- 您的位置:
- 标准下载网 >>
- 标准分类 >>
- 国家标准(GB) >>
- GB/T 11345-1989 钢焊缝手工超声波探伤方法和探伤结果分级
标准号:
GB/T 11345-1989
标准名称:
钢焊缝手工超声波探伤方法和探伤结果分级
标准类别:
国家标准(GB)
标准状态:
现行-
发布日期:
1989-05-08 -
实施日期:
1990-01-01 出版语种:
简体中文下载格式:
.rar.pdf下载大小:
663.38 KB
标准ICS号:
机械制造>>焊接、钎焊和低温焊>>25.160.40焊接接头中标分类号:
冶金>>金属理化性能试验方法>>H26金属无损检验方法

点击下载
标准简介:
标准下载解压密码:www.bzxz.net
本标准规定了检验焊缝及热影响区缺陷,确定缺陷位置、尺寸和缺陷评定的一般方法及探伤结果的分级方法。本标准适用于母材厚度不小于8mm的铁素体类钢全焊透熔化焊对接焊缝脉冲反射法手工超声波检验。本标准不适用于铸钢及奥氏体不锈钢焊缝;外径小于159mm的钢管对接焊缝;内径小于等于200mm的管座角焊缝及外径小于250mm和内外径之比小于80%的纵向焊缝。 GB/T 11345-1989 钢焊缝手工超声波探伤方法和探伤结果分级 GB/T11345-1989

部分标准内容:
中华人民共和国国家标准
钢焊缝手工超声波探伤方法和
探伤结果分级
批准部门:国家技术监督局
批准日期:1989-05-08
实施日期:1990-01-01
主题内容与适用范围
GB/T 11345-1989
本标准规定了检验焊缝及热影响区缺陷,确定缺陷位置、尺寸和缺陷评定的一般方法及探伤结果的分级方法。
本标准适用于母材厚度不小于8mm的铁素体类钢全焊透熔化焊对接焊缝脉冲反射法手工超声波检验。
本标准不适用于铸钢及奥氏体不锈钢焊缝;外径小于159mm的钢管对接焊缝;内径小于等于200mm的管座角焊缝及外径小于250mm和内外径之比小于80%的纵向焊缝。2
引用标准
ZBY344超声探伤用探头型号命名方法ZBY231超声探伤用探头性能测试方法2BY232超声探伤用1号标准试块技术条件ZBJ(14001A型脉冲反射式超声探伤系统工作性能测试方法3术语
3.1简化水平距离1
从探头前沿到缺陷在探伤面上测量的水平距离。3.2缺陷指示长度△1
焊缝超声检验中,按规定的测量方法以探头移动距离测得的缺陷长度。
3.3探头接触面宽度W
环缝检验时为探头宽度,纵缝检验为探头长度,见图1。3.4纵向缺陷
大致上平行于焊缝走向的缺陷。3.5横向缺陷
大致上垂直于焊缝走向的缺陷。3.6儿何临界角β
筒形件检验,折射声束轴线与内壁相切时的折射角。3.7平行扫查
在斜角探伤中,将探头置于焊缝及热影响区表面,使声束指向焊缝方向,并沿焊缝方向移动的扫查方法。990
图1探头接触面宽度
GB/T11345—1989
3.8斜平行扫查
在斜角探伤中,使探头与焊缝中心线成一角度,平行于焊缝方向移动的扫查方法。3.9探伤截面
串列扫查探伤时,作为探伤对象的截面,般以焊缝坡口面为探伤截面,见图2。3.10串列基准线
串列扫查时,作为一发一收两探头等间隔移动基准的线。一般设在离探伤截面距离为0.5跨距的位置,见图2。
3.11参考线
探伤截面的位置焊后已被盖住,所以施焊前应预先在探伤面上,离焊缝坡口一定距离画出一标记线,该线即为参考线,将作为确定串列基准线的依据,见图3。3.12横方形串列扫查
将发、收一组探头,使其人射点对串列基准线经常保持等距离平行于焊缝移动的扫查方法,见图4。3.13纵方形串列扫查
将发、收一组探头使其人射点对串列基准线经常保持等距离,垂直于焊缝移动的扫查方法,见图4。串列基准线
探伤截面
探伤截面及串列基准线
横方形扫查
串列基准线
参考线
纵方形扫查
图4横方形扫查及纵方形扫查
熔合面
坡口面
图3参考线
蚕考线
4检验人员
4.1从事焊缝探伤的检验人员必须掌握超声波探伤的基础技术,具有足够的焊缝超声波探伤经验,并991
GB/T 11345--1989
掌握一定的材料、焊接基础知识。4.2焊缝超声检验人员应按有关规程或技术条件的规定经严格的培训和考核,并持有相应考核组织颁发的等级资格证书,从事相对应考核项目的检验工作。注:一般焊接检验专业考核项目分为板对接焊缝;管件对接焊缝;管座角焊缝;节点焊缝等四种。4.3超声检验人员的视力应每年检查一次,校正视力不得低于1.0。5探伤仪、探头及系统性能
5.1探伤仪
使用A型显示脉冲反射式探伤仪,其工作频率范围至少为1~5MHz,探伤仪应配备衰减器或增益控制器,其精度为任意相邻12dB误差在士1dB内。步进级每档不大于2dB,总调节量应大于60dB,水平线性误差不大于1%,垂直线性误差不大于5%。5.2探头
5.2.1探头应按ZBY344标准的规定作出标志。5.2.2晶片的有效面积不应超过500mm,且任-边长不应大于25mm。5.2.3声束轴线水平偏离角应不大于2°5.2.4探头主声束垂直方向的偏离,不应有明显的双峰,其测试方法见ZBY231。5.2.5斜探头的公称折射角β为45°、60°、70°或K值为1.0、1.5、2.0、2.5,折射角的实测值与公称值的偏差应不大于2K值偏差不应超过土0.1),前沿距离的偏差应不大于1mm。如受工件几何形状或探伤面曲率等限制也可选用其他小角度的探头。5.2.6当证明确能提高探测结果的准确性和可靠性,或能够较好地解决一般检验时的困难而又确保结果的正确,推荐采用聚焦等特种探头。5.3系统性能
5.3.1灵敏度余量
系统有效灵敏度必须大于评定灵敏度10dB以上。5.3.2远场分辨力
a)直探头:X≥30dB;
b)斜探头:Z≥6 dB。
5.4探伤仪、探头及系统性能和周期检查5.4.1探伤仪、探头及系统性能,除灵敏度余量外,均应按ZBJ04001的规定方法进行测试。5.4.2探伤仪的水平线性和垂直线性,在设备首次使用及每隔3个月应检查一次。5.4.3斜探头及系统性能,在表1规定的时间内必须检查一次。表 1斜探头及系统性能检查期
检查项目
前沿距离
折射角或K值
偏离角
灵敏度余量
分辨力
6试块
检查周期
开始使用及每隔6个工作日
开始使用、修补后及每隔1个月
6.1标试块的形状和尺寸见附录A,试块制造的技术要求应符合ZBY232的规定,该试块主要用于992
测定探伤仪、探头及系统性能。6.2对比试块的形状和尺寸见附录B。GB/T 11345--1989
6.2.1对比试块采用与被检验材料相同或声学性能相近的钢材制成。试块的探测面及侧面,在以2.5MHz以上频率及高灵敏条件下进行检验时,不得出现大于距探测面20mm处的$2mm平底孔反射回来的回波幅度1/4的缺陷回波。
6.2.2试块上的标准孔,根据探伤需要,可以采取其他形式布置或添加标准孔,但应注意不应与试块端角和相邻标准孔的反射发生混淆。6.2.3检验曲面工件时,如探伤面曲率半径R小于等于W2/4时,应采用与探伤面曲率相同的对比试块。反射体的布置可参照对比试块确定,试块宽度应满足式(1)。b≥2
式中:b--一试块宽度(mm);
^-波长(mm);
S-声程(m);
D。----声源有效直径(mm)。
6.3现场检验,为校验灵敏度和时基线,可以采用其他型式的等效试块。7检验等级
7.1检验等级的分级
根据质量要求检验等级分为A、B、C三级,检验的完善程度A级最低,B级一般,C级最高,检验工作的难度系数按A、B、C顺序逐级增高。应按照工件的材质、结构、焊接方法、使用条件及承受载荷的不同,合理的选用检验级别。检验等级应按产品技术条件和有关规定选择或经合同双方协商选定。注:A级难度系数为1;B级为5~6;C级为10~12。本标准给出了三个检验等级的检验条件,为避免焊件的几何形状限制相应等级检验的有效性,设计、工艺人员应在考虑超声检验可行性的基础上进行结构设计和工艺安排。7.2检验等级的检验范围
