- 您的位置:
- 标准下载网 >>
- 标准分类 >>
- 机械行业标准(JB) >>
- JB/T 6335.2-2006 摇臂钻床 第2部分:技术条件
标准号:
JB/T 6335.2-2006
标准名称:
摇臂钻床 第2部分:技术条件
标准类别:
机械行业标准(JB)
标准状态:
现行-
发布日期:
2006-08-16 -
实施日期:
2007-02-01 出版语种:
简体中文下载格式:
.rar.pdf下载大小:
3.49 MB
替代情况:
替代JB/T 6335-1992
起草单位:
中捷摇臂钻床厂归口单位:
全国金属切削机床标委会提出单位:
中国机械工业联合会发布部门:
国家发展和改革委员会主管部门:
国家发展和改革委员会相关标签:
技术

点击下载
标准简介:
标准下载解压密码:www.bzxz.net
JB/T 6335的本部分规定了普通摇臂钻床设计、制造和验收的要求。 JB/T 6335.2-2006 摇臂钻床 第2部分:技术条件 JB/T6335.2-2006

部分标准内容:
ICS25.080.40
备案号:18313—2006
中华人民共和国机械行业标准
JB/T6335.2--2006
代替JB/T6335—1992
摇臂钻床
第2部分:技术条件
Radial drilling machine - Part 2: Specifications2006-08-16发布
2007-02-01实施
中华人民共和国国家发展和改革委员会发布前言
规范性引用文件
技术要求.
4检验与验收,
制造厂的保证,
JB/T6335.2—2006
0...00...
JB/T6335《摇臂钻床》拟分为两个部分:-第1部分:型式与参数;
第2部分:技术条件。
本部分是JB/T6335的第2部分。
本部分代替JB/T6335—1992《摇臂钻床技术条件》。本部分与JB/T6335—1992相比,主要变化如下:JB/T6335.2—2006
原版7.2最大进给抗力试验表9中的“机床最大钻孔直径40~50,主轴转速50,改为63”(见本版4.7.3表9);
增加了对电源开关安装位置的要求(见3.3.11);-增加了对包装的要求(见第5章);增加了制造厂的保证(见第6章)。与本部分配套使用的标准有:
GB/T4017-1997摇臂钻床精度检验。本部分由中国机械工业联合会提出。本部分由全国金属切削机床标准化技术委员会(SAC/TC22)归口。本部分起草单位:中捷摇臂钻床厂。本部分主要起草人:郑淑萍、岳毓才。本部分所代替标准的历次版本发布情况:JB/T3062—1982,JB/T6335—1992;-ZBJ54004—1987,JB/T6335—1992。Ⅲ
1范围
摇臂钻床第2部分:技术条件
JB/T6335的本部分规定了普通摇臂钻床设计、制造和验收的要求。本部分适用于最大钻孔直径25mm~125mm的普通摇臂钻床(以下简称机床)。2规范性引用文件
JB/T6335.2—2006
下列文件中的条款通过JB/T6335的本部分的引用而成为本部分的条款。凡是注日期的引用文件,其随后所有的修改单(不包括勘误的内容)或修订版均不适用于本部分,然而,鼓励根据本部分达成协议的各方研究是否可使用这些文件的最新版本。凡是不注日期的引用文件,其最新版本适用于本部分。GB/T4017—1997摇臂钻床精度检验(eqVISO2423:1982)GB5226.1--2002/EC60204-1:2000机械安全机械电气设备第1部分:通用技术条件(IEC60204-1:2000,IDT)
GB/T9061—2006金属切削机床通用技术条件GB15760-2004金属切削机床安全防护通用技术条件GB/T167691997金属切削机床噪声声压级的测量方法JB/T9877—1999金属切削机床清洁度的测定JB/T98721999
JB/T9873-—1997
JB/T9874—1999
金属切削机床机械加工件通用技术条件金属切削机床焊接件通用技术条件金属切削机床装配通用技术条件JB/T10051—1999
金属切削机床液压系统通用技术条件3技术要求
3.1一般要求
本部分是对GB/T9061、JB/T9872、JB/T9874等标准的补充和具体化,按本部分验收机床时应同时对上述标准中未经本部分具体化的其余有关验收项目进行检验。3.2附件和工具
