- 您的位置:
- 标准下载网 >>
- 标准分类 >>
- 铁路运输行业标准(TB) >>
- TB/T 3154-2007 机车车辆车轮和轮箍伤损代码
标准号:
TB/T 3154-2007
标准名称:
机车车辆车轮和轮箍伤损代码
标准类别:
铁路运输行业标准(TB)
标准状态:
现行-
发布日期:
2007-08-13 -
实施日期:
2007-12-01 出版语种:
简体中文下载格式:
.rar.pdf下载大小:
2.70 MB

部分标准内容:
ICS 45.060.20
中华人民共和国铁道行业标准
TB/T 3154--2007
机车车辆车轮和轮箍伤损代码
Damage codes of wheel and tyre forlocomotive and vehicle
2007-08-13发布
2007-12-01实施
中华人民共和国铁道部发布
编码规则
代码结构
编码示例
主要车轮轮箍伤摄名称,代码、伤损描述、伤摄主要原网及形貌示例5
车轮轮箍伤损代码明细
附录A(规范性附录)焊补缺陷编码示例附录B(资料性附录)机车车辆车轮和轮箍伤损术语的中英文对照TB/F3154—2007
TB/T3154—2007
本标推由铁道部标准计量研究所提出并归口。本标准的附录A为规范性附录。
本标准的附录 B 为资料性附录。本标准起草单位;铁道科学研究院金属及化学研究所,铁道部标准计策研究所、马鞍山钢铁股份有限公司车轮公司、北京铁路局。本标准主要起草人:付秀琴、朱梅、张弘、张斌、安涛、郎顺明。1范圈
机车车辆车轮和轮箍伤损代码
TB/T3154--2007
本标准规定了在役铁道机车车辆车轮,轮箍伤摄编码规则、代码结构,给出了编码示例及主要车轮轮箍伤摄名称,代码、伤损描述、原因及形貌示例。本标准适用于在役铁道机车车辆车轮、轮箍(以下简称车轮、轮箍)伤损分析、判定及信息处理。2编码规则
2.1车轮、轮箍伤损编码采用面分类体系,用特征组合码表示。2.2若同时出现几种伤损,则以主要的伤损进行编码。3代码结构
3.1车轮和轮箍各部位名称见图1和图2。: ..
图1车轮各部位名称
图2轮箍各部位名称
TB/T3154—2007
3.2车轮和轮箍伤损代码由七位数字组成,结构说明如下:XXXXXXX
第六、第七位:伤损主要原因
第五位:伤损类型
第四位:伤损部位
第三位:车轮、轮箍所属机车、车辆类型第二位:制造或成型方式
第一位:伤损产品名称
3.3代码结构各位组成及代号见表1~表6。表1第一位代码的组成及代号
伤损产品名称
制造或成型方式
撬钢轧制
表2第二位代码的组成及代号
表3第三位代码的组成及代号
车轮、轮箍所属机车、车辆类型机车
动车组
表4第四位代码的组成及代号
伤损部位
辐板孔
轮芯挡
碾边(碾堆)
异常磨耗
划伤(拉伤)
其他伤损
伤损类型
表5第五位代码的组成及代号
表6第六、第七位代码的组成及代号伤损主要原因
由于制造方面的缺陷造成的伤损由于轮轨接触疲劳或轮轨接触应力过大造成的伤损由于制动时闸瓦接触造成的热伤损由于车轮、轮箍维护和装配方面造成的伤损由于车轮、轮箍与钢轨强烈摩擦造成的热伤损由于焊补或其他处理方法(包括表面处理)造成的伤损由于制动不当造成的伤摄
由于外界工具撞击或其他机械作用造成的伤损由于打印标记造成的伤损
由于其他原因造成的伤损
编码示例
示例1:客车车轮轮辋裂纹代码
第一位,伤损产品名称:车轮,W;第二位,制造或成型方式:钢,0;第三位,车轮、轮箍所属类型:客车,1;第四位,伤损部位:轮辆,2;
第五位,伤损类型:裂纹,0;
第六、七位,伤损主要原因:由于制造方面的缺陷造成的伤损,00。代码:w012000
示例2:轮箍踏面热裂纹代码
第一位,伤损产品名称:轮箍,T:第二位,制造或成型方式:辗钢,0;第三位,车轮、轮箍所属类型:机车,0;0