7.2.1A级检验采用一种角度的探头在焊缝的单面单侧进行检验,只对允许扫查到的焊缝截面进行探测。一般不要求作横向缺陷的检验。母材厚度大于50mm时,不得采用A级检验。7.2.2B级检验原则上采用一种角度探头在焊缝的单面双侧进行检验,对整个焊缝截面进行探测。母材厚度大于100mm时,采用双面双侧检验。受几何条件的限制,可在焊缝的双面单侧采用两种角度探头进行探伤。条件允许时应作横向缺陷的检验。7.2.3(级检验至少要采用两种角度探头在焊缝的单面双侧进行检验。同时要作两个扫查方向和两种探头角度的横向缺陷检验。母材厚度大于100mm时,采用双面双侧检验。其他附加要求是:a)对接焊缝余高要磨平,以便探头在焊缝上作平行扫查;b)焊缝两侧斜探头扫查经过的母材部分要用直探头作检查;c)焊缝母材厚度大于等于100mm,窄间隙焊缝母材厚度大于等于40mm时,一般要增加串列式扫查,扫查方法见附录C。
8检验准备
8.1探伤面
8.1.1按不同检验等级要求选择探伤面。推荐的探伤面如图5和表2所示。993
GB/T11345--1989
板厚(mm)
>25~50
>50~100
单面单侧
位置3
位置2
位置4
图5侧和面
表 2 探伤面及使用折射角
单面双侧(1和2或3和
4)或双面单侧(1和3或
2和4)
双面双侧
探伤法
直射法及
一次反射法
直射法
使用折射角或K值
70(K2. 5,K2. 0)
70°或 60°(K2.5,K2.0.K1.5)
45°或60°;45°和60°,45°和70°并用(K1 或K1.5;K1 和K1.5,
K1和K2.0并用)
45°和60°并用(K1和K1.5或
K2并用)
8.1.2检验区域的宽度应是焊缝本身再加上焊缝两侧各相当于母材厚度30%的一段区域,这个区域最小10mm,最大20mm见图6。
位置1
检查区
检验面
图6检验区域
位置2
8.1.3探头移动区应清除焊接飞溅、铁屑、油垢及其他外部杂质。探伤表面应平整光滑,便于探头的自由扫查,其表面粗糙度不应超过6.3μm,必要时应进行打磨。a)采用一次反射法或串列式扫查探伤时,探头移动区应大于1.25P。P=2· tg β
或P=28·K
式中:P.
跨距(mm);
母材厚度(mm)。
(3)
b)采用直射法探伤时,探头移动区应大于0.75P。GB/T11345—1989
8.1.4去除余高的焊缝,应将余高打磨到与邻近母材平齐。保留余高的焊缝,如焊缝表面有咬边,较大的隆起和凹陷等也应进行适当的修磨,并作圆滑过渡以免影响检验结果的评定。8.1.5焊缝检验前,应划好检验区段,标记出检验区段编号。8.2检验频率
检验频率f一般在25MHz范围内选择,推荐选用2~2.5MHz公称频率检验。特殊情况下,可选用低=于F2MHz或高于2.5MHz的检验频率,但必须保证系统灵敏度的要求。8.3探头角度
8.3.1斜探头的折射角β或K值应依据材料厚度,焊缝坡口型式及预期探测的主要缺陷种类来选择。对不同板厚推荐的探头角度和探头数量见表2。8.3.2串列式扫查,推荐选用公称折射角均为45°的两个探头,两个探头实际折射角相差不应超过2°探头前沿长度相差应小于2mm。为便于探测厚焊缝坡口边缘未熔合缺陷,亦可选用两个不同角度的探头·但两个探头角度均应在35°~55°范围内。8.4耦合剂
8.4.1应选用适当的液体或糊状物作为耦合剂,耦合剂应具有良好透声性和适宜流动性,不应对材料和人体有损伤作用,同时应便于检验后清理。8.4.2典型的耦合剂为水、机油、甘油和浆糊,耦合剂中可加人适量的“润湿剂”或活性剂以便改善耦合性能。
8.4.3在试块上调节仪器和产品检验应采用相同的耦合剂。8.5母材的检查
采用C级检验时,斜探头扫查声束通过的母材区域应用直探头作检查,以便探测是否有影响斜角探伤结果解释的分层性或其他种类缺陷存在。该项检查仅作记录,不属于对母材的验收检验。母材检查的规程要点如下:免费标准bzxz.net
a)方法:接触式脉冲反射法,采用频率2~5MHz的直探头,晶片直径10~25mm;b)灵敏度:将无缺陷处二次底波调节为荧光屏满幅的100%;c)记录:凡缺陷信号幅度超过荧光屏满幅20%的部位,应在工件表面作出标记,并予以记录。9仪器调整和校验
9.1时基线扫描的调节
荧光屏时基线刻度可按比例调节为代表缺陷的水平距离l(简化水平距离1\)深度h;或声程S见图7。图7时基线扫描调节示意图
9.1.1探伤面为平面时,可在对比试块上进行时基线扫描调节,扫描比例依据工件厚度和选用的探头角度来确定,最大检验范围应调至荧光屏时基线满刻度的2/3以上。995
GB/T11345—1989
9.1.2探伤面曲率半径R大于W2/4时,可在平面对比试块上或与探伤面曲率相近的曲面对比试块土,进行时基线扫描调节。
9.1.3探伤面曲率半径R小于等于W2/4时,探头楔块应磨成与工件曲面相吻合,在6.2.3条规定的对比试块上作时基线扫描调节。9.2距离-波幅曲线(DAC)的绘制9.2.1距离-波幅曲线由选用的仪器、探头系统在对比试块上的实测数据绘制见图8,其绘制方法见附录D,曲线由判废线RL,定量线SL和评定线EL组成,不同验收级别的各线灵敏度见表3。表中的DAC是以3 mm标准反射体绘制的距离-波幅曲线,即DAC基准线。评定线以上至定量线以下为 I区(弱信号评定区);定量线至判废线以下为IⅡ区(长度评定区);判废线及以上区域为Ⅲ区(判废区)。判废线(RL)
定量线 (SL)
评定线(EL)
距离(mm)
图8距离-波幅曲线示意图
装 3距离-波幅曲线的灵敏度
判废线
定量线
评定线
板厚(mm)
8~50
DAC-10 dB
DAC-16 dB
9.2.2探测横向缺陷时,应将各线灵敏度均提高6dB。B
DAC-4 dB
DAC-10 dB
DAC-16 dB
DAC-2 dB
DAC-8 dB
DAC-14 dB
9.2.3探伤面曲率半径R小于等于W2/4时,距离-波幅曲线的绘制应在曲面对比试块上进行。9.2.4受检工件的表面耦合损失及材质衰减应与试块相同,否则应进行传输损失修整见附录E,在1跨距声程内最大传输损失差在2 dB以内可不进行修整。9.2.5距离-波幅曲线可绘制在坐标纸上也可直接绘制在荧光屏刻度板上,但在整个检验范围内,曲线应处于荧光屏满幅度的20%以上,见图9,如果作不到,可采用分段绘制的方法见图10。2
图9距离-波幅曲线板的范围
图10分段距离-波幅曲线
9.3仪器调整的校验
GB/T11345—1989
9.3.1每次检验前应在对比试块上,对时基线扫描比例和距离-波幅曲线(灵敏度)进行调节或校验校验点不少于两点。
9.3.2检验过程中每4h之内或检验工作结束后应对时基线扫描和灵敏度进行校验,校验可在对比试块或其他等效试块上进行。
9.3.3扫描调节校验时,如发现校验点反射波在扫描线上偏移超过原校验点刻度读数的10%或满刻度的5%(两者取较小值),则扫描比例应重新调整,前次校验后已经记录的缺陷,位置参数应重新测定,并予以更正。
9.3.4灵敏度校验时,如校验点的反射波幅比距离-波幅曲线降低20%或2dB以上,则仪器灵敏度应重新调,并对前次校验后检查的全部焊缝应重新检验。如校验点的反射波幅比距离-波幅曲线增加20%或2dB以上,仪器灵敏度应重新调整,而前次校验后,已经记录的缺陷,应对缺陷尺寸参数重新测定并予以评定。
10初始检验
10.1-般要求
10.1.1超声检验应在焊缝及探伤表面经外观检查合格并满足8.1.3条的要求后进行。10.1.2检验前,探伤人员应了解受检工件的材质、结构、曲率、厚度、焊接方法、焊缝种类、坡口形式、焊缝余高及背面衬垫、沟槽等情况。10.1.3探伤灵敏度应不低于评定线灵敏度。10.1.4扫查速度不应大于150mm/s,相邻两次探头移动间隔保证至少有探头宽度10%的重叠。10.1.5对波幅超过评定线的反射波,应根据探头位置、方向、反射波的位置及10.1.2条了解的焊缝情况,判断其是否为缺陷。判断为缺陷的部位应在焊缝表面作出标记。10.2平板对接焊缝的检验
