- 您的位置:
- 标准下载网 >>
- 标准分类 >>
- 机械行业标准(JB) >>
- JB/T 6887-2004 风机用铸铁件 技术条件
标准号:
JB/T 6887-2004
标准名称:
风机用铸铁件 技术条件
标准类别:
机械行业标准(JB)
标准状态:
现行-
发布日期:
2004-10-20 -
实施日期:
2005-04-01 出版语种:
简体中文下载格式:
.rar.pdf下载大小:
517.33 KB

点击下载
标准简介:
标准下载解压密码:www.bzxz.net
本标准规定了风机用铸铁件的技术要求、试验方法与验收规则。 JB/T 6887-2004 风机用铸铁件 技术条件 JB/T6887-2004

部分标准内容:
ICS23.120
中华人民共和国机械行业标准
JB/T6887--2004
代替JB/T6887-1993
JB/T68891993
风机用铸铁件
技术条件
Technical condition of cast iron for fans blower and compressors2004-10-20发布
2005-04-01实施
中华人民共和国国家发展和改革委员会发布前言,
1范围
2规范性引用文件,
3技术要求
3.1材料..
3.2生产方法和热处理
3.3力学性能和化学成分。
3.4金相组织..
几何形状、加工余量及尺寸公差3.6
表面质量
修整、
缺陷修补方法及质量要求
泄漏试验,
3.12底漆。
4试验方法和检验规则
5标志与证明书
附录A(规范性附录)铸件木模样起模斜度(JB/T5105)附录B(规范性附录)铸件机械加工余量(RMA)(GB/T6414)附录C(规范性附录)铸件尺寸公差数值(GB/T6414)附录D(规范性附录)铸件重量公差等级数值(GB/T11351)表旋转类铸件的同轴度公差
表2三开箱铸件尺寸公差
表.错箱值.
表4不需要修补缺陷的范围
表5毛环铸件缺陷允许焊补的范围表6机械加工中出现的缺陷允许焊补的范围表7套简的最小壁厚
表A.1铸件木模样起模斜度
铸件机械加工余量(RMA)
铸件尺寸公差数值
铸件重量公差等级数值
JB/T6887—2004
本标准是对JB/T6887—1993《风机用铸铁件技术条件》的修订。JB/T6887—2004
本标准在规范性引用文件上做了修改,并增加了一些有关内容。在技术内容和编写格式上,对原标准进行了必要的修订。
本标准与JB/T6887—1993相比,主要变化如下:将JB/T68891993《风机用铸铁件缺陷修补技术条件》主要内容并人本标准。-对铸件尺寸公差与机械加工余量的等级按照GB/T6414一1999重新进行了规定.质量等级有所提高。
铸件重量公差规定按GB/T11351一1989中MT13级执行,不采用惟一的7%重量偏差值。对风机铸件流道和外表面质量作了新的较高的要求,以适应市场对产品质量的要求在缺陷焊补范围中,对铸件分类作了新的划分,其中重量大于6300kg为特大件:满足风机铸件向大型化发展的需要。
由于振动时效新工艺的成熟,本标准首次明确将其与退火消除内应力方法等同有效。一对轴承箱、变速箱等铸件渗煤油试验和铸件涂底漆都作了进一步具体规定,便于实施。本标准对原铸铁件焊补工艺在内容上作了较大删减。附录B按照GBT6414--1999列出新的机械加工余量等级值,并新增附录D“铸件重量公差等级值\。
本标准的附录A、附录B、附录C、附录D都是规范性附录。本标准由中国机械工业联合会提出。本标准由全国风机标准化技术委员会归口。本标准由陕西鼓风机(集团)有限公司,沈阳鼓风机(集团)有限公司参加起草。本标准主要起草人:王奎旺、宋里里。本标准所代替标准的历次版本发布情况为:JB/T6887—1993:
JB/T6889—1993.
1范围
风机用铸铁件技术条件
本标准规定了风机用铸铁件的技术要求、试验方法与验收规则。JB/T6887--2004
本标准适用于透平式通风机、鼓风机、压缩机、膨胀机及罗茨、叶氏鼓风机所使用的灰铸铁、球墨铸铁和中锰抗磨球墨铸铁、高硅耐蚀铸铁、耐热铸铁等合金铸铁的铸铁件(以下简称铸件)。2规范性引用文件
下列文件中的条款通过本标准的引用而成为本标准的条款。凡是注日期的引用文件,其随后所有的修改单(不包括勘误的内容)或修订版均不适用于本标准,然而,鼓励根据本标准达成协议的各方研究是否可使用这些文件的最新版本。凡是不注日期的引用文件,其最新版本适用于本标准。GB/T223.3~78钢铁及合金化学分析方法GB/T228金属材料室温拉伸试验法(GB/T228—2002,eqvISO6892:1998(E))GB/T229
金属夏比缺口冲击试验方法(GB/T229--1994,eqvISO148:1983)金属洛氏硬度试验方法(GB/T230—1991,neqIS06508:1986)GB/T230
GB/T231.13金属布氏硬度试验方法GB/T1348
GB/T3180
球墨铸铁件
中锰抗磨球墨铸铁件技术条件
GB/T6060.1
GB/T6414
GB/T7216
GB/T8491
GB/T9437
表面粗糙度比较样块铸造表面(GB/T6060.1--1997,eqvISO2632-3:1979)铸件尺寸公差与机械加工余量(GB/T6414—1999,eqvISO8062:1994)灰铸铁金相(neqISO945:1975)高硅耐蚀铸铁件
耐热铸铁件
灰铸铁件
GB/T9439.
GB/T9441
GB/T11351
GB/T15056
JB/T5926
JB/T6886
JB/T7699
球墨铸铁金相检验
铸件重量公差
铸造表面粗糙度评定方法
振动时效工艺参数选择及技术要求通风机涂装技术条件
铸造用木制模样和芯盒技术条件JB/T7945灰铸铁力学性能试验方法3技术要求
3.1材料
本标准的各类铸铁件应使用符合GB/T9439、GB/T1348、GB/T9437、GB/T8491、GB/T3180规定的材料牌号。
3.2生产方法和热处理
铸件均应经退火处理或振动时效方法消除内应力。铸件的生产方法和热处理由供方自行决定,但必须达到本标准规定的牌号及有关技术性能。作调整力学性能和加工性能的重复热处理不能超过二次。若采用振动时效时,应严格按JB/T5926规定执行。对热处理和消除内应力方法有特殊要求时,应在图样JB/T6887—2004
或订货协议上注明。
3.3力学性能和化学成分
3.3.1铸件的力学性能和化学成分数值应符合3.1的规定。3.3.2灰铸铁件以抗拉强度作为验收依据:球墨铸铁件以抗拉强度和延伸率为验收依据:中锰抗磨球墨铸铁件以冲击值和硬度为验收依据:耐蚀铸件以化学成分和室温抗拉强度为验收依据。如有其他特殊要求时,应在订货协议中注明。3.3.3铸件的试棒试块:
a)灰铸铁件、高硅耐蚀铸铁件、RT型耐热铸铁件的抗拉强度、抗弯强度试棒,应采用砂型中立浇的@30mm单铸试棒:
b)球墨铸铁件、RQT型耐热铸铁件的抗拉强度、抗弯强度试块,应采用25mmX55mm的Y型单铸试块:
c)中锰球墨铸铁件的冲击值试块,应采用20mm×20mm×110mm单铸冲击试块;d)对有特殊要求的铸件,需附铸试棒试块时,应在图样或订货协议中注明(其中球墨铸铁牌号后面加A,表示应为附铸试块)。
3.3.4风机铸件加工表面的硬度,一般应控制在255HB以下;非加工面不作硬度检查。对硬度高影响加工性能的铸铁,允许采用高温退火热处理。3.4金相组织
铸件金相组织检验结果只作为控制质量的参考,需方如果对金相有要求时,灰铸铁件按GB/T7216球墨铸铁件按GB/T9441,球化级别应不低于3级,球化率应大于80%:耐热件和耐蚀件参照GB/T7216GB/T944上,由供需双方商定检验项目级别及取样位置和数量等具体规定。3.5几何形状、加工余盘及尺寸公差3.5.1般规定
铸件的几何形状及尺寸应符合图样或订货时的模样及有关协议。木模应按JB/T7699的二级精度执行。工艺上未注明的起模斜度应符合附录A的规定。3.5.2铸件加工余量
