- 您的位置:
- 标准下载网 >>
- 标准分类 >>
- 铁路运输行业标准(TB) >>
- TB/T 2951-2009 铁道货车空气控制阀
标准号:
TB/T 2951-2009
标准名称:
铁道货车空气控制阀
标准类别:
铁路运输行业标准(TB)
标准状态:
现行-
发布日期:
2009-11-11 出版语种:
简体中文下载格式:
.rar .pdf下载大小:
5.54 MB
替代情况:
替代TB/T 2951-1999

部分标准内容:
ICS 45.060.20
中华人民共和国铁道行业标准
TB/T2951-2009
代替TB/T29511999
铁道货车空气控制阀
Air controlling valve of railway wagon2009-11-11发布
2010-05-01实施
中华人民共和国铁道部发 布
规范性引用文件
控制阀组成
性能要求
技术要求
检验规则
8标志、包装、贮存及运输
附录A(规范性附录)
附录B(规范性附录)
控制阀的试验台试验方法
专用试验台的机能检测方法
TB/T2951-2009
TB/T2951-2009
本标准代替TB/T2951--1999《铁路车辆用120型货车空气制动控制阀技术条件》。本标准与TB/T2951—1999相比主要变化如下:适用范围不同;
增加了性能要求;
一增加了控制阀中主阀、紧急阀在专用试验台上的试验方法及专用试验台机能检测方法;增加了控制阀的型式试验;
修改了材料的技术要求。
本标准的附录A,附录B为规范性附录。本标准由青岛四方车辆研究所有限公司提出并归口。本标准起草单位:中国铁道科学研究院机车车辆研究所。本标准主要起草人:陶强、吴培元、孙德环、姚小沛。本标准所代替标准的历次版本发布情况为:TB/T2951—1999。
1范围
铁道货车空气控制阀
TB/T 2951-2009
本标准规定了铁道货车空气控制阀(以下简称控制阀)的技术要求,试验,检验规则,标志、包装、贮存及运输等。
本标准适用于新造铁道货车二压力直接作用式120系列空气控制阀。2规范性引用文件
下列文件中的条款通过本标准的引用而成为本标准的条款。凡是注日期的引用文件,其随后所有的修改单(不包括勘误的内容)或修订版均不适用于本标准,然而,鼓励根据本标准达成协议的各方研究是否可使用这些文件的最新版本。凡是不注日期的引用文件,其最新版本适用于本标准。GB/T1173—1995铸造铝合金
GB/T 1176-1987
铸造铜合金技术条件(neqIS01338:1997)GB/T1184—1996
5形状和位置公差未注公差值(eqvIS02768—2:1989)GB/T1348—1988
球墨铸铁件
GB/T1804—2000
一般公差未注公差的线性和角度尺寸的公差(eqvIS02768—1:1989)GB/T4237-—2007
GB/T6414—1999
GB/T10125—1997
GB/T15114—1994
GB/T15115-1994
GB/T16947-1997
GB/T18684—-2002
TB/T 66—1995
不锈钢热轧钢板和钢带
铸件尺寸公差与机械加工余量(eqvIS08062:1994)人造气氛腐蚀试验盐雾试验(eqvIS09227:1990)铝合金压铸件
压铸铝合金
螺旋弹簧疲劳试验规范
锌铬涂层技术条件
机车车辆制动机弹簧技术条件
TB/T1492—2002
2铁道车辆制动机单车试验方法
TB/T2206—1991
3控制阀组成
车辆用103/104型空气分配阀橡胶件控制阀由主阀(包括半自动缓解阀)、紧急阀和中间体组成。4性能要求
4.1控制阀性能及作用应能与国内现有货车阀无条件混编运用。4.2控制阀在制动管定压为500kPa或600kPa时均应正常工作。4.3控制阀应能与JZ-7、26-L、DK-1、CCBⅡ等型机车制动机匹配,并既能适应机车制动机无压力保持操纵又能适应机车制动机有压力保持操纵的要求。4.4为适应货物列车运用要求,控制阀应具有充气、减速充气、缓解、加速缓解、常用制动、常用加速制动(120-1型货车空气控制阀),保压、紧急制动等作用。紧急制动时,制动缸压力应有二段上升,跃升压力应为110kPa~170kPa。
4.5控制阀可与直径为356mm、305mm、254mm及203mm的制动缸配套使用。1
TB/T2951--2009
4.6控制阀本身应具有半自动缓解功能。4.7控制阀在-50℃~70℃使用环境温度下应能正常工作;经110℃、3h解冻工况,恢复使用环境温度后控制阀的制动、保压、缓解等各项性能均应能符合单车试验要求。4.8控制阀的紧急制动波速应大于250m/s,常用制动波速不应小于180m/s,缓解波速不应小于150m/s。
