- 您的位置:
- 标准下载网 >>
- 标准分类 >>
- 机械行业标准(JB) >>
- JB/T 5000.15-1998 重型机械通用技术条件 锻钢件无损探伤
标准号:
JB/T 5000.15-1998
标准名称:
重型机械通用技术条件 锻钢件无损探伤
标准类别:
机械行业标准(JB)
英文名称:
General technical conditions for heavy machinery Non-destructive testing of forged steel parts标准状态:
已作废-
发布日期:
1998-09-30 -
实施日期:
1998-12-01 -
作废日期:
2008-02-01 出版语种:
简体中文下载格式:
.rar.pdf下载大小:
351.17 KB
标准ICS号:
试验>>19.100无损检测中标分类号:
冶金>>冶金机械设备>>H90冶金机械设备综合
替代情况:
被JB/T 5000.15-2007替代

点击下载
标准简介:
JB/T 5000.15-1998 1.1 本标准规定了超声波、磁粉和渗透三种无损检测方法及质量等级。 1.2 本标准所述各种无损检测方法适用于对各类普通锻钢件进行检测。 1.3 选用本标准后,必须在相应的锻件图样上标明要求探伤的方法种类,具体的探伤部位和不同缺陷类型的质量验收等级,也可另行附加质量验收等级。 1.4 本标准中超声波探伤不适用于曲率半径小于 125mm、探测厚度小于 50mm 锻件的纵波探伤以及内外径之比小于 75% 的环形或筒形锻件超声波横波探伤。也不适用于奥氏体不锈钢等粗晶材料的超声波探伤。 1.5 本标准可能会涉及危害性的材料、操作和设备。本标准的宗旨不在于论述有关使用的安全问题。使用本标准者在使用疥有责任制订有关安全防护和保健实施方法,并应确定有关应用范围的管理条例。 (注: 本标准“磁粉探伤和质量等级”中部分采用 A 275/A275M-86 锻钢件磁粉检测方法 及A 709/A709M-85 磁粉探伤实施方法标准中关于中心导体磁化章节的内容。) JB/T 5000.15-1998 重型机械通用技术条件 锻钢件无损探伤 JB/T5000.15-1998

