- 您的位置:
- 标准下载网 >>
- 标准分类 >>
- 石油化工行业标准(SH) >>
- SH 3501-2001 石油化工剧毒 可燃介质管道工程施工及验收规范
标准号:
SH 3501-2001
标准名称:
石油化工剧毒 可燃介质管道工程施工及验收规范
标准类别:
石油化工行业标准(SH)
标准状态:
已作废-
实施日期:
2002-05-01 出版语种:
简体中文下载格式:
.rar.pdf下载大小:
10.76 MB

部分标准内容:
中华人民共和国行业标准
SH3501-2001
石油化工有毒、可燃介质管道
工程施工及验收规范
Specification for construction and acceptance of hypertoxic andcombustible medium piping engineering in petrochemical industry主编单位:中国石化集团第五建设公司批准部门:中华人民共和国国家经济贸易委员会2002-03-11发布
2002-05-01实施
中华人民共和国国家经济贸易委员会发布中华人民共和国国家经济贸易委员会二00二年第12号
关于发布《石油化工防火堤设计规范》等19项石油化工行业标准的公告
中国石油化工集团公司:
你公司报批的《石油化工防火堤设计规范》等19项石油化工行业标准草案,经国家经贸委批准,现予发布,自2002年5月1日起实施。标准名称、编号为:强制性标准:
序号标准编号
SH3125—2001
2.SH3059—2001
3.SH3021—2001
SH3126—2001
5.SH3020—2001
6.SH 3501—2001
7.SH3503—2001
8.SH3514-2001
SH3534—2001
10.SH3009-2001
推荐性标准:
序号标准编号
标准名称
石油化工防火堤设计规范
石油化工管道设计器材选用通则(代替SH3059-94、SH3059-1994)
石油化工仪表及管道隔离平吹洗设计规范代替SHJ21-90、SH3021-1990)
石油化工仪表及管道伴热和隔热设计规范(代替SHJ21—90、SH3021-1990)
石油化工仪表供气设计规范(代替SHJ20—90、SH3020-1990)石油化工剧毒、可燃介质管道工程施工及验收规范(代替SH3501-1997)
石油化工工程建设交工技术文件规定(代替SH3503—93、SH3503-1993)
石油化工设备安装工程质量检验评定标准(代替SHJ514-90、SH3514—1990)
石油化工筑炉工程施工及验收规范石油化工企业燃料气系统和可燃性气体排放系统设计规范(代替SHJ9-89、SH3009—2000)
标准名称
11.SH/T3110-2001石油化工设计能量消耗计算方法(代替SYJ1029-82、SH/T3110-2000)
SH/T3123-2001
13.SH/T3124-2001
石油化工钢储罐地基充水预压监测规程石油化工给水排水工艺流程设计图例SH/T 3517-2001
1石油化工钢制管道工程施工工艺标准(代替SHJ517-91、SH/T3517—1991)
15.SH/T3516—2001
催化裂化装置轴流压缩机-烟气轮机机组施工技术规程(代替SHJ516—90、SH/T3516—1990)石油化工立式圆筒形钢制储罐施工工艺标准(代替SH16.
SH/T 3530-2001
3530-93、SH/T3530-1993)
17.SH/T3127-2001
石油化工管式炉铬钼钢焊接回弯头技术规范2
SH/T3109-2001炼油厂添加剂设施设计规范(代替SYJ1025-82、SH/T3109—2000)
19.SH/T3096-2001
加工高硫原油重点装置主要设备设计选材导则(代替SH/T3096-1999)
中华人民共和国国家经济贸易委员会二00二年三月十一日
本规范是根据中国石化20011建标字088号文的通知,由我公司对《石油化工剧毒、可燃介质管道施工及验收规范》SH3501一1997进行修订而成本规范共分七章和三个附录。这次修订内容主要包括以下几个方面:1.将有关内容与GB50235一97进行了协调,修改条文主要有:第4.1.7条、第5.4.9条、第5.5.3~5.5.6条、第5.5.8条;2.将原规范中第2.0.1条管道分级规定进行了调整;3.修改了原规范中阀门检、试验的有关规定。在修订过程中,针对原规范中存在的问题,进行了广泛的调查研究,总结了近几年来石油化工管道施工方面的实践经验,并征求了有关施工、设计、生产等方面的意见,对其中的主要问题进行了多次讨论,最后经审查定稿。本规范在实施过程中,如发现需要修改补充之处,请将意见和有关资料提供给我公司,以便今后修订时参考。
我公司的通讯地址及邮政编码
通讯地址:甘肃省兰州市西固区康乐路35号邮政编码:730060
主编单位:中国石化集团第五建设公司主要起草人:姚代贵、张西庚、汪庆华、单承家1总则
1.0.1本规范适用于石油化工企业设计压力400Pa【绝压]】~42MPa【表压],设计温度.196~850℃的有毒(毒性程度为极度危害、高度危害、中度危害和轻度危害)、可燃介质钢制管道的新建、改建或扩建工程的施工及验收。1.0.2本规范不适用于长输管道及城镇公用燃气管道的施工及验收。1.0.3有毒、可燃介质管道施工除执行本规范的规定外,尚应符合设计文件的规定。1.0.4有毒、可燃介质管道施工时,修改设计或材料代用,应经设计单位批准。1.0.5管道施工的安全技术和劳动保护,应按国家现行的有关法规、标准及《石油化工施工安全技术规程》SH3505的规定执行。在已投入生产的区域内施工时,应按生产区域的特点制订施工安全技术措施。1.0.6承担有毒、可燃介质管道施工的单位,必须持有质量技术监督行政部门相应的压力管道安装许可证。