3.5.2.1如图样、订货协议无特殊要求时,铸件底面和侧面加工余量应按GBT6414一RMA的H级规定执行(见附录B)。项面加工余量为对应底面的1.25倍。3.5.2.2需方应在图样上规定需要由铸造厂进行预机械加工的表面和为进行最终机械加工所需的机械加工余量。为达到预机械加工状态所需的机械加工余量或满足二次时效后再精加工的铸件的要求,加工余量为GB/T6414一RMA的H级数值的1.2~1.5倍。3.5.3未注尺寸公差
图样中没有特别注明的一般尺寸公差,则按GB/T6414的CT12等级执行,其公差值见附录C。般公差带应对称分布,即公差的一半取正值,另一半取负值。对于一些特殊情况,经设计与铸件生产单位双方同意,公差可以一部分或全部取正值或负值3.5.4风机铸件特殊部位的尺寸公差3.5.4.1铸件壁厚、筋厚、辐板厚及回流室、扩压器叶片厚度的尺寸公差,当基本尺寸小于20mm时,按GB/T6414的CT11级执行:当基本尺寸等于或大于20mm时,按GB/T6414的CT13级执行。3.5.4.2机壳、轴承体、变速箱和油泵、壳体等铸件中分面的法兰盘及流体进出口法兰盘的厚度尺寸公差,按GB/T6414的CT13级执行。3.5.4.3由于错箱偏心使带轮、轴盘等旋转类铸件产生同轴度偏差,在保证轴孔和轮缘外侧足够加工量的情况下,其轮缘内侧等非加工面对轴孔轴线的同轴度公差,应符合表1的规定(见图1)。2
最大外廓直径
公差值
≤300
表1旋转类铸件的同轴度公差
>300~500
>500~800
JB/T6887-2004
3.5.4.4机壳(见图2)娲室开口处(A面),应保证有足够的加工余量,不许留黑皮。装密封、轴衬、螺丝
JB/T6887-2004
隔板的脐环C的位置尺寸,在加工划线时,都以蜗室中线为基准,加工后须保证脐环上牙厚E不小」原尺寸的80%。为了不使脐环C位移过大,蜗室轴线在轴向的偏移量不得大于3mm。机壳、轴承座、盖、变速箱等铸件的轴线,在径向的偏移量应不大于3mm,免得造成过大的错口台阶。3.5.4.5机壳蜗室内流道尺寸(见图2)H、B的尺寸的公差,当其尺寸小于或等于120mm时,应不大于被测部位基本尺寸的土4%,当流道尺寸大于120mm时,应不大于基本尺寸的士2%,最大不超过±5mm
3.5.4.6回流室、隔板和扩压器流道内尺寸公差,应在所测部位基本尺寸的土6%内,最大不超过土5mm机壳、轴承座、变速箱、壳体、底座等铸件上的凸台(脐子)的位置度公差不得大于3mm,3.5.4.7
否则需修正。
3.5.4.8轴承座、变速箱等三开箱铸件(见图3)的全高尺寸A、内腔深度H、底面加工空刀B及与轴承侧盖接合的凸台高度C等尺寸公差,应符合表2的规定。图3
表2三开箱铸件尺寸公差
最大外廊尺寸
≤700
≥700
3.6重量
3.6.1以计算重量或供需双方共同认定的任一合格铸件的实际重量作为公称重量。±3
3.6.2订货协议无特殊要求时,铸件重量公差,应按GB/T11351MT13等级执行,其重量公差值见附录D。
3.6.3当铸件的重量公差作为验收依据时,应在图样或订货协议中注明。3.7表面质量
3.7.1机壳、隔板、扩压器等铸件流道表面粗糙度,其表面80%以上应符合GB/T6060.1的R.25其余部分符合R.50的规定:铸件的外表面粗糙度应不超过R50。如有特殊要求应在订货协议中注明3.7.2除另有规定外,铸件均以不加工状态交货。但应清理干净,修整多肉,去除芯骨、粘砂、内腔残余物及浇、冒口残余(加工面上允许有残留量,但不得大于4mm)。轴承座、变速箱内腔及机壳、回流室等铸件与流体接触部位的粘砂必须仔细清理干净。3.7.3铸件外露的非加工表面的直线度偏差,在同一铸型平面内,任意600mm长度上不大于3mm4
3.7.4,铸件非加工面(外表面)错箱值应符合表3的规定。铸件外露非加工面产生错箱后,应清铲成10°的坡玻度形状(见图4)。表3错箱值
铸件最大尺寸
≤250
>250~630
>630~1600
>16004000
>4000~6300
3.8修整
错铬处
清掉的部分免费标准bzxz.net
JB/T6887—2004
非加工面错箱值
对机壳上下两半、变速箱座和盖等两半件接合处的错口台阶,在不超过其壁厚1/5时,机械加工后应将错口处倒角60°修整。
3.9缺陷
3.9.1不允许修补的零件或部位和不允许的缺陷为:a)回流室、扩压器、叶盘上的叶片:b)轮毂、带轮、联轴器等件轴孔:c)通风机的轮毂表面、罗茨风机叶轮表面(端面除外):d)加工表面粗糙度为R1.6或小于R1.6的部位,以及金属与金属的摩擦工作面:e)机壳、变速器等件的起重吊耳或其他易发生安全事故的部位缺陷:f)储存稀油和承压铸件上,足以引起渗漏的缺陷(对局部渗漏部位可用带螺纹的塞子进行塞补):g)凡受冲击负荷和承受较大弯矩、扭矩的铸件上的裂纹类缺陷:h)轴承压盖铸件上的缩孔、缩松类缺陷。3.9.2除3.9.1以外的其他铸件存在的微小的气孔、砂眼、夹渣、缩孔和缩松等缺陷不需修补,不需要修补的缺陷具体规定如下:
a)凡不超过表4规定范围的小缺陷,不需修补。b)每处密集气孔面积不大于300mm2,其部位和范围见表4c)静止铸件、不储存稀油和非承压部件,缩松缺陷深度不得大于6mm,并不大于所在处壁厚的一半,缺陷面积不得大于该收缩区域(热节)的15%,但最大不大于@25mm。d)轮毂、带轮、半联轴器等旋转件,加工后在其轴孔表面上,距两端各为半径长度的范围内,不允许有任何缺陷:轴孔内表面的其余部分,缺陷深度不大于3mm,直径不大于轴径的1/5,两个缺陷边缘间的周向距离大于轴径时,其缺陷允许存在。5
JB/T6887-2004
铸件种类
非加工表面
静止件
运动件
加工后表面
非加工表面
加工后表面
孔眼名称
密集性气孔
密集性气孔
表4不需要修补缺陷的范围
孔径尺寸
≥104
≥10/3
离所在面边缘的距离每100cm2面上孔眼数最>8
分子表示长度,分母表示小气孔数,103表示每10mm长度内不多于3个小气孔。3.10缺陷修补方法及质盘要求
3.10.1塞补
≤6个
≤6个
≤5个
≤5个
≤2处
3.10.1.1储存稀油、承压部位的铸件上的气孔、砂眼、夹渣等缺陷,可用与母材相同的铸铁(或铬钢)螺纹塞子塞堵。其塞子直径不得大于壁厚。3.10.1.2对于1000kg以上的静止件,在加工面上的孔眼缺陷,可以用与母材相同铸铁(或铬钢)嵌人物(塞子或镶块)塞补。嵌人物尺寸不大于堵塞部位尺寸的1/5,嵌人深度为20mm~45mm(不超过堵塞处壁厚度的1/2),嵌入物边缘到所在面边缘距离不小于30mm,每个工艺面上塞补不超过2处。圆柱形塞子应满足只~只配合,镶块应满足兴的配合。n6
3.10.2焊补
3.10.2.1对风机铸件上除3.9.1规定外的其他部位,出现的气孔、砂眼、夹渣、缩孔、裂纹、冷隔、缺肉等缺陷,在不影响铸件使用性能、寿命和外观质量情况下,可按下列规定进行焊补:a)对于符合焊补范围的缺陷,应经检查允许后,方可进行修焊。b)焊前需将缺陷清铲干净,露出金属母材并铲出坡口后,按照焊补工艺方法进行施焊。施焊人员须经过铸件电气焊的专门培训,并持有其资格证书。焊补后,一般均应进行消除应力退火:对机加工中出现的缺陷,当焊补面积小及焊接应力不大时,焊后可不做退火处理。c)对加工面上缺陷,应采用铸铁热焊补法,焊前对铸件进行局部或整体预热(450℃~600℃)然后进行气焊或电焊,焊后立即盖上保温材料(如稻草灰或木炭屑):对精加工后出现的局部小缺陷,可用镍铁或镍铜铸铁电焊条进行冷焊;对非加工面上的孔洞缺陷,可采用无镍铸铁电焊条进行冷焊或半热焊(预热至400℃左右)来修补。d)铸件上的筋板和不储油、非承压部位出现裂纹、冷隔时,当缺陷长度不大于壁厚3倍时,可以焊补,焊前在其端部钻4mm~68mm止裂孔。e)对铸件上不储油和非承压件部位,出现单个透孔且孔径小于壁厚1.5倍(最大不超过35mm)时、可以焊补。
f)铸件毛坏上出现的气孔、砂眼、夹渣、缩孔等缺陷,其焊补的尺寸和数量不得大于表5的规定:缺陷的深度:对静止件不得大于壁厚的2/3,对于运动件不得大于壁厚的1/3:两缺陷距离不得小于最大缺陷尺寸的2.5倍。