部分标准内容:
中华人民共和国机械行业标准
JB/T5000.15-1998
重型机械通用技术条件
锻钢件无损探伤
The heaw mechanical gener al techniques and standardsNon-destructive testing of forging1998-09-30发布
国家机械工业局
1998-12-01实施
JB/T5000.15-1998
引用标准·
3定义
4一般要求
超声波探伤及其质量等级
6磁粉探伤及其质量等级
7渗透探伤及其质量等级
附录A(标准的附录)锻钢件横波探伤方法和质量验收要求附录B(标准的附录)质量验收等级的选择2
JB/T5000.15-1998
本标准的附录A、附录B都是标准的附录。本标准由机械工业部冶金机械设备标准化技术委员会提出并归口。本标准负责起草单位:第二重型机械集团公司。本标准参加起草单位:西安重型机械研究所。本标准主要起草人:王国元、范吕慧。I
1范围
中华人民共和国机械行业标准
重型机械通用技术条件
锻钢件无损探伤
Theheavymechanical ganeral tedhniquesand standardsNon-destructivetestingof forging1.1本标准规定了超声波、磁粉和渗透三种无损检测方法及质量等级。1.2本标准所述各种无损检测方法适用于对各类普通锻钢件进行检测。JB/T5000.15-1998
1.3选用本标准后,必须在相应的锻件图样上标明要求探伤的方法种类、具体的探伤部位和不同缺陷类型的质量验收等级,也可另行附加质量验收等级。1.4本标准中超声波探伤不适用于曲率半径小于125mm、探测厚度小于50mm锻件的纵波探伤以及内外径之比小于75%的环形或筒形锻件超声横波探伤。也不适用于奥氏体不锈钢等粗晶材料的超声波探伤。
1.5本标准可能会涉及危害性的材料、操作和设备。本标准的宗旨不在于论述有关使用的安全问题。使用本标准者在使用前有责任制订有关安全防护和保健实施方法,并应确定有关应用范围的管理条例。2引用标准
