- 您的位置:
- 标准下载网 >>
- 标准分类 >>
- 机械行业标准(JB) >>
- JB/T 10792.2-2007 五轴联动立式加工中心 第2部分:技术条件
标准号:
JB/T 10792.2-2007
标准名称:
五轴联动立式加工中心 第2部分:技术条件
标准类别:
机械行业标准(JB)
标准状态:
现行-
发布日期:
2007-10-08 -
实施日期:
2008-03-01 出版语种:
简体中文下载格式:
.rar.pdf下载大小:
5.16 MB

点击下载
标准简介:
标准下载解压密码:www.bzxz.net
JB/T 10792的本部分规定了五轴联动立式加工中心设计、制造和验收的基本要求。本部分适用于线性轴线行程至2000mm,加工叶片、叶轮等用途的普通精度五轴联动立式加工中心。 JB/T 10792.2-2007 五轴联动立式加工中心 第2部分:技术条件 JB/T10792.2-2007

部分标准内容:
ICS25.040.20
备案号:21865—2007
中华人民共和国机械行业标准 JB/T 10792.2—2007
五轴联动立式加工中心
第2部分:技术条件
The 5-axes simultaneous vertical machining centersPart2:Specifications
2007-10-08发布
2008-03-01实施
中华人民共和国国家发展和改革委员会发布前言:
1范围
2规范性引用文件,
3一般要求
4附件和工具.
安全卫生,
加工和装配质量,
空运转试验
7.1温升、主运动和进给运动试验,功能试验.
连续空运转试验。
8负荷试验(按设计编制的负荷试验规范进行)8.1机床应做下列负荷试验
机床承载工件最大重量的运转试验8.2
机床主传动系统最大扭矩的试验机床最大切削抗力的试验
8.5机床主传动系统达到最大功率的试验9最小设定单位试验..
最小设定单位试验的分类及要求直线坐标最小设定单位试验
回转坐标最小设定单位试验.
原点返回试验,
原点返回试验的分类及要求
直线坐标原点返回试验..
回转坐标原点返回试验
11精度检验。
12随行技术文件..
参考文献
图1直线坐标最小设定单位试验方法,A
图2回转坐标最小设定单位试验方法图3直线坐标原点返回试验方法
图4回转坐标原点返回试验方法
JB/T10792.2—2007
前·言
JB/T10792《五轴联动立式加工中心》分为以下两部分:第1部分:精度检验;
一第2部分:技术要求。
本部分为JB/T·10792的第2部分。JB/T10792.2-—2007
请注意本部分的某些内容有可能涉及专利。本部分的发布机构不应承担识别这些专利的责任本部分由中国机械工业联合会提出。本部分由全国金属切削机床标准化技术委员会(SAC/TC22)归口。本部分起草单位:北京机电院高技术股份有限公司。本部分主要起草人:高琦、李锦武、芦金旗、刘景祎、郭庆兴、肖业喜。本部分为首次发布。
1范围
JB/T10792.2—2007
五轴联动立式加工中心第2部分:技术条件JBT10792的本部分规定了五轴联动立式加工中心设计、制造和验收的基本要求。本部分适用于线性轴线行程至2000mm,加工叶片、叶轮等用途的普通精度五轴联动立式加工中心。2规范性引用文件
下列文件中的条款通过JB/T10792的本部分的引用而成为本部分的条款。凡是注日期的引用文件,其随后所有的修改单(不包括勘误的内容)或修订版均不适用于本部分,然而,鼓励根据本部分达成协议的各方研究是否可使用这些文件的最新版本。凡是不注日期的引用文件,其最新版本适用于本部分。GB/T3168一1993数字控制机床操作指示形象化符号(neqISO2972:1979)GB5226.1一2002机械安全机械电气设备第1部分:通用技术条件(IEC60204-1:2000,IDT)GB/T6576—2002机床润滑系统(ISO5170:1997,MOD)气动系统通用技术条件(ISO4414:1998,IDT)GB/T7932—2003
GB/T9061-2006金属切削机床通用技术条件GB/T16769—1997金属切削机床噪声声压级测量方法(neqISO/DIS230:5.2:1996)GB/T17421.2一2000机床检验通则第2部分:数控轴线的定位精度和重复定位精度的确定(eqvISO 230-2:1997)
GB18568-2001
JB/T9872—1999
JB/T9873—1999
加工中心安全防护技术条件
金属切削机床机械加工件通用技术条件金属切削机床焊接件通用技术条件JB/T9874—-1999
金属切削机床装配通用技术条件金属切削机床结合面涂色法检验及评定JB/T9876—1999
JB/T9877—1999
金属切削机床清洁度的测定
金属切削机床液压系统通用技术条件JB/T10051—1999
JB/T10792.1--2007五轴联动立式加工中心第1部分:精度检验3般要求
本部分是对GB/T9061、JB/T9872、JB/T9874的补充和具体化。按本部分验收机床时,应同时对上述标准中未经本部分具体化的有关的验收项目进行检验。4附件和工具
4.1应随行供应下列附件和工具
a)垫铁及地脚螺栓:1套;
b)专用调整工具:1套。
4.2可按协议供应扩大机床使用功能的特殊附件。5安全卫生
5.1机床的安全防护应符合GB18568和GB5226.1的有关规定。5.2按GB/T16769的规定检测机床的空运转噪声。机床运转时,不应有不正常的尖叫声和冲击声。JB/T10792.2--2007
机床在空运转条件下,整机噪声声压级不应超过83dB(A)。6加工和装配质量
6.1床身、工作台、立柱、主轴箱、蜗轮箱、头架箱体、尾架箱体、滑板、滑枕等为重要铸件(焊接件),应在粗加工后进行时效处理。必要时在半精加工后再进行一次时效处理。6.2主轴、主轴套筒、丝杠副、凸轮和高速、重载齿轮等零、部件的易磨损部位,应采取与寿命相适应的耐磨措施。
6.3下列导轨副为重要导轨副,应采用与寿命相适应的耐磨措施。a)工作台与滑板导轨副:
b)滑板与床身导轨副;
c)立柱(或立柱滑板)与床身导轨副;d)滑枕与垂向滑板导轨副:
e)垂向滑板与立柱导轨副;
f)工作台与床身导轨副;
g)主轴箱与立柱导轨副;
h)回转导轨副;
i)其他重要导轨副。
6.4重要固定结合面应紧密贴合,紧固后用0.04mm塞尺检验时不应插人。下列结合面应按“重要固定结合面”的要求考核:a)滑动导轨压板的固定结合面;b)立柱与床身的固定结合面;
c)前后床身的固定结合面;
d)立柱与立柱滑板的固定结合面;e)主轴箱与主轴箱滑板的固定结合面;f)直线滚动导轨滑块与工作台、移动的立柱、滑板等零件的固定结合面;g)头架箱体与工作台、尾架箱体与滑板的固定结合面;h)箱体与床身的固定结合面。
6.5特别重要固定结合面应紧密贴合,除用涂色法检验外,紧固前、后用0.03mm塞尺检验均不应插人(与水平面垂直的特别重要固定结合面可在紧固后检验)。下列结合面应按“特别重要固定结合面”的要求考核:a)滚珠丝杠托架的结合面;
b)滚珠丝杠螺母座的固定结合面;c)端齿盘的固定结合面;
d)镶钢导轨的结合面;
e)直线滚动导轨的结合面。
6.6重要和特别重要固定结合面用塞尺检验时,允许局部(1处或2处)插人,插入深度小于结合面宽度的1/5,但不应超过5mm。插人部位的长度小于或等于结合面长度的1/5,但不大于100mm时则按一处计。
