- 您的位置:
- 标准下载网 >>
- 标准分类 >>
- 机械行业标准(JB) >>
- JB/T 5000.12-2007 重型机械通用技术条件 第12部分:涂装
标准号:
JB/T 5000.12-2007
标准名称:
重型机械通用技术条件 第12部分:涂装
标准类别:
机械行业标准(JB)
标准状态:
现行-
发布日期:
2007-08-28 -
实施日期:
2008-02-01 出版语种:
简体中文下载格式:
.rar.pdf下载大小:
706.57 KB
标准ICS号:
机械制造>>无屑加工设备>>25.120.20轧制、挤压和拉制设备中标分类号:
冶金>>冶金机械设备>>H90冶金机械设备综合
替代情况:
替代JB/T 5000.12-1998

点击下载
标准简介:
标准下载解压密码:www.bzxz.net
JB/T 5000的本部分规定了重型机械产品及其零部件的涂装技术要求及检测要求。本部分主要适用于钢铁产品的表面涂装。凡合同文件无特殊要求的,其产品表面的涂装均应符合本部分的规定。 JB/T 5000.12-2007 重型机械通用技术条件 第12部分:涂装 JB/T5000.12-2007

部分标准内容:
ICS25.120.20
备案号:21706-2007
中华人民共和国机械行业标准
JB/T5000.12—2007
代替JB/T5000.12—1998
重型机械通用技术条件
第12部分:涂装
Heavy mechanical general technigues and standardsPart12:Paint
2007-08-28发布
2008-02-01实施
中华人民共和国国家发展和改革委员会发布前言
1范围
2规范性引用文件
3术语和定义
4技术要求..
4.1涂装前的表面处理,
4.2机器产品的防腐蚀涂层设计
4.3机器产品特殊部位的涂装要求.4.4涂漆颜色要求,
4.5涂装施工要求
5涂装质量控制与检测
6涂层脱离底材的抗性评定
附录A(规范性附录)酸洗
A.1适用范围及质量要求
A.2酸洗前的表面处理.
A.3酸洗方法及要求
A.4安全措施,
附录B(规范性附录)涂层耐久性目
附录C(规范性附录)漆膜划格试验结果分级.表1除锈方法、除锈等级及适用范围..表2机器产品的环境腐蚀类别..
表3常用涂料推荐品种..
表4机器产品的推荐面漆颜色
表5机器产品特殊部位的推荐面漆颜色表6八种基本识别色及其色标
表B.1涂层耐久性与预期防腐年限的对应关系表B.2涂层厚度与预期防腐年限的对应关系试验结果分级
JB/T5000.12—2007
JB/T5000.12--2007
JB/T5000《重型机械通用技术条件》分为15部分第1部分:产品检验;
第2部分:火焰切割件;
第3部分:焊接件:
第4部分:铸铁件;
第5部分:有色金属铸件;
第6部分:铸钢件;
第7部分:铸钢件补焊;
第8部分:锻件;
第9部分:切削加工件;
第10部分:装配;
第11部分:配管;
第12部分:涂装:
第13部分:包装:
-第14部分:铸钢件无损检测;
第15部分:锻钢件无损检测。
本部分为JB/T5000的第12部分。本部分代替JB/T5000.12—1998《重型机械通用技术条件涂装》。本部分与JB/T5000.12—1998相比,主要变化如下:-取消了原表1中的酸洗代号“Be”,同时引用了石油行业标准SYT0407中关于酸洗的内容(见附录A)。
取消了原表2,增加了机器产品环境腐蚀类别的划分、涂层耐久性的划分以及涂层厚度与预期防腐年限的对照等内容(符合ISO12944-2的相关规定),见4.2.1及附录B。明确规定了产品设计工程师与产品防腐蚀工程师在产品防腐蚀工作中的职责和分工。见4.2.2和4.2.3。
增加了钢制容器内部、工矿车辆铸锻构件、高强度螺栓连接件结合面等的涂漆要求,见4.3.5、4.3.6、4.3.7。
-强调了涂料质量检测部门和相关人员的职责,见5.1、5.2、5.3。增加了划格法评定涂层脱离底材的抗性的内容(符合GB/T9286)。将“涂层附着力”改称为“涂层脱离底材的抗性”,使与GB/T9286保持一致。见第6章及附录C。删除了原标准中的附录A。
本部分的附录A、附录C为规范性附录,附录B为资料性附录。本部分由中国机械工业联合会提出。本部分由机械工业冶金设备标准化技术委员会归口。本部分起草单位:大连重工·起重集团有限公司。本部分主要起草人:关明、张连滨。本部分所代替标准的历次版本发布情况:JB/T5000.12—1998。
1范围
JB/T5000.12—2007
重型机械通用技术条件第12部分:涂装JB/T5000的本部分规定了重型机械产品及其零部件的涂装技术要求及检测要求。本部分主要适用于钢铁产品的表面涂装。凡合同文件无特殊要求的,其产品表面的涂装均应符合本部分的规定。
2规范性引用文件
下列文件中的条款通过JB/T5000本部分的引用而成为本部分的条款。凡是注日期的引用文件,其随后所有的修改单(不包括勘误的内容)或修订版均不适用于本部分,然而,鼓励根据本部分达成协议的各方研究是否可使用这些文件的最新版本。凡是不注日期的引用文件,其最新版本适用于本部分。GB2893安全色(GB/T2893-—2001,negISO3864:1984)GB/T5206.1色漆和清漆词汇第部分通用术语(GB/T5206.1-1985,eqvISO4618-11978)
GB/T5206.4色漆和清漆词汇第四部分涂料及涂膜物化性能术语(GB/T5206.4—1989,negISO4618-1:1984)
GB/T5206.5色漆和清漆词汇第五部分涂料及涂膜病态术语(GB/T5206.5-1991,neqISO4618-2:1984)
涂装作业安全规程涂漆工艺安全及其通风净化(GB6514—1995,neqNFPA33:1989)GB6514
工业管道的基本识别色、识别符号和安全标识GB/T7231
涂装作业安全规程涂漆前处理工艺安全及其通风净化GB7692
GB/T8264
涂装技术术语
GB/T8923
GB/T9286
SY/T0407
涂装前钢材表面锈蚀等级和除锈等级(GB/T8923--1988,eqvISO8501-1:1988)色漆和清漆漆膜的划格试验(GB/T986-1998,eqvISO2481:1992)涂装前钢材表面预处理规范
GSB05-1426漆膜颜色标准样卡
ISO12944-2
色漆及清漆防护漆体系对钢结构腐蚀防护第2部分:环境分类ISO12944-5
3术语和定义
色漆及清漆防护漆体系对钢结构腐蚀防护第5部分:防护漆体系GB/T5206.1、GB/T5206.4、GB/T5206.5、GB/T8264中确立的术语和定义适用于本部分。4技术要求
4.1涂装前的表面处理
所有用于设备制造的钢铁原材料,涂漆前均需进行表面除锈处理。所有需要进行涂装的钢铁原材料或制件表面,在涂漆前必须将铁锈、氧化皮、油脂、灰尘、泥土、盐和污物等清除干净。
4.1.1除锈前,应先用有机溶剂、碱液、乳化剂、蒸汽等除去钢铁表面的油脂、污垢。4.1.2钢铁表面除锈方法、除锈等级及适用范围见表1。表1中Sa及St各等级的除锈要求及评定方法按GB/T8923的规定。
JB/T5000.12--2007
酸洗除锈方法及处理要求详见附录A。4.1.3焊接件在组装焊接后需要进行热处理的,应将除锈工序放在热处理之后进行。表1除锈方法、除锈等级及适用范围除锈方法
喷射或抛射
手工或动力
工具除锈
酸洗除锈
除锈等级
GB/T8923
Sa21/2
适用范围
辅助部件或辅助设备及用于轻度腐蚀性环境中的钢铁制件表面:与混凝土接触或理入其中的钢铁制件表面主要部件或主要设备及用于腐蚀性较强的环境中的钢铁制件表面长期在潮湿、潮热、盐雾等环境下作业的钢铁制件表面;与高温接触并且需要涂耐热漆的钢铁制件表面与液体介质或腐蚀性介质接触的表面,如油箱、减速机箱、水箱等内表面与高温接触但不需要涂耐热漆的钢铁制件受设备限制,无法进行喷丸除锈的特大钢铁构件;钢铁构件形状特殊无法进行喷丸除锈的部位设备上的各类钢制管道;不能喷丸的薄板件(壁厚小于5mm);结构复杂的中、小型零件
4.1.4喷(抛)丸除锈用的磨料可采用铸铁(钢)丸粒、钢丝段、铜矿渣等,所用弹丸应带有棱角、铸、锻件用的钢铁弹丸直径不得大于2mm;钢板及型钢用的钢铁弹丸直径为0.6mm~1.2mm;喷砂用的石英砂、铜矿渣直径不得大于2.5mm。处理后的表面粗糙度不得大于100μm。4.1.5经喷丸或手工除锈、动力工具除锈后的待涂表面,应立即涂底漆,其间隔时间不得大于6h(空气相对湿度人于70%的环境区域,其间隔时问不得大于4h)。酸洗除锈后经过磷化处理的待涂表面,涂底漆的间隔时间不得小于48h(在北方冬季寒冷的气候环境下,其间隔时间不得小于72h),涂漆前表面不得出现返锈和污染现象。
