- 您的位置:
- 标准下载网 >>
- 标准分类 >>
- 国家标准(GB) >>
- GB 10869-1989 电站调节阀技术条件
标准号:
GB 10869-1989
标准名称:
电站调节阀技术条件
标准类别:
国家标准(GB)
标准状态:
已作废-
发布日期:
1989-03-31 -
实施日期:
1990-01-01 -
作废日期:
2008-07-01 出版语种:
简体中文下载格式:
.rar.pdf下载大小:
314.89 KB
替代情况:
被GB/T 10869-2008代替

部分标准内容:
中华人民共和国国家标准
电站调节阀技术条件
Specifications of control valves for fossil power stations主题内容与适用范围
本标准规定了电站调节阀的性能要求及其试验、检验方法。本标准适用于火力发电站用的调节阀。引用标准
GB1048管子与管路附件的公称压力和试验压力GB4213
、气动调节阀通用技术条件
GB5677铸钢件射线照相及底片等级分类方法JB106
阀门标志和识别涂漆
JB1615
JB2640
JB3595
JB4018
3术语
锅炉油漆和包装技术条件
锅炉管道附件承压铸钢件技术条件电站阀门制造技术条件
电站阀门型号编制方法
3.1基本误差 intrinsic error
调节阀的实际上升、下降特性曲线与规定的特性曲线之间的最大偏差。3.2回差hysteresis error
同--输入信号上升和下降的两相应行程值间的最大差值。3. 3 死区 dead band
GB 10869-89
输入信号正、反方向的变化不致引起阀杆行程有任何可察觉变化的有限区间。3.4行程travel
为改变流体的流量,阀内组件从关闭位置标起的线位移或角位移。3.5额定行程rated travel
规定全开位置上的行程。
3.6相对行程 relative travel
某给定开度上的行程与额定行程之比。3.7额定容量 rated valve capacity在规定试验压力条件下,试验流体通过调节阀额定行程时的流量。3.8渗漏量leakage
在规定实验条件下,实验流体通过调节阀处于关闭位置时的流量。3.9流量系数 flow coefficient中华人民共和国机械电子工业部1989-03-21批准1990-01-01实施
GB 10869-89
在规定条件下,即阀的两端压差为0.1MPa、介质密度为1g/cm\时,某给定行程时流经调节阀以m3/h或t/h计的流量数。
3.10额定流量系数Cv rated flow coefficient额定行程时的流量系数值。
3.11相对流量系数 relative flow coefficient某给定开度的流量系数与额定流量系数之比。3.12固有流量特性 inherent flow characteristic相对流量系数和对应的相对行程之间的固有关系。3.13液体压力恢复系数 liquid pressure recovery factor在塞流条件下实际最大流量与理论的非塞流的流量之比。3.14正作用式downward
当信号压力增大时,推杆向下动作为正作用式。3.15反作用式upward
当信号压力增大时,推杆向上动作为反作用式。4技术要求
4.1调节阀可以配用常规的电动和气动执行机构,它们应该接受来自变送单元或调节单元的0~10mA(DC)或4~20mA(DC)的标准输入电流信号和0.02~0.1MPa(0.2~1kgf/cm)的标准输入压力信号,输出可以是与输入信号相对应的转角位移或阀门直线位移。4.2电动与气动执行机构的工作条件至少应满足表1的规定。表1
执行机构类别
电动执行机构
气动执行机构
执行机构
伺服放大器
环境温度,℃
-10~+55
0~+50
—10~+55或40~+70
环境相对湿度,%
4.3调节阀的固有流量特性推荐直线、抛物线和等百分比流量特性。其他特殊流量特性应根据需要由制造厂提供,但制造厂均应提供给用户流量特性曲线。4.4调节阀可以是正作用式,也可以是反作用式。4.5除非有特殊要求,调节阀的整机基本误差、回差、死区和额定行程偏差应符合表2要求。表2
基本误差,%
差,%
额定行程偏差,%
电动调节阀
气动调节阀
4.6执行机构的技术要求按有关执行机构技术条件的规定。4.7调节阀应能经受1.5倍公称压力的壳体试验,试验期间不应有肉眼可见的渗漏。由于壳体试验引起壳体变形导致阀门不能正常工作的,应当判废。866
GB 10869-89
4.8调节阀的渗漏量应符合表4的规定,一般情况下单座调节阀渗漏量不得低于V级,双座调节阀的渗漏量不得低于正级。
4.9制造厂应该提供调节阀的额定流量系数Cv值,其实测值与规定值的偏差应不大于士10%。4.9.1Cv值的基本试验介质是水。Cv和流量Q的关系如式(1)所示:Cy =
式中:Cv—额定流量系数;
Q~-体积流量,m/h;
△p—阀前后压差,kPa;
G,——-密度(水为 1),kg/m。
4.9.2用于蒸汽介质的阀,其Cv与质量流量W的关系如式(2)所示:W 3. 156Cvy /xprl
式中,W
一质量流量,kg/h;
一额定流量系数;
阀前压力,kPa;
阀前蒸汽密度,kg/m;
膨胀系数,按式(3)计算:
式中:Fk——比热系数,F=K/1.4,K—蒸汽绝热指数;
XT—塞流状态下的压差比;
X——对阀前压力的压差比,即 X=Ap/pr,且 X≤FXr;Ap———阀前后压差,kPa。
4.9.3-般情况下,液体的Cv值用水试验,蒸汽的Cv值用空气实验求得。(1)
(2)
对于蒸汽介质用低压力恢复的截止型调节阀(图1所示)或者临界压力比X,=0.5处出现的调节阀(图2所示),其C值也可以用水来代替实验求得。867
GB10869—89
P2高压力恢复
p2低压力恢复
低压力恢复
高压力恢复
4.10调节阀应能保证正常工作,无异常的因流体扰动引起的机械振动和噪声。运行工况下,在调节阀下游1m处、距管壁1m处测量其噪声声压级应不大于90dB(A)。调节阀噪声声压级的试验和要求按供需双方的协议执行。
4.11对承压铸钢件的要求应符合JB3595和JB2640的规定。其射线探伤要求应符合GB5677的相应规定。
5试验与检验
5.1制造出厂的每台调节阀必须进行水压强度试验,渗漏量试验和整机基本误差、死区、回差及额定行程偏差的试验。
