- 您的位置:
- 标准下载网 >>
- 标准分类 >>
- 国家标准(GB) >>
- GB/T 9438-1999 铝合金铸件
标准号:
GB/T 9438-1999
标准名称:
铝合金铸件
标准类别:
国家标准(GB)
标准状态:
现行-
发布日期:
1999-09-03 -
实施日期:
2000-03-01 出版语种:
简体中文下载格式:
.rar.pdf下载大小:
356.56 KB
替代情况:
GB/T 9438-1988采标情况:
≈ASTM B26/B26M-1992a ≈ASTM B108-1992a ≈ASTM E155-1985 ≈OCT1 90021-1992

点击下载
标准简介:
标准下载解压密码:www.bzxz.net
本标准规定了铝合金铸件的分类和铸件的外观质量、内在质量以及铸件修补等内容的技术要求与检验规则等。本标准适用于采用砂型铸造和特种铸造(不含压力铸造)生产的铝合金铸件。 GB/T 9438-1999 铝合金铸件 GB/T9438-1999

部分标准内容:
GB/T9438--1999
本标准是对GB/T94381988的修订。吸收10年来我国铸造铝合金方面的科研成果和生产实践经验,参照美国 ASTM B26/B26M一92a《Standard Specification for Aluminium-Alloy Sand Castings》ASTM Bl08-92a《Standard Specification for Aluminium-Alloy Permanent Mold Castings 》,ASTME155-85《Standard Radiographs for Inspection of Aluminium and Magnesium Castings 》, 罗斯 OCT190021-92《OT.JIHBK DACOHHbIE M3 AJIOMIHHEBBIX CIIJIABOB TEXHIIHECKHE TPELOBAHH》等国外先进标准及国内航空系统的相关标准,并考虑到与GB/T1173--1995《铸造铝合金》的配套性,本标准与被修订的标准在以下重要技术内容上有所改变:一第4.3.2.1条,从铸件上切取试样检验力学性能,三根试样的抗拉强度的平均值由不低于规定值的80%改为75%。ASTMB26/B26M-92a、ASTMB108-92a及俄罗斯OCT190021-92标准的规定均为75%。
第4.6.6条,取消了铸件表面质量的分级规定。因为实际上铸件是按类别验收的,表面质量按级验收生产中较少使用。在表面孔洞限量的表1中,对1类铸件的要求略有提高,Ⅱ类铸件不变,亚类铸件略有放松
第4.7.1条,当用X射线照相方法检验内部针孔时,局部允许的针孔级别由3级改为4级。第4.7.2条,对铸件内部的其他缺陷作出明确而严格的规定。为顾及各个层面的使用者,本条明确规定允许用户和制造厂家按HB6578--1992规定的部分内容进行验收。本标准自实施之日起,同时代替GB/T9438--1988《铝合金铸件技术条件》。本标准与GB/T1173-1995《铸造铝合金》配套使用。本标准由国家机械工业局提出。本标准由全国铸造标准化技术委员会归口。本标准起草单位:沈阳铸造研究所、北京航空材料研究院、洛阳七二五研究所、阿城市有色金属铸造本标准主要起草人:李德成、李玉胜、余应梅、金长庚、孙建科、熊文定、刘志启、张斌。292
中华人民共和国国家标准
铝合金铸件
Aluminium alloy castings
GB/T9438--1999
代替GB/T94381988
本标准规定了铝合金铸件的分类和铸件的外观质量、内在质量以及铸件修补等内容的技术要求与检验规则等,
本标准适用于采用砂型铸造和特种铸造(不含压力铸造)生产的铝合金铸件。2引用标准
下列标准所包含的条文,通过在本标准中引用而构成本标准的条文。本标准出版时,所示版本均为有效。所有标准都会被修订,使用本标准的各方应探讨使用下列标准最新版本的可能性。GB/T228—1987金属拉伸试验方法GB/T1173--1995铸造铝合金
GB/T6060.1-1997表面粗糙度比较样块铸造表面GB/T6414---1999铸件尺寸公差和机械加工余量GB/T11346-1989铝合金铸件X射线照相检验针孔(圆形)分级GB/T11351--1989铸件重量公差
HB6578--1992铝镁合金铸件检验用标准参考射线底片JB/T7946.3—1995铸造铝合金针孔3铸件分类
3.11类铸件
承受重载荷,工作条件复杂,用于关键部位、铸件损坏将危及整机安全运行的重要铸件。3.2I类铸件
承受中等载荷,用于重要部位,铸件损坏将影响部件的正常工作,造成事故的铸件。3.3亚类铸件
承受轻载荷,用于一般部位的铸件。4技术要求
4.1化学成分
4.1.1合金的化学成分应符合GB/T1173的规定。4.1.2对于不承受载荷或承受轻微载荷且没有特殊物理性能和使用性能要求的Ⅱ类铸件,经用户同意,可不进行化学成分分析。
4.2供应状态
4.2.1铸件按GB/T1173的规定,呈铸态或热处理状态供应。4.2.2铸件的供应状态由设计部门或用户在图样中规定,国家质量技术监督局1999-09-03批准2000-03-01实施