TB/T3154—2007
TB/T3154—2007
第四位,伤损部位:踏面,1;
第五位,伤损类型:裂纹,0;
第六、七位,伤损主要原因:由于制动时阐瓦接触造成的热伤损,02。代码:T001002
5主要车轮轮箍伤损名称、代码、伤损描述、伤损主要原因及形貌示例在以下主要各类车轮、轮箍伤损代码中,代码组成已明确的给出了代号:代码组成不明确的用“×表示,在具体应用中确定。
5.1轮辋内部疲劳裂纹(筒称“辋裂”)代码:×××2000
可能发生的车轮、轮箍类型:辗钢车轮、铸钢车轮、轮箍。伤损描述:“辋裂”特征主要表现为轮辋外侧面裂纹、轮辋内侧面裂纹、发展到轮缘的裂纹,裂纹源通常位于踏面下15mm左右,通过超声波探伤可大致判断其裂纹扩展区域及深度,伤损主要原因:由于制造方面的缺陷造成的伤损。除特殊情况外,裂纹源处存在较大颗粒的非金属夹杂物,在轮轨作用力下萌生裂纹并扩展,导致“辋裂”。形貌示例:见图3。
a)发展到轮辋外侧面的轮辋疲劳裂纹c)发展到轮缘的轮辑疲劳裂纹
5.2轮辋掉块
代码:×××2600
图3辋裂形貌示例
可能发生的车轮、轮箍类型:辗钢车轮、铸钢车轮、轮箍。b)发展到轮辋内侧面的轮鞘疲劳裂纹d超声波探伤检查轮辋内部疲劳裂纹区城伤损描述:由于轮辋内部疲劳裂纹扩展导致轮辋局部脱落即掉块,掉块及掉块对应偶合面上具有“贝壳状”疲劳弧线及疲劳裂纹源。4
TB/T 3154—2007
伤损主要原因:由于制造方面的缺陷造成的伤损。除特殊情况外,一般裂纹源处存在较大颗粒的非金属夹杂物,在轮轨作用力下萌生裂纹并扩展导致轮辋掉块。形貌示例:见图4。
a)轮辋块及模块对应偶合面
5)轮辋局部掉块
图4轮辋掉块形貌示例
5.3因车轮冶金缺陷造成的崩轮(裂损)代码:W××7500
可能发生的车轮、轮箍类型:辗钢车轮、铸钢车轮。伤损描述:车轮裂损多表现为车轮整体崩裂成数块。c)裂纹源处非金属夹杂物
伤损主要原因:由于制造方面的缺陷造成的伤损。主要是车轮钢存在严重异型偏析、疏松、内裂、白点等不允许有的治金缺陷等,运用过程中受力作用导致车轮崩裂。形貌示例:见图5。
图5裂损形貌示例
TB/T3154—2007
5.4制动产生的热裂纹导致车轮(轮箍)径向崩裂代码:×××7506
可能发生的车轮、轮箍类型:镶钢车轮、铸钢车轮、轮箍。盘形制动除外。伤损描述:车轮(轮箍)径向崩裂。伤损主要原因:由于制动不当造成的伤损,制动导致踏面产生热裂纹,在轮轨接触应力作用下热裂纹进一步扩展导致车轮(轮箍)径向崩裂。形貌示例:见图6。
a)车轮径向期裂
b)车轮踏面制动热裂纹
图6,车轮径向期裂形貌示例
5.5由于车轮辆板孔裂纹造成的车轮裂代码:WO×3599
可能发生的车轮、轮箍类型:辗钢车轮。伤损描述:车轮辐板处沿周向崩裂破损,裂纹源位于辐板孔边缘棱角处。伤损主要原因:由于其他原因造成的伤损。辐板工艺孔设计不合理,辐板孔边缘处尖锐并导致应力集中,运用中疲劳裂纹扩展导致车轮崩裂。形貌示例:见图7。www.bzxz.net
a)车轮胡裂
一裂纹源
b)车轮辐板孔裂纹起源及疲劳展图7由于车轮辐板孔裂纹造成的车轮崩裂形貌示例6
5.6车轮辐板裂纹
5.6.1辐板工艺孔裂纹
代码:W0×4099
可能发生的车轮、轮箍类型:辗钢车轮。伤损描述:在车轮辐板工艺孔边缘向两侧发展为周向裂纹。TB/T3154—-2007
伤损主要原因:由于其他原因造成的伤损。辐板孔、工艺孔设计不合理,孔边缘尖锐,使该部位形成应力集中,从而萌生裂纹。
形貌示例:见图8。
a)货车车轮辑板工艺孔周向裂纹c)机车车轮辐板孔裂纹
b)a)图辐板孔裂蚊打开后裂纹源及疲劳扩展图8车轮辐板孔裂纹形貌示例
5.6.2辐板其他部位裂纹
代码:W××3000
