- 您的位置:
- 标准下载网 >>
- 标准分类 >>
- 国家标准(GB) >>
- GB/T 16856-1997 机械安全风险评价的原则
标准号:
GB/T 16856-1997
标准名称:
机械安全风险评价的原则
标准类别:
国家标准(GB)
标准状态:
已作废-
发布日期:
1997-06-06 -
实施日期:
1998-01-01 -
作废日期:
2009-04-01 出版语种:
简体中文下载格式:
.rar.pdf下载大小:
408.42 KB
标准ICS号:
环保、保健与安全>>13.110机械安全中标分类号:
机械>>机械综合>>J09卫生、安全、劳动保护
替代情况:
被GB/T 16856.1-2008代替采标情况:
PREN 1050-1994,EQV

点击下载
标准简介:
标准下载解压密码:www.bzxz.net
本标准描述了被称之为风险评价的程序,通过这种程序将有关机械的设计、使用、事件、事故和伤害的知识和经验汇集到一起,以进行机器寿命周期内各种风险的评价。 GB/T 16856-1997 机械安全风险评价的原则 GB/T16856-1997

部分标准内容:
GB/T16856—1997
本标准等效采用欧洲标准(草案)prEN1050—1994《机械安全—~风险评价的原则》,在一般要素上和补充要素上有以下两点差异:1.引用标准的导言是按GB/T1.1的规定编写的,并将原标准中引用的欧洲标准改为相应的国家标准;
2.取消了原提示的附录B\分析危险和评估风险的方法”。因为这些“方法”只是作为提示信息给出的,无法进行具体的操作。
本标准的附录 A是提示的附录。本标准由中华人民共和国机械工业部提出。本标准由全国机械安全标准化技术委员会归口。本标准由机械部机械科学研究院负责起草。本标准主娶起草人:张尔正、李勤、马贤智、徐自芬、萧维、张铭续。759
0引言
中华人民共和国国家标准
风险评价的原则
机械安全)
Safety of machinery-
Principles for risk assessmentGB/T 16856-1997
本标准规定了供风险评价(见GB/T15706.1一1995第6章)用的统一系统原则。本标准给出了机械设计(见GB/T15706.1-1995的3.11)过程中的决策指南,它将有助于制定B类和C类标准中统一、合适的安全要求,以便符合GB/T15706.2中规定的基本安全要求。建议将本标准纳入培训教程和手册,以对设计方法给予基本指导。1范围
本标准描述了被称之为风险评价的程序,通过这种程序将有关机械的设计、使用、事件、事故和伤害的知识和经验汇集到一起,以进行机器寿命周期内各种风险的评价。本标准给出了赖以进行风险评价所需要的信息指南。规定了识别危险、评估和评定风险的程序。本标准的目的是对有关机械安全问题及为验证风险评价所需的文件类型问题进行决策时提供建议。本标准对分析危险和评估风险的方法不作详细规定。这种详细规定在其他文献(如教科书或其他参考文件)中另有述及。
2 引用标准
下列标准所包含的条文,通过在本标准中引用而构成本标准的条文。本标准出版时,所有版本均为有效。所有标准都会被修订,使用本标准的各方应探讨使用下列标准最新版本的可能性。GB/T5226.1--1996.工业机械电气设备第1部分:般要求GB/T15706.1--1995机械安全基本概念与设计通则第1部分基本术语、方法学GB/T15706.2-1995机械安全基本概念与设计通则第2部分:技术原则与规范3定义
除GB/T15706.1给出的定义外,本标准还采用以下定义:3.1伤害.harm
对健康或财产的物理损伤和/或危害。3.2危险事件hazardous event
引起伤害的事件。
3.3遗留风险residual risk
采取安全措施之后所剩余的风险。3.4安全措施safetymeasure
消除危险或减小风险的手段。(见GB/T15706.1—1995的第5章)国家技术监督局1997-06-06批准760
1998-01-01实施
4总则
4.1基本概念
GB/T16856-1997
风险评价是以系统方式对与机械有关的危险进行考察的一系列逻辑步骤。当需要时,风险评价后应按照GB/T15706.1一1995第5章所描述的方法减小风险。当重复这一过程时,就可达到尽可能消除危险和根据现有工艺水平实施安全措施的送代过程(见图1)。开始
机械限制的确定(第5章)
危险识别(第6章)
风险评估(第7章)
风险评定(第8章)
风险减小方案分析
(见注和附录A)
机器是安全的吗?
风险分析
风险评价
注:减小风险和选择适当的安全措施不是风险评价的内容,进一步的解释见GB/T15706.1一1995第5章和GB/T 15706.2
图1实现安全的选代过程
风险评价包括
风险分析
1)机械限制的确定(第5章)
2)危险识别(第6章)
3)风险评估(第7章)
-风险评定(第8章)
风险分析提供了风险评定所需的信息,有了这种信息就可对机械安全做出判断。风险评价依赖于判断决定。这些决定应通过定性的方法来支持,并尽可能通过定量方法补充。当可预见伤害严重度高且范大时,定量法是特别合适的。定量法对评价可替换的安全措施和决定何种防护更好是有用的。注:由于定量法的使用受可得到的有用数据量的限制,因此,在许多应用场合,只能使用定性的风险评价。风险评价的程序应以形成文件的方式进行:已进行过评价的机械的预期使用(技术规范、限制等);所识别的危险、危险状态和危险事件;使用的有关信息(事故历史,由对类似机器进行减小风险获得的经验等),-通过安全措施要达到的目标;
为消除识别的危险或减小风险所实施的安全措施;761
GB/T16856—1997
一通过规定某种有关假设(载荷、安全因素等)后,各种危险的遗留风险。4.2风险评价信息
风险评价信息和定性、定量分析应包括以下内容:—机械的限制(GB/T15706.1--1995的5.1);机械各寿命阶段的要求(见GB/T15706.1--1995的3.11a),一规定机械特性的设计图样或其他手段,—有关动力源的信息;
