- 您的位置:
- 标准下载网 >>
- 标准分类 >>
- 国家标准(GB) >>
- GB/T 38642-2020 工业机器人生命周期风险评价方法
标准号:
GB/T 38642-2020
标准名称:
工业机器人生命周期风险评价方法
标准类别:
国家标准(GB)
标准状态:
现行出版语种:
简体中文下载格式:
.zip .pdf下载大小:
2.42 MB

点击下载
标准简介:
GB/T 38642-2020.Industrial robot life cycle risk assessment methods.
1范围
GB/T 38642规定了工业机器人生命周期风险评价方法的基本原则、风险评价程序及文件要求,并给出了工业机器人危险源识别、AGV危险源识别及风险评价和风险减小实例。
GB/T 38642适用于工业机器人的生命周期风险评价。本标准建立的安全原则可被其他类型的机器人参考使用。
GB/T 38642不包含工业机器人系统集成的风险评价。针对特殊的应用(焊接、激光切割、机械加工等)可能产生另外的危险,这些危险宜进行针对性的风险评估。
2规范性引用文件
下列文件对于本文件的应用是必不可少的。凡是注日期的引用文件,仅注日期的版本适用于本文件。凡是不注日期的引用文件,其最新版本(包括所有的修改单)适用于本文件。
GB 11291.1-2011工业环境用机器人 安全要求第)1 部分:机器人
GB 11291.2机器人 与机器人装备工业机器 人的安全要求第 2部分:机器人系统与集成
GB/T 15706-2012机械安全 设计通 则风险评 估与风险减小
GB/T 16855.1-2018机械安全 控制 系统安全相关部件第 1部分:设计通则
GB/T 16856-2015机械安全风险评估 实施指 南和方法举例
GB 28526-2012机械电气安全安全相关电气、电子和可编程电子控制系统的功能安全
3术语和定义
下列术语和定义适用于本文件。
3.1
工业机器人 industrial robot
自动控制的、可重复编程、多用途的操作机,可对三个或三个以上轴进行编程。它可以是固定式或移动式。在工业自动化中使用。
注1:工业机器人包括:
一操作机,含致动 器;
一控制器,含示教盒和某些通讯接口(硬件和软件)。
注2:这包括某些集成的附加轴。
[GB/T 12643-2013,定义2.9]
3.2
充分的风险减小 adequate risk reduction
至少符合法律法规的要求并考虑了现有技术水平的风险减小。
注:确定风险是否充分减小的准则在GB/T 15706-2012的5.6.2中给出。
[GB/T 15706-2012,定 义3.18]

部分标准内容:
