- 您的位置:
- 标准下载网 >>
- 标准分类 >>
- 国家标准(GB) >>
- GB/T 12605-1990 钢管环缝熔化焊对接接头 射线透照工艺和质量分级
标准号:
GB/T 12605-1990
标准名称:
钢管环缝熔化焊对接接头 射线透照工艺和质量分级
标准类别:
国家标准(GB)
标准状态:
已作废-
发布日期:
1990-01-02 -
实施日期:
1991-01-02 -
作废日期:
2008-11-01 出版语种:
简体中文下载格式:
.rar.pdf下载大小:
372.63 KB
标准ICS号:
机械制造>>焊接、钎焊和低温焊>>25.160.40焊接接头中标分类号:
冶金>>金属理化性能试验方法>>H26金属无损检验方法
替代情况:
被GB/T 12605-2008代替采标情况:
≈ISO 1106-3-84

点击下载
标准简介:
标准下载解压密码:www.bzxz.net
本标准规定了钢管环缝熔化焊对接接头射线透照工艺方法及质量评定分级。本标准适用于管壁厚为3~120mm的低碳及低合金钢管焊缝,对焊制管件(三通、弯头)、焊管(纵缝、螺旋缝)及不锈管焊缝也可参照使用。 本标准不适用于摩擦焊、闪光焊等机械方法施焊的焊缝。 GB/T 12605-1990 钢管环缝熔化焊对接接头 射线透照工艺和质量分级 GB/T12605-1990

部分标准内容:
中华人民共和国国家标准
钢管环缝熔化焊对接接头
射线透照工艺和质量分级
Methods of radiographic inspection andquality clnssification of circumferential fusion weldedbutt joints in steel pipes and tubesGB/T.12605--90
本标准参照采用国际标准ISO1106-3一1984《熔化焊对接焊缝射线照相的推荐方法第三部分:壁厚50mm以下的钢管环缝熔化焊焊缝》。1主囊内容与适用范围
本标准规定了钢管环缝熔化焊对接接头(以下简称焊缝)射线透照工艺方法及质量评定分级。本标准适用于管壁厚为3~120mm的低碳及低合金钢管焊缝,对焊制管件(三通、弯头)、焊管(纵缝、螺旋缝)及不锈管焊缝也可参照使用。本标准不适用于摩擦焊、闪光焊等机械方法施焊的焊缝。2引用标准
GB3323钢熔化焊对接接头射线照相和质量分级GB4792放射卫生防护基本标准
GB5618线型象质计
金属熔化焊焊缝缺陷分类及说明GB6417
GB9445无损检测人员技术资格鉴定规则ZB'J04004射线照相探伤方法
电力建设施工及验收技术规范(钢制承压管道对接焊缝射线检验篇)SD 143
3检验人员
3.1从事射线检验的人员,必须持有国家有关部门颂发的,并与其工种和级别相适应的资格证书,同时,亦需持有国家卫生防护部门颁发的射线安全操作资格证书。3.2底片评判人员必须具有二、三级资格证书,视力不低于1.0。3.3射线检验人员应按照GB4792的规定进行身体检查,并符合要求。4表面状态
4.1焊缝及热影响区的表面质量(包括余高高度)应经外观检查合格。表面的不规则状态在底片上的图象应不掩盖焊缝中的缺陷或与之相混淆,否则应做适当的修正。4.2多层多道手工施焊的横焊焊缝其余高应进行打磨,以满足焊缝质量评定的要求。国豪技术监督局1990-12-18批准1991-12-01实施
5避照方法
5.1外遵法
5.1.1单壁透照法
GB/T 12605—90
射线源置于钢管外,胶片放置在离射线源最近侧钢管内壁相应焊缝的区城上,并与焊缝贴紧(见图1)。
射线源
图1单壁透照法
5.1.2双壁单投影法
射线源置于钢管外,胶片放置在远离射线源一侧的钢管外表面相应焊缝的区域上,并与焊缝贴紧(见图2)。
射线源
射线源
5.1.3双壁双投影法
图2双壁单投影法
5.1.3.1射线源置于钢管外,胶片放置在远离射线源一侧的钢管外表面相应焊缝的区域上,且使射线的透照方向与环形焊缝平面成适当的夹角,使上下两焊缝在底片上的影象呈椭圆形显示。其间距一般以3~10mm为宜(见图3a)。
