- 您的位置:
- 标准下载网 >>
- 标准分类 >>
- 其他行业标准 >>
- GJB 3054-1997 飞机液压管路系统设计、安装要求
标准号:
GJB 3054-1997
标准名称:
飞机液压管路系统设计、安装要求
标准类别:
其他行业标准
标准状态:
现行出版语种:
简体中文下载格式:
.rar .pdf下载大小:

部分标准内容:
中华人民共和国国家军用标准
FL1650
GJB3054-97
飞机液压管路系统
设计、安装要求
Hydraulic tubing systems,aircraftdesign,installation requirements for1997-11-05发布
1998-05-01实施
国防科学技术工业委员会批准
1范围
1.1主题内容
1.2适用范围
2引用文件
3要求
导管、接头及其连接型式
3.2导管规格的确定
管路布暨
3.4支承、卡箍和电搭接
导管的尺寸精度
导管应力·
允许的导管缺陷和修理…
保护层·
挠性连接
污染控制
导管的标记
导管模型和鉴定
3.13检验、测试和试验程序,
4质量保证规定
4.1检验责任
4.2检验方法和检验规则
4.3管路系统和管路件的清洗
附录A应用指南(参考件)
1范围
中华人民共和国国家军用标准
飞机液压管路系统设计、安装要求Hydraulic tubing systems,aircraft,design,installation requirements for1.1主题内容
GJB3054-97
本标准规定了飞机I、IⅡ型液压系统和A、B型气动系统的管路系统设计和安装的通用技术要求。
1.2适用范围
本标准适用于飞机I、Ⅱ型液压系统和飞机A、B型气动系统。改进改型飞机液压系统和气动系统亦可参照使用。
2引用文件
GBn221-84
GJB380-87
GJB420A-96
GJB456-88
GJB638A-97
GJB1194-91
GJB1396-92
GJB2296-95
GJB3058-97
GJB3059-97
HB32583
HB 32683
HB 32783
HB4-1-83
HB 4383
HB 4 52 83
HB 4 55 95
HB 4 6983
HB 4 133 83
铝及铝合金薄壁管
飞机液压系统污染测试
飞机液压系统固体污染度分级
飞机液压系统温度型别和压力级别飞机I、Ⅱ型液压系统设计、安装要求飞机气动系统通用规范
飞机液压、应急气动系统试验要求和方法航空用不锈无缝钢管
飞机I、Ⅱ型液压系统污染度验收水平和控制水平飞机I、Ⅱ型液压系统重要附件污染度验收水平带垫的夹紧卡箍
单螺栓侧面固定带垫的夹紧卡箍双螺栓侧面固定带垫的夹紧卡箍扩口管路连接件技术条件
管接头的螺纹部分
导管扩口
导管弯曲半径
管接头的堵盖
航空橡胶棉线编织软管技术条件国防科学技术工业委员会1997-11-05发布1998-05-01实施
HB 4 -142-83
HB5653~5655-81
HB 5663~579483
HB5876-85
HB 5931.8 -89
HB59666075-86
HB6129-87
HB6133-87
HB6442-90
HB/Z228-93
HB/Z 507778
SY1181-76
Q/SY11507-79
3要求
GJB3054-97
航空橡胶钢丝编织软管技术条件航空导管识别标志
卡套式无扩口导管连接件
飞机电搭接技术要求
飞机液压系统污染测试一用显微镜对比法测定工作液固体污染度挤压式无扩口导管连接件
飞机雷击防护要求及试验方法
液压软管、导管、接头组件的脉冲试验飞机液压导管及连接件弯曲疲劳试验挤压式无扩口导管连接工艺指南铝及铝合金化学氧化(磷酸铬酸法)工艺10号航空液压油
12号航空液压油
3.1导管、接头及其连接型式
3.1.1导管的选用原则
导管的选用应遵循以下的原则:a,导管选择应与其工作压力相适应,既有足够的强度又使系统重量最轻;b.导管应与系统的工作介质相容,在系统工作条件下具有良好的防腐蚀性能;C.导管应与接头的连接型式相适应,使导管组件具有良好的密封性、抗振性和耐疲劳性能。塑性较差的高强度薄壁导管应采用无扩口连接型式;d.导管应有良好的扩口、成形、预装工艺特性;e.导管应与其使用的环境相适应。高温区、高振动区、常拆卸及外露部位应采用不锈钢导管。
3.1.2导管的种类
根据系统的设计要求,可选用不锈钢管、钛合金管或铝管。主要选用材料的物理性能参见附录A2.1。
3.1.3接头的选用原则
接头的连接型式应与导管相匹配,接头型式的选择应遵循以下原则:a.接头材料应与导管材料、工作介质相容,有良好的防腐蚀性能;b.接头选择应与工作压力相适应,既有足够的强度又使系统重量最轻;c.接头选择应考虑加工工艺性;d.接头和导管的组件应具有良好的气密性、抗振性和耐疲劳的特性,以及有良好的预装工艺性、维修性和可靠性。
3.1.4接头种类
用于飞机液压系统的接头有多种型式。常用接头的结构形式及说明参见附录A2.2。2
3.2导管规格的确定
GJB3054-97
能量损失和工作压力是确定导管的合理尺寸和材料的主要依据。一般来说,前者是选定导管内径的依据,后者是选定导管材料和壁厚的依据,但同时还需考虑到导管的安装部位、重量、成本,以求得效率高、重量轻、安全可靠的综合效果。3.2.1导管管径的确定
3.2.1.1经验法则
确定系统管路内径的方法有多种,主要是根据管路中预期的流速、压降以及冲击压力进行计算,并反复进行修正。常用的经验法则有:流速极限法、压降分配法、和冲击压力极限法。其详细的计算方法参见附录A3.1。3.2.1.2压降仿真分析法
