- 您的位置:
- 标准下载网 >>
- 标准分类 >>
- 国家标准(GB) >>
- GB/T 6038-1993 橡胶试验胶料的配料、混炼和硫化设备及操作程序
标准号:
GB/T 6038-1993
标准名称:
橡胶试验胶料的配料、混炼和硫化设备及操作程序
标准类别:
国家标准(GB)
标准状态:
已作废-
发布日期:
1993-01-02 -
实施日期:
1994-10-01 -
作废日期:
2006-12-01 出版语种:
简体中文下载格式:
.rar.pdf下载大小:
223.59 KB
替代情况:
替代GB 6038-1985;被GB/T 6038-2006代替采标情况:
≈ISO/DIS 2393-89

点击下载
标准简介:
标准下载解压密码:www.bzxz.net
本标准规定了橡胶试验胶料的配料、混炼、硫化等步骤所需设备和一般操作程序。本标准适用于试验室橡胶试验用胶料和试样的制备。 GB/T 6038-1993 橡胶试验胶料的配料、混炼和硫化设备及操作程序 GB/T6038-1993

部分标准内容:
中华人民共和国国家标准
橡胶试验胶料的配料、混炼和硫化设备及操作程序
Rubber test mixes--Preparation,mixing andvulcanization-Equipment and proceduresGB 6038—93
代替GB6038-85
本标准参照采用国际标准ISO/DIS2393-1989《橡胶试验胶料-—一配料混炼和硫化-一设备及
操作程序》。
1主题内容与适用范围
本标准规定了橡胶试验胶料的配料、混炼、硫化等步骤所需设备和一般操作程序。本标准适用于试验室橡胶试验用胶料和试样的制备。2引用标准
GB2941橡胶试样环境调节和试验的标准温度、湿度及时间HG/T5-1615实验用开放式炼胶机3术语
基本配方量:以生胶或油充生胶为100g时胶和配方中所有配合剂的总量,以克计。批混炼量:指一次加工所制得的胶料总量。4试验胶料的配料
4.1配合剂
4.1.1制备橡胶试验用胶料的各种配合剂应符合有关标准的规定。4.1.2凡要求加工处理(如干燥、粉碎、过筛等)后使用的配合剂,应按加工技术条件进行处理。4.2混炼胶的批量
非在有关标准中另有规定,用标准试验室开放式炼胶机每次批混炼量应是基本配方量的四倍。标准密炼机每次批混炼量应等于密炼机额定容量乘以混炼胶的密度。注:若采用较小的批混炼量,其结果可能不同。建议最低混炼生胶质量为200g。4.3称量允许误差
生胶和炭黑的称量应精确至1g;油类应精确至1g或土1%(以精确度高的为准);硫黄和促进剂精确至0.02g,氧化锌和硬酯酸精确至0.1g;所有其他配合剂应精确至士1%。5试验胶料的混炼
5.1混炼设备
5.1.1开放式炼胶机应符合HG/T51615及下述规定,其主要技术特征如下:辊简直径(外径),mm
150~155
国家技术监督局1993-12-30批准242
1994-10-01实施
辊简长度(两挡板间),mm
前辊简(慢辊)转速,r/min
辊简速比
两辊筒间隙(可调),mm
辊距允许偏差
控温偏差,℃
GB6038—93
250~280
0. 2~8. 0
士10%或0.05mm,取其中较大者
注:①若使用其他规格开放式炼胶机,需调整混炼程序才能获得可比结果。②辊距调整方法见附录A。
5.1.2密炼机
