- 您的位置:
- 标准下载网 >>
- 标准分类 >>
- 铁路运输行业标准(TB) >>
- TB/T 3294-2013 CRTS I型轨道板专用真空脱模机
标准号:
TB/T 3294-2013
标准名称:
CRTS I型轨道板专用真空脱模机
标准类别:
铁路运输行业标准(TB)
标准状态:
现行出版语种:
简体中文下载格式:
.zip .pdf下载大小:
3.16 MB

点击下载
标准简介:
TB/T 3294-2013.Special vacuum demoulding machine for the CRTS II track slab.
1范围
TB/T 3294规定了CRTS I型轨道板专用真空脱模机的术语和定义、产品型号编制方法、要求、检验方法、检验规则以及标志、包装、运输和贮存。
TB/T 3294适用于CRTS I型轨道板专用真空脱模机(以下简称真空脱模机)的制造及检验。
2规范性引用文件
下列文件对于本文件的应用是必不可少的。凡是注日期的引用文件,仅所注日期的版本适用于本文件。凡是不注日期的引用文件,其最新版本(包括所有的修改单)适用于本文件。
GB 2893安 全色
CB 4208- 2008 外壳防护 等级(IP代码)
CB 6067起重机械安全规程 .
GB 8923--1988涂装前钢材表面锈蚀等级和除锈等级
GB 11345--1989钢焊缝手工超声波探伤方法和探伤结果分级
CB 50054低压配电设计规范
GB/T 191包装 储运图示标志
GB/T 985.1气焊 、焊条电弧焊、气体保护焊和高能束焊的推荐坡口
GB/T985.2埋弧焊的推荐坡口
GB/T 2893(所有部分)图形符号 安全 色和安全标志
GB/T 3323- 2005金属熔化焊焊接接头射线照相
CB/T 3766液压系统通用技术条件
GB/T 3811起 重机设计规范
3术语和定义
下列术语和定义适用于本文件。
3.1真空吸盘vacuum sucker
用来吸附轨道板的部件,由真空吸盘钢结构和真空吸盘唇组成,当真空吸盘唇贴合轨道板表面时可形成-一个密闭的真空容腔。
3.2安全工作真空度degree of safe operation vacuum
设备安全工作时的最低真空度值。

部分标准内容:
中华人民共和国铁道行业标准
TB/T3294—2013
CRTSⅡ型轨道板专用真空脱模机Special vacuum demoulding machine for the CRTS I track slab2013-02-20发布
2013-06-01实施
中华人民共和国铁道部发布