中华人民共和国国家标准
GB/T38642—2020
工业机器人生命周期风险评价方法Industrial robot life cycle risk assessment methods2020-04-28发布
国家市场监督管理总局
国家标准化管理委员会
2020-11-01实施
GB/T38642—2020
规范性引用文件
术语和定义
基本原则
风险评估和风险减小的策略
风险减小目标
5风险评价程序
般规定
确定风险评价对象
成立风险评价工作组
收集评价对象相关信息
生命周期划分及危险区域划分
风险评估
出具风险评价报告
风险减小
6文件
附录A(资料性附录)
附录B(资料性附录)
附录C(资料性附录)
参考文献
工业机器人(不含AGV)危险源识别AGV危险源识别
风险评价和风险减小示例
本标准按照GB/T1.1-2009给出的规则起草本标准由中国机械工业联合会提出。本标准由全国自动化系统与集成标准化技术委员会(SAC/TC159)归口。GB/T38642—2020
本标准起草单位:上海电器科学研究院、山东鲁能智能技术有限公司、安徽省配天机器人技术有限公司、哈工大机器人集团有限公司、青岛钢铁侠科技有限公司、上海电器科学研究所(集团)有限公司、上海机器人产业技术研究院有限公司、上海电器设备检测所有限公司、上海添唯认证技术有限公司、佛山小林智慧科技发展有限公司
本标准主要起草人:道深、邢琳、傅孟朝、庞泰、于振中、张锐、曹际娜、陈灏、郑军奇、王爱国、湛志勇。
1范围
工业机器人生命周期风险评价方法GB/T38642—2020
本标准规定了工业机器人生命周期风险评价方法的基本原则、风险评价程序及文件要求,并给出了工业机器人危险源识别、AGV危险源识别及风险评价和风险减小实例。本标准适用于工业机器人的生命周期风险评价。本标准建立的安全原则可被其他类型的机器人参考使用。
本标准不包含工业机器人系统集成的风险评价。针对特殊的应用(焊接、激光切割、机械加工等)可能产生另外的危险,这些危险宜进行针对性的风险评估规范性引用文件
下列文件对于本文件的应用是必不可少的。凡是注日期的引用文件,仅注日期的版本适用于本文件。凡是不注日期的引用文件,其最新版本(包括所有的修改单)适用于本文件GB11291.1一2011工业环境用机器人安全要求第1部分:机器人GB11291.2机器人与机器人装备工业机器人的安全要求第2部分:机器人系统与集成GB/T15706—2012机械安全设计通则风险评估与风险减小GB/T16855.1一2018,机械安全控制系统安全相关部件第1部分:设计通则GB/T16856—2015机械安全风险评估实施指南和方法举例GB28526—2012机械电气安全安全相关电气、电子和可编程电子控制系统的功能安全术语和定义