5.1.2.1密炼机的主要技术特征如下:转子型式
非啮合转子或切向式转子
混炼室容积,L
额定混炼容量,L
1.17±0.04
转子速度(快转子),r/min
转子摩擦比
转子间隙,mm
2. 38±1. 13
功率(快转子),kw
上顶栓混炼时压力,MPa
77±10
110±10
5.1.2.2密炼机应装有测温系统、记时装置和功率或转距记录系统,以便分别指示和记录混炼操作中的温度、时间和所消耗的功率和转矩。5.1.2.3密炼机还应配有有效的加热和冷却系统,以便控制转子和混炼室内腔壁表面的温度。5.1.2.4为防止发生事故,密炼机应装有适当的排气系统和安全装置。5.1.2.5为将密炼机排出的胶料压实,应同时备有符合5.1.1条所规定的开放式炼胶机。5.1.2.6使用不同类型密炼机,最终所得混炼胶性能可能不同,若适当调整混炼程序有可能得到可比较的结果。仲裁试验时这种调整应通过试验由有关双方协商确定。注;当转子间隙达到3.70mm时,约增加10%的混炼容积,当间隙超过3.70mm时需进行大修,否则影响混炼质量。
5.2混炼程序
5.2.1开放式炼胶机混炼程序
5.2.1.1除非在相应标准中另有规定,每批胶料混炼时都要包在前辊上。5.2.1.2在混炼过程中,辊筒温度始终保持在规定温度的土5℃范围内,采用精度为士1C的表面测温计测量辊简表面中间部位的温度。为了测量前辊简表面温度,可以把胶料迅速地从炼胶机上取下,测定辊温之后再将胶放回。
5.2.1.3作3/4割刀时,其操作方法是:分别由右向左,由左向右,割取包辊胶宽度的3/4,待辊上积胶全部通过辑简间隙时,将割下的胶推向辑简的左边或右边并续入,如此往返切割。左右切割一次为-刀。两次连续割力之间允许间隔时间为20s。5.2.1.4当堆积胶或辊简表面上还有明显的游离粉料时不应切割胶料,从间隙散落下来的配合剂应及时小心收集并重新混入胶料中。5.2.1.5需分两个阶段混炼的胶料,在进行第二阶段混炼操作之前让混炼胶至少放置30min或直至胶料达到室温为止,两个阶段混炼之间最长放置时间为24h。243
GB6038--93
5.2.1.6为获得压延效应,建议在取出硫化仪试样和混炼胶粘度试样后,余下混炼胶在50士5℃下过辊四次,每次过辊之后沿混炼胶纵向对折,并让胶片总以同一方向过辊,调整辊距使收缩后胶片厚度为2.2~2.4mm,适于制备哑铃试样的硫化胶片。若需制备环形试样的硫化胶圆片,让压出胶片厚度为4.2~4. 4 mm
5.2.1.7混炼后胶料质量与所有原材料总质量之差为0.5%~一1.5%。5.2.1.8混炼后胶料应放在平整、干净、干燥的金属表面冷至室温,冷却后胶料应用铝箔或其他合适材料包好以防污染。
5.2.2密炼机混炼程序
5.2.2.1密炼机混炼方法应按不同橡胶相应标准规定进行,若无现成标准可以依据,可按供需双方协议规定进行混炼。
5.2.2.2开始混炼试验时,可先混炼一个与试验胶料配方相同的胶料调整密炼机的工作状态。对同--批混炼胶料,密炼机的控制条件应保持相同。5.2.2.3密炼机排出胶料应在开放式炼胶机上压实,并在平整、洁净金属表面上冷至室温。5.2.2.4进行第二段混炼的胶料应按5.2.1.5的规定放置。当用开放式炼胶机进行二段混炼时,应按有关标准和配方要求加入剩余配合剂,同时每批混炼胶量应减至基本配方量的四倍。当用密炼机进行二段混炼时,应先将胶料切成条状投入密炼机,然后再按规定加入余下配合剂。从密炼机排出胶料应按5.2.2.3条所述压实,冷至室温。5.2.2.5欲获得具压延效应的胶片制备哑铃状试样时,应按5.2.1.6规定下片。5.2.2.6混炼后胶料的质量与所有原材料总质量之差为0.5%~一1.5%。注:已知某些橡胶和配合剂含有少量挥发物,它们在密炼机混炼温度下可能挥发,其结果无法满足上述质量差允许界限,此时应在试验报告中注明实际质量差。6试样用胶片的硫化