6.7下列导轨副应按“滑(滚)动导轨”的要求考核:a)工作台与滑板导轨副;
b)滑板与床身导轨副;
c)立柱(或立柱滑板)与床身导轨副;d)滑枕与垂向滑板导轨副;
e)垂向滑板与立柱导轨副:
f)工作台与床身导轨副;
g)主轴箱与立柱导轨副。
JB/T10792.2—2007
6.8滑动导轨表面应用涂色法检验接触情况,检验方法按JB/T9876的规定。除用涂色法检验外,还应用0.04mm塞尺检验,塞尺在导轨、镶条、压板端部的滑动面间插入深度不应大于表1的规定。表1
机床重量t
塞尺插入深度bzxz.net
6.9配合件的结合面均是刮研面,用配合件的结合面(研具)做涂色法检验时,刮研点应均匀。按规定的计算面积平均计算,在每25mm×25mm的面积内,接触点数不应少于表2的规定。表2
滑(滚)动导轨
每条导轨宽度
≤250
≤100
移置导轨
镶条、压板滑动面
接触点数
特别重要固定结合面
6.10配合件的结合面,一个是刮研面,另一个是机械加工面,用配合件的机械加工面检验刮研面的接触点时,不应少于表2中规定点数的75%。6.11配合件的结合面均是机械加工面,应用涂色法检验时,接触应均匀,接触指标不应低于表3的规定。
滑(滚)动导轨
全长上
全宽上
移置导轨
接触指标(%)
全长上
全宽上
特别重要固定结合面
全长上
全宽上
多段拼接镶钢导轨的接合处应留有0.02mm~0.04mm的缝隙。接合处导轨面的错位量应符合JB/T9874—1999的规定。
6.13镶钢导轨淬火后应进行无损检测,不应有裂纹,6.14贴塑和涂层导轨与基体应贴合紧密,粘接牢固可靠,不应有缝隙和气泡;与相配导轨的接触应均匀,并应符合有关规定。导轨边缘应倒角修圆。6.15滚动导轨安装的基面应符合设计文件的规定。组装后运动应轻便、灵活,无阻滞现象,6.16、各运动坐标轴安装的滚珠丝杠副、数控回转坐标轴,组装后应进行多次运转,其反向间隙应不大于表4的规定。
直线坐标反向间隙
回转坐标反向间隙
6.17焊接件和焊接部件的质量应符合JB/T9873一1999的规定。重要焊接构件应进行无损检测,不应有裂纹。
6.18拉刀机构及其他重要机构所用碟形弹簧,组装后进行工作压力试验,应符合图样和技术文件规定的要求。
6.19机床润滑系统、液压系统和气动系统应分别符合GB/T6576、JB/T10051.和GB/T7932的规定。3
JB/T10792.2—2007
6.20重要的压力油缸,组装后应按工作压力的150%进行不少于0.5h的保压试验,不应有渗漏现象。6.21主轴组件,应做动平衡,以达到与主轴转速相适应的技术要求。6.22机床采用电主轴、力矩电机或直线电机时,应配置恒温冷却装置,使用的介质和介质的压力、流量、温度应符合电主轴、力矩电机或直线电机规定的要求,不应有渗漏现象。6.23按JB/T9877规定检验机床总装后的清洁度。主轴箱、液压箱内部清洁度按重量法抽检,其单位体积中的脏物重量:主轴箱不应超过400mg/L,液压箱不应超过150mg/L。其他部件用目测、手感法进行检查,不应有明显脏物。
6.24机床电气应符合GB5226.1的规定。6.25机床数控操作指示形象化符号应符合GB/T3168的规定,面板上的数字刻字及表征功能的文字符号和标志,应清晰端正。
7空运转试验
7.1温升、主运动和进给运动试验7.1.1机床主运动机构应从最低转速起,依次运转,每级速度的运转时间不应少于2min。无级变速的机床,可做低、中、高速运转。在最高速度运转时,时间不应少于1h,使主轴轴承达到稳定温度,并在靠近主轴定心轴承处测量温度和温升,其温度不应超过60℃,温升不应超过30℃。在各级速度运转时运转应平稳,工作机构应正常、可靠。7.1.2.对直线坐标、回转坐标上的运动部件,分别用低、中、高进给速度和快速进行空运转试验,其运动应平稳、可靠,高速无振动,低速无明显爬行现象。7.1.3在空运转条件下,有级传动的各级主轴转速和进给量的实际偏差,不应超过标牌指示值-2%~十6%;无级变速传动的主轴转速和进给量的实际偏差,不应超过标牌指示值的土10%。7.1.4机床主传动系统的空运转功率(不包括主电动机空载功率)不应超过设计文件的规定。7.2功能试验
7.2.1手动功能试验,用手动或数控手动方式操作机床各部进行试验,具体试验应包含下列内容:a)对主轴连续进行不少于五次的锁刀、松刀和吹气的动作试验,动作应灵活、可靠、准确。b)用中速连续对主轴进行10次的正、反转的起动、停止(包括制动)和定向操作试验,动作应灵活、可靠。
c)无级变速的主轴至少应在低、中、高的转速范围内,有级变速的主轴应在各级转速进行变速操作试验,动作应灵活、可靠。
d)对各直线坐标、回转坐标上的运动部件,用中等进给速度连续进行各10次的正向、负向的起动、停止的操作试验,并选择适当的增量进给进行正向、负向的操作试验,动作应灵活、可靠、准确。
e)对进给系统在低、中、高进给速度和快速范围内,进行不少于10种的变速操作试验,动作应灵活、可靠。
f)对数控回转坐标轴连续进行10次的分度、定位试验,动作应灵活、可靠、准确。g)对刀库、机械手以任选方式进行换刀试验。刀库上刀具配置应包括设计规定的最大重量、最大重力矩、最大长度和最大直径的刀具;换刀动作应灵活、可靠、准确;机械手的承载重量和换刀时间应符合设计规定,并不应超过最大重力矩。h)对机床数控的各种指示灯、控制按钮、数据输出输入设备和风扇等进行空运转试验,动作应灵活、可靠。
i)对机床的安全、保险、防护装置进行必要的试验,功能应可靠,动作应灵活、准确。j)对机床的液压、润滑、冷却系统进行试验,应密封可靠,冷却充分,润滑良好,动作灵活、可靠;各系统不应渗漏。
k)对机床的各附属装置进行试验,工作应灵活、可靠。JB/T10792.2-2007
7.2.2自动功能试验,用数控程序操作机床各部件进行试验,具体试验应包含下列内容:a)用中速连续对主轴进行10次的正、反转起动、停止(包括制动)和定向的操作试验,动作应灵活、可靠。
b)无级变速的主轴至少在低、中、高转速范围内,有级变速的主轴在各级转速进行变速操作试验,动作应灵活、可靠。
c)对各直线坐标、回转坐标上的运动部件,用中等进给速度连续进行正、负向的起动、停止和增量进给方式的操作试验,动作应灵活、可靠、准确。d)对进给系统至少进行低、中、高进给速度和快速的变速操作试验,动作应灵活、可靠。e)数控回转工作台连续进行10次的分度、定位试验,动作应灵活,运转应平稳、可靠、准确。f)对刀库总容量中包括最大重量刀具在内的每把刀具,以任选方式进行不少于三次的自动换刀试验,动作应灵活、可靠。
g)对机床所具备的坐标联动、坐标选择、机械锁定、定位、直线及圆弧等各种插补,螺距、间隙、刀具等各种补偿,程序的暂停、急停等各种指令,有关部件、刀具的夹紧、松开以及液压、冷却、气动润滑系统的起动、停止等数控功能逐一进行试验,其功能应可靠,动作应灵活、准确7.3连续空运转试验
7.3.1连续空运转试验应在完成7.2.1和7.2.2试验之后,精度检验之前进行。7.3.2连续空运转试验应用包括机床各种主要功能在内的数控程序,操作机床各部件进行连续空运转。时间应不少于48h。
7.3.3连续空运转的整个过程中,机床运转应正常、平稳、可靠,不应发生故障,否则必须重新进行运转。