当执行机构与阀门是由不同制造厂生产时,则执行机构和阀门应根据对执行机构与阀的不同要求分别试验出厂。
5.2新产品或改型设计的调节阀型式试验除按本标准第5.1条规定的项目检查外,还需要进行流量特性试验及Cv值的测定。
5.3基本误差
将规定的输入信号平稳地按增大和减小方向输入执行机构,测量各点所对应的行程值,并按式(4)计算实际“信号-行程”关系与理论关系之间的各点误差:=L×100%
式中:.—第i点的误差;
l—第i点的实际行程;
L第i点的理论行程,
L-—调节阀的额定行程。
GB10869—89
除非另有规定,试验点应至少包括信号范围的0%,25%,50%,75%,100%5个点。测量仪表的基本误差应小于被试调节阀基本误差准许值的1/4。5.4回差试验
试验程序与本标准第5.3条相同,在同一输入信号上所测得的正、反行程的最大差值即为回差。5.5死区
5.5.1缓慢改变(增大或减小)输入信号,直到观察出一个可察觉的行程变化,记下这时的输入信号值。5.5.2按相反方向进行本标准第5.5.1条规定的试验。5.5.3本标准第5.5.1和5.5.2条两项输入信号之差即为死区,死区应在输入信号量程的25%,50%和75%3点上进行试验,其最大值不得大于本标准第4.5条的规定。5.6额定行程偏差
将输入信号输入执行机构,使阀杆走完全行程,按式(4)计算额定行程偏差。5.7壳体试验
5.7.1试验条件和要求
阀门壳体试验必须在5~5QC温度下进行。壳体试验之前,不得涂漆与使用防渗漏的涂层。如果抽查库存的阀门,可去掉已有的涂层。壳体试验时,可拆除怕损坏的零件,如阀杆、填料隔膜等。试验过程中,不得对阀门施加影响试验结果的任何外力。试验介质用水(可以加入防锈剂)、煤油或粘度不大于水的其他适宜液体。试验压力按GB1048的规定。
试验时,应排除壳体内的气体。5.7.2保压时间及检验要求
5.7.2.1保压时间按表3的规定。表3壳体试验保压时间
公称通径Dn,mm
保压时间,s
5.7.2.2达到保压时间后,不允许壳体发生渗漏。5.8渗漏试验
65~200
≥250
≥180
5.8.1渗漏等级
每-渗漏等级规定的阀座最大允许渗漏量不允许超过表4的规定,从Ⅱ级~V级必须对每一个阀门进行试验。
a。等级I,不要求做试验。
b.等级Ⅱ,适用于结构为双通道双阀座或带活塞环密封金属对金属密封阀座平衡式单通道的阀门,用A型试验方法。
等级Ⅲ,适用的阀门同于等级I,但对阀座和密封件的要求比较严格,用A型试验方法。c.
等级NV,适用于结构为非平衡式单通道单阀座及具有超级密封活塞环的金属对金属密封阀座d.
平衡式单通道的阀门,用A型试验方法。等级V,-般用于具有关键性用途,如作闭路装置、不带阻塞阀、整个阀长期处于高压差状态869
GB 1086989
等。本等级主要适用于结构为金属阀座非平衡式单通道,单阀座或带特殊阀座和特殊密封的平衡式单通道的阀门,用B型试验方法。在最大工作压差时用水做试验。表4阀座最大渗漏量
渗漏等级
等级1
等级1
等级NV
等级V
阀座最大渗漏量
额定容量的0.5%
额定容量的 0.1%
额定容量的0.01%
每毫米通径压差0.1MPa允许渗漏量(水)5×10-12m/s注:1)通径是指阀座的内径。
5.8.2试验方法
5.8.2.1A型试验方法
试验介质为温度5~50℃的清洁空气或水。试验介质压力为0.3~0.4MPa(表压)或者最大工作压差,选择其较小值。渗漏量和压力值应精确到读数的士10%。试验方法
试验介质应从规定的阀体入口端进入,出口端应通向大气或与压头损失低的测量装置连接。d.
必须将执行机构调整到规定的工作条件。如果使用的气体对正常关闭产生强烈冲击力时,应当e
采用弹簧或其他措施。如果试验压差低于阀门最大工作压差时,不应对阀座负荷作任何增值补偿。用水做试验时,应当注意排除阀体和管道中的气体。f.
5.8.2.2B型试验方法
试验介质为5~50℃的清洁水。
试验时,压差应为最大工作压差,或根据制造厂与用户商定的压力,压力可小些(最小压力降b.
0.7MPa),压力测量精度按本标准第5.8.2.1中c条的规定。试验介质应从阀体规定的入口端进入阀体。阀门关闭件处于开启状态,阀体组件,包括出口部c.
分及其连接管应全部充满水,然后急速关闭。调整执行机构,使其符合规定的工作条件,并按照本标准第5.8.2.2中b条的规定,进行渗漏d.
量试验。执行机构的有效关闭力应是规定的最大值,但不得超过最大值。当渗漏介质流量稳定时,应对其观察一段时间,以便得到本标准第5.8.2.1中条规定的精e.
所得到的渗漏值不应大于表4中规定的等级V阀座最大允许渗漏量的计算值。f
5.9流量系数的测定
5.9.1试验设备
5.9.1.1流量试验装置示意图见图3。870
GB 10869--89
1--压力源;2—试验段前节流阀;3一温度传感器;4—-流量传感器;5—试验阀门;6--实验段管路;7--实验段后节流阀;8·压力测点5.9.1.2试验段管路
试验段管路的规格应按被试的不同规格的阀门而定。阀门前后应有足够的直段管长,以保证液a.
体流速均匀,阀后首段管长至少大于10D(D为管子内径),阀前直段管长至少大于20I),见图4。D
b.试验段管路的内表面应无铁锈、氧化皮及任何足以引起激烈紊流的不规则形状试验段管路的中心线应对准试验阀的进口与出口的中心线,其同轴度应符合表5要求。C,
管子尺寸D
32~152
203以上
d.试验管路不应有收缩,入口出口应一样。同轴度
1%管子直径
5.9.1.3压力表接点
压力表在任何情况下都不应插入管子内部,试验阀前后的两个压力测点接点都应保持水平!a.
阀前测压点应距试验阀进口至少2D,见图4。阀后测点应距试验阀出口至少6D,见图4。5.9.1.4试验段前后的节流阀主要用来调节试验阀的压差,同时也用来维持试验阀后定的背压,使之压力稳定。
5.9.1.5流量测量
可以用流量孔板、电磁流量计、涡轮流量计或其他仪表测量流量,测量精度必须符合规定要求。a.
流量计可装在试验阀前或试验阀后,但当试验管路有泄漏和吸入空气时,安装点应仍能保证流b.
量测定精度。
5.9.1.6测量精度
测量试验阀前后压差的仪表应能测量试验过程中的任何压差,测量精度为土2%。测量流量的仪表应经常校验,以保证维持规定精度。校验时所用管系的外形尺寸应与阀门试b.