g)铸件在机械加工中出现的气孔、砂眼、夹渣、缩孔等缺陷,经修补后不影响使用性能和加工性能,并符合如下规定者,允许焊补后使用;其缺陷焊补尺寸和数量不得大于表6的规定:缺陷的深度:对静止件不大于壁厚1/2,对运动件不大于壁厚的1/4:两缺陷距离不得小于最大缺陷6
尺寸的2.5倍。
铸件分类
重量kg
静止件
运动件
静止件
运动件
缺陷尺寸mm
表5毛坏铸件缺陷允许焊补的范围小件
每个面缺陷数量不多于(个)
缺陷尺寸mm
每个面缺陷数量不多于(个)
>400~1600
JB/T6887-2004
特大件
>1600~6300
表6机械加工中出现的缺陷充许焊补的范围铸件分类
重量kg
缺陷直径gmm
每个面缺陷数量不多于(个)
缺陷直径gmm
每个面缺陷数费不多于(个)
≤400
>400~1600
>1600~6300
≤100
特大件
若铸件缺陷超过3.10.2.1的有关规定,但生产单位有较高技能和可靠的焊补质量措施,且经3.10.2.2
过设计部门或需方同意后也可进行补焊修复,但需进行必要的无损探伤和渗漏试验检查。3.10.2.3焊补质量要求
a)焊缝金属应与母材熔合良好、焊缝平整、无气孔、夹渣和裂纹:b)加工后焊缝的色泽与母材相同或相近:c)对于外露加工面上的缺陷,其焊接区(包括焊缝、熔合区及热影响区)的硬度不得高于255HB,并不得影响切削加工性:
d)对于需进行泄漏试验的铸件上的缺陷,焊补后,应符合3.11的要求。3.10.3镂套
3.10.3.1、在个别情况下,铸件不重要的圆孔内表面加工后发现的气孔、缩孔、渣孔及孔径偏差等缺陷,在不影响零件质量和风机性能的条件下,可按本标推将铸件圆孔适当扩大后镶人套简。3.10.3.2镶套的技术要求:
a)套筒的最小壁厚应符合表7规定;b)套简与孔的配合应符合兴~只的要求:n6
c)套筒应用骑缝螺钉固定在铸件上。当套简受轴向力时应镶配带凸台的套筒:d)不得镶嵌偏心套筒,也不得在镶套后加工成偏心套;e)同一孔内只能镶一个套筒
表7套筒的最小壁厚
镶套内径
>80~150
>150~200
>200~500
套简的最小娶厚
JB/T6887--2004
3.10.3.3主轴孔、油箱和液压件孔、轴承压盖孔等重要部位不得镶套。3.10.4填补
铸件外露非加工面上的小缺陷(气孔、砂眼、夹渣等),在不影响铸件刚度和外观质量的前提下,可用环氧树脂专用填料或腻子填补。无精度要求的工艺加工面、覆盖加工面及不重要的固定结合面上的小缺陷,不宜焊补和塞补者也可用颜色相近、粘结固定的环氧树脂专用填补剂填补(铸件工作温度一般不宜超过90℃)。
填补前,缺陷部位应按有关规程进行锉、刮、喷砂等机械处理或采用汽油、丙酮等溶剂进行清洗如铸件需经去应力退火,则应在退火后填补。3.11泄漏试验
当产品标准或订货协议上对铸件的泄漏试验无特殊要求时,可以按3.11.1~3.11.3规定进行泄漏试验。
储存稀油的变速箱、轴承箱、油箱和工作压力小于或等于0.25MPa(表压)的机壳、泵、壳体、3.11.1
阀体等铸件应在涂底漆前(最好在退火前)进行刷涂煤油的渗漏试验:铸件壁内外表面清理干净后,将煤油均勾刷涂于试验表面的一侧(至少刷三遍),使表面得到足够的浸润,经30min后,观察另一侧,没有油渍者为合格。如果有进行填充煤油试验等特殊要求时,应在图样或订货协议上注明。3.11.2承受压力的水冷轴承流道部分和工作压力大于0.25MPa(表压)的各种机壳、泵壳体、阀体等皆应做水压试验。试验压力为其最高工作压力的1.5倍,保压30min内无渗漏。3.11.3对用于有毒或易燃气体的风机机壳等铸件,应该用一种惰性气体,加压到额定压力后(机壳最高工作压力的1.5倍),保压30min,用发泡液等检查无气体泄漏。3.12底漆
3.12.1铸件经过精整、热处理和检查合格后,应按JB/T6886中有关规定对非加工表面进行抛喷丸或滚筒简清理,达到清洁度Sa21/2级的要求。3.12.2铸件在抛喷丸处理后24h内,即应涂底漆:涂漆前铸件上的粉尘等物应用无油无水压缩空气或吸尘器清理干净。
3.12.3图样或订货协议无特殊要求时,铸件非加工面均涂刷铁红色防锈底漆。4试验方法和检验规则
4.1铸件由供方技术检查部门,按第3章技术要求进行检查和验收,需方有权对铸件进行检验。若需方到现场检查执行情况时,供方应提供一切合理的方便。4.2试样的选取方法按3.3.3执行。若铸件需热处理时,其试样与铸件采用同炉热处理。仅消除内应力时,试样可不进行热处理。
4.3铸件力学性能试验方法,灰铸铁件和RT型耐热铸件的抗拉试验、高硅耐蚀件的抗弯试验均按IB/T7945规定进行:球墨铸铁件和耐热球铁(RQT)件的抗拉试验按GB/T228的规定进行。中锰球铁件冲击试验按GB/T229进行,其洛氏硬度试验按GB/T230进行:其他各种铸铁的布氏硬度试验按GB/T231.13规定进行。直接在铸件表面上测定硬度时,应将铸件表面去除不小于2mm的厚度,并仔细修平。测定的位置应选在距铸件边缘不小于10mm的工作面上。4.4铸件的化学分析方法按GB/T223有关规定进行。化学分析试样可取自同一批铁水的试棒(块)或铸件本体,取样部位在离表层6mm以下处。4.5批量的划分:
a)由同一包铁水浇注的铸件为一个批量。b)每批量铸件的最大重量为清铲完好的2000kg铸件。如果一个铸件重量大于2000kg时,就单独成为一一个批量。
c)当连续不断地熔化大量同一牌号铁水时,每一批量最大重量不得超过2h内所浇注的铸件重量8
JB/T6887—2004
如果一种牌号的铁水熔量很大,而且在原材料固定、熔化工艺稳定的生产条件下,经供需双方协商同意,也可把若干批量合并成一组验收。d)每处理一包球墨铸铁,应把该包铁水定为一批。e)有附铸试棒(块)的铸铁,每件可单独定为一批。4.6铸件的材质验收,应按3.3规定执行。每一批量至少应取一组(三根)试样,进行有关的力学性能试验和化学成分分析。在检验时,先用一根试样进行试验,如果符合要求,即该批铸件在材质上为合格:若试验结果达不到要求,允许从同一批的试样中另取两根进行复验,其都达到要求时,则该批铸件材质仍为合格。
4.7铸件表面、外观用目测方法逐件进行检验。首件和重要铸件,应按3.5逐件进行尺寸和几何形状检查:一般铸件及用保证尺寸稳定性方法生产出来的铸件可以抽查。件表面粗糙度采用GB/T15056规定进行检验,若未达到要求时,允许进行打磨返修。4.8焊补质量的检验:
a)应逐个检验缺陷焊补处的准备情况,应按3.10.2.1b)和3.10.2.ld)要求执行b)采用的焊补方法及焊条,应按3.10.2.1c)有关规定执行。c)缺陷焊补后,应逐个检验各焊接区的质量,符合3.10.2.3的要求。用锤击式或肖氏硬度计检验硬度。
d)焊补的缺陷的数量、尺寸、面积等,不得超过本标准的规定。e)铸件上的裂纹类缺陷,焊补后应采用有效方法检验。4.9根据图样、技术文件或订货协议上的规定需作泄漏试验的铸件,按3.11要求逐件进行试验检查,如果试件试验不合格、允许返修,返修后应重新作泄漏试验。5标志与证明书
5.1经检查合格的铸件,应有生产技术检查部门的标志,标志可以是打印的或油漆的(一般应选用白色油漆标注合格品)。
5.2铸件交库或出厂时,应有符合本标准的产品合格证,其中包括:a)供方名称:
b)铸件名称:
c)铸件图号、材质牌号有必要的检验结果:d)制造日期(或编号)或生产批号。6拒收
6.1铸件有外部或内部缺陷,而这些缺陷对根据铸造材质和铸件类型所测得的加工性能和使用性能有明显的损害时,应予报废拒收。6.2用户必须给生产单位以确认报废拒收合理性的机会,报废拒收的铸件在办理手续之前,应尽可能由供方保存。
小提示:此标准内容仅展示完整标准里的部分截取内容,若需要完整标准请到上方自行免费下载完整标准文档。
中华人民共和国机械行业标准
JB/T6887--2004
代替JB/T6887-1993
JB/T68891993
风机用铸铁件
技术条件
Technical condition of cast iron for fans blower and compressors2004-10-20发布
2005-04-01实施
中华人民共和国国家发展和改革委员会发布前言,
1范围
2规范性引用文件,
3技术要求
3.1材料..
