- 您的位置:
- 标准下载网 >>
- 标准分类 >>
- 建筑材料行业标准(JC) >>
- JC/T 842-1999 水泥工业用单筒冷却机
标准号:
JC/T 842-1999
标准名称:
水泥工业用单筒冷却机
标准类别:
建筑材料行业标准(JC)
标准状态:
现行-
发布日期:
1999-04-09 -
实施日期:
1999-08-01 出版语种:
简体中文下载格式:
.rar.pdf下载大小:
310.49 KB

部分标准内容:
中华人民共和国建材行业标准
JC/T842-1999
水泥工业用单简冷却机
1999-04-09发布
国家建筑材料工业局
1999-08-01实施
JC/T842-1999
本标准是根据我国现行国产水泥工业用单简冷却机的基本技术要求及德国有关技术资料制定的。本标准由国家建筑材料工业局建材机械标准化技术委员会提出并归口。本标准由中国建筑材料科学研究院、国家建筑材料工业局成都建材设计研究院负资起草,天津水泥工业设计研究院、北京水泥机械总厂、朝阳重型机器厂、云南建材机械厂、四川矿山机器厂参加起草。本标准主要起草人,张朝亮李露光黄祝生夏明沫张玉慧
张志林李杰朱树志邱茂荣
1范围
中华人民共和国建材行业标准
水泥工业用单筒冷却机
Rotary cooler for cement
JC/T842-1999
本标准规定了水泥工业用单简冷却机(以下简称“单冷机”)的技术要求、试验方法、检验规则及标志、包装、运输和贮存。
本标准适用于直径为@2.2~@4.6m的各种规格的单冷机。直径超出上述规定的单冷机可参照使用。
2引用标准
下列标准所包含的条文,通过在本标准中引用而构成为本标准的条文。本标准出版时,所示版本均为有效。所有标准都会被修订,使用本标准的各方应探讨使用下列标准最新版本的可能性,GB/T321-80优先数和优先数系
GB/T699-881
优质碳索结构钢技术条件
GB/T700-88碳素结构钢
GB/T1176-87铸造铜合金技术条件GB/T1184-1996形状和位置公差未注公差值GB/T1591-94低合金高强度结构钢GB/T1804-92
GB/T3274-88
GB/T3323-87
GB/T5117—95
GB/T5118--95
GB/T8492—87
一般公差线性尺寸的未注公差
碳素结构钢和低合金结构钢热轧厚钢板和钢带钢熔化焊对接接头射线照相和质量分级碳钢焊条
低合金钢焊条
耐热钢铸件
GB/T9439-88
灰铸铁件
GB/T10095-88
GB/T11345-89
GB/T13306—91
渐开线圆柱齿轮精度
钢焊缝手工超声波探伤方法和探伤结果分级标牌
JB4730-94压力容器无损检测
JC/T355-84(1996)
水泥机械产品型号编制方法
JC/T401.2一91(1996)建材机械用碳钢和低合金钢铸件技术条件。JC/T401.3-911996)建材机械用链钢件缺陷处理规定JC/T402-91水泥机械涂漆防锈技术条件JC/T406-91水泥机械包装技术条件JC/T532-94建材机械钢焊接件通用技术条件国家建筑材料工业局1999-04-09批准各类玩注行业资免费下载
199908-01实施
ZBJ19004-88,圆柱齿轮减速器
3产品型号及规格
3.1产品型号按JC/T355执行。
JC/T842-1999
3.2产品规格及基本参数应符合表的规定表1
简体内直径系列D
简体长度L
长径比的最佳范围L/D
主传动
辅助传动
挡轮型式
托轮轴承型式
4技术要求
参数值
按GB/T321选定
机械或液压
滑动或液动
4.1基本要求
4.1.1单冷机应符合本标准的要求,并按照国家规定程序批准的图样和技术文件制造。凡本标准、图样和技术文件未规定的技术要求,按建材机械行业等有关通用技术规定执行。4.1.2图样上未注公差尺寸的极限偏差应符合GB/T1804中有关规定。即:a)切削加工部位应符合GB/T1804-92中m级,b)非切削加工部位应符合GB/T1804—92中v级。4.1.3如有特殊要求,用户与制造厂商定。4.2主要零部件技术要求
4.2.1简体
4.2.1.1材料应不低于GB/T700-88中Q235-B的性能指标4.2.1.2钢板表面质量应符合GB/T3274中的有关规定:对于厚度不小于38mm的钢板或轧制宽度超过1900mm的钢板,下料前应对成材边缘宽度为60mm的区域内进行超声波探伤检查,不得有裂纹、分层等缺陷。其质量应符合JB4730一94中I级的有关规定。4.2.1.3当简体段节沿环向拼板时,每个段节上的纵焊缝条数应符合下列规定:简体直径D≤3m时,n≤2。
简体直径D>3m时,n≤3。
最小拼板弧长不得小于1/4圆周长。4.2.1.4简体段节的最短长度不得小于1m.两支承间小于1.5m的段节不能多于两节,并应将其布置在两支承间的中间部位。
4.2.1.5各相邻段节的纵向焊缝应相互错开,其错开距离不得小于800mm。4.2.1.6焊缝对口错边量6,不得大于1.5mm,b不得大于2mm(如图1所示)。2
纵向婵缝
JC/T842-1999
环向焊缝
4.2.1.7出厂大段节两端偏差值不得大于1mm,在制造厂焊接段节两端面偏差值不得大于2mm(如图2所示)。
大段节(多节组焊后)
4.2.1.8焊前应对简体的坡口形式、尺寸进行检查,坡口处不允许有裂纹、夹渣和分层等影响质的缺陷。
4.2.1.9不等厚钢板对焊时,当两板厚度差大于5mm或超过薄板厚度的30%时,必须将段节外璧(如图3所示)的A长度范围加工成过渡斜面.其表面粗糙度Ra上限值为12.5um,A≥5(S,一S,)。4.2.1.10对焊接缝形成的校角E,不得大于3mm,E,不得大于1.5mm。图3
纵焊缝用弦长B等于D/6,且用长度不小于500mm的样板检查(如图4所示),环焊缝用长度不小于500mm的直尺检查(如图5所示)。B
JC/T842-1999
4.2.1.11简体焊缝用焊条应符合GB/T5117和GB/T5118的有关规定,应保证焊缝的机械性能不低于被焊件的机械性能。
4.2.1.12焊缝表面及热影响区不允许有裂纹等影响强度的缺陷。4.2.1.13垫板处的焊缝和垫板不得与简体焊缝重叠,应保证50mm以上的距离。4.2.1.14,简体上固定扬料板的螺栓孔不得钻在焊缝上,孔边与焊缝的距离应大于80mm。孔周不得有裂纹、分层等影响质盘的缺陷。螺栓孔的粗糙度Ra上限值为25um。4.2.1.15,焊缝咬边深度不得大于0.5mm,连续长度不大于100mm,每条焊缝的咬边总长度(焊缝两侧之和)不得超过该条焊缝长度的10%。4.2.1.16,焊缝要饱满,最低点不得低于母体金网表面。耐火材料砌筑段的焊缝不得高出简体内表面1mm,其他部位的焊缝不得高出筋体内表面及外表面3mm。4.2.1.17安装轮带和大齿圈的段节,在同一断面上最大直径与最小直径之差应小于0.0015D,其余段节小于0.002D.