压降仿真分析法是一种确定系统管路参数的有效方法。压降仿真分析法是将液压系统的结构模型转换成描述系统的数学模型,在计算机上进行求解,确定不同条件下系统中任何处的压力、流量分布情况,确认系统管路设计的合理性。压降仿真分析法有较高的计算精度,易于选择不同的系统管路参数,便于实现管路参数优化设计。有稳态仿真计算和瞬态仿真计算程序。一般应按稳态程序确定管路参数,然后按瞬态程序进行检查。
3.2.1.3全性能最低设计温度
在设计管路系统时要考虑的主要问题之一是要满足在最低工作温度时所允许的压降。最低工作温度往往由飞机性能规范直接给出,或者由规定飞机在指定的低温环境中,接到报警信号以后的允许起飞准备时间间接给出。在后一种情况中,在决定为满足全性能飞行条件所必要的温度时,可以考虑各种使系统油液升温的方法。要综合地考虑所有可能的方法,力求获得加热设备、管路规格的最佳匹配,以使管路具有最小(或在规定范围内)重量和最低成本。3.2.1.3.1起落架收放系统管路
动力操纵的起落架,当系统温度高于一29C时,放下并锁住起落架最大允许时间为15s,收起并锁住起落架最大允许时间为10s,而且要求起落架必须在飞机达到收起起落架的限定速度的75%前收起并锁住。当温度稳定在55C到-29℃之间时,且收放起落架前不充许有系统升温时间时,放下并锁住起落架最大允许时间为30s,收起起落架并锁住起落架的最大允许时间为10s,也要求起落架必须在飞机达到收起起落架的限定速度的75%前收起并锁住。若特定型号的飞机对起落架收放时间及系统温度有特殊要求时,应在专用技术规范中规定。
管路系统参数应满足上述要求。3.2.1.3.2飞行控制系统管路
要保证在气流开始分离以后,在一55C时,驱动飞行控制系统所需增加的力应不大于21℃时所需力的150%,同时还应保证飞行中可能遇到的所有温度下能正常工作。在一55℃到一29℃之间,襟、副翼驱动系统管路的操纵时间应不超过额定操纵时间的150%。管路系统参数应满足上述要求。3.2.1.4吸油管路
3.2.1.4.1低温工作
CJB3054-97
从油箱到油泵的吸油管路设计,应使飞机在最大升限上以可能的最大流量工作时,油泵进口处的油液仍有足够的流量和压力。此时要求油液的温度不低于29℃。对于在上述飞行环境中油泵不工作的系统,可以适当地考虑一个比飞机升限较低的高度,但这一高度不应低于海拔3000m。
上述的有关吸油管路压降的要求不适用于飞机在地面环境温度为一55C的冷起动。吸油管路上不应安装油滤,如果特殊需要,则应保证飞机在任何飞行状态下不影响系统的工作,同时在油滤内要装上合适的旁通阀。3.2.1.4.2瞬态响应
正确地选定油泵的吸油管径,能保证在正常工作的条件下不产生气穴现象。油箱的增压压力值应同时满足稳态和瞬态的工作条件。稳态计算用于确定吸油管路的压降;瞬态计算则考虑了当系统的流量需求变化时,吸油管路内流体加速所需的压力值。瞬态计算公式参见A3.1.4。
3.2.1.5小尺寸导管
在液压系统中一般不采用外径小于6mm的导管,若采用小于6mm的导管则对它的安装、支承和保护必须给予特别注意,而且必须证明装用这类导管的附件能在规定的系统最低温度下正常工作。
3.2.2导管壁厚的确定
3.2.2.1确定壁厚的一般原则
导管壁厚确定应考虑以下因素:a.导管材料特性,如拉伸强度极限、拉伸屈服极限、材料纵向强度和横向强度的差异性、抗疲劳性能等;
b.经受的系统工作压力和安全系数;c.导管的管径;bZxz.net
d.导管的允许尺寸公差和允许缺陷;e.经受的环境条件如温度、振动、冲击等;f.任何材料和规格的导管,其最小壁厚一般不应小于0.5mm。导管壁厚必须经合理的试验来验证,至少应进行脉冲试验、弯曲疲劳试验和弯管组件的爆破试验。
3.2.2.2确定壁厚的方法
飞机液压管路设计中对导管壁厚进行计算时,通常采用薄壁或厚壁圆简的计算公式,并通过爆破压力的核算来最终确定。常用的计算方法参见附录A3.2。3.3管路布置
3.3.1线路确定
3.3.1.1载流管路敷设的一般原则应精心进行管路设计,以降低系统的复杂性,并减轻重量,使可能的损坏和泄漏减至最少。液压管路装置的设计应使其具有与飞机机体结构相当的工作寿命,并便手更换和维修。尽量4
GJB3054-97
减少弯管和分支,采用最直接的线路并与其他要求相协调。为使管路具有足够的强度,工作寿命长,安全可靠,设计时应遵循以下的基本原则:a。避免在两个刚性支承接头之间安装直导管。在必须安装这类直导管处,应在附件或刚性接头的安装方面采取措施,保证导管和接头不承受过大的安装应力,并要考虑使用中的热应力。若有必要,可将导管制成半环形,以保证安装时易于对准和承受振动;b.在两个允许有相对运动的接头之间不采用铝导管和直钢管;c.液压管路不要进入驾驶舱或座舱内,并要远离人员所处的位置。此外,液压管路必须远离排气管道、热总管、电气线路、无线电线路、氧气管道、各种设备和绝缘材料。在所有场合下,为防止导管泄漏引起火,液压管路都要位于上述各种装置之下。不应将液压管路与其他易燃流体管路汇集在一起,以免各种不同系统相互接错;d.所有系统的压力管路和易着火区内的回油管路,应使用不锈钢管或钛合金管;e.铝合金导管仅限用于易着火区以外的回油和吸油管路;f.管路安装应保证合适的支承间隔:g.导管和导管之间,导管和结构、运动部件之间,导管和其他系统之间应有合理的足够的间隙,以保证在最不利的制造公差,最严酷的环境条件,最严重变形条件下不产生相互接触和磨损。
3.3.1.2排油及通气管路
排油管应伸到飞机的下外表面,以免排出的油液或蒸汽吹回到飞机里,喷在排气管、热总管及其他火源上,或聚积在结构的凹陷处。不允许油液进到机翼前缘、检查窗口、机轮舱、排气口、进气口及其他火源处。应从外面将排油管周围盖住,以防止油液及蒸汽回流至舱内;还要加上一个斜端口以使气流通过时产生负压。在放油装置下不应安装任何附件。在飞行或地面作机动操作时,油箱通气口不应有油液损失,对于在飞行中通气口有可能向外少量漏油的系统,可将其引至一个容器中收集起来,在维修时放出。对伸出机外的排油、通气口应考虑设置网罩,以防异物进入而堵塞。3.3.1.3样机