可能发生的车轮、轮箍类型:辗钢车轮、铸钢车轮:伤损描述:在轮辋及辐板过渡区处存在的周向裂纹。伤损主要原因:由于制造方面的缺陷造成的伤损。由于辐板表面不加工可能存在表面轧制裂纹、发纹、铸造裂纹或其他制造缺陷;当轮辋使用过薄,导致该部位承受应力较大形成应力集中而萌生裂纹:
形貌示例:见图9。
TB/T3154—2007
5.7踏面擦伤
代码:×××1204
a)车轮辐板裂纹(箭头所指)
b)车轮辐板裂纹打开后的疲劳扩展断口图9车轮辐板裂纹形貌示例
可能发生的车轮、轮箍类型:辗钢车轮、铸钢车轮、轮箍。伤损描述:车轮或轮箍踏面呈现类似椭圆形痕迹,该部位局部凹陷,一般情况一条轮对的两个车轮或轮箍对称部位均能看到擦伤形貌。伤损主要原因:由于车轮、轮箍与钢轨强烈摩擦造成的热伤损。车轮或轮箍与钢轨间发生相对滑动,导致强烈摩擦,摩擦热使车轮或轮箍踏面局部产生相变,形成硬而脆的马氏体组织,严重时会导致擦伤处剥离掉块。
形貌示例:见图10。
a)踏面擦伤
b)一条轮对上两个车轮踏面对称部位擦伤(箭头所指)c)擦伤处马氏体白层
图10踏面擦伤及擦伤处马氏体白层形貌示例8
5.8踏面熔
代码:×××1902
可能发生的车轮、轮箍类型:辗钢车轮、铸钢车轮、轮箍。盘形制动除外。TB/T3154—2007
伤损描述:踏面局部出现熔融现象或问瓦熔渣现象,该种伤损多出现在踏面闸瓦制动方式的情况下。伤损主要原因:由于制动时闸瓦接触造成的热伤损。由于强烈制动,闸瓦与车轮或轮箍踏面接触部位产生高热,使局部熔融。
形貌示例:见图11。
a)车轮踏面熔着
图11踏面熔融形貌示例
5.9踏面制动热裂纹
代码:×××1002
b)面熔着导致拉伤
可能发生的车轮、轮箍类型:钢车轮、铸钢车轮、轮箍。盘形制动除外,伤损描述:车轮或轮箍踏面周向存在较规则的“刻度\状裂纹,一般出现在踏面闸瓦制动方式的情况下。伤损主要原因:由于制动时闸瓦接触造成的热伤损。制动条件恶劣,制动系统作用不良,使车轮承受过高的热载荷,导致表面出现制动热裂纹。形貌示例:见图12。
a)踏面刻度状制动热裂纹
显微硬度
)金相显微销下观察到热影响组织及热裂纹b)踏面纵向切片裂纹
热裂纹
图12踏面制动热裂纹及热影响组织和热裂纹形貌示例9
小提示:此标准内容仅展示完整标准里的部分截取内容,若需要完整标准请到上方自行免费下载完整标准文档。
中华人民共和国铁道行业标准
TB/T 3154--2007
机车车辆车轮和轮箍伤损代码
Damage codes of wheel and tyre forlocomotive and vehicle
2007-08-13发布
2007-12-01实施
中华人民共和国铁道部发布
编码规则
代码结构
编码示例
主要车轮轮箍伤摄名称,代码、伤损描述、伤摄主要原网及形貌示例5
车轮轮箍伤损代码明细
附录A(规范性附录)焊补缺陷编码示例附录B(资料性附录)机车车辆车轮和轮箍伤损术语的中英文对照TB/F3154—2007
TB/T3154—2007
本标推由铁道部标准计量研究所提出并归口。本标准的附录A为规范性附录。
本标准的附录 B 为资料性附录。本标准起草单位;铁道科学研究院金属及化学研究所,铁道部标准计策研究所、马鞍山钢铁股份有限公司车轮公司、北京铁路局。本标准主要起草人:付秀琴、朱梅、张弘、张斌、安涛、郎顺明。1范圈
机车车辆车轮和轮箍伤损代码
TB/T3154--2007
本标准规定了在役铁道机车车辆车轮,轮箍伤摄编码规则、代码结构,给出了编码示例及主要车轮轮箍伤摄名称,代码、伤损描述、原因及形貌示例。本标准适用于在役铁道机车车辆车轮、轮箍(以下简称车轮、轮箍)伤损分析、判定及信息处理。2编码规则
2.1车轮、轮箍伤损编码采用面分类体系,用特征组合码表示。2.2若同时出现几种伤损,则以主要的伤损进行编码。3代码结构
3.1车轮和轮箍各部位名称见图1和图2。: ..