事故或事件的历史(如果可得到的话):有损健康的任何信息。
当设计改进和需更改时,信息也应适时更新。假如能得到那些危险状态中的有关危险和事故环境的足够信息,可对不同类型机械的类似危险状态进行比较通常是可行的。
在事故历史不明的情况下,不应根据少量事故及严重性不大的事故主观做出低风险推测。对于定量评价,可以使用数据库、手册、实验室和制造厂技术规范中的数据(假如对它们的适用性有把握的话)。有关该数据的不确定度应在文件中指明(见第9章)。专家一致认可的经验数据可作为补充定性数据。5 机械限制的确定
风险评价应考虑:
—机器寿命的各个阶段(见GB/T15706.1—1995的3.11a)。机械的限制,包括预定使用(见GB/T15706.1一1995的5.1),除了合理预见的误用和失灵的后果外,还应包括机器的正确使用和正确操作两方面。另外,风险评价还应适当根据人的情况来考虑:可预见的机械(如工业用、非工业用和家用)全部使用范围,人的情况可依据性别、年龄及用手习惯或体能限制(如视力或听力损伤、身材大小、体力强弱)来确定。一可预见的使用者预期训练水平、经验或能力,例如:1)经过培训的热练技术维修人员;2)经过培训的操作人员,
3)学员和初学者,
4)一般人员,bzxZ.net
一一暴露于可合理预见机械危险场合的其他人员。6危险识别
应识别与机械有关的所有危险、危险状态和危险事件。附录A(提示的附录)给出的例子有助于这种识别(描述由机械产生危险的进一步信息参见GB/T15706.1一1995的第4章)。7风险评估
危险识别(第6章)后,对一种危险都应通过测定7.1给出的风险要素进行风险评估。在测定这些风险要素时,需考虑7.2给出的几个方面。7.1风险要素
与特殊情况或技术过程相关的风险由以下要素组合得出:一伤害的严重度;
伤害出现的概率;
置)。
GB/T16856--1997
1)人员暴露于危险中的频次和持续时间,2)危险事件出现的概率;
-在技术上和人为方面避免或限制伤害的可能性(如对风险的了解、降低速度、急停装置、使动装风险要素示于图2中,附加细节在7.1.1和7.1.2中给出。注:在许多情况下,这些风险要素不能被精确地测定,而只能估计。这特别适用于可能伤害出现的概率。在基些情况(如由于有毒物质或精神压力有损健康的情况)下,可能伤害的严重度不容易确定。为改普这种情况,可使用附加辅助值即所谓的风险参数,以方便风险评估,总的来说,特别适用于这种情况的风险参数型式取决于所涉及的危险类型。
伤害出现的概率
景露的频次及持续时间
与所考患的
危险有关的
7.1.1严重度(可能伤害的程度)该危险可
能伤害的
严重度
危险事件出现的概率
避免或限制伤客的可能性
图2风险要素
严重度可通过考虑以下因素评估:防护对象的性质:
1)人,
2)财产,
3)环境。
损伤的严重度(对人的情况):1)轻度(可正常恢复的)损伤或危害健康;2)严重(不能正常恢复的)损伤或危害健康;3)死亡。
-伤害的限度(对每台机器)。对人的情况:1)一个人
2)几个人。
7.1.2伤害出现的概率
伤害出现的概率可通过考虑7.1.2.1到7.1.2.3来进行评估:7.1.2.1暴露的题次和持续时间:接近危险的需要(如生产的原因、维护或修理),-接近的性质(如手动送料),
-处于危险区的时间;
需要接近危险的人数;
一进入危险区的频次。
7.1.2.2危险事件出现的概率
-可靠性和其他统计数据;
事故历史;
风险比较。
的函数
GB/T16856-1997
注:危险事件的出现可能源于技术的或人的原因。7.1.2.3避免或限制伤害的可能性一机器是
1)由熟练工操作;
2)由非熟练工操作;或
3)无人操作。
危险事件出现的速度:
1)突然;
2)快;
3)慢。
对风险的了解;
1)一般信息;
2)直接观察,
3)通过指示装置,
一人员避免危险的可能性(如反应、灵敏性、逃脱的可能性):1)可能;
2)在某些情况下可能;
3)不可能。
一实践经验和知识:
1)该机械的;
2)类似机械的;
3)没经验的。
7.2确定风险要素应考虑的诸方面7.2.1暴露的人员
风险估计应考虑所有暴露于危险中的人员,包括操作者、维修人员和可合理预见的可能受到机器影响的其他人员。
7.2.2暴露的类型、频次和持续时间对所考虑危险中暴露的评估,需要分析并应说明机器的各种操作模式和使机器工作的方法。这尤其影响到在设定、示教、过程转换或调整、清理、查找故障和维修(见GB/T15706.1--1995的3.11)期间进入危险区的需要。
当必须暂停安全功能时(如维修期间),风险评估应说明这种情况。7.2.3暴露和影响之间的关系
当确定在一种危险中的暴露及其影响之间的关系时,就可行而言,风险评估应根据合适的认可数据。
注:事故数据可用来表明与具有特定安全措施的特定型式机械的使用有关的损伤概率和严重度。7.2.4人的因素
风险评估应不限于技术因素。风险可能受人为因素的影响,诸如,一方面,与机械的相互作用有关的、与人们之间的相互作用有关的、与心理学有关的和与人类工效影响有关的因素,另一方面,与认识在给定条件下风险的能力高低有关的因素。这种情况取决于操作者和可能受影响的其他人的培训情况、经验和能力。
对暴露于危险中的人员能力的评估应考虑以下几个方面:一与人类工效学原则有关的机械设计;一执行所需任务固有的或被开发的能力;764
——对各种风险的认识;
GB/T16856—1997
一如果不发生有意或无意差错时执行所需任务的把握程度;一一防止诱使偏离规定的和必要的安全工作规程的能力。训练、经验和能力都会影响到风险,但是它们都不能用来代替可能通过设计或安全防护来消除危险、减小风险的措。
7.2.5安全功能的可靠性
风险评估应考虑元件和系统的可靠性。尤其是判定作为主要安全功能(见GB/T15706.1一1995的3.13.1)部分的元件和系统应受到特别注意。评估应:一一判明可能导致伤害的环境(例如,元件故障,电气干扰);一一当合适时,使用定量法比较可供选择的安全措施;—一提供用以选择适当的安全功能、元件和装置的信息:对承担一种安全功能的有关安全装置不只一个时,选择这些装置需考虑它们的性能和可靠性应是协调一致的。