3.2.1为保证机床的基本性能,应随机供应下列附件和工具:a)箱形工作台一件:
b)扁尾锥柄用楔一套:
c)锥柄工具过渡套
一套:
d)机油枪一件;
e)地脚螺栓或地脚塔一套;
f)退刀扳手(对设有手动卸刀孔的机床)一件;g)吊具(对分箱包装的机床)一套。3.2.2为扩大机床的使用性能,可按协议供应特殊附件。3.3安全卫生
3.3.1本部分中未规定的安全防护要求,还应符合GB15760的有关要求。3.3.2运转时不允许变速的机床,应在靠近操纵部位设置警告字样或符号的标示牌。3.3.3摇臂升降的极限位置,应有限位的安全装置。电器、机械限位应可靠。再次操纵摇臂作相反方1
JB/T6335.2—2006
向移动时,机床应能正常工作。3.3.4设有主轴扭矩保险装置的机床,保险装置应可靠。3.3.5在最高转速时,主轴制动停止回转的延迟时间不应超过5s。3.3.6
与外柱接触的摇臂大孔两端处,应设有防尘装置。主轴箱水平移动,限位装置应安全可靠。进给机构应有主轴最大进给抗力超负荷的保险装置。最大钻孔直径大于32mm机床,摇臂升降螺母应有安全装置,以防摇臂自行滑落。当主轴箱、摇臂、外柱处在夹紧状态时,动力或控制信号中断,仍能可靠的夹紧。钻孔直径小于等于50mm的机床电源开关的安装高度不低于0.35m。内柱下部电源壁和摇臂后面电气壁的盖和门在其外面应有带电(高压)警告标记。内柱与外柱、外柱与摇臂,摇臂与主轴箱之间,应用跨接地线连接起来并与接地系统相联。3.3.13
机床其他电气设备应符合GB5226.1的有关规定。下列内容在使用说明书中应予以说明:a)主轴采用弹簧平衡装置的,当拆卸时会引起伤害操作者时;b)机床未固定在地基上时,不应松开内外柱夹紧机构,以防摇臂自由回转造成伤害。3.3.16按GB/T16769的规定检验机床空运转噪声。检验时,摇臂位于机床的纵平面内并靠近立柱下端1/3行程处。主轴箱位于其行程的中间位置。夹紧主轴箱、摇臂、外柱。整机噪声声压级不应超过85dB(A)。3.3.17手轮、手柄操纵力宜符合表1的规定。表1
机床最大钻
孔直径
≥40~50
≥63~80
100~125
主轴箱移
动手轮
主轴移
动手柄
主轴微动
进给手轮
手轮、手柄类别
主轴液压变速手柄
进给结合
子手柄
液压预
选旋钮
正反转
零位!变速
主轴机械变速手柄
正反转
主轴箱夹紧后,在手轮轮缘上施加切向力,主轴箱不应移动,切向力的数值应符合表2的规定。表2
机床最大钻孔直径
切向力
3.4加工和装配质量
摇臂、底座、主轴箱、主轴箱盖为重要铸件,宜在粗加工后进行振动时效、热时效等时效处理。3.4.1
摇臂上导轨面、内外柱滚道面应采取电接触感应淬火或其他耐磨措施。3.4.2
主轴套简外圆柱面应采取氮化或其他耐磨措施。3.4.33
主轴箱与摇臂导轨面、外柱与摇臂大孔导轨面不应焊补。3.4.4
主轴加工质量应符合有关标准的规定。其他未规定的零件加工质量,应符合JB/T9872的有关规3.4.5
JB/T6335.2—2006
3.4.6下列结合面按“重要结合面”要求考核。紧固后用0.04mm塞尺检验,不应插入。用塞尺检验时,允许局部(1处~2处)插人深度小于结合面宽度的1/5,但不应大于5mm。插人部位的长度小于或等于结合面长度的1/5,但不大于100mm则按--处计。a)内柱与底座结合面;
b)主轴导向套凸缘与主轴箱下端结合面;c)主轴箱与其夹紧支架结合面;d)升降体壳与外柱结合面。
3.4.7主轴箱与摇臂导轨副、外柱与摇臂导轨副按“移置导轨”的要求考核。3.4.7.1主轴箱导轨采用刮研,摇臂导轨采用机械加工的机床:a)若主轴箱采用研具作涂色法检验,其接触点数在每25mm×25mm面积内不应少于六个点;b)若采用互研的方法,其接触点数在每25mm×25mm面积内不应少于五个点。3.4.7.2主轴箱与摇臂导轨均为机械加工的机床:a)若采用成套组合检具,分别作涂色法检验,接触面积在长度上为全长的60%,宽度上为全宽的55%;
b)若采用合研的方法时,接触面积在长度上为全长的60%,宽度上为全宽的40%。3.4.7.3主轴箱导轨中间允许留空刀处,其长度不大于全长的1/3。3.4.7.4主轴箱在夹紧状态下,用0.04mm塞尺检验主轴箱与摇臂的间隙,在各条导轨副(包括主轴箱,压板与导轨副的间隙)两端局部插人深度不应大于表3的规定。允许局部(1处~2处)插人,其宽度在12mm以下。