图1车轮各部位名称
图2轮箍各部位名称
TB/T3154—2007
3.2车轮和轮箍伤损代码由七位数字组成,结构说明如下:XXXXXXX
第六、第七位:伤损主要原因
第五位:伤损类型
第四位:伤损部位
第三位:车轮、轮箍所属机车、车辆类型第二位:制造或成型方式
第一位:伤损产品名称
3.3代码结构各位组成及代号见表1~表6。表1第一位代码的组成及代号
伤损产品名称
制造或成型方式
撬钢轧制
表2第二位代码的组成及代号
表3第三位代码的组成及代号
车轮、轮箍所属机车、车辆类型机车
动车组
表4第四位代码的组成及代号
伤损部位
辐板孔
轮芯挡
碾边(碾堆)
异常磨耗
划伤(拉伤)
其他伤损
伤损类型
表5第五位代码的组成及代号
表6第六、第七位代码的组成及代号伤损主要原因
由于制造方面的缺陷造成的伤损由于轮轨接触疲劳或轮轨接触应力过大造成的伤损由于制动时闸瓦接触造成的热伤损由于车轮、轮箍维护和装配方面造成的伤损由于车轮、轮箍与钢轨强烈摩擦造成的热伤损由于焊补或其他处理方法(包括表面处理)造成的伤损由于制动不当造成的伤摄
由于外界工具撞击或其他机械作用造成的伤损由于打印标记造成的伤损
由于其他原因造成的伤损
编码示例
示例1:客车车轮轮辋裂纹代码
第一位,伤损产品名称:车轮,W;第二位,制造或成型方式:钢,0;第三位,车轮、轮箍所属类型:客车,1;第四位,伤损部位:轮辆,2;
第五位,伤损类型:裂纹,0;
第六、七位,伤损主要原因:由于制造方面的缺陷造成的伤损,00。代码:w012000
示例2:轮箍踏面热裂纹代码
第一位,伤损产品名称:轮箍,T:第二位,制造或成型方式:辗钢,0;第三位,车轮、轮箍所属类型:机车,0;0
TB/T3154—2007
TB/T3154—2007
第四位,伤损部位:踏面,1;
第五位,伤损类型:裂纹,0;
第六、七位,伤损主要原因:由于制动时阐瓦接触造成的热伤损,02。代码:T001002