7.3.4连续空运转程序中应包括下列内容:a)主轴速度应包括低、中、高在内的五种以上正转、反转、停止和定位。其中高速运转时间一般不少于每个循环程序所用时间的10%。b)进给速度应把各坐标上的运动部件包括低、中、高速度和快速的正向、负向组合在一起,在接近全程范围内运行。并可选任意点进行定位。运行中不允许使用倍率开关,高速进给和快速运行时间不少于每个循环程序所用时间的10%。c)刀库中各刀位上的刀具不少于两次的自动交换。d)数控回转坐标轴的自动分度、定位不少于两个循环。e)各联动坐标的联动运行。
f)各循环程序间的暂停时间不应超过0.5min。8负荷试验(按设计编制的负荷试验规范进行)8.1·机床应做下列负荷试验
a)机床承载工件最大重量的运转试验(抽查);b)机床主传动系统最大扭矩的试验;c)机床最大切削抗力的试验(抽查)d)机床主传动系统达到最大功率的试验(抽查)。8.2机床承载工件最大重量的运转试验8.2.1用与设计规定的承载工作最大重量相当的重物作为工件置于工作台上,使其载荷均匀。8.2.2分别以最低、最高进给速度和快速运转。用最低进给速度运转时,般应在接近行程的两端和中间往复进行,每次移动距离应不少于20mm或15°;用最高进给速度和快速运转时,均应在接近全行程上进行,分别往复一次和五次。JB/T10792.2—2007
8.2.3试验时机床运转应平稳、可靠,无明显爬行现象。8.3机床主传动系统最大扭矩的试验8.3.1在机床主轴恒扭矩调速范围内,选择一适当的主轴转速,采用铣削方式进行试验。改变进给速度或切削深度,使机床主传动系统达到设计规定的最大扭矩。8.3.2切削试件材料:HT200或45钢;切削刀具:端铣刀或其他适用刀具。8.3.3试验时,机床传动系统各元、部件和变速机构工作应正常、可靠,运转应平稳、准确。8.4机床最大切削抗力的试验
8.4.1在机床主轴恒扭矩转速范围内选择一适当的主轴转速,采用铣削或适用方式进行试验。改变进给速度或切削深度,使机床达到设计规定的最大切削抗力。8.4.2切削试件材料:HT200;
切削刀具:端铣刀或其他适用刀具。8.4.3试验时机床工作应正常,各运动机构应灵活、可靠,过载保护装置应正常、可靠。8.5机床主传动系统达到最大功率的试验8.5.1在机床主轴恒功率调速范围内,选择一适当的主轴转速,采用铣削方式进行试验,改变进给速度或切削深度,使机床达到主电动机的额定功率或设计规定的最大功率。8.5.2切削试件材料:45钢;
切削刀具:端铣刀或其他适用刀具。8.5.3试验时,机床各部分工作应正常、可靠,无明显的颤振现象,并记录金属切除率,单位为cm2/min。9最小设定单位试验
9.1最小设定单位试验的分类及要求机床最小设定单位试验有直线坐标最小设定单位试验和回转坐标最小设定单位试验两种时,应分别进行试验。试验某一坐标最小设定单位时,其他运动部件,原则上置于行程的中间位置。试验时可在使用螺距补偿和间隙补偿条件下进行。9.2直线坐标最小设定单位试验
9.2.1试验方法
先以快速使直线坐标上的运动部件向正(或负)向移动一定距离,停止后,向同方向给出数个最小设定单位的指令,再停止,以此位置为基准位置,每次给出一个,共给出20个最小设定单位的指令,向同方向移动\,测量各个指令的停止位置。从上述的最终位置,继续向同方向给出数个最小设定单位指令,停止后,向负(或正)向给出数个最小设定单位的指令,约返回到上述最终的测量位置,这些正向和负向的数个最小设定单位指令的停止位置均不作测量。然后从上述的最终位置开始,每次给出一个,共给出20个最小设定单位的指令,继续向负(或正)向移动,测量各指令的停止位置,见图1。至少在行程的中间及靠近两端的三个位置上分别进行试验。各直线坐标均应进行试验。9.2.2误差计算
误差分为最小设定单位误差和最小设定单位相对误差。分别按式(1)和式(2)进行计算,以三个位置上最大误差值作为该项的误差。9.2.2.1最小设定单位误差
Sa=L,-ml
1)要注意实际移动的方向。
式中:
Sa最小设定单位误差,单位为mm;L2
个最小设定单位指令的实际位移,单位为mm;m
个最小设定单位指令的理论位移,单位为mm。数个最小设定
单位指令的停止
位置不作测量
测量范围
9.2.2.2最小设定单位相对误差
式中:
最小设定单位相对误差:
实际移动距离
直线坐标最小设定单位试验方法20m
20个最小设定单位指令的实际位移的总和,单位为mm。9.2.3允差
Sa:根据机床的具体情况由制造厂规定。Sb:不应大于25%。
9.2.4检验工具
激光干涉仪或读数显微镜和金属线纹尺。9.3回转坐标最小设定单位试验
9.3.1试验方法
JB/T10792.2--2007
最小设定单位
先以快速使回转坐标上的运动部件向正(或负)向转动一定角度,停止后,向同方向给出数个最小设定单位的指令,再停止,以此位置作为基准位置,每次给出一个,共给出20个最小设定单位的指令,向同一方向转动3,测量各个指令的停止位置。从上述的最终位置,继续向同方向给出数个最小设定单2)实际位移的方向如与给出的方向相反,其位移应为负值。3)要注意实际转动的方向。
JB/T10792.2—2007
位指令,停止后,向负(或正)向给出数个最小设定单位的指令,约返回到上述的最终测量位置,这些正向和负向的数个最小设定单位指令停止的位置不作测量。然后从上述的最终位置开始,每次给出一个,共给出20个最小设定单位的指令,继续向负(或正)向转动,测量各指令的停止位置,见图2。至少应在回转范围内的任意三个位置上进行试验。各回转坐标均进行试验。数个最小设定
单位指令的停止
位置不作测量
测量范围
事实际转动角度
最小设定单位
图2回转坐标最小设定单位试验方法9.3.2误差计算
误差分为最小设定单位角位移误差和最小设定单位角位移相对误差,分别按式(3)和式(4)进行计算,误差以三个位置上最大误差值作为该项的误差。9.3.2.1最小设定单位角位移误差aa0; -mol
式中:
最小设定单位角位移误差,单位为(”);个最小设定单位指令的实际角位移,单位为(”):个最小设定单位指令的理论角位移,单位为(”)。9.3.2.2最小设定单位角位移相对误差20
Ze;-20mo
式中:
最小设定单位角位移相对误差:20mo
20个最小设定单位指令的实际角位移总和,单位为(”)。4)实际角位移的方向如与给出的方向相反,其角位移应为负值。8
小提示:此标准内容仅展示完整标准里的部分截取内容,若需要完整标准请到上方自行免费下载完整标准文档。
备案号:21865—2007
中华人民共和国机械行业标准 JB/T 10792.2—2007
五轴联动立式加工中心
第2部分:技术条件
The 5-axes simultaneous vertical machining centersPart2:Specifications
2007-10-08发布
2008-03-01实施
中华人民共和国国家发展和改革委员会发布前言:
1范围
2规范性引用文件,
3一般要求
4附件和工具.
安全卫生,
加工和装配质量,
空运转试验
7.1温升、主运动和进给运动试验,功能试验.
连续空运转试验。
8负荷试验(按设计编制的负荷试验规范进行)8.1机床应做下列负荷试验
机床承载工件最大重量的运转试验8.2
机床主传动系统最大扭矩的试验机床最大切削抗力的试验
8.5机床主传动系统达到最大功率的试验9最小设定单位试验..
最小设定单位试验的分类及要求直线坐标最小设定单位试验
回转坐标最小设定单位试验.
原点返回试验,
原点返回试验的分类及要求
直线坐标原点返回试验..
回转坐标原点返回试验
11精度检验。
12随行技术文件..