下列标准所包含的条文,通过在本标准中引用而构成为本标准的条文。本标准出版时,所示版本均为有效。所有标准都会被修订,使用本标准的各方应探讨使用下列标准最新版本的可能性。GB3721—83
GB5097—85
GB 9445—88
GB/T12604.1~12604.6—90
ZB J04 001—87
ZB J04 003—87
ZB Y23084
ZB Y231—84
ZBY232—84
3定义
本标准采用下列定义。
3.1密集区缺陷
磁粉探伤机
黑光源的间接评定方法
无损检测人员技术资格鉴定通则无损检测术语
A型脉冲反射式超声波探伤系统工作性能测试方法控制渗透探伤材料质量的方法
A型脉冲反射式超声探伤仪通用技术条件超声探伤用探头性能测试方法
超声探伤用1号标准试块技术条件在荧光屏扫描线相当于5amm声程范围内同时有5个或5个以上的缺陷反射信号;或是在50mm×50mm的检测面上在同一深度范围内有5个或5个以上的缺陷反射信号。其反射波幅均大于某一特定当国家机械工业局1998-09-30批准1998-12-01实施
量缺陷基准反射波幅。
JB/T5000.15—1998
3.2缺陷引起的底波降低量BG/BF(dB)在缺陷附近完好区内第一次底波幅度BG与缺陷区内第一次底波幅度BF之比,用声压级(dB)值来表示。
3.3其余定义均按GB/T12604.112604.6的规定4一般要求
4.1选择原则
4.1.1检测方法和质量验收等级的选择应就锻件的具体使用和种类确定,并符合相应技术文件的要求。4.1.2凡要求用表面检测的铁磁性锻件,应优先选用磁粉检测方法,若因结构形状等原因不能使用磁粉检测时,才选用渗透检测。
检测档案免费标准bzxz.net
4.2.1当按本标准对锻件进行检测时,必要时可按本标准的规定制定出符合有关规范要求的无损检验规程。
4.2.2检测程序及结果应正确、完整并有相应责任人员签名认可。检测记录、报告等保存期不得少于5年。5年后,若用户需要可转交用户保管。4.2.3检测档案中,对于检测人员承担检测项目的相应资格等级和有效期应有记录。4.2.4检测所用仪器、设备的性能应定期检验,合格后才能使用,并有检验记录。4.3检测人员