下列术语和定义适用于本文件。3.1
工业机器人industrialrobot
自动控制的、可重复编程、多用途的操作机,可对三个或三个以上轴进行编程。它可以是固定式或移动式。在工业自动化中使用。注1:工业机器人包括:
操作机,含致动器;
控制器,含示教盒和某些通讯接口(硬件和软件)。注2:这包括某些集成的附加轴,[GB/T12643—2013.定义2.9
充分的风险减小
adequateriskreduction
至少符合法律法规的要求并考虑了现有技术水平的风险减小。注:确定风险是否充分减小的准则在GB/T15706一2012的5.6.2中给出。[GB/T15706—2012.定义3.18]GB/T38642—2020
工业机器人生命周期industrialrobotlifecycle从工业机器人产品运输、使用到回收利用的整个过程。注:本标准所述的工业及其生命周期一般包括运输、安装调试、示教、运行、清洁、维护、故障查找/故障排查、拆卸停用等过程。
接触区
contact zone
机器人最大空间所能覆盖的区域3.5
安全防护空间
safeguarded space
由周边安全防护装置确定的空间。[GB11291.2—2013,定义3.13.3]3.6
控制站
control station
机器人系统的部分,包括一个或多个控制装置,用以激活或停止系统或系统部件的功能注:控制站可以是固定式的或移动式的3.7
控制区
control zone
机器人的控制站所在的区域。
注:通常处于安全防护空间外
aeeiKAca
自动导引车automatedguidedvehicle;AGv装备有电磁或光学等自动导引装置,由计算机控制,以轮式移动为特征,自带动力或动力转换装置,并且能够沿规定的导引路径自动行驶的运输工具,一般具有安全防护、移载等多种功能[GB/T30030—2013.定义2.1]
riskassessment
风险评估
包括风险分析和风险评价在内的全过程。[GB/T15706—2012,定义3.17]3.10
可合理预见的误用
reasonablyforeseeablemisuse
不是按设计者预定的方法而是按照常理可预见的人类习惯来使用机器[GB/T15706—2012,定义3.24]
residual risk
剩余风险
采取保护措施之后仍然存在的风险。[GB/T15706—2012.定义3.13]3.12
commonzone
公共区
没有单独预留给某个AGV的区域。[EN1525:1997.定义3.1.1]
危险区hazardzone
危险增加的区域,属于公共区域一部分注:没有充分的人员安全距离和货物运输操作的区域[EN1525:1997.定义3.1.2]