参考文献
图1直线坐标最小设定单位试验方法,A
图2回转坐标最小设定单位试验方法图3直线坐标原点返回试验方法
图4回转坐标原点返回试验方法
JB/T10792.2—2007
前·言
JB/T10792《五轴联动立式加工中心》分为以下两部分:第1部分:精度检验;
一第2部分:技术要求。
本部分为JB/T·10792的第2部分。JB/T10792.2-—2007
请注意本部分的某些内容有可能涉及专利。本部分的发布机构不应承担识别这些专利的责任本部分由中国机械工业联合会提出。本部分由全国金属切削机床标准化技术委员会(SAC/TC22)归口。本部分起草单位:北京机电院高技术股份有限公司。本部分主要起草人:高琦、李锦武、芦金旗、刘景祎、郭庆兴、肖业喜。本部分为首次发布。
1范围
JB/T10792.2—2007
五轴联动立式加工中心第2部分:技术条件JBT10792的本部分规定了五轴联动立式加工中心设计、制造和验收的基本要求。本部分适用于线性轴线行程至2000mm,加工叶片、叶轮等用途的普通精度五轴联动立式加工中心。2规范性引用文件
下列文件中的条款通过JB/T10792的本部分的引用而成为本部分的条款。凡是注日期的引用文件,其随后所有的修改单(不包括勘误的内容)或修订版均不适用于本部分,然而,鼓励根据本部分达成协议的各方研究是否可使用这些文件的最新版本。凡是不注日期的引用文件,其最新版本适用于本部分。GB/T3168一1993数字控制机床操作指示形象化符号(neqISO2972:1979)GB5226.1一2002机械安全机械电气设备第1部分:通用技术条件(IEC60204-1:2000,IDT)GB/T6576—2002机床润滑系统(ISO5170:1997,MOD)气动系统通用技术条件(ISO4414:1998,IDT)GB/T7932—2003
GB/T9061-2006金属切削机床通用技术条件GB/T16769—1997金属切削机床噪声声压级测量方法(neqISO/DIS230:5.2:1996)GB/T17421.2一2000机床检验通则第2部分:数控轴线的定位精度和重复定位精度的确定(eqvISO 230-2:1997)
GB18568-2001
JB/T9872—1999
JB/T9873—1999
加工中心安全防护技术条件
金属切削机床机械加工件通用技术条件金属切削机床焊接件通用技术条件JB/T9874—-1999
金属切削机床装配通用技术条件金属切削机床结合面涂色法检验及评定JB/T9876—1999
JB/T9877—1999
金属切削机床清洁度的测定
金属切削机床液压系统通用技术条件JB/T10051—1999
JB/T10792.1--2007五轴联动立式加工中心第1部分:精度检验3般要求
本部分是对GB/T9061、JB/T9872、JB/T9874的补充和具体化。按本部分验收机床时,应同时对上述标准中未经本部分具体化的有关的验收项目进行检验。4附件和工具
4.1应随行供应下列附件和工具
a)垫铁及地脚螺栓:1套;
b)专用调整工具:1套。
4.2可按协议供应扩大机床使用功能的特殊附件。5安全卫生
5.1机床的安全防护应符合GB18568和GB5226.1的有关规定。5.2按GB/T16769的规定检测机床的空运转噪声。机床运转时,不应有不正常的尖叫声和冲击声。JB/T10792.2--2007
机床在空运转条件下,整机噪声声压级不应超过83dB(A)。6加工和装配质量
6.1床身、工作台、立柱、主轴箱、蜗轮箱、头架箱体、尾架箱体、滑板、滑枕等为重要铸件(焊接件),应在粗加工后进行时效处理。必要时在半精加工后再进行一次时效处理。6.2主轴、主轴套筒、丝杠副、凸轮和高速、重载齿轮等零、部件的易磨损部位,应采取与寿命相适应的耐磨措施。
6.3下列导轨副为重要导轨副,应采用与寿命相适应的耐磨措施。a)工作台与滑板导轨副:
b)滑板与床身导轨副;
c)立柱(或立柱滑板)与床身导轨副;d)滑枕与垂向滑板导轨副:
e)垂向滑板与立柱导轨副;
f)工作台与床身导轨副;
g)主轴箱与立柱导轨副;
h)回转导轨副;
i)其他重要导轨副。