4.3.1凡从事无损检测的人员,必须经过技术培训,并按GB9445进行考核鉴定。4.3.2无损检测人员技术等级分为高、中、初级。取得不同无损检测方法的各技术等级人员只能从事与该等级相对应的无损检测工作,并负相应的技术责任。4.3.3凡从事无损检测工作的人员,除具有良好的身体素质外,视力必须满足下列要求:4.3.3.1校正视力不得低于1.0,并一年检查一次。4.3.3.2凡从事表面检测工作的人员不得有色盲、色弱。5超声波探伤及其质量等级
5.1检验依据
5.1.1凡采用本标准时,用户或设计工艺部门应予说明并提供锻件超声波探伤的部位范围和质量验收等级。
5.1.2建立灵敏度的方法、仪器设备的选用、性能的测试等应与本标准中规定一致。5.2仪器设备
5.2.1使用脉冲反射式超声波探伤仪,至少具有1~5MHz的频率范围。5.2.1.1超声波探伤仪的垂直线性至少在屏高80%内呈线性显示,其误差在土5%以内,水平线性误差为土2%。仪器的线性应按ZBY230中要求进行鉴定。5.2.1.2仪器的灵敏度余量应在30dB以上,其测定方法按ZBJ04001中的要求进行5.3探头
5.3.1各种探头应在标定的频率下使用,原则上采用2~2.5MH、晶片直径20~30mm的直探头。2
JB/T5000.15—1998
5.3.2探头主声束应无明显的双峰,声束线偏斜应小于2°。5.3.3各类探头应有相应的AVG曲线图表。5.3.4可更换其他探头来评定缺陷和对缺陷准确定位。5.3.5探头性能测试方法见ZBY231。5.4耦合剂
5.4.1耦合剂应具有良好的润湿性,可使用机油、甘油、浆糊或水作为耦合剂,对于成品锻件推荐使用30号机油作为耦合剂。
5.4.2不同的耦合剂不能进行对比,因此,探伤系统性能测试、灵敏度调节和校正等必须和探伤时使用的耦合剂相同。
5.5试块
5.5.1试块应采用与被检工件相同或近似声学性能的材料制成。该材料用直探头检测时,不得有大于Φ2mm平底孔当量直径的缺陷。
5.5.2校准用反射体可采用平底孔和V形槽等,校准时探头主声束应对准反射体,且与平底孔的反射面相垂直,与V形槽轴线相垂直。5.5.3试块的外形尺寸应能代表被检工件的特征,试块厚度应与被检工件的厚度相对应。其误差不超过探测厚度的10%。