5技术要求
5.1控制阀应符合本标准及经规定程序批准的设计图样和技术文件的规定。5.2机械加工零件未注尺寸公差的极限偏差按GB/T1804一m执行,未注形位公差按GB/T1184-K执行。
5.3球墨铸铁件应满足GB/T1348—1988的规定,其未注铸件尺寸公差的极限偏差按GB/T6414—CT10执行。铸件金相组织球化率为2级~4级。5.4铜件应满足GB/T1176—1987的规定,其未注铸件尺寸公差的极限偏差按GB/T6414-CT10执行。
5.5铝合金压铸件应满足GB/T15114—1994、GB/T1173—1995的规定,未注铸件尺寸公差的极限偏差按GB/T6414—CT6执行,化学成分及机械性能应符合CB/T15115--1994的规定。铸件加工后进行阳极氧化处理,镀层厚为0.008mm~0.025mm。5.6铸铁件应进行煮蜡处理,在温度为80℃~110℃的液体石蜡中浸泡15min以上,取出后应立即用不低于500kPa的压缩空气吹净多余石蜡。5.7阀内各不锈钢套应满足GB/T42372007的规定。5.8弹簧应符合TB/T66—1995的要求。弹簧表面处理应符合GB/T18684—2002的规定,镀层厚为0.004mm~0.01mm。弹簧抗腐蚀性能应符合CB/T10125一1997的规定,出现红锈的时间不应低于240h。弹簧疲劳寿命试验应符合GB/T16947—1997的规定,疲劳试验循环1×10°次,弹簧的可靠性评定应达到合格。
5.9压装阀套、阀座时应先将零件吹洗干净,在零部件待结合面均匀涂以适量的白铅油。5.10主阀组装时,在节制阀、滑阀,滑阀套之研磨面上涂以适量的改性甲基硅油,在各活动0形密封圈处涂以适量GP-9或7057硅脂。主活塞、滑阀、节止阀装人阀体内拉动时,动作应灵活,阻力应适宜,膜板边缘应完全入膜板槽内。5.11橡胶件应满足图样及TB/T2206-—1991和有关合成橡胶的技术要求,各橡胶件不应接触煤油、汽油、机油及酸碱等腐蚀性物质。5.12主阀体组成、缓解阀体组成、紧急阀体组成、中间体及铝合金铸件应进行不低于700kPa压力下的密封试验,保压时间不应低于30s,各气路间不应串风或漏泄。铸件、压铸件加工后应进行不低于700kPa风压试验,保压时间不应低于30s,各气路不应串风和漏泄。5.13控制阀组装后,在非安装面涂以底漆和面漆,干膜厚度应分别不小于0.03mm。6试验
6.1试验项目
6.1.1控制阀中主阀、紧急阀的性能试验。6.1.2包括常温、低温和高温三种工况的环境试验,其温度及保温时间如下:——常温试验试验温度为-10℃~30℃,保温12h。低温试验试验温度为-50℃~-48℃,保温48h。高温试验试验温度为65℃~70℃,保温12h。6.2性能试验
TB/T2951-2009
主阀(包括半自动缓解阀)、紧急阀组装后在控制阀专用试验台上进行试验,试验方法及要求见附录A。专用试验台机能检测方法见附录B。6.3环境试验
6.3.1试验设备及试件
6.3.1.1试验设备包括一个标准的货车单车试验器(以下简称单车试验器)、全套单车试验装置和环境试验室。试验装置在环境试验室的布局如图1所示。风源
无燥器
(选用)
试验器
环境试验室
储风征
试验紧急阀
试验主阀
制动管容录风缸
副风缸
图1试验装置示意图
6.3.1.2单车试验器应符合TB/T1492-2002的规定。制动缸容量风缸
加速缓解风缸
6.3.1.3环境试验室的面积应足以容纳全套单车试验装置(推荐面积为4.5m2以上)。试验室应能在-50℃~70℃温度范围内连续工作。6.3.1.4用以测定温度用的温度计的精度应在±1℃以内,试验期间应有连续的温度记录。6.3.1.5制动管容量风缸容积应为(15.5±0.15)L。6.3.1.6
管路的各连接处在各试验温度下不应漏泄。允许使用柔性软管。6.3.1.7
环境试验室外部的管路应用隔热材料保护。来自储风缸的管路公称内径为15mm~25mm。9储风缸容积应大于450L。
6.3.1.10在进行各种预定温度下的试验时,应使用同套试件。6.3.2试验步骤
6.3.2.1在各工况试验前,控制阀和储风缸压力空气应在相应温度下保持6.1.2要求的时间。单车试验器操纵阀手把(以下简称手把)置充气位,在保温期间及进行试验前不应使控制阀反复动作。6.3.2.2控制阀按TB/T1492—2002中装120型或120-1型制动机有关项目进行,其缓解感度试验参照车辆制动管公称内径为32mm、长度16m以下的规定。低温试验与TB/T1492-—2002要求不同点如下:“全车漏泄试验”要求制动管压力在1min内下降不应超过20kPa。“制动感度试验”要求减压50kPa前,应发生制动作用。制动管的压力继续减压不应超过50kPa。