4.1.6用于制造机器构件的钢铁板材及型材,厚度大于5mm的,应预先进行喷(抛)丸除锈,除锈质量等级应达到Sa21/2级;厚度小于5mm的,可进行化学处理(酸洗、冲洗、中和、钝化或磷化等),其除锈质量等级应达到附录A的有关规定,并在规定的时间范围内涂保养底漆(车间底漆)。预处理时的漆膜厚度及涂料选择推荐如下:a)推荐漆膜(干膜)厚度:15um~25um。b)推荐涂料品种:无机硅酸锌(车间)底漆、环氧底漆、环氧富锌底漆、磷酸锌底漆、铁红环氧脂底漆等。
c)所用的底漆必须是产品配套漆系中的品种或与配套漆系中的底漆相适应的漆种。4.2机器产品的防腐蚀涂层设计
4.2.1机器产品的环境腐蚀类别见表2。常用涂料推荐品种见表3。推荐面漆颜色见表4。涂层耐久性与预期防腐年限及涂层厚度的对应关系见附录B。4.2.2产品设计工程师应根据表2确定机器产品的环境腐蚀类别,根据表4选择产品的主体面漆颜色并将所确定的内容在产品图样或技术文件中予以注明。如:“产品使用环境类别为C3,面漆颜色为59橘黄(YR04)”。
4.2.3产品防腐蚀工程师应根据产品设计工程师对产品环境腐蚀类别、主体面漆颜色的要求,参考附录B及表3的有关规定,进行产品的防腐蚀设计。该设计包括:a)确定涂料配套漆系(涂料品种、涂层厚度);b)确定产品主体及各部位、各系统颜色:2
c)编制“产品涂装工艺说明”。表2机器产品的环境腐蚀类别
典型环境
空气洁净、有保温设施的建筑物内部(室内)边远地区,低污染区域
城市及工业环境。二氧化硫含量、湿度为中等程度的生产区域工业及沿海区域、化工厂
高湿度的工业区域及严酷环境
高盐度的海洋、近海、港湾、沿海区域注:本表中的类别及典型环境的划分符合ISO12944-2的规定。表3常用涂料推荐品种
中间漆
耐油漆
耐高温漆
耐潮湿漆
推荐品种
铁红醇酸底漆、铁红环氧脂底漆、硅酸锌防锈漆、磷酸锌底漆、环氧富锌底漆等
环氧云母氧化铁漆,环氧中间漆、磷酸锌底漆等醇酸磁漆、氯化橡胶面漆、聚氨脂面漆、丙烯酸磁漆、醇酸铝粉漆、环氧面漆等
JB/T5000.12—2007
厚度要求
各种涂料的涂层厚度
(干膜),根据涂料配套漆
过氯乙烯油箱漆、环氧耐油漆、聚氨酯耐油漆,硝基内用磁漆(底、面系确定漆应配套,且涂层不易太厚)等无机硅酸锌底漆、有机硅耐热漆、醇酸铝粉漆、各色酮漆等氯化橡胶漆、焦油环氧沥青防锈漆等4.2.4所选定的涂料配套漆系中的所有涂料,原则上应是同一厂家或同一品牌的产品。4.3机器产品特殊部位的涂装要求4.3.1铆接件相互接触的表面,在连接前必须涂以厚度为30um~40um的底漆。所用涂料品种应是涂料配套漆系中的漆种。搭接边缘应用油漆、腻子或粘合剂封闭。在加工或焊接过程中损坏的漆面,应重新进行表面处理和涂装。
4.3.2不封闭的箱形梁、箱形结构的内表面、各类安全罩的内表面等,无特殊要求的,一般须涂60um~80um厚的底漆;封闭的箱形梁、箱形结构的内表面不涂漆。4.3.3装配后不能靠近、无法涂装的部位,应在装配前完成涂漆。4.3.4有涂漆要求的有色金属表面,应根据不同情况,选用相适应的底漆、面漆。如锌表面应选用磷化底漆或磷酸锌底漆等。面漆(或中间漆)要与底漆配套。4.3.5钢制容器内部的涂装(无人孔的除外),应根据容器内工作介质的性质选择油漆或涂硬膜防锈油。不锈钢容器不涂漆。
4.3.6工矿车辆、冶金车辆的碰头车钩以及转向架中的铸造侧架、铸造摇枕、车轮、轮轴等,如无特殊要求,应涂清油或清漆,涂层厚度不低于30μm。4.3.7高强度螺栓联接件结合面,应根据摩擦系数的不同或按图样要求,在喷砂后涂高固体份、高锌粉含量(80%)的无机富锌底漆(如Interzinc22*底漆),厚度为60um。或者涂刷两层过氯乙烯可剥清漆(两层之间贴一层纱布)加以保护,联接前再将可剥清漆剥除。必要时,表面还应使用薄铁皮加以覆盖。
4.3.8属下列情况之一的,不进行涂装。a)产品或部件与混凝土接触或埋人混凝土中的部位、紧贴耐火材料的部位;3
JB/T5000.12—2007
b)机械加工的配合面、工作面、摩擦面;c)配管的各种阀、泵及法兰表面;d)不锈钢制件表面;
e)钢丝绳、地脚螺栓及其底板;f)电镀表面、无特殊要求的有色金属表面;g)非金属制件表面;
h)电动机等外购机电配套件表面。4.4涂漆颜色要求
4.4.1机器产品的面漆颜色应符合合同要求。合同中无规定的,按表4的推荐选取颜色,4.4.2除用户有特殊要求外,“产品涂装工艺说明”中提到的油漆颜色,均应符合GSB05-1426中标示的颜色。
产品类别
热轧设备
冷轧设备
装卸机械
连铸设备
冶金机械
锻压机械
矿山设备
焦炉机械、煤气设备
工矿车辆
冶金车辆
破碎机械
造矿烧结设备
人造板设备
橡胶设备
水泥设备
表4机器产品的推荐面漆颜色
推荐面漆颜色
30淡绿(G02)、24潮绿(BG02)、28苹果绿(G01)、32中绿(G04)、31艳绿(G03)24湖绿(BG02)、28苹果绿(GO1)、40豆绿(GY01)、10天(酸)蓝(PB09)59橘黄(YR04)、60橘红(R05)、72中灰(B02)、57棕(YR05)28苹果绿(G01)、38纺绿(GY02)、银白、30淡绿(G02)28苹果绿(G01)、73淡灰(B03)、黑色28苹果绿(G01)、30淡绿(G02)、24潮绿(BG02)、32中绿(G04)、6海蓝(PB05)28苹果绿(G01)、40豆绿(GY01)、48淡黄(Y06)、60橘红(R05)、黑色72中灰(B02)、28苹果绿(G01)、38纺绿(GY02)、淡海(铁)蓝(B11)59橘黄(YR04)、60橘红(R05)、32中灰(B02)、黑色黑色
73淡灰(B03)
38纺绿(GY02)
24湖绿(BG02)
24湖绿(BG02)
73淡灰(B03)
机器产品的特殊部位按表5的规定选择面漆颜色表5机器产品特殊部位的推荐面漆颜色产品特殊部位名称
油箱、减速机内壁及其内部零件的涂漆表面栏杆、扶手
操纵室的顶棚及内壁
操纵室地板
盖板、走台板、销板、楼梯板
机械停止按钮、制动及停车装置的操纵手柄;机器转动部件的裸露部分,如飞轮、齿轮、带轮等的轮幅部分;指示器上各种表头的极限位置的刻度注:表中有关大红色的使用规定符合GB2893的相关规定。面漆颜色
奶油色(Y03)
黄色(Y06、07、08)
半光浅色漆
铁红色(R01)
与主机同色或绿色(GY02)
大红色(R03)
4.4.4有暂时或永久性危险的机械部位或装置,应涂以宽度约100mm、与水平面成45°斜角、颜色为黄、黑相间的“虎皮”状警示条纹。同一条棱线两侧的条纹倾斜方向应相反。如果表面面积较小,条纹4
宽度可以适当缩小,但黄条纹与黑条纹每种不得少于两条。JB/T5000.12-—2007
前述有暂时或永久性危险的机械部位或装置包括:各种机械在工作或移动时容易产生碰撞的部位,如移动式起重机的外伸腿、起重机的吊钩滑轮侧板、起重臂的顶端、四轮配重;平顶拖车的排障器及侧面栏杆;门式起重机门架下端;剪板机的压紧装置;冲床的滑块等。4.4.5机器产品配管的面漆颜色应与机器的面漆颜色相同。距机器1m以外的配管颜色,应符合表6关于基本识别色的规定。
表6八种基本识别色及其色标
输送介质种类
水燕气
酸或碱
可燃液体
其他液体
注:本表符合GB/T7231的规定。4.5涂装施工要求
4.5.1环境要求
基本识别色
色标(GSB05-1426)
4.5.1.1一般情况下,涂装施工环境温度不得低于5℃,相对湿度应不大于85%。对北方地区的冬季施工,应尽量选用适合低温下施工和固化的油漆。4.5.1.2雨、雪、雾天气及风力超过4级时,禁止在室外施工。待涂装表面有结箱、结露的,不许施工。Www.bzxZ.net
涂装及固化过程中,涂装件表面温度不得超过60℃。禁止漆膜在烈日下暴晒。4.5.1.3
4.5.1.4施工区域必须保持空气流通。涂装及固化过程中应无粉尘及其他异物飞扬。4.5.2施工要求
涂装时,应严格遵守各种涂料对温度、湿度等的要求,遵守重涂间隔时间及调配方法的有关4.5.2.1
规定。
施工前,如发现涂料出现胶化、结块等异常现象,应停止调配和施工。4.5.2.3
涂装施工过程中,应注意各种施工方法对漆膜的影响。要尽量保证漆膜的均匀,不可漏涂。对于边、角、夹缝、螺钉头、铆接缝、焊缝等部位要先涂刷,然后再大面积涂装。4.5.2.4对焊后或装配后无法涂漆的构件部位,应在焊前或组装前涂漆。4.5.2.5两种不同颜色的涂层交界处,其界面必须明显、整齐。4.5.2.6需经常拆装的零件,其相互连接处的油漆面必须平整。缝线应明显,不得出现漆膜崩落、界线不分或漆成一片等现象。