导管安装用的全尺寸模型(即样机)是一种十分有效的协调工具。它可以用来确定管路最佳的走向、弯曲部位、连接型式以及最佳的支承部位。样机应尽量模拟周围的结构和相邻的设备,用以对是否有足够的安装操作空间、管路容差、可达性以及中心对准等情况进行验证。3.3.1.4温度
液压系统应有良好的冷起动性能,在最低地面环境温度(-55C)下能正常起动。但并不要求在这样的温度下达到全性能。如冷起动需要分支回路,应使回路回到油箱而不要直接回到液压泵,以免回路过短,不能散热而使系统升温,以致局部过热损坏油泵。管路布置中应尽量避免使导管穿越电气设备、热总管或其它热源区。如导管必须靠近某一超过系统型别规定的最高温度的局部热源,则应采取有效的隔热、局部冷却或其他保护措施。表1给出了液压系统一些常用非金属材料的温度上限。这里给出的是长时间工作的温度极限,其中有些材料能短时间地工作在更高的温度下而不致严重损坏。5
GJB3054-97
表1液压系统常用非金属材料长期工作的最高温度YH-10
液压油
3.3.1.5防火
液压油
液压油
120℃
氟橡胶
180℃
聚四氟乙
烯SFB-1
260℃
聚酰铵
(尼龙)
液压系统设计时应与其他一些系统综合考虑,使液压系统消除或隔离附近的可燃气体、热源、发动机排气管或电器设备等可能造成的火险。凡是安置在会引起泄油液自发着火或持续燃烧的热源、发火源附近的液压管路和液压附件,均须由防火墙、防火罩或防止油液着火的相应装置加以保护。
根据特定型号飞机的防火要求,如燃油系统或滑油系统(或两个系统)必须有切断阀,则应设暨液压泵供油(吸油)切断阀。若要设置这类阀,则不应位于防火墙或隔火板的装有发动机的一侧,但要尽可能靠近这些构件。阀相对发动机要有一定距离,以保证发动机从连接结构上脱离时阀的工作不受影响。此类阀的关闭和打开应能在驾驶舱内进行操纵。3.3.1.6防炮火
凡在设置双套液压系统之处,这些系统应尽量离得远些,以便最大程度地减少炮火或发动机着火对双套系统所引起的破坏作用。应尽可能将两套系统分开布置在机身、翼梁的相对两侧,或采取类似的隔开措施。对安全飞行必需的各系统应尽量做到相距450mm。3.3.1.7维护性
当系统出现导管或接头的损坏、泄漏等情况时,应能保证方便地对主要管路进行维护和修理。导管和接头的修理应尽量不需要拆下相邻的附件。3.3.1.7.1接头位置
所有可能需要拆卸的接头应该安装在易于接近的地方,以便在冷天戴着手套能进行拆装和检查。
附件上的管路
3.3.1.7.2
当一个液压附件与两个或两个以上的管路相连,有可能发生错接的情况时,应采取有效的防错措施。
3.3.1.7.3排油管路
从油泵、油箱或其他液压附件中引出的排油和通气管路,不允许和任何其他管路及飞机上任何其他系统相连,致使这些附件的油液被混合排出。3.3.1.7.4轻附件的安装
本身没有安装件的重量轻的附件可由其连接的导管来支承,但附件必须装得很牢固,而且不使所安装的导管产生破坏性振动或其它不利状态。这些附件也可用卡箍或类似的装置固定在结构上,但必须保证铭牌、流向箭头、各种标记或其他数据不被遮盖,而支承件也不影响附件的工作。如果一个卡箍不能支承附件,则在该附件两侧的导管上,距附件50mm的范围内都应有卡箍支承在结构上。
3.3.1.7.5排除混入的空气
GJB3054-97
凡是在混入的空气会影响系统正常工作的地方,应采取适当的措施,如安装排气阀,排出混入的空气。不采取松开导管螺母的方法来排出混入的空气。液压系统和液压设备的布局要尽可能使系统中游离的空气能自动流向液压油箱或其他不影响工作又便于排出的聚积处。3.3.1.7.6地面试验装置
每个液压系统应包括一套自封连接装置,供连接地面试验设备用。液压系统地面连接装置应这样设计:即在飞机上试验一个液压系统时,不必对飞机上其他系统增压。特别是只用一个液压试验设备试验飞机液压系统时,在试验设备和飞机系统之间不采用“Y\型连接。若机上的几套液压系统需同时工作,应用相同套数的地面独立液压源与飞机系统相连。各个液压系统应尽量集中设置地面试验连接座。该连接座上要有连接地面试验设备用的各种接头,供系统检查、系统清洗、液压油箱排气、液压油箱加油以及蓄压器充气之用。应采取措施防止水分、空气及其他污染物在加油和试验过程中通过地面连接装置进入系统。由隔板式半法兰接头和保护盖组成的成套自封接头,应安装在飞机上的适当部位,使在地面容易接近并便于连接地面试验设备。应急系统或辅助系统中使用的电动机驱动的液压泵不用于地面试验,除非电动机是按连续工作要求设计的。还须注意到以下情况:
a.地面试验装置上的吸油管路的管径尺寸应与其长度相适应;b.飞机上与地面试验装置相连接的压力管路,应直接通向系统的供压油滤,以防止对飞机液压系统的污染。
3.3.2间隔
下面提出的间隔和距离是推荐的最小数值。3.3.2.1并列管的间隔
系统导管最小间隔是根据扳手(或连接相配导管的其他工具)和导管端头尺寸要求决定的。导管间的间隔应尽可能地大一些。推荐的最小间隔参见附录A4.1。3.3.2.2相邻结构
要考虑振动、磨损、结构变形、制造公差以及由于温度、压力变化造成导管的偏移。有些地方的间隙是由维修和工作的要求来决定的,在另一些地方则根据变形或其他性质的偏移来估计决定。每段导管的更换或维修应不影响相邻的管路、结构或附件。3.3.2.2.1有支承处
在导管用卡箍固定在结构或其他刚性零件上的地方,卡箍两边附近处导管与结构之间至少要留有6mm的间隙,而在卡箍处则至少要有3mm的间隙。在相邻零件有相对运动处,在最不利的情况下至少应有6mm的间隙。3.3.2.2.2无支承处