1.0.7从事有毒、可燃介质管道施工的焊工应按《锅炉压力容器压力管道焊工考试与管理规则》进行考试,取得合格证书。无损检测人员应按《锅炉压力容器无损检测人员资格考核规则》进行考核,取得相应资格证书。2管道分级
2.0.1输送有毒、可燃介质管道的分级,应符合《石油化工管道设计器材选用通则》SH3059的规定,见表2.0.1。
表2.0.1管道分级Www.bzxZ.net
管道级别
适用范围
毒性程度为极度危害介质管道(苯管道除外)2毒性程度为高度危害介质的丙烯睛、光气、二硫化碳和氟化氢介质管道3设计压力大于或等于10.0MPa的介质管道毒性程度为极度危害介质的苯管道2毒性程度为高度危害介质管道(丙烯、光气、二硫化碳和氟化氢管道除外)甲类、乙类可燃气体和甲类液化烃、甲:类、乙类可燃液体介质管道3
毒性程度为中度、轻度危害介质管道乙:类、丙类可燃液体介质管道设计温度低于-29℃的低温管道
注:常见毒性介质、可燃介质见附录A。2.0.2
输送同时具有毒性和可燃特性介质的管道,应按本规范中的高级别管道的处理。2.0.3
输送混合介质的管道,应以主导介质作为管道分级的依据。3管道组成件检验
3.1一般规定
3.1.1管道组成件(管子、阀门、管件、法兰、补偿器、安全保护装置等)的制造单位,应具有质量技术监督行政部门颁发的《压力管道元件制造单位安全注册证书》。3.1.2有毒、可燃介质管道工程使用的管道组成件,应符合设计文件规定及本规范的有关要求。
3.1.3管道组成件必须具有质量证明书或合格证,无质量证明书或合格证的产品不得使用。
产品在使用前,应对质量证明书认真审查,若对证明书中的特性数据有异议,应进行必要的分析检验。
3.1.4管道组成件在使用前应进行外观检查,其表面应符合下列要求:无裂纹、缩孔、夹渣、折叠、重皮等缺陷;锈蚀、凹陷及其他机械损伤的深度,不应超过产品相应标准允许的壁厚负偏差;2
螺纹、密封面、坡口的加工精度及粗糙度应达到设计文件要求或制造标准:3
4有产品标识。
3.1.5合金钢管道组成件主体的关键合金成分,应逐件采用快速光谱分析或其他方法复查,并作好标记。
3.1.6设计文件有低温冲击值要求的材料,产品质量证明书应有低温冲击韧性试验值,否则应按《金属低温夏比冲击试验方法》GB4159的规定进行补项试验。3.1.7凡按规定作抽样检查或检验的样品中,若有一件不合格,必须按原规定数加倍抽检,若仍有不合格,则该批管道组成件不得使用,并应作好标记和隔离。3.1.8管道组成件应分区存放。不锈钢与非合金钢、低合金钢管道组成件不得接触。3.2管子检验
3.2.1输送有毒、可燃介质的管子,使用前应按设计文件要求核对管子的规格、数量和标记。
管子的质量证明书应包括以下内容:产品标准号;
钢的牌号;
炉罐号、批号、交货状态、重量和件数;4
品种名称、规格及质量等级;
5产品标准中规定的各项检验结果;6技术监督部门的印记。
3.2.3若到货管子的钢号、炉罐号与质量证明书不符或对特性数据有异议,供货方应按相应的标准作校验性检验或追溯到产品制造单位。异议未解决前,该批管子不得使用。3.2.4有耐晶间腐蚀要求的材料,产品质量证明书应注明晶间腐蚀试验结果,否则应按《不锈耐酸钢晶间腐蚀倾向试验方法》GB4334.1~9中的有关规定,进行补项试验。3.2.5SHA级管道中,设计压力等于或大于10MPa的管子,外表面应按下列方法逐根进行无损检测,不得有线性缺陷:1外径大于12mm的导磁性钢管,应采用磁粉检测;2非导磁性钢管,应采用渗透检测。3.2.6管子经磁粉或渗透检测发现的表面缺陷允许修磨,修磨后的实际壁厚不应小于管子公称壁厚的90%,且不得小于设计文件规定的最小壁厚。3.2.7SHA级管道中,设计压力小于I0MPa的输送极度危害介质的管子,每批(指同批号、同炉罐号、同材质、同规格)应抽5%且不少于一根,进行外表面磁粉或渗透检测,不得有线性缺陷。抽样检验不合格时,应按第3.1.7条的规定处理。5
3.2.8输送毒性程度为极度危害和高度危害介质管子的质量证明书中应有超声检测结果,否则应按现行《无缝钢管超声波探伤方法》GB5777或《不锈钢管超声波探伤方法》GB4163的规定,逐根进行补项试验。3.3阀门检验
3.3.1设计文件要求做低温密封试验的阀门,应有制造单位的低温密封性试验合格证明书。
用于SHA级管道的通用阀门,其焊缝或阀体、阀盖的铸钢件,应有符合现行《石油化工钢制通用阀门选用、检验及验收》SH3064规定的无损检测合格证明书。3.3.3阀门安装前,应按设计文件中的“阀门规格书”,对阀门的阀体和密封面,以及有特殊要求的垫片和填料的材质进行抽检,每批至少抽查一件。合金钢阀门的阀体应逐件进行快速光谱分析。若不符合要求,该批阀门不得使用。3.3.4阀门在安装前,应逐个对阀体进行液体压力试验,试验压力为公称压力的1.5倍,停压5min无泄漏为合格。
3.3.5具有上密封结构的阀门,应逐个对上密封进行试验,试验压力为公称压力的1.1倍。试验时应关闭上密封面,并松开填料压盖,停压4min,无渗漏为合格。3.3.6阀门液体压力试验和上密封试验应以洁净水为介质。不锈钢阀门液体压力试验时,水中的氯离子含量不得超过100mg/L试验合格后应立即将水渍清除干净。3.3.7阀门的阀座密封面应按现行《石油化工钢制通用阀门选用、检验及验收》SH3064的规定进行密封性试验。
3.3.8凡按现行《石油化工钢制通用阀门选用、检验及验收》SH3064或API标准制造并有相应认证标志,且用户到制造厂监造和验收的阀门,每批可按5%且不少于一个进行抽检,若有不合格,应按第3.1.7条的规定处理。3.3.9安全阀应按设计文件规定的开启压力进行调试。调压时压力应平稳,启闭试验不得少于三次。调试合格后,应及时进行铅封。3.3.10试验合格的阀门,应作出标识,并填写阀门试验记录。3.4其他管道组成件检验
对管道组成件的产品质量证明书,应进行核对,且下列项目应符合设计文件要求:
化学成分及力学性能;
2合金钢锻件的金相分析结果;
