铸钢件无损检测;
第15部分:锻钢件无损检测。
本部分为JB/T5000的第4部分。
本部分代替JB/T5000.4--1998《重型机械通用技术条件铸铁件》。本部分与JB/T5000.4-1998相比,主要变化如下:一对表1中黑框推荐的小批和单件生产铸铁件的尺寸公差等级进行调整。JB/T5000.4—2007
-3.2.4条增加“为减少产生裂纹的危险,内圆角根据工件壁厚应保证表2中的最小值”增加3.2.5起模斜度。
增加3.9.6.3铸件表面粗糙度不含3.9.3和3.9.4允许的缺陷。本部分的附录A是规范性附录。
本部分由中国机械工业联合会提出。本部分由机械工业治金设备标准化技术委员会归口。本部分负责起草单位:第一重型机械集团公司。本部分参加起草单位:西安重型机械研究所。本部分主要起草人:段秀明、李剑平。本部分所代替标准的历次版本发布情况:JB/T5000.4—1998。
1范围
JB/T5000.4--2007
重型机械通用技术条件第4部分:铸铁件JB/T5000的本部分规定了铸铁件的技术要求、试验方法、检验规则、标志与证明。本部分适用于重型机械中用砂型或导热性与砂型相仿的铸型中铸造的灰铸铁件、球墨铸铁件和耐热铸铁件。
2规范性引用文件
下列文件中的条款通过JB/T5000的本部分的引用而成为本部分的条款。凡是注明日期的引用文件,其随后所有的修改单(不包括勘误的内容)或修订版均不适用于本部分,然而,鼓励根据本部分达成协议的各方研究是否可使用这些文件的最新版本。凡是不注日期的引用文件,其最新版本适用于本部分。
GB/T1348球墨铸铁件
GB/T6060.1表面粗糙度比较样块铸造表面(GB/T6060.1--1997,eqVISO2632-3:1979)GB/T6414
铸件尺寸公差与机械加工余量(GB/T6414—1999,eqvISO8062:1994)GB/T9437
耐热铸铁件
GB/T9439
灰铸铁件
GB/T11351铸件重量公差
JB/T5000.12重型机械用技术条件第12部分:涂装3技术要求
