- 您的位置:
- 标准下载网 >>
- 标准分类 >>
- 水产行业标准(SC) >>
- SC/T 8036-1994 渔船轴系及螺旋桨修理技术要求
标准号:
SC/T 8036-1994
标准名称:
渔船轴系及螺旋桨修理技术要求
标准类别:
水产行业标准(SC)
标准状态:
现行-
发布日期:
1994-11-01 -
实施日期:
1995-01-01 出版语种:
简体中文下载格式:
.rar.pdf下载大小:
864.04 KB
替代情况:
替代SC 36-79

点击下载
标准简介:
标准下载解压密码:www.bzxz.net
本标准规定了渔船轴系修理及螺旋桨装配技术要求。本标准适用渔船轴系及螺旋桨修理及验收, SC/T 8036-1994 渔船轴系及螺旋桨修理技术要求 SC/T8036-1994

部分标准内容:
中华人民共和国水产行业标准
渔船轴系及螺旋浆修理技术要求1主题内容与适用范围
本标准规定了渔船轴系修理及螺旋奖装配技术要求。本标准适用渔船轴系及螺旋桨修理及验收。2 引用标准
GB1184形状和位置公差
3轴系修理技术婴求
3.1中间轴,尾轴及联轴节修换技术要求SC/T 8036—94
代替 SC 36 --79
3.1.1铸锻件如工要求
3.1.1.1中间轴、尾轴及联轴节锻件成品,不得有过烧现象,表面不允许有裂纹,折痕,夹渣,夹层及密集的发纹,轴端部不得有缩孔或疏松。3.1.1.2表面缺陷若能在加工后保证去除,而且不影响表面质量时允许存留。3.1.1.3联轴节非接合面允许存留个别不大的凹陷,刻痕或黑点,允许用焊补的方法修补表面缺陷,大面积焊补后应重新热处理。
3.1.1.4中间轴,尾轴及联轴节铸锻件应经高温退火或回火,以消除内应力,并获得均匀细致的结晶组织。
3.1.1.5热轧钢材可不必再作热处理,但当中间轴采用焊接法兰时,必须进行整体或局部退火。局部退火加热部位应包括除法兰以外,不少于一半轴颈长度,轴与法兰的焊接,应采用合理的接缝,建议将轴端镦粗进行焊接,或者采用V型接缝焊接法兰。3.1.1.6中间轴、尾轴经粗加工后应进行退火处理,以消除切削应力。在轴经小于150mm时,允许采用控制最后三到四道切前量的办法(进刀小于0.207mm)减少切削应力,此时可不进行退火处理。3.1.1.7中间轴、尾轴加工后表面应光洁,不得有密集发纹、裂缝,蜂窝孔或非金属夹杂物,非工作面上个别较细的凹陷,刻痕或黑斑经清理后允许存在,对表面质量有怀疑处应进行探伤检查。3.1.2中间轴、尾轴
3.1.2.1中间轴、尾轴的工作轴颈,锥体法兰及法兰定位凸肩外圆相对于轴中心线的径向跳动公差,新制中间轴,尾轴应不低于GB1184规定的7级精度,精车修理不低于8级精度,在轴的长径比L/D大于30时,应不低于9级精度。
新制轴的非工作轴径相对于轴中心线的径向跳动公差应不低于GB1184规定的10级精度,见表1。
修理中未经精车修理的中间轴,尾轴径向跳动公差值为相应各值的3倍。中华人民共和国农业部1994-11-01批准268
1995-01-01实施
糟度等级
公称尺寸,mm
>50~120
>120~250
>250~500
SC/T8036-94
3.1.2.2中间轴、尾轴及联轴节法兰,法兰定位凸肩相对于轴中心线的垂直度公差,新制时应符合GB1184规定的5级精度,精车修理时应符合7级精度,且只准内凹,不能外凸。未精车的法兰,垂直度应不低于8级精度的规定,见表2,端面跳动应小于0.04mm。糖度等级
公称尺寸,mm
>63~100
>100~160
>160~250
>250~400
>400~630
3.1.2.3中间轴、尾轴工作轴颈的圆度和圆柱度公差,新制轴及精车后应不低于GB1184规定的8级精度,轴承档长度大于轴径时每增加100mm,圆柱度允差可增加0.01mm。中间轴磨耗极限应不低于11级精度,尾轴不低于12级精度,低于这个标准时,必须修复。3.1.2.4经加工后的非工作轴径的圆度公差,应不低于GB1184规定的10级精度,见表3。表3
糖度等级
公称尺寸
>30~50
>50~80
>80~120
>120~180
3.1.2.5轴上的螺纹应光洁,在与螺母旋合时,不应有可感觉到的松动,在最初3~4牙用手轻便的旋入,用扳手可以顺利旋到底,螺纹轻度碰损,允许修锉后继续使用,较重的碰损应车削修理。此刻若螺纹直径减少较多时,应进行强度校核。3.1.2.6键槽与平键加工技术要求a.
键槽宽度应一致,在任何位置测量时,其槽侧二面平行度偏差应不小于0.03mm。在任何位置测量键槽高度时,每10mm高不得超过0.10mm。键槽两侧与轴中心线应平行,平行度每100mm不超过0.01mm。尾轴键槽允许重新铣直加宽,其极限宽度为锥体平均轴颈的0.33倍。平键四侧应光洁平直,在平板上检查时应插不进0.05mm厚薄规。269
SC/T8036-94
键槽底应有R=1~3mm的圆角,与螺旋桨相配之键槽首端最好制成雪撬形,以减少应力集平键两侧允许借偏心,偏中量不得超过键宽的5%,但最大不得超过2mm。3.1.2.7中间轴或尾轴凡是车削轴颈(或铜套)时,法兰平面都应切削并允许留黑。3.1.2.8中间轴、尾轴换新或修理加工后,表面粗糙度要求见图1。曼
3.1.2.9经车削修理的中间轴或尾轴,轴承部位轴颈最少不小于非工作轴颈外径,并允许堆焊后精车,低温镀铁及金属喷镀等方法予以加大。3.1.2.10采用堆焊修理轴颈时,预热温度按表4选取,焊后进行退火处理。表4
轴材含碳量,%
堆焊预热温度,C
0.2以下
100~120
3.1.2.11尾轴锥体大端锈蚀检查a.
120~~150
0. 3~~0. 45
150~250
0.45以上
250~400
当锈蚀为圆状,且个别锈蚀处深不超过0.03d,较长锈蚀深不超过0.02d,整个圆周锈蚀深不超过0.015d,经清理检查后允许继续使用(d—轴颈直径)。b.当锈蚀为尖角状,应仔细检查其深度与周长长度,然后应修锉或车削成圆弧状,并须探伤检查,凡深度符合上述a条要求时,可允许继续使用。当蚀深超过上述规定时,应将锈蚀处车去,车削后轴径必须经过强度校核合格,方准继续使用。C
3.1.3轴端法兰螺孔与连接螺栓
3.1.3.1法兰连接螺栓,其中紧配螺栓数目应不少于总数的50%要求紧松螺栓间隔排列相配,紧配螺栓与螺孔的配合加工精度见表5。表5
螺栓直径
配合间隙
圆柱度
圆柱度
30以下
0.005~0.005
51~70
SC/T 8036-94
3.1.3.2锥形螺栓应与锥孔均匀接触,接触面积在75%以上。3.1.3.3经加工修理后的中间轴,尾轴,法兰螺孔边缘至法兰外圆的厚度,不应少于连接螺栓直径的0.3倍,法兰的厚度不应小于基本轴径的0.2倍。3.1.3.4绞削连接螺孔时,应将成对的轴安放在合理支承上,见图2,并使相配法兰的偏移与曲折皆为0。Www.bzxZ.net
ar-b,=n.21.
= br= 0. 2.
3.1.3.5在修理中,螺栓杆体上不大的擦伤或刮痕,螺孔内表面少量的刮痕允许修刮后继续使用。螺栓材料强度不得低于中间轴或尾轴材料的强度,一般需用35号钢或40号钢。3.1.3.6新制螺栓装配后的旋紧余量为6~~12mm图3尺寸A),螺栓与螺孔装配后,螺栓头或螺母的支承面与法兰之间应紧密接触,在80%周长上应插不进0.05mm厚薄规,并应采用双螺母或槽形螺母等防松装置,以免松动。
3.1.4中间轴,尾轴可拆联轴节
3.1.4.1法兰式可拆联轴节加工技术要求见图4联轴节法兰外表的精加工,应在锥孔修拂后套装到轴上进行其粗糙度和加工技术要求与整锻法兰相同。
其键槽加工的宽度、高度与轴线平行度都与轴键槽加工要求相同,以最终与轴键相配质量为验b.