4.5.2.7喷涂施工时,应对产品不需涂装的部位进行遮盖,防止误涂。4.5.2.8机器产品表面是否需要刮腻子,应在图样或技术文件中注明。刮腻子时,应先涂底漆,底漆于燥后再进行刮腻子操作。刮腻子一般进行1次~2次,每次厚度约为0.5mm~1mm,局部最大总厚度不得超过5mm。腻子干燥后须对表面进行打磨,打磨后的腻子表面应平整、光滑、牢固、无裂纹。4.5.2.9机器产品的最后一遍面漆一般应在总装试车完成后再进行涂装。4.5.2.10对安装过程中损坏的漆膜应进行修补。修补前应对表面进行清理。修补部分对周围涂层的覆盖宽度应不少于50mm(损坏面积较小时,修补的面积应比损坏的面积大一倍以上)。修补应符合相关5
JB/T5000.12—2007
工艺或标准的规定。补漆部位的颜色、涂层厚度应与周围的颜色、涂层厚度一致。4.5.3涂装安全及通风要求
涂装预处理的施工安全及通风要求按GB7692的规定执行。涂装施工中的安全及通风要求按GB6514的规定执行。5涂装质量控制与检测
5.1涂料质量的检测按涂料说明书规定的方法进行。a)涂料说明书中规定的检测方法,必须符合相关国家标准的规定。b)对于配套漆系中的涂料,若其说明书中无检测项目或指标,而使用厂防腐蚀工程师认为确有必要了解的,则涂料供应商应无条件提供由国家质量技术监督部门出具的该项目或指标的检测报告。
5.2涂料供应商在向使用厂提供涂料时,必须附带本批次涂料的产品合格证和检测报告,否则涂料使用厂有权拒收。
5.3使用涂料的企业的质量管理部门,对涂料供应商提供的涂料产品质量负有日常监督职责。5.4涂料的调配应严格按照说明书的规定和要求进行。5.5施工时,应经常用湿膜测厚仪测定漆膜厚度,以便更准确地控制干膜厚度。5.6漆膜的干膜厚度检测,应在涂料说明书规定的干燥时间以外进行。5.7漆膜外观应满足以下要求:底漆、中层漆、面漆漆膜不允许有针孔、气泡、裂纹、咬底、渗色、漏涂、流挂、局部剥落等缺陷;面漆表面应平整均匀、漆膜丰满、色泽一致。检查方法经协商可采用肉眼或用五倍放大镜观察。
5.8涂层厚度的检测应在每一涂层干燥后进行。全部涂层涂装完毕后,再检测总厚度。检测方法是:用电磁式膜厚仪检测,每10m2(漆膜面积不足10m2的按10m2计)作为一处,管路等细长体每3m4m长作为一处,每处测3点~5点。每处所测各点厚度的平均值,不得低于规定涂层总厚度的90%,且不高于120%。每处所测各点厚度中的最小值不应小于规定涂层总厚度的70%。6涂层脱离底材的抗性评定
涂层脱离底材的抗性评定按以下方法进行:选六块规格为200mmX200mm的试板,经表面处理后,涂上与产品相同的涂层漆系。抗性评定在漆膜实干后进行(根据用户要求,可分层逐次评定或最终一次性评定),最终的评定经协商可采用画叉法或划格法进行。画叉法:用锋利的刀片或保险刀片在试板表面划一个夹角为60°的叉,刀痕要划至钢板,然后贴上宽度为25mm的专业压敏胶带,使胶带贴紧漆膜,然后用手迅速扯起,刀痕两边涂层被揭下的总宽度若不超过2mm即为合格。
划格法:按GB/T9286的规定进行评定。其评定结果应不低于附录C中的2级要求。A.1适用范围及质量要求
附录A
(规范性附录)
A.1.1本附录符合SY/T0407的规定,适用于钢材表面的酸洗处理,JB/T5000.12-2007
A.1.2可用化学和电解两种方法做酸洗处理。酸洗后钢材表面应没有肉眼可见的氧化皮、锈和旧涂层。A.1.3钢材表面的腐蚀程度应适合规定的涂装要求。A.1.4允许酸洗后的钢材表面在颜色的均匀性上受钢材的钢号、原始锈蚀程度、外形、轧制或加工痕迹以及腐蚀方式的影响。
A,2酸洗前的表面处理
A.2.1按照SY/T0407中规定的方法,除掉钢材表面上绝大部分油、油脂、润滑剂和其他污物(不包括氧化皮、氧化物和锈)。
A.2.2宜用工具除锈方法或喷(射)除锈方法(只要求达到Sa1级),除掉表面上大部分氧化皮、锈和旧涂层,以缩短酸洗除锈的时间。A.3酸洗方法及要求
A.3.1将钢材表面浸人常温下的硫酸、盐酸或磷酸溶液中,酸洗液中应加入足量缓蚀剂,以减少对基层金属的腐蚀,直到所有的氧化皮和锈全部除掉后,用淡水充分冲洗,再做钝化处理。A.3.2将钢材表面没人60℃以上、浓度为5%~10%(按重量计)的硫酸溶液中,酸洗液中应加人足量缓蚀剂,直至所有的氧化皮和锈全部除掉后再用淡水充分冲洗,最后将钢材表面放在80℃左右、含0.3%~0.5%磷酸铁、浓度为1%~2%(按重量计)的磷酸溶液中浸泡(1~5)min。A.3.3将钢材表面浸人(75~80)℃、体积分数为5%的的硫酸溶液中,酸洗液中应加人足量缓蚀剂,直至所有的氧化皮和锈全部除掉后再用(75~80)℃的热水冲洗2min,最后用85℃以上的钝化液浸泡2min以上。钝化液中应合有0.75%的重铬酸钠或0.5%左右的正磷酸。A.3.4将钢材放置在酸或碱电解槽中电解。电解中若工件作为阴极,应做适当处理以防止或减少氢脆现象的发生。如果在碱溶液中进行电解,电解后需用热水充分冲洗,接着在稀磷酸或稀重铬酸盐的溶液中浸泡,直至残留在表面上的碱迹全部清除为止。A.3.5酸洗处理应满足下列要求:a)硫酸槽中所溶铁的含量不应超过6%,盐酸槽中所溶铁的含量不应超过10%。b)必须用纯净的淡水或蒸馏水做溶液或冲洗液。在冲洗过程中,必须连续不断地向冲洗槽中注人清水,使每升水中携带的酸及可溶盐的总量不超过2g。c)从酸洗槽中取出的钢材应在该槽上方短时悬挂,沥净大部分酸洗液。d)酸洗后必须除掉有害的酸洗残渣、未发生反应的酸或碱、金属沉积物和其他有害污物。e)不应将酸洗后的钢材垒起来使表面互相接触,应在表面完全干燥后再重叠。f)必须在可见锈出现之前进行涂装。A.4安全措施
A.4.1应设置足够的通风设施,以保证工作人员的身体健康并应限制氢气的浓度,使其在爆炸的极限7
JB/T5000.12—2007
范围以下。
A.4.2操作人员应戴护目镜。
A.4.3工作人员必须穿戴橡胶围裙、橡胶靴子、橡胶手套。A.4.4酸洗和电解过程中所产生的废液的排放,应按国家现行的有关标准执行。A.4.5酸洗和电解过程所使用的化学药品的搬运和储存应符合国家现行的有关规定。A.4.6必须将浓酸缓慢地倒人水或稀酸中,而且应边倒边搅动。附录B
(规范性附录)
涂层耐久性
涂层耐久性与预期防腐年限及涂层厚度的对应关系符合ISO12944-5的规定。涂层耐久性与预期防腐年限的对应关系见表B.1。B.1
表B.1涂层耐久性与预期防腐年限的对应关系类别
高耐久性
中耐久性
低耐久性
B.2涂层厚度与预期防腐年限的对应关系见表B.2。预期防腐年限
预期防腐年限为15年以上
预期防腐年限为5~15年
预期防腐年限为5年以下
预期防腐年限的选择应符合合同的规定。合同无规定的,按低档年限(2~5)年进行涂层设计表B.2涂层厚度与预期防腐年限的对应关系环境类别
厚度范围μm
80~120
160~200
120~160
160~200
200~240
预期防腐年限
低(2~5年)
中(5~15年)
高(>15年)
低(2~5年)
中(515年)
高(>15年)
环境类别
厚度范围μum
160~200
200~240
240~320
240280
280~400
注:因C1为空气洁净的室内环境,所以在本表中未列出其涂层厚度与预期防腐年限的对应关系。附录C
(规范性附录)
漆膜划格试验结果分级
漆膜的划格试验结果分级符合GB/T9286的规定。漆膜的划格试验结果分级见表C.1。8
预期防腐年限
低(2~5年)
中(5~15年)
高(>15年)
低(2~5年)
中(5~15年)
高(>15年)
表C.1试验结果分级
切割边缘完全平滑,无一格脱落在切口交叉处有少许涂层脱落,但交叉切割面积受影响不能明显大于5%
在切口交叉处和/或沿切口边缘有涂层脱落,受影响的交叉切割面积明显大于5%,但不能明显大于15%涂层沿切割边缘部分或全部以大碎片脱落,和/或在格子不同部位上部分或全部剥落,受影响的交叉切割面积明显大于15%,但不能明显大于35%
涂层沿切割边缘大碎片脱落,和/或一些方格部分或全部出现脱落。受影响的交叉切割面积明显大于35%,但不能明显大于65%剥落的程度超过4级
JB/T5000.12—2007
发生脱落的十字交叉切割区的
表面外观
小提示:此标准内容仅展示完整标准里的部分截取内容,若需要完整标准请到上方自行免费下载完整标准文档。
备案号:21706-2007
中华人民共和国机械行业标准
JB/T5000.12—2007
代替JB/T5000.12—1998
重型机械通用技术条件
第12部分:涂装
Heavy mechanical general technigues and standardsPart12:Paint
2007-08-28发布
2008-02-01实施
中华人民共和国国家发展和改革委员会发布前言
1范围
2规范性引用文件
3术语和定义
4技术要求..