5主要车轮轮箍伤损名称、代码、伤损描述、伤损主要原因及形貌示例在以下主要各类车轮、轮箍伤损代码中,代码组成已明确的给出了代号:代码组成不明确的用“×表示,在具体应用中确定。
5.1轮辋内部疲劳裂纹(筒称“辋裂”)代码:×××2000
可能发生的车轮、轮箍类型:辗钢车轮、铸钢车轮、轮箍。伤损描述:“辋裂”特征主要表现为轮辋外侧面裂纹、轮辋内侧面裂纹、发展到轮缘的裂纹,裂纹源通常位于踏面下15mm左右,通过超声波探伤可大致判断其裂纹扩展区域及深度,伤损主要原因:由于制造方面的缺陷造成的伤损。除特殊情况外,裂纹源处存在较大颗粒的非金属夹杂物,在轮轨作用力下萌生裂纹并扩展,导致“辋裂”。形貌示例:见图3。
a)发展到轮辋外侧面的轮辋疲劳裂纹c)发展到轮缘的轮辑疲劳裂纹
5.2轮辋掉块
代码:×××2600
图3辋裂形貌示例
可能发生的车轮、轮箍类型:辗钢车轮、铸钢车轮、轮箍。b)发展到轮辋内侧面的轮鞘疲劳裂纹d超声波探伤检查轮辋内部疲劳裂纹区城伤损描述:由于轮辋内部疲劳裂纹扩展导致轮辋局部脱落即掉块,掉块及掉块对应偶合面上具有“贝壳状”疲劳弧线及疲劳裂纹源。4
TB/T 3154—2007
伤损主要原因:由于制造方面的缺陷造成的伤损。除特殊情况外,一般裂纹源处存在较大颗粒的非金属夹杂物,在轮轨作用力下萌生裂纹并扩展导致轮辋掉块。形貌示例:见图4。
a)轮辋块及模块对应偶合面
5)轮辋局部掉块
图4轮辋掉块形貌示例
5.3因车轮冶金缺陷造成的崩轮(裂损)代码:W××7500
可能发生的车轮、轮箍类型:辗钢车轮、铸钢车轮。伤损描述:车轮裂损多表现为车轮整体崩裂成数块。c)裂纹源处非金属夹杂物
伤损主要原因:由于制造方面的缺陷造成的伤损。主要是车轮钢存在严重异型偏析、疏松、内裂、白点等不允许有的治金缺陷等,运用过程中受力作用导致车轮崩裂。形貌示例:见图5。
图5裂损形貌示例
TB/T3154—2007
5.4制动产生的热裂纹导致车轮(轮箍)径向崩裂代码:×××7506