6.4重要固定结合面应紧密贴合,紧固后用0.04mm塞尺检验时不应插人。下列结合面应按“重要固定结合面”的要求考核:a)滑动导轨压板的固定结合面;b)立柱与床身的固定结合面;
c)前后床身的固定结合面;
d)立柱与立柱滑板的固定结合面;e)主轴箱与主轴箱滑板的固定结合面;f)直线滚动导轨滑块与工作台、移动的立柱、滑板等零件的固定结合面;g)头架箱体与工作台、尾架箱体与滑板的固定结合面;h)箱体与床身的固定结合面。
6.5特别重要固定结合面应紧密贴合,除用涂色法检验外,紧固前、后用0.03mm塞尺检验均不应插人(与水平面垂直的特别重要固定结合面可在紧固后检验)。下列结合面应按“特别重要固定结合面”的要求考核:a)滚珠丝杠托架的结合面;
b)滚珠丝杠螺母座的固定结合面;c)端齿盘的固定结合面;
d)镶钢导轨的结合面;
e)直线滚动导轨的结合面。
6.6重要和特别重要固定结合面用塞尺检验时,允许局部(1处或2处)插人,插入深度小于结合面宽度的1/5,但不应超过5mm。插人部位的长度小于或等于结合面长度的1/5,但不大于100mm时则按一处计。
6.7下列导轨副应按“滑(滚)动导轨”的要求考核:a)工作台与滑板导轨副;
b)滑板与床身导轨副;
c)立柱(或立柱滑板)与床身导轨副;d)滑枕与垂向滑板导轨副;
e)垂向滑板与立柱导轨副:
f)工作台与床身导轨副;
g)主轴箱与立柱导轨副。
JB/T10792.2—2007
6.8滑动导轨表面应用涂色法检验接触情况,检验方法按JB/T9876的规定。除用涂色法检验外,还应用0.04mm塞尺检验,塞尺在导轨、镶条、压板端部的滑动面间插入深度不应大于表1的规定。表1
机床重量t
塞尺插入深度bzxz.net
6.9配合件的结合面均是刮研面,用配合件的结合面(研具)做涂色法检验时,刮研点应均匀。按规定的计算面积平均计算,在每25mm×25mm的面积内,接触点数不应少于表2的规定。表2
滑(滚)动导轨
每条导轨宽度
≤250
≤100
移置导轨
镶条、压板滑动面
接触点数
特别重要固定结合面
6.10配合件的结合面,一个是刮研面,另一个是机械加工面,用配合件的机械加工面检验刮研面的接触点时,不应少于表2中规定点数的75%。6.11配合件的结合面均是机械加工面,应用涂色法检验时,接触应均匀,接触指标不应低于表3的规定。
滑(滚)动导轨
全长上
全宽上
移置导轨
接触指标(%)
全长上
全宽上
特别重要固定结合面
全长上
全宽上
多段拼接镶钢导轨的接合处应留有0.02mm~0.04mm的缝隙。接合处导轨面的错位量应符合JB/T9874—1999的规定。
6.13镶钢导轨淬火后应进行无损检测,不应有裂纹,6.14贴塑和涂层导轨与基体应贴合紧密,粘接牢固可靠,不应有缝隙和气泡;与相配导轨的接触应均匀,并应符合有关规定。导轨边缘应倒角修圆。6.15滚动导轨安装的基面应符合设计文件的规定。组装后运动应轻便、灵活,无阻滞现象,6.16、各运动坐标轴安装的滚珠丝杠副、数控回转坐标轴,组装后应进行多次运转,其反向间隙应不大于表4的规定。
直线坐标反向间隙
回转坐标反向间隙
6.17焊接件和焊接部件的质量应符合JB/T9873一1999的规定。重要焊接构件应进行无损检测,不应有裂纹。
6.18拉刀机构及其他重要机构所用碟形弹簧,组装后进行工作压力试验,应符合图样和技术文件规定的要求。
6.19机床润滑系统、液压系统和气动系统应分别符合GB/T6576、JB/T10051.和GB/T7932的规定。3
JB/T10792.2—2007
6.20重要的压力油缸,组装后应按工作压力的150%进行不少于0.5h的保压试验,不应有渗漏现象。6.21主轴组件,应做动平衡,以达到与主轴转速相适应的技术要求。6.22机床采用电主轴、力矩电机或直线电机时,应配置恒温冷却装置,使用的介质和介质的压力、流量、温度应符合电主轴、力矩电机或直线电机规定的要求,不应有渗漏现象。6.23按JB/T9877规定检验机床总装后的清洁度。主轴箱、液压箱内部清洁度按重量法抽检,其单位体积中的脏物重量:主轴箱不应超过400mg/L,液压箱不应超过150mg/L。其他部件用目测、手感法进行检查,不应有明显脏物。
6.24机床电气应符合GB5226.1的规定。6.25机床数控操作指示形象化符号应符合GB/T3168的规定,面板上的数字刻字及表征功能的文字符号和标志,应清晰端正。