规范性引用文件
术语和定义
型号编制方法
检验方法
检验规则
标志、包装、运输和贮存
TB/T3294—2013
TB/T3294—2013
本标准按照GB/T1.1一2009给出的规则进行起草。本标准由中铁科工集团有限公司归口。本标准起草单位:中铁六局集团有限公司、中铁丰桥桥梁有限公司、上海瓦科自动化设备有限公司、中铁科工集团有限公司。
本标准主要起草人:张恩龙、李阳、张小娟、刘文伟、张劭明、金雁鹏、郑志敏。1范围
CRTSⅡ型轨道板专用真空脱模机TB/T3294—2013
本标准规定了CRTSⅡ型轨道板专用真空脱模机的术语和定义、产品型号编制方法、要求、检验方法、检验规则以及标志、包装、运输和贮存。本标准适用于CRTSⅡ型轨道板专用真空脱模机(以下简称真空脱模机)的制造及检验。2规范性引用文件
下列文件对于本文件的应用是必不可少的。凡是注日期的引用文件,仅所注日期的版本适用于本文件。凡是不注日期的引用文件,其最新版本(包括所有的修改单)适用于本文件。GB2893安全色
GB4208—2008外壳防护等级(IP代码)GB6067起重机械安全规程
GB8923--1988涂装前钢材表面锈蚀等级和除锈等级GB11345—1989钢焊缝手工超声波探伤方法和探伤结果分级GB50054
GB/T191
低压配电设计规范
包装储运图示标志
GB/T985.1
气焊、焊条电弧焊、气体保护焊和高能束焊的推荐坡口GB/T985.2
埋弧焊的推荐坡口
GB/T2893(所有部分)图形符号安全色和安全标志GB/T3323—2005金属熔化焊焊接接头射线照相GB/T3766
GB/T3811
液压系统通用技术条件
起重机设计规范
GB/T5226.1
机械安全机械电气设备第1部分:通用技术条件GB/T10051.1
吊钩技术标准
GB/T12237
石油、石化及相关工业用的钢制球阀般起重机用锻造卸扣D形卸扣和弓形卸扣JB/T8108.1
起重用标准短环链技术参数
JB/T8356.1机床包装技术条件
JB/T8356.2机床包装箱
JB/T8521(所有部分)编制吊索安全性JB/T8861球阀静压寿命试验规程标准JB/T8870喉箍
3术语和定义
下列术语和定义适用于本文件。3.1
vacuum sucker
真空吸盘
用来吸附轨道板的部件,由真空吸盘钢结构和真空吸盘唇组成,当真空吸盘唇贴合轨道板表面时1
TB/T3294-2013
可形成一个密闭的真空容腔。
安全工作真空度degreeof safeoperationvacuum设备安全工作时的最低真空度值。3.3