可能发生的车轮、轮箍类型:镶钢车轮、铸钢车轮、轮箍。盘形制动除外。伤损描述:车轮(轮箍)径向崩裂。伤损主要原因:由于制动不当造成的伤损,制动导致踏面产生热裂纹,在轮轨接触应力作用下热裂纹进一步扩展导致车轮(轮箍)径向崩裂。形貌示例:见图6。
a)车轮径向期裂
b)车轮踏面制动热裂纹
图6,车轮径向期裂形貌示例
5.5由于车轮辆板孔裂纹造成的车轮裂代码:WO×3599
可能发生的车轮、轮箍类型:辗钢车轮。伤损描述:车轮辐板处沿周向崩裂破损,裂纹源位于辐板孔边缘棱角处。伤损主要原因:由于其他原因造成的伤损。辐板工艺孔设计不合理,辐板孔边缘处尖锐并导致应力集中,运用中疲劳裂纹扩展导致车轮崩裂。形貌示例:见图7。www.bzxz.net
a)车轮胡裂
一裂纹源
b)车轮辐板孔裂纹起源及疲劳展图7由于车轮辐板孔裂纹造成的车轮崩裂形貌示例6
5.6车轮辐板裂纹
5.6.1辐板工艺孔裂纹
代码:W0×4099
可能发生的车轮、轮箍类型:辗钢车轮。伤损描述:在车轮辐板工艺孔边缘向两侧发展为周向裂纹。TB/T3154—-2007
伤损主要原因:由于其他原因造成的伤损。辐板孔、工艺孔设计不合理,孔边缘尖锐,使该部位形成应力集中,从而萌生裂纹。
形貌示例:见图8。
a)货车车轮辑板工艺孔周向裂纹c)机车车轮辐板孔裂纹
b)a)图辐板孔裂蚊打开后裂纹源及疲劳扩展图8车轮辐板孔裂纹形貌示例
5.6.2辐板其他部位裂纹
代码:W××3000
可能发生的车轮、轮箍类型:辗钢车轮、铸钢车轮:伤损描述:在轮辋及辐板过渡区处存在的周向裂纹。伤损主要原因:由于制造方面的缺陷造成的伤损。由于辐板表面不加工可能存在表面轧制裂纹、发纹、铸造裂纹或其他制造缺陷;当轮辋使用过薄,导致该部位承受应力较大形成应力集中而萌生裂纹:
形貌示例:见图9。
TB/T3154—2007
5.7踏面擦伤
代码:×××1204
a)车轮辐板裂纹(箭头所指)
b)车轮辐板裂纹打开后的疲劳扩展断口图9车轮辐板裂纹形貌示例