验时的管系相同。测量精度为士2%。GB 10869-89
c.测量系统中测量水温的仪表安装位置应不影响介质的流动状态。试验时任何测点的流体进口温度应保持不变,允许误差士5℃,测量精度为土2℃。5.9.2试验介质
试验介质可用温度为5~50℃的清洁水,在不影响试验值的条件下,允许加少量防腐剂;也可用空气或其他气体,试验时不应出现冰冻。5.9.3液体C值的试验方法
5.9.3.1为了求得额定流量系数Cv,试验阀门应在三个不同的压差下进行试验,压差应在35~100kPa范围内,每次增量不少于15kPa。试验介质的雷诺数应大于105,阀门的行程应为100%额定行程。为使阀后的管路充满介质和防止介质突然汽化,试验阀前压力必须高于或等于表6所列的最低值。表6最小的阀前试验压力
压差,kPa
FL(按本标准3.9.4条)
5.9.3.2测试与记录
在下述阀门行程下分别测定流量与压差:5.9. 3.2. 12
在100%额定行程;
每隔10%额定行程测一次;
在到达最低调节点时。
5.9.3.2.2记录下述数据:
阀门行程,误差不应超过额定行程的士0.5%;b.
阀前后压力p与p2,误差为读数的士2%;试验阀的压差,误差为读数的土2%;容积流量,误差为读数的2%;
介质温度,误差为士1℃;
大气压力,误差不超过2%。
阀入口压力pi,kPa
5.9.3.3将测量数据代入式(1)求C、值。取三次试验的算术平均值即为该阀的额定流量系数。5.9.4压力恢复系数F的测定
5.9.4.1使试验阀处于100%的额定行程测定最大体积流量Qmax。5.9.4.2阀前压力力,固定,系统后的节流阀全开,测出试验阀的最大压差。5.9.4.3第二次试验时压差为第一次试验时最大压差的90%,此时测出的流量与第--~次最大压差下测出的流量应相差在士2%范围内,则在最大压差下测出的流量为Qmi。如超出上述范围应取更高的阀前压力,将试验重复进行次。
注意:试验段后的节流阀的节流面积应大于试验阀的节流面积,以保证塞流不产生在节流阀内。5.9.4.4按式(5)求出Fl:
0. 1Cv V(p1 - 0. 9pv)/G,
式中:FL
压力恢复系数;
最大体积流量,m2/h;
额定流量系数;
GB 10869-89
p-阀前压力,kPa;
pv——阀入口温度下的液体蒸发压力,kPa;Gf
密度(水为1),kg/m2。
5.9.5气体的K值试验方法
试验阀门应在三个不同的压差下进行试验,压差比(X=Ap/p1)应不大于0.02,试验阀应为额定行程状态。
测试与记录同本标准第5.9.3.2条规定。b.
将测量数据代入式(6)求出K,值:TG
体积流量,m2/h;
式中:Q
阀前压力,kPa;
T—一介质温度(绝对),K;
X-—压力比;
G—一气体相对空气密度比。
5.9.6塞流状态下的压差比X的测定.(6)
5.9.6.1测Xr时应使试验阀在额定行程下试验。5.9.6.2在一定的压力比△p/p,下,测出流量Qmax,即当出口压力P2下降时,流量不再增加的流量。不再增加指流量绝对值不超过2%。对进口压力要求能产生塞流,任何压差下都要产生塞流,出口节流阀应全开。
第二次试验时,改变节流阀使压差至少减少10%,在同样进口压力下,如果第二次与第一次流量变化不超过0.5%,这时的流量即是最大流量。5.9.6.3记录下列数据:
阀门行程,误差为规定行程值的士0.5%;阀前后压力p与2,误差为读数的士2%;b.
体积流量Q,误差为读数的士2%;c.
介质的温度,误差为士1℃,
大气压力,误差不超过2%。
5.9.6.4按式(7)代入数据求出Xr:XT
调节阀额定行程时流量,m2/h;式中:Qmax
pi阀前压力,kPa;
T,介质温度(绝对),K。bZxz.net
3.25Cvp14
5.10试验合格的产品,应将体腔内水渍清除干净。产品合格证的内容应包括下列各项:a.产品名称;
产品型号;
出厂编号;
公称通径,mm;
公称压力,MPa;
最大允许压差,MPa;
最高工作温度,C;
产品的额定流量系数Cv;
GB10869--89
承压铸件的材料牌号,炉号,化学成分,机械性能;制造日期;
编制者,校对者,质量检验部门签章,检查员章。标志、包装、保管、运输
检验合格的产品应钉有金属铭牌,铭牌内容为下列各项:a.
产品名称;
产品型号;
产品编号;
公称通径,mm;
公称压力,MPa;
最大允许压差,MPa;
最高工作温度,℃;
产品额定流量系数Cv;
制造日期,
制造广名称。
注:对不同的固有流量特性应在铭牌内加以区别。6.2
阀门的标志及识别涂漆的颜色,可参照JB106的规定。产品的油漆、包装应符合JB1615的规定。6.3
6.4产品应保存在干燥地方,不允许露天存放或将产品堆置。6.5包装,保管和运输过程中,应使阀瓣处于关闭状态,两侧通道以盖板或塞子封闭,防止尘垢、污水侵入。
附加说明:
本标准由上海发电设备成套设计研究所提出并归口。本标准由哈尔滨锅炉厂和上海发电设备成套设计研究所负责起草。871
小提示:此标准内容仅展示完整标准里的部分截取内容,若需要完整标准请到上方自行免费下载完整标准文档。
电站调节阀技术条件
Specifications of control valves for fossil power stations主题内容与适用范围
本标准规定了电站调节阀的性能要求及其试验、检验方法。本标准适用于火力发电站用的调节阀。引用标准
GB1048管子与管路附件的公称压力和试验压力GB4213
、气动调节阀通用技术条件
GB5677铸钢件射线照相及底片等级分类方法JB106
阀门标志和识别涂漆
JB1615
JB2640
JB3595
JB4018
3术语
锅炉油漆和包装技术条件
锅炉管道附件承压铸钢件技术条件电站阀门制造技术条件
电站阀门型号编制方法
3.1基本误差 intrinsic error
调节阀的实际上升、下降特性曲线与规定的特性曲线之间的最大偏差。3.2回差hysteresis error
同--输入信号上升和下降的两相应行程值间的最大差值。3. 3 死区 dead band
GB 10869-89
输入信号正、反方向的变化不致引起阀杆行程有任何可察觉变化的有限区间。3.4行程travel
为改变流体的流量,阀内组件从关闭位置标起的线位移或角位移。3.5额定行程rated travel
规定全开位置上的行程。
3.6相对行程 relative travel
某给定开度上的行程与额定行程之比。3.7额定容量 rated valve capacity在规定试验压力条件下,试验流体通过调节阀额定行程时的流量。3.8渗漏量leakage