机床最大钻孔直径
80~125
3.4.7.5外柱与摇臂导轨副不作涂色法检查。塞尺局部插人深度
3.4.7.6摇臂夹紧在外柱上,用0.04mm塞尺检验摇臂与外柱的配合间隙,局部插入深度不应大于表3的规定。
外柱及摇臂夹紧后,在摇臂末端施加主轴最大进给抗力的8%的水平力,内外柱不应有相对转3.4.7.7
3.4.7.7.1最大钻孔直径相同的机床,跨距增大时,施力大小与位置按跨距最小的一种检验。3.4.7.7.2对大跨距的机床,不能在摇臂末端测量时,可按能够检测的位置进行折算。3.4.7.7.3主轴箱摇臂分别位于行程中间位置。3.4.7.8主轴箱、摇臂分别位于行程中间位置,外柱松开后,在摇臂末端施加30N的水平力,摇臂应能转动。
3.4.7.9主轴在其行程范围内不应有下沉现象。当向主轴施加主轴组件总重量6%~10%的重力时,主轴不应回升(反弹)。
3.4.8有刻度装置的手轮、手柄反向空程量宜符合表4的规定。表4
机床最大钻孔直径
80~125
3.4.9机床的焊接件应符合JB/T9873等有关标准的规定。空程量
JB/T6335.2-—2006
3.4.10机床的液压系统应符合JB/T10051等标准的有关规定。3.4.11清洁度按JB/T9877规定的方法检验3.4.11.1目测、手感法检测的部位有:a)底座盛冷却液的内腔;
b)摇臂夹紧机构内腔、油池:
c)外柱外表面、键槽;
d)主轴套外表面、齿沟;
e)内柱电源壁毫、摇臂电气壁毫内腔。3.4.11.2重量法检测的部位应符合表5的规定(抽查)。表5
3.4.11.3重量法检测指标
主轴箱(包括进给箱)
升降机构减速箱
液压系统
检测部位
主轴箱内壁及箱内所有零件
减速箱内壁及箱内所有零件
液压油箱
a)从液压系统的每个液压油箱中取油液,在100mL中所含脏物重量不应大于45mgb)主轴箱(包括进给箱)、升降机构减速箱所含脏物重量不应超过表6规定。表6
机床最大钻孔直径
主轴箱部件
升降机构减速箱
3.4.11.4采用润滑脂的主轴箱、升降机构减速箱,不应用重量法进行测定。80~125
3.4.12机床主要零件:主轴箱体、主轴箱盖、主轴、主轴导向套、主轴套筒、主轴花键套、主轴花键套轴承座、摇臂、内柱、外柱、底座。3.4.13主轴进给保险离合器的可靠性用压力计按表7的规定。表7
进给抗力
≤(1+K)F
>(1+K)F~(1.25+K)F
>(1.25+K)F
考核要求
正常工作
允许打滑
必须打滑
注:F为设计规定的最大进给抗力(单位为N),K为系数。4检验与验收
4.1概述
最大钻孔直径
80~125
4.1.1每台机床应在制造厂经检验合格后出厂。某些机床在特殊情况下经用户同意也可在机床使用处4
进行检验。
4.1.2机床的检验与验收一般应包括以下内容:a)外观检验;
b)附件和工具的检验;
c)参数检验;
d)机床的空运转试验;
e)机床的负荷试验;
f)机床的精度检验;
g)机床的安全卫生检验。
4.2一般要求
JB/T6335.2—2006
用地脚螺栓紧固的机床,在检验过程中不应重新调整安装水平。不宜紧固地脚螺栓的机床,负荷试验后可重新调整安装水平。
4.3外观检验下载标准就来标准下载网
按GB/T9061的有关条款及产品设计图样规定检验。4.4附件和工具的检验
按3.2检验随机供应的附件和工具是否符合规定。4.5参数检验(抽查)
按设计规定的主要技术参数检验。4.6机床空运转试验
4.6.1机床空运转试验应符合GB/T90612006中4.6的有关规定。4.6.2机床空运转试验后,下列部位不得漏油。a)水平轴与蜗杆轴下端处:
b)液压预选旋钮处:
c)各油窗、油标及结合口处;
d)变速箱及升降体壳下端轴承座结合处;e)主轴变速操纵杆处。
主传动系统各级转速空载功率(不包括主电动机空载功率)其值宜符合表8的规定。4.6.3
最大钻孔直径
≥40~63
≥80125
主传动系统空载功率/主电动机额定功率%
4.6.4对变型或有特殊要求的摇臂钻床,其空载功率值按设计规定。4.6.5摇臂上升和下降时应平稳,起落时不得有下滑现象。4.6.6液压预选的机床,变换主轴转速和进给量时,操纵变速手柄的次数不应超过两次。4.7机床负荷试验