保压时间pressure maintaining time由最大真空度下降至安全工作真空度的时间间隔,以分钟为单位。4型号编制方法
真空脱模机的型号由组别代号、吸盘个数、额定起重量和改进代号组成,具体编制方法及图示如下:改进代号:用大写的拉丁字母,从A开始··额定起重量:以两位数表示,单位t吸盘个数:1、2、3....9,以个位数表示组别代号:真空脱模机ZT
示例:ZT609-A型真空脱模机一表示第一次改进设计的额定负载为9t,6个吸盘的真空脱模机。5要求
5.1适用环境要求
5.1.1环境温度:5℃~55℃。
5.1.2环境湿度:20%~90%。
5.1.3海拨:不应高于2000m。
5.1.4电压:380V,波动范围不应大于5%;频率50Hz,波动范围不应超过±2%。5.2整机技术要求
5.2.1真空脱模机应由真空吸附系统、同步顶升脱模系统、电气控制系统、安全保护装置等组成。5.2.2真空脱模机应能够实现轨道板无预设吊点、被吸附面平面度不应大于6mm、拉毛深度不应大于3mm工况下的脱模和搬运。
额定起重量不应小于9t,额定吸附力不应小于240kN。轨道板的吸附和同步顶升脱模工作时间不应大于90s真空脱模机应具备断电情况下轨道板的安全吸附和保护功能,保压时间不应小于30min。真空脱模机的外观质量应满足以下要求:所有零部件表面应平整、不得有明显变形和损伤,焊缝要均匀美观。b)
油漆应色泽均匀,没有涂斑、漏漆和剥落。c)
各紧固部位应无松动,各紧固件应无漏装,各相同部位的紧固件外露长度一致。d)
管线应排列整齐分明,液压油管线、电源线、控制信号线层次分明、互不干扰。e)
设备铭牌、安全警示标志和功能指示标牌齐全。真空脱模机所有钢结构喷涂面均应进行除锈处理,除锈质量等级不低于GB8923-1988的St25.2.7
级。设备涂装部位防锈底漆不应少于两层,面漆不应少于三层,漆层总厚度不应小于0.4mm。5.3真空吸附系统
5.3.1真空吸附系统应由真空泵、单向阀、主梁、真空压力表、过滤器、真空电磁阀、真空压力开关、真空吸盘等主要部件组成。
TB/T3294—2013
5.3.2真空系统初次建立安全工作真空度的时间不应大于6min;在连续工作工况下,真空吸盘建立安全工作真空度时间不应大于1min;从最大真空度降至安全工作真空度的时间不应少于30min。5.3.3真空吸附系统所用手动球阀应满足GB/T12237、JB/T8861的要求。5.3.4
真空吸附系统所用喉箍应满足JB/T8870的要求。5.3.5
真空吸盘应满足以下要求:
真空吸盘数量宜为4个或6个,吸盘布置位置应使轨道板应力最小;a)