当安全措施包括工作组织、正确行为、小心注意、应用个体防护装备、技能或培训时,在风险评估中必须考虑到:这些措施与经过验证的技术措施相比,可靠性相对较低。7.2.6毁坏或避开安全措施的能力风险评估应说明某一一特定安全措施被轻易毁坏或避开的可能性。风险评估还应考虑毁坏或避开系统的诱因。如:
是否安全措施延缓了生产或干扰使用者的某些其他活动或选择;一安全措施难以使用;
——是否涉及操作者以外的人员;一安全措施的功能是否未被认可或接受。毁坏安全措施的能力可能取决于安全措施的类型及其设计细节两方面。如果对有关安全软件的存取设计和监控不当,使用可编程电子系统会导致毁坏或避开安全措施的附加可能性。风险评估应判明有关安全功能在什么地方没与其他机器功能分开和存取可能达到的范围。当为诊断或过程校正需要遥控存取时,这是特别重要的(见GB/T5226.1—1995的12.3.5)。当进行风险评估时,需要考虑毁坏或避开可调防护装置和可编程自动停机装置的可能性。7.2.7保持安全措施的能力
风险评估应考虑安全措施是否能保持在为提供需要的防护水平所必需的状态。注:如果安全措施不容易保持在正确工作状态下,为了使机械连续使用,这可能促使毁坏或邀开安全措施。7.2.8使用信息
风险评估应考虑随机械提供的使用信息。应考虑妥善地实施GB/T15706.2--1995第5章的要求。8风险评定
风险评估后,要进行风险评定,以确定是否需要减小风险或是否达到了安全。如果风险需要减小,则应选择和应用相应的安全措施,并应重复该程序(见图1)。在这种选代过程中,重要的是当应用新的安全措施时,设计者应核对是否又产生了附加危险。如果附加危险的确出现了,则这些危险应列入到危险识别清单中。
风险减小目标的实现(见8.1)和风险比较的有效结果(见8.2)可以使人确信机械是安全的(见GB/T15706.1—-1995的3.4)。
8.1风险减小目标的实现
下列条件的实现(见GB/T15706.1—1995的表2和GB/T15706.2-1995的3~6)将表明减小风765
险的过程可以结束:
GB/T16856—1997
通过以下措施消除了危险或减小了风险:1)通过设计或替代稍有危险的材料或物质,和/或2)按照现有工艺水平进行安全防护;所选的安全防护类型是经过验证的,对预期使用能起到充分的防护;针对以下儿种情况,所选择的防护类型是合适的:1)毁坏或避开的概率,
2)伤害的严重度,
3)对执行所要求任务的妨碍,
有关机械的预定使用信息十分清楚;一使用机械的操作程序与使用该机械的人员或可能暴露于与该机械有关的危险中的其他人员的能力协调一致;
推荐的该机械使用安全操作规程和有关的培训要求已充分说明;一关于遗留风险已充分告知了用户;一如果推荐用个体防护装备来对付遗留风险,对这种防护装备的需要和使用该防护装备的培训要求已充分说明;
附加预防措施是充分的(GB/T15706.2-—1995的第6章)。8.2风险比较
只要下列判定适用,作为风险评定过程的一部分,与机械有关的风险可与类似机械的风险相比较:类似机械证明了按照现有工艺水平风险减小是可接受的,两种机械的预定使用和所采用的工艺都是可比的,危险和风险要素是可比的,
技术目标是可比的,
一使用条件是可比的。
使用这种比较方法不排除在特定使用条件下(如用于切肉的带锯机与用于切割木材的带锯机相比较时应评价与材料变化有关的风险)还需要遵循本标准描述的风险评价过程。9文件
形成风险评价文件是描述所识别的危险和实施安全措施的一种手段。文件应包含以下充分的信息:
风险评价所依据的信息(见4.2);已经评价过的机械(规范、限制等);已做过某些有关假设,如载荷、强度、安全因素等,判明的危险:
判明的危险状态;
-在评价中考虑的危险事件,
一使用的数据及原始资料;
与使用的数据有关的不确定度和对风险评价的影响;一通过安全措施达到的目标;
一某些补充要求(如使用的标准或其他规范);一关于遗留风险的信息;
一最终风险评定的结果。
A1机械危险
GB/T16856—1997
附录A
(提示的附录)
危险、危险状态和危险事件的例子A1.1由机器零件产生的或由工件引起的(见GB/T15706.1—1995的4.2和GB/T15706.2—1995的3.2)
A1.1.1形状
A1.1.2相对位置
A1.1.3质量和稳定性(在重力的影响下可以运动的元件位能)A1.1.4质量和速度(受控或非受控运动元件的动能)A1.1.5机械强度不合适
A1.2机械内部能量积累引起的,例如由:A1.2.1弹性元件(弹簧)
A1.2.2压力下的液体和气体
A1.2.3真空影响
A1.3机械危险的基本形式
挤压危险(见GB/T15706.1—1995的4.2.1)A1.3.1E
A1.3.2剪切危险(见GB/T15706.1—1995的4.2.1)A1.3.3切割或切断危险(见GB/T15706.1--1995的4.2.1)缠绕危险(见GB/T15706.1—1995的4.2.1)A1.3. 4
A1.3.5引入或卷人危险(见GB/T15706.1--1995的4.2.1)A1.3.6冲击危险(见GB/T15706.1—1995的4.2.1)A1.3.7刺伤或扎伤危险(见GB/T15706.1--1995的4.2.1)A1.3.8摩擦或磨损危险(见GB/T15706.1--1995的4.2.1)A1.3.9高压流体喷射或抛射危险(见GB/T15706.1-1995的4.2.1)A2电的危险(见GB/T15706.1—1995的4.3和GB/T15706.2—1995的3.9),由于A2.1人与带电零件接触(直接接触)A2.2人与在故障条件下变为带电的零件接触(间接接触)(见GB/T15706.1-1995的4.3)A2.3趋近于高压下的带电零件