4.7.1本系列机床应作下列负荷试验:a)最大进给抗力试验;
b)主传动系统最大功率试验;
c)主传动系统扭矩试验。
4.7.2机床负荷试验时,摇臂位于机床的纵平面内并靠近立柱下端1/3行程处。主轴箱位于其行程的中5
JB/T6335.2-2006
间位置。夹紧主轴箱、摇臂、外柱。机床允许紧固在地基上。试验时,机床各部位应正常。4.7.3最大进给抗力试验:
在实心的试件上,用钻孔的方法进行强力切削。试验参数宜符合表9规定。表9
机床最大
钻孔直径
试验类别
钻孔直径D
注:主轴转速n为近似值。
切削条件:
主轴转速n
a)试件材料灰铸铁,190HBS土15HBSb)刀具标准高速钢麻花钻头,2@=118°c)冷却液不加;
d)抗力计算公式:
F~595Ds0.8
式中:
F-切削抗力的主分力,单位为N;Q
一钻孔直径,单位为mm;
进给量,单位为mm/r:
HBS-—试件材料硬度。
进给量S
钻孔深度
钻孔个数
抗力计算值
4.7.3.2最大进给抗力试验,成批生产的机床,可用压力计代替切削,但要有批量的2%,且每批不少于一台进行切削试验。
4.7.3.3非系列机床,按本抗力计算公式自行选定切削参数。4.7.4主传动系统最大功率试验:4.7.4.1在实心的试件上,用钻孔方法进行高速切,试验参数宜符合表10的规定。6
机床最大钻孔直径
切削条件:
钻孔直径
小于机床最大
钻孔直径
切削速度
50~70
a)试件材料灰铸铁,190HBS土15HBS:b)刀具硬质合金麻花钻头;
c)冷却液不加。
进给量
钻孔深度
4.7.4.2成批生产时,以批量的2%,每批不少于一台进行最大功率切削试验。4.7.5主传动系统扭矩试验:
a)主传动系统最大扭矩试验;
b)短时间超过最大扭矩25%试验。JB/T6335.2—2006
钻孔个数
功率测定值
不低于主电动
机额定功率
4.7.5.1在有预钻孔作导向的试件上,用镗孔方法进行强力切削,试验参数宜符合表11的规定。表11
试验类别
镗孔直径D
切削深度t
切削速度√
进给量S
镗孔深度
镗孔个数
扭矩计算值
切削条件:
a)试件材料灰铸铁,190HBS土15HBS:b)刀具硬质合金双刃镗刀板:
c)冷却液宜加:
d)转矩计算公式
号T/3及T
(1.4~2.4)×机床最大钻孔直径(0.08~0.18)D
不低于规定的扭矩值
9550(P-P)
式中:
T主传动系统最大扭矩,单位为N·m;1.25T
..............................(2)
JB/T6335.2--2006
P—切削时电动机的输人功率(指电网输给电动机的功率),单位为kW;Po—机床装有刀具时的空运转功率(指电网输给电动机的功率),单位为kW;一机床主轴转速,单位为/min。4.7.5.2最大扭矩试验,成批生产的机床,在2/3最大扭矩下进行试验,也可用仪器代替切削试验,但要有批量的2%,每批不应少于一台进行最大扭矩和超最大扭矩25%和切削试验。4.8机床精度检验
机床精度检验按GB/T4017检验。4.9机床安全卫生
机床安全卫生的检验应符合3.3的规定。5包装
5.1机床的包装应符合包装设计图样及文件的规定。5.2分箱包装的机床应符合装箱单中规定的内容。5.3出厂文件应包括使用说明书、合格证明书、装箱单等。6制造厂的保证
在符合机床的运输、保管、安装、调试、维修和遵守使用规程的条件下,用户自收货之日起一年内,因设计、制造包装质量不良等原因造成机床损坏或其不能正常使用时,制造厂应负责包修、包退、包换。8
小提示:此标准内容仅展示完整标准里的部分截取内容,若需要完整标准请到上方自行免费下载完整标准文档。
备案号:18313—2006
中华人民共和国机械行业标准
JB/T6335.2--2006
代替JB/T6335—1992
摇臂钻床
第2部分:技术条件
Radial drilling machine - Part 2: Specifications2006-08-16发布
2007-02-01实施
中华人民共和国国家发展和改革委员会发布前言
规范性引用文件
技术要求.
4检验与验收,
制造厂的保证,
JB/T6335.2—2006
0...00...