4.2.1.18出厂的任意段节两端面处的圆周长公差为0.0025D,两相邻段节接口处的周长差不大于0.002D,且不得大于7mm。
4.2.1.19出厂的段节中心线的直线度:安装轮带与大齿图的段节其公差为@4mm,其余段节为@5mm,长度公差为该段节长度的0.00025L。4.2.1.20出厂段节两端焊接坡口在制造厂加工,坡口形式按设计图样规定。4.2.1.21焊缝应进行探伤,当采用超声波探伤时,应符合GB/T11345-89中1级的有关规定要求;当采用射线探伤时,应符合GB/T3323一87中1级的要求。4.2.1.22轮带下段节与垫板应紧密贴合,用0.5mm塞尺检查,最大塞入深度不大于100mm,可塞入深度小于100mm时的数量不多于两处,垫板的外圆表面需焊后加工。4.2.1.23焊接除应符合上述规定外,还应符合JC/T532的有关规定。4.2.2大齿圈
4.2.2.1材质应不低于JC/T401.2-94(1996)中有关ZG310-570的规定.铸件应正火处理,加工后齿顶圆表面的硬度值不低于170HB。4.2.2.2加工后轮缘厚度应均勾,其偏差为轮缘设计厚度的一5%~十10%。4.2.2.3大齿图基准端面的全跳动和齿项圆的圆跳动公差应符合GB/T1184-1996表B4中的8级规定。大齿图制造精度应符合GB/T10095-88中9一9—8JL级要求,分度圆直径大于@4000mm的应满足制造图标注的精度要求。
4.2.3小齿轮
4.2.3.1材质应不低于GB/T69988中有关45号锻钢的要求,调质处理后齿顶圆表面硬度值不低于201HB。且其硬度值应高于大齿圈齿顶圆表面硬度值,其差值不低于20HB。4.2.3.2齿顶圆与轴孔圆柱面的同轴度公差应符合GB/T1184-1996表B4中的8级规定。4.2.3.3小齿轮制造精度应符合GB/T10095-88中9-9-8GJ级要求。4.2.4托轮
4.2.4.1材质应不低于JC/T401.2-94(1996)中有关ZG340-640的规定。进行正火处理后,其外圆4
JC/T842-1999
表面硬度值不低于190HB,且其值应高于轮带20HB以上,4. 2.4.2托轮外圆与轴孔圆柱面的向轴度公差应符合GB/T1184-1996表B4中的9级规定。4.2.4.3加工后托轮轮缘、轮毂厚度俯差小于其设计尺寸的5%。4.2.5托轮轴
4.2.5.1材质应不低于GB/T699-88中有关45号锻钢的规定。调质处理硬度值为201241HB:4.2.5.2托轮轴轴径各配合处应符合下列要求,8)各段的同轴度公差应符合GB/T1184-1996表B4中的8级规定,b)与轴瓦配合处的圆柱度公差应符合GB/T1184—1996表B2中的8级规定e)与轴瓦、密封件配合处的表面粗糙度Ra上限值为1.6μm,与托轮配合处的Ra上限值为3.2μm.
4.2.6托轮轴承衬瓦
4.2.6.1材质应不低于GB/T1176一87中有关ZCuAl10Fe3的规定.铸件不允许有夹砂,缩孔等影响强度的缺陷。
4.2.6.2衬瓦内孔与外圆表面的同轴度公差应符合GB/T1184一1996表B4中的8级规定,内孔与两端面的垂直度公差应符合GB/T1184一1996表B3中的7级规定。4.2.7托轮球面瓦
4.2.7.1材质应不低于GB/T9439一88中有关HT200的规定,铸件不允许有裂纹、砂眼、缩孔等影响强度的缺陷,并且应进行时效处理。4.2.7.2球面瓦的球心对内孔轴线及其沿轴线的对称中心线的位登度公差为球0.10mm。4.2.7.3球面瓦需进行水压试验,无渗漏现象。4.2.8挡轮
4.2.8.1材料应不低于JC/T401.2-94(1996)中ZG340—640的规定。铸件应正火处理,圆锥工作表面硬度值不低于190HB。
4.2.8.2挡轮工作表面与轴承配合圆柱面的同轴度公差应符合GB/T1184一1996表B4中的8级规定。
4.2.8.3加工后,挡轮内外圆轮缘的厚度偏差应小于设计尺寸的5%。4.2.9轮带
4.2.9.1待造轮带的材质应不低于JC/T401.2-94(1996)中有关ZG310-570的性能指标,锻造轮带的材质不应低于GB/T699一88中有关45号锻钢的规定。工件应正火处理,加工后外圆表面硬度值不低于170HB
4.2.9.2轮带内外圆柱面的同轴度公差应符合GB/T1184一1996表B4中的8级规定。4.2.9.3加工后对箱体结构轮带的内外轮缘厚度偏差不应超过其设计厚度的一5%~十10%。4.2.10扬料斗
4.2.10.1材质应符合如下规定:高温段的扬料斗材质应不低于GB/T8492一87中ZG35Cr26Ni12的性能指标。低温段的扬料斗材质不低于GB/T1591-94中有关Q345-A的性能指标。4.2.11铸钢件的缺陷处理
4.2.11.1铸钢件缺陷的处理应符合JC/T401.3的有关规定。4.2.11.2对大齿圆、轮带、挡轮和托轮的缺陷处理还应满足下列要求,a)粗加工后各外圆表面及大齿图轮缘的缺陷,当不超过下述情况时允许补焊,切留宽度不超过工作宽度的10%,深度不超过壁厚的25%,切凿面积总和不超过各该表面总面积的2%,但连同毛坏件的切留缺陷面积在内,总和小于各该表面积的4%时:s t
b)补焊前必须预热,焊后必须进行热处理。补焊处硬度应低于母材硬度,其中心地带与母材硬度差值不得大于10%。
c)精加工后工作表面不允许补煤,JC/T842-1999
4.3装配与安装
4.3.1所有零件必须检验合格。外购件、外协件必须有质量合格证或厂内检验合格证后方可进行装配。4.3.2简体部分
4.3.2.1制造厂将过长简体分段出厂,并做好分段和对接标志。简体安装在现场进行,4.3.2.2简体安装后,各长度和轮带间距的偏差(见图6所示)应符合下列规定:LA
a)相邻两轮带中心距L,的,=0.00015L图6
b)进料端(热端)到第「档轮带的距离L,的A,=0.0003L;c)全长L的=0.0003L。