为了防止在工作中由于变形或运动而与零件的凸出部分、螺母、螺栓、卡箍或结构的锐棱相接触,与上述物体之间必须留有足够的间隙,在最不利的情况下应有不少于6mm的间隙。在卡箍间的设备与相邻结构之间要留有13mm的间隙。在导管通过护孔圈的地方,应防止护7
GJB3054-97
孔圈偏斜,以免导管与结构接触或划伤护孔盟。3.3.2.2.3其他管路和线路
液压附件、导管及连接件与操纵系统的钢索和联动装置至少相距25mm;在靠滑轮处的最小间隙为13mm。但在钢索跨度的中间处最好相距50mm。相互平行的氧气管路和液压管路之间至少要保持50mm的距离。所有接头和连接点离开交叉点至少50mm。液压管路与电气线路至少相距50mm,且液压管路应装在电气线路的下方。要固定交叉的液压管路,并至少保持6mm的距离。
3.3.3弯管
只要空间尺寸和卡箍的安装位置允许,弯曲半径应尽可能大。导管的弯曲应均匀并应符合HB4一55的要求。两个弯曲之间应有足够长的直线段。导管端头也应有足够长的直线段,以便进行端头加工。弯曲半径和直线段长度应符合HB4一55的要求,并应检查是否满足所用导管弯曲设备和端头加工设备的要求。若用数控弯管,一般要求一根导管只能用同一弯曲半径。3.3.4导管连接
所有可能需要拆卸的接头应按以下准则安排在适当的部位以便于装配和维修。&.接头的安装部位应使各种附件便于拆下而不需松开或拆下管路;b.应使接头间的导管尽可能长一些,以减少接头数量,减轻重量,减少泄漏点;c.直接头、弯接头、三通接头等零件一端或另一端的管路在150mm内应有支承。3.3.5防止破坏
应防止由于机内发生某些情况对液压系统的破坏,如工作中的附加应力,机上的偶然事故以及腐蚀等。还要尽可能防止当飞机起飞和着陆时碰上各种障碍物和碎石以及遭到炮火袭击等外部事故对液压系统的破坏。3.3.5.1工作应力
液压导管的破裂和接头的损坏主要因弯曲疲劳所致。弯曲破坏有两种主要形式:a由于支承结构的相对运动而产生的低频大振幅弯曲,这种情况大多出现在如隔板或附件等刚性连接处;
b.高频小振幅振动将诱导管路的某一部分弯曲应力升高而导致疲劳破坏,这种情况多出现在导管支承处或跨度中间无支承的连接处。为防止弯曲破坏建议遵守以下准则:a.导管装置的设计应考虑支持结构变形的影响;b.管路的布置应根据预计的疲劳寿命进行应力分析,要计算由于导管各端头之间相对运动以及由于振动、热膨胀、导管在支承中的滑动等原因产生的应力;c.只有当计算证明:由扭转、拉伸和压缩等作用产生的组合应力值低于导管材料极限应力的10%时,才允许钢导管的末端有相对运动;d.铝合金导管的末端不允许有相对运动。3.3.5.2机上事故
液压管路的布置应预先考虑某些可能发生的机上不测事故。它们可能发生在易着火区,8
GJB3054-97
发动机舱以及不相容的流体管道或电气系统的附近。应避免将管路安装在当装配或维修时,易当作扶手或踏阶而遭破坏的地方。应防止蓄电池中的酸液溅出对导管的损坏。凡处于发动机舱内或其他易着火区内,以及穿过燃油箱的管路,不论其所承受的压力如何都不应该采用铝合金导管和铝合金接头。液压管路的布置应尽可能地远离所有易燃流体的导管。3.3.5.3腐蚀
要防止铝合金管路在开散的区域,如机轮舱和武器舱内遭到腐蚀。在减震支柱、主起落架、前起落架的支柱上,以及发动机舱内都应采用不锈钢管。要合理选择与接头相配零件的金属材料,以及所用的润滑剂,以免由于电化腐蚀或材料与油液相容性不佳而使零件遭破坏。3.3.5.4外部事故
管路布暨应考虑到由于机轮卷起的碎石及轮胎爆破对导管的可能破坏和发动机转子以及其它附件损坏对管路的威胁。应考虑对炮火的防护。要尽量利用飞机的主要结构和装甲板所提供的保护作用。在起落架减震支柱上和机轮舱内的所有外露管路应受到保护,以防止因轮胎可能突然漏气和轮胎的碎片所造成的破坏。3.3.5.5系统的隔离
在需要设置多个系统以提高安全性的地方,应将每个液压系统管路布置在各种结构元件的两侧,或用防护板将其彼此隔开。当考虑应急系统设暨双重管路时,应使正常管路与应急管路尽可能地彼此远离,以保证即使一个系统被完全损坏时也不致影响另一系统。3.4支承、卡箍和电搭接
3.4.1导管支承的基本功能
导管支承的基本功能是:
&.使导管与设备、电缆、结构或其他导管之间保持固定的距离;b.防止活动和振动,以免导管因与相邻设备、操纵机构、结构、其他导管或支承本身发生摩擦而遭损坏;
c.防止导管由于支承结构的偏移而损坏。在实现以上功能的同时,必须允许导管因热膨胀相对于卡箍装置有某种程度的轴向运动。3.4.2支承设计的一般要求
导管支承通常都直接固定在结构或通过支架固定在结构上。应防止结构对导管施加有害的载荷。在设计上必须考虑结构的振动特性,以及用以固定相邻支承的各种构件的不同弹性等因素。
3.4.3支承的型式和应用
液压导管应由符合HB3-25、HB3-26、HB3-27带垫的夹紧卡箍或符合要求的多管夹支承在刚性结构上。其应用参见附录A5.1和A5.2。导管通过隔板处,过隔板接头可以作为导管的支承起固定作用。3.4.4支承间距
小提示:此标准内容仅展示完整标准里的部分截取内容,若需要完整标准请到上方自行免费下载完整标准文档。
FL1650
GJB3054-97
飞机液压管路系统
设计、安装要求
Hydraulic tubing systems,aircraftdesign,installation requirements for1997-11-05发布
1998-05-01实施
国防科学技术工业委员会批准
1范围
1.1主题内容
1.2适用范围
2引用文件
3要求
导管、接头及其连接型式
3.2导管规格的确定
管路布暨
3.4支承、卡箍和电搭接
导管的尺寸精度
导管应力·
允许的导管缺陷和修理…
保护层·
挠性连接
污染控制
导管的标记
导管模型和鉴定
3.13检验、测试和试验程序,
4质量保证规定
4.1检验责任
4.2检验方法和检验规则
4.3管路系统和管路件的清洗
