- 您的位置:
- 标准下载网 >>
- 标准分类 >>
- 化工行业标准(HG) >>
- HG/T 2387-2007 工业设备化学清洗质量标准
标准号:
HG/T 2387-2007
标准名称:
工业设备化学清洗质量标准
标准类别:
化工行业标准(HG)
标准状态:
现行-
发布日期:
2007-09-22 -
实施日期:
2008-04-01 出版语种:
简体中文下载格式:
.rar.pdf下载大小:
228.82 KB
替代情况:
替代HG/T 2387-1992

点击下载
标准简介:
标准下载解压密码:www.bzxz.net
本标准规定了工业设备化学清洗的技术要求、质量指标和试验方法。本标准适用于碳钢类、不锈钢类、紫铜及铜合金、铝及铝合金等材质的工业设备表面形成的水垢、锈垢、油垢及其他污垢的化学清洗;工业设备的物料垢化学清洗和其他材料制工业设备污垢的化学清洗可参照执行。 HG/T 2387-2007 工业设备化学清洗质量标准 HG/T2387-2007

部分标准内容:
中华人民共和国化工行业标准
HG/T2387—2007
代替HG/T2387—1992
工业设备化学清洗质量标准
Chemical cleaning quality code for industrial facility2007-09-22发布
2008-04-01实施
中华人民共和国国家发展和改革委员会发布前
工业设备化学清洗质量标准。
2规范性引用文件
3术语和定义
3.1化学清洗
3.2腐蚀率
3.3缓蚀率
3.4腐蚀量
3.5除垢率
3.6洗净率
3.7监视管
3.8指定面
3.9未指表面
3.10视觉清洁
3.11油含量
3.12钝化膜
3.13柔性取样框
4分类..
5要求..
5.1一般要求
5.2质量要求,
6试验方法
6.1腐蚀率及腐蚀量的测定
6.2除垢率的测定.
6.3洗净率的测定.
6.4油含量的测定。
6.5钝化膜的检测,.
7.1腐蚀率和腐蚀量
7.2除垢率或洗净率。
7.3油含量的检验:
7.4钝化膜...
7.5特殊要求,
8化学清洗工程交工验收
8.1资料提交,
8.2设备交验..
8.3文件归档.,
附录A金属表面油含量分析方法一一四氯化碳法A.1油含量分析仪测定法.
A.1.1仪器及材料
A.1.2操作步骤。
A.1.3结果计算
标准分享网一免费标准下载网站bzfxw.comHG/T 2387-2007
A.2油含量重量测定法
A.2.1仪器及材料
A.2.2操作步骤..
A.2.3结果计算
附录B柔性取样框
附录C工业设备化学清洗工程质量评定及验收单标准分享网提示您:非正式出版物仅供参考标准分享网一免费标准下载网站bzfxw.comHG/T 2387-2007
bzfxw.com
本标准代替HG/T2387-1992《工业设备化学清洗质量标准》。本标准与HG/T2387-1992相比主要变化如下:增加了新的名词,并对原有名词做了进一步的解释;增加了对清洗后钝化膜的检测要求和方法:对特殊条件下奥氏体不锈钢的钝化膜和其它酸洗后的钝化分类检测:增加了垢的分类和清洗质量要求;增加了开车前设备的洗净率简易检验方法:修正了腐蚀率和腐蚀量的部分指标:HG/T2387-2007
对氧、富氧、浓硝酸等强氧化性介质接触的设备表面油含量和检验方法进行了具体规定;在技术要求方面,提出了一般要求和质量要求:对工业设备化学清洗工程质量评定及验收单进行了修订。本标准的附录A是规范性附录,附录B、附录C是资料性附录。本标准由中国石油和化学工业协会提出。本标准由化学工业机械设备标准化技术委员会归口。本标准起草单位:中国蓝(集团)总公司、天华化工机械及自动化研究设计院。本标准主要起草人:陆韶华、陈虹、李彩萍、李德福、张恒录、李嵘、赵智科、刘炀、张建军、张学发。
本标准所代替标准历次发布版本为:HG/T2387-1992。标准分享网一免费标准下载网站bzfxw.comIV
1范围
工业设备化学清洗质量标准
本标准规定了工业设备化学清洗的技术要求,质量指标和试验方法。HG/T2387-2007
本标准适用于碳钢类、不锈钢类、紫铜及铜合金、铝及铝合金等材质的工业设备表面形成的水垢、锈垢、油垢及其它污垢的化学清洗;工业设备的物料垢化学清洗和其它材料制工业设备污垢的化学清洗可参照执行。
2规范性引用文件
下列文件中的条款通过本标准的引用而成为本标准的条款。凡是注日期的引用文件,其随后所有的修改单(不包括勘误的内容)或修订版均不适用于本标准,然而,鼓励根据本标准达成协议的各方研究是否可使用这些文件的最新版本。凡是不注日期的引用文件,其最新版本适用手本标准。GB8978污水综合排放标准
GB8923涂装前钢材表面锈蚀等级和除锈等级DL/T794火力发电厂锅炉化学清洗导则HG/T3523冷却水化学处理标准腐蚀试片技术条件HG20202脱脂工程施工及验收规范JB/T6074腐蚀试样的制备、清洗和评定SH/T3517石油化工钢制管道工程施工工艺标准3术语和定义
以下术语和定义只适合于本标准。3.1化学清洗chemicalcleaning
采用化学药剂及其水溶液与被清洗设备或管线表面污垢发生化学反应而去除污垢的方法。3.2K—腐蚀率corrosion rate
化学药剂及其水溶液与被清洗设备或管线的金属接触时金属被腐蚀的相对速率。腐蚀率可用单位时间内单位面积上的金属腐蚀的质量表示:克每平方米每小时或g/(m·h)。3.3n缓蚀率inhibition efficiency测定缓蚀剂缓蚀性能的参数。
n=未添加缓蚀剂时的金属离蚀率-添加级蚀剂时的金属腐浊率×100%未添加缓蚀剂时的金属腐蚀率
3.4A-腐蚀量corrosionquantity化学清洗过程中,化学药剂及其水溶液与被清洗设备或管线的金属接触时金属单位面积上被腐蚀的质量。腐蚀量单位为:克每平方米(g/m)。3.5N除垢率removingdirtystuffrate被洗除的垢量与清洗前原有垢量之比的百分数(%)。3.6B—洗净率cleaningrate
清洗设备表面经化学清洗后除掉污垢的面积与清洗前原污垢覆盖面积之比的百分数(%)。3.7监视管tubeofwatch
在化学清洗施工时,用来监视清洗过程进展情况和用以测定除垢率的一段管子,这段管子可以从被1
HG/T2387-2007
清洗设备上割取,其上附着污垢应能代表该设备的结垢特点。监视管的取法和要求参照JB/T6074。3.8指定面specifiedsurface
在清洗前由用户方和施工方共同指定设备清洗表面的一部分可见表面,用来测定除垢率或洗净率其上附着污垢应能代表该设备的结垢特点。3.9未指表面unspecifiedsurface设备指定面以外的可见清洗面。3.10视觉清洁visiblyclean
用肉眼观察在要求清洗的视觉范围内,没有可见污垢存在的状态,3.11油含量oilcontent
被清洗金属表面在清洗除油后的残留油量,单位为毫克每平方米或mg/m2。3.12钝化膜passivationmembrane为防止被清洗的金属表面产生二次浮锈,通过化学方法在金属表面形成的一种临时性保护膜,3.13柔性取样框Flexiblesampleframe由柔性材料制作而成的具有规定尺寸的,可用于确定取样面积的框架。4分类
清洗可分为开车前装置的清洗和运行中的设备结垢的清洗,运行中的设备结垢分类见表1表1
运行中设备结垢的分类和定性鉴别垢的分类
CaCO3占60%以上为
碳酸盐垢
CaS04占40%以上为
硫酸盐垢
Si02占20%以上为
硅酸盐垢
氧化铁或铁的氧化
物占80%以上为
含油5%以上为油垢
黄白色或白色
灰白色
棕褐色
鉴别方法
在5%盐酸溶液中,大部分可溶解,同时会产生大量气泡,反应结束后,溶液中不溶物很少在盐酸溶液中很少产生气泡,溶解很少,加入10%氯化钡溶液后,生成大量的白色沉淀物