10.2.1为探测纵向缺陷,斜探头垂直于焊缝中心线放置在探伤面上,作锯齿型扫查见图11。探头前后移动的范围应保证扫查到全部焊缝截面及热影响区。在保持探头垂直焊缝作前后移动的同时,还应作10°~15°的左右转动。
图11锯齿形扫查
10.2.2为探测焊缝及热影响区的横向缺陷应进行平行和斜平行扫查。a)B级检验时,可在焊缝两侧边缘使探头与焊缝中心线成10°~~20°作斜平行扫查(图12);b)C级检验时,可将探头放在焊缝及热影响区上作两个方向的平行扫查(图13),焊缝母材厚度超过100mm时,应在焊缝的两面作平行扫查或者采用两种角度探头(45°和60°或45°和70°并用)作单面两个方向的平行扫查;亦可用两个45°探头作串列式平行扫查;997
GB/T 11345—1989
c)对电渣焊缝还应增加与焊缝中心线成45°的斜向扫查。日
图12斜平行扫查
图13平行扫查
10.2.3为确定缺陷的位置、方向、形状、观察缺陷动态波形或区分缺陷讯号与伪讯号,可采用前后、左右、转角、环绕等四种探头基本扫查方式(图14)。(o((
(o(o(
((o(d
10.3曲面工件对接焊缝的检验
图14四种基本扫查方法
10.3.1探伤面为曲面时,应按6.2.3和9.1.3条的规定选用对比试块,并采用10.2条的方法进行检验,级检验时,受工件几何形状限制,横向缺陷探测无法实施时,应在检验记录中予以注明。10.3.2环缝检验时,对比试块的曲率半径为探伤面曲率半径0.9~1.5倍的对比试块均可采用。探测横向缺陷时按10.3.3条的方法进行。10.3.3纵缝检验时,对比试块的曲率半径与探伤面曲率半径之差应小于10%。10.3.3.1根据工件的曲率和材料厚度选择探头角度,并考虑几何临界角的限制,确保声束能扫查到整个焊缝厚度。条件允许时,声束在曲底面的人射角度不应超过70°。10.3.3.2探头接触面修磨后,应注意探头人射点和折射角或K值的变化,并用曲面试块作实际测定。10.3.3.3当R大于W2/4采用平面对比试块调节仪器时,检验中应注意到荧光屏指示的缺陷深度或水平距离与缺陷实际的径向埋藏深度或水平距离弧长的差异,必要时应进行修正。10.4其他结构焊缝的检验
10.4.1般原则
a)尽可能采用平板焊缝检验中已经行之有效的各种方法;b)在选择探伤面和探头时应考虑到检测各种类型缺陷的可能性,并使声束尽可能垂直于该结构焊缝中的主要缺陷。
10.4.2T型接头
10.4.2.1腹板厚度不同时,选用的折射角见表4,斜探头在腹板一侧作直射法和一次反射法探伤见998
图15位置2。
腹板厚度(mm)
表 4腹板厚度与选用的折射角
70 (K2.5)
GB/T11345—1989
折射角(\)
60 (K2.5, K2.0)
45(K1,K1.5)
10.4.2.2采用折射角45°K1)探头在腹板一侧作直射法和一次反射法探测焊缝及腹板侧热影响区的裂纹(图16)。
位置1
图15T型接头
/翼板
位置3
位置3
图16T型接头
10.4.2.3为探侧腹板和翼板间未焊透或翼板侧焊缝下层状撕製等缺陷,可采用直探头(图15位置1)或斜探头(图16位置3)在翼板外侧探伤或采用折射角45°(K1)探头在翼板内侧作一次反射法探伤(图15位置3)。
10.4.3角接接头
角接接头探伤面及折射角一般按图17和表4选择。10.4.4管座角焊缝
10.4.4.1根据焊缝结构形式,管座角焊缝的检验有如下五种探测方式,可选择其中一种或几种方式组合实施检验。探测方式的选择应由合同双方商定,并重点考虑主要探测对象和几何条件的限制(图18、19)。
a)在接管内壁表面采用直探头探伤(图18位置1);b)在容器内表面用直探头探伤(图19位置1);c)在接管外表面采用斜探头探伤(图19位置2);d)在接管内表面采用斜探头探伤(图18位置3,图19位置3),图17角接接头
GB/T 11345—1989
e)在容器外表面采用斜探头探伤(图18位置2)位置3
位置1
图18管座角焊缝
位置1
图19管座角焊缝
位置3
10.4.4.2管座角焊缝以直探头检验为主,对直探头扫查不到的区域或结构,缺陷方向性不适于采用直探头检验时,可采用斜探头检验,斜探头检验应符合10.4.1条的规定。10.4.5直探头检验的规程
a)推荐采用频率2.5MHz直探头或双晶直探头,探头与工件接触面的尺寸W应小于2VR;b)灵敏度可在与工件同曲率的试块上调节,也可采用计算法或DGS曲线法,以工件底面回波调节。其检验等级评定见表5。
表5直探头检验等级评定
检验等级
评定灵敏度
定量灵敏度
判废灵敏度
11规定检验
?般要求
11.1.1规定检验只对初始检验中被标记的部位进行检验。11.1.2探伤灵敏度应调节到评定灵敏度。B
11.1.3对所有反射波幅超过定量线的缺陷,均应确定其位置,最大反射波幅所在区域和缺陷指示长度。
11.2最大反射波幅的测定
11.2.1对判定为缺陷的部位,采取10.2.3条的探头扫查方式、增加探伤面、改变探头折射角度进行探测,测出最大反射波幅并与距离-波幅曲线作比较,确定波幅所在区域。波幅测定的允许误差为2dB。11.2.2最大反射波幅A与定量线SI的dB差值记为SL士1000
11.3位置参数的测定
11.3.1缺陷位置以获得缺陷最大反射波的位置来表示,根据相应的探头位置和反射波在荧光屏上的位置来确定如下全部或部分参数。
a)纵坐标L代表缺陷沿焊缝方向的位置。以检验区段编号为标记基准点(即原点)建立坐标。坐标正方向距离L表示缺陷到原点之间的距离见图20。
b)深度坐标h代表缺陷位置到探伤面的垂直距离(mm)。以缺陷最大反射波位置的深度值表示。c)横坐标q代表缺陷位置离开焊缝中心线的垂直距离,可由缺陷最大反射波位置的水平距离或简化水平距离求得。GB/T11345—1989
记为1.1
图20纵坐标L示意图
11.3.2缺陷的深度和水平距离(或简化水平距离)两数值中的一个可由缺陷最大反射波在荧光屏上的位置直接读出,另一数值可采用计算法、曲线法、作图法或缺陷定位尺求出。11.4尺寸参数的测定
应根据缺陷最大反射波幅确定缺陷当量@值或测定缺陷指示长度△1。11.4.1缺陷当量@,用当量平底孔直径表示,主要用于直探头检验,可采用公式计算、DGS曲线、试块对比或当量计算尺确定缺陷当量尺寸。11.4.2缺陷指示长度△1的测定推荐采用如下两种方法。a)当缺陷反射波只有一个高点时,用降低6dB相对灵敏度法测长见图21;b)在测长扫查过程中,如发现缺陷反射波峰值起伏变化,有多个高点,则以缺陷两端反射波极大值之间探头的移动长度确定为缺陷指示长度,即端点峰值法见图22。最大反射波
探头移动
缺陷指示长度
长度(mm)
图21相对灵敏度测长法
12缺陷评定
缺陷指示长度
图22端点峰值测长法
12.1超过评定线的信号应注意其是否具有裂纹等危害性缺陷特征,如有怀疑时应采取改变探头角度、增加探伤面、观察动态波型、结合结构工艺特征作判定,如对波型不能准确判断时,应辅以其他检验作综合判定。
12.2最大反射波幅位于Ⅱ区的缺陷,其指示长度小于10mm时按5mm计。12.3相邻两缺陷各向间距小于8mm时,两缺陷指示长度之和作为单个缺陷的指示长度。13检验结果的等级分类
13.1最大反射波幅位于Ⅱ区的缺陷,根据缺陷指示长度按表6的规定予以评级。1001
小提示:此标准内容仅展示完整标准里的部分截取内容,若需要完整标准请到上方自行免费下载完整标准文档。
钢焊缝手工超声波探伤方法和
探伤结果分级
批准部门:国家技术监督局
批准日期:1989-05-08
实施日期:1990-01-01
主题内容与适用范围
GB/T 11345-1989
本标准规定了检验焊缝及热影响区缺陷,确定缺陷位置、尺寸和缺陷评定的一般方法及探伤结果的分级方法。
本标准适用于母材厚度不小于8mm的铁素体类钢全焊透熔化焊对接焊缝脉冲反射法手工超声波检验。
本标准不适用于铸钢及奥氏体不锈钢焊缝;外径小于159mm的钢管对接焊缝;内径小于等于200mm的管座角焊缝及外径小于250mm和内外径之比小于80%的纵向焊缝。2
引用标准