4.3力学性能
GB/T 9438—1999
4.3.1单铸或附铸试样的力学性能应符合GB/T1173的要求。4.3.2铸件应按其类别检验力学性能、4.3.2.1从铸件上切取试样检验力学性能,三根试样的抗拉强度和伸长率的平均值,分别不低于GB/T1173规定值的75%和50%。允许其中一根试样的性能偏低,I类铸件设计指定部位的抗拉强度和延伸率分别不低于规定值的70%和40%,1类铸件非指定部位和I类铸件分别不低于规定值的65%和40%。
4.3.2.2当设计部门或用户要求1类铸件切取试样的力学性能高于上述要求时,应取得生产厂家的同意。
4.3.3按图样或有关文件的规定,对铸件进行硬度检验,其硬度值不得低于GB/T1173的规定。4.4铸件尺寸
铸件的尺寸和几何形状应符合铸件图的要求,铸件尺寸公差应符合GB/T6414的规定。4.5铸件重量
除另有规定外,铸件的重量公差按GB/T11351规定执行。4.6表面质量
4.6.1铸件应清理干净,不得有毛刺、飞边,非加工表面上的浇冒口应清理与铸件表面齐平。待加工面上浇冒口等的残留量应在图样规定的余量范围内,如果没有专门规定,般不应高出铸件表面5mm,但不得影响射线检查。
4.6.2铸件表面上不允许有冷隔、裂纹、缩孔和穿透性缺陷及严重的残缺类缺陷(如欠铸、机械损伤等)。
4.6.3铸件待加工表面上,允许有经加工可去掉的任何缺陷。但裂纹必须打磨干净。4.6.4铸件上作为加工基准所用的部位应平整。4.6.5在金属型铸件的非加工表面上,允许有铸型分型、错箱、顶杆及排气塞等痕迹,但凸出表面不超过1mm或凹下表面不超过0.5mm
4.6.6砂型、金属型等铸件的非加工表面和加工后表面,-般允许有:a)在非加工表面上,单个孔洞的最大直径不大于3mm,深度不超过壁厚的1/3。在安装边上不超过壁厚的1/4,且不大于1.5mm。在上述缺陷的同一截面的反面,不得有类似缺陷。成组孔洞对于1、类铸件孔洞的最大直径不大于1.5mm,深度不超过壁厚的1/3,且不大于1mm;对于皿类铸件,最大直径不大于2mm,深度不超过壁厚的1/3,且不大于1.5mm。b)在加工后表面上,单个孔洞的最大直径不大于1.5mm,深度不大于1mm,上述缺陷的数量、边距等应符合表1的规定,4.6.7I类或液压、气压件的砂型、金属型等铸件的加工表面一般按JB/T7946.3-1995的2级针孔验收,局部允许3级针孔但一般不超过受检面积的25%。当气密性试验满足设计要求时,允许降一级验收。1类或其他砂型和金属型等铸件按3级针孔验收。4.6.8螺纹孔内起始旋入四个牙距之内不允许有缺陷。四个牙距之外是否允许有缺陷以及允许缺陷的大小、数量按图样规定。
4.6.9铸件非加工表面上的铸字和标志应清晰可辨,位置和字体应符合图样要求。4.6.10对于不同于本标准规定的铸件表面缺陷·由专用技术标准规定。4.7内部质量
4.7.1铸件内部针孔,当用X射线照相方法检验时,对于I类铸件或液压、气压件应按GB/T11346-1989和HB6578-1992的2级验收,允许局部有4级针孔,但--般不得超过受检面积的25%。当气密性试验满足设计要求时,允许降一级验收。Ⅱ类铸件按3级针孔验收。4.7.2各类铸件内部不允许存在裂纹。各类铸件内部气孔、缩孔、疏松、夹杂物等缺陷不超过表2中所294
GB/T 9438 -- 1999
规定的级别。允许用户和制造厂家按HB6578规定的部分内容进行验收。表1表面孔洞限量
1000~3000
≥3 000~6 000
>6 000~8 000
>8 000~30 000
>30 000-~100 000
单个孔洞
在10cm×
成组孔洞
孔洞边缘距
在个铸
孔洞边距
一个铸件
以3cm×
上的孔洞总 3cm单位面件上组的数 铸件边缘的距10cm单位不小于
面积上孔洞
总数不多于
数不多于
积为一组其孔量不多于
洞数不多于
不小于孔洞最
大直径的2倍
注:在非加工表面上最大直径小于1mm,加工后表面上最大直径小于0.5mm的单个孔洞不予计算表2内部缺陷允许级别
缺陷种类
检验部位
费件壁厚
夹杂物(低密度)
夹杂物(高密度)
I类铸件指定部位
≤12 mm
>12~50 mml
1类铸件非指定部
位和!类铸件
≤12mm
>12~50 mm
其他铸件
≤12mm
12~~50 mm
4.7.3在4.7.1、4.7.2条中所述缺陷,系指其中一种缺陷单独存在时的规定。如两种或两种以上不同类型的缺陷同时存在,其验收方法与用户另行商定。4.7.4铸件内部针孔,当用低倍试验方法检验时,对于1类铸件或液压、气压件应按JB/T7946.31995的2级验收,允许局部有3级针孔,但一般不得超过受检面积的25%。当气密性试验满足设计要求时,允许降一级验收。I类铸件按3级针孔验收。4.7.5铸件内部的偏析,由专用技术标准规定。4.7.6要求气密性的铸件,应按图样或专用技术文件的要求进行气密性试验。必要时,允许对铸件进行漫渗处理。
4.8铸件修补及矫正
4.8.1可用打磨的方法清除任何缺陷。但打磨后的尺寸,应符合铸件尺寸公差的要求。4.8.2变形的铸件允许用机械方法矫正。矫正后全部检查有无裂纹。热处理后的机械矫形,事先应取295
得用户的同意并按专用文件进行。GB/T 9438 - 1999
