- 您的位置:
- 标准下载网 >>
- 标准分类 >>
- 国家标准(GB) >>
- GB/T 13315-1991 锻钢冷轧工作辊超声波探伤方法
标准号:
GB/T 13315-1991
标准名称:
锻钢冷轧工作辊超声波探伤方法
标准类别:
国家标准(GB)
标准状态:
已作废-
发布日期:
1991-01-02 -
实施日期:
1992-05-01 -
作废日期:
2008-11-01 出版语种:
简体中文下载格式:
.rar.pdf下载大小:
349.34 KB

点击下载
标准简介:
标准下载解压密码:www.bzxz.net
本标准规定了锻钢冷轧工作辊超声波探伤方法。本标准适用于直径大于等于80mm,供金属板、带、箔材冷轧用锻钢工作辊的超声波检测。 GB/T 13315-1991 锻钢冷轧工作辊超声波探伤方法 GB/T13315-1991

部分标准内容:
中华人民共和国国家标准
锻钢冷轧工作辊超声波探伤方法Method of ultrasonic inspection forforged steel cold rolling working rells1 主题内容与适用范围
本标准规定了锻钢冷轧工作辊(以下简称轧辊)超声波探伤方法GB/T 13315—91
本标准适用直径大于等于 80 mm,供金属板、带、箱材冷轧用锻钢工作辑的超声波检测。2引用标准
GB9445无损检测人员技术资格鉴定通则JB3111无损检测名词术语
ZBY230A型脉冲反射式超声探伤仪通用技术条件ZBY231.超声探伤用操头性能测试方法3符号、术语
3.1符号
符号及其意义见表1。
3.2术语
轧辊成品辊身直径
探测部位直径
探测部位半径
轧辊内扎半径
灵敏度增量
3. 2. 1AVG(DGS)法
第一改底波反射信号
第一次底被反射信号
当基平底孔
癌减系数(dB/mm)
在一定条件下,根据超声场声压变化规律,利用反射体声压、尺寸利反射体离探头距离之间的定量关系来对工件内的缺陷进行定量评价的方法,称作AVG法,亦可称DGS法。3. 2. 26 dB法
最大回波高度降低一半的测量方法。3.2.3基准高度
将荧光屏某-高度定为基准,该高度即为基准高度(通常用荧光斥满尿高度的百分数来表示)。3.2. 4单个缺陷
间距大丁5mm,当量直径不小丁蛇㎡m的缺陷信号称为单个缺陷。国家技术监督局1991-12-13批准1992-05-01实施
3.2.5分散缺陷
GB/T1331591
在边长50mm的立方体内,数量少于5个,当量吉径不小于2mm的缺陷信号,称为分散缺陷。3.2.6密集缺陷
在边长50mm立方体内,数量不少于5个,当量直径不小于mm的缺陷信号,称为密集缺陷。3.2.7游动信号缺陷
探头在被探部位移动时,缺陷借号前沿位置的移动距离相当于25mm或25mm以上工件厚度的缺陷,称为游动借号缺陷。
3.2.8线性缺陷
探头在被探部位移动时,缺陷指示长度不小于50mm,当量直径不小于$2mm的缺陷信号,称为线性缺陷,
3.3其他符号及术语
其他符号及术语,按[B3111的规定。4一般要求
4.1仪器、探头
4.1.1应采而A型脉冲反射式超声波探伤仪。其性能须符合ZBY230的要求。4.1.2原则[:采用单晶片直探头,探头工作频率为2~2.5MHz,操头直径按表2规定选择。必要时可变换题率及探头型式进行辅助探伤。探头性能的测试方法应符合ZBY231的要求。表2
探测部位尺寸
实心乳辊(D))
4.2轧锯
≥120~200
空心轧辑(R一)
4.2.1轧辑操伤表面加工粗糙度R.应不大于6.3μm;探份表面不应有影响探伤的划及污物。妨碍超声被探伤的机械加工应在探伤后进行。4.2.2轧辊衰减系数α应不大于0.004dB/mm。当轧辑穿透性不良时,应重新热处理后再作探伤。衰减系数α应在被检轧辑辊身无缺陷信号部位圆周面上测得,其计算方法如式(1)、式(2)所示:实心轧辑辊
空心轧崛
(B) - B) — 6
(B, - B.) - 6 - 10 1g 会
2(R—m)
4.2.3轧辊应放置在能自由转动的支架上进行操伤,以保证对轧辑整体进行扫描。4.3探人员
轧辑探伤应由经考核取得符合GB9445规定的超声探伤资格证书者担任,5探伤方法
5.1采用直接接触法探伤。
\(2)
5.2采用机油作为声耦合剂
GB/T13315—91
5.3以径向探测为主,对轮辊进行100%扫描,如图1所示。实心乳辑
空心轧辑
5.4探头扫查速度应不大于150mm/s,相邻两次扫查之间至少应有15%重叠。6探伤灵敏度
6.1操伤灵敏度按AVG法,最大探测深度处2mm平底孔波高等于20%满屏高为探伤灵度6.2探伤灵敏度调整
6.2.1将探头置于轧辑完好部位,调整第一次底波反射(B1)至荧光屏时间基线的4/5处。6.2.2调整仪器增益,使第一饮底波反射(B,)为满屏高度的20%作为基准高度。6.2.3根据被探部位的尺寸,按下列方法之一求取灵敏度增量,提高仪器增益作为探伤灵敏度。。从图2或图3中查出灵敏度增量:h、按式(3)、式(4)求得灵敏度增量。实心程= 201us会
A(R, —r)
空心轧据
△ = 20 lg
式中^取2MHz与2.5MHz的平均值。R
100 200.3004005008007008008001000直轻,
