- 您的位置:
- 标准下载网 >>
- 标准分类 >>
- 机械行业标准(JB) >>
- JB/T 4201-1999 直齿锥齿轮精密热锻件 技术条件
标准号:
JB/T 4201-1999
标准名称:
直齿锥齿轮精密热锻件 技术条件
标准类别:
机械行业标准(JB)
标准状态:
现行-
发布日期:
1999-06-24 -
实施日期:
2000-06-24 出版语种:
简体中文下载格式:
.rar.pdf下载大小:
306.19 KB
替代情况:
JB 4201-1986

点击下载
标准简介:
标准下载解压密码:www.bzxz.net
JB/T 4201-1999 本标准是对 JB 4201-86《直齿锥齿轮精锻件 技术条件》的修订,适用范围有所增加,质量中晶粒度及脱碳深度作了适当调整。 本标准适用于在热模锻压机、模锻锤、螺旋压力机等设备上,采用精密热模锻工艺生产的直齿锥齿轮带齿锻件。它的轮齿表面不再加工,达到 GB/T 11365-1989《锥齿轮和准双曲面齿轮 精度》中 9~12 级精度。 本标准适用于重量小于或等于 20kg,最大外径和总厚度均小于或等于 250mm 的精锻件。超过上述范围时,对精锻件的要求由供需双方协商确定。 用冷挤压工艺成形的直齿锥齿轮精锻件可参照采用,但齿形精度相应提高一级以上按需选用。 本标准于年月日首次发布。 JB/T 4201-1999 直齿锥齿轮精密热锻件 技术条件 JB/T4201-1999

部分标准内容:
JB/T4201-·1999
本标准是对JB4201-86《直齿锥齿轮精锻件技术条件》的修订。本标准与JB4201—86相比,主要技术内容改变如下:1)原标准名称为《直齿锥齿轮精锻件技术条件》,更改为《直齿锥齿轮精密热锻件技术条件》,正文中也作了相应的更改。
2)标准适用范围增加了冷挤压精锻件。3)原标准内在质量中,晶粒度及脱碳深度作了适当调整。4)顶料杆压痕深度改为正负值,见本标准表5。5)标准格式按要求,增加了第2章“引用标谁”和第3章“定义”,原章条作了相应的变更,本标准自实施之日起代替JB4201-86。本标准的附录A是提示的附录。
本标推由全国锻压标推化技术委员会提出并归口本标准起草单位:上海汽车股份有限公司汽车齿轮总厂。本标准主要起草人:杨歧华、庄建华、沈震耀、殷伟民。253
中华人民共和国机械行业标准
直齿锥齿轮精密热锻件
技术条件
Technical requirements on precision hot forgings of straight bevel gear1范围
JB/T 4201--.1999
代替JB4201-86
本标准适用于在热模锻压力机、模锻锤、螺旋压力机等设备上,采用精密热模锻工艺生产的直齿锥齿轮带齿锻件(以下简称精锻件)。它的轮齿表面不再加工,达到GB/T11365--1989《锥齿轮和准双曲面齿轮精度》中9~12级精度。
本标准适用于重量小于或等于20kg,最大外径和总厚度均小于或等于250mm的精锻件。超过上述范围时,对精锻件的要求由供需双方协商确定。用冷挤压工艺成形的直齿锥齿轮精锻件,可参照采用,但齿形精度应相应提高一级以上按需选用。2引用标准
下列标准所包含的条文,通过在本标中引用而构成为本标准的条文。本标准出版时,所示版本均为有效。所有标准都会被修订,使用本标准的各方应探讨使用下列标准最新版本的可能性。GB/T113651989锥齿轮和推双曲面齿轮精度GB/T12362—1990钢质模锻件公差及机械加工余量3定义
本标准采用下列定义。
3.1直齿锥齿轮精密热锻件
采用精密热模锻工艺获得的直齿锥齿轮带齿锻件,其轮齿表面不再进行切削加工,精度达到GB/T11365所规定的12级以上,这类锻件通称为直齿锥齿轮精密热锻件。4技术要求
4.1原材料
精锻件使用的原材料应为含碳量小于或等于0.65%的碳素结构钢材或合金元素总含量小于或等于5.0%的合金结构钢材。
4.2机械加工余量
4.2.1外径的双面加工余量Aα,根据外径D和总厚度H选择,见表1。4.2.2内径的双面加工余量△b,根据内径d和总厚度H选择,见表2。4.2.3端面的加工余量△c,根据端面直径D和总厚度H选择,见表3。4.3公差及极限值
4.3.1直径、高度、厚度公差及横向残余毛边、切人锻件深度、错差、顶料杆压痕深度极限值直径、高度、厚度公差根据下列三要素,从表4和表5中查得:a)精锻件的最大直径、总高度、总厚度;b)精锻件的重量;
国家机械工业局1999-06-24批准254
2000-01-01实施
JB/T4201—1999
c)精锻件的形状复杂系数(其计算和分级均按GB/T12362—1990中3.1.2的规定)。表1外径的双面加工余量
表4和表5的使用方法:
总厚度
至10!