TB/T2951--2009
一“缓解感度试验”要求制动缸压力应在30s内开始缓解。-“加速缓解试验”手把移至3位,5s后,手把置2位。其他相同。“紧急制动试验”要求制动管减压150kPa前应能产生紧急放风作用。7检验规则
7.1出厂检验
7.1.1出厂检验按5.1.6.2内容逐件检验。7.1.2检验合格的产品应有合格证,合格证的内容包括:a)产品名称、型号;
b)制造单位;
生产日期;
检查人员姓名或代号;
e)产品编号;
f)合格印章。
7.2型式检验
7.2.1型式检验的项目包括6.2、6.3的内容。7.2.2在下列情况下应进行型式检验:a)新产品鉴定试验时;
累计生产数量每达到2×10*套或连续生产一年时;b)
结构、生产工艺或材料有重大改变时;c
d)产品停产一年后,恢复生产时;e)定型产品转厂生产时。
8标志、包装、贮存及运输
8.1主阀体、缓解阀体、中间体、紧急阀体及各压铸件上应按图样技术要求铸有制造厂名称或代号。主阀体、主阀上盖应按图样技术要求铸有控制阀型号。主阀体、中间体应按图样技术要求铸有铸造日期(年、月)。
8.2中间体组成包装:所有管口应采用相应的尼龙塞堵堵好,不应松动,主阀、紧急阀两安装法兰面分别用尼龙压板盖好,用螺母拧紧,螺栓丝扣处应涂有适量的油脂。8.3主阀组成包装:法兰面用尼龙压板盖好,用尼龙丝堵塞紧,局减阀盖和缓解阀上盖的通气孔用尼龙丝堵塞紧,主阀排气口用尼龙丝堵塞紧,缓解阀手柄座用手柄防护罩加以保护,缓解阀手柄用袋装好,一并放人塑料袋后,封好袋口。8.4紧急阀组成包装:法兰面用尼龙压板盖好,用尼龙丝堵塞紧,再装人塑料袋内,封好袋口。8.5中间体、主阀组成、紧急阀组成可根据运输要求分箱(或筐)装运,所用包装箱(或筐)规格和质量应符合铁路运输搬运和堆放的要求。8.6控制阀应存放于干燥、洁净场所。当存放期超过6个月时,应重新清洗换油,存放期超过1年应分解,橡胶件更换新品,并应在控制阀专用试验台上试验,合格后方准使用。8.7每套控制阀应附有合格证。
8.8控制阀运输中应避免接触油类和有机溶剂等,避免碰撞和阳光暴晒。4
A.1试验台要求
附录A
(规范性附录)
控制阀的试验台试验方法
A.1.1试验台的结构如图A.1所示。试验台用压力表量程和精度应满足表A.1要求。A. 1. 2
测量范围
0~1000
0~1000
精度等级
1.6及以上
使用部位
储风缸
TB/T2951-—2009
制动管容景风缸、副风缸、制动缸、加速缓解风缸、紧急室、制动管管路、副风缸管路、加速缓解风缸管路、制动缸管路局减室
风缸、风缸与管路总容积误差应在1%之内,其容积及管路内径的要求如下:储风缸容积为82L,储风缸与管路总容积为82.4L,管路内径为Φ17mm;-副风缸容积为40L,副风缸与管路总容积为40.4L,管路内径为Φ17mm;制动缸容量风缸容积为11.6L,制动缸容量风缸与管路总容积为12L,管路内径为Φ17mm;-加速缓解风缸容积为11L,加速缓解风缸与管路总容积为11.4L,管路内径为Φ17mm;制动管容量风缸容积为15L,制动管容量风缸与管路总容积为15.7L,管路内径为Φ17mm;紧急室容积为1.5L,紧急室与管路总容积为1.51L,管路内径为Φ4mm;局减室容积为0.6L,局减室与管路总容积为0.61L,管路内径为Φ4mm。A.1.4试验台用压差显示器和与其配套的压差变送器、流量显示器、流量控制器和压力传感器应满足表A.2要求。
压差显示器和配套的
压差变送器
流盘显示器和配套的
流量控制器
压力传感器
测量范围
流量范围(量程)
测量范围
- 100 kPa ~ +100 kPa
±0.5% F.S
0mL/min~500ml/min
0 kPa~1000kPa
±0.2%F.S
试验台应能够满足对风缸及管路进行充气和排气的要求,电磁阀应满足表A.3的要求。表A.3
换向时间
2位2通
2位3通电磁阀
2位5通电磁阀此内容来自标准下载网
工作压力
换向时间
工作压力
TB/T2951—2009
直通电磁阀
储缸(校)
客二号
制动缸
制动管容量风缸与制动管间的开关;2-
副风缸与副风缸管路间的开关;3—制动缸与制动缸管路间的开关;制动缸管路排风开关;
5加速缓解风缸与加速缓解风缸管路间开关;6
加速缓解风缸管路排气口与流量计间开关:一制动管容量风缸排风开关;
7a——制动管管路排风开关;
主阀排气口与流量计间开关;
一加速缓解风缸快充风开关;
10—储风缸截断开关;
一副风缸管路与流量计间开关;11
一制动管容量风缸与加速缓解风缸间开关;-制动缸快充风开关;
-制动管、副风缸管路与压差计间开关:副风缸快充风开关;