4.3.2.3大齿圈安装后径向圆跳动公差为1.5mm端面圆跳动公差为1mm。4.3.2.4各档轮带端面圆跳动公差为2mm。LA
4.3.2.5以两档轮带处简体中心连线为准,冷热两端简体中心应在该连线上,进料端(热端)的径向圆跳动公差为5mm。
4.3.3传动装置
4.3.3.1减速器应符合ZBJ19004的有关规定,并在制造厂完成组装及调试。4.3.3.2减速器低速轴与小齿轮轴的同轴度公差为@0.2mm。4.3.3.3大齿轮与小齿轮轴向相对位互的偏差为士2mm。4.3.3.4大小齿轮齿项间欧(冷态时)应在0.25m+(2~3)mm的范围内,其中m为齿轮模数。4.3.3.5大小齿轮的齿面接触斑点沿齿高不少于40%,沿齿宽不少于50%4.3.4支承装置
4.3.4.1装配时,托轮衬瓦刮研后与轴径的接触角度应为30~45,每10mm×10mm面积上接触点为1~2点,侧间隙每边保持(0.002~0.003)d,其中d为轴颈直径。4.3.4.2球面瓦和轴承底座的配合面,刮研后每25mm×25mm范围内接触点不少于1~2点,4.3.4.3安装时,托轮中心线应与简体中心线平行,平行度公差为0.1mm/m。4.3.4.4同一组托轮轴承座的中心高应相等,简差不应大于0.1mm。4.3.4.5托轮轴承冷却水系统应进行水压试验,无渗溉现象。4.3.4.6采用液压挡轮时,液压系统应按有关规定进行油压试验,无渗漏现象。4.3.5涂漆防锈要求
产品涂漆防锈应符合JC/T402的规定,未涂防锈油和防锈漆的产品不准出厂。4.4试运转要求
4.4.1空载试运转
在砌筑前和扬料装置安装后进行JC/T842-1999
4.4.1.1液压系统、冷却系统、润滑系统及泵、阀连续正常运转不少于4h,无渗漏、供油供水良好,压力稳定,各泵、阀动作灵活,准确。4.4.1.2先由辅助电机带动连续运转2h,再由主电动机带动连续运转不低于4h,传动装置无异常声响,运转平稳,电动机、轴承及轴瓦温升小于25℃,电机负荷不应超过额定功率的25%4.4.1.3轮带与托轮接触宽度不小于工作宽度的75%。4.4.1.4密封装置等处密封正常。4.4.1.5各处螺栓无松动现象。
4.4.2砌筑后试运转
砌筑后,投产前,不宜快速转动,以防衬体松动。为防简体变形,可8天左右用辅助传动侵转90°或180。投入运行前应重新检查衬体,若有松动,应加固锁牢,4.4.3负荷试运转
轴承温升不大于35℃,润滑油、动力轴(用液压挡轮时)、冷却水、压缩空气系统运行正常,压力移定,无渗漏,泵、阔灵活,动作准确,可靠。5试验方法
5.1水压试验
在0.6MPa的压力下保压10min,检查系统有无渗漏(对4.2.7.3及4.3.4.5)。5.2油压试验
在最大工作压力的1.5倍的试验压力下保压10min,检查系统有无渗漏,5.3焊缝的超声波探伤检验
按GB/T11345有关规定进行。
5.4焊缝射线探伤检验
按GB/T3323有关规定进行。
5.5钢板的超声波探伤检验
按JB4730有关规定进行。www.bzxz.net
5.6尺寸检验
未规定检测方法的尺寸用最小刻度为1mm的钢卷尺或钢直尺测量。6检验规则
6.1出厂检验
每台产品需经制造厂的质检部门检验合格后方可出厂。产品出厂必须有质检合格证书及有关技术文件。
6.2简体焊缝检验规定
6.2.1每一条焊缝都必须进行探伤检验。当用超声波探衔时,被检焊缝长度不小于该焊缝长度的25%;当用射线探伤时,被检焊缝长度不小于该焊缝长度的15%:焊缝交叉处必须检验。6.2.2对用超声波探出的焊缝可疑处,应采用射线探伤进一步评定。6.2.3对焊缝探伤检验不合格时,对该条焊缝应加倍长度检验,仍不合格时,应对该条焊缝全长范围进行检验。
6.2.4焊缝同一部位的返修次数不能超过两次,超过两次时应经施焊企业技术总负资人批准,且返修部位和次数应在产品质量证书中有所记载。6.3型式检验
专基标监行业资科免费
JC/T842-1999
有下列情况之一时,应对本标准的技术要求进行型式检验:a)新产品试制定型鉴定:
b)正常生产后,如结构、材料、工艺有较大改变,可能影响整机性能时,c)出厂检验与上次型式检验有较大差异时;d)产品停产3年后,饮复生产时。6.4判定规则
当出厂检验或型式检验结果全部符合要求时,判为合格。述各项中有一项不符合要求时,则判为该产品不合格。
7标志、包装、运输和贮存
7.1产品必须在适当而明显的位笠固定产品标牌,其形式与尺寸应符合GB/T13306的规定,并应标明下列内容:
a)产品名称和型号
b)产品标准号:
c)主要技术参数;
d)制造厂名称、厂址和商标:
e)产品编号:
f>出厂日期。
7.2产品的包装和运输应符合JC/T406的规定,并适应水上及公路运输的要求。7.3产品在安装使用前,制造厂和用户均需将零、部件妥善保管,防止锈蚀、损伤变形及丢失。7.4堆放的轮带、大齿圈等重要零、部件必须单独、水平存放,其上不允许放任何重物。长期贮存的零、部件产品需定期检查维护
7.5随机附带技术文件:
a)装箱单:
b)产品合格证书:
c)产品使用说明书,
d)产品安装图、基础图,
e)产品易损件表。
标准搜控险
中华人民共和国建材
行业标准
水泥工业用单筒冷却机
Rotary cooler for cement
JC/T842-1999
国家建筑材料工业局标准化研究所出版发行地址:北京朔阳区管庄
邮政编码:100024
电话:65755125
机械科学研充院标准出版中心印剧版权专有不得翻印
开本880×12301/16印张3/4
字数18,000
1999年5月第一版1999年5月第一次印刷印数1200
编号1126
m各美标准行业造科先费下装
小提示:此标准内容仅展示完整标准里的部分截取内容,若需要完整标准请到上方自行免费下载完整标准文档。
JC/T842-1999
水泥工业用单简冷却机
1999-04-09发布
国家建筑材料工业局
1999-08-01实施
JC/T842-1999