6.1胶料准备
6.1.1混炼后的胶料应按GB2941规定调节2~24h。6.1.2将调节后的胶片切成与模腔尺寸相对应的胶还,并标出胶料名称、编号和硫化条件,对哑铃状试样应同时标出胶料压延方向。
6.1.3胶料尽可能不要返炼,一旦需要返炼,应按混炼时的辑温进行返炼。6.1.4胶坏质量可按以下方法计算:胶坏质量(g)=模腔容积(cm)×胶料密度(g/cm2)×(1.05~1.10)为保证模压硫化时有充足的胶量,胶料的实际用量应比计算的量再增加(5~10)%。6.2平板硫化机
6.2.1硫化机两热板加压面应相互平行,将软质铅条放置在热板之间,当热板在150℃满压下闭合时,其平行度应在0.25mm/m范围之内。6.2.2热板采用蒸汽加热或电加热。当使用蒸汽加热时,在蒸汽管道引出端需安装自动汽水分离器或汽孔,以便使蒸汽连续通过热板。如用箱式热板,则应将蒸汽出口设置在略低于蒸气室的部位,以保证良好的排水。
6.2.3平板在整个硫化过程中,在模具型腔面积上施加的压强不低于3.5MPa。6.2.4无论使用何种型号的热板,整个模具面积上的温度分布应均匀。同一热板内各点间及各点与中心点间的最大温差不超过1C。相邻二热板之间其对应位置点的温差不超过1C。在热板中心处的最大温度偏差不超过士0.5C。热板温度分布测定方法见附录B6.2.5为了防止加热板与加压活动平台之间的热传导,最好在它们之间加上钢制隔离板或用其他方法使之尽量减少热损失,并对热板周围的通风进行适当的隔离。244
6.3模具
GB6038—93
6.3.1用于硫化橡胶物理试验用试样的模具应根据试验中所规定试样尺寸、形状以及硫化设备的有效面积来设计制造。材料采用中碳钢或不锈钢,模腔表面应镀铬或抛光,粗糙度R。不大1.6。模具的模盖与模底的厚度不应小于10 mm。6.3.2模腔表面在一般情况下,不使用隔离剂,如果需要时可使用少量与硫化胶不产生化学作用的残留型隔离剂。适用的隔离剂有硅油或中性皂液等。为避免模腔中遗留材料的污染,可以将玻璃纸、聚酯薄膜,铝箔等薄材料垫在模腔中的上下两面,同时对胶坏用胶量适当予以调整。6.4硫化程序
6.4.1胶坏硫化前应将模具放在闭合平板上预热至规定的硫化温度土1℃范围内,并在该温度下保持20min,连续硫化时可不再预热。硫化时每层热板仅允许放置一个模具。6.4.2开启平板并在尽可能短时间内将准备好胶坏装入模具,闭合平板。当取出模具装胶坏时,应采取预防措施以免模具因接触冷金属板或暴露在空气流中而过冷。6.4.3硫化时以加足压力开始至泄压这段时间作为硫化时间。硫化期间模腔压强不得少于3.5MPa。硫化时间允许误差为士20 s。
平板一打开立即取出硫化胶片,放入室温水或低于室温水中冷却,或放在金属板上冷却10~15min,用于电学测量的胶片应放在金属板上冷却。放水中冷却的胶片擦干后在GB2941规定的温度“下保存备验。上述两种操作要仔细,以防胶片过分拉伸和变形。6.4.4硫化过程中应记录实际硫化温度和时间。2