5.1.3.2射线源置于钢管外,胶片放置在远离射线源一侧的钢管外表面相应焊缝的区域上,使射线垂直于焊缝(见图3b)。
5.2内遗遵法
5.2.1中心全周透照法
射线源
GB/T 12605—90
图3双壁双投影法
射线源
射线源置于钢管环缝的中心,胶片放置在钢管外表面环形焊缝上,并与之贴紧(见图4)。射线源
“图4中心全周透照法
5.2.2偏心透照法
射线源置于钢管环缝中心以外的位置上,胶片放置在钢管外表面相应焊缝的区域上,并与之贴紧(见图5)。
射线源
图5偏心透照法
透照工艺
6.1胶片
GB/T12605—90
透照用胶片应选用GB3323中规定的J1或J2型胶片,其固有灰雾度不大于0.3。6.2增感屏
一般选用金属增感屏,在特殊情况下经合同双方同意也可使用金属荧光增感屏。6.2.1
6.2.2金属增感屏应根据不同的射线能量选用,并参照表1的规定。表1
射线源种类
x射线<100kV
x射线100~250kV
X射线>250kV
Y射线Tm170
射线Ir192
射线 Cs137
射线Eu152+164
射线Co
注,如使用屏,应增加曝光时间。6.3射线源的选择
增感屏材料
铅或金属荧光
钢、铅
前屏厚度
0.02~0.03
0. 03~0. 05
0.05~0.16
0. 10~0. 20
0. 25~~1. 0
后屏厚度
≥0 16
0. 50~2. 0
6.3.1以管电压为400kV以下的X射线透照焊缝时,应根据透照厚度选取管电压值,一般需符合图6的规定。
5678910
透照厚度 T。、 如和
304050 60 70 80
图6透照厚度和允许使用最高管电压的关系当焊缝余高大于2mm,透照厚度比大于1.1时,允许降低反差。如选取高于图6规定的管电压值,其最大增量应不超过50kV。
6.3.2超过表2的透照厚度值时,可使用射线源174
Eu152+154
GB/T 12605--90
能量,MeV(平均值)
最小透照厚度,mm
注:表2所列最小透照厚度,并不代表射线与X射线具有等同检测灵敏度时的厚度。6.4象质计及放置位置
6.4.1外径大于89mm的钢管,其焊缝透照采用GB5618中规定的R10系列象质计。一般放置在胶片一端与管表面间(被检区长度的1/4处)。壁厚大于20mm时,需做对比试验。6.4.2外径小于和等于89mm的钢管,其焊缝透照应采用附录A规定的I型专用象质计。一般放置于被检区一端的胶片与管表面之间。6.4.3外径小于和等于76 mm的钢管,采用双壁双投影法透照椭圆~次成象时,应采用附录A规定的Ⅱ型专用象质计。一般放置在环缝上余高中心处。6.5未焊透深度对比块
对比焊缝的未焊透和内凹缺陷的黑度,应采用附录A规定的未焊透深度对比块。其应平行放置在距焊缝边缘5mm处。
6.6标记
6.6.1定位标记
表明焊缝透照部位的定位标记应为铅质符号,又可分为中心标记(4)和搭接标记()(当分段透照时称为有效区段标记)。
6.6.2识别标记
。被检的焊缝处附近均应有下列铅质识别标记:工件编号、焊缝编号和部位编号。如系返修的焊缝,其透照部位还应有返修标记。b。工件表面应做出永久保留的标记,以作为对每张底片位置对照的依据。一般用钢印在工件上做出永久标记,如不适合打钢印时,可用准确的草图作标记。6.6.3标记位置
定位标记和识别标记均需离焊缝边缘至少5mm,并在底片上显示。6.7透照的几何条件
6.7.1射线源至钢管外表面最小距离L1的确定,一般应符合图7的规定。175
GB/T 12605--90
wlulul
图?确定射线源至钢管距离的诺模图EE
6.7.2在特殊情况下,采用中心全周透照法时,其射线源至钢管内表面最小距离L的确定可由合同双方商定;但对焊缝根部质量必须具备有效监控措施。6.8分段透照的数量