3.1铸铁件牌号、化学成分和力学性能3.1.1灰铸铁件的牌号和力学性能应符合GB/T9439的规定,化学成分由供方自行决定,但应达到GB/T9439规定的牌号及相应的力学性能指标。如需方对化学成分有特殊要求时由供需双方商定。3.1.2球墨铸铁件的牌号和力学性能应符合GB/T1348的规定,化学成分由供方自行决定,但应达到GB/T1348规定的牌号及相应的力学性能指标。如需方对化学成分有特殊要求时由供需双方商定。
3.1.3耐热铸铁件的牌号、化学成分和力学性能应符合GB/T9437的规定。3.2尺寸公差及公差带的分布
3.2.1铸件尺寸公差应符合GB/T6414的规定,常用等级代号与公差见表1。同一铸件应选用同一种公差等级,公差等级按毛坏铸件基本尺寸选取。3.2.2铸件尺寸公差带应相对于毛坏铸件基本尺寸对称分布,即公差的一半位于基本尺寸之上,另一半位于基本尺寸之下(见图1)。有特殊要求时,公差带也可以不对称分布,但应在图样上标注或技术文件中规定。
毛坏铸件基本尺寸包括必要的机械加工余量(见图1),分为下列三种情况:a)图样中标注的两个非机械加工面间尺寸;b)图样中标注的非机械加工内外径、圆角和圆弧;c)图样中标注的机械加工尺寸加上加工余量(见图1)。JB/T5000.4-2007
毛坏铸件基本尺寸
>25~40
>40~63
>63100
>100~160
>160~250
>250~400
>400~630
>630~1000
>1000~1600
>1600~2500
>2500~4000
>4000~6300
>6300~10000
注1:尺寸公差不包括起模斜度。表1铸铁件尺寸公差
公差等级
单位:mm
注2:图样及技术文件未作规定时,小批和单件生产铸铁件的尺寸公差等级按黑框推荐的等级选取;成批和大量生产铸铁件的尺寸公差等级相应提高两级毛坏铸件基本尺寸
加工后尺寸
加工余量
铸件公差/2
最小极限尺寸
最大极限尺寸
图1尺寸公差与极限尺寸
加工余盘
铸件公差/2
铸件有倾斜的部位,其尺寸公差带应沿倾斜面对称分布(见图2)。2
铸件尺寸公差带
图2倾斜部位的尺寸公差带