3.2生产方法和热处理
3.3力学性能和化学成分。
3.4金相组织..
几何形状、加工余量及尺寸公差3.6
表面质量
修整、
缺陷修补方法及质量要求
泄漏试验,
3.12底漆。
4试验方法和检验规则
5标志与证明书
附录A(规范性附录)铸件木模样起模斜度(JB/T5105)附录B(规范性附录)铸件机械加工余量(RMA)(GB/T6414)附录C(规范性附录)铸件尺寸公差数值(GB/T6414)附录D(规范性附录)铸件重量公差等级数值(GB/T11351)表旋转类铸件的同轴度公差
表2三开箱铸件尺寸公差
表.错箱值.
表4不需要修补缺陷的范围
表5毛环铸件缺陷允许焊补的范围表6机械加工中出现的缺陷允许焊补的范围表7套简的最小壁厚
表A.1铸件木模样起模斜度
铸件机械加工余量(RMA)
铸件尺寸公差数值
铸件重量公差等级数值
JB/T6887—2004
本标准是对JB/T6887—1993《风机用铸铁件技术条件》的修订。JB/T6887—2004
本标准在规范性引用文件上做了修改,并增加了一些有关内容。在技术内容和编写格式上,对原标准进行了必要的修订。
本标准与JB/T6887—1993相比,主要变化如下:将JB/T68891993《风机用铸铁件缺陷修补技术条件》主要内容并人本标准。-对铸件尺寸公差与机械加工余量的等级按照GB/T6414一1999重新进行了规定.质量等级有所提高。
铸件重量公差规定按GB/T11351一1989中MT13级执行,不采用惟一的7%重量偏差值。对风机铸件流道和外表面质量作了新的较高的要求,以适应市场对产品质量的要求在缺陷焊补范围中,对铸件分类作了新的划分,其中重量大于6300kg为特大件:满足风机铸件向大型化发展的需要。
由于振动时效新工艺的成熟,本标准首次明确将其与退火消除内应力方法等同有效。一对轴承箱、变速箱等铸件渗煤油试验和铸件涂底漆都作了进一步具体规定,便于实施。本标准对原铸铁件焊补工艺在内容上作了较大删减。附录B按照GBT6414--1999列出新的机械加工余量等级值,并新增附录D“铸件重量公差等级值\。
本标准的附录A、附录B、附录C、附录D都是规范性附录。本标准由中国机械工业联合会提出。本标准由全国风机标准化技术委员会归口。本标准由陕西鼓风机(集团)有限公司,沈阳鼓风机(集团)有限公司参加起草。本标准主要起草人:王奎旺、宋里里。本标准所代替标准的历次版本发布情况为:JB/T6887—1993:
JB/T6889—1993.
1范围
风机用铸铁件技术条件
本标准规定了风机用铸铁件的技术要求、试验方法与验收规则。JB/T6887--2004
本标准适用于透平式通风机、鼓风机、压缩机、膨胀机及罗茨、叶氏鼓风机所使用的灰铸铁、球墨铸铁和中锰抗磨球墨铸铁、高硅耐蚀铸铁、耐热铸铁等合金铸铁的铸铁件(以下简称铸件)。2规范性引用文件
下列文件中的条款通过本标准的引用而成为本标准的条款。凡是注日期的引用文件,其随后所有的修改单(不包括勘误的内容)或修订版均不适用于本标准,然而,鼓励根据本标准达成协议的各方研究是否可使用这些文件的最新版本。凡是不注日期的引用文件,其最新版本适用于本标准。GB/T223.3~78钢铁及合金化学分析方法GB/T228金属材料室温拉伸试验法(GB/T228—2002,eqvISO6892:1998(E))GB/T229
金属夏比缺口冲击试验方法(GB/T229--1994,eqvISO148:1983)金属洛氏硬度试验方法(GB/T230—1991,neqIS06508:1986)GB/T230
GB/T231.13金属布氏硬度试验方法GB/T1348
GB/T3180
球墨铸铁件
中锰抗磨球墨铸铁件技术条件
GB/T6060.1
GB/T6414
GB/T7216
GB/T8491
GB/T9437
表面粗糙度比较样块铸造表面(GB/T6060.1--1997,eqvISO2632-3:1979)铸件尺寸公差与机械加工余量(GB/T6414—1999,eqvISO8062:1994)灰铸铁金相(neqISO945:1975)高硅耐蚀铸铁件
耐热铸铁件
灰铸铁件
GB/T9439.
GB/T9441
GB/T11351
GB/T15056
JB/T5926
JB/T6886
JB/T7699
球墨铸铁金相检验
铸件重量公差
铸造表面粗糙度评定方法
振动时效工艺参数选择及技术要求通风机涂装技术条件
铸造用木制模样和芯盒技术条件JB/T7945灰铸铁力学性能试验方法3技术要求
3.1材料
本标准的各类铸铁件应使用符合GB/T9439、GB/T1348、GB/T9437、GB/T8491、GB/T3180规定的材料牌号。
3.2生产方法和热处理
铸件均应经退火处理或振动时效方法消除内应力。铸件的生产方法和热处理由供方自行决定,但必须达到本标准规定的牌号及有关技术性能。作调整力学性能和加工性能的重复热处理不能超过二次。若采用振动时效时,应严格按JB/T5926规定执行。对热处理和消除内应力方法有特殊要求时,应在图样JB/T6887—2004