3热处理结果及焊缝无损检测报告。若对质量证明书中的特性数据有异议,应及时追溯到制造单位。异议未解决前,该批产品不得使用。
3.4.2SHA级管道的管件应按第3.2.5条和第3.2.7条的规定进行检验。3.4.3螺栓、螺母的螺纹应完整,无划痕、毛刺等缺陷。螺栓、螺母应配合良好,无松动或卡涩现象。
3.4.4设计压力等于或大于10MPa管道用的合金钢螺栓、螺母,应逐件进行快速光谱分析,每批应抽两件进行硬度检验,若有不合格,按第3.1.7条的规定处理。3.4.5设计温度低于-29℃的低温管道合金钢螺栓、螺母,应逐件进行快速光谱分析检验,每批应抽两根螺栓进行低温冲击性能检验。若有不合格,应按第3.1.7条的规定进行处理。
3.4.6其他合金钢管道组成件的快速光谱分析,每批应抽检5%,且不少于一件。若有不合格,应按第3.1.7条的规定处理。3.4.7耐油石棉橡胶板垫片和石棉橡胶板垫片的边缘应切割整齐,表面应平整光滑,不得有气泡、分层、折皱等缺陷。3.4.8制作耐油石棉橡胶板垫片和石棉橡胶板垫片时,不得在低于15℃的环境中进行。自板材制成之日起,耐油石棉橡胶板储存期限不得超过一年半,石棉橡胶板储存期限不得超过两年。
3.4.9法兰密封面、金属环垫、缠绕式垫片不得有径向划痕、松散、翘曲等缺陷。4管道预制及安装
4.1管道预制
4.1.1管道预制加工应按现场审查确认的设计单线图或依据管道平、剖面图绘制的单线图进行,预制加工图上应标注管线编号、现场组焊位置和调节裕量。4,1.2管道预制过程中的每一道工序,均应核对管子的标记,并做好标记的移植。不锈钢管道、低温钢管道,不得使用钢印作标记。4.1.3弯管最小弯曲半径应符合设计文件要求,当设计文件未规定时,应符合表4.1.3的规定。
表4.1.3弯管最小弯曲半径
管道设计压力(MPa)
注:D。为管子外径。
弯管制作方式
冷、热弯
最小弯曲半径
当设计允许用焊接钢管弯制弯管时,焊缝应避开受拉或受压区。4.1.4
4.1.5弯管制作后,弯管处的最小壁厚不得小于管子公称壁厚的90%。弯管处的最大外径与最小外径之差,应符合下列规定:SHA级管道应小于弯制前管子外径的5%;SHB、SHC及SHD级管道应小于弯制前管子外径的8%。2
4.1.6弯管制作后,直管段中心线偏差△不得大于1.5mm/m,且不得大于5mm。要源中心
实际中心
图4.1.6弯管中心偏差
4.1.7钢管热弯或冷弯后的热处理,应符合下列规定:钢管的热弯温度与弯后热处理应按表4.1.7-1的规定进行;2
钢管冷弯后的热处理应按表4.1.7-2的规定进行:3公称直径大于100mm或壁厚大于13mm的铁素体合金钢管弯制后,应进行消除应力的热处理;
4有应力腐蚀的冷弯弯管,应作消除应力的热处理;5热处理时的加热速度、恒温时间、冷却速度应符合本规范第5.4.9条的规定表4.1.7-1
钢管热弯温度及热处理
钢种或钢号
10,20
12CrMo
15CrMo
12CrIMo
ICr5Mo
1Cr18Ni9
Cr18Ni 12Mo2Ti
Cr25Ni20
热弯温度(℃)
7501050
900~1050
800~1050
800~1050
8001050
900~1200
热处理要求
900~920℃正火
9801020℃正火加720~760℃回火850~875℃完全退火或
725~750℃高温回火
1050~1100℃固溶化
注:①10、20号钢和16Mn钢的终弯温度低于900℃,壁厚等于或大于19mm的热弯管,应进行600650℃的回火处理:
②表中未列入的钢号,
应按该材料供货状态的要求进行热处理。表4.1.7-24
钢管冷弯后热处理
钢种或钢号
10,20
12CrMo
15CrMo
12CrIMov
1CrI8Ni9
Cr18Ni12Mo2Ti
Cr25Ni20
壁厚(mm)
弯曲半径
≤5Do
热处理要求
600~650℃退火
680~700℃退火
720~760℃退火
按设计文件要求
4.1.8SHA级管道弯制后应进行磁粉检测或渗透检测。若有缺陷应予以修磨,修磨后的壁厚不得小于管子公称壁厚的90%,且不得小于设计文件规定的最小壁厚。4.1.9SHA级管道弯管加工、检测合格后,应填写SHA级管道弯管加工记录,见附录B。4.1.10夹套管内的主管必须使用无缝钢管。当主管上有环焊缝时,该焊缝应经100%射线检测,经试压合格后方可进行隐蔽作业。套管与主管间的间隙应均匀,并按设计文件要求焊接支承块。4.1.11检验合格后的管道预制件应有标记,其内部不得有砂土、铁屑、熔渣及其他杂物,并封闭。存放时应防止损伤和污染。4.1.12管道采用螺纹法兰连接时,螺纹和密封面的加工、检验应符合设计文件的规定。4.2管道安装
4.2.1管道安装前,应逐件清除管道组成件内部的砂土、铁屑、熔渣及其他杂物。有特殊要求的管道,应按设计文件要求进行清除。清除合格后,应及时封闭。4.2.2管道上的开孔应在管段安装前完成。当在已安装的管道上开孔时,管内因切割而产生的异物应清除干净。
4.2.3管道安装时,应检查法兰密封面及垫片,不得有影响密封性能的划痕、锈斑等缺陷存在。
4.2.4安装前,法兰环槽密封面与金属环垫应作接触线检查。当金属环垫在密封面上转动45°后,检查接触线不得有间断现象。4.2.5有拧紧力矩要求的螺栓,应严格按设计文件规定的力矩拧紧。测力扳手应预先经过校验,允许偏差为土5%。带有测力螺帽的螺栓,必须紧到螺帽脱落。4.2.6流量孔板上、下游直管的长度应符合设计文件要求,且在此范围内的焊缝内表面应与管道内表面平齐。
4.2.7温度计套管及其他插入件的安装方向与长度,应符合《石油化工仪表工程施工技术规程》SH3521的要求。
4.2.8连接法兰的螺栓应能在螺栓孔中顺利通过。法兰密封面间的平行偏差及间距应符合表4.2.8的规定。
表4.2.8法兰密封面间的平行偏差及间距(mm)管道级别
SHB、SHC、SHD
DN≤300
平行偏差
DN>300