附录A应用指南(参考件)
1范围
中华人民共和国国家军用标准
飞机液压管路系统设计、安装要求Hydraulic tubing systems,aircraft,design,installation requirements for1.1主题内容
GJB3054-97
本标准规定了飞机I、IⅡ型液压系统和A、B型气动系统的管路系统设计和安装的通用技术要求。
1.2适用范围
本标准适用于飞机I、Ⅱ型液压系统和飞机A、B型气动系统。改进改型飞机液压系统和气动系统亦可参照使用。
2引用文件
GBn221-84
GJB380-87
GJB420A-96
GJB456-88
GJB638A-97
GJB1194-91
GJB1396-92
GJB2296-95
GJB3058-97
GJB3059-97
HB32583
HB 32683
HB 32783
HB4-1-83
HB 4383
HB 4 52 83
HB 4 55 95
HB 4 6983
HB 4 133 83
铝及铝合金薄壁管
飞机液压系统污染测试
飞机液压系统固体污染度分级
飞机液压系统温度型别和压力级别飞机I、Ⅱ型液压系统设计、安装要求飞机气动系统通用规范
飞机液压、应急气动系统试验要求和方法航空用不锈无缝钢管
飞机I、Ⅱ型液压系统污染度验收水平和控制水平飞机I、Ⅱ型液压系统重要附件污染度验收水平带垫的夹紧卡箍
单螺栓侧面固定带垫的夹紧卡箍双螺栓侧面固定带垫的夹紧卡箍扩口管路连接件技术条件
管接头的螺纹部分
导管扩口
导管弯曲半径
管接头的堵盖
航空橡胶棉线编织软管技术条件国防科学技术工业委员会1997-11-05发布1998-05-01实施
HB 4 -142-83
HB5653~5655-81
HB 5663~579483
HB5876-85
HB 5931.8 -89
HB59666075-86
HB6129-87
HB6133-87
HB6442-90
HB/Z228-93
HB/Z 507778
SY1181-76
Q/SY11507-79
3要求
GJB3054-97
航空橡胶钢丝编织软管技术条件航空导管识别标志
卡套式无扩口导管连接件
飞机电搭接技术要求
飞机液压系统污染测试一用显微镜对比法测定工作液固体污染度挤压式无扩口导管连接件
飞机雷击防护要求及试验方法
液压软管、导管、接头组件的脉冲试验飞机液压导管及连接件弯曲疲劳试验挤压式无扩口导管连接工艺指南铝及铝合金化学氧化(磷酸铬酸法)工艺10号航空液压油
12号航空液压油
3.1导管、接头及其连接型式
3.1.1导管的选用原则
导管的选用应遵循以下的原则:a,导管选择应与其工作压力相适应,既有足够的强度又使系统重量最轻;b.导管应与系统的工作介质相容,在系统工作条件下具有良好的防腐蚀性能;C.导管应与接头的连接型式相适应,使导管组件具有良好的密封性、抗振性和耐疲劳性能。塑性较差的高强度薄壁导管应采用无扩口连接型式;d.导管应有良好的扩口、成形、预装工艺特性;e.导管应与其使用的环境相适应。高温区、高振动区、常拆卸及外露部位应采用不锈钢导管。
3.1.2导管的种类
根据系统的设计要求,可选用不锈钢管、钛合金管或铝管。主要选用材料的物理性能参见附录A2.1。
3.1.3接头的选用原则
接头的连接型式应与导管相匹配,接头型式的选择应遵循以下原则:a.接头材料应与导管材料、工作介质相容,有良好的防腐蚀性能;b.接头选择应与工作压力相适应,既有足够的强度又使系统重量最轻;c.接头选择应考虑加工工艺性;d.接头和导管的组件应具有良好的气密性、抗振性和耐疲劳的特性,以及有良好的预装工艺性、维修性和可靠性。
3.1.4接头种类
用于飞机液压系统的接头有多种型式。常用接头的结构形式及说明参见附录A2.2。2
3.2导管规格的确定
GJB3054-97
能量损失和工作压力是确定导管的合理尺寸和材料的主要依据。一般来说,前者是选定导管内径的依据,后者是选定导管材料和壁厚的依据,但同时还需考虑到导管的安装部位、重量、成本,以求得效率高、重量轻、安全可靠的综合效果。3.2.1导管管径的确定
3.2.1.1经验法则
确定系统管路内径的方法有多种,主要是根据管路中预期的流速、压降以及冲击压力进行计算,并反复进行修正。常用的经验法则有:流速极限法、压降分配法、和冲击压力极限法。其详细的计算方法参见附录A3.1。3.2.1.2压降仿真分析法
压降仿真分析法是一种确定系统管路参数的有效方法。压降仿真分析法是将液压系统的结构模型转换成描述系统的数学模型,在计算机上进行求解,确定不同条件下系统中任何处的压力、流量分布情况,确认系统管路设计的合理性。压降仿真分析法有较高的计算精度,易于选择不同的系统管路参数,便于实现管路参数优化设计。有稳态仿真计算和瞬态仿真计算程序。一般应按稳态程序确定管路参数,然后按瞬态程序进行检查。
3.2.1.3全性能最低设计温度
在设计管路系统时要考虑的主要问题之一是要满足在最低工作温度时所允许的压降。最低工作温度往往由飞机性能规范直接给出,或者由规定飞机在指定的低温环境中,接到报警信号以后的允许起飞准备时间间接给出。在后一种情况中,在决定为满足全性能飞行条件所必要的温度时,可以考虑各种使系统油液升温的方法。要综合地考虑所有可能的方法,力求获得加热设备、管路规格的最佳匹配,以使管路具有最小(或在规定范围内)重量和最低成本。3.2.1.3.1起落架收放系统管路
动力操纵的起落架,当系统温度高于一29C时,放下并锁住起落架最大允许时间为15s,收起并锁住起落架最大允许时间为10s,而且要求起落架必须在飞机达到收起起落架的限定速度的75%前收起并锁住。当温度稳定在55C到-29℃之间时,且收放起落架前不充许有系统升温时间时,放下并锁住起落架最大允许时间为30s,收起起落架并锁住起落架的最大允许时间为10s,也要求起落架必须在飞机达到收起起落架的限定速度的75%前收起并锁住。若特定型号的飞机对起落架收放时间及系统温度有特殊要求时,应在专用技术规范中规定。