在规定实验条件下,实验流体通过调节阀处于关闭位置时的流量。3.9流量系数 flow coefficient中华人民共和国机械电子工业部1989-03-21批准1990-01-01实施
GB 10869-89
在规定条件下,即阀的两端压差为0.1MPa、介质密度为1g/cm\时,某给定行程时流经调节阀以m3/h或t/h计的流量数。
3.10额定流量系数Cv rated flow coefficient额定行程时的流量系数值。
3.11相对流量系数 relative flow coefficient某给定开度的流量系数与额定流量系数之比。3.12固有流量特性 inherent flow characteristic相对流量系数和对应的相对行程之间的固有关系。3.13液体压力恢复系数 liquid pressure recovery factor在塞流条件下实际最大流量与理论的非塞流的流量之比。3.14正作用式downward
当信号压力增大时,推杆向下动作为正作用式。3.15反作用式upward
当信号压力增大时,推杆向上动作为反作用式。4技术要求
4.1调节阀可以配用常规的电动和气动执行机构,它们应该接受来自变送单元或调节单元的0~10mA(DC)或4~20mA(DC)的标准输入电流信号和0.02~0.1MPa(0.2~1kgf/cm)的标准输入压力信号,输出可以是与输入信号相对应的转角位移或阀门直线位移。4.2电动与气动执行机构的工作条件至少应满足表1的规定。表1
执行机构类别
电动执行机构
气动执行机构
执行机构
伺服放大器
环境温度,℃
-10~+55
0~+50
—10~+55或40~+70
环境相对湿度,%
4.3调节阀的固有流量特性推荐直线、抛物线和等百分比流量特性。其他特殊流量特性应根据需要由制造厂提供,但制造厂均应提供给用户流量特性曲线。4.4调节阀可以是正作用式,也可以是反作用式。4.5除非有特殊要求,调节阀的整机基本误差、回差、死区和额定行程偏差应符合表2要求。表2
基本误差,%
差,%
额定行程偏差,%
电动调节阀
气动调节阀
4.6执行机构的技术要求按有关执行机构技术条件的规定。4.7调节阀应能经受1.5倍公称压力的壳体试验,试验期间不应有肉眼可见的渗漏。由于壳体试验引起壳体变形导致阀门不能正常工作的,应当判废。866
GB 10869-89
4.8调节阀的渗漏量应符合表4的规定,一般情况下单座调节阀渗漏量不得低于V级,双座调节阀的渗漏量不得低于正级。
4.9制造厂应该提供调节阀的额定流量系数Cv值,其实测值与规定值的偏差应不大于士10%。4.9.1Cv值的基本试验介质是水。Cv和流量Q的关系如式(1)所示:Cy =
式中:Cv—额定流量系数;
Q~-体积流量,m/h;
△p—阀前后压差,kPa;
G,——-密度(水为 1),kg/m。
4.9.2用于蒸汽介质的阀,其Cv与质量流量W的关系如式(2)所示:W 3. 156Cvy /xprl
式中,W
一质量流量,kg/h;
一额定流量系数;
阀前压力,kPa;
阀前蒸汽密度,kg/m;
膨胀系数,按式(3)计算:
式中:Fk——比热系数,F=K/1.4,K—蒸汽绝热指数;
XT—塞流状态下的压差比;
X——对阀前压力的压差比,即 X=Ap/pr,且 X≤FXr;Ap———阀前后压差,kPa。
4.9.3-般情况下,液体的Cv值用水试验,蒸汽的Cv值用空气实验求得。(1)
(2)
对于蒸汽介质用低压力恢复的截止型调节阀(图1所示)或者临界压力比X,=0.5处出现的调节阀(图2所示),其C值也可以用水来代替实验求得。867
GB10869—89
P2高压力恢复
p2低压力恢复
低压力恢复
高压力恢复
4.10调节阀应能保证正常工作,无异常的因流体扰动引起的机械振动和噪声。运行工况下,在调节阀下游1m处、距管壁1m处测量其噪声声压级应不大于90dB(A)。调节阀噪声声压级的试验和要求按供需双方的协议执行。
4.11对承压铸钢件的要求应符合JB3595和JB2640的规定。其射线探伤要求应符合GB5677的相应规定。
5试验与检验
5.1制造出厂的每台调节阀必须进行水压强度试验,渗漏量试验和整机基本误差、死区、回差及额定行程偏差的试验。
当执行机构与阀门是由不同制造厂生产时,则执行机构和阀门应根据对执行机构与阀的不同要求分别试验出厂。
5.2新产品或改型设计的调节阀型式试验除按本标准第5.1条规定的项目检查外,还需要进行流量特性试验及Cv值的测定。
5.3基本误差
将规定的输入信号平稳地按增大和减小方向输入执行机构,测量各点所对应的行程值,并按式(4)计算实际“信号-行程”关系与理论关系之间的各点误差:=L×100%
式中:.—第i点的误差;
l—第i点的实际行程;
L第i点的理论行程,
L-—调节阀的额定行程。
GB10869—89
除非另有规定,试验点应至少包括信号范围的0%,25%,50%,75%,100%5个点。测量仪表的基本误差应小于被试调节阀基本误差准许值的1/4。5.4回差试验
试验程序与本标准第5.3条相同,在同一输入信号上所测得的正、反行程的最大差值即为回差。5.5死区
5.5.1缓慢改变(增大或减小)输入信号,直到观察出一个可察觉的行程变化,记下这时的输入信号值。5.5.2按相反方向进行本标准第5.5.1条规定的试验。5.5.3本标准第5.5.1和5.5.2条两项输入信号之差即为死区,死区应在输入信号量程的25%,50%和75%3点上进行试验,其最大值不得大于本标准第4.5条的规定。5.6额定行程偏差
将输入信号输入执行机构,使阀杆走完全行程,按式(4)计算额定行程偏差。5.7壳体试验
5.7.1试验条件和要求
阀门壳体试验必须在5~5QC温度下进行。壳体试验之前,不得涂漆与使用防渗漏的涂层。如果抽查库存的阀门,可去掉已有的涂层。壳体试验时,可拆除怕损坏的零件,如阀杆、填料隔膜等。试验过程中,不得对阀门施加影响试验结果的任何外力。试验介质用水(可以加入防锈剂)、煤油或粘度不大于水的其他适宜液体。试验压力按GB1048的规定。
试验时,应排除壳体内的气体。5.7.2保压时间及检验要求
5.7.2.1保压时间按表3的规定。表3壳体试验保压时间
公称通径Dn,mm
保压时间,s
5.7.2.2达到保压时间后,不允许壳体发生渗漏。5.8渗漏试验
65~200
≥250
≥180
5.8.1渗漏等级
每-渗漏等级规定的阀座最大允许渗漏量不允许超过表4的规定,从Ⅱ级~V级必须对每一个阀门进行试验。
a。等级I,不要求做试验。
b.等级Ⅱ,适用于结构为双通道双阀座或带活塞环密封金属对金属密封阀座平衡式单通道的阀门,用A型试验方法。
等级Ⅲ,适用的阀门同于等级I,但对阀座和密封件的要求比较严格,用A型试验方法。c.