A2.4静电现象(见GB/T15706.1—1995的4.3)A2.5热辐射或其他现象例如由于短路或过载等而引起的熔化粒子喷射和化学效应(见GB/T15706.1—1995的4.3)
A3热危险(见GB/T15706.1--1995的4.4)导:A3.1由可能与人接触的火焰或爆炸也可能由热源辐射引起燃烧和烫伤(见GB/T15706.1--1995的4.4)
A3.2由于热的或冷的工作环境影响对健康的危害(见GB/T15706.1-—1995的4.4)767
CB/T 16856-1997
A4由噪声产生的危险(见GB/T15706.1--1995的4.5),导致A4.1听力损失(耳聋)、其他生理异常(例如失去平衡,失去知觉)(见GB/T15706.1—1995的4.5)A4.2对语言通讯和听觉信号等的于扰(见GB/T15706.1一1995的4.5)A5由振动产生的危险
A5.1使用手持式机器导致神经病变和血脉失调(见GB/T15706.1—1995的4.6)A5.2尤其当与不良的姿势结合时的全身振动A6由辐射产生的危险(见GB/T15706.1—1995的4.7)A6.1低频、无线频率辐射、微波(见GB/T15706.1--1995的4.7)A6.2红外线、可见光和紫外光
A6.3X和射线(见GB/T15706.1—1995的4.7)A6.4α和β射线、电子或离子束、中子(见GB/T15706.1--1995的4.7)A6.5激光(见GB/T15706.1-1995的4.7)A7由机械加工、使用和它的构成材料和物质产生的危险(见GB/T 15706.1~—1995的4.8)A7.1由于接触或吸入有害的液体、气体、油雾、烟雾和灰尘产生的危险(见GB/T15706.1--1995的4.8)
A7.2火和爆炸危险(见GB/T15706.1—1995的4.8)A7.3生物或微生物(病毒或细菌)危险(见(GB/T15706.1--1995的4.8)A8在机械设计中由于怒略了人类工效学原则而产生的危险(见GB/T15706.1—1995的4.9)A8.1过分用力的不利于健康的姿势(见GB/T15706.1—-1995的4.9)A8.2没有适当考虑手-臂或脚-腿的结构A8.3忽略了使用个人防护装备
A8.4局部照明不合适
A8.5精神负担过重或准备不足(见GB/T15706.1—1995的4.9)A8.6人的差错、人的行为(见GB/T15706.1—1995的4.9)A9各种危险的组合(见GB/T15706.1—1995的4.10)危险事件
由 A1~A9中所列的一种或几种危险的风险可能导致的事件:A10由以下原因引起的意外起动、意外超行程/超速(或某种类似的失灵):A10.1控制系统的失效/失调
A10.2中断后的能源恢复
A10.3电气设备外部干扰
A10.4其他外部干扰(重力、风等)A10.5软件的差错
A10.6由操作者产生差错(由于机械和人的特征能力不协调,见8.6)A11机器不能停在最好可能条件下768
工具在合理速度下偏转
动力源失效
控制电路失效
设定错误
运行期间制动
物体或流体下落或抛出
机械不稳定/翻倒
GB/T16856--1997
A19人(相对机械)滑例、继倒和跌倒见GB/T15706.1的4.2.3)由于移动性增加的危险和危险事件A20与运行功能有关的
A20.1启动发动机时的运动
A20.2驱动位置无司机而运动
A20.3不是所有部件都在安全位置而运动A20.4非专业人员控制的机械超速A20.5运动时过分摇摆
A20.6机械不能有效地减速、停机和固定与机器的工作位量相关联的(包括驱动站)A21
A21.1人在进入(或在/离开)工作位置时跌倒A21.2在工作位置排气/缺氧
A21.3着火(座舱易燃、缺乏灭火手段)A21.4在工作位置的机械危险
-与轮子接触
—物体落下,由物体穿透
一高速旋转零件的制动
一人与机器零件或工具接触(非专业人员操纵的机器)A21.5由于工作位置可视性不足
A21.6照明不足
A21.7密封不充分
A21.8在工作位置有噪声
A21.9在工作位置有振动
A21.10排空/急停措施不充分
A22由于控制系统
GB/T 16856-1997
A22.1控制器/控制装置的位置不合适A22.2操纵模式和(或)控制器动作模式不合适A23来自机器的搬运(缺乏稳定性)A24 由于动力源和动力传输
A24.1来自发动机和蓄电池的危险A24.2来自机器之间动力传输的危险A24.3来自偶合和拖动的危险
A25由/至第三人
A25.1未经允许起动/使用
A25.2部分偏离其停止位置
A25.3视觉或听觉报警器缺乏或不合适A26对司机/操作者的指导不够
由于提升附加的危险和危险事件A27机械危险和危险事件
A27.1.由于以下原因引起的负载跌落、碰撞、机器翻倒:A27.1.1缺乏稳定性
2非受控的载荷
A27. 1. 2
—超载
非受控的运动幅度
一超行程运动
A27.1.4载荷的意外/非预期的运动A27.1.5夹紧装盘/辅具不合适
A27.2由于人的升高
A27.3由于脱轨
A27.4由于零件的机械强度不够
A27.5由于带轮、鼓轮设计不合适A27.6由于链条、绳、提升附件选择/装人机器不合适A27.7由于磨擦破裂负荷降低
A27.8由于不正常的装配/试验/使用/维修条件A27.9由于载荷与人相干扰(通过载荷/配重冲击)A28电的危险
A28.1由于照明
A29由于您略了人类工效学原则产生的危险A29.1由于驱动位置可视性不足
小提示:此标准内容仅展示完整标准里的部分截取内容,若需要完整标准请到上方自行免费下载完整标准文档。
本标准等效采用欧洲标准(草案)prEN1050—1994《机械安全—~风险评价的原则》,在一般要素上和补充要素上有以下两点差异:1.引用标准的导言是按GB/T1.1的规定编写的,并将原标准中引用的欧洲标准改为相应的国家标准;
2.取消了原提示的附录B\分析危险和评估风险的方法”。因为这些“方法”只是作为提示信息给出的,无法进行具体的操作。