在盐酸中不溶解,加热后其它成分部分地缓慢溶解,有透明状砂粒沉淀物,加入1%HF可有效溶解加稀盐酸可缓慢溶解,溶液呈黄绿色。加硝酸能较快地溶解,溶液黄色
将垢样研碎,加入乙醚后,溶液呈黄绿色除油可根据要求不同采取分类:直接或可能与氧、富氧、浓硝酸等强氧化性介质接触的设备上的油污必须彻底清除;其它情况的除油作为酸洗的预处理过程。5要求
化学清洗工程在制定施工方案及现场施工时,除应符合本标准外,还应符合设备相关技术条件或规范以及用户方和施工方共同商定的其它技术要求,例如DL/T794、HG20202、各地方或企业污水排放标准等。
5.1一般要求
5.1.1化学清洗前应拆除或隔离能受清洗液损害而影响正常运行的部件和其它配件,无法拆除或隔离者不应产生由于清洗而造成的损伤。拆除后的管件、仪表、阀门等可单独清洗5.1.2化学清洗后设备内的残液、残渣应清除干净。5.1.3设备被清洗结束后,表面应无二次浮锈、无惰性金属置换析出、无金属粗晶析出的过洗现象,应形成完整的钝化膜。
5.1.4在被清洗的设备和管线中,有不锈钢或含有不锈钢的混合材质时,清洗溶液中的氯离子(C1)含量不得大于25mg/L。
HG/T2387-2007
5.1.5在酸洗过程中,溶液中三价铁离子(Fe)含量超过1000mg/L时,可适当加入三价铁离子还原剂或络合剂,以降低三价铁离子的腐蚀。同时在酸洗时,应挂入与清洗系统中所有材质相同的腐蚀监测试片。一次酸洗的时间不应超过12小时。5.1.6在加入钝化药剂前清洗系统内溶液的总铁离子浓度不宜大于350mg/L。5.1.7化学清洗过程中的废液不允许直接排入水体中,应就近纳入当地的污水处理系统。具体指标参照GB8978或当地污水排放标准的规定执行。5.2质量要求
腐蚀率及腐蚀量
在化学清洗过程中,必须控制设备结构材料的腐蚀率和腐蚀量,其指标应不大于表2的规定。表2腐蚀率及腐蚀量指标
设备材料
碳钢类
不锈钢类
铜合金
铝及铝合金
5.2.2除垢率及洗净率
腐蚀率K
g/(m·h)
腐蚀量A
5.2.2.1对于清洗后的金属表面,可用视觉清洁法进行检验,若视觉清洁无残留垢或达到表3的要求即为合格。
5.2.2.2开车前装置的清洗可不考虑除垢率,但洗净率应不小于95%,若用数点法确定洗净率时,100cm的被清洗面上直径为5mm~10mm的残留垢点三次取样平均应不多于1个或5mm以下的残留垢点三次取样平均应不多于3个;运行中的设备结垢后化学清洗的除垢率和洗净率应不小于表3的规定。表3运行中的设备除垢率及洗净率指标质量百分数
污垢类型
碳酸盐垢
硫酸盐垢和硅酸盐垢
其它垢型
除垢率N
洗净率B
注:其它垢型是指除碳酸盐、硫酸盐、硅酸盐、锈垢、油垢以外的其他各类垢型,如:积炭垢、聚合物购、物料垢等
5.2.3油含量
5.2.3.1直接或可能与氧、富氧、浓硝酸等强氧化性介质接触的设备或管线上的油污必须彻底清除,应达到以下任意一种要求。
用波长320nm~380nm的紫外光检查被除油金属表面,应无油脂荧光;a)
用清洁干燥的白色滤纸擦拭被除油金属表面,纸上应无油脂痕迹;HG/T2387-2007
用无油蒸汽吹洗除油金属表面,去其冷凝液,放入一小粒直径不大于1mm的纯樟脑(萘),樟脑粒应不停旋转;
用脱脂棉沾四氯化碳擦拭一定面积的被除油金属表面,测得被除油金属表面油含量应不大于125mg/m:
5.2.3.2作为酸洗的预处理过程除油,只需要达到清洗方案的要求即可。5.2.3.3其它情况下的除油,按除垢率和洗净率指标即表3的要求执行。5.2.4钝化
5.2.4.1对于清洗后碳钢材质的钝化膜质量,用酸性硫酸铜(CuS0)点滴液检验(红点法)。用点滴液点滴钝化表面,点滴液由蓝色变为红色的时间不小于5秒为合格。5.2.4.2对于清洗后有特殊要求的奥氏体不锈钢材质的钝化膜质量,用酸性铁氰化钾(K[Fe(CN).])点滴液检验(蓝点法)。用点滴液点滴钝化表面,点滴液覆盖的面内10分钟内出现的蓝色小点不多于8个点为合格。
6试验方法
6.1腐蚀率及腐蚀量的测定
6.1.1金属腐蚀试片
金属腐蚀试片应符合HG/T3523的规定,处理方法如下:首先将试片用320#水砂纸在平面玻璃板上前后方向打磨,并仔细磨去棱边的小毛刺,然后用丙酮浸泡去掉油污(注意擦洗试片挂孔内污物),用纱布擦干后放入无水乙醇中浸泡1~2分钟,取出后热风吹干放入干燥器中,1小时后将试片称重备用。使用精度为分析天平(称量精确度为土0.0001)分别进行称重,称得重量为Wi:在计算表面积时,用游标卡尺测量其长、宽、厚度,以此计算表面积,测得表面积为S:使用时,将试片置于清洗系统的指定位置,待清洗结束后立即取出用清水淋洗,用滤纸吸去水分,放入无水乙醇中浸泡1~2分钟,取出后快速吹干放置入干燥器中,1小时后用分析天平称重,称得重量为W2:同时记录下清洗时间t。6.1.2腐蚀率及腐蚀量的的计算
式中:K
试片在清洗液中的腐蚀率,单位为克每平方米小时(g/m·h);试片的总表面积,单位为平方米(m);试片在清洗液中浸泡的时间,单位为小时(h);清洗液浸泡前试片的质量,单位为克(g):清洗液浸泡后试片的质量,单位为克(g);试片在清洗液中的腐蚀量,单位为克每平方米,(g/m)。注1:应分别计算三片试片的腐蚀速度,取其中两个数值相近的平均值计算其缓蚀效率。注2:清洗时间t的计算方法是当清洗系统开始加入清洗液直到排尽清洗液止的时间间隔为清洗时间,当试片挂入系统不能随时取出时,终止时间以加入钝化药剂为止计算时间间隔。6.2除垢率的测定
6.2.1视觉清洁法
HG/T 2387-2007
对清洗过的金属表面,通过目测观察除垢情况,若无残留垢或残留垢量目测达到5.2.2的要求,则认为合格,当无法通过视觉清洁法确定除垢率或洗净率时,可用以下相应方法测定。6.2.2容积法:
用蒸馏水和量筒精确测量清洗前后监视管的体积V1、V2,根据已知无垢监视管内径D(或用游标卡尺测量),按式(3)计算污垢监视管的体积Vo,再用式(4)计算除垢率。V
×D2×L
V。-V
式中:N-除垢率,%;
V。-无垢监视管体积,单位为毫升(ml);D-无垢监视管内径,单位为毫米(mm);L-监视管长度,单位为毫米(mm));Vi-清洗前监视管体积,单位为毫升(ml);Vz-清洗后监视管体积,单位为毫升(ml)。6.2.3重量法
取原始监视管一段,干燥后,称得原始监视管重量为M。,将原始监视管段装入清洗系统中,待清洗结束后取出监视管,干燥,称得第一次清洗后的监视管重量为M,同时测量监视管被清洗表面积为S,计算出清洗时的腐蚀量A::
再将第一次清洗后的监视管单独进行清洗,并保证彻底清除其表面污垢,干燥,称得第二次清洗后的监视管重量为M2,同时计算出该次清洗的腐蚀量A2用上述方法重复测定3次,并将每次所得除垢率用算术平均法计算的数值作为除垢率。通过式(5)计算重量法除垢率。
m。-m,- A,× S
mo-m2 -(A,+ A,)× S
式中:N-除垢率,%:wwW.bzxz.Net
m。-原始监视管重量,单位为克(g):?100%
m,-第一次清洗后的监视管重量,单位为克(g);m,-第二次清洗后的监视管重量,单位为克(g);S-无垢监视管被清洗表面积,单位为平方厘米(cm2);Ar-第一次清洗时的腐蚀量,单位为克每平方厘米(g/cm2):A2-第二次清洗时的腐蚀量,单位为克每平方厘米(g/cm2)。6.3洗净率的测定
6.3.1拓印法
当指定面确定后得到污垢覆盖面的面积为S。,清洗结束后,用直角坐标纸和复写纸在指定面上拓印残留污垢面积得S1,按式(6)计算洗净率。B
式中:B-洗净率,%;
So-清洗前指定面中污垢覆盖的面积,单位为厘米(cm2)):?