等级NV,适用于结构为非平衡式单通道单阀座及具有超级密封活塞环的金属对金属密封阀座d.
平衡式单通道的阀门,用A型试验方法。等级V,-般用于具有关键性用途,如作闭路装置、不带阻塞阀、整个阀长期处于高压差状态869
GB 1086989
等。本等级主要适用于结构为金属阀座非平衡式单通道,单阀座或带特殊阀座和特殊密封的平衡式单通道的阀门,用B型试验方法。在最大工作压差时用水做试验。表4阀座最大渗漏量
渗漏等级
等级1
等级1
等级NV
等级V
阀座最大渗漏量
额定容量的0.5%
额定容量的 0.1%
额定容量的0.01%
每毫米通径压差0.1MPa允许渗漏量(水)5×10-12m/s注:1)通径是指阀座的内径。
5.8.2试验方法
5.8.2.1A型试验方法
试验介质为温度5~50℃的清洁空气或水。试验介质压力为0.3~0.4MPa(表压)或者最大工作压差,选择其较小值。渗漏量和压力值应精确到读数的士10%。试验方法
试验介质应从规定的阀体入口端进入,出口端应通向大气或与压头损失低的测量装置连接。d.
必须将执行机构调整到规定的工作条件。如果使用的气体对正常关闭产生强烈冲击力时,应当e
采用弹簧或其他措施。如果试验压差低于阀门最大工作压差时,不应对阀座负荷作任何增值补偿。用水做试验时,应当注意排除阀体和管道中的气体。f.
5.8.2.2B型试验方法
试验介质为5~50℃的清洁水。
试验时,压差应为最大工作压差,或根据制造厂与用户商定的压力,压力可小些(最小压力降b.
0.7MPa),压力测量精度按本标准第5.8.2.1中c条的规定。试验介质应从阀体规定的入口端进入阀体。阀门关闭件处于开启状态,阀体组件,包括出口部c.
分及其连接管应全部充满水,然后急速关闭。调整执行机构,使其符合规定的工作条件,并按照本标准第5.8.2.2中b条的规定,进行渗漏d.
量试验。执行机构的有效关闭力应是规定的最大值,但不得超过最大值。当渗漏介质流量稳定时,应对其观察一段时间,以便得到本标准第5.8.2.1中条规定的精e.
所得到的渗漏值不应大于表4中规定的等级V阀座最大允许渗漏量的计算值。f
5.9流量系数的测定
5.9.1试验设备
5.9.1.1流量试验装置示意图见图3。870
GB 10869--89
1--压力源;2—试验段前节流阀;3一温度传感器;4—-流量传感器;5—试验阀门;6--实验段管路;7--实验段后节流阀;8·压力测点5.9.1.2试验段管路
试验段管路的规格应按被试的不同规格的阀门而定。阀门前后应有足够的直段管长,以保证液a.
体流速均匀,阀后首段管长至少大于10D(D为管子内径),阀前直段管长至少大于20I),见图4。D
b.试验段管路的内表面应无铁锈、氧化皮及任何足以引起激烈紊流的不规则形状试验段管路的中心线应对准试验阀的进口与出口的中心线,其同轴度应符合表5要求。C,
管子尺寸D
32~152
203以上
d.试验管路不应有收缩,入口出口应一样。同轴度
1%管子直径
5.9.1.3压力表接点
压力表在任何情况下都不应插入管子内部,试验阀前后的两个压力测点接点都应保持水平!a.
阀前测压点应距试验阀进口至少2D,见图4。阀后测点应距试验阀出口至少6D,见图4。5.9.1.4试验段前后的节流阀主要用来调节试验阀的压差,同时也用来维持试验阀后定的背压,使之压力稳定。
5.9.1.5流量测量
可以用流量孔板、电磁流量计、涡轮流量计或其他仪表测量流量,测量精度必须符合规定要求。a.
流量计可装在试验阀前或试验阀后,但当试验管路有泄漏和吸入空气时,安装点应仍能保证流b.
量测定精度。
5.9.1.6测量精度
测量试验阀前后压差的仪表应能测量试验过程中的任何压差,测量精度为土2%。测量流量的仪表应经常校验,以保证维持规定精度。校验时所用管系的外形尺寸应与阀门试b.
验时的管系相同。测量精度为士2%。GB 10869-89
c.测量系统中测量水温的仪表安装位置应不影响介质的流动状态。试验时任何测点的流体进口温度应保持不变,允许误差士5℃,测量精度为土2℃。5.9.2试验介质
试验介质可用温度为5~50℃的清洁水,在不影响试验值的条件下,允许加少量防腐剂;也可用空气或其他气体,试验时不应出现冰冻。5.9.3液体C值的试验方法
5.9.3.1为了求得额定流量系数Cv,试验阀门应在三个不同的压差下进行试验,压差应在35~100kPa范围内,每次增量不少于15kPa。试验介质的雷诺数应大于105,阀门的行程应为100%额定行程。为使阀后的管路充满介质和防止介质突然汽化,试验阀前压力必须高于或等于表6所列的最低值。表6最小的阀前试验压力
压差,kPa
FL(按本标准3.9.4条)
5.9.3.2测试与记录
在下述阀门行程下分别测定流量与压差:5.9. 3.2. 12
在100%额定行程;
每隔10%额定行程测一次;
在到达最低调节点时。
5.9.3.2.2记录下述数据:
阀门行程,误差不应超过额定行程的士0.5%;b.