A1准备工作
GB 6038-93
附录A
辑距调准方法
(补充件)
A1.1准备两根铅条,长至少50mm、宽10±3mm;厚度比欲测辊距厚0.25~0.50mm。A1.2准备---块尺寸约75mm×75mm×6mm混炼胶,其门尼粘度ML(1+4)100C大于50。A2辑距允许偏差
在距为0.2~0.5mm时为±0.05mm,在辊距为1.0~3.0mm时为士0.10mm。辑距为3.0~8.0 mm时辊距容许偏差为土10%。A3调整步骤
A3.1调辊距前,将辊简温度调节至混炼所要求的温度,再根据手轮指针将辊距大致调至所需数值。A3.2把两根铅条放在辑筒两端,在距挡板约25mm处各插一条,同时把混炼胶从两辊筒中心部位过,
A3.3铅条经辊筒间轧过后用精度0.01mm厚度计测其厚度。A3.4当实测辊距超出允许偏差时,应适当调整辊距后再次按A3.2和A3.3规定测定调整后的辊距.直至符合辑距要求为止。
附录B
热板温度分布测定方法免费标准下载网bzxz
(补充件)
81一般说明
本附录提出了测定平板硫化机热板温度均匀性的方法。本方法采用测温电偶或其他测温装置进行测量,测温点以多点矩形排列法(如图B1所示)安排,主要测量在工作压力下的温度,其误差不大于IC。
B2测温点的数量
按多点矩形排列法测温点数量最少应选择9点,测温点的横排、竖行与热板边缘的距离应根据热板的大小而均匀分布在平板上。
B3测定步骤
B3.1用热电偶多点排列法有测温点位置固定和测量迅速的优点,但要求热电偶导线的特性--致,以保证测定温度的准确可靠。
将测温热电偶排列在热绝缘板(橡胶板)上。橡胶板的厚度为15~20mm,硬度(邵尔A)65~~70,面积与平板相同。在橡胶板测温点背面留有可放置测温热电偶导线沟槽,把测温热电偶从橡胶的背面穿过,固定在橡胶板上,也可以在同一板上相对排成两组,能同时测量相邻的两块平板。在测量试验中将测温橡胶板夹在两平板之间,使它们紧密接触。当温度稳定时,用测温电位差计(精确度0.5级)测量各测定点的温度。每个测温点最少测量3次。B3.2测量注意事项
a.测定开始前平板必须在工作温度下预热90min。2.16
测定时热板温度必须稳定。
GB6038—93
每个测量点最少测量3次,每次测温间隔为10min,取平均值。当各点与中心温差超过规定时,应调动测温点位置,以测出热板温度达到均匀分布的区域。应定期检测及校正硫化平板的温度。橡胶板
接测温电位差计
测温热电偶分布排列图
附加说明:
本标准由中华人民共和国化学工业部提出。GB6038--93
本标准由化学工业部北京橡胶工业研究设计院归口。本标准由化学工业部北京橡胶工业研究设计院负责起草。本标准主要起草人张芬厚、陈颜、张涛。本标准由化学工业部北京橡胶工业研究设计院负责解释。248
小提示:此标准内容仅展示完整标准里的部分截取内容,若需要完整标准请到上方自行免费下载完整标准文档。
橡胶试验胶料的配料、混炼和硫化设备及操作程序
Rubber test mixes--Preparation,mixing andvulcanization-Equipment and proceduresGB 6038—93
代替GB6038-85
本标准参照采用国际标准ISO/DIS2393-1989《橡胶试验胶料-—一配料混炼和硫化-一设备及