JB/T6335《摇臂钻床》拟分为两个部分:-第1部分:型式与参数;
第2部分:技术条件。
本部分是JB/T6335的第2部分。
本部分代替JB/T6335—1992《摇臂钻床技术条件》。本部分与JB/T6335—1992相比,主要变化如下:JB/T6335.2—2006
原版7.2最大进给抗力试验表9中的“机床最大钻孔直径40~50,主轴转速50,改为63”(见本版4.7.3表9);
增加了对电源开关安装位置的要求(见3.3.11);-增加了对包装的要求(见第5章);增加了制造厂的保证(见第6章)。与本部分配套使用的标准有:
GB/T4017-1997摇臂钻床精度检验。本部分由中国机械工业联合会提出。本部分由全国金属切削机床标准化技术委员会(SAC/TC22)归口。本部分起草单位:中捷摇臂钻床厂。本部分主要起草人:郑淑萍、岳毓才。本部分所代替标准的历次版本发布情况:JB/T3062—1982,JB/T6335—1992;-ZBJ54004—1987,JB/T6335—1992。Ⅲ
1范围
摇臂钻床第2部分:技术条件
JB/T6335的本部分规定了普通摇臂钻床设计、制造和验收的要求。本部分适用于最大钻孔直径25mm~125mm的普通摇臂钻床(以下简称机床)。2规范性引用文件
JB/T6335.2—2006
下列文件中的条款通过JB/T6335的本部分的引用而成为本部分的条款。凡是注日期的引用文件,其随后所有的修改单(不包括勘误的内容)或修订版均不适用于本部分,然而,鼓励根据本部分达成协议的各方研究是否可使用这些文件的最新版本。凡是不注日期的引用文件,其最新版本适用于本部分。GB/T4017—1997摇臂钻床精度检验(eqVISO2423:1982)GB5226.1--2002/EC60204-1:2000机械安全机械电气设备第1部分:通用技术条件(IEC60204-1:2000,IDT)
GB/T9061—2006金属切削机床通用技术条件GB15760-2004金属切削机床安全防护通用技术条件GB/T167691997金属切削机床噪声声压级的测量方法JB/T9877—1999金属切削机床清洁度的测定JB/T98721999
JB/T9873-—1997
JB/T9874—1999
金属切削机床机械加工件通用技术条件金属切削机床焊接件通用技术条件金属切削机床装配通用技术条件JB/T10051—1999
金属切削机床液压系统通用技术条件3技术要求
3.1一般要求
本部分是对GB/T9061、JB/T9872、JB/T9874等标准的补充和具体化,按本部分验收机床时应同时对上述标准中未经本部分具体化的其余有关验收项目进行检验。3.2附件和工具
3.2.1为保证机床的基本性能,应随机供应下列附件和工具:a)箱形工作台一件:
b)扁尾锥柄用楔一套:
c)锥柄工具过渡套
一套:
d)机油枪一件;
e)地脚螺栓或地脚塔一套;
f)退刀扳手(对设有手动卸刀孔的机床)一件;g)吊具(对分箱包装的机床)一套。3.2.2为扩大机床的使用性能,可按协议供应特殊附件。3.3安全卫生
3.3.1本部分中未规定的安全防护要求,还应符合GB15760的有关要求。3.3.2运转时不允许变速的机床,应在靠近操纵部位设置警告字样或符号的标示牌。3.3.3摇臂升降的极限位置,应有限位的安全装置。电器、机械限位应可靠。再次操纵摇臂作相反方1
JB/T6335.2—2006
向移动时,机床应能正常工作。3.3.4设有主轴扭矩保险装置的机床,保险装置应可靠。3.3.5在最高转速时,主轴制动停止回转的延迟时间不应超过5s。3.3.6
与外柱接触的摇臂大孔两端处,应设有防尘装置。主轴箱水平移动,限位装置应安全可靠。进给机构应有主轴最大进给抗力超负荷的保险装置。最大钻孔直径大于32mm机床,摇臂升降螺母应有安全装置,以防摇臂自行滑落。当主轴箱、摇臂、外柱处在夹紧状态时,动力或控制信号中断,仍能可靠的夹紧。钻孔直径小于等于50mm的机床电源开关的安装高度不低于0.35m。内柱下部电源壁和摇臂后面电气壁的盖和门在其外面应有带电(高压)警告标记。内柱与外柱、外柱与摇臂,摇臂与主轴箱之间,应用跨接地线连接起来并与接地系统相联。3.3.13