本标准是根据我国现行国产水泥工业用单简冷却机的基本技术要求及德国有关技术资料制定的。本标准由国家建筑材料工业局建材机械标准化技术委员会提出并归口。本标准由中国建筑材料科学研究院、国家建筑材料工业局成都建材设计研究院负资起草,天津水泥工业设计研究院、北京水泥机械总厂、朝阳重型机器厂、云南建材机械厂、四川矿山机器厂参加起草。本标准主要起草人,张朝亮李露光黄祝生夏明沫张玉慧
张志林李杰朱树志邱茂荣
1范围
中华人民共和国建材行业标准
水泥工业用单筒冷却机
Rotary cooler for cement
JC/T842-1999
本标准规定了水泥工业用单简冷却机(以下简称“单冷机”)的技术要求、试验方法、检验规则及标志、包装、运输和贮存。
本标准适用于直径为@2.2~@4.6m的各种规格的单冷机。直径超出上述规定的单冷机可参照使用。
2引用标准
下列标准所包含的条文,通过在本标准中引用而构成为本标准的条文。本标准出版时,所示版本均为有效。所有标准都会被修订,使用本标准的各方应探讨使用下列标准最新版本的可能性,GB/T321-80优先数和优先数系
GB/T699-881
优质碳索结构钢技术条件
GB/T700-88碳素结构钢
GB/T1176-87铸造铜合金技术条件GB/T1184-1996形状和位置公差未注公差值GB/T1591-94低合金高强度结构钢GB/T1804-92
GB/T3274-88
GB/T3323-87
GB/T5117—95
GB/T5118--95
GB/T8492—87
一般公差线性尺寸的未注公差
碳素结构钢和低合金结构钢热轧厚钢板和钢带钢熔化焊对接接头射线照相和质量分级碳钢焊条
低合金钢焊条
耐热钢铸件
GB/T9439-88
灰铸铁件
GB/T10095-88
GB/T11345-89
GB/T13306—91
渐开线圆柱齿轮精度
钢焊缝手工超声波探伤方法和探伤结果分级标牌
JB4730-94压力容器无损检测
JC/T355-84(1996)
水泥机械产品型号编制方法
JC/T401.2一91(1996)建材机械用碳钢和低合金钢铸件技术条件。JC/T401.3-911996)建材机械用链钢件缺陷处理规定JC/T402-91水泥机械涂漆防锈技术条件JC/T406-91水泥机械包装技术条件JC/T532-94建材机械钢焊接件通用技术条件国家建筑材料工业局1999-04-09批准各类玩注行业资免费下载
199908-01实施
ZBJ19004-88,圆柱齿轮减速器
3产品型号及规格
3.1产品型号按JC/T355执行。
JC/T842-1999
3.2产品规格及基本参数应符合表的规定表1
简体内直径系列D
简体长度L
长径比的最佳范围L/D
主传动
辅助传动
挡轮型式
托轮轴承型式
4技术要求
参数值
按GB/T321选定
机械或液压
滑动或液动
4.1基本要求
4.1.1单冷机应符合本标准的要求,并按照国家规定程序批准的图样和技术文件制造。凡本标准、图样和技术文件未规定的技术要求,按建材机械行业等有关通用技术规定执行。4.1.2图样上未注公差尺寸的极限偏差应符合GB/T1804中有关规定。即:a)切削加工部位应符合GB/T1804-92中m级,b)非切削加工部位应符合GB/T1804—92中v级。4.1.3如有特殊要求,用户与制造厂商定。4.2主要零部件技术要求
4.2.1简体
4.2.1.1材料应不低于GB/T700-88中Q235-B的性能指标4.2.1.2钢板表面质量应符合GB/T3274中的有关规定:对于厚度不小于38mm的钢板或轧制宽度超过1900mm的钢板,下料前应对成材边缘宽度为60mm的区域内进行超声波探伤检查,不得有裂纹、分层等缺陷。其质量应符合JB4730一94中I级的有关规定。4.2.1.3当简体段节沿环向拼板时,每个段节上的纵焊缝条数应符合下列规定:简体直径D≤3m时,n≤2。
简体直径D>3m时,n≤3。
最小拼板弧长不得小于1/4圆周长。4.2.1.4简体段节的最短长度不得小于1m.两支承间小于1.5m的段节不能多于两节,并应将其布置在两支承间的中间部位。
4.2.1.5各相邻段节的纵向焊缝应相互错开,其错开距离不得小于800mm。4.2.1.6焊缝对口错边量6,不得大于1.5mm,b不得大于2mm(如图1所示)。2
纵向婵缝
JC/T842-1999
环向焊缝
4.2.1.7出厂大段节两端偏差值不得大于1mm,在制造厂焊接段节两端面偏差值不得大于2mm(如图2所示)。
大段节(多节组焊后)
4.2.1.8焊前应对简体的坡口形式、尺寸进行检查,坡口处不允许有裂纹、夹渣和分层等影响质的缺陷。
4.2.1.9不等厚钢板对焊时,当两板厚度差大于5mm或超过薄板厚度的30%时,必须将段节外璧(如图3所示)的A长度范围加工成过渡斜面.其表面粗糙度Ra上限值为12.5um,A≥5(S,一S,)。4.2.1.10对焊接缝形成的校角E,不得大于3mm,E,不得大于1.5mm。图3
纵焊缝用弦长B等于D/6,且用长度不小于500mm的样板检查(如图4所示),环焊缝用长度不小于500mm的直尺检查(如图5所示)。B
JC/T842-1999
4.2.1.11简体焊缝用焊条应符合GB/T5117和GB/T5118的有关规定,应保证焊缝的机械性能不低于被焊件的机械性能。
4.2.1.12焊缝表面及热影响区不允许有裂纹等影响强度的缺陷。4.2.1.13垫板处的焊缝和垫板不得与简体焊缝重叠,应保证50mm以上的距离。4.2.1.14,简体上固定扬料板的螺栓孔不得钻在焊缝上,孔边与焊缝的距离应大于80mm。孔周不得有裂纹、分层等影响质盘的缺陷。螺栓孔的粗糙度Ra上限值为25um。4.2.1.15,焊缝咬边深度不得大于0.5mm,连续长度不大于100mm,每条焊缝的咬边总长度(焊缝两侧之和)不得超过该条焊缝长度的10%。4.2.1.16,焊缝要饱满,最低点不得低于母体金网表面。耐火材料砌筑段的焊缝不得高出简体内表面1mm,其他部位的焊缝不得高出筋体内表面及外表面3mm。4.2.1.17安装轮带和大齿圈的段节,在同一断面上最大直径与最小直径之差应小于0.0015D,其余段节小于0.002D.