6.8.1采用双壁单投影法透照时,射线源在钢管外表面的距离,当小于或等于15mm时,可分为不少于3段的透照,即每段中心角为120°;当大于15mm时,可分为至少4段的透照,即每段中心角为90。6.8.2对外径大于76mm且小于和等于89mm的钢管,其焊缝以双壁双投影法透照时,至少分2段透照,两次间隔90°。
6.8.3对外径小于和等于76mm的钢管,其焊缝以双壁双投影法透照时,允许椭圆-次成象,但需保证其检出范围不少于周长的90%。其测量计算方法应符合附录B的规定,底片质量应满足第9章的要求。
7防散射线措施
7.1暗盒后面应放置厚度为2~~3mm的铅板,以消除反向散射对胶片感光的影响。检查反向散射的方法应按GB3323中的规定进行。
7.2采用双壁双投影法透照小径管焊缝时,必须采用适当的铅罩遮挡,以屏蔽散射线,扩大检出范围,提高成象质量。
8胶片处理
GB/T 12605—90
胶片处理应按ZBJ04004标准中的有关要求进行。9底片质
9.1象质指数
9.1.1底片上应清晰显示出象质计钢丝影象,9.1.2在透照厚度比不大于1.1时,透照厚度值应根据透照方法确定,并应符合表3的规定。表3
外透法
内透法
注,①h为焊缝的余高。
②T为钢管实际壁厚。
单壁透照法
双壁单投影法
中心全周透照法
偏心透照法
透照厚度 T
T×2+h
9.1.3外径小于和等于76mm的钢管焊缝,用双壁双投影法透照椭圆-次成象时,其透照厚度应按附录B的规定计算,检出范应符合6.8.3条的要求。9.1.4象质指数应根据透照厚度确定,并符合表4的规定。表4透照厚度与象质指数的关系
透照厚度,mm
线直径,mm
9.2黑度
>8~1212~16≥16~20≥20~25>25~3232~50>50~80>80~120>6~8
底片有效检出范围内焊缝成象区的黑度范围应为1.5~3.5(包括固有灰雾度)。9.3标志
底片上应清晰地显示象质计、未焊透深度对比块、定位标记和识别标记。9.4不应有的假缺陷
底片有效评定区域内,不应有因胶片处理不当引起的假缺陷或其他妨碍评定的假缺陷。10评片
10.1评片时应在光线较暗的室内进行,并避免使底片表面产生反射的光源。6
10.2评片时应选用专用的观片灯,其应具有可调观察底片成象区最大黑度为3.5的亮度,照明区域应能遮蔽至所需的最小面积。
10.3评片时允许使用低倍放大镜(小于5倍),辅助观察底片的局部部分。11焊缝质量的分级
根据焊接缺陷类型和数量,把焊缝质量分为四级。11.1裂纹未熔合缺陷的评级
I、II、II级焊缝内应无裂纹、未熔合;凡焊缝内有裂纹、未熔合即为IV级,该级为通用的判废级。11.2圆型缺陷的评级
11.2.1评定方法
GB/T12605--90
11.2.1.1长宽比小于或等于3的缺陷(包括气孔、夹渣、夹钨)定义为圆型缺陷。11.2.1.2圆型缺陷用评定框尺进行评定,框尺应置于缺陷密集处,评定框尺寸的选定应依母材厚度确定,并符合表5的规定。
母材厚度T
评定框尺尺寸
10×10
>25~100
10×20
评定时带把圆型缺陷尺寸换算成点数,并应符合表6的规定。表6
缺陷长径,mm
11.2. 1. 4
>2~3
10×30
>6~8
评定时不计点数的缺陷尺寸应根据母材厚度确定,并符合表7的规定。表7
母材厚度T
>25~50
缺陷长径
≤1. 4% T
11.2.1.5当若干缺陷与评定框尺边界线相交时,该缺陷点数应按其数值的三分之一计算。mm
11.2.1.6当评定框尺附近缺陷较少,且确认只用该评定框尺大小划分级别不适当时,经合同双方协商,可将评定框尺面积沿焊缝方向扩大到3倍,求出缺陷总点数,用此值的三分之一进行评定。11.2.2分级评定
圆型缺陷的焊缝质量分级应根据母材厚度和评定框尺尺寸确定,各级允许点数的上限值应符合表8的规定。
评定框尺尺寸,mm
母材厚度,mm
质量级别
10×10
>10~~15
11.2.2.1单个圆型缺陷长径大于1/2T时,评为IV级。>15~25
10×20
>25~50
>50~100
10×30