紧急室快充风开关;
副风缸管路排风开关;
表A.3(续)
工作压力
压差计15
副风缸
列车管缸
局减口
缓解阀手柄
排气口
60流盘计
速线解风缸
加速缓解风缸管路排风开关;
局减排气口与流量计间开关;
控制局减排气口和加速缓解风缸管路排气口的测漏气缸动作开关;
控制主阀排气口的测漏气缸动作开关;-推动缓解阀手柄动作及自动复位开关;一制动管容量风缸快充开关;
制动管容量风缸慢充开关;
一制动管容量风缸排风开关;
D—--制动管容量风缸排风开关;E
一制动管容量风缸排风开关;
F——制动管容量风缸排风开关;G——制动管容量风缸排开关风;K1、K2——夹紧开关;
一号—
二号—
三号一
一总风源截断塞门;
储风缸截断塞门;
储风缸压力表截断塞门。
图A.1控制阀试验台结构示意图
A.2试验准备
TB/T2951—2009
开启一、二、三号塞门:确认总风源压力不低于650kPa:打开试验台所有电源开关,预热15min:调整调压阀,使储风缸压力为590kPa~610kPa(试验台定压);每天应进行试验台机能检测,机能检测合格后方可进行控制阀性能试验;由微机控制进行自动试验(试验台置于自动位)时,各开关均由微机控制自动开闭。手动试验(试验台置于手动位)时,人工开闭各开关。A.3试验步骤
A.3.1主阀试验
A.3.1.1主阀安装
开通夹紧开关K1,将主阀卡紧在主阀安装座上。开通夹紧开关K2,将紧急阀座首板卡紧在紧急阀安装座上。
A.3.1.2漏泄试验
A.3.1.2.1漏泄试验准备
依次开通10、1、2、3.5、9、A、16,待副风缸和加速缓解风缸压力均充至定压后,关断9、16;关断1,开通7a,使主阀动作,待制动管管路压力空气排至零后,关断7a:开通1、9、16,副风缸和加速缓解风缸压力充至定压。关断A、9、5,开通D,制动管压力降至550kPa时,关断D。待制动管压力稳定在550kPa后,关断16、1。开通7a,制动管管路压力空气排至零后关断7a,开通5。A.3.1.2.2制动位漏泄试验
A.3.1.2.2.1各结合面
在各结合面处及缓解阀排气口、缓解阀手柄处涂刷防锈检漏剂(以下简称为检漏剂)进行检查,不应产生漏泄。
A3.1.2.2.2局减阀膜板
在局减阀呼吸孔涂刷检漏剂进行检查,不应产生漏泄。A3.1.2.2.3滑阀
开通8、23,检查主阀排气口漏泄量,流量计显示值不应大于80mL/min,关断8、23。开通21、22,检查局减排气口的漏泄量,流量计显示值不应大于80mL/min,关断21、22。A.3.1.2.2.4主活塞膜板及0形密封圈,加速缓解夹心阀及0形密封圈,局减阀杆、紧急二段阀杆、缓解活塞杆O形密封圈及排风阀。关断2、3、5,检查副风缸管路和加速缓解风缸管路压力,在10s内压力下降不应超过5kPa。开通2、3、5。
A.3.1.2.2.5缓解阀膜板及0形密封圈开通24,将缓解阀手柄推至制动缸压力开始下降时,立即关断24,制动缸压力空气排零。在缓解阀上呼吸孔涂刷检漏剂进行检查,不应产生漏泄。A.3.1.2.2.6缓解阀内副风缸及加速缓解风缸气路、小止回阀、排风阀开通24,将缓解阀手柄推至全开位,使副风缸压力降至100kPa后关断24。在缓解阀手柄处涂刷检漏剂进行检查,不应产生漏泄;在缓解阀排气口涂刷检漏剂进行检查,在10s内产生的气泡高度不应大于12mm。
关断3,开通A、1、9后,再开通16,待副风缸和加速缓解风缸压力均充至定压后,关断9、16。A.3.1.2.3缓解位漏泄试验
A.3.1.2.3.1缓解位漏泄试验准备确认10、1、2、5、A已开通,制动管、副风缸和加速缓解风缸压力均充至定压。A3.1.2.3.2结合面
除主阀前盖及缓解阀下盖外,在各结合面周围涂检漏剂进行检查,不应漏泄。7
小提示:此标准内容仅展示完整标准里的部分截取内容,若需要完整标准请到上方自行免费下载完整标准文档。
中华人民共和国铁道行业标准
TB/T2951-2009
代替TB/T29511999
铁道货车空气控制阀
Air controlling valve of railway wagon2009-11-11发布
2010-05-01实施
中华人民共和国铁道部发 布
规范性引用文件
控制阀组成
性能要求
技术要求
检验规则
8标志、包装、贮存及运输
附录A(规范性附录)
附录B(规范性附录)
控制阀的试验台试验方法
专用试验台的机能检测方法
TB/T2951-2009
TB/T2951-2009
本标准代替TB/T2951--1999《铁路车辆用120型货车空气制动控制阀技术条件》。本标准与TB/T2951—1999相比主要变化如下:适用范围不同;
增加了性能要求;