救标准。
SC/T 8036-94
3.1.4.2法兰式可拆联轴节装配技术要求如下:(0. 02~0.03
联轴节锥孔与轴锥体接触应良好,接触面积在75%以上。a.
联轴节锥孔与轴锥体在采用环氧树脂胶合安装时,其接触面积不少于30%。b.
平键与轴键槽两侧接触面积不少于 75%,与联轴节键槽相配时在 85%长度上应插不进0.05mm的厚薄规,其余部分应插不进0.10mm,平键与轴键槽底应接触,接触面不少于30%~~40%。d,联轴节紧固螺母安装后,接合面的90%周长上,应插不进0.05mm厚薄规,其接触面积不少于75%,并有可靠的防松装置。
3.1.5轴衬套及保护层。
3.1.5.1尾轴铜衬套材料及铸件检查:衬套材料ZCuSn10Zn2。
铜衬套不允许有裂纹,密集气孔,疏松和砂眼等缺陷,对于不甚严重的缺陷允许经修补后使用。b.
铜衬套经粗加工后,套装在轴上之前,如表面有不甚严重之砂眼、疏松等缺陷,应进行水压试验,试验压力为0.1MPa,5min内不得有渗漏。轴套表面产生渗漏的个别小空隙,允许用焊补,熔锡或填补塑料等方法予以消除,处理后应再经水压试验。3.1.5.2轴套加工时,轴套内圆粗糙度不得低于√其圆柱度和圆度应符合GB1184规定的9级精度,见表6。
轴颈直径d.mm
公差值,m
80~120
121~180
181~250
3.1.5.3铜衬套红套轴上时,加热温度一般不超过320℃。套合后应紧密,不许采用螺钉或其他止动钉的办法来固定轴套,不许采用两半焊接的组合铜衬套。3.1.5.4尾轴铜衬套(般在油封装置处)允许小段镶套,接缝处应车有凸肩,镶套后外圆精车,接缝处不能塞进0.05mm厚薄规,超过0.10mm时应加填料或焊锡,保持水密。3.1.5.5尾轴铜衬套厚度要求见表7。272
计算式
新制最小厚度
t≥0. 03d +7. 5
注:①表中d为尾轴直径,mm,
SC/T 8036-94
非工作轴颈部位
to≥0.75t
光车修理时厚度
t:≥0.02d+4
②填料函部位锅衬套极限厚度照上述规定可适当放低要求,但最薄不得低于4mm。3.1.5.6轴套修理技术要求
a.轴套部分裂缝,允许只换损坏部分,其接缝应符合第3.1.5.3条的规定。极限厚度
tj0. 15d-+ 3. 5
b.轴套表面明显磨损,应予少量精车留黑,但残留磨痕深度不得大于0.20mm,在填料部位轴套精车后允许残留磨痕,深度不大于0.40mm,圆周不大于1/4元d。3.1.5.7非工作轴颈玻璃钢保护层的技术质量要求。a。玻璃布的卷向应与螺旋桨转向相反,应从尾端向前端包裹,玻璃布的重叠层不少于二层,每圈重叠量为15~30mm。
b.严格按照磷化底漆及环氧树脂的工艺要求,在包裹中,应随时将气泡挤出,硬化后严禁有连续气泡存在,表面应光洁无毛刺。C、对玻璃钢接口不良,局部破损,脱壳,泛黄锈和膨胀现象应予修补,允许采用局部涂环氧树脂或一段进行包裹的方法修补。
d、对玻璃钢保护层严禁硬物冲击或碰撞,严禁与腐蚀性介质接触,在吊运时,严禁在玻璃钢外直接缠钢丝绳。
3.2轴系轴承修理技术要求
3.2.1中间轴承
3.2.1.1轴承座与轴承盖的技术要求铸件不允许有裂纹,缩孔,疏松,绕不足等严重缺陷,对于较小缺陷允许经修补后使用,铸件应a.
彻底清理干净,并进行必要的热处理,以消除内应力。b.盖与座的接合面应与轴中心线平行,平行度每米不超过0.20mm,各接合面应光洁平直。c.盖与座两端阻油羊毛毡,可比轴瓦白合金面略高0.20~0.50mm不应过高,致使中间轴搁空发热。
3.2.1.2白合金轴承浇铸质量和装配要求:a.浇铸白合金材料可为ZChSn82Sb11-6、ZChSnSb7,5-3等,轴瓦浇铸表面不应有裂纹,疏松和密集气泡等缺陷,不允许用不同牌号的白合金混杂浇铸,熔融的白合金不得有过烧现象。b.白合金与瓦底的粘合质量应良好,不应有脱壳现象存在。白合金壁厚应力求均匀,厚薄差不得大于壁厚的20%,粘合白合金的轴承表面粗糙度应在以上,以保证粘结强度。c.轴颈与白合金轴承应进行拂刮,在底部60°范围内接触面积达65%以上,即每25×25mm内有2~3个接触点。
d.轴瓦的背面与轴承座内圆应均匀接触,接触面积在65%以上,允许用冷压或锤击的方法,涨大其圆颈后进行修拂,要求在没有负荷作用下,轻轻敲击便可取出轴瓦。甩油圈不许漏装,要求二个半圈结合良好。e,
f.轴瓦白合金显著脱壳,严重过热和咬损,应予重浇白合金。3.2.2中间轴承垫片
3.2.2.1轴承垫片接触,其面积至少应为轴承底座面积的50%。3.2.2.2钢质垫片最大厚度等于小于75mm,最小厚度等于大于6mm。3.2.2.3铸铁垫片厚度最大厚度等于小于75mm,最小厚度等于大于10mm。3.2.2.4允许加装少量的金属薄垫片,需要整块使用,并且有足够的接触面积。273
3.2.2.5轴承垫片加工要求:
SC/T 8 0 3 6-9 4
金属厚垫片各平面应平正,在平板上检查应插不进0.05mm厚薄规,球形接触面间亦应插不进a.
0.05mm厚薄规。
调节式垫片的接触螺纹不得少于5牙,调节环与球形势片的最小厚度不得小于8mm。使承受b.
负荷强度大于轴系静负荷的12倍以上。c.双联式斜楔垫片,小端厚度不小于10mm,二斜楔重合不小于全长的60%。3.2.2.6当轴承底脚螺栓旋紧后,检查垫片各接合面间的接触情况,要求70%周长上插不进0.05mm厚薄规。
3.2.2.7垫片装配后应对轴系进行检查中间轴颈与中间轴承的底部要求接触良好,应插不进0.05mm厚薄规。a.
中间轴承后的左右方向间隙应大致相同,不允许轴与轴承单边靠近。b.
轴承座与底座连接螺栓应有锁紧装置,轴承座与盖的连接螺栓要加锁紧螺帽。.
3.2.3尾轴承
3.2.3.1尾轴管衬套一般采用铸铜,铸件不允许有裂缝,密集渣孔等足以影响强度与紧密性的缺陷,对于直径小于5mm,深度小于4mm的表面气孔允许修补后使用。3.2.3.2白合金尾轴承建议采用离心浇铸,加工后的表面粗糙度以上,水槽应拉削平直,修净毛刺后方可装配。
3.2.3.3白合金尾轴承当白合金脱落成轴颈咬痕严重时,应重浇白合金,对轻度的咬痕允许磨平使用,个别脱落处允许焊补修复。3.2.3.4铁梨木或层压胶木尾轴承:a.
缺陷。
铁梨木或层压胶木材料应挺直不曲,长度不短于轴承长度,木材表面不应有凹陷,严重裂纹等衬套内应装止动条2~3根,其长度约为板条厚的60%,宽度为0.8(D-d)(Db.
村套内径,
一尾轴颈直径)但不少于20mm,止动条背后应紧密与衬套内圆贴合,并用螺钉固定。d
c.衬套下半部的板条应采用横纹,上部为纵纹,板条宽度基本相同,纵向接缝在-一条直线上,其总长部分应使板条在轴向留有3~8mm的膨胀间隙。d.板条镶嵌应紧密,在85%的板条长度上插不进0.10mm厚薄规,板条背面与衬套内圆应紧密贴合,其不紧密区允许为总面积的20%以内,且不集中一处。周向板条数目的选用见表8。
轴颈直径d
板条数量
≤120
>120~180
10~14
>180~260
14~20
>260~360
3.2.3.5铁梨木或层压胶木轴承加工后表面粗糙度应在以上,端面及流水槽附近不允许有缺口和断块,轴承内圆度和圆柱度不应大于0.10~~0.15mm,流水槽应平直无毛刺.形状可采用梯形。U形、V形,深度和宽度的要求见表9,图5。表9
轴颈直径d
梯形U形槽
V形槽
水槽布置
宽5×深6
逆长7
180~260
宽6×深6
边长8
每二条接缝一条水槽
261~360
宽6×深7
边长9
每-条接缝一条水槽
SC/T 8036-94
斜度:100
1纵纹板条;2止动条;3横纹板条;4-流水槽;5—衬套3.2.3.6铁梨木或层压胶木尾轴承修理要求a.