管路系统参数应满足上述要求。3.2.1.3.2飞行控制系统管路
要保证在气流开始分离以后,在一55C时,驱动飞行控制系统所需增加的力应不大于21℃时所需力的150%,同时还应保证飞行中可能遇到的所有温度下能正常工作。在一55℃到一29℃之间,襟、副翼驱动系统管路的操纵时间应不超过额定操纵时间的150%。管路系统参数应满足上述要求。3.2.1.4吸油管路
3.2.1.4.1低温工作
CJB3054-97
从油箱到油泵的吸油管路设计,应使飞机在最大升限上以可能的最大流量工作时,油泵进口处的油液仍有足够的流量和压力。此时要求油液的温度不低于29℃。对于在上述飞行环境中油泵不工作的系统,可以适当地考虑一个比飞机升限较低的高度,但这一高度不应低于海拔3000m。
上述的有关吸油管路压降的要求不适用于飞机在地面环境温度为一55C的冷起动。吸油管路上不应安装油滤,如果特殊需要,则应保证飞机在任何飞行状态下不影响系统的工作,同时在油滤内要装上合适的旁通阀。3.2.1.4.2瞬态响应
正确地选定油泵的吸油管径,能保证在正常工作的条件下不产生气穴现象。油箱的增压压力值应同时满足稳态和瞬态的工作条件。稳态计算用于确定吸油管路的压降;瞬态计算则考虑了当系统的流量需求变化时,吸油管路内流体加速所需的压力值。瞬态计算公式参见A3.1.4。
3.2.1.5小尺寸导管
在液压系统中一般不采用外径小于6mm的导管,若采用小于6mm的导管则对它的安装、支承和保护必须给予特别注意,而且必须证明装用这类导管的附件能在规定的系统最低温度下正常工作。
3.2.2导管壁厚的确定
3.2.2.1确定壁厚的一般原则
导管壁厚确定应考虑以下因素:a.导管材料特性,如拉伸强度极限、拉伸屈服极限、材料纵向强度和横向强度的差异性、抗疲劳性能等;
b.经受的系统工作压力和安全系数;c.导管的管径;bZxz.net
d.导管的允许尺寸公差和允许缺陷;e.经受的环境条件如温度、振动、冲击等;f.任何材料和规格的导管,其最小壁厚一般不应小于0.5mm。导管壁厚必须经合理的试验来验证,至少应进行脉冲试验、弯曲疲劳试验和弯管组件的爆破试验。
3.2.2.2确定壁厚的方法
飞机液压管路设计中对导管壁厚进行计算时,通常采用薄壁或厚壁圆简的计算公式,并通过爆破压力的核算来最终确定。常用的计算方法参见附录A3.2。3.3管路布置
3.3.1线路确定
3.3.1.1载流管路敷设的一般原则应精心进行管路设计,以降低系统的复杂性,并减轻重量,使可能的损坏和泄漏减至最少。液压管路装置的设计应使其具有与飞机机体结构相当的工作寿命,并便手更换和维修。尽量4
GJB3054-97
减少弯管和分支,采用最直接的线路并与其他要求相协调。为使管路具有足够的强度,工作寿命长,安全可靠,设计时应遵循以下的基本原则:a。避免在两个刚性支承接头之间安装直导管。在必须安装这类直导管处,应在附件或刚性接头的安装方面采取措施,保证导管和接头不承受过大的安装应力,并要考虑使用中的热应力。若有必要,可将导管制成半环形,以保证安装时易于对准和承受振动;b.在两个允许有相对运动的接头之间不采用铝导管和直钢管;c.液压管路不要进入驾驶舱或座舱内,并要远离人员所处的位置。此外,液压管路必须远离排气管道、热总管、电气线路、无线电线路、氧气管道、各种设备和绝缘材料。在所有场合下,为防止导管泄漏引起火,液压管路都要位于上述各种装置之下。不应将液压管路与其他易燃流体管路汇集在一起,以免各种不同系统相互接错;d.所有系统的压力管路和易着火区内的回油管路,应使用不锈钢管或钛合金管;e.铝合金导管仅限用于易着火区以外的回油和吸油管路;f.管路安装应保证合适的支承间隔:g.导管和导管之间,导管和结构、运动部件之间,导管和其他系统之间应有合理的足够的间隙,以保证在最不利的制造公差,最严酷的环境条件,最严重变形条件下不产生相互接触和磨损。
3.3.1.2排油及通气管路
排油管应伸到飞机的下外表面,以免排出的油液或蒸汽吹回到飞机里,喷在排气管、热总管及其他火源上,或聚积在结构的凹陷处。不允许油液进到机翼前缘、检查窗口、机轮舱、排气口、进气口及其他火源处。应从外面将排油管周围盖住,以防止油液及蒸汽回流至舱内;还要加上一个斜端口以使气流通过时产生负压。在放油装置下不应安装任何附件。在飞行或地面作机动操作时,油箱通气口不应有油液损失,对于在飞行中通气口有可能向外少量漏油的系统,可将其引至一个容器中收集起来,在维修时放出。对伸出机外的排油、通气口应考虑设置网罩,以防异物进入而堵塞。3.3.1.3样机
导管安装用的全尺寸模型(即样机)是一种十分有效的协调工具。它可以用来确定管路最佳的走向、弯曲部位、连接型式以及最佳的支承部位。样机应尽量模拟周围的结构和相邻的设备,用以对是否有足够的安装操作空间、管路容差、可达性以及中心对准等情况进行验证。3.3.1.4温度
液压系统应有良好的冷起动性能,在最低地面环境温度(-55C)下能正常起动。但并不要求在这样的温度下达到全性能。如冷起动需要分支回路,应使回路回到油箱而不要直接回到液压泵,以免回路过短,不能散热而使系统升温,以致局部过热损坏油泵。管路布置中应尽量避免使导管穿越电气设备、热总管或其它热源区。如导管必须靠近某一超过系统型别规定的最高温度的局部热源,则应采取有效的隔热、局部冷却或其他保护措施。表1给出了液压系统一些常用非金属材料的温度上限。这里给出的是长时间工作的温度极限,其中有些材料能短时间地工作在更高的温度下而不致严重损坏。5
GJB3054-97
表1液压系统常用非金属材料长期工作的最高温度YH-10
液压油
3.3.1.5防火
液压油
液压油
120℃
氟橡胶
180℃