ZBY344超声探伤用探头型号命名方法ZBY231超声探伤用探头性能测试方法2BY232超声探伤用1号标准试块技术条件ZBJ(14001A型脉冲反射式超声探伤系统工作性能测试方法3术语
3.1简化水平距离1
从探头前沿到缺陷在探伤面上测量的水平距离。3.2缺陷指示长度△1
焊缝超声检验中,按规定的测量方法以探头移动距离测得的缺陷长度。
3.3探头接触面宽度W
环缝检验时为探头宽度,纵缝检验为探头长度,见图1。3.4纵向缺陷
大致上平行于焊缝走向的缺陷。3.5横向缺陷
大致上垂直于焊缝走向的缺陷。3.6儿何临界角β
筒形件检验,折射声束轴线与内壁相切时的折射角。3.7平行扫查
在斜角探伤中,将探头置于焊缝及热影响区表面,使声束指向焊缝方向,并沿焊缝方向移动的扫查方法。990
图1探头接触面宽度
GB/T11345—1989
3.8斜平行扫查
在斜角探伤中,使探头与焊缝中心线成一角度,平行于焊缝方向移动的扫查方法。3.9探伤截面
串列扫查探伤时,作为探伤对象的截面,般以焊缝坡口面为探伤截面,见图2。3.10串列基准线
串列扫查时,作为一发一收两探头等间隔移动基准的线。一般设在离探伤截面距离为0.5跨距的位置,见图2。
3.11参考线
探伤截面的位置焊后已被盖住,所以施焊前应预先在探伤面上,离焊缝坡口一定距离画出一标记线,该线即为参考线,将作为确定串列基准线的依据,见图3。3.12横方形串列扫查
将发、收一组探头,使其人射点对串列基准线经常保持等距离平行于焊缝移动的扫查方法,见图4。3.13纵方形串列扫查
将发、收一组探头使其人射点对串列基准线经常保持等距离,垂直于焊缝移动的扫查方法,见图4。串列基准线
探伤截面
探伤截面及串列基准线
横方形扫查
串列基准线
参考线
纵方形扫查
图4横方形扫查及纵方形扫查
熔合面
坡口面
图3参考线
蚕考线
4检验人员
4.1从事焊缝探伤的检验人员必须掌握超声波探伤的基础技术,具有足够的焊缝超声波探伤经验,并991
GB/T 11345--1989
掌握一定的材料、焊接基础知识。4.2焊缝超声检验人员应按有关规程或技术条件的规定经严格的培训和考核,并持有相应考核组织颁发的等级资格证书,从事相对应考核项目的检验工作。注:一般焊接检验专业考核项目分为板对接焊缝;管件对接焊缝;管座角焊缝;节点焊缝等四种。4.3超声检验人员的视力应每年检查一次,校正视力不得低于1.0。5探伤仪、探头及系统性能
5.1探伤仪
使用A型显示脉冲反射式探伤仪,其工作频率范围至少为1~5MHz,探伤仪应配备衰减器或增益控制器,其精度为任意相邻12dB误差在士1dB内。步进级每档不大于2dB,总调节量应大于60dB,水平线性误差不大于1%,垂直线性误差不大于5%。5.2探头
5.2.1探头应按ZBY344标准的规定作出标志。5.2.2晶片的有效面积不应超过500mm,且任-边长不应大于25mm。5.2.3声束轴线水平偏离角应不大于2°5.2.4探头主声束垂直方向的偏离,不应有明显的双峰,其测试方法见ZBY231。5.2.5斜探头的公称折射角β为45°、60°、70°或K值为1.0、1.5、2.0、2.5,折射角的实测值与公称值的偏差应不大于2K值偏差不应超过土0.1),前沿距离的偏差应不大于1mm。如受工件几何形状或探伤面曲率等限制也可选用其他小角度的探头。5.2.6当证明确能提高探测结果的准确性和可靠性,或能够较好地解决一般检验时的困难而又确保结果的正确,推荐采用聚焦等特种探头。5.3系统性能
5.3.1灵敏度余量
系统有效灵敏度必须大于评定灵敏度10dB以上。5.3.2远场分辨力
a)直探头:X≥30dB;
b)斜探头:Z≥6 dB。
5.4探伤仪、探头及系统性能和周期检查5.4.1探伤仪、探头及系统性能,除灵敏度余量外,均应按ZBJ04001的规定方法进行测试。5.4.2探伤仪的水平线性和垂直线性,在设备首次使用及每隔3个月应检查一次。5.4.3斜探头及系统性能,在表1规定的时间内必须检查一次。表 1斜探头及系统性能检查期
检查项目
前沿距离
折射角或K值
偏离角
灵敏度余量
分辨力
6试块
检查周期
开始使用及每隔6个工作日
开始使用、修补后及每隔1个月
6.1标试块的形状和尺寸见附录A,试块制造的技术要求应符合ZBY232的规定,该试块主要用于992
测定探伤仪、探头及系统性能。6.2对比试块的形状和尺寸见附录B。GB/T 11345--1989
6.2.1对比试块采用与被检验材料相同或声学性能相近的钢材制成。试块的探测面及侧面,在以2.5MHz以上频率及高灵敏条件下进行检验时,不得出现大于距探测面20mm处的$2mm平底孔反射回来的回波幅度1/4的缺陷回波。
6.2.2试块上的标准孔,根据探伤需要,可以采取其他形式布置或添加标准孔,但应注意不应与试块端角和相邻标准孔的反射发生混淆。6.2.3检验曲面工件时,如探伤面曲率半径R小于等于W2/4时,应采用与探伤面曲率相同的对比试块。反射体的布置可参照对比试块确定,试块宽度应满足式(1)。b≥2
式中:b--一试块宽度(mm);
^-波长(mm);
S-声程(m);
D。----声源有效直径(mm)。
6.3现场检验,为校验灵敏度和时基线,可以采用其他型式的等效试块。7检验等级
7.1检验等级的分级
根据质量要求检验等级分为A、B、C三级,检验的完善程度A级最低,B级一般,C级最高,检验工作的难度系数按A、B、C顺序逐级增高。应按照工件的材质、结构、焊接方法、使用条件及承受载荷的不同,合理的选用检验级别。检验等级应按产品技术条件和有关规定选择或经合同双方协商选定。注:A级难度系数为1;B级为5~6;C级为10~12。本标准给出了三个检验等级的检验条件,为避免焊件的几何形状限制相应等级检验的有效性,设计、工艺人员应在考虑超声检验可行性的基础上进行结构设计和工艺安排。7.2检验等级的检验范围
7.2.1A级检验采用一种角度的探头在焊缝的单面单侧进行检验,只对允许扫查到的焊缝截面进行探测。一般不要求作横向缺陷的检验。母材厚度大于50mm时,不得采用A级检验。7.2.2B级检验原则上采用一种角度探头在焊缝的单面双侧进行检验,对整个焊缝截面进行探测。母材厚度大于100mm时,采用双面双侧检验。受几何条件的限制,可在焊缝的双面单侧采用两种角度探头进行探伤。条件允许时应作横向缺陷的检验。7.2.3(级检验至少要采用两种角度探头在焊缝的单面双侧进行检验。同时要作两个扫查方向和两种探头角度的横向缺陷检验。母材厚度大于100mm时,采用双面双侧检验。其他附加要求是:a)对接焊缝余高要磨平,以便探头在焊缝上作平行扫查;b)焊缝两侧斜探头扫查经过的母材部分要用直探头作检查;c)焊缝母材厚度大于等于100mm,窄间隙焊缝母材厚度大于等于40mm时,一般要增加串列式扫查,扫查方法见附录C。
8检验准备
8.1探伤面
8.1.1按不同检验等级要求选择探伤面。推荐的探伤面如图5和表2所示。993
GB/T11345--1989
板厚(mm)
>25~50
>50~100
单面单侧
位置3
位置2
位置4
图5侧和面
表 2 探伤面及使用折射角
单面双侧(1和2或3和
4)或双面单侧(1和3或
2和4)
双面双侧
探伤法
直射法及
一次反射法
直射法
使用折射角或K值
70(K2. 5,K2. 0)
70°或 60°(K2.5,K2.0.K1.5)
45°或60°;45°和60°,45°和70°并用(K1 或K1.5;K1 和K1.5,
K1和K2.0并用)
45°和60°并用(K1和K1.5或
K2并用)
8.1.2检验区域的宽度应是焊缝本身再加上焊缝两侧各相当于母材厚度30%的一段区域,这个区域最小10mm,最大20mm见图6。
位置1
检查区
检验面
图6检验区域
位置2
8.1.3探头移动区应清除焊接飞溅、铁屑、油垢及其他外部杂质。探伤表面应平整光滑,便于探头的自由扫查,其表面粗糙度不应超过6.3μm,必要时应进行打磨。a)采用一次反射法或串列式扫查探伤时,探头移动区应大于1.25P。P=2· tg β
或P=28·K
式中:P.