真空吸盘钢结构应具有足够的强度、刚度,焊接接头应符合GB/T985.1、GB/T985.2的规定;真空吸盘钢结构焊接后应进行探伤,焊缝质量不应低于GB/T11345-1989中规定的I级和c)
GB/T3323—2005中规定的Ⅱ级;真空吸盘焊接后应进行时效处理,吸盘唇槽平面度不应大于2mm;d
真空吸盘唇宜选用闭孔发泡的天然橡胶,其截面及各项参数应满足产品安全吸附及密封性的e)
要求,且使用寿命不应小于\5000次工作循环;f)
吸盘唇槽与吸盘唇的粘结、吸盘唇接缝处的粘结应牢固,在寿命期内应无开裂现象。5.3.6主梁应满足以下要求:
主梁应为中空密闭箱型结构,其结构应具备脱模承载的功能,其空腔应具备为真空系统蓄能的功能;
b)主梁的强度和刚度应符合GB6067、GB/T3811的相关要求,在1.25倍额定荷载作用下,主梁最大变形量不超过2mm;
主梁钢结构的焊缝质量不应低于GB/T11345-1989中规定的I级和GB/T3323—2005中规c)
定的Ⅱ级;
主梁焊接后应用接触式超声波探伤,并进行气密性试验,在24h内压降为零;e)
主梁焊接后应进行时效处理,吸盘安装孔、吊装孔的分布应合理。5.4同步顶升脱模系统
5.4.1同步项升脱模系统宜采用液压驱动方式,其设计制造应符合GB/T3766的规定。5.4.2
同步顶升脱模系统应满足油缸顶升端部距模型顶面距离不一致时的同步顶升脱模的要求。
油缸脱模顶升同步精度不应低于3%。5.4.4
油缸压力反馈压力值不应大于额定压力的10%。5.4.5
油缸顶升脱模力应大于额定吸附力。5.4.61
项升油缸的布置应与轨道板模型支点一致。系统工作最高压力不宜大于15MPa。5.4.7
系统宜采用压力反馈自动控制齿轮分流器,实现同步顶升,且压力反馈值可根据工况手动调整。
项升脱模油缸伸缩动作应平稳自如,定位准确、无松动和异响,移动中无阻滞现象。5.5电气控制系统
电气控制系统应符合GB50054、GB/T5226.1的相关规定。电气设备外壳防护等级不应低于GB4208-2008中IP55。5.5.2
5.5.3在低于安全真空度时,控制系统应能自动停止同步顶升脱模系统的工作,并发出声、光报警信号。
应对每个吸盘分别设置声、光报警装置。5.5.5电气控制系统宜采用PLC可编程控制器,实现作业循环的程序控制。5.5.6控制系统应具有自动、手动两种工作方式。5.5.7
应设置连接可靠并具有锁紧装置的电缆快速插头,其容量应与设备功率匹配。3
TB/T3294—2013
5.6安全保护装置