11.2.2.2级焊缝或母材厚度小于或等于5mm的I级焊缝内,在评定框尺内不计点数的圆型缺陷数不得多于10个。
11.3条状缺陷的评级
11.3.1长宽比大于3的缺陷定义为条状缺陷,11.3.2条状缺陷的焊缝质量分级应根据母材厚度确定,并符合表9的规定。178
质量级别
母材厚度T
12TA60
T≥60
T≥45
GB/T 12605—90
连续长度
大于Ⅲ级者
往:①表中”L”为该组条状缺陷最长者的长度。条状缺陷总长
在任意直线上,相邻两缺陷间距均不超过 6 L 的任何一组缺陷,其累计长度在12T焊键长度内不超过T在任意直线上,相邻两缺陷间距均不超过 3 L 的任何一组缺陷,其累计长度在 6 T焊缝长度内不超过 T②当被检焊缝长度小于12T(ⅡI级)或6T(Ⅱ级)时,可按被检焊鐘长度与12T(I级)或6T(ⅡI级)的比例折算出被检焊缝长度内条状缺陷允许值。当折算的条状缺陷总长小于单个条状缺陷长度时,以单个条状缺陷长度为允许值。
11.4未焊透的评级
11.4.1外径大于89mm钢管,未焊透的焊缝质量分级应符合表10的规定,表10
未焊透深度
占壁厚百分比,%
极限深度,mm
连续未焊透长度bzxZ.net
未焊透总长,mm
断续未焊透长度
T≤12时,不大于4;12T<
60时,不大于1/3T;T≥60时,
不大于20
T≤9时不大于6,9间距小于6L时,不超过连续
未焊透长度,间距等于或大于
6L时,在任何12T焊缠长度内
不大于 T
间距小于3L时,不超过连续
未焊透长度,间距等于或大于
时,不大于2/3 T;T≥45时,不
大于30
大于Ⅲ级者
注:①表中\L”为断续未焊透中最长者,“T”为管壁厚度3时,在任何 6 T焊缝长度内不
②同一焊缝质量级别中,未焊透深度中占壁厚的百分比和极限深度此两个条件需同时满足。11.4.2外径小于和等于89mm钢管,未焊透的焊缝质量分级应符合表11的规定。表11
质量级别
未焊透深度
占壁厚百分比,%
极限深度,mm
大于Ⅲ级者
连续或断续未焊透总长
占焊缝周长的百分比,%
11.5根部内凹的评级
GB/T 12605—90
11.5.1外径大于89mm钢管,其焊缝根部内凹缺陷的质量分级应符合表12的规定。表12
质量级别
内凹深度
占壁厚百分比,%
极限深度,mm
大于Ⅲ级者
内凹总长占焊缝
总长的百分比,%
外径小于和等于89mm钢管,其焊缝根部内凹缺陷的质量分级应符合表13的规定,11.5.2
质量级别
11.6'综合评级
占壁厚百分比,%
极限深度,mm
大于Ⅲ级者
内凹总长占爆婆
总长的百分比,%
在评定框尺内,同时存在几种类型缺陷时,应先按各类缺陷分别评级,再将各自评定级别之和减1作为最终级别。
12检验报告及底片的保存
12.1检验报告的要求
爆缝透照后应写出检验报告,其内容至少应包括:产品(工程)名称、检验部位、检验方法、透照规范缺陷名称、评片级别、返修次数及日期等,检验报告的格式应参照附录C的规定。检验报告需经评片和复评人员签字。
12.2检验报告及底片的保存
检验报告和底片必须妥善保存至少五年,以备随时查核。180
1型专用象质计
GB/T 12605—90
附录A
专用象质计和未焊透深度对比块(简称对比块)的型式和规格
(补充件)
外径大于76mm且小于和等于89mm的钢管焊缝,采用双壁单投影法分段透照,应选用1型专用象质计。
A1.11型专用象质计由5根直径相同的钢丝和铅字符号组成,其制做要求应符合GB5618的规定。其型式、线编号见图A1。
GB/T12605-
图A11型专用象质计
L -25mm, 8-3~5 mm
A1.2图A1中编号由3位数字表示,第1、2位表示材料,第3位表示线编号。A21 型专用象质计
外径小于和等于76 mm的钢管焊缝,采用双壁双投影法透照,应选用II型专用象质计。Ⅱ型专用象质计由一一根或两根钢丝(其长度大于所透照的管子外周长)和铅字符号组成。制做要求应符合GB5618的规定,其型式、线编号见图A2。181
A3专用对比块