机床其他电气设备应符合GB5226.1的有关规定。下列内容在使用说明书中应予以说明:a)主轴采用弹簧平衡装置的,当拆卸时会引起伤害操作者时;b)机床未固定在地基上时,不应松开内外柱夹紧机构,以防摇臂自由回转造成伤害。3.3.16按GB/T16769的规定检验机床空运转噪声。检验时,摇臂位于机床的纵平面内并靠近立柱下端1/3行程处。主轴箱位于其行程的中间位置。夹紧主轴箱、摇臂、外柱。整机噪声声压级不应超过85dB(A)。3.3.17手轮、手柄操纵力宜符合表1的规定。表1
机床最大钻
孔直径
≥40~50
≥63~80
100~125
主轴箱移
动手轮
主轴移
动手柄
主轴微动
进给手轮
手轮、手柄类别
主轴液压变速手柄
进给结合
子手柄
液压预
选旋钮
正反转
零位!变速
主轴机械变速手柄
正反转
主轴箱夹紧后,在手轮轮缘上施加切向力,主轴箱不应移动,切向力的数值应符合表2的规定。表2
机床最大钻孔直径
切向力
3.4加工和装配质量
摇臂、底座、主轴箱、主轴箱盖为重要铸件,宜在粗加工后进行振动时效、热时效等时效处理。3.4.1
摇臂上导轨面、内外柱滚道面应采取电接触感应淬火或其他耐磨措施。3.4.2
主轴套简外圆柱面应采取氮化或其他耐磨措施。3.4.33
主轴箱与摇臂导轨面、外柱与摇臂大孔导轨面不应焊补。3.4.4
主轴加工质量应符合有关标准的规定。其他未规定的零件加工质量,应符合JB/T9872的有关规3.4.5
JB/T6335.2—2006
3.4.6下列结合面按“重要结合面”要求考核。紧固后用0.04mm塞尺检验,不应插入。用塞尺检验时,允许局部(1处~2处)插人深度小于结合面宽度的1/5,但不应大于5mm。插人部位的长度小于或等于结合面长度的1/5,但不大于100mm则按--处计。a)内柱与底座结合面;
b)主轴导向套凸缘与主轴箱下端结合面;c)主轴箱与其夹紧支架结合面;d)升降体壳与外柱结合面。
3.4.7主轴箱与摇臂导轨副、外柱与摇臂导轨副按“移置导轨”的要求考核。3.4.7.1主轴箱导轨采用刮研,摇臂导轨采用机械加工的机床:a)若主轴箱采用研具作涂色法检验,其接触点数在每25mm×25mm面积内不应少于六个点;b)若采用互研的方法,其接触点数在每25mm×25mm面积内不应少于五个点。3.4.7.2主轴箱与摇臂导轨均为机械加工的机床:a)若采用成套组合检具,分别作涂色法检验,接触面积在长度上为全长的60%,宽度上为全宽的55%;
b)若采用合研的方法时,接触面积在长度上为全长的60%,宽度上为全宽的40%。3.4.7.3主轴箱导轨中间允许留空刀处,其长度不大于全长的1/3。3.4.7.4主轴箱在夹紧状态下,用0.04mm塞尺检验主轴箱与摇臂的间隙,在各条导轨副(包括主轴箱,压板与导轨副的间隙)两端局部插人深度不应大于表3的规定。允许局部(1处~2处)插人,其宽度在12mm以下。
机床最大钻孔直径
80~125
3.4.7.5外柱与摇臂导轨副不作涂色法检查。塞尺局部插人深度
3.4.7.6摇臂夹紧在外柱上,用0.04mm塞尺检验摇臂与外柱的配合间隙,局部插入深度不应大于表3的规定。
外柱及摇臂夹紧后,在摇臂末端施加主轴最大进给抗力的8%的水平力,内外柱不应有相对转3.4.7.7
3.4.7.7.1最大钻孔直径相同的机床,跨距增大时,施力大小与位置按跨距最小的一种检验。3.4.7.7.2对大跨距的机床,不能在摇臂末端测量时,可按能够检测的位置进行折算。3.4.7.7.3主轴箱摇臂分别位于行程中间位置。3.4.7.8主轴箱、摇臂分别位于行程中间位置,外柱松开后,在摇臂末端施加30N的水平力,摇臂应能转动。
3.4.7.9主轴在其行程范围内不应有下沉现象。当向主轴施加主轴组件总重量6%~10%的重力时,主轴不应回升(反弹)。
3.4.8有刻度装置的手轮、手柄反向空程量宜符合表4的规定。表4
机床最大钻孔直径
80~125
3.4.9机床的焊接件应符合JB/T9873等有关标准的规定。空程量
JB/T6335.2-—2006
3.4.10机床的液压系统应符合JB/T10051等标准的有关规定。3.4.11清洁度按JB/T9877规定的方法检验3.4.11.1目测、手感法检测的部位有:a)底座盛冷却液的内腔;
b)摇臂夹紧机构内腔、油池:
c)外柱外表面、键槽;
d)主轴套外表面、齿沟;