Si-清洗前指定面经化学清洗后残留污垢的面积,单位为厘米(cm)。注1用上述方法重复3次,并将每次所得清洗率用算术平均法计算的数据作为洗净率注2上述方法多用于运行设备结垢的清洗。6.3.2数点法
HG/T2387-2007
清洗结束后,任选定一被清洗表面,用10cm×10cm柔性取样框(见附录B)框定被清洗表面,然后观察框定面残留垢点的数量和直径,并且取三次计算其算术平均值。6.4油含量的测定
6.4.1擦法
用清洁干燥的白色滤纸在被清洗表面上用力往返擦拭1次,然而用目测滤纸上是否有油脂痕迹。6.4.2紫外光法
将要检查的设备或监视管、指定面、未指定面等被清洗表面置于黑暗处,用波长为320nm~380nm的专用紫外光灯照射被清洗表面,然后观察有无油脂荧光。6.4.3樟脑球法
用无油蒸汽吹洗被清洗金属表面,取其冷凝液,放入一小粒直径不大于1mm的纯樟脑(萘),观察樟脑(萘)是否旋转。
6.4.4四氯化碳法
详见附录A
6.5钝化膜的检测
6.5.1碳钢材质钝化膜的测定(红点法)在钝化后的金属表面,选择3~5个测试点,然后逐点滴上CuSO溶液(该溶液破坏钝化膜后将产生如下反应:Fe+Cu+=Cu++Fe+),并用秒表记录CuSO4点滴溶液由蓝变红的时间,根据蓝色消失全部变为红色的时间快慢来评定钝化膜的质量,根据同一检测面上各点变色时间的长短差别来评定钝化膜的完整性和均匀程度。
完成测定后,测定面应采用滤纸吸干,然后用水磨砂纸除去检验点上的红色痕迹,最后用钝化液擦洗干净。
酸性CuSo4点滴液的组成为:
CuS04·5H20
0.mo1/1HC1
蒸馏水
(分析纯)
(分析纯)
(分析纯)
稀释至100ml。
注:酸性CuS04点滴液的在5℃~35℃下有效使用期限为7天。6.5.2奥氏体不锈钢材质钝化膜的测定(蓝点法)在钝化后的金属表面,任意选择3~5个测试点,用蒸馏水反复冲洗干净,用棉纱擦干,然后逐点滴上酸性铁氰化钾Ks[Fe(CN)。]溶液(该溶液破坏钝化膜后将产生如下反应:2H+Fe=Fe\+H2t:3Fe+2[Fe(CN)]-Fe:[Fe(CN)]2+),并用秒表记录该点滴溶液出现蓝点的时间,根据蓝点出现的时间快慢来评定钝化膜的质量,同一检测面上各点出现蓝点时间的长短评定钝化膜的完整性和均匀程度。测定完后,可用20%的醋酸对测定点擦除,然后用脱盐水或蒸馏水冲洗干净。6
酸性铁氰化钾点滴液的组成为:H2S0(98%)
HC1(36%)
K3[Fe(CN)]
蒸馏水
(分析纯)
(分析纯)
(分析纯)
余量(稀释至100ml)。
HG/T2387-2007
注1:此法适用于对奥氏体不锈钢有特殊要求(强氧化性介质接触的设备)的钝化检测,通常情况下的奥氏体不锈钢清洗可不采用此方法。
注2:酸性铁氰化钾点滴液在5℃~35℃下有效使用期限为7天。注3:铁氧化钾无毒,但在加热时分解产生可能产生剧毒物HCN,所以不能在加热条件下使用。7检验
7.1腐蚀率和腐蚀量
清洗期间腐蚀率和腐蚀量达到5.2.1的要求为合格。7.2除垢率或洗净率
清洗后设备表面除垢率和洗净率达到5.2.2的要求为合格。7.3油含量的检验
7.3.1直接或可能与氧、富氧、浓硝酸等强氧化性介质接触的设备或管线,清洗后被清洗表面油含量达到5.2.3.1或5.2.3.2的要求为合格。7.3.2当清洗设备对清除油污无特别要求时,按5.2.3.3的规定执行7.4钝化膜
清洗后设备表面形成的钝化膜质量达到5.2.4.1或5.2.4.2的要求为合格。7.5特殊要求
当设计规定检验标准时,应按设计规定的标准检验8化学清洗工程交工验收
资料提交
化学清洗工程验收时,施工方应向用户方提交:设备化学清洗方案、施工记录及各种分析化验数据。8.2设备交验
由施工方和用户方质量检验员共同对设备进行化学清洗质量检验,将结果填入《工业设备化学清洗工程质量评定及验收单》(见附录C)。清洗质量符合本标准规定,双方可在表中签字交工。8.3文件归档
待双方完成设备交验后,由施工方负责将设备化学清洗方案、作业计划书、施工原始记录、分析化验数据、《工业设备化学清洗工程质量评定及验收单》及《工业设备化学清洗工程施工总结》等施工资料进行汇总归类,自存入技术档案。7
附录A金属表面油含量分析方法一一四氯化碳法(规范性附录)
A.1油含量分析仪测定法
用四氯化碳擦洗被测表面,采用油含量分析仪检测擦洗液获得残油量。A.1.1
仪器及材料
四氯化碳
中速定量滤纸
油含量分析仪
容量瓶
脱脂棉
A.1.2操作步骤
HG/T2387-2007
将烧杯、容量瓶和镊子用四氯化碳洗净并干燥,取100ml左右四氯化碳于洁净烧杯中,取一团脱脂棉浸于装有四氯化碳的烧杯中,然后用镊子将脱脂棉拧干后,用力擦柔性取样框(祥见附录B)框定面积S(10×10cm=100cm2)的被测金属表面,搽完后将脱脂棉置于装有四氯化碳的烧杯中洗涤,如此反复3~5次后可将框定的金属面油物洗干净,洗涤后的四氯化碳用中速定量滤纸过滤后转移到V=250毫升(m1)容量瓶中,并将脱脂棉和烧杯用四氯化碳洗涤两次,将脱脂棉拧干,洗涤烧杯的四氯化碳溶液也用中速定量滤纸过滤后移到容量瓶并稀释至刻度保存待用。A.1.3结果计算
按照油含量分析仪的说明取一定量含油四氯化碳得读数a,并按照式(7)计算被测金属表面的残油量F
axVx10
式中:F-金属表面油含量,单位为毫克每平方米(mg/m);(7)
V-待测含油四氯化碳溶液的体积(或容量瓶的容积),单位为毫升(ml);S-指定取样的金属表面积(取样框框定的面积),单位为平方厘米(cm):a-含量分析仪读数,单位为毫克每升(mg/L)。A.2油含量重量测定法
A.2.1仪器及材料
四氯化碳
中速定量滤纸
一油含量分析仪
容量瓶
小提示:此标准内容仅展示完整标准里的部分截取内容,若需要完整标准请到上方自行免费下载完整标准文档。
HG/T2387—2007
代替HG/T2387—1992
工业设备化学清洗质量标准
Chemical cleaning quality code for industrial facility2007-09-22发布
2008-04-01实施
中华人民共和国国家发展和改革委员会发布前
工业设备化学清洗质量标准。
2规范性引用文件
3术语和定义
3.1化学清洗
3.2腐蚀率
3.3缓蚀率
3.4腐蚀量
3.5除垢率
3.6洗净率
3.7监视管
3.8指定面
3.9未指表面
3.10视觉清洁
3.11油含量
3.12钝化膜
3.13柔性取样框
4分类..