JB/T5000.4—2007
3.2.3除非另有规定,壁厚尺寸公差等级可降一级选用。例如:如果图样上标注的一般尺寸公差为CT12,则壁厚尺寸公差为CT13。3.2.4非机械加工铸造内、外圆角或圆弧其最小极限尺寸为图样标注尺寸,最大极限尺寸为图样标注尺寸加表1中公差值。
为减少产生裂纹的危险,内圆角根据工件壁厚应保证表2中的最小值。表2内圆角
单位:mm
最小内圆角
3.2.5起模斜度:
>10~30
0.33×壁厚
铸件的起模斜度满足了铸件和铸模、模型和铸模之间的相互分离要求,由此造成的与毛坏铸件公称形状相比的尺寸和形状变化不记人公差范围。起模斜度相对于毛坏铸件基本尺寸对称分布。推荐的起模斜度见表3。
表3起模斜度
高度mm
起模斜度
高度mm
起模斜度
>18~30
>500~630>630~800
>30~50
>50~80
>1000~
注:高度180~250以上的“起模斜度”是宽度之差。3.3错型(错箱)
>250~315>315~400|>400~500
>80~180>180~250
>1250~
>1600~
>2000~
>2500~
>3150~
除非另有规定,错型值应处在表1所规定的公差范围内(见图3)。当需要进一步限制错型时,应在图样上注明最大错型值。
JB/T5000.4—2007
3.4加工余量
最大错型
最大错型
最小极限尺寸
最大极限尺寸
图3最大错型
最大错型
除非另有规定,要求的机械加工余量适用于整个毛坏铸件,即对所有需机械加工的表面只规定一个值,且该值应根据最终机械加工后成品铸件的最大外形尺寸,在表4中按相应的尺寸范围选取。铸件某一部位在铸态下的最大尺寸应不超过成品尺寸与要求的加工余量及铸造总公差之和(见图1)。当采用斜度时,由斜度引起的铸件最大尺寸变化应另外考虑,如图2所示。3.4.1加工余量是指一个面的加工余量,数值见表4。个旋转体或两个面需加工的表面总加工余量应按表4的2倍计算。
表4铸件加工余量
单位:mm
加工余量
铸件最大尺寸
≤180
>180~500
>500~800
>800~1250