或订货协议上注明。
3.3力学性能和化学成分
3.3.1铸件的力学性能和化学成分数值应符合3.1的规定。3.3.2灰铸铁件以抗拉强度作为验收依据:球墨铸铁件以抗拉强度和延伸率为验收依据:中锰抗磨球墨铸铁件以冲击值和硬度为验收依据:耐蚀铸件以化学成分和室温抗拉强度为验收依据。如有其他特殊要求时,应在订货协议中注明。3.3.3铸件的试棒试块:
a)灰铸铁件、高硅耐蚀铸铁件、RT型耐热铸铁件的抗拉强度、抗弯强度试棒,应采用砂型中立浇的@30mm单铸试棒:
b)球墨铸铁件、RQT型耐热铸铁件的抗拉强度、抗弯强度试块,应采用25mmX55mm的Y型单铸试块:
c)中锰球墨铸铁件的冲击值试块,应采用20mm×20mm×110mm单铸冲击试块;d)对有特殊要求的铸件,需附铸试棒试块时,应在图样或订货协议中注明(其中球墨铸铁牌号后面加A,表示应为附铸试块)。
3.3.4风机铸件加工表面的硬度,一般应控制在255HB以下;非加工面不作硬度检查。对硬度高影响加工性能的铸铁,允许采用高温退火热处理。3.4金相组织
铸件金相组织检验结果只作为控制质量的参考,需方如果对金相有要求时,灰铸铁件按GB/T7216球墨铸铁件按GB/T9441,球化级别应不低于3级,球化率应大于80%:耐热件和耐蚀件参照GB/T7216GB/T944上,由供需双方商定检验项目级别及取样位置和数量等具体规定。3.5几何形状、加工余盘及尺寸公差3.5.1般规定
铸件的几何形状及尺寸应符合图样或订货时的模样及有关协议。木模应按JB/T7699的二级精度执行。工艺上未注明的起模斜度应符合附录A的规定。3.5.2铸件加工余量
3.5.2.1如图样、订货协议无特殊要求时,铸件底面和侧面加工余量应按GBT6414一RMA的H级规定执行(见附录B)。项面加工余量为对应底面的1.25倍。3.5.2.2需方应在图样上规定需要由铸造厂进行预机械加工的表面和为进行最终机械加工所需的机械加工余量。为达到预机械加工状态所需的机械加工余量或满足二次时效后再精加工的铸件的要求,加工余量为GB/T6414一RMA的H级数值的1.2~1.5倍。3.5.3未注尺寸公差
图样中没有特别注明的一般尺寸公差,则按GB/T6414的CT12等级执行,其公差值见附录C。般公差带应对称分布,即公差的一半取正值,另一半取负值。对于一些特殊情况,经设计与铸件生产单位双方同意,公差可以一部分或全部取正值或负值3.5.4风机铸件特殊部位的尺寸公差3.5.4.1铸件壁厚、筋厚、辐板厚及回流室、扩压器叶片厚度的尺寸公差,当基本尺寸小于20mm时,按GB/T6414的CT11级执行:当基本尺寸等于或大于20mm时,按GB/T6414的CT13级执行。3.5.4.2机壳、轴承体、变速箱和油泵、壳体等铸件中分面的法兰盘及流体进出口法兰盘的厚度尺寸公差,按GB/T6414的CT13级执行。3.5.4.3由于错箱偏心使带轮、轴盘等旋转类铸件产生同轴度偏差,在保证轴孔和轮缘外侧足够加工量的情况下,其轮缘内侧等非加工面对轴孔轴线的同轴度公差,应符合表1的规定(见图1)。2
最大外廓直径
公差值
≤300
表1旋转类铸件的同轴度公差
>300~500
>500~800
JB/T6887-2004
3.5.4.4机壳(见图2)娲室开口处(A面),应保证有足够的加工余量,不许留黑皮。装密封、轴衬、螺丝
JB/T6887-2004
隔板的脐环C的位置尺寸,在加工划线时,都以蜗室中线为基准,加工后须保证脐环上牙厚E不小」原尺寸的80%。为了不使脐环C位移过大,蜗室轴线在轴向的偏移量不得大于3mm。机壳、轴承座、盖、变速箱等铸件的轴线,在径向的偏移量应不大于3mm,免得造成过大的错口台阶。3.5.4.5机壳蜗室内流道尺寸(见图2)H、B的尺寸的公差,当其尺寸小于或等于120mm时,应不大于被测部位基本尺寸的土4%,当流道尺寸大于120mm时,应不大于基本尺寸的士2%,最大不超过±5mm
3.5.4.6回流室、隔板和扩压器流道内尺寸公差,应在所测部位基本尺寸的土6%内,最大不超过土5mm机壳、轴承座、变速箱、壳体、底座等铸件上的凸台(脐子)的位置度公差不得大于3mm,3.5.4.7
否则需修正。
3.5.4.8轴承座、变速箱等三开箱铸件(见图3)的全高尺寸A、内腔深度H、底面加工空刀B及与轴承侧盖接合的凸台高度C等尺寸公差,应符合表2的规定。图3
表2三开箱铸件尺寸公差
最大外廊尺寸
≤700
≥700
3.6重量
3.6.1以计算重量或供需双方共同认定的任一合格铸件的实际重量作为公称重量。±3
3.6.2订货协议无特殊要求时,铸件重量公差,应按GB/T11351MT13等级执行,其重量公差值见附录D。
3.6.3当铸件的重量公差作为验收依据时,应在图样或订货协议中注明。3.7表面质量
