- 您的位置:
- 标准下载网 >>
- 标准分类 >>
- 轻工行业标准(QB) >>
- QB 6008-1995 真空制盐厂设计规范
标准号:
QB 6008-1995
标准名称:
真空制盐厂设计规范
标准类别:
轻工行业标准(QB)
标准状态:
已作废-
实施日期:
1995-01-01 出版语种:
简体中文下载格式:
.rar.pdf下载大小:
2.25 MB

部分标准内容:
1总则
中华人民共和国轻工行业标准
真空制盐厂设计规范
QB6008—1995
1.1真空制盐厂设计,必须认贵彻执行国家有关科学技术发展和工程建设的方针、政策,紧密结合我国国情,从全局出发·做到划合实际,技术先进,安全适用,节约能源,保护环境,提高效益。1.2本规范适用于建设规模为3~60万吨/年规模的真空制盐厂工程设计(包括副产品硫酸钠,不包含矿区、牛活区及综合利用下程)。扩建、收建及技术改造项目的设计亦可适用。1.3设计原则
a。真空制盐厂设计,应根据已批准的有美文件要求,搞好工厂的总体规划,做到近期为主,适当考虑发展的可能。改建、扩建工程,应充分挖掘潜力,合理利原有设施:b,应积极采用可靠的,经过实践证明有经济效益,社会效益、环境效益的新技术:C.采用的工艺,设备要力求技术先逊,各项技术经济指标达到或超过国内先进水平;机械化和自动化水平应符合国情,逐步提高。1.4真空制盐厂设计:除应符合本规定外尚应符合国家现行有关法规,标准,规范的规定。2厂址选择
2.1真空制盐厂的厂址选择,除席遵循选厂的一殿原则外,尚应遵循下刻原则:a.以兆矿盐为原料的真空制盐厂,厂址宜尽量靠近矿区,尽量缩短输卤管线的长度;b,以原盐为原料的真空制盐厂,厂址选择时,应根据原盐及成品盐的流向、运输方式进行比较确定;
,建厂范围应尽量不占用资源开采区域。如遇不可避免的特殊情况,应采取必要的措施;d,由于真空制盐厂货流量大,」址应具备交通便利的条件:心有条件时真空制盐厂宜靠近娥镇,以使充分利用城镇的生活文化设施,方使职工生活,有利生产。
2.2真空制盐厂在选厂过程中.应对厂址的地形、地质、水文、上游水库、资源、地震、气象、交通运输、给水、排水、供电、燃料及原材料供应、生活条件、场地及场地附近的现有设施、环境污染、劳动力来源、耕地状况以及当地城建规划等各种情说进行广泛深人的调查分析,取得可靠的设计基础资料,逊行!址多方案的技术经济比较,推荐最佳厂址方案:3总图布置及运输
3.1一般规定
3.1.1真空制盐厂的总图布置及运输设计应综合考虑下列要求:3.1.1.1在已确定的厂址基础上:应根生产要求,结合场地的地形、地质,气象等自然条件,就建(构筑物、堆场、运输路线、工程管线、绿化设施等素综合考虑,统等安排,合理紧凑地进行总图布置。3.1.1.2生产流程通畅,物料运输路线短捷方便,避免频繁的物流与主要人流的交义;盐与煤的运输路线应尽最分开。
中国轻工总会1994-12-02批准
1995-01-01实施
QR 6008—1995
TTTKAONIKAca
3.1.1.3满足功能分区的要求各种辅助和附属设施靠近所服务的车间;各种动力供应设施应尽量接近负荷中心
3.1.1.4满是防火,安全,卫生等规范要求。3.1.1.5为施下和企业管理的方使创造条件,3.1.1.6节约用地,并为生产和生活创造良好条件。有条件时,生产车间尽量组成联合厂房。3.1.2真空制盐严改,扩建工程总图布置,尽量合理地利用原有的各设施,尽鼠避免影响生产。3.1.3厂区预留发展用地,原则上应根据批雅的有关文件全面考虑.统一规划。3.1.3.1当批准的有关文件已明确分期建设时.应尽量使近期建设项自集中紧凑布置,阅时为后期建设创造良好条件,后期建设而地:一般宜预留在厂区外,在近期不过多占用土地的情况下,也可在半车简一衡留出扩铲建用地。
3.1.3.2当批准的有关文件未明确分期建设时,应根据国家的行业规划,在总图布置时,考虑T厂发展的可能性,相应规划出预留发展用地,并应征求当地规划部门的意见。3.1.4真空制盐厂的总图布置及运输设计除应符合本章规定外,尚应符介国家和行业的现行有关标准和规范的规定。位于特殊自然条件的厂区,如抗囊设防区,湿陷性黄土区、膨胀土,岩溶土、枯溃土、软土地区等,还应执行相应的专门规定。3.2建(构)筑物布置
3.2.1制盐车闭的布置应符合下列要求:3.2.1.1制盐车问的各工段宜合建在一个建筑物内。如不允许含建时,应尽量靠近布置。3.2.1.2制盐车间是重要生产车间,体量大,人流多,荷载较大,它靠近厂前区和工厂主要出人口,并尽量布置在地质祭件较好,地基承载力较简的地段。3.2、1.3制盐车间生产过程中温混度较高,并有摘蚀性-体,宜布置在」前区全年或夏季主导风向的下风侧,并应有良好的自然通风条件。3.2.2卤水净化车间(.T段)可靠近制盐车间布置,也可布置在矿区的适当地段;盐碱联产的工厂,也可布置在制碱车问的附近。其周围应考愿布置废荐场地,如设有石炭窑时,尬注意其烟尘对周国车间的污染此内容来自标准下载网
3.2.3独立设置的提硝车间(工段),应靠近制盐车问布置,以使丁母液的输送,3.2.4热电站的布置除应符合国家现行有关规范外,还应符合下列要求:3.2.4.1建(构)筑物应集中布置,统一规划、留有余地。3.2.4.2煤和灰渣的运输量大,并有较多的烟尘散发,宜布置在厂区边缘地带。煤场和灰渣场宜布置在热电站土厂房和主要生产车间最小风赖1.风侧,并有方便的运输条件。3.2.4.3主厂房及烟函荷载较人,应布置在地质条件较好,地基承载力较高的地段。3.2.4.4室外变电装置的布置应注意高压线迹出线的方便,并应与散发烟尘和腐蚀性气体的车间有适当的防护距离
3.2.5给水处理设施般靠近用户布置.并应避免生产区粉尘、有害气体及污水影响水质。3.2.6循环水系统应布置在通风良好的地段,不宜布置在变配电室,露大生产装置的冬季主导风向的上风侧。
3.2.7机修、仪电修可集中布置:其周制要留有室外作业和物料堆存场地不应布置在散发腐蚀性气体车间的下风侧。
3.2.8成品包装库(成品包装工段)宜用廊道与制盐车问相连,并应布置在运输方便的地方。3.2.9办公楼、食堂、汽车库、浴案、哺乳空门卫等厂前区设施,应布置在散发烟尘和腐蚀性气体车间复季最小风频的下风侧。厂前区的建筑可适当合并,相应绿化,与城镇及居民区联系方便。3.3通道及间距
3.3.1真空制盐厂厂区内通道的宽度,应满足下列要求:456
QB60081995
3.3.1.1通道两边建筑物、构筑物、露天设备防火、防爆、卫生间距的要求。3.3.1.2地上地下管线、交通运输线路及绿化设施所需要的觉度。3.3.1.3主要通道的宽度宜与两侧筑物高度相协调。厂区内通道的宽度宜符合表1的规定。表1厂区通道宽度
制盐厂规模,万吨/年
主要通道
通道宽度:m
注:通道内管线及运输线路较多,且地形复杂或气候影响时,可采用上限。次要通道
12:~18
3.3.2厂区内相邻建(构)筑物及堆场的防火间距应按现行《建筑设计防火规范》执行:改扩建厂执行防火间距确有困难时,应与当地有关部门协商确定。3.3.3个别相邻建(构)筑物及堆场按防火间距布置有困难时,应与当地有关部门协商确定。3.3.4相邻建(构)筑物的卫生间距应按现行的“工业企业设计卫生标推》执行。3.4技术经济指标
3.4.1总图布置及运输设计的技术经济指标,一般包括下列内容:3,4.1.1厂区占地面积:厂区.用墙内的面积,按围墙轴线计算,单位以ha 计。3.4.1.2建(构)筑物占地面积:设计的建(构)筑物外轮廊面积,单位以m2计。初步设计可按建(构)筑物外壤轴线计算,圆形拘筑物按内径计算。施工图按建(构)筑物外墙的外包尺寸计算。3.4.1.3露天堆场或作业场地占地面积:固定的露天堆场或操作场地,单位以m2计。有基础的露天堆场,占地面积算至基础外轮廓线。3.4.1.4道路及广场占面积:道路及广场的铺面积(包括车间引道、人行道回车场、停车场等),单位以m2计。
3.4.1.5厂内铁路长度:厂内铁路所有股道长度的总和,单位以km计。3. 4, 1. 6土石方工程量;厂区土石方的填方和挖方的总和(包括场地整平,建(构)筑物基础余十、道路路槽挖土,管道、管沟余士等),单位以㎡\计。3.4.1.7厂区建筑系数:为建(构)筑物占地面积与露天堆场、作业场地占地面积的总和除以厂区占地面积乘100%。
3.4.1,8场地利用系数:为建(构)筑物、露天堆场、作业场、铁路与道路、地上地下管线、散水等占地面积的总和除以厂区占地面积乘100%。3.4.1.9绿化系数:为厂区绿化覆盖面积除以厂区占地面积乘100%。绿化覆盖面积即全厂绿化面积总和,单位以㎡计,计算时,重点绿化区的成片绿化,按实际几何面积计算:行道和单植绿篱,按树冠外缘宽度乘长度计算,单梢的乔,灌木,按树冠正投影面积计算。3.4.2真空制盐厂厂区的建筑系数宜为 25%~30%,场地利用系数不宜低于50%,绿化系数应不低于10%
4 工艺设计
4.1一般规定
4.1.1真空制盐工艺设计,必须根据原料卤水条件和产品质量要求,制定生产方法和计工艺流程。4.1.2真空制盐的原料卤水分为天然卤水和人工卤水。除氟化钠以外,其他组分以硫酸钠为主的称为硫酸钠型卤水;以硫酸钙为主的称为硫酸钙型卤水;以氯化物为主的称为氯化物型卤水。457
QB6008—1995
TTTKAONIKAca
4.1.3在工艺设计中,对原料卤水中的其他有用组分,凡有T业利用价值的,应同时考虑综合利用,4.1.4精制盐质量应达到国家标准GB5461优级或一级精制盐标准;无水硝成品质量应达到国家标推GB6009一级或一级工业无水硫酸钠标推。4.1.5一般情况下原料卤水中氯化钠和其他组分总含量不宜抵于300g/I.。4.1.6真空制盐厂为连续性生产,在各项衡算中,每夜生产时问按21h为计算依据。考患设备结垢清洗与生产操作变化,设计波幅取10%~15%。4.1.7设计采用的实际生产日数,应根据项目实际情况确定,-殷每年为300-~330.3天,年生产时间7200-~8000h.