跨距(mm);
母材厚度(mm)。
(3)
b)采用直射法探伤时,探头移动区应大于0.75P。GB/T11345—1989
8.1.4去除余高的焊缝,应将余高打磨到与邻近母材平齐。保留余高的焊缝,如焊缝表面有咬边,较大的隆起和凹陷等也应进行适当的修磨,并作圆滑过渡以免影响检验结果的评定。8.1.5焊缝检验前,应划好检验区段,标记出检验区段编号。8.2检验频率
检验频率f一般在25MHz范围内选择,推荐选用2~2.5MHz公称频率检验。特殊情况下,可选用低=于F2MHz或高于2.5MHz的检验频率,但必须保证系统灵敏度的要求。8.3探头角度
8.3.1斜探头的折射角β或K值应依据材料厚度,焊缝坡口型式及预期探测的主要缺陷种类来选择。对不同板厚推荐的探头角度和探头数量见表2。8.3.2串列式扫查,推荐选用公称折射角均为45°的两个探头,两个探头实际折射角相差不应超过2°探头前沿长度相差应小于2mm。为便于探测厚焊缝坡口边缘未熔合缺陷,亦可选用两个不同角度的探头·但两个探头角度均应在35°~55°范围内。8.4耦合剂
8.4.1应选用适当的液体或糊状物作为耦合剂,耦合剂应具有良好透声性和适宜流动性,不应对材料和人体有损伤作用,同时应便于检验后清理。8.4.2典型的耦合剂为水、机油、甘油和浆糊,耦合剂中可加人适量的“润湿剂”或活性剂以便改善耦合性能。
8.4.3在试块上调节仪器和产品检验应采用相同的耦合剂。8.5母材的检查
采用C级检验时,斜探头扫查声束通过的母材区域应用直探头作检查,以便探测是否有影响斜角探伤结果解释的分层性或其他种类缺陷存在。该项检查仅作记录,不属于对母材的验收检验。母材检查的规程要点如下:免费标准bzxz.net
a)方法:接触式脉冲反射法,采用频率2~5MHz的直探头,晶片直径10~25mm;b)灵敏度:将无缺陷处二次底波调节为荧光屏满幅的100%;c)记录:凡缺陷信号幅度超过荧光屏满幅20%的部位,应在工件表面作出标记,并予以记录。9仪器调整和校验
9.1时基线扫描的调节
荧光屏时基线刻度可按比例调节为代表缺陷的水平距离l(简化水平距离1\)深度h;或声程S见图7。图7时基线扫描调节示意图
9.1.1探伤面为平面时,可在对比试块上进行时基线扫描调节,扫描比例依据工件厚度和选用的探头角度来确定,最大检验范围应调至荧光屏时基线满刻度的2/3以上。995
GB/T11345—1989
9.1.2探伤面曲率半径R大于W2/4时,可在平面对比试块上或与探伤面曲率相近的曲面对比试块土,进行时基线扫描调节。
9.1.3探伤面曲率半径R小于等于W2/4时,探头楔块应磨成与工件曲面相吻合,在6.2.3条规定的对比试块上作时基线扫描调节。9.2距离-波幅曲线(DAC)的绘制9.2.1距离-波幅曲线由选用的仪器、探头系统在对比试块上的实测数据绘制见图8,其绘制方法见附录D,曲线由判废线RL,定量线SL和评定线EL组成,不同验收级别的各线灵敏度见表3。表中的DAC是以3 mm标准反射体绘制的距离-波幅曲线,即DAC基准线。评定线以上至定量线以下为 I区(弱信号评定区);定量线至判废线以下为IⅡ区(长度评定区);判废线及以上区域为Ⅲ区(判废区)。判废线(RL)
定量线 (SL)
评定线(EL)
距离(mm)
图8距离-波幅曲线示意图
装 3距离-波幅曲线的灵敏度
判废线
定量线
评定线
板厚(mm)
8~50
DAC-10 dB
DAC-16 dB
9.2.2探测横向缺陷时,应将各线灵敏度均提高6dB。B
DAC-4 dB
DAC-10 dB
DAC-16 dB
DAC-2 dB
DAC-8 dB
DAC-14 dB
9.2.3探伤面曲率半径R小于等于W2/4时,距离-波幅曲线的绘制应在曲面对比试块上进行。9.2.4受检工件的表面耦合损失及材质衰减应与试块相同,否则应进行传输损失修整见附录E,在1跨距声程内最大传输损失差在2 dB以内可不进行修整。9.2.5距离-波幅曲线可绘制在坐标纸上也可直接绘制在荧光屏刻度板上,但在整个检验范围内,曲线应处于荧光屏满幅度的20%以上,见图9,如果作不到,可采用分段绘制的方法见图10。2