本标准的附录 A是提示的附录。本标准由中华人民共和国机械工业部提出。本标准由全国机械安全标准化技术委员会归口。本标准由机械部机械科学研究院负责起草。本标准主娶起草人:张尔正、李勤、马贤智、徐自芬、萧维、张铭续。759
0引言
中华人民共和国国家标准
风险评价的原则
机械安全)
Safety of machinery-
Principles for risk assessmentGB/T 16856-1997
本标准规定了供风险评价(见GB/T15706.1一1995第6章)用的统一系统原则。本标准给出了机械设计(见GB/T15706.1-1995的3.11)过程中的决策指南,它将有助于制定B类和C类标准中统一、合适的安全要求,以便符合GB/T15706.2中规定的基本安全要求。建议将本标准纳入培训教程和手册,以对设计方法给予基本指导。1范围
本标准描述了被称之为风险评价的程序,通过这种程序将有关机械的设计、使用、事件、事故和伤害的知识和经验汇集到一起,以进行机器寿命周期内各种风险的评价。本标准给出了赖以进行风险评价所需要的信息指南。规定了识别危险、评估和评定风险的程序。本标准的目的是对有关机械安全问题及为验证风险评价所需的文件类型问题进行决策时提供建议。本标准对分析危险和评估风险的方法不作详细规定。这种详细规定在其他文献(如教科书或其他参考文件)中另有述及。
2 引用标准
下列标准所包含的条文,通过在本标准中引用而构成本标准的条文。本标准出版时,所有版本均为有效。所有标准都会被修订,使用本标准的各方应探讨使用下列标准最新版本的可能性。GB/T5226.1--1996.工业机械电气设备第1部分:般要求GB/T15706.1--1995机械安全基本概念与设计通则第1部分基本术语、方法学GB/T15706.2-1995机械安全基本概念与设计通则第2部分:技术原则与规范3定义
除GB/T15706.1给出的定义外,本标准还采用以下定义:3.1伤害.harm
对健康或财产的物理损伤和/或危害。3.2危险事件hazardous event
引起伤害的事件。
3.3遗留风险residual risk
采取安全措施之后所剩余的风险。3.4安全措施safetymeasure
消除危险或减小风险的手段。(见GB/T15706.1—1995的第5章)国家技术监督局1997-06-06批准760
1998-01-01实施
4总则
4.1基本概念
GB/T16856-1997
风险评价是以系统方式对与机械有关的危险进行考察的一系列逻辑步骤。当需要时,风险评价后应按照GB/T15706.1一1995第5章所描述的方法减小风险。当重复这一过程时,就可达到尽可能消除危险和根据现有工艺水平实施安全措施的送代过程(见图1)。开始
机械限制的确定(第5章)
危险识别(第6章)
风险评估(第7章)
风险评定(第8章)
风险减小方案分析
(见注和附录A)
机器是安全的吗?
风险分析
风险评价
注:减小风险和选择适当的安全措施不是风险评价的内容,进一步的解释见GB/T15706.1一1995第5章和GB/T 15706.2
图1实现安全的选代过程
风险评价包括
风险分析
1)机械限制的确定(第5章)
2)危险识别(第6章)
3)风险评估(第7章)
-风险评定(第8章)
风险分析提供了风险评定所需的信息,有了这种信息就可对机械安全做出判断。风险评价依赖于判断决定。这些决定应通过定性的方法来支持,并尽可能通过定量方法补充。当可预见伤害严重度高且范大时,定量法是特别合适的。定量法对评价可替换的安全措施和决定何种防护更好是有用的。注:由于定量法的使用受可得到的有用数据量的限制,因此,在许多应用场合,只能使用定性的风险评价。风险评价的程序应以形成文件的方式进行:已进行过评价的机械的预期使用(技术规范、限制等);所识别的危险、危险状态和危险事件;使用的有关信息(事故历史,由对类似机器进行减小风险获得的经验等),-通过安全措施要达到的目标;
为消除识别的危险或减小风险所实施的安全措施;761
GB/T16856—1997
一通过规定某种有关假设(载荷、安全因素等)后,各种危险的遗留风险。4.2风险评价信息
风险评价信息和定性、定量分析应包括以下内容:—机械的限制(GB/T15706.1--1995的5.1);机械各寿命阶段的要求(见GB/T15706.1--1995的3.11a),一规定机械特性的设计图样或其他手段,—有关动力源的信息;
事故或事件的历史(如果可得到的话):有损健康的任何信息。
当设计改进和需更改时,信息也应适时更新。假如能得到那些危险状态中的有关危险和事故环境的足够信息,可对不同类型机械的类似危险状态进行比较通常是可行的。
在事故历史不明的情况下,不应根据少量事故及严重性不大的事故主观做出低风险推测。对于定量评价,可以使用数据库、手册、实验室和制造厂技术规范中的数据(假如对它们的适用性有把握的话)。有关该数据的不确定度应在文件中指明(见第9章)。专家一致认可的经验数据可作为补充定性数据。5 机械限制的确定
风险评价应考虑:
—机器寿命的各个阶段(见GB/T15706.1—1995的3.11a)。机械的限制,包括预定使用(见GB/T15706.1一1995的5.1),除了合理预见的误用和失灵的后果外,还应包括机器的正确使用和正确操作两方面。另外,风险评价还应适当根据人的情况来考虑:可预见的机械(如工业用、非工业用和家用)全部使用范围,人的情况可依据性别、年龄及用手习惯或体能限制(如视力或听力损伤、身材大小、体力强弱)来确定。一可预见的使用者预期训练水平、经验或能力,例如:1)经过培训的热练技术维修人员;2)经过培训的操作人员,
3)学员和初学者,
4)一般人员,bzxZ.net
一一暴露于可合理预见机械危险场合的其他人员。6危险识别
应识别与机械有关的所有危险、危险状态和危险事件。附录A(提示的附录)给出的例子有助于这种识别(描述由机械产生危险的进一步信息参见GB/T15706.1一1995的第4章)。7风险评估