图2实心轧灵度增量
6.3探伤灵敏度的重新调整
GB/T 13315—91
020~28mm
内孔直控中10mm
-内孔直径=120mm
一内及直径10心m
一内孔直径481m
内孔直450mm
300 400 500600:200800900100010#20斤
轧辑外径mm
图3空心轧辊灵敏度增量
6. 3. 1在同一轧辊不同部位探伤时,应接 6. 2 条重新调整操伤灵敏度。6.3.2当更换探头,探头连线或电源时,应按6.2条重新调整探伤灵敏度。6.3.3探伤完毕,应按 6.2条重新校核探伤灵敏度,以验证探伤结果的正确性7缺陷的测定
7.1单个缺陷的测定
7.1.1对小于探头直径的单个缺陷,按AVG法确定缺陷的当量直径。7.1.2对大于探头直径的单个缺陷,按AVG法确定缺陷的最大当量直径,同时应按6dB法测定缺陷边界尺寸,并根据缺陷位置进行儿何修正。7.2密集缺陷的测定
密集缺陷按AVG法测定缺荫的最大当基直径,同时按6dB法测定其边界尺寸,并根据缺陷位置进行儿何修正。
7.3线性缺陷的测定
线性缺陷按AVG法测定缺陷的最大当量直径,并按6dB法测定缺陷指示长度。7.4游动信号缺陷的测定
游动信号缺陷按AVG法测定缺陷的最大当量直径,同时按6dB法测定缺陷指示长度,并计算缺陷在工件中的游动范围,
75缺降当量直径的测定
缺陷当量直径的测定方法可按附录B(参考件)的规定进行8轧辗区域的划分
按轧辊各个部位的功能分为 1,[I,II 和 [四个区域。各区域的示意位置见图 4。图中:I——表面区,
一中间区:
—中心区,
(a)实心轧
CB/T13315—91
图生轧辗区城示意图
(b)空心轧辑
I—辗非传动区,当两端均为传动端或辊颈需表面辫火时,则属I区。S
当 D≤250,取 0.2 D
1当 D250,取0. 15 D
S,取0.1 h
9探伤记录与报告
9.1探伤记录
9.1.1应对存在的缺陷做详细记录,记录可采用文字说明,也可采用图形与数字、符号来表明缺陷的性质、大小和位置。如用图形、数字、符号记录时,可参照附录C(参考件)规定进行。9.1.2对轧辊「区内的缺陷均应在探伤记录中记录。9.1.3除1区外,其他区域存在的单个小于mm当量直径缺陷可不做记录。9.2探伤报告
探伤报告至少应包括以下内容:工件名称、生产编号、规格、材质、热处理状态、探伤表面粗度;使用仪器型号、探头规格及型号、工作频率,灵敏度、耦合剂等,b.
轧辗简图及缺陷分布位置、缺陷当量值,必要时应附以探伤波型照片;探伤结论:根据供需双方参照附录A(补充件)共同确定的超声波操伤质量级别,对所检查的轧d
超声波探伤质量做出结论;
探伤日期。
GB/T13315—91
附录A
探伤结果分级
(补充件)
A1轧辑经超声波探伤检查,其质量等级分为A级和B级。A2不充许有裂纹、白点,缩孔或缩警残余等缺陷。A3不允许有线性缺陷和游动信号缺陷。A4实心轧据不允许有大于其直径12%的中心草状波信号区。注:中心草状波信号区是指在探伤扫描灵敏度下,中心出现卓状波《必要时用较低频率探头探测核对),按AVG法调节仪器至该位置2mm当盘波高为20%满屏商,此时中心反射的草状波低于20%满再高的区域,A5实心轧辑按图4(a)所示分区,各区在各质量级别中所规定的条件见表A1。表AI
区城辊身直径
质量级别
在规定的
灵敏度下,本允
许有缺陷波
充许有不
大于mm当
量的单个或分
散缺陷
允许有不
大于 4 mm 当
量的单个或分
散缺陷
在规定的
灵敏度下,不允
许有缺陷被
250~600
充许有
-4mm尚量的
单个缺陷,在辊
身部位,此种缺
陷总数不得多
充许有蛇
~5 mm当量的
单个缺陷,在辊
身位~ 5
Em当蛋的缺陷
总数不得多于
A6空心轧辊按图4(b)所示分区,各区在各质量级别中所规定的条件见表A2。充许有
~6 mm当量的
单个缺陷,其中
~m当量
的缺陷总数不
得多于5个。
充许有
~3 mm 当童的
分散缺陷和密
集缺陷,其中密
集缺陷区不得
多于 3 处,每个
密巢区的面积
不得大于9
cm2,各密集区
间距应不小于
区舰身直径
质量级别
定的灵敏
度下,不充
许有缺陷
TT、IF
GB/T 13315-91
有不大于
#3 mm 当
量的单个
或分散缺
有不大于
4mm当
虽的单个
或分散缺bzxz.net
有不太于
$2 mm当
量的单个
或分散缺
定的灵敏
度下,不允
许有缺陷
有蛇~4
mm当的
单个缺陷,
在辊身部
位,此种缺
陷总数不
得多于10
有 蛇~ 5
mm当量的
单个缺陷,
有不大于
盘的单个
有不大于
垦的单个
在辊身部
位4~5
mm当量的
缺陷总数
不得多于
有~6
mm当量的
单个缺陷,
其中~6
mm当量的
缺陷总数
不得多于5
mm当量的
分散缺陷
和密集缺
陷,其中
集缺陷区
不得多于3
处,每个密
巢区的面
积不得大
于 g cm2、
各密集区
间距应不
小于150
A7轧辑探伤检查所要求的质量级别、协商检查的项目和条件,由供需双方商定,在订货合同和设计图纸上说明。
附录B
缺陷当量的测定与换算
(参考件)
B1缺陷当量的测定与换算方法