GBT126105—90A
搭接部
线编号
GB/T 12605-90
图A2II型专用象质计
专用对比块的型式和规格应符合图A3和表A1的规定。专用对比块应与被检体属同类材料。A-A旋转
管壁厚 T
第一阶厚度 T
B-B旋转
钢管外径
图A3专用对比块
第二阶厚度 T2
GB/ T 12605—90
搭接部
线编号
C-C能转
第三阶厚度T,
小提示:此标准内容仅展示完整标准里的部分截取内容,若需要完整标准请到上方自行免费下载完整标准文档。
钢管环缝熔化焊对接接头
射线透照工艺和质量分级
Methods of radiographic inspection andquality clnssification of circumferential fusion weldedbutt joints in steel pipes and tubesGB/T.12605--90
本标准参照采用国际标准ISO1106-3一1984《熔化焊对接焊缝射线照相的推荐方法第三部分:壁厚50mm以下的钢管环缝熔化焊焊缝》。1主囊内容与适用范围
本标准规定了钢管环缝熔化焊对接接头(以下简称焊缝)射线透照工艺方法及质量评定分级。本标准适用于管壁厚为3~120mm的低碳及低合金钢管焊缝,对焊制管件(三通、弯头)、焊管(纵缝、螺旋缝)及不锈管焊缝也可参照使用。本标准不适用于摩擦焊、闪光焊等机械方法施焊的焊缝。2引用标准
GB3323钢熔化焊对接接头射线照相和质量分级GB4792放射卫生防护基本标准
GB5618线型象质计
金属熔化焊焊缝缺陷分类及说明GB6417
GB9445无损检测人员技术资格鉴定规则ZB'J04004射线照相探伤方法
电力建设施工及验收技术规范(钢制承压管道对接焊缝射线检验篇)SD 143
3检验人员
3.1从事射线检验的人员,必须持有国家有关部门颂发的,并与其工种和级别相适应的资格证书,同时,亦需持有国家卫生防护部门颁发的射线安全操作资格证书。3.2底片评判人员必须具有二、三级资格证书,视力不低于1.0。3.3射线检验人员应按照GB4792的规定进行身体检查,并符合要求。4表面状态
4.1焊缝及热影响区的表面质量(包括余高高度)应经外观检查合格。表面的不规则状态在底片上的图象应不掩盖焊缝中的缺陷或与之相混淆,否则应做适当的修正。4.2多层多道手工施焊的横焊焊缝其余高应进行打磨,以满足焊缝质量评定的要求。国豪技术监督局1990-12-18批准1991-12-01实施
5避照方法
5.1外遵法
5.1.1单壁透照法
GB/T 12605—90
射线源置于钢管外,胶片放置在离射线源最近侧钢管内壁相应焊缝的区城上,并与焊缝贴紧(见图1)。
射线源
图1单壁透照法
5.1.2双壁单投影法
射线源置于钢管外,胶片放置在远离射线源一侧的钢管外表面相应焊缝的区域上,并与焊缝贴紧(见图2)。
射线源
射线源
5.1.3双壁双投影法
图2双壁单投影法
5.1.3.1射线源置于钢管外,胶片放置在远离射线源一侧的钢管外表面相应焊缝的区域上,且使射线的透照方向与环形焊缝平面成适当的夹角,使上下两焊缝在底片上的影象呈椭圆形显示。其间距一般以3~10mm为宜(见图3a)。
5.1.3.2射线源置于钢管外,胶片放置在远离射线源一侧的钢管外表面相应焊缝的区域上,使射线垂直于焊缝(见图3b)。
5.2内遗遵法
5.2.1中心全周透照法
射线源
GB/T 12605—90
图3双壁双投影法
射线源
射线源置于钢管环缝的中心,胶片放置在钢管外表面环形焊缝上,并与之贴紧(见图4)。射线源
“图4中心全周透照法
5.2.2偏心透照法
射线源置于钢管环缝中心以外的位置上,胶片放置在钢管外表面相应焊缝的区域上,并与之贴紧(见图5)。
射线源
图5偏心透照法
透照工艺
6.1胶片
GB/T12605—90
透照用胶片应选用GB3323中规定的J1或J2型胶片,其固有灰雾度不大于0.3。6.2增感屏
一般选用金属增感屏,在特殊情况下经合同双方同意也可使用金属荧光增感屏。6.2.1
