- 您的位置:
- 标准下载网 >>
- 标准分类 >>
- 其他行业标准 >>
- GJB 1057-1990 LC9铝合金过时效锻件
标准号:
GJB 1057-1990
标准名称:
LC9铝合金过时效锻件
标准类别:
其他行业标准
标准状态:
现行出版语种:
简体中文下载格式:
.rar .pdf下载大小:
2.10 MB

部分标准内容:
中华人民共和国国家军用标准
GJB 1057-90
LC9铝合金过时效锻件
Overaging forging of aluminium alloy(L C9)1991—01-26发布
1991-06—01实施
国防科学技术工业委员会
中华人民共和国国家军用标准
LC9铝合金过时效锻件
Overaging forging of aluminium alloy(LC9)1主题内容与适用范围
GJB1057-90
本标准规定了LC9铝合金过时效锻件的品种,技术要求、质量控制、试验方法、检验规则及包装、标志、运输和贮存等。本标准适用于具有良好抗应力腐蚀性能的LC9铝合金过时效自由锻件和模锻件。2引用标准
GBn223
GB3199
GB3246
GB6519
铝合金锻件
金属拉伸试验方法
金属布氏硬度试验方法
铝及铝合金加工产品的包装、标志、运输、贮存铝及铝合金加工制品显微组织检验方法铝及铝合金加工制品低倍组织检验方法变形铝合金超声波检验方法
GB6987.1~6987.21铝及铝合金化学分析方法GB8545
GB/T12966
3产品分类
供应状态
铝及铝合金模锻件的尺寸偏差及加工余量铅合金电导率涡流测试方法
锻件以固溶热处理人工过时效状态供应。状态标记为CGS1或CGS3。最大厚度处的三个方向(纵、横、高)尺寸均大于80mm的锻件,呈热锻状态供应。其热处理由需方或委托供方经粗加工后进行。
3.2类别
锻件按使用要求分为1、Ⅱ、函三类,并在图样上注明。未注明者为耳类。3.3尺寸及允许偏差
3.3.1锻件的几何形状和尺寸应符合供需双方议定的图样或合同要求3.3.2锻件的加工余量和尺寸偏差应符合GB8545或供需双方议定的图样或技术协议。3.4标记示例
国防科学技术工业委员会1991一01一26发布1991—06-01实施
GJB 1057-90
用LC9铝合金锻造的,以固溶热处理人工过时效状态CGS1供应的J8一114Ⅱ类自由锻件标记为:
自由锻件J8-114LC9CGS1I类GJB1057-90技术要求
4.1化学成分
锻件的化学成分应符合表1的规定。表1
主要成分,%
4.2热处理制度
4.2.1固溶热处理温度为465士5℃,其它按现行工艺。4.2.2
过时效制度应符合表2的规定。
时效阶段
第一阶段
第二阶段
第一阶段
第二阶段
注:时效保温时间按金具实际温度达到时效温度下限起计算。4.3力学性能
锻件的室温力学性能应符合表3的规定。4.4抗应力腐蚀性能
4.4.1锻件的电导率应符合表4的规定。Fe
杂质,不大于,%
加热温度,℃
110±5
177±5
110±5
165±5
保温时间,h
8~10
8~10
4.4.2锻件按表5规定的试验应力和时间进行应力腐蚀试验后应无应力腐蚀破裂现象。4.5超击波探伤
4.5.1锻件的超声波探伤应在固溶热处理人工过时效后进行。热锻(R)状态交货的锻件探伤应由供需双方议定,并在图样上注明。2
模锻件
自由锻件
模锻件
自由锻件
伸长率
规定残余
伸长应力
GJB1057-90
力学性
能,不小于
规定残余1
伸长率
伸长应力
注热慢(R)状态供应的锻件,其试样经热处理后的力学性能应符合表3的规定。表4
电导率,MS/m
取样方向
高向(ST)
力学性能
满足本标准要求
满足本标要求,但纵向
0.0.2≤467N/mm2
满足本标准要求,但纵向
Or0. 2>467N/mm2
任何情况
满足本标准要求
任何情况
试验应力,N/mm2
伸长率
10/1000/30
不台格
不合格
试验时间,d
4.5.2需超声波探伤的、Ⅱ类锻件的探伤级别和部位应在图样上注明,1类锻件不做超声波探伤。
GJB 1057-90
4.5.3超声波探伤分A,B两级,其允许的缺陷值应符合表6的规定。表6
单个缺陷
当量平底
孔直径
多个缺陷
每个缺陷当
量平底孔直径
注:当量平底孔直径为记录直径4.6显微组织
锻件的显微组织不允许过烧。
4.7低倍组织
中心距
长条形缺陷
缺陷任何部位反
射的当量平底孔直径
4.7.1模锻件的流线应顺着受检截面的外形分布。不允许有穿流和严重涡流,流线应符合首批试制件或供需双方认可的低倍标样图片。4.7.2低倍组织为充分变形组织,并应符合首批试制件或供需双方认可的低倍试样图片。4.8表面质量bZxz.net
4.8.1自由锻件不蚀洗,其表面不应有裂纹和折选,如有,应清除。其它缺陷深度(包括清除处)应保证锻件留有三分之一的名义加工余量。4.8.2模锻件需经蚀洗。待加工锻件表面的裂纹、折迭和腐蚀斑痕必须清除。起皮、气泡、碰伤、压入物等其它缺陷可进行检验清理,但应保证锻件留有三分之一的名义加工余量。非加I锻件表面的裂纹及影响使用的其它缺陷,应清除,清除缺陷的部位应保证模锻件的单面极限尺寸。