4.1涂装前的表面处理,
4.2机器产品的防腐蚀涂层设计
4.3机器产品特殊部位的涂装要求.4.4涂漆颜色要求,
4.5涂装施工要求
5涂装质量控制与检测
6涂层脱离底材的抗性评定
附录A(规范性附录)酸洗
A.1适用范围及质量要求
A.2酸洗前的表面处理.
A.3酸洗方法及要求
A.4安全措施,
附录B(规范性附录)涂层耐久性目
附录C(规范性附录)漆膜划格试验结果分级.表1除锈方法、除锈等级及适用范围..表2机器产品的环境腐蚀类别..
表3常用涂料推荐品种..
表4机器产品的推荐面漆颜色
表5机器产品特殊部位的推荐面漆颜色表6八种基本识别色及其色标
表B.1涂层耐久性与预期防腐年限的对应关系表B.2涂层厚度与预期防腐年限的对应关系试验结果分级
JB/T5000.12—2007
JB/T5000.12--2007
JB/T5000《重型机械通用技术条件》分为15部分第1部分:产品检验;
第2部分:火焰切割件;
第3部分:焊接件:
第4部分:铸铁件;
第5部分:有色金属铸件;
第6部分:铸钢件;
第7部分:铸钢件补焊;
第8部分:锻件;
第9部分:切削加工件;
第10部分:装配;
第11部分:配管;
第12部分:涂装:
第13部分:包装:
-第14部分:铸钢件无损检测;
第15部分:锻钢件无损检测。
本部分为JB/T5000的第12部分。本部分代替JB/T5000.12—1998《重型机械通用技术条件涂装》。本部分与JB/T5000.12—1998相比,主要变化如下:-取消了原表1中的酸洗代号“Be”,同时引用了石油行业标准SYT0407中关于酸洗的内容(见附录A)。
取消了原表2,增加了机器产品环境腐蚀类别的划分、涂层耐久性的划分以及涂层厚度与预期防腐年限的对照等内容(符合ISO12944-2的相关规定),见4.2.1及附录B。明确规定了产品设计工程师与产品防腐蚀工程师在产品防腐蚀工作中的职责和分工。见4.2.2和4.2.3。
增加了钢制容器内部、工矿车辆铸锻构件、高强度螺栓连接件结合面等的涂漆要求,见4.3.5、4.3.6、4.3.7。
-强调了涂料质量检测部门和相关人员的职责,见5.1、5.2、5.3。增加了划格法评定涂层脱离底材的抗性的内容(符合GB/T9286)。将“涂层附着力”改称为“涂层脱离底材的抗性”,使与GB/T9286保持一致。见第6章及附录C。删除了原标准中的附录A。
本部分的附录A、附录C为规范性附录,附录B为资料性附录。本部分由中国机械工业联合会提出。本部分由机械工业冶金设备标准化技术委员会归口。本部分起草单位:大连重工·起重集团有限公司。本部分主要起草人:关明、张连滨。本部分所代替标准的历次版本发布情况:JB/T5000.12—1998。
1范围
JB/T5000.12—2007
重型机械通用技术条件第12部分:涂装JB/T5000的本部分规定了重型机械产品及其零部件的涂装技术要求及检测要求。本部分主要适用于钢铁产品的表面涂装。凡合同文件无特殊要求的,其产品表面的涂装均应符合本部分的规定。
2规范性引用文件
下列文件中的条款通过JB/T5000本部分的引用而成为本部分的条款。凡是注日期的引用文件,其随后所有的修改单(不包括勘误的内容)或修订版均不适用于本部分,然而,鼓励根据本部分达成协议的各方研究是否可使用这些文件的最新版本。凡是不注日期的引用文件,其最新版本适用于本部分。GB2893安全色(GB/T2893-—2001,negISO3864:1984)GB/T5206.1色漆和清漆词汇第部分通用术语(GB/T5206.1-1985,eqvISO4618-11978)
GB/T5206.4色漆和清漆词汇第四部分涂料及涂膜物化性能术语(GB/T5206.4—1989,negISO4618-1:1984)
GB/T5206.5色漆和清漆词汇第五部分涂料及涂膜病态术语(GB/T5206.5-1991,neqISO4618-2:1984)
涂装作业安全规程涂漆工艺安全及其通风净化(GB6514—1995,neqNFPA33:1989)GB6514
工业管道的基本识别色、识别符号和安全标识GB/T7231
涂装作业安全规程涂漆前处理工艺安全及其通风净化GB7692
GB/T8264
涂装技术术语
GB/T8923
GB/T9286
SY/T0407
涂装前钢材表面锈蚀等级和除锈等级(GB/T8923--1988,eqvISO8501-1:1988)色漆和清漆漆膜的划格试验(GB/T986-1998,eqvISO2481:1992)涂装前钢材表面预处理规范
GSB05-1426漆膜颜色标准样卡
ISO12944-2
色漆及清漆防护漆体系对钢结构腐蚀防护第2部分:环境分类ISO12944-5
3术语和定义
色漆及清漆防护漆体系对钢结构腐蚀防护第5部分:防护漆体系GB/T5206.1、GB/T5206.4、GB/T5206.5、GB/T8264中确立的术语和定义适用于本部分。4技术要求
4.1涂装前的表面处理
所有用于设备制造的钢铁原材料,涂漆前均需进行表面除锈处理。所有需要进行涂装的钢铁原材料或制件表面,在涂漆前必须将铁锈、氧化皮、油脂、灰尘、泥土、盐和污物等清除干净。