e)内柱电源壁毫、摇臂电气壁毫内腔。3.4.11.2重量法检测的部位应符合表5的规定(抽查)。表5
3.4.11.3重量法检测指标
主轴箱(包括进给箱)
升降机构减速箱
液压系统
检测部位
主轴箱内壁及箱内所有零件
减速箱内壁及箱内所有零件
液压油箱
a)从液压系统的每个液压油箱中取油液,在100mL中所含脏物重量不应大于45mgb)主轴箱(包括进给箱)、升降机构减速箱所含脏物重量不应超过表6规定。表6
机床最大钻孔直径
主轴箱部件
升降机构减速箱
3.4.11.4采用润滑脂的主轴箱、升降机构减速箱,不应用重量法进行测定。80~125
3.4.12机床主要零件:主轴箱体、主轴箱盖、主轴、主轴导向套、主轴套筒、主轴花键套、主轴花键套轴承座、摇臂、内柱、外柱、底座。3.4.13主轴进给保险离合器的可靠性用压力计按表7的规定。表7
进给抗力
≤(1+K)F
>(1+K)F~(1.25+K)F
>(1.25+K)F
考核要求
正常工作
允许打滑
必须打滑
注:F为设计规定的最大进给抗力(单位为N),K为系数。4检验与验收
4.1概述
最大钻孔直径
80~125
4.1.1每台机床应在制造厂经检验合格后出厂。某些机床在特殊情况下经用户同意也可在机床使用处4
进行检验。
4.1.2机床的检验与验收一般应包括以下内容:a)外观检验;
b)附件和工具的检验;
c)参数检验;
d)机床的空运转试验;
e)机床的负荷试验;
f)机床的精度检验;
g)机床的安全卫生检验。
4.2一般要求
JB/T6335.2—2006
用地脚螺栓紧固的机床,在检验过程中不应重新调整安装水平。不宜紧固地脚螺栓的机床,负荷试验后可重新调整安装水平。
4.3外观检验下载标准就来标准下载网
按GB/T9061的有关条款及产品设计图样规定检验。4.4附件和工具的检验
按3.2检验随机供应的附件和工具是否符合规定。4.5参数检验(抽查)
按设计规定的主要技术参数检验。4.6机床空运转试验
4.6.1机床空运转试验应符合GB/T90612006中4.6的有关规定。4.6.2机床空运转试验后,下列部位不得漏油。a)水平轴与蜗杆轴下端处:
b)液压预选旋钮处:
c)各油窗、油标及结合口处;
d)变速箱及升降体壳下端轴承座结合处;e)主轴变速操纵杆处。
主传动系统各级转速空载功率(不包括主电动机空载功率)其值宜符合表8的规定。4.6.3
最大钻孔直径
≥40~63
≥80125
主传动系统空载功率/主电动机额定功率%
4.6.4对变型或有特殊要求的摇臂钻床,其空载功率值按设计规定。4.6.5摇臂上升和下降时应平稳,起落时不得有下滑现象。4.6.6液压预选的机床,变换主轴转速和进给量时,操纵变速手柄的次数不应超过两次。4.7机床负荷试验
4.7.1本系列机床应作下列负荷试验:a)最大进给抗力试验;
b)主传动系统最大功率试验;
c)主传动系统扭矩试验。
4.7.2机床负荷试验时,摇臂位于机床的纵平面内并靠近立柱下端1/3行程处。主轴箱位于其行程的中5
JB/T6335.2-2006
间位置。夹紧主轴箱、摇臂、外柱。机床允许紧固在地基上。试验时,机床各部位应正常。4.7.3最大进给抗力试验:
在实心的试件上,用钻孔的方法进行强力切削。试验参数宜符合表9规定。表9
机床最大
钻孔直径
试验类别
钻孔直径D
注:主轴转速n为近似值。
切削条件:
主轴转速n
a)试件材料灰铸铁,190HBS土15HBSb)刀具标准高速钢麻花钻头,2@=118°c)冷却液不加;
d)抗力计算公式:
F~595Ds0.8
式中:
F-切削抗力的主分力,单位为N;Q
一钻孔直径,单位为mm;
进给量,单位为mm/r:
HBS-—试件材料硬度。
进给量S
钻孔深度
钻孔个数
抗力计算值
4.7.3.2最大进给抗力试验,成批生产的机床,可用压力计代替切削,但要有批量的2%,且每批不少于一台进行切削试验。
4.7.3.3非系列机床,按本抗力计算公式自行选定切削参数。4.7.4主传动系统最大功率试验:4.7.4.1在实心的试件上,用钻孔方法进行高速切,试验参数宜符合表10的规定。6
机床最大钻孔直径
切削条件:
钻孔直径
小于机床最大
钻孔直径
切削速度
50~70
a)试件材料灰铸铁,190HBS土15HBS:b)刀具硬质合金麻花钻头;
c)冷却液不加。
进给量
钻孔深度