阀前后压力p与p2,误差为读数的士2%;试验阀的压差,误差为读数的土2%;容积流量,误差为读数的2%;
介质温度,误差为士1℃;
大气压力,误差不超过2%。
阀入口压力pi,kPa
5.9.3.3将测量数据代入式(1)求C、值。取三次试验的算术平均值即为该阀的额定流量系数。5.9.4压力恢复系数F的测定
5.9.4.1使试验阀处于100%的额定行程测定最大体积流量Qmax。5.9.4.2阀前压力力,固定,系统后的节流阀全开,测出试验阀的最大压差。5.9.4.3第二次试验时压差为第一次试验时最大压差的90%,此时测出的流量与第--~次最大压差下测出的流量应相差在士2%范围内,则在最大压差下测出的流量为Qmi。如超出上述范围应取更高的阀前压力,将试验重复进行次。
注意:试验段后的节流阀的节流面积应大于试验阀的节流面积,以保证塞流不产生在节流阀内。5.9.4.4按式(5)求出Fl:
0. 1Cv V(p1 - 0. 9pv)/G,
式中:FL
压力恢复系数;
最大体积流量,m2/h;
额定流量系数;
GB 10869-89
p-阀前压力,kPa;
pv——阀入口温度下的液体蒸发压力,kPa;Gf
密度(水为1),kg/m2。
5.9.5气体的K值试验方法
试验阀门应在三个不同的压差下进行试验,压差比(X=Ap/p1)应不大于0.02,试验阀应为额定行程状态。
测试与记录同本标准第5.9.3.2条规定。b.
将测量数据代入式(6)求出K,值:TG
体积流量,m2/h;
式中:Q
阀前压力,kPa;
T—一介质温度(绝对),K;
X-—压力比;
G—一气体相对空气密度比。
5.9.6塞流状态下的压差比X的测定.(6)
5.9.6.1测Xr时应使试验阀在额定行程下试验。5.9.6.2在一定的压力比△p/p,下,测出流量Qmax,即当出口压力P2下降时,流量不再增加的流量。不再增加指流量绝对值不超过2%。对进口压力要求能产生塞流,任何压差下都要产生塞流,出口节流阀应全开。