4.1.8制盐单套装置的规模,应竖持人型化方向,一般采用10.15.20,30万吨/年,4.1.9制盐工艺设计所需各种数据必须可靠,指标必领先进可行。4.2牛产方法
4.2.1生产方法的确定要在4,1.1条原则基础1.,根据技术先进可靠性和经济合理,经多方案比选确定,
4.2.2原料卤水宜逊行净化处理,除去钙,镁离子.通常采用石灰-芒硝-二氧化碳法、石灰-纯碱法或烧碱-纯碱法,应根据技术经济比较选定。条件不具备时,硫酸钠型卤水采用热法提硝可结合除钙;硫酸钙型卤水宜采用石晶种法防垢,以减轻传热管璧结垢,延长潮周期。4.2.3原料卤水中含有较高硫化物,将加剧制盐设备、管道的腐蚀,含有过量钡、铅等有害组分会影响成品盐质量,都必须进行化学净化处埋。4.2.4卤永净化车间(或工段)宜单独设置,并相应包括各处理工序。4.2.5硫酸钠型卤水,硫酸钠含量一般为15~30g/L,宜采用热法提硝。在此范国外的宜采用冷法提硝。
4.2.6热法提硝,采用原料卤水或净化后卤水洗涤制盐系统排出的盐浆,得到含硫酸钠人于70g/L的洗盐卤水:作为提硝原料:洗盐卤水升温盐析或蒸发)后,母送制盐系统作原料。末净化的卤水,洗盐过程生成的含钙硫酸盐复盐颗粒较细,可结合除钙过进行处理,母藏回收法是制盐蒸发系统控制硫酸钠始终处于饱和点以下,并连续从制盐蒸发末效排出母液,于独立的问收系统向收母液中所含的氯化和蔬鞍钠。
4.2.7冷法提硝,在原料卤水或净化后卤水含硫酸钠大于40/1.时,直接作提硝原料;硫酸钠含量较低时,应以制盐系统排出的含硫酸钠大干 45 /L 的盘液作为提硝原料。提硝踪料卤水经冷冻析硝得到芒硝母液送制盐系统作原料。4.2.8制盐生产方法为:原料卤水经蒸发结晶、离心脱水、沸腾下燥得到成品精制盐。制盐车间包括蒸发,脱水与干爆工序。硫酸钙型卤水采用石膏晶种法时,相应增加石旁处理工序。4.2.9热法提硝生产方法为:洗盐卤水经升温盐析、沉降分离、离心脱水、气流或沸腾干燥得到成品无水硝。热法提硝系统宜作为提硝工段附设于制盐车间,提硝工段包括盐析、脱水与干燥工序,4.2、10冷法提硝生产方法为:提硝原料卤水经冷冻析硝、沉降浓缩、真空过滤、热熔蒸发、离心脱水、气流或沸腾干燥得到成品无水硝。提硝车间包括制冷、冷冻、过滤.蒸发,脱水与干燥工序。4.2.11成品精制盐与无水硝的包装储运系统一般采用机械化的计量包装与转运堆码生产线。包装储运系统包括输送,计量、包装与外运工序。4.2.12真空制盐厂原料卤水中氧化钠总间收率应达到85~95%,硫酸钠回收率60%~90%。4.3工艺流程
4.3.1工艺流程应根据原料卤水组成、产品质量标准及产品品种要求、生产方法及项目外部条件进行设计,并要求技术先进成熟和良好的经济效益。4.3.2工艺流程的设计,在保证产品质量和技经指标条件下,应力求简化和缩短流程,充分考虑节约能源措施,
QB 6008—1995
4.3.3T艺流程的设计,必须考虑装设必要的计量及自动控制仪表,以提高生产管理水平。4.3.4丁艺流程的设计,必须考虑生产废液、废渣的利用,尽量减少废液、废道、废气的排放量,搞好综合利用稚环境保护。
4.3.5工艺流程设计的具体要求,按照卤水净化、制盐,热法提硝、冷冻提硝、盐石膏的利用五部分分别说明:
(1)卤水净化
4.3,6采用石灰-芒硝-一氧化碳法除去钙,镁离子的两段净化流程。第一段为原料卤水和事先配好的石灰乳在反应器内进行反应,沉降分离氢氧化镁和硫酸钙(一次泥)的清液;第二段在碳化器内,用石灰蜜气或烟道气进行碳化除钙反应。就降分离碳酸钙(二次泥)后的清液通常称作精卤,作制带原料。为了加速一、二次泥的沉降,需人絮凝剂,白备石炭密时,石灰右的质量应符合下列指标:石灰石:含碳酸钙(CaCO,)>92%含碳酸镁(MgCO)<2%
含二氧化硅(SiO)2%
有灰穿气经净化后,便气体含尘量低于50mg/1可供二段除钙反应之用,4.3.7卤水净化来用石灰、纯碱法,应根据卤水中的钙、镁离子含量,经过技术经济对比,决定采用一段静批或三段净化流程。
-段净化,在原料卤水中一次同时加人石灰乳和纯碱溶液,沉降分离反应所生成的钙镁泥后可得精卤,采用二段净化·先在原料卤水中加人石灰乳除镁,经澄清后的清液,加人纯碱羧除钙,生成的碳酸(二砍泥)转人一段净化.形成钙镁泥(一次泥),经沉降可得精卤。4.3.8硫化物含量高于0.1名/I的天綫卤水,采用空气吹出-氯气氧化-石求、硫代巅较钠还原净化处理流程。硫化物含量低于0.1g/L的原料卤水,宜采用电化法除硫化氢。净化后的卤水硫化氮含量在2. 5 mg/L 以下。
4.3.9含有过量钡的天然卤水,如含钡黄卤,除钡流程是与含有部分碗酸根的岩盐卤混合反应,生成硫酸钡沉淀,经澄清后的卤水作为制盐原料。对含铅的原料卤水,必须用石灰法除销。(Ⅱ)制盐
4.3.10原料卤水或精制卤水在制盐蒸发工序经蒸发结品折出固体盐,其他有用组分浓缩富集后的母液排出作为提取副产品的原料。4.3.11蒸发工序一般采用四效或五效蒸发流程,加压与多效蒸发并用流程.在有廉价电力的地区可考虑采用机械加压蒸发,应通过热力方案平衡计算、节能与综合技术经济比较来决定,并相应选定热电站配套方案:
4.3.12蒸发T.序应尽量利用热电站的低压饱和蒸汽,不足部分可用减压蒸汽补充。生蒸汽冷凝水经适当降温后送回热电站作锅炉给水;二次蒸汽冷凝水用作锅炉补充水时,应采取必要措施,保证水质符合锅炉水标准及有关规定
4.3.13为进一步提高多效蒸发系统热效率、达到热法提硝对于洗盐卤水预热温度的要求,除充分利用各效冷凝水余热外,宜适当捆取客效二次蒸汽预热进罐卤水或洗盐卤水。4.3.14为减轻卤水的蚀和提高蒸发设备蒸汽给热系数,经初步预热的卤水或盐析析硝后的树液宜进行真空脱氧。
4.3.15蒸发加料操作宜采用平流或逆流平流并用方式,排盐操作宜采用顺流转料,以降低蒸发系统排出盐浆的温度,减少热能损尖。硫酸钙型卤水制盐,采用石膏晶种防垢-排盐时宜将石宵返回各效蒸发爆,使各效固相中石寓含量保持15~30g/L,4.3.16为了提高成品盐质量,盐浆应进行洗涤。硫酸钠型卤水宜卧式搅拌槽或立式洗盐器内进行两级逆流洗漆,硫酸钙型卤水制盐宜在立式洗盐器中洗涤分级:459
QB 6008—1995
TYKAONYKAca
4.3.17脱水工序中,盐浆应经水力旋流器增稠器增浓后直接或通过搅拌槽向离心机喂料,经离心脱水,湿点含水量在4究以下,滤应回收。4.3.18干燥工序应采用沸腾干燥冷却设备,以降低成品盘的温度。于燥后,成品盐含水量应符合质量标推。干燥尾气应通过两级除尘设备回收粉尘。(皿)热法提硝
4.3.19硫酸钠型卤水末除钙、镁离子直接制盐,为了保证成品无水硝的质量,在热祛提硝过程,必须进行高温除钙。洗盐卤水预热至95~100℃,将高温析出物分离,可达到除钙目的。4.3.20盐析工序加盐操作,宜入干燥后的固体盐。可采用制盐T燥工序下式除尘器间收的粉盐,并设置必要的计量输送装置。可直接加入盐析结晶器(盐析槽),也可在搅拌槽与洗盐卤水混合成浆料后加人盐析结晶器。采用蒸发析硝时.可将预热升温后的洗盐卤水引入蒸发结晶器,蒸发水分,析出无水硝。
盐析硫酸钠以后的料液进行沉降分离,澄清的高温盐析后母液(盐析母液),经真空脱氧后去制4.3.21
盐,无水硝浆送脱水工序。
4.3.22脱水工序中,无水硝浆经离心机分离得到粗硝(指含有一定杂质),加人硫酸钠溶液或少量淡水洗涤除去氣化钠,经离心机二饮脱水。4.3.23干燥工序,应根据实际情况,选用气流干燥或沸腾干燥,并采取相应除尘措施。()冷法提硝
4.3.24制冷工序,宜采用单级压缩机制冷流程,氨器中液氨送冷冻工序直接冷冻,在冷冻结晶器蒸发成气氨,送回氨压缩机乐缩,经氨冷凝器玲凝成液氨,返回氨器。4.3.25冷冻丁序,提硝原料卤水必须用析硝后冷母液(或称精卤),预冷至12℃以下,以节省玲量,4.3.26冷冻工序,应考虑冷冻过程芒硝呈过饱和析出。为了减轻冷冻结晶器传热管壁结垢,必须将部分玲冻后母液与芒硝结晶同流,与原料卤水混合,添加芒硝晶种,以降低冷冻结晶过程硫酸钠的过饱和度。
4.3.27由于冷冻后母液中硫酸钠星过饱和状态,应在其有足够容积和面积的增稠器中,进行芒硝结晶的生长和沉降。
4.3.28为了保证成品无水硝的质量,可用淡水洗涤芒硝,亦可在芒硝热溶蒸发系统排放一定量氯化钠含量高的母获。
4.3.29蒸发工序,芒硝热溶宜采用末效蒸发罐母液或离心机滤液,应避免采用生蒸汽作为热熔热源,4.3.30蒸发工序,宜采用多效蒸发流程或热压缩蒸发流程。4.3.31无水硝的干燥,宜采用气流或沸腾干燥流程。()裁石荐的处理
4.3.32为了充分利用资源,对于未除钙、镁离子的硫酸钙型卤水,在制盐过程所产生的盐石膏应回收利用。将制盐蒸发排出的石膏与盐在分级器中避行初步分离,4.3.33将石膏将在品形转化器中转化为二水石膏。经水洗和过滤的湿料,可作石膏制品的原料。4.4技术参数与指标
4.4.1设计中采用的回收率应符合 4.2.12的要求,4.4.2采用卤水净化时,净化卤水应达到下列指标:Ca*+ -20 mg/I.
Mg*+<10 mg/L
4.4.3蒸发经济(t水/t生蒸汽)不得低于下列指标:制盐(多效蒸发)
提硝(多效蒸发)
4.4.4蒸发与换热设备传热系数,/(m2,K),不宜低于下列指标:460
制盐蒸发:净化卤水
未净化
换热设备:汽液
被液(列管式)
液液(板式)
4.4.5卤水净化主要操作控制参数如下:石灰窑密加料,石灰石焦碳配比100:8QB 6008—-1995
1 800--2 900
1 200~-2 100
500~700
250~~350
900--1 100
氢辑化钙或氮氧化钠过量 0. 05~0. 10 g/L碳酸钠过虚0.2~0.3g/
4.4.6制盐主要操作控制参数
原卤预热温度(只用冷凝水预热)第一效蒸发罐进汽压力(绝压)
末效二次蒸汽压力(绝压)
气压式冷凝器进水温度
>50℃
300~450kPa
制盐母液(作为冷冻提硝原料)含硫酸钠量>45g/L进离心机浓度
脱水后湿盐含水量
沸腾干燥热风温度
成品盐含水量
4.4.7热法提硝主要操作控制参数:洗盘卤水含硫酸钠量
洗盐卤水预热温度
盐析母液含氮化钠量
、粗硝洗涤加水量
离心机进料浓度
脱水后湿硝含水量
干爆装置热风温度
成品无水硝含水量
4.4.8冷冻提硝主要操作控制参数:氨冷凝器冷凝温度
卤水预冷冻温度
卤水冷冻温度
氨蒸发器蒸发温度
氨压缩机排气温度
析硝母液含硫酸钠量
过滤后混芒硝含游离子分量
芒硝热溶温度
>60%(重量)
24%(重量)
>130℃
>70 g/L
95~100℃
300~-305 g/1.
150~300kg/t
60%(重量)
5%(重量)
>130℃
10~12℃
--4--2℃
—10~-15℃
100℃
10~12 g/1.