B1.1将所检部位B,调整至荧光屏时间扫描线满屏10格处。B1.2按标准正文第6章规定调整探伤灵敏度。B1.3找出缺陷最大反射信号,记下缺陷信号前沿在时间扫描线的位置(格数)。B1.4调节仪器衰减器,使缺陷波降至20%满屏高度,并读出此时仪器的衰减量(dB值)。B1.5根据缺陷在时间扫描线的位置及仪器的衰减量(dB值),查图 B1即得该缺陷的当量直径。B2应用举例
CB/T 13315---91
图B1缺陷当量换算图
例1:按B1方法调整仪器,如发现某-缺陷信号在4格,仅器分贝读数为16dB,查图B1,得出该缺陷当量直径为 。
例2:按 B1方法调整仪器,如发现某一缺陷信号在 5.5格,仪器分贝读数为 36dB.查图 B1,得出该缺陷当量直径为 mm+2.0 dB
附录C
缺陷记录方法
(参考件)
当采用符号与数字来记录缺陷时,为使记录能为双方所确认,推荐下述的记录方法。C1缺陷的记录
缺陷采用三段记录形式
G×× / ×X-××
第三段
第二段
-第一段
C1. 1 第一段是记录缺陷在轴向削面上投影位置。用 D, 表示缺陷所在轴段(以打印端的轴段为 D,);用GB/T 13315- 91
数字表示缺陷与该轴段基准面(近打印端方向的端面)的距离(mm)。游动信号则上小括号并以分子表示距离,分母表示深度。
C1.2第二段是记录缺陷在径向剖面上投影的位置。以G;表示 4个等分圆周的基准点,顺时针方向排列(其中G与“打印位置”方向相同),用分数表示缺陷位置,表中分子表示距离基准点周向距离(mm),分母表示缺陷径向深度。游动信号则加上小括号,小括号的下角表示对应的轴向距离。C1.3第三段是记录缺陷大小及性质。C1.3.1当量缺陷以当量值表示,例如4。C1.3.2线性缺陷以当量值和长度(mm)表示,例如$4×50。C1.3.3大于探头晶片直径的缺陷以方括号内的面积(cm*)表示,例如[20×30]。C1.3.4密集缺陷用当量大小及大括号内的面积(cm\)表示,例如4{3×4)。当缺陷当量不大于$2 mm时,缺陷当量符号可以省略。C2记录示例
参看图C1。
打印位置减镶槽位置
打印端面
例1:缺陷A记为:D,50-G,120/40-4图C1
表示缺陷A在第一轴段,轴向距基准面 50 mm,周向距 Gz120 mm,径向深度 40·mm,缺陷大小为4 mm当量直径
例 2:缺陷B记为:D,200-G,100/50-$6×50表示缺陷 B 在第二轴段,轴向距基准面 200 mm,周向距 G,100 mtm,径向深度 50 mm,缺陷为mm当量直径,长50mm的线性缺陷。例3:缺陷C记为:D,(140/70~200/30)-G(80/40~160/30)200表示缺陷为游动信号C在第二轴段,轴向距基准面140mm,径向深度70mm,游动到轴向距基准面200mm,径向深度30mm.在轴向距基准面20Dmm处该缺陷从距G,80mm,径向深40mm游动到距G,160mm,径向深度为30mm。
例 4;D;150-G,120/40-[20×30]表示缺陷在第一轴段,轴向距基准面150mm,周向距G,120mm,径向深度40mm,为大于探头晶片直径的缺陷,其尺寸为20×30cm2。例5;D,180-G,160/50-$33X4)
GB/T13315—91
表示该缺陷为$3mm密集缺陷,缺陷轴向位置在第2轴段,距离基准面180mm,周向距G,160.mm,径向深度50切m,缺陷面积为3×4cm2。附加说明:
本标准由中华人民共和国治金工业部提出。本标准由治金工业部北京治金设备研究所归口。本标准由衡阳有色冶金机概总厂负责起草。本标准主要起草人文青、叶剑勇。本标准自实施之日起,原冶金工业部部标准YB3209—82即行废止。本标准委托冶金工业部北京治金设备研究所负责解释。
小提示:此标准内容仅展示完整标准里的部分截取内容,若需要完整标准请到上方自行免费下载完整标准文档。
锻钢冷轧工作辊超声波探伤方法Method of ultrasonic inspection forforged steel cold rolling working rells1 主题内容与适用范围
本标准规定了锻钢冷轧工作辊(以下简称轧辊)超声波探伤方法GB/T 13315—91
本标准适用直径大于等于 80 mm,供金属板、带、箱材冷轧用锻钢工作辑的超声波检测。2引用标准
GB9445无损检测人员技术资格鉴定通则JB3111无损检测名词术语
ZBY230A型脉冲反射式超声探伤仪通用技术条件ZBY231.超声探伤用操头性能测试方法3符号、术语
3.1符号
符号及其意义见表1。
3.2术语
轧辊成品辊身直径
探测部位直径
探测部位半径
轧辊内扎半径
灵敏度增量
3. 2. 1AVG(DGS)法
第一改底波反射信号
第一次底被反射信号
当基平底孔
癌减系数(dB/mm)
在一定条件下,根据超声场声压变化规律,利用反射体声压、尺寸利反射体离探头距离之间的定量关系来对工件内的缺陷进行定量评价的方法,称作AVG法,亦可称DGS法。3. 2. 26 dB法
最大回波高度降低一半的测量方法。3.2.3基准高度
将荧光屏某-高度定为基准,该高度即为基准高度(通常用荧光斥满尿高度的百分数来表示)。3.2. 4单个缺陷
间距大丁5mm,当量直径不小丁蛇㎡m的缺陷信号称为单个缺陷。国家技术监督局1991-12-13批准1992-05-01实施
3.2.5分散缺陷