5质量控制
5.1.锻件用坏料应符合有关标准或供需双方协议。5.2供方提供的首批试制件经需方复验鉴定后,如主导工艺(毛料选择、响锻件组织和性能的锻造及热处理工艺制度》需要变更时,其试验总结和工艺规范等技术文件必须经供方总工程师(或总工艺师)审批,并通知需方认可。如三个月内不答复则表示认可。5.3供方有责任保存锻件质量跟踪所必要的原始记录(如工艺卡片、组织性能报告),保存期不少于7年。
5.4需方认为必要时,可派代表到生产厂家抽查主导工艺,以确定其是否符合本标准的要求。6试验方法
6.1锻件的化学成分仲裁分析方法按GB6987.1~6987.21的规定进行。4
GJB 1057-90
6.2件的室温拉伸性能试验方法按GB228的规定进行。6.3搬件的布氏硬度试验方法按GB231的规定进行。6.4锻件的电导率测试方法按GB/T12966的规定进行。6.5锻件的应力腐蚀试验方法按附录A(补充件)的规定进行。6.6锻件的超声波探伤方法按GB6519的规定进行。6.7锻件的显微组织检验方法按GB3246的规定进行。6.8锻件的低倍组织检验方法按GB3247的规定进行。6.9自由锻件的外形尺寸用钢板尺、卷尺等专用工具或简易样板检测。模锻件的外形尺寸用划线法或专用样板工量具及精度不低于0.02mm的卡尺检测,7检验规则
7.1检查和验收
锻件应由供方技术监督部门验收,并保证产品质量符合本标准要求。7.2组批
锻件应成批提交验收,同批次锻件应由同一合金,同一熔次、同一规格、同一热处理炉次的组成。当设备条件受限时,一批也可由几个固溶热处理炉次的组成。每批重量不限。7.3检验项目和取样数量
锻件的检验项目和取样数量应符合表7的规定。7.4重复试验
7.4.1低倍组织试验不合格时,1类锻件不允许重复试验,I、I类锻件允许供方重复试验,需方不复验。
7.4.2锻件的室温力学性能不合格时,允许从该试样的相邻部位或另一锻件取双倍数量试样复验。仍有个试样不合格时,则该批(炉)次报废或做重复热处理。100%取拉伸试样的锻件,按件报废。
检验项目
表面质量几何
尺寸印记
化学成分
力学性能
拉伸性能
每熔次取1个试样
有试验余料的懒件取
100%,每件取1个或2个
试样,无试验余料的锻件,
按固溶热处理炉次每炉取1
件、每件取1个或2个试样
每熔次取1个试样
按固溶热处理炉次每炉
取1件,每件1个或2
个试样
每熔次取1个试样
检验项目
抗应力腐
蚀性能
电导率
应力腐蚀
显徽组织
低倍组织
超声波探伤
GJB 1057-90
续表?
首批或有重大工艺变更时
取1件,每件取5个试样
有试验余料的锻件取
100%,每件取1个试样,无
试验余料的锻件,按固溶热
处理炉次每炉取1件,每件
取1个试样
每批取1件,每件取1个试
首批或有重天工艺变更
时取1件,每件取5个试
每固溶热处理炉次取1
件,每件取1个试样
每批取1件,每件取1个
每固溶热处理炉次取1
件,每件取1个试样
首批或有重天工艺变更
时取1件,每件取1个试
7.4.3当锻件的电导率可疑时,可从该热处理炉(批)次中取一个试样做固溶热处理(固溶热处理温度为465士5℃,保温30分钟,在室温水中淬火)后,于15分钟内测电导率,若测量结果与原值之差不小于3.5Ms/m,则锻件合格,反之不合格。7.5重复热处理
7.5.1当力学性能、电导率或应力腐蚀试验结果不合格时,允许补充时效或重复热处理。其重复热处理次数不得超过两次,补充时效不算重复热处理。7.5.2重复热处理后必须重新按表7规定检测显微组织、力学性能和抗应力腐蚀性能。7.6其他
7.6.1纵向拉伸性能合格时,硬度试验结果不做为报废的依据。7.6.2对于超声波探伤所能反映的一些缺陷(如包括氧化膜在内的非金属夹杂、气孔、裂纹)按超声波探伤结果验收,低倍组织检查结果不作为报废依据。7.6.3以热锻(R)状态供应的锻件,取试块进行热处理,也可锻成相应的锻造试样进行热处理。热处理后的试块的室温力学性能及抗应力腐蚀性能应符合本标推的规定。8标志、包装、运输、贮存
8.1标志
锻件的标志应符合GB3199的要求。每个检验合格的锻件上应按图样标明的位置打上卜列标记:
a.供方质量监督部门的印记;
b.合金牌号及供应状态;
c.模锻件或自由锻件代号:
d熔次号、批号、1类锻件的顺序号:6
e:固溶热处理炉次号。
8.2包装、运输和贮存
GJB1057→90
8.2.1锻件的包装、运输和贮存应符合GB3199的规定8.2.2自由锻件可裸件交货,重量小于10kg的自由锻件可装箱交货,有特殊要求时,由供需双方议定。
8.2.3全加工模锻件可简易包装交货。精密模锻件和局部不加工的模锻件涂油包装。有特殊要求时,由供需双方议定。
8.3质量证明书
每批锻件应附有符合本标准要求的质量证明书,其上应注明:a.供方名称:
b,合金牌号及状态代号;
c.锻件代号:
d.熔次号、批号、固溶热处理炉次号:e.重量和件数?