垫片厚+1.5
垫片厚+2.0
4.2.9与转动机器(以下简称机器)连接的管道,宜从机器侧开始安装,应先安装管支架。管道和阀门等的重量和附加力矩不得作用在机器上。管道的水平度或垂直度偏差应小于1mm/m。气体压缩机入口管道因水平偏差造成的坡度,应坡向分液罐一侧。4.2.10与机器连接的管道及其支、吊架安装完毕后,应卸下接管上的法兰螺栓,在自由状态下所有螺栓应能在螺栓孔中顺利通过。法兰密封面间的平行偏差、径向偏差及间距,当设计或制造厂未规定时,不应超过表4.2.10的规定值。
表4.2.10
法兰密封面平行偏差、径向偏差及间距机器旋转速度
(r /min)
3000~6000
平行偏差
径向偏差
垫片厚+1.5
垫片厚+1.0
垫片厚+1.0
4.2.11机器试车前,应对管道与机器的连接法兰进行最终连接检查。检查时,在联轴器上架设百分表监视其位移,然后松开和拧紧法兰连接螺栓进行观测。当转速大于6000r/min时,其位移值应小于0.02mm;当转速小于或等于6000r/min时,其位移值应小于0.05mm。
4.2.12管道系统试运行时,高温或低温管道的连接螺栓,应按下列规定进行热态紧固或冷态紧固
1螺栓热态紧固或冷态紧固作业的温度应符合表4.2.12的规定表4.2.12螺栓热态紧固、冷态紧固作业温度(℃)工作温度
250~350
.70~-29
一次热紧、冷紧
工作温度
工作温度
2热态紧固或冷态紧固应在紧固作业温度保持2h后进行;3紧固管道连接螺栓时,管道的最大内压力应符合下列规定:二次热紧、冷紧
工作温度
工作温度
a)当设计压力小于6MPa时,热态紧固的最大内压力应小于0.3MPa;b)当设计压力大于6MPa时,热态紧固的最大内压力应小于0.5MPa;c)冷态紧固应在卸压后进行。
4螺栓紧固应有安全技术措施,保障操作人员的安全。4.2.13有静电接地要求的管道,各段间应导电良好。当每对法兰或螺纹接头间电阻值大于0.032时,应有导线跨接。
4.2.14管道系统静电接地引线,宜采用焊接形式。对地电阻值及接地位置应符合设计文件要求。
4.2.15用作静电接地的材料或零件,安装前不得刷油。导电接触面必须除锈并连接可靠。
4.2.16有静电接地要求的不锈钢管道,导线跨接或接地引线应采用不锈钢板过渡,不得与不锈钢管直接连接。
4.2.17管道的静电接地安装完毕测试合格后,应及时填写管道静电接地测试记录4.2.18管道安装时,应同时进行支、吊架的固定和调整工作。支、吊架位置应正确,安装应牢固,管子和支承面接触应良好。4.2.19无热位移管道的管道吊架,其吊杆应垂直安装。有热位移管道的管道吊架,其吊点应在位移相反方向,按位移值的1/2偏位安装。4.2.20
D固定支架和限位支架应严格按设计文件要求安装。固定支架应在补偿装置预拉10
伸或预压缩前固定。
4.2.21导向支架或滑动支架的滑动面应洁净平整,不得有歪斜和卡涩现象。绝热层不得妨碍其位移。
4.2.22弹簧支、吊架的弹簧安装高度,应按设计文件规定进行调整。弹簧支架的限位板,应在试车前拆除。
4.2.23焊接支、吊架时,焊缝不得有漏焊、裂纹、高度和长度不够等缺陷。支架与管道焊接时,管子表面不得有咬边现象。4.2.24管道安装时,不宜使用临时支、吊架。当使用临时支、吊架时,不得将其焊在管道上。在管道安装完毕后,应及时更换成正式支、吊架。4.2.25管道安装完毕后,应按设计文件逐个核对、确认支、吊架的形式和位置。6“ⅡI”形补偿器安装,应按设计文件规定进行预拉伸或预压缩,允许偏差为预4.2.26
伸缩量的10%,且不大于10mm。
“Ⅱ”形补偿器水平安装时,平行臂应与管道坡度相同,垂直臂应呈水平状态。4.2.27波形补偿器安装,应按下列要求进行:按设计文件规定进行预拉伸或预压缩,受力应均匀;2波形补偿器内套有焊缝的一端,在水平管道上应位于介质流入端,在垂直管道上应置于上部;
3波形补偿器应与管道保持同轴,不得偏斜;4波形补偿器预拉伸或预压缩合格后,应设临时约束装置将其固定,待管道负荷运行前,再拆除临时约束装置。4.2.28管道补偿器安装调试合格后,应做好安装记录。5管道焊接
5.1一般规定
5.1.1施焊前,应根据焊接工艺评定编制焊接作业指导书。焊工应按指定的焊接作业指导书施焊。
5.1.2焊工应在合格的焊接项目内从事管道的焊接。连续中断合格项目焊接工作六个月以上,仍需担任压力管道焊接时,应重新考核。5.1.3焊材应具有产品质量证明书。焊条的药皮不得有脱落或明显裂纹。焊丝在使用前应清除其表面的油污、锈蚀等。焊条应按说明书或焊接作业指导书的要求进行烘烤,并在使用过程中保持干燥,出厂期超过一年的焊条,应进行焊条焊接工艺性能试验,合格后方可使用。5.1.4焊接环境温度低于下列要求时,应采取提高焊接环境温度的措施。非合金钢焊接,不低于-20℃;
低合金钢焊接,不低于.10℃;
奥氏体不锈钢焊接,不低于-5℃;3
其他合金钢焊接,不低于0℃。
管道的施焊环境若出现下列情况之一,而未采取防护措施时,应停止焊接工作。5.1.5
电弧焊焊接时,风速等于或大于8m/s;气体保护焊焊接时,风速等于或大于2m/s;11
小提示:此标准内容仅展示完整标准里的部分截取内容,若需要完整标准请到上方自行免费下载完整标准文档。
SH3501-2001
石油化工有毒、可燃介质管道
工程施工及验收规范
Specification for construction and acceptance of hypertoxic andcombustible medium piping engineering in petrochemical industry主编单位:中国石化集团第五建设公司批准部门:中华人民共和国国家经济贸易委员会2002-03-11发布
2002-05-01实施
中华人民共和国国家经济贸易委员会发布中华人民共和国国家经济贸易委员会二00二年第12号
关于发布《石油化工防火堤设计规范》等19项石油化工行业标准的公告