危险识别(第6章)后,对一种危险都应通过测定7.1给出的风险要素进行风险评估。在测定这些风险要素时,需考虑7.2给出的几个方面。7.1风险要素
与特殊情况或技术过程相关的风险由以下要素组合得出:一伤害的严重度;
伤害出现的概率;
置)。
GB/T16856--1997
1)人员暴露于危险中的频次和持续时间,2)危险事件出现的概率;
-在技术上和人为方面避免或限制伤害的可能性(如对风险的了解、降低速度、急停装置、使动装风险要素示于图2中,附加细节在7.1.1和7.1.2中给出。注:在许多情况下,这些风险要素不能被精确地测定,而只能估计。这特别适用于可能伤害出现的概率。在基些情况(如由于有毒物质或精神压力有损健康的情况)下,可能伤害的严重度不容易确定。为改普这种情况,可使用附加辅助值即所谓的风险参数,以方便风险评估,总的来说,特别适用于这种情况的风险参数型式取决于所涉及的危险类型。
伤害出现的概率
景露的频次及持续时间
与所考患的
危险有关的
7.1.1严重度(可能伤害的程度)该危险可
能伤害的
严重度
危险事件出现的概率
避免或限制伤客的可能性
图2风险要素
严重度可通过考虑以下因素评估:防护对象的性质:
1)人,
2)财产,
3)环境。
损伤的严重度(对人的情况):1)轻度(可正常恢复的)损伤或危害健康;2)严重(不能正常恢复的)损伤或危害健康;3)死亡。
-伤害的限度(对每台机器)。对人的情况:1)一个人
2)几个人。
7.1.2伤害出现的概率
伤害出现的概率可通过考虑7.1.2.1到7.1.2.3来进行评估:7.1.2.1暴露的题次和持续时间:接近危险的需要(如生产的原因、维护或修理),-接近的性质(如手动送料),
-处于危险区的时间;
需要接近危险的人数;
一进入危险区的频次。
7.1.2.2危险事件出现的概率
-可靠性和其他统计数据;
事故历史;
风险比较。
的函数
GB/T16856-1997
注:危险事件的出现可能源于技术的或人的原因。7.1.2.3避免或限制伤害的可能性一机器是
1)由熟练工操作;
2)由非熟练工操作;或
3)无人操作。
危险事件出现的速度:
1)突然;
2)快;
3)慢。
对风险的了解;
1)一般信息;
2)直接观察,
3)通过指示装置,
一人员避免危险的可能性(如反应、灵敏性、逃脱的可能性):1)可能;
2)在某些情况下可能;
3)不可能。
一实践经验和知识:
1)该机械的;
2)类似机械的;
3)没经验的。
7.2确定风险要素应考虑的诸方面7.2.1暴露的人员
风险估计应考虑所有暴露于危险中的人员,包括操作者、维修人员和可合理预见的可能受到机器影响的其他人员。
7.2.2暴露的类型、频次和持续时间对所考虑危险中暴露的评估,需要分析并应说明机器的各种操作模式和使机器工作的方法。这尤其影响到在设定、示教、过程转换或调整、清理、查找故障和维修(见GB/T15706.1--1995的3.11)期间进入危险区的需要。
当必须暂停安全功能时(如维修期间),风险评估应说明这种情况。7.2.3暴露和影响之间的关系
当确定在一种危险中的暴露及其影响之间的关系时,就可行而言,风险评估应根据合适的认可数据。
注:事故数据可用来表明与具有特定安全措施的特定型式机械的使用有关的损伤概率和严重度。7.2.4人的因素
风险评估应不限于技术因素。风险可能受人为因素的影响,诸如,一方面,与机械的相互作用有关的、与人们之间的相互作用有关的、与心理学有关的和与人类工效影响有关的因素,另一方面,与认识在给定条件下风险的能力高低有关的因素。这种情况取决于操作者和可能受影响的其他人的培训情况、经验和能力。
对暴露于危险中的人员能力的评估应考虑以下几个方面:一与人类工效学原则有关的机械设计;一执行所需任务固有的或被开发的能力;764
——对各种风险的认识;
GB/T16856—1997
一如果不发生有意或无意差错时执行所需任务的把握程度;一一防止诱使偏离规定的和必要的安全工作规程的能力。训练、经验和能力都会影响到风险,但是它们都不能用来代替可能通过设计或安全防护来消除危险、减小风险的措。
7.2.5安全功能的可靠性
风险评估应考虑元件和系统的可靠性。尤其是判定作为主要安全功能(见GB/T15706.1一1995的3.13.1)部分的元件和系统应受到特别注意。评估应:一一判明可能导致伤害的环境(例如,元件故障,电气干扰);一一当合适时,使用定量法比较可供选择的安全措施;—一提供用以选择适当的安全功能、元件和装置的信息:对承担一种安全功能的有关安全装置不只一个时,选择这些装置需考虑它们的性能和可靠性应是协调一致的。
当安全措施包括工作组织、正确行为、小心注意、应用个体防护装备、技能或培训时,在风险评估中必须考虑到:这些措施与经过验证的技术措施相比,可靠性相对较低。7.2.6毁坏或避开安全措施的能力风险评估应说明某一一特定安全措施被轻易毁坏或避开的可能性。风险评估还应考虑毁坏或避开系统的诱因。如:
是否安全措施延缓了生产或干扰使用者的某些其他活动或选择;一安全措施难以使用;
——是否涉及操作者以外的人员;一安全措施的功能是否未被认可或接受。毁坏安全措施的能力可能取决于安全措施的类型及其设计细节两方面。如果对有关安全软件的存取设计和监控不当,使用可编程电子系统会导致毁坏或避开安全措施的附加可能性。风险评估应判明有关安全功能在什么地方没与其他机器功能分开和存取可能达到的范围。当为诊断或过程校正需要遥控存取时,这是特别重要的(见GB/T5226.1—1995的12.3.5)。当进行风险评估时,需要考虑毁坏或避开可调防护装置和可编程自动停机装置的可能性。7.2.7保持安全措施的能力
风险评估应考虑安全措施是否能保持在为提供需要的防护水平所必需的状态。注:如果安全措施不容易保持在正确工作状态下,为了使机械连续使用,这可能促使毁坏或邀开安全措施。7.2.8使用信息
风险评估应考虑随机械提供的使用信息。应考虑妥善地实施GB/T15706.2--1995第5章的要求。8风险评定