规定。
渔船修理轴线变化在标准范围内时,允许只更换下半部分。允许在板条之间垫以薄铜皮,以增加紧密性,但若全部板条松驰,干裂严重时,应予换新。允许在板条背部衬以整张铜皮,以缩小其内径,但镗削后铁梨木或层压胶木应满足最小厚度的允许偏心镗削尾轴承来借正轴线,但最薄处的铁梨木或层压胶木应能满足最小厚度要求。3.2.3.7
3.3轴系密封装置修理技术要求
3.3.1尾轴管首端密封装置
3.3.1.1橡皮环式密封装置
材料采用丁腈橡胶,氟橡胶塑料制品等,产品应符合设计要求,并应在使用限期内。a.
装配前应仔细检查环边应无裂纹、缺口、毛边等缺陷。橡皮环破裂损伤,唇边硬化裂纹,唇边较严重磨损和老化,均应换新。油压试验以船上专用注油设备(或相当此种设备)进行泵油,到有回油为准,历时5min不准有机油漏泄,允许微微转动尾轴进行检查。3.3.1.2尾轴管前端填料函密封装置填料一般采用油脂棉麻绳(俗称牛油盼更)。a.
加装填料时,每圈的长度应使两端刚好接拢,各道填料搭口应相互错开。b.
填料压盖前后移动应灵活,压盖与轴的装配间隙为尾轴承装配间隙的4倍。C,
压盖衬套内圆不应与轴有接触,并力求上下左右方向间隙大约对等。3.3.1.3试车要求见表10。
水润滑填料函
油润滑填料函
中间轴承
3.3.2尾轴管尾端金属环式密封装置使
应有少量尾管内的水流出
每分钟漏油量不超过8滴
允许少量渗油,不许滴油
3.3.2.1零件的制造与修换要求见表11。极限使用温度
≤60℃
(1)工作表面粗糙度,
(2)外圆、圆度<0. 05;
SC/T 80 36-9 4
(1)衬套最小极限厚度t:按下表:衬套外径
(3)内圆与轴颈配合间隙0.10~0.30当靠衬套法兰凸肩定中时,测内圆与轴配合,间隙为0.30~0.50
(1)任何地方的厚薄差≤0.02;
(2)两面平直,误差≤0.02,
(3)环内孔与衬套配合要求按下表:D
>150~220 />220~360
0~0. 02
(1)两平面及座槽平面厚度允差≤0.02(2)座档与油环外,板内孔与衬套径向间隙K按下表:
(1)内孔直径:
D,≥D+26+(2~3);
式中 D为衬套外径;
(2)橡皮糖深:
b, -b--(0. 20~0. 50);
式中6为橡皮厚度;
>150~220
(3)内孔圆弧应光滑圆顺
>220~360
(1)根据衬套外径D选用橡皮厚度b,按下表:D
>150~220
(2)橡皮内孔割測尺寸:
Di =0. 9D-- (15~18);
>220~360
(3)橡皮应无裂纹,割制内孔唇边应光洁无裂纹和缺口,橡皮未老化
>150~220
>220~360
(2)村套经光车后使用者,其橡皮唇口部不允许有疤
金环凡经装配后,一经拆下时应作换新处理座槽内工作面最小极限厚度按下表:D
>150~220
>220~360
装配及试验要求:
金属环装配时,环与环槽两侧轴向间隙(包括衬纸厚度在内)应大于推力轴向间隙,一般a.
取 0.20~~0.30mm。
SC/T 80 3 6-94
b.油压试验与3.3.1.1条d款同,试验时不准有漏泄。3.3.3轴系隔舱填料函
3.3.3.1填料函零部件的加工要求:a.零件内外圆,同轴度小于0.10mm,各端面与内孔中心线垂直度小于0.20mm/m。部分式填料函本体与压盖,部分平面应位于轴孔中心线上,偏差小于0.20mm,两接合面间b.
80%以上配合良好,用0.05mm厚薄规插不进。相配两端的接合面应用不少于2个螺钉或定位销定位。c.
隔舱平板平面应光洁,其平面最好与轴系中心线垂直,允许用厚薄中间垫片来修正垂直度,使d.
不垂直度小于0.50mm/m。
填料函本体装于隔舱壁上时,应在接合面间衬以密封填料。在隔舱填料函装配完毕后,应保证水密。3.4尾轴管修理及加工技术要求
3.4.1尾轴管的修理
3.4.1.1尾轴管裂纹,局部渗漏允许焊补或填补塑料等方法予以修补,焊补时应采取有效措施,尽量减少其内应力。修补后应作0.2MPa水压试验,历时5min不得有渗漏。3.4.1.2、尾轴管上的局部腐蚀或凹陷,其深度不超过该壁厚的1/2,直径不大于尾轴管外径的1/6,允许堆焊修理,但修补处不得多于3处,对于更小范围的局部腐蚀或凹陷,允许用塑料或铁粉环氧树脂填补,堆焊或填补后,均应作水压试验。3.4.1.3允许就地借偏心镗削尾轴管,镗孔中心线应比理论中心线提高尾轴间隙值的一半。装衬套部位管壁最薄处的厚度,不得小于新制最小值的60%。3.4.1.4在采用镗削尾柱毂孔及尾隔舱孔借正轴线时,允许将尾轴管上相应毂孔配合段,包以玻璃钢、铁粉环氧树脂等扩大尺寸,亦可采用金属刚性镶套。3.4.2尾轴管的加工
3.4.2.1尾轴管铸件表面应光洁,不允许有裂缝,砂眼,巢中渣孔,浇铸不足等足以影响强度与紧密性的缺陷,对较小缺陷允许修补后使用。3.4.2.2铸件需经热处理,以消除内应力。3.4.2.3尾轴管加工后应经水压试验,压力为0.2MPa,5min内不得有渗漏,允许用焊补,填补塑料等方法清除个别渗漏,补后应重新进行水压试验。3.4.2.4加工尾轴管时,尾轴管前端法兰面对中心线的不垂直度及端面跳动公差,应满足GB1184规定的8级精度,见表12。
外圆直径D,mm
允许值,μm
≥63~100
≥100~160
>160~250
>250~400
>400~630
>630~1000
3.4.2.5加工尾轴管时,尾轴管内的同轴度公差应满足GB1184规定的9级精度,但利用偏心镗削尾轴管以借正轴线的情况除外。外圆各档配合尺寸及内孔各档配合尺寸的同轴度应满足GB1184的8级精度,见表13。
公称尺寸D,mm
8级精度公差值,μm
9级精度公差值,um
3.4.3尾轴管装配要求:
50~120
≥120~250
>250~500
≥500~800
>800~1250
SC/T8036-94
3.4.3.1尾轴管尾端螺母旋紧后,螺母与尾柱毂孔平面应贴台,允许在贴合面垫帆布,涂红粉,白漆等,以确保不渗水。螺母需有可靠的锁紧装置。3.4.3.2尾轴管首法兰面与尾隔舱平面应保证水密,允许用浇注白合金或铁粉环氧树脂密封。3.4.3.3允许采用环氧树脂固定尾轴管,在浇注前,必须根据拉线结果定好尾轴中心。浇注后,不允许托架及尾轴管区域大面积超过200℃的明火作业,但仍允许局部割焊。环氧树脂定中心的尾轴管,不允许在尾轴安装时有强烈撞击。3.4.3.4尾轴管装要后,对穿过尾轴管的水舱应进行水密试验,凡与尾轴管配合部位,不允许有任何渗漏,允许用嵌捻,塘水泥,除补塑修补个别小渗漏。3.4.4尾柱毂孔
3.4.4.1毂孔壁厚t应满足规范的规定(t>0.33d,1.>3d;d-定减薄量,超过此值时应以极限壁厚校核。表14
尾轴颈直径d
允许减薄量
≤180
尾轴毂的极限壁厚为0.27d;d——3.4.4.2毂孔镗削技术要求
>180~260
为尾轴最小直径。
尾轴颈直径),其壁厚允许有表14所mm
≥260~360
>360~500
a。镗削中心与轴孔原定位中心线偏差小于0.10mm,尾轴毂孔与尾隔舱中心应同轴,其同轴度在0.10mm以内。
b。毂孔尾端以及尾隔舱法兰面应与轴孔中心线垂直,垂直度不得超过0.15mm。毂孔加工的圆度和圆柱度应满足GB1184规定的10级精度,见表15。c
毂孔直径,mm
公差值·um
3.5轴系安装配合要求
80~120
>120~180
>180~250
>250~315
3.5.1中间轴与中间轴承配合间隙,修换间隙和白合金修换厚度见表16。表16
≤100
>100~120
>120~150