6.2.2金属增感屏应根据不同的射线能量选用,并参照表1的规定。表1
射线源种类
x射线<100kV
x射线100~250kV
X射线>250kV
Y射线Tm170
射线Ir192
射线 Cs137
射线Eu152+164
射线Co
注,如使用屏,应增加曝光时间。6.3射线源的选择
增感屏材料
铅或金属荧光
钢、铅
前屏厚度
0.02~0.03
0. 03~0. 05
0.05~0.16
0. 10~0. 20
0. 25~~1. 0
后屏厚度
≥0 16
0. 50~2. 0
6.3.1以管电压为400kV以下的X射线透照焊缝时,应根据透照厚度选取管电压值,一般需符合图6的规定。
5678910
透照厚度 T。、 如和
304050 60 70 80
图6透照厚度和允许使用最高管电压的关系当焊缝余高大于2mm,透照厚度比大于1.1时,允许降低反差。如选取高于图6规定的管电压值,其最大增量应不超过50kV。
6.3.2超过表2的透照厚度值时,可使用射线源174
Eu152+154
GB/T 12605--90
能量,MeV(平均值)
最小透照厚度,mm
注:表2所列最小透照厚度,并不代表射线与X射线具有等同检测灵敏度时的厚度。6.4象质计及放置位置
6.4.1外径大于89mm的钢管,其焊缝透照采用GB5618中规定的R10系列象质计。一般放置在胶片一端与管表面间(被检区长度的1/4处)。壁厚大于20mm时,需做对比试验。6.4.2外径小于和等于89mm的钢管,其焊缝透照应采用附录A规定的I型专用象质计。一般放置于被检区一端的胶片与管表面之间。6.4.3外径小于和等于76 mm的钢管,采用双壁双投影法透照椭圆~次成象时,应采用附录A规定的Ⅱ型专用象质计。一般放置在环缝上余高中心处。6.5未焊透深度对比块
对比焊缝的未焊透和内凹缺陷的黑度,应采用附录A规定的未焊透深度对比块。其应平行放置在距焊缝边缘5mm处。
6.6标记
6.6.1定位标记
表明焊缝透照部位的定位标记应为铅质符号,又可分为中心标记(4)和搭接标记()(当分段透照时称为有效区段标记)。
6.6.2识别标记
。被检的焊缝处附近均应有下列铅质识别标记:工件编号、焊缝编号和部位编号。如系返修的焊缝,其透照部位还应有返修标记。b。工件表面应做出永久保留的标记,以作为对每张底片位置对照的依据。一般用钢印在工件上做出永久标记,如不适合打钢印时,可用准确的草图作标记。6.6.3标记位置
定位标记和识别标记均需离焊缝边缘至少5mm,并在底片上显示。6.7透照的几何条件
6.7.1射线源至钢管外表面最小距离L1的确定,一般应符合图7的规定。175
GB/T 12605--90
wlulul
图?确定射线源至钢管距离的诺模图EE
6.7.2在特殊情况下,采用中心全周透照法时,其射线源至钢管内表面最小距离L的确定可由合同双方商定;但对焊缝根部质量必须具备有效监控措施。6.8分段透照的数量
6.8.1采用双壁单投影法透照时,射线源在钢管外表面的距离,当小于或等于15mm时,可分为不少于3段的透照,即每段中心角为120°;当大于15mm时,可分为至少4段的透照,即每段中心角为90。6.8.2对外径大于76mm且小于和等于89mm的钢管,其焊缝以双壁双投影法透照时,至少分2段透照,两次间隔90°。
6.8.3对外径小于和等于76mm的钢管,其焊缝以双壁双投影法透照时,允许椭圆-次成象,但需保证其检出范围不少于周长的90%。其测量计算方法应符合附录B的规定,底片质量应满足第9章的要求。
7防散射线措施
7.1暗盒后面应放置厚度为2~~3mm的铅板,以消除反向散射对胶片感光的影响。检查反向散射的方法应按GB3323中的规定进行。
7.2采用双壁双投影法透照小径管焊缝时,必须采用适当的铅罩遮挡,以屏蔽散射线,扩大检出范围,提高成象质量。
8胶片处理
GB/T 12605—90
胶片处理应按ZBJ04004标准中的有关要求进行。9底片质