内径的双面加工余量
总厚度H
表3端面的加工余量
外径D
双面加工余量2a
大于30
总厚度H
内径d
双面加工余量
端面直径D
端面加工余量△c
以精锻件重量为起始点,在表中重量栏内选定相应的范围,然后沿水平线向右移,查得直径、高度、厚度的公差值;向左移,查得横向残余毛边、切入锻件深度、错差极限值及顶料杆压痕深度极限值。当向右查找直径等公差值时,若形状复杂系数为S,,则按精锻件重量沿水平线向右移至与该直径等相交的框格即可;如遇形状复杂系数为S(或S、S.),则沿倾斜线向下至与S,(或S:S.)垂线的交点,再沿水平线向右移至与该直径等相交的框格。框格内数据即为所要查找的公差值。所有直径、高度、厚度的公差均按精锻件上相应的最大尺寸查得。机械加工.面与非机械加工面(不包括轮齿表面,以下同)的公差值相同。顶料杆压痕的直径和位置应在锻件图土标注。横向残余毛边、切人锻件深度、错差及顶料杆压痕深度极限值的应用与任何其他公差无关。在确定机械加工余量时应加上这些项目的实际偏差值。4.3.2圆角半径及其公差
4.3.2.1当与某圆角相连接的面均不作机械加工时,该圆角半径可通过表6计算得到。4.3.2.2当与某圆角相连接的两个面中,有一个面或两个面必须机械加工时,该圆角半径通过式(1)、式(2)计算得到:
外圆角r=机械加工余量+产品倒角值(mm)其相应的内圆角R r+(2~5)mm
(2)
JB/T4201--1999
J6't+i
12*0—
060/00-
b60干
b80干下载标准就来标准下载网
pe o-/oo-
b90干
p80-/80
pg0于
JB/T4201—1999
6*0—
+'0—
JB/T 4201-—1999
表6非机械加工部位的圆角半径计算表H/D
4.3.2.3通过上述计算所得的圆角均应圆整至表7中的数值。圆角半径系列
圆角半径的公差值以相应尺寸的百分比表示,见表8。表8
圆角半径公差的计算
上(1)
下(—)
拔模斜度及其公差
0. 061- 0. 5
0.0711+0. 5
2. 5r +0.5
3.0r-+-0.5
3. 5r-t 0. 5
拔模斜度应根据精锻件的有关高度与直径的比值H/D和有无顶料装置,通过表9确定。表9拔模斜度
模锻斜度公差按GB/T12362—1990表10中的精密级确定。4.3.4纵向毛刺极限值
外拔模斜度α
10°00°
内拔模斜度β
130″
10°00%
12°00″
切边、冲孔以及顶料杆与型腔模孔间的配合间隙等,都会在精锻件上造成纵向毛刺,其极限值根据精锻件重量由表10查得。它与其他公差无关。纵向毛刺应在机械加工过程中去除。表10纵向毛刺极限值
精锻件重量
极限值
4.4质量要求
4.4.1表面质量
4.4.1.1齿面的质量要求如下:
JB/T 4201—1999
氧化皮厚度不得大于0.04mm,应通过表面清理去除干净。此时,表面粗糙度必须符合技术文件中的要求,一般应在Ra6.3以下(包括Ra6.3);不允许存在裂纹、爽杂物、折叠、凸起等缺陷;不影响齿轮精度的碰伤、微小凹坑等缺陷,其极限值由表11确定,表11齿面缺陷极限值
极限值
左右两侧齿面缺陷处数(个)
的规定。
累计缺陷总处数(个)
每一缺陷最大长度
每一缺陷深度
分度圆直径
机械加工表面的缺陷及非机械加工表面的缺陷按GB/T12362—1990中3.2.14中a)及b)4.4.2内在质量
4.4.2.1精锻件表面硬度及其测量位置等可由供需双方协商确定,并在技术文件上注明。4.4.2.2精锻件的晶粒度应达到3~8级,视材料而定。4.4.2.3精锻后作渗碳淬火的精锻件,其半脱碳深度不允许超过渗碳深度的15%。除本章规定外,如有其他要求时,可由供需双方协商确定。5检验规则
检验的抽样方式和检查项目具体要求见表12或由供需双方协商选择,并在技术文件上注明,由制造厂质检部门检查验收。除表12外,如有其他要求(如探伤、内应力测定、轮齿强度等)由供需双方协商后,在技术文件上注明。
表12抽样方式和检查项目
抽样方式
每换齿形模腔,必须对首件和第二件,以及之后每锻300~~400件后的首件和第二件进行检查。每换与齿形模腔相对使用的非齿形模腔,必须对首件和第二件,以及之后每锻500~600件后的首件和第二件进行检查。
6标志、防锈、包装及贮存
a)齿轮精度
b)齿面缺陷
检查项目
a)高度
b)厚度
c)有关的圆角半径
a)拔模角
b)有关的圆角半径
c)有关的表面缺陷
d)表面硬度
)直径
d)错差
e)横向残余毛边
f)切人锻件深度
g)纵向毛刺
h)顶料杆压痕深度
精密热锻件的标志、防锈、包装、运输及贮存等,由供需双方协商确定,并在定货协议上注明。259
应用示例见图A1、表A1和表A2。Ratas(rs)
2 -0.2 (R2)
端面模数
分度圆直径
分度圆压力角
节锥母线长
齿项高
齿全高
安装距
分度圆上理论弦齿摩(参考)
齿项至弦高度(参考)
齿面粗糙度
渗碳深度
齿面修整
JB/T 4201-1999
附录A
(提示的附录)
应用示例
$ 60. 2 =(D)
6rn'2r
(H))S
R, tae(r2)
$100 (D,)
($100)
表A1齿轮参数
(1 'oz)
(1'12)
6.579-8:98
20CrMnTi
0. 7~1. 1
9-b(GB/T 11365 --1989)
JB/T4201—1999
各加工余量、公差、极限值等计算,列于表A2,除齿面粗糙度外,表中未注单位均为mm。表A2各加工余量、公差和极限值的计算项目
加工余量
端面A、B的
加工余量
外径公差
错差极限值
横向残余毛边极限值
切人锻件深度极限值
厚度公差
顶料杆压痕
深度极限值
圆角半径及其公差
已知外圆D=58,厚度H=71.1。查表1,得D处加工余量1为1.7,加上实际错差值0.5。
Di =1. 7+0. 5+58
D2不作机械加工,取2100
D,不加工
1)-±100
已知直径50~$120,总厚度71.1,查表3,得A面和B面的加工余量为1.4。
H - 20. 1-1. 4
H, =71. 1+ 1. 4
锻件复杂系数的计算:
精锻件重2.1kg,外廊包容体重:W外购
X1002×71.1×7.85×10~64.384kg0.479属S2,
查表4得:±1.1
查表4得:0.6
查表4得:
横向残余毛边极限值十0.6;
切入锻件深度极限值-0.3
已知总厚度为71.1,锻件重2.1kg,Sz=0.479。查表5得:+1.4
查表5得:
H, -- 2l. 5
D,100t!