5.5.4试块的制造要求应符合ZBY232的规定。5.5.5现场检测时,也可采用其他型式的等效试块。5.6系统组合性能的测试见ZBJ04001。5.7探伤前锻件的准备
5.7.1除订货时另有规定外,轴类锻件径向探伤时应加工出圆柱形表面;轴向探伤时两端面应加工成与锻件轴向垂直的平面,饼形和矩形锻件其表面加工成平面。且相互平行。5.7.2除订货时另有规定外,锻件表面的粗糙度R不得超过63μm。5.7.3锻件探伤面应无异物存在,如氧化皮、油漆、污物等。5.8探伤规程
5.8.1一般规则
5.8.1.1除由于倒圆、钻孔等造成锻件的截面和局部外形改变而不可能进行探伤外,要尽可能对整个锻件进行超声波探伤。
5.8.1.2锻件应在力学性能热处理后(不包括去应力处理),精加工成形前进行超声波探伤,如果经热处理后锻件的外形不可能进行全面探伤,则允许在性能热处理前进行超声波探伤,但热处理后应尽可能全面地对锻件进行超声波复探。5.8.1.3探头每次移动至少有15%的重合,以确保能完全扫查整个锻件。探头扫查速度:手工操作时不得超过150mm/s自动探伤时不得超过1000mm/s5.8.1.4要尽可能在两个相互垂直的方向上对锻件的所有截面进行扫查。5.8.1.5对于饼形锻件,除至少从一个平面扫查外,还应尽可能从圆周面进行径向扫查。5.8.1.6对于圆柱形实心或空心锻件进行探伤时,除要从径向进行扫查外,还应从轴向进行辅助扫查。5.8.1.7对于环形和筒形锻件的探伤,要同时参照附录A(标准的附录)执行。3
JB/T5000.15—1998
5.8.1.8制造厂或用户进行复查或重新评定时,要尽可能用可比较的仪器、探头和耦合剂。5.8.1.9锻件探伤可在静止状态下进行,也可在转动状态下(用车床或转胎转动进行。如果用户未作规定,制造厂可以任意选择。
5.8.1.10锻件厚度大于40mm时,应从相互平行的相对面进行探伤。5.8.2探伤灵敏度
5.8.2.1原则上采用AVG法确定探伤灵敏度,对于因几何形状所限和探测厚度接近近场区长度的锻件则采用试块比较法。