限制区restrictedzone
仅授权者才能允许进人的物理隔离的区域。[EN1525:1997.定义3.1.3]
performancelevel;PL
性能等级
在可预期条件下,用于规定控制系统有关安全部件执行安全功能的离散等级。注:改写GB/T16855.1-2018定义3.1.23所需的性能等级
requiredperformancelevel;PL,每种安全功能为达到所需的风险减小所应用的性能等级(PL)。Aca
注:改写GB/T16855.1-2018,定义3.1.24。安全完整性等级safetyintegritylevel;SILGB/T38642—2020
一种离散的等级(三种可能的等级之一)用于规定分配给安全相关电气控制系统(SRECS)安全相-iika
关控制功能的安全完整性要求。在这里,安全完整性等级3是最高的,安全完整性等级1是最低的注:改写GB/T28526—2012.定义3.2.23。4基本原则
4.1风险评估和风险减小的策略
本标准是为了确保工业机器人满足现行的标准,进而确保在使用过程中对人员、环境及财产是安全的。
风险评估和风险减小的策略如下:确定工业机器人的各种限制,包括预定使用和任何可合理预见的误用:识别危险及其伴随的危险状态;一对每一种识别出的危险和危险状态进行风险评估;评价风险并决定是否需要减小风险:一采取保护措施消除危险或减小危险伴随的风险。风险减小过程选代三步法应符合GB/T15706—2012中第4章的要求。2风险减小目标
按5.6.2的规定,当风险指数小于或等于2时,无需进行进一步风险减小;当风险指数大于2时,应进行进一步风险减小,并使剩余风险的风险指数小于或等于2;针对特殊应用或工艺,应进行充分的风险减小。
GB/T38642—2020
5风险评价程序
5.1一般规定
工业机器人风险评价,是针对确定的评价对象,进行的危险、危险状态与危险事件、发生危险概率和后果严重程度评估、风险类别确定、风险等级评定,以及风险减小和重新评价的选代过程(见图1),其工作程序一般包括下列9部分:
确定风险评价对象;
成立风险评价工作组;
收集评价对象相关信息;
进行子系统划分、危险状态及危险事件分析;评估发生危险的概率和后果严重程度;确定风险类别;
评定风险等级;
出具风险评价报告;
对于不可接受的风险,采取措施降低风险,再重新进行评价开始
1. 确定风险评价对象
2.成立风险评价上作
3. 收评价对象相关信息
4.机器人生合周期别分和
危险区划分
5.风险坪估
6.风险等级评定
7.出尺风险评价提告免费标准bzxz.net
8.风给是否已被充分
9.降低风险
风险评估和风险减小程序
5.2确定风险评价对象