5要求..
5.1一般要求
5.2质量要求,
6试验方法
6.1腐蚀率及腐蚀量的测定
6.2除垢率的测定.
6.3洗净率的测定.
6.4油含量的测定。
6.5钝化膜的检测,.
7.1腐蚀率和腐蚀量
7.2除垢率或洗净率。
7.3油含量的检验:
7.4钝化膜...
7.5特殊要求,
8化学清洗工程交工验收
8.1资料提交,
8.2设备交验..
8.3文件归档.,
附录A金属表面油含量分析方法一一四氯化碳法A.1油含量分析仪测定法.
A.1.1仪器及材料
A.1.2操作步骤。
A.1.3结果计算
标准分享网一免费标准下载网站bzfxw.comHG/T 2387-2007
A.2油含量重量测定法
A.2.1仪器及材料
A.2.2操作步骤..
A.2.3结果计算
附录B柔性取样框
附录C工业设备化学清洗工程质量评定及验收单标准分享网提示您:非正式出版物仅供参考标准分享网一免费标准下载网站bzfxw.comHG/T 2387-2007
bzfxw.com
本标准代替HG/T2387-1992《工业设备化学清洗质量标准》。本标准与HG/T2387-1992相比主要变化如下:增加了新的名词,并对原有名词做了进一步的解释;增加了对清洗后钝化膜的检测要求和方法:对特殊条件下奥氏体不锈钢的钝化膜和其它酸洗后的钝化分类检测:增加了垢的分类和清洗质量要求;增加了开车前设备的洗净率简易检验方法:修正了腐蚀率和腐蚀量的部分指标:HG/T2387-2007
对氧、富氧、浓硝酸等强氧化性介质接触的设备表面油含量和检验方法进行了具体规定;在技术要求方面,提出了一般要求和质量要求:对工业设备化学清洗工程质量评定及验收单进行了修订。本标准的附录A是规范性附录,附录B、附录C是资料性附录。本标准由中国石油和化学工业协会提出。本标准由化学工业机械设备标准化技术委员会归口。本标准起草单位:中国蓝(集团)总公司、天华化工机械及自动化研究设计院。本标准主要起草人:陆韶华、陈虹、李彩萍、李德福、张恒录、李嵘、赵智科、刘炀、张建军、张学发。
本标准所代替标准历次发布版本为:HG/T2387-1992。标准分享网一免费标准下载网站bzfxw.comIV
1范围
工业设备化学清洗质量标准
本标准规定了工业设备化学清洗的技术要求,质量指标和试验方法。HG/T2387-2007
本标准适用于碳钢类、不锈钢类、紫铜及铜合金、铝及铝合金等材质的工业设备表面形成的水垢、锈垢、油垢及其它污垢的化学清洗;工业设备的物料垢化学清洗和其它材料制工业设备污垢的化学清洗可参照执行。
2规范性引用文件
下列文件中的条款通过本标准的引用而成为本标准的条款。凡是注日期的引用文件,其随后所有的修改单(不包括勘误的内容)或修订版均不适用于本标准,然而,鼓励根据本标准达成协议的各方研究是否可使用这些文件的最新版本。凡是不注日期的引用文件,其最新版本适用手本标准。GB8978污水综合排放标准
GB8923涂装前钢材表面锈蚀等级和除锈等级DL/T794火力发电厂锅炉化学清洗导则HG/T3523冷却水化学处理标准腐蚀试片技术条件HG20202脱脂工程施工及验收规范JB/T6074腐蚀试样的制备、清洗和评定SH/T3517石油化工钢制管道工程施工工艺标准3术语和定义
以下术语和定义只适合于本标准。3.1化学清洗chemicalcleaning
采用化学药剂及其水溶液与被清洗设备或管线表面污垢发生化学反应而去除污垢的方法。3.2K—腐蚀率corrosion rate
化学药剂及其水溶液与被清洗设备或管线的金属接触时金属被腐蚀的相对速率。腐蚀率可用单位时间内单位面积上的金属腐蚀的质量表示:克每平方米每小时或g/(m·h)。3.3n缓蚀率inhibition efficiency测定缓蚀剂缓蚀性能的参数。
n=未添加缓蚀剂时的金属离蚀率-添加级蚀剂时的金属腐浊率×100%未添加缓蚀剂时的金属腐蚀率
3.4A-腐蚀量corrosionquantity化学清洗过程中,化学药剂及其水溶液与被清洗设备或管线的金属接触时金属单位面积上被腐蚀的质量。腐蚀量单位为:克每平方米(g/m)。3.5N除垢率removingdirtystuffrate被洗除的垢量与清洗前原有垢量之比的百分数(%)。3.6B—洗净率cleaningrate
清洗设备表面经化学清洗后除掉污垢的面积与清洗前原污垢覆盖面积之比的百分数(%)。3.7监视管tubeofwatch
在化学清洗施工时,用来监视清洗过程进展情况和用以测定除垢率的一段管子,这段管子可以从被1
HG/T2387-2007
清洗设备上割取,其上附着污垢应能代表该设备的结垢特点。监视管的取法和要求参照JB/T6074。3.8指定面specifiedsurface
在清洗前由用户方和施工方共同指定设备清洗表面的一部分可见表面,用来测定除垢率或洗净率其上附着污垢应能代表该设备的结垢特点。3.9未指表面unspecifiedsurface设备指定面以外的可见清洗面。3.10视觉清洁visiblyclean
用肉眼观察在要求清洗的视觉范围内,没有可见污垢存在的状态,3.11油含量oilcontent
被清洗金属表面在清洗除油后的残留油量,单位为毫克每平方米或mg/m2。3.12钝化膜passivationmembrane为防止被清洗的金属表面产生二次浮锈,通过化学方法在金属表面形成的一种临时性保护膜,3.13柔性取样框Flexiblesampleframe由柔性材料制作而成的具有规定尺寸的,可用于确定取样面积的框架。4分类
清洗可分为开车前装置的清洗和运行中的设备结垢的清洗,运行中的设备结垢分类见表1表1
运行中设备结垢的分类和定性鉴别垢的分类
CaCO3占60%以上为
碳酸盐垢
CaS04占40%以上为
硫酸盐垢
Si02占20%以上为
硅酸盐垢
氧化铁或铁的氧化
物占80%以上为
含油5%以上为油垢
黄白色或白色
灰白色
棕褐色
鉴别方法
在5%盐酸溶液中,大部分可溶解,同时会产生大量气泡,反应结束后,溶液中不溶物很少在盐酸溶液中很少产生气泡,溶解很少,加入10%氯化钡溶液后,生成大量的白色沉淀物
在盐酸中不溶解,加热后其它成分部分地缓慢溶解,有透明状砂粒沉淀物,加入1%HF可有效溶解加稀盐酸可缓慢溶解,溶液呈黄绿色。加硝酸能较快地溶解,溶液黄色
将垢样研碎,加入乙醚后,溶液呈黄绿色除油可根据要求不同采取分类:直接或可能与氧、富氧、浓硝酸等强氧化性介质接触的设备上的油污必须彻底清除;其它情况的除油作为酸洗的预处理过程。5要求
化学清洗工程在制定施工方案及现场施工时,除应符合本标准外,还应符合设备相关技术条件或规范以及用户方和施工方共同商定的其它技术要求,例如DL/T794、HG20202、各地方或企业污水排放标准等。
5.1一般要求