聚四氟乙
烯SFB-1
260℃
聚酰铵
(尼龙)
液压系统设计时应与其他一些系统综合考虑,使液压系统消除或隔离附近的可燃气体、热源、发动机排气管或电器设备等可能造成的火险。凡是安置在会引起泄油液自发着火或持续燃烧的热源、发火源附近的液压管路和液压附件,均须由防火墙、防火罩或防止油液着火的相应装置加以保护。
根据特定型号飞机的防火要求,如燃油系统或滑油系统(或两个系统)必须有切断阀,则应设暨液压泵供油(吸油)切断阀。若要设置这类阀,则不应位于防火墙或隔火板的装有发动机的一侧,但要尽可能靠近这些构件。阀相对发动机要有一定距离,以保证发动机从连接结构上脱离时阀的工作不受影响。此类阀的关闭和打开应能在驾驶舱内进行操纵。3.3.1.6防炮火
凡在设置双套液压系统之处,这些系统应尽量离得远些,以便最大程度地减少炮火或发动机着火对双套系统所引起的破坏作用。应尽可能将两套系统分开布置在机身、翼梁的相对两侧,或采取类似的隔开措施。对安全飞行必需的各系统应尽量做到相距450mm。3.3.1.7维护性
当系统出现导管或接头的损坏、泄漏等情况时,应能保证方便地对主要管路进行维护和修理。导管和接头的修理应尽量不需要拆下相邻的附件。3.3.1.7.1接头位置
所有可能需要拆卸的接头应该安装在易于接近的地方,以便在冷天戴着手套能进行拆装和检查。
附件上的管路
3.3.1.7.2
当一个液压附件与两个或两个以上的管路相连,有可能发生错接的情况时,应采取有效的防错措施。
3.3.1.7.3排油管路
从油泵、油箱或其他液压附件中引出的排油和通气管路,不允许和任何其他管路及飞机上任何其他系统相连,致使这些附件的油液被混合排出。3.3.1.7.4轻附件的安装
本身没有安装件的重量轻的附件可由其连接的导管来支承,但附件必须装得很牢固,而且不使所安装的导管产生破坏性振动或其它不利状态。这些附件也可用卡箍或类似的装置固定在结构上,但必须保证铭牌、流向箭头、各种标记或其他数据不被遮盖,而支承件也不影响附件的工作。如果一个卡箍不能支承附件,则在该附件两侧的导管上,距附件50mm的范围内都应有卡箍支承在结构上。
3.3.1.7.5排除混入的空气
GJB3054-97
凡是在混入的空气会影响系统正常工作的地方,应采取适当的措施,如安装排气阀,排出混入的空气。不采取松开导管螺母的方法来排出混入的空气。液压系统和液压设备的布局要尽可能使系统中游离的空气能自动流向液压油箱或其他不影响工作又便于排出的聚积处。3.3.1.7.6地面试验装置
每个液压系统应包括一套自封连接装置,供连接地面试验设备用。液压系统地面连接装置应这样设计:即在飞机上试验一个液压系统时,不必对飞机上其他系统增压。特别是只用一个液压试验设备试验飞机液压系统时,在试验设备和飞机系统之间不采用“Y\型连接。若机上的几套液压系统需同时工作,应用相同套数的地面独立液压源与飞机系统相连。各个液压系统应尽量集中设置地面试验连接座。该连接座上要有连接地面试验设备用的各种接头,供系统检查、系统清洗、液压油箱排气、液压油箱加油以及蓄压器充气之用。应采取措施防止水分、空气及其他污染物在加油和试验过程中通过地面连接装置进入系统。由隔板式半法兰接头和保护盖组成的成套自封接头,应安装在飞机上的适当部位,使在地面容易接近并便于连接地面试验设备。应急系统或辅助系统中使用的电动机驱动的液压泵不用于地面试验,除非电动机是按连续工作要求设计的。还须注意到以下情况:
a.地面试验装置上的吸油管路的管径尺寸应与其长度相适应;b.飞机上与地面试验装置相连接的压力管路,应直接通向系统的供压油滤,以防止对飞机液压系统的污染。
3.3.2间隔
下面提出的间隔和距离是推荐的最小数值。3.3.2.1并列管的间隔
系统导管最小间隔是根据扳手(或连接相配导管的其他工具)和导管端头尺寸要求决定的。导管间的间隔应尽可能地大一些。推荐的最小间隔参见附录A4.1。3.3.2.2相邻结构
要考虑振动、磨损、结构变形、制造公差以及由于温度、压力变化造成导管的偏移。有些地方的间隙是由维修和工作的要求来决定的,在另一些地方则根据变形或其他性质的偏移来估计决定。每段导管的更换或维修应不影响相邻的管路、结构或附件。3.3.2.2.1有支承处
在导管用卡箍固定在结构或其他刚性零件上的地方,卡箍两边附近处导管与结构之间至少要留有6mm的间隙,而在卡箍处则至少要有3mm的间隙。在相邻零件有相对运动处,在最不利的情况下至少应有6mm的间隙。3.3.2.2.2无支承处
为了防止在工作中由于变形或运动而与零件的凸出部分、螺母、螺栓、卡箍或结构的锐棱相接触,与上述物体之间必须留有足够的间隙,在最不利的情况下应有不少于6mm的间隙。在卡箍间的设备与相邻结构之间要留有13mm的间隙。在导管通过护孔圈的地方,应防止护7
GJB3054-97
孔圈偏斜,以免导管与结构接触或划伤护孔盟。3.3.2.2.3其他管路和线路
液压附件、导管及连接件与操纵系统的钢索和联动装置至少相距25mm;在靠滑轮处的最小间隙为13mm。但在钢索跨度的中间处最好相距50mm。相互平行的氧气管路和液压管路之间至少要保持50mm的距离。所有接头和连接点离开交叉点至少50mm。液压管路与电气线路至少相距50mm,且液压管路应装在电气线路的下方。要固定交叉的液压管路,并至少保持6mm的距离。
3.3.3弯管
只要空间尺寸和卡箍的安装位置允许,弯曲半径应尽可能大。导管的弯曲应均匀并应符合HB4一55的要求。两个弯曲之间应有足够长的直线段。导管端头也应有足够长的直线段,以便进行端头加工。弯曲半径和直线段长度应符合HB4一55的要求,并应检查是否满足所用导管弯曲设备和端头加工设备的要求。若用数控弯管,一般要求一根导管只能用同一弯曲半径。3.3.4导管连接