在进行风险评价前,应首先确定评价对象。本标准评价对象为工业机器人。5.3成立风险评价工作组
GB/T38642—2020
在对工业机器人进行风险评价及风险减小时,宜由一个评价组完成并且达成共识,该评价组应由具备不同学科知识、多种经验和专业技能的专家组成。宜明确实施项自的评价组组长,按照本标准开展风险评价工作并在执行过程中全面负责,将评价结果和(或)建议报告给相关人员。实际工作中不一定总是要建立风险评价评估组,因为有些机械的危险已被充分认知宜根据风险评价需要的技能和专业知识选择评价组成员。评价组中宜包括下列人员能回答关于机械设计和功能方面技术问题的人员:一具备机械操作、调试、保养、维修等实际经验的人员;一了解类机器人产品事故历史的人员:熟悉有关法规、标准,特别是GB/T15706—2012以及与所评价机械有关的具体安全问题的人员;
—了解人为因素的人员(见GB/T15706—2012中的5.5.3.4)。leeiKAca
不同的团队针对相似的情况的分析所形成的详细结果存在略微差异,应尽量完善评价组的知识和专业技能,提高该风险评价结果的可信度5.4收集评价对象相关信息
5.4.1样品说明
对被评估的工业机器人进行基本说明,至少包括电源要求、类型(例如关节机器人,SCARA机器人、并联机器人、AGV等)、驱动方式、安全系统、机械臂骨架材料说明等。5.4.2使用说明
使用说明应包含以下内容:
一安全防护空间防护说明,例如互锁功能的围栏保护说明,或者对应安全等级的保护设备说明:一被评估样品是否包括末端执行器;被评估样品防护等级说明;
被评估样品使用环境说明,例如爆炸环境;被评估样品的应用领域说明。
5.4.3使用限制
5.4.3.1预定使用
在工业机器人的生命周期中,所有与机器人有关的人员都应经过严格培训。当机器人运行在自动模式时,机器人宜工作在带有互锁装置的围栏中间,围栏应有一定的高度,防止人员跨越,围栏通常由固定式防护装置及安全光幕、安全光栅等具有安全等级的设备组成。末端执行器应按GB11291.2的要求5来设计。机器人的系统集成在开始运行之前,应经过安全评估。机器人应按照要求进行清洁/维护。应对产品进行预定使用的描述,如果存在与上述预定使用不一致的情况,应在报告中说明。5.4.3.2可合理预见的误用
可合理预见的误用是未按照设计者预定的方法而是按照常理可预见的人类习惯来使用工业机GB/T38642—2020
器人。
常见的误用如下:
售后服务人员没有经过充分的培训而进行售后服务或维护;机械臂在调试时碰撞到其他设备或围栏;调试时,未正确安装机器人;
机器人过载:
没经过授权或培训的人员进入机器人安全防护空间:非专业人员拆装;
工作环境不合适;
其他。
空间限制