7空运转试验
7.1温升、主运动和进给运动试验7.1.1机床主运动机构应从最低转速起,依次运转,每级速度的运转时间不应少于2min。无级变速的机床,可做低、中、高速运转。在最高速度运转时,时间不应少于1h,使主轴轴承达到稳定温度,并在靠近主轴定心轴承处测量温度和温升,其温度不应超过60℃,温升不应超过30℃。在各级速度运转时运转应平稳,工作机构应正常、可靠。7.1.2.对直线坐标、回转坐标上的运动部件,分别用低、中、高进给速度和快速进行空运转试验,其运动应平稳、可靠,高速无振动,低速无明显爬行现象。7.1.3在空运转条件下,有级传动的各级主轴转速和进给量的实际偏差,不应超过标牌指示值-2%~十6%;无级变速传动的主轴转速和进给量的实际偏差,不应超过标牌指示值的土10%。7.1.4机床主传动系统的空运转功率(不包括主电动机空载功率)不应超过设计文件的规定。7.2功能试验
7.2.1手动功能试验,用手动或数控手动方式操作机床各部进行试验,具体试验应包含下列内容:a)对主轴连续进行不少于五次的锁刀、松刀和吹气的动作试验,动作应灵活、可靠、准确。b)用中速连续对主轴进行10次的正、反转的起动、停止(包括制动)和定向操作试验,动作应灵活、可靠。
c)无级变速的主轴至少应在低、中、高的转速范围内,有级变速的主轴应在各级转速进行变速操作试验,动作应灵活、可靠。
d)对各直线坐标、回转坐标上的运动部件,用中等进给速度连续进行各10次的正向、负向的起动、停止的操作试验,并选择适当的增量进给进行正向、负向的操作试验,动作应灵活、可靠、准确。
e)对进给系统在低、中、高进给速度和快速范围内,进行不少于10种的变速操作试验,动作应灵活、可靠。
f)对数控回转坐标轴连续进行10次的分度、定位试验,动作应灵活、可靠、准确。g)对刀库、机械手以任选方式进行换刀试验。刀库上刀具配置应包括设计规定的最大重量、最大重力矩、最大长度和最大直径的刀具;换刀动作应灵活、可靠、准确;机械手的承载重量和换刀时间应符合设计规定,并不应超过最大重力矩。h)对机床数控的各种指示灯、控制按钮、数据输出输入设备和风扇等进行空运转试验,动作应灵活、可靠。
i)对机床的安全、保险、防护装置进行必要的试验,功能应可靠,动作应灵活、准确。j)对机床的液压、润滑、冷却系统进行试验,应密封可靠,冷却充分,润滑良好,动作灵活、可靠;各系统不应渗漏。
k)对机床的各附属装置进行试验,工作应灵活、可靠。JB/T10792.2-2007
7.2.2自动功能试验,用数控程序操作机床各部件进行试验,具体试验应包含下列内容:a)用中速连续对主轴进行10次的正、反转起动、停止(包括制动)和定向的操作试验,动作应灵活、可靠。
b)无级变速的主轴至少在低、中、高转速范围内,有级变速的主轴在各级转速进行变速操作试验,动作应灵活、可靠。
c)对各直线坐标、回转坐标上的运动部件,用中等进给速度连续进行正、负向的起动、停止和增量进给方式的操作试验,动作应灵活、可靠、准确。d)对进给系统至少进行低、中、高进给速度和快速的变速操作试验,动作应灵活、可靠。e)数控回转工作台连续进行10次的分度、定位试验,动作应灵活,运转应平稳、可靠、准确。f)对刀库总容量中包括最大重量刀具在内的每把刀具,以任选方式进行不少于三次的自动换刀试验,动作应灵活、可靠。
g)对机床所具备的坐标联动、坐标选择、机械锁定、定位、直线及圆弧等各种插补,螺距、间隙、刀具等各种补偿,程序的暂停、急停等各种指令,有关部件、刀具的夹紧、松开以及液压、冷却、气动润滑系统的起动、停止等数控功能逐一进行试验,其功能应可靠,动作应灵活、准确7.3连续空运转试验
7.3.1连续空运转试验应在完成7.2.1和7.2.2试验之后,精度检验之前进行。7.3.2连续空运转试验应用包括机床各种主要功能在内的数控程序,操作机床各部件进行连续空运转。时间应不少于48h。
7.3.3连续空运转的整个过程中,机床运转应正常、平稳、可靠,不应发生故障,否则必须重新进行运转。