4.8.3除另有规定外,铸件可用焊补的方法修复。焊补方法由供需双方协商确定。4.8.4焊补用填充金属按合同规定或由供需双方协商确定。4.8.5当采用氩弧焊焊补时,焊补面积、焊补处数、焊补最大深度,一般应符合表3的规定。特殊情况下的焊补,由用户在专用技术文件中规定。4.8.6同一处焊补不超过三次。焊区边缘间距(包括反面的焊区)不得小于两相邻焊区直径之和。4.8.7凡以热处理状态供应的铸件,焊补后需按原规定状态进行热处理,热处理后的铸件按4.3与5.4条检验力学性能。当氩孤焊区面积小于2cm2,焊区间距不小于100mm,经冶金部门同意,焊补后可不经热处理,但在个铸件上,不得多于五处。而ZL301、ZL305合金的铸件,焊补后一律按原状态进行热处理。
4.8.8焊补区不得有裂纹、未焊透、未熔合等缺陷。在任一焊区中允许有最大直径不大于2mm且不超过壁厚1/3的气泡和夹杂三个。边距不小于10mm,直径小于0.5mm的分散气泡或夹杂不计。4.8.9铸件焊补应按焊补工艺规定进行。4.8.10凡经焊补的铸件应在焊补处标记,或在有关技术文件中标注在示意图上以备检验,4.8.11铸件还允许采用经供需双方商定的其他方法,如浸渗、粘补、热等静压、锤击等进行修补。表3铸件允许的焊补面积及数量
铸件类型
小型件
中型件
大型件
铸件表面积
>1000~3000
>3 000~6000
>6 000
焊补面积不大于
10($36mm)
15(Φ44mm)
20(§50mm)
25($56 mm)
焊补面积是指扩修后的面积;
2焊补面积小于2cm2的焊区,不计入焊补数。5试验方法和检验规则
5.1铸件检验组批
5.1.11类铸件检验批次
修补处数
不多于,个
焊补最大深度
个铸件上总焊
补数不多于,个
同一熔炼炉次的合金、同一铸造工艺条件在8h以内浇注的、采用同一热处理工艺总量不超过1000kg的全部铸件。特殊情况下的组批由供需双方商定。5.1.2I类铸件检验批次
同一合金,在8h之内浇注的、采用同一热处理工.艺总量不超过3000kg的全部铸件。5.1.3类铸件检验批次
在生产稳定的情况下(包括原材料、熔炼工艺、浇注工艺、检验等工序的稳定)、一周内浇注的同一合296
金的全部铸件。
5.2检验项目
GB/T 9438—1999
5.2.1每批铸件按其类别检验各项性能,各类铸件的检验项目见表4。5.2.2铸件类别由用户在图样中标注或在有关技术文件中规定。对于未注明类别的铸件视为亚类铸件。图样标记包括:所用合金牌号或代号、铸造方法、铸件供应状态、铸件类别以及所执行的标准等。ZL 101-SB-T6
示例:1GB/9438-1999
表4各类铸件检验项目
伸长率Www.bzxZ.net
粗糙度
公差组织
X射线
符号^为必检项目,为仅当用户要求时才进行检验,一为不须检验的项目。2带*为铸件本体取样性能如已检验,则单铸试样性能不必再检验2
5.3化学成分
气密性
5.3.1合金化学成分的检验方法应符合GB/T1173-—1995中5.1的规定,性能
强度、
伸长率
(本体
取样)
5.3.2对每一熔炼炉(批)次的铸件必须对合金元素和主要杂质元素(由铸件生产厂确定)进行分析,其余杂质仅在用户要求或工艺检验时进行分析。5.3.3当用几个熔炼炉次的合金浇注一个「类或1类铸件时,每炉都要检验化学成分。5.3.4合金化学成分第一次分析不合格,允许重新取样分析不合格元素。若第二次分析仍不合格时,铸件为不合格件。
5.3.5合金化学成分分析试样也可取自铸件,并按5.3.4条的规定验收。5.4力学性能
5.4.1每批铸件按其类别检验力学性能。5.4.2合金力学性能的检验方法应符合GB/T228的规定。5.4.31类铸件除用单铸试样(或附铸试样)检验力学性能外,还应按供需双方商定的比例,从铸件的指定部位和非指定部位切取试样检验力学性能。5.4.3.1切取试样的部位由用户在图样中规定,无明确规定时,由铸件生产厂确定。5.4.3.2切取试样选用GB/T228中直径不小于6mm的短试样,当不能切取圆试样时,允许按专用标准切取板形试样。
5.4.3.3对小于10kg或不便于切取拉伸试样的铸件可检验铸件的硬度。抽检比例由供需双方商定。5.4.4I类、类铸件用单铸试样或附铸试样检验力学性能,按GB/T1173-1995中5.2.3及5.2.4进行;如复验仍不合格,则从该批次中随机或按供需双方商定的方法选取铸件,切取试样检验力学性能,检验方法按5.4.3及5.4.6进行。如不合格,则该批次全部铸件由供需双方协商处理。5.4.5如果一个熔炼炉次中同一热处理状态的铸件,在不同的热处理炉次中进行热处理,并且该熔炼炉次的试样已在一个热处理炉次中经检验合格,则另一热处理炉次中该熔炼炉次的铸件可按同热处理297
GB/T 9438—1999
炉次中任--熔炼炉次的合格试样交付。如果所提交验收的单铸或附铸试样性能不合格,需从铸件上切取试样时,应从该热处理炉次的各个熔炼炉次中随机或按供需双方商定的方法选取铸件,切取试样测定力学性能。