4.1.1除锈前,应先用有机溶剂、碱液、乳化剂、蒸汽等除去钢铁表面的油脂、污垢。4.1.2钢铁表面除锈方法、除锈等级及适用范围见表1。表1中Sa及St各等级的除锈要求及评定方法按GB/T8923的规定。
JB/T5000.12--2007
酸洗除锈方法及处理要求详见附录A。4.1.3焊接件在组装焊接后需要进行热处理的,应将除锈工序放在热处理之后进行。表1除锈方法、除锈等级及适用范围除锈方法
喷射或抛射
手工或动力
工具除锈
酸洗除锈
除锈等级
GB/T8923
Sa21/2
适用范围
辅助部件或辅助设备及用于轻度腐蚀性环境中的钢铁制件表面:与混凝土接触或理入其中的钢铁制件表面主要部件或主要设备及用于腐蚀性较强的环境中的钢铁制件表面长期在潮湿、潮热、盐雾等环境下作业的钢铁制件表面;与高温接触并且需要涂耐热漆的钢铁制件表面与液体介质或腐蚀性介质接触的表面,如油箱、减速机箱、水箱等内表面与高温接触但不需要涂耐热漆的钢铁制件受设备限制,无法进行喷丸除锈的特大钢铁构件;钢铁构件形状特殊无法进行喷丸除锈的部位设备上的各类钢制管道;不能喷丸的薄板件(壁厚小于5mm);结构复杂的中、小型零件
4.1.4喷(抛)丸除锈用的磨料可采用铸铁(钢)丸粒、钢丝段、铜矿渣等,所用弹丸应带有棱角、铸、锻件用的钢铁弹丸直径不得大于2mm;钢板及型钢用的钢铁弹丸直径为0.6mm~1.2mm;喷砂用的石英砂、铜矿渣直径不得大于2.5mm。处理后的表面粗糙度不得大于100μm。4.1.5经喷丸或手工除锈、动力工具除锈后的待涂表面,应立即涂底漆,其间隔时间不得大于6h(空气相对湿度人于70%的环境区域,其间隔时问不得大于4h)。酸洗除锈后经过磷化处理的待涂表面,涂底漆的间隔时间不得小于48h(在北方冬季寒冷的气候环境下,其间隔时间不得小于72h),涂漆前表面不得出现返锈和污染现象。
4.1.6用于制造机器构件的钢铁板材及型材,厚度大于5mm的,应预先进行喷(抛)丸除锈,除锈质量等级应达到Sa21/2级;厚度小于5mm的,可进行化学处理(酸洗、冲洗、中和、钝化或磷化等),其除锈质量等级应达到附录A的有关规定,并在规定的时间范围内涂保养底漆(车间底漆)。预处理时的漆膜厚度及涂料选择推荐如下:a)推荐漆膜(干膜)厚度:15um~25um。b)推荐涂料品种:无机硅酸锌(车间)底漆、环氧底漆、环氧富锌底漆、磷酸锌底漆、铁红环氧脂底漆等。
c)所用的底漆必须是产品配套漆系中的品种或与配套漆系中的底漆相适应的漆种。4.2机器产品的防腐蚀涂层设计
4.2.1机器产品的环境腐蚀类别见表2。常用涂料推荐品种见表3。推荐面漆颜色见表4。涂层耐久性与预期防腐年限及涂层厚度的对应关系见附录B。4.2.2产品设计工程师应根据表2确定机器产品的环境腐蚀类别,根据表4选择产品的主体面漆颜色并将所确定的内容在产品图样或技术文件中予以注明。如:“产品使用环境类别为C3,面漆颜色为59橘黄(YR04)”。
4.2.3产品防腐蚀工程师应根据产品设计工程师对产品环境腐蚀类别、主体面漆颜色的要求,参考附录B及表3的有关规定,进行产品的防腐蚀设计。该设计包括:a)确定涂料配套漆系(涂料品种、涂层厚度);b)确定产品主体及各部位、各系统颜色:2
c)编制“产品涂装工艺说明”。表2机器产品的环境腐蚀类别
典型环境
空气洁净、有保温设施的建筑物内部(室内)边远地区,低污染区域
城市及工业环境。二氧化硫含量、湿度为中等程度的生产区域工业及沿海区域、化工厂
高湿度的工业区域及严酷环境
高盐度的海洋、近海、港湾、沿海区域注:本表中的类别及典型环境的划分符合ISO12944-2的规定。表3常用涂料推荐品种
中间漆
耐油漆
耐高温漆
耐潮湿漆
推荐品种
铁红醇酸底漆、铁红环氧脂底漆、硅酸锌防锈漆、磷酸锌底漆、环氧富锌底漆等
环氧云母氧化铁漆,环氧中间漆、磷酸锌底漆等醇酸磁漆、氯化橡胶面漆、聚氨脂面漆、丙烯酸磁漆、醇酸铝粉漆、环氧面漆等
JB/T5000.12—2007
厚度要求
各种涂料的涂层厚度
(干膜),根据涂料配套漆
过氯乙烯油箱漆、环氧耐油漆、聚氨酯耐油漆,硝基内用磁漆(底、面系确定漆应配套,且涂层不易太厚)等无机硅酸锌底漆、有机硅耐热漆、醇酸铝粉漆、各色酮漆等氯化橡胶漆、焦油环氧沥青防锈漆等4.2.4所选定的涂料配套漆系中的所有涂料,原则上应是同一厂家或同一品牌的产品。4.3机器产品特殊部位的涂装要求4.3.1铆接件相互接触的表面,在连接前必须涂以厚度为30um~40um的底漆。所用涂料品种应是涂料配套漆系中的漆种。搭接边缘应用油漆、腻子或粘合剂封闭。在加工或焊接过程中损坏的漆面,应重新进行表面处理和涂装。
4.3.2不封闭的箱形梁、箱形结构的内表面、各类安全罩的内表面等,无特殊要求的,一般须涂60um~80um厚的底漆;封闭的箱形梁、箱形结构的内表面不涂漆。4.3.3装配后不能靠近、无法涂装的部位,应在装配前完成涂漆。4.3.4有涂漆要求的有色金属表面,应根据不同情况,选用相适应的底漆、面漆。如锌表面应选用磷化底漆或磷酸锌底漆等。面漆(或中间漆)要与底漆配套。4.3.5钢制容器内部的涂装(无人孔的除外),应根据容器内工作介质的性质选择油漆或涂硬膜防锈油。不锈钢容器不涂漆。