>150~180
>180~220
>220~260
安装间隙△
0. 17~0. 21
0. 21~~0. 25
0. 25~0. 30
0.30~0. 35
0.35~0.40
0.40~0.45
白合金新制最小厚度
注:本表所列安装间隙适用于转速300≤n≤400r/min,之中间轴承。当n小于300r/min时,应将安装间隙缩小0.02~0.04mm。当n=400~750r/min时,应将安装间隙增大0.04~0.06mm。3.5.2尾轴承衬套外圆与尾轴管的配合要求见表17。278
修换间隙A,
>315~~400
白含金修换厚度
衬套外径I
80~120
>120~180
>180~260
>260~~360
SC/T8036--94
配合长度L>2D
- 0. 04 ~--- 0. 01
0. 05 - 0. 02
-0. 06 ~ — 0. 03
0. 07 ~ - 0. 04
3.5.3尾轴铜衬套与尾轴配合的过盈量见表18。表18
轴颈直径d.mm
盈,%
尾轴与尾轴承配合要求
>120~180
>180~260
滑油润滑白合金,尾轴承安装间隙,修换间隙及白合金厚度见表19。表19
≥100~120
≥120~150
>150~180
≥180~220
≥220~260
安装间隙△
0.45~0.55
0.50~~0.60
0.55~0.65
0.60~0.70
0. 65~0.75
0.70~0.80
白合金新制最小厚度
配合长度L<2D
0.02~0.00
0. 03~0. 005
- 0. 04 ~0. 001
0. 05 ~ - 0. 02
>260~360
修换间隙△
白合金极限厚度
注:(D当白合金长度L>3d时,其安装间隙可按表值放大10%~20%,其修换间隙可放大20%。②当渔船在排上修理因更换尾部船板、龙骨等造成尾轴管变形,尾轴装不进时,允许把安装间放大50%,放大间隙仍不能安装者,应检查原因。③填料压盖内孔与尾轴铜套的间隙,可以取尾轴承安装间隙值的4倍。3.5.4.2铁梨木及层压胶木尾轴承安装间隙、修换间隙见表20。表20
100~120
>120~150
≥150~180
≥180~220
>220~260
安装间隙A
0. 80~0. 90
0. 90~~1. 00
1. 00~1. 10
1.10~~1.20
板条新制最小厚度
修换间隙△
板条极限厚度
注:(D偏心镗削尾轴承时,镗孔中心线应提高,其值可为安装间隙的50%~75%(前端轴承取50%)。削后最薄处铁梨木或层压胶木板条的厚度应满足表中规定的新制最小厚度值。(2)用铁梨木及层压胶木作尾轴承,在加工前应用水浸泡5关以上或用温水漫泡2天,以保证正确的配合间隙279
小提示:此标准内容仅展示完整标准里的部分截取内容,若需要完整标准请到上方自行免费下载完整标准文档。
渔船轴系及螺旋浆修理技术要求1主题内容与适用范围
本标准规定了渔船轴系修理及螺旋奖装配技术要求。本标准适用渔船轴系及螺旋桨修理及验收。2 引用标准
GB1184形状和位置公差
3轴系修理技术婴求
3.1中间轴,尾轴及联轴节修换技术要求SC/T 8036—94
代替 SC 36 --79
3.1.1铸锻件如工要求
3.1.1.1中间轴、尾轴及联轴节锻件成品,不得有过烧现象,表面不允许有裂纹,折痕,夹渣,夹层及密集的发纹,轴端部不得有缩孔或疏松。3.1.1.2表面缺陷若能在加工后保证去除,而且不影响表面质量时允许存留。3.1.1.3联轴节非接合面允许存留个别不大的凹陷,刻痕或黑点,允许用焊补的方法修补表面缺陷,大面积焊补后应重新热处理。
3.1.1.4中间轴,尾轴及联轴节铸锻件应经高温退火或回火,以消除内应力,并获得均匀细致的结晶组织。
3.1.1.5热轧钢材可不必再作热处理,但当中间轴采用焊接法兰时,必须进行整体或局部退火。局部退火加热部位应包括除法兰以外,不少于一半轴颈长度,轴与法兰的焊接,应采用合理的接缝,建议将轴端镦粗进行焊接,或者采用V型接缝焊接法兰。3.1.1.6中间轴、尾轴经粗加工后应进行退火处理,以消除切削应力。在轴经小于150mm时,允许采用控制最后三到四道切前量的办法(进刀小于0.207mm)减少切削应力,此时可不进行退火处理。3.1.1.7中间轴、尾轴加工后表面应光洁,不得有密集发纹、裂缝,蜂窝孔或非金属夹杂物,非工作面上个别较细的凹陷,刻痕或黑斑经清理后允许存在,对表面质量有怀疑处应进行探伤检查。3.1.2中间轴、尾轴
3.1.2.1中间轴、尾轴的工作轴颈,锥体法兰及法兰定位凸肩外圆相对于轴中心线的径向跳动公差,新制中间轴,尾轴应不低于GB1184规定的7级精度,精车修理不低于8级精度,在轴的长径比L/D大于30时,应不低于9级精度。
新制轴的非工作轴径相对于轴中心线的径向跳动公差应不低于GB1184规定的10级精度,见表1。
修理中未经精车修理的中间轴,尾轴径向跳动公差值为相应各值的3倍。中华人民共和国农业部1994-11-01批准268
1995-01-01实施
糟度等级
公称尺寸,mm
>50~120
>120~250
>250~500
SC/T8036-94
3.1.2.2中间轴、尾轴及联轴节法兰,法兰定位凸肩相对于轴中心线的垂直度公差,新制时应符合GB1184规定的5级精度,精车修理时应符合7级精度,且只准内凹,不能外凸。未精车的法兰,垂直度应不低于8级精度的规定,见表2,端面跳动应小于0.04mm。糖度等级
公称尺寸,mm
>63~100
>100~160
>160~250
>250~400
>400~630
3.1.2.3中间轴、尾轴工作轴颈的圆度和圆柱度公差,新制轴及精车后应不低于GB1184规定的8级精度,轴承档长度大于轴径时每增加100mm,圆柱度允差可增加0.01mm。中间轴磨耗极限应不低于11级精度,尾轴不低于12级精度,低于这个标准时,必须修复。3.1.2.4经加工后的非工作轴径的圆度公差,应不低于GB1184规定的10级精度,见表3。表3
糖度等级
公称尺寸
>30~50
>50~80
>80~120
>120~180
3.1.2.5轴上的螺纹应光洁,在与螺母旋合时,不应有可感觉到的松动,在最初3~4牙用手轻便的旋入,用扳手可以顺利旋到底,螺纹轻度碰损,允许修锉后继续使用,较重的碰损应车削修理。此刻若螺纹直径减少较多时,应进行强度校核。3.1.2.6键槽与平键加工技术要求a.
键槽宽度应一致,在任何位置测量时,其槽侧二面平行度偏差应不小于0.03mm。在任何位置测量键槽高度时,每10mm高不得超过0.10mm。键槽两侧与轴中心线应平行,平行度每100mm不超过0.01mm。尾轴键槽允许重新铣直加宽,其极限宽度为锥体平均轴颈的0.33倍。平键四侧应光洁平直,在平板上检查时应插不进0.05mm厚薄规。269
SC/T8036-94
键槽底应有R=1~3mm的圆角,与螺旋桨相配之键槽首端最好制成雪撬形,以减少应力集平键两侧允许借偏心,偏中量不得超过键宽的5%,但最大不得超过2mm。3.1.2.7中间轴或尾轴凡是车削轴颈(或铜套)时,法兰平面都应切削并允许留黑。3.1.2.8中间轴、尾轴换新或修理加工后,表面粗糙度要求见图1。曼
3.1.2.9经车削修理的中间轴或尾轴,轴承部位轴颈最少不小于非工作轴颈外径,并允许堆焊后精车,低温镀铁及金属喷镀等方法予以加大。3.1.2.10采用堆焊修理轴颈时,预热温度按表4选取,焊后进行退火处理。表4
轴材含碳量,%
堆焊预热温度,C
0.2以下
100~120
3.1.2.11尾轴锥体大端锈蚀检查a.