风险评估后,要进行风险评定,以确定是否需要减小风险或是否达到了安全。如果风险需要减小,则应选择和应用相应的安全措施,并应重复该程序(见图1)。在这种选代过程中,重要的是当应用新的安全措施时,设计者应核对是否又产生了附加危险。如果附加危险的确出现了,则这些危险应列入到危险识别清单中。
风险减小目标的实现(见8.1)和风险比较的有效结果(见8.2)可以使人确信机械是安全的(见GB/T15706.1—-1995的3.4)。
8.1风险减小目标的实现
下列条件的实现(见GB/T15706.1—1995的表2和GB/T15706.2-1995的3~6)将表明减小风765
险的过程可以结束:
GB/T16856—1997
通过以下措施消除了危险或减小了风险:1)通过设计或替代稍有危险的材料或物质,和/或2)按照现有工艺水平进行安全防护;所选的安全防护类型是经过验证的,对预期使用能起到充分的防护;针对以下儿种情况,所选择的防护类型是合适的:1)毁坏或避开的概率,
2)伤害的严重度,
3)对执行所要求任务的妨碍,
有关机械的预定使用信息十分清楚;一使用机械的操作程序与使用该机械的人员或可能暴露于与该机械有关的危险中的其他人员的能力协调一致;
推荐的该机械使用安全操作规程和有关的培训要求已充分说明;一关于遗留风险已充分告知了用户;一如果推荐用个体防护装备来对付遗留风险,对这种防护装备的需要和使用该防护装备的培训要求已充分说明;
附加预防措施是充分的(GB/T15706.2-—1995的第6章)。8.2风险比较
只要下列判定适用,作为风险评定过程的一部分,与机械有关的风险可与类似机械的风险相比较:类似机械证明了按照现有工艺水平风险减小是可接受的,两种机械的预定使用和所采用的工艺都是可比的,危险和风险要素是可比的,
技术目标是可比的,
一使用条件是可比的。
使用这种比较方法不排除在特定使用条件下(如用于切肉的带锯机与用于切割木材的带锯机相比较时应评价与材料变化有关的风险)还需要遵循本标准描述的风险评价过程。9文件
形成风险评价文件是描述所识别的危险和实施安全措施的一种手段。文件应包含以下充分的信息:
风险评价所依据的信息(见4.2);已经评价过的机械(规范、限制等);已做过某些有关假设,如载荷、强度、安全因素等,判明的危险:
判明的危险状态;
-在评价中考虑的危险事件,
一使用的数据及原始资料;
与使用的数据有关的不确定度和对风险评价的影响;一通过安全措施达到的目标;
一某些补充要求(如使用的标准或其他规范);一关于遗留风险的信息;
一最终风险评定的结果。
A1机械危险
GB/T16856—1997
附录A
(提示的附录)
危险、危险状态和危险事件的例子A1.1由机器零件产生的或由工件引起的(见GB/T15706.1—1995的4.2和GB/T15706.2—1995的3.2)
A1.1.1形状
A1.1.2相对位置
A1.1.3质量和稳定性(在重力的影响下可以运动的元件位能)A1.1.4质量和速度(受控或非受控运动元件的动能)A1.1.5机械强度不合适
A1.2机械内部能量积累引起的,例如由:A1.2.1弹性元件(弹簧)
A1.2.2压力下的液体和气体
A1.2.3真空影响
A1.3机械危险的基本形式
挤压危险(见GB/T15706.1—1995的4.2.1)A1.3.1E
A1.3.2剪切危险(见GB/T15706.1—1995的4.2.1)A1.3.3切割或切断危险(见GB/T15706.1--1995的4.2.1)缠绕危险(见GB/T15706.1—1995的4.2.1)A1.3. 4
A1.3.5引入或卷人危险(见GB/T15706.1--1995的4.2.1)A1.3.6冲击危险(见GB/T15706.1—1995的4.2.1)A1.3.7刺伤或扎伤危险(见GB/T15706.1--1995的4.2.1)A1.3.8摩擦或磨损危险(见GB/T15706.1--1995的4.2.1)A1.3.9高压流体喷射或抛射危险(见GB/T15706.1-1995的4.2.1)A2电的危险(见GB/T15706.1—1995的4.3和GB/T15706.2—1995的3.9),由于A2.1人与带电零件接触(直接接触)A2.2人与在故障条件下变为带电的零件接触(间接接触)(见GB/T15706.1-1995的4.3)A2.3趋近于高压下的带电零件
A2.4静电现象(见GB/T15706.1—1995的4.3)A2.5热辐射或其他现象例如由于短路或过载等而引起的熔化粒子喷射和化学效应(见GB/T15706.1—1995的4.3)
A3热危险(见GB/T15706.1--1995的4.4)导:A3.1由可能与人接触的火焰或爆炸也可能由热源辐射引起燃烧和烫伤(见GB/T15706.1--1995的4.4)
A3.2由于热的或冷的工作环境影响对健康的危害(见GB/T15706.1-—1995的4.4)767
CB/T 16856-1997
A4由噪声产生的危险(见GB/T15706.1--1995的4.5),导致A4.1听力损失(耳聋)、其他生理异常(例如失去平衡,失去知觉)(见GB/T15706.1—1995的4.5)A4.2对语言通讯和听觉信号等的于扰(见GB/T15706.1一1995的4.5)A5由振动产生的危险
A5.1使用手持式机器导致神经病变和血脉失调(见GB/T15706.1—1995的4.6)A5.2尤其当与不良的姿势结合时的全身振动A6由辐射产生的危险(见GB/T15706.1—1995的4.7)A6.1低频、无线频率辐射、微波(见GB/T15706.1--1995的4.7)A6.2红外线、可见光和紫外光
A6.3X和射线(见GB/T15706.1—1995的4.7)A6.4α和β射线、电子或离子束、中子(见GB/T15706.1--1995的4.7)A6.5激光(见GB/T15706.1-1995的4.7)A7由机械加工、使用和它的构成材料和物质产生的危险(见GB/T 15706.1~—1995的4.8)A7.1由于接触或吸入有害的液体、气体、油雾、烟雾和灰尘产生的危险(见GB/T15706.1--1995的4.8)