f、化学成分、力学性能、电导率、应力腐蚀、超声波探伤、显微组织、低倍组织等试验结果;多,技术监督部门的印记;
h.本标准号
i.包装日期。
A1概述及适用范围
GJB1057-90
附录A
C环形试样恒应变应力痴蚀试验方法(补充件)
本方法为恒应变应力腐蚀试验方法,用于检验铝合金材料对应力腐蚀的敏感性。本方法用腐蚀破裂时间来评定材料的耐应力腐蚀破裂性能,主要适用于高强度铝合金。A2试样制备
A2.1取样方法
A2.1.1对于板、带材,C环的取向应使主应力方向(平行于加力螺栓)与短横向平行。A2.1.2对于锻件,C环的取向应使主应力方向与流线相垂直(图A1)。A2.1.3对于管、棒材,可沿纵向直接切取。A2.2试样加工
A2.2.1试样规格由试验者依具体情况而定,但须保证试样的直径为16~32mm,且径厚比在11~16范围内。试样的精加工应在热处理后进行,以免产生较大的残余应力。试样主表面的粗糙度不得大于0.8um。试样不得有划痕、凹坑、毛刺等缺陷。加工过程中应避免试样产生塑性变形。
A2.2.2试样的型式如图A2所示。A2.2.3每种试验条件应至少取5个平行试样。A3表面制备
用有机溶剂(如汽油和酒精)去除试样表面的油污。A4试验条件
A4.1试验溶液
A4.1.1配制溶液用的容器,可用硬塑料板、玻璃塘瓷等情性材料制做,试验溶液为3.5%NaC1水溶液,pH值控制在6.4~7.2之间(用稀NaOH水溶液或稀HC1水溶液调节)。S
试样的制取位置
GJB1057-90
山股小1910.,
图A2C环形应力腐蚀试验
A4.1.2配制溶液所需试剂为化学纯(cp)级以.b,水为蒸馏水或去离子水。A4.2试验温度
如无特别规定,试验温度取27℃C,温度变化范围为士1℃C。A4.3试验湿度
应尽量控制试验空间的相对湿度在45士6%范围内。A4.4试验时间
试验时间依材料的技术条件面定,一般在20~~90天。A4.5试验应力
试验应力按材料的技术条件确定。A5试验程序
A5.1采用与试验合金同系的材料做螺栓、螺母。扭紧拉力螺栓,即可使C环处表面受到拉应力作用。
C环的径向变化量按下式计算(C环直径在加力螺栓方向上测量,精度应达到士0.01mm):
ODf=OD-
4=fnD2/AEtz
式中OD—加力前C环的外径,mm;ODf—加力后C环的外径,mm;
A一c环的径向压缩量,mm:
一C环的中径(D=OD-t),mm;
E-一材料的弹性模量,N/mm\
t-c环的壁厚,mm;
Z—曲梁修正系数(参见图A3)
f—试验应力N/mm\。
GJB1057--90
A5.2试样加力后要用耐水涂料对螺栓、螺母与试样的接触部位进行封闭。试验前用蘸有有机溶剂的棉球擦拭试样受力表面,以除去可能沾染的油污。1.00
图人3弯曲梁的修正系数
A5.3试样加力后应在4小时内做间漫试验。试样周期沉漫于试验溶液中,每周期内沉漫于溶液10分钟,在空气中暴露干燥50分钟。不同合金的试样不允许共用同一槽溶液。试样应避免互相接触。A5.4每天定期补充挥发掉的水份,每周更换一次溶液。A5.5用肉眼或借助放大镜观察。记录试样腐蚀破裂时间。A5.6试验结束附,为了便于观察,可用下列清洗剂清洗试样。清洗剂「:
HsPo,(d=1.69)50ml
洁净为止
清洗剂1;
HNO,(d=1.42)
小提示:此标准内容仅展示完整标准里的部分截取内容,若需要完整标准请到上方自行免费下载完整标准文档。
GJB 1057-90
LC9铝合金过时效锻件
Overaging forging of aluminium alloy(L C9)1991—01-26发布
1991-06—01实施
国防科学技术工业委员会
中华人民共和国国家军用标准
LC9铝合金过时效锻件
Overaging forging of aluminium alloy(LC9)1主题内容与适用范围
GJB1057-90
本标准规定了LC9铝合金过时效锻件的品种,技术要求、质量控制、试验方法、检验规则及包装、标志、运输和贮存等。本标准适用于具有良好抗应力腐蚀性能的LC9铝合金过时效自由锻件和模锻件。2引用标准
GBn223
GB3199
GB3246
GB6519
铝合金锻件
金属拉伸试验方法
金属布氏硬度试验方法
铝及铝合金加工产品的包装、标志、运输、贮存铝及铝合金加工制品显微组织检验方法铝及铝合金加工制品低倍组织检验方法变形铝合金超声波检验方法
GB6987.1~6987.21铝及铝合金化学分析方法GB8545
GB/T12966
3产品分类
供应状态
铝及铝合金模锻件的尺寸偏差及加工余量铅合金电导率涡流测试方法
锻件以固溶热处理人工过时效状态供应。状态标记为CGS1或CGS3。最大厚度处的三个方向(纵、横、高)尺寸均大于80mm的锻件,呈热锻状态供应。其热处理由需方或委托供方经粗加工后进行。
3.2类别
锻件按使用要求分为1、Ⅱ、函三类,并在图样上注明。未注明者为耳类。3.3尺寸及允许偏差
3.3.1锻件的几何形状和尺寸应符合供需双方议定的图样或合同要求3.3.2锻件的加工余量和尺寸偏差应符合GB8545或供需双方议定的图样或技术协议。3.4标记示例
国防科学技术工业委员会1991一01一26发布1991—06-01实施
GJB 1057-90
用LC9铝合金锻造的,以固溶热处理人工过时效状态CGS1供应的J8一114Ⅱ类自由锻件标记为:
自由锻件J8-114LC9CGS1I类GJB1057-90技术要求
4.1化学成分
锻件的化学成分应符合表1的规定。表1
主要成分,%
4.2热处理制度
4.2.1固溶热处理温度为465士5℃,其它按现行工艺。4.2.2
过时效制度应符合表2的规定。
时效阶段
第一阶段
第二阶段
第一阶段
第二阶段
注:时效保温时间按金具实际温度达到时效温度下限起计算。4.3力学性能
锻件的室温力学性能应符合表3的规定。4.4抗应力腐蚀性能
4.4.1锻件的电导率应符合表4的规定。Fe
杂质,不大于,%
加热温度,℃
110±5
177±5
110±5
165±5
保温时间,h
8~10
8~10
4.4.2锻件按表5规定的试验应力和时间进行应力腐蚀试验后应无应力腐蚀破裂现象。4.5超击波探伤
4.5.1锻件的超声波探伤应在固溶热处理人工过时效后进行。热锻(R)状态交货的锻件探伤应由供需双方议定,并在图样上注明。2
模锻件
自由锻件
模锻件
自由锻件
伸长率
规定残余
伸长应力
GJB1057-90
力学性
能,不小于
规定残余1
伸长率
伸长应力