5.1.1化学清洗前应拆除或隔离能受清洗液损害而影响正常运行的部件和其它配件,无法拆除或隔离者不应产生由于清洗而造成的损伤。拆除后的管件、仪表、阀门等可单独清洗5.1.2化学清洗后设备内的残液、残渣应清除干净。5.1.3设备被清洗结束后,表面应无二次浮锈、无惰性金属置换析出、无金属粗晶析出的过洗现象,应形成完整的钝化膜。
5.1.4在被清洗的设备和管线中,有不锈钢或含有不锈钢的混合材质时,清洗溶液中的氯离子(C1)含量不得大于25mg/L。
HG/T2387-2007
5.1.5在酸洗过程中,溶液中三价铁离子(Fe)含量超过1000mg/L时,可适当加入三价铁离子还原剂或络合剂,以降低三价铁离子的腐蚀。同时在酸洗时,应挂入与清洗系统中所有材质相同的腐蚀监测试片。一次酸洗的时间不应超过12小时。5.1.6在加入钝化药剂前清洗系统内溶液的总铁离子浓度不宜大于350mg/L。5.1.7化学清洗过程中的废液不允许直接排入水体中,应就近纳入当地的污水处理系统。具体指标参照GB8978或当地污水排放标准的规定执行。5.2质量要求
腐蚀率及腐蚀量
在化学清洗过程中,必须控制设备结构材料的腐蚀率和腐蚀量,其指标应不大于表2的规定。表2腐蚀率及腐蚀量指标
设备材料
碳钢类
不锈钢类
铜合金
铝及铝合金
5.2.2除垢率及洗净率
腐蚀率K
g/(m·h)
腐蚀量A
5.2.2.1对于清洗后的金属表面,可用视觉清洁法进行检验,若视觉清洁无残留垢或达到表3的要求即为合格。
5.2.2.2开车前装置的清洗可不考虑除垢率,但洗净率应不小于95%,若用数点法确定洗净率时,100cm的被清洗面上直径为5mm~10mm的残留垢点三次取样平均应不多于1个或5mm以下的残留垢点三次取样平均应不多于3个;运行中的设备结垢后化学清洗的除垢率和洗净率应不小于表3的规定。表3运行中的设备除垢率及洗净率指标质量百分数
污垢类型
碳酸盐垢
硫酸盐垢和硅酸盐垢
其它垢型
除垢率N
洗净率B
注:其它垢型是指除碳酸盐、硫酸盐、硅酸盐、锈垢、油垢以外的其他各类垢型,如:积炭垢、聚合物购、物料垢等
5.2.3油含量
5.2.3.1直接或可能与氧、富氧、浓硝酸等强氧化性介质接触的设备或管线上的油污必须彻底清除,应达到以下任意一种要求。
用波长320nm~380nm的紫外光检查被除油金属表面,应无油脂荧光;a)
用清洁干燥的白色滤纸擦拭被除油金属表面,纸上应无油脂痕迹;HG/T2387-2007
用无油蒸汽吹洗除油金属表面,去其冷凝液,放入一小粒直径不大于1mm的纯樟脑(萘),樟脑粒应不停旋转;
用脱脂棉沾四氯化碳擦拭一定面积的被除油金属表面,测得被除油金属表面油含量应不大于125mg/m:
5.2.3.2作为酸洗的预处理过程除油,只需要达到清洗方案的要求即可。5.2.3.3其它情况下的除油,按除垢率和洗净率指标即表3的要求执行。5.2.4钝化
5.2.4.1对于清洗后碳钢材质的钝化膜质量,用酸性硫酸铜(CuS0)点滴液检验(红点法)。用点滴液点滴钝化表面,点滴液由蓝色变为红色的时间不小于5秒为合格。5.2.4.2对于清洗后有特殊要求的奥氏体不锈钢材质的钝化膜质量,用酸性铁氰化钾(K[Fe(CN).])点滴液检验(蓝点法)。用点滴液点滴钝化表面,点滴液覆盖的面内10分钟内出现的蓝色小点不多于8个点为合格。
6试验方法
6.1腐蚀率及腐蚀量的测定
6.1.1金属腐蚀试片
金属腐蚀试片应符合HG/T3523的规定,处理方法如下:首先将试片用320#水砂纸在平面玻璃板上前后方向打磨,并仔细磨去棱边的小毛刺,然后用丙酮浸泡去掉油污(注意擦洗试片挂孔内污物),用纱布擦干后放入无水乙醇中浸泡1~2分钟,取出后热风吹干放入干燥器中,1小时后将试片称重备用。使用精度为分析天平(称量精确度为土0.0001)分别进行称重,称得重量为Wi:在计算表面积时,用游标卡尺测量其长、宽、厚度,以此计算表面积,测得表面积为S:使用时,将试片置于清洗系统的指定位置,待清洗结束后立即取出用清水淋洗,用滤纸吸去水分,放入无水乙醇中浸泡1~2分钟,取出后快速吹干放置入干燥器中,1小时后用分析天平称重,称得重量为W2:同时记录下清洗时间t。6.1.2腐蚀率及腐蚀量的的计算
式中:K
试片在清洗液中的腐蚀率,单位为克每平方米小时(g/m·h);试片的总表面积,单位为平方米(m);试片在清洗液中浸泡的时间,单位为小时(h);清洗液浸泡前试片的质量,单位为克(g):清洗液浸泡后试片的质量,单位为克(g);试片在清洗液中的腐蚀量,单位为克每平方米,(g/m)。注1:应分别计算三片试片的腐蚀速度,取其中两个数值相近的平均值计算其缓蚀效率。注2:清洗时间t的计算方法是当清洗系统开始加入清洗液直到排尽清洗液止的时间间隔为清洗时间,当试片挂入系统不能随时取出时,终止时间以加入钝化药剂为止计算时间间隔。6.2除垢率的测定
6.2.1视觉清洁法
HG/T 2387-2007
对清洗过的金属表面,通过目测观察除垢情况,若无残留垢或残留垢量目测达到5.2.2的要求,则认为合格,当无法通过视觉清洁法确定除垢率或洗净率时,可用以下相应方法测定。6.2.2容积法:
用蒸馏水和量筒精确测量清洗前后监视管的体积V1、V2,根据已知无垢监视管内径D(或用游标卡尺测量),按式(3)计算污垢监视管的体积Vo,再用式(4)计算除垢率。V
×D2×L
V。-V
式中:N-除垢率,%;
V。-无垢监视管体积,单位为毫升(ml);D-无垢监视管内径,单位为毫米(mm);L-监视管长度,单位为毫米(mm));Vi-清洗前监视管体积,单位为毫升(ml);Vz-清洗后监视管体积,单位为毫升(ml)。6.2.3重量法
取原始监视管一段,干燥后,称得原始监视管重量为M。,将原始监视管段装入清洗系统中,待清洗结束后取出监视管,干燥,称得第一次清洗后的监视管重量为M,同时测量监视管被清洗表面积为S,计算出清洗时的腐蚀量A::
再将第一次清洗后的监视管单独进行清洗,并保证彻底清除其表面污垢,干燥,称得第二次清洗后的监视管重量为M2,同时计算出该次清洗的腐蚀量A2用上述方法重复测定3次,并将每次所得除垢率用算术平均法计算的数值作为除垢率。通过式(5)计算重量法除垢率。
m。-m,- A,× S
mo-m2 -(A,+ A,)× S
式中:N-除垢率,%:wwW.bzxz.Net
m。-原始监视管重量,单位为克(g):?100%
m,-第一次清洗后的监视管重量,单位为克(g);m,-第二次清洗后的监视管重量,单位为克(g);S-无垢监视管被清洗表面积,单位为平方厘米(cm2);Ar-第一次清洗时的腐蚀量,单位为克每平方厘米(g/cm2):A2-第二次清洗时的腐蚀量,单位为克每平方厘米(g/cm2)。6.3洗净率的测定
6.3.1拓印法
当指定面确定后得到污垢覆盖面的面积为S。,清洗结束后,用直角坐标纸和复写纸在指定面上拓印残留污垢面积得S1,按式(6)计算洗净率。B
式中:B-洗净率,%;
So-清洗前指定面中污垢覆盖的面积,单位为厘米(cm2)):?