图9距离-波幅曲线板的范围
图10分段距离-波幅曲线
9.3仪器调整的校验
GB/T11345—1989
9.3.1每次检验前应在对比试块上,对时基线扫描比例和距离-波幅曲线(灵敏度)进行调节或校验校验点不少于两点。
9.3.2检验过程中每4h之内或检验工作结束后应对时基线扫描和灵敏度进行校验,校验可在对比试块或其他等效试块上进行。
9.3.3扫描调节校验时,如发现校验点反射波在扫描线上偏移超过原校验点刻度读数的10%或满刻度的5%(两者取较小值),则扫描比例应重新调整,前次校验后已经记录的缺陷,位置参数应重新测定,并予以更正。
9.3.4灵敏度校验时,如校验点的反射波幅比距离-波幅曲线降低20%或2dB以上,则仪器灵敏度应重新调,并对前次校验后检查的全部焊缝应重新检验。如校验点的反射波幅比距离-波幅曲线增加20%或2dB以上,仪器灵敏度应重新调整,而前次校验后,已经记录的缺陷,应对缺陷尺寸参数重新测定并予以评定。
10初始检验
10.1-般要求
10.1.1超声检验应在焊缝及探伤表面经外观检查合格并满足8.1.3条的要求后进行。10.1.2检验前,探伤人员应了解受检工件的材质、结构、曲率、厚度、焊接方法、焊缝种类、坡口形式、焊缝余高及背面衬垫、沟槽等情况。10.1.3探伤灵敏度应不低于评定线灵敏度。10.1.4扫查速度不应大于150mm/s,相邻两次探头移动间隔保证至少有探头宽度10%的重叠。10.1.5对波幅超过评定线的反射波,应根据探头位置、方向、反射波的位置及10.1.2条了解的焊缝情况,判断其是否为缺陷。判断为缺陷的部位应在焊缝表面作出标记。10.2平板对接焊缝的检验
10.2.1为探测纵向缺陷,斜探头垂直于焊缝中心线放置在探伤面上,作锯齿型扫查见图11。探头前后移动的范围应保证扫查到全部焊缝截面及热影响区。在保持探头垂直焊缝作前后移动的同时,还应作10°~15°的左右转动。
图11锯齿形扫查
10.2.2为探测焊缝及热影响区的横向缺陷应进行平行和斜平行扫查。a)B级检验时,可在焊缝两侧边缘使探头与焊缝中心线成10°~~20°作斜平行扫查(图12);b)C级检验时,可将探头放在焊缝及热影响区上作两个方向的平行扫查(图13),焊缝母材厚度超过100mm时,应在焊缝的两面作平行扫查或者采用两种角度探头(45°和60°或45°和70°并用)作单面两个方向的平行扫查;亦可用两个45°探头作串列式平行扫查;997
GB/T 11345—1989
c)对电渣焊缝还应增加与焊缝中心线成45°的斜向扫查。日
图12斜平行扫查
图13平行扫查
10.2.3为确定缺陷的位置、方向、形状、观察缺陷动态波形或区分缺陷讯号与伪讯号,可采用前后、左右、转角、环绕等四种探头基本扫查方式(图14)。(o((
(o(o(
((o(d
10.3曲面工件对接焊缝的检验
图14四种基本扫查方法
10.3.1探伤面为曲面时,应按6.2.3和9.1.3条的规定选用对比试块,并采用10.2条的方法进行检验,级检验时,受工件几何形状限制,横向缺陷探测无法实施时,应在检验记录中予以注明。10.3.2环缝检验时,对比试块的曲率半径为探伤面曲率半径0.9~1.5倍的对比试块均可采用。探测横向缺陷时按10.3.3条的方法进行。10.3.3纵缝检验时,对比试块的曲率半径与探伤面曲率半径之差应小于10%。10.3.3.1根据工件的曲率和材料厚度选择探头角度,并考虑几何临界角的限制,确保声束能扫查到整个焊缝厚度。条件允许时,声束在曲底面的人射角度不应超过70°。10.3.3.2探头接触面修磨后,应注意探头人射点和折射角或K值的变化,并用曲面试块作实际测定。10.3.3.3当R大于W2/4采用平面对比试块调节仪器时,检验中应注意到荧光屏指示的缺陷深度或水平距离与缺陷实际的径向埋藏深度或水平距离弧长的差异,必要时应进行修正。10.4其他结构焊缝的检验