应对工业机器人室内使用或室外使用进行说明;应对机器人使用环境限制进行描述,例如非爆炸环境或者无火环境;应对机器人臂展、运行空间进行说明。5.4.3.4时间限制
应对预计使用年限、每天使用班次和工作周期进行限定。为了获得运行寿命,机器人应按照说明书进行良好维护。
人员限制
应对操作人员的要求进行说明,例如培训、资质等要求。5.5
生命周期划分及危险区域划分
5.5.1生命周期划分
可导致危险状态的任务清单见表1。表1可导致危险状态的任务清单
生命周期阶段
安装调试
清洁维护
故障查找/故障排查
拆卸停用
提升、加载、包装、运输、卸载、拆包等任务
集成到产线、设备组装、固定、连接电源、无负载手动测试等调整以及设置保护设备及其他元件、机器功能参数(例如速度、气压、压力、行程限制)的微调和设定、固定末端执行器、示教程序、最终程序的验证控制/检查、自动运行、运行期间的微小干预、停机后的重新启动调整,重新标定精度.清洁,拆卸/移除机器的部件、组件和装置,隔离及能源耗散,润滑.更换磨损部件
故障查找,隔离及能源释放,控制装置和保护装置失效后的恢复,阻塞之后的恢复,更换机器的部件、组件和装置,营救被困人员,重新标定精度,重新设定断开连接及能源消散、拆卸、提升、加载、包装、运输、卸载注1:本表列举的任务为工业机器人常见任务,某些情况下工业机器人/AGV的任务可能与表中不一致。附录A、附录B给出的是工业机器人/AGV的常见任务示例注2:不宜照搬这些条目,以选择和组织合适的文字,以最方便的方式进行描述6
5.5.2危险区域划分
GB/T38642—2020
危险区域包括控制区、安全防护空间(运行空间)、接触区、危险区、限制区、公共区等。工业机械臂危险区域的示例如图2所示,AGV危险区域的示例如图3所示。安全防护空间
控制区
工业机械臂危险区域图
危险区
限制区
危陵区
公共区
注:箭头方向为AGV运动方向。
AGV危险区域图
5.6风险评估
5.6.1危险识别
针对工业机器人生命周期中各个阶段可能出现的危险源,参考附录A及附录B进行危险源识别。注:并非所有在本标准描述的危险都适用于每一台机器人,同样某一特定危险情况的风险水平,在不同机器人间也可能有所不同,因此在本标准中识别的风险对不同机器人可能会有不同,宜进行风险评估,明确危险的风险指数。
5.6.2风险估计
危险估计按GB/T16856—2015中6.3规定的风险图的方法实施GB/T38642—2020
S、F、O及A的定义如下:
S:伤害的严重程度:
F:暴露在危害环境下的频率或时间:O:危险事件出现的可能性;
A:避免或减少危害的可能性。
根据图4可以得到风险指数。
严重程度
S1.轻微的
s2,的
说明:
缺娱度
上1,F2
F1,很少的