注热慢(R)状态供应的锻件,其试样经热处理后的力学性能应符合表3的规定。表4
电导率,MS/m
取样方向
高向(ST)
力学性能
满足本标准要求
满足本标要求,但纵向
0.0.2≤467N/mm2
满足本标准要求,但纵向
Or0. 2>467N/mm2
任何情况
满足本标准要求
任何情况
试验应力,N/mm2
伸长率
10/1000/30
不台格
不合格
试验时间,d
4.5.2需超声波探伤的、Ⅱ类锻件的探伤级别和部位应在图样上注明,1类锻件不做超声波探伤。
GJB 1057-90
4.5.3超声波探伤分A,B两级,其允许的缺陷值应符合表6的规定。表6
单个缺陷
当量平底
孔直径
多个缺陷
每个缺陷当
量平底孔直径
注:当量平底孔直径为记录直径4.6显微组织
锻件的显微组织不允许过烧。
4.7低倍组织
中心距
长条形缺陷
缺陷任何部位反
射的当量平底孔直径
4.7.1模锻件的流线应顺着受检截面的外形分布。不允许有穿流和严重涡流,流线应符合首批试制件或供需双方认可的低倍标样图片。4.7.2低倍组织为充分变形组织,并应符合首批试制件或供需双方认可的低倍试样图片。4.8表面质量bZxz.net
4.8.1自由锻件不蚀洗,其表面不应有裂纹和折选,如有,应清除。其它缺陷深度(包括清除处)应保证锻件留有三分之一的名义加工余量。4.8.2模锻件需经蚀洗。待加工锻件表面的裂纹、折迭和腐蚀斑痕必须清除。起皮、气泡、碰伤、压入物等其它缺陷可进行检验清理,但应保证锻件留有三分之一的名义加工余量。非加I锻件表面的裂纹及影响使用的其它缺陷,应清除,清除缺陷的部位应保证模锻件的单面极限尺寸。
5质量控制
5.1.锻件用坏料应符合有关标准或供需双方协议。5.2供方提供的首批试制件经需方复验鉴定后,如主导工艺(毛料选择、响锻件组织和性能的锻造及热处理工艺制度》需要变更时,其试验总结和工艺规范等技术文件必须经供方总工程师(或总工艺师)审批,并通知需方认可。如三个月内不答复则表示认可。5.3供方有责任保存锻件质量跟踪所必要的原始记录(如工艺卡片、组织性能报告),保存期不少于7年。
5.4需方认为必要时,可派代表到生产厂家抽查主导工艺,以确定其是否符合本标准的要求。6试验方法
6.1锻件的化学成分仲裁分析方法按GB6987.1~6987.21的规定进行。4
GJB 1057-90
6.2件的室温拉伸性能试验方法按GB228的规定进行。6.3搬件的布氏硬度试验方法按GB231的规定进行。6.4锻件的电导率测试方法按GB/T12966的规定进行。6.5锻件的应力腐蚀试验方法按附录A(补充件)的规定进行。6.6锻件的超声波探伤方法按GB6519的规定进行。6.7锻件的显微组织检验方法按GB3246的规定进行。6.8锻件的低倍组织检验方法按GB3247的规定进行。6.9自由锻件的外形尺寸用钢板尺、卷尺等专用工具或简易样板检测。模锻件的外形尺寸用划线法或专用样板工量具及精度不低于0.02mm的卡尺检测,7检验规则
7.1检查和验收
锻件应由供方技术监督部门验收,并保证产品质量符合本标准要求。7.2组批
锻件应成批提交验收,同批次锻件应由同一合金,同一熔次、同一规格、同一热处理炉次的组成。当设备条件受限时,一批也可由几个固溶热处理炉次的组成。每批重量不限。7.3检验项目和取样数量
锻件的检验项目和取样数量应符合表7的规定。7.4重复试验
7.4.1低倍组织试验不合格时,1类锻件不允许重复试验,I、I类锻件允许供方重复试验,需方不复验。
7.4.2锻件的室温力学性能不合格时,允许从该试样的相邻部位或另一锻件取双倍数量试样复验。仍有个试样不合格时,则该批(炉)次报废或做重复热处理。100%取拉伸试样的锻件,按件报废。
检验项目
表面质量几何
尺寸印记
化学成分
力学性能
拉伸性能
每熔次取1个试样
有试验余料的懒件取
100%,每件取1个或2个
试样,无试验余料的锻件,
按固溶热处理炉次每炉取1
件、每件取1个或2个试样
每熔次取1个试样
按固溶热处理炉次每炉
取1件,每件1个或2
个试样
每熔次取1个试样
检验项目
抗应力腐
蚀性能
电导率
应力腐蚀
显徽组织
低倍组织
超声波探伤
GJB 1057-90
续表?
首批或有重大工艺变更时
取1件,每件取5个试样
有试验余料的锻件取
100%,每件取1个试样,无
试验余料的锻件,按固溶热
处理炉次每炉取1件,每件
取1个试样
每批取1件,每件取1个试
首批或有重天工艺变更
时取1件,每件取5个试
每固溶热处理炉次取1
件,每件取1个试样
每批取1件,每件取1个
每固溶热处理炉次取1
件,每件取1个试样
首批或有重天工艺变更
时取1件,每件取1个试
7.4.3当锻件的电导率可疑时,可从该热处理炉(批)次中取一个试样做固溶热处理(固溶热处理温度为465士5℃,保温30分钟,在室温水中淬火)后,于15分钟内测电导率,若测量结果与原值之差不小于3.5Ms/m,则锻件合格,反之不合格。7.5重复热处理
7.5.1当力学性能、电导率或应力腐蚀试验结果不合格时,允许补充时效或重复热处理。其重复热处理次数不得超过两次,补充时效不算重复热处理。7.5.2重复热处理后必须重新按表7规定检测显微组织、力学性能和抗应力腐蚀性能。7.6其他
7.6.1纵向拉伸性能合格时,硬度试验结果不做为报废的依据。7.6.2对于超声波探伤所能反映的一些缺陷(如包括氧化膜在内的非金属夹杂、气孔、裂纹)按超声波探伤结果验收,低倍组织检查结果不作为报废依据。7.6.3以热锻(R)状态供应的锻件,取试块进行热处理,也可锻成相应的锻造试样进行热处理。热处理后的试块的室温力学性能及抗应力腐蚀性能应符合本标推的规定。8标志、包装、运输、贮存
8.1标志
锻件的标志应符合GB3199的要求。每个检验合格的锻件上应按图样标明的位置打上卜列标记:
a.供方质量监督部门的印记;
b.合金牌号及供应状态;
c.模锻件或自由锻件代号:
d熔次号、批号、1类锻件的顺序号:6
e:固溶热处理炉次号。
8.2包装、运输和贮存
GJB1057→90
8.2.1锻件的包装、运输和贮存应符合GB3199的规定8.2.2自由锻件可裸件交货,重量小于10kg的自由锻件可装箱交货,有特殊要求时,由供需双方议定。
8.2.3全加工模锻件可简易包装交货。精密模锻件和局部不加工的模锻件涂油包装。有特殊要求时,由供需双方议定。
8.3质量证明书
每批锻件应附有符合本标准要求的质量证明书,其上应注明:a.供方名称:
b,合金牌号及状态代号;
c.锻件代号:
d.熔次号、批号、固溶热处理炉次号:e.重量和件数?