Si-清洗前指定面经化学清洗后残留污垢的面积,单位为厘米(cm)。注1用上述方法重复3次,并将每次所得清洗率用算术平均法计算的数据作为洗净率注2上述方法多用于运行设备结垢的清洗。6.3.2数点法
HG/T2387-2007
清洗结束后,任选定一被清洗表面,用10cm×10cm柔性取样框(见附录B)框定被清洗表面,然后观察框定面残留垢点的数量和直径,并且取三次计算其算术平均值。6.4油含量的测定
6.4.1擦法
用清洁干燥的白色滤纸在被清洗表面上用力往返擦拭1次,然而用目测滤纸上是否有油脂痕迹。6.4.2紫外光法
将要检查的设备或监视管、指定面、未指定面等被清洗表面置于黑暗处,用波长为320nm~380nm的专用紫外光灯照射被清洗表面,然后观察有无油脂荧光。6.4.3樟脑球法
用无油蒸汽吹洗被清洗金属表面,取其冷凝液,放入一小粒直径不大于1mm的纯樟脑(萘),观察樟脑(萘)是否旋转。
6.4.4四氯化碳法
详见附录A
6.5钝化膜的检测
6.5.1碳钢材质钝化膜的测定(红点法)在钝化后的金属表面,选择3~5个测试点,然后逐点滴上CuSO溶液(该溶液破坏钝化膜后将产生如下反应:Fe+Cu+=Cu++Fe+),并用秒表记录CuSO4点滴溶液由蓝变红的时间,根据蓝色消失全部变为红色的时间快慢来评定钝化膜的质量,根据同一检测面上各点变色时间的长短差别来评定钝化膜的完整性和均匀程度。
完成测定后,测定面应采用滤纸吸干,然后用水磨砂纸除去检验点上的红色痕迹,最后用钝化液擦洗干净。
酸性CuSo4点滴液的组成为:
CuS04·5H20
0.mo1/1HC1
蒸馏水
(分析纯)
(分析纯)
(分析纯)
稀释至100ml。
注:酸性CuS04点滴液的在5℃~35℃下有效使用期限为7天。6.5.2奥氏体不锈钢材质钝化膜的测定(蓝点法)在钝化后的金属表面,任意选择3~5个测试点,用蒸馏水反复冲洗干净,用棉纱擦干,然后逐点滴上酸性铁氰化钾Ks[Fe(CN)。]溶液(该溶液破坏钝化膜后将产生如下反应:2H+Fe=Fe\+H2t:3Fe+2[Fe(CN)]-Fe:[Fe(CN)]2+),并用秒表记录该点滴溶液出现蓝点的时间,根据蓝点出现的时间快慢来评定钝化膜的质量,同一检测面上各点出现蓝点时间的长短评定钝化膜的完整性和均匀程度。测定完后,可用20%的醋酸对测定点擦除,然后用脱盐水或蒸馏水冲洗干净。6
酸性铁氰化钾点滴液的组成为:H2S0(98%)
HC1(36%)
K3[Fe(CN)]
蒸馏水
(分析纯)
(分析纯)
(分析纯)
余量(稀释至100ml)。
HG/T2387-2007
注1:此法适用于对奥氏体不锈钢有特殊要求(强氧化性介质接触的设备)的钝化检测,通常情况下的奥氏体不锈钢清洗可不采用此方法。