第二次试验时,改变节流阀使压差至少减少10%,在同样进口压力下,如果第二次与第一次流量变化不超过0.5%,这时的流量即是最大流量。5.9.6.3记录下列数据:
阀门行程,误差为规定行程值的士0.5%;阀前后压力p与2,误差为读数的士2%;b.
体积流量Q,误差为读数的士2%;c.
介质的温度,误差为士1℃,
大气压力,误差不超过2%。
5.9.6.4按式(7)代入数据求出Xr:XT
调节阀额定行程时流量,m2/h;式中:Qmax
pi阀前压力,kPa;
T,介质温度(绝对),K。bZxz.net
3.25Cvp14
5.10试验合格的产品,应将体腔内水渍清除干净。产品合格证的内容应包括下列各项:a.产品名称;
产品型号;
出厂编号;
公称通径,mm;
公称压力,MPa;
最大允许压差,MPa;
最高工作温度,C;
产品的额定流量系数Cv;
GB10869--89
承压铸件的材料牌号,炉号,化学成分,机械性能;制造日期;
编制者,校对者,质量检验部门签章,检查员章。标志、包装、保管、运输
检验合格的产品应钉有金属铭牌,铭牌内容为下列各项:a.
产品名称;
产品型号;
产品编号;
公称通径,mm;
公称压力,MPa;
最大允许压差,MPa;
最高工作温度,℃;
产品额定流量系数Cv;
制造日期,
制造广名称。
注:对不同的固有流量特性应在铭牌内加以区别。6.2
阀门的标志及识别涂漆的颜色,可参照JB106的规定。产品的油漆、包装应符合JB1615的规定。6.3
6.4产品应保存在干燥地方,不允许露天存放或将产品堆置。6.5包装,保管和运输过程中,应使阀瓣处于关闭状态,两侧通道以盖板或塞子封闭,防止尘垢、污水侵入。
附加说明:
本标准由上海发电设备成套设计研究所提出并归口。本标准由哈尔滨锅炉厂和上海发电设备成套设计研究所负责起草。871
小提示:此标准内容仅展示完整标准里的部分截取内容,若需要完整标准请到上方自行免费下载完整标准文档。

标准图片预览:
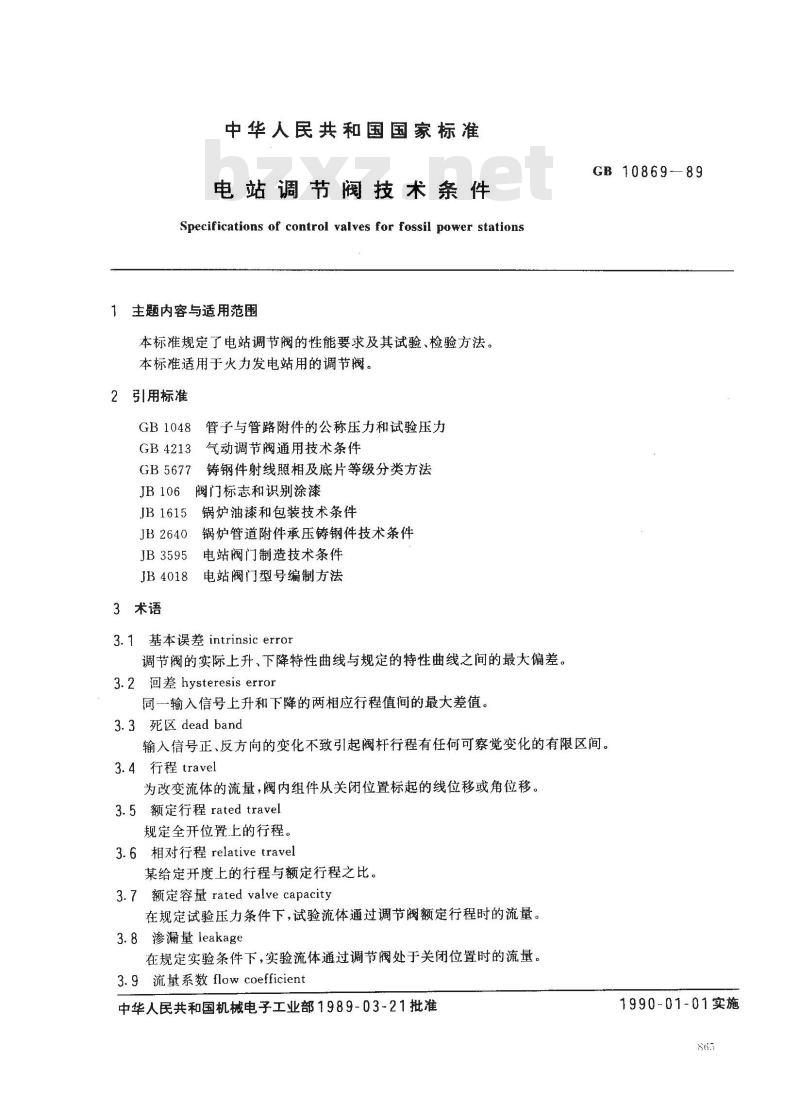
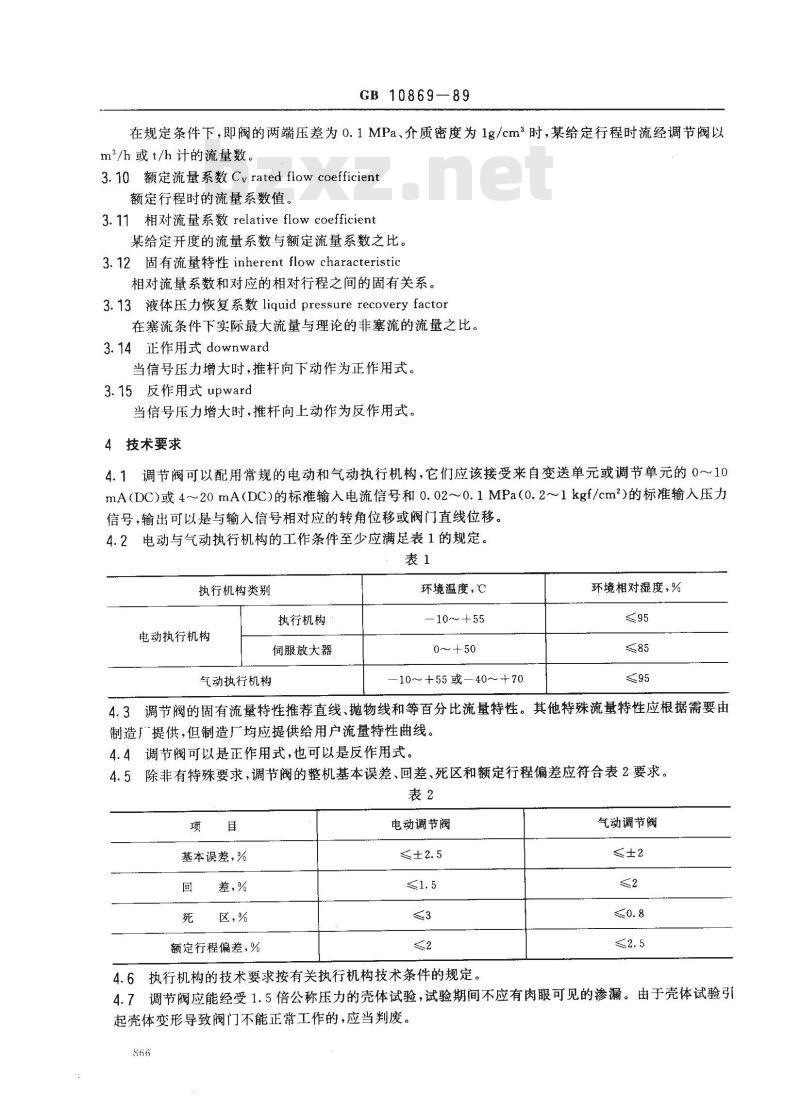