10%(重量)
第一效蒸发罐进汽压力(绝压)300~400kPa气压式冷凝器进水温度
蒸发过程析硝母液含氯化钠量
离心机进料浓度
脱水后湿硝含水量
100 g/L
>60%(重量)
<5%(重量)
于燥装置热风温度
成品无水硝含水量
QB6008-1995
>130℃
TTTKAOIKAca
4.4.9生产车问用水,分为三类,即冷却用水、生产用水和生活用水,应达到相应水质标准和供水压力。4. 4.9. 1冷却用水;用于蒸发工序蒸发缠木效二次蒸汽冷凝和制冷工序氨冷避器的气氨冷凝,其水质指标:
pH值.6.5~8.5
水温:不超过32℃
肉眼而见物:水中无明显的泡沫、油膜及泥砂等杂物。色:无异色
臭和味:无异臭和异味
4.4.9.2生产用水:用于各工序生产过程补水,洗涤及设备冷却,其水质指标:悬浮物:不超过 5 mg/1.
色:透明,亦不呈其他异色
臭和味:小得有兄臭兄味
pH值:6. 5~8. 5
总硬度(以碳酸钙计):不超过180mg/L铁不超过 0. 3 mg/L
锰 不超过 0. 1 mg/I
铅不超过 (. 05 mg/ L.
神不超过 0. 05 tng/L
4.4.9.3生活用水,水质应达到国家《生活饮用水卫生标准GB5749,4. 4. 9. 4 供水压力一般采用:冷却用水压力(表压)
生产用水压力(表压)
生活用水压力(表压)
150--200 kPa
200--300 kPa
150-~250 kPa
4.4.10生产车闯用汽一般为低压蒸汽,采用以蒸汽为动力源的机械加压工序时,需要提供中压或次高压蒸汽。生产用低压燕汽参数-般采用:蒸发装置加热汽压力(绝压)300~~450kPa干燥装置加热蒸汽压力(绝压)400~700kPa4.5设备选型
4.5.1必须选用先进、成熟或经过技术鉴定的新设备。4.5.2应结合真空盐厂生产实际情况,选择机械化程度和效率较高、能耗较低的大型化设备:并应考虑不断提高自动化水平。
4.5.3选用设备时必须考虑易于操作和拆装,结构较简单,制造较容易,易损零件容易更换,维修方便;同时,设备的材质要适应生产过程物料性质的要求。(I)卤水净化
4.5.4自备石灰窑,应采用竖式,窑容积按二氧化碳实际用量的1.2~~1.4倍选取,容罩大的窕送料设备宜采用垂直斗式升运机;较小的窑宜用结构简单的倾斜式升运机。4.5.5窑气或烟道气洗涤净化宜采用泡沫塔。4.5.6石嵌消化设备宜采用机械化灰机,消化时间可按15~-20mi1n选取。石灰除砂机一般选用惯性式高频振动筛将石灰乳中的石块与砂粒筛分出去。4.5,7除镁与加纯碱除钙的反应器,宜采用立式带搅拌的钢制圆槽,加二氧化碳除钙采用锥形碳化罐。4.5.8钙、镁泥沉降.宜采用连续沉降器,钙、镁泥过滤宜采用外滤面转鼓真空过滤桃或板框压滤机,162
(Ⅱ)制盐
QB6008—1995
4.5.9制蒸发,宜用外加热式强制循环蒸发罐。4.5.10外加热式蒸发罐配套循环泵,宜采用卧式轴流泵。4.5,11末效二次蒸汽冷凝设备,可采用混合式冷凝器。抽真空设备可采用机械真空泵、蒸汽喷射泵。4.5.12各级卤水预热器,宜选用多程列管式换热器。为充分利用低位冷凝水余热,可采用板式换热器,以获得较好的节能效果。
4.5,13原料卤水的储存,可采用方形与圆形钢筋混凝土池或圆形钢储槽。储存容积,根据采区室厂区输卤管道长度与材质决定,一般为1~2大的用盈。4.5.14料液的输送设备,应根据物料性质、流量及要求达到的扬程选取,为保证连续生产,宜适当考虑备用。
4.5.15湿盐与下盐的愉送设备宜来用带式输送机,4.5.16盐浆脱水,宜采用卧式活塞推料离心机、螺旋推料离心机或卧式锥篮离心机。有多台离心机时,宜配置检修用起重设备,其能力应以离心机的不可拆部件巾的最大件的重量来考虑。4.5.17盐的干燥设备,宜采用玲热床沸腾干燥器,冷床面积般为热床面积的30%~50%;干燥筛分设备,宜采用振动筛:除尘设备,宜采用旋风及湿式除尘器。4.5.18洗盐设备宜采用卧式螺旋带搅拌槽或立式洗漆桶。(Ⅲ)热法提硝
4.5.19盐析析硝设备宜采用卧式螺带搅拌槽、盐析结晶器,并配套加盐用穿积式或重量式计量装置。蒸发析硝宜采用蒸发结晶器。
4.5.20无水硝沉降浓缩设备宜采用连续沉降器。4.5.21无水硝浆脱水可采用立式、卧式刮刀卸料离心机或卧式活塞推料离心机。4.5.22湿硝干燥可采用沸腾于燥冷却器或气流干燥器。除尘设备宜采用旋风及湿式除尘器。(I)羚法提硝
4.5.23制冷设备宜选择活塞式或螺杆式氮制冷压缩机,并考患必要的备用机台。4.524原卤预拎器宜采用卧式多程列管式换热器或板式换热器。4.5.25冷冻结品器宜采用列管式氨蒸发器或循环式冷冻结晶器。采用列管式氨蒸发器时,应增加兑卤系统,以降低料液饱和度,并添加晶种。4.5.26蓝硝沉降浓缩宜采用连续沉降器或圆薇型沉降器,保证足够的停留时间。4.5.27芒硝过滤宣采用外滤面转鼓真空过滤机,可采用水环式真空泵或水喷射泵抽真空。4.5.28芒硝热熔宜用机械搅拌槽。4,5.29硝液蒸发应采用外加热式强制循环蒸发罐,配置卧式轴流泵。无水硝浆脱水宜采用卧式活塞推料离心机,4.5.30
4.5.31湿硝干燥可采用沸腾干燥器或气流干燥器。()盐石膏利用
4.5.32盐与石膏的分离官宦用立式水力分级槽.石言的沉降浓缩可用斜板沉降器。4.5.33盐石膏的石膏转型可用立式搅拌桶。二水不膏的过滤可采用圆盘真空过滤机。4.6设备布置
4.6,1根据已确定的T艺流程及选定的设备进行布置,4.6.2设备布置应在满足生产操作、设备检修和餐道布置的前提下,力求紧凑减少占地面积,4.6.3厂房的柱距和跨度,应根据主要设备外形尺寸、设备布置的合理间距,操作面的要求以及设备组合方式等因繁,并结合土建模数合理确定。4.6.4厂房净高的确定.应考虑楼面的设备,管遵安装的需要和便于检修。46.5设备布置,要尽量满足通风采光的要求,充分利用白然通风与来光。高大设备千宣靠衡布置:设463
QB6008—1995
备布置在门窗和楼梯附近时,不得妨碍门窗的开启和阻碍通行。TTTKAONIKAca
4.6.6操作频繁的主要生产设备的操作面.应有良好的通风采光条件。散发热量较多的设备操作面应加强通风降温。
4.6.7同类型的设备宜集中布置,便于设备轮换、调配使用与维修。1生条件差的设备亦宜相对集中布置,防止污染扩散。
4.6.8震动大的设备应避免布置在楼面;噪音大的设备应采取消声或隔离措施,地面设备尽量避免布置在地坑中,以利于车问清洁卫生,4.6.9车间内各层楼面应设吊装孔和预埋吊钩,外墙在需要时可预留墙孔,供设备安装或日常检修之用。留孔大小,根据最大吊件的外形尺寸确定。4.6.10根据操作和检修的需要,部分设备应合理布置操作台,其高度、宽度、通道与梯子应符合操作和检修的有关要求,
4.6.11车间大门、便门的大小和位置,应根据用途、性质、最大设备部件的外形尺寸及车辆人流情况合理设置
4.6.12车间化验室应布置在采光条件好、干爽,不受噪音与震动影响以及便于到现场取样较为方便的地方。主车间宣设置必要的生活卫生设施。:(I)卤水净化
4.6.13卤水净化设备宜单独设置为午间或工段布置。4.6.14钙、镁泥的沉降设备应露天布置,与厂区总平面布暨协调一致,并注意尽堡碱少占地面积。化灰机、二氧化碳压缩机、各种料液泵、反应器宜布置在室内,过滤设备宜布置在二层或操作平台上。4.6.15化灰机灰乳桶、灰乳储桶、反应器等设备应布置在-起,设备间距尽量紧凑,缩短灰乳管道长度。碳化应集中布置,并设置操作层或平台。4.6.16本车间(丁段)用电负荷集中在二氧化碳压缩机间和料液泵房,配电间应靠近负荷中心。(Ⅱ)制盐
4.6.17制盐车间蒸发、洗盐、脱水与干工序宜布置在同一建筑物内,并有良好的通风和采光。4.6.18蒸发工序厂房多采用二层或三层布置,楼面高度应根据设备的外形尺寸、安装、操作、维修需要的空间决定·蒸发室和加热室可支承在不同标高的框架或支架上。4.6.19燕发罐可来用半露天布置,即蒸发室支承在钢筋混泥士平台上,蒸发罐顶与二次汽管局部露天其余部分布置在室内,
4.6.20蒸发设备的操作面应有足够的宽度,有视镜的蒸发罐,操作面的最小宽度以人站立并能观察到最高视镜液面距离为准,其他设备操作面觉度应能满足操作、检修和生产联系的需要。设备旁的人行过道净空一般不小于800mm
4.6.21蒸发工序楼面,在适当位置设置设备吊装孔,其尺寸应大丁最大吊件外径400~800mm。4.6.22洗盐、离心脱水工序宜紧邻蒸发工序,离心机宜布置在楼面上,湿盐胶带输送机可布置在操作平台或地面上,洗盐槽、滤液槽与料液泵等设备它布置在地面,楼面高度应无于4m,操作平台高度应大于311,离心机操作层层高应大于4㎡。4.6.23离心机操作面宜靠窗布置,并有足够宽度,离心机间距应能满足操作、安装和维修的要求。4.6.24脱水工序楼面应预留吊装孔,以满足离心机整机吊装的要求。4.6.25十燥工序温度较高,一般宜作单层厂房布置,留有足够的风空间。如必须布置在多层厂房的层·应考虑适当的层高。
4.6.26湿物料胶带输送机输送角度应<18°,采用溜槽进人沸腾干燥冷却器时,流送坡度应>45°。4.6.27沸腾干燥器配套风机宜集中设置在风机室内,以降低车问噪音。4.6.28干燥尾气除尘设备的布置应尽量简化和缩短风管。4.6.29沸腾干燥器应设置操作平台。464
(山)热法提硝
QB 6008-1995
4.6.30热法提硝作为一个工段,结合制盐系统布置在同一厂房内。热法提硝工段若单独设置时,应尽量靠近制盐车间尘厂房。
4.6.31盐析工序温度较高,且散失一定量蒸汽,在盐析槽加盖密闭与设置排汽管措施外,本工序应单独隔开,并尽量散开布置,以改善通风条件。燕发析硝可与制盐蒸发罐的布一并考虑。4.6.32无水硝沉降器宜布置在室外,硝浆泵、母液某宜就近布置在沉降器下面。4.6.33脱水与干燥工序可参照制盐部分有关条文布置。()冷法提硝
4.6.34冷法提硝应独立设置一个车间,根据总平面布置要求,各T.序可布置在--座或两座建筑物内。4.6.35制冷工序应设罩在底层,氨制冷压缩机布置在厂房内:人部分辅机可布實在室外,出于车用电负荷集中在本工序,车间变电间应紧靠制冷工序。4.6.36氢制冷压缩机布置应充分考虑运行、管理与维修方便,操作阀门与就地仪表应面向主要操作通道。
4.6.37氨冷凝器的安装商度,应保证冷凝的液氨能自动流入贮氢器,立式冷凝器应设置操作平台,以利操作与除垢。此氨器应有谌阳设施。4.6.38冷冻工序宜设置在二层,兑卤槽与料液藜宜布置在底层,预羚器可布置在室外。预冷和冷冻设备操作面的宽度应能满足操作与维修的要求,并设置排水管沟,将清洗设备的废水排人厂区排水系统。4.6.39冷冻工序楼面所留吊装孔,应能满足设备整体吊装的要求。4.6.40制冷与冷冻工序,在生产中,其在设备检修时可能有少量氮气逸出,应强通风,相应设置机械强制通风装置。
4.6.41芒硝沉降器宜设置在室外,浓缩后芒硝浆储存槽及硝浆泵、母液泵宜就近布置在沉降器下面。4.6.42芒硝真空过滤机应布置在二层,真空泵、热熔槽、料液浆等设备宜布置在底层。4.6.43蒸发、脱水与干燥工序参见制盐部分有关条文。(V)盐石膏的处理
4.6,44石膏晶形转化器、盐与石膏分离设备宜露天布置,二水石膏的过滤设备、真空泵,料液泵等宜布置在室内。
4.7管道布置
4. 7. 1 生产车问工艺管道设计压力为 8~~3 000 kPa(绝压),设计温度为—15~~180℃。4.7.2管道直径应根据输送介质的特点、流量和常用流速进行计算,并考虑生产波动、阻力摄失、积垢和管子规格等因素确定。
4.7.3常用介质流速宜按表2数据选取,表2常用介质流速表
卤水、母液
盐浆、硝浆
石灰乳
生蒸汽
二次蒸汽
冷凝水
生产用水
冷却用水
介质名称
1. 0~-2. 0