>1250~1600
>1600~2500
>2500~3150
>3150~6300
>6300~10000
小批和单件生产
底面和侧面单个面
注1:机械加工余量不包括起模斜度。孔和顶面加量
注2:“铸件最大尺寸”是指铸件最终机械加工后的最大轮廓尺寸。3.4.2加工余量按铸件最大尺寸选取。成批和大量生产
底面和侧面单个面
孔和顶面加量
3.4.3对于有二次加工(指粗加工后返回铸造车间精整修或二次时效后精加工)的铸件,其加工余量为表4的1.2倍~1.5倍。
3.4.4铸件毛坏尺寸计算示例(见表5)。铸铁圆环(单件生产)见图4。
铸件尺寸公差等级CT12。
铸铁圆环最大尺寸@1000mm,每个面加工余量按表4。表5铸铁圆环毛坏尺寸
加工件公称尺寸
加工余量
注:铸件毛坏尺寸不包括起模斜度。金Www.bzxZ.net
3.5铸件的几何形状、尺寸
尺寸公差
JB/T5000.4—2007
单位:mm
铸件毛坏尺寸
最小尺寸
图4铸铁圆环
铸件的几何形状、尺寸应符合图样或订货技术条件的要求。3.6铸件的热处理
最大尺寸
对铸件有人工时效处理(低温退火)或其他热处理要求时,应在图样或订货技术文件中注明。3.7
铸件重量公差
铸件重量公差按GB/T11351规定执行。当铸件的重量公差作为验收依据时,应在图样或技术文件中注明。
3.8铸件的冒口切割余量及其处理方法3.8.1
铸件的冒口切割余量按表6。
表6铸件的冒口切割余量
单位:mm
冒口残留
最大凸起值
冒口根部最大尺寸
≤6060~100>100~200>200~300>300~400>400~500>500~600>600~800>800~1000>10005
不得超过该处加工余量的1/2,最小要有3mm~5mm的机械加工余量。当铸件置口设置在非加工面上时,应刨磨修平达到表面质量要求。3.8.2
3.8.3铸件冒口一般应在热处理前去除。3.9表面质量要求
3.9.1铸件上的型砂、芯砂、芯骨、多肉、粘砂、夹砂等应铲磨平整,清理干净。3.9.2对错型、凸台铸偏等应给予修正,达到圆滑过渡,以保证外观质量。32