H1 = 21. 5+82
H* -- 72. 5t:1
a)已知r1处倒角要求为1.5×45°,外径与端面均需切削加工
r-- 1. 4+1. 7-+1. 5-- 4. 6
R,=r1+2-~ 6. 6
b)已知r2处不作机械加工,
查表6得:r2—0.63Rz=2
c)已知r3处无倒角要求,端面作机械加工,加工余量为1.4r31. 4
查表7、表
8,并经圆整
rr=5+1
Ri=6+1
圆整得:
r21+82
R2 2+8:5
圆整得:
r-2+85
外拔模斜度α
及其公差
纵向毛刺极限值
表面质量
内在质量
齿轮精度
JB/T4201-—1999
表A22(完)
已知:H-51、D-58,
查表9得:α一3°
=0.88,无顶出装置。
查GB/T12362—1990中表9得公差为:1°已知锻件重2.1kg,查表10得:
高度极限1.0;宽度极限0.5
a)齿面:
氧化皮厚度不大于0.04。粗糙度Ra6.3。已知分度圆直径为100,查表11,得不影响齿轮精度的缺陷,在左右两侧面处数不多于2处,累计缺陷总处数不多于5处,每--缺陷最大长度不大于1.2,每一缺陷深度不大于0.15。不允许存在裂纹、夹杂物、折叠、凸起等缺陷b)加工表面的缺陷深度不大于加工余量的1/4。即A面和B面处不大于1.4/4:D外径处不大于1.7/4c)非加工表面的缺陷深度不大于厚度公差的1/3。即不大于 1.8/3
a)精锻件的晶粒度3~8级;
b)已知渗碳深度为0.7~1.1,半脱碳深度应为:(0. 7~1. 1)×15% = (0. 105~~0. 165)c)已知材料为20CrMnTi,
HB=156~217,dg=4.1~4.8
按技术文件要求,齿轮精度为:9-b(GB/T 11365--1989)
采用鼓形齿
高度:1.0
宽度:0,5
0.35;0.43
0.105~0. 165
HB- 156~217
dg== 4. 1--4. 8
小提示:此标准内容仅展示完整标准里的部分截取内容,若需要完整标准请到上方自行免费下载完整标准文档。
本标准是对JB4201-86《直齿锥齿轮精锻件技术条件》的修订。本标准与JB4201—86相比,主要技术内容改变如下:1)原标准名称为《直齿锥齿轮精锻件技术条件》,更改为《直齿锥齿轮精密热锻件技术条件》,正文中也作了相应的更改。
2)标准适用范围增加了冷挤压精锻件。3)原标准内在质量中,晶粒度及脱碳深度作了适当调整。4)顶料杆压痕深度改为正负值,见本标准表5。5)标准格式按要求,增加了第2章“引用标谁”和第3章“定义”,原章条作了相应的变更,本标准自实施之日起代替JB4201-86。本标准的附录A是提示的附录。