5.4.6当被抽检的铸件本体取样力学性能不合格时(不论试样上是否存在铸造缺陷),可加倍抽检,重新取样检验力学性能。如果加倍抽检的结果都合格,则该炉(批)铸件力学性能合格。否则不合格。当加倍抽检仍不合格时,允许重新热处理后取样检验,但只允许重复热处理二次。每次热处理后,若单铸试样不合格,铸件上切取的力学性能合格时,则该熔炼炉次铸件为合格件。5.4.7当用户对切取试样力学性能要求不同于本标准时,应与铸件生产厂协商按专用技术文件规定进行。
5.4.8-般情况下,硬度不做检验。当设计有要求时,应按GB/T1173-1995中5.2.12条的规定,在同一批次铸件中抽检。如不合格,抽检数量加倍。加倍抽检的铸件硬度都合格,则该批铸件硬度合格。否则不合格。当加倍抽捡后仍不合格,允许重复热处理,但重复热处理次数不允许超过二次。5.4.8.1铸件硬度检验部位及抽检方法,应符合图样或有关文件规定。如无明确规定,则在铸件需要保证特定硬度的部位检验硬度。
5.4.8.2铸件硬度值应符合GB/T1173—1995表3的规定。5.4.8.3由于硬度不合格而重复热处理时,除检验硬度外,还应按原要求检验单铸或切取试样的抗拉强度和伸长率。
5.4.8.4当对铸件的硬度值有特殊要求时,应征得生产厂家同意并在图样上标明,铸件的热处理规范可作适当的调整,
5.4.9以铸态提供的铸件,当力学性能不合格时,允许对铸件进行适当的热处理,其力学性能仍按原铸态指标验收。
5.4.10对铸件有其他力学性能要求时,其技术要求和验收方法忠设计部门或用户和生产厂家协商后。在图样或有关技术文件中规定。5.5铸件尺寸
铸件易变动的尺寸应逐件检验,其他尺寸进行抽查。不解剖无法检验的尺寸,由检验部门定期解剖检验。
5.6铸件重量
铸件重量按图样或合同规定验收。如无明确定,铸件重量公差应符合GB/T11351之规定。抽检方法由供需双方商定。
5.7外观质量
5.7.1铸件均用目视(或用10倍以下的放大镜)及适当的量具、仪器或试验方法检验其外观质量。5.7.2铸件非加工表面的粗糙度评级可按GB/T6060.1进行。5.7.3铸件加工表面针孔度评级按JB/T7946.3进行。5.7.4铸件按图样要求进行荧光探伤或煤油漫润等检查5.8内部质量
5.8.1低倍试验检验针孔时按JB/T7946.3的要求进行。5.8.21类、I类铸件应按图样或有关技术文件的规定,进行X射线检验。其检验部位和比例由设计部门或用户和生产厂家商定。检验数量按每个熔炼炉次所浇注的铸件数计算。5.8.3当X射线照相检验抽查有不合格时,应取双倍。如仍有不合格,全部铸件逐个进行检验5.8.4当用低倍试验方法检验内部缺陷(针孔除外)时,应按专用技术文件验收5.8.5当用X射线照相方法检验时,铸件内部针孔、气孔、疏松等缺陷评级可按GB/T11346及HB6578或专用文件进行。
5.8.6铸件焊补后,用肉眼(可借助10倍以下放大镜)、荧光等检查其表面焊补质量,检查面积不小于298
GB/T 9438 -1999
焊补面积的两倍。焊区不得有裂纹、缩孔、咬边、未熔合等缺陷。5.8.7当焊补要求不同于本标准时,可按合同或专用技术文件验收。5.8.8铸件焊补后应对焊区内部进行无损检验。检验面积不小于焊补面积的两倍。1类铸件焊补部位全部检查,1类铸件焊补后,根据用户的要求按一定比例抽检。焊区内不得有裂纹、未焊透、分层等内部缺陷。焊区内部所允许的其他缺陷可按专用文件规定。对于焊补面积不大于2cm的焊区,且不能X射线检验时,经冶金部门同意可不做X射线检验。5.8.9铸件断口,显微组织及抗腐蚀性能等按专用文件进行检验。5.8.10铸件气密性等其他性能检验按合同或专用文件进行。5.9工艺检验
5.9.1工艺检验的目的是全面检查批生产铸件的质量情况,以便及时采取措施保证产品质量。5.9.2经生产试制、定型、转入批生产的铸件,连续生产六个月进行一次工艺检验。停产半年以上恢复生产时,首批铸件也需进行检验。5.9.3工艺检验的项目包括合金化学成分的全面分析、全面的X射线检验、荧光检查、煤油浸润、从铸件上切取性能、低倍和金相检验等。根据生产情况,允许治金部门和检验部门协商选取上述部分项目进行检验。5.9.4治金部门根据上述要求制定工艺检验专用技术文件,检验部门按专用文件进行工艺检验。工艺检验中发现有不符合铸件工艺定型的质量要求时,应改进工艺、采取措施,达到质量要求后方可继续生产。对于已生产的铸件由检验部门会同冶金部门协商处理。6标志、包装、运输、贮存
6.1铸件上应有检验印记、合金代号、商标等。各种印记应清晰可见。尺寸小的铸件可仅有检验印记或挂标签。
6.2铸件包装应保证运输中和存放期间不锈蚀和无机械损伤。6:3铸件应附有合格证。合格证应标明该批铸件符合图样或合同及有关技术标准规定的要求。299
小提示:此标准内容仅展示完整标准里的部分截取内容,若需要完整标准请到上方自行免费下载完整标准文档。