10.4.1般原则
a)尽可能采用平板焊缝检验中已经行之有效的各种方法;b)在选择探伤面和探头时应考虑到检测各种类型缺陷的可能性,并使声束尽可能垂直于该结构焊缝中的主要缺陷。
10.4.2T型接头
10.4.2.1腹板厚度不同时,选用的折射角见表4,斜探头在腹板一侧作直射法和一次反射法探伤见998
图15位置2。
腹板厚度(mm)
表 4腹板厚度与选用的折射角
70 (K2.5)
GB/T11345—1989
折射角(\)
60 (K2.5, K2.0)
45(K1,K1.5)
10.4.2.2采用折射角45°K1)探头在腹板一侧作直射法和一次反射法探测焊缝及腹板侧热影响区的裂纹(图16)。
位置1
图15T型接头
/翼板
位置3
位置3
图16T型接头
10.4.2.3为探侧腹板和翼板间未焊透或翼板侧焊缝下层状撕製等缺陷,可采用直探头(图15位置1)或斜探头(图16位置3)在翼板外侧探伤或采用折射角45°(K1)探头在翼板内侧作一次反射法探伤(图15位置3)。
10.4.3角接接头
角接接头探伤面及折射角一般按图17和表4选择。10.4.4管座角焊缝
10.4.4.1根据焊缝结构形式,管座角焊缝的检验有如下五种探测方式,可选择其中一种或几种方式组合实施检验。探测方式的选择应由合同双方商定,并重点考虑主要探测对象和几何条件的限制(图18、19)。
a)在接管内壁表面采用直探头探伤(图18位置1);b)在容器内表面用直探头探伤(图19位置1);c)在接管外表面采用斜探头探伤(图19位置2);d)在接管内表面采用斜探头探伤(图18位置3,图19位置3),图17角接接头
GB/T 11345—1989
e)在容器外表面采用斜探头探伤(图18位置2)位置3
位置1
图18管座角焊缝
位置1
图19管座角焊缝
位置3
10.4.4.2管座角焊缝以直探头检验为主,对直探头扫查不到的区域或结构,缺陷方向性不适于采用直探头检验时,可采用斜探头检验,斜探头检验应符合10.4.1条的规定。10.4.5直探头检验的规程
a)推荐采用频率2.5MHz直探头或双晶直探头,探头与工件接触面的尺寸W应小于2VR;b)灵敏度可在与工件同曲率的试块上调节,也可采用计算法或DGS曲线法,以工件底面回波调节。其检验等级评定见表5。
表5直探头检验等级评定
检验等级
评定灵敏度
定量灵敏度
判废灵敏度
11规定检验
?般要求
11.1.1规定检验只对初始检验中被标记的部位进行检验。11.1.2探伤灵敏度应调节到评定灵敏度。B
11.1.3对所有反射波幅超过定量线的缺陷,均应确定其位置,最大反射波幅所在区域和缺陷指示长度。
11.2最大反射波幅的测定
11.2.1对判定为缺陷的部位,采取10.2.3条的探头扫查方式、增加探伤面、改变探头折射角度进行探测,测出最大反射波幅并与距离-波幅曲线作比较,确定波幅所在区域。波幅测定的允许误差为2dB。11.2.2最大反射波幅A与定量线SI的dB差值记为SL士1000
11.3位置参数的测定
11.3.1缺陷位置以获得缺陷最大反射波的位置来表示,根据相应的探头位置和反射波在荧光屏上的位置来确定如下全部或部分参数。
a)纵坐标L代表缺陷沿焊缝方向的位置。以检验区段编号为标记基准点(即原点)建立坐标。坐标正方向距离L表示缺陷到原点之间的距离见图20。
b)深度坐标h代表缺陷位置到探伤面的垂直距离(mm)。以缺陷最大反射波位置的深度值表示。c)横坐标q代表缺陷位置离开焊缝中心线的垂直距离,可由缺陷最大反射波位置的水平距离或简化水平距离求得。GB/T11345—1989
记为1.1
图20纵坐标L示意图
11.3.2缺陷的深度和水平距离(或简化水平距离)两数值中的一个可由缺陷最大反射波在荧光屏上的位置直接读出,另一数值可采用计算法、曲线法、作图法或缺陷定位尺求出。11.4尺寸参数的测定