5.6.1安全防护装置应符合GB6067、GB/T5226.1、GB/T3766的规定。5.6.2电气系统应具备防止误操作功能。5.6.3真空脱模机应设置意外断电报警单元和应急处理的保护装置。5.6.4所有用于起重承载的吊索、卸扣、吊环等附件,应符合JB/T8521(所有部分)、JB/T8108.1、JB8112、GB/T10051.1的规定。
6检验方法
6.1整机技术要求检查
6.1.1目测检查真空脱模机的系统组成、外观质量是否符合要求。6.1.2选择符合要求的轨道板进行模拟脱模试验,检验脱模和搬运轨道板是否符合要求。6.1.3利用秒表和观测压力表,通过模拟脱模试验和动载试验,检查额定起重量、额定吸附力、轨道板的吸附和同步顶升脱模工作时间、断电保护功能和保压时间是否符合要求。6.2真空吸附系统检查
目测真空吸附系统各主要组成部件是否符合要求。6.2.1
6.2.2通过模拟脱模试验观察真空压力表,检查是否符合要求。按照GB/T12237、JB/T8861规定的方法,检查手动球阀是否满足要求。6.2.3
按照JB/T8870规定的方法,检查喉箍是否符合要求。6.2.5通过目测和卷尺测量,检查真空吸盘数量及分布是否符合要求。6.2.6按照GB/T985.1、GB/T985.2的规定检查真空吸盘钢结构是否符合要求。按照GB/T11345—1989和GB/T3323的规定,检查焊缝质量是否符合要求。6.2.7查看技术资料,核实真空吸盘的探伤报告、吸盘唇槽平面度和真空密封唇材质是否符合要求。6.2.8通过模拟脱模试验,检查吸盘唇的粘结是否符合要求。6.2.9主梁的检查方法如下:
查看技术图纸检查主梁的结构型式和功能是否符合要求;a)
在1.1倍额定荷载作用下,通过模拟脱模试验,利用DNA电子水准仪及标尺分别测量主梁吸b)
盘安装处上部中心处和主梁中间上部中心处的高程,检查主梁的刚度是否符合要求:c)
按照GB/T11345一1989和GB/T3323—2005给出的方法,核实主梁的探伤报告,检查焊缝质量是否符合要求:
用0.5MPa的压缩空气进行气密性试验,在温度变化不大于3℃的条件下,使用0.4级压力d
表,测量主梁内压力,检查主梁气密性是否符合要求;通过目测和卷尺测量,检查吸盘安装孔、吊装孔是否符合要求。e
6.3同步顶升脱模系统检查
6.3.1目测检查设备驱动方式和顶升油缸分布是否符合要求。6.3.2通过模拟脱模试验,利用钢尺测量轨道板各边起模过程中离试验台面的垂直距离,观察项升油缸同步情况;观察压力表,确定压力值;观测油缸运行情况。在轨道板模型任意支点上方放50mm×50mm×50mm金属垫块,操作设备进行顶升脱模,测量轨道板各边起模过程中离试验台面的垂直距离,观察顶升油缸同步情况。