本标准是对GB/T94381988的修订。吸收10年来我国铸造铝合金方面的科研成果和生产实践经验,参照美国 ASTM B26/B26M一92a《Standard Specification for Aluminium-Alloy Sand Castings》ASTM Bl08-92a《Standard Specification for Aluminium-Alloy Permanent Mold Castings 》,ASTME155-85《Standard Radiographs for Inspection of Aluminium and Magnesium Castings 》, 罗斯 OCT190021-92《OT.JIHBK DACOHHbIE M3 AJIOMIHHEBBIX CIIJIABOB TEXHIIHECKHE TPELOBAHH》等国外先进标准及国内航空系统的相关标准,并考虑到与GB/T1173--1995《铸造铝合金》的配套性,本标准与被修订的标准在以下重要技术内容上有所改变:一第4.3.2.1条,从铸件上切取试样检验力学性能,三根试样的抗拉强度的平均值由不低于规定值的80%改为75%。ASTMB26/B26M-92a、ASTMB108-92a及俄罗斯OCT190021-92标准的规定均为75%。
第4.6.6条,取消了铸件表面质量的分级规定。因为实际上铸件是按类别验收的,表面质量按级验收生产中较少使用。在表面孔洞限量的表1中,对1类铸件的要求略有提高,Ⅱ类铸件不变,亚类铸件略有放松
第4.7.1条,当用X射线照相方法检验内部针孔时,局部允许的针孔级别由3级改为4级。第4.7.2条,对铸件内部的其他缺陷作出明确而严格的规定。为顾及各个层面的使用者,本条明确规定允许用户和制造厂家按HB6578--1992规定的部分内容进行验收。本标准自实施之日起,同时代替GB/T9438--1988《铝合金铸件技术条件》。本标准与GB/T1173-1995《铸造铝合金》配套使用。本标准由国家机械工业局提出。本标准由全国铸造标准化技术委员会归口。本标准起草单位:沈阳铸造研究所、北京航空材料研究院、洛阳七二五研究所、阿城市有色金属铸造本标准主要起草人:李德成、李玉胜、余应梅、金长庚、孙建科、熊文定、刘志启、张斌。292
中华人民共和国国家标准
铝合金铸件
Aluminium alloy castings
GB/T9438--1999
代替GB/T94381988
本标准规定了铝合金铸件的分类和铸件的外观质量、内在质量以及铸件修补等内容的技术要求与检验规则等,
本标准适用于采用砂型铸造和特种铸造(不含压力铸造)生产的铝合金铸件。2引用标准
下列标准所包含的条文,通过在本标准中引用而构成本标准的条文。本标准出版时,所示版本均为有效。所有标准都会被修订,使用本标准的各方应探讨使用下列标准最新版本的可能性。GB/T228—1987金属拉伸试验方法GB/T1173--1995铸造铝合金
GB/T6060.1-1997表面粗糙度比较样块铸造表面GB/T6414---1999铸件尺寸公差和机械加工余量GB/T11346-1989铝合金铸件X射线照相检验针孔(圆形)分级GB/T11351--1989铸件重量公差
HB6578--1992铝镁合金铸件检验用标准参考射线底片JB/T7946.3—1995铸造铝合金针孔3铸件分类
3.11类铸件
承受重载荷,工作条件复杂,用于关键部位、铸件损坏将危及整机安全运行的重要铸件。3.2I类铸件
承受中等载荷,用于重要部位,铸件损坏将影响部件的正常工作,造成事故的铸件。3.3亚类铸件
承受轻载荷,用于一般部位的铸件。4技术要求
4.1化学成分
4.1.1合金的化学成分应符合GB/T1173的规定。4.1.2对于不承受载荷或承受轻微载荷且没有特殊物理性能和使用性能要求的Ⅱ类铸件,经用户同意,可不进行化学成分分析。
4.2供应状态
4.2.1铸件按GB/T1173的规定,呈铸态或热处理状态供应。4.2.2铸件的供应状态由设计部门或用户在图样中规定,国家质量技术监督局1999-09-03批准2000-03-01实施
4.3力学性能
GB/T 9438—1999
4.3.1单铸或附铸试样的力学性能应符合GB/T1173的要求。4.3.2铸件应按其类别检验力学性能、4.3.2.1从铸件上切取试样检验力学性能,三根试样的抗拉强度和伸长率的平均值,分别不低于GB/T1173规定值的75%和50%。允许其中一根试样的性能偏低,I类铸件设计指定部位的抗拉强度和延伸率分别不低于规定值的70%和40%,1类铸件非指定部位和I类铸件分别不低于规定值的65%和40%。
4.3.2.2当设计部门或用户要求1类铸件切取试样的力学性能高于上述要求时,应取得生产厂家的同意。
4.3.3按图样或有关文件的规定,对铸件进行硬度检验,其硬度值不得低于GB/T1173的规定。4.4铸件尺寸
铸件的尺寸和几何形状应符合铸件图的要求,铸件尺寸公差应符合GB/T6414的规定。4.5铸件重量
除另有规定外,铸件的重量公差按GB/T11351规定执行。4.6表面质量
4.6.1铸件应清理干净,不得有毛刺、飞边,非加工表面上的浇冒口应清理与铸件表面齐平。待加工面上浇冒口等的残留量应在图样规定的余量范围内,如果没有专门规定,般不应高出铸件表面5mm,但不得影响射线检查。
4.6.2铸件表面上不允许有冷隔、裂纹、缩孔和穿透性缺陷及严重的残缺类缺陷(如欠铸、机械损伤等)。
4.6.3铸件待加工表面上,允许有经加工可去掉的任何缺陷。但裂纹必须打磨干净。4.6.4铸件上作为加工基准所用的部位应平整。4.6.5在金属型铸件的非加工表面上,允许有铸型分型、错箱、顶杆及排气塞等痕迹,但凸出表面不超过1mm或凹下表面不超过0.5mm