中国石油化工集团公司:
你公司报批的《石油化工防火堤设计规范》等19项石油化工行业标准草案,经国家经贸委批准,现予发布,自2002年5月1日起实施。标准名称、编号为:强制性标准:
序号标准编号
SH3125—2001
2.SH3059—2001
3.SH3021—2001
SH3126—2001
5.SH3020—2001
6.SH 3501—2001
7.SH3503—2001
8.SH3514-2001
SH3534—2001
10.SH3009-2001
推荐性标准:
序号标准编号
标准名称
石油化工防火堤设计规范
石油化工管道设计器材选用通则(代替SH3059-94、SH3059-1994)
石油化工仪表及管道隔离平吹洗设计规范代替SHJ21-90、SH3021-1990)
石油化工仪表及管道伴热和隔热设计规范(代替SHJ21—90、SH3021-1990)
石油化工仪表供气设计规范(代替SHJ20—90、SH3020-1990)石油化工剧毒、可燃介质管道工程施工及验收规范(代替SH3501-1997)
石油化工工程建设交工技术文件规定(代替SH3503—93、SH3503-1993)
石油化工设备安装工程质量检验评定标准(代替SHJ514-90、SH3514—1990)
石油化工筑炉工程施工及验收规范石油化工企业燃料气系统和可燃性气体排放系统设计规范(代替SHJ9-89、SH3009—2000)
标准名称
11.SH/T3110-2001石油化工设计能量消耗计算方法(代替SYJ1029-82、SH/T3110-2000)
SH/T3123-2001
13.SH/T3124-2001
石油化工钢储罐地基充水预压监测规程石油化工给水排水工艺流程设计图例SH/T 3517-2001
1石油化工钢制管道工程施工工艺标准(代替SHJ517-91、SH/T3517—1991)
15.SH/T3516—2001
催化裂化装置轴流压缩机-烟气轮机机组施工技术规程(代替SHJ516—90、SH/T3516—1990)石油化工立式圆筒形钢制储罐施工工艺标准(代替SH16.
SH/T 3530-2001
3530-93、SH/T3530-1993)
17.SH/T3127-2001
石油化工管式炉铬钼钢焊接回弯头技术规范2
SH/T3109-2001炼油厂添加剂设施设计规范(代替SYJ1025-82、SH/T3109—2000)
19.SH/T3096-2001
加工高硫原油重点装置主要设备设计选材导则(代替SH/T3096-1999)
中华人民共和国国家经济贸易委员会二00二年三月十一日
本规范是根据中国石化20011建标字088号文的通知,由我公司对《石油化工剧毒、可燃介质管道施工及验收规范》SH3501一1997进行修订而成本规范共分七章和三个附录。这次修订内容主要包括以下几个方面:1.将有关内容与GB50235一97进行了协调,修改条文主要有:第4.1.7条、第5.4.9条、第5.5.3~5.5.6条、第5.5.8条;2.将原规范中第2.0.1条管道分级规定进行了调整;3.修改了原规范中阀门检、试验的有关规定。在修订过程中,针对原规范中存在的问题,进行了广泛的调查研究,总结了近几年来石油化工管道施工方面的实践经验,并征求了有关施工、设计、生产等方面的意见,对其中的主要问题进行了多次讨论,最后经审查定稿。本规范在实施过程中,如发现需要修改补充之处,请将意见和有关资料提供给我公司,以便今后修订时参考。
我公司的通讯地址及邮政编码
通讯地址:甘肃省兰州市西固区康乐路35号邮政编码:730060
主编单位:中国石化集团第五建设公司主要起草人:姚代贵、张西庚、汪庆华、单承家1总则
1.0.1本规范适用于石油化工企业设计压力400Pa【绝压]】~42MPa【表压],设计温度.196~850℃的有毒(毒性程度为极度危害、高度危害、中度危害和轻度危害)、可燃介质钢制管道的新建、改建或扩建工程的施工及验收。1.0.2本规范不适用于长输管道及城镇公用燃气管道的施工及验收。1.0.3有毒、可燃介质管道施工除执行本规范的规定外,尚应符合设计文件的规定。1.0.4有毒、可燃介质管道施工时,修改设计或材料代用,应经设计单位批准。1.0.5管道施工的安全技术和劳动保护,应按国家现行的有关法规、标准及《石油化工施工安全技术规程》SH3505的规定执行。在已投入生产的区域内施工时,应按生产区域的特点制订施工安全技术措施。1.0.6承担有毒、可燃介质管道施工的单位,必须持有质量技术监督行政部门相应的压力管道安装许可证。
1.0.7从事有毒、可燃介质管道施工的焊工应按《锅炉压力容器压力管道焊工考试与管理规则》进行考试,取得合格证书。无损检测人员应按《锅炉压力容器无损检测人员资格考核规则》进行考核,取得相应资格证书。2管道分级
2.0.1输送有毒、可燃介质管道的分级,应符合《石油化工管道设计器材选用通则》SH3059的规定,见表2.0.1。
表2.0.1管道分级Www.bzxZ.net
管道级别
适用范围
毒性程度为极度危害介质管道(苯管道除外)2毒性程度为高度危害介质的丙烯睛、光气、二硫化碳和氟化氢介质管道3设计压力大于或等于10.0MPa的介质管道毒性程度为极度危害介质的苯管道2毒性程度为高度危害介质管道(丙烯、光气、二硫化碳和氟化氢管道除外)甲类、乙类可燃气体和甲类液化烃、甲:类、乙类可燃液体介质管道3
毒性程度为中度、轻度危害介质管道乙:类、丙类可燃液体介质管道设计温度低于-29℃的低温管道
注:常见毒性介质、可燃介质见附录A。2.0.2
输送同时具有毒性和可燃特性介质的管道,应按本规范中的高级别管道的处理。2.0.3
输送混合介质的管道,应以主导介质作为管道分级的依据。3管道组成件检验
3.1一般规定