3.9.3铸件表面铸造缺陷,在不影响使用性能的情况下,经清理后符合下列情况者允许存在:a)加工面上的缺陷,经加工应能除去;b)铸件非加工外表面凹坑不得超过表7的规定。50
JB/T5000.4—2007
铸件重量
凹坑尺寸和数量
表7在100mm×100mm范围内允许的凹坑大小≤2000kg
Φ2mm~g3mm,深2mm,三个
注1:重量不大于2000kg的铸件,不大于2mm的散存坑不计。注2:重量大于2000kg的铸件,不大于3mm的散存凹坑不计。3.9.4铸件非加工表面的皱褶,深度小于2mm,间距应大于100mm。3.9.5铸件不允许存在的缺陷:
a)影响铸件使用性能的铸造缺陷,如裂纹、冷隔、缩孔、夹渣等;>2000kg
3mm~6mm,深3mm,三个
b)重要的螺纹孔、滚动元件的工作面、滚轮的踏面等表面的铸造缺陷;c)非加工表面导致泄漏的缺陷:d)在订货文件中注明的其他重要工作面上的缺陷。3.9.6铸件非加工表面的粗糙度的要求3.9.6.1铸件非加工表面的粗糙度应符合表8的规定。表8铸件非加工表面粗糙度
单位:μm
手工干型
Rg≤50
机器干型
R≤50
3.9.6.2铸件表面粗糙度以GB/T6060.1规定的比较样块或自制的比较样件对比检查。比较样件由供需双方协商选定和确定。铸件表面有80%面积不低于比较样块时,则认为合格。铸件表面经检验人员确认不低于比较样件时也认为合格。3.9.6.3铸件表面粗糙度不含3.9.3和3.9.4允许的缺陷。3.9.7铸件如喷丸处理则表面粗糙度以喷丸处理后为准。3.10铸件的补焊
3.10.1铸件在保证使用性能和外观质量的情况下,经技术检验部门同意及需方认可才能进行补焊。3.10.2补焊时必须将补焊部位清理干净、露出母材,以保证补焊质量。补焊时应根据铸件的材质、形状、结构和使用要求等制订可靠的补焊工艺并在补焊过程中严格执行。3.10.3精度稳定性要求较高,且在补焊过程中有可能产生较大应力的铸件应进行消除应力处理,但冷加工后发现的缺陷采用铸308焊条补焊的除外。3.11喷丸、涂底漆