9.1象质指数
9.1.1底片上应清晰显示出象质计钢丝影象,9.1.2在透照厚度比不大于1.1时,透照厚度值应根据透照方法确定,并应符合表3的规定。表3
外透法
内透法
注,①h为焊缝的余高。
②T为钢管实际壁厚。
单壁透照法
双壁单投影法
中心全周透照法
偏心透照法
透照厚度 T
T×2+h
9.1.3外径小于和等于76mm的钢管焊缝,用双壁双投影法透照椭圆-次成象时,其透照厚度应按附录B的规定计算,检出范应符合6.8.3条的要求。9.1.4象质指数应根据透照厚度确定,并符合表4的规定。表4透照厚度与象质指数的关系
透照厚度,mm
线直径,mm
9.2黑度
>8~1212~16≥16~20≥20~25>25~3232~50>50~80>80~120>6~8
底片有效检出范围内焊缝成象区的黑度范围应为1.5~3.5(包括固有灰雾度)。9.3标志
底片上应清晰地显示象质计、未焊透深度对比块、定位标记和识别标记。9.4不应有的假缺陷
底片有效评定区域内,不应有因胶片处理不当引起的假缺陷或其他妨碍评定的假缺陷。10评片
10.1评片时应在光线较暗的室内进行,并避免使底片表面产生反射的光源。6
10.2评片时应选用专用的观片灯,其应具有可调观察底片成象区最大黑度为3.5的亮度,照明区域应能遮蔽至所需的最小面积。
10.3评片时允许使用低倍放大镜(小于5倍),辅助观察底片的局部部分。11焊缝质量的分级
根据焊接缺陷类型和数量,把焊缝质量分为四级。11.1裂纹未熔合缺陷的评级
I、II、II级焊缝内应无裂纹、未熔合;凡焊缝内有裂纹、未熔合即为IV级,该级为通用的判废级。11.2圆型缺陷的评级
11.2.1评定方法
GB/T12605--90
11.2.1.1长宽比小于或等于3的缺陷(包括气孔、夹渣、夹钨)定义为圆型缺陷。11.2.1.2圆型缺陷用评定框尺进行评定,框尺应置于缺陷密集处,评定框尺寸的选定应依母材厚度确定,并符合表5的规定。
母材厚度T
评定框尺尺寸
10×10
>25~100
10×20
评定时带把圆型缺陷尺寸换算成点数,并应符合表6的规定。表6
缺陷长径,mm
11.2. 1. 4
>2~3
10×30
>6~8
评定时不计点数的缺陷尺寸应根据母材厚度确定,并符合表7的规定。表7
母材厚度T
>25~50
缺陷长径
≤1. 4% T
11.2.1.5当若干缺陷与评定框尺边界线相交时,该缺陷点数应按其数值的三分之一计算。mm
11.2.1.6当评定框尺附近缺陷较少,且确认只用该评定框尺大小划分级别不适当时,经合同双方协商,可将评定框尺面积沿焊缝方向扩大到3倍,求出缺陷总点数,用此值的三分之一进行评定。11.2.2分级评定
圆型缺陷的焊缝质量分级应根据母材厚度和评定框尺尺寸确定,各级允许点数的上限值应符合表8的规定。
评定框尺尺寸,mm
母材厚度,mm
质量级别
10×10
>10~~15
11.2.2.1单个圆型缺陷长径大于1/2T时,评为IV级。>15~25
10×20
>25~50
>50~100
10×30
11.2.2.2级焊缝或母材厚度小于或等于5mm的I级焊缝内,在评定框尺内不计点数的圆型缺陷数不得多于10个。
11.3条状缺陷的评级
11.3.1长宽比大于3的缺陷定义为条状缺陷,11.3.2条状缺陷的焊缝质量分级应根据母材厚度确定,并符合表9的规定。178
质量级别
母材厚度T
12TA60
T≥60
T≥45
GB/T 12605—90
连续长度
大于Ⅲ级者
往:①表中”L”为该组条状缺陷最长者的长度。条状缺陷总长
在任意直线上,相邻两缺陷间距均不超过 6 L 的任何一组缺陷,其累计长度在12T焊键长度内不超过T在任意直线上,相邻两缺陷间距均不超过 3 L 的任何一组缺陷,其累计长度在 6 T焊缝长度内不超过 T②当被检焊缝长度小于12T(ⅡI级)或6T(Ⅱ级)时,可按被检焊鐘长度与12T(I级)或6T(ⅡI级)的比例折算出被检焊缝长度内条状缺陷允许值。当折算的条状缺陷总长小于单个条状缺陷长度时,以单个条状缺陷长度为允许值。