3.1.1管道组成件(管子、阀门、管件、法兰、补偿器、安全保护装置等)的制造单位,应具有质量技术监督行政部门颁发的《压力管道元件制造单位安全注册证书》。3.1.2有毒、可燃介质管道工程使用的管道组成件,应符合设计文件规定及本规范的有关要求。
3.1.3管道组成件必须具有质量证明书或合格证,无质量证明书或合格证的产品不得使用。
产品在使用前,应对质量证明书认真审查,若对证明书中的特性数据有异议,应进行必要的分析检验。
3.1.4管道组成件在使用前应进行外观检查,其表面应符合下列要求:无裂纹、缩孔、夹渣、折叠、重皮等缺陷;锈蚀、凹陷及其他机械损伤的深度,不应超过产品相应标准允许的壁厚负偏差;2
螺纹、密封面、坡口的加工精度及粗糙度应达到设计文件要求或制造标准:3
4有产品标识。
3.1.5合金钢管道组成件主体的关键合金成分,应逐件采用快速光谱分析或其他方法复查,并作好标记。
3.1.6设计文件有低温冲击值要求的材料,产品质量证明书应有低温冲击韧性试验值,否则应按《金属低温夏比冲击试验方法》GB4159的规定进行补项试验。3.1.7凡按规定作抽样检查或检验的样品中,若有一件不合格,必须按原规定数加倍抽检,若仍有不合格,则该批管道组成件不得使用,并应作好标记和隔离。3.1.8管道组成件应分区存放。不锈钢与非合金钢、低合金钢管道组成件不得接触。3.2管子检验
3.2.1输送有毒、可燃介质的管子,使用前应按设计文件要求核对管子的规格、数量和标记。
管子的质量证明书应包括以下内容:产品标准号;
钢的牌号;
炉罐号、批号、交货状态、重量和件数;4
品种名称、规格及质量等级;
5产品标准中规定的各项检验结果;6技术监督部门的印记。
3.2.3若到货管子的钢号、炉罐号与质量证明书不符或对特性数据有异议,供货方应按相应的标准作校验性检验或追溯到产品制造单位。异议未解决前,该批管子不得使用。3.2.4有耐晶间腐蚀要求的材料,产品质量证明书应注明晶间腐蚀试验结果,否则应按《不锈耐酸钢晶间腐蚀倾向试验方法》GB4334.1~9中的有关规定,进行补项试验。3.2.5SHA级管道中,设计压力等于或大于10MPa的管子,外表面应按下列方法逐根进行无损检测,不得有线性缺陷:1外径大于12mm的导磁性钢管,应采用磁粉检测;2非导磁性钢管,应采用渗透检测。3.2.6管子经磁粉或渗透检测发现的表面缺陷允许修磨,修磨后的实际壁厚不应小于管子公称壁厚的90%,且不得小于设计文件规定的最小壁厚。3.2.7SHA级管道中,设计压力小于I0MPa的输送极度危害介质的管子,每批(指同批号、同炉罐号、同材质、同规格)应抽5%且不少于一根,进行外表面磁粉或渗透检测,不得有线性缺陷。抽样检验不合格时,应按第3.1.7条的规定处理。5
3.2.8输送毒性程度为极度危害和高度危害介质管子的质量证明书中应有超声检测结果,否则应按现行《无缝钢管超声波探伤方法》GB5777或《不锈钢管超声波探伤方法》GB4163的规定,逐根进行补项试验。3.3阀门检验
3.3.1设计文件要求做低温密封试验的阀门,应有制造单位的低温密封性试验合格证明书。
用于SHA级管道的通用阀门,其焊缝或阀体、阀盖的铸钢件,应有符合现行《石油化工钢制通用阀门选用、检验及验收》SH3064规定的无损检测合格证明书。3.3.3阀门安装前,应按设计文件中的“阀门规格书”,对阀门的阀体和密封面,以及有特殊要求的垫片和填料的材质进行抽检,每批至少抽查一件。合金钢阀门的阀体应逐件进行快速光谱分析。若不符合要求,该批阀门不得使用。3.3.4阀门在安装前,应逐个对阀体进行液体压力试验,试验压力为公称压力的1.5倍,停压5min无泄漏为合格。
3.3.5具有上密封结构的阀门,应逐个对上密封进行试验,试验压力为公称压力的1.1倍。试验时应关闭上密封面,并松开填料压盖,停压4min,无渗漏为合格。3.3.6阀门液体压力试验和上密封试验应以洁净水为介质。不锈钢阀门液体压力试验时,水中的氯离子含量不得超过100mg/L试验合格后应立即将水渍清除干净。3.3.7阀门的阀座密封面应按现行《石油化工钢制通用阀门选用、检验及验收》SH3064的规定进行密封性试验。
3.3.8凡按现行《石油化工钢制通用阀门选用、检验及验收》SH3064或API标准制造并有相应认证标志,且用户到制造厂监造和验收的阀门,每批可按5%且不少于一个进行抽检,若有不合格,应按第3.1.7条的规定处理。3.3.9安全阀应按设计文件规定的开启压力进行调试。调压时压力应平稳,启闭试验不得少于三次。调试合格后,应及时进行铅封。3.3.10试验合格的阀门,应作出标识,并填写阀门试验记录。3.4其他管道组成件检验
对管道组成件的产品质量证明书,应进行核对,且下列项目应符合设计文件要求:
化学成分及力学性能;
2合金钢锻件的金相分析结果;
3热处理结果及焊缝无损检测报告。若对质量证明书中的特性数据有异议,应及时追溯到制造单位。异议未解决前,该批产品不得使用。
3.4.2SHA级管道的管件应按第3.2.5条和第3.2.7条的规定进行检验。3.4.3螺栓、螺母的螺纹应完整,无划痕、毛刺等缺陷。螺栓、螺母应配合良好,无松动或卡涩现象。
3.4.4设计压力等于或大于10MPa管道用的合金钢螺栓、螺母,应逐件进行快速光谱分析,每批应抽两件进行硬度检验,若有不合格,按第3.1.7条的规定处理。3.4.5设计温度低于-29℃的低温管道合金钢螺栓、螺母,应逐件进行快速光谱分析检验,每批应抽两根螺栓进行低温冲击性能检验。若有不合格,应按第3.1.7条的规定进行处理。
3.4.6其他合金钢管道组成件的快速光谱分析,每批应抽检5%,且不少于一件。若有不合格,应按第3.1.7条的规定处理。3.4.7耐油石棉橡胶板垫片和石棉橡胶板垫片的边缘应切割整齐,表面应平整光滑,不得有气泡、分层、折皱等缺陷。3.4.8制作耐油石棉橡胶板垫片和石棉橡胶板垫片时,不得在低于15℃的环境中进行。自板材制成之日起,耐油石棉橡胶板储存期限不得超过一年半,石棉橡胶板储存期限不得超过两年。