4.6.6砂型、金属型等铸件的非加工表面和加工后表面,-般允许有:a)在非加工表面上,单个孔洞的最大直径不大于3mm,深度不超过壁厚的1/3。在安装边上不超过壁厚的1/4,且不大于1.5mm。在上述缺陷的同一截面的反面,不得有类似缺陷。成组孔洞对于1、类铸件孔洞的最大直径不大于1.5mm,深度不超过壁厚的1/3,且不大于1mm;对于皿类铸件,最大直径不大于2mm,深度不超过壁厚的1/3,且不大于1.5mm。b)在加工后表面上,单个孔洞的最大直径不大于1.5mm,深度不大于1mm,上述缺陷的数量、边距等应符合表1的规定,4.6.7I类或液压、气压件的砂型、金属型等铸件的加工表面一般按JB/T7946.3-1995的2级针孔验收,局部允许3级针孔但一般不超过受检面积的25%。当气密性试验满足设计要求时,允许降一级验收。1类或其他砂型和金属型等铸件按3级针孔验收。4.6.8螺纹孔内起始旋入四个牙距之内不允许有缺陷。四个牙距之外是否允许有缺陷以及允许缺陷的大小、数量按图样规定。
4.6.9铸件非加工表面上的铸字和标志应清晰可辨,位置和字体应符合图样要求。4.6.10对于不同于本标准规定的铸件表面缺陷·由专用技术标准规定。4.7内部质量
4.7.1铸件内部针孔,当用X射线照相方法检验时,对于I类铸件或液压、气压件应按GB/T11346-1989和HB6578-1992的2级验收,允许局部有4级针孔,但--般不得超过受检面积的25%。当气密性试验满足设计要求时,允许降一级验收。Ⅱ类铸件按3级针孔验收。4.7.2各类铸件内部不允许存在裂纹。各类铸件内部气孔、缩孔、疏松、夹杂物等缺陷不超过表2中所294
GB/T 9438 -- 1999
规定的级别。允许用户和制造厂家按HB6578规定的部分内容进行验收。表1表面孔洞限量
1000~3000
≥3 000~6 000
>6 000~8 000
>8 000~30 000
>30 000-~100 000
单个孔洞
在10cm×
成组孔洞
孔洞边缘距
在个铸
孔洞边距
一个铸件
以3cm×
上的孔洞总 3cm单位面件上组的数 铸件边缘的距10cm单位不小于
面积上孔洞
总数不多于
数不多于
积为一组其孔量不多于
洞数不多于
不小于孔洞最
大直径的2倍
注:在非加工表面上最大直径小于1mm,加工后表面上最大直径小于0.5mm的单个孔洞不予计算表2内部缺陷允许级别
缺陷种类
检验部位
费件壁厚
夹杂物(低密度)
夹杂物(高密度)
I类铸件指定部位
≤12 mm
>12~50 mml
1类铸件非指定部
位和!类铸件
≤12mm
>12~50 mm
其他铸件
≤12mm
12~~50 mm
4.7.3在4.7.1、4.7.2条中所述缺陷,系指其中一种缺陷单独存在时的规定。如两种或两种以上不同类型的缺陷同时存在,其验收方法与用户另行商定。4.7.4铸件内部针孔,当用低倍试验方法检验时,对于1类铸件或液压、气压件应按JB/T7946.31995的2级验收,允许局部有3级针孔,但一般不得超过受检面积的25%。当气密性试验满足设计要求时,允许降一级验收。I类铸件按3级针孔验收。4.7.5铸件内部的偏析,由专用技术标准规定。4.7.6要求气密性的铸件,应按图样或专用技术文件的要求进行气密性试验。必要时,允许对铸件进行漫渗处理。
4.8铸件修补及矫正
4.8.1可用打磨的方法清除任何缺陷。但打磨后的尺寸,应符合铸件尺寸公差的要求。4.8.2变形的铸件允许用机械方法矫正。矫正后全部检查有无裂纹。热处理后的机械矫形,事先应取295
得用户的同意并按专用文件进行。GB/T 9438 - 1999
4.8.3除另有规定外,铸件可用焊补的方法修复。焊补方法由供需双方协商确定。4.8.4焊补用填充金属按合同规定或由供需双方协商确定。4.8.5当采用氩弧焊焊补时,焊补面积、焊补处数、焊补最大深度,一般应符合表3的规定。特殊情况下的焊补,由用户在专用技术文件中规定。4.8.6同一处焊补不超过三次。焊区边缘间距(包括反面的焊区)不得小于两相邻焊区直径之和。4.8.7凡以热处理状态供应的铸件,焊补后需按原规定状态进行热处理,热处理后的铸件按4.3与5.4条检验力学性能。当氩孤焊区面积小于2cm2,焊区间距不小于100mm,经冶金部门同意,焊补后可不经热处理,但在个铸件上,不得多于五处。而ZL301、ZL305合金的铸件,焊补后一律按原状态进行热处理。
4.8.8焊补区不得有裂纹、未焊透、未熔合等缺陷。在任一焊区中允许有最大直径不大于2mm且不超过壁厚1/3的气泡和夹杂三个。边距不小于10mm,直径小于0.5mm的分散气泡或夹杂不计。4.8.9铸件焊补应按焊补工艺规定进行。4.8.10凡经焊补的铸件应在焊补处标记,或在有关技术文件中标注在示意图上以备检验,4.8.11铸件还允许采用经供需双方商定的其他方法,如浸渗、粘补、热等静压、锤击等进行修补。表3铸件允许的焊补面积及数量
铸件类型
小型件
中型件
大型件
铸件表面积
>1000~3000
>3 000~6000
>6 000
焊补面积不大于
10($36mm)
15(Φ44mm)
20(§50mm)
25($56 mm)
焊补面积是指扩修后的面积;
2焊补面积小于2cm2的焊区,不计入焊补数。5试验方法和检验规则
5.1铸件检验组批
5.1.11类铸件检验批次
修补处数