4.7.4.2成批生产时,以批量的2%,每批不少于一台进行最大功率切削试验。4.7.5主传动系统扭矩试验:
a)主传动系统最大扭矩试验;
b)短时间超过最大扭矩25%试验。JB/T6335.2—2006
钻孔个数
功率测定值
不低于主电动
机额定功率
4.7.5.1在有预钻孔作导向的试件上,用镗孔方法进行强力切削,试验参数宜符合表11的规定。表11
试验类别
镗孔直径D
切削深度t
切削速度√
进给量S
镗孔深度
镗孔个数
扭矩计算值
切削条件:
a)试件材料灰铸铁,190HBS土15HBS:b)刀具硬质合金双刃镗刀板:
c)冷却液宜加:
d)转矩计算公式
号T/3及T
(1.4~2.4)×机床最大钻孔直径(0.08~0.18)D
不低于规定的扭矩值
9550(P-P)
式中:
T主传动系统最大扭矩,单位为N·m;1.25T
..............................(2)
JB/T6335.2--2006
P—切削时电动机的输人功率(指电网输给电动机的功率),单位为kW;Po—机床装有刀具时的空运转功率(指电网输给电动机的功率),单位为kW;一机床主轴转速,单位为/min。4.7.5.2最大扭矩试验,成批生产的机床,在2/3最大扭矩下进行试验,也可用仪器代替切削试验,但要有批量的2%,每批不应少于一台进行最大扭矩和超最大扭矩25%和切削试验。4.8机床精度检验
机床精度检验按GB/T4017检验。4.9机床安全卫生
机床安全卫生的检验应符合3.3的规定。5包装
5.1机床的包装应符合包装设计图样及文件的规定。5.2分箱包装的机床应符合装箱单中规定的内容。5.3出厂文件应包括使用说明书、合格证明书、装箱单等。6制造厂的保证
在符合机床的运输、保管、安装、调试、维修和遵守使用规程的条件下,用户自收货之日起一年内,因设计、制造包装质量不良等原因造成机床损坏或其不能正常使用时,制造厂应负责包修、包退、包换。8
小提示:此标准内容仅展示完整标准里的部分截取内容,若需要完整标准请到上方自行免费下载完整标准文档。

标准图片预览:
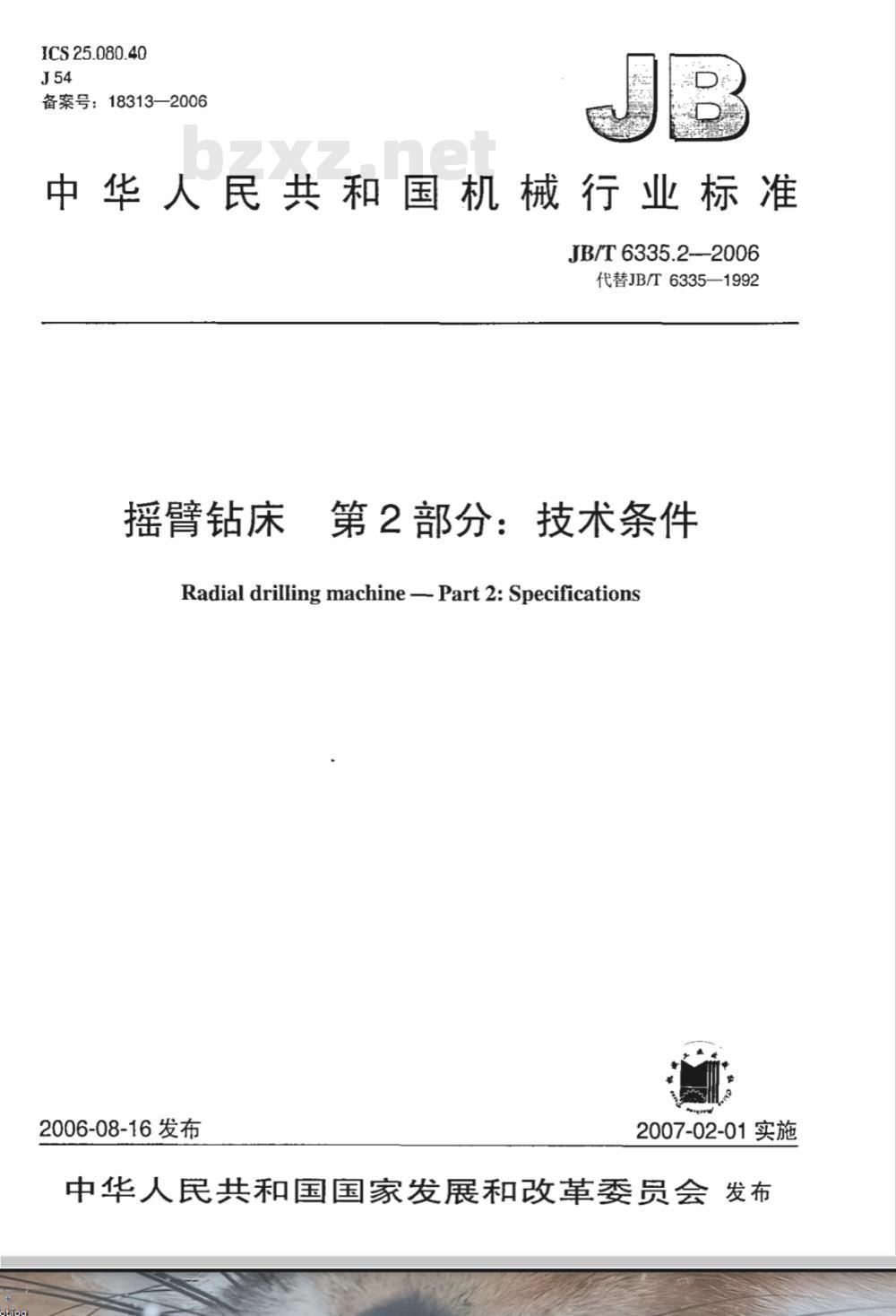
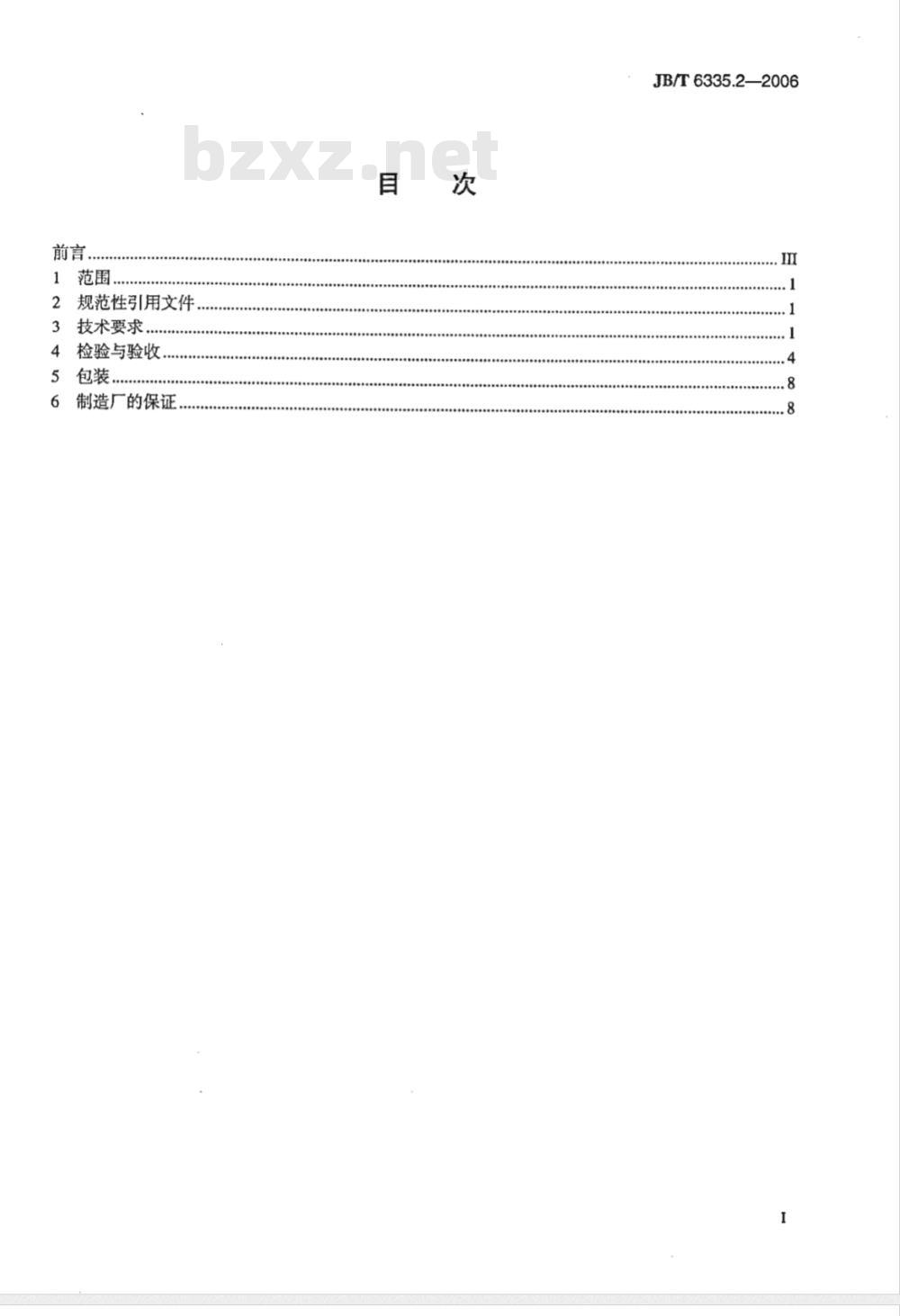
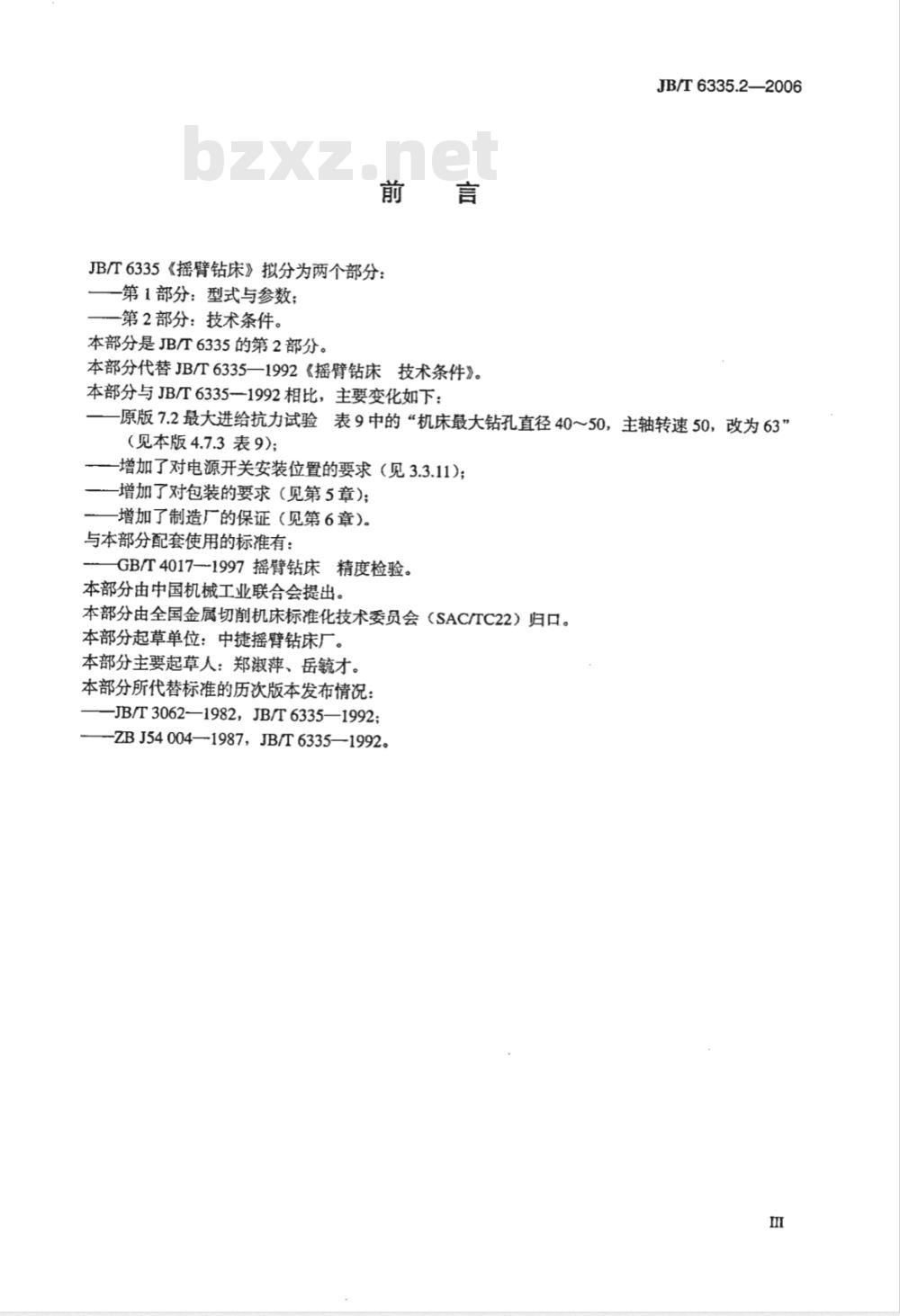
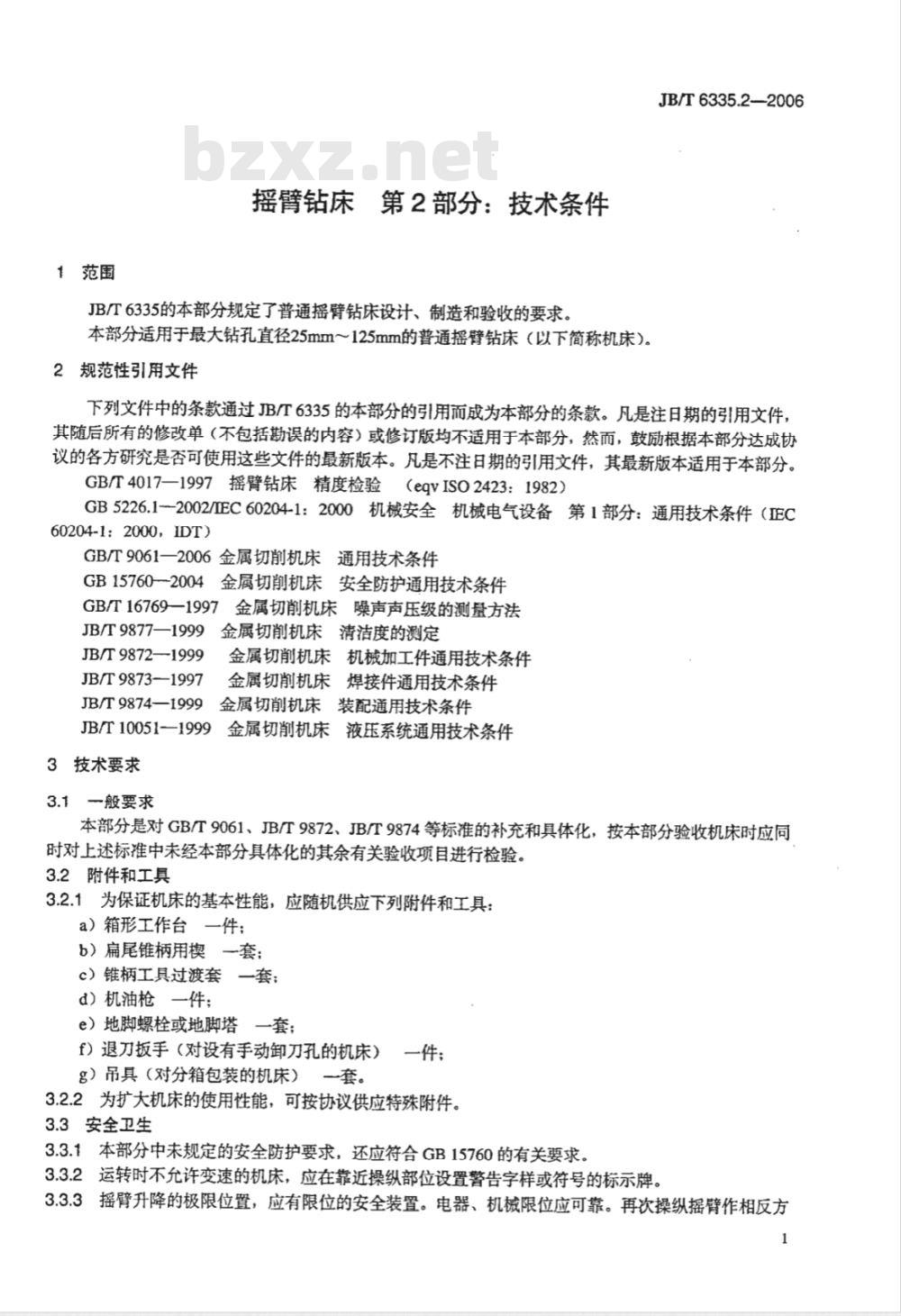
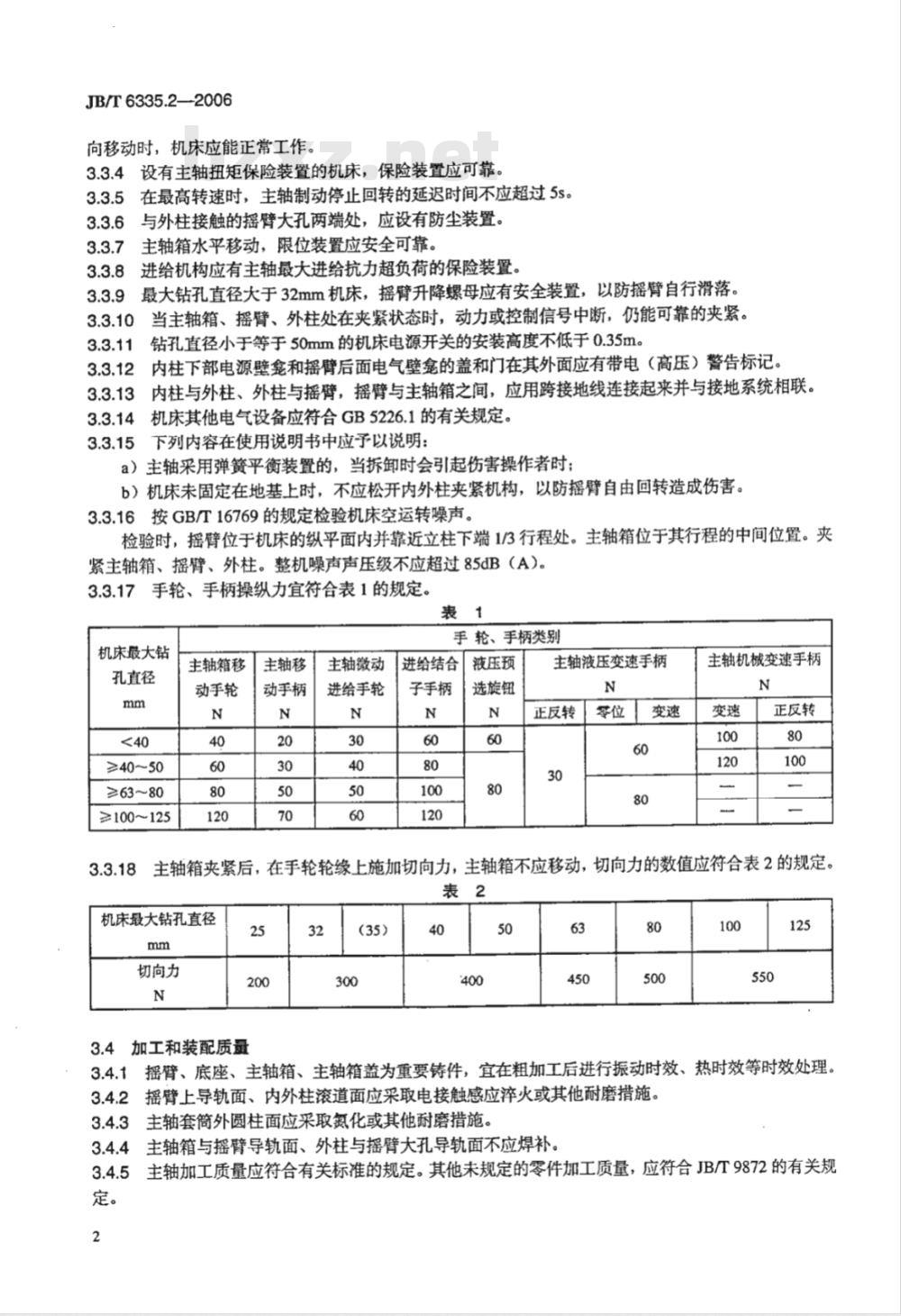
- 其它标准
- 热门标准
- 机械行业标准(JB)
- JB/T10725-2007 天然金刚石车刀
- JB/T10723-2007 焊接聚晶金刚石或立方氮化硼镗刀
- JB/T10565-2006 工业过程测量和控制系统用动圈式指示仪性能评定方法
- JB/T10767-2007 装载机铜基湿式粉末冶金摩擦片 技术条件
- JB8589-1997 DZ 20系列塑料外壳式断路器
- JB/DQ1545.8-1989 英制紧固件 半圆头螺栓
- JB/GQOE14-1988 熔模铸钢ZG310-570正大组织金相检验
- JB/T8704-2012 蜂窝式电除焦油器
- JB/T2361-1992 恒压刷握
- JB3228-1983 闭式机械压力机 紧固模具用槽打(顶)杆孔的分布形式与尺寸
- JB/T6237.8-2008 电触头材料用银粉化学分析方法 第8部分:银粉水溶液pH值测定
- JB/T6220-2011 无损检测仪器 射线探伤用密度计
- JB/T9220.3-1999 铸造化铁炉酸性炉渣化学分析方法 重铬酸钾容量法测定氧化亚铁量
- JB/T4015.6-1999 电缆设备通用部件 收放线装置 第6部分:静盘放线装置
- JB/T10782.2-2007 闭式双动拉伸多连杆压力机 第2部分:精度
- 行业新闻
请牢记:“bzxz.net”即是“标准下载”四个汉字汉语拼音首字母与国际顶级域名“.net”的组合。 ©2009 标准下载网 www.bzxz.net 本站邮件:bzxznet@163.com
网站备案号:湘ICP备2023016450号-1
网站备案号:湘ICP备2023016450号-1