检查同步顶升脱模系统是否符合要求。6.3.3空载运行设备,调至手动脱模工况,调节每个油缸所对应的触点式压力表的压力值,观察不同压力值时,各触点式压力表的输人信号;进行模拟脱模试验时,目测检查齿轮分流器的启动信号与各触点式压力表输出信号的一致性。6.3.4在空载条件下操作同步顶升油缸连续伸缩运动不少于50次和模拟脱模试验,目测检查顶升脱模油缸是否符合要求。
6.4电气控制系统检查
6.4.1目测电气控制系统的布线、布线端子连接、电缆快速插头是否符合要求。6.4.2按GB4208—2008规定的方法检查设备的外壳防护等级是否符合要求。TB/T3294—2013
6.4.3将设备置于模拟脱模试验场,吸附轨道板,进行模拟脱模作业,将设备调至自动状态,吸附轨道板,待系统真空报警解除后,在同步顶升脱模过程中松开任意一吸盘的气管喉箍,使设备真空压力值迅速下降,检查电气控制系统能否符合要求。6.4.4空载运行设备,关闭设备各个吸盘上的手动球阀,待系统报警解除后,打开任意一真空吸盘上的手动球阀,检查是否符合要求。6.4.5在模拟脱模试验中手动操作设备各部分控制按钮、旋钮,自动运行设备进行脱模试验,检测控制旋钮及控制按钮工作过程中功能是否符合要求。6.5安全保护装置检查
目测检查起重承载的吊索型号、意外断电报警单元和应急处理的保护装置、电气系统和警示标志及颜色,检查是否符合要求。
6.6模拟脱模试验
模拟脱模试验前准备好一块轨道板、模拟脱模液压系统和工作台,将脱模机安装后(如图1所示),分别进行0.25倍额定负荷脱模试验、150kN脱模力试验和1.1倍额定负荷静载试验。具体方法如下:脱模力油缸向下
中间脱模油缸此内容来自标准下载网
蜂鸣报警灯
中间脱模油缸支点
运动压在轨道
板表面并保持
恒定压力
轨道板
真空泵
图1模拟脱模试验示意图
a)0.25倍额定负荷脱模试验
模拟脱模力油缸
真空压力表
顶升油缸
模拟脱模力油缸
真空吸盘
启动真空脱模机将轨道板吸住,调整模拟脱模系统液压油缸压力,使加载在轨道板四角的液压缸压力之和为轨道板总重的0.25倍;启动脱模机液压系统,缓慢、平稳顶升,离开试验台100mm,再缓慢放下。
TB/T3294—-2013
b)150kN脱模力试验
调整模拟脱模系统液压油缸压力,使加载在轨道板四角的液压缸压力之和为150kN;启动脱模机液压系统,缓慢、平稳项升,离开试验台100mm,悬吊10min,再缓慢放下。c)1.1倍额定负荷静载试验
调整模拟脱模系统液压油缸压力,使加载在轨道板四角的液压缸压力之和为1.1倍额定荷载,并使模拟脱模力油缸锁住;启动脱模机液压系统,单独控制中心脱模油缸使其压力达到1.1倍的额定荷载。