不多于,个
焊补最大深度
个铸件上总焊
补数不多于,个
同一熔炼炉次的合金、同一铸造工艺条件在8h以内浇注的、采用同一热处理工艺总量不超过1000kg的全部铸件。特殊情况下的组批由供需双方商定。5.1.2I类铸件检验批次
同一合金,在8h之内浇注的、采用同一热处理工.艺总量不超过3000kg的全部铸件。5.1.3类铸件检验批次
在生产稳定的情况下(包括原材料、熔炼工艺、浇注工艺、检验等工序的稳定)、一周内浇注的同一合296
金的全部铸件。
5.2检验项目
GB/T 9438—1999
5.2.1每批铸件按其类别检验各项性能,各类铸件的检验项目见表4。5.2.2铸件类别由用户在图样中标注或在有关技术文件中规定。对于未注明类别的铸件视为亚类铸件。图样标记包括:所用合金牌号或代号、铸造方法、铸件供应状态、铸件类别以及所执行的标准等。ZL 101-SB-T6
示例:1GB/9438-1999
表4各类铸件检验项目
伸长率Www.bzxZ.net
粗糙度
公差组织
X射线
符号^为必检项目,为仅当用户要求时才进行检验,一为不须检验的项目。2带*为铸件本体取样性能如已检验,则单铸试样性能不必再检验2
5.3化学成分
气密性
5.3.1合金化学成分的检验方法应符合GB/T1173-—1995中5.1的规定,性能
强度、
伸长率
(本体
取样)
5.3.2对每一熔炼炉(批)次的铸件必须对合金元素和主要杂质元素(由铸件生产厂确定)进行分析,其余杂质仅在用户要求或工艺检验时进行分析。5.3.3当用几个熔炼炉次的合金浇注一个「类或1类铸件时,每炉都要检验化学成分。5.3.4合金化学成分第一次分析不合格,允许重新取样分析不合格元素。若第二次分析仍不合格时,铸件为不合格件。
5.3.5合金化学成分分析试样也可取自铸件,并按5.3.4条的规定验收。5.4力学性能
5.4.1每批铸件按其类别检验力学性能。5.4.2合金力学性能的检验方法应符合GB/T228的规定。5.4.31类铸件除用单铸试样(或附铸试样)检验力学性能外,还应按供需双方商定的比例,从铸件的指定部位和非指定部位切取试样检验力学性能。5.4.3.1切取试样的部位由用户在图样中规定,无明确规定时,由铸件生产厂确定。5.4.3.2切取试样选用GB/T228中直径不小于6mm的短试样,当不能切取圆试样时,允许按专用标准切取板形试样。
5.4.3.3对小于10kg或不便于切取拉伸试样的铸件可检验铸件的硬度。抽检比例由供需双方商定。5.4.4I类、类铸件用单铸试样或附铸试样检验力学性能,按GB/T1173-1995中5.2.3及5.2.4进行;如复验仍不合格,则从该批次中随机或按供需双方商定的方法选取铸件,切取试样检验力学性能,检验方法按5.4.3及5.4.6进行。如不合格,则该批次全部铸件由供需双方协商处理。5.4.5如果一个熔炼炉次中同一热处理状态的铸件,在不同的热处理炉次中进行热处理,并且该熔炼炉次的试样已在一个热处理炉次中经检验合格,则另一热处理炉次中该熔炼炉次的铸件可按同热处理297
GB/T 9438—1999
炉次中任--熔炼炉次的合格试样交付。如果所提交验收的单铸或附铸试样性能不合格,需从铸件上切取试样时,应从该热处理炉次的各个熔炼炉次中随机或按供需双方商定的方法选取铸件,切取试样测定力学性能。
5.4.6当被抽检的铸件本体取样力学性能不合格时(不论试样上是否存在铸造缺陷),可加倍抽检,重新取样检验力学性能。如果加倍抽检的结果都合格,则该炉(批)铸件力学性能合格。否则不合格。当加倍抽检仍不合格时,允许重新热处理后取样检验,但只允许重复热处理二次。每次热处理后,若单铸试样不合格,铸件上切取的力学性能合格时,则该熔炼炉次铸件为合格件。5.4.7当用户对切取试样力学性能要求不同于本标准时,应与铸件生产厂协商按专用技术文件规定进行。
5.4.8-般情况下,硬度不做检验。当设计有要求时,应按GB/T1173-1995中5.2.12条的规定,在同一批次铸件中抽检。如不合格,抽检数量加倍。加倍抽检的铸件硬度都合格,则该批铸件硬度合格。否则不合格。当加倍抽捡后仍不合格,允许重复热处理,但重复热处理次数不允许超过二次。5.4.8.1铸件硬度检验部位及抽检方法,应符合图样或有关文件规定。如无明确规定,则在铸件需要保证特定硬度的部位检验硬度。
5.4.8.2铸件硬度值应符合GB/T1173—1995表3的规定。5.4.8.3由于硬度不合格而重复热处理时,除检验硬度外,还应按原要求检验单铸或切取试样的抗拉强度和伸长率。
5.4.8.4当对铸件的硬度值有特殊要求时,应征得生产厂家同意并在图样上标明,铸件的热处理规范可作适当的调整,
5.4.9以铸态提供的铸件,当力学性能不合格时,允许对铸件进行适当的热处理,其力学性能仍按原铸态指标验收。
5.4.10对铸件有其他力学性能要求时,其技术要求和验收方法忠设计部门或用户和生产厂家协商后。在图样或有关技术文件中规定。5.5铸件尺寸
铸件易变动的尺寸应逐件检验,其他尺寸进行抽查。不解剖无法检验的尺寸,由检验部门定期解剖检验。
5.6铸件重量
铸件重量按图样或合同规定验收。如无明确定,铸件重量公差应符合GB/T11351之规定。抽检方法由供需双方商定。
5.7外观质量