可能发生的车轮、轮箍类型:辗钢车轮、铸钢车轮、轮箍。伤损描述:车轮或轮箍踏面呈现类似椭圆形痕迹,该部位局部凹陷,一般情况一条轮对的两个车轮或轮箍对称部位均能看到擦伤形貌。伤损主要原因:由于车轮、轮箍与钢轨强烈摩擦造成的热伤损。车轮或轮箍与钢轨间发生相对滑动,导致强烈摩擦,摩擦热使车轮或轮箍踏面局部产生相变,形成硬而脆的马氏体组织,严重时会导致擦伤处剥离掉块。
形貌示例:见图10。
a)踏面擦伤
b)一条轮对上两个车轮踏面对称部位擦伤(箭头所指)c)擦伤处马氏体白层
图10踏面擦伤及擦伤处马氏体白层形貌示例8
5.8踏面熔
代码:×××1902
可能发生的车轮、轮箍类型:辗钢车轮、铸钢车轮、轮箍。盘形制动除外。TB/T3154—2007
伤损描述:踏面局部出现熔融现象或问瓦熔渣现象,该种伤损多出现在踏面闸瓦制动方式的情况下。伤损主要原因:由于制动时闸瓦接触造成的热伤损。由于强烈制动,闸瓦与车轮或轮箍踏面接触部位产生高热,使局部熔融。
形貌示例:见图11。
a)车轮踏面熔着
图11踏面熔融形貌示例
5.9踏面制动热裂纹
代码:×××1002
b)面熔着导致拉伤
可能发生的车轮、轮箍类型:钢车轮、铸钢车轮、轮箍。盘形制动除外,伤损描述:车轮或轮箍踏面周向存在较规则的“刻度\状裂纹,一般出现在踏面闸瓦制动方式的情况下。伤损主要原因:由于制动时闸瓦接触造成的热伤损。制动条件恶劣,制动系统作用不良,使车轮承受过高的热载荷,导致表面出现制动热裂纹。形貌示例:见图12。
a)踏面刻度状制动热裂纹
显微硬度
)金相显微销下观察到热影响组织及热裂纹b)踏面纵向切片裂纹
热裂纹
图12踏面制动热裂纹及热影响组织和热裂纹形貌示例9
小提示:此标准内容仅展示完整标准里的部分截取内容,若需要完整标准请到上方自行免费下载完整标准文档。

标准图片预览:
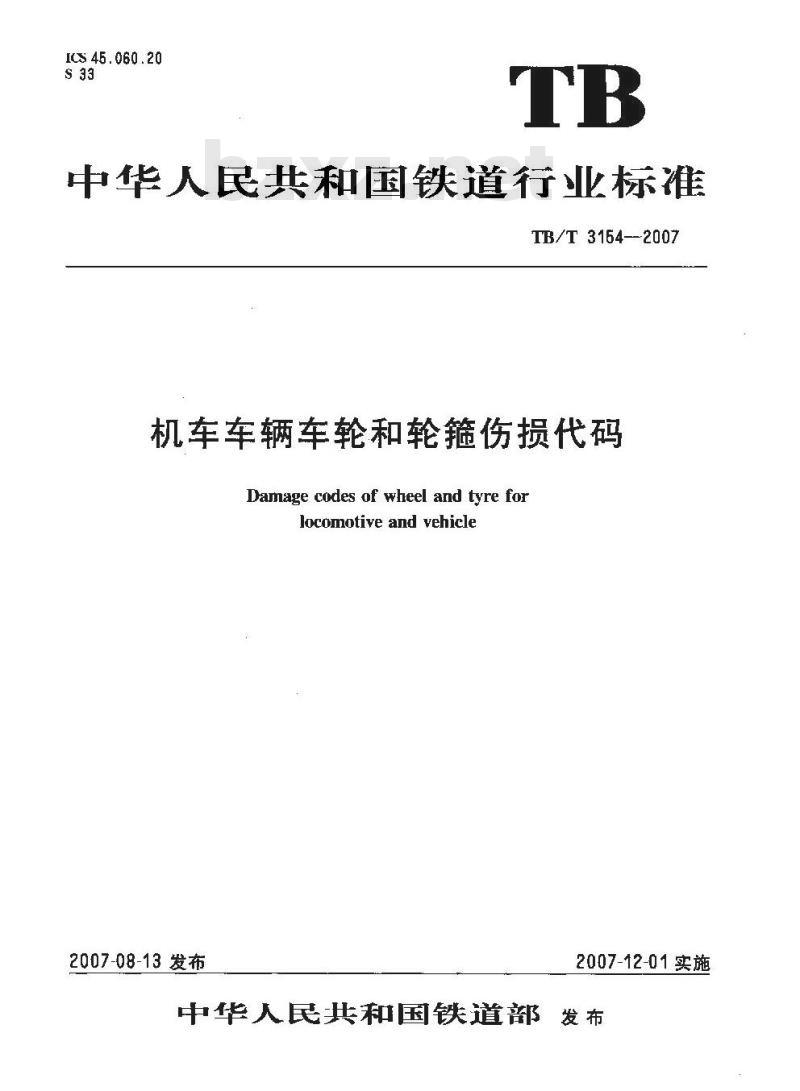
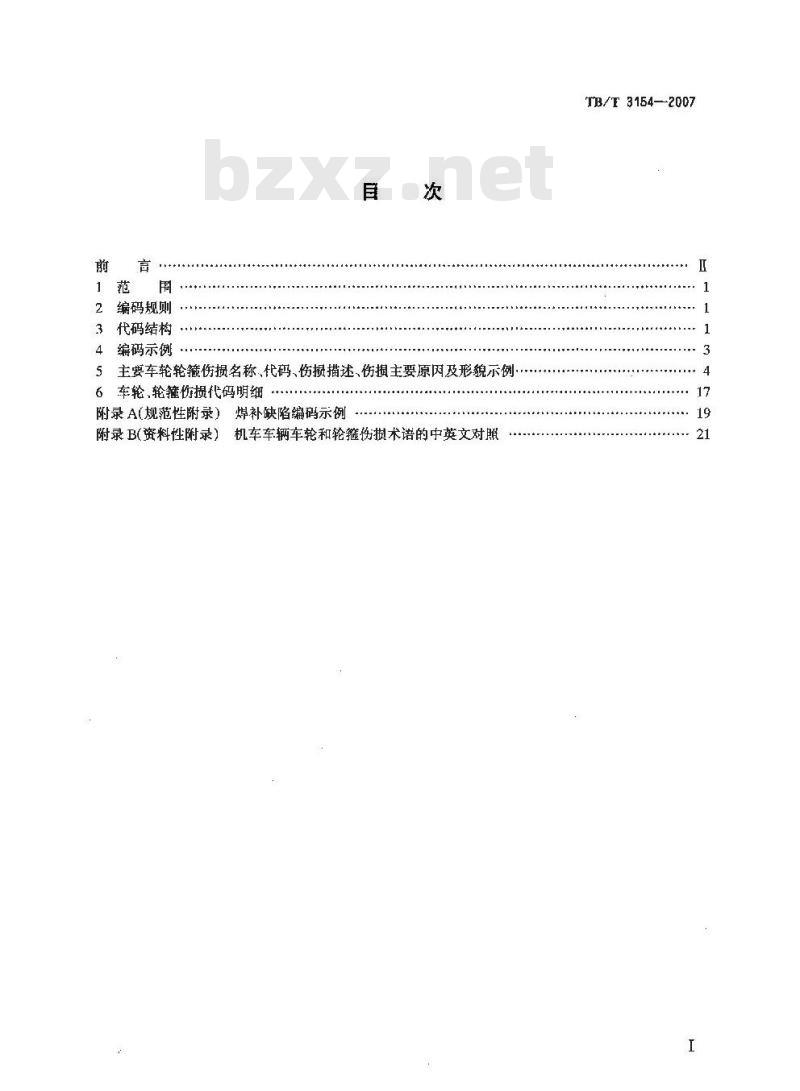