GB/T1331591
在边长50mm的立方体内,数量少于5个,当量吉径不小于2mm的缺陷信号,称为分散缺陷。3.2.6密集缺陷
在边长50mm立方体内,数量不少于5个,当量直径不小于mm的缺陷信号,称为密集缺陷。3.2.7游动信号缺陷
探头在被探部位移动时,缺陷借号前沿位置的移动距离相当于25mm或25mm以上工件厚度的缺陷,称为游动借号缺陷。
3.2.8线性缺陷
探头在被探部位移动时,缺陷指示长度不小于50mm,当量直径不小于$2mm的缺陷信号,称为线性缺陷,
3.3其他符号及术语
其他符号及术语,按[B3111的规定。4一般要求
4.1仪器、探头
4.1.1应采而A型脉冲反射式超声波探伤仪。其性能须符合ZBY230的要求。4.1.2原则[:采用单晶片直探头,探头工作频率为2~2.5MHz,操头直径按表2规定选择。必要时可变换题率及探头型式进行辅助探伤。探头性能的测试方法应符合ZBY231的要求。表2
探测部位尺寸
实心乳辊(D))
4.2轧锯
≥120~200
空心轧辑(R一)
4.2.1轧辑操伤表面加工粗糙度R.应不大于6.3μm;探份表面不应有影响探伤的划及污物。妨碍超声被探伤的机械加工应在探伤后进行。4.2.2轧辊衰减系数α应不大于0.004dB/mm。当轧辑穿透性不良时,应重新热处理后再作探伤。衰减系数α应在被检轧辑辊身无缺陷信号部位圆周面上测得,其计算方法如式(1)、式(2)所示:实心轧辑辊
空心轧崛
(B) - B) — 6
(B, - B.) - 6 - 10 1g 会
2(R—m)
4.2.3轧辊应放置在能自由转动的支架上进行操伤,以保证对轧辑整体进行扫描。4.3探人员
轧辑探伤应由经考核取得符合GB9445规定的超声探伤资格证书者担任,5探伤方法
5.1采用直接接触法探伤。
\(2)
5.2采用机油作为声耦合剂
GB/T13315—91
5.3以径向探测为主,对轮辊进行100%扫描,如图1所示。实心乳辑
空心轧辑
5.4探头扫查速度应不大于150mm/s,相邻两次扫查之间至少应有15%重叠。6探伤灵敏度
6.1操伤灵敏度按AVG法,最大探测深度处2mm平底孔波高等于20%满屏高为探伤灵度6.2探伤灵敏度调整
6.2.1将探头置于轧辑完好部位,调整第一次底波反射(B1)至荧光屏时间基线的4/5处。6.2.2调整仪器增益,使第一饮底波反射(B,)为满屏高度的20%作为基准高度。6.2.3根据被探部位的尺寸,按下列方法之一求取灵敏度增量,提高仪器增益作为探伤灵敏度。。从图2或图3中查出灵敏度增量:h、按式(3)、式(4)求得灵敏度增量。实心程= 201us会
A(R, —r)
空心轧据
△ = 20 lg
式中^取2MHz与2.5MHz的平均值。R
100 200.3004005008007008008001000直轻,
图2实心轧灵度增量
6.3探伤灵敏度的重新调整
GB/T 13315—91
020~28mm
内孔直控中10mm
-内孔直径=120mm
一内及直径10心m
一内孔直径481m
内孔直450mm
300 400 500600:200800900100010#20斤
轧辑外径mm
图3空心轧辊灵敏度增量
6. 3. 1在同一轧辊不同部位探伤时,应接 6. 2 条重新调整操伤灵敏度。6.3.2当更换探头,探头连线或电源时,应按6.2条重新调整探伤灵敏度。6.3.3探伤完毕,应按 6.2条重新校核探伤灵敏度,以验证探伤结果的正确性7缺陷的测定
7.1单个缺陷的测定
7.1.1对小于探头直径的单个缺陷,按AVG法确定缺陷的当量直径。7.1.2对大于探头直径的单个缺陷,按AVG法确定缺陷的最大当量直径,同时应按6dB法测定缺陷边界尺寸,并根据缺陷位置进行儿何修正。7.2密集缺陷的测定
密集缺陷按AVG法测定缺荫的最大当基直径,同时按6dB法测定其边界尺寸,并根据缺陷位置进行儿何修正。
7.3线性缺陷的测定
线性缺陷按AVG法测定缺陷的最大当量直径,并按6dB法测定缺陷指示长度。7.4游动信号缺陷的测定
游动信号缺陷按AVG法测定缺陷的最大当量直径,同时按6dB法测定缺陷指示长度,并计算缺陷在工件中的游动范围,
75缺降当量直径的测定
缺陷当量直径的测定方法可按附录B(参考件)的规定进行8轧辗区域的划分
按轧辊各个部位的功能分为 1,[I,II 和 [四个区域。各区域的示意位置见图 4。图中:I——表面区,
一中间区:
—中心区,
(a)实心轧
CB/T13315—91
图生轧辗区城示意图
(b)空心轧辑
I—辗非传动区,当两端均为传动端或辊颈需表面辫火时,则属I区。S
当 D≤250,取 0.2 D
1当 D250,取0. 15 D
S,取0.1 h
9探伤记录与报告
9.1探伤记录
9.1.1应对存在的缺陷做详细记录,记录可采用文字说明,也可采用图形与数字、符号来表明缺陷的性质、大小和位置。如用图形、数字、符号记录时,可参照附录C(参考件)规定进行。9.1.2对轧辊「区内的缺陷均应在探伤记录中记录。9.1.3除1区外,其他区域存在的单个小于mm当量直径缺陷可不做记录。9.2探伤报告
探伤报告至少应包括以下内容:工件名称、生产编号、规格、材质、热处理状态、探伤表面粗度;使用仪器型号、探头规格及型号、工作频率,灵敏度、耦合剂等,b.