6.7动载试验
采用起吊总重量为1.25倍额定载荷的试验件,并分别在纵、横向质心各偏载额定载荷10%的情况下,各试验三次。
检验规则
检验分为出厂检验和型式检验。每台新造设备在出厂前,均应进行出厂检验,检查与试验项目按表1中带“S\符号的项目进行。设备属下列情况之一时应进行型式检验,检查与试验项目按表1中带“T”符号的项目进行。7.3
新产品试制、定型时;
转厂生产时;
正常生产时结构、材料、工艺等有较大改变,可能影响产品性能时;产品停产三年后,重新恢复生产时;出厂检验结果与上次型式检验有较大差异时。表1检验项目表
检验项目内容
真空脱模机的主要组成部分
真空脱模机的功能要求
额定起重量、额定吸附力
吸附和脱模时间
断电保护和保压时间
外观要求
除锈及面漆
真空吸附系统构成
初次建立真空度时间、连续工作吸附时间、保压时间手动球阀
真空吸盘的数量及分布
刚度、强度、焊接接头
真空吸盘的焊缝质量要求
真空吸盘的时效处理,槽平面度吸盘唇的材质、寿命
吸盘唇的粘结
检验方法
检验类型
检验项目内容
主梁结构形式、功能
主梁刚度、强度、变形量
主梁焊缝质量
主梁气密性
主梁的时效处理、安装孔
顶升脱模系统
防护等级
报警装置
控制检查
电控系统的控制形式
电气的连接
安全保护装置及颜色
模拟脱模试验
动载试验
标志、包装、运输和贮存
表1(续)
TB/T3294-2013
检验方法
检验类型
在设备显著部位应涂上醒目的安全警示标志,安全警示标志及颜色应符合GB2893、GB/T2893(所有部分)的规定。
在设备的明显部位设置设备铭牌,铭牌应标注以下内容:8.1.2
设备型号、编号;
额定功率、额定负载、自重;
出厂日期;
制造商名称、地址。
8.2包装、运输与贮存
包装应符合GB/T191、JB/T8356.1、JB/T8356.2的规定,随机技术文件应采用防潮防湿材料8.2.1
包裹,随机文件应包括以下内容:a)
设备操作说明书;
保修卡;
检验合格证;
发货及备件清单。
长途运输时,应配有在运输过程中不使吊具变形的支架,设备在运输过程中应无破损。8.2.3存放前,应视外表面防锈漆漆皮脱落面积的大小来确定是用补漆的办法还是用整机重新喷漆TB/T3294—2013
的方法进行修补,金属裸露处涂抹黄油。8.2.4长期存放前,须对机械进行保养、修复损坏机件,并对其进行彻底清理,保持技术状态良好。8.2.5应将设备放置在自带的专用支座上并停放在干燥的车间内。不得已停在室外者,应选平坦的地面并铺上木板。停放后用帆布罩盖好。8.2.6在设备停放场地的排列和布置,应保证任何一台设备的进出均不受其他机械的影响。中华人民共和国