3.11.1机器产品铸件的非加工表面均需喷丸处理或滚筒清理处理,达到清洁度Sa21/2级的要求。喷丸粒度应满足铸件表面质量要求。3.11.2铸件在最后喷丸处理后6h内即应涂底漆。涂底漆时,铸件本身温度和环境温度不得低于涂漆允许的温度。涂漆前,铸件上的粉尘等物应用无油无水压缩空气或吸尘器清理干净。3.11.3有关涂漆的要求按JB/T5000.12的规定。4试验方法
4.1灰铸铁件试验方法应符合GB/T9439的规定。4.2球墨铸铁件试验方法应符合GB/T1348的规定。4.3耐热铸铁件试验方法应符合GB/T9437的规定。5检验规则
5.1检验权利和检验地点
JB/T5000.4—2007
5.1.1铸件应由供方技术检验部门检验和验收。需方有权对铸件进行检验。需方要求参加供方检验时,双方应商定提交检验的日期。若需方在商定的时间未能到场,供方可自行检验,并将检验结果提交需方。5.1.2除供需双方商定只能在需方检验外,最终检验一般在供方进行。供需双方对铸件质量发生争议时,检验可在双方商定的第三方进行。5.2批量的划定
5.2.1由同一包铁水浇注的铸件为一个批量。5.2.2每一批铸件的最大重量为清铲完重2000kg的铸件。经供需双方同意,批量的重量可以变动。5.2.3如果一个铸件的重量大于或等于2000kg时,就单成为一个批量。5.2.4当连续不断地熔化大量同一一牌号的铁水时,以2h内所浇注的铸件为一个批量。5.3试验次数、试验结果的评定和复验5.3.1检验抗拉强度或冲击值时,每批至少取一根抗拉试样或一组(三根)冲击试样进行试验。试验结果符合要求,则该批铸件为合格;如果试验结果达不到要求,再用双倍同批试样进行复验。5.3.2当复验结果都达到要求时,则该批铸件为合格;如果复验中有1/2达不到要求时,则该批铸件为不合格。
若因热处理不当造成不合格时,允许再次热处理,但重复热处理的次数不得超过两次。5.3.3耐热铸铁件每一批铸件应进行一次化学成分的分析,若化学成分不合格,允许用双倍同批试样重新复验一次,试样全合格时为合格。5.3.4,铸件以铸态供货时,如果性能达不到要求,经需方同意,供方可将铸件和其代表的试块进行热处理后重新试验。