所有可能需要拆卸的接头应按以下准则安排在适当的部位以便于装配和维修。&.接头的安装部位应使各种附件便于拆下而不需松开或拆下管路;b.应使接头间的导管尽可能长一些,以减少接头数量,减轻重量,减少泄漏点;c.直接头、弯接头、三通接头等零件一端或另一端的管路在150mm内应有支承。3.3.5防止破坏
应防止由于机内发生某些情况对液压系统的破坏,如工作中的附加应力,机上的偶然事故以及腐蚀等。还要尽可能防止当飞机起飞和着陆时碰上各种障碍物和碎石以及遭到炮火袭击等外部事故对液压系统的破坏。3.3.5.1工作应力
液压导管的破裂和接头的损坏主要因弯曲疲劳所致。弯曲破坏有两种主要形式:a由于支承结构的相对运动而产生的低频大振幅弯曲,这种情况大多出现在如隔板或附件等刚性连接处;
b.高频小振幅振动将诱导管路的某一部分弯曲应力升高而导致疲劳破坏,这种情况多出现在导管支承处或跨度中间无支承的连接处。为防止弯曲破坏建议遵守以下准则:a.导管装置的设计应考虑支持结构变形的影响;b.管路的布置应根据预计的疲劳寿命进行应力分析,要计算由于导管各端头之间相对运动以及由于振动、热膨胀、导管在支承中的滑动等原因产生的应力;c.只有当计算证明:由扭转、拉伸和压缩等作用产生的组合应力值低于导管材料极限应力的10%时,才允许钢导管的末端有相对运动;d.铝合金导管的末端不允许有相对运动。3.3.5.2机上事故
液压管路的布置应预先考虑某些可能发生的机上不测事故。它们可能发生在易着火区,8
GJB3054-97
发动机舱以及不相容的流体管道或电气系统的附近。应避免将管路安装在当装配或维修时,易当作扶手或踏阶而遭破坏的地方。应防止蓄电池中的酸液溅出对导管的损坏。凡处于发动机舱内或其他易着火区内,以及穿过燃油箱的管路,不论其所承受的压力如何都不应该采用铝合金导管和铝合金接头。液压管路的布置应尽可能地远离所有易燃流体的导管。3.3.5.3腐蚀
要防止铝合金管路在开散的区域,如机轮舱和武器舱内遭到腐蚀。在减震支柱、主起落架、前起落架的支柱上,以及发动机舱内都应采用不锈钢管。要合理选择与接头相配零件的金属材料,以及所用的润滑剂,以免由于电化腐蚀或材料与油液相容性不佳而使零件遭破坏。3.3.5.4外部事故
管路布暨应考虑到由于机轮卷起的碎石及轮胎爆破对导管的可能破坏和发动机转子以及其它附件损坏对管路的威胁。应考虑对炮火的防护。要尽量利用飞机的主要结构和装甲板所提供的保护作用。在起落架减震支柱上和机轮舱内的所有外露管路应受到保护,以防止因轮胎可能突然漏气和轮胎的碎片所造成的破坏。3.3.5.5系统的隔离
在需要设置多个系统以提高安全性的地方,应将每个液压系统管路布置在各种结构元件的两侧,或用防护板将其彼此隔开。当考虑应急系统设暨双重管路时,应使正常管路与应急管路尽可能地彼此远离,以保证即使一个系统被完全损坏时也不致影响另一系统。3.4支承、卡箍和电搭接
3.4.1导管支承的基本功能
导管支承的基本功能是:
&.使导管与设备、电缆、结构或其他导管之间保持固定的距离;b.防止活动和振动,以免导管因与相邻设备、操纵机构、结构、其他导管或支承本身发生摩擦而遭损坏;
c.防止导管由于支承结构的偏移而损坏。在实现以上功能的同时,必须允许导管因热膨胀相对于卡箍装置有某种程度的轴向运动。3.4.2支承设计的一般要求
导管支承通常都直接固定在结构或通过支架固定在结构上。应防止结构对导管施加有害的载荷。在设计上必须考虑结构的振动特性,以及用以固定相邻支承的各种构件的不同弹性等因素。
3.4.3支承的型式和应用
液压导管应由符合HB3-25、HB3-26、HB3-27带垫的夹紧卡箍或符合要求的多管夹支承在刚性结构上。其应用参见附录A5.1和A5.2。导管通过隔板处,过隔板接头可以作为导管的支承起固定作用。3.4.4支承间距
小提示:此标准内容仅展示完整标准里的部分截取内容,若需要完整标准请到上方自行免费下载完整标准文档。

标准图片预览:
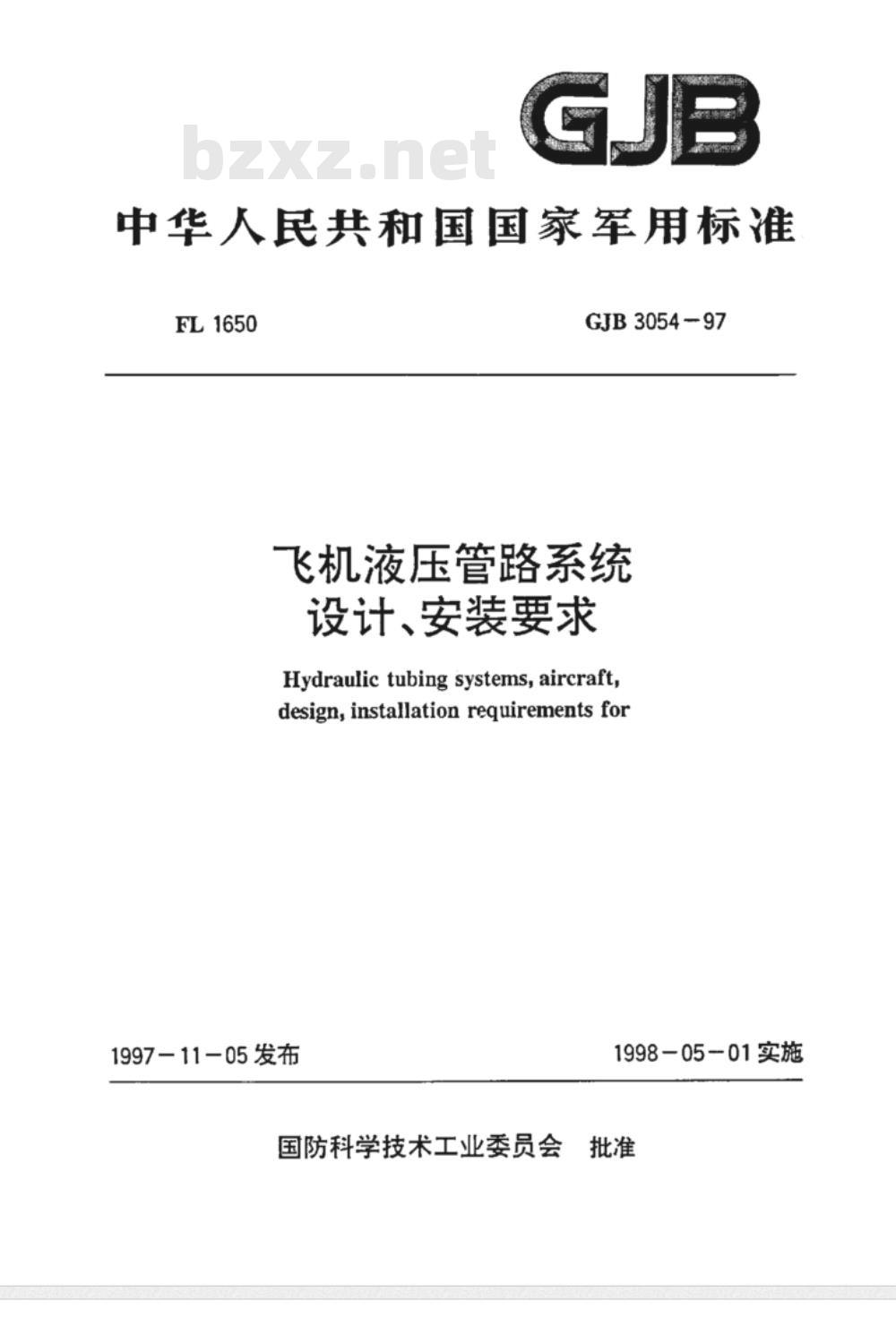
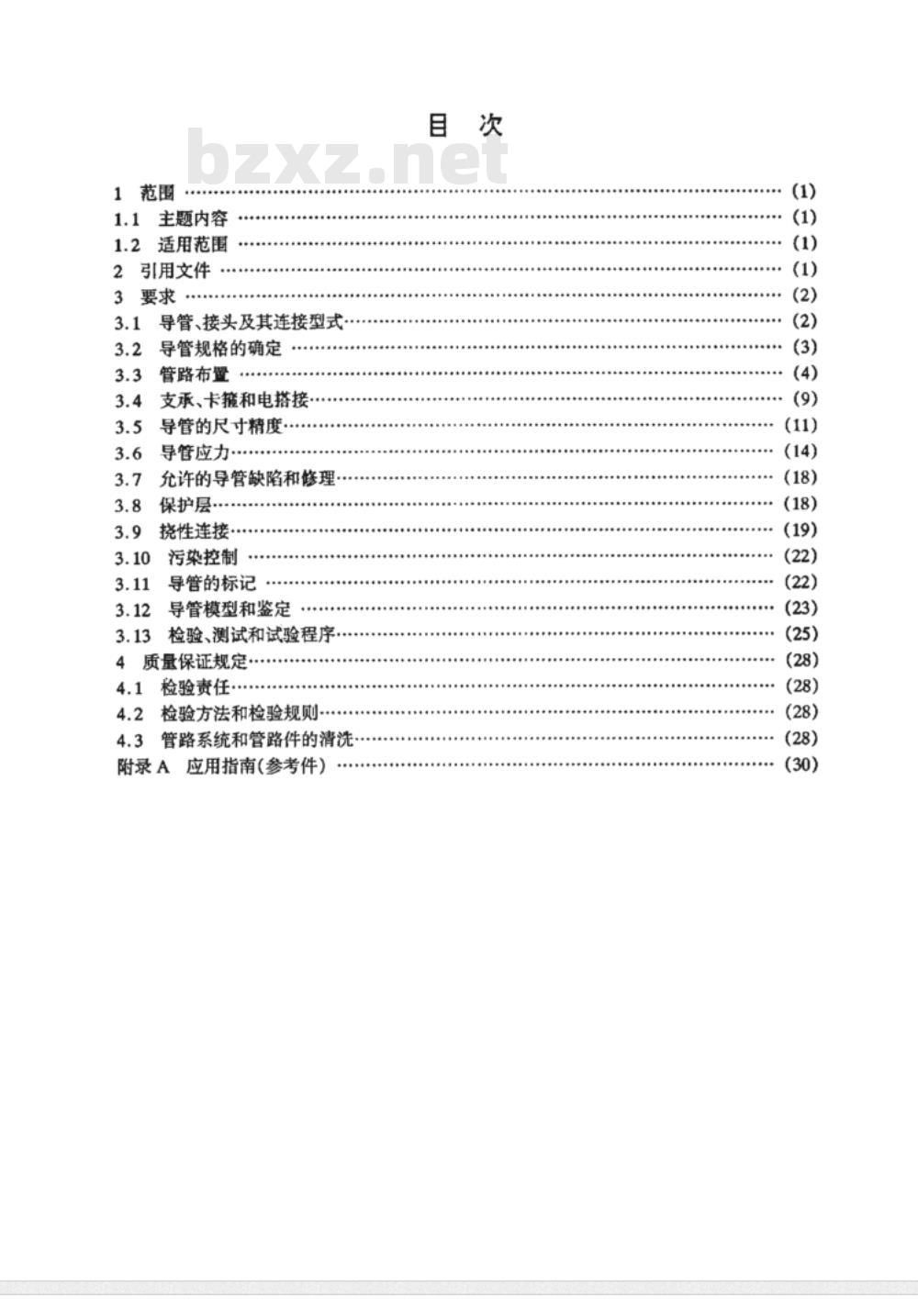
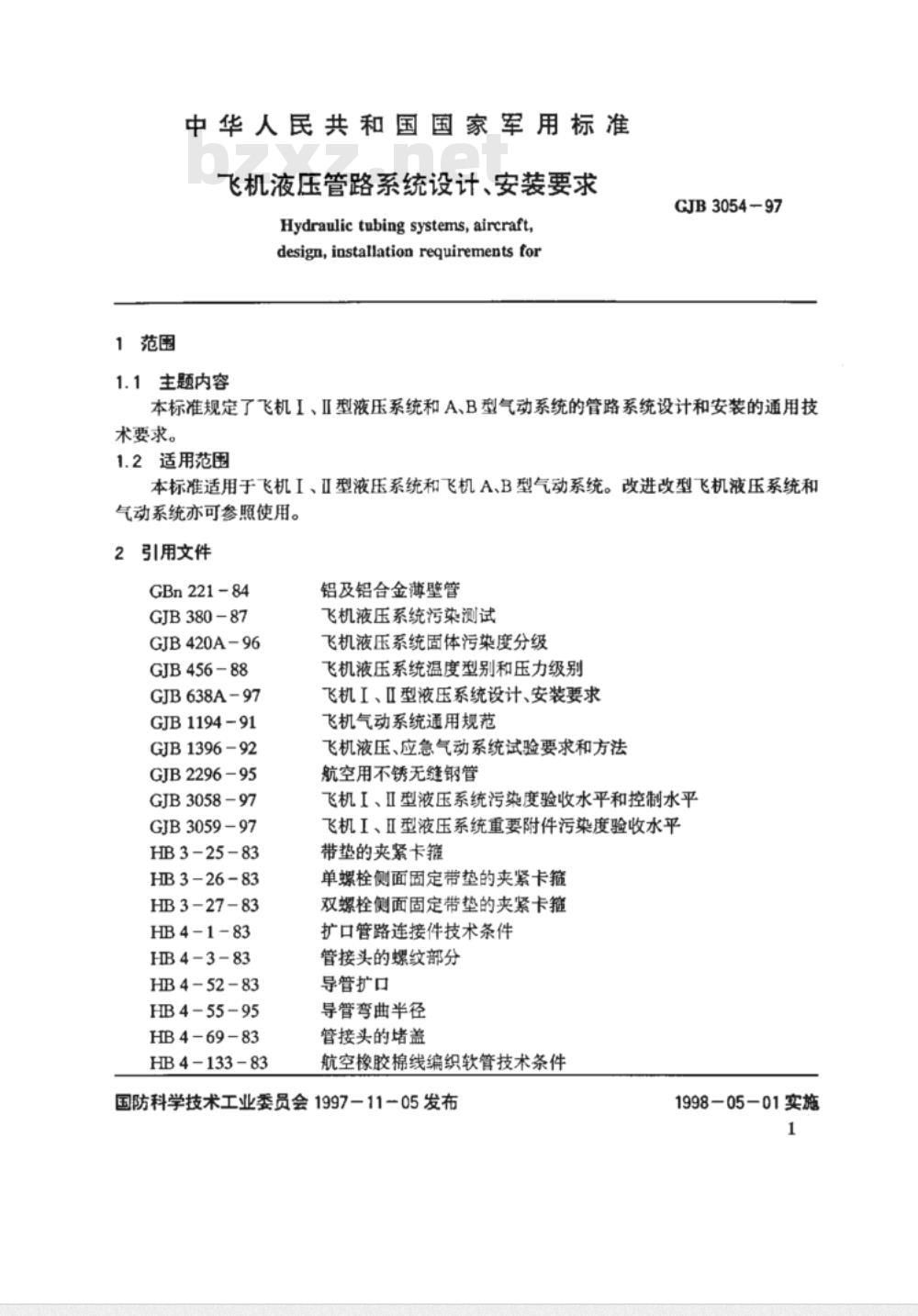
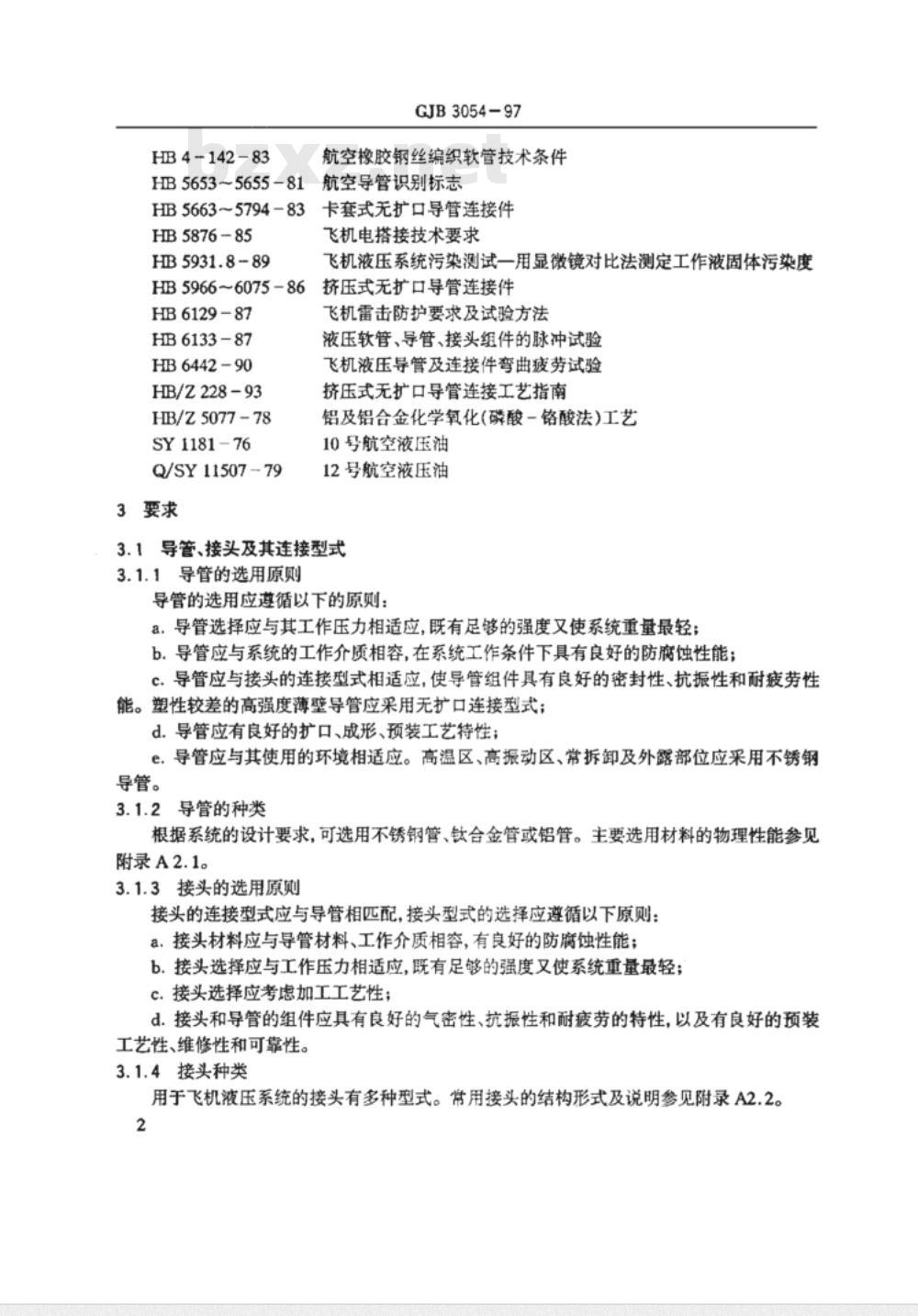
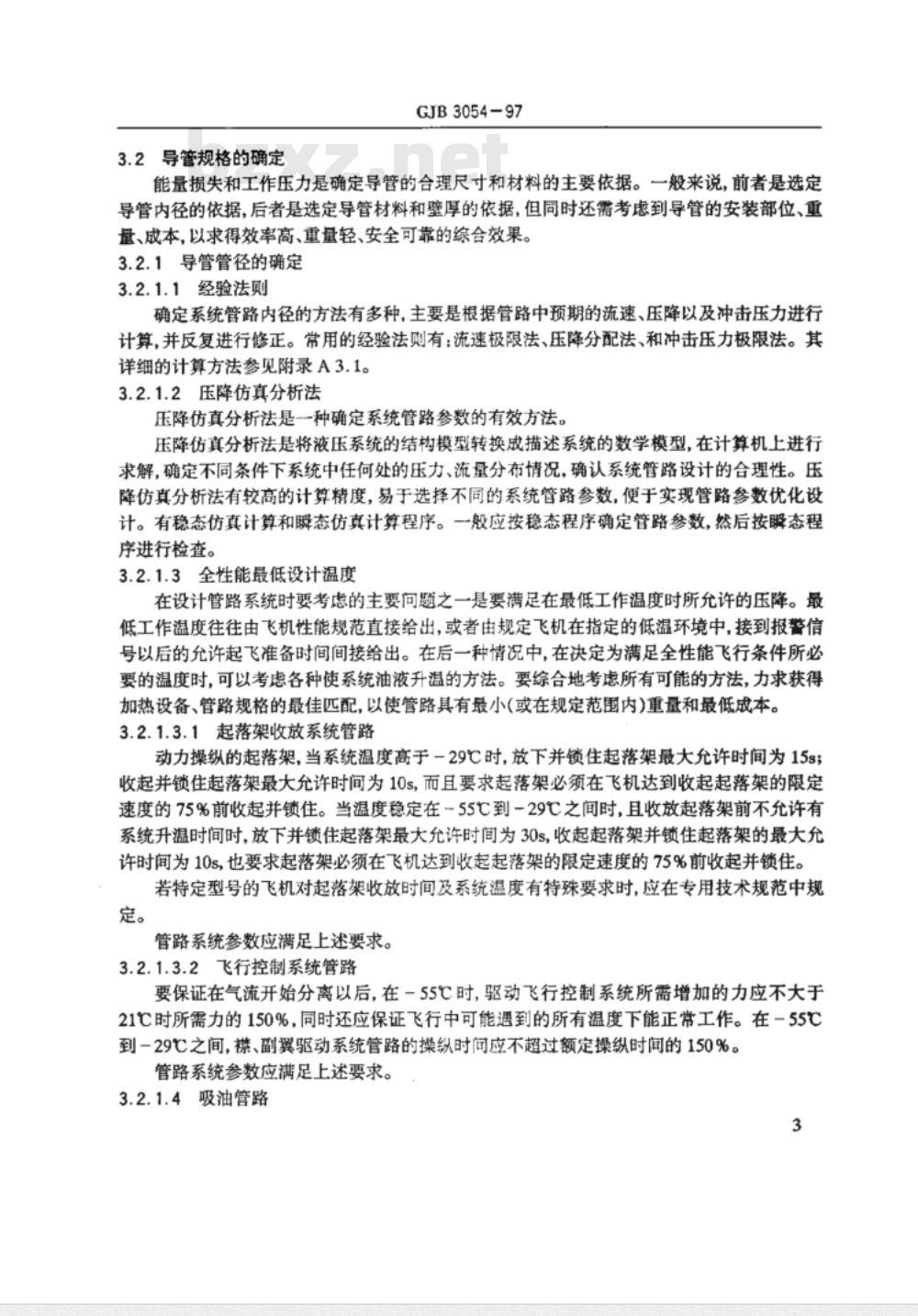
- 热门标准
- 行业标准
- QX/T285-2015 电离层闪烁指数数据格式
- QX/T286-2015 15个时段年最大降水量数据文件格式
- QB/T4155-2010 自动号码机
- QX/T294-2015 太阳射电流量观测规范
- QX/T176-2012 遥感卫星光学辐射校正场数据格式
- QX/T219-2013 空气流速计量实验室技术要求
- QX/T175-2012 风云二号静止气象卫星S-VISSR数据接收系统
- QMYC0001S-2014 勐海县云茶科技有限责任公司 普洱茶膏(粉)
- QX/T174-2012 大气成分站选址要求
- QX/T217-2013 大气中氨(铵)测定靛酚蓝分光光度法
- QX/T352-2016 气象信息服务单位服务文件归档管理规范
- QX/T222-2013 气象气球浸渍法天然胶乳气球
- QHXRS0002S-2016 河南旭瑞食品有限公司 熟咸蛋
- QXZW0001S-2016 广汉喜之味食品有限公司 半固态复合调味料(含油型)
- QB/T4197-2011 合成革用聚氨酯树脂
请牢记:“bzxz.net”即是“标准下载”四个汉字汉语拼音首字母与国际顶级域名“.net”的组合。 ©2009 标准下载网 www.bzxz.net 本站邮件:bzxznet@163.com
网站备案号:湘ICP备2023016450号-1
网站备案号:湘ICP备2023016450号-1