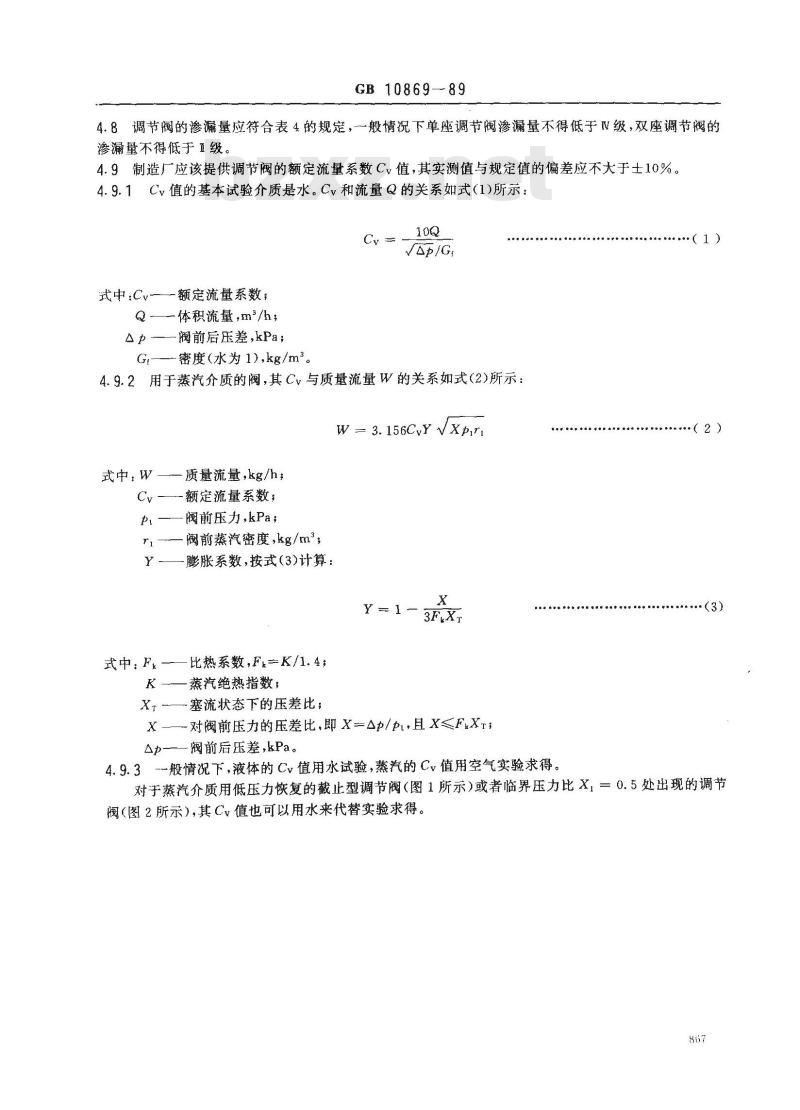
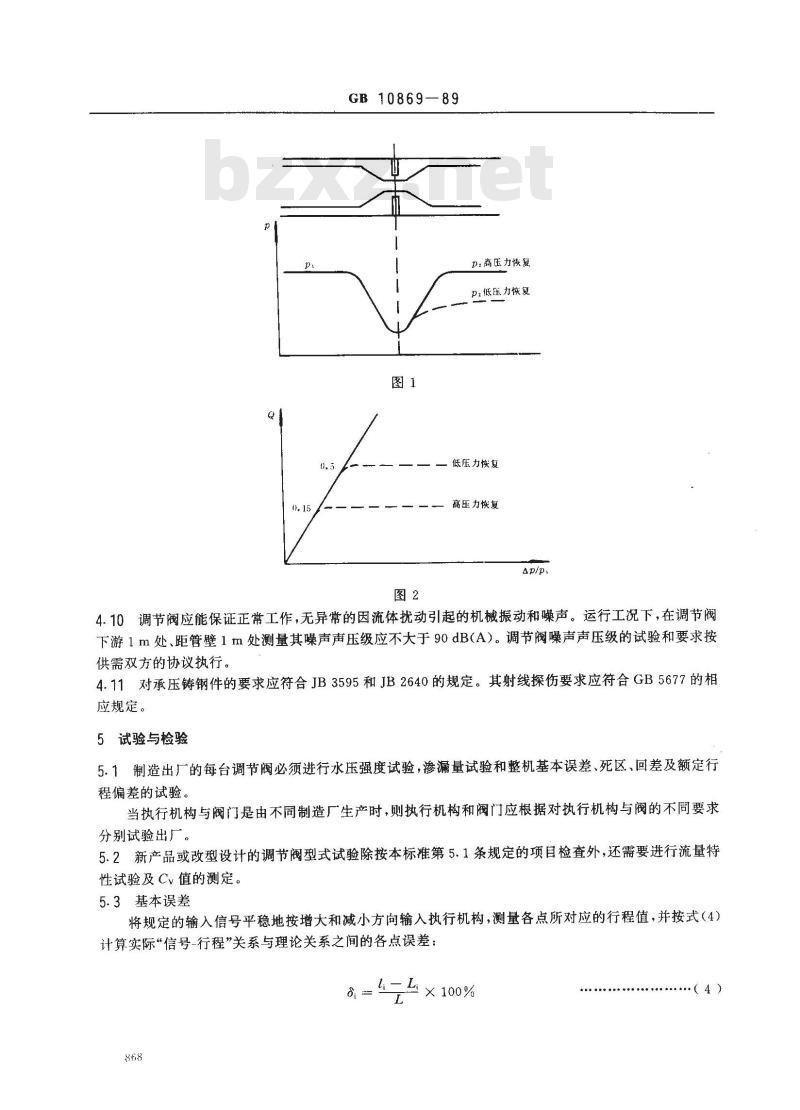
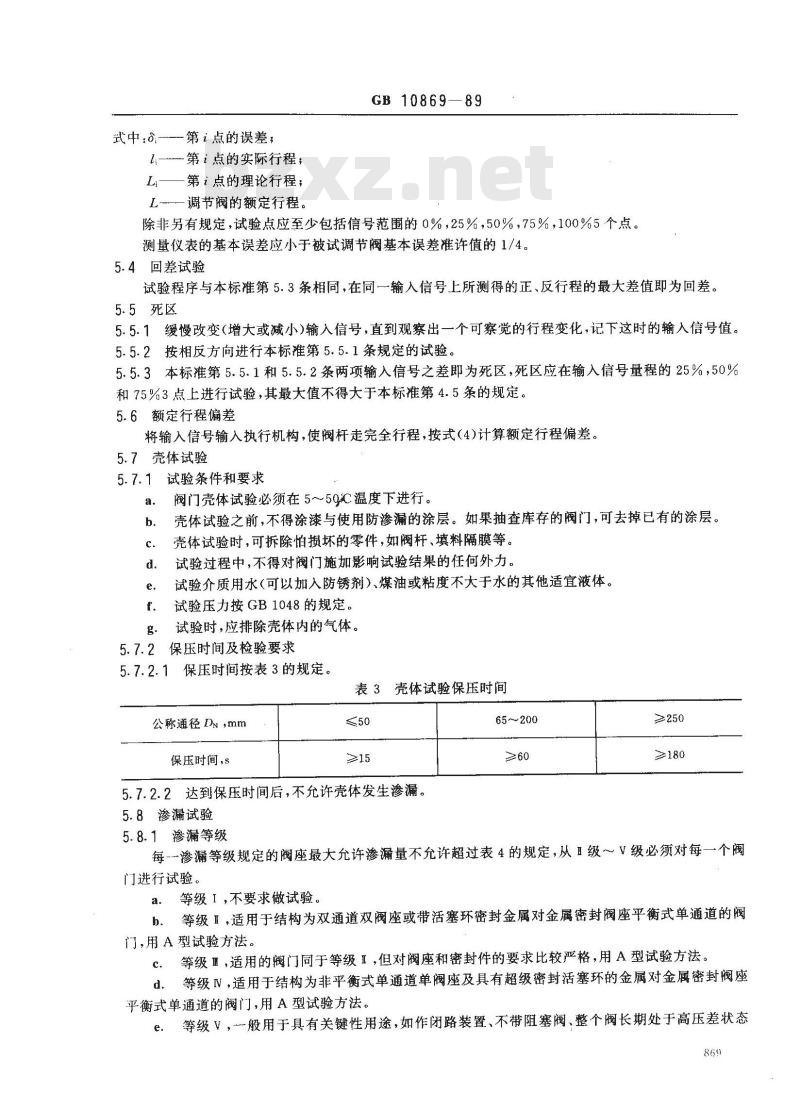
- 其它标准
- 上一篇: GB 10868-1989 电站减温减压阀技术条件
- 下一篇: GB 10877-1989 氧气瓶阀
- 热门标准
- 国家标准(GB)
- GB/T2828.1-2012 计数抽样检验程序 第1部分:按接收质量限(AQL)检索的逐批检验抽样计划
- GB/T7251.1-2023 低压成套开关设备和控制设备 第1部分:总则
- GB4623-1994 环形预应力混凝土电杆
- GB/T1567-2003 薄型 平键
- GB/T51435-2021 农村生活垃圾收运和处理技术标准
- GB50777-2012 ±800KV及以下换流站构支架施工及验收规范
- GB50268-2008 给水排水管道工程施工及验收规范
- GB50057-2010 建筑物防雷设计规范
- GB/T3098.1-2010 紧固件机械性能 螺栓、螺钉和螺柱
- GB50210-2018 建筑装饰装修工程质量验收标准
- GB/T50010-2010 混凝土结构设计标准(2024年版)
- GB7521—1987 多个控制器在一CA MAC机箱中
- GB/T228.1-2021 金属材料 拉伸试验 第1部分:室温试验方法
- GB/T3836.1-2021 爆炸性环境 第1部分:设备 通用要求
- GB/T5465.2-2023 电气设备用图形符号 第2部分:图形符号
- 行业新闻
请牢记:“bzxz.net”即是“标准下载”四个汉字汉语拼音首字母与国际顶级域名“.net”的组合。 ©2009 标准下载网 www.bzxz.net 本站邮件:bzxznet@163.com
网站备案号:湘ICP备2023016450号-1
网站备案号:湘ICP备2023016450号-1