本标推由全国锻压标推化技术委员会提出并归口本标准起草单位:上海汽车股份有限公司汽车齿轮总厂。本标准主要起草人:杨歧华、庄建华、沈震耀、殷伟民。253
中华人民共和国机械行业标准
直齿锥齿轮精密热锻件
技术条件
Technical requirements on precision hot forgings of straight bevel gear1范围
JB/T 4201--.1999
代替JB4201-86
本标准适用于在热模锻压力机、模锻锤、螺旋压力机等设备上,采用精密热模锻工艺生产的直齿锥齿轮带齿锻件(以下简称精锻件)。它的轮齿表面不再加工,达到GB/T11365--1989《锥齿轮和准双曲面齿轮精度》中9~12级精度。
本标准适用于重量小于或等于20kg,最大外径和总厚度均小于或等于250mm的精锻件。超过上述范围时,对精锻件的要求由供需双方协商确定。用冷挤压工艺成形的直齿锥齿轮精锻件,可参照采用,但齿形精度应相应提高一级以上按需选用。2引用标准
下列标准所包含的条文,通过在本标中引用而构成为本标准的条文。本标准出版时,所示版本均为有效。所有标准都会被修订,使用本标准的各方应探讨使用下列标准最新版本的可能性。GB/T113651989锥齿轮和推双曲面齿轮精度GB/T12362—1990钢质模锻件公差及机械加工余量3定义
本标准采用下列定义。
3.1直齿锥齿轮精密热锻件
采用精密热模锻工艺获得的直齿锥齿轮带齿锻件,其轮齿表面不再进行切削加工,精度达到GB/T11365所规定的12级以上,这类锻件通称为直齿锥齿轮精密热锻件。4技术要求
4.1原材料
精锻件使用的原材料应为含碳量小于或等于0.65%的碳素结构钢材或合金元素总含量小于或等于5.0%的合金结构钢材。
4.2机械加工余量
4.2.1外径的双面加工余量Aα,根据外径D和总厚度H选择,见表1。4.2.2内径的双面加工余量△b,根据内径d和总厚度H选择,见表2。4.2.3端面的加工余量△c,根据端面直径D和总厚度H选择,见表3。4.3公差及极限值
4.3.1直径、高度、厚度公差及横向残余毛边、切人锻件深度、错差、顶料杆压痕深度极限值直径、高度、厚度公差根据下列三要素,从表4和表5中查得:a)精锻件的最大直径、总高度、总厚度;b)精锻件的重量;
国家机械工业局1999-06-24批准254
2000-01-01实施
JB/T4201—1999
c)精锻件的形状复杂系数(其计算和分级均按GB/T12362—1990中3.1.2的规定)。表1外径的双面加工余量
表4和表5的使用方法:
总厚度
至10!