11.4未焊透的评级
11.4.1外径大于89mm钢管,未焊透的焊缝质量分级应符合表10的规定,表10
未焊透深度
占壁厚百分比,%
极限深度,mm
连续未焊透长度bzxZ.net
未焊透总长,mm
断续未焊透长度
T≤12时,不大于4;12T<
60时,不大于1/3T;T≥60时,
不大于20
T≤9时不大于6,9
未焊透长度,间距等于或大于
6L时,在任何12T焊缠长度内
不大于 T
间距小于3L时,不超过连续
未焊透长度,间距等于或大于
时,不大于2/3 T;T≥45时,不
大于30
大于Ⅲ级者
注:①表中\L”为断续未焊透中最长者,“T”为管壁厚度3时,在任何 6 T焊缝长度内不
②同一焊缝质量级别中,未焊透深度中占壁厚的百分比和极限深度此两个条件需同时满足。11.4.2外径小于和等于89mm钢管,未焊透的焊缝质量分级应符合表11的规定。表11
质量级别
未焊透深度
占壁厚百分比,%
极限深度,mm
大于Ⅲ级者
连续或断续未焊透总长
占焊缝周长的百分比,%
11.5根部内凹的评级
GB/T 12605—90
11.5.1外径大于89mm钢管,其焊缝根部内凹缺陷的质量分级应符合表12的规定。表12
质量级别
内凹深度
占壁厚百分比,%
极限深度,mm
大于Ⅲ级者
内凹总长占焊缝
总长的百分比,%
外径小于和等于89mm钢管,其焊缝根部内凹缺陷的质量分级应符合表13的规定,11.5.2
质量级别
11.6'综合评级
占壁厚百分比,%
极限深度,mm
大于Ⅲ级者
内凹总长占爆婆
总长的百分比,%
在评定框尺内,同时存在几种类型缺陷时,应先按各类缺陷分别评级,再将各自评定级别之和减1作为最终级别。
12检验报告及底片的保存
12.1检验报告的要求
爆缝透照后应写出检验报告,其内容至少应包括:产品(工程)名称、检验部位、检验方法、透照规范缺陷名称、评片级别、返修次数及日期等,检验报告的格式应参照附录C的规定。检验报告需经评片和复评人员签字。
12.2检验报告及底片的保存
检验报告和底片必须妥善保存至少五年,以备随时查核。180
1型专用象质计
GB/T 12605—90
附录A
专用象质计和未焊透深度对比块(简称对比块)的型式和规格
(补充件)
外径大于76mm且小于和等于89mm的钢管焊缝,采用双壁单投影法分段透照,应选用1型专用象质计。
A1.11型专用象质计由5根直径相同的钢丝和铅字符号组成,其制做要求应符合GB5618的规定。其型式、线编号见图A1。
GB/T12605-
图A11型专用象质计
L -25mm, 8-3~5 mm
A1.2图A1中编号由3位数字表示,第1、2位表示材料,第3位表示线编号。A21 型专用象质计
外径小于和等于76 mm的钢管焊缝,采用双壁双投影法透照,应选用II型专用象质计。Ⅱ型专用象质计由一一根或两根钢丝(其长度大于所透照的管子外周长)和铅字符号组成。制做要求应符合GB5618的规定,其型式、线编号见图A2。181
A3专用对比块
GBT126105—90A
搭接部
线编号
GB/T 12605-90
图A2II型专用象质计
专用对比块的型式和规格应符合图A3和表A1的规定。专用对比块应与被检体属同类材料。A-A旋转
管壁厚 T
第一阶厚度 T
B-B旋转
钢管外径
图A3专用对比块
第二阶厚度 T2
GB/ T 12605—90
搭接部
线编号
C-C能转
第三阶厚度T,
小提示:此标准内容仅展示完整标准里的部分截取内容,若需要完整标准请到上方自行免费下载完整标准文档。

标准图片预览:
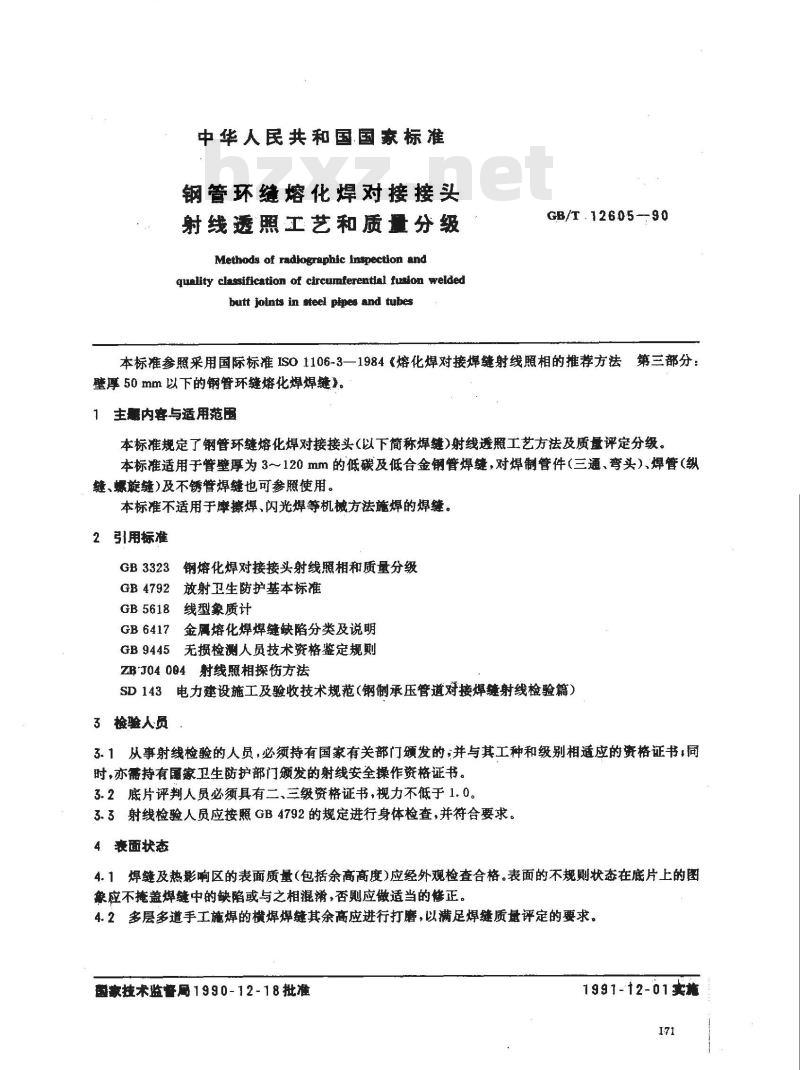
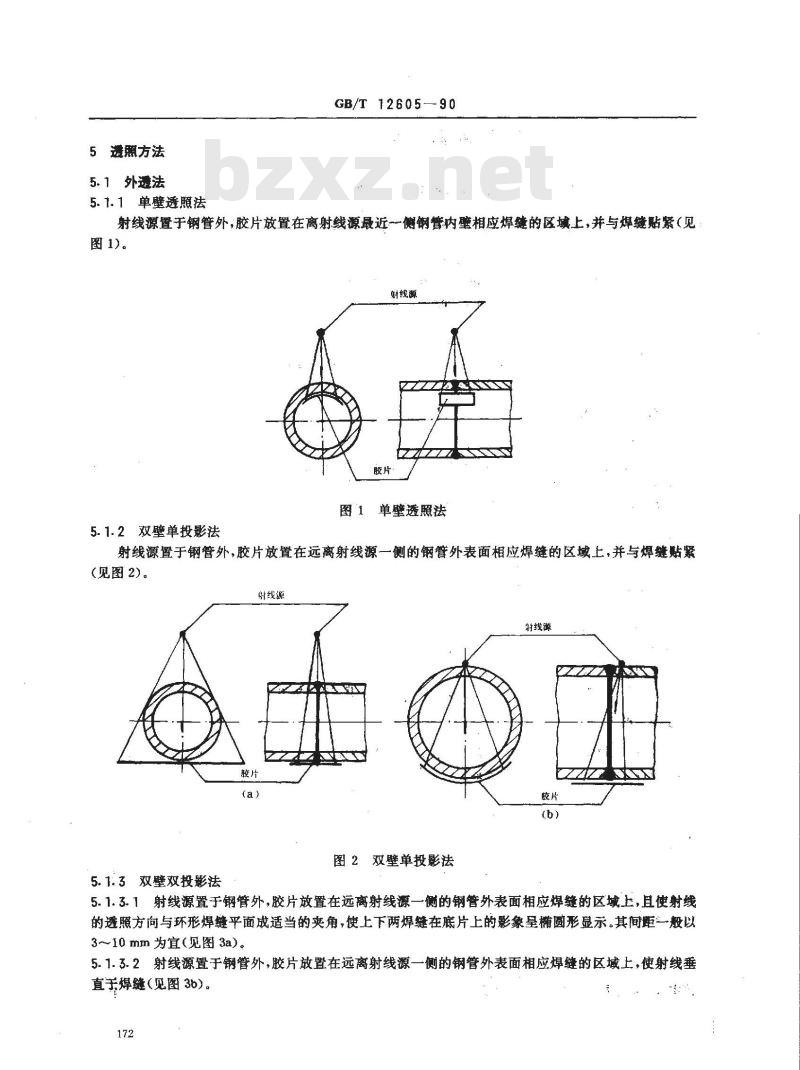
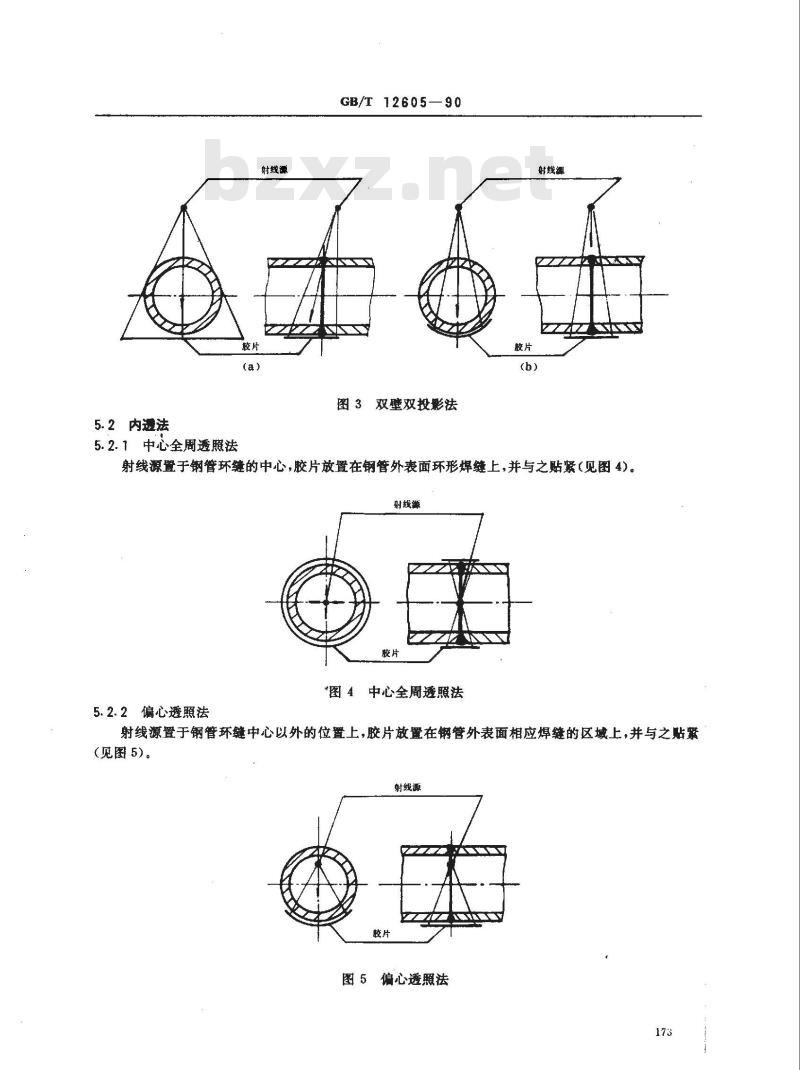
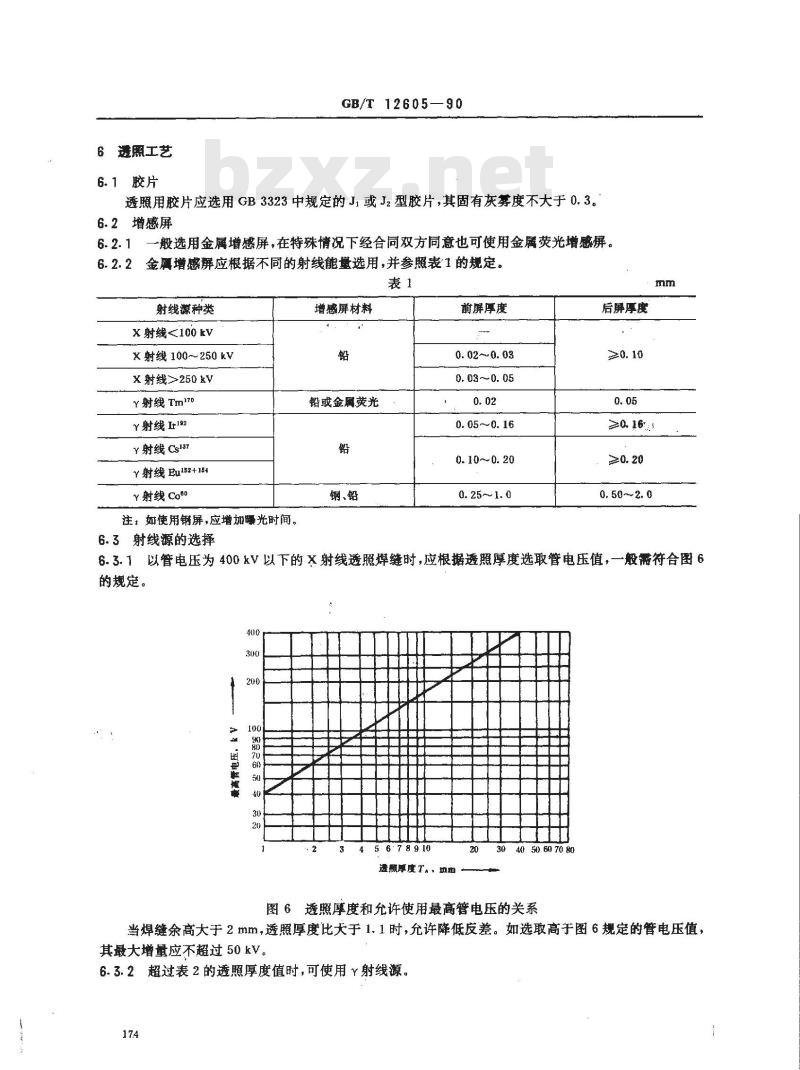