操作程序》。
1主题内容与适用范围
本标准规定了橡胶试验胶料的配料、混炼、硫化等步骤所需设备和一般操作程序。本标准适用于试验室橡胶试验用胶料和试样的制备。2引用标准
GB2941橡胶试样环境调节和试验的标准温度、湿度及时间HG/T5-1615实验用开放式炼胶机3术语
基本配方量:以生胶或油充生胶为100g时胶和配方中所有配合剂的总量,以克计。批混炼量:指一次加工所制得的胶料总量。4试验胶料的配料
4.1配合剂
4.1.1制备橡胶试验用胶料的各种配合剂应符合有关标准的规定。4.1.2凡要求加工处理(如干燥、粉碎、过筛等)后使用的配合剂,应按加工技术条件进行处理。4.2混炼胶的批量
非在有关标准中另有规定,用标准试验室开放式炼胶机每次批混炼量应是基本配方量的四倍。标准密炼机每次批混炼量应等于密炼机额定容量乘以混炼胶的密度。注:若采用较小的批混炼量,其结果可能不同。建议最低混炼生胶质量为200g。4.3称量允许误差
生胶和炭黑的称量应精确至1g;油类应精确至1g或土1%(以精确度高的为准);硫黄和促进剂精确至0.02g,氧化锌和硬酯酸精确至0.1g;所有其他配合剂应精确至士1%。5试验胶料的混炼
5.1混炼设备
5.1.1开放式炼胶机应符合HG/T51615及下述规定,其主要技术特征如下:辊简直径(外径),mm
150~155
国家技术监督局1993-12-30批准242
1994-10-01实施
辊简长度(两挡板间),mm
前辊简(慢辊)转速,r/min
辊简速比
两辊筒间隙(可调),mm
辊距允许偏差
控温偏差,℃
GB6038—93
250~280
0. 2~8. 0
士10%或0.05mm,取其中较大者
注:①若使用其他规格开放式炼胶机,需调整混炼程序才能获得可比结果。②辊距调整方法见附录A。
5.1.2密炼机
5.1.2.1密炼机的主要技术特征如下:转子型式
非啮合转子或切向式转子
混炼室容积,L
额定混炼容量,L
1.17±0.04
转子速度(快转子),r/min
转子摩擦比
转子间隙,mm
2. 38±1. 13
功率(快转子),kw
上顶栓混炼时压力,MPa
77±10
110±10
5.1.2.2密炼机应装有测温系统、记时装置和功率或转距记录系统,以便分别指示和记录混炼操作中的温度、时间和所消耗的功率和转矩。5.1.2.3密炼机还应配有有效的加热和冷却系统,以便控制转子和混炼室内腔壁表面的温度。5.1.2.4为防止发生事故,密炼机应装有适当的排气系统和安全装置。5.1.2.5为将密炼机排出的胶料压实,应同时备有符合5.1.1条所规定的开放式炼胶机。5.1.2.6使用不同类型密炼机,最终所得混炼胶性能可能不同,若适当调整混炼程序有可能得到可比较的结果。仲裁试验时这种调整应通过试验由有关双方协商确定。注;当转子间隙达到3.70mm时,约增加10%的混炼容积,当间隙超过3.70mm时需进行大修,否则影响混炼质量。
5.2混炼程序
5.2.1开放式炼胶机混炼程序
5.2.1.1除非在相应标准中另有规定,每批胶料混炼时都要包在前辊上。5.2.1.2在混炼过程中,辊筒温度始终保持在规定温度的土5℃范围内,采用精度为士1C的表面测温计测量辊简表面中间部位的温度。为了测量前辊简表面温度,可以把胶料迅速地从炼胶机上取下,测定辊温之后再将胶放回。