注2:酸性铁氰化钾点滴液在5℃~35℃下有效使用期限为7天。注3:铁氧化钾无毒,但在加热时分解产生可能产生剧毒物HCN,所以不能在加热条件下使用。7检验
7.1腐蚀率和腐蚀量
清洗期间腐蚀率和腐蚀量达到5.2.1的要求为合格。7.2除垢率或洗净率
清洗后设备表面除垢率和洗净率达到5.2.2的要求为合格。7.3油含量的检验
7.3.1直接或可能与氧、富氧、浓硝酸等强氧化性介质接触的设备或管线,清洗后被清洗表面油含量达到5.2.3.1或5.2.3.2的要求为合格。7.3.2当清洗设备对清除油污无特别要求时,按5.2.3.3的规定执行7.4钝化膜
清洗后设备表面形成的钝化膜质量达到5.2.4.1或5.2.4.2的要求为合格。7.5特殊要求
当设计规定检验标准时,应按设计规定的标准检验8化学清洗工程交工验收
资料提交
化学清洗工程验收时,施工方应向用户方提交:设备化学清洗方案、施工记录及各种分析化验数据。8.2设备交验
由施工方和用户方质量检验员共同对设备进行化学清洗质量检验,将结果填入《工业设备化学清洗工程质量评定及验收单》(见附录C)。清洗质量符合本标准规定,双方可在表中签字交工。8.3文件归档
待双方完成设备交验后,由施工方负责将设备化学清洗方案、作业计划书、施工原始记录、分析化验数据、《工业设备化学清洗工程质量评定及验收单》及《工业设备化学清洗工程施工总结》等施工资料进行汇总归类,自存入技术档案。7
附录A金属表面油含量分析方法一一四氯化碳法(规范性附录)
A.1油含量分析仪测定法
用四氯化碳擦洗被测表面,采用油含量分析仪检测擦洗液获得残油量。A.1.1
仪器及材料
四氯化碳
中速定量滤纸
油含量分析仪
容量瓶
脱脂棉
A.1.2操作步骤
HG/T2387-2007
将烧杯、容量瓶和镊子用四氯化碳洗净并干燥,取100ml左右四氯化碳于洁净烧杯中,取一团脱脂棉浸于装有四氯化碳的烧杯中,然后用镊子将脱脂棉拧干后,用力擦柔性取样框(祥见附录B)框定面积S(10×10cm=100cm2)的被测金属表面,搽完后将脱脂棉置于装有四氯化碳的烧杯中洗涤,如此反复3~5次后可将框定的金属面油物洗干净,洗涤后的四氯化碳用中速定量滤纸过滤后转移到V=250毫升(m1)容量瓶中,并将脱脂棉和烧杯用四氯化碳洗涤两次,将脱脂棉拧干,洗涤烧杯的四氯化碳溶液也用中速定量滤纸过滤后移到容量瓶并稀释至刻度保存待用。A.1.3结果计算
按照油含量分析仪的说明取一定量含油四氯化碳得读数a,并按照式(7)计算被测金属表面的残油量F
axVx10
式中:F-金属表面油含量,单位为毫克每平方米(mg/m);(7)