5.8.2.2探伤灵敏度以起始记录当量值为准,其基准波高不得低于满屏高的40%5.8.2.3对缺陷进行评定时,应在锻件完好部位调节评价灵敏度5.8.2.4探伤灵敏度的重新校验
a)遇下列情况之一时,必须对探伤灵敏度进行重新校验:校正后的探头、耦合剂和仪器旋钮等发生任何改变时;外部电源电压波动较大或操作者怀凝探伤灵敏度有变动时:一连续工作达4h及工作结束时。b)当探伤灵敏度降低2dB以上时,应重新对锻件进行全面复探;提高2cB以上时,应对所有的记录信号进行重新评定。
5.8.2.5探伤灵敏度的调节方法
a)对于实心圆柱形和探伤面与反射面平行的锻件,当声程大于3倍近场时,所需增加的cB值应按式(1)计算:
dB=201g
式中:S—一声程,mm:
a一一波长,mm;
Φ一一探伤灵敏度当量直径,mm。b)对于空心圆柱形锻件,当声程大于3倍近场时,所需增加的dB值应按式(②)计算:2as
dB=201g
式中:D——工件外径,mm;
d一一工件内径,mm;
+一一内孔探测,凹面反射;
一工件外圆径向探测,凸面反射。其余符号与5.8.2.5a)相同。
5.8.3锻件可探性的测定
当探伤灵敏度确定之后,以探伤灵敏度为基准,信噪比大于或等于6dB,则认为该锻件具有足够的可探性,否则由供需双方协商处理。5.8.4材质衰减系数的测定
5.8.4.1当声程大于3倍近场时,在锻件无缺陷区域内,至少选取三处具有代表性的部位测出B,/B之dB差值,即第一次底波高度B,与第二次底波高度B,之间的dB差值。材质衰减系数a(dB/mm)按式4
(3)计算:
式中:S一一声程,mm。
JB/T5000.15—1998
(B /B2)- 6
5.8.4.2当材质衰减系数a超过0.004dB/mm时,必须对探伤结果给予修正。5.8.5远场区声束直径的计算
6dB声束直径的计算应按式(4):d6=
式中:Ts—一晶片直径,mm;
d6——6dB声束直径,mm。
其余符号与5.8.2.5a)相同。
5.8.6缺陷当量大小的确定
5.8.6.1AVG法定量
当声程大于3倍近场时,缺陷当量直径的大小应按式(③计算:B/B=201g2
1+2a(y -S) ..
式中:a一—材质衰减系数,dB/mm;一一缺陷深度,mm;
Φ一一缺陷当量直径,mm;