F2,频紫的
危险事件发牛的概本
02,低
02,低
避免的可能性
2,不能
A2、不可能
A2,不可能
A2,不可能
风险数
轻微伤害(通常是可以恢复的伤害,例如擦伤、淤青、需简单包扎的轻伤等),损工时间不可超过2天,重伤(不可恢复的伤害或死亡,包括骨折,四肢粉碎性砸伤,严重穿刺,需要缝针的伤害,重大骨折伤害等),大于2天的损工时间
每个班次暴露在危害环境下小于或等于2次,或者每个班次累计少于15min。每个班次暴露在危害环境下大于2次,或者每个班次累计多于15min。低,成熟的科技,证明过的及被认可的安全应用:鲁棒性强。中,过去两年发生过技术问题;具有良好培训的工人且在工作岗位上已经6个月,在工作岗位上存在不合适的行为。
高技术故障常发生(每6个月发生一次或者更额繁);过去2年发生过技术间题;没经过良好培训的工人且在工作岗位上少于6个月,在工作岗位上存在不合适的行为。在某种情况下有可能避开危害,运动速度小于0.25m/s.操作工熟悉面临的风险,以及指明了危险状态或危险事件,操作工能够注意到危险状态且能够对危险状态做出反应。不可能避开危害,运动速度大于或等于0.25m/s.操作工不熟悉面临的风险,以及危险状态或危险事件,操作工不能够注意到危险状态且不能够对危险状态做出反应。图4用于风险估计的风险图示例
出具风险评价报告
评价组在完成风险分析和风险等级评定工作后,应出具风险评价报告。评价报告至少包括以下内容:
评价对象基本信息;
评价组成员名单;
一评价时间和地点;
评价依据的方法;
评价结果及建议措施等。
5.8风险减小
5.8.1概述
GB/T38642—2020
通过消除危险,或通过分别或同时减小下述决定相关风险的两个因素,可以实现风险减小:所考虑危险产生伤害的严重程度;伤害发生的概率。
所有预定用于达到此目标的保护措施应按5.8.2~5.8.4的顺序进行,即“三步法”。5.8.2本质安全设计措施
本质安全设计措施通过适当选择工业机器人的设计特性和/或暴露人员与工业机器人的交互作用消除危险或减小相关的风险
注:第一步是不采用安全防护或补充保护措施等保护措施而消除危险的唯一阶段如果通过提高控制系统性能来减小风险,宜按GB/T16855.1-一2018或GB28526一2012等标准要求进行控制系统功能安全评估,应在资料中清楚地说明该控制系统所满足的功能安全等级及评估时所采用的标准。风险指数对应的功能安全等级要求见表2。表2风险指数相应功能安全等级要求风险指数
(GB/T16856—2015)
PL,等级
(GB/T16855.1—2018)
SIL等级
(GB28526—2012)
无对应等级