内径的双面加工余量
总厚度H
表3端面的加工余量
外径D
双面加工余量2a
大于30
总厚度H
内径d
双面加工余量
端面直径D
端面加工余量△c
以精锻件重量为起始点,在表中重量栏内选定相应的范围,然后沿水平线向右移,查得直径、高度、厚度的公差值;向左移,查得横向残余毛边、切入锻件深度、错差极限值及顶料杆压痕深度极限值。当向右查找直径等公差值时,若形状复杂系数为S,,则按精锻件重量沿水平线向右移至与该直径等相交的框格即可;如遇形状复杂系数为S(或S、S.),则沿倾斜线向下至与S,(或S:S.)垂线的交点,再沿水平线向右移至与该直径等相交的框格。框格内数据即为所要查找的公差值。所有直径、高度、厚度的公差均按精锻件上相应的最大尺寸查得。机械加工.面与非机械加工面(不包括轮齿表面,以下同)的公差值相同。顶料杆压痕的直径和位置应在锻件图土标注。横向残余毛边、切人锻件深度、错差及顶料杆压痕深度极限值的应用与任何其他公差无关。在确定机械加工余量时应加上这些项目的实际偏差值。4.3.2圆角半径及其公差
4.3.2.1当与某圆角相连接的面均不作机械加工时,该圆角半径可通过表6计算得到。4.3.2.2当与某圆角相连接的两个面中,有一个面或两个面必须机械加工时,该圆角半径通过式(1)、式(2)计算得到:
外圆角r=机械加工余量+产品倒角值(mm)其相应的内圆角R r+(2~5)mm
(2)
JB/T4201--1999
J6't+i
12*0—
060/00-
b60干
b80干下载标准就来标准下载网
pe o-/oo-
b90干
p80-/80
pg0于
JB/T4201—1999
6*0—
+'0—
JB/T 4201-—1999
表6非机械加工部位的圆角半径计算表H/D
4.3.2.3通过上述计算所得的圆角均应圆整至表7中的数值。圆角半径系列
圆角半径的公差值以相应尺寸的百分比表示,见表8。表8
圆角半径公差的计算
上(1)
下(—)
拔模斜度及其公差
0. 061- 0. 5
0.0711+0. 5
2. 5r +0.5
3.0r-+-0.5
3. 5r-t 0. 5
拔模斜度应根据精锻件的有关高度与直径的比值H/D和有无顶料装置,通过表9确定。表9拔模斜度
模锻斜度公差按GB/T12362—1990表10中的精密级确定。4.3.4纵向毛刺极限值
外拔模斜度α
10°00°
内拔模斜度β
130″
10°00%
12°00″
切边、冲孔以及顶料杆与型腔模孔间的配合间隙等,都会在精锻件上造成纵向毛刺,其极限值根据精锻件重量由表10查得。它与其他公差无关。纵向毛刺应在机械加工过程中去除。表10纵向毛刺极限值
精锻件重量