5.7.1铸件均用目视(或用10倍以下的放大镜)及适当的量具、仪器或试验方法检验其外观质量。5.7.2铸件非加工表面的粗糙度评级可按GB/T6060.1进行。5.7.3铸件加工表面针孔度评级按JB/T7946.3进行。5.7.4铸件按图样要求进行荧光探伤或煤油漫润等检查5.8内部质量
5.8.1低倍试验检验针孔时按JB/T7946.3的要求进行。5.8.21类、I类铸件应按图样或有关技术文件的规定,进行X射线检验。其检验部位和比例由设计部门或用户和生产厂家商定。检验数量按每个熔炼炉次所浇注的铸件数计算。5.8.3当X射线照相检验抽查有不合格时,应取双倍。如仍有不合格,全部铸件逐个进行检验5.8.4当用低倍试验方法检验内部缺陷(针孔除外)时,应按专用技术文件验收5.8.5当用X射线照相方法检验时,铸件内部针孔、气孔、疏松等缺陷评级可按GB/T11346及HB6578或专用文件进行。
5.8.6铸件焊补后,用肉眼(可借助10倍以下放大镜)、荧光等检查其表面焊补质量,检查面积不小于298
GB/T 9438 -1999
焊补面积的两倍。焊区不得有裂纹、缩孔、咬边、未熔合等缺陷。5.8.7当焊补要求不同于本标准时,可按合同或专用技术文件验收。5.8.8铸件焊补后应对焊区内部进行无损检验。检验面积不小于焊补面积的两倍。1类铸件焊补部位全部检查,1类铸件焊补后,根据用户的要求按一定比例抽检。焊区内不得有裂纹、未焊透、分层等内部缺陷。焊区内部所允许的其他缺陷可按专用文件规定。对于焊补面积不大于2cm的焊区,且不能X射线检验时,经冶金部门同意可不做X射线检验。5.8.9铸件断口,显微组织及抗腐蚀性能等按专用文件进行检验。5.8.10铸件气密性等其他性能检验按合同或专用文件进行。5.9工艺检验
5.9.1工艺检验的目的是全面检查批生产铸件的质量情况,以便及时采取措施保证产品质量。5.9.2经生产试制、定型、转入批生产的铸件,连续生产六个月进行一次工艺检验。停产半年以上恢复生产时,首批铸件也需进行检验。5.9.3工艺检验的项目包括合金化学成分的全面分析、全面的X射线检验、荧光检查、煤油浸润、从铸件上切取性能、低倍和金相检验等。根据生产情况,允许治金部门和检验部门协商选取上述部分项目进行检验。5.9.4治金部门根据上述要求制定工艺检验专用技术文件,检验部门按专用文件进行工艺检验。工艺检验中发现有不符合铸件工艺定型的质量要求时,应改进工艺、采取措施,达到质量要求后方可继续生产。对于已生产的铸件由检验部门会同冶金部门协商处理。6标志、包装、运输、贮存
6.1铸件上应有检验印记、合金代号、商标等。各种印记应清晰可见。尺寸小的铸件可仅有检验印记或挂标签。
6.2铸件包装应保证运输中和存放期间不锈蚀和无机械损伤。6:3铸件应附有合格证。合格证应标明该批铸件符合图样或合同及有关技术标准规定的要求。299
小提示:此标准内容仅展示完整标准里的部分截取内容,若需要完整标准请到上方自行免费下载完整标准文档。

标准图片预览:
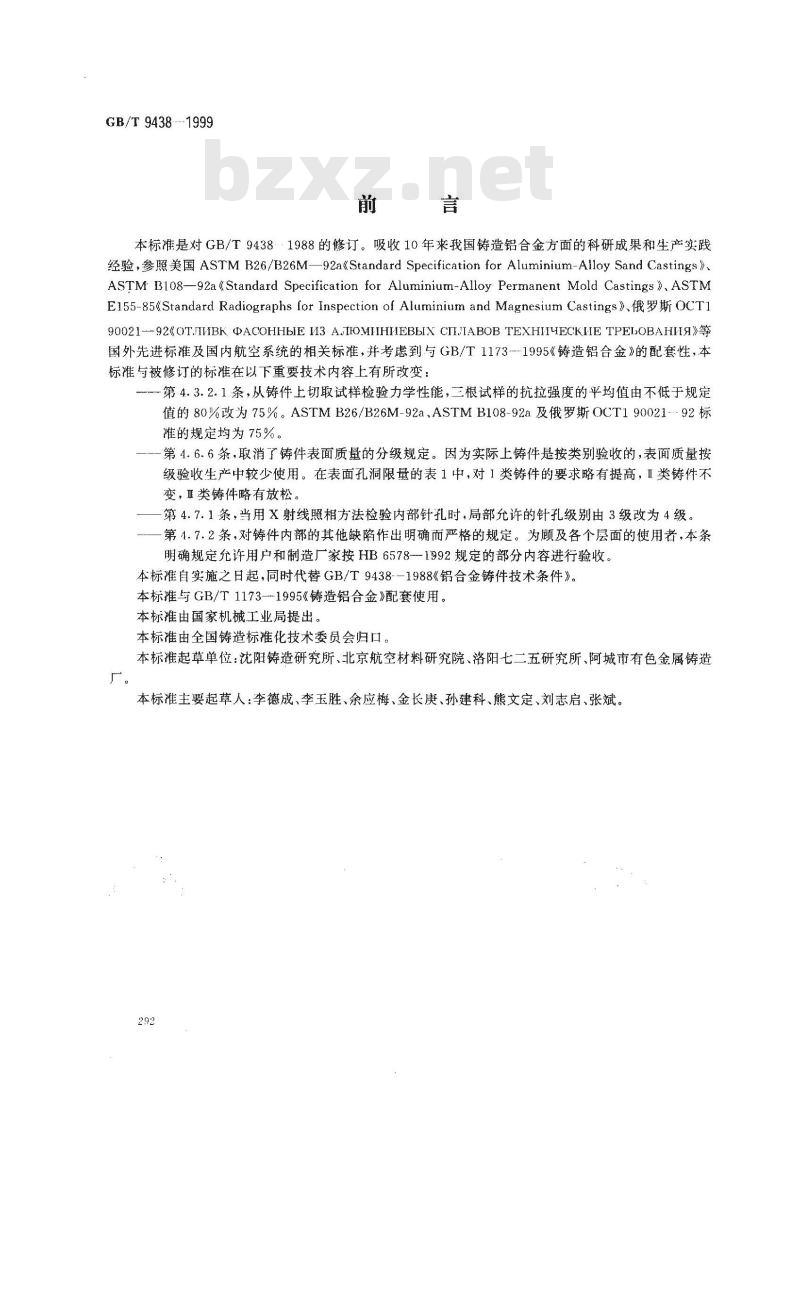
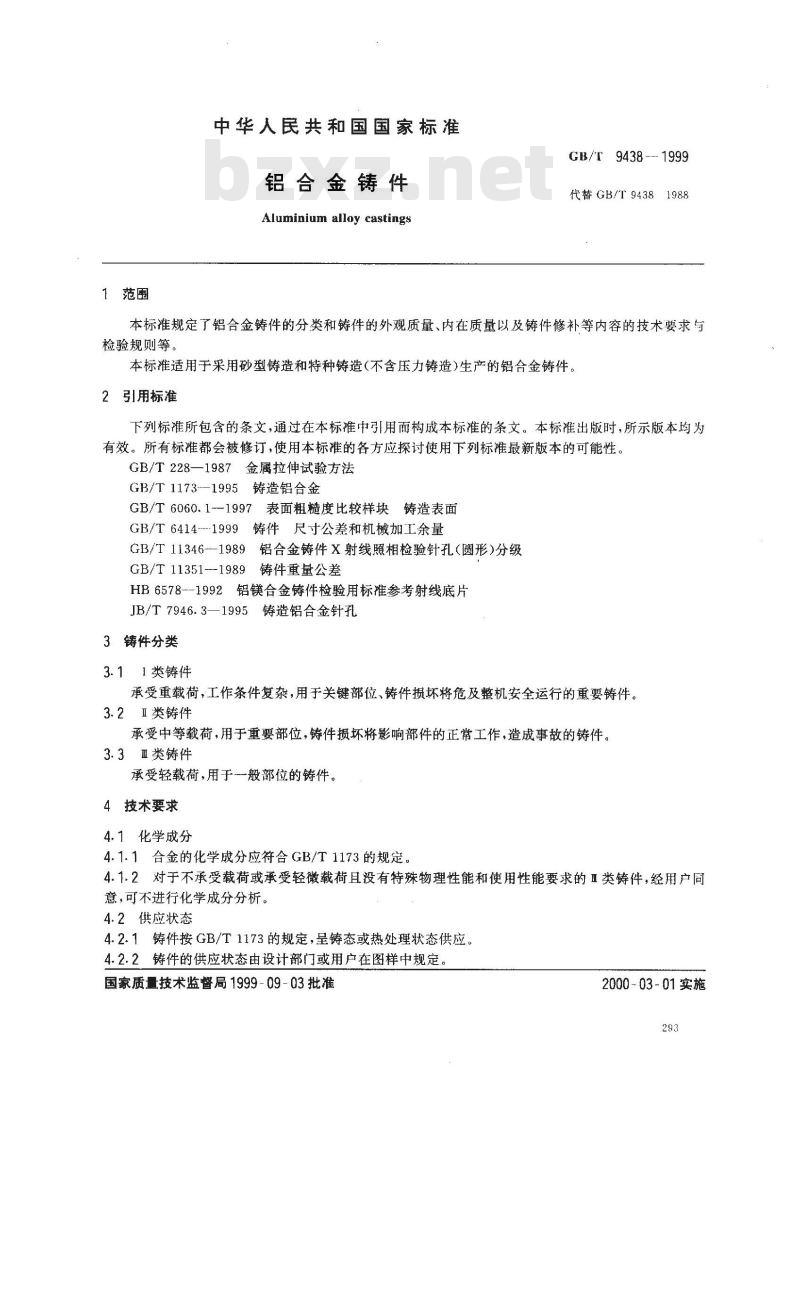
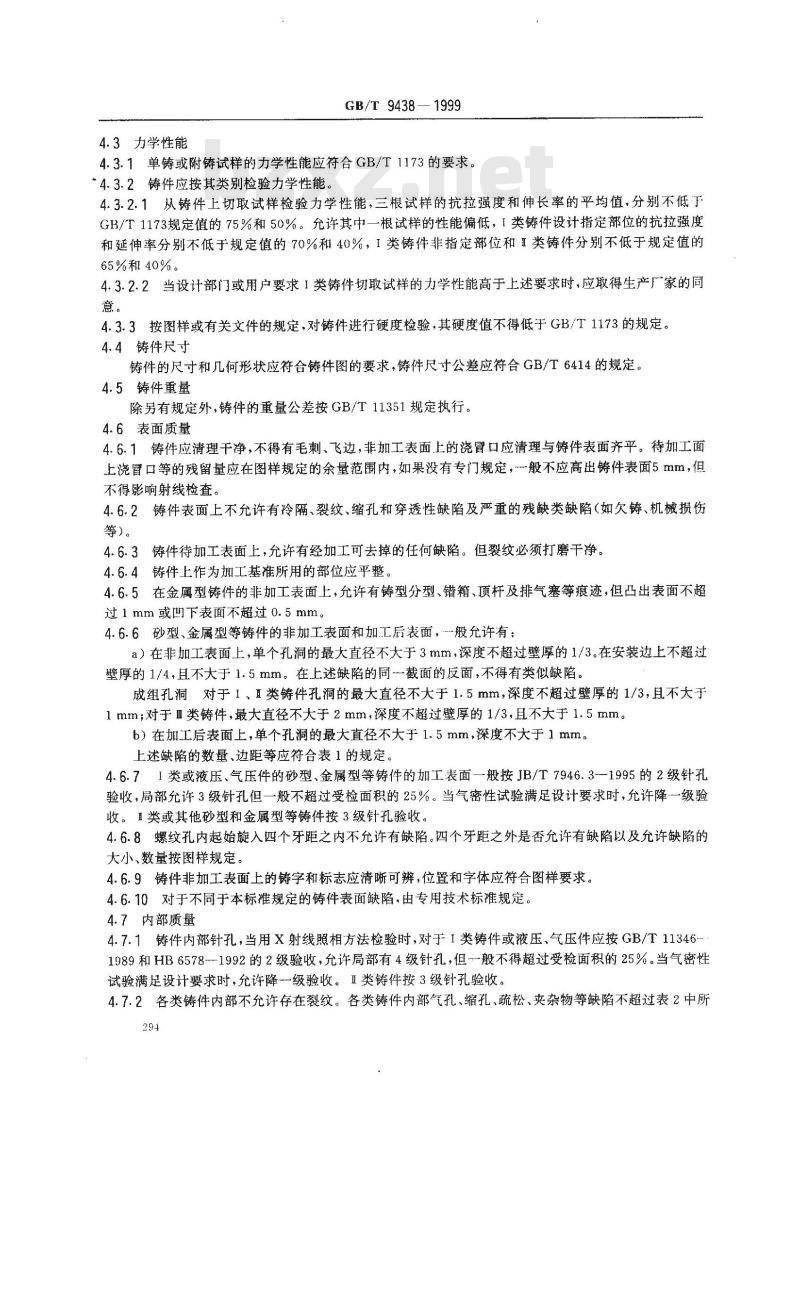
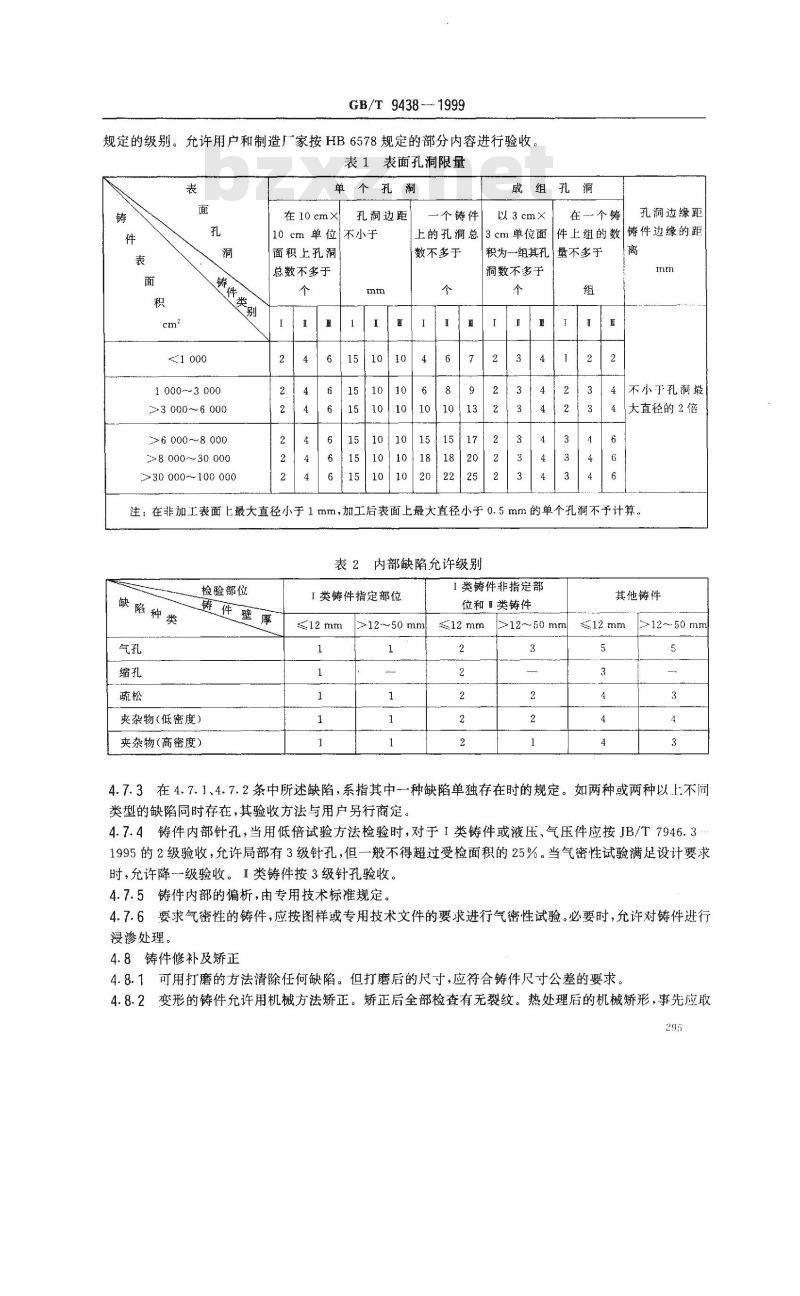
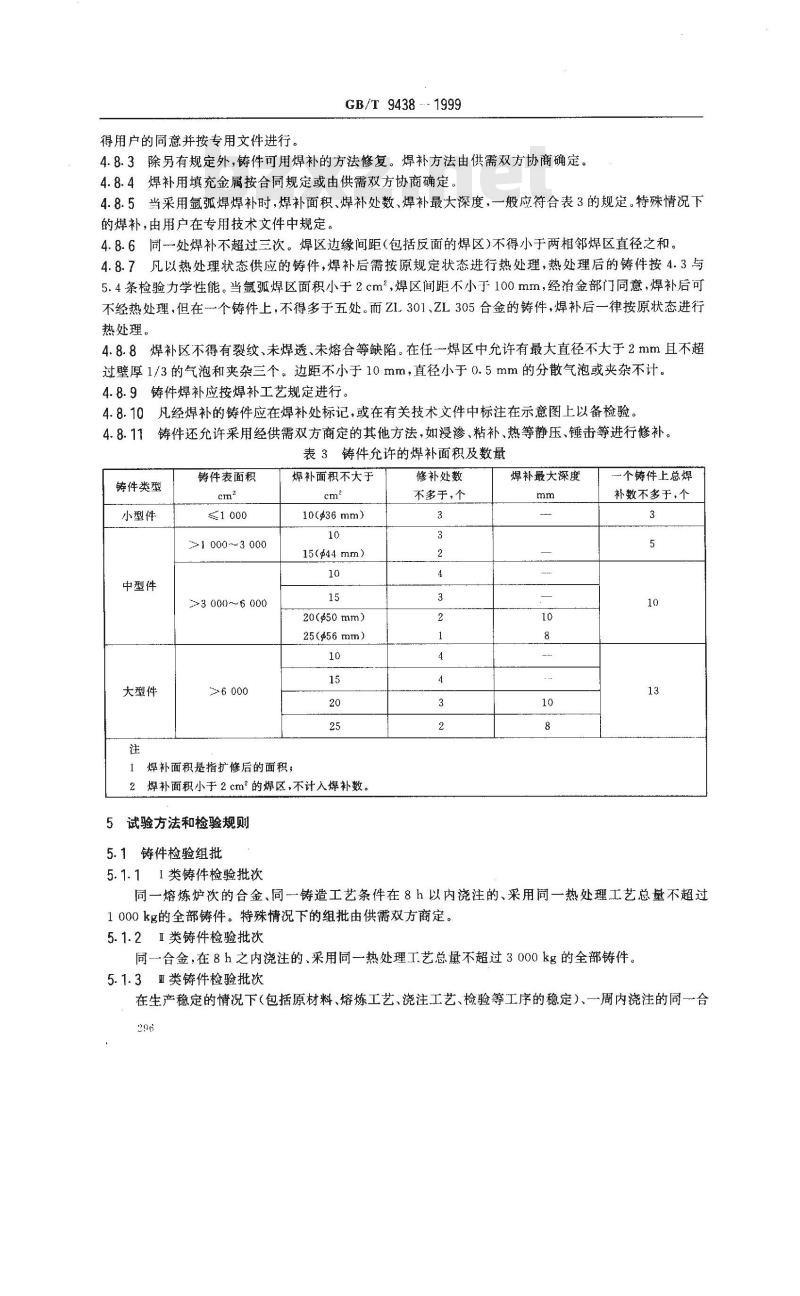
- 其它标准
- 上一篇: GB/T 9437-1988 耐热铸铁件
- 下一篇: GB 9439-1988 灰铸铁件
- 热门标准
- 国家标准(GB)
- GB/T2828.1-2012 计数抽样检验程序 第1部分:按接收质量限(AQL)检索的逐批检验抽样计划
- GB/T15310.3-1994 外贸出口单证格式 装运声明
- GB2761—2005 食品中真菌毒素限量
- GB7521—1987 多个控制器在一CA MAC机箱中
- GB/T2988—2004 高铝砖
- GB3033.1—2005 /ISO 14726-1 : 1999 船舶与海上技术管路系统内含物的识别颜色第1部分:主颜色和介质
- GB/T80-2007 内六角凹端紧定螺钉
- GB13077-2004 铝合金无缝气瓶定期检验与评定
- GB/T4789.4-2003 食品卫生微生物学检验沙门氏菌检验
- GB/T28784.5-2022 机械振动 船舶振动测量 第5部分:客船和商船适居性振动测量、评价和报告准则
- GB917.2—2000 公路路线标识规则国道名称和编号
- GB/T14652.1-2001 小艇耐火燃油软管
- GB/T155—2006 原木缺陷
- GB/T6283-2008 化工产品中水分含量的测定卡尔·费休法(通用方法)
- GB9116.5-1988 PN1.6MPa(16bar)凸面带颈平焊钢制管法兰
- 行业新闻
请牢记:“bzxz.net”即是“标准下载”四个汉字汉语拼音首字母与国际顶级域名“.net”的组合。 ©2009 标准下载网 www.bzxz.net 本站邮件:bzxznet@163.com
网站备案号:湘ICP备2023016450号-1
网站备案号:湘ICP备2023016450号-1