注:风险指数的确定按GB/T16856—2015中6.3的规定:PLr的确定按GB/T16855.1—2018中附录A的规定;PLr等级和SIL等级的对立关系按GB/T16855.1—2018中表3的规定。5.8.3安全防护和(或)补充保护措施考虑到预定使用和可合理预见的误用,如果通过本质安全设计措施消除危险或充分减小与其相关的风险实际不可行,则可使用经适当选择的安全防护和补充保护措施来减小风险。应符合GB11291.12011中关于安全防护和/或补充保护措施的要求。5.8.4使用信息
尽管采用了本质安全设计措施、安全防护和(或)补充保护措施,但风险仍然存在时,则应在使用信息中明确剩余风险:该信息应包括但不限于下列内容:使用机械的操作程序符合机械使用人员或其他暴露于机械有关危险的人员的预期能力;
小提示:此标准内容仅展示完整标准里的部分截取内容,若需要完整标准请到上方自行免费下载完整标准文档。

标准图片预览:
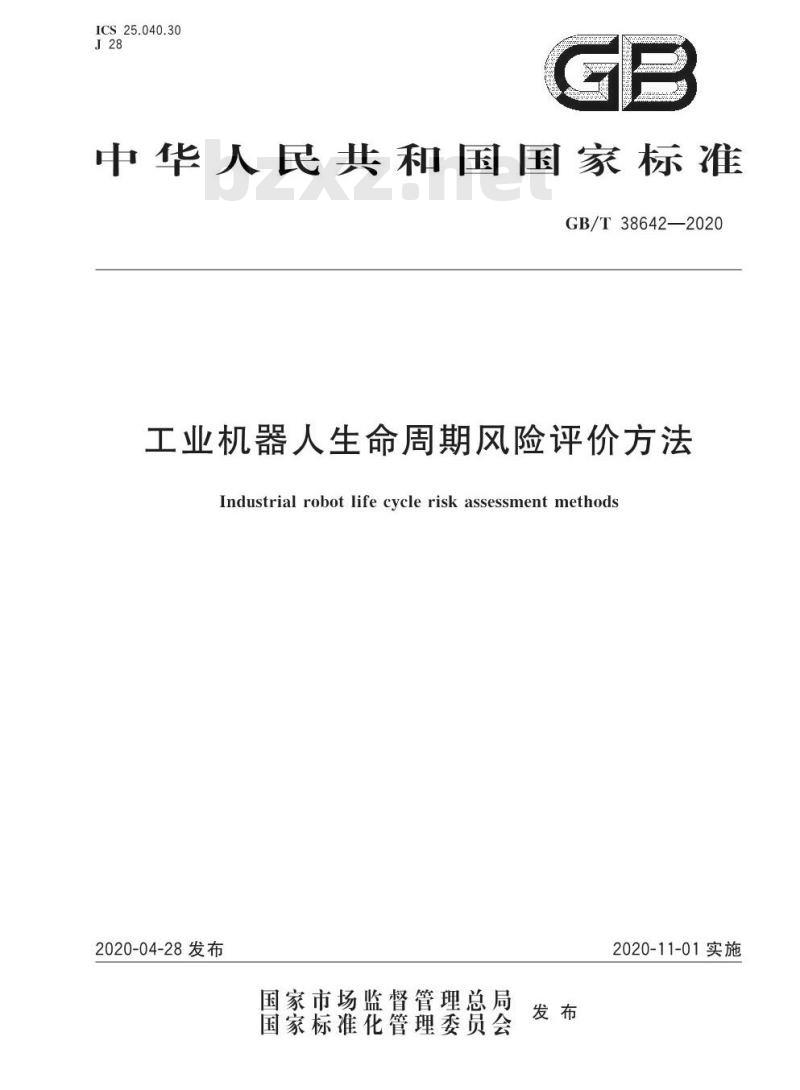
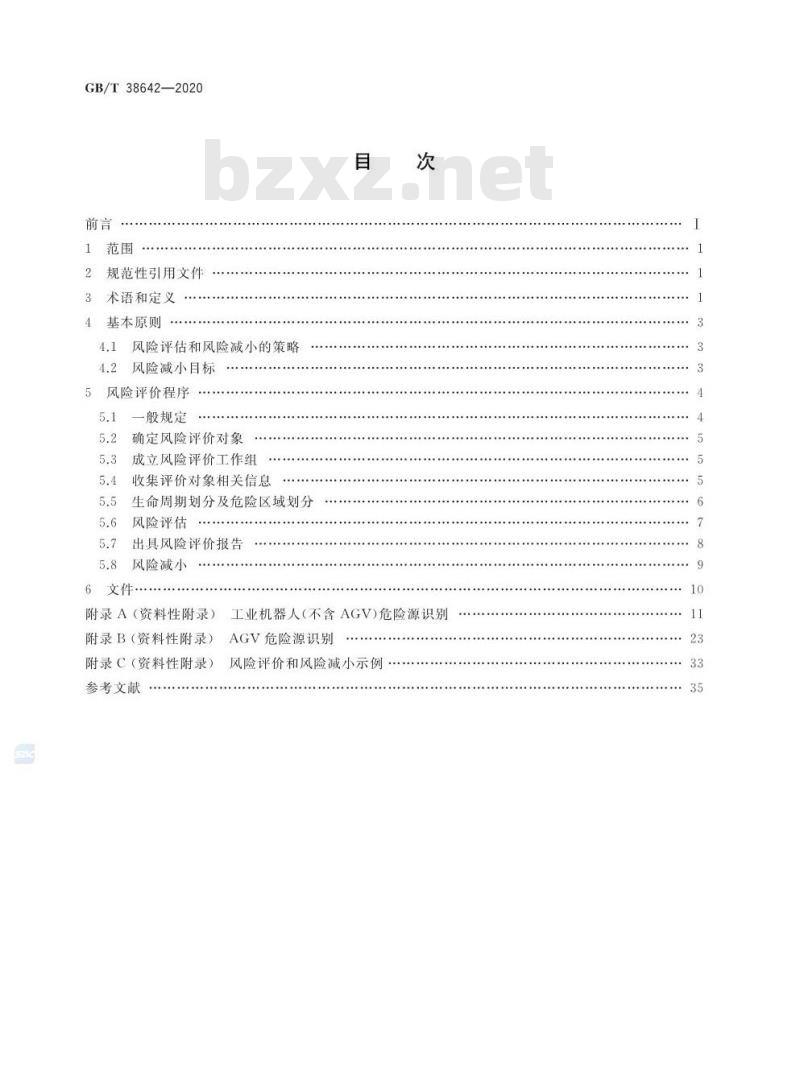
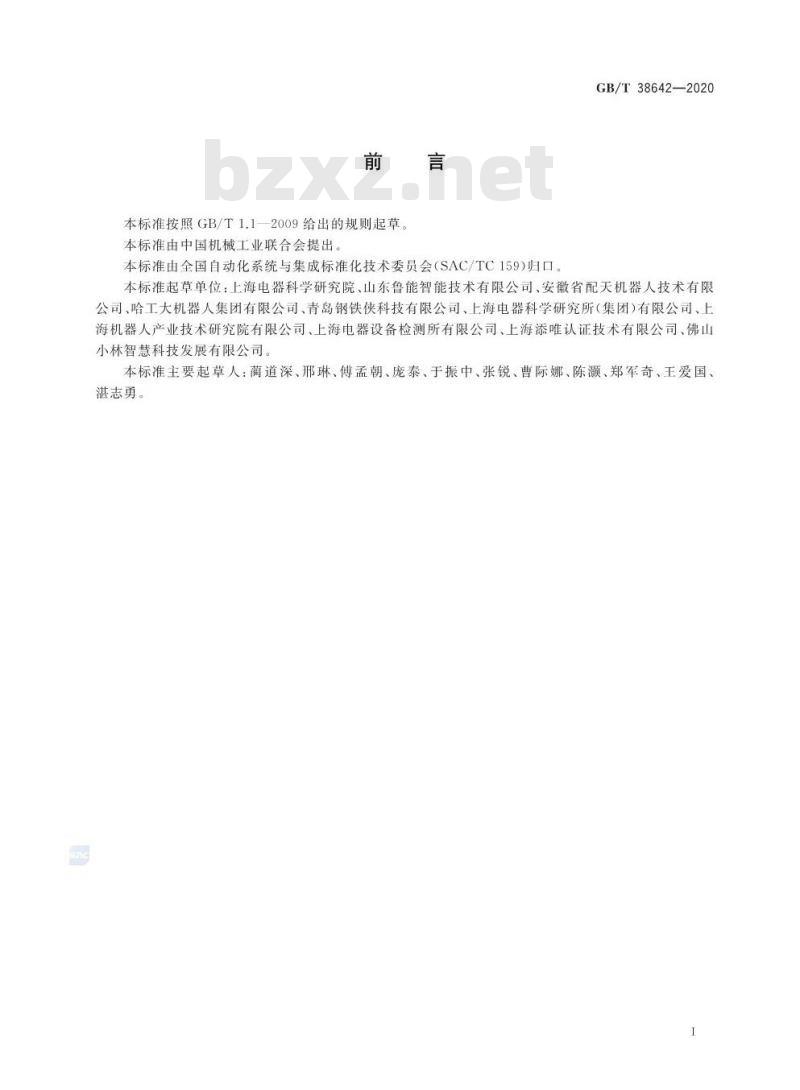
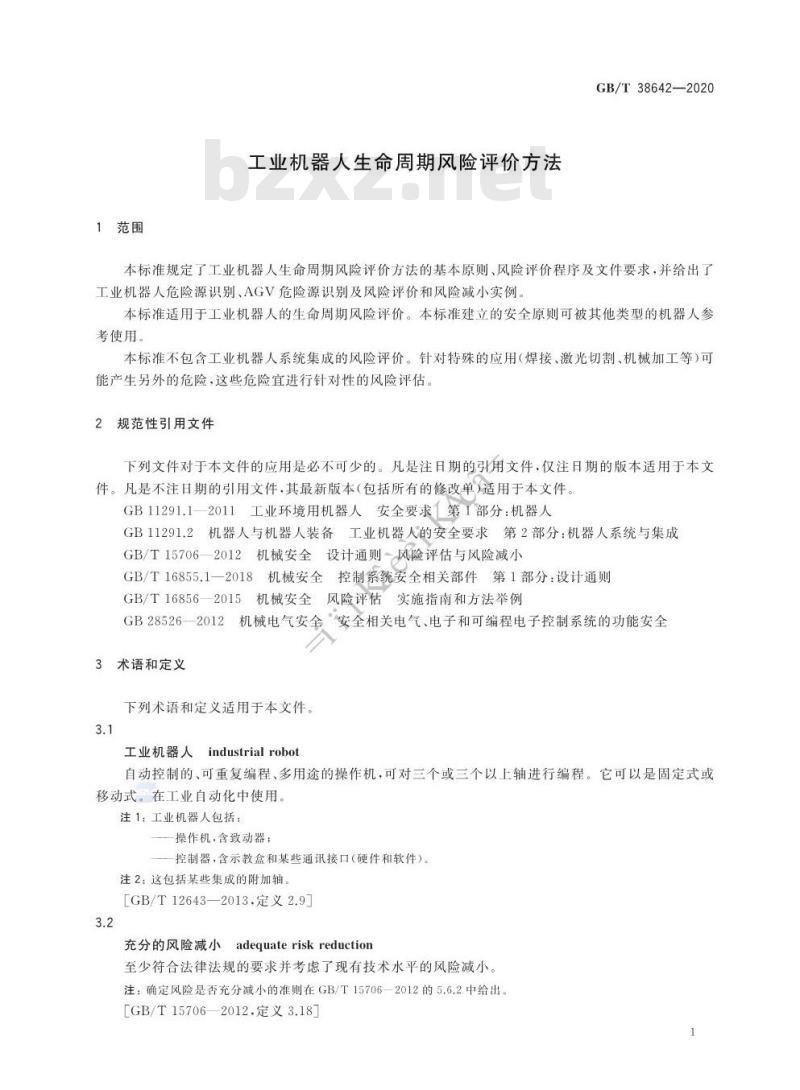
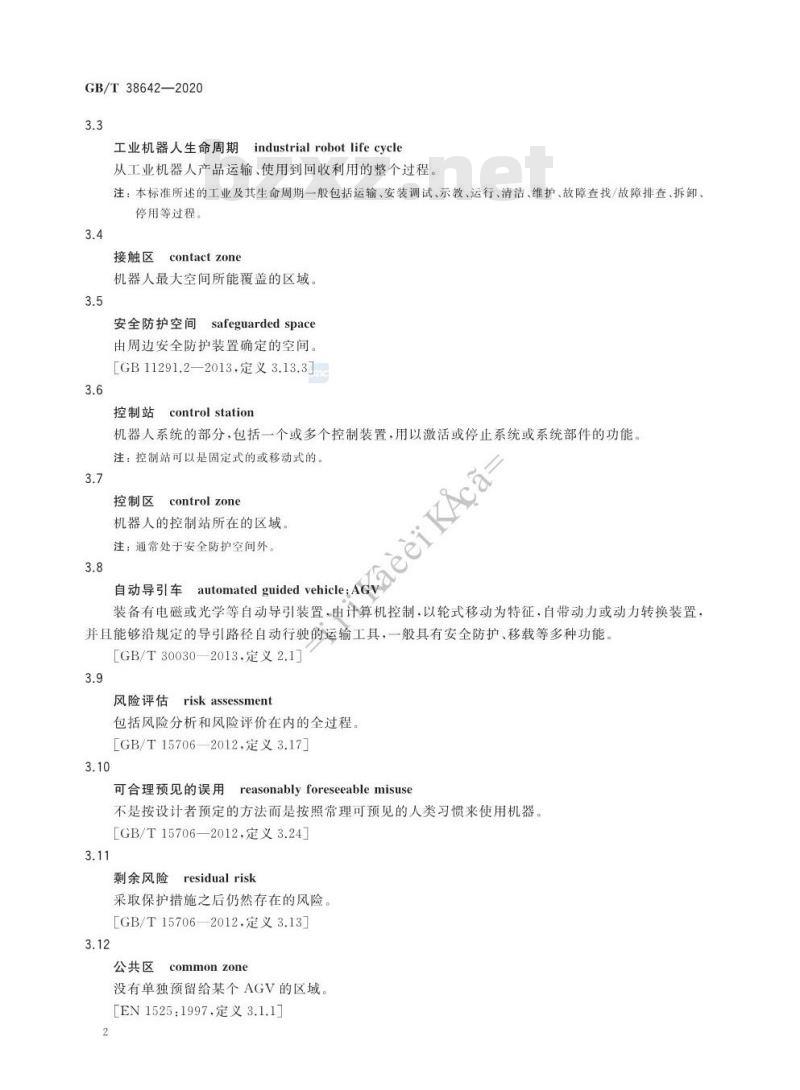
- 热门标准
- GB国家标准
- GB/T2828.1-2012 计数抽样检验程序 第1部分:按接收质量限(AQL)检索的逐批检验抽样计划
- GB/T228.1-2021 金属材料 拉伸试验 第1部分:室温试验方法
- GB/T3836.1-2021 爆炸性环境 第1部分:设备 通用要求
- GB/T5972-2023 起重机 钢丝绳 保养、维护、检验和报废
- GB/T51435-2021 农村生活垃圾收运和处理技术标准
- GB50777-2012 ±800KV及以下换流站构支架施工及验收规范
- GB50661-2011 钢结构焊接规范
- GB7521—1987 多个控制器在一CA MAC机箱中
- GB/T29863-2023 服装制图
- GB50057-2010 建筑物防雷设计规范
- JGJ130-2011 建筑施工扣件式钢管脚手架安全技术规范
- GB/T4458.2—2003 机械制图装配图中零、部件序号及其编排方法
- GB/T43542-2023 机关办公区域物业服务监管和评价规范
- GB/T1804-2000 一般公差 未注公差的线性和角度尺寸的公差
- GB/T13477.19-2017 建筑密封材料试验方法 第19部分:质量与体积变化的测定
网站备案号:湘ICP备2023016450号-1