一增加了控制阀中主阀、紧急阀在专用试验台上的试验方法及专用试验台机能检测方法;增加了控制阀的型式试验;
修改了材料的技术要求。
本标准的附录A,附录B为规范性附录。本标准由青岛四方车辆研究所有限公司提出并归口。本标准起草单位:中国铁道科学研究院机车车辆研究所。本标准主要起草人:陶强、吴培元、孙德环、姚小沛。本标准所代替标准的历次版本发布情况为:TB/T2951—1999。
1范围
铁道货车空气控制阀
TB/T 2951-2009
本标准规定了铁道货车空气控制阀(以下简称控制阀)的技术要求,试验,检验规则,标志、包装、贮存及运输等。
本标准适用于新造铁道货车二压力直接作用式120系列空气控制阀。2规范性引用文件
下列文件中的条款通过本标准的引用而成为本标准的条款。凡是注日期的引用文件,其随后所有的修改单(不包括勘误的内容)或修订版均不适用于本标准,然而,鼓励根据本标准达成协议的各方研究是否可使用这些文件的最新版本。凡是不注日期的引用文件,其最新版本适用于本标准。GB/T1173—1995铸造铝合金
GB/T 1176-1987
铸造铜合金技术条件(neqIS01338:1997)GB/T1184—1996
5形状和位置公差未注公差值(eqvIS02768—2:1989)GB/T1348—1988
球墨铸铁件
GB/T1804—2000
一般公差未注公差的线性和角度尺寸的公差(eqvIS02768—1:1989)GB/T4237-—2007
GB/T6414—1999
GB/T10125—1997
GB/T15114—1994
GB/T15115-1994
GB/T16947-1997
GB/T18684—-2002
TB/T 66—1995
不锈钢热轧钢板和钢带
铸件尺寸公差与机械加工余量(eqvIS08062:1994)人造气氛腐蚀试验盐雾试验(eqvIS09227:1990)铝合金压铸件
压铸铝合金
螺旋弹簧疲劳试验规范
锌铬涂层技术条件
机车车辆制动机弹簧技术条件
TB/T1492—2002
2铁道车辆制动机单车试验方法
TB/T2206—1991
3控制阀组成
车辆用103/104型空气分配阀橡胶件控制阀由主阀(包括半自动缓解阀)、紧急阀和中间体组成。4性能要求
4.1控制阀性能及作用应能与国内现有货车阀无条件混编运用。4.2控制阀在制动管定压为500kPa或600kPa时均应正常工作。4.3控制阀应能与JZ-7、26-L、DK-1、CCBⅡ等型机车制动机匹配,并既能适应机车制动机无压力保持操纵又能适应机车制动机有压力保持操纵的要求。4.4为适应货物列车运用要求,控制阀应具有充气、减速充气、缓解、加速缓解、常用制动、常用加速制动(120-1型货车空气控制阀),保压、紧急制动等作用。紧急制动时,制动缸压力应有二段上升,跃升压力应为110kPa~170kPa。
4.5控制阀可与直径为356mm、305mm、254mm及203mm的制动缸配套使用。1
TB/T2951--2009
4.6控制阀本身应具有半自动缓解功能。4.7控制阀在-50℃~70℃使用环境温度下应能正常工作;经110℃、3h解冻工况,恢复使用环境温度后控制阀的制动、保压、缓解等各项性能均应能符合单车试验要求。4.8控制阀的紧急制动波速应大于250m/s,常用制动波速不应小于180m/s,缓解波速不应小于150m/s。
5技术要求
5.1控制阀应符合本标准及经规定程序批准的设计图样和技术文件的规定。5.2机械加工零件未注尺寸公差的极限偏差按GB/T1804一m执行,未注形位公差按GB/T1184-K执行。
5.3球墨铸铁件应满足GB/T1348—1988的规定,其未注铸件尺寸公差的极限偏差按GB/T6414—CT10执行。铸件金相组织球化率为2级~4级。5.4铜件应满足GB/T1176—1987的规定,其未注铸件尺寸公差的极限偏差按GB/T6414-CT10执行。
5.5铝合金压铸件应满足GB/T15114—1994、GB/T1173—1995的规定,未注铸件尺寸公差的极限偏差按GB/T6414—CT6执行,化学成分及机械性能应符合CB/T15115--1994的规定。铸件加工后进行阳极氧化处理,镀层厚为0.008mm~0.025mm。5.6铸铁件应进行煮蜡处理,在温度为80℃~110℃的液体石蜡中浸泡15min以上,取出后应立即用不低于500kPa的压缩空气吹净多余石蜡。5.7阀内各不锈钢套应满足GB/T42372007的规定。5.8弹簧应符合TB/T66—1995的要求。弹簧表面处理应符合GB/T18684—2002的规定,镀层厚为0.004mm~0.01mm。弹簧抗腐蚀性能应符合CB/T10125一1997的规定,出现红锈的时间不应低于240h。弹簧疲劳寿命试验应符合GB/T16947—1997的规定,疲劳试验循环1×10°次,弹簧的可靠性评定应达到合格。