A7.2火和爆炸危险(见GB/T15706.1—1995的4.8)A7.3生物或微生物(病毒或细菌)危险(见(GB/T15706.1--1995的4.8)A8在机械设计中由于怒略了人类工效学原则而产生的危险(见GB/T15706.1—1995的4.9)A8.1过分用力的不利于健康的姿势(见GB/T15706.1—-1995的4.9)A8.2没有适当考虑手-臂或脚-腿的结构A8.3忽略了使用个人防护装备
A8.4局部照明不合适
A8.5精神负担过重或准备不足(见GB/T15706.1—1995的4.9)A8.6人的差错、人的行为(见GB/T15706.1—1995的4.9)A9各种危险的组合(见GB/T15706.1—1995的4.10)危险事件
由 A1~A9中所列的一种或几种危险的风险可能导致的事件:A10由以下原因引起的意外起动、意外超行程/超速(或某种类似的失灵):A10.1控制系统的失效/失调
A10.2中断后的能源恢复
A10.3电气设备外部干扰
A10.4其他外部干扰(重力、风等)A10.5软件的差错
A10.6由操作者产生差错(由于机械和人的特征能力不协调,见8.6)A11机器不能停在最好可能条件下768
工具在合理速度下偏转
动力源失效
控制电路失效
设定错误
运行期间制动
物体或流体下落或抛出
机械不稳定/翻倒
GB/T16856--1997
A19人(相对机械)滑例、继倒和跌倒见GB/T15706.1的4.2.3)由于移动性增加的危险和危险事件A20与运行功能有关的
A20.1启动发动机时的运动
A20.2驱动位置无司机而运动
A20.3不是所有部件都在安全位置而运动A20.4非专业人员控制的机械超速A20.5运动时过分摇摆
A20.6机械不能有效地减速、停机和固定与机器的工作位量相关联的(包括驱动站)A21
A21.1人在进入(或在/离开)工作位置时跌倒A21.2在工作位置排气/缺氧
A21.3着火(座舱易燃、缺乏灭火手段)A21.4在工作位置的机械危险
-与轮子接触
—物体落下,由物体穿透
一高速旋转零件的制动
一人与机器零件或工具接触(非专业人员操纵的机器)A21.5由于工作位置可视性不足
A21.6照明不足
A21.7密封不充分
A21.8在工作位置有噪声
A21.9在工作位置有振动
A21.10排空/急停措施不充分
A22由于控制系统
GB/T 16856-1997
A22.1控制器/控制装置的位置不合适A22.2操纵模式和(或)控制器动作模式不合适A23来自机器的搬运(缺乏稳定性)A24 由于动力源和动力传输
A24.1来自发动机和蓄电池的危险A24.2来自机器之间动力传输的危险A24.3来自偶合和拖动的危险
A25由/至第三人
A25.1未经允许起动/使用
A25.2部分偏离其停止位置
A25.3视觉或听觉报警器缺乏或不合适A26对司机/操作者的指导不够
由于提升附加的危险和危险事件A27机械危险和危险事件
A27.1.由于以下原因引起的负载跌落、碰撞、机器翻倒:A27.1.1缺乏稳定性
2非受控的载荷
A27. 1. 2
—超载
非受控的运动幅度
一超行程运动
A27.1.4载荷的意外/非预期的运动A27.1.5夹紧装盘/辅具不合适
A27.2由于人的升高
A27.3由于脱轨
A27.4由于零件的机械强度不够
A27.5由于带轮、鼓轮设计不合适A27.6由于链条、绳、提升附件选择/装人机器不合适A27.7由于磨擦破裂负荷降低
A27.8由于不正常的装配/试验/使用/维修条件A27.9由于载荷与人相干扰(通过载荷/配重冲击)A28电的危险
A28.1由于照明
A29由于您略了人类工效学原则产生的危险A29.1由于驱动位置可视性不足
小提示:此标准内容仅展示完整标准里的部分截取内容,若需要完整标准请到上方自行免费下载完整标准文档。

标准图片预览:
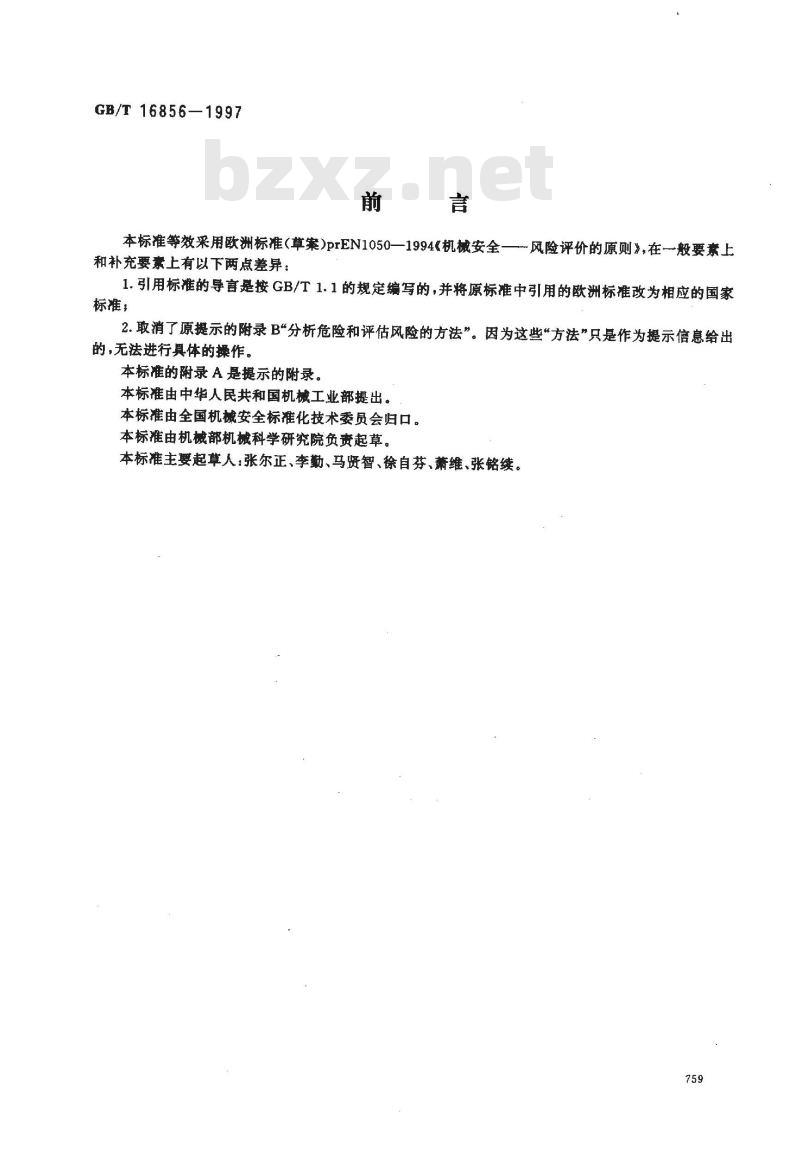
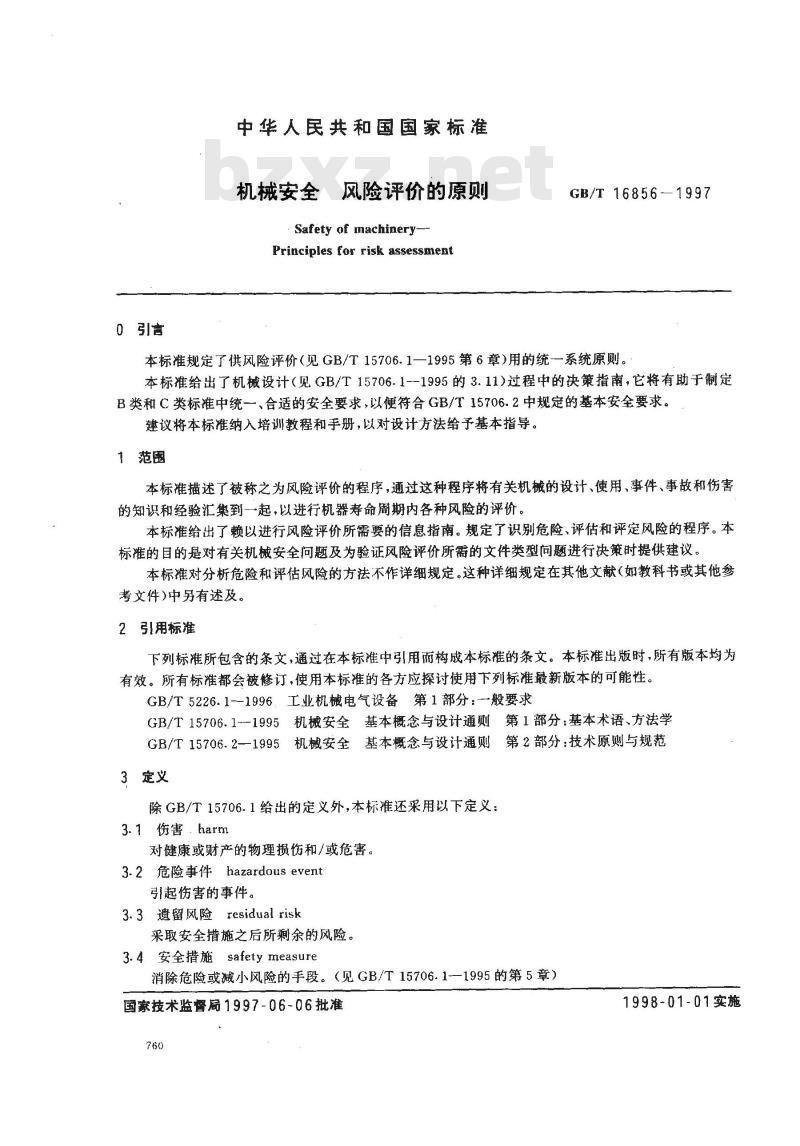
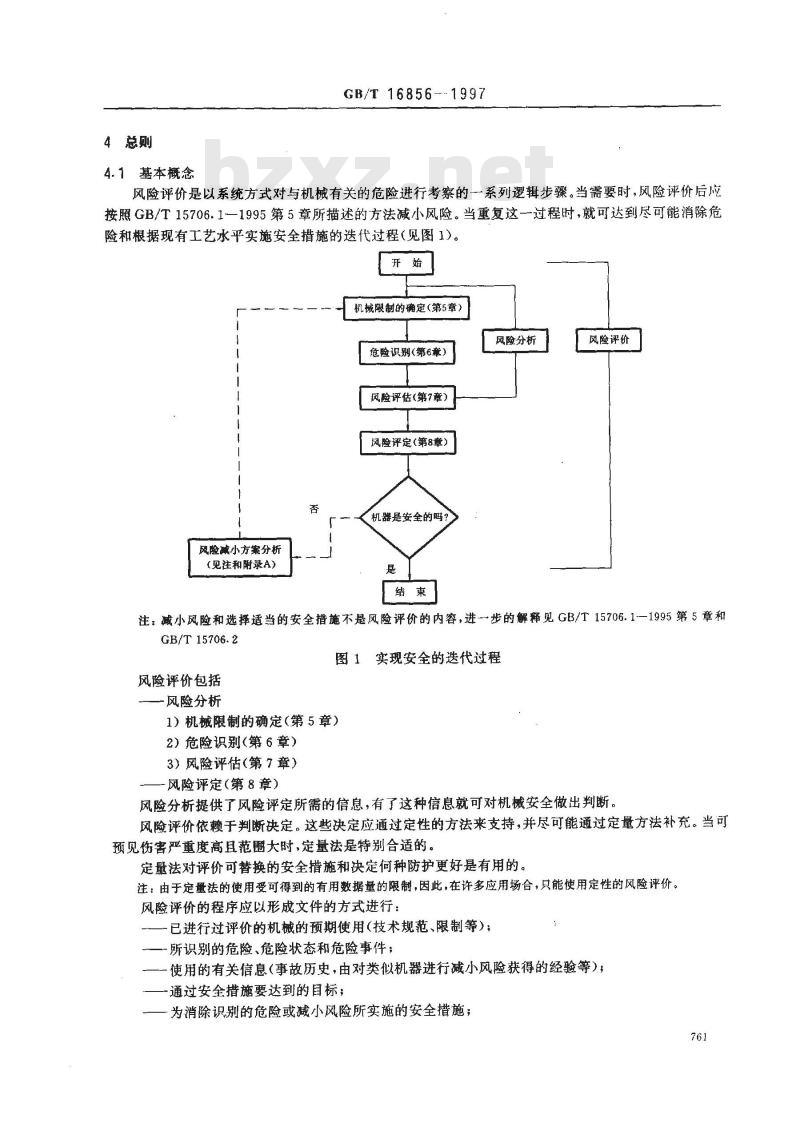
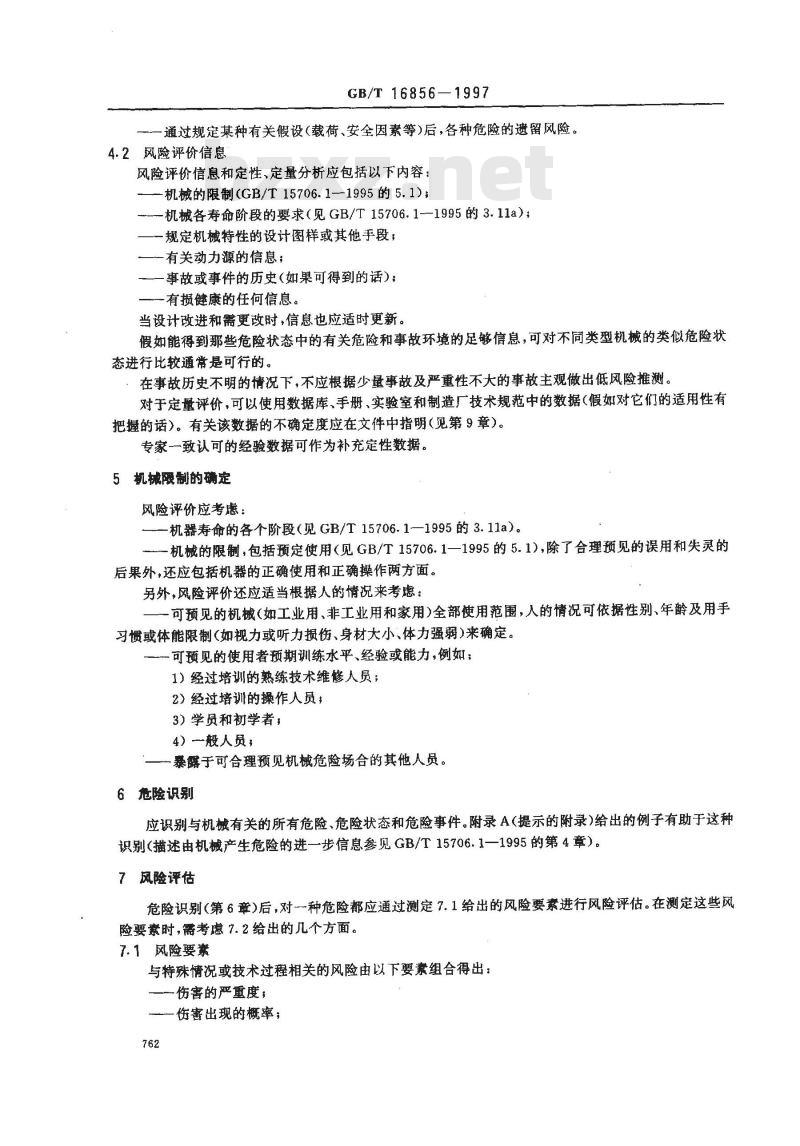
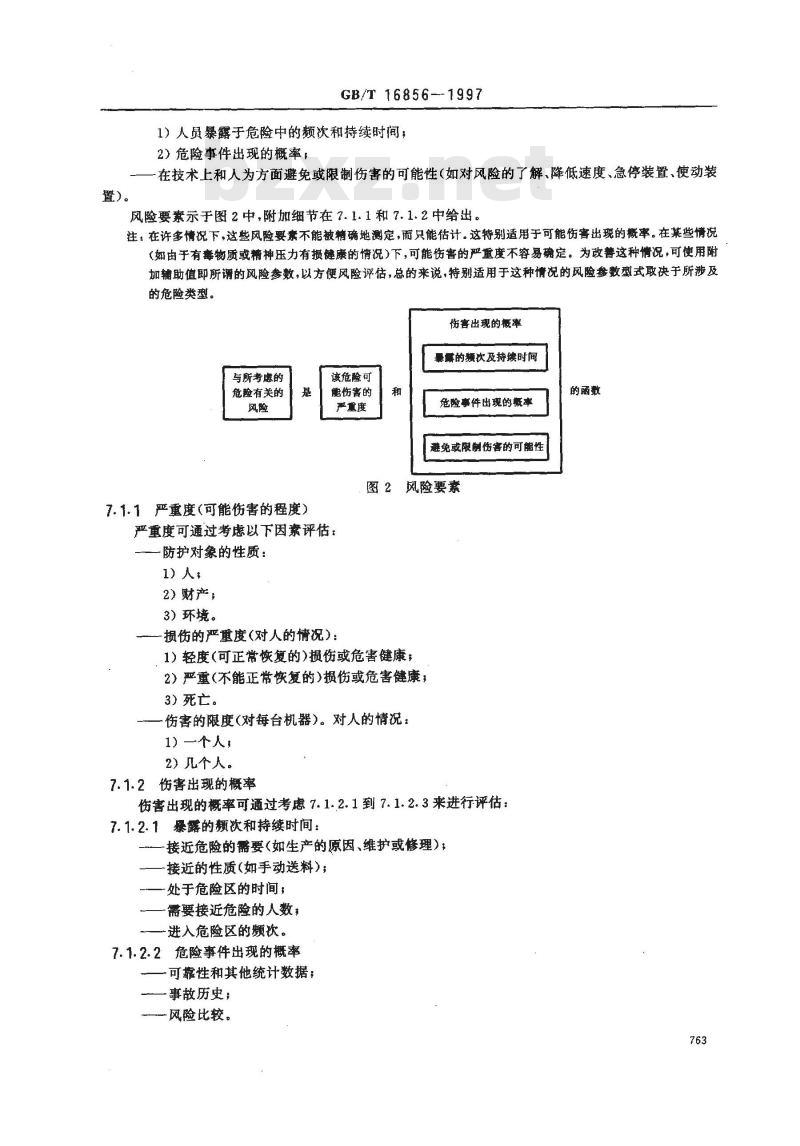
- 热门标准
- 国家标准(GB)
- GB/T2828.1-2012 计数抽样检验程序 第1部分:按接收质量限(AQL)检索的逐批检验抽样计划
- GB/T14946-2002 全国干部、人事管理信息系统指标体系分类与代码
- GB/T15361-2009 岸边集装箱起重机
- GB/T41251-2022 生产过程质量控制 生产装备全生命周期管理
- GB/T51435-2021 农村生活垃圾收运和处理技术标准
- GB4943.1-2011 信息技术设备 安全 第1部分:通用要求
- GB50777-2012 ±800KV及以下换流站构支架施工及验收规范
- GB7521—1987 多个控制器在一CA MAC机箱中
- GB50268-2008 给水排水管道工程施工及验收规范
- GB/T7251.1-2023 低压成套开关设备和控制设备 第1部分:总则
- GB/T43542-2023 机关办公区域物业服务监管和评价规范
- GB/T13477.19-2017 建筑密封材料试验方法 第19部分:质量与体积变化的测定
- GB/T5210-2006 色漆和清漆拉开法附着力试验
- GB917.2—2000 公路路线标识规则国道名称和编号
- GB12838-1999 大芯腔轮胎气门芯
请牢记:“bzxz.net”即是“标准下载”四个汉字汉语拼音首字母与国际顶级域名“.net”的组合。 ©2009 标准下载网 www.bzxz.net 本站邮件:bzxznet@163.com
网站备案号:湘ICP备2023016450号-1
网站备案号:湘ICP备2023016450号-1