0. 5~1. 0
25 ~ 80
0. 5 ~1. 5
1. 2--2. 0
1. 5-~2. 5
疏速范围·/s
医缩空气
介质名称
密气,烟道气(C)
管材的选择应符合下列规定:
QB6008-1995
表2(完)
c. 5 -1. 0
TTKAOIKAca
流建范围,m/g
车间内输送盐浆,冷凝水、卤水的管道宜采用耐腐蚀材料,其余管道可采用水煤气管(D<100 mm)无缝钢管(Dk=10~500 mim)或卷焊钢管(Dz300 mm)。车间外输卤、输水管道Ⅲ采用钢管,铸铁管或其他耐腐蚀材料管4.7.5选用的各类管子必须符合有关质量标准。管子壁厚应根据介质的特性、使用年限、T.作压力和工作温度等因素确定。
4.7.6管道布置必须满足生,产需要,便于安装和维修,并尽量缩短管线长度,节省材料。管道应尽量架空敷设,架空管道经过车间人行道上方,最小净空高度为2.2 m。在不影响操作的条件下,部分管道可沿地面、埋地或在地沟内敷设。4.7.7管道布置不应妨碍建筑物的使用及门窗的启闭,不宜影响室内采光,不宜通过电动机、配电盘、仪表盘的上方。管道应尽量沿墙和柱敷设,以便于支承,并考建筑物对管道荷载的支承能力,管道不宜穿过建筑物的伸缩缝、沉降缝。若必须穿过时,应来取相应的技术措施。4.7.8管道布置应同时考虑管道组装、焊接、仪表、附件和保温结构等的安装位置。4.7.9在同一空间布置儿种介质管道,水平并列时,一般应将大管径、保温,非腐蚀性介质的管道布置在上面。制羚压缩机的排气管应布置在逆气管的上面。4.7.10管道的间距根据管道法兰直径大小,并列管法兰安装的形式、保温管道的保温层厚度、管道焊接和支吊架安装的合理位置等因素确定。4.7.11管道在穿墙或楼板时,应预留孔,留孔大小应根据管道法兰大小,保温管道的保温层厚度,并列管道的间距等凶素确定
4.7.12管道安装完毕,除不锈钢管、镀锌钢管、钛管·般不宜涂漆外,其余管道按不同介质分别刷不间颜色油漆,详见表3。
表3管道涂色表
管道内介质名称
齿水、母液
盐浆、硝浆
右炭乳
生产,生活用水
循环玲却水
冷凝水
生产废水
涂漆颜色
小提示:此标准内容仅展示完整标准里的部分截取内容,若需要完整标准请到上方自行免费下载完整标准文档。
中华人民共和国轻工行业标准
真空制盐厂设计规范
QB6008—1995
1.1真空制盐厂设计,必须认贵彻执行国家有关科学技术发展和工程建设的方针、政策,紧密结合我国国情,从全局出发·做到划合实际,技术先进,安全适用,节约能源,保护环境,提高效益。1.2本规范适用于建设规模为3~60万吨/年规模的真空制盐厂工程设计(包括副产品硫酸钠,不包含矿区、牛活区及综合利用下程)。扩建、收建及技术改造项目的设计亦可适用。1.3设计原则
a。真空制盐厂设计,应根据已批准的有美文件要求,搞好工厂的总体规划,做到近期为主,适当考虑发展的可能。改建、扩建工程,应充分挖掘潜力,合理利原有设施:b,应积极采用可靠的,经过实践证明有经济效益,社会效益、环境效益的新技术:C.采用的工艺,设备要力求技术先逊,各项技术经济指标达到或超过国内先进水平;机械化和自动化水平应符合国情,逐步提高。1.4真空制盐厂设计:除应符合本规定外尚应符合国家现行有关法规,标准,规范的规定。2厂址选择
2.1真空制盐厂的厂址选择,除席遵循选厂的一殿原则外,尚应遵循下刻原则:a.以兆矿盐为原料的真空制盐厂,厂址宜尽量靠近矿区,尽量缩短输卤管线的长度;b,以原盐为原料的真空制盐厂,厂址选择时,应根据原盐及成品盐的流向、运输方式进行比较确定;
,建厂范围应尽量不占用资源开采区域。如遇不可避免的特殊情况,应采取必要的措施;d,由于真空制盐厂货流量大,」址应具备交通便利的条件:心有条件时真空制盐厂宜靠近娥镇,以使充分利用城镇的生活文化设施,方使职工生活,有利生产。
2.2真空制盐厂在选厂过程中.应对厂址的地形、地质、水文、上游水库、资源、地震、气象、交通运输、给水、排水、供电、燃料及原材料供应、生活条件、场地及场地附近的现有设施、环境污染、劳动力来源、耕地状况以及当地城建规划等各种情说进行广泛深人的调查分析,取得可靠的设计基础资料,逊行!址多方案的技术经济比较,推荐最佳厂址方案:3总图布置及运输
3.1一般规定
3.1.1真空制盐厂的总图布置及运输设计应综合考虑下列要求:3.1.1.1在已确定的厂址基础上:应根生产要求,结合场地的地形、地质,气象等自然条件,就建(构筑物、堆场、运输路线、工程管线、绿化设施等素综合考虑,统等安排,合理紧凑地进行总图布置。3.1.1.2生产流程通畅,物料运输路线短捷方便,避免频繁的物流与主要人流的交义;盐与煤的运输路线应尽最分开。
中国轻工总会1994-12-02批准
1995-01-01实施
QR 6008—1995
TTTKAONIKAca
3.1.1.3满足功能分区的要求各种辅助和附属设施靠近所服务的车间;各种动力供应设施应尽量接近负荷中心
3.1.1.4满是防火,安全,卫生等规范要求。3.1.1.5为施下和企业管理的方使创造条件,3.1.1.6节约用地,并为生产和生活创造良好条件。有条件时,生产车间尽量组成联合厂房。3.1.2真空制盐严改,扩建工程总图布置,尽量合理地利用原有的各设施,尽鼠避免影响生产。3.1.3厂区预留发展用地,原则上应根据批雅的有关文件全面考虑.统一规划。3.1.3.1当批准的有关文件已明确分期建设时.应尽量使近期建设项自集中紧凑布置,阅时为后期建设创造良好条件,后期建设而地:一般宜预留在厂区外,在近期不过多占用土地的情况下,也可在半车简一衡留出扩铲建用地。
3.1.3.2当批准的有关文件未明确分期建设时,应根据国家的行业规划,在总图布置时,考虑T厂发展的可能性,相应规划出预留发展用地,并应征求当地规划部门的意见。3.1.4真空制盐厂的总图布置及运输设计除应符合本章规定外,尚应符介国家和行业的现行有关标准和规范的规定。位于特殊自然条件的厂区,如抗囊设防区,湿陷性黄土区、膨胀土,岩溶土、枯溃土、软土地区等,还应执行相应的专门规定。3.2建(构)筑物布置
3.2.1制盐车闭的布置应符合下列要求:3.2.1.1制盐车问的各工段宜合建在一个建筑物内。如不允许含建时,应尽量靠近布置。3.2.1.2制盐车间是重要生产车间,体量大,人流多,荷载较大,它靠近厂前区和工厂主要出人口,并尽量布置在地质祭件较好,地基承载力较简的地段。3.2、1.3制盐车间生产过程中温混度较高,并有摘蚀性-体,宜布置在」前区全年或夏季主导风向的下风侧,并应有良好的自然通风条件。3.2.2卤水净化车间(.T段)可靠近制盐车间布置,也可布置在矿区的适当地段;盐碱联产的工厂,也可布置在制碱车问的附近。其周围应考愿布置废荐场地,如设有石炭窑时,尬注意其烟尘对周国车间的污染此内容来自标准下载网
3.2.3独立设置的提硝车间(工段),应靠近制盐车问布置,以使丁母液的输送,3.2.4热电站的布置除应符合国家现行有关规范外,还应符合下列要求:3.2.4.1建(构)筑物应集中布置,统一规划、留有余地。3.2.4.2煤和灰渣的运输量大,并有较多的烟尘散发,宜布置在厂区边缘地带。煤场和灰渣场宜布置在热电站土厂房和主要生产车间最小风赖1.风侧,并有方便的运输条件。3.2.4.3主厂房及烟函荷载较人,应布置在地质条件较好,地基承载力较高的地段。3.2.4.4室外变电装置的布置应注意高压线迹出线的方便,并应与散发烟尘和腐蚀性气体的车间有适当的防护距离
3.2.5给水处理设施般靠近用户布置.并应避免生产区粉尘、有害气体及污水影响水质。3.2.6循环水系统应布置在通风良好的地段,不宜布置在变配电室,露大生产装置的冬季主导风向的上风侧。
3.2.7机修、仪电修可集中布置:其周制要留有室外作业和物料堆存场地不应布置在散发腐蚀性气体车间的下风侧。
3.2.8成品包装库(成品包装工段)宜用廊道与制盐车问相连,并应布置在运输方便的地方。3.2.9办公楼、食堂、汽车库、浴案、哺乳空门卫等厂前区设施,应布置在散发烟尘和腐蚀性气体车间复季最小风频的下风侧。厂前区的建筑可适当合并,相应绿化,与城镇及居民区联系方便。3.3通道及间距
3.3.1真空制盐厂厂区内通道的宽度,应满足下列要求:456
QB60081995
3.3.1.1通道两边建筑物、构筑物、露天设备防火、防爆、卫生间距的要求。3.3.1.2地上地下管线、交通运输线路及绿化设施所需要的觉度。3.3.1.3主要通道的宽度宜与两侧筑物高度相协调。厂区内通道的宽度宜符合表1的规定。表1厂区通道宽度
制盐厂规模,万吨/年
主要通道
通道宽度:m
注:通道内管线及运输线路较多,且地形复杂或气候影响时,可采用上限。次要通道
12:~18
3.3.2厂区内相邻建(构)筑物及堆场的防火间距应按现行《建筑设计防火规范》执行:改扩建厂执行防火间距确有困难时,应与当地有关部门协商确定。3.3.3个别相邻建(构)筑物及堆场按防火间距布置有困难时,应与当地有关部门协商确定。3.3.4相邻建(构)筑物的卫生间距应按现行的“工业企业设计卫生标推》执行。3.4技术经济指标
3.4.1总图布置及运输设计的技术经济指标,一般包括下列内容:3,4.1.1厂区占地面积:厂区.用墙内的面积,按围墙轴线计算,单位以ha 计。3.4.1.2建(构)筑物占地面积:设计的建(构)筑物外轮廊面积,单位以m2计。初步设计可按建(构)筑物外壤轴线计算,圆形拘筑物按内径计算。施工图按建(构)筑物外墙的外包尺寸计算。3.4.1.3露天堆场或作业场地占地面积:固定的露天堆场或操作场地,单位以m2计。有基础的露天堆场,占地面积算至基础外轮廓线。3.4.1.4道路及广场占面积:道路及广场的铺面积(包括车间引道、人行道回车场、停车场等),单位以m2计。
3.4.1.5厂内铁路长度:厂内铁路所有股道长度的总和,单位以km计。3. 4, 1. 6土石方工程量;厂区土石方的填方和挖方的总和(包括场地整平,建(构)筑物基础余十、道路路槽挖土,管道、管沟余士等),单位以㎡\计。3.4.1.7厂区建筑系数:为建(构)筑物占地面积与露天堆场、作业场地占地面积的总和除以厂区占地面积乘100%。
3.4.1,8场地利用系数:为建(构)筑物、露天堆场、作业场、铁路与道路、地上地下管线、散水等占地面积的总和除以厂区占地面积乘100%。3.4.1.9绿化系数:为厂区绿化覆盖面积除以厂区占地面积乘100%。绿化覆盖面积即全厂绿化面积总和,单位以㎡计,计算时,重点绿化区的成片绿化,按实际几何面积计算:行道和单植绿篱,按树冠外缘宽度乘长度计算,单梢的乔,灌木,按树冠正投影面积计算。3.4.2真空制盐厂厂区的建筑系数宜为 25%~30%,场地利用系数不宜低于50%,绿化系数应不低于10%
4 工艺设计
4.1一般规定
4.1.1真空制盐工艺设计,必须根据原料卤水条件和产品质量要求,制定生产方法和计工艺流程。4.1.2真空制盐的原料卤水分为天然卤水和人工卤水。除氟化钠以外,其他组分以硫酸钠为主的称为硫酸钠型卤水;以硫酸钙为主的称为硫酸钙型卤水;以氯化物为主的称为氯化物型卤水。457
QB6008—1995
TTTKAONIKAca
4.1.3在工艺设计中,对原料卤水中的其他有用组分,凡有T业利用价值的,应同时考虑综合利用,4.1.4精制盐质量应达到国家标准GB5461优级或一级精制盐标准;无水硝成品质量应达到国家标推GB6009一级或一级工业无水硫酸钠标推。4.1.5一般情况下原料卤水中氯化钠和其他组分总含量不宜抵于300g/I.。4.1.6真空制盐厂为连续性生产,在各项衡算中,每夜生产时问按21h为计算依据。考患设备结垢清洗与生产操作变化,设计波幅取10%~15%。4.1.7设计采用的实际生产日数,应根据项目实际情况确定,-殷每年为300-~330.3天,年生产时间7200-~8000h.