5.4几何形状和尺寸
首批铸件和重要铸件,应按图样规定逐件检查几何形状和尺寸。一般铸件及用保证尺寸稳定性方法生产出来的铸件可以抽查,抽查的方法按双方商定的方式进行。5.5铸件表面质量
按3.9要求验收。
5.6试验的有效性
如果不是由于铸件本身的质量问题,而是由于下列原因之一造成试验结果不符合要求时,则该试验无效。
a)试样在试验机上的装卡不当或试验机的操作不当;b)试样有铸造缺陷或试样切削加工不当:c)拉伸试样在标距外断裂;
d)试样拉伸、冲击后在断口上有铸造缺陷。5.7铸铁件的理化检查
铸铁件的理化检查项目见附录A。6标志与证明
6.1重要或单独订货的铸件上应有制造厂的标志。6.2标志的位置、尺寸和方法应由供需双方商定,但要注意不使铸件质量受到损伤。6.3出厂铸件应附有供方检验部门签章的质量证明书,质量证明书应包括下列内容:a)制造厂名或工厂标志:
b)零件号或订货合同号;
c)材料牌号;
d)主要检验结果。
JB/T5000.4--2007
铸铁件的理化检验项目见表A.1。附录A
(规范性附录)
铸铁件的理化检验
铸铁件的理化检验项目
灰铸铁
球墨铸铁
耐热铸铁
化学成分
注:“+”为必检项目,“”
抗拉强度
为抽检项目。
力学性能
仲长率
冲击韧度
中华人民共和国
机械行业标准
重型机械通用技术条件
第4部分:铸铁件
JB/T5000.4—2007
机械工业出版社出版发行
北京市百万庄大街22号
邮政编码:100037
210mm×297mm?0.75印张·21千字2008年2月第1版第1次印刷
书号:15111:8673
网址:http://cmpbook.com(010)88379779
编辑部电话:
直销中心电话:(010)88379693封面无防伪标均为盗版
版权专有
侵权必究
200000
小提示:此标准内容仅展示完整标准里的部分截取内容,若需要完整标准请到上方自行免费下载完整标准文档。

标准图片预览:
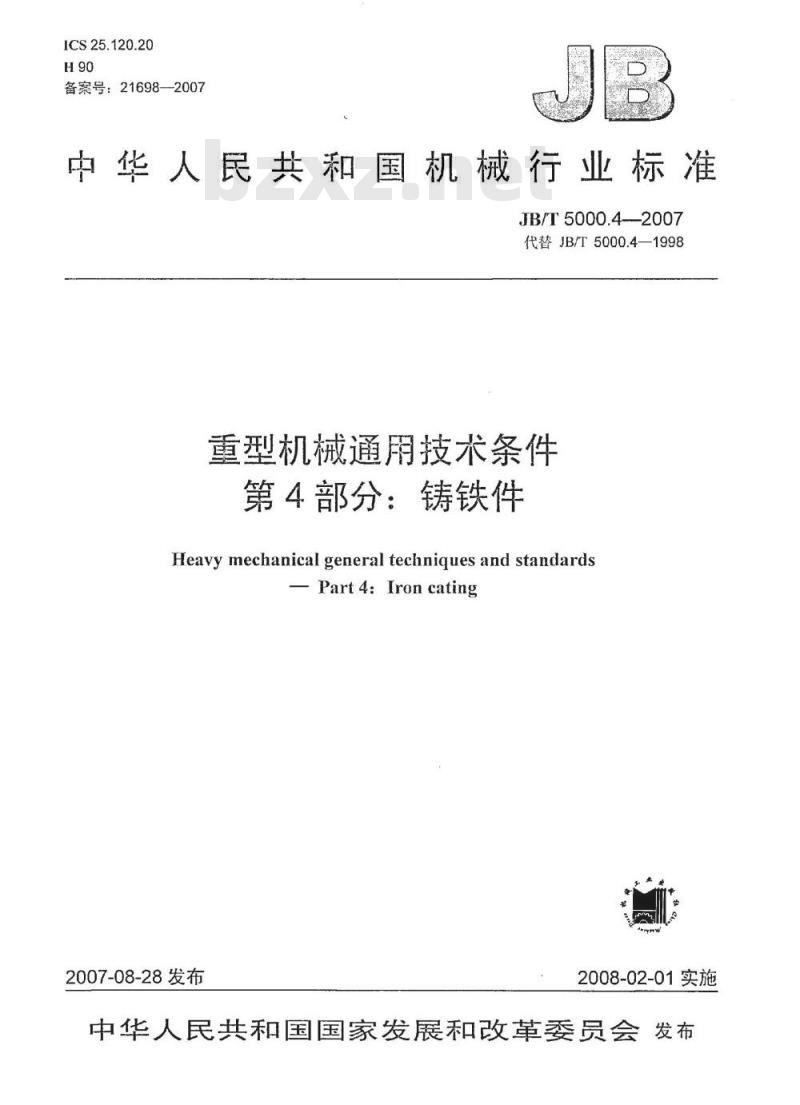