f、化学成分、力学性能、电导率、应力腐蚀、超声波探伤、显微组织、低倍组织等试验结果;多,技术监督部门的印记;
h.本标准号
i.包装日期。
A1概述及适用范围
GJB1057-90
附录A
C环形试样恒应变应力痴蚀试验方法(补充件)
本方法为恒应变应力腐蚀试验方法,用于检验铝合金材料对应力腐蚀的敏感性。本方法用腐蚀破裂时间来评定材料的耐应力腐蚀破裂性能,主要适用于高强度铝合金。A2试样制备
A2.1取样方法
A2.1.1对于板、带材,C环的取向应使主应力方向(平行于加力螺栓)与短横向平行。A2.1.2对于锻件,C环的取向应使主应力方向与流线相垂直(图A1)。A2.1.3对于管、棒材,可沿纵向直接切取。A2.2试样加工
A2.2.1试样规格由试验者依具体情况而定,但须保证试样的直径为16~32mm,且径厚比在11~16范围内。试样的精加工应在热处理后进行,以免产生较大的残余应力。试样主表面的粗糙度不得大于0.8um。试样不得有划痕、凹坑、毛刺等缺陷。加工过程中应避免试样产生塑性变形。
A2.2.2试样的型式如图A2所示。A2.2.3每种试验条件应至少取5个平行试样。A3表面制备
用有机溶剂(如汽油和酒精)去除试样表面的油污。A4试验条件
A4.1试验溶液