4.1.8制盐单套装置的规模,应竖持人型化方向,一般采用10.15.20,30万吨/年,4.1.9制盐工艺设计所需各种数据必须可靠,指标必领先进可行。4.2牛产方法
4.2.1生产方法的确定要在4,1.1条原则基础1.,根据技术先进可靠性和经济合理,经多方案比选确定,
4.2.2原料卤水宜逊行净化处理,除去钙,镁离子.通常采用石灰-芒硝-二氧化碳法、石灰-纯碱法或烧碱-纯碱法,应根据技术经济比较选定。条件不具备时,硫酸钠型卤水采用热法提硝可结合除钙;硫酸钙型卤水宜采用石晶种法防垢,以减轻传热管璧结垢,延长潮周期。4.2.3原料卤水中含有较高硫化物,将加剧制盐设备、管道的腐蚀,含有过量钡、铅等有害组分会影响成品盐质量,都必须进行化学净化处埋。4.2.4卤永净化车间(或工段)宜单独设置,并相应包括各处理工序。4.2.5硫酸钠型卤水,硫酸钠含量一般为15~30g/L,宜采用热法提硝。在此范国外的宜采用冷法提硝。
4.2.6热法提硝,采用原料卤水或净化后卤水洗涤制盐系统排出的盐浆,得到含硫酸钠人于70g/L的洗盐卤水:作为提硝原料:洗盐卤水升温盐析或蒸发)后,母送制盐系统作原料。末净化的卤水,洗盐过程生成的含钙硫酸盐复盐颗粒较细,可结合除钙过进行处理,母藏回收法是制盐蒸发系统控制硫酸钠始终处于饱和点以下,并连续从制盐蒸发末效排出母液,于独立的问收系统向收母液中所含的氯化和蔬鞍钠。
4.2.7冷法提硝,在原料卤水或净化后卤水含硫酸钠大于40/1.时,直接作提硝原料;硫酸钠含量较低时,应以制盐系统排出的含硫酸钠大干 45 /L 的盘液作为提硝原料。提硝踪料卤水经冷冻析硝得到芒硝母液送制盐系统作原料。4.2.8制盐生产方法为:原料卤水经蒸发结晶、离心脱水、沸腾下燥得到成品精制盐。制盐车间包括蒸发,脱水与干爆工序。硫酸钙型卤水采用石膏晶种法时,相应增加石旁处理工序。4.2.9热法提硝生产方法为:洗盐卤水经升温盐析、沉降分离、离心脱水、气流或沸腾干燥得到成品无水硝。热法提硝系统宜作为提硝工段附设于制盐车间,提硝工段包括盐析、脱水与干燥工序,4.2、10冷法提硝生产方法为:提硝原料卤水经冷冻析硝、沉降浓缩、真空过滤、热熔蒸发、离心脱水、气流或沸腾干燥得到成品无水硝。提硝车间包括制冷、冷冻、过滤.蒸发,脱水与干燥工序。4.2.11成品精制盐与无水硝的包装储运系统一般采用机械化的计量包装与转运堆码生产线。包装储运系统包括输送,计量、包装与外运工序。4.2.12真空制盐厂原料卤水中氧化钠总间收率应达到85~95%,硫酸钠回收率60%~90%。4.3工艺流程
4.3.1工艺流程应根据原料卤水组成、产品质量标准及产品品种要求、生产方法及项目外部条件进行设计,并要求技术先进成熟和良好的经济效益。4.3.2工艺流程的设计,在保证产品质量和技经指标条件下,应力求简化和缩短流程,充分考虑节约能源措施,
QB 6008—1995
4.3.3T艺流程的设计,必须考虑装设必要的计量及自动控制仪表,以提高生产管理水平。4.3.4丁艺流程的设计,必须考虑生产废液、废渣的利用,尽量减少废液、废道、废气的排放量,搞好综合利用稚环境保护。
4.3.5工艺流程设计的具体要求,按照卤水净化、制盐,热法提硝、冷冻提硝、盐石膏的利用五部分分别说明:
(1)卤水净化
4.3,6采用石灰-芒硝-一氧化碳法除去钙,镁离子的两段净化流程。第一段为原料卤水和事先配好的石灰乳在反应器内进行反应,沉降分离氢氧化镁和硫酸钙(一次泥)的清液;第二段在碳化器内,用石灰蜜气或烟道气进行碳化除钙反应。就降分离碳酸钙(二次泥)后的清液通常称作精卤,作制带原料。为了加速一、二次泥的沉降,需人絮凝剂,白备石炭密时,石灰右的质量应符合下列指标:石灰石:含碳酸钙(CaCO,)>92%含碳酸镁(MgCO)<2%
含二氧化硅(SiO)2%
有灰穿气经净化后,便气体含尘量低于50mg/1可供二段除钙反应之用,4.3.7卤水净化来用石灰、纯碱法,应根据卤水中的钙、镁离子含量,经过技术经济对比,决定采用一段静批或三段净化流程。
-段净化,在原料卤水中一次同时加人石灰乳和纯碱溶液,沉降分离反应所生成的钙镁泥后可得精卤,采用二段净化·先在原料卤水中加人石灰乳除镁,经澄清后的清液,加人纯碱羧除钙,生成的碳酸(二砍泥)转人一段净化.形成钙镁泥(一次泥),经沉降可得精卤。4.3.8硫化物含量高于0.1名/I的天綫卤水,采用空气吹出-氯气氧化-石求、硫代巅较钠还原净化处理流程。硫化物含量低于0.1g/L的原料卤水,宜采用电化法除硫化氢。净化后的卤水硫化氮含量在2. 5 mg/L 以下。
4.3.9含有过量钡的天然卤水,如含钡黄卤,除钡流程是与含有部分碗酸根的岩盐卤混合反应,生成硫酸钡沉淀,经澄清后的卤水作为制盐原料。对含铅的原料卤水,必须用石灰法除销。(Ⅱ)制盐
4.3.10原料卤水或精制卤水在制盐蒸发工序经蒸发结品折出固体盐,其他有用组分浓缩富集后的母液排出作为提取副产品的原料。4.3.11蒸发工序一般采用四效或五效蒸发流程,加压与多效蒸发并用流程.在有廉价电力的地区可考虑采用机械加压蒸发,应通过热力方案平衡计算、节能与综合技术经济比较来决定,并相应选定热电站配套方案:
4.3.12蒸发T.序应尽量利用热电站的低压饱和蒸汽,不足部分可用减压蒸汽补充。生蒸汽冷凝水经适当降温后送回热电站作锅炉给水;二次蒸汽冷凝水用作锅炉补充水时,应采取必要措施,保证水质符合锅炉水标准及有关规定
4.3.13为进一步提高多效蒸发系统热效率、达到热法提硝对于洗盐卤水预热温度的要求,除充分利用各效冷凝水余热外,宜适当捆取客效二次蒸汽预热进罐卤水或洗盐卤水。4.3.14为减轻卤水的蚀和提高蒸发设备蒸汽给热系数,经初步预热的卤水或盐析析硝后的树液宜进行真空脱氧。
4.3.15蒸发加料操作宜采用平流或逆流平流并用方式,排盐操作宜采用顺流转料,以降低蒸发系统排出盐浆的温度,减少热能损尖。硫酸钙型卤水制盐,采用石膏晶种防垢-排盐时宜将石宵返回各效蒸发爆,使各效固相中石寓含量保持15~30g/L,4.3.16为了提高成品盐质量,盐浆应进行洗涤。硫酸钠型卤水宜卧式搅拌槽或立式洗盐器内进行两级逆流洗漆,硫酸钙型卤水制盐宜在立式洗盐器中洗涤分级:459
QB 6008—1995
TYKAONYKAca
4.3.17脱水工序中,盐浆应经水力旋流器增稠器增浓后直接或通过搅拌槽向离心机喂料,经离心脱水,湿点含水量在4究以下,滤应回收。4.3.18干燥工序应采用沸腾干燥冷却设备,以降低成品盘的温度。于燥后,成品盐含水量应符合质量标推。干燥尾气应通过两级除尘设备回收粉尘。(皿)热法提硝
4.3.19硫酸钠型卤水末除钙、镁离子直接制盐,为了保证成品无水硝的质量,在热祛提硝过程,必须进行高温除钙。洗盐卤水预热至95~100℃,将高温析出物分离,可达到除钙目的。4.3.20盐析工序加盐操作,宜入干燥后的固体盐。可采用制盐T燥工序下式除尘器间收的粉盐,并设置必要的计量输送装置。可直接加入盐析结晶器(盐析槽),也可在搅拌槽与洗盐卤水混合成浆料后加人盐析结晶器。采用蒸发析硝时.可将预热升温后的洗盐卤水引入蒸发结晶器,蒸发水分,析出无水硝。
盐析硫酸钠以后的料液进行沉降分离,澄清的高温盐析后母液(盐析母液),经真空脱氧后去制4.3.21
盐,无水硝浆送脱水工序。
4.3.22脱水工序中,无水硝浆经离心机分离得到粗硝(指含有一定杂质),加人硫酸钠溶液或少量淡水洗涤除去氣化钠,经离心机二饮脱水。4.3.23干燥工序,应根据实际情况,选用气流干燥或沸腾干燥,并采取相应除尘措施。()冷法提硝
4.3.24制冷工序,宜采用单级压缩机制冷流程,氨器中液氨送冷冻工序直接冷冻,在冷冻结晶器蒸发成气氨,送回氨压缩机乐缩,经氨冷凝器玲凝成液氨,返回氨器。4.3.25冷冻丁序,提硝原料卤水必须用析硝后冷母液(或称精卤),预冷至12℃以下,以节省玲量,4.3.26冷冻工序,应考虑冷冻过程芒硝呈过饱和析出。为了减轻冷冻结晶器传热管壁结垢,必须将部分玲冻后母液与芒硝结晶同流,与原料卤水混合,添加芒硝晶种,以降低冷冻结晶过程硫酸钠的过饱和度。
4.3.27由于冷冻后母液中硫酸钠星过饱和状态,应在其有足够容积和面积的增稠器中,进行芒硝结晶的生长和沉降。
4.3.28为了保证成品无水硝的质量,可用淡水洗涤芒硝,亦可在芒硝热溶蒸发系统排放一定量氯化钠含量高的母获。
4.3.29蒸发工序,芒硝热溶宜采用末效蒸发罐母液或离心机滤液,应避免采用生蒸汽作为热熔热源,4.3.30蒸发工序,宜采用多效蒸发流程或热压缩蒸发流程。4.3.31无水硝的干燥,宜采用气流或沸腾干燥流程。()裁石荐的处理
4.3.32为了充分利用资源,对于未除钙、镁离子的硫酸钙型卤水,在制盐过程所产生的盐石膏应回收利用。将制盐蒸发排出的石膏与盐在分级器中避行初步分离,4.3.33将石膏将在品形转化器中转化为二水石膏。经水洗和过滤的湿料,可作石膏制品的原料。4.4技术参数与指标
4.4.1设计中采用的回收率应符合 4.2.12的要求,4.4.2采用卤水净化时,净化卤水应达到下列指标:Ca*+ -20 mg/I.