4.3.6工矿车辆、冶金车辆的碰头车钩以及转向架中的铸造侧架、铸造摇枕、车轮、轮轴等,如无特殊要求,应涂清油或清漆,涂层厚度不低于30μm。4.3.7高强度螺栓联接件结合面,应根据摩擦系数的不同或按图样要求,在喷砂后涂高固体份、高锌粉含量(80%)的无机富锌底漆(如Interzinc22*底漆),厚度为60um。或者涂刷两层过氯乙烯可剥清漆(两层之间贴一层纱布)加以保护,联接前再将可剥清漆剥除。必要时,表面还应使用薄铁皮加以覆盖。
4.3.8属下列情况之一的,不进行涂装。a)产品或部件与混凝土接触或埋人混凝土中的部位、紧贴耐火材料的部位;3
JB/T5000.12—2007
b)机械加工的配合面、工作面、摩擦面;c)配管的各种阀、泵及法兰表面;d)不锈钢制件表面;
e)钢丝绳、地脚螺栓及其底板;f)电镀表面、无特殊要求的有色金属表面;g)非金属制件表面;
h)电动机等外购机电配套件表面。4.4涂漆颜色要求
4.4.1机器产品的面漆颜色应符合合同要求。合同中无规定的,按表4的推荐选取颜色,4.4.2除用户有特殊要求外,“产品涂装工艺说明”中提到的油漆颜色,均应符合GSB05-1426中标示的颜色。
产品类别
热轧设备
冷轧设备
装卸机械
连铸设备
冶金机械
锻压机械
矿山设备
焦炉机械、煤气设备
工矿车辆
冶金车辆
破碎机械
造矿烧结设备
人造板设备
橡胶设备
水泥设备
表4机器产品的推荐面漆颜色
推荐面漆颜色
30淡绿(G02)、24潮绿(BG02)、28苹果绿(G01)、32中绿(G04)、31艳绿(G03)24湖绿(BG02)、28苹果绿(GO1)、40豆绿(GY01)、10天(酸)蓝(PB09)59橘黄(YR04)、60橘红(R05)、72中灰(B02)、57棕(YR05)28苹果绿(G01)、38纺绿(GY02)、银白、30淡绿(G02)28苹果绿(G01)、73淡灰(B03)、黑色28苹果绿(G01)、30淡绿(G02)、24潮绿(BG02)、32中绿(G04)、6海蓝(PB05)28苹果绿(G01)、40豆绿(GY01)、48淡黄(Y06)、60橘红(R05)、黑色72中灰(B02)、28苹果绿(G01)、38纺绿(GY02)、淡海(铁)蓝(B11)59橘黄(YR04)、60橘红(R05)、32中灰(B02)、黑色黑色
73淡灰(B03)
38纺绿(GY02)
24湖绿(BG02)
24湖绿(BG02)
73淡灰(B03)
机器产品的特殊部位按表5的规定选择面漆颜色表5机器产品特殊部位的推荐面漆颜色产品特殊部位名称
油箱、减速机内壁及其内部零件的涂漆表面栏杆、扶手
操纵室的顶棚及内壁
操纵室地板
盖板、走台板、销板、楼梯板
机械停止按钮、制动及停车装置的操纵手柄;机器转动部件的裸露部分,如飞轮、齿轮、带轮等的轮幅部分;指示器上各种表头的极限位置的刻度注:表中有关大红色的使用规定符合GB2893的相关规定。面漆颜色
奶油色(Y03)
黄色(Y06、07、08)
半光浅色漆
铁红色(R01)
与主机同色或绿色(GY02)
大红色(R03)
4.4.4有暂时或永久性危险的机械部位或装置,应涂以宽度约100mm、与水平面成45°斜角、颜色为黄、黑相间的“虎皮”状警示条纹。同一条棱线两侧的条纹倾斜方向应相反。如果表面面积较小,条纹4
宽度可以适当缩小,但黄条纹与黑条纹每种不得少于两条。JB/T5000.12-—2007
前述有暂时或永久性危险的机械部位或装置包括:各种机械在工作或移动时容易产生碰撞的部位,如移动式起重机的外伸腿、起重机的吊钩滑轮侧板、起重臂的顶端、四轮配重;平顶拖车的排障器及侧面栏杆;门式起重机门架下端;剪板机的压紧装置;冲床的滑块等。4.4.5机器产品配管的面漆颜色应与机器的面漆颜色相同。距机器1m以外的配管颜色,应符合表6关于基本识别色的规定。
表6八种基本识别色及其色标
输送介质种类
水燕气
酸或碱
可燃液体
其他液体
注:本表符合GB/T7231的规定。4.5涂装施工要求
4.5.1环境要求
基本识别色
色标(GSB05-1426)
4.5.1.1一般情况下,涂装施工环境温度不得低于5℃,相对湿度应不大于85%。对北方地区的冬季施工,应尽量选用适合低温下施工和固化的油漆。4.5.1.2雨、雪、雾天气及风力超过4级时,禁止在室外施工。待涂装表面有结箱、结露的,不许施工。Www.bzxZ.net
涂装及固化过程中,涂装件表面温度不得超过60℃。禁止漆膜在烈日下暴晒。4.5.1.3
4.5.1.4施工区域必须保持空气流通。涂装及固化过程中应无粉尘及其他异物飞扬。4.5.2施工要求
涂装时,应严格遵守各种涂料对温度、湿度等的要求,遵守重涂间隔时间及调配方法的有关4.5.2.1
规定。
施工前,如发现涂料出现胶化、结块等异常现象,应停止调配和施工。4.5.2.3
涂装施工过程中,应注意各种施工方法对漆膜的影响。要尽量保证漆膜的均匀,不可漏涂。对于边、角、夹缝、螺钉头、铆接缝、焊缝等部位要先涂刷,然后再大面积涂装。4.5.2.4对焊后或装配后无法涂漆的构件部位,应在焊前或组装前涂漆。4.5.2.5两种不同颜色的涂层交界处,其界面必须明显、整齐。4.5.2.6需经常拆装的零件,其相互连接处的油漆面必须平整。缝线应明显,不得出现漆膜崩落、界线不分或漆成一片等现象。