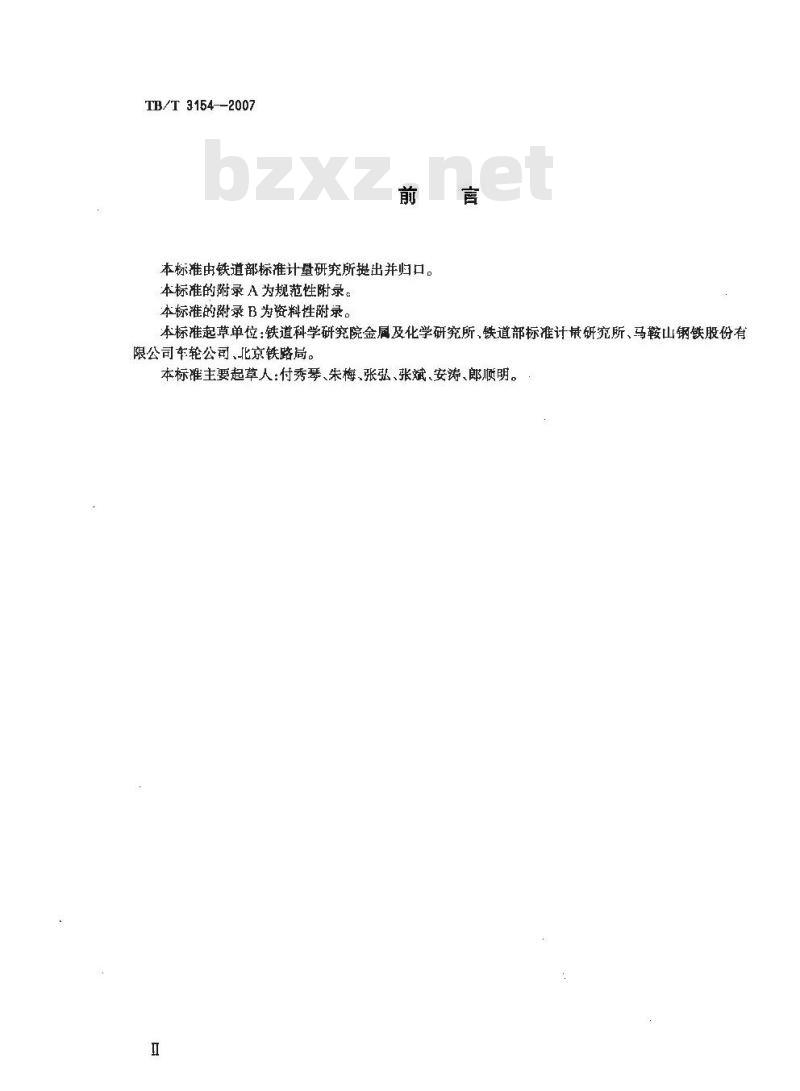
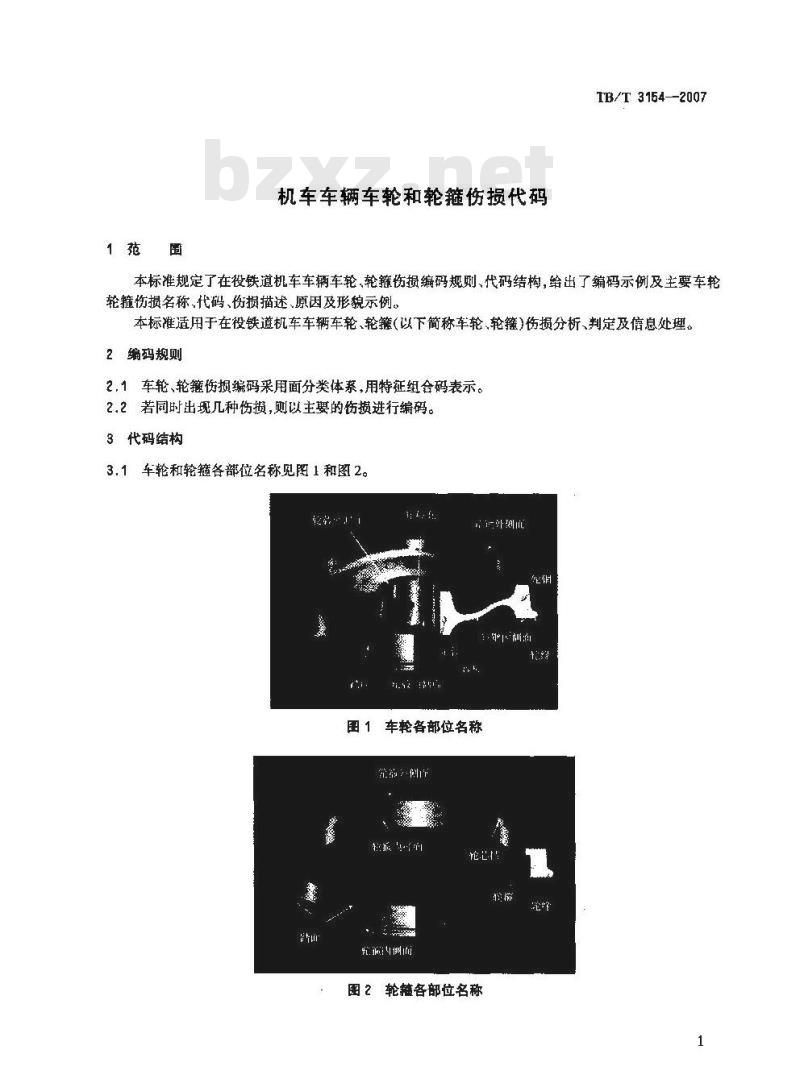
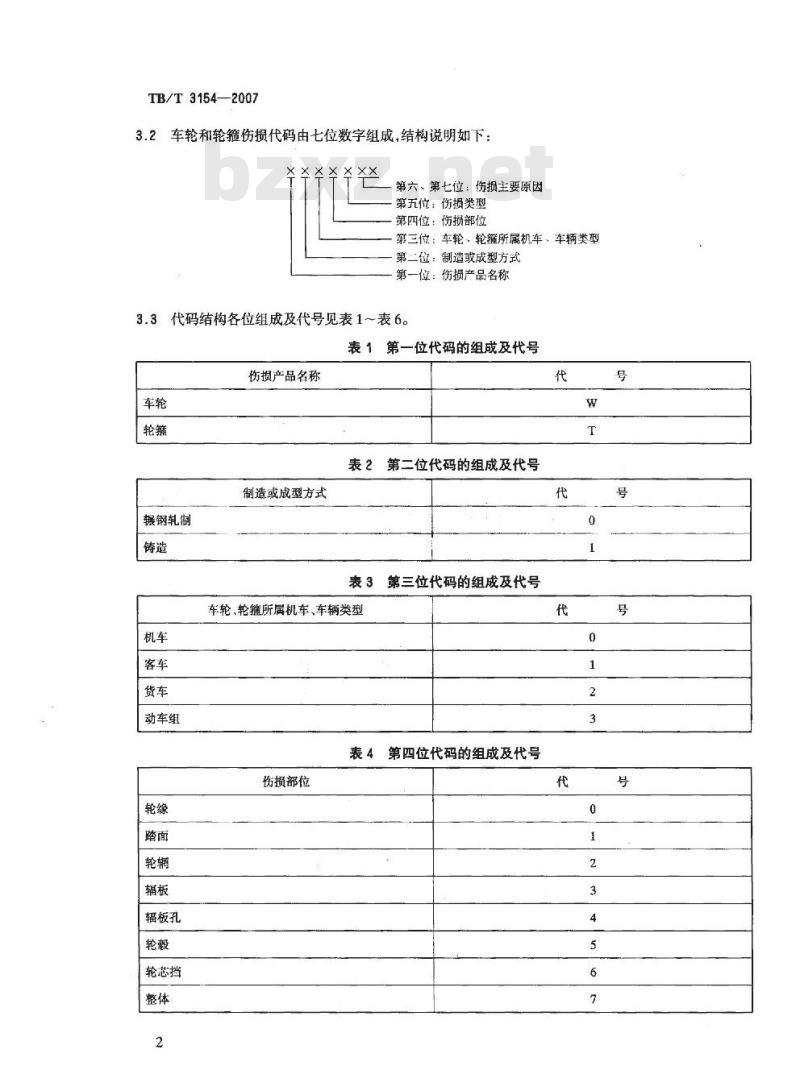
- 热门标准
- 铁路运输行业标准(TB)
- TB10002.3-2005 铁路桥涵钢筋混凝土和预应力混凝土结构设计规范(附条文说明)
- TB/T2993.5-2016 铁路通信电源第5部分:交流配电设备
- TB/T3199.2-2018 电气化铁路接触网用绝缘子第2部分:棒形复合绝缘子
- TB10038-2012 铁路工程特殊岩土勘察规程
- TB/T2152.27-1990 铁路工人技术标准 机务 接触网工
- TB10003-2016 铁路隧道设计规范
- TB/T2690-1996 铁路货物运输品名分类与代码
- TB/T2365-93 机车最大牵引|力、起动加速能力试验方法
- TB/T2685.1-1995 铁路环境监测质量控制环境监测指标体系及体系表
- TB/T2342.4-1993 75kg/m钢轨用接头夹板型式尺寸
- TB/T1669.6-1985 13号车钩钩舌回转样板上侧曲面(R86)的校对样板的基准样板
- TB2066-1989 蒸汽机车零部件高分子涂层修复通用技术条件
- TB/T1824-1987 蒸汽机车铸钢轮心技术条件
- TB/T2262-1991 上游型蒸汽机车
- TB/T2152.28-1990 铁路工人技术标准 机务 继电保护工
- 行业新闻
请牢记:“bzxz.net”即是“标准下载”四个汉字汉语拼音首字母与国际顶级域名“.net”的组合。 ©2009 标准下载网 www.bzxz.net 本站邮件:bzxznet@163.com
网站备案号:湘ICP备2023016450号-1
网站备案号:湘ICP备2023016450号-1