轧辗简图及缺陷分布位置、缺陷当量值,必要时应附以探伤波型照片;探伤结论:根据供需双方参照附录A(补充件)共同确定的超声波操伤质量级别,对所检查的轧d
超声波探伤质量做出结论;
探伤日期。
GB/T13315—91
附录A
探伤结果分级
(补充件)
A1轧辑经超声波探伤检查,其质量等级分为A级和B级。A2不充许有裂纹、白点,缩孔或缩警残余等缺陷。A3不允许有线性缺陷和游动信号缺陷。A4实心轧据不允许有大于其直径12%的中心草状波信号区。注:中心草状波信号区是指在探伤扫描灵敏度下,中心出现卓状波《必要时用较低频率探头探测核对),按AVG法调节仪器至该位置2mm当盘波高为20%满屏商,此时中心反射的草状波低于20%满再高的区域,A5实心轧辑按图4(a)所示分区,各区在各质量级别中所规定的条件见表A1。表AI
区城辊身直径
质量级别
在规定的
灵敏度下,本允
许有缺陷波
充许有不
大于mm当
量的单个或分
散缺陷
允许有不
大于 4 mm 当
量的单个或分
散缺陷
在规定的
灵敏度下,不允
许有缺陷被
250~600
充许有
-4mm尚量的
单个缺陷,在辊
身部位,此种缺
陷总数不得多
充许有蛇
~5 mm当量的
单个缺陷,在辊
身位~ 5
Em当蛋的缺陷
总数不得多于
A6空心轧辊按图4(b)所示分区,各区在各质量级别中所规定的条件见表A2。充许有
~6 mm当量的
单个缺陷,其中
~m当量
的缺陷总数不
得多于5个。
充许有
~3 mm 当童的
分散缺陷和密
集缺陷,其中密
集缺陷区不得
多于 3 处,每个
密巢区的面积
不得大于9
cm2,各密集区
间距应不小于
区舰身直径
质量级别
定的灵敏
度下,不充
许有缺陷
TT、IF
GB/T 13315-91
有不大于
#3 mm 当
量的单个
或分散缺
有不大于
4mm当
虽的单个
或分散缺bzxz.net
有不太于
$2 mm当
量的单个
或分散缺
定的灵敏
度下,不允
许有缺陷
有蛇~4
mm当的
单个缺陷,
在辊身部
位,此种缺
陷总数不
得多于10
有 蛇~ 5
mm当量的
单个缺陷,
有不大于
盘的单个
有不大于
垦的单个
在辊身部
位4~5
mm当量的
缺陷总数
不得多于