4.5.2.7喷涂施工时,应对产品不需涂装的部位进行遮盖,防止误涂。4.5.2.8机器产品表面是否需要刮腻子,应在图样或技术文件中注明。刮腻子时,应先涂底漆,底漆于燥后再进行刮腻子操作。刮腻子一般进行1次~2次,每次厚度约为0.5mm~1mm,局部最大总厚度不得超过5mm。腻子干燥后须对表面进行打磨,打磨后的腻子表面应平整、光滑、牢固、无裂纹。4.5.2.9机器产品的最后一遍面漆一般应在总装试车完成后再进行涂装。4.5.2.10对安装过程中损坏的漆膜应进行修补。修补前应对表面进行清理。修补部分对周围涂层的覆盖宽度应不少于50mm(损坏面积较小时,修补的面积应比损坏的面积大一倍以上)。修补应符合相关5
JB/T5000.12—2007
工艺或标准的规定。补漆部位的颜色、涂层厚度应与周围的颜色、涂层厚度一致。4.5.3涂装安全及通风要求
涂装预处理的施工安全及通风要求按GB7692的规定执行。涂装施工中的安全及通风要求按GB6514的规定执行。5涂装质量控制与检测
5.1涂料质量的检测按涂料说明书规定的方法进行。a)涂料说明书中规定的检测方法,必须符合相关国家标准的规定。b)对于配套漆系中的涂料,若其说明书中无检测项目或指标,而使用厂防腐蚀工程师认为确有必要了解的,则涂料供应商应无条件提供由国家质量技术监督部门出具的该项目或指标的检测报告。
5.2涂料供应商在向使用厂提供涂料时,必须附带本批次涂料的产品合格证和检测报告,否则涂料使用厂有权拒收。
5.3使用涂料的企业的质量管理部门,对涂料供应商提供的涂料产品质量负有日常监督职责。5.4涂料的调配应严格按照说明书的规定和要求进行。5.5施工时,应经常用湿膜测厚仪测定漆膜厚度,以便更准确地控制干膜厚度。5.6漆膜的干膜厚度检测,应在涂料说明书规定的干燥时间以外进行。5.7漆膜外观应满足以下要求:底漆、中层漆、面漆漆膜不允许有针孔、气泡、裂纹、咬底、渗色、漏涂、流挂、局部剥落等缺陷;面漆表面应平整均匀、漆膜丰满、色泽一致。检查方法经协商可采用肉眼或用五倍放大镜观察。
5.8涂层厚度的检测应在每一涂层干燥后进行。全部涂层涂装完毕后,再检测总厚度。检测方法是:用电磁式膜厚仪检测,每10m2(漆膜面积不足10m2的按10m2计)作为一处,管路等细长体每3m4m长作为一处,每处测3点~5点。每处所测各点厚度的平均值,不得低于规定涂层总厚度的90%,且不高于120%。每处所测各点厚度中的最小值不应小于规定涂层总厚度的70%。6涂层脱离底材的抗性评定
涂层脱离底材的抗性评定按以下方法进行:选六块规格为200mmX200mm的试板,经表面处理后,涂上与产品相同的涂层漆系。抗性评定在漆膜实干后进行(根据用户要求,可分层逐次评定或最终一次性评定),最终的评定经协商可采用画叉法或划格法进行。画叉法:用锋利的刀片或保险刀片在试板表面划一个夹角为60°的叉,刀痕要划至钢板,然后贴上宽度为25mm的专业压敏胶带,使胶带贴紧漆膜,然后用手迅速扯起,刀痕两边涂层被揭下的总宽度若不超过2mm即为合格。
划格法:按GB/T9286的规定进行评定。其评定结果应不低于附录C中的2级要求。A.1适用范围及质量要求
附录A
(规范性附录)
A.1.1本附录符合SY/T0407的规定,适用于钢材表面的酸洗处理,JB/T5000.12-2007
A.1.2可用化学和电解两种方法做酸洗处理。酸洗后钢材表面应没有肉眼可见的氧化皮、锈和旧涂层。A.1.3钢材表面的腐蚀程度应适合规定的涂装要求。A.1.4允许酸洗后的钢材表面在颜色的均匀性上受钢材的钢号、原始锈蚀程度、外形、轧制或加工痕迹以及腐蚀方式的影响。
A,2酸洗前的表面处理
A.2.1按照SY/T0407中规定的方法,除掉钢材表面上绝大部分油、油脂、润滑剂和其他污物(不包括氧化皮、氧化物和锈)。
A.2.2宜用工具除锈方法或喷(射)除锈方法(只要求达到Sa1级),除掉表面上大部分氧化皮、锈和旧涂层,以缩短酸洗除锈的时间。A.3酸洗方法及要求
A.3.1将钢材表面浸人常温下的硫酸、盐酸或磷酸溶液中,酸洗液中应加入足量缓蚀剂,以减少对基层金属的腐蚀,直到所有的氧化皮和锈全部除掉后,用淡水充分冲洗,再做钝化处理。A.3.2将钢材表面没人60℃以上、浓度为5%~10%(按重量计)的硫酸溶液中,酸洗液中应加人足量缓蚀剂,直至所有的氧化皮和锈全部除掉后再用淡水充分冲洗,最后将钢材表面放在80℃左右、含0.3%~0.5%磷酸铁、浓度为1%~2%(按重量计)的磷酸溶液中浸泡(1~5)min。A.3.3将钢材表面浸人(75~80)℃、体积分数为5%的的硫酸溶液中,酸洗液中应加人足量缓蚀剂,直至所有的氧化皮和锈全部除掉后再用(75~80)℃的热水冲洗2min,最后用85℃以上的钝化液浸泡2min以上。钝化液中应合有0.75%的重铬酸钠或0.5%左右的正磷酸。A.3.4将钢材放置在酸或碱电解槽中电解。电解中若工件作为阴极,应做适当处理以防止或减少氢脆现象的发生。如果在碱溶液中进行电解,电解后需用热水充分冲洗,接着在稀磷酸或稀重铬酸盐的溶液中浸泡,直至残留在表面上的碱迹全部清除为止。A.3.5酸洗处理应满足下列要求:a)硫酸槽中所溶铁的含量不应超过6%,盐酸槽中所溶铁的含量不应超过10%。b)必须用纯净的淡水或蒸馏水做溶液或冲洗液。在冲洗过程中,必须连续不断地向冲洗槽中注人清水,使每升水中携带的酸及可溶盐的总量不超过2g。c)从酸洗槽中取出的钢材应在该槽上方短时悬挂,沥净大部分酸洗液。d)酸洗后必须除掉有害的酸洗残渣、未发生反应的酸或碱、金属沉积物和其他有害污物。e)不应将酸洗后的钢材垒起来使表面互相接触,应在表面完全干燥后再重叠。f)必须在可见锈出现之前进行涂装。A.4安全措施