5.2.1.3作3/4割刀时,其操作方法是:分别由右向左,由左向右,割取包辊胶宽度的3/4,待辊上积胶全部通过辑简间隙时,将割下的胶推向辑简的左边或右边并续入,如此往返切割。左右切割一次为-刀。两次连续割力之间允许间隔时间为20s。5.2.1.4当堆积胶或辊简表面上还有明显的游离粉料时不应切割胶料,从间隙散落下来的配合剂应及时小心收集并重新混入胶料中。5.2.1.5需分两个阶段混炼的胶料,在进行第二阶段混炼操作之前让混炼胶至少放置30min或直至胶料达到室温为止,两个阶段混炼之间最长放置时间为24h。243
GB6038--93
5.2.1.6为获得压延效应,建议在取出硫化仪试样和混炼胶粘度试样后,余下混炼胶在50士5℃下过辊四次,每次过辊之后沿混炼胶纵向对折,并让胶片总以同一方向过辊,调整辊距使收缩后胶片厚度为2.2~2.4mm,适于制备哑铃试样的硫化胶片。若需制备环形试样的硫化胶圆片,让压出胶片厚度为4.2~4. 4 mm
5.2.1.7混炼后胶料质量与所有原材料总质量之差为0.5%~一1.5%。5.2.1.8混炼后胶料应放在平整、干净、干燥的金属表面冷至室温,冷却后胶料应用铝箔或其他合适材料包好以防污染。
5.2.2密炼机混炼程序
5.2.2.1密炼机混炼方法应按不同橡胶相应标准规定进行,若无现成标准可以依据,可按供需双方协议规定进行混炼。
5.2.2.2开始混炼试验时,可先混炼一个与试验胶料配方相同的胶料调整密炼机的工作状态。对同--批混炼胶料,密炼机的控制条件应保持相同。5.2.2.3密炼机排出胶料应在开放式炼胶机上压实,并在平整、洁净金属表面上冷至室温。5.2.2.4进行第二段混炼的胶料应按5.2.1.5的规定放置。当用开放式炼胶机进行二段混炼时,应按有关标准和配方要求加入剩余配合剂,同时每批混炼胶量应减至基本配方量的四倍。当用密炼机进行二段混炼时,应先将胶料切成条状投入密炼机,然后再按规定加入余下配合剂。从密炼机排出胶料应按5.2.2.3条所述压实,冷至室温。5.2.2.5欲获得具压延效应的胶片制备哑铃状试样时,应按5.2.1.6规定下片。5.2.2.6混炼后胶料的质量与所有原材料总质量之差为0.5%~一1.5%。注:已知某些橡胶和配合剂含有少量挥发物,它们在密炼机混炼温度下可能挥发,其结果无法满足上述质量差允许界限,此时应在试验报告中注明实际质量差。6试样用胶片的硫化
6.1胶料准备
6.1.1混炼后的胶料应按GB2941规定调节2~24h。6.1.2将调节后的胶片切成与模腔尺寸相对应的胶还,并标出胶料名称、编号和硫化条件,对哑铃状试样应同时标出胶料压延方向。
6.1.3胶料尽可能不要返炼,一旦需要返炼,应按混炼时的辑温进行返炼。6.1.4胶坏质量可按以下方法计算:胶坏质量(g)=模腔容积(cm)×胶料密度(g/cm2)×(1.05~1.10)为保证模压硫化时有充足的胶量,胶料的实际用量应比计算的量再增加(5~10)%。6.2平板硫化机
6.2.1硫化机两热板加压面应相互平行,将软质铅条放置在热板之间,当热板在150℃满压下闭合时,其平行度应在0.25mm/m范围之内。6.2.2热板采用蒸汽加热或电加热。当使用蒸汽加热时,在蒸汽管道引出端需安装自动汽水分离器或汽孔,以便使蒸汽连续通过热板。如用箱式热板,则应将蒸汽出口设置在略低于蒸气室的部位,以保证良好的排水。