3.4.9法兰密封面、金属环垫、缠绕式垫片不得有径向划痕、松散、翘曲等缺陷。4管道预制及安装
4.1管道预制
4.1.1管道预制加工应按现场审查确认的设计单线图或依据管道平、剖面图绘制的单线图进行,预制加工图上应标注管线编号、现场组焊位置和调节裕量。4,1.2管道预制过程中的每一道工序,均应核对管子的标记,并做好标记的移植。不锈钢管道、低温钢管道,不得使用钢印作标记。4.1.3弯管最小弯曲半径应符合设计文件要求,当设计文件未规定时,应符合表4.1.3的规定。
表4.1.3弯管最小弯曲半径
管道设计压力(MPa)
注:D。为管子外径。
弯管制作方式
冷、热弯
最小弯曲半径
当设计允许用焊接钢管弯制弯管时,焊缝应避开受拉或受压区。4.1.4
4.1.5弯管制作后,弯管处的最小壁厚不得小于管子公称壁厚的90%。弯管处的最大外径与最小外径之差,应符合下列规定:SHA级管道应小于弯制前管子外径的5%;SHB、SHC及SHD级管道应小于弯制前管子外径的8%。2
4.1.6弯管制作后,直管段中心线偏差△不得大于1.5mm/m,且不得大于5mm。要源中心
实际中心
图4.1.6弯管中心偏差
4.1.7钢管热弯或冷弯后的热处理,应符合下列规定:钢管的热弯温度与弯后热处理应按表4.1.7-1的规定进行;2
钢管冷弯后的热处理应按表4.1.7-2的规定进行:3公称直径大于100mm或壁厚大于13mm的铁素体合金钢管弯制后,应进行消除应力的热处理;
4有应力腐蚀的冷弯弯管,应作消除应力的热处理;5热处理时的加热速度、恒温时间、冷却速度应符合本规范第5.4.9条的规定表4.1.7-1
钢管热弯温度及热处理
钢种或钢号
10,20
12CrMo
15CrMo
12CrIMo
ICr5Mo
1Cr18Ni9
Cr18Ni 12Mo2Ti
Cr25Ni20
热弯温度(℃)
7501050
900~1050
800~1050
800~1050
8001050
900~1200
热处理要求
900~920℃正火
9801020℃正火加720~760℃回火850~875℃完全退火或
725~750℃高温回火
1050~1100℃固溶化
注:①10、20号钢和16Mn钢的终弯温度低于900℃,壁厚等于或大于19mm的热弯管,应进行600650℃的回火处理:
②表中未列入的钢号,
应按该材料供货状态的要求进行热处理。表4.1.7-24
钢管冷弯后热处理
钢种或钢号
10,20
12CrMo
15CrMo
12CrIMov
1CrI8Ni9
Cr18Ni12Mo2Ti
Cr25Ni20
壁厚(mm)
弯曲半径
≤5Do
热处理要求
600~650℃退火
680~700℃退火
720~760℃退火
按设计文件要求
4.1.8SHA级管道弯制后应进行磁粉检测或渗透检测。若有缺陷应予以修磨,修磨后的壁厚不得小于管子公称壁厚的90%,且不得小于设计文件规定的最小壁厚。4.1.9SHA级管道弯管加工、检测合格后,应填写SHA级管道弯管加工记录,见附录B。4.1.10夹套管内的主管必须使用无缝钢管。当主管上有环焊缝时,该焊缝应经100%射线检测,经试压合格后方可进行隐蔽作业。套管与主管间的间隙应均匀,并按设计文件要求焊接支承块。4.1.11检验合格后的管道预制件应有标记,其内部不得有砂土、铁屑、熔渣及其他杂物,并封闭。存放时应防止损伤和污染。4.1.12管道采用螺纹法兰连接时,螺纹和密封面的加工、检验应符合设计文件的规定。4.2管道安装
4.2.1管道安装前,应逐件清除管道组成件内部的砂土、铁屑、熔渣及其他杂物。有特殊要求的管道,应按设计文件要求进行清除。清除合格后,应及时封闭。4.2.2管道上的开孔应在管段安装前完成。当在已安装的管道上开孔时,管内因切割而产生的异物应清除干净。
4.2.3管道安装时,应检查法兰密封面及垫片,不得有影响密封性能的划痕、锈斑等缺陷存在。
4.2.4安装前,法兰环槽密封面与金属环垫应作接触线检查。当金属环垫在密封面上转动45°后,检查接触线不得有间断现象。4.2.5有拧紧力矩要求的螺栓,应严格按设计文件规定的力矩拧紧。测力扳手应预先经过校验,允许偏差为土5%。带有测力螺帽的螺栓,必须紧到螺帽脱落。4.2.6流量孔板上、下游直管的长度应符合设计文件要求,且在此范围内的焊缝内表面应与管道内表面平齐。
4.2.7温度计套管及其他插入件的安装方向与长度,应符合《石油化工仪表工程施工技术规程》SH3521的要求。
4.2.8连接法兰的螺栓应能在螺栓孔中顺利通过。法兰密封面间的平行偏差及间距应符合表4.2.8的规定。
表4.2.8法兰密封面间的平行偏差及间距(mm)管道级别
SHB、SHC、SHD
DN≤300
平行偏差
DN>300
垫片厚+1.5
垫片厚+2.0
4.2.9与转动机器(以下简称机器)连接的管道,宜从机器侧开始安装,应先安装管支架。管道和阀门等的重量和附加力矩不得作用在机器上。管道的水平度或垂直度偏差应小于1mm/m。气体压缩机入口管道因水平偏差造成的坡度,应坡向分液罐一侧。4.2.10与机器连接的管道及其支、吊架安装完毕后,应卸下接管上的法兰螺栓,在自由状态下所有螺栓应能在螺栓孔中顺利通过。法兰密封面间的平行偏差、径向偏差及间距,当设计或制造厂未规定时,不应超过表4.2.10的规定值。
表4.2.10
法兰密封面平行偏差、径向偏差及间距机器旋转速度
(r /min)
3000~6000
平行偏差
径向偏差
垫片厚+1.5
垫片厚+1.0
垫片厚+1.0
4.2.11机器试车前,应对管道与机器的连接法兰进行最终连接检查。检查时,在联轴器上架设百分表监视其位移,然后松开和拧紧法兰连接螺栓进行观测。当转速大于6000r/min时,其位移值应小于0.02mm;当转速小于或等于6000r/min时,其位移值应小于0.05mm。
4.2.12管道系统试运行时,高温或低温管道的连接螺栓,应按下列规定进行热态紧固或冷态紧固