Mg*+<10 mg/L
4.4.3蒸发经济(t水/t生蒸汽)不得低于下列指标:制盐(多效蒸发)
提硝(多效蒸发)
4.4.4蒸发与换热设备传热系数,/(m2,K),不宜低于下列指标:460
制盐蒸发:净化卤水
未净化
换热设备:汽液
被液(列管式)
液液(板式)
4.4.5卤水净化主要操作控制参数如下:石灰窑密加料,石灰石焦碳配比100:8QB 6008—-1995
1 800--2 900
1 200~-2 100
500~700
250~~350
900--1 100
氢辑化钙或氮氧化钠过量 0. 05~0. 10 g/L碳酸钠过虚0.2~0.3g/
4.4.6制盐主要操作控制参数
原卤预热温度(只用冷凝水预热)第一效蒸发罐进汽压力(绝压)
末效二次蒸汽压力(绝压)
气压式冷凝器进水温度
>50℃
300~450kPa
制盐母液(作为冷冻提硝原料)含硫酸钠量>45g/L进离心机浓度
脱水后湿盐含水量
沸腾干燥热风温度
成品盐含水量
4.4.7热法提硝主要操作控制参数:洗盘卤水含硫酸钠量
洗盐卤水预热温度
盐析母液含氮化钠量
、粗硝洗涤加水量
离心机进料浓度
脱水后湿硝含水量
干爆装置热风温度
成品无水硝含水量
4.4.8冷冻提硝主要操作控制参数:氨冷凝器冷凝温度
卤水预冷冻温度
卤水冷冻温度
氨蒸发器蒸发温度
氨压缩机排气温度
析硝母液含硫酸钠量
过滤后混芒硝含游离子分量
芒硝热溶温度
>60%(重量)
24%(重量)
>130℃
>70 g/L
95~100℃
300~-305 g/1.
150~300kg/t
60%(重量)
5%(重量)
>130℃
10~12℃
--4--2℃
—10~-15℃
100℃
10~12 g/1.
10%(重量)
第一效蒸发罐进汽压力(绝压)300~400kPa气压式冷凝器进水温度
蒸发过程析硝母液含氯化钠量
离心机进料浓度
脱水后湿硝含水量
100 g/L
>60%(重量)
<5%(重量)
于燥装置热风温度
成品无水硝含水量
QB6008-1995
>130℃
TTTKAOIKAca
4.4.9生产车问用水,分为三类,即冷却用水、生产用水和生活用水,应达到相应水质标准和供水压力。4. 4.9. 1冷却用水;用于蒸发工序蒸发缠木效二次蒸汽冷凝和制冷工序氨冷避器的气氨冷凝,其水质指标:
pH值.6.5~8.5
水温:不超过32℃
肉眼而见物:水中无明显的泡沫、油膜及泥砂等杂物。色:无异色
臭和味:无异臭和异味
4.4.9.2生产用水:用于各工序生产过程补水,洗涤及设备冷却,其水质指标:悬浮物:不超过 5 mg/1.
色:透明,亦不呈其他异色
臭和味:小得有兄臭兄味
pH值:6. 5~8. 5
总硬度(以碳酸钙计):不超过180mg/L铁不超过 0. 3 mg/L
锰 不超过 0. 1 mg/I
铅不超过 (. 05 mg/ L.
神不超过 0. 05 tng/L
4.4.9.3生活用水,水质应达到国家《生活饮用水卫生标准GB5749,4. 4. 9. 4 供水压力一般采用:冷却用水压力(表压)
生产用水压力(表压)
生活用水压力(表压)
150--200 kPa
200--300 kPa
150-~250 kPa
4.4.10生产车闯用汽一般为低压蒸汽,采用以蒸汽为动力源的机械加压工序时,需要提供中压或次高压蒸汽。生产用低压燕汽参数-般采用:蒸发装置加热汽压力(绝压)300~~450kPa干燥装置加热蒸汽压力(绝压)400~700kPa4.5设备选型
4.5.1必须选用先进、成熟或经过技术鉴定的新设备。4.5.2应结合真空盐厂生产实际情况,选择机械化程度和效率较高、能耗较低的大型化设备:并应考虑不断提高自动化水平。
4.5.3选用设备时必须考虑易于操作和拆装,结构较简单,制造较容易,易损零件容易更换,维修方便;同时,设备的材质要适应生产过程物料性质的要求。(I)卤水净化
4.5.4自备石灰窑,应采用竖式,窑容积按二氧化碳实际用量的1.2~~1.4倍选取,容罩大的窕送料设备宜采用垂直斗式升运机;较小的窑宜用结构简单的倾斜式升运机。4.5.5窑气或烟道气洗涤净化宜采用泡沫塔。4.5.6石嵌消化设备宜采用机械化灰机,消化时间可按15~-20mi1n选取。石灰除砂机一般选用惯性式高频振动筛将石灰乳中的石块与砂粒筛分出去。4.5,7除镁与加纯碱除钙的反应器,宜采用立式带搅拌的钢制圆槽,加二氧化碳除钙采用锥形碳化罐。4.5.8钙、镁泥沉降.宜采用连续沉降器,钙、镁泥过滤宜采用外滤面转鼓真空过滤桃或板框压滤机,162
(Ⅱ)制盐
QB6008—1995
4.5.9制蒸发,宜用外加热式强制循环蒸发罐。4.5.10外加热式蒸发罐配套循环泵,宜采用卧式轴流泵。4.5,11末效二次蒸汽冷凝设备,可采用混合式冷凝器。抽真空设备可采用机械真空泵、蒸汽喷射泵。4.5.12各级卤水预热器,宜选用多程列管式换热器。为充分利用低位冷凝水余热,可采用板式换热器,以获得较好的节能效果。
4.5,13原料卤水的储存,可采用方形与圆形钢筋混凝土池或圆形钢储槽。储存容积,根据采区室厂区输卤管道长度与材质决定,一般为1~2大的用盈。4.5.14料液的输送设备,应根据物料性质、流量及要求达到的扬程选取,为保证连续生产,宜适当考虑备用。
4.5.15湿盐与下盐的愉送设备宜来用带式输送机,4.5.16盐浆脱水,宜采用卧式活塞推料离心机、螺旋推料离心机或卧式锥篮离心机。有多台离心机时,宜配置检修用起重设备,其能力应以离心机的不可拆部件巾的最大件的重量来考虑。4.5.17盐的干燥设备,宜采用玲热床沸腾干燥器,冷床面积般为热床面积的30%~50%;干燥筛分设备,宜采用振动筛:除尘设备,宜采用旋风及湿式除尘器。4.5.18洗盐设备宜采用卧式螺旋带搅拌槽或立式洗漆桶。(Ⅲ)热法提硝
4.5.19盐析析硝设备宜采用卧式螺带搅拌槽、盐析结晶器,并配套加盐用穿积式或重量式计量装置。蒸发析硝宜采用蒸发结晶器。