120~~150
0. 3~~0. 45
150~250
0.45以上
250~400
当锈蚀为圆状,且个别锈蚀处深不超过0.03d,较长锈蚀深不超过0.02d,整个圆周锈蚀深不超过0.015d,经清理检查后允许继续使用(d—轴颈直径)。b.当锈蚀为尖角状,应仔细检查其深度与周长长度,然后应修锉或车削成圆弧状,并须探伤检查,凡深度符合上述a条要求时,可允许继续使用。当蚀深超过上述规定时,应将锈蚀处车去,车削后轴径必须经过强度校核合格,方准继续使用。C
3.1.3轴端法兰螺孔与连接螺栓
3.1.3.1法兰连接螺栓,其中紧配螺栓数目应不少于总数的50%要求紧松螺栓间隔排列相配,紧配螺栓与螺孔的配合加工精度见表5。表5
螺栓直径
配合间隙
圆柱度
圆柱度
30以下
0.005~0.005
51~70
SC/T 8036-94
3.1.3.2锥形螺栓应与锥孔均匀接触,接触面积在75%以上。3.1.3.3经加工修理后的中间轴,尾轴,法兰螺孔边缘至法兰外圆的厚度,不应少于连接螺栓直径的0.3倍,法兰的厚度不应小于基本轴径的0.2倍。3.1.3.4绞削连接螺孔时,应将成对的轴安放在合理支承上,见图2,并使相配法兰的偏移与曲折皆为0。Www.bzxZ.net
ar-b,=n.21.
= br= 0. 2.
3.1.3.5在修理中,螺栓杆体上不大的擦伤或刮痕,螺孔内表面少量的刮痕允许修刮后继续使用。螺栓材料强度不得低于中间轴或尾轴材料的强度,一般需用35号钢或40号钢。3.1.3.6新制螺栓装配后的旋紧余量为6~~12mm图3尺寸A),螺栓与螺孔装配后,螺栓头或螺母的支承面与法兰之间应紧密接触,在80%周长上应插不进0.05mm厚薄规,并应采用双螺母或槽形螺母等防松装置,以免松动。
3.1.4中间轴,尾轴可拆联轴节
3.1.4.1法兰式可拆联轴节加工技术要求见图4联轴节法兰外表的精加工,应在锥孔修拂后套装到轴上进行其粗糙度和加工技术要求与整锻法兰相同。
其键槽加工的宽度、高度与轴线平行度都与轴键槽加工要求相同,以最终与轴键相配质量为验b.
救标准。
SC/T 8036-94
3.1.4.2法兰式可拆联轴节装配技术要求如下:(0. 02~0.03
联轴节锥孔与轴锥体接触应良好,接触面积在75%以上。a.
联轴节锥孔与轴锥体在采用环氧树脂胶合安装时,其接触面积不少于30%。b.
平键与轴键槽两侧接触面积不少于 75%,与联轴节键槽相配时在 85%长度上应插不进0.05mm的厚薄规,其余部分应插不进0.10mm,平键与轴键槽底应接触,接触面不少于30%~~40%。d,联轴节紧固螺母安装后,接合面的90%周长上,应插不进0.05mm厚薄规,其接触面积不少于75%,并有可靠的防松装置。
3.1.5轴衬套及保护层。
3.1.5.1尾轴铜衬套材料及铸件检查:衬套材料ZCuSn10Zn2。
铜衬套不允许有裂纹,密集气孔,疏松和砂眼等缺陷,对于不甚严重的缺陷允许经修补后使用。b.
铜衬套经粗加工后,套装在轴上之前,如表面有不甚严重之砂眼、疏松等缺陷,应进行水压试验,试验压力为0.1MPa,5min内不得有渗漏。轴套表面产生渗漏的个别小空隙,允许用焊补,熔锡或填补塑料等方法予以消除,处理后应再经水压试验。3.1.5.2轴套加工时,轴套内圆粗糙度不得低于√其圆柱度和圆度应符合GB1184规定的9级精度,见表6。
轴颈直径d.mm
公差值,m
80~120
121~180
181~250
3.1.5.3铜衬套红套轴上时,加热温度一般不超过320℃。套合后应紧密,不许采用螺钉或其他止动钉的办法来固定轴套,不许采用两半焊接的组合铜衬套。3.1.5.4尾轴铜衬套(般在油封装置处)允许小段镶套,接缝处应车有凸肩,镶套后外圆精车,接缝处不能塞进0.05mm厚薄规,超过0.10mm时应加填料或焊锡,保持水密。3.1.5.5尾轴铜衬套厚度要求见表7。272
计算式
新制最小厚度
t≥0. 03d +7. 5
注:①表中d为尾轴直径,mm,
SC/T 8036-94
非工作轴颈部位
to≥0.75t
光车修理时厚度
t:≥0.02d+4
②填料函部位锅衬套极限厚度照上述规定可适当放低要求,但最薄不得低于4mm。3.1.5.6轴套修理技术要求
a.轴套部分裂缝,允许只换损坏部分,其接缝应符合第3.1.5.3条的规定。极限厚度
tj0. 15d-+ 3. 5
b.轴套表面明显磨损,应予少量精车留黑,但残留磨痕深度不得大于0.20mm,在填料部位轴套精车后允许残留磨痕,深度不大于0.40mm,圆周不大于1/4元d。3.1.5.7非工作轴颈玻璃钢保护层的技术质量要求。a。玻璃布的卷向应与螺旋桨转向相反,应从尾端向前端包裹,玻璃布的重叠层不少于二层,每圈重叠量为15~30mm。
b.严格按照磷化底漆及环氧树脂的工艺要求,在包裹中,应随时将气泡挤出,硬化后严禁有连续气泡存在,表面应光洁无毛刺。C、对玻璃钢接口不良,局部破损,脱壳,泛黄锈和膨胀现象应予修补,允许采用局部涂环氧树脂或一段进行包裹的方法修补。
d、对玻璃钢保护层严禁硬物冲击或碰撞,严禁与腐蚀性介质接触,在吊运时,严禁在玻璃钢外直接缠钢丝绳。
3.2轴系轴承修理技术要求
3.2.1中间轴承
3.2.1.1轴承座与轴承盖的技术要求铸件不允许有裂纹,缩孔,疏松,绕不足等严重缺陷,对于较小缺陷允许经修补后使用,铸件应a.
彻底清理干净,并进行必要的热处理,以消除内应力。b.盖与座的接合面应与轴中心线平行,平行度每米不超过0.20mm,各接合面应光洁平直。c.盖与座两端阻油羊毛毡,可比轴瓦白合金面略高0.20~0.50mm不应过高,致使中间轴搁空发热。
3.2.1.2白合金轴承浇铸质量和装配要求:a.浇铸白合金材料可为ZChSn82Sb11-6、ZChSnSb7,5-3等,轴瓦浇铸表面不应有裂纹,疏松和密集气泡等缺陷,不允许用不同牌号的白合金混杂浇铸,熔融的白合金不得有过烧现象。b.白合金与瓦底的粘合质量应良好,不应有脱壳现象存在。白合金壁厚应力求均匀,厚薄差不得大于壁厚的20%,粘合白合金的轴承表面粗糙度应在以上,以保证粘结强度。c.轴颈与白合金轴承应进行拂刮,在底部60°范围内接触面积达65%以上,即每25×25mm内有2~3个接触点。
d.轴瓦的背面与轴承座内圆应均匀接触,接触面积在65%以上,允许用冷压或锤击的方法,涨大其圆颈后进行修拂,要求在没有负荷作用下,轻轻敲击便可取出轴瓦。甩油圈不许漏装,要求二个半圈结合良好。e,
f.轴瓦白合金显著脱壳,严重过热和咬损,应予重浇白合金。3.2.2中间轴承垫片
3.2.2.1轴承垫片接触,其面积至少应为轴承底座面积的50%。3.2.2.2钢质垫片最大厚度等于小于75mm,最小厚度等于大于6mm。3.2.2.3铸铁垫片厚度最大厚度等于小于75mm,最小厚度等于大于10mm。3.2.2.4允许加装少量的金属薄垫片,需要整块使用,并且有足够的接触面积。273
3.2.2.5轴承垫片加工要求:
SC/T 8 0 3 6-9 4
金属厚垫片各平面应平正,在平板上检查应插不进0.05mm厚薄规,球形接触面间亦应插不进a.
0.05mm厚薄规。
调节式垫片的接触螺纹不得少于5牙,调节环与球形势片的最小厚度不得小于8mm。使承受b.
负荷强度大于轴系静负荷的12倍以上。c.双联式斜楔垫片,小端厚度不小于10mm,二斜楔重合不小于全长的60%。3.2.2.6当轴承底脚螺栓旋紧后,检查垫片各接合面间的接触情况,要求70%周长上插不进0.05mm厚薄规。
3.2.2.7垫片装配后应对轴系进行检查中间轴颈与中间轴承的底部要求接触良好,应插不进0.05mm厚薄规。a.
中间轴承后的左右方向间隙应大致相同,不允许轴与轴承单边靠近。b.
轴承座与底座连接螺栓应有锁紧装置,轴承座与盖的连接螺栓要加锁紧螺帽。.