4.2.1.18出厂的任意段节两端面处的圆周长公差为0.0025D,两相邻段节接口处的周长差不大于0.002D,且不得大于7mm。
4.2.1.19出厂的段节中心线的直线度:安装轮带与大齿图的段节其公差为@4mm,其余段节为@5mm,长度公差为该段节长度的0.00025L。4.2.1.20出厂段节两端焊接坡口在制造厂加工,坡口形式按设计图样规定。4.2.1.21焊缝应进行探伤,当采用超声波探伤时,应符合GB/T11345-89中1级的有关规定要求;当采用射线探伤时,应符合GB/T3323一87中1级的要求。4.2.1.22轮带下段节与垫板应紧密贴合,用0.5mm塞尺检查,最大塞入深度不大于100mm,可塞入深度小于100mm时的数量不多于两处,垫板的外圆表面需焊后加工。4.2.1.23焊接除应符合上述规定外,还应符合JC/T532的有关规定。4.2.2大齿圈
4.2.2.1材质应不低于JC/T401.2-94(1996)中有关ZG310-570的规定.铸件应正火处理,加工后齿顶圆表面的硬度值不低于170HB。4.2.2.2加工后轮缘厚度应均勾,其偏差为轮缘设计厚度的一5%~十10%。4.2.2.3大齿图基准端面的全跳动和齿项圆的圆跳动公差应符合GB/T1184-1996表B4中的8级规定。大齿图制造精度应符合GB/T10095-88中9一9—8JL级要求,分度圆直径大于@4000mm的应满足制造图标注的精度要求。
4.2.3小齿轮
4.2.3.1材质应不低于GB/T69988中有关45号锻钢的要求,调质处理后齿顶圆表面硬度值不低于201HB。且其硬度值应高于大齿圈齿顶圆表面硬度值,其差值不低于20HB。4.2.3.2齿顶圆与轴孔圆柱面的同轴度公差应符合GB/T1184-1996表B4中的8级规定。4.2.3.3小齿轮制造精度应符合GB/T10095-88中9-9-8GJ级要求。4.2.4托轮
4.2.4.1材质应不低于JC/T401.2-94(1996)中有关ZG340-640的规定。进行正火处理后,其外圆4
JC/T842-1999
表面硬度值不低于190HB,且其值应高于轮带20HB以上,4. 2.4.2托轮外圆与轴孔圆柱面的向轴度公差应符合GB/T1184-1996表B4中的9级规定。4.2.4.3加工后托轮轮缘、轮毂厚度俯差小于其设计尺寸的5%。4.2.5托轮轴
4.2.5.1材质应不低于GB/T699-88中有关45号锻钢的规定。调质处理硬度值为201241HB:4.2.5.2托轮轴轴径各配合处应符合下列要求,8)各段的同轴度公差应符合GB/T1184-1996表B4中的8级规定,b)与轴瓦配合处的圆柱度公差应符合GB/T1184—1996表B2中的8级规定e)与轴瓦、密封件配合处的表面粗糙度Ra上限值为1.6μm,与托轮配合处的Ra上限值为3.2μm.
4.2.6托轮轴承衬瓦
4.2.6.1材质应不低于GB/T1176一87中有关ZCuAl10Fe3的规定.铸件不允许有夹砂,缩孔等影响强度的缺陷。
4.2.6.2衬瓦内孔与外圆表面的同轴度公差应符合GB/T1184一1996表B4中的8级规定,内孔与两端面的垂直度公差应符合GB/T1184一1996表B3中的7级规定。4.2.7托轮球面瓦