1螺栓热态紧固或冷态紧固作业的温度应符合表4.2.12的规定表4.2.12螺栓热态紧固、冷态紧固作业温度(℃)工作温度
250~350
.70~-29
一次热紧、冷紧
工作温度
工作温度
2热态紧固或冷态紧固应在紧固作业温度保持2h后进行;3紧固管道连接螺栓时,管道的最大内压力应符合下列规定:二次热紧、冷紧
工作温度
工作温度
a)当设计压力小于6MPa时,热态紧固的最大内压力应小于0.3MPa;b)当设计压力大于6MPa时,热态紧固的最大内压力应小于0.5MPa;c)冷态紧固应在卸压后进行。
4螺栓紧固应有安全技术措施,保障操作人员的安全。4.2.13有静电接地要求的管道,各段间应导电良好。当每对法兰或螺纹接头间电阻值大于0.032时,应有导线跨接。
4.2.14管道系统静电接地引线,宜采用焊接形式。对地电阻值及接地位置应符合设计文件要求。
4.2.15用作静电接地的材料或零件,安装前不得刷油。导电接触面必须除锈并连接可靠。
4.2.16有静电接地要求的不锈钢管道,导线跨接或接地引线应采用不锈钢板过渡,不得与不锈钢管直接连接。
4.2.17管道的静电接地安装完毕测试合格后,应及时填写管道静电接地测试记录4.2.18管道安装时,应同时进行支、吊架的固定和调整工作。支、吊架位置应正确,安装应牢固,管子和支承面接触应良好。4.2.19无热位移管道的管道吊架,其吊杆应垂直安装。有热位移管道的管道吊架,其吊点应在位移相反方向,按位移值的1/2偏位安装。4.2.20
D固定支架和限位支架应严格按设计文件要求安装。固定支架应在补偿装置预拉10
伸或预压缩前固定。
4.2.21导向支架或滑动支架的滑动面应洁净平整,不得有歪斜和卡涩现象。绝热层不得妨碍其位移。
4.2.22弹簧支、吊架的弹簧安装高度,应按设计文件规定进行调整。弹簧支架的限位板,应在试车前拆除。
4.2.23焊接支、吊架时,焊缝不得有漏焊、裂纹、高度和长度不够等缺陷。支架与管道焊接时,管子表面不得有咬边现象。4.2.24管道安装时,不宜使用临时支、吊架。当使用临时支、吊架时,不得将其焊在管道上。在管道安装完毕后,应及时更换成正式支、吊架。4.2.25管道安装完毕后,应按设计文件逐个核对、确认支、吊架的形式和位置。6“ⅡI”形补偿器安装,应按设计文件规定进行预拉伸或预压缩,允许偏差为预4.2.26
伸缩量的10%,且不大于10mm。
“Ⅱ”形补偿器水平安装时,平行臂应与管道坡度相同,垂直臂应呈水平状态。4.2.27波形补偿器安装,应按下列要求进行:按设计文件规定进行预拉伸或预压缩,受力应均匀;2波形补偿器内套有焊缝的一端,在水平管道上应位于介质流入端,在垂直管道上应置于上部;
3波形补偿器应与管道保持同轴,不得偏斜;4波形补偿器预拉伸或预压缩合格后,应设临时约束装置将其固定,待管道负荷运行前,再拆除临时约束装置。4.2.28管道补偿器安装调试合格后,应做好安装记录。5管道焊接
5.1一般规定
5.1.1施焊前,应根据焊接工艺评定编制焊接作业指导书。焊工应按指定的焊接作业指导书施焊。
5.1.2焊工应在合格的焊接项目内从事管道的焊接。连续中断合格项目焊接工作六个月以上,仍需担任压力管道焊接时,应重新考核。5.1.3焊材应具有产品质量证明书。焊条的药皮不得有脱落或明显裂纹。焊丝在使用前应清除其表面的油污、锈蚀等。焊条应按说明书或焊接作业指导书的要求进行烘烤,并在使用过程中保持干燥,出厂期超过一年的焊条,应进行焊条焊接工艺性能试验,合格后方可使用。5.1.4焊接环境温度低于下列要求时,应采取提高焊接环境温度的措施。非合金钢焊接,不低于-20℃;
低合金钢焊接,不低于.10℃;
奥氏体不锈钢焊接,不低于-5℃;3
其他合金钢焊接,不低于0℃。
管道的施焊环境若出现下列情况之一,而未采取防护措施时,应停止焊接工作。5.1.5
电弧焊焊接时,风速等于或大于8m/s;气体保护焊焊接时,风速等于或大于2m/s;11
小提示:此标准内容仅展示完整标准里的部分截取内容,若需要完整标准请到上方自行免费下载完整标准文档。

标准图片预览:

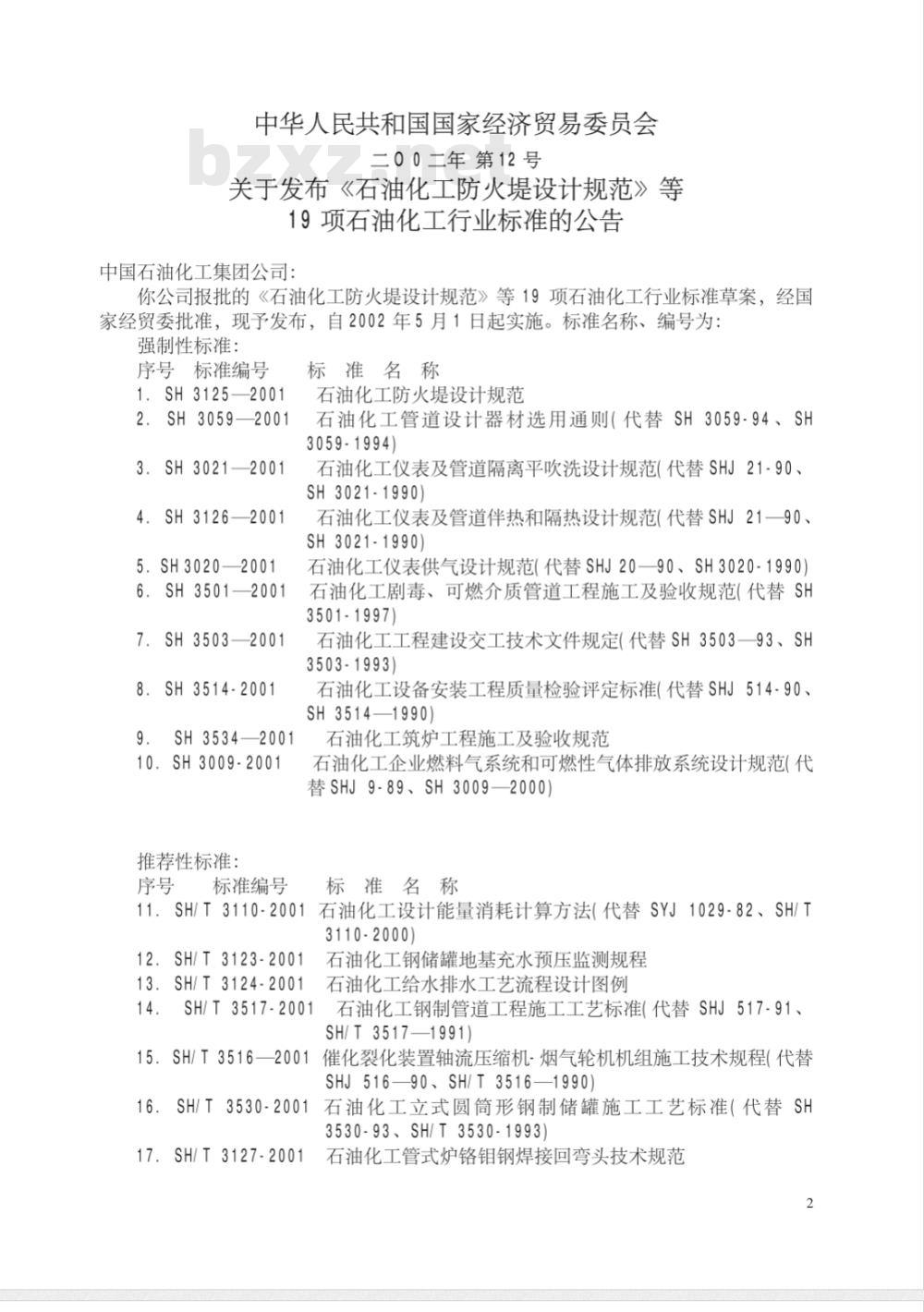
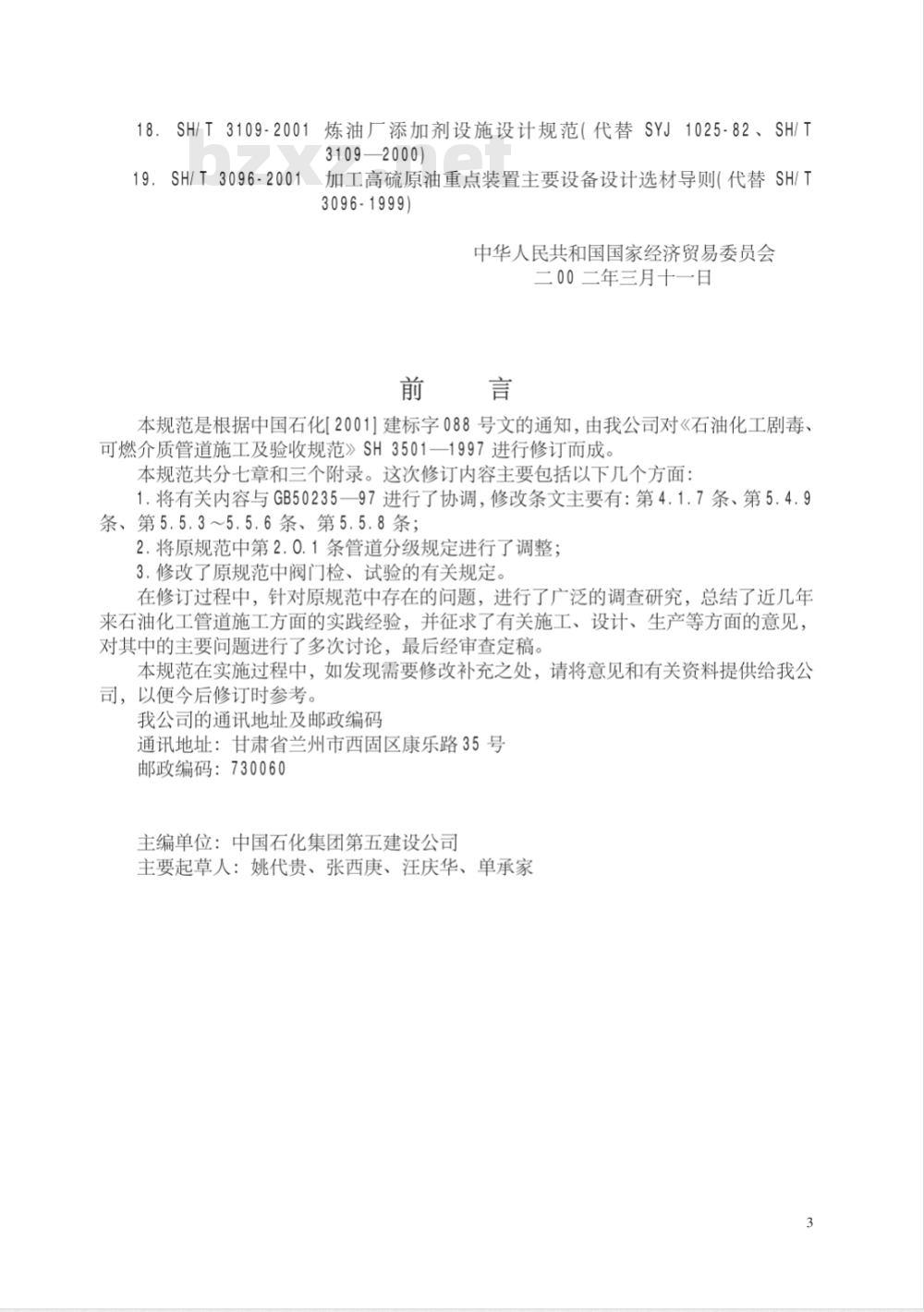
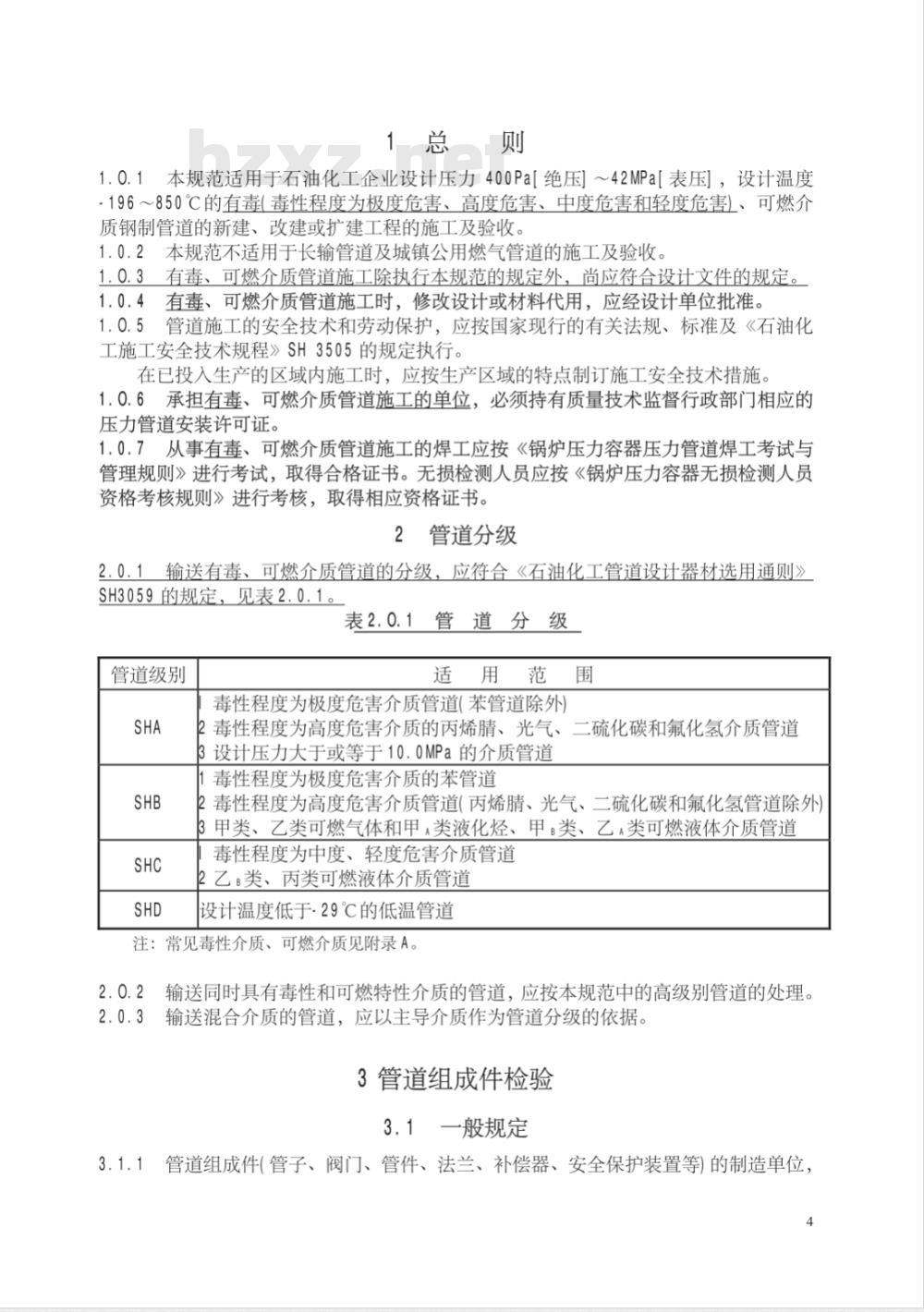
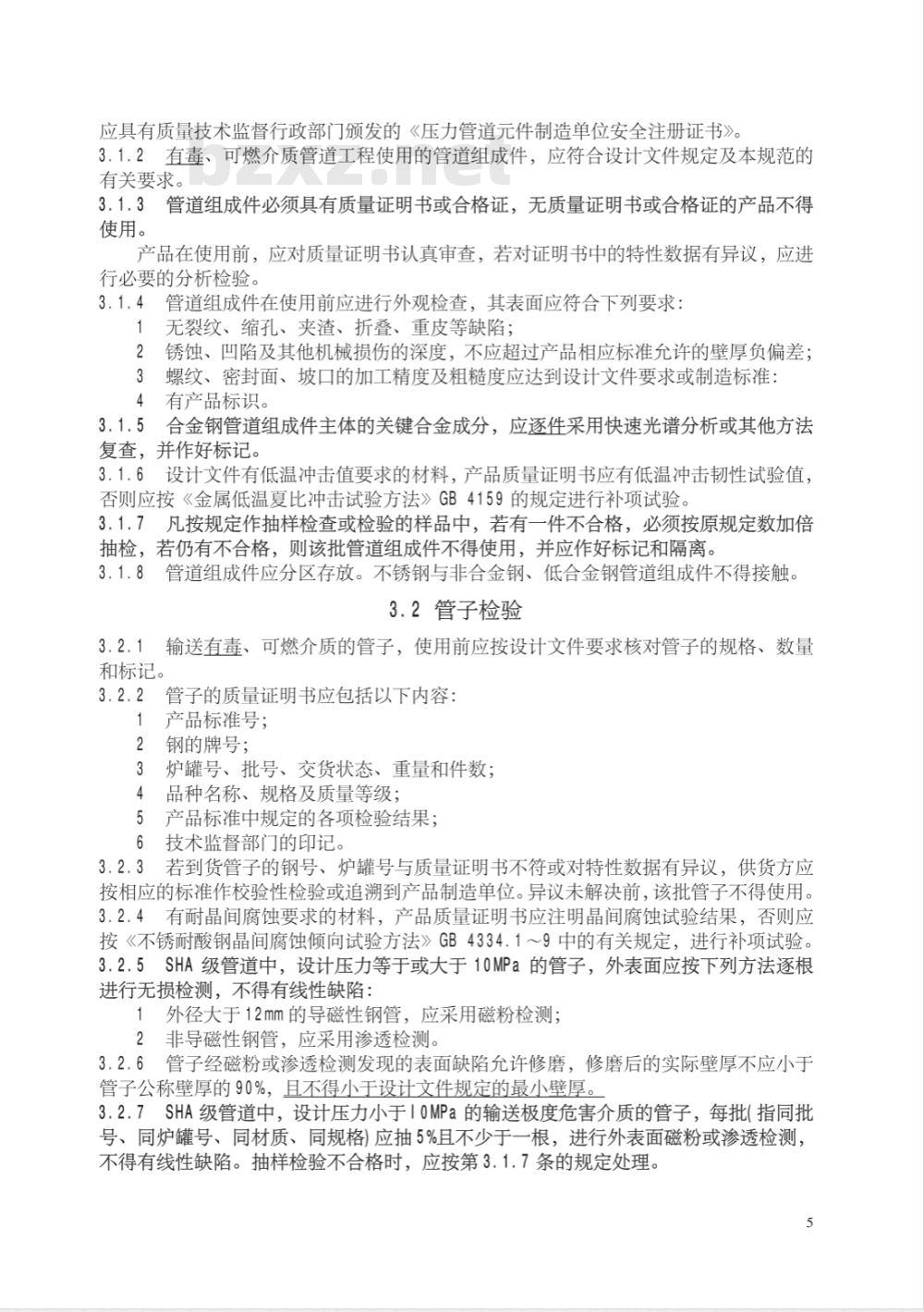
- 其它标准
- 热门标准
- 石油化工行业标准(SH)
- SH/T3405-2017 石油化工钢管尺寸系列
- SH/T0024-1990 润滑油沉淀值测定法
- SH/T0036-1990 防锈油水置换性试验法
- SHS07003-2004 单组合仪表
- SH/T3555-2014 石油化工工程钢脚手架搭设安全技术规范
- SH/T0218-1992 防锈油脂试验试片制备法
- SH/T0556-1993 石油蜡含油量测定法(丁桐--甲苯法)
- SH/T0588-1994 石油蜡体积收缩率测定法
- SH/T0118-1992 溶剂油芳香烃含量测定法
- SH/T3092-1999 石油化工分散控制系统设计规范
- SH/T3503-2007 石油化工建设工程项目交工技术文件规定(中英文表格)
- SH/T0605-2008 润滑油及添加剂中钼含量的测定 原子吸收光谱法
- SH/T0028-1990 润滑油清净剂浊度测定法
- SH/T1499.7-1997 精己二酸中硝酸含量的测定 分光光度法
- SH/T0403-1992 石蜡色度测定法
- 行业新闻
请牢记:“bzxz.net”即是“标准下载”四个汉字汉语拼音首字母与国际顶级域名“.net”的组合。 ©2009 标准下载网 www.bzxz.net 本站邮件:bzxznet@163.com
网站备案号:湘ICP备2023016450号-1
网站备案号:湘ICP备2023016450号-1