5.9压装阀套、阀座时应先将零件吹洗干净,在零部件待结合面均匀涂以适量的白铅油。5.10主阀组装时,在节制阀、滑阀,滑阀套之研磨面上涂以适量的改性甲基硅油,在各活动0形密封圈处涂以适量GP-9或7057硅脂。主活塞、滑阀、节止阀装人阀体内拉动时,动作应灵活,阻力应适宜,膜板边缘应完全入膜板槽内。5.11橡胶件应满足图样及TB/T2206-—1991和有关合成橡胶的技术要求,各橡胶件不应接触煤油、汽油、机油及酸碱等腐蚀性物质。5.12主阀体组成、缓解阀体组成、紧急阀体组成、中间体及铝合金铸件应进行不低于700kPa压力下的密封试验,保压时间不应低于30s,各气路间不应串风或漏泄。铸件、压铸件加工后应进行不低于700kPa风压试验,保压时间不应低于30s,各气路不应串风和漏泄。5.13控制阀组装后,在非安装面涂以底漆和面漆,干膜厚度应分别不小于0.03mm。6试验
6.1试验项目
6.1.1控制阀中主阀、紧急阀的性能试验。6.1.2包括常温、低温和高温三种工况的环境试验,其温度及保温时间如下:——常温试验试验温度为-10℃~30℃,保温12h。低温试验试验温度为-50℃~-48℃,保温48h。高温试验试验温度为65℃~70℃,保温12h。6.2性能试验
TB/T2951-2009
主阀(包括半自动缓解阀)、紧急阀组装后在控制阀专用试验台上进行试验,试验方法及要求见附录A。专用试验台机能检测方法见附录B。6.3环境试验
6.3.1试验设备及试件
6.3.1.1试验设备包括一个标准的货车单车试验器(以下简称单车试验器)、全套单车试验装置和环境试验室。试验装置在环境试验室的布局如图1所示。风源
无燥器
(选用)
试验器
环境试验室
储风征
试验紧急阀
试验主阀
制动管容录风缸
副风缸
图1试验装置示意图
6.3.1.2单车试验器应符合TB/T1492-2002的规定。制动缸容量风缸
加速缓解风缸
6.3.1.3环境试验室的面积应足以容纳全套单车试验装置(推荐面积为4.5m2以上)。试验室应能在-50℃~70℃温度范围内连续工作。6.3.1.4用以测定温度用的温度计的精度应在±1℃以内,试验期间应有连续的温度记录。6.3.1.5制动管容量风缸容积应为(15.5±0.15)L。6.3.1.6
管路的各连接处在各试验温度下不应漏泄。允许使用柔性软管。6.3.1.7
环境试验室外部的管路应用隔热材料保护。来自储风缸的管路公称内径为15mm~25mm。9储风缸容积应大于450L。
6.3.1.10在进行各种预定温度下的试验时,应使用同套试件。6.3.2试验步骤
6.3.2.1在各工况试验前,控制阀和储风缸压力空气应在相应温度下保持6.1.2要求的时间。单车试验器操纵阀手把(以下简称手把)置充气位,在保温期间及进行试验前不应使控制阀反复动作。6.3.2.2控制阀按TB/T1492—2002中装120型或120-1型制动机有关项目进行,其缓解感度试验参照车辆制动管公称内径为32mm、长度16m以下的规定。低温试验与TB/T1492-—2002要求不同点如下:“全车漏泄试验”要求制动管压力在1min内下降不应超过20kPa。“制动感度试验”要求减压50kPa前,应发生制动作用。制动管的压力继续减压不应超过50kPa。
TB/T2951--2009
一“缓解感度试验”要求制动缸压力应在30s内开始缓解。-“加速缓解试验”手把移至3位,5s后,手把置2位。其他相同。“紧急制动试验”要求制动管减压150kPa前应能产生紧急放风作用。7检验规则
7.1出厂检验
7.1.1出厂检验按5.1.6.2内容逐件检验。7.1.2检验合格的产品应有合格证,合格证的内容包括:a)产品名称、型号;
b)制造单位;
生产日期;
检查人员姓名或代号;
e)产品编号;
f)合格印章。
7.2型式检验
7.2.1型式检验的项目包括6.2、6.3的内容。7.2.2在下列情况下应进行型式检验:a)新产品鉴定试验时;
累计生产数量每达到2×10*套或连续生产一年时;b)
结构、生产工艺或材料有重大改变时;c
d)产品停产一年后,恢复生产时;e)定型产品转厂生产时。
8标志、包装、贮存及运输
8.1主阀体、缓解阀体、中间体、紧急阀体及各压铸件上应按图样技术要求铸有制造厂名称或代号。主阀体、主阀上盖应按图样技术要求铸有控制阀型号。主阀体、中间体应按图样技术要求铸有铸造日期(年、月)。