4.2.7.1材质应不低于GB/T9439一88中有关HT200的规定,铸件不允许有裂纹、砂眼、缩孔等影响强度的缺陷,并且应进行时效处理。4.2.7.2球面瓦的球心对内孔轴线及其沿轴线的对称中心线的位登度公差为球0.10mm。4.2.7.3球面瓦需进行水压试验,无渗漏现象。4.2.8挡轮
4.2.8.1材料应不低于JC/T401.2-94(1996)中ZG340—640的规定。铸件应正火处理,圆锥工作表面硬度值不低于190HB。
4.2.8.2挡轮工作表面与轴承配合圆柱面的同轴度公差应符合GB/T1184一1996表B4中的8级规定。
4.2.8.3加工后,挡轮内外圆轮缘的厚度偏差应小于设计尺寸的5%。4.2.9轮带
4.2.9.1待造轮带的材质应不低于JC/T401.2-94(1996)中有关ZG310-570的性能指标,锻造轮带的材质不应低于GB/T699一88中有关45号锻钢的规定。工件应正火处理,加工后外圆表面硬度值不低于170HB
4.2.9.2轮带内外圆柱面的同轴度公差应符合GB/T1184一1996表B4中的8级规定。4.2.9.3加工后对箱体结构轮带的内外轮缘厚度偏差不应超过其设计厚度的一5%~十10%。4.2.10扬料斗
4.2.10.1材质应符合如下规定:高温段的扬料斗材质应不低于GB/T8492一87中ZG35Cr26Ni12的性能指标。低温段的扬料斗材质不低于GB/T1591-94中有关Q345-A的性能指标。4.2.11铸钢件的缺陷处理
4.2.11.1铸钢件缺陷的处理应符合JC/T401.3的有关规定。4.2.11.2对大齿圆、轮带、挡轮和托轮的缺陷处理还应满足下列要求,a)粗加工后各外圆表面及大齿图轮缘的缺陷,当不超过下述情况时允许补焊,切留宽度不超过工作宽度的10%,深度不超过壁厚的25%,切凿面积总和不超过各该表面总面积的2%,但连同毛坏件的切留缺陷面积在内,总和小于各该表面积的4%时:s t
b)补焊前必须预热,焊后必须进行热处理。补焊处硬度应低于母材硬度,其中心地带与母材硬度差值不得大于10%。
c)精加工后工作表面不允许补煤,JC/T842-1999
4.3装配与安装
4.3.1所有零件必须检验合格。外购件、外协件必须有质量合格证或厂内检验合格证后方可进行装配。4.3.2简体部分
4.3.2.1制造厂将过长简体分段出厂,并做好分段和对接标志。简体安装在现场进行,4.3.2.2简体安装后,各长度和轮带间距的偏差(见图6所示)应符合下列规定:LA
a)相邻两轮带中心距L,的,=0.00015L图6
b)进料端(热端)到第「档轮带的距离L,的A,=0.0003L;c)全长L的=0.0003L。
4.3.2.3大齿圈安装后径向圆跳动公差为1.5mm端面圆跳动公差为1mm。4.3.2.4各档轮带端面圆跳动公差为2mm。LA
4.3.2.5以两档轮带处简体中心连线为准,冷热两端简体中心应在该连线上,进料端(热端)的径向圆跳动公差为5mm。
4.3.3传动装置
4.3.3.1减速器应符合ZBJ19004的有关规定,并在制造厂完成组装及调试。4.3.3.2减速器低速轴与小齿轮轴的同轴度公差为@0.2mm。4.3.3.3大齿轮与小齿轮轴向相对位互的偏差为士2mm。4.3.3.4大小齿轮齿项间欧(冷态时)应在0.25m+(2~3)mm的范围内,其中m为齿轮模数。4.3.3.5大小齿轮的齿面接触斑点沿齿高不少于40%,沿齿宽不少于50%4.3.4支承装置