A4.1.1配制溶液用的容器,可用硬塑料板、玻璃塘瓷等情性材料制做,试验溶液为3.5%NaC1水溶液,pH值控制在6.4~7.2之间(用稀NaOH水溶液或稀HC1水溶液调节)。S
试样的制取位置
GJB1057-90
山股小1910.,
图A2C环形应力腐蚀试验
A4.1.2配制溶液所需试剂为化学纯(cp)级以.b,水为蒸馏水或去离子水。A4.2试验温度
如无特别规定,试验温度取27℃C,温度变化范围为士1℃C。A4.3试验湿度
应尽量控制试验空间的相对湿度在45士6%范围内。A4.4试验时间
试验时间依材料的技术条件面定,一般在20~~90天。A4.5试验应力
试验应力按材料的技术条件确定。A5试验程序
A5.1采用与试验合金同系的材料做螺栓、螺母。扭紧拉力螺栓,即可使C环处表面受到拉应力作用。
C环的径向变化量按下式计算(C环直径在加力螺栓方向上测量,精度应达到士0.01mm):
ODf=OD-
4=fnD2/AEtz
式中OD—加力前C环的外径,mm;ODf—加力后C环的外径,mm;
A一c环的径向压缩量,mm:
一C环的中径(D=OD-t),mm;
E-一材料的弹性模量,N/mm\
t-c环的壁厚,mm;
Z—曲梁修正系数(参见图A3)
f—试验应力N/mm\。
GJB1057--90
A5.2试样加力后要用耐水涂料对螺栓、螺母与试样的接触部位进行封闭。试验前用蘸有有机溶剂的棉球擦拭试样受力表面,以除去可能沾染的油污。1.00