有~6
mm当量的
单个缺陷,
其中~6
mm当量的
缺陷总数
不得多于5
mm当量的
分散缺陷
和密集缺
陷,其中
集缺陷区
不得多于3
处,每个密
巢区的面
积不得大
于 g cm2、
各密集区
间距应不
小于150
A7轧辑探伤检查所要求的质量级别、协商检查的项目和条件,由供需双方商定,在订货合同和设计图纸上说明。
附录B
缺陷当量的测定与换算
(参考件)
B1缺陷当量的测定与换算方法
B1.1将所检部位B,调整至荧光屏时间扫描线满屏10格处。B1.2按标准正文第6章规定调整探伤灵敏度。B1.3找出缺陷最大反射信号,记下缺陷信号前沿在时间扫描线的位置(格数)。B1.4调节仪器衰减器,使缺陷波降至20%满屏高度,并读出此时仪器的衰减量(dB值)。B1.5根据缺陷在时间扫描线的位置及仪器的衰减量(dB值),查图 B1即得该缺陷的当量直径。B2应用举例
CB/T 13315---91
图B1缺陷当量换算图
例1:按B1方法调整仪器,如发现某-缺陷信号在4格,仅器分贝读数为16dB,查图B1,得出该缺陷当量直径为 。
例2:按 B1方法调整仪器,如发现某一缺陷信号在 5.5格,仪器分贝读数为 36dB.查图 B1,得出该缺陷当量直径为 mm+2.0 dB
附录C
缺陷记录方法
(参考件)
当采用符号与数字来记录缺陷时,为使记录能为双方所确认,推荐下述的记录方法。C1缺陷的记录
缺陷采用三段记录形式
G×× / ×X-××
第三段
第二段
-第一段
C1. 1 第一段是记录缺陷在轴向削面上投影位置。用 D, 表示缺陷所在轴段(以打印端的轴段为 D,);用GB/T 13315- 91
数字表示缺陷与该轴段基准面(近打印端方向的端面)的距离(mm)。游动信号则上小括号并以分子表示距离,分母表示深度。
C1.2第二段是记录缺陷在径向剖面上投影的位置。以G;表示 4个等分圆周的基准点,顺时针方向排列(其中G与“打印位置”方向相同),用分数表示缺陷位置,表中分子表示距离基准点周向距离(mm),分母表示缺陷径向深度。游动信号则加上小括号,小括号的下角表示对应的轴向距离。C1.3第三段是记录缺陷大小及性质。C1.3.1当量缺陷以当量值表示,例如4。