极限值
4.4质量要求
4.4.1表面质量
4.4.1.1齿面的质量要求如下:
JB/T 4201—1999
氧化皮厚度不得大于0.04mm,应通过表面清理去除干净。此时,表面粗糙度必须符合技术文件中的要求,一般应在Ra6.3以下(包括Ra6.3);不允许存在裂纹、爽杂物、折叠、凸起等缺陷;不影响齿轮精度的碰伤、微小凹坑等缺陷,其极限值由表11确定,表11齿面缺陷极限值
极限值
左右两侧齿面缺陷处数(个)
的规定。
累计缺陷总处数(个)
每一缺陷最大长度
每一缺陷深度
分度圆直径
机械加工表面的缺陷及非机械加工表面的缺陷按GB/T12362—1990中3.2.14中a)及b)4.4.2内在质量
4.4.2.1精锻件表面硬度及其测量位置等可由供需双方协商确定,并在技术文件上注明。4.4.2.2精锻件的晶粒度应达到3~8级,视材料而定。4.4.2.3精锻后作渗碳淬火的精锻件,其半脱碳深度不允许超过渗碳深度的15%。除本章规定外,如有其他要求时,可由供需双方协商确定。5检验规则
检验的抽样方式和检查项目具体要求见表12或由供需双方协商选择,并在技术文件上注明,由制造厂质检部门检查验收。除表12外,如有其他要求(如探伤、内应力测定、轮齿强度等)由供需双方协商后,在技术文件上注明。
表12抽样方式和检查项目
抽样方式
每换齿形模腔,必须对首件和第二件,以及之后每锻300~~400件后的首件和第二件进行检查。每换与齿形模腔相对使用的非齿形模腔,必须对首件和第二件,以及之后每锻500~600件后的首件和第二件进行检查。
6标志、防锈、包装及贮存
a)齿轮精度
b)齿面缺陷
检查项目
a)高度
b)厚度
c)有关的圆角半径
a)拔模角
b)有关的圆角半径
c)有关的表面缺陷
d)表面硬度
)直径
d)错差
e)横向残余毛边
f)切人锻件深度
g)纵向毛刺
h)顶料杆压痕深度
精密热锻件的标志、防锈、包装、运输及贮存等,由供需双方协商确定,并在定货协议上注明。259
应用示例见图A1、表A1和表A2。Ratas(rs)
2 -0.2 (R2)
端面模数
分度圆直径
分度圆压力角
节锥母线长
齿项高
齿全高
安装距
分度圆上理论弦齿摩(参考)
齿项至弦高度(参考)
齿面粗糙度
渗碳深度
齿面修整
JB/T 4201-1999
附录A
(提示的附录)
应用示例
$ 60. 2 =(D)
6rn'2r
(H))S
R, tae(r2)
$100 (D,)
($100)
表A1齿轮参数
(1 'oz)
(1'12)
6.579-8:98
20CrMnTi
0. 7~1. 1
9-b(GB/T 11365 --1989)