6.2.3平板在整个硫化过程中,在模具型腔面积上施加的压强不低于3.5MPa。6.2.4无论使用何种型号的热板,整个模具面积上的温度分布应均匀。同一热板内各点间及各点与中心点间的最大温差不超过1C。相邻二热板之间其对应位置点的温差不超过1C。在热板中心处的最大温度偏差不超过士0.5C。热板温度分布测定方法见附录B6.2.5为了防止加热板与加压活动平台之间的热传导,最好在它们之间加上钢制隔离板或用其他方法使之尽量减少热损失,并对热板周围的通风进行适当的隔离。244
6.3模具
GB6038—93
6.3.1用于硫化橡胶物理试验用试样的模具应根据试验中所规定试样尺寸、形状以及硫化设备的有效面积来设计制造。材料采用中碳钢或不锈钢,模腔表面应镀铬或抛光,粗糙度R。不大1.6。模具的模盖与模底的厚度不应小于10 mm。6.3.2模腔表面在一般情况下,不使用隔离剂,如果需要时可使用少量与硫化胶不产生化学作用的残留型隔离剂。适用的隔离剂有硅油或中性皂液等。为避免模腔中遗留材料的污染,可以将玻璃纸、聚酯薄膜,铝箔等薄材料垫在模腔中的上下两面,同时对胶坏用胶量适当予以调整。6.4硫化程序
6.4.1胶坏硫化前应将模具放在闭合平板上预热至规定的硫化温度土1℃范围内,并在该温度下保持20min,连续硫化时可不再预热。硫化时每层热板仅允许放置一个模具。6.4.2开启平板并在尽可能短时间内将准备好胶坏装入模具,闭合平板。当取出模具装胶坏时,应采取预防措施以免模具因接触冷金属板或暴露在空气流中而过冷。6.4.3硫化时以加足压力开始至泄压这段时间作为硫化时间。硫化期间模腔压强不得少于3.5MPa。硫化时间允许误差为士20 s。
平板一打开立即取出硫化胶片,放入室温水或低于室温水中冷却,或放在金属板上冷却10~15min,用于电学测量的胶片应放在金属板上冷却。放水中冷却的胶片擦干后在GB2941规定的温度“下保存备验。上述两种操作要仔细,以防胶片过分拉伸和变形。6.4.4硫化过程中应记录实际硫化温度和时间。2
A1准备工作
GB 6038-93
附录A
辑距调准方法
(补充件)
A1.1准备两根铅条,长至少50mm、宽10±3mm;厚度比欲测辊距厚0.25~0.50mm。A1.2准备---块尺寸约75mm×75mm×6mm混炼胶,其门尼粘度ML(1+4)100C大于50。A2辑距允许偏差
在距为0.2~0.5mm时为±0.05mm,在辊距为1.0~3.0mm时为士0.10mm。辑距为3.0~8.0 mm时辊距容许偏差为土10%。A3调整步骤
A3.1调辊距前,将辊简温度调节至混炼所要求的温度,再根据手轮指针将辊距大致调至所需数值。A3.2把两根铅条放在辑筒两端,在距挡板约25mm处各插一条,同时把混炼胶从两辊筒中心部位过,
A3.3铅条经辊筒间轧过后用精度0.01mm厚度计测其厚度。A3.4当实测辊距超出允许偏差时,应适当调整辊距后再次按A3.2和A3.3规定测定调整后的辊距.直至符合辑距要求为止。
附录B
热板温度分布测定方法免费标准下载网bzxz
(补充件)
81一般说明
本附录提出了测定平板硫化机热板温度均匀性的方法。本方法采用测温电偶或其他测温装置进行测量,测温点以多点矩形排列法(如图B1所示)安排,主要测量在工作压力下的温度,其误差不大于IC。
B2测温点的数量
按多点矩形排列法测温点数量最少应选择9点,测温点的横排、竖行与热板边缘的距离应根据热板的大小而均匀分布在平板上。
B3测定步骤