C1.3.2线性缺陷以当量值和长度(mm)表示,例如$4×50。C1.3.3大于探头晶片直径的缺陷以方括号内的面积(cm*)表示,例如[20×30]。C1.3.4密集缺陷用当量大小及大括号内的面积(cm\)表示,例如4{3×4)。当缺陷当量不大于$2 mm时,缺陷当量符号可以省略。C2记录示例
参看图C1。
打印位置减镶槽位置
打印端面
例1:缺陷A记为:D,50-G,120/40-4图C1
表示缺陷A在第一轴段,轴向距基准面 50 mm,周向距 Gz120 mm,径向深度 40·mm,缺陷大小为4 mm当量直径
例 2:缺陷B记为:D,200-G,100/50-$6×50表示缺陷 B 在第二轴段,轴向距基准面 200 mm,周向距 G,100 mtm,径向深度 50 mm,缺陷为mm当量直径,长50mm的线性缺陷。例3:缺陷C记为:D,(140/70~200/30)-G(80/40~160/30)200表示缺陷为游动信号C在第二轴段,轴向距基准面140mm,径向深度70mm,游动到轴向距基准面200mm,径向深度30mm.在轴向距基准面20Dmm处该缺陷从距G,80mm,径向深40mm游动到距G,160mm,径向深度为30mm。
例 4;D;150-G,120/40-[20×30]表示缺陷在第一轴段,轴向距基准面150mm,周向距G,120mm,径向深度40mm,为大于探头晶片直径的缺陷,其尺寸为20×30cm2。例5;D,180-G,160/50-$33X4)
GB/T13315—91
表示该缺陷为$3mm密集缺陷,缺陷轴向位置在第2轴段,距离基准面180mm,周向距G,160.mm,径向深度50切m,缺陷面积为3×4cm2。附加说明:
本标准由中华人民共和国治金工业部提出。本标准由治金工业部北京治金设备研究所归口。本标准由衡阳有色冶金机概总厂负责起草。本标准主要起草人文青、叶剑勇。本标准自实施之日起,原冶金工业部部标准YB3209—82即行废止。本标准委托冶金工业部北京治金设备研究所负责解释。
小提示:此标准内容仅展示完整标准里的部分截取内容,若需要完整标准请到上方自行免费下载完整标准文档。

标准图片预览:
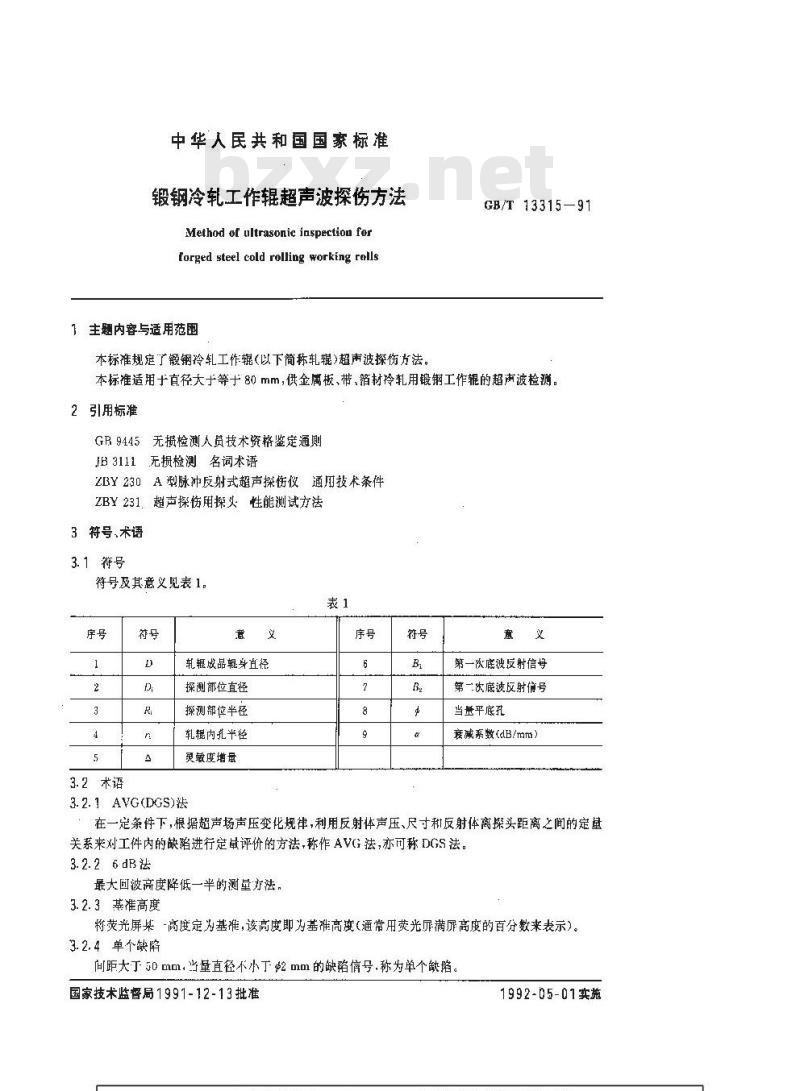
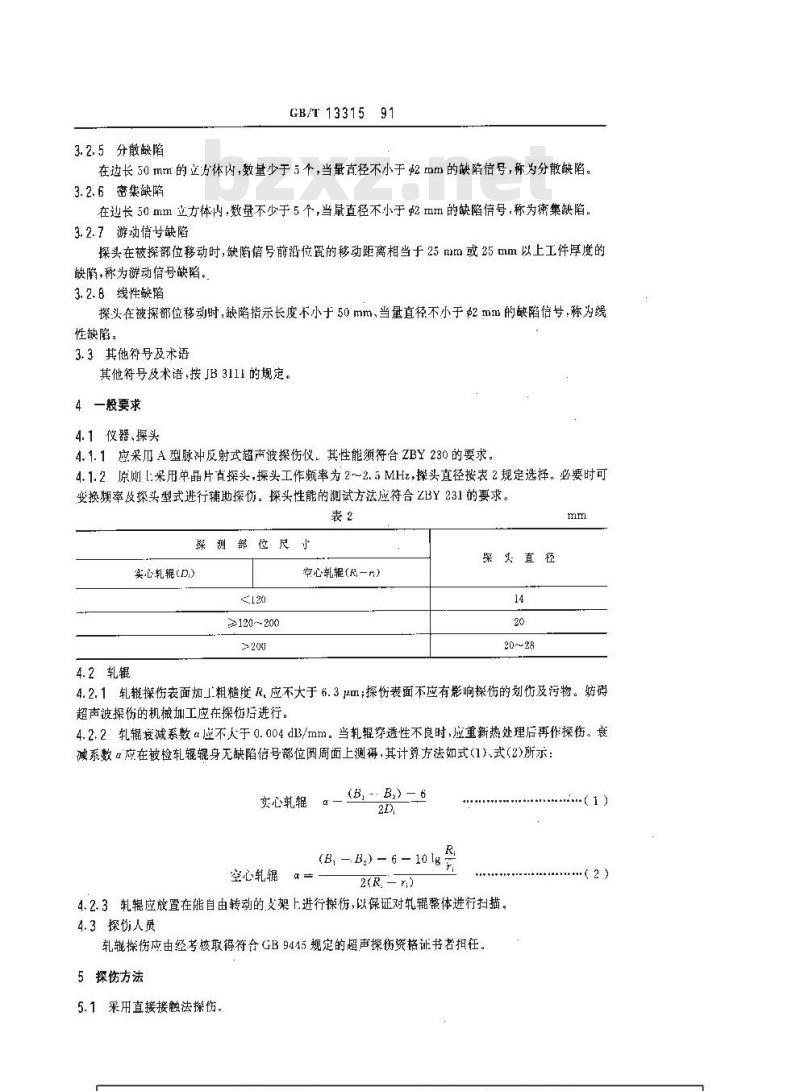
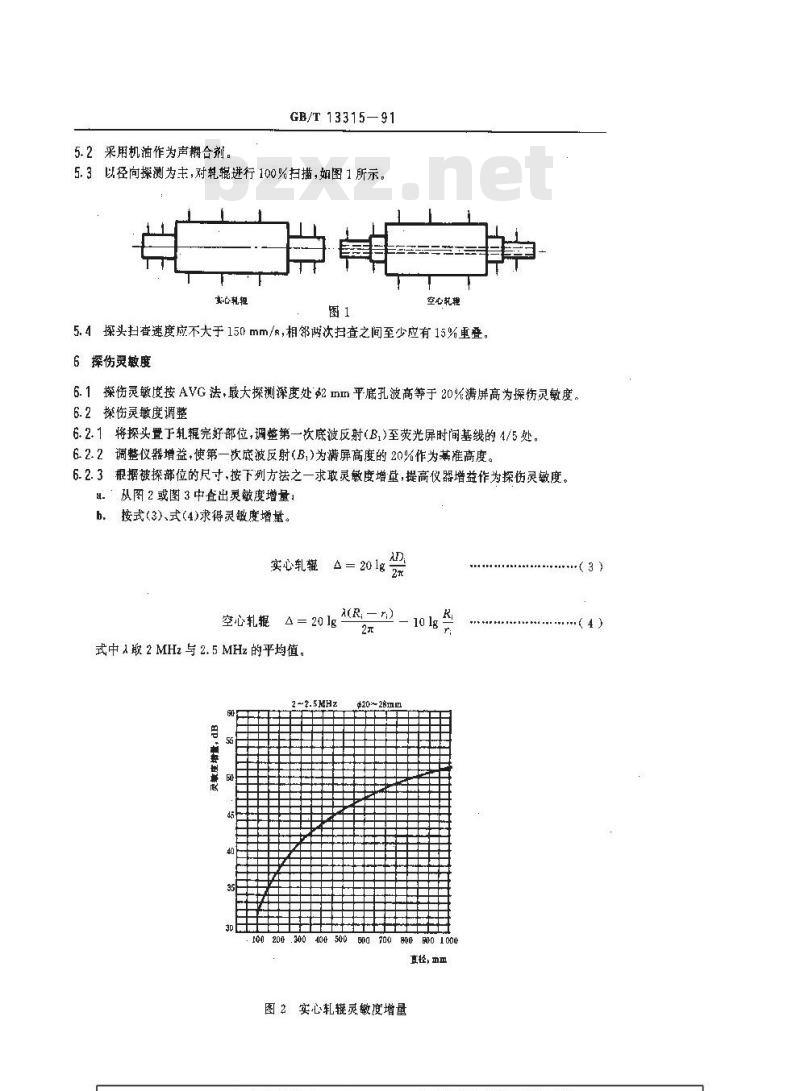
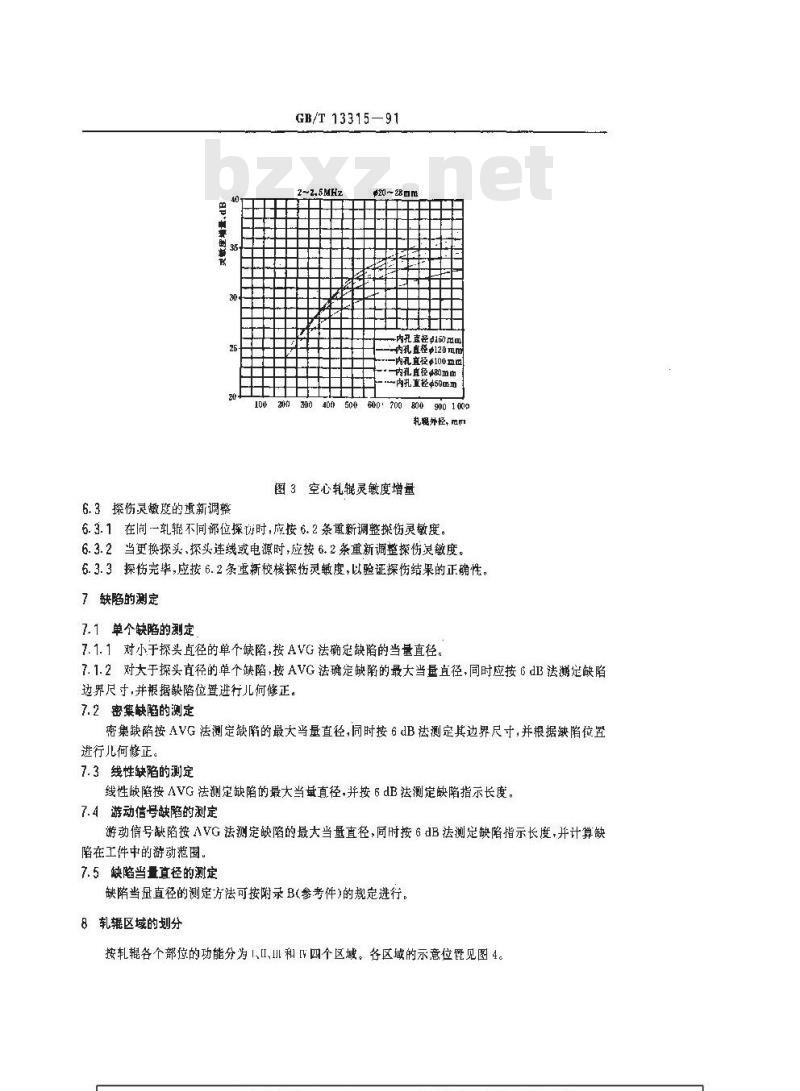
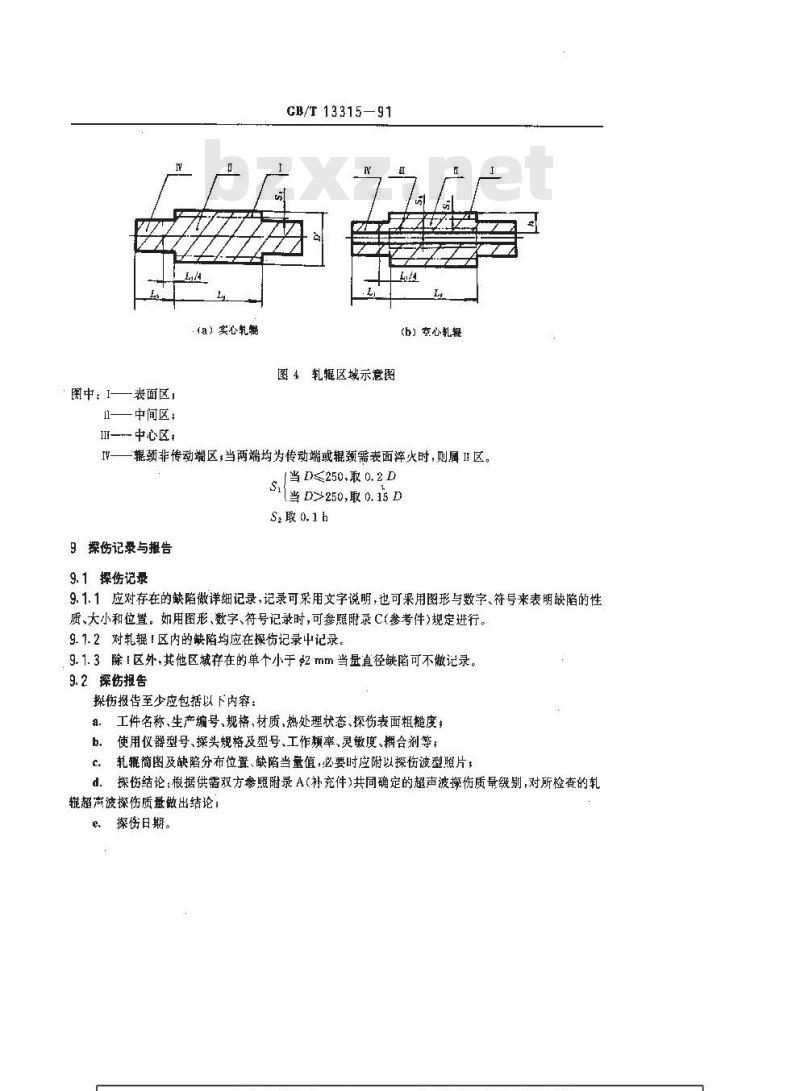
- 其它标准
- 热门标准
- 国家标准(GB)
- GB/T39318-2020 军民通用资源 标识代码映射要求
- GB30441.1-2013 信息技术通用多八位编码字符集满文名义字符与变形显现字符16点阵字型第1部分:铅印白体
- GB4623-1994 环形预应力混凝土电杆
- GB/T26949.10-2011 工业车辆 稳定性验证 第10部分:在由动力装置侧移载荷条件下堆垛作业的附加稳定性试验
- GB/T32070-2022 土方机械 物体监测系统及其可视辅助装置 性能要求和试验
- GB/T22395-2022 锅炉钢结构设计规范
- GB/T14993-1994 转动部件用高温合金热轧棒材
- GB/T5286-2001 螺栓、螺钉和螺母用平垫圈 总方案
- GB/T15738-2008 导电和抗静电纤维增强塑料电阻率试验方法
- GB/T24681-2009 植物保护机械 喷雾飘移的田间测量方法
- GB/T40175.3—2021 纺织品生物化学分析方法第3部分:有机磷类农药(酶联免疫法)
- GB/T14652.1-2001 小艇耐火燃油软管
- GB29380—2012 胺菊酯原药
- GB17013-1997 包虫病诊断标准及处理原则
- GB/T775.2-2003 绝缘子试验方法 第2部分: 电气试验方法
- 行业新闻
请牢记:“bzxz.net”即是“标准下载”四个汉字汉语拼音首字母与国际顶级域名“.net”的组合。 ©2009 标准下载网 www.bzxz.net 本站邮件:bzxznet@163.com
网站备案号:湘ICP备2023016450号-1
网站备案号:湘ICP备2023016450号-1