应根据缺陷最大反射波幅确定缺陷当量@值或测定缺陷指示长度△1。11.4.1缺陷当量@,用当量平底孔直径表示,主要用于直探头检验,可采用公式计算、DGS曲线、试块对比或当量计算尺确定缺陷当量尺寸。11.4.2缺陷指示长度△1的测定推荐采用如下两种方法。a)当缺陷反射波只有一个高点时,用降低6dB相对灵敏度法测长见图21;b)在测长扫查过程中,如发现缺陷反射波峰值起伏变化,有多个高点,则以缺陷两端反射波极大值之间探头的移动长度确定为缺陷指示长度,即端点峰值法见图22。最大反射波
探头移动
缺陷指示长度
长度(mm)
图21相对灵敏度测长法
12缺陷评定
缺陷指示长度
图22端点峰值测长法
12.1超过评定线的信号应注意其是否具有裂纹等危害性缺陷特征,如有怀疑时应采取改变探头角度、增加探伤面、观察动态波型、结合结构工艺特征作判定,如对波型不能准确判断时,应辅以其他检验作综合判定。
12.2最大反射波幅位于Ⅱ区的缺陷,其指示长度小于10mm时按5mm计。12.3相邻两缺陷各向间距小于8mm时,两缺陷指示长度之和作为单个缺陷的指示长度。13检验结果的等级分类
13.1最大反射波幅位于Ⅱ区的缺陷,根据缺陷指示长度按表6的规定予以评级。1001
小提示:此标准内容仅展示完整标准里的部分截取内容,若需要完整标准请到上方自行免费下载完整标准文档。

标准图片预览:
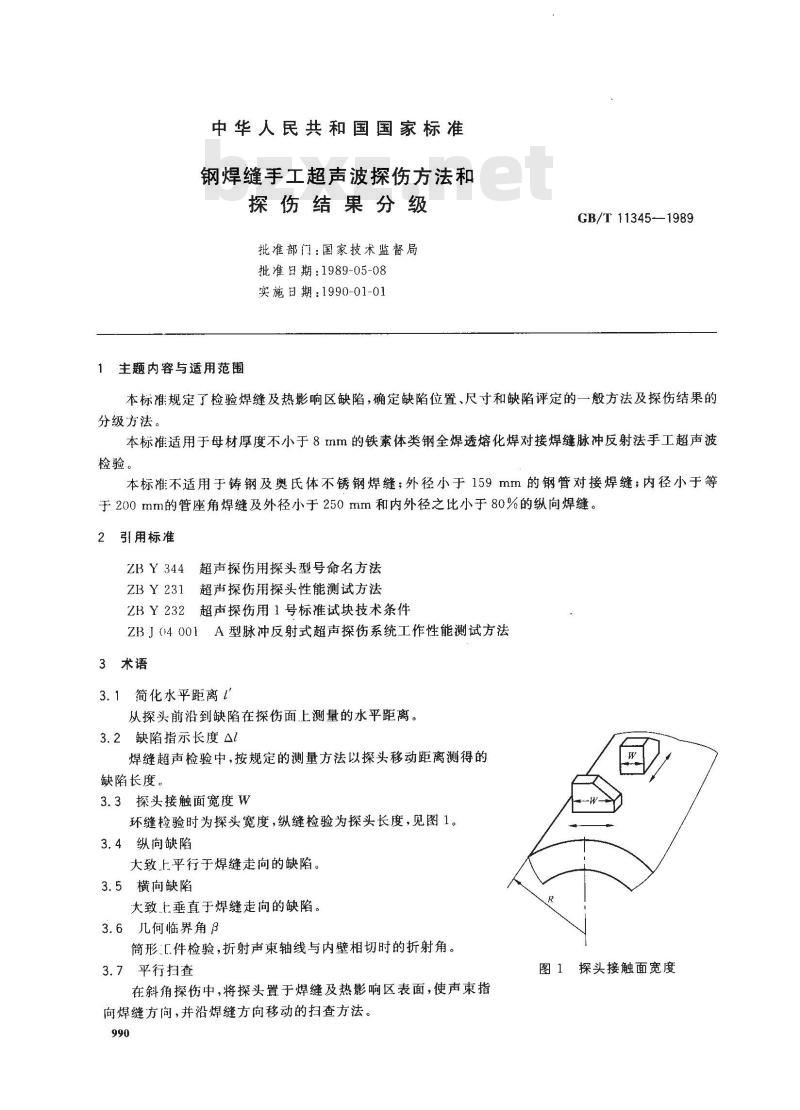
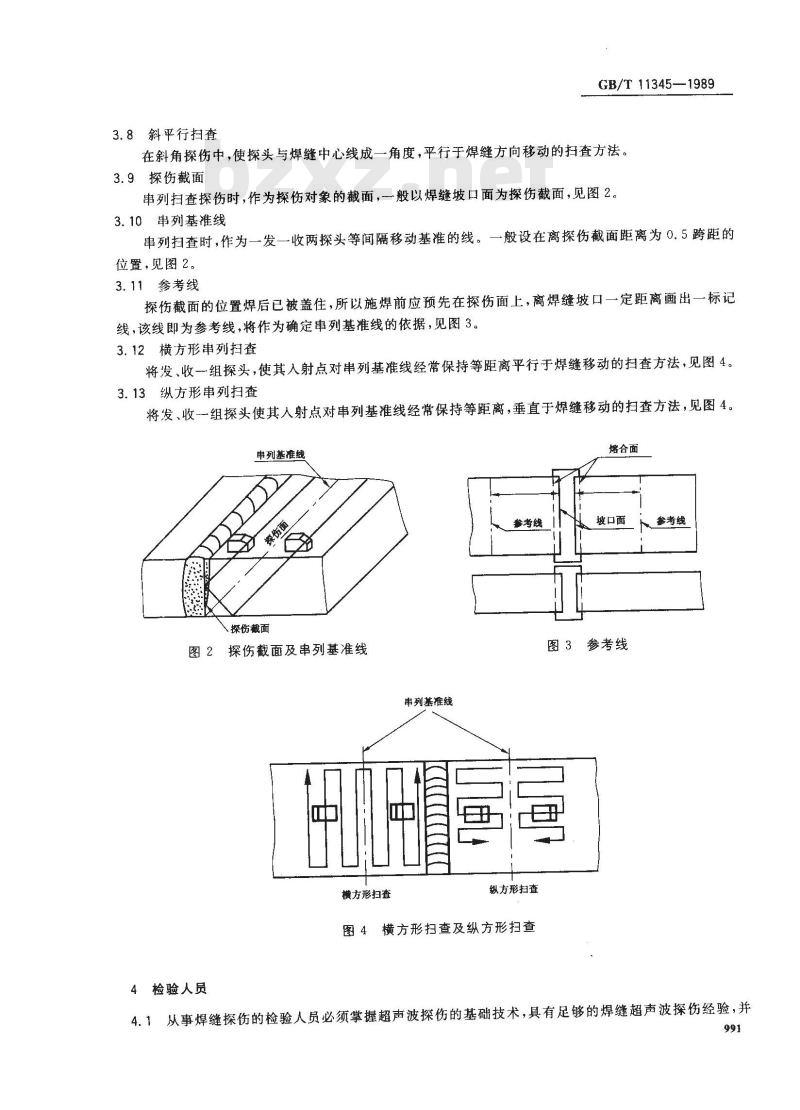
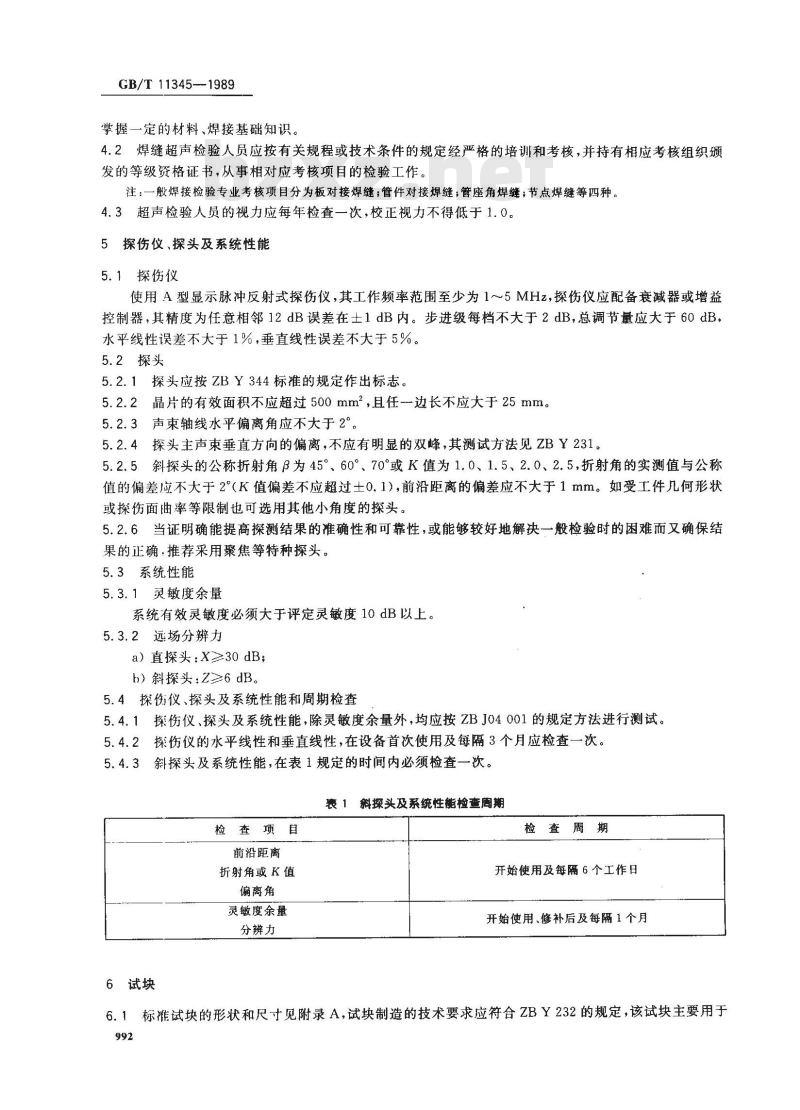
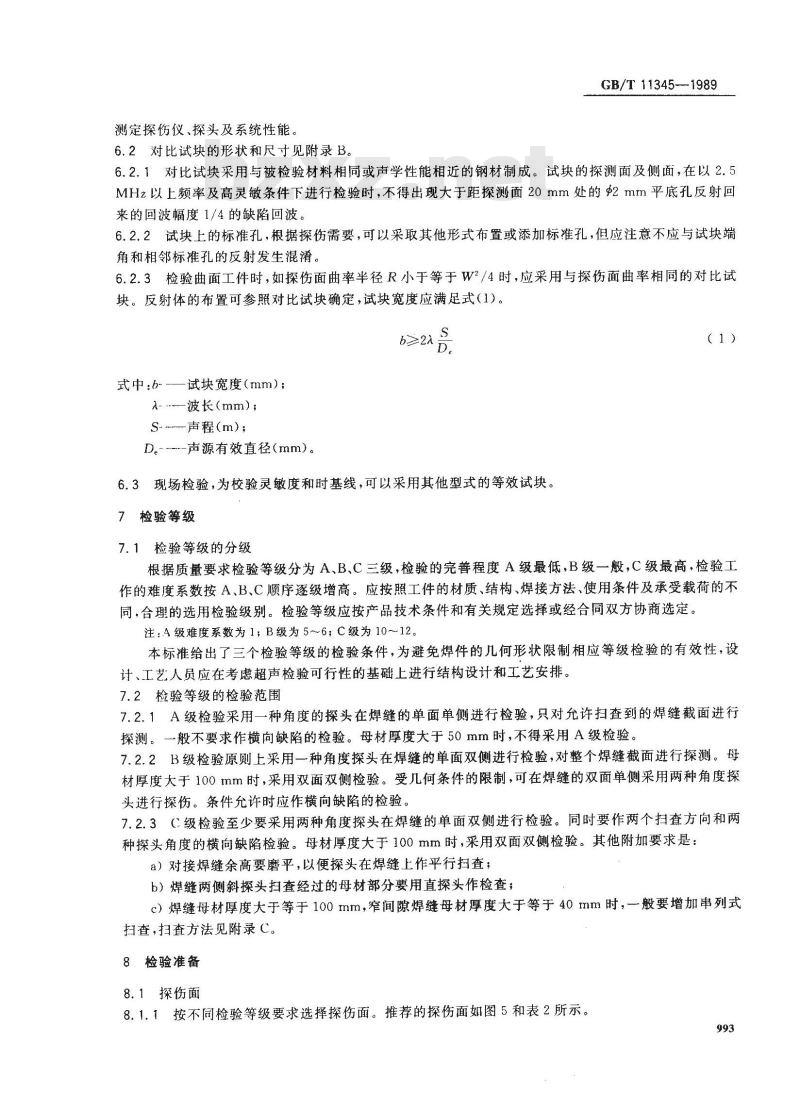
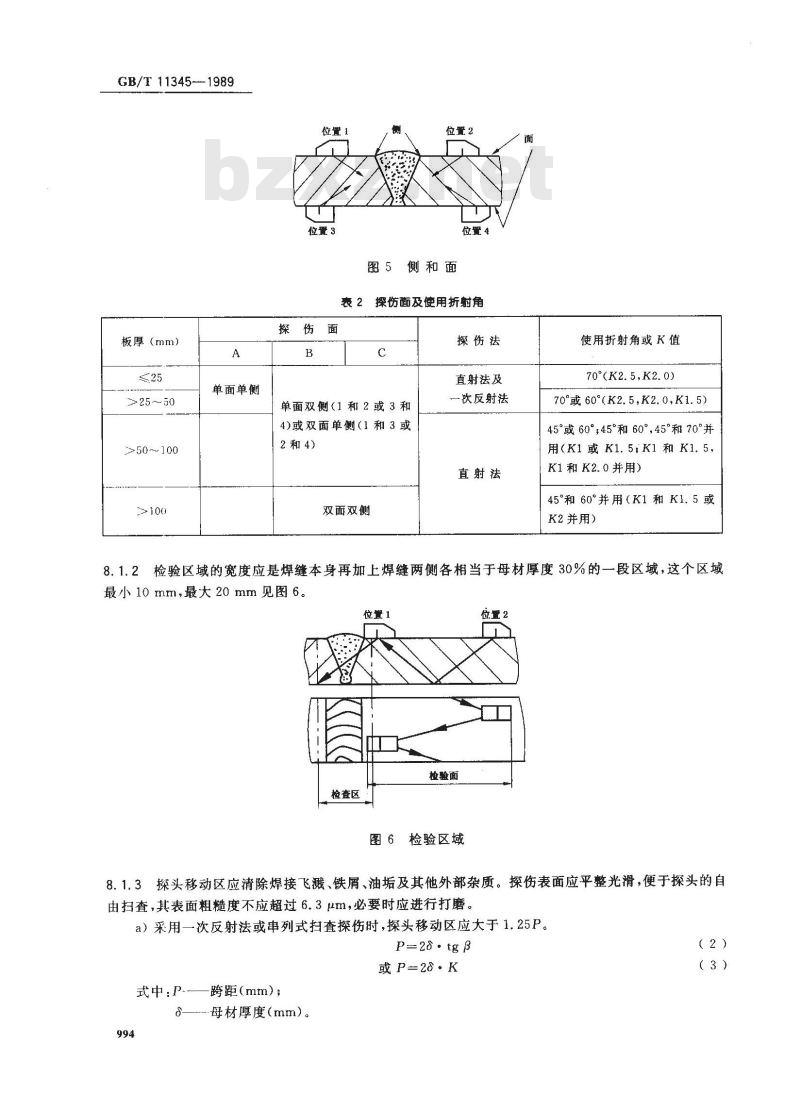
- 其它标准
- 热门标准
- 国家标准(GB)
- GB/T2828.1-2012 计数抽样检验程序 第1部分:按接收质量限(AQL)检索的逐批检验抽样计划
- GB3552-2018 船舶水污染物排放控制标准
- GB/T31732-2015 测土配方施肥配肥服务点技术规范
- GB/T24748-2009 往复式内燃机 飞轮 技术条件
- GB/T228.1-2021 金属材料 拉伸试验 第1部分:室温试验方法
- GB/T12706.1-2020 额定电压1 kV(Um=1.2 kV)到35 kV(Um=40.5 kV)挤包绝缘电力电缆及附件第1部分:额定电压1 kV(Um=1.2 kV)和3 kV(Um=3.6 kV)电缆
- GB/T10125-2021 人造气氛腐蚀试验 盐雾试验
- GB4943.1-2022 音视频、信息技术和通信技术设备 第1部分:安全要求
- GB4623-1994 环形预应力混凝土电杆
- GB/T14048.1-2023 低压开关设备和控制设备 第1部分:总则
- GB/T17886.1-1999 标称电压1kV及以下交流电力系统用非自愈式并联电容器 第1部分:总则 -- 性能、试验和定额 -- 安全要求 安装和运行导则
- GB/T25871-2010 结球生菜 预冷和冷藏运输指南
- GB175-2023 通用硅酸盐水泥
- GB50057-2010 建筑物防雷设计规范
- GB/T40175.1—2021 纺织品生物化学分析方法 第1部分:镉和铅(胶体金法)
- 行业新闻
请牢记:“bzxz.net”即是“标准下载”四个汉字汉语拼音首字母与国际顶级域名“.net”的组合。 ©2009 标准下载网 www.bzxz.net 本站邮件:bzxznet@163.com
网站备案号:湘ICP备2023016450号-1
网站备案号:湘ICP备2023016450号-1