JB/T4201—1999
各加工余量、公差、极限值等计算,列于表A2,除齿面粗糙度外,表中未注单位均为mm。表A2各加工余量、公差和极限值的计算项目
加工余量
端面A、B的
加工余量
外径公差
错差极限值
横向残余毛边极限值
切人锻件深度极限值
厚度公差
顶料杆压痕
深度极限值
圆角半径及其公差
已知外圆D=58,厚度H=71.1。查表1,得D处加工余量1为1.7,加上实际错差值0.5。
Di =1. 7+0. 5+58
D2不作机械加工,取2100
D,不加工
1)-±100
已知直径50~$120,总厚度71.1,查表3,得A面和B面的加工余量为1.4。
H - 20. 1-1. 4
H, =71. 1+ 1. 4
锻件复杂系数的计算:
精锻件重2.1kg,外廊包容体重:W外购
X1002×71.1×7.85×10~64.384kg0.479属S2,
查表4得:±1.1
查表4得:0.6
查表4得:
横向残余毛边极限值十0.6;
切入锻件深度极限值-0.3
已知总厚度为71.1,锻件重2.1kg,Sz=0.479。查表5得:+1.4
查表5得:
H, -- 2l. 5
D,100t!
H1 = 21. 5+82
H* -- 72. 5t:1
a)已知r1处倒角要求为1.5×45°,外径与端面均需切削加工
r-- 1. 4+1. 7-+1. 5-- 4. 6
R,=r1+2-~ 6. 6
b)已知r2处不作机械加工,
查表6得:r2—0.63Rz=2
c)已知r3处无倒角要求,端面作机械加工,加工余量为1.4r31. 4
查表7、表
8,并经圆整
rr=5+1
Ri=6+1
圆整得:
r21+82
R2 2+8:5
圆整得:
r-2+85
外拔模斜度α
及其公差
纵向毛刺极限值
表面质量
内在质量
齿轮精度
JB/T4201-—1999
表A22(完)
已知:H-51、D-58,
查表9得:α一3°
=0.88,无顶出装置。
查GB/T12362—1990中表9得公差为:1°已知锻件重2.1kg,查表10得:
高度极限1.0;宽度极限0.5
a)齿面:
氧化皮厚度不大于0.04。粗糙度Ra6.3。已知分度圆直径为100,查表11,得不影响齿轮精度的缺陷,在左右两侧面处数不多于2处,累计缺陷总处数不多于5处,每--缺陷最大长度不大于1.2,每一缺陷深度不大于0.15。不允许存在裂纹、夹杂物、折叠、凸起等缺陷b)加工表面的缺陷深度不大于加工余量的1/4。即A面和B面处不大于1.4/4:D外径处不大于1.7/4c)非加工表面的缺陷深度不大于厚度公差的1/3。即不大于 1.8/3
a)精锻件的晶粒度3~8级;