3.2.3尾轴承
3.2.3.1尾轴管衬套一般采用铸铜,铸件不允许有裂缝,密集渣孔等足以影响强度与紧密性的缺陷,对于直径小于5mm,深度小于4mm的表面气孔允许修补后使用。3.2.3.2白合金尾轴承建议采用离心浇铸,加工后的表面粗糙度以上,水槽应拉削平直,修净毛刺后方可装配。
3.2.3.3白合金尾轴承当白合金脱落成轴颈咬痕严重时,应重浇白合金,对轻度的咬痕允许磨平使用,个别脱落处允许焊补修复。3.2.3.4铁梨木或层压胶木尾轴承:a.
缺陷。
铁梨木或层压胶木材料应挺直不曲,长度不短于轴承长度,木材表面不应有凹陷,严重裂纹等衬套内应装止动条2~3根,其长度约为板条厚的60%,宽度为0.8(D-d)(Db.
村套内径,
一尾轴颈直径)但不少于20mm,止动条背后应紧密与衬套内圆贴合,并用螺钉固定。d
c.衬套下半部的板条应采用横纹,上部为纵纹,板条宽度基本相同,纵向接缝在-一条直线上,其总长部分应使板条在轴向留有3~8mm的膨胀间隙。d.板条镶嵌应紧密,在85%的板条长度上插不进0.10mm厚薄规,板条背面与衬套内圆应紧密贴合,其不紧密区允许为总面积的20%以内,且不集中一处。周向板条数目的选用见表8。
轴颈直径d
板条数量
≤120
>120~180
10~14
>180~260
14~20
>260~360
3.2.3.5铁梨木或层压胶木轴承加工后表面粗糙度应在以上,端面及流水槽附近不允许有缺口和断块,轴承内圆度和圆柱度不应大于0.10~~0.15mm,流水槽应平直无毛刺.形状可采用梯形。U形、V形,深度和宽度的要求见表9,图5。表9
轴颈直径d
梯形U形槽
V形槽
水槽布置
宽5×深6
逆长7
180~260
宽6×深6
边长8
每二条接缝一条水槽
261~360
宽6×深7
边长9
每-条接缝一条水槽
SC/T 8036-94
斜度:100
1纵纹板条;2止动条;3横纹板条;4-流水槽;5—衬套3.2.3.6铁梨木或层压胶木尾轴承修理要求a.
规定。
渔船修理轴线变化在标准范围内时,允许只更换下半部分。允许在板条之间垫以薄铜皮,以增加紧密性,但若全部板条松驰,干裂严重时,应予换新。允许在板条背部衬以整张铜皮,以缩小其内径,但镗削后铁梨木或层压胶木应满足最小厚度的允许偏心镗削尾轴承来借正轴线,但最薄处的铁梨木或层压胶木应能满足最小厚度要求。3.2.3.7
3.3轴系密封装置修理技术要求
3.3.1尾轴管首端密封装置
3.3.1.1橡皮环式密封装置
材料采用丁腈橡胶,氟橡胶塑料制品等,产品应符合设计要求,并应在使用限期内。a.
装配前应仔细检查环边应无裂纹、缺口、毛边等缺陷。橡皮环破裂损伤,唇边硬化裂纹,唇边较严重磨损和老化,均应换新。油压试验以船上专用注油设备(或相当此种设备)进行泵油,到有回油为准,历时5min不准有机油漏泄,允许微微转动尾轴进行检查。3.3.1.2尾轴管前端填料函密封装置填料一般采用油脂棉麻绳(俗称牛油盼更)。a.
加装填料时,每圈的长度应使两端刚好接拢,各道填料搭口应相互错开。b.
填料压盖前后移动应灵活,压盖与轴的装配间隙为尾轴承装配间隙的4倍。C,
压盖衬套内圆不应与轴有接触,并力求上下左右方向间隙大约对等。3.3.1.3试车要求见表10。
水润滑填料函
油润滑填料函
中间轴承
3.3.2尾轴管尾端金属环式密封装置使
应有少量尾管内的水流出
每分钟漏油量不超过8滴
允许少量渗油,不许滴油
3.3.2.1零件的制造与修换要求见表11。极限使用温度
≤60℃
(1)工作表面粗糙度,
(2)外圆、圆度<0. 05;
SC/T 80 36-9 4
(1)衬套最小极限厚度t:按下表:衬套外径
(3)内圆与轴颈配合间隙0.10~0.30当靠衬套法兰凸肩定中时,测内圆与轴配合,间隙为0.30~0.50
(1)任何地方的厚薄差≤0.02;
(2)两面平直,误差≤0.02,
(3)环内孔与衬套配合要求按下表:D
>150~220 />220~360
0~0. 02
(1)两平面及座槽平面厚度允差≤0.02(2)座档与油环外,板内孔与衬套径向间隙K按下表:
(1)内孔直径:
D,≥D+26+(2~3);
式中 D为衬套外径;
(2)橡皮糖深:
b, -b--(0. 20~0. 50);
式中6为橡皮厚度;
>150~220
(3)内孔圆弧应光滑圆顺
>220~360
(1)根据衬套外径D选用橡皮厚度b,按下表:D
>150~220
(2)橡皮内孔割測尺寸:
Di =0. 9D-- (15~18);
>220~360
(3)橡皮应无裂纹,割制内孔唇边应光洁无裂纹和缺口,橡皮未老化
>150~220
>220~360
(2)村套经光车后使用者,其橡皮唇口部不允许有疤
金环凡经装配后,一经拆下时应作换新处理座槽内工作面最小极限厚度按下表:D