3.7.1机壳、隔板、扩压器等铸件流道表面粗糙度,其表面80%以上应符合GB/T6060.1的R.25其余部分符合R.50的规定:铸件的外表面粗糙度应不超过R50。如有特殊要求应在订货协议中注明3.7.2除另有规定外,铸件均以不加工状态交货。但应清理干净,修整多肉,去除芯骨、粘砂、内腔残余物及浇、冒口残余(加工面上允许有残留量,但不得大于4mm)。轴承座、变速箱内腔及机壳、回流室等铸件与流体接触部位的粘砂必须仔细清理干净。3.7.3铸件外露的非加工表面的直线度偏差,在同一铸型平面内,任意600mm长度上不大于3mm4
3.7.4,铸件非加工面(外表面)错箱值应符合表3的规定。铸件外露非加工面产生错箱后,应清铲成10°的坡玻度形状(见图4)。表3错箱值
铸件最大尺寸
≤250
>250~630
>630~1600
>16004000
>4000~6300
3.8修整
错铬处
清掉的部分免费标准bzxz.net
JB/T6887—2004
非加工面错箱值
对机壳上下两半、变速箱座和盖等两半件接合处的错口台阶,在不超过其壁厚1/5时,机械加工后应将错口处倒角60°修整。
3.9缺陷
3.9.1不允许修补的零件或部位和不允许的缺陷为:a)回流室、扩压器、叶盘上的叶片:b)轮毂、带轮、联轴器等件轴孔:c)通风机的轮毂表面、罗茨风机叶轮表面(端面除外):d)加工表面粗糙度为R1.6或小于R1.6的部位,以及金属与金属的摩擦工作面:e)机壳、变速器等件的起重吊耳或其他易发生安全事故的部位缺陷:f)储存稀油和承压铸件上,足以引起渗漏的缺陷(对局部渗漏部位可用带螺纹的塞子进行塞补):g)凡受冲击负荷和承受较大弯矩、扭矩的铸件上的裂纹类缺陷:h)轴承压盖铸件上的缩孔、缩松类缺陷。3.9.2除3.9.1以外的其他铸件存在的微小的气孔、砂眼、夹渣、缩孔和缩松等缺陷不需修补,不需要修补的缺陷具体规定如下:
a)凡不超过表4规定范围的小缺陷,不需修补。b)每处密集气孔面积不大于300mm2,其部位和范围见表4c)静止铸件、不储存稀油和非承压部件,缩松缺陷深度不得大于6mm,并不大于所在处壁厚的一半,缺陷面积不得大于该收缩区域(热节)的15%,但最大不大于@25mm。d)轮毂、带轮、半联轴器等旋转件,加工后在其轴孔表面上,距两端各为半径长度的范围内,不允许有任何缺陷:轴孔内表面的其余部分,缺陷深度不大于3mm,直径不大于轴径的1/5,两个缺陷边缘间的周向距离大于轴径时,其缺陷允许存在。5
JB/T6887-2004
铸件种类
非加工表面
静止件
运动件
加工后表面
非加工表面
加工后表面
孔眼名称
密集性气孔
密集性气孔
表4不需要修补缺陷的范围
孔径尺寸
≥104
≥10/3
离所在面边缘的距离每100cm2面上孔眼数最>8
分子表示长度,分母表示小气孔数,103表示每10mm长度内不多于3个小气孔。3.10缺陷修补方法及质盘要求
3.10.1塞补
≤6个
≤6个
≤5个
≤5个
≤2处
3.10.1.1储存稀油、承压部位的铸件上的气孔、砂眼、夹渣等缺陷,可用与母材相同的铸铁(或铬钢)螺纹塞子塞堵。其塞子直径不得大于壁厚。3.10.1.2对于1000kg以上的静止件,在加工面上的孔眼缺陷,可以用与母材相同铸铁(或铬钢)嵌人物(塞子或镶块)塞补。嵌人物尺寸不大于堵塞部位尺寸的1/5,嵌人深度为20mm~45mm(不超过堵塞处壁厚度的1/2),嵌入物边缘到所在面边缘距离不小于30mm,每个工艺面上塞补不超过2处。圆柱形塞子应满足只~只配合,镶块应满足兴的配合。n6
3.10.2焊补
3.10.2.1对风机铸件上除3.9.1规定外的其他部位,出现的气孔、砂眼、夹渣、缩孔、裂纹、冷隔、缺肉等缺陷,在不影响铸件使用性能、寿命和外观质量情况下,可按下列规定进行焊补:a)对于符合焊补范围的缺陷,应经检查允许后,方可进行修焊。b)焊前需将缺陷清铲干净,露出金属母材并铲出坡口后,按照焊补工艺方法进行施焊。施焊人员须经过铸件电气焊的专门培训,并持有其资格证书。焊补后,一般均应进行消除应力退火:对机加工中出现的缺陷,当焊补面积小及焊接应力不大时,焊后可不做退火处理。c)对加工面上缺陷,应采用铸铁热焊补法,焊前对铸件进行局部或整体预热(450℃~600℃)然后进行气焊或电焊,焊后立即盖上保温材料(如稻草灰或木炭屑):对精加工后出现的局部小缺陷,可用镍铁或镍铜铸铁电焊条进行冷焊;对非加工面上的孔洞缺陷,可采用无镍铸铁电焊条进行冷焊或半热焊(预热至400℃左右)来修补。d)铸件上的筋板和不储油、非承压部位出现裂纹、冷隔时,当缺陷长度不大于壁厚3倍时,可以焊补,焊前在其端部钻4mm~68mm止裂孔。e)对铸件上不储油和非承压件部位,出现单个透孔且孔径小于壁厚1.5倍(最大不超过35mm)时、可以焊补。
f)铸件毛坏上出现的气孔、砂眼、夹渣、缩孔等缺陷,其焊补的尺寸和数量不得大于表5的规定:缺陷的深度:对静止件不得大于壁厚的2/3,对于运动件不得大于壁厚的1/3:两缺陷距离不得小于最大缺陷尺寸的2.5倍。