4.5.20无水硝沉降浓缩设备宜采用连续沉降器。4.5.21无水硝浆脱水可采用立式、卧式刮刀卸料离心机或卧式活塞推料离心机。4.5.22湿硝干燥可采用沸腾于燥冷却器或气流干燥器。除尘设备宜采用旋风及湿式除尘器。(I)羚法提硝
4.5.23制冷设备宜选择活塞式或螺杆式氮制冷压缩机,并考患必要的备用机台。4.524原卤预拎器宜采用卧式多程列管式换热器或板式换热器。4.5.25冷冻结品器宜采用列管式氨蒸发器或循环式冷冻结晶器。采用列管式氨蒸发器时,应增加兑卤系统,以降低料液饱和度,并添加晶种。4.5.26蓝硝沉降浓缩宜采用连续沉降器或圆薇型沉降器,保证足够的停留时间。4.5.27芒硝过滤宣采用外滤面转鼓真空过滤机,可采用水环式真空泵或水喷射泵抽真空。4.5.28芒硝热熔宜用机械搅拌槽。4,5.29硝液蒸发应采用外加热式强制循环蒸发罐,配置卧式轴流泵。无水硝浆脱水宜采用卧式活塞推料离心机,4.5.30
4.5.31湿硝干燥可采用沸腾干燥器或气流干燥器。()盐石膏利用
4.5.32盐与石膏的分离官宦用立式水力分级槽.石言的沉降浓缩可用斜板沉降器。4.5.33盐石膏的石膏转型可用立式搅拌桶。二水不膏的过滤可采用圆盘真空过滤机。4.6设备布置
4.6,1根据已确定的T艺流程及选定的设备进行布置,4.6.2设备布置应在满足生产操作、设备检修和餐道布置的前提下,力求紧凑减少占地面积,4.6.3厂房的柱距和跨度,应根据主要设备外形尺寸、设备布置的合理间距,操作面的要求以及设备组合方式等因繁,并结合土建模数合理确定。4.6.4厂房净高的确定.应考虑楼面的设备,管遵安装的需要和便于检修。46.5设备布置,要尽量满足通风采光的要求,充分利用白然通风与来光。高大设备千宣靠衡布置:设463
QB6008—1995
备布置在门窗和楼梯附近时,不得妨碍门窗的开启和阻碍通行。TTTKAONIKAca
4.6.6操作频繁的主要生产设备的操作面.应有良好的通风采光条件。散发热量较多的设备操作面应加强通风降温。
4.6.7同类型的设备宜集中布置,便于设备轮换、调配使用与维修。1生条件差的设备亦宜相对集中布置,防止污染扩散。
4.6.8震动大的设备应避免布置在楼面;噪音大的设备应采取消声或隔离措施,地面设备尽量避免布置在地坑中,以利于车问清洁卫生,4.6.9车间内各层楼面应设吊装孔和预埋吊钩,外墙在需要时可预留墙孔,供设备安装或日常检修之用。留孔大小,根据最大吊件的外形尺寸确定。4.6.10根据操作和检修的需要,部分设备应合理布置操作台,其高度、宽度、通道与梯子应符合操作和检修的有关要求,
4.6.11车间大门、便门的大小和位置,应根据用途、性质、最大设备部件的外形尺寸及车辆人流情况合理设置
4.6.12车间化验室应布置在采光条件好、干爽,不受噪音与震动影响以及便于到现场取样较为方便的地方。主车间宣设置必要的生活卫生设施。:(I)卤水净化
4.6.13卤水净化设备宜单独设置为午间或工段布置。4.6.14钙、镁泥的沉降设备应露天布置,与厂区总平面布暨协调一致,并注意尽堡碱少占地面积。化灰机、二氧化碳压缩机、各种料液泵、反应器宜布置在室内,过滤设备宜布置在二层或操作平台上。4.6.15化灰机灰乳桶、灰乳储桶、反应器等设备应布置在-起,设备间距尽量紧凑,缩短灰乳管道长度。碳化应集中布置,并设置操作层或平台。4.6.16本车间(丁段)用电负荷集中在二氧化碳压缩机间和料液泵房,配电间应靠近负荷中心。(Ⅱ)制盐
4.6.17制盐车间蒸发、洗盐、脱水与干工序宜布置在同一建筑物内,并有良好的通风和采光。4.6.18蒸发工序厂房多采用二层或三层布置,楼面高度应根据设备的外形尺寸、安装、操作、维修需要的空间决定·蒸发室和加热室可支承在不同标高的框架或支架上。4.6.19燕发罐可来用半露天布置,即蒸发室支承在钢筋混泥士平台上,蒸发罐顶与二次汽管局部露天其余部分布置在室内,
4.6.20蒸发设备的操作面应有足够的宽度,有视镜的蒸发罐,操作面的最小宽度以人站立并能观察到最高视镜液面距离为准,其他设备操作面觉度应能满足操作、检修和生产联系的需要。设备旁的人行过道净空一般不小于800mm
4.6.21蒸发工序楼面,在适当位置设置设备吊装孔,其尺寸应大丁最大吊件外径400~800mm。4.6.22洗盐、离心脱水工序宜紧邻蒸发工序,离心机宜布置在楼面上,湿盐胶带输送机可布置在操作平台或地面上,洗盐槽、滤液槽与料液泵等设备它布置在地面,楼面高度应无于4m,操作平台高度应大于311,离心机操作层层高应大于4㎡。4.6.23离心机操作面宜靠窗布置,并有足够宽度,离心机间距应能满足操作、安装和维修的要求。4.6.24脱水工序楼面应预留吊装孔,以满足离心机整机吊装的要求。4.6.25十燥工序温度较高,一般宜作单层厂房布置,留有足够的风空间。如必须布置在多层厂房的层·应考虑适当的层高。
4.6.26湿物料胶带输送机输送角度应<18°,采用溜槽进人沸腾干燥冷却器时,流送坡度应>45°。4.6.27沸腾干燥器配套风机宜集中设置在风机室内,以降低车问噪音。4.6.28干燥尾气除尘设备的布置应尽量简化和缩短风管。4.6.29沸腾干燥器应设置操作平台。464
(山)热法提硝
QB 6008-1995
4.6.30热法提硝作为一个工段,结合制盐系统布置在同一厂房内。热法提硝工段若单独设置时,应尽量靠近制盐车间尘厂房。
4.6.31盐析工序温度较高,且散失一定量蒸汽,在盐析槽加盖密闭与设置排汽管措施外,本工序应单独隔开,并尽量散开布置,以改善通风条件。燕发析硝可与制盐蒸发罐的布一并考虑。4.6.32无水硝沉降器宜布置在室外,硝浆泵、母液某宜就近布置在沉降器下面。4.6.33脱水与干燥工序可参照制盐部分有关条文布置。()冷法提硝