图人3弯曲梁的修正系数
A5.3试样加力后应在4小时内做间漫试验。试样周期沉漫于试验溶液中,每周期内沉漫于溶液10分钟,在空气中暴露干燥50分钟。不同合金的试样不允许共用同一槽溶液。试样应避免互相接触。A5.4每天定期补充挥发掉的水份,每周更换一次溶液。A5.5用肉眼或借助放大镜观察。记录试样腐蚀破裂时间。A5.6试验结束附,为了便于观察,可用下列清洗剂清洗试样。清洗剂「:
HsPo,(d=1.69)50ml
洁净为止
清洗剂1;
HNO,(d=1.42)
小提示:此标准内容仅展示完整标准里的部分截取内容,若需要完整标准请到上方自行免费下载完整标准文档。

标准图片预览:
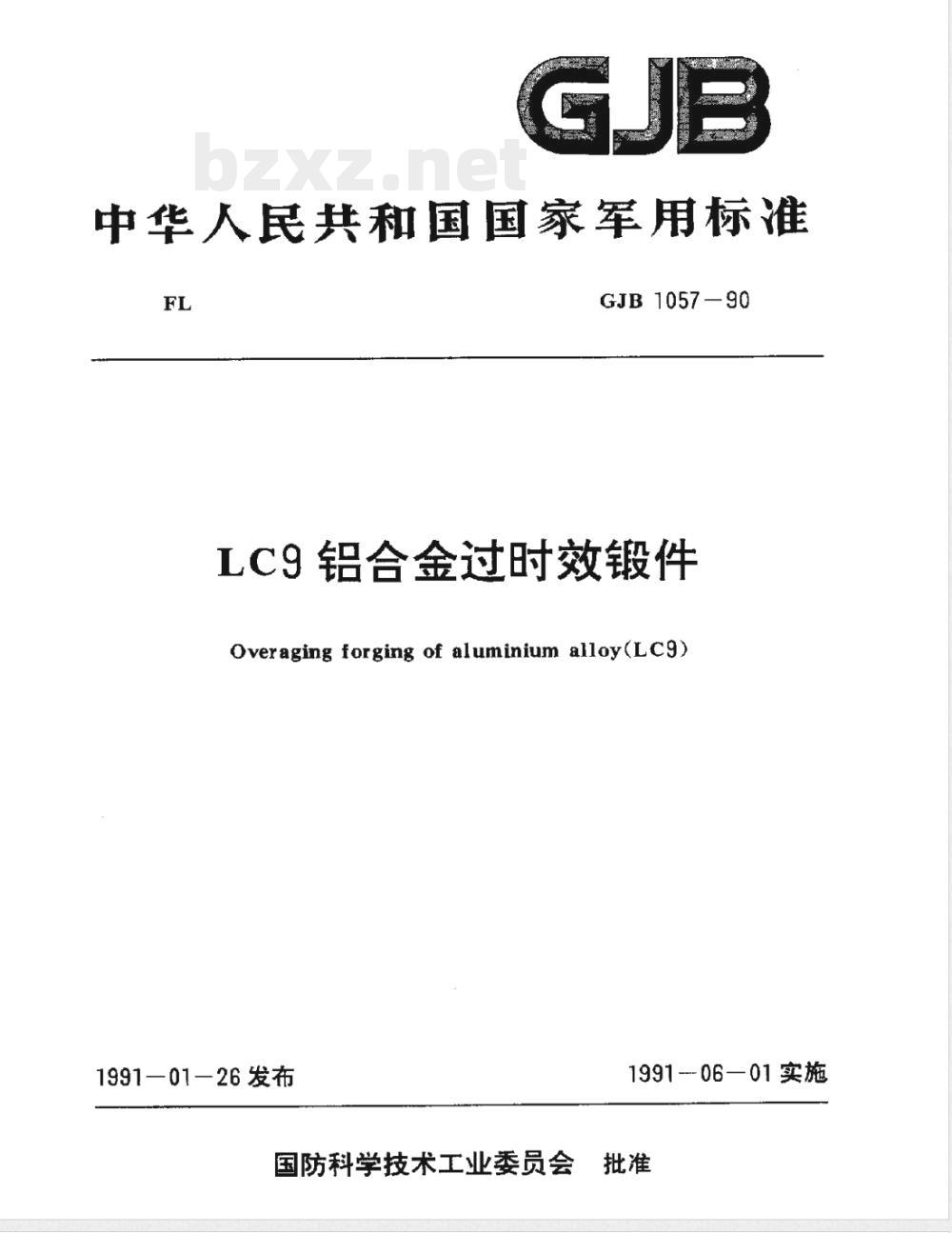
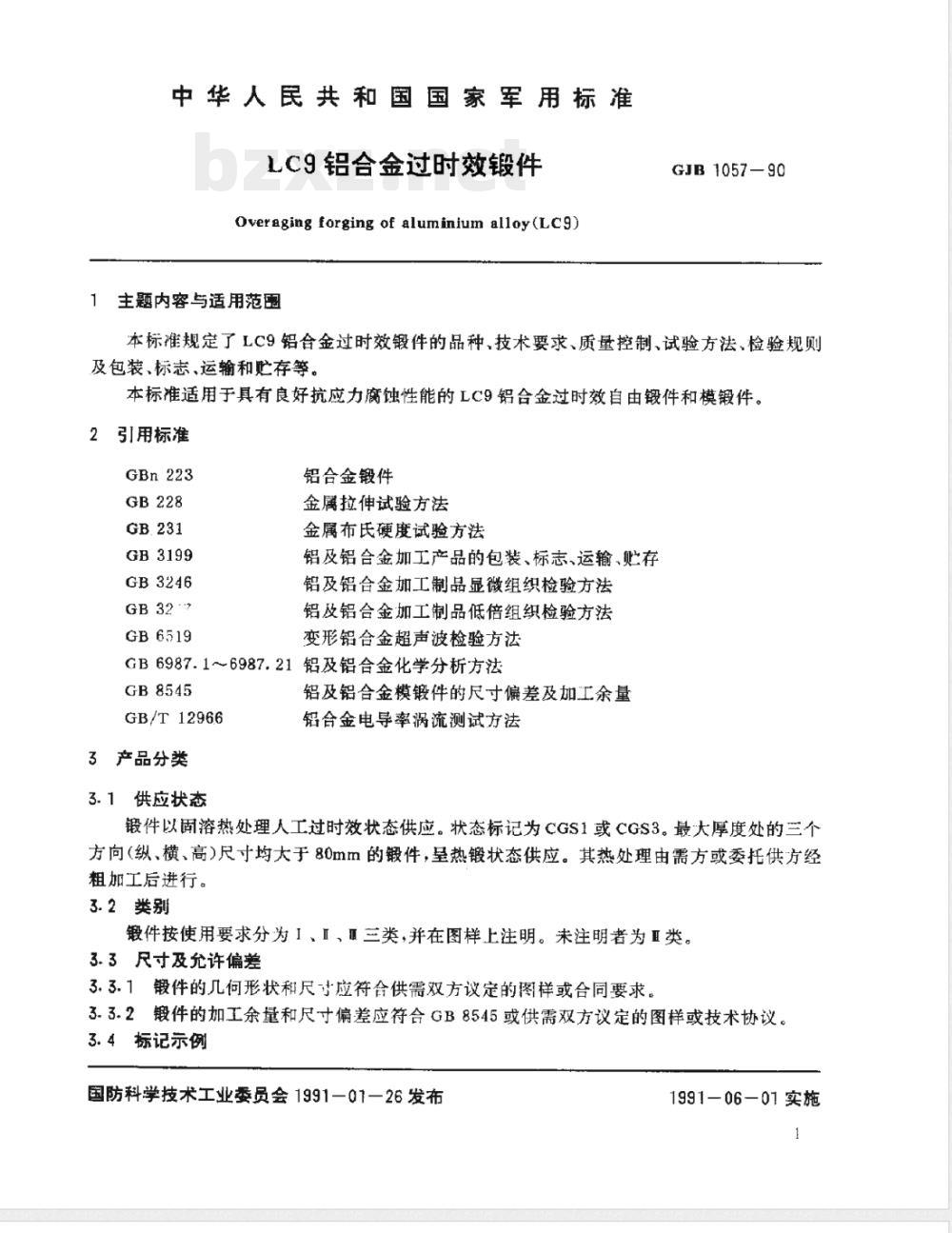
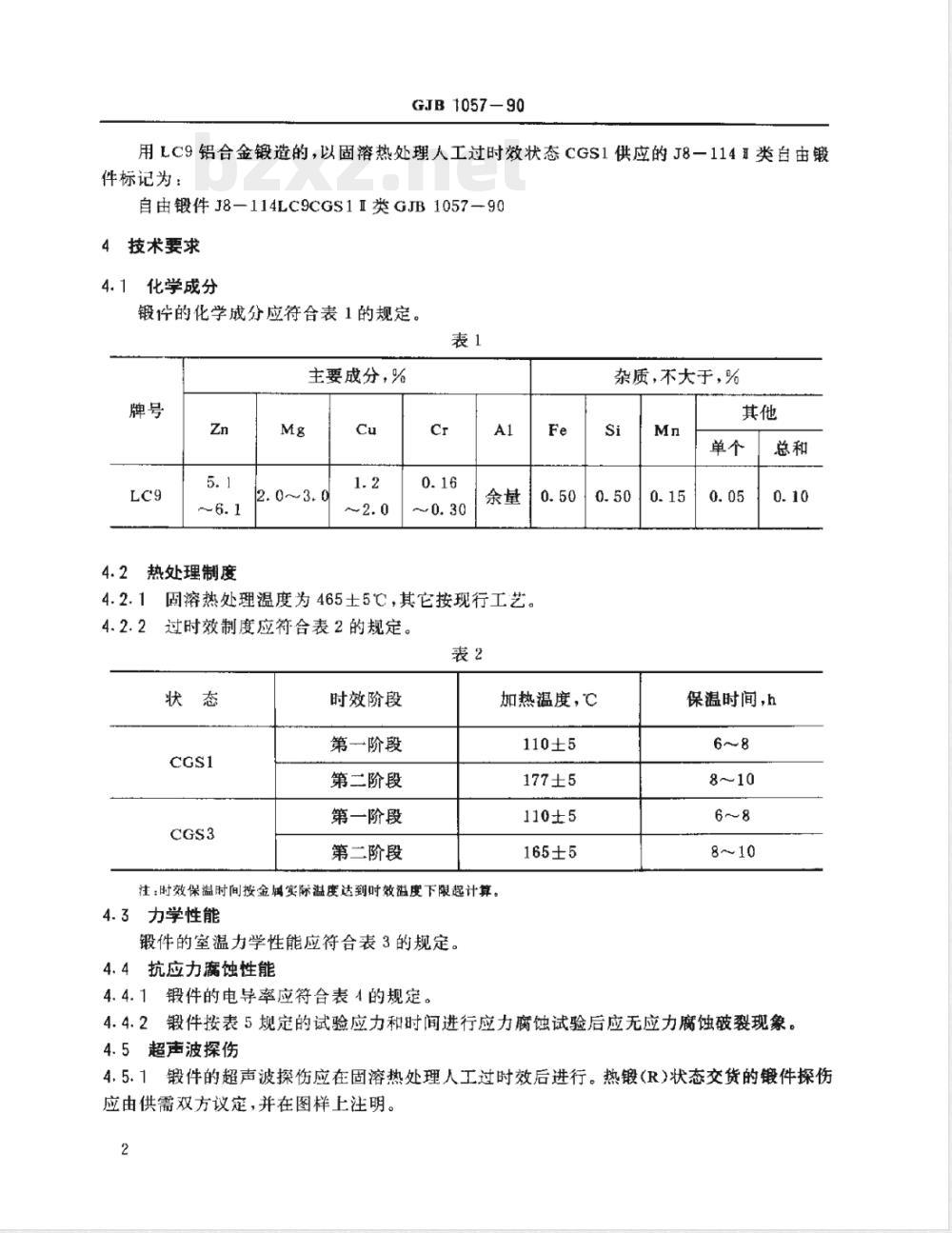
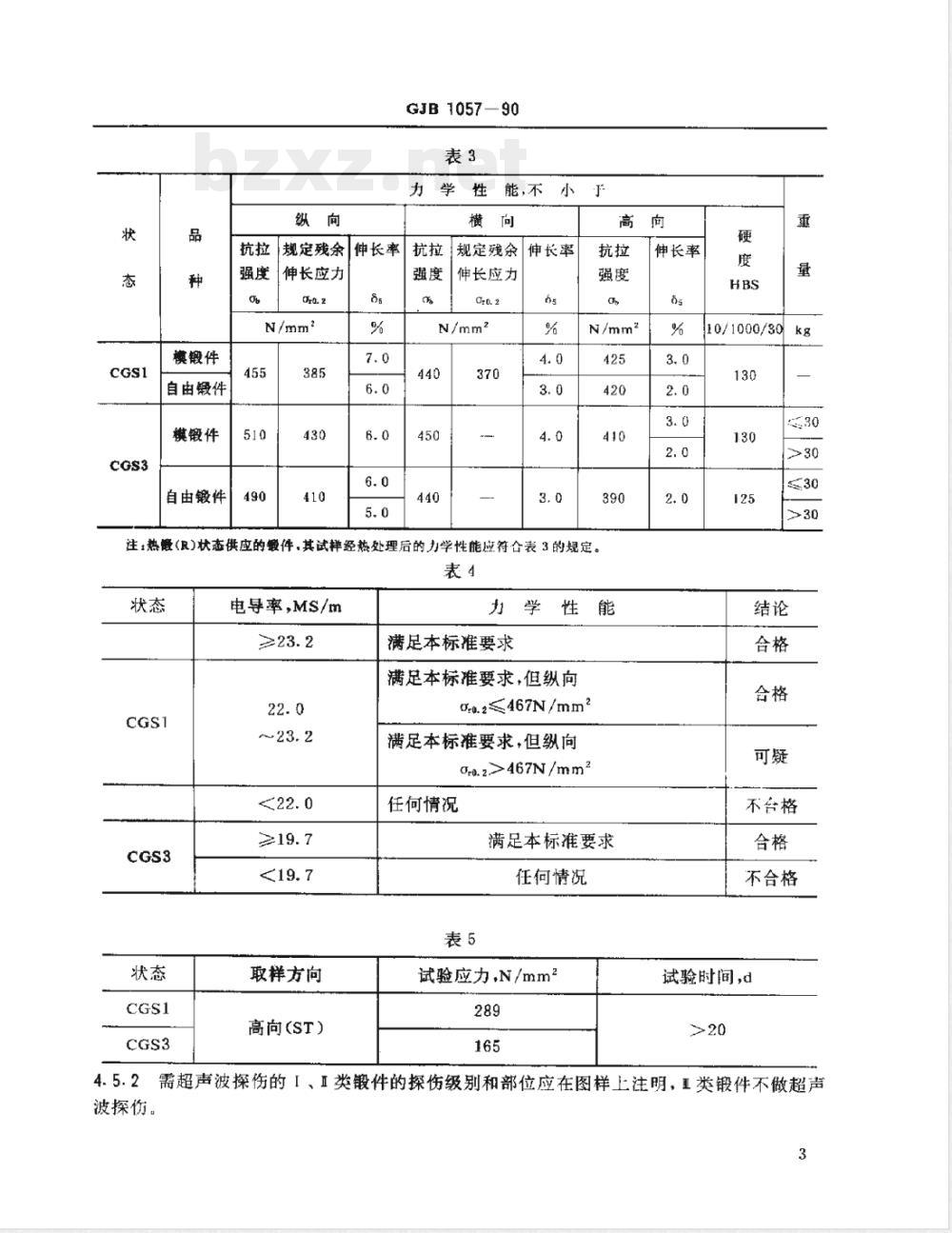
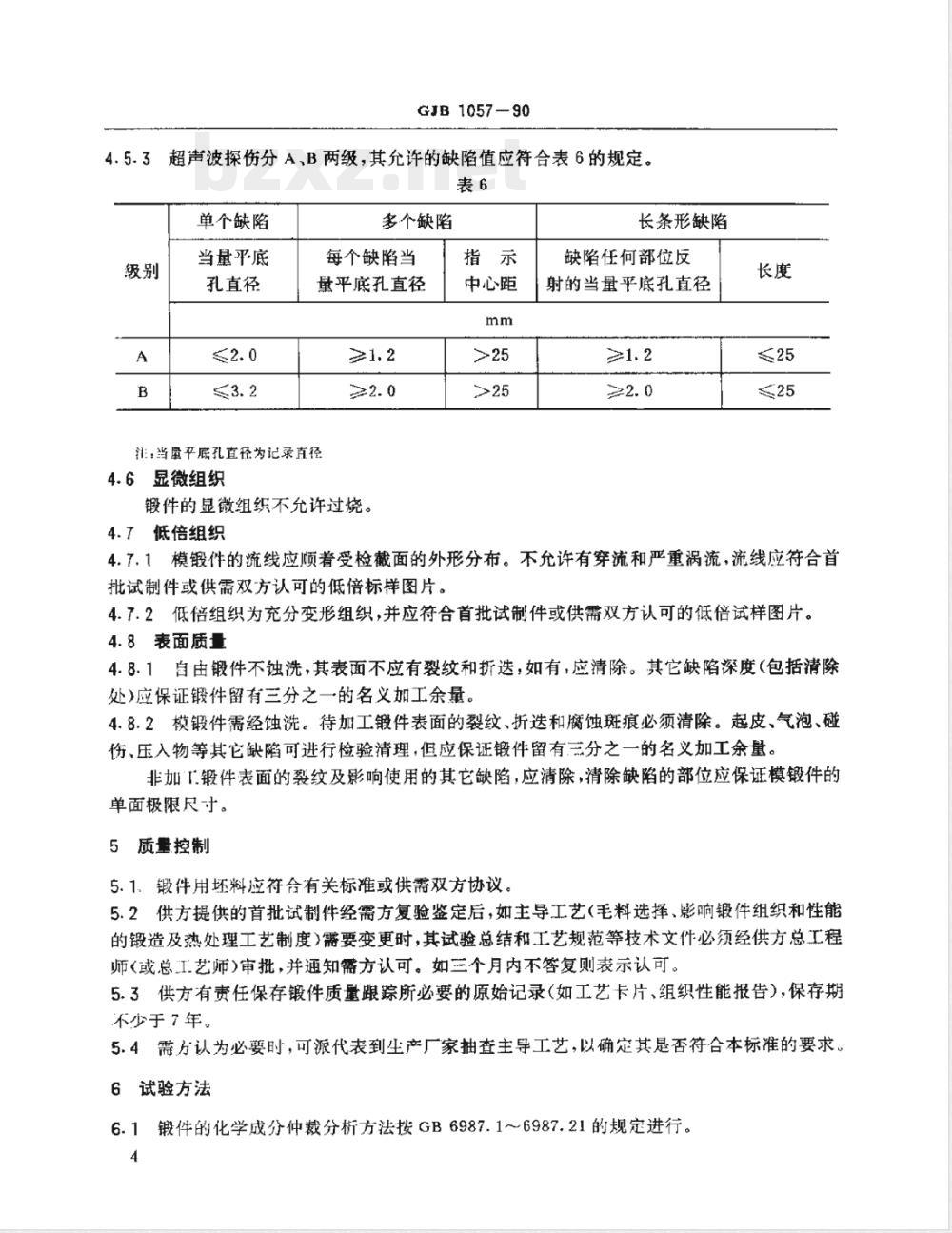
- 其它标准
- 热门标准
- HG/T3766-2004 炔螨特乳油