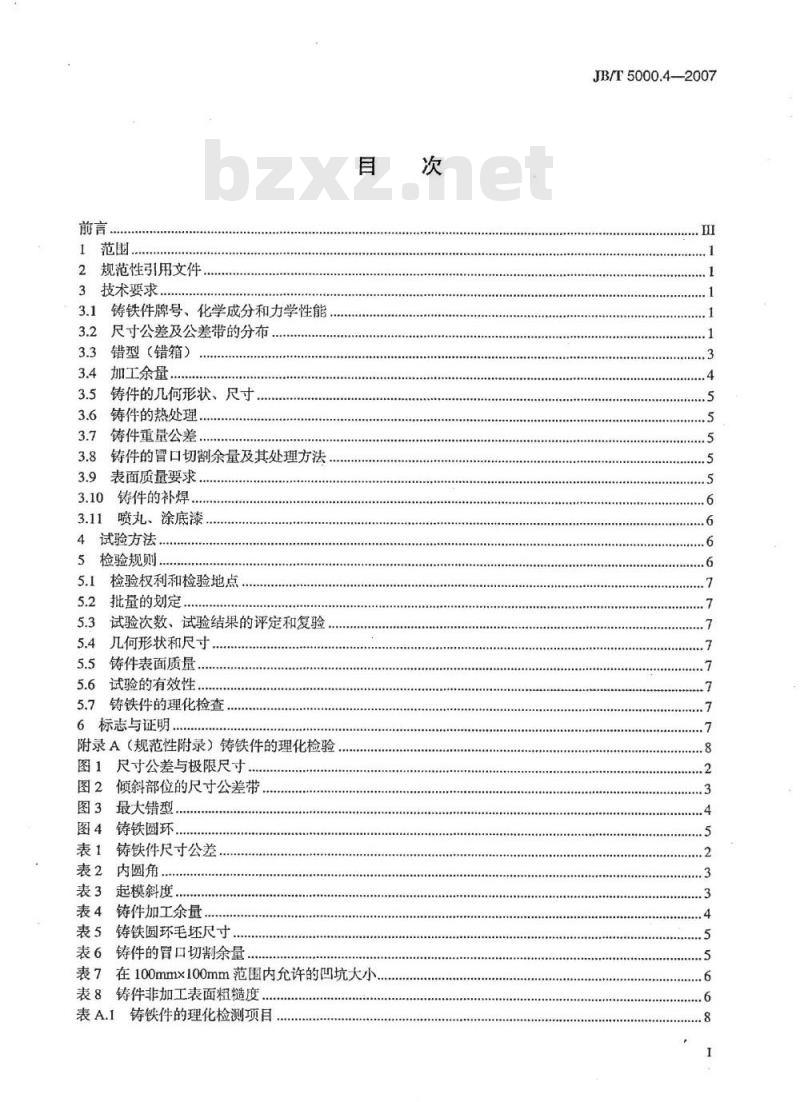
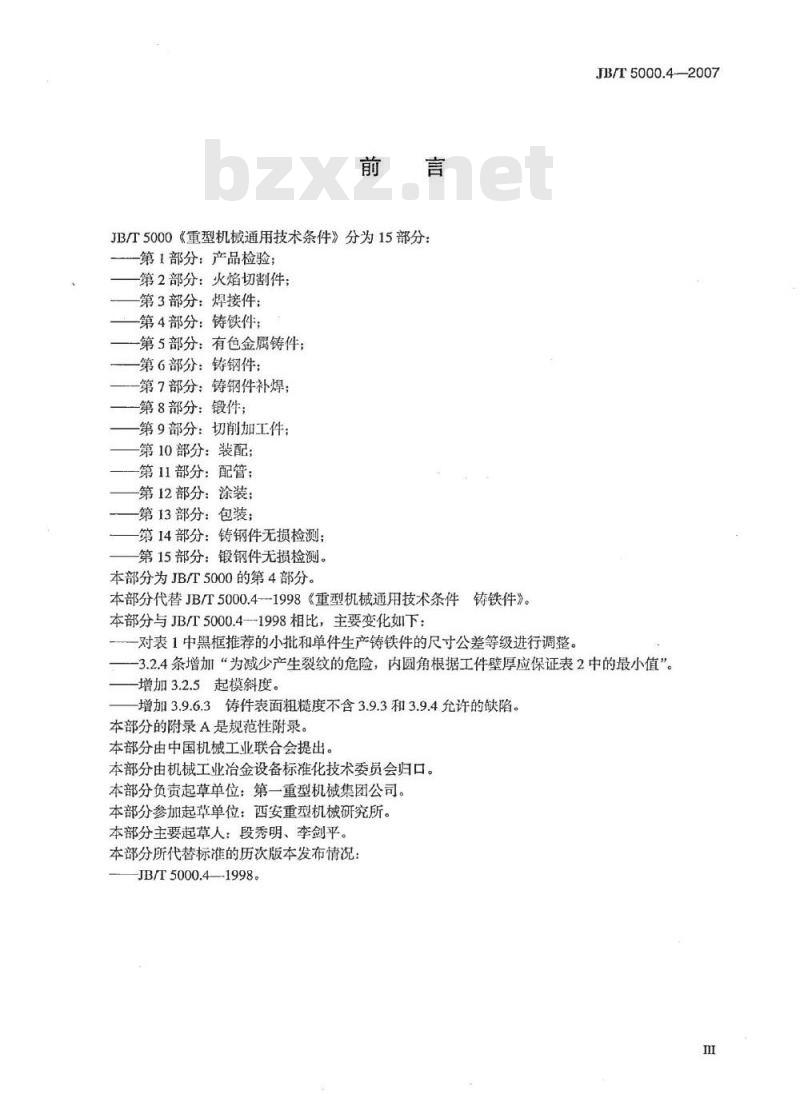
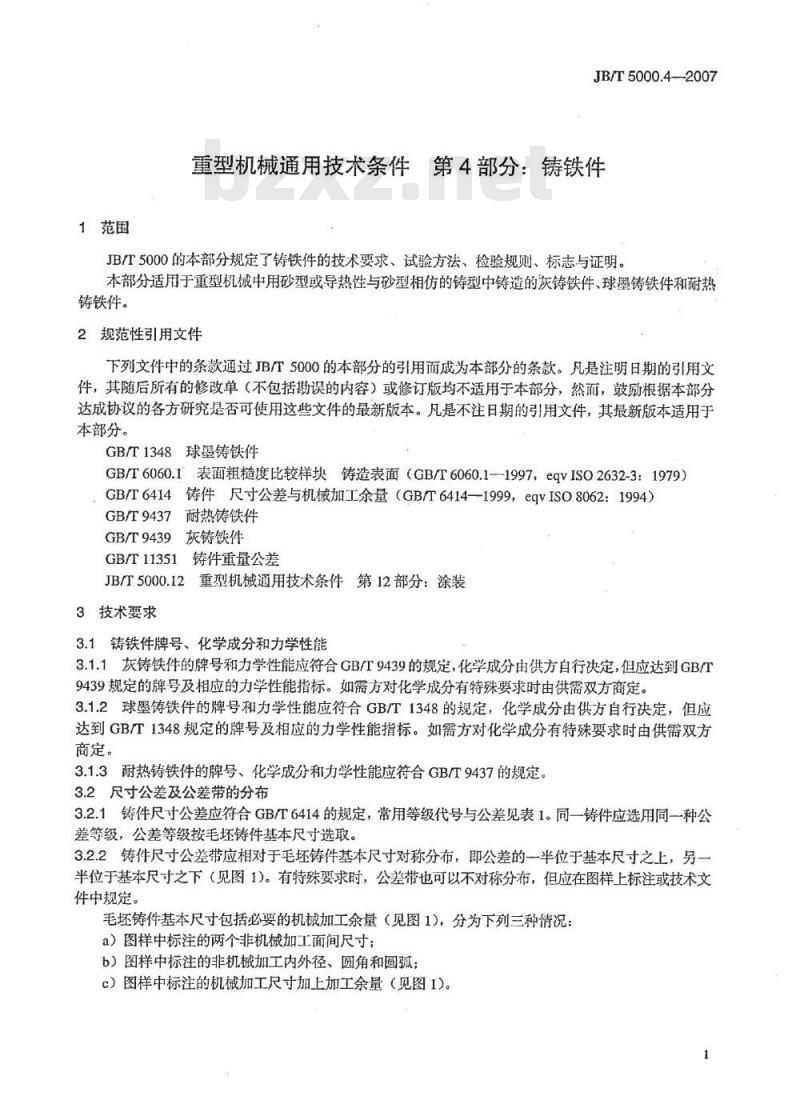
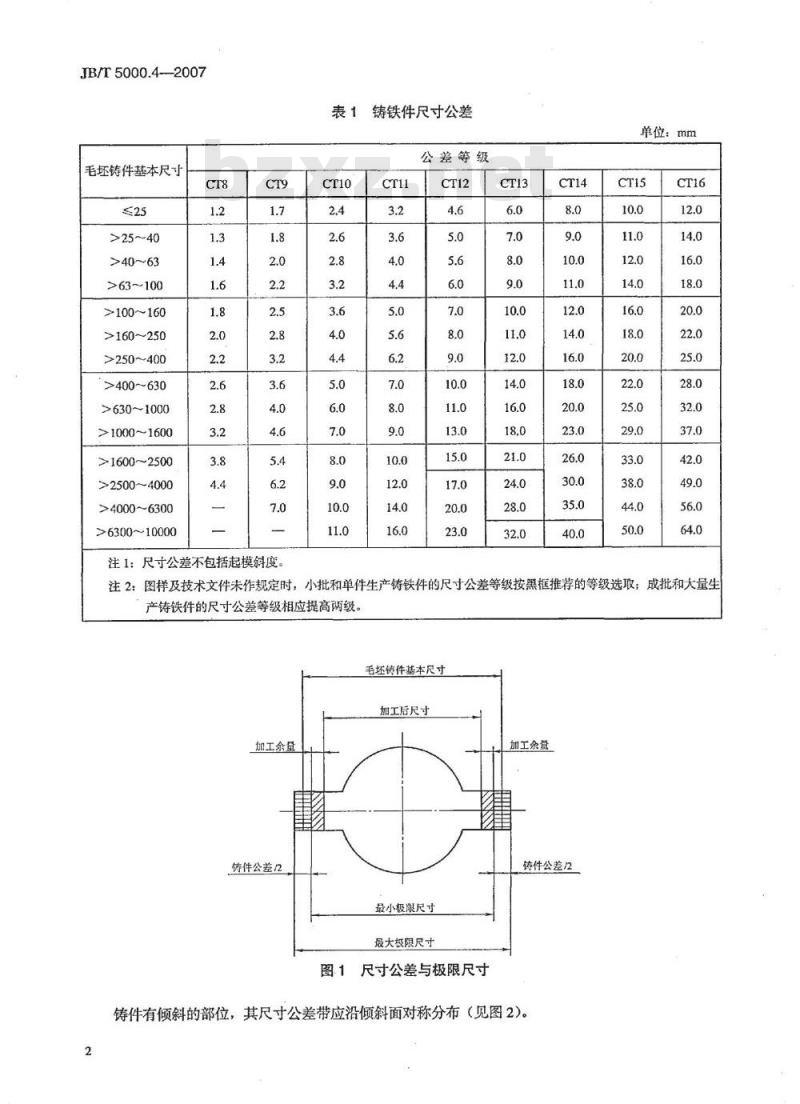
- 热门标准
- 机械行业标准(JB)
- JB/T8471-2010 袋式除尘器 安装技术要求与验收规范
- JB/T5946-1991 工程机械 涂装通用技术条件
- JB/T10767-2007 装载机铜基湿式粉末冶金摩擦片 技术条件
- JB3228-1983 闭式机械压力机 紧固模具用槽打(顶)杆孔的分布形式与尺寸
- JB/GQOE14-1988 熔模铸钢ZG310-570正大组织金相检验
- JB/T6237.8-2008 电触头材料用银粉化学分析方法 第8部分:银粉水溶液pH值测定
- JB/T8704-2012 蜂窝式电除焦油器
- JB/T11225-2011 烘烤机械 层式电烤炉
- JB/T10565-2006 工业过程测量和控制系统用动圈式指示仪性能评定方法
- JB/T7881.5-2010 剪羊毛机 第5部分:刀片
- JB/T9220.3-1999 铸造化铁炉酸性炉渣化学分析方法 重铬酸钾容量法测定氧化亚铁量
- JB/T2361-1992 恒压刷握
- JB/T10225-2013 表格印刷机
- JB/T5883.6-1991 电控设备图样及技术文件 技术文件的编写规定
- JB/T9014.1-1999 连续输送设备 散粒物料 性能术语及其分类
- 行业新闻
请牢记:“bzxz.net”即是“标准下载”四个汉字汉语拼音首字母与国际顶级域名“.net”的组合。 ©2009 标准下载网 www.bzxz.net 本站邮件:bzxznet@163.com
网站备案号:湘ICP备2023016450号-1
网站备案号:湘ICP备2023016450号-1