8.2中间体组成包装:所有管口应采用相应的尼龙塞堵堵好,不应松动,主阀、紧急阀两安装法兰面分别用尼龙压板盖好,用螺母拧紧,螺栓丝扣处应涂有适量的油脂。8.3主阀组成包装:法兰面用尼龙压板盖好,用尼龙丝堵塞紧,局减阀盖和缓解阀上盖的通气孔用尼龙丝堵塞紧,主阀排气口用尼龙丝堵塞紧,缓解阀手柄座用手柄防护罩加以保护,缓解阀手柄用袋装好,一并放人塑料袋后,封好袋口。8.4紧急阀组成包装:法兰面用尼龙压板盖好,用尼龙丝堵塞紧,再装人塑料袋内,封好袋口。8.5中间体、主阀组成、紧急阀组成可根据运输要求分箱(或筐)装运,所用包装箱(或筐)规格和质量应符合铁路运输搬运和堆放的要求。8.6控制阀应存放于干燥、洁净场所。当存放期超过6个月时,应重新清洗换油,存放期超过1年应分解,橡胶件更换新品,并应在控制阀专用试验台上试验,合格后方准使用。8.7每套控制阀应附有合格证。
8.8控制阀运输中应避免接触油类和有机溶剂等,避免碰撞和阳光暴晒。4
A.1试验台要求
附录A
(规范性附录)
控制阀的试验台试验方法
A.1.1试验台的结构如图A.1所示。试验台用压力表量程和精度应满足表A.1要求。A. 1. 2
测量范围
0~1000
0~1000
精度等级
1.6及以上
使用部位
储风缸
TB/T2951-—2009
制动管容景风缸、副风缸、制动缸、加速缓解风缸、紧急室、制动管管路、副风缸管路、加速缓解风缸管路、制动缸管路局减室
风缸、风缸与管路总容积误差应在1%之内,其容积及管路内径的要求如下:储风缸容积为82L,储风缸与管路总容积为82.4L,管路内径为Φ17mm;-副风缸容积为40L,副风缸与管路总容积为40.4L,管路内径为Φ17mm;制动缸容量风缸容积为11.6L,制动缸容量风缸与管路总容积为12L,管路内径为Φ17mm;-加速缓解风缸容积为11L,加速缓解风缸与管路总容积为11.4L,管路内径为Φ17mm;制动管容量风缸容积为15L,制动管容量风缸与管路总容积为15.7L,管路内径为Φ17mm;紧急室容积为1.5L,紧急室与管路总容积为1.51L,管路内径为Φ4mm;局减室容积为0.6L,局减室与管路总容积为0.61L,管路内径为Φ4mm。A.1.4试验台用压差显示器和与其配套的压差变送器、流量显示器、流量控制器和压力传感器应满足表A.2要求。
压差显示器和配套的
压差变送器
流盘显示器和配套的
流量控制器
压力传感器
测量范围
流量范围(量程)
测量范围
- 100 kPa ~ +100 kPa
±0.5% F.S
0mL/min~500ml/min
0 kPa~1000kPa
±0.2%F.S
试验台应能够满足对风缸及管路进行充气和排气的要求,电磁阀应满足表A.3的要求。表A.3
换向时间
2位2通
2位3通电磁阀
2位5通电磁阀此内容来自标准下载网
工作压力
换向时间
工作压力
TB/T2951—2009
直通电磁阀
储缸(校)
客二号
制动缸
制动管容量风缸与制动管间的开关;2-
副风缸与副风缸管路间的开关;3—制动缸与制动缸管路间的开关;制动缸管路排风开关;
5加速缓解风缸与加速缓解风缸管路间开关;6
加速缓解风缸管路排气口与流量计间开关:一制动管容量风缸排风开关;
7a——制动管管路排风开关;
主阀排气口与流量计间开关;
一加速缓解风缸快充风开关;
10—储风缸截断开关;
一副风缸管路与流量计间开关;11
一制动管容量风缸与加速缓解风缸间开关;-制动缸快充风开关;
-制动管、副风缸管路与压差计间开关:副风缸快充风开关;
紧急室快充风开关;
副风缸管路排风开关;
表A.3(续)
工作压力
压差计15
副风缸
列车管缸
局减口
缓解阀手柄
排气口
60流盘计
速线解风缸
加速缓解风缸管路排风开关;
局减排气口与流量计间开关;
控制局减排气口和加速缓解风缸管路排气口的测漏气缸动作开关;
控制主阀排气口的测漏气缸动作开关;-推动缓解阀手柄动作及自动复位开关;一制动管容量风缸快充开关;
制动管容量风缸慢充开关;
一制动管容量风缸排风开关;
D—--制动管容量风缸排风开关;E
一制动管容量风缸排风开关;
F——制动管容量风缸排风开关;G——制动管容量风缸排开关风;K1、K2——夹紧开关;
一号—
二号—
三号一
一总风源截断塞门;
储风缸截断塞门;
储风缸压力表截断塞门。
图A.1控制阀试验台结构示意图
A.2试验准备
TB/T2951—2009
开启一、二、三号塞门:确认总风源压力不低于650kPa:打开试验台所有电源开关,预热15min:调整调压阀,使储风缸压力为590kPa~610kPa(试验台定压);每天应进行试验台机能检测,机能检测合格后方可进行控制阀性能试验;由微机控制进行自动试验(试验台置于自动位)时,各开关均由微机控制自动开闭。手动试验(试验台置于手动位)时,人工开闭各开关。A.3试验步骤
A.3.1主阀试验