A.4.1应设置足够的通风设施,以保证工作人员的身体健康并应限制氢气的浓度,使其在爆炸的极限7
JB/T5000.12—2007
范围以下。
A.4.2操作人员应戴护目镜。
A.4.3工作人员必须穿戴橡胶围裙、橡胶靴子、橡胶手套。A.4.4酸洗和电解过程中所产生的废液的排放,应按国家现行的有关标准执行。A.4.5酸洗和电解过程所使用的化学药品的搬运和储存应符合国家现行的有关规定。A.4.6必须将浓酸缓慢地倒人水或稀酸中,而且应边倒边搅动。附录B
(规范性附录)
涂层耐久性
涂层耐久性与预期防腐年限及涂层厚度的对应关系符合ISO12944-5的规定。涂层耐久性与预期防腐年限的对应关系见表B.1。B.1
表B.1涂层耐久性与预期防腐年限的对应关系类别
高耐久性
中耐久性
低耐久性
B.2涂层厚度与预期防腐年限的对应关系见表B.2。预期防腐年限
预期防腐年限为15年以上
预期防腐年限为5~15年
预期防腐年限为5年以下
预期防腐年限的选择应符合合同的规定。合同无规定的,按低档年限(2~5)年进行涂层设计表B.2涂层厚度与预期防腐年限的对应关系环境类别
厚度范围μm
80~120
160~200
120~160
160~200
200~240
预期防腐年限
低(2~5年)
中(5~15年)
高(>15年)
低(2~5年)
中(515年)
高(>15年)
环境类别
厚度范围μum
160~200
200~240
240~320
240280
280~400
注:因C1为空气洁净的室内环境,所以在本表中未列出其涂层厚度与预期防腐年限的对应关系。附录C
(规范性附录)
漆膜划格试验结果分级
漆膜的划格试验结果分级符合GB/T9286的规定。漆膜的划格试验结果分级见表C.1。8
预期防腐年限
低(2~5年)
中(5~15年)
高(>15年)
低(2~5年)
中(5~15年)
高(>15年)
表C.1试验结果分级
切割边缘完全平滑,无一格脱落在切口交叉处有少许涂层脱落,但交叉切割面积受影响不能明显大于5%
在切口交叉处和/或沿切口边缘有涂层脱落,受影响的交叉切割面积明显大于5%,但不能明显大于15%涂层沿切割边缘部分或全部以大碎片脱落,和/或在格子不同部位上部分或全部剥落,受影响的交叉切割面积明显大于15%,但不能明显大于35%
涂层沿切割边缘大碎片脱落,和/或一些方格部分或全部出现脱落。受影响的交叉切割面积明显大于35%,但不能明显大于65%剥落的程度超过4级
JB/T5000.12—2007
发生脱落的十字交叉切割区的
表面外观
小提示:此标准内容仅展示完整标准里的部分截取内容,若需要完整标准请到上方自行免费下载完整标准文档。

标准图片预览:
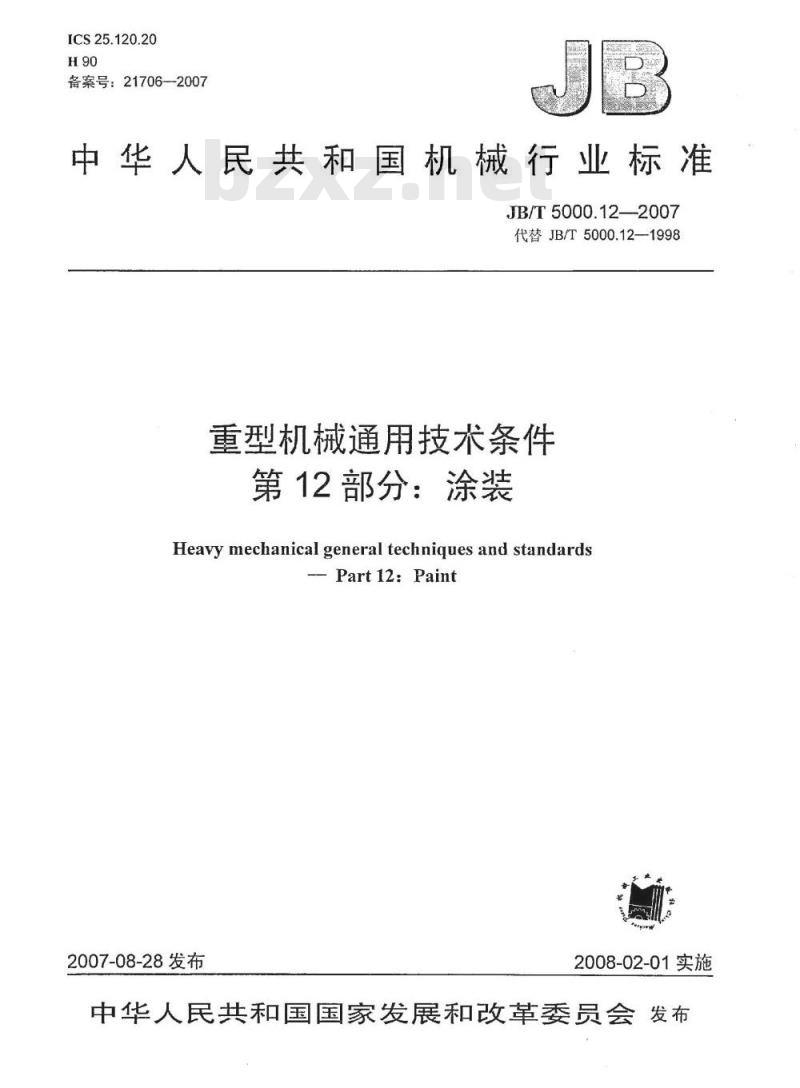
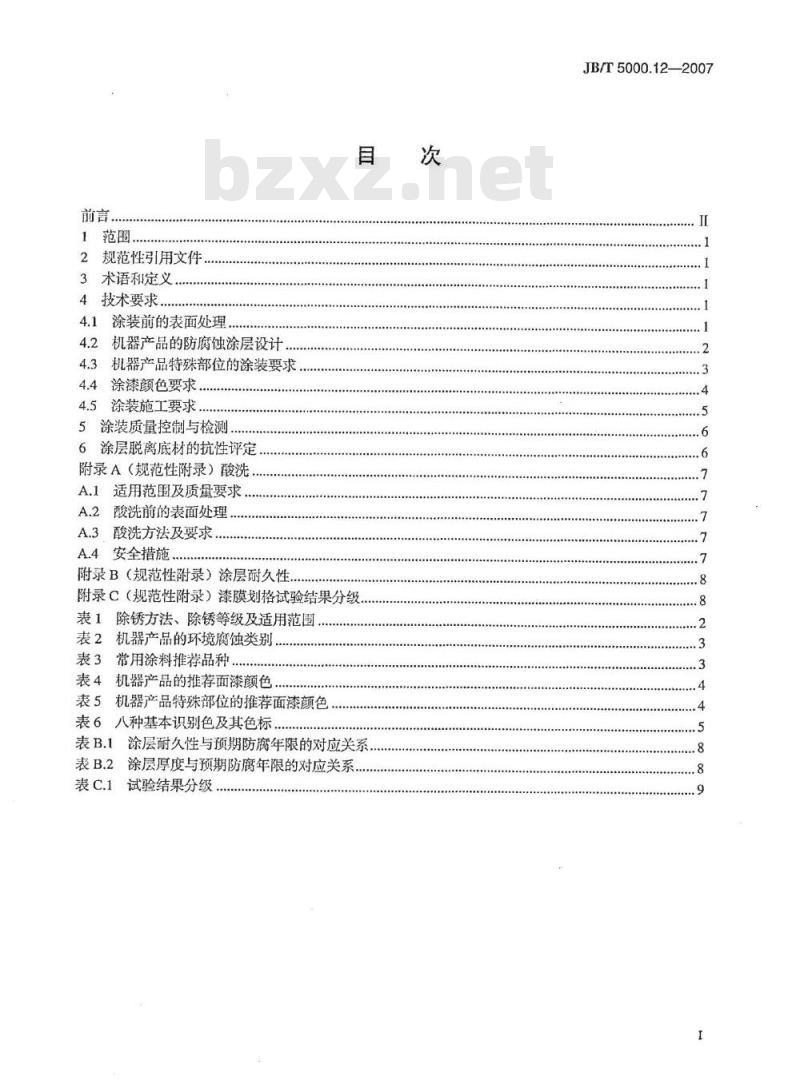
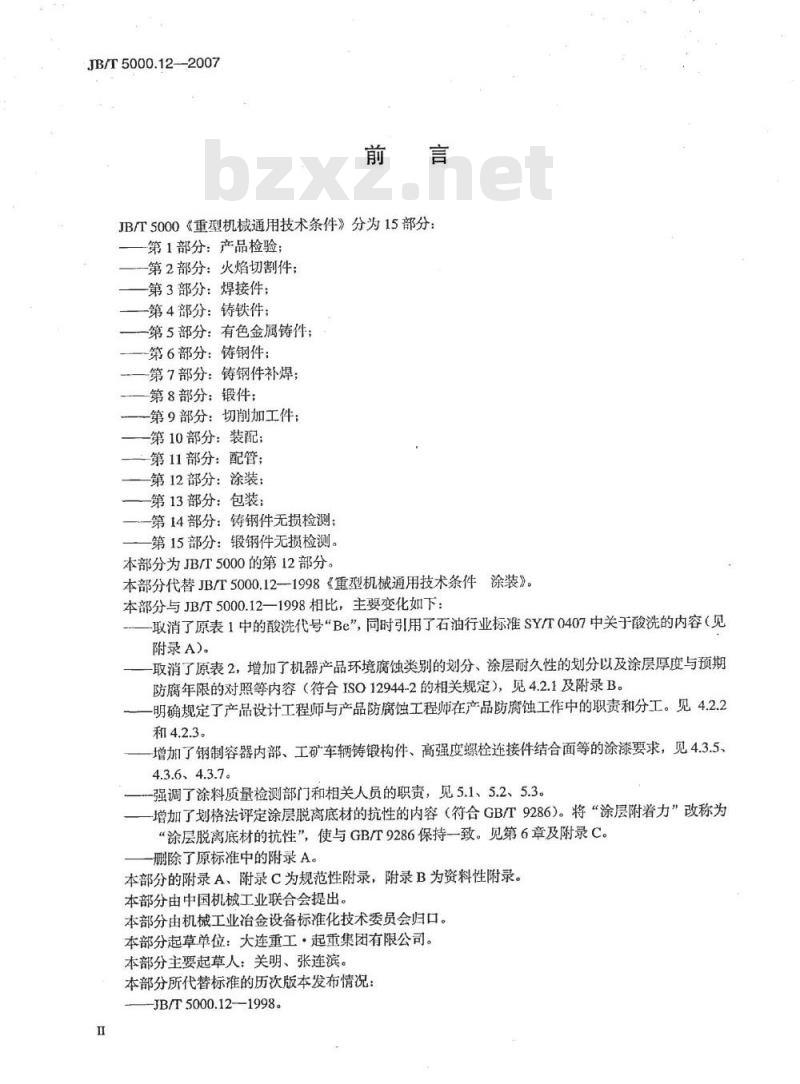
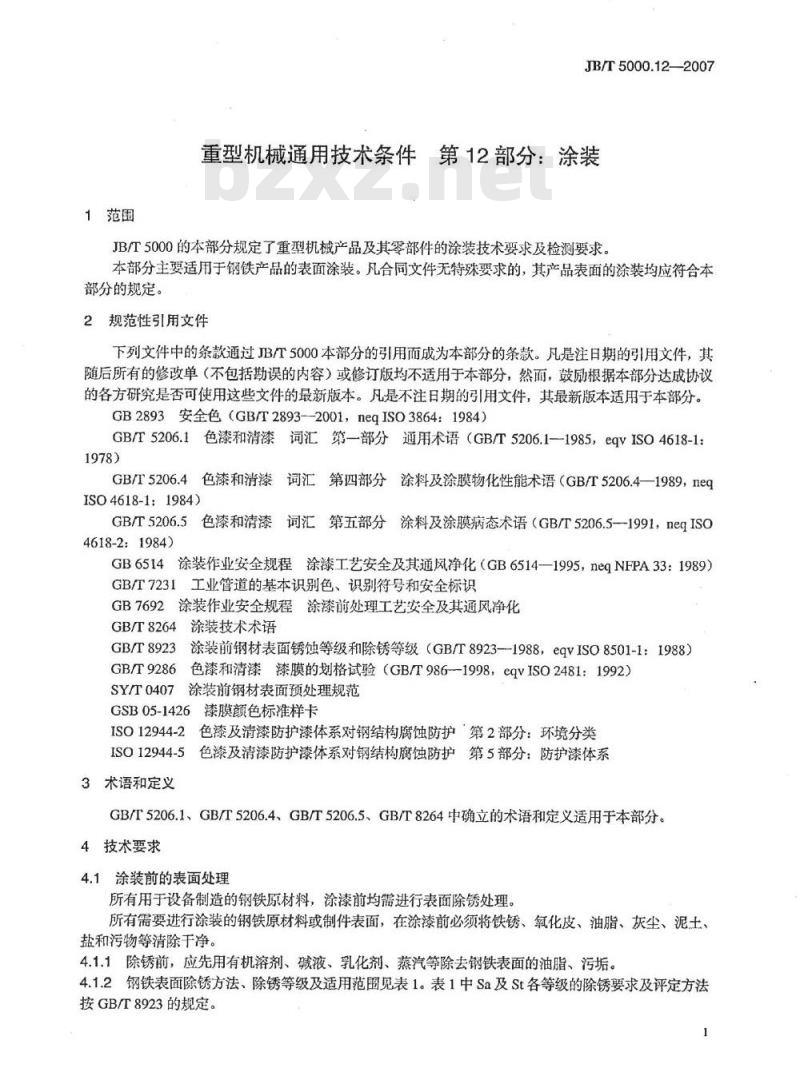
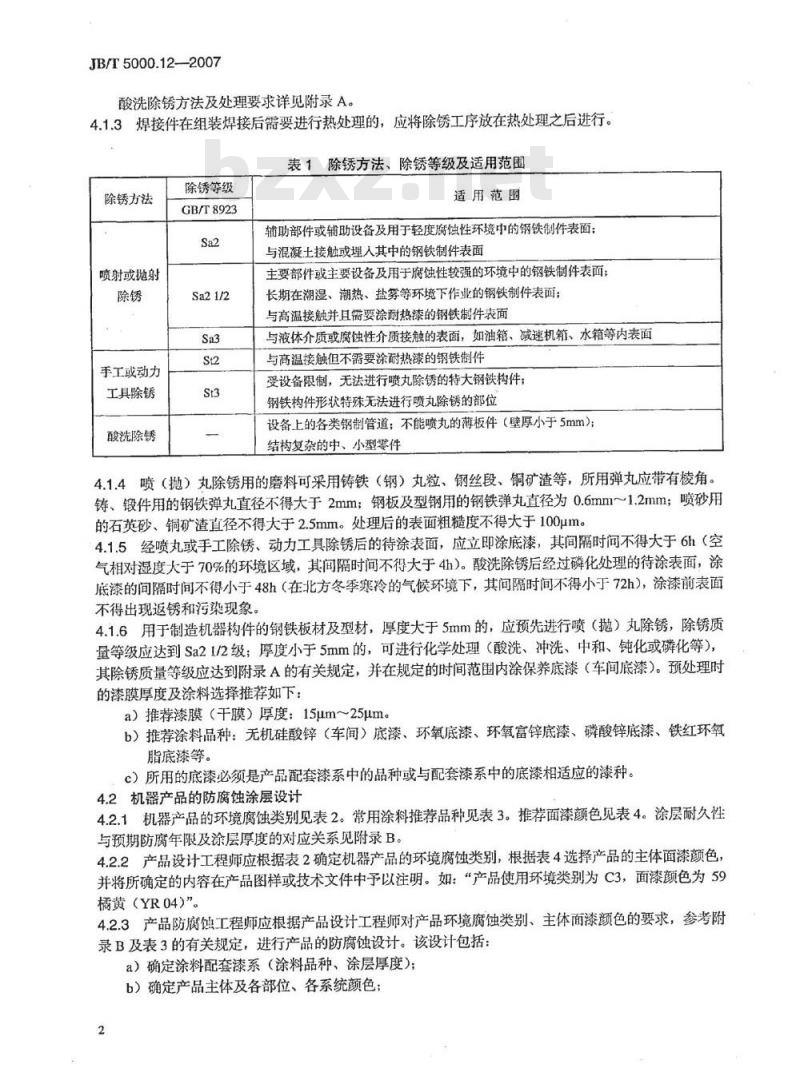
- 热门标准
- 机械行业标准(JB)
- JB/T5946-1991 工程机械 涂装通用技术条件
- JB/T3103.2-2010 锯条开齿机 第2部分:精度
- JB3228-1983 闭式机械压力机 紧固模具用槽打(顶)杆孔的分布形式与尺寸
- JB/T5366.9-1991 8mm槽系组合夹具基础件 45°圆形基础板
- JB/T10620-2006 金属覆盖层 铜-锡合金电镀层
- JB/T10767-2007 装载机铜基湿式粉末冶金摩擦片 技术条件
- JB/T9984.1-1999 通过式抛丸清理机 参数
- JB/T5110.5-1992 螺旋压力机锻模 矩形模块用模座
- JB3458-1983 孔用弹性挡圈安装钳子尺寸
- JB/T5367.11-1991 8mm槽系组合夹具支承件 加筋角铁
- JB/T6237.8-2008 电触头材料用银粉化学分析方法 第8部分:银粉水溶液pH值测定
- JB/T10565-2006 工业过程测量和控制系统用动圈式指示仪性能评定方法
- JB/T7881.5-2010 剪羊毛机 第5部分:刀片
- JB/T7411-2012 无损检测仪器 电磁轭磁粉探伤仪技术条件
- JB/T11225-2011 烘烤机械 层式电烤炉
- 行业新闻
请牢记:“bzxz.net”即是“标准下载”四个汉字汉语拼音首字母与国际顶级域名“.net”的组合。 ©2009 标准下载网 www.bzxz.net 本站邮件:bzxznet@163.com
网站备案号:湘ICP备2023016450号-1
网站备案号:湘ICP备2023016450号-1