7.3.4连续空运转程序中应包括下列内容:a)主轴速度应包括低、中、高在内的五种以上正转、反转、停止和定位。其中高速运转时间一般不少于每个循环程序所用时间的10%。b)进给速度应把各坐标上的运动部件包括低、中、高速度和快速的正向、负向组合在一起,在接近全程范围内运行。并可选任意点进行定位。运行中不允许使用倍率开关,高速进给和快速运行时间不少于每个循环程序所用时间的10%。c)刀库中各刀位上的刀具不少于两次的自动交换。d)数控回转坐标轴的自动分度、定位不少于两个循环。e)各联动坐标的联动运行。
f)各循环程序间的暂停时间不应超过0.5min。8负荷试验(按设计编制的负荷试验规范进行)8.1·机床应做下列负荷试验
a)机床承载工件最大重量的运转试验(抽查);b)机床主传动系统最大扭矩的试验;c)机床最大切削抗力的试验(抽查)d)机床主传动系统达到最大功率的试验(抽查)。8.2机床承载工件最大重量的运转试验8.2.1用与设计规定的承载工作最大重量相当的重物作为工件置于工作台上,使其载荷均匀。8.2.2分别以最低、最高进给速度和快速运转。用最低进给速度运转时,般应在接近行程的两端和中间往复进行,每次移动距离应不少于20mm或15°;用最高进给速度和快速运转时,均应在接近全行程上进行,分别往复一次和五次。JB/T10792.2—2007
8.2.3试验时机床运转应平稳、可靠,无明显爬行现象。8.3机床主传动系统最大扭矩的试验8.3.1在机床主轴恒扭矩调速范围内,选择一适当的主轴转速,采用铣削方式进行试验。改变进给速度或切削深度,使机床主传动系统达到设计规定的最大扭矩。8.3.2切削试件材料:HT200或45钢;切削刀具:端铣刀或其他适用刀具。8.3.3试验时,机床传动系统各元、部件和变速机构工作应正常、可靠,运转应平稳、准确。8.4机床最大切削抗力的试验
8.4.1在机床主轴恒扭矩转速范围内选择一适当的主轴转速,采用铣削或适用方式进行试验。改变进给速度或切削深度,使机床达到设计规定的最大切削抗力。8.4.2切削试件材料:HT200;
切削刀具:端铣刀或其他适用刀具。8.4.3试验时机床工作应正常,各运动机构应灵活、可靠,过载保护装置应正常、可靠。8.5机床主传动系统达到最大功率的试验8.5.1在机床主轴恒功率调速范围内,选择一适当的主轴转速,采用铣削方式进行试验,改变进给速度或切削深度,使机床达到主电动机的额定功率或设计规定的最大功率。8.5.2切削试件材料:45钢;
切削刀具:端铣刀或其他适用刀具。8.5.3试验时,机床各部分工作应正常、可靠,无明显的颤振现象,并记录金属切除率,单位为cm2/min。9最小设定单位试验
9.1最小设定单位试验的分类及要求机床最小设定单位试验有直线坐标最小设定单位试验和回转坐标最小设定单位试验两种时,应分别进行试验。试验某一坐标最小设定单位时,其他运动部件,原则上置于行程的中间位置。试验时可在使用螺距补偿和间隙补偿条件下进行。9.2直线坐标最小设定单位试验
9.2.1试验方法
先以快速使直线坐标上的运动部件向正(或负)向移动一定距离,停止后,向同方向给出数个最小设定单位的指令,再停止,以此位置为基准位置,每次给出一个,共给出20个最小设定单位的指令,向同方向移动\,测量各个指令的停止位置。从上述的最终位置,继续向同方向给出数个最小设定单位指令,停止后,向负(或正)向给出数个最小设定单位的指令,约返回到上述最终的测量位置,这些正向和负向的数个最小设定单位指令的停止位置均不作测量。然后从上述的最终位置开始,每次给出一个,共给出20个最小设定单位的指令,继续向负(或正)向移动,测量各指令的停止位置,见图1。至少在行程的中间及靠近两端的三个位置上分别进行试验。各直线坐标均应进行试验。9.2.2误差计算
误差分为最小设定单位误差和最小设定单位相对误差。分别按式(1)和式(2)进行计算,以三个位置上最大误差值作为该项的误差。9.2.2.1最小设定单位误差
Sa=L,-ml
1)要注意实际移动的方向。
式中:
Sa最小设定单位误差,单位为mm;L2
个最小设定单位指令的实际位移,单位为mm;m
个最小设定单位指令的理论位移,单位为mm。数个最小设定
单位指令的停止
位置不作测量
测量范围
9.2.2.2最小设定单位相对误差
式中:
最小设定单位相对误差:
实际移动距离
直线坐标最小设定单位试验方法20m
20个最小设定单位指令的实际位移的总和,单位为mm。9.2.3允差