B,B一一缺陷回波与底波的dB差,dB其余符号与5.8.2.5a)相同。
5.8.6.2试块法定量
a)当声程大于3倍近场时,缺陷当量直径的大小应按式(6)计算:@x+2ax-2atx
4=401g1
式中:4一一缺陷与试块平底孔之dB差值,dB;一平底孔深度,mm;
一材质衰减系数(对比试块),dB/mm;af——缺陷处材质衰减系数,dB/mm。其余符号与5.8.6.1相同。
b)当声程小于3倍近场时,应用试块直接比较或用实测的AVG曲线来定缺陷当量直径的大小。5.9缺陷的分类
5.9.1单个缺陷
间距大于50mm,当量直径不小于起始记录当量的缺陷。5.9.2分散缺陷
缺陷间距小于或等于50mm,同时存在2个或2个以上且5个以下,当量直径不小于起始记录当量的缺陷。
5.9.3密集区缺陷
按3.1。
5.9.4游动信号
JB/T 5000.15-1998
随探头在锻件表面某一方向移动时,其信号前沿连续移动25mm以上深度的缺陷信号5.9.5延伸性缺陷
缺陷连续回波高度至少在一个方向上不得低于起始记录当量值,其延伸长度应大于缺陷容许的最大当量直径。延伸性缺陷的延伸尺寸采用半波高度法测定(6dB法)。在测定延伸尺寸时应考虑探头的声域特性进行修正。
5.9.6缺陷引起的底波降低量BG/BF(dB)按3.2。
5.10缺陷的记录
5.10.1记录当量直径不小于起始记录当量的缺陷及其在锻件上的坐标位置。5.10.2密集区缺陷的记录
5.10.2.1记录密集区的分布范围。5.10.2.2记录密集区中最大当量直径的缺陷深度、当量及其在锻件上的坐标位置。5.10.3游动缺陷信号的记录
记录游动缺陷信号的深度、长度范围、最大当量及起点和终点的位置坐标。5.10.4延伸性缺陷的记录
记录延伸性缺陷的深度、长度范围、最大当量及起点和终点的位置坐标。5.10.5缺陷引起的底波降低量BG/BF(dB)的记录记录缺陷附近完好区内第一次底波幅度BG与缺陷区内第一次底波幅度BF达同一基准波高时的dB差值。
5.11质量等级