>150~220
>220~360
装配及试验要求:
金属环装配时,环与环槽两侧轴向间隙(包括衬纸厚度在内)应大于推力轴向间隙,一般a.
取 0.20~~0.30mm。
SC/T 80 3 6-94
b.油压试验与3.3.1.1条d款同,试验时不准有漏泄。3.3.3轴系隔舱填料函
3.3.3.1填料函零部件的加工要求:a.零件内外圆,同轴度小于0.10mm,各端面与内孔中心线垂直度小于0.20mm/m。部分式填料函本体与压盖,部分平面应位于轴孔中心线上,偏差小于0.20mm,两接合面间b.
80%以上配合良好,用0.05mm厚薄规插不进。相配两端的接合面应用不少于2个螺钉或定位销定位。c.
隔舱平板平面应光洁,其平面最好与轴系中心线垂直,允许用厚薄中间垫片来修正垂直度,使d.
不垂直度小于0.50mm/m。
填料函本体装于隔舱壁上时,应在接合面间衬以密封填料。在隔舱填料函装配完毕后,应保证水密。3.4尾轴管修理及加工技术要求
3.4.1尾轴管的修理
3.4.1.1尾轴管裂纹,局部渗漏允许焊补或填补塑料等方法予以修补,焊补时应采取有效措施,尽量减少其内应力。修补后应作0.2MPa水压试验,历时5min不得有渗漏。3.4.1.2、尾轴管上的局部腐蚀或凹陷,其深度不超过该壁厚的1/2,直径不大于尾轴管外径的1/6,允许堆焊修理,但修补处不得多于3处,对于更小范围的局部腐蚀或凹陷,允许用塑料或铁粉环氧树脂填补,堆焊或填补后,均应作水压试验。3.4.1.3允许就地借偏心镗削尾轴管,镗孔中心线应比理论中心线提高尾轴间隙值的一半。装衬套部位管壁最薄处的厚度,不得小于新制最小值的60%。3.4.1.4在采用镗削尾柱毂孔及尾隔舱孔借正轴线时,允许将尾轴管上相应毂孔配合段,包以玻璃钢、铁粉环氧树脂等扩大尺寸,亦可采用金属刚性镶套。3.4.2尾轴管的加工
3.4.2.1尾轴管铸件表面应光洁,不允许有裂缝,砂眼,巢中渣孔,浇铸不足等足以影响强度与紧密性的缺陷,对较小缺陷允许修补后使用。3.4.2.2铸件需经热处理,以消除内应力。3.4.2.3尾轴管加工后应经水压试验,压力为0.2MPa,5min内不得有渗漏,允许用焊补,填补塑料等方法清除个别渗漏,补后应重新进行水压试验。3.4.2.4加工尾轴管时,尾轴管前端法兰面对中心线的不垂直度及端面跳动公差,应满足GB1184规定的8级精度,见表12。
外圆直径D,mm
允许值,μm
≥63~100
≥100~160
>160~250
>250~400
>400~630
>630~1000
3.4.2.5加工尾轴管时,尾轴管内的同轴度公差应满足GB1184规定的9级精度,但利用偏心镗削尾轴管以借正轴线的情况除外。外圆各档配合尺寸及内孔各档配合尺寸的同轴度应满足GB1184的8级精度,见表13。
公称尺寸D,mm
8级精度公差值,μm
9级精度公差值,um
3.4.3尾轴管装配要求:
50~120
≥120~250
>250~500
≥500~800
>800~1250
SC/T8036-94
3.4.3.1尾轴管尾端螺母旋紧后,螺母与尾柱毂孔平面应贴台,允许在贴合面垫帆布,涂红粉,白漆等,以确保不渗水。螺母需有可靠的锁紧装置。3.4.3.2尾轴管首法兰面与尾隔舱平面应保证水密,允许用浇注白合金或铁粉环氧树脂密封。3.4.3.3允许采用环氧树脂固定尾轴管,在浇注前,必须根据拉线结果定好尾轴中心。浇注后,不允许托架及尾轴管区域大面积超过200℃的明火作业,但仍允许局部割焊。环氧树脂定中心的尾轴管,不允许在尾轴安装时有强烈撞击。3.4.3.4尾轴管装要后,对穿过尾轴管的水舱应进行水密试验,凡与尾轴管配合部位,不允许有任何渗漏,允许用嵌捻,塘水泥,除补塑修补个别小渗漏。3.4.4尾柱毂孔
3.4.4.1毂孔壁厚t应满足规范的规定(t>0.33d,1.>3d;d-定减薄量,超过此值时应以极限壁厚校核。表14
尾轴颈直径d
允许减薄量
≤180
尾轴毂的极限壁厚为0.27d;d——3.4.4.2毂孔镗削技术要求
>180~260
为尾轴最小直径。
尾轴颈直径),其壁厚允许有表14所mm
≥260~360
>360~500
a。镗削中心与轴孔原定位中心线偏差小于0.10mm,尾轴毂孔与尾隔舱中心应同轴,其同轴度在0.10mm以内。
b。毂孔尾端以及尾隔舱法兰面应与轴孔中心线垂直,垂直度不得超过0.15mm。毂孔加工的圆度和圆柱度应满足GB1184规定的10级精度,见表15。c
毂孔直径,mm
公差值·um
3.5轴系安装配合要求
80~120
>120~180
>180~250
>250~315
3.5.1中间轴与中间轴承配合间隙,修换间隙和白合金修换厚度见表16。表16
≤100