Sa:根据机床的具体情况由制造厂规定。Sb:不应大于25%。
9.2.4检验工具
激光干涉仪或读数显微镜和金属线纹尺。9.3回转坐标最小设定单位试验
9.3.1试验方法
JB/T10792.2--2007
最小设定单位
先以快速使回转坐标上的运动部件向正(或负)向转动一定角度,停止后,向同方向给出数个最小设定单位的指令,再停止,以此位置作为基准位置,每次给出一个,共给出20个最小设定单位的指令,向同一方向转动3,测量各个指令的停止位置。从上述的最终位置,继续向同方向给出数个最小设定单2)实际位移的方向如与给出的方向相反,其位移应为负值。3)要注意实际转动的方向。
JB/T10792.2—2007
位指令,停止后,向负(或正)向给出数个最小设定单位的指令,约返回到上述的最终测量位置,这些正向和负向的数个最小设定单位指令停止的位置不作测量。然后从上述的最终位置开始,每次给出一个,共给出20个最小设定单位的指令,继续向负(或正)向转动,测量各指令的停止位置,见图2。至少应在回转范围内的任意三个位置上进行试验。各回转坐标均进行试验。数个最小设定
单位指令的停止
位置不作测量
测量范围
事实际转动角度
最小设定单位
图2回转坐标最小设定单位试验方法9.3.2误差计算
误差分为最小设定单位角位移误差和最小设定单位角位移相对误差,分别按式(3)和式(4)进行计算,误差以三个位置上最大误差值作为该项的误差。9.3.2.1最小设定单位角位移误差aa0; -mol
式中:
最小设定单位角位移误差,单位为(”);个最小设定单位指令的实际角位移,单位为(”):个最小设定单位指令的理论角位移,单位为(”)。9.3.2.2最小设定单位角位移相对误差20
Ze;-20mo
式中:
最小设定单位角位移相对误差:20mo
20个最小设定单位指令的实际角位移总和,单位为(”)。4)实际角位移的方向如与给出的方向相反,其角位移应为负值。8
小提示:此标准内容仅展示完整标准里的部分截取内容,若需要完整标准请到上方自行免费下载完整标准文档。

标准图片预览:
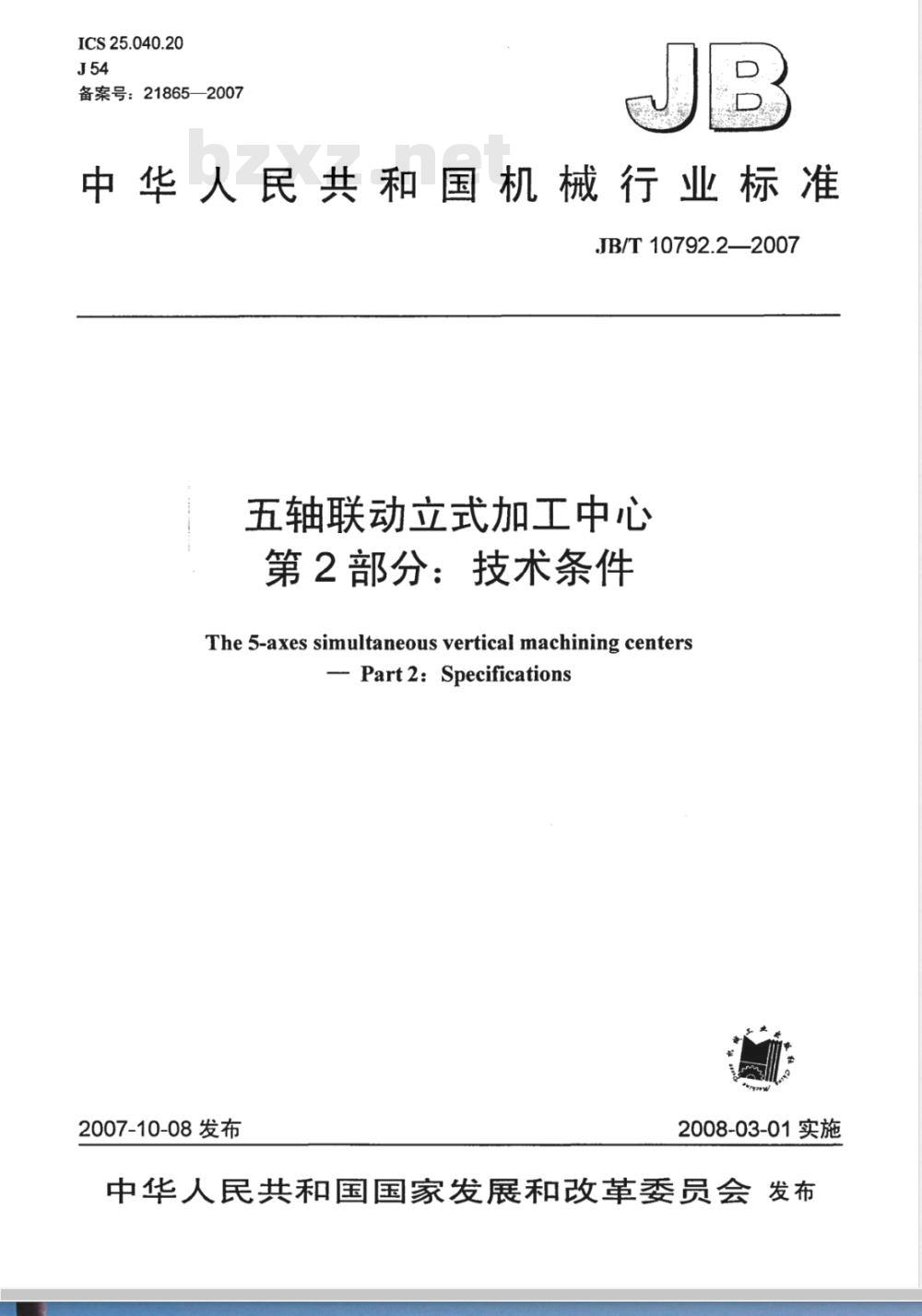
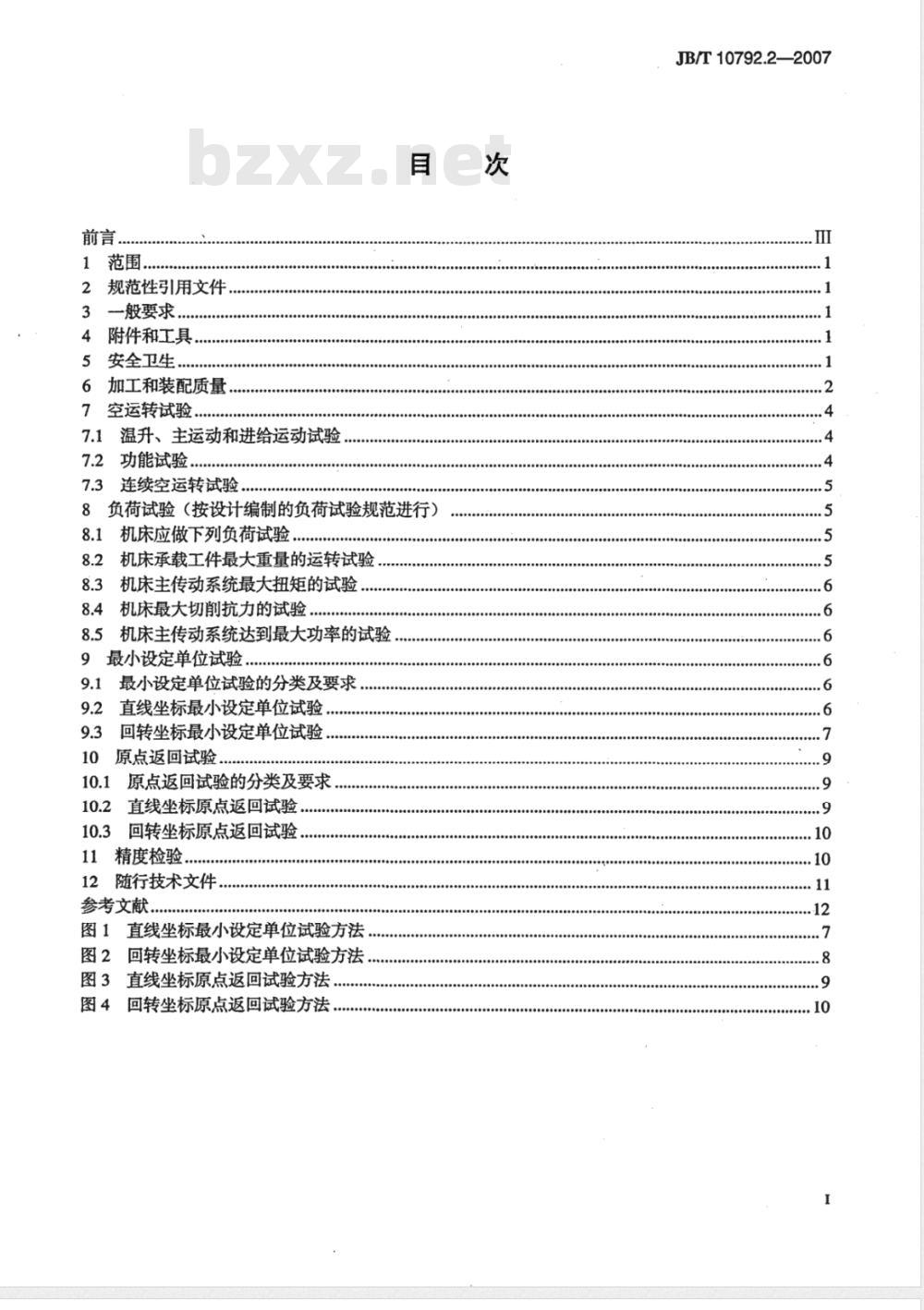
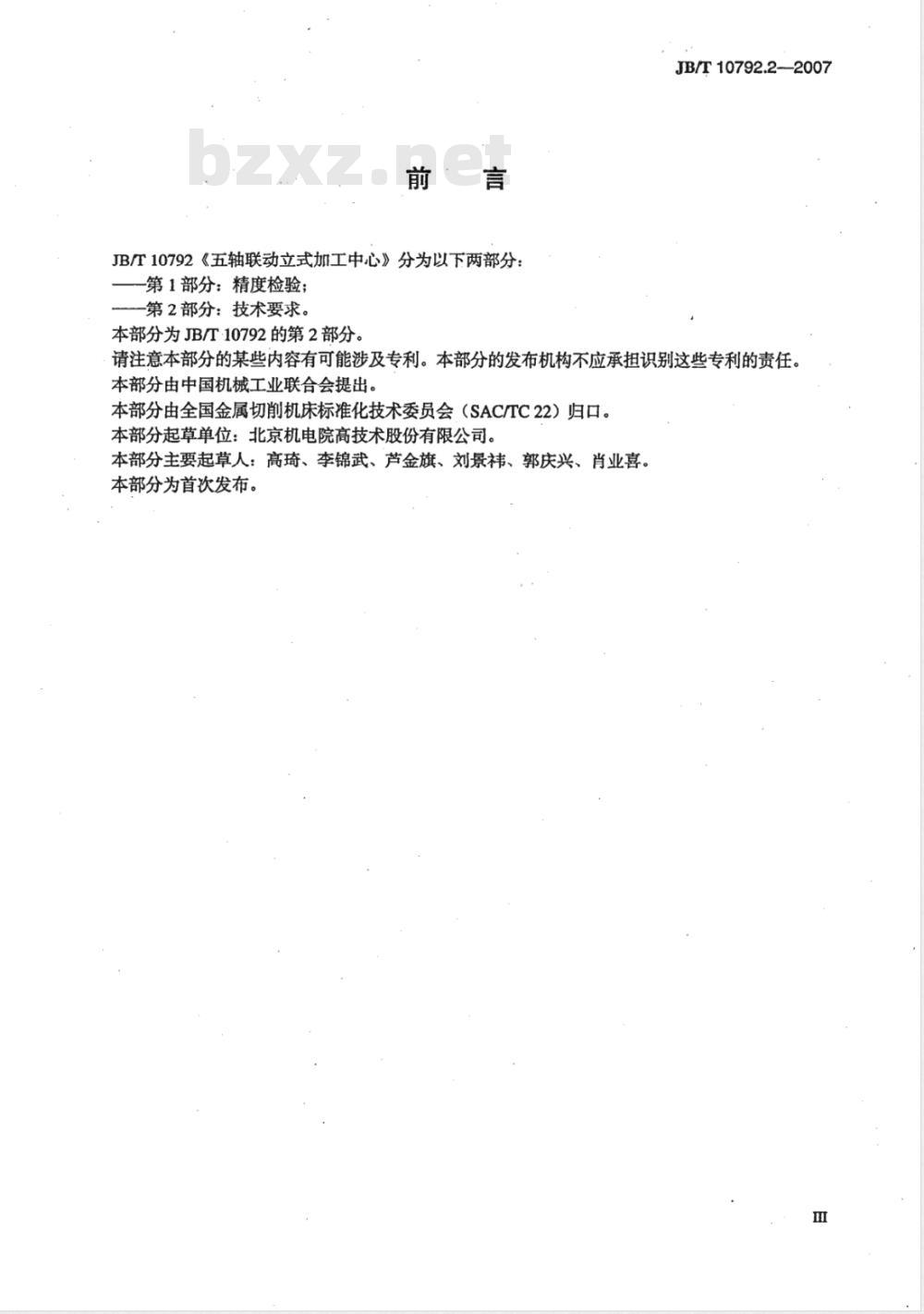
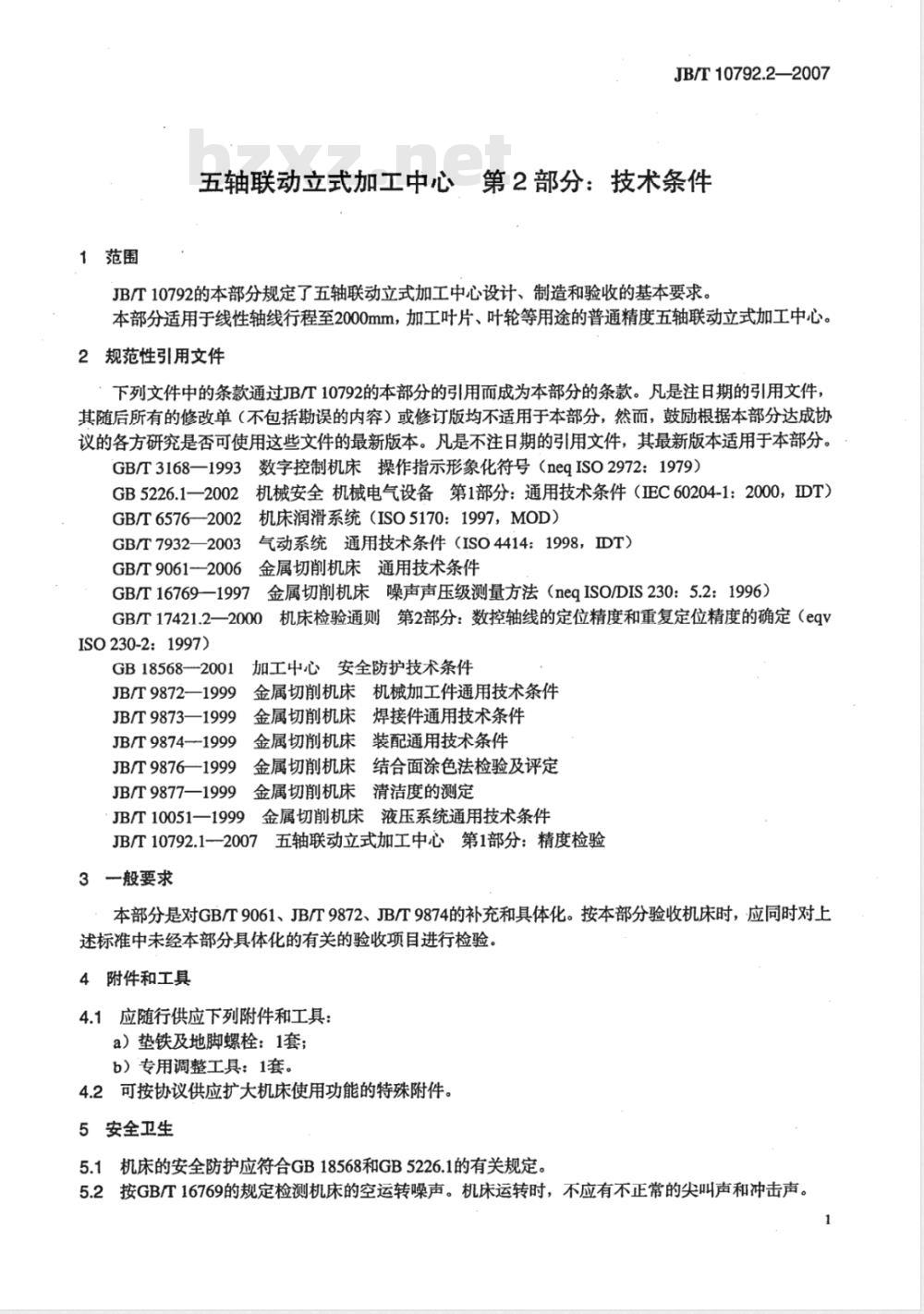
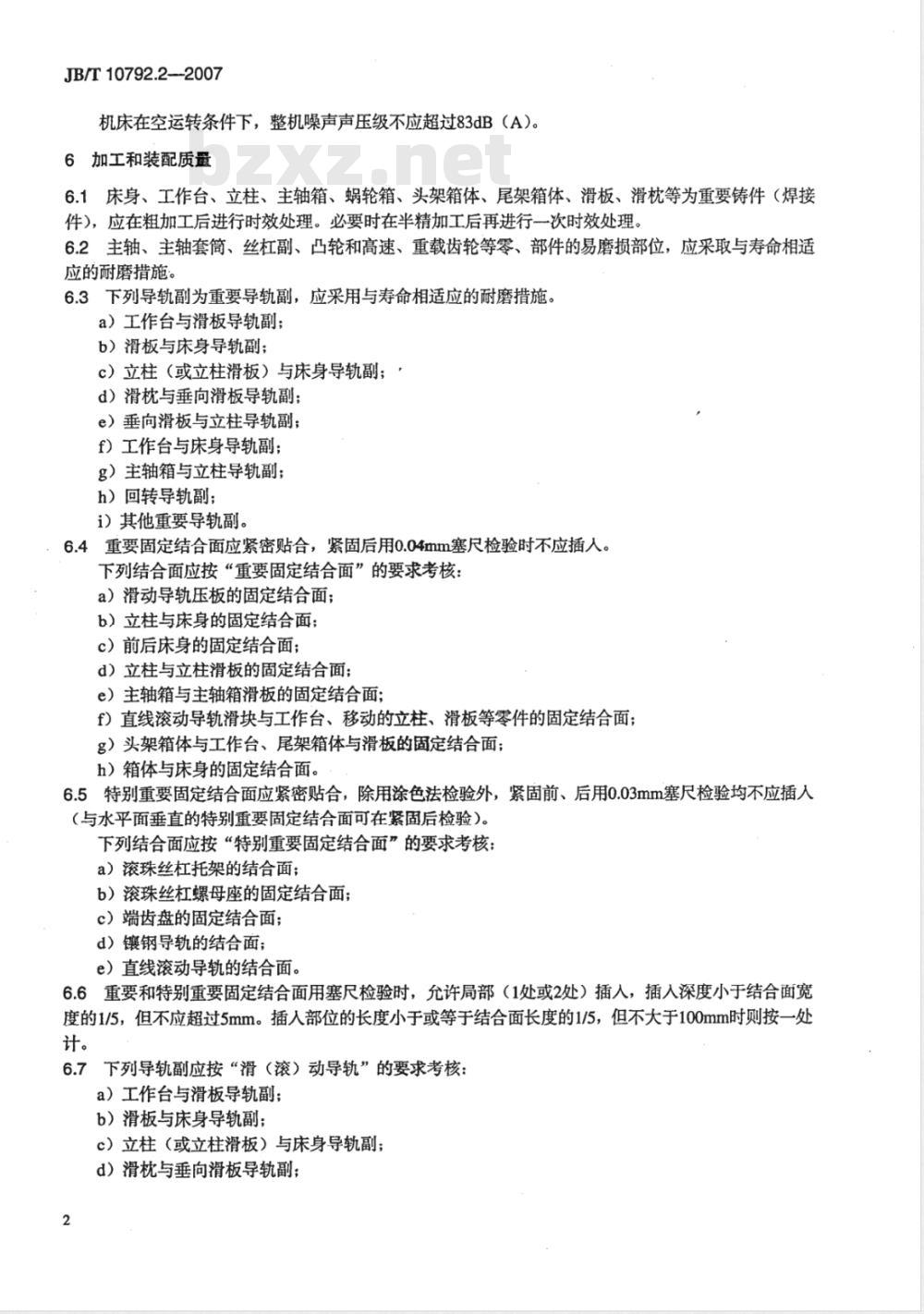
- 热门标准
- 机械行业标准(JB)
- JB/T10725-2007 天然金刚石车刀
- JB/T10723-2007 焊接聚晶金刚石或立方氮化硼镗刀
- JB/T10565-2006 工业过程测量和控制系统用动圈式指示仪性能评定方法
- JB/T10767-2007 装载机铜基湿式粉末冶金摩擦片 技术条件
- JB/T10216-2013 电控配电用电缆桥架
- JB8589-1997 DZ 20系列塑料外壳式断路器
- JB/T8521.1-2007 编织吊索 安全性 第1部分:一般用途合成纤维扁平吊装带
- JB/T8770.2-1998 板料边缘刨床 技术条件
- JB/T11225-2011 烘烤机械 层式电烤炉
- JB3228-1983 闭式机械压力机 紧固模具用槽打(顶)杆孔的分布形式与尺寸
- JB/DQ1545.8-1989 英制紧固件 半圆头螺栓
- JB/GQOE14-1988 熔模铸钢ZG310-570正大组织金相检验
- JB/T6237.8-2008 电触头材料用银粉化学分析方法 第8部分:银粉水溶液pH值测定
- JB/T8704-2012 蜂窝式电除焦油器
- JB/T9220.3-1999 铸造化铁炉酸性炉渣化学分析方法 重铬酸钾容量法测定氧化亚铁量
- 行业新闻
请牢记:“bzxz.net”即是“标准下载”四个汉字汉语拼音首字母与国际顶级域名“.net”的组合。 ©2009 标准下载网 www.bzxz.net 本站邮件:bzxznet@163.com
网站备案号:湘ICP备2023016450号-1
网站备案号:湘ICP备2023016450号-1