V-待测含油四氯化碳溶液的体积(或容量瓶的容积),单位为毫升(ml);S-指定取样的金属表面积(取样框框定的面积),单位为平方厘米(cm):a-含量分析仪读数,单位为毫克每升(mg/L)。A.2油含量重量测定法
A.2.1仪器及材料
四氯化碳
中速定量滤纸
一油含量分析仪
容量瓶
小提示:此标准内容仅展示完整标准里的部分截取内容,若需要完整标准请到上方自行免费下载完整标准文档。

标准图片预览:
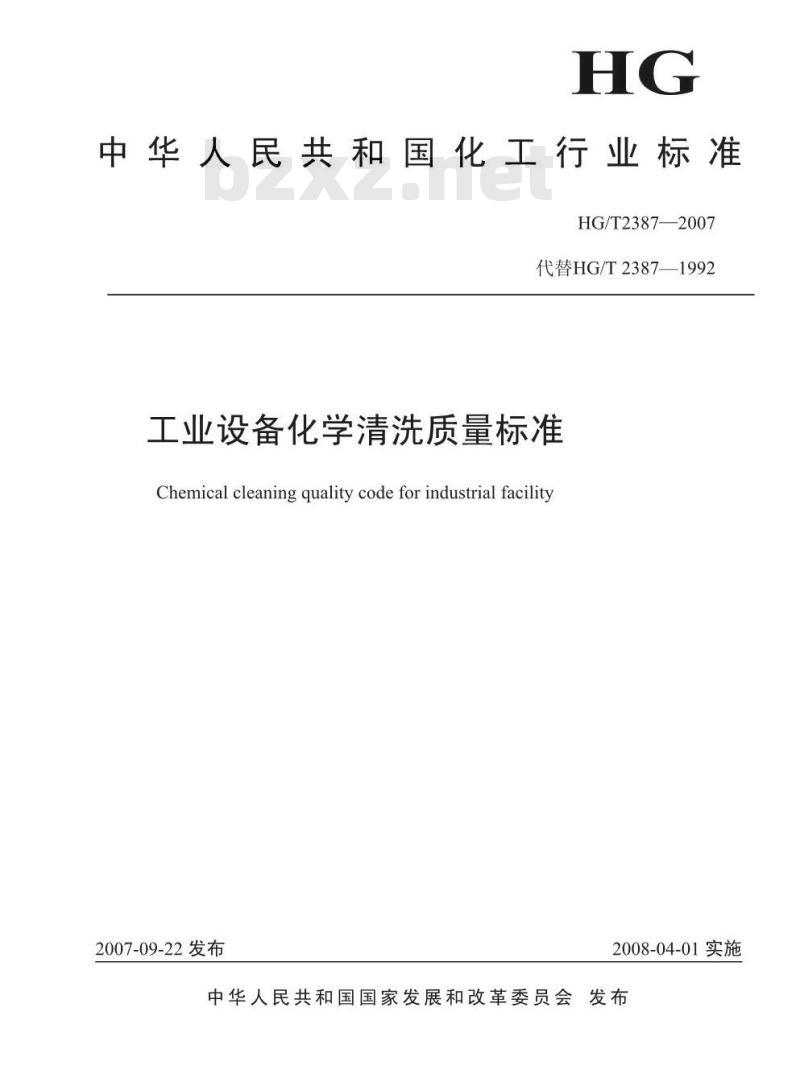
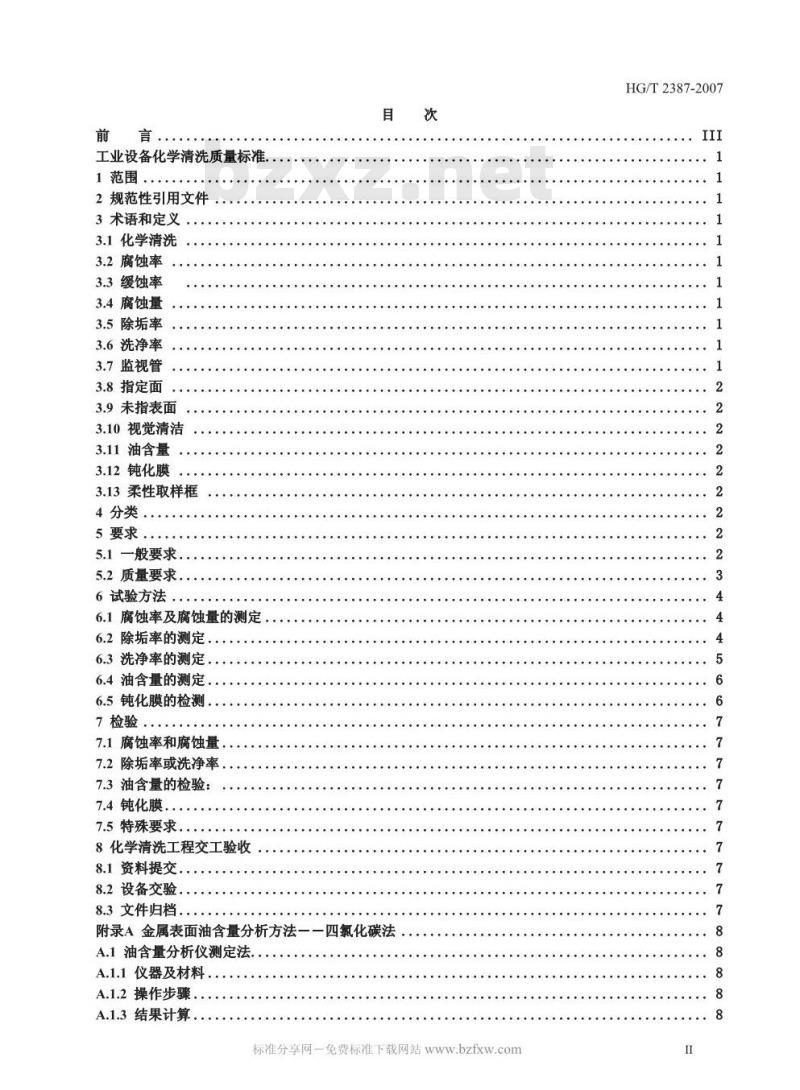
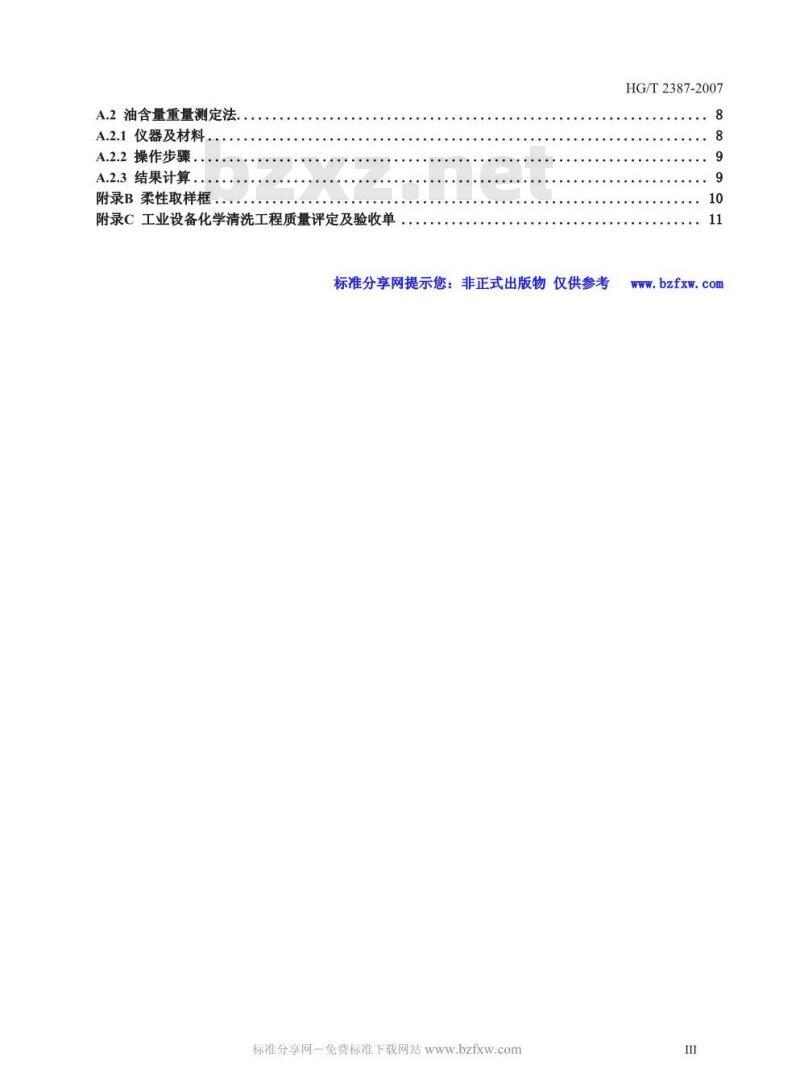
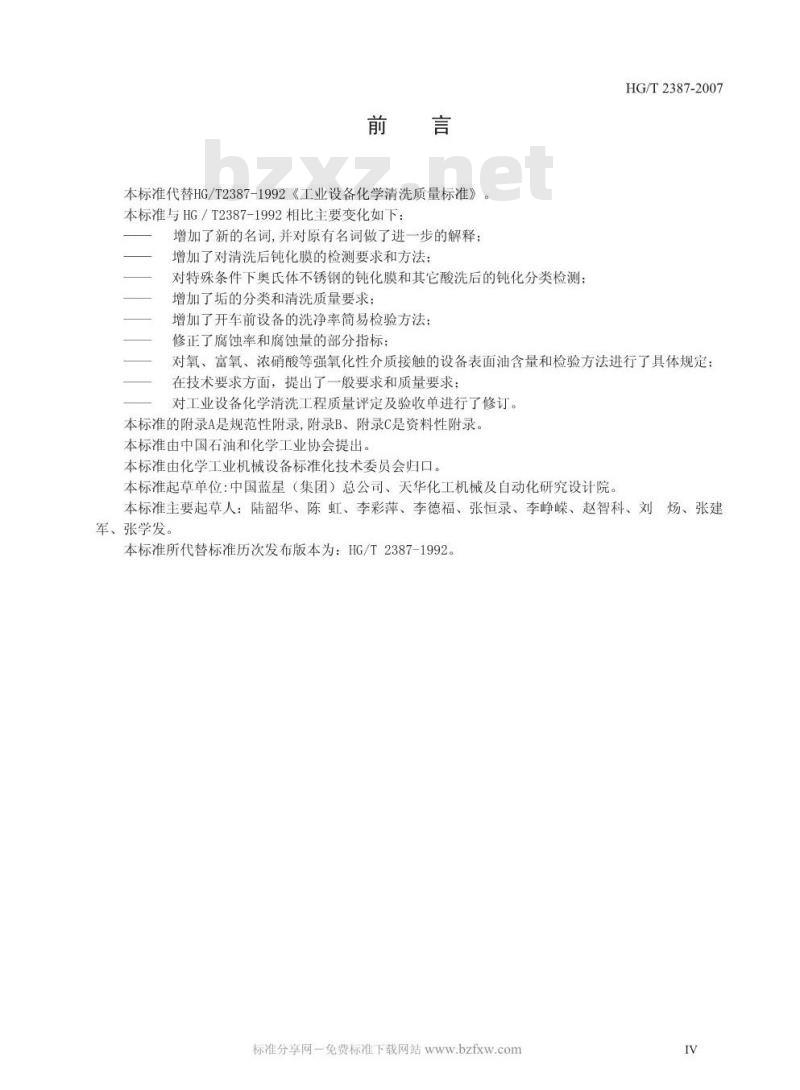
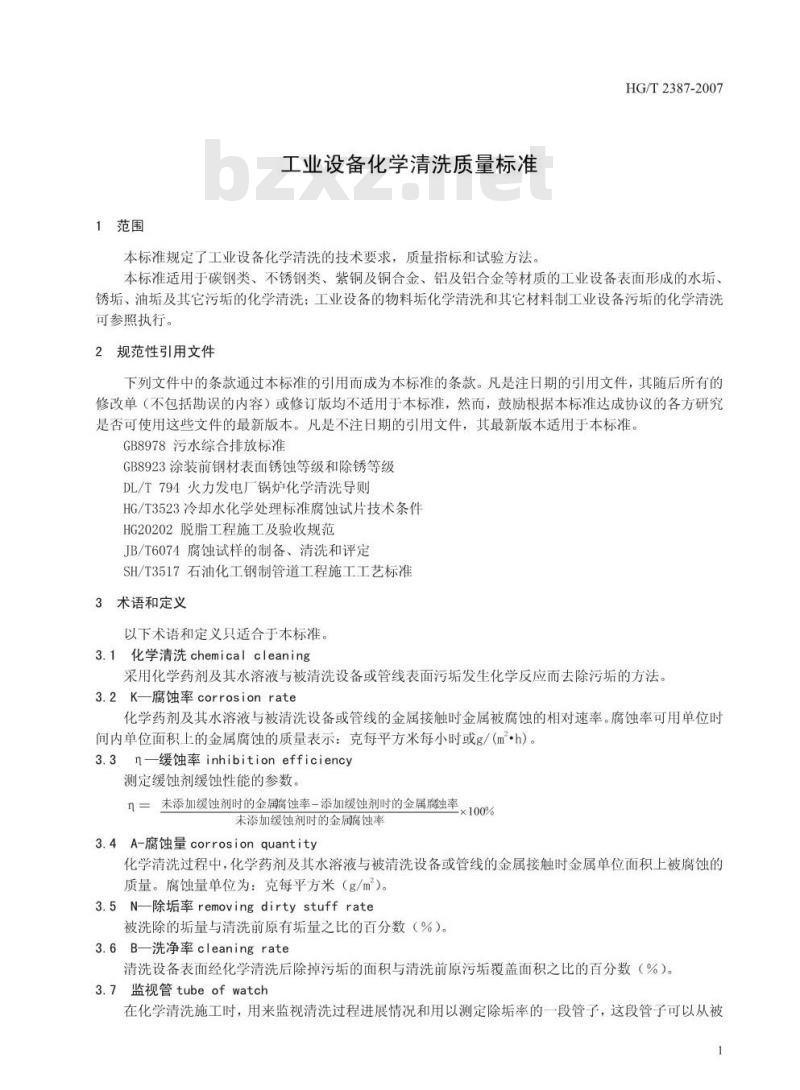
- 热门标准
- 化工行业标准(HG)
- HG/T20592-2009 钢制管法兰(PN系列)
- HG/T4903-2016 动态全硫化热塑性弹性体 (TPV) 三元乙丙橡胶/聚丙烯型
- HG/T2992-198297 直接铜盐蓝2R(原GB/T 1649-1982)
- HG/T5015-2016 含镍废液处理处置方法
- HG/T2129.3-1991 耐酸酚醛塑料制化工设备零部件 凸缘式底筒
- HG/T3148-1985 平底锥顶贮罐系列
- HG/T3069-1999 橡胶配合剂 沉淀水合二氧化硅总锰含量的测定
- HG/T4372-2012 化工用复合材料管及管件
- HG/T20553-2011 代替 HG 20553-1993 化工配管用无缝及焊接钢管尺寸选用系列
- HG/T2821.1-2013 代替 HG/T 2821-2008 V带和多楔带用浸胶聚酯线绳 第1部分:硬线绳
- HG/T2809-2009 代替 HG/T 2809-1996 浮顶油罐软密封装置 橡胶密封带
- HG/T4264-2011 纺织染整助剂 防水防油加工剂 防水性的测定(喷淋法)
- HG/T21596-2014 代替 HG 21596-1999 回转盖衬不锈钢人孔
- HG/T5779-2020 热转印粉末涂料
- HG/T3164-87超 粉碎机械名词术语
请牢记:“bzxz.net”即是“标准下载”四个汉字汉语拼音首字母与国际顶级域名“.net”的组合。 ©2009 标准下载网 www.bzxz.net 本站邮件:bzxznet@163.com
网站备案号:湘ICP备2023016450号-1
网站备案号:湘ICP备2023016450号-1