4.3.4.1装配时,托轮衬瓦刮研后与轴径的接触角度应为30~45,每10mm×10mm面积上接触点为1~2点,侧间隙每边保持(0.002~0.003)d,其中d为轴颈直径。4.3.4.2球面瓦和轴承底座的配合面,刮研后每25mm×25mm范围内接触点不少于1~2点,4.3.4.3安装时,托轮中心线应与简体中心线平行,平行度公差为0.1mm/m。4.3.4.4同一组托轮轴承座的中心高应相等,简差不应大于0.1mm。4.3.4.5托轮轴承冷却水系统应进行水压试验,无渗溉现象。4.3.4.6采用液压挡轮时,液压系统应按有关规定进行油压试验,无渗漏现象。4.3.5涂漆防锈要求
产品涂漆防锈应符合JC/T402的规定,未涂防锈油和防锈漆的产品不准出厂。4.4试运转要求
4.4.1空载试运转
在砌筑前和扬料装置安装后进行JC/T842-1999
4.4.1.1液压系统、冷却系统、润滑系统及泵、阀连续正常运转不少于4h,无渗漏、供油供水良好,压力稳定,各泵、阀动作灵活,准确。4.4.1.2先由辅助电机带动连续运转2h,再由主电动机带动连续运转不低于4h,传动装置无异常声响,运转平稳,电动机、轴承及轴瓦温升小于25℃,电机负荷不应超过额定功率的25%4.4.1.3轮带与托轮接触宽度不小于工作宽度的75%。4.4.1.4密封装置等处密封正常。4.4.1.5各处螺栓无松动现象。
4.4.2砌筑后试运转
砌筑后,投产前,不宜快速转动,以防衬体松动。为防简体变形,可8天左右用辅助传动侵转90°或180。投入运行前应重新检查衬体,若有松动,应加固锁牢,4.4.3负荷试运转
轴承温升不大于35℃,润滑油、动力轴(用液压挡轮时)、冷却水、压缩空气系统运行正常,压力移定,无渗漏,泵、阔灵活,动作准确,可靠。5试验方法
5.1水压试验
在0.6MPa的压力下保压10min,检查系统有无渗漏(对4.2.7.3及4.3.4.5)。5.2油压试验
在最大工作压力的1.5倍的试验压力下保压10min,检查系统有无渗漏,5.3焊缝的超声波探伤检验
按GB/T11345有关规定进行。
5.4焊缝射线探伤检验
按GB/T3323有关规定进行。
5.5钢板的超声波探伤检验
按JB4730有关规定进行。www.bzxz.net
5.6尺寸检验
未规定检测方法的尺寸用最小刻度为1mm的钢卷尺或钢直尺测量。6检验规则
6.1出厂检验
每台产品需经制造厂的质检部门检验合格后方可出厂。产品出厂必须有质检合格证书及有关技术文件。
6.2简体焊缝检验规定
6.2.1每一条焊缝都必须进行探伤检验。当用超声波探衔时,被检焊缝长度不小于该焊缝长度的25%;当用射线探伤时,被检焊缝长度不小于该焊缝长度的15%:焊缝交叉处必须检验。6.2.2对用超声波探出的焊缝可疑处,应采用射线探伤进一步评定。6.2.3对焊缝探伤检验不合格时,对该条焊缝应加倍长度检验,仍不合格时,应对该条焊缝全长范围进行检验。
6.2.4焊缝同一部位的返修次数不能超过两次,超过两次时应经施焊企业技术总负资人批准,且返修部位和次数应在产品质量证书中有所记载。6.3型式检验
专基标监行业资科免费
JC/T842-1999
有下列情况之一时,应对本标准的技术要求进行型式检验:a)新产品试制定型鉴定:
b)正常生产后,如结构、材料、工艺有较大改变,可能影响整机性能时,c)出厂检验与上次型式检验有较大差异时;d)产品停产3年后,饮复生产时。6.4判定规则