4.6.34冷法提硝应独立设置一个车间,根据总平面布置要求,各T.序可布置在--座或两座建筑物内。4.6.35制冷工序应设罩在底层,氨制冷压缩机布置在厂房内:人部分辅机可布實在室外,出于车用电负荷集中在本工序,车间变电间应紧靠制冷工序。4.6.36氢制冷压缩机布置应充分考虑运行、管理与维修方便,操作阀门与就地仪表应面向主要操作通道。
4.6.37氨冷凝器的安装商度,应保证冷凝的液氨能自动流入贮氢器,立式冷凝器应设置操作平台,以利操作与除垢。此氨器应有谌阳设施。4.6.38冷冻工序宜设置在二层,兑卤槽与料液藜宜布置在底层,预羚器可布置在室外。预冷和冷冻设备操作面的宽度应能满足操作与维修的要求,并设置排水管沟,将清洗设备的废水排人厂区排水系统。4.6.39冷冻工序楼面所留吊装孔,应能满足设备整体吊装的要求。4.6.40制冷与冷冻工序,在生产中,其在设备检修时可能有少量氮气逸出,应强通风,相应设置机械强制通风装置。
4.6.41芒硝沉降器宜设置在室外,浓缩后芒硝浆储存槽及硝浆泵、母液泵宜就近布置在沉降器下面。4.6.42芒硝真空过滤机应布置在二层,真空泵、热熔槽、料液浆等设备宜布置在底层。4.6.43蒸发、脱水与干燥工序参见制盐部分有关条文。(V)盐石膏的处理
4.6,44石膏晶形转化器、盐与石膏分离设备宜露天布置,二水石膏的过滤设备、真空泵,料液泵等宜布置在室内。
4.7管道布置
4. 7. 1 生产车问工艺管道设计压力为 8~~3 000 kPa(绝压),设计温度为—15~~180℃。4.7.2管道直径应根据输送介质的特点、流量和常用流速进行计算,并考虑生产波动、阻力摄失、积垢和管子规格等因素确定。
4.7.3常用介质流速宜按表2数据选取,表2常用介质流速表
卤水、母液
盐浆、硝浆
石灰乳
生蒸汽
二次蒸汽
冷凝水
生产用水
冷却用水
介质名称
1. 0~-2. 0
0. 5~1. 0
25 ~ 80
0. 5 ~1. 5
1. 2--2. 0
1. 5-~2. 5
疏速范围·/s
医缩空气
介质名称
密气,烟道气(C)
管材的选择应符合下列规定:
QB6008-1995
表2(完)
c. 5 -1. 0
TTKAOIKAca
流建范围,m/g
车间内输送盐浆,冷凝水、卤水的管道宜采用耐腐蚀材料,其余管道可采用水煤气管(D<100 mm)无缝钢管(Dk=10~500 mim)或卷焊钢管(Dz300 mm)。车间外输卤、输水管道Ⅲ采用钢管,铸铁管或其他耐腐蚀材料管4.7.5选用的各类管子必须符合有关质量标准。管子壁厚应根据介质的特性、使用年限、T.作压力和工作温度等因素确定。
4.7.6管道布置必须满足生,产需要,便于安装和维修,并尽量缩短管线长度,节省材料。管道应尽量架空敷设,架空管道经过车间人行道上方,最小净空高度为2.2 m。在不影响操作的条件下,部分管道可沿地面、埋地或在地沟内敷设。4.7.7管道布置不应妨碍建筑物的使用及门窗的启闭,不宜影响室内采光,不宜通过电动机、配电盘、仪表盘的上方。管道应尽量沿墙和柱敷设,以便于支承,并考建筑物对管道荷载的支承能力,管道不宜穿过建筑物的伸缩缝、沉降缝。若必须穿过时,应来取相应的技术措施。4.7.8管道布置应同时考虑管道组装、焊接、仪表、附件和保温结构等的安装位置。4.7.9在同一空间布置儿种介质管道,水平并列时,一般应将大管径、保温,非腐蚀性介质的管道布置在上面。制羚压缩机的排气管应布置在逆气管的上面。4.7.10管道的间距根据管道法兰直径大小,并列管法兰安装的形式、保温管道的保温层厚度、管道焊接和支吊架安装的合理位置等因素确定。4.7.11管道在穿墙或楼板时,应预留孔,留孔大小应根据管道法兰大小,保温管道的保温层厚度,并列管道的间距等凶素确定
4.7.12管道安装完毕,除不锈钢管、镀锌钢管、钛管·般不宜涂漆外,其余管道按不同介质分别刷不间颜色油漆,详见表3。
表3管道涂色表
管道内介质名称
齿水、母液
盐浆、硝浆
右炭乳
生产,生活用水
循环玲却水
冷凝水
生产废水
涂漆颜色
小提示:此标准内容仅展示完整标准里的部分截取内容,若需要完整标准请到上方自行免费下载完整标准文档。

标准图片预览:
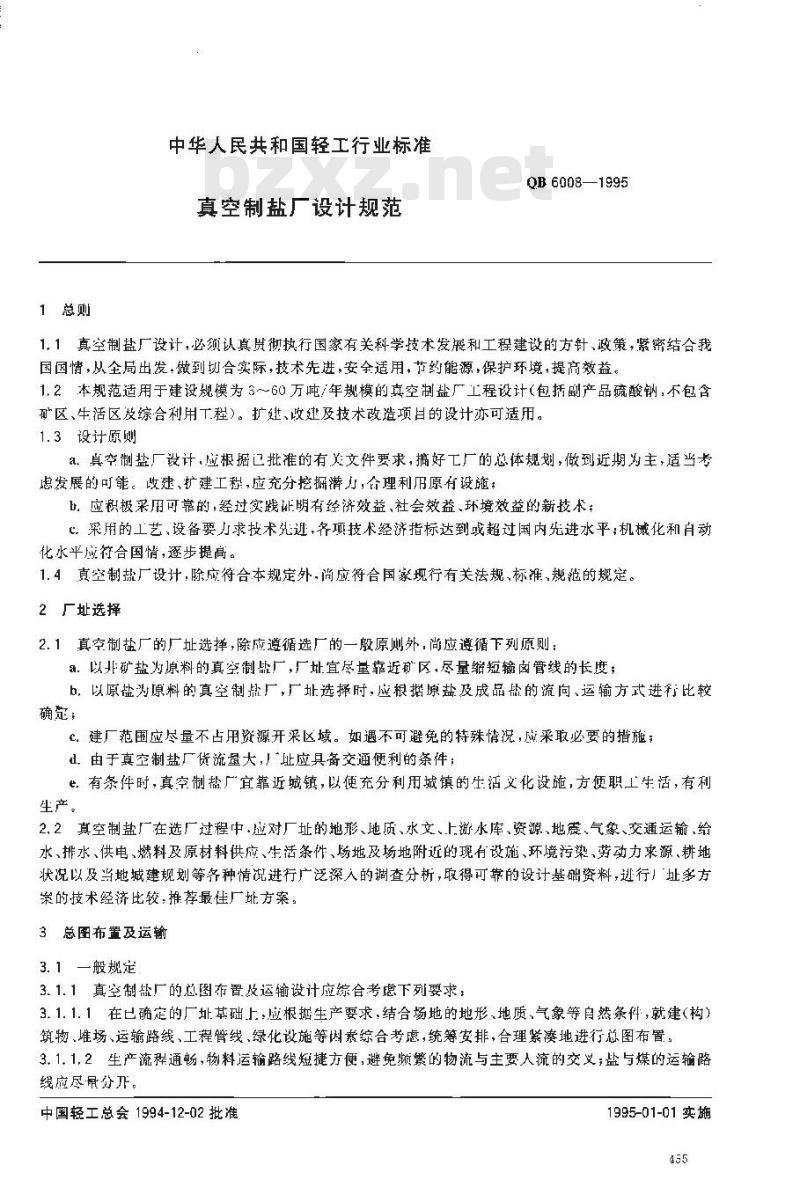
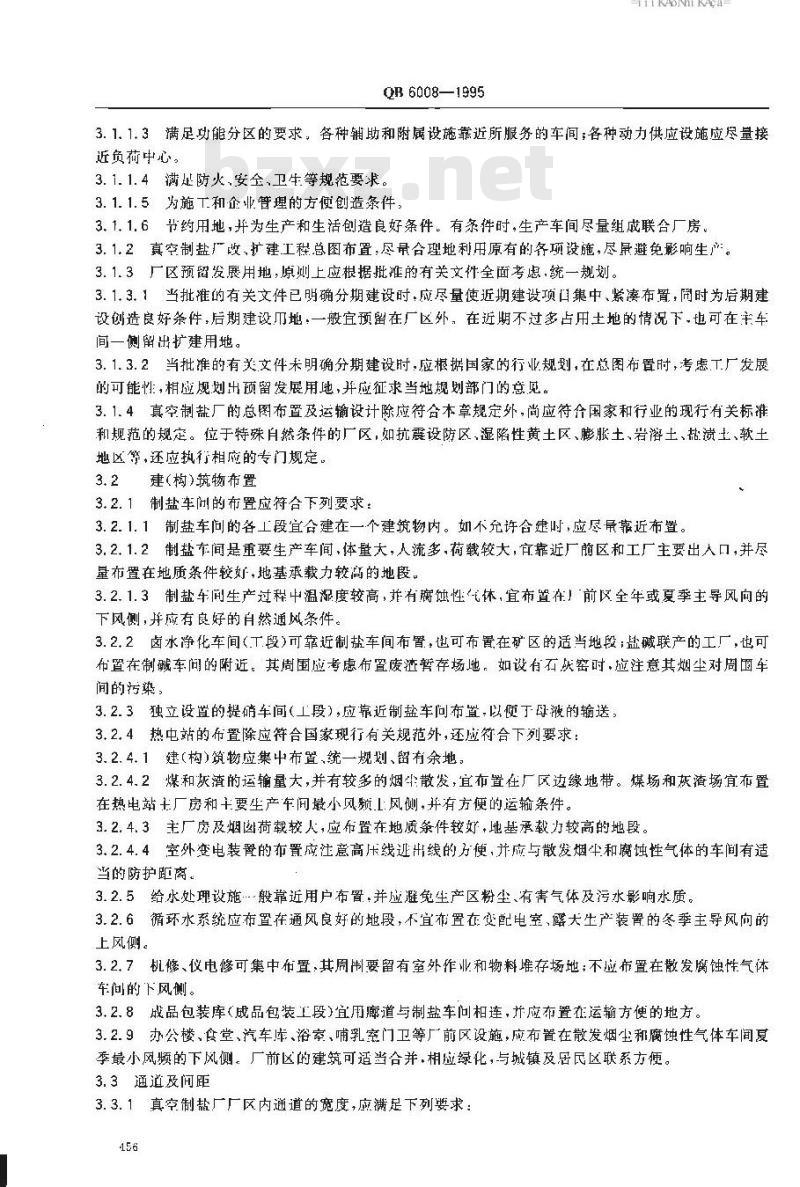
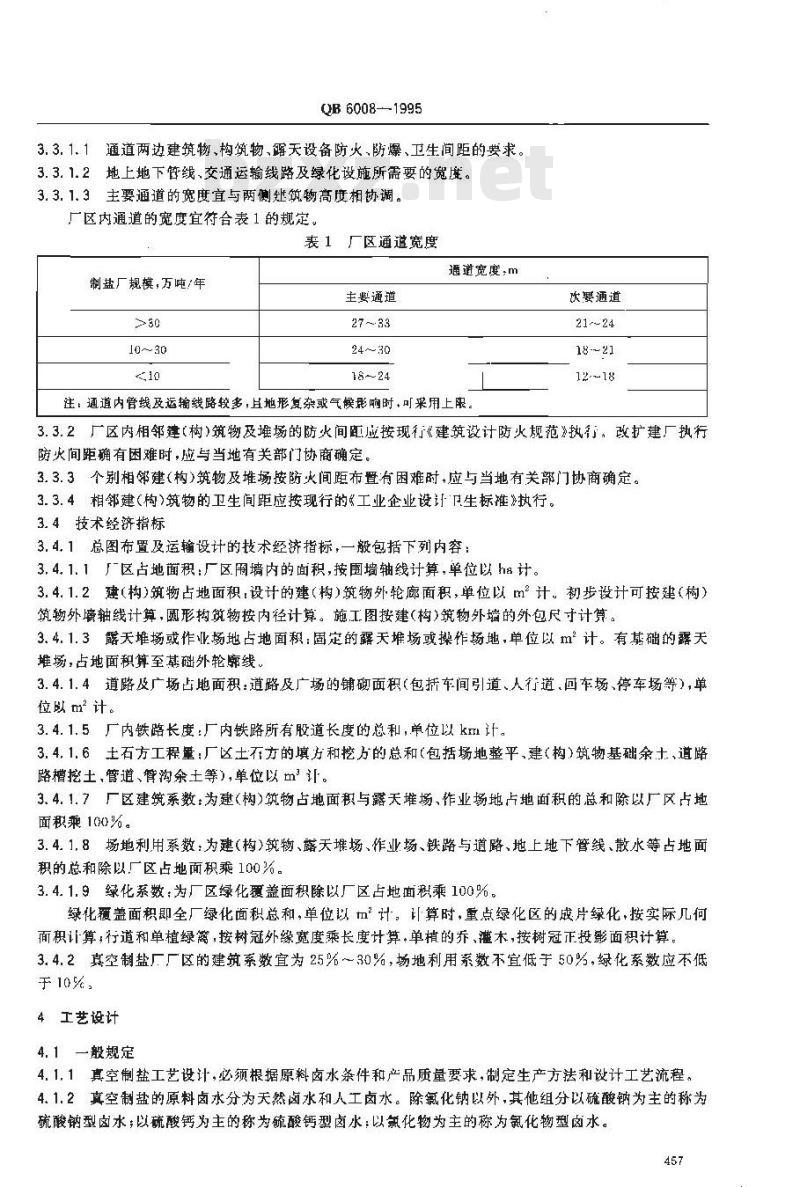
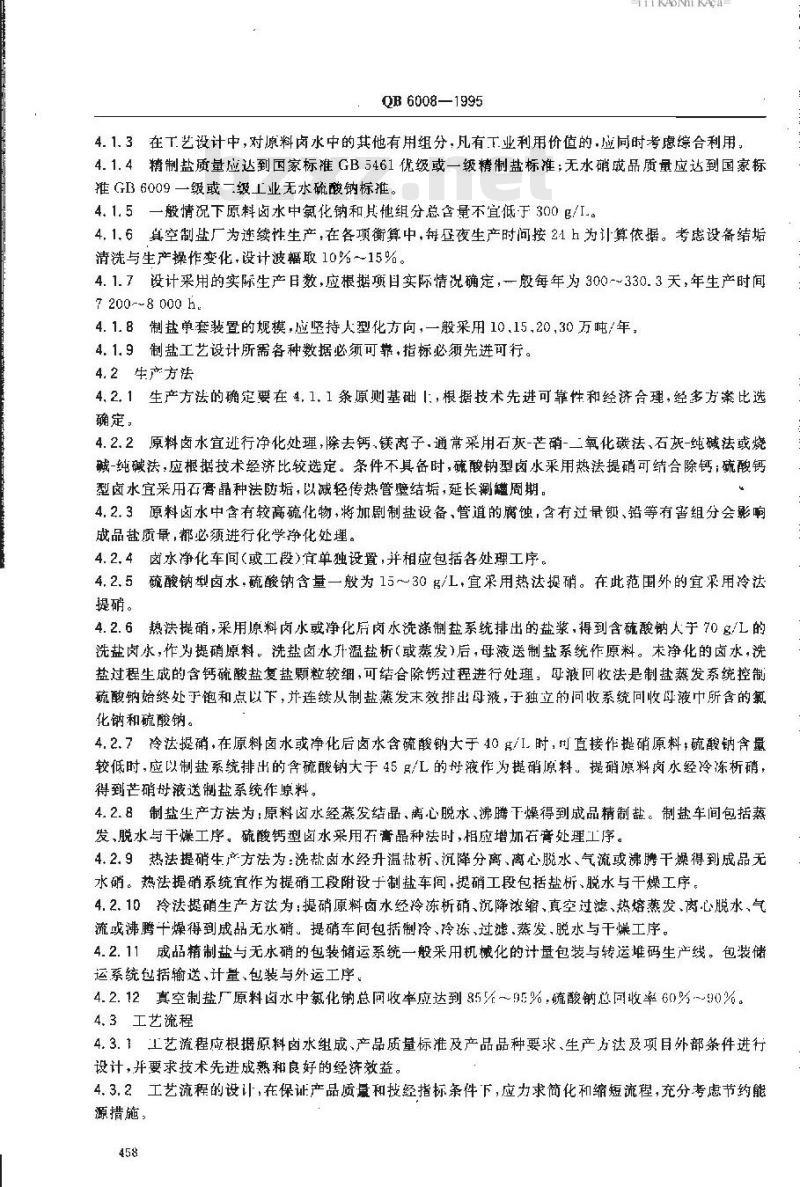
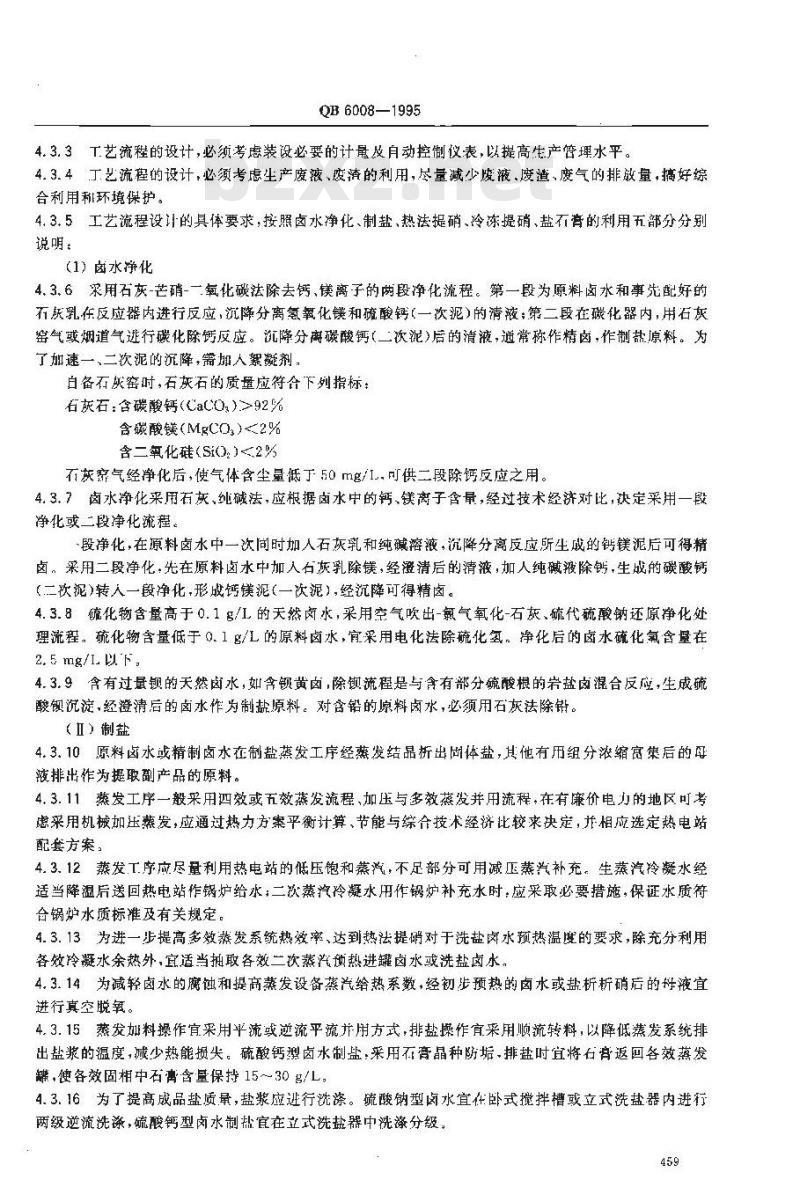
- 其它标准
- 上一篇: QB 6007-1993 合成洗涤剂工厂设计规范
- 下一篇: QB 6009-1995 味精厂设计规范
- 热门标准
- 轻工行业标准(QB)
- QB/T2855—2007 首饰贵金属含量的无损检测密度综合法
- QB6002-1991 制糖专用设备施工及验收规范
- QB/T2613.5-2003 防爆工具防爆用梅花扳手
- GB/T15051-1994 针刺地毯
- QB/T4707-2014 玉米低聚肽粉
- QB1126-1991 聚烯烃填充母料
- QB/T2094.2-1995 伐木锯条
- QB/T2623.1-2003 肥皂试验方法肥皂中游离苛性碱含量的测定
- QB/T2758.2-2005 羽毛球网柱
- QB/T2485-2008 香皂
- QB/T2944-2008 植物生长用荧光灯
- QB/T1472-2013 鞋用纤维板屈挠指数
- QB/T1959-1994 手用缝纫针
- QB/T1720-1993 自行车涨闸
- QB/T2772—2006 笔袋
- 行业新闻
请牢记:“bzxz.net”即是“标准下载”四个汉字汉语拼音首字母与国际顶级域名“.net”的组合。 ©2009 标准下载网 www.bzxz.net 本站邮件:bzxznet@163.com
网站备案号:湘ICP备2023016450号-1
网站备案号:湘ICP备2023016450号-1