5.11.1锻件中小于起始记录当量的单个、分散缺陷不计。5.11.2凡判定为裂纹、白点、缩孔类型的缺陷不允许存在。5.11.3游动缺陷信号如能判定为非危害性缺陷时,按延伸性缺陷进行质量等级评定;若判定为危害性缺陷时,则按5.11.2规定执行。5.11.4除因几何原因造成底波衰减外,任何底波衰减不允许超过26dB5.11.5表1中给出锻钢件中不同缺陷类型的质量等级的容许值。表1不同缺陷类型的质量等级划分第级
小提示:此标准内容仅展示完整标准里的部分截取内容,若需要完整标准请到上方自行免费下载完整标准文档。

标准图片预览:
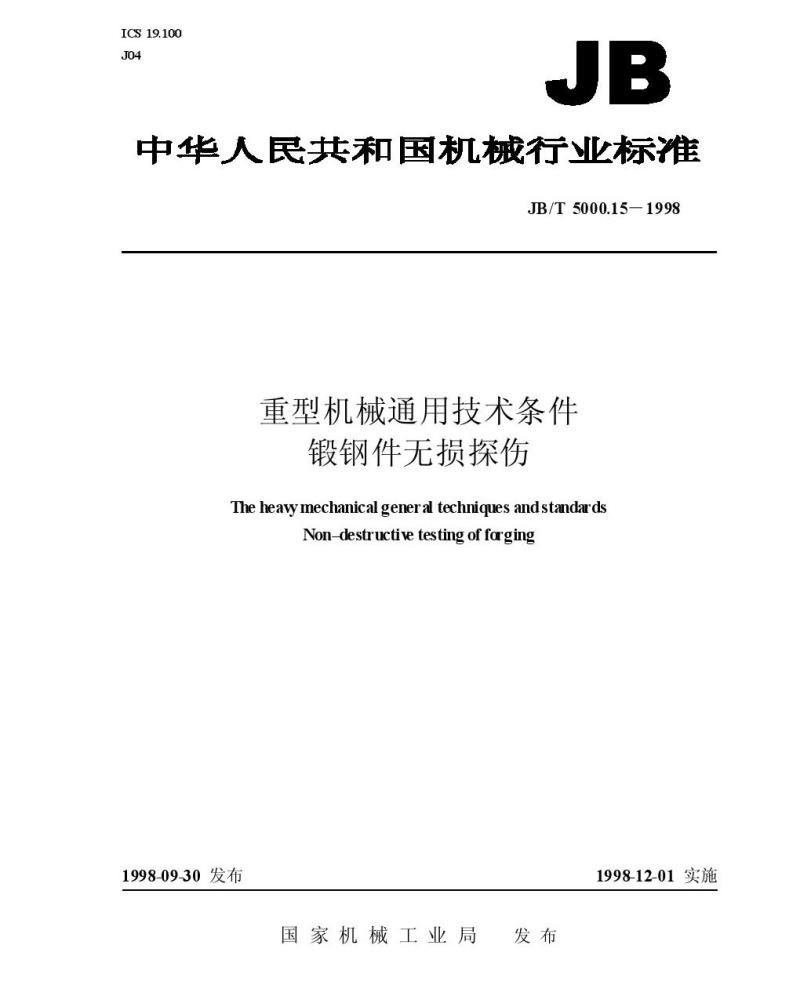
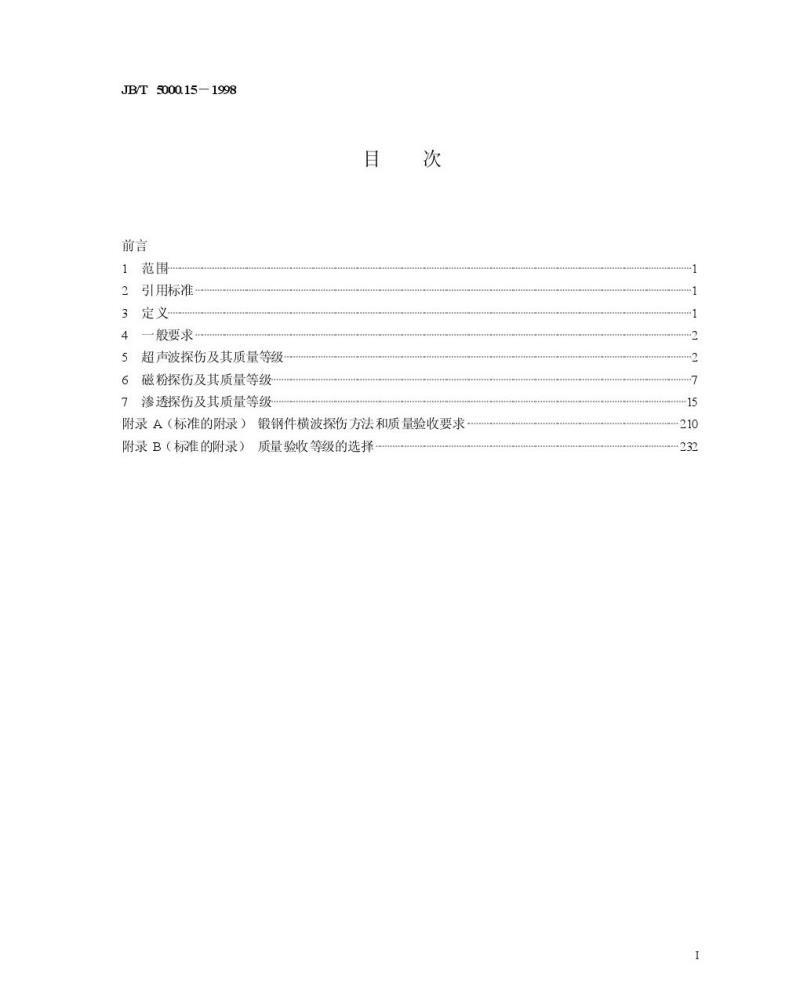
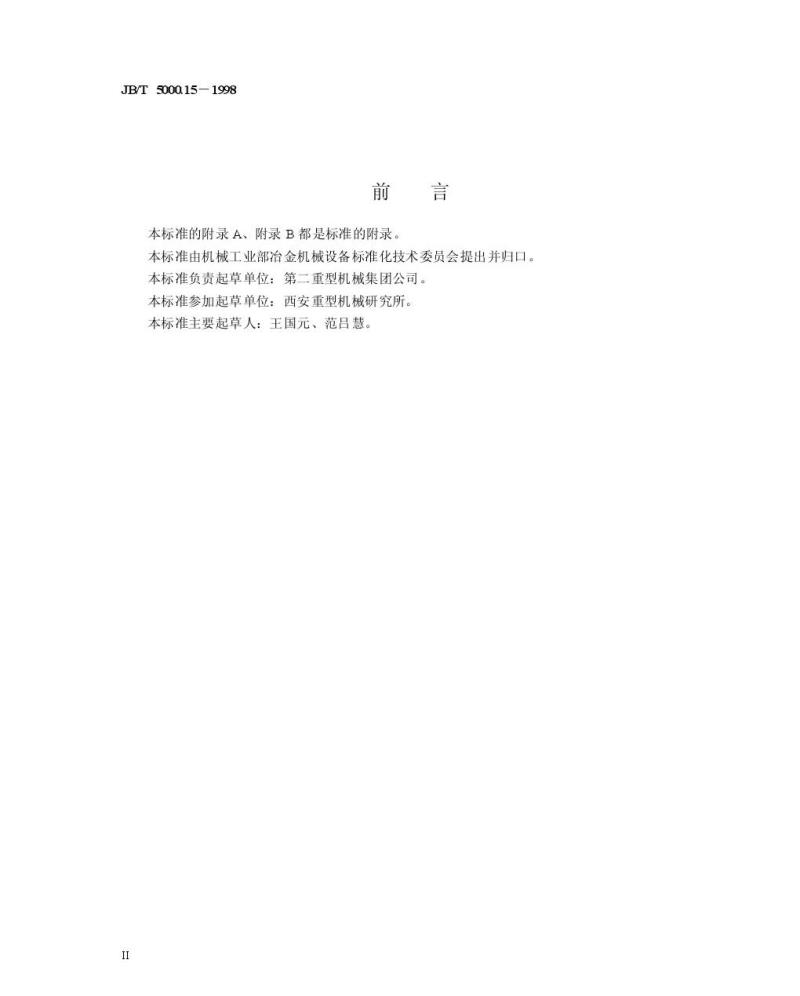
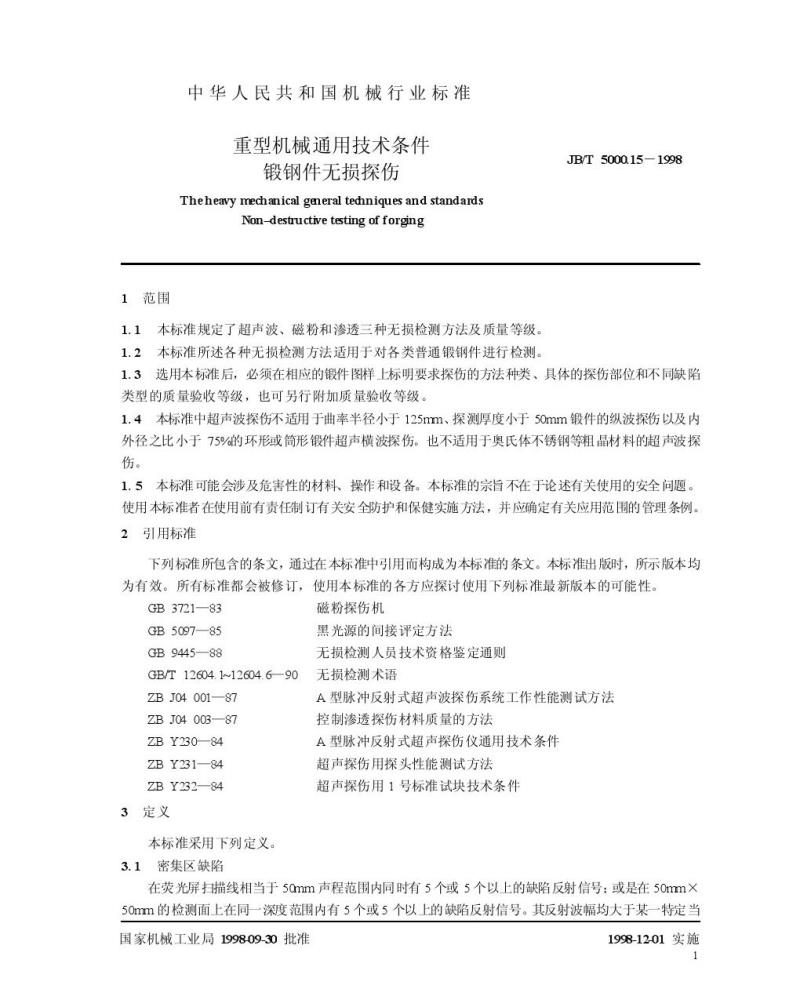
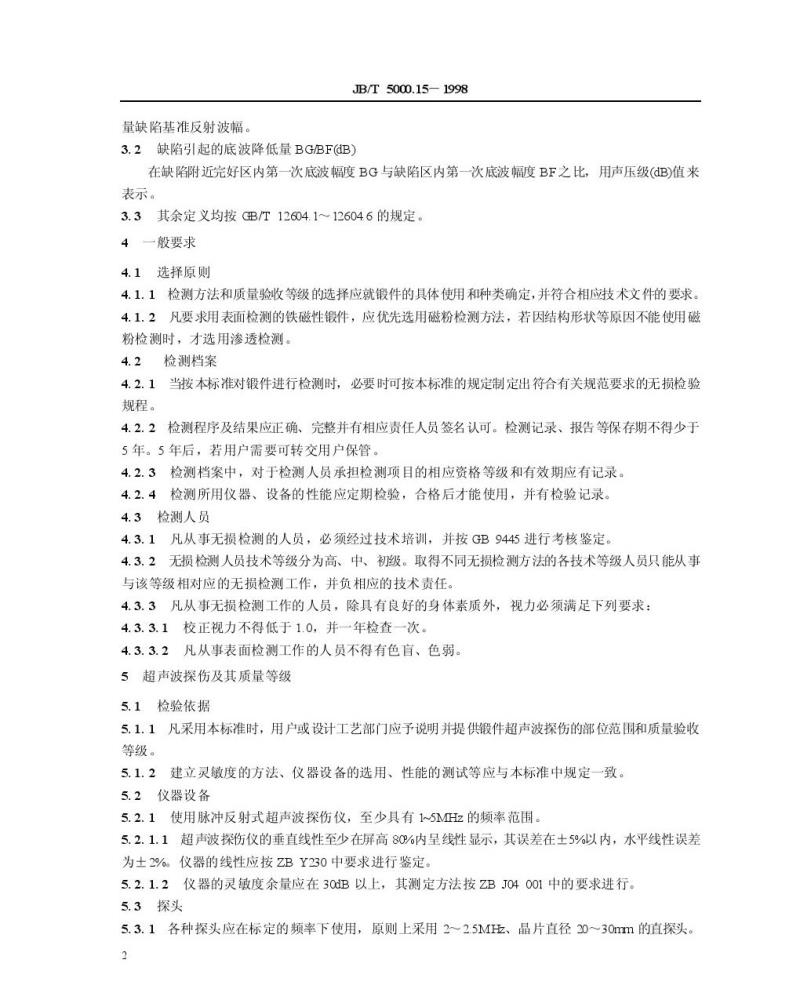
- 其它标准
- 热门标准
- 机械行业标准(JB)
- JB/T5762.2-2006 转塔车床 第2部分:精度
- JB/T10719-2007 焊接聚晶金刚石或立方氮化硼槽刀
- JB/T10725-2007 天然金刚石车刀
- JB/T10596-2006 磁阻式步进电动机通用技术条件
- JB/T10723-2007 焊接聚晶金刚石或立方氮化硼镗刀
- JB/T7144.1-1993 青饲料切碎机 技术条件
- JB/T5372.6-1991 8mm槽系组合夹具其他件 鳞齿支承螺母
- JB/T5742.1-2010 单排多轴木工钻床 第1部分:参数
- JB/T9162.8-1999 表柱 尺寸
- JB/T5368.18-1991 8mm槽系组合夹具定位件 V形板
- JB/T10216-2013 电控配电用电缆桥架
- JB/T5368.16-1991 8mm槽系组合夹具定位件 定位板
- JB/T7712-2007 高温合金热处理
- JB3930.58-1985 U形角铁
- JB/T5371.12-1991 8mm槽系组合夹具压紧件 V形压板
- 行业新闻
网站备案号:湘ICP备2023016450号-1