- QX/T286-2015 15个时段年最大降水量数据文件格式
- QX/T219-2013 空气流速计量实验室技术要求
- QX/T285-2015 电离层闪烁指数数据格式
- QB/T4155-2010 自动号码机
- QX/T294-2015 太阳射电流量观测规范
- QX/T217-2013 大气中氨(铵)测定靛酚蓝分光光度法
- QX/T222-2013 气象气球浸渍法天然胶乳气球
- QX/T158-2012 气象卫星数据分级
- QXZW0001S-2016 广汉喜之味食品有限公司 半固态复合调味料(含油型)
- QX/T174-2012 大气成分站选址要求
- QX/T159-2012 地基傅立叶变换高光谱仪大气光谱观测规范
- QJH001-2014 地面清洁工具企业标准
- QB/T2564.11-2015 螺钉旋具 Z型一字槽螺钉旋具
- QX/T352-2016 气象信息服务单位服务文件归档管理规范
- 行业新闻
请牢记:“bzxz.net”即是“标准下载”四个汉字汉语拼音首字母与国际顶级域名“.net”的组合。 ©2009 标准下载网 www.bzxz.net 本站邮件:bzxznet@163.com
网站备案号:湘ICP备2023016450号-1
网站备案号:湘ICP备2023016450号-1