g)铸件在机械加工中出现的气孔、砂眼、夹渣、缩孔等缺陷,经修补后不影响使用性能和加工性能,并符合如下规定者,允许焊补后使用;其缺陷焊补尺寸和数量不得大于表6的规定:缺陷的深度:对静止件不大于壁厚1/2,对运动件不大于壁厚的1/4:两缺陷距离不得小于最大缺陷6
尺寸的2.5倍。
铸件分类
重量kg
静止件
运动件
静止件
运动件
缺陷尺寸mm
表5毛坏铸件缺陷允许焊补的范围小件
每个面缺陷数量不多于(个)
缺陷尺寸mm
每个面缺陷数量不多于(个)
>400~1600
JB/T6887-2004
特大件
>1600~6300
表6机械加工中出现的缺陷充许焊补的范围铸件分类
重量kg
缺陷直径gmm
每个面缺陷数量不多于(个)
缺陷直径gmm
每个面缺陷数费不多于(个)
≤400
>400~1600
>1600~6300
≤100
特大件
若铸件缺陷超过3.10.2.1的有关规定,但生产单位有较高技能和可靠的焊补质量措施,且经3.10.2.2
过设计部门或需方同意后也可进行补焊修复,但需进行必要的无损探伤和渗漏试验检查。3.10.2.3焊补质量要求
a)焊缝金属应与母材熔合良好、焊缝平整、无气孔、夹渣和裂纹:b)加工后焊缝的色泽与母材相同或相近:c)对于外露加工面上的缺陷,其焊接区(包括焊缝、熔合区及热影响区)的硬度不得高于255HB,并不得影响切削加工性:
d)对于需进行泄漏试验的铸件上的缺陷,焊补后,应符合3.11的要求。3.10.3镂套
3.10.3.1、在个别情况下,铸件不重要的圆孔内表面加工后发现的气孔、缩孔、渣孔及孔径偏差等缺陷,在不影响零件质量和风机性能的条件下,可按本标推将铸件圆孔适当扩大后镶人套简。3.10.3.2镶套的技术要求:
a)套筒的最小壁厚应符合表7规定;b)套简与孔的配合应符合兴~只的要求:n6
c)套筒应用骑缝螺钉固定在铸件上。当套简受轴向力时应镶配带凸台的套筒:d)不得镶嵌偏心套筒,也不得在镶套后加工成偏心套;e)同一孔内只能镶一个套筒
表7套筒的最小壁厚
镶套内径
>80~150
>150~200
>200~500
套简的最小娶厚
JB/T6887--2004
3.10.3.3主轴孔、油箱和液压件孔、轴承压盖孔等重要部位不得镶套。3.10.4填补
铸件外露非加工面上的小缺陷(气孔、砂眼、夹渣等),在不影响铸件刚度和外观质量的前提下,可用环氧树脂专用填料或腻子填补。无精度要求的工艺加工面、覆盖加工面及不重要的固定结合面上的小缺陷,不宜焊补和塞补者也可用颜色相近、粘结固定的环氧树脂专用填补剂填补(铸件工作温度一般不宜超过90℃)。
填补前,缺陷部位应按有关规程进行锉、刮、喷砂等机械处理或采用汽油、丙酮等溶剂进行清洗如铸件需经去应力退火,则应在退火后填补。3.11泄漏试验
当产品标准或订货协议上对铸件的泄漏试验无特殊要求时,可以按3.11.1~3.11.3规定进行泄漏试验。
储存稀油的变速箱、轴承箱、油箱和工作压力小于或等于0.25MPa(表压)的机壳、泵、壳体、3.11.1
阀体等铸件应在涂底漆前(最好在退火前)进行刷涂煤油的渗漏试验:铸件壁内外表面清理干净后,将煤油均勾刷涂于试验表面的一侧(至少刷三遍),使表面得到足够的浸润,经30min后,观察另一侧,没有油渍者为合格。如果有进行填充煤油试验等特殊要求时,应在图样或订货协议上注明。3.11.2承受压力的水冷轴承流道部分和工作压力大于0.25MPa(表压)的各种机壳、泵壳体、阀体等皆应做水压试验。试验压力为其最高工作压力的1.5倍,保压30min内无渗漏。3.11.3对用于有毒或易燃气体的风机机壳等铸件,应该用一种惰性气体,加压到额定压力后(机壳最高工作压力的1.5倍),保压30min,用发泡液等检查无气体泄漏。3.12底漆
3.12.1铸件经过精整、热处理和检查合格后,应按JB/T6886中有关规定对非加工表面进行抛喷丸或滚筒简清理,达到清洁度Sa21/2级的要求。3.12.2铸件在抛喷丸处理后24h内,即应涂底漆:涂漆前铸件上的粉尘等物应用无油无水压缩空气或吸尘器清理干净。
3.12.3图样或订货协议无特殊要求时,铸件非加工面均涂刷铁红色防锈底漆。4试验方法和检验规则
4.1铸件由供方技术检查部门,按第3章技术要求进行检查和验收,需方有权对铸件进行检验。若需方到现场检查执行情况时,供方应提供一切合理的方便。4.2试样的选取方法按3.3.3执行。若铸件需热处理时,其试样与铸件采用同炉热处理。仅消除内应力时,试样可不进行热处理。
4.3铸件力学性能试验方法,灰铸铁件和RT型耐热铸件的抗拉试验、高硅耐蚀件的抗弯试验均按IB/T7945规定进行:球墨铸铁件和耐热球铁(RQT)件的抗拉试验按GB/T228的规定进行。中锰球铁件冲击试验按GB/T229进行,其洛氏硬度试验按GB/T230进行:其他各种铸铁的布氏硬度试验按GB/T231.13规定进行。直接在铸件表面上测定硬度时,应将铸件表面去除不小于2mm的厚度,并仔细修平。测定的位置应选在距铸件边缘不小于10mm的工作面上。4.4铸件的化学分析方法按GB/T223有关规定进行。化学分析试样可取自同一批铁水的试棒(块)或铸件本体,取样部位在离表层6mm以下处。4.5批量的划分:
a)由同一包铁水浇注的铸件为一个批量。b)每批量铸件的最大重量为清铲完好的2000kg铸件。如果一个铸件重量大于2000kg时,就单独成为一一个批量。
c)当连续不断地熔化大量同一牌号铁水时,每一批量最大重量不得超过2h内所浇注的铸件重量8
JB/T6887—2004
如果一种牌号的铁水熔量很大,而且在原材料固定、熔化工艺稳定的生产条件下,经供需双方协商同意,也可把若干批量合并成一组验收。d)每处理一包球墨铸铁,应把该包铁水定为一批。e)有附铸试棒(块)的铸铁,每件可单独定为一批。4.6铸件的材质验收,应按3.3规定执行。每一批量至少应取一组(三根)试样,进行有关的力学性能试验和化学成分分析。在检验时,先用一根试样进行试验,如果符合要求,即该批铸件在材质上为合格:若试验结果达不到要求,允许从同一批的试样中另取两根进行复验,其都达到要求时,则该批铸件材质仍为合格。
4.7铸件表面、外观用目测方法逐件进行检验。首件和重要铸件,应按3.5逐件进行尺寸和几何形状检查:一般铸件及用保证尺寸稳定性方法生产出来的铸件可以抽查。件表面粗糙度采用GB/T15056规定进行检验,若未达到要求时,允许进行打磨返修。4.8焊补质量的检验:
a)应逐个检验缺陷焊补处的准备情况,应按3.10.2.1b)和3.10.2.ld)要求执行b)采用的焊补方法及焊条,应按3.10.2.1c)有关规定执行。c)缺陷焊补后,应逐个检验各焊接区的质量,符合3.10.2.3的要求。用锤击式或肖氏硬度计检验硬度。
d)焊补的缺陷的数量、尺寸、面积等,不得超过本标准的规定。e)铸件上的裂纹类缺陷,焊补后应采用有效方法检验。4.9根据图样、技术文件或订货协议上的规定需作泄漏试验的铸件,按3.11要求逐件进行试验检查,如果试件试验不合格、允许返修,返修后应重新作泄漏试验。5标志与证明书
5.1经检查合格的铸件,应有生产技术检查部门的标志,标志可以是打印的或油漆的(一般应选用白色油漆标注合格品)。
5.2铸件交库或出厂时,应有符合本标准的产品合格证,其中包括:a)供方名称:
b)铸件名称:
c)铸件图号、材质牌号有必要的检验结果:d)制造日期(或编号)或生产批号。6拒收
6.1铸件有外部或内部缺陷,而这些缺陷对根据铸造材质和铸件类型所测得的加工性能和使用性能有明显的损害时,应予报废拒收。6.2用户必须给生产单位以确认报废拒收合理性的机会,报废拒收的铸件在办理手续之前,应尽可能由供方保存。
小提示:此标准内容仅展示完整标准里的部分截取内容,若需要完整标准请到上方自行免费下载完整标准文档。

标准图片预览:
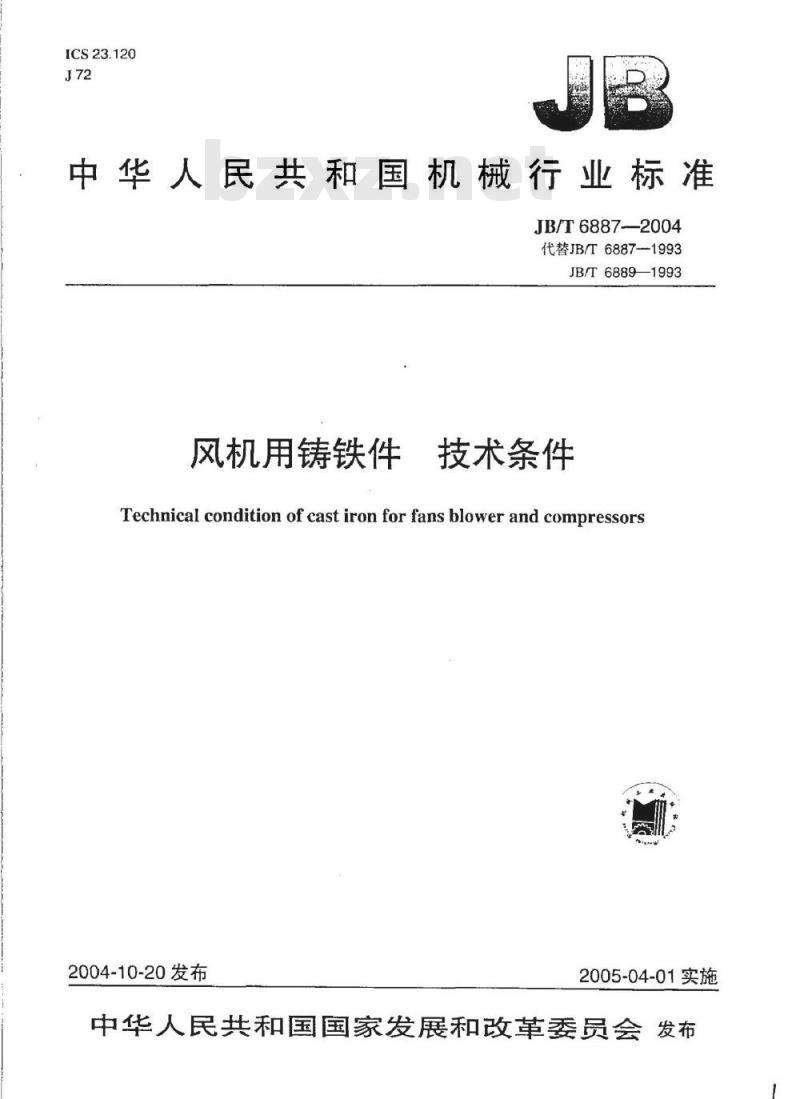
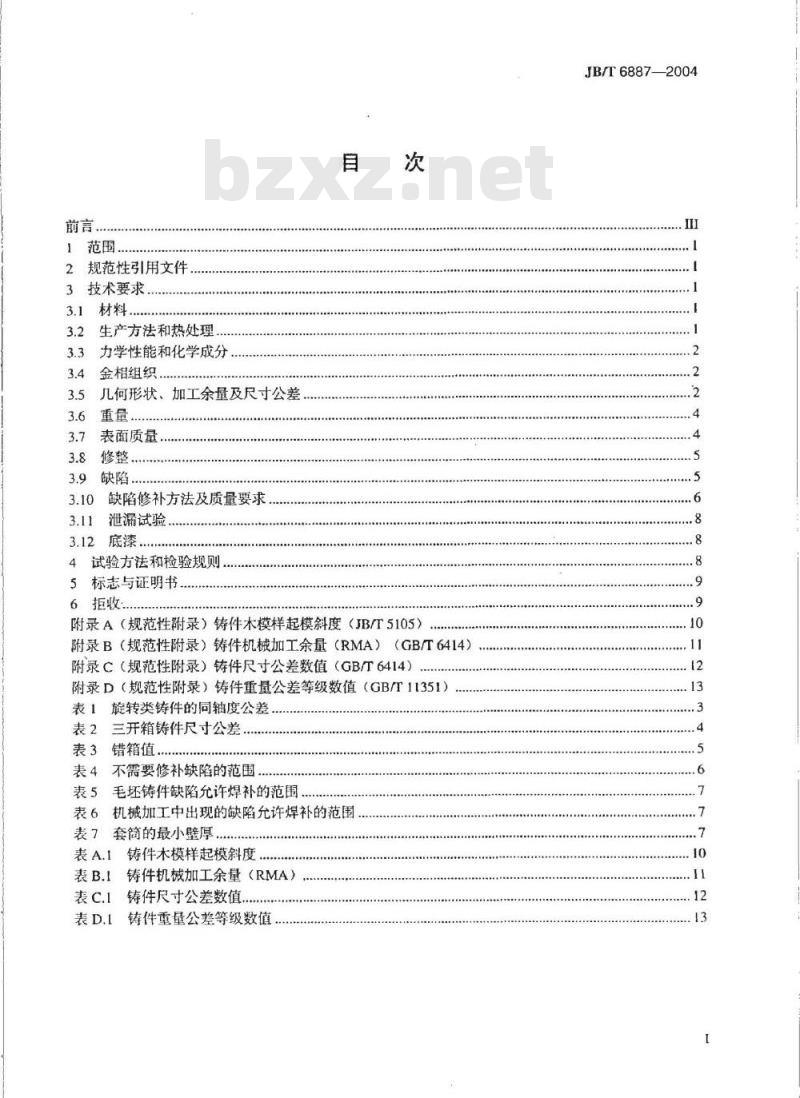
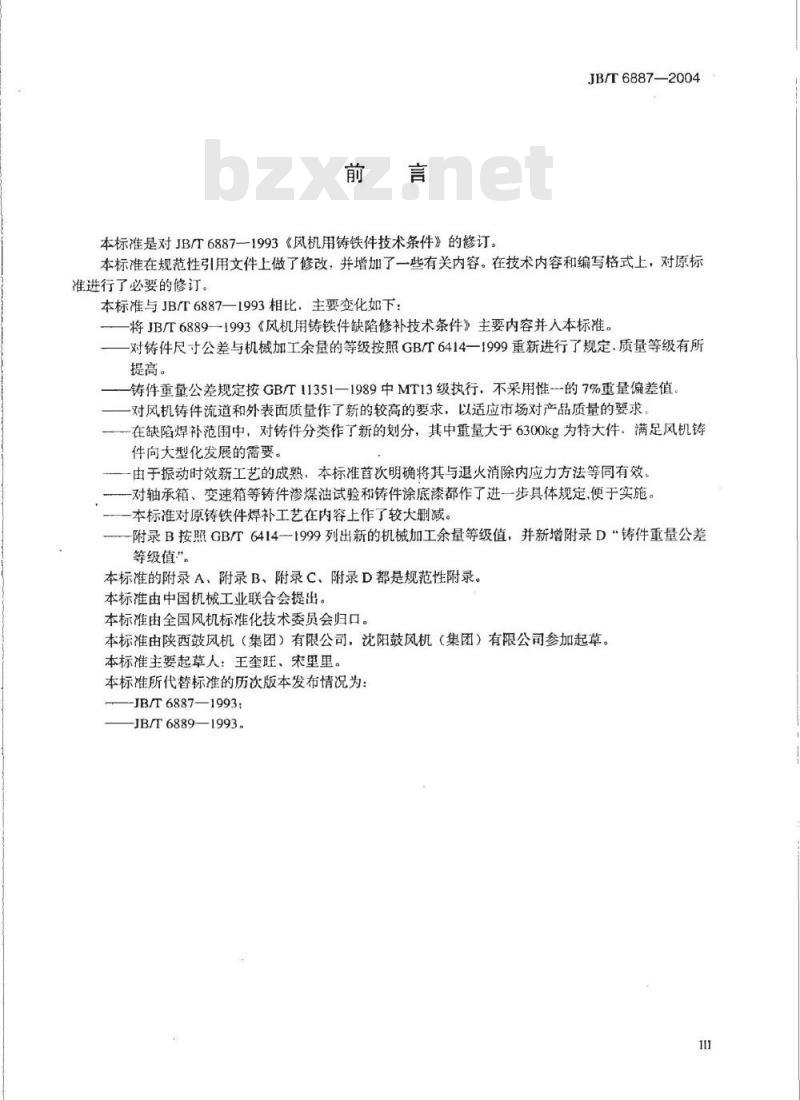
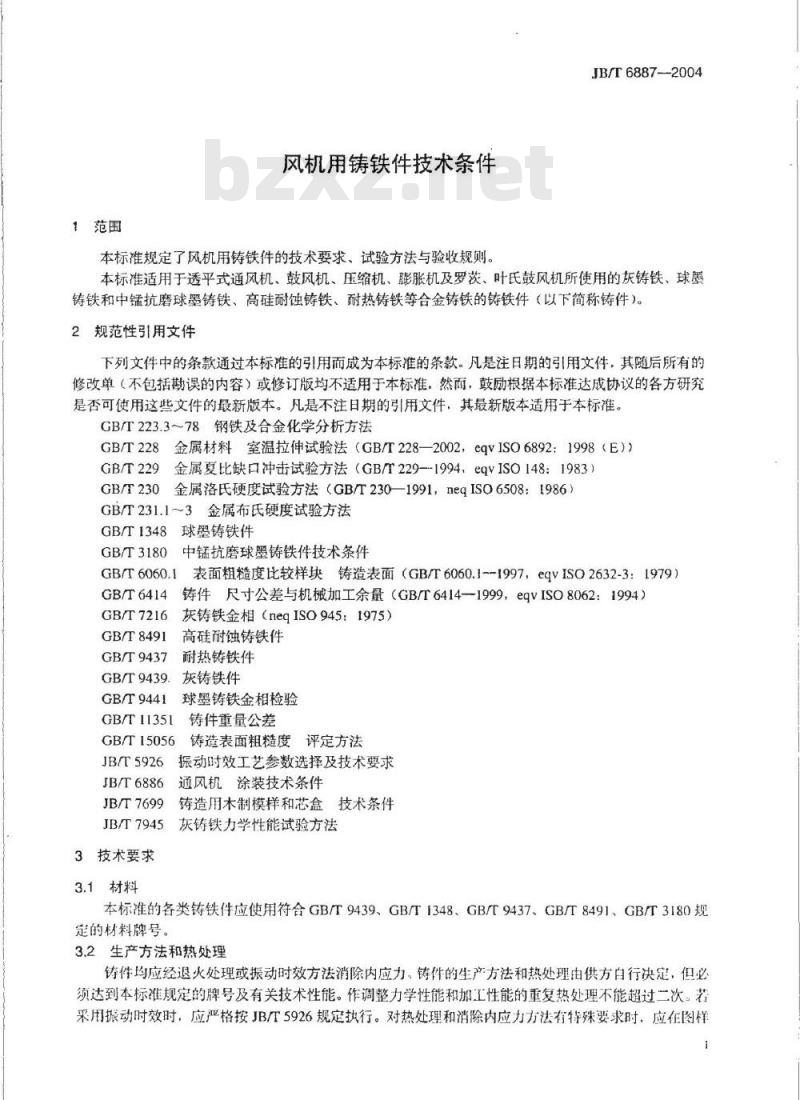
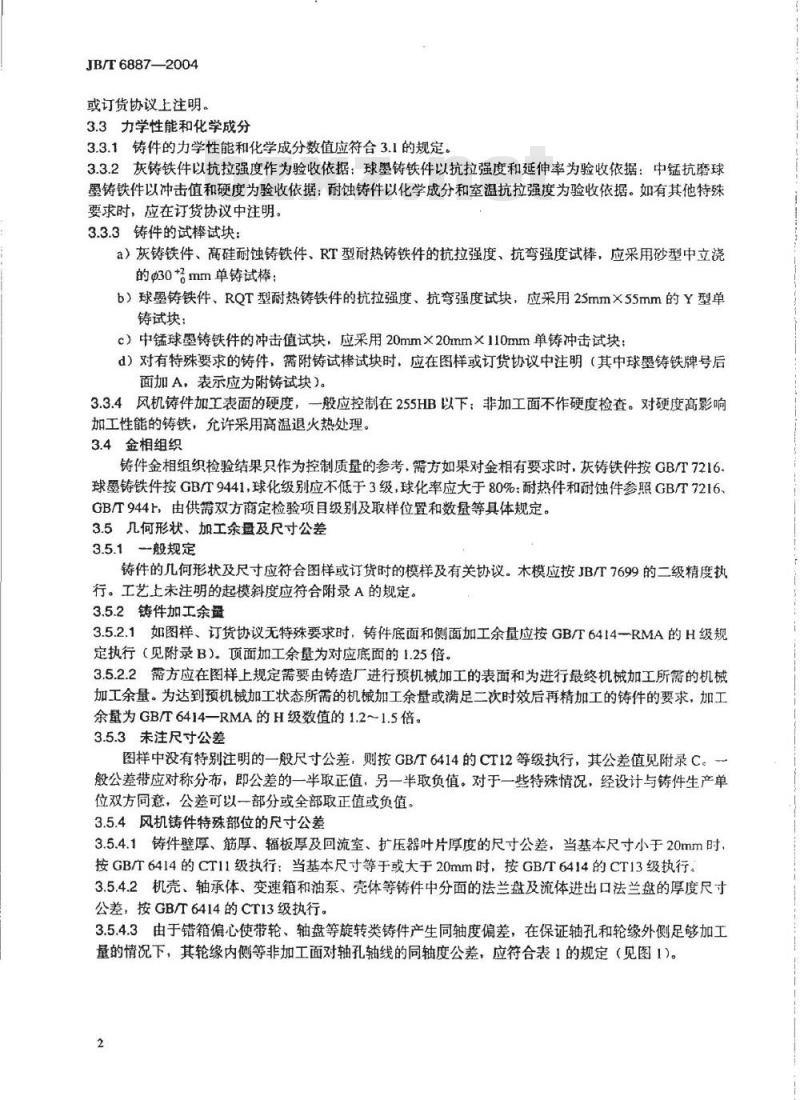
- 其它标准
- 热门标准
- 机械行业标准(JB)
- JB/T10725-2007 天然金刚石车刀
- JB/T10723-2007 焊接聚晶金刚石或立方氮化硼镗刀
- JB/T10216-2013 电控配电用电缆桥架
- JB/T10565-2006 工业过程测量和控制系统用动圈式指示仪性能评定方法
- JB/T10767-2007 装载机铜基湿式粉末冶金摩擦片 技术条件
- JB/T8467-2014 锻钢件超声检测
- JB/T9313-1999 光学仪器特种细牙螺纹
- JB8589-1997 DZ 20系列塑料外壳式断路器
- JB/T6446-2004 真空阀门
- JB/T5000.15-2007 重型机械通用技术条件 第15部分:锻钢件无损探伤
- JB/T8935-2014 工艺流程用压缩机安全要求
- JB/T11338-2012 微型阀控式铅酸蓄电池
- JB/T4736-2002 补强圈钢制压力容器用封头
- JB/T4746-2002 钢制压力容器用封头
- JB/T6502-1993 NGW行星齿轮减速器
- 行业新闻
请牢记:“bzxz.net”即是“标准下载”四个汉字汉语拼音首字母与国际顶级域名“.net”的组合。 ©2009 标准下载网 www.bzxz.net 本站邮件:bzxznet@163.com
网站备案号:湘ICP备2023016450号-1
网站备案号:湘ICP备2023016450号-1