当出厂检验或型式检验结果全部符合要求时,判为合格。述各项中有一项不符合要求时,则判为该产品不合格。
7标志、包装、运输和贮存
7.1产品必须在适当而明显的位笠固定产品标牌,其形式与尺寸应符合GB/T13306的规定,并应标明下列内容:
a)产品名称和型号
b)产品标准号:
c)主要技术参数;
d)制造厂名称、厂址和商标:
e)产品编号:
f>出厂日期。
7.2产品的包装和运输应符合JC/T406的规定,并适应水上及公路运输的要求。7.3产品在安装使用前,制造厂和用户均需将零、部件妥善保管,防止锈蚀、损伤变形及丢失。7.4堆放的轮带、大齿圈等重要零、部件必须单独、水平存放,其上不允许放任何重物。长期贮存的零、部件产品需定期检查维护
7.5随机附带技术文件:
a)装箱单:
b)产品合格证书:
c)产品使用说明书,
d)产品安装图、基础图,
e)产品易损件表。
标准搜控险
中华人民共和国建材
行业标准
水泥工业用单筒冷却机
Rotary cooler for cement
JC/T842-1999
国家建筑材料工业局标准化研究所出版发行地址:北京朔阳区管庄
邮政编码:100024
电话:65755125
机械科学研充院标准出版中心印剧版权专有不得翻印
开本880×12301/16印张3/4
字数18,000
1999年5月第一版1999年5月第一次印刷印数1200
编号1126
m各美标准行业造科先费下装
小提示:此标准内容仅展示完整标准里的部分截取内容,若需要完整标准请到上方自行免费下载完整标准文档。

标准图片预览:
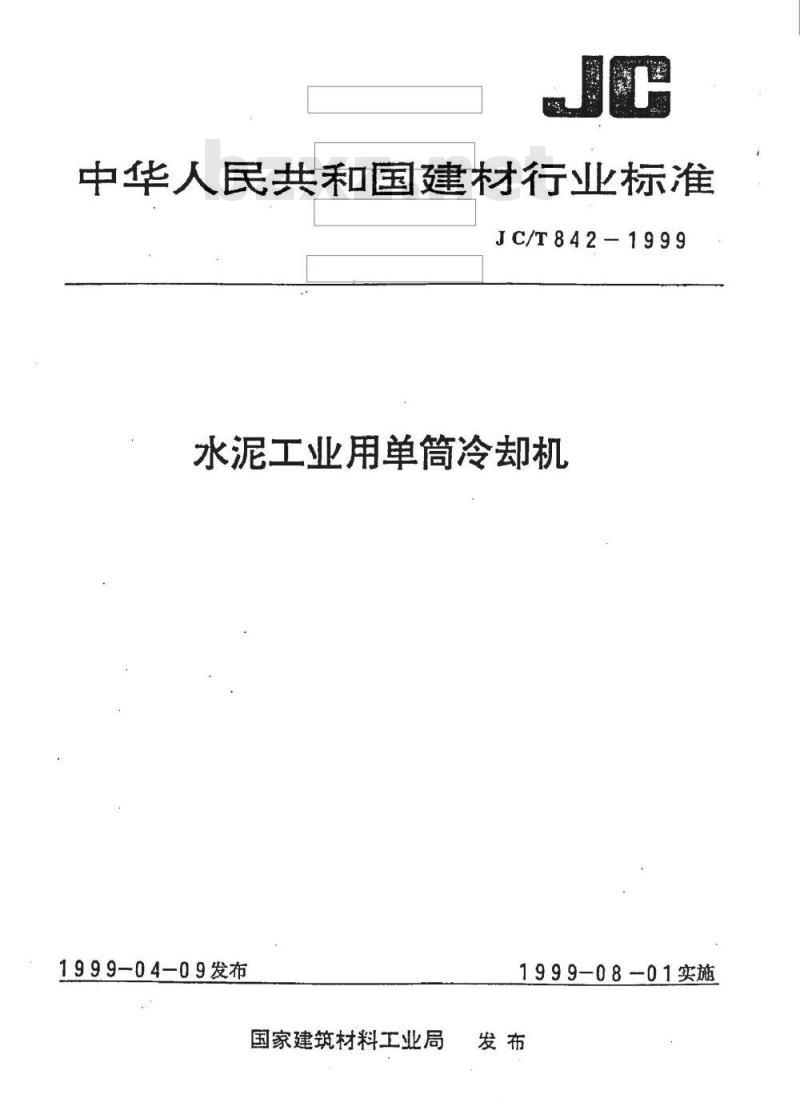

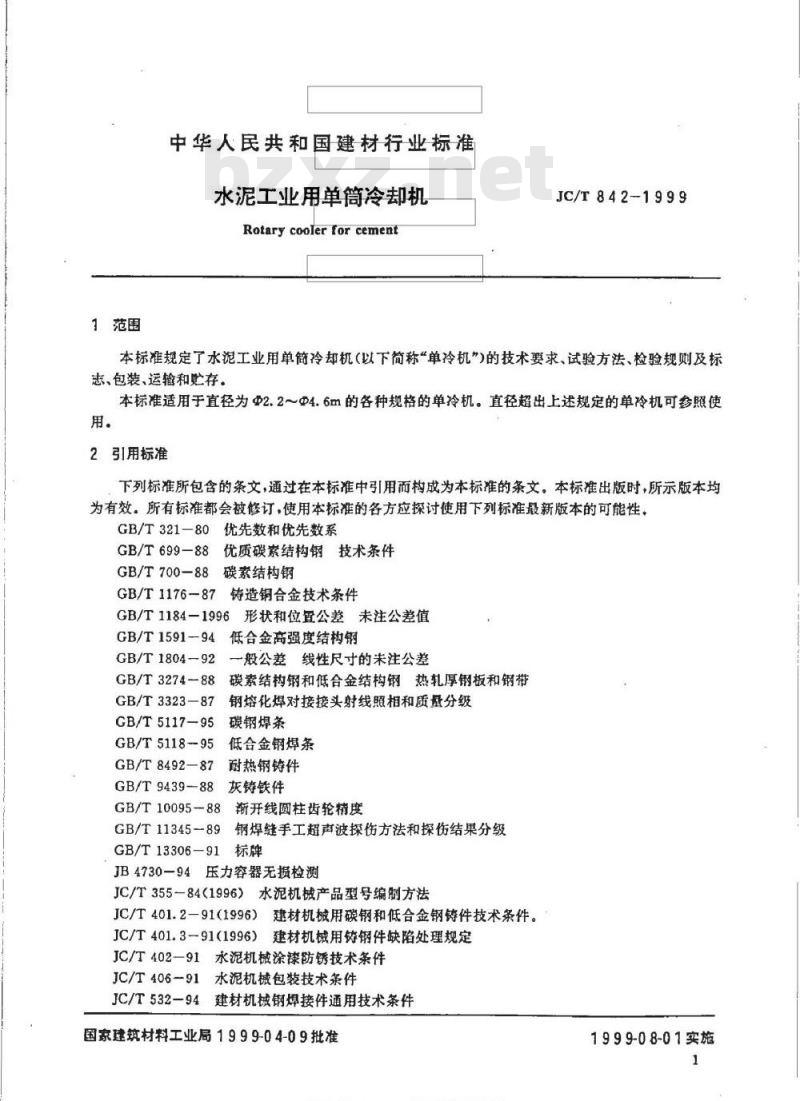
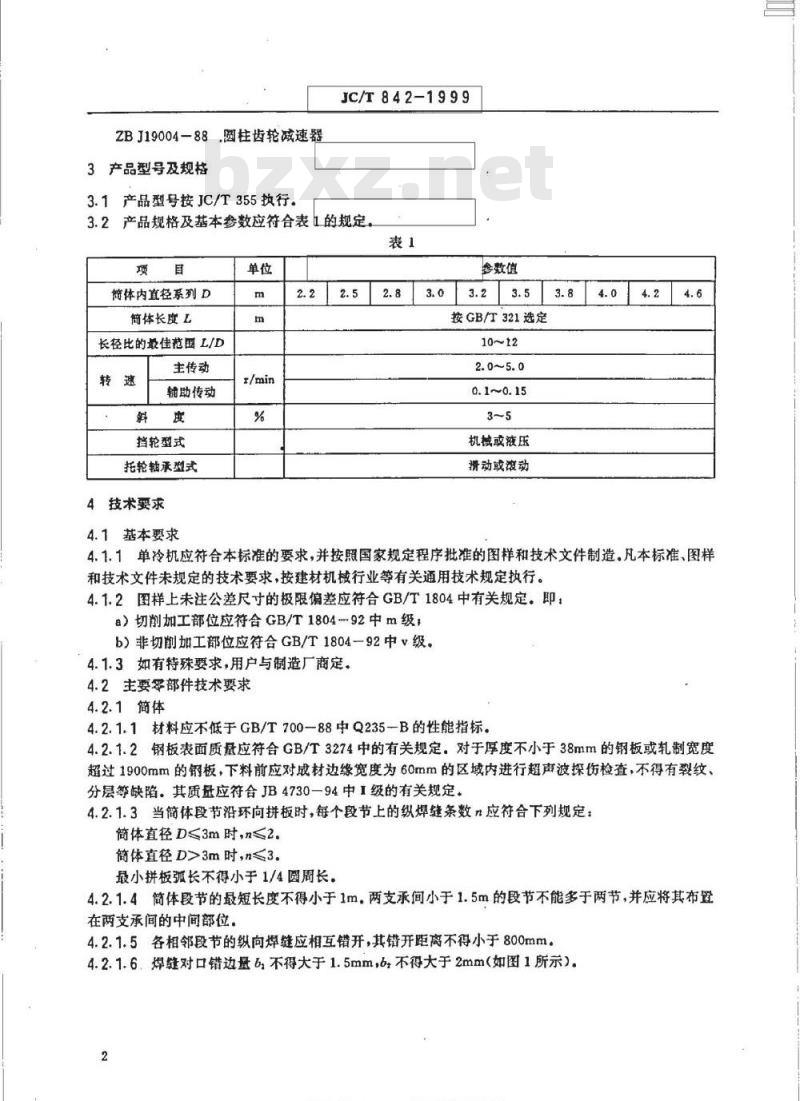
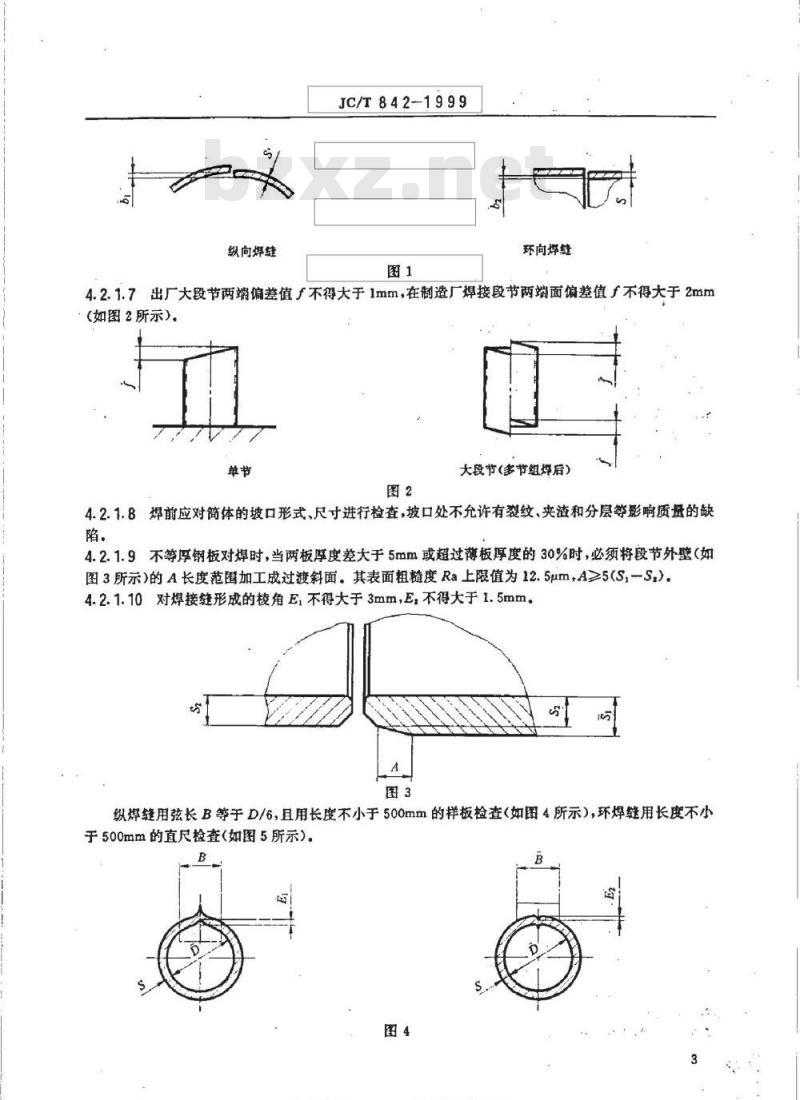
- 其它标准
- 热门标准
- 建筑材料行业标准(JC)
- JC/T781-2006 蜂窝型芯子胶条分离强度试验方法
- JC/T907-2002 混凝土界面处理剂
- JC/T175-2007 玻璃纤维套管坯管
- JC/T2217-2014 环氧树脂防水涂料
- JC/T225-2012 液位计用透明石英玻璃管
- JC/T2209-2014 氧化铝陶瓷衬板耐磨管件
- JC/T514.3-1993 铸石制品 铸石粉
- JC/T877-2007 预应力钢筒混凝土管和三阶段管用辊射机
- JC/T720-2011 蒸压釜
- JC/T185-1996 光学石英玻璃
- JC/T617-1996 纤维玻璃室热平衡测定与计算方法
- JC/T453-1992(1996) 自应力水泥物理检验方法
- JC/T1034-2007 预应力钢筒混凝土管管模
- JC/T463-2006 水泥工业用气力提升泵
- JC/T1093-2009 树脂装饰砖
请牢记:“bzxz.net”即是“标准下载”四个汉字汉语拼音首字母与国际顶级域名“.net”的组合。 ©2009 标准下载网 www.bzxz.net 本站邮件:bzxznet@163.com
网站备案号:湘ICP备2023016450号-1
网站备案号:湘ICP备2023016450号-1