b)已知渗碳深度为0.7~1.1,半脱碳深度应为:(0. 7~1. 1)×15% = (0. 105~~0. 165)c)已知材料为20CrMnTi,
HB=156~217,dg=4.1~4.8
按技术文件要求,齿轮精度为:9-b(GB/T 11365--1989)
采用鼓形齿
高度:1.0
宽度:0,5
0.35;0.43
0.105~0. 165
HB- 156~217
dg== 4. 1--4. 8
小提示:此标准内容仅展示完整标准里的部分截取内容,若需要完整标准请到上方自行免费下载完整标准文档。

标准图片预览:
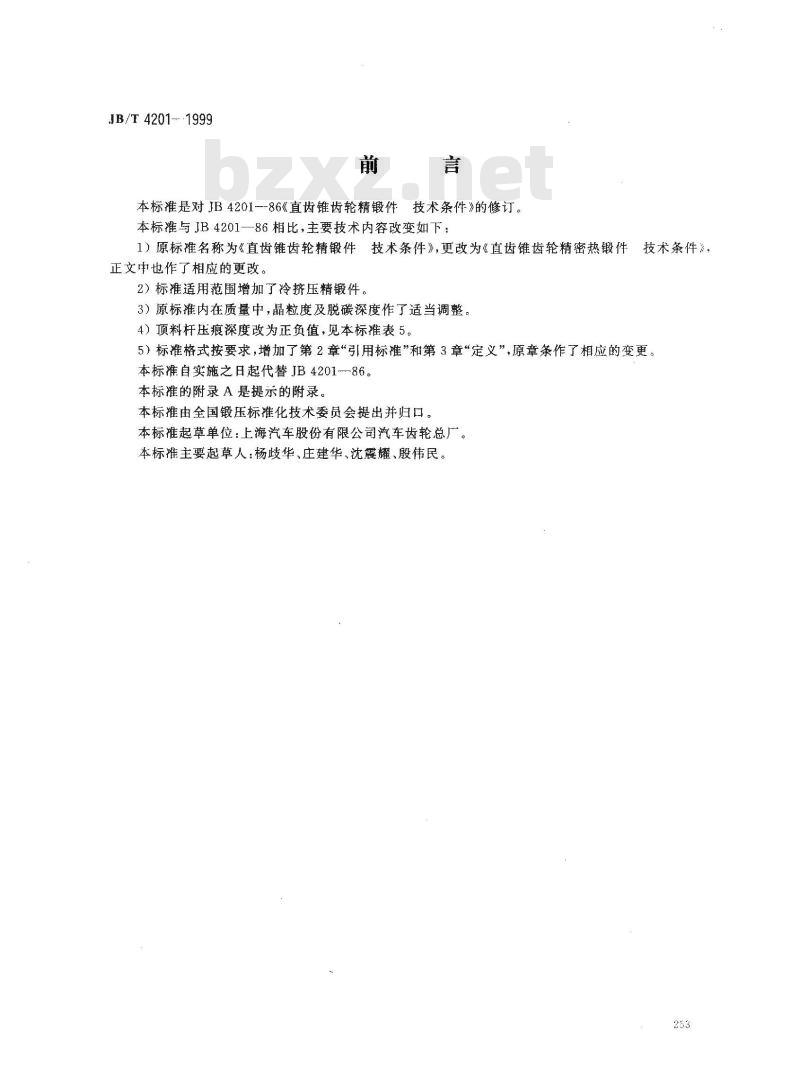
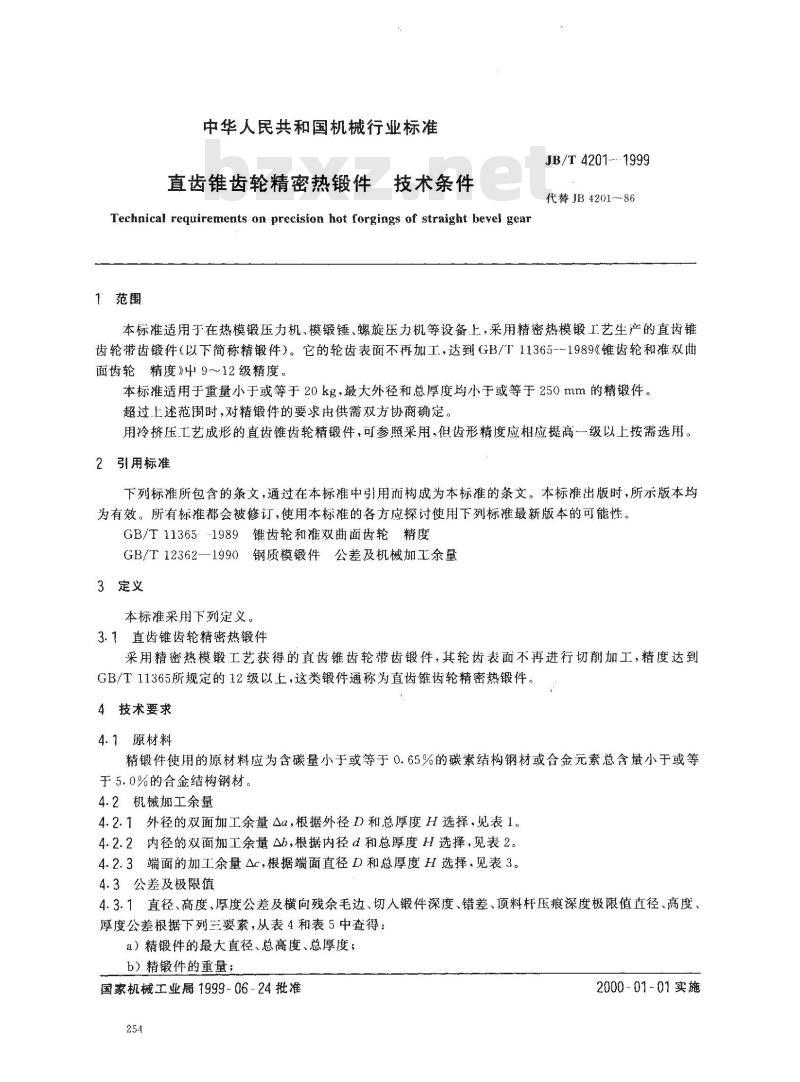
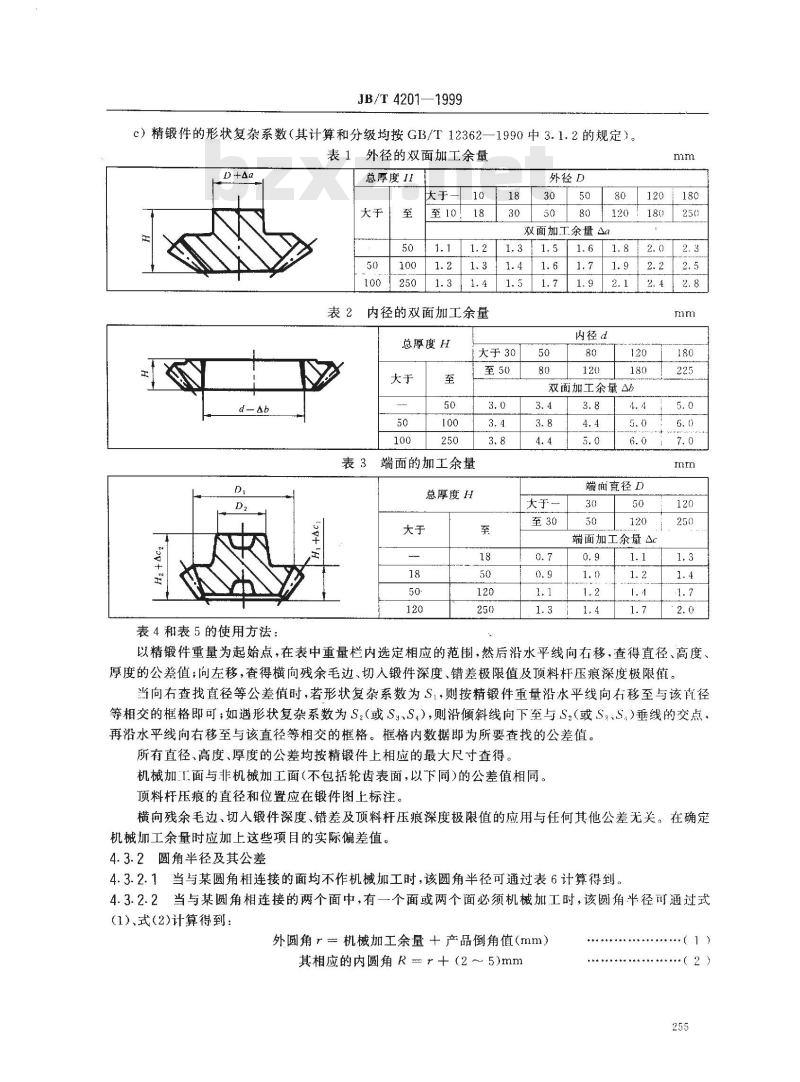
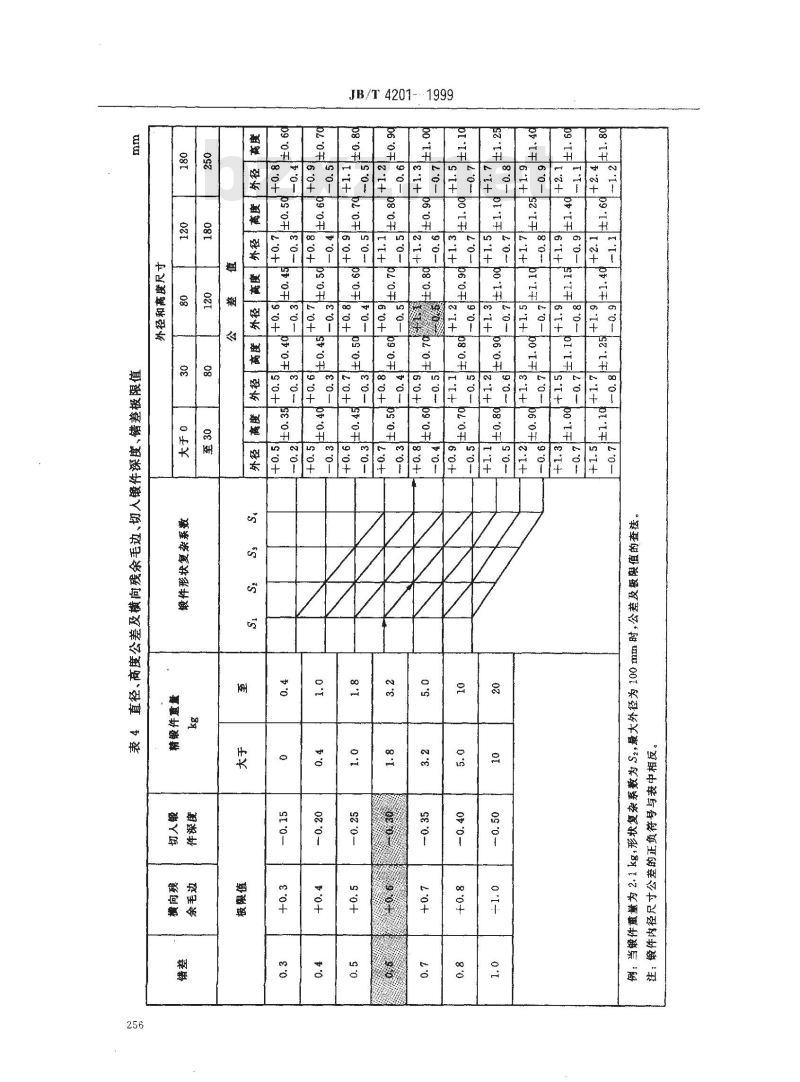
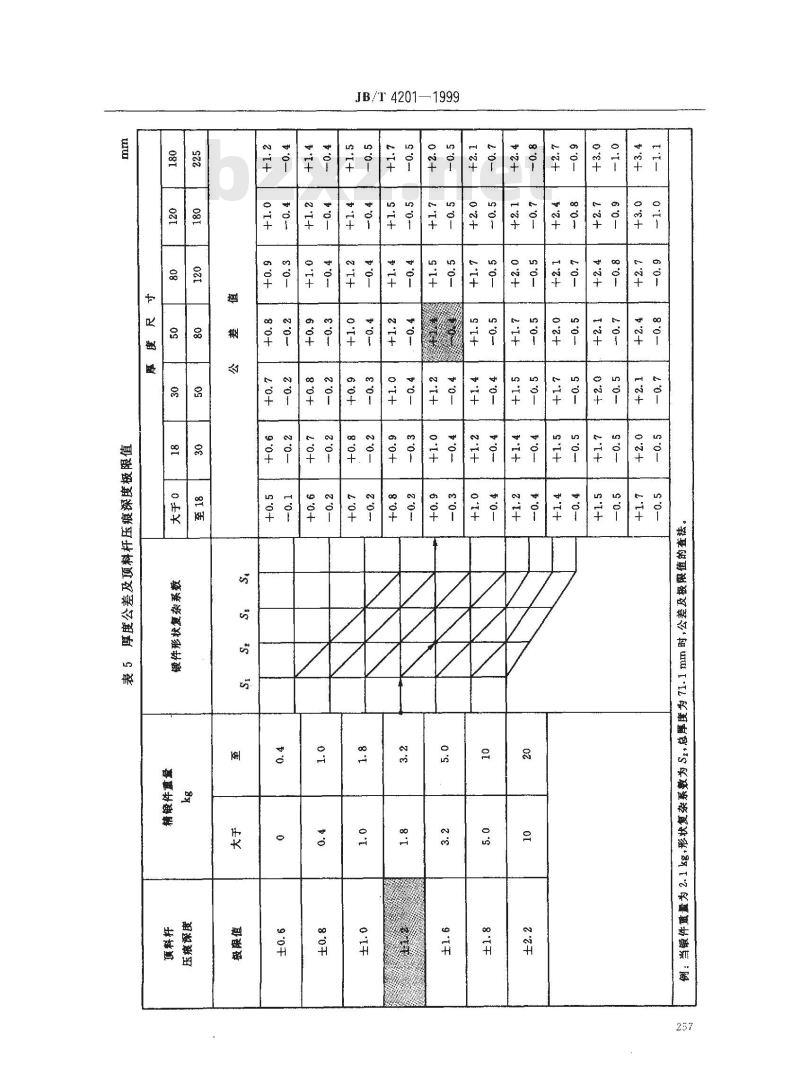
- 其它标准
- 热门标准
- 机械行业标准(JB)
- JB/T5762.2-2006 转塔车床 第2部分:精度
- JB/T10719-2007 焊接聚晶金刚石或立方氮化硼槽刀
- JB/T10725-2007 天然金刚石车刀
- JB/T10596-2006 磁阻式步进电动机通用技术条件
- JB/T10723-2007 焊接聚晶金刚石或立方氮化硼镗刀
- JB/T7993-2012 碳化硼化学分析方法
- JB/T7144.1-1993 青饲料切碎机 技术条件
- JB/T5372.6-1991 8mm槽系组合夹具其他件 鳞齿支承螺母
- JB/T5742.1-2010 单排多轴木工钻床 第1部分:参数
- JB/T9162.8-1999 表柱 尺寸
- JB/T5368.18-1991 8mm槽系组合夹具定位件 V形板
- JB/T7712-2007 高温合金热处理
- JB/T5368.16-1991 8mm槽系组合夹具定位件 定位板
- JB3930.58-1985 U形角铁
- JB/T5371.12-1991 8mm槽系组合夹具压紧件 V形压板
- 行业新闻
请牢记:“bzxz.net”即是“标准下载”四个汉字汉语拼音首字母与国际顶级域名“.net”的组合。 ©2009 标准下载网 www.bzxz.net 本站邮件:bzxznet@163.com
网站备案号:湘ICP备2023016450号-1
网站备案号:湘ICP备2023016450号-1