铁道行业标准
CRTSⅡ型轨道板专用真空脱模机Special vacuum demioulding machine for the CRTS I track slabTB/T3294—2013
中国铁道出版社出版、发行
(100054,北京市西城区右安门西街8号)读者服务部电话:市电(010)51873174,路电(021)73174中国铁道出版社印刷厂印刷
版权专有侵权必究
开本:880mmx1230mm
2013年4月第1版
字数:15千字
印张:1
2013年4月第1次印刷
151133859
定价:10.00元
小提示:此标准内容仅展示完整标准里的部分截取内容,若需要完整标准请到上方自行免费下载完整标准文档。

标准图片预览:
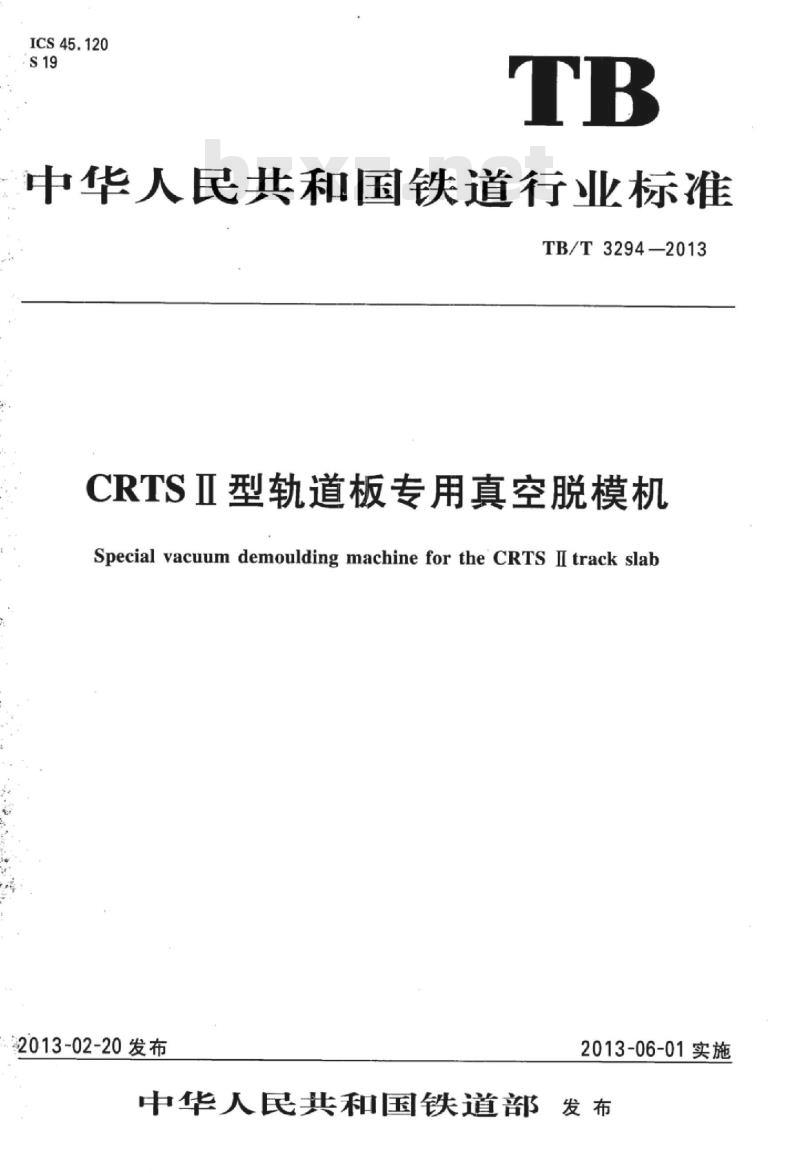
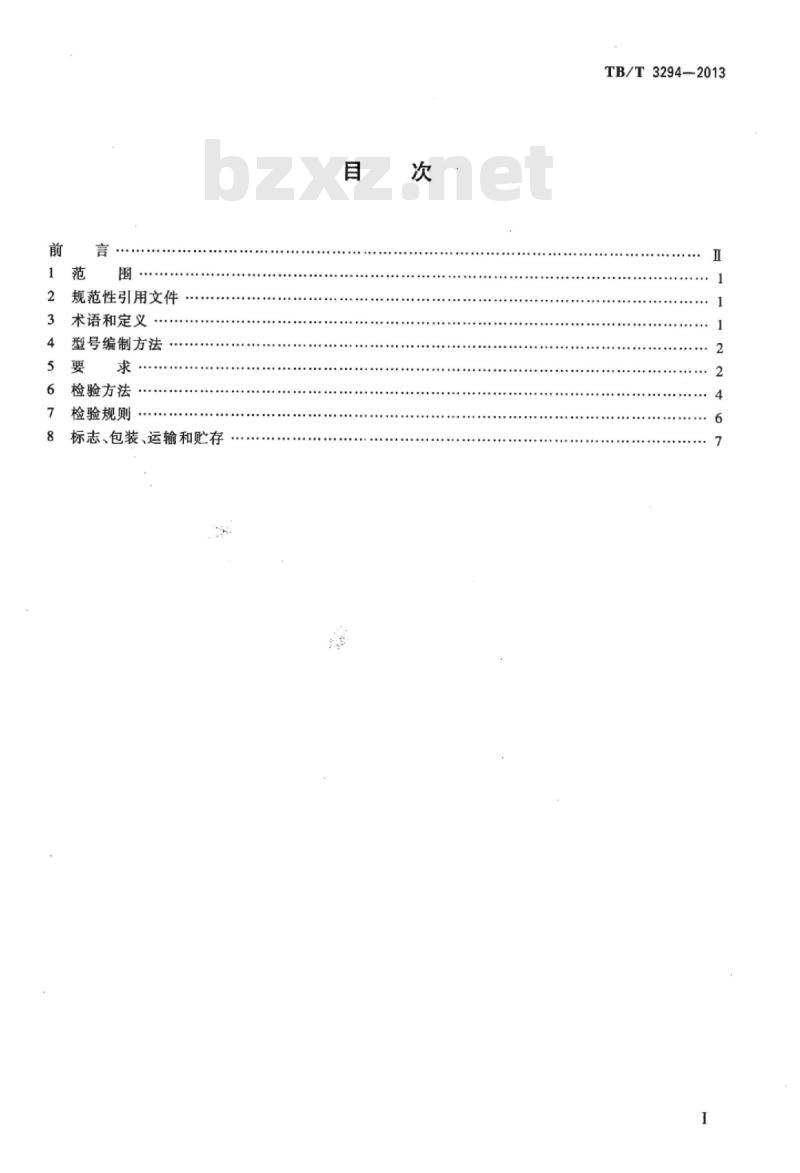
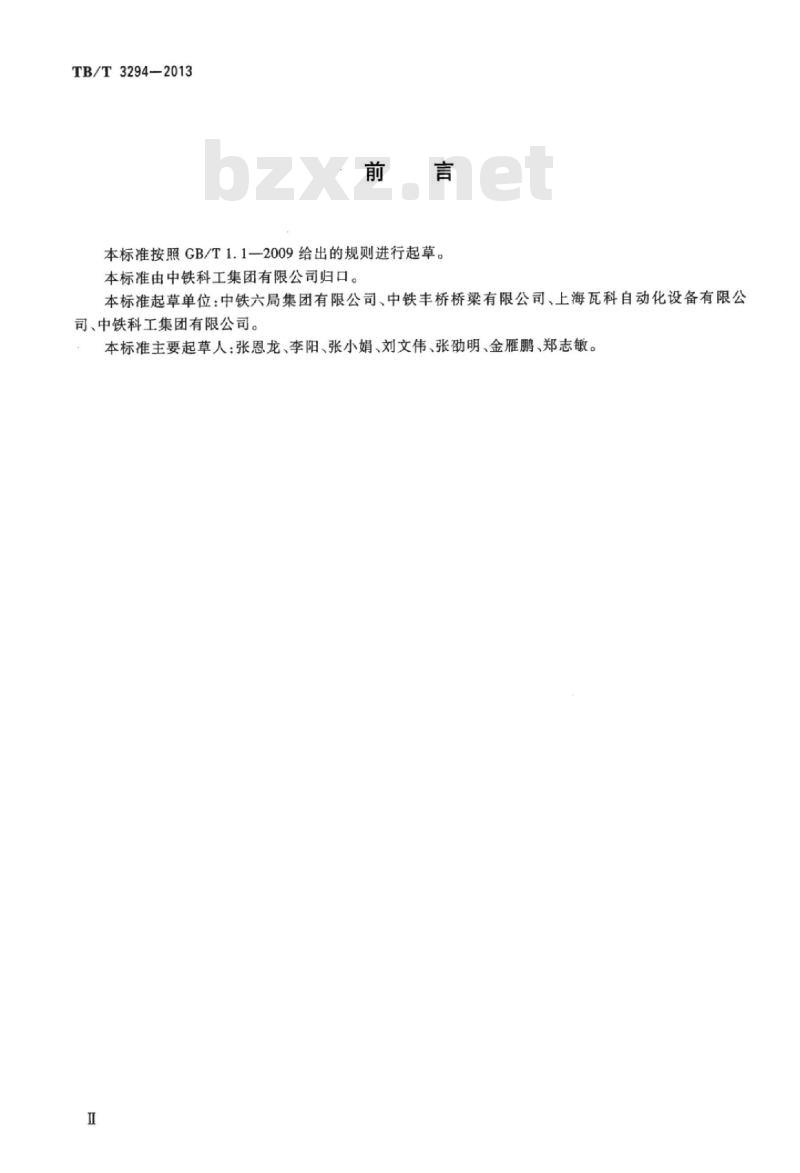
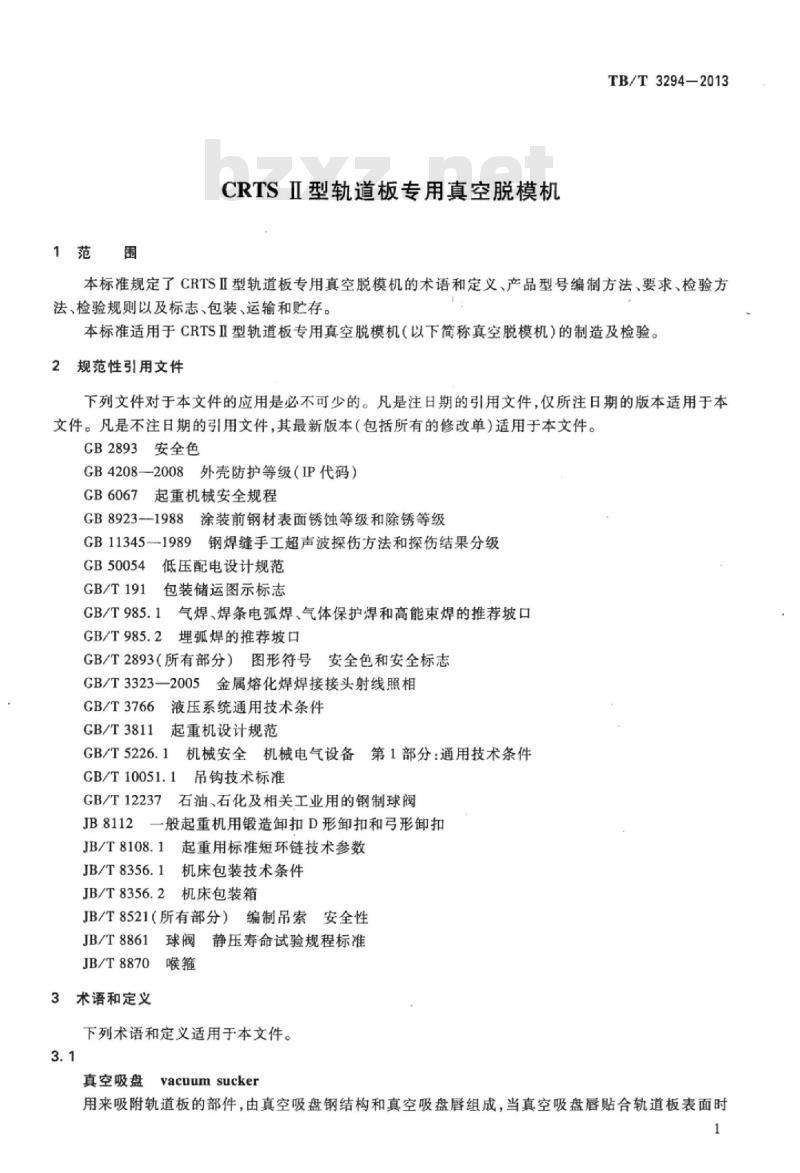
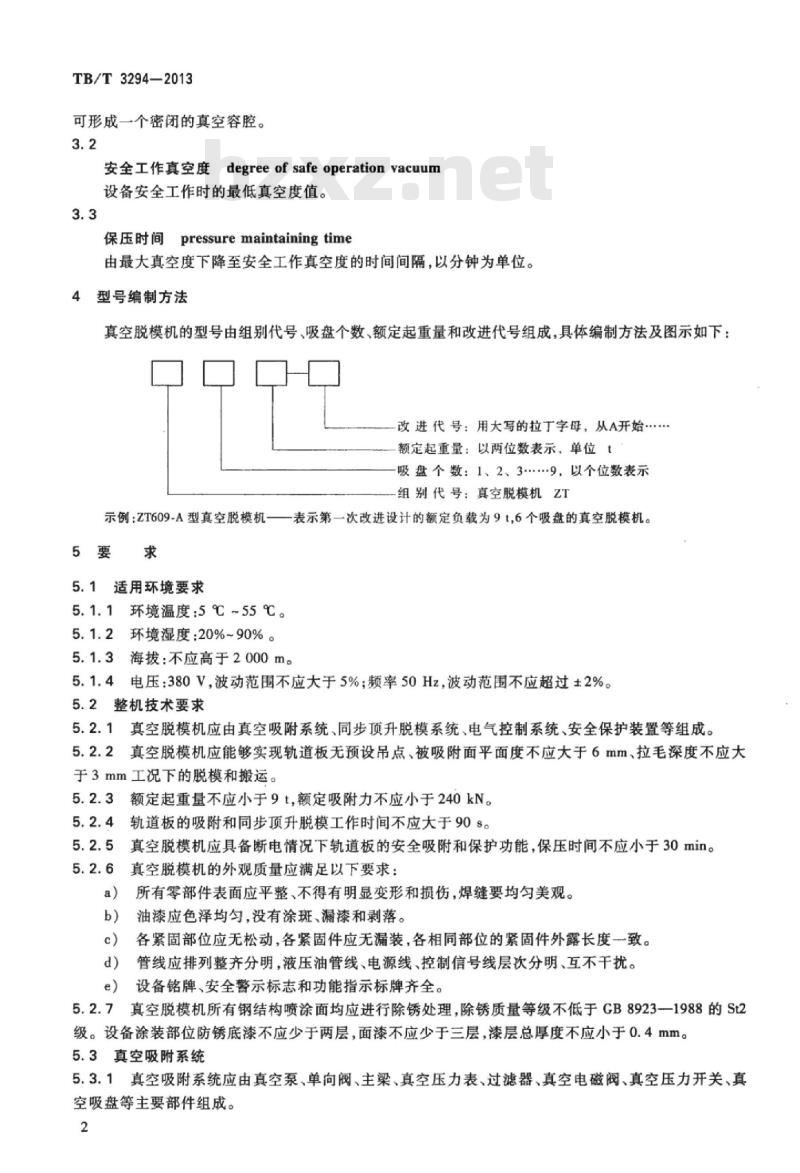
- 热门标准
- TB铁路运输标准
- TB10122-2008 铁路路堑边坡光面(预裂)爆破技术规程
- TB/T1760-1986 客车门锁技术条件
- TB/T1632.4-2005 钢轨焊接 第4部分:气压焊接
- TB/T2563-1995 内燃机车用柴油机机体清洁度测定方法
- TB/T3523.2-2018 交流传动电力机车试验方法第2部分:输入特性试验
- TB/T2769.9-1997 重型轨道车试验方法动力学性能试验方法及评定标准
- TB/T2599-1996 细长钢管内壁涂塑技术条件
- TB/T2820.1-1997 铁路桥隧建筑物劣化评定标准钢梁
- TB/T2521-1995 电力机车平波电抗器装车后温升与电感值试验计算方法
- TB/T3416.3-2015 动车组编码标识系统第3部分:安装地点与位置的标识
- TB/T1932-2009 旅客列车卫生及监测技术规定
- TB/T3170-2007 货车车钩、钩尾框采购和验收技术条件
- TB/T1869.4-2013 铁路信号用变压器第4部分:25 Hz系列轨道变压器
- TB/T2472-93D ●S型道口闪光器
- TB10424-2018 铁路混凝土工程施工质量验收标准
网站备案号:湘ICP备2023016450号-1