B3.1用热电偶多点排列法有测温点位置固定和测量迅速的优点,但要求热电偶导线的特性--致,以保证测定温度的准确可靠。
将测温热电偶排列在热绝缘板(橡胶板)上。橡胶板的厚度为15~20mm,硬度(邵尔A)65~~70,面积与平板相同。在橡胶板测温点背面留有可放置测温热电偶导线沟槽,把测温热电偶从橡胶的背面穿过,固定在橡胶板上,也可以在同一板上相对排成两组,能同时测量相邻的两块平板。在测量试验中将测温橡胶板夹在两平板之间,使它们紧密接触。当温度稳定时,用测温电位差计(精确度0.5级)测量各测定点的温度。每个测温点最少测量3次。B3.2测量注意事项
a.测定开始前平板必须在工作温度下预热90min。2.16
测定时热板温度必须稳定。
GB6038—93
每个测量点最少测量3次,每次测温间隔为10min,取平均值。当各点与中心温差超过规定时,应调动测温点位置,以测出热板温度达到均匀分布的区域。应定期检测及校正硫化平板的温度。橡胶板
接测温电位差计
测温热电偶分布排列图
附加说明:
本标准由中华人民共和国化学工业部提出。GB6038--93
本标准由化学工业部北京橡胶工业研究设计院归口。本标准由化学工业部北京橡胶工业研究设计院负责起草。本标准主要起草人张芬厚、陈颜、张涛。本标准由化学工业部北京橡胶工业研究设计院负责解释。248
小提示:此标准内容仅展示完整标准里的部分截取内容,若需要完整标准请到上方自行免费下载完整标准文档。

标准图片预览:
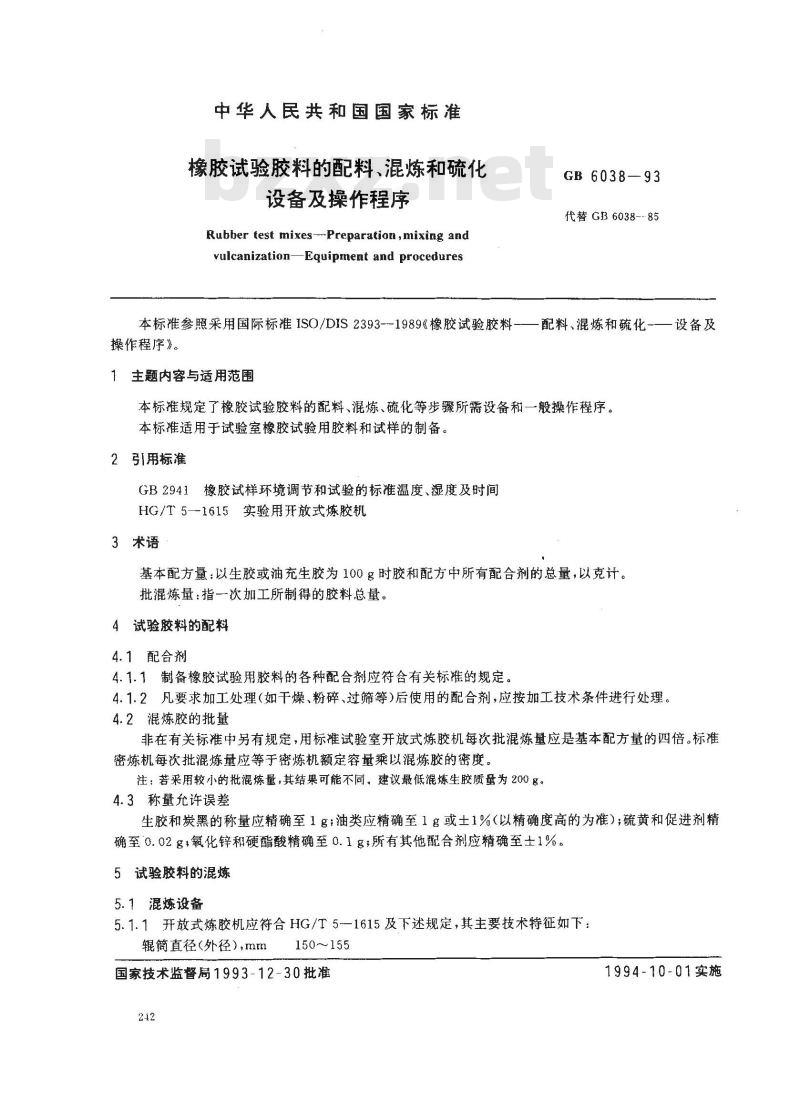
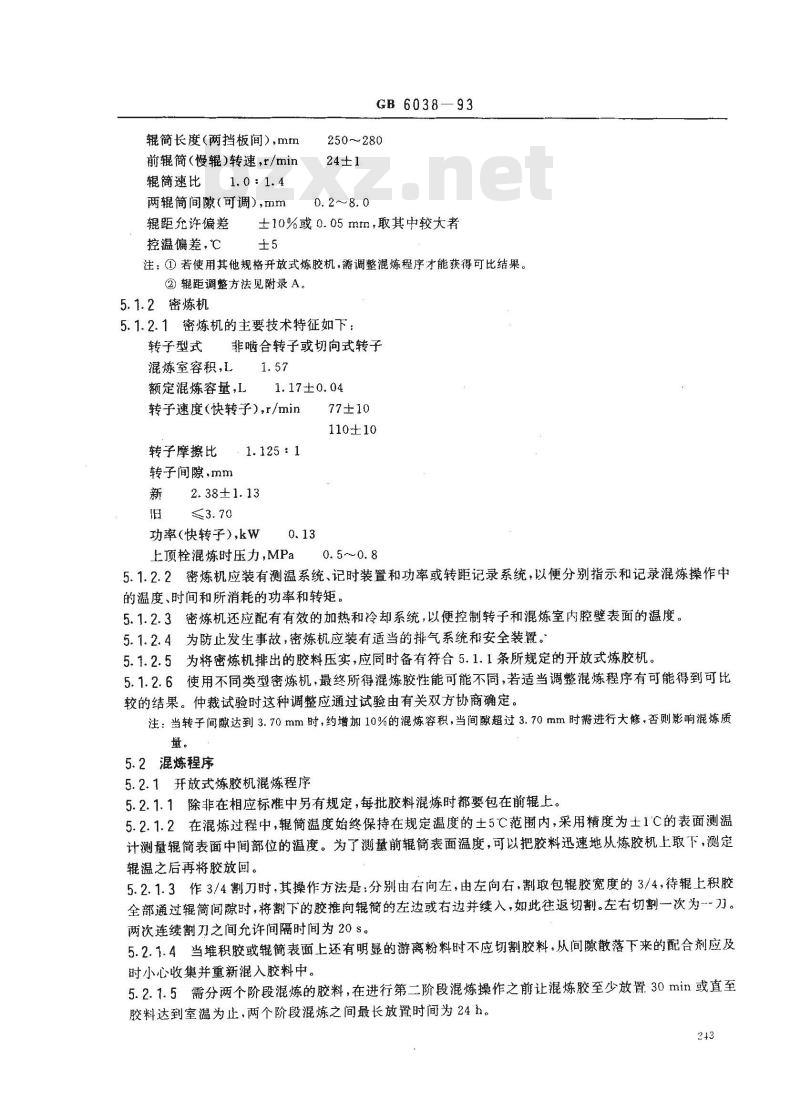

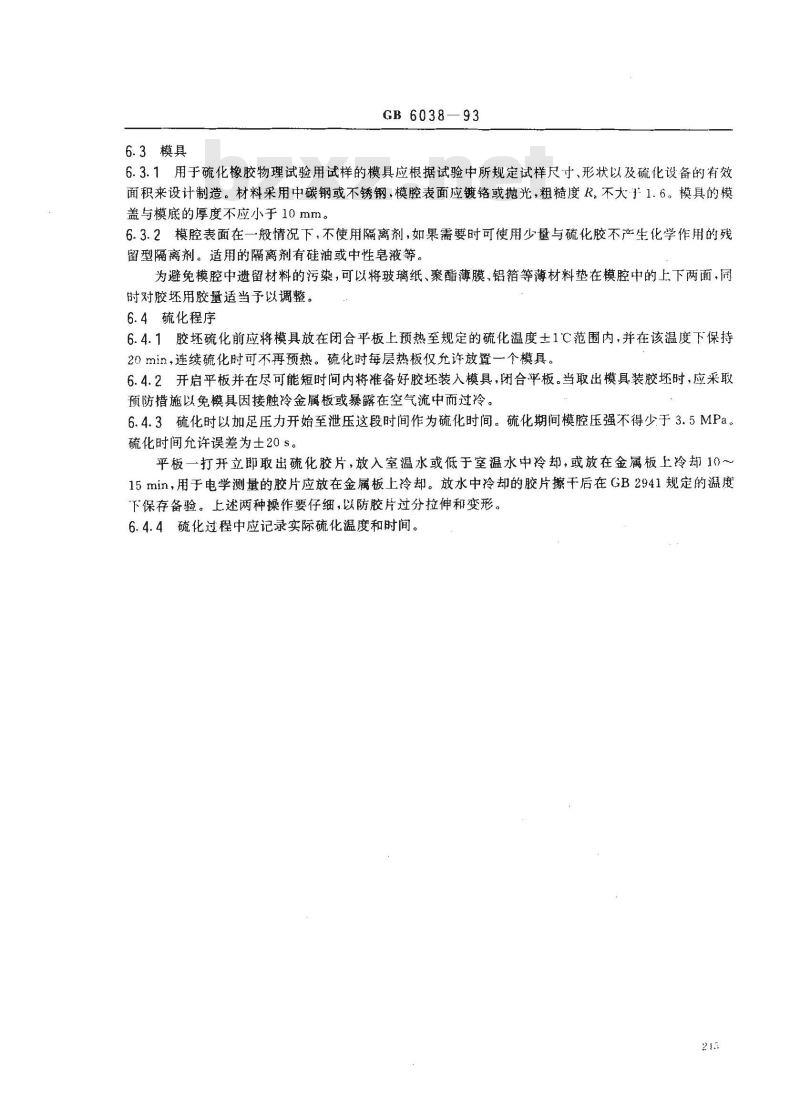
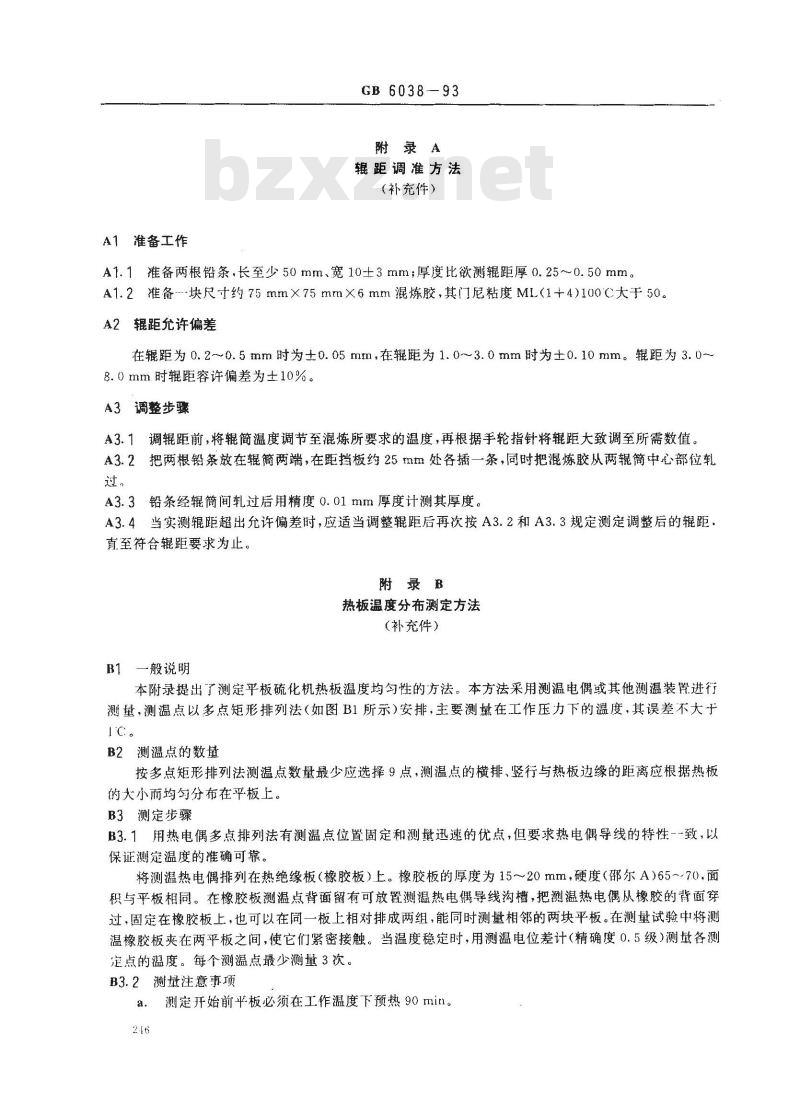
- 其它标准
- 热门标准
- 国家标准(GB)
- GB/T28784.5-2022 机械振动 船舶振动测量 第5部分:客船和商船适居性振动测量、评价和报告准则
- GB/T43456-2023 用电检查规范
- GB50236-2011 现场设备、工业管道焊接工程施工规范
- GB/T155—2006 原木缺陷
- GB/T36198-2018 土壤质量 土壤气体采样指南
- GB/T24675.5-2009 保护性耕作机械 根茬粉碎还田机
- GB50794-2012 光伏发电站施工规范
- GB/T3047.6—2007 电子设备台式机箱基本尺寸系列
- GB/T6682-2008 分析实验室用水规格和试验方法
- GB/T1768-2006 色漆和清漆 耐磨性的测定 旋转橡胶砂轮法
- GB/T29863-2023 服装制图
- GB/T39973—2021 纺织行业能源管理体系实施指南
- GB/T14652.1-2001 小艇耐火燃油软管
- GB/T1804-2000 一般公差 未注公差的线性和角度尺寸的公差
- GB6336.3-1986 模具铣刀 莫氏锥柄圆柱形球头立铣刀
- 行业新闻
请牢记:“bzxz.net”即是“标准下载”四个汉字汉语拼音首字母与国际顶级域名“.net”的组合。 ©2009 标准下载网 www.bzxz.net 本站邮件:bzxznet@163.com
网站备案号:湘ICP备2023016450号-1
网站备案号:湘ICP备2023016450号-1