A.3.1.1主阀安装
开通夹紧开关K1,将主阀卡紧在主阀安装座上。开通夹紧开关K2,将紧急阀座首板卡紧在紧急阀安装座上。
A.3.1.2漏泄试验
A.3.1.2.1漏泄试验准备
依次开通10、1、2、3.5、9、A、16,待副风缸和加速缓解风缸压力均充至定压后,关断9、16;关断1,开通7a,使主阀动作,待制动管管路压力空气排至零后,关断7a:开通1、9、16,副风缸和加速缓解风缸压力充至定压。关断A、9、5,开通D,制动管压力降至550kPa时,关断D。待制动管压力稳定在550kPa后,关断16、1。开通7a,制动管管路压力空气排至零后关断7a,开通5。A.3.1.2.2制动位漏泄试验
A.3.1.2.2.1各结合面
在各结合面处及缓解阀排气口、缓解阀手柄处涂刷防锈检漏剂(以下简称为检漏剂)进行检查,不应产生漏泄。
A3.1.2.2.2局减阀膜板
在局减阀呼吸孔涂刷检漏剂进行检查,不应产生漏泄。A3.1.2.2.3滑阀
开通8、23,检查主阀排气口漏泄量,流量计显示值不应大于80mL/min,关断8、23。开通21、22,检查局减排气口的漏泄量,流量计显示值不应大于80mL/min,关断21、22。A.3.1.2.2.4主活塞膜板及0形密封圈,加速缓解夹心阀及0形密封圈,局减阀杆、紧急二段阀杆、缓解活塞杆O形密封圈及排风阀。关断2、3、5,检查副风缸管路和加速缓解风缸管路压力,在10s内压力下降不应超过5kPa。开通2、3、5。
A.3.1.2.2.5缓解阀膜板及0形密封圈开通24,将缓解阀手柄推至制动缸压力开始下降时,立即关断24,制动缸压力空气排零。在缓解阀上呼吸孔涂刷检漏剂进行检查,不应产生漏泄。A.3.1.2.2.6缓解阀内副风缸及加速缓解风缸气路、小止回阀、排风阀开通24,将缓解阀手柄推至全开位,使副风缸压力降至100kPa后关断24。在缓解阀手柄处涂刷检漏剂进行检查,不应产生漏泄;在缓解阀排气口涂刷检漏剂进行检查,在10s内产生的气泡高度不应大于12mm。
关断3,开通A、1、9后,再开通16,待副风缸和加速缓解风缸压力均充至定压后,关断9、16。A.3.1.2.3缓解位漏泄试验
A.3.1.2.3.1缓解位漏泄试验准备确认10、1、2、5、A已开通,制动管、副风缸和加速缓解风缸压力均充至定压。A3.1.2.3.2结合面
除主阀前盖及缓解阀下盖外,在各结合面周围涂检漏剂进行检查,不应漏泄。7
小提示:此标准内容仅展示完整标准里的部分截取内容,若需要完整标准请到上方自行免费下载完整标准文档。

标准图片预览:
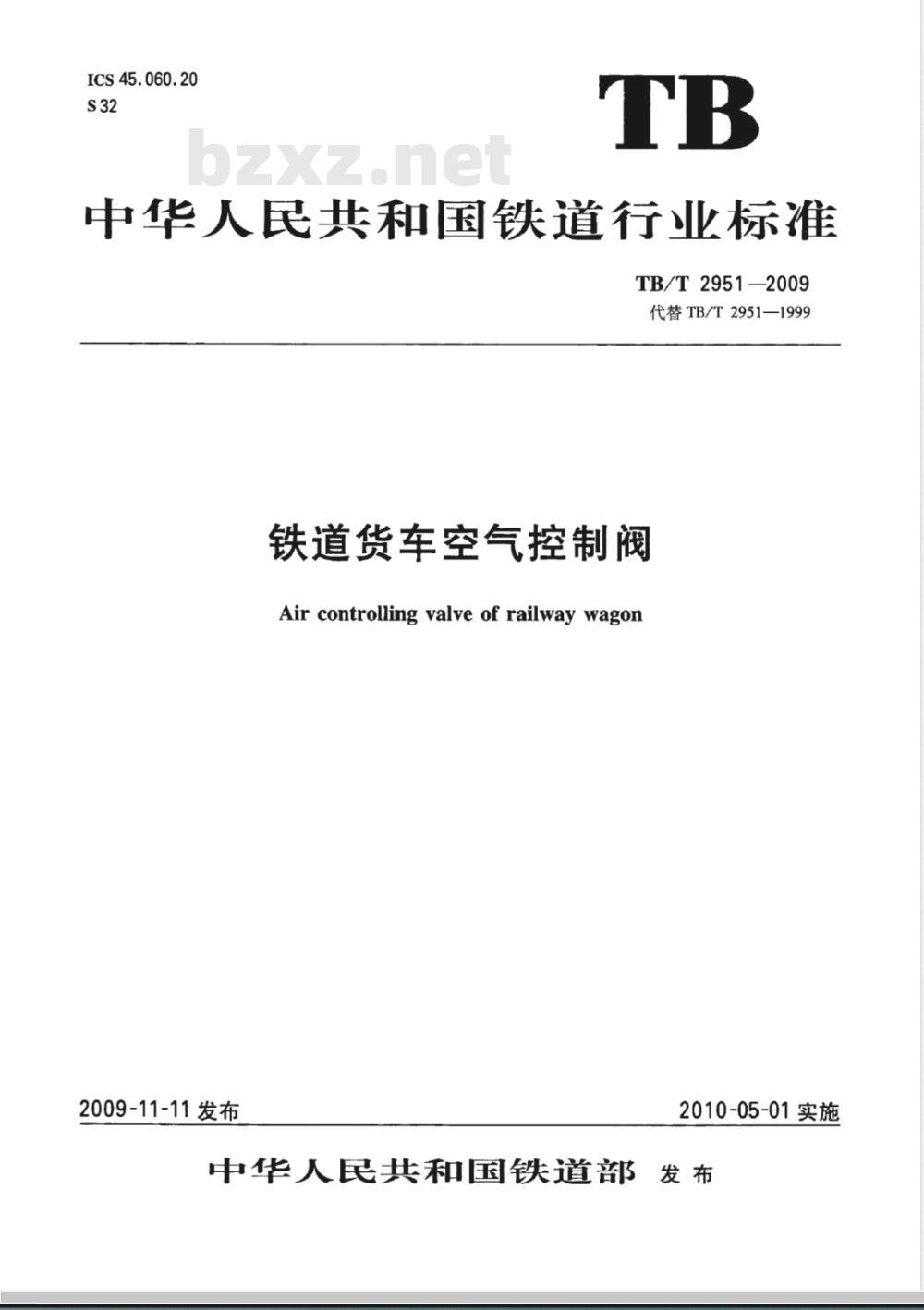
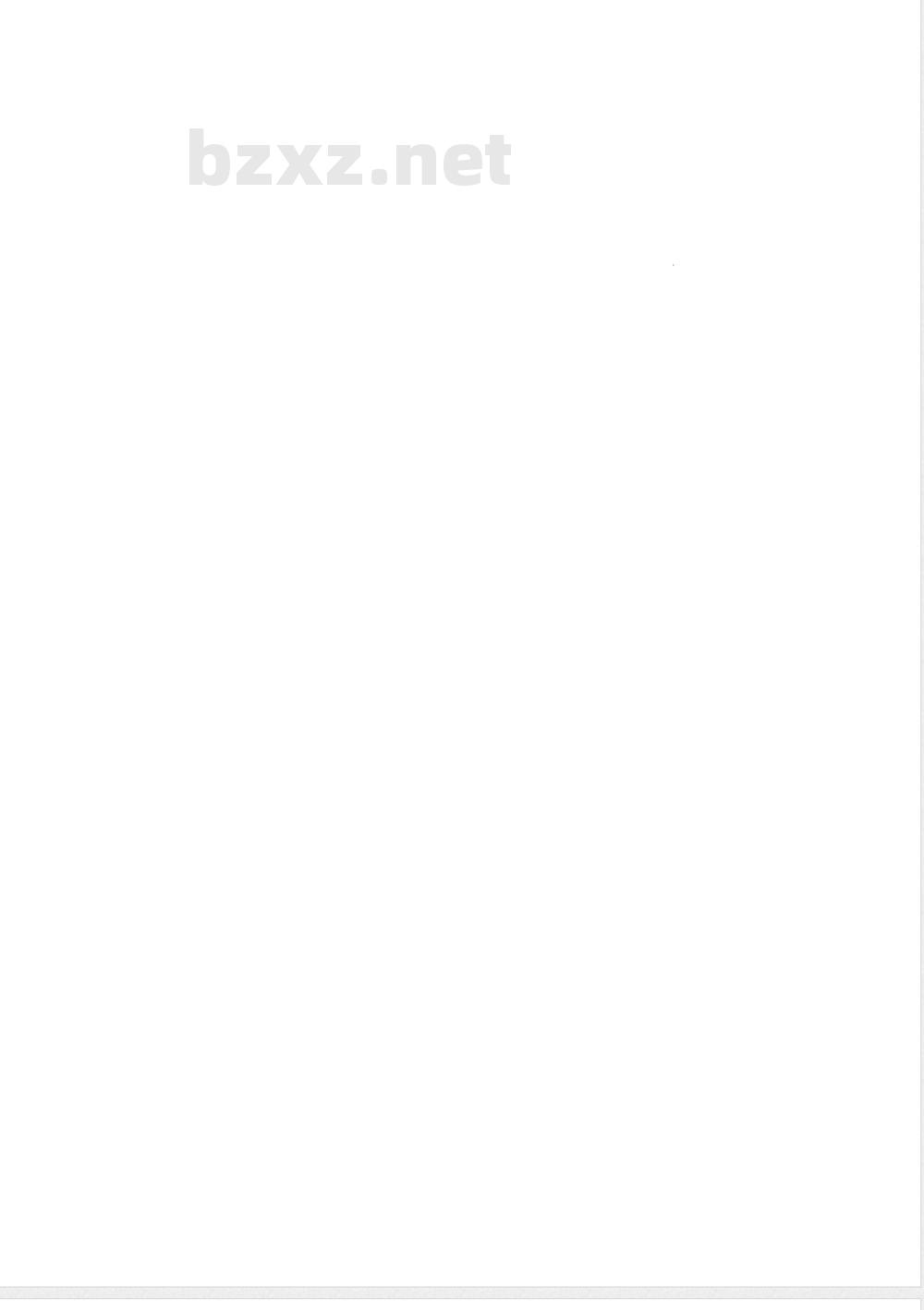
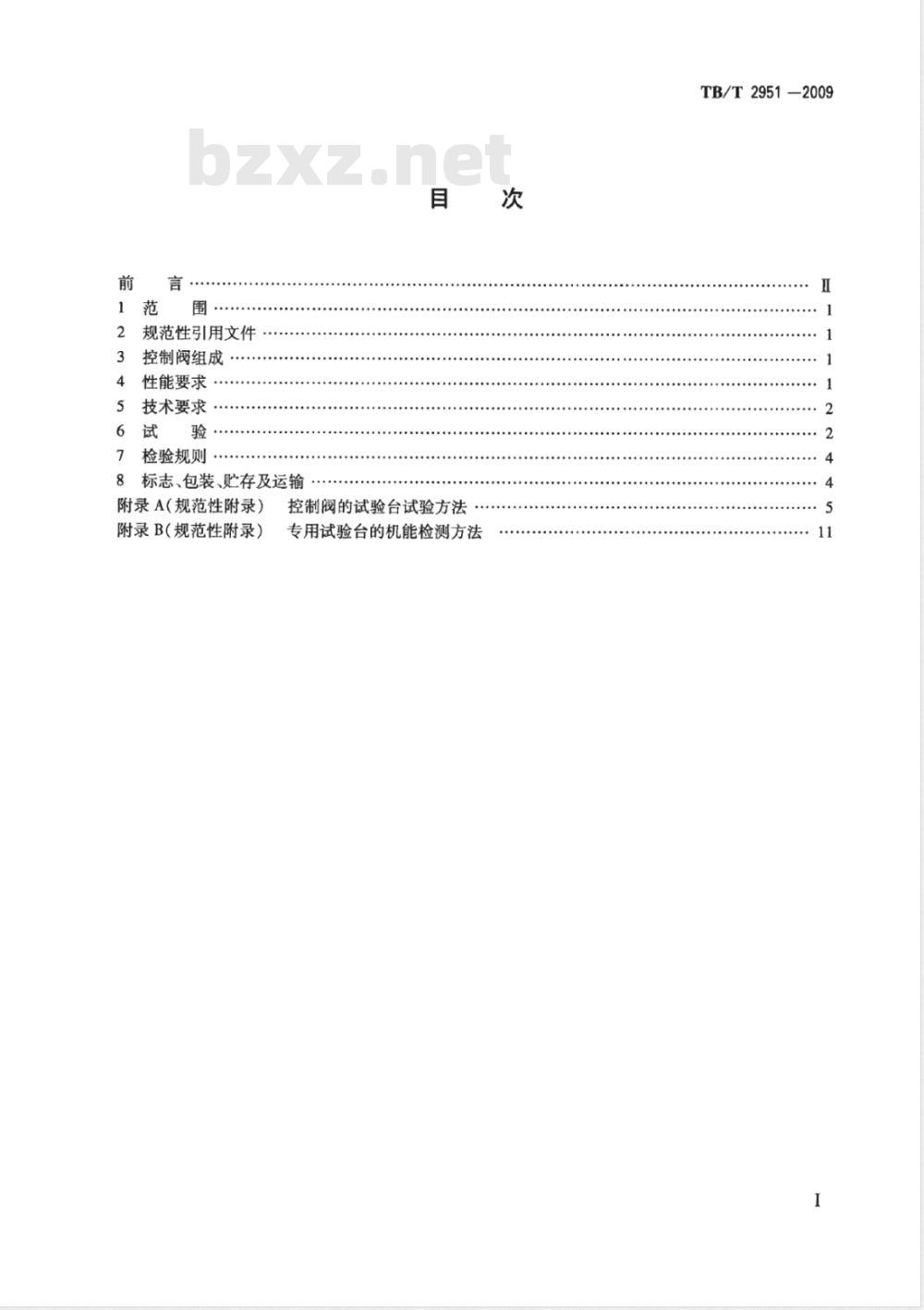
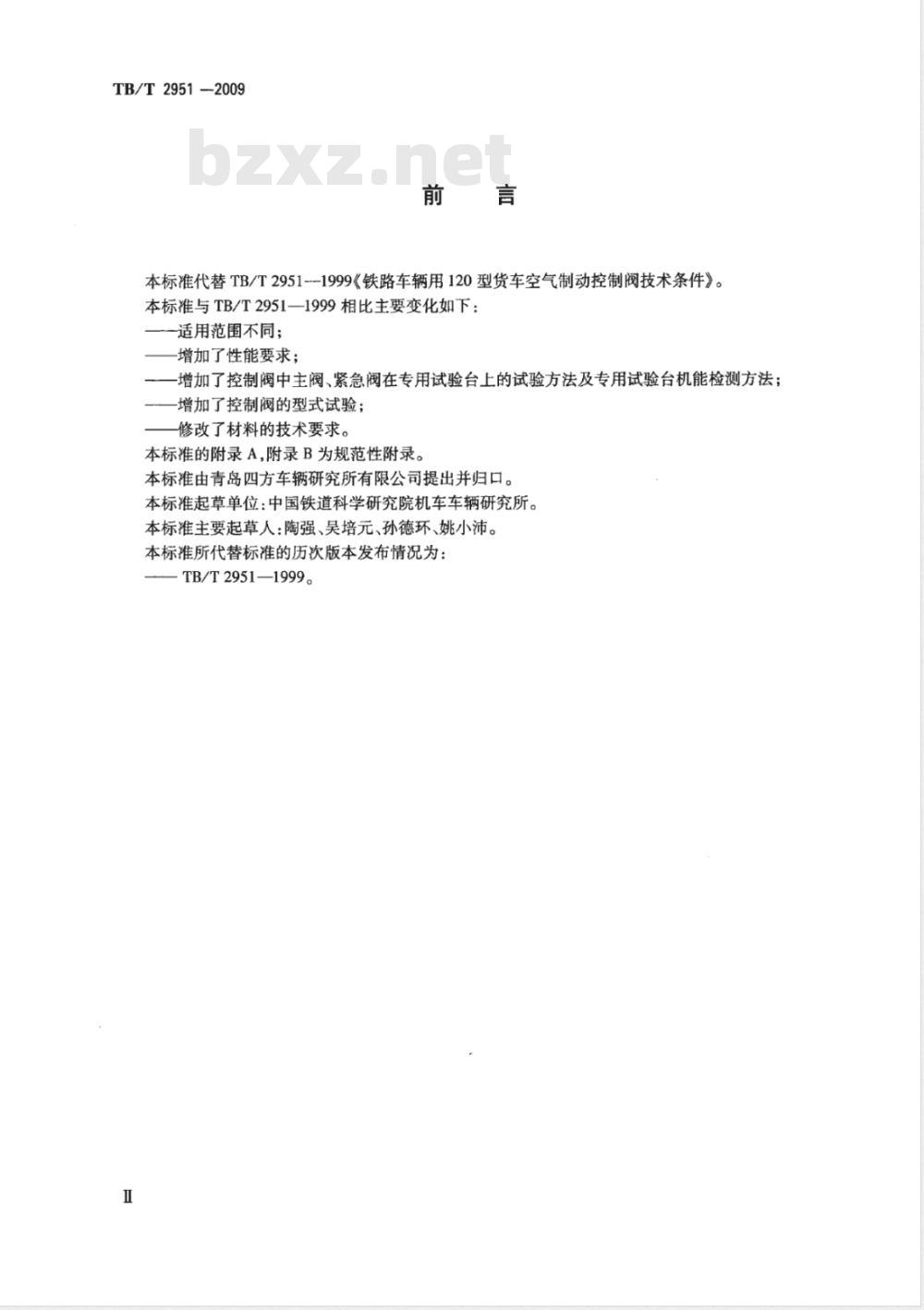
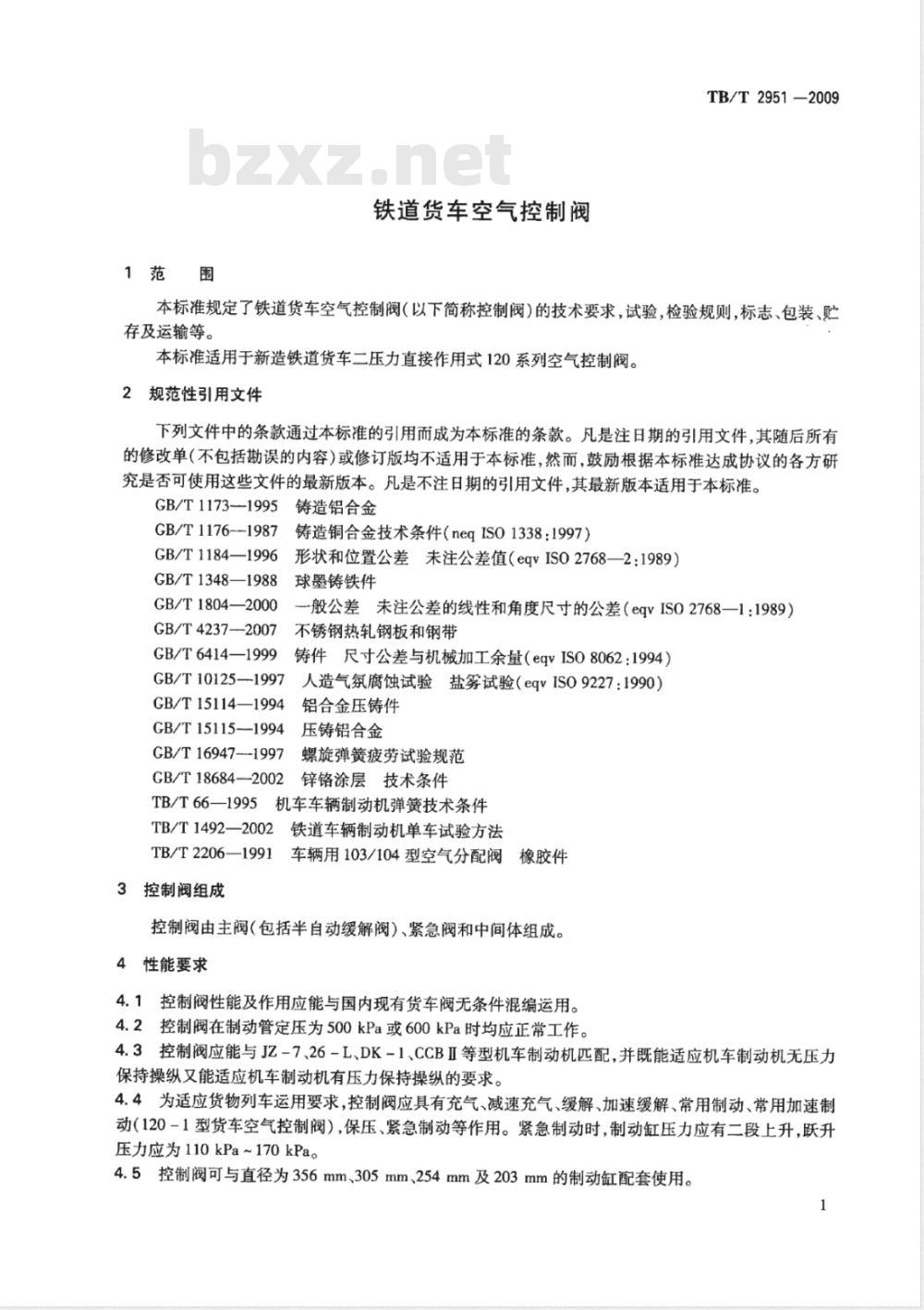
- 热门标准
- 铁路运输行业标准(TB)
- TB10122-2008 铁路路堑边坡光面(预裂)爆破技术规程
- TB/T1760-1986 客车门锁技术条件
- TB/T1632.4-2005 钢轨焊接 第4部分:气压焊接
- TB/T2599-1996 细长钢管内壁涂塑技术条件
- TB/T2563-1995 内燃机车用柴油机机体清洁度测定方法
- TB/T3523.2-2018 交流传动电力机车试验方法第2部分:输入特性试验
- TB/T2769.9-1997 重型轨道车试验方法动力学性能试验方法及评定标准
- TB/T2521-1995 电力机车平波电抗器装车后温升与电感值试验计算方法
- TB/T2820.1-1997 铁路桥隧建筑物劣化评定标准钢梁
- TB/T3416.3-2015 动车组编码标识系统第3部分:安装地点与位置的标识
- TB/T2152.8-1990 铁路工人技术标准 机务 运用值班员
- TB/T1932-2009 旅客列车卫生及监测技术规定
- TB/T3170-2007 货车车钩、钩尾框采购和验收技术条件
- TB/T1869.4-2013 铁路信号用变压器第4部分:25 Hz系列轨道变压器
- TB/T2472-93D ●S型道口闪光器
- 行业新闻
请牢记:“bzxz.net”即是“标准下载”四个汉字汉语拼音首字母与国际顶级域名“.net”的组合。 ©2009 标准下载网 www.bzxz.net 本站邮件:bzxznet@163.com
网站备案号:湘ICP备2023016450号-1
网站备案号:湘ICP备2023016450号-1