>100~120
>120~150
>150~180
>180~220
>220~260
安装间隙△
0. 17~0. 21
0. 21~~0. 25
0. 25~0. 30
0.30~0. 35
0.35~0.40
0.40~0.45
白合金新制最小厚度
注:本表所列安装间隙适用于转速300≤n≤400r/min,之中间轴承。当n小于300r/min时,应将安装间隙缩小0.02~0.04mm。当n=400~750r/min时,应将安装间隙增大0.04~0.06mm。3.5.2尾轴承衬套外圆与尾轴管的配合要求见表17。278
修换间隙A,
>315~~400
白含金修换厚度
衬套外径I
80~120
>120~180
>180~260
>260~~360
SC/T8036--94
配合长度L>2D
- 0. 04 ~--- 0. 01
0. 05 - 0. 02
-0. 06 ~ — 0. 03
0. 07 ~ - 0. 04
3.5.3尾轴铜衬套与尾轴配合的过盈量见表18。表18
轴颈直径d.mm
盈,%
尾轴与尾轴承配合要求
>120~180
>180~260
滑油润滑白合金,尾轴承安装间隙,修换间隙及白合金厚度见表19。表19
≥100~120
≥120~150
>150~180
≥180~220
≥220~260
安装间隙△
0.45~0.55
0.50~~0.60
0.55~0.65
0.60~0.70
0. 65~0.75
0.70~0.80
白合金新制最小厚度
配合长度L<2D
0.02~0.00
0. 03~0. 005
- 0. 04 ~0. 001
0. 05 ~ - 0. 02
>260~360
修换间隙△
白合金极限厚度
注:(D当白合金长度L>3d时,其安装间隙可按表值放大10%~20%,其修换间隙可放大20%。②当渔船在排上修理因更换尾部船板、龙骨等造成尾轴管变形,尾轴装不进时,允许把安装间放大50%,放大间隙仍不能安装者,应检查原因。③填料压盖内孔与尾轴铜套的间隙,可以取尾轴承安装间隙值的4倍。3.5.4.2铁梨木及层压胶木尾轴承安装间隙、修换间隙见表20。表20
100~120
>120~150
≥150~180
≥180~220
>220~260
安装间隙A
0. 80~0. 90
0. 90~~1. 00
1. 00~1. 10
1.10~~1.20
板条新制最小厚度
修换间隙△
板条极限厚度
注:(D偏心镗削尾轴承时,镗孔中心线应提高,其值可为安装间隙的50%~75%(前端轴承取50%)。削后最薄处铁梨木或层压胶木板条的厚度应满足表中规定的新制最小厚度值。(2)用铁梨木及层压胶木作尾轴承,在加工前应用水浸泡5关以上或用温水漫泡2天,以保证正确的配合间隙279
小提示:此标准内容仅展示完整标准里的部分截取内容,若需要完整标准请到上方自行免费下载完整标准文档。

标准图片预览:
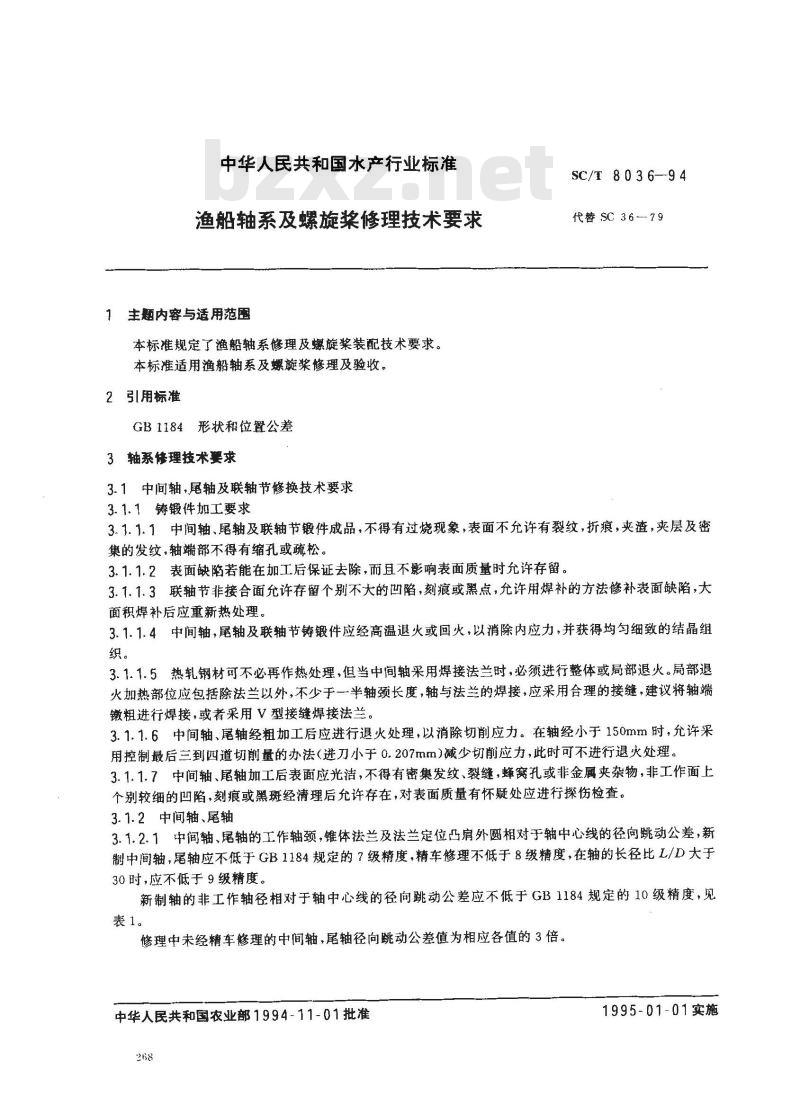
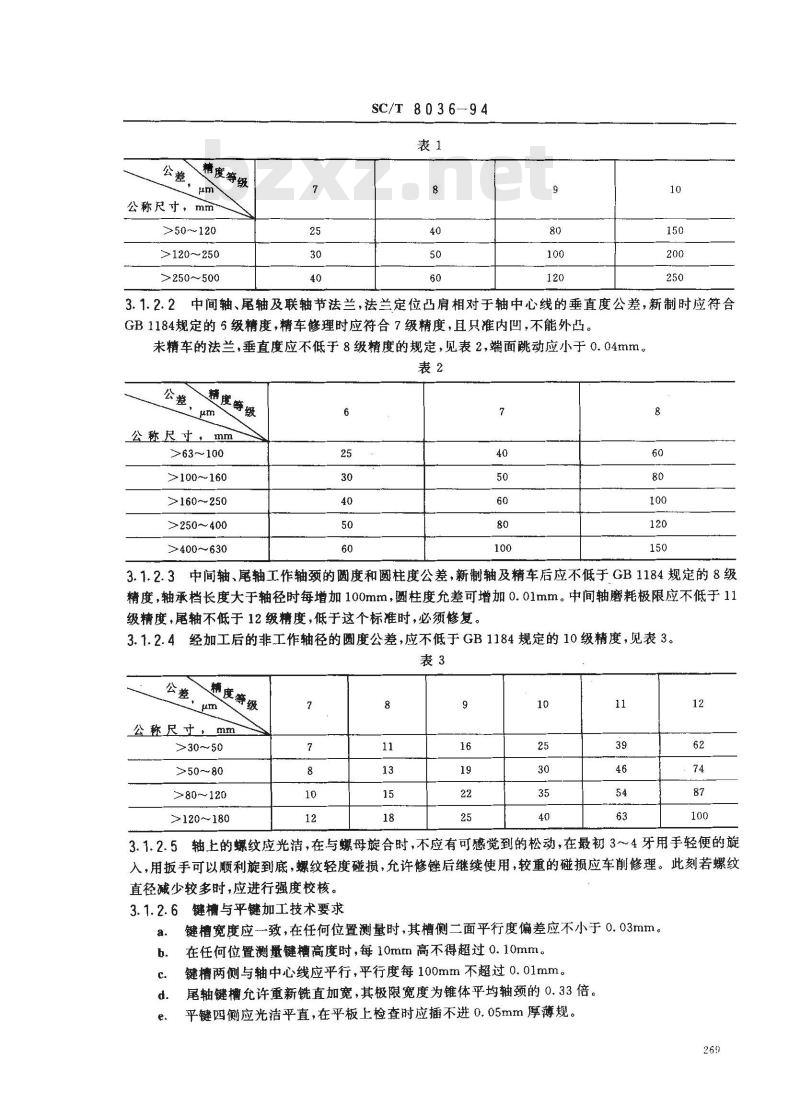

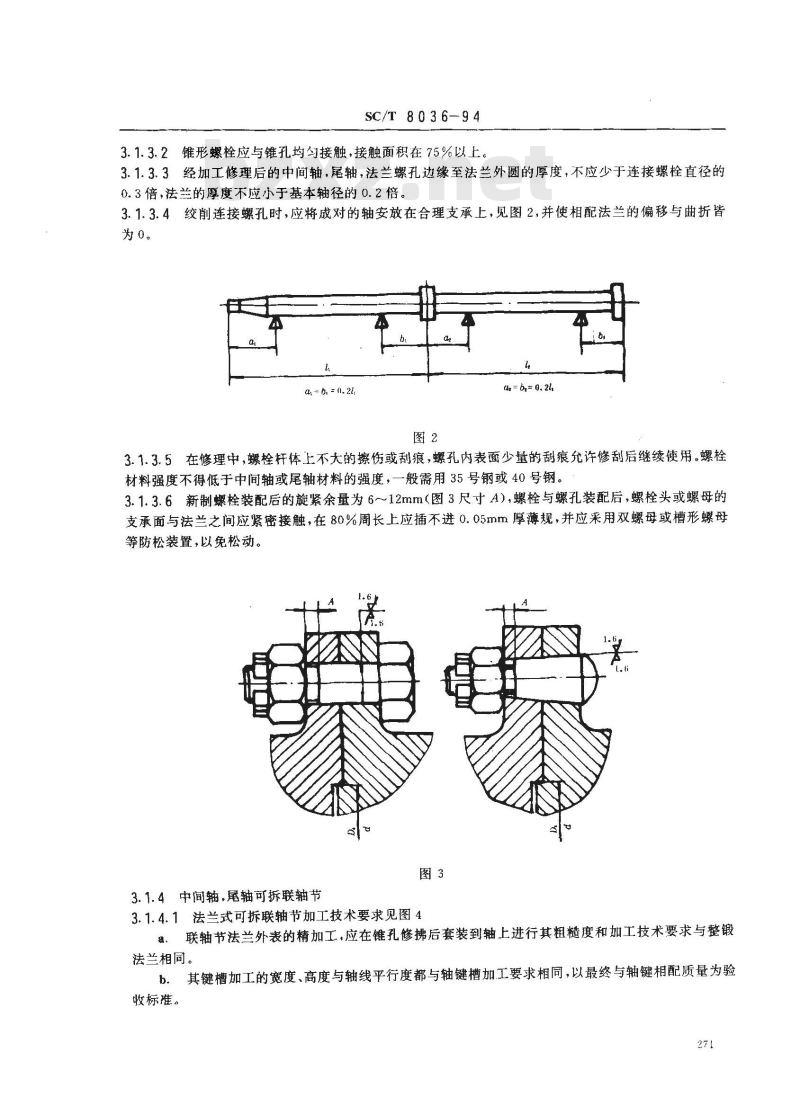
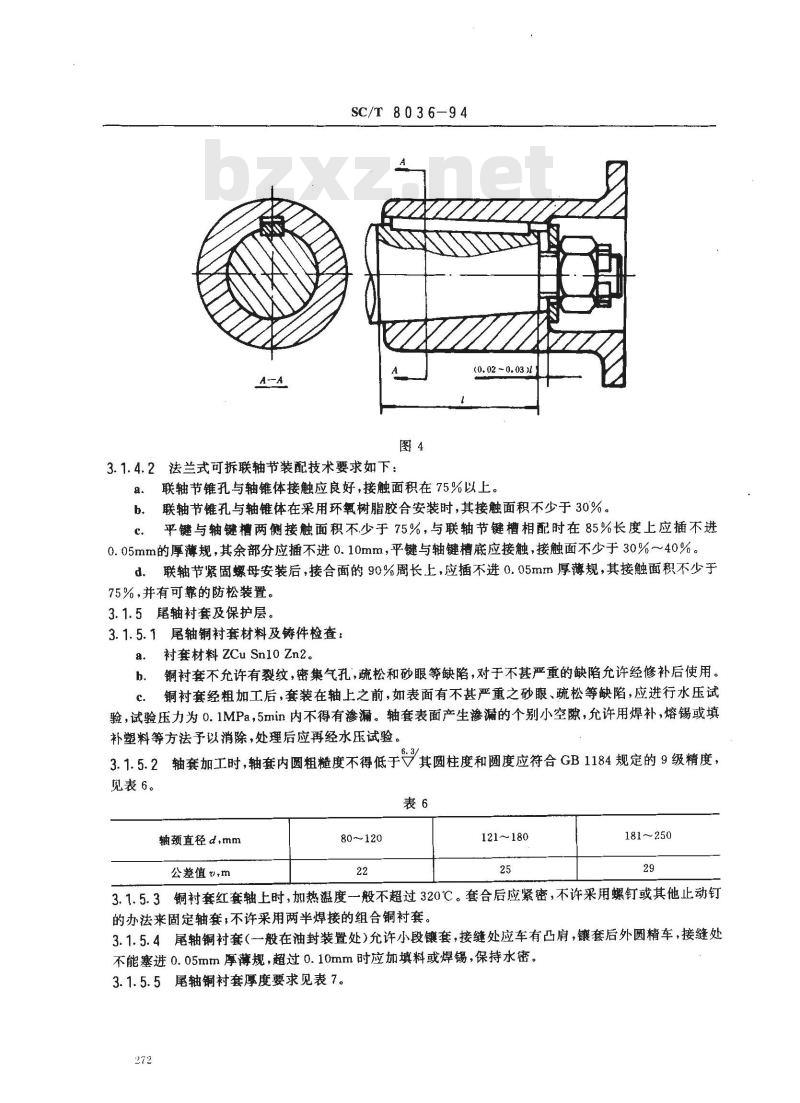
- 其它标准
- 热门标准
- 水产行业标准(SC)
- SC/T3309-2016 调味烤酥鱼
- SC/T3220-2016 干制对虾
- SC/T3309-2016 调味烤酥鱼
- SC/T8114-1998 船用主机小功率轴带交流发电装置
- SC/T3020-2004 水产品中已烯雌酚残留量的测定 酶联免疫法
- SC152.2-1986 渔船玻璃钢舾装件消防砂箱
- SC/T8019-1994 渔船吊杆承座
- SC/T1016.7-1995 中国池塘养鱼技术规范珠江三角洲地区食用鱼饲养技术
- SC1092-2007 麦瑞加拉鲮
- SC/T7012-2008 水产养殖动物病害经济损失计算方法
- SC/T8011-1994 渔船起重钢索滑车
- SC/T8018-1994 渔船吊杆
- SC/T6001.3-2001 渔业机械基本术语 水产品加工机械
- SC/T8043-1997 渔船主机前端齿轮箱安装技术要求
- SC/T8113-2000 渔船170系列柴油要修理技术要求
- 行业新闻
请牢记:“bzxz.net”即是“标准下载”四个汉字汉语拼音首字母与国际顶级域名“.net”的组合。 ©2009 标准下载网 www.bzxz.net 本站邮件:bzxznet@163.com
网站备案号:湘ICP备2023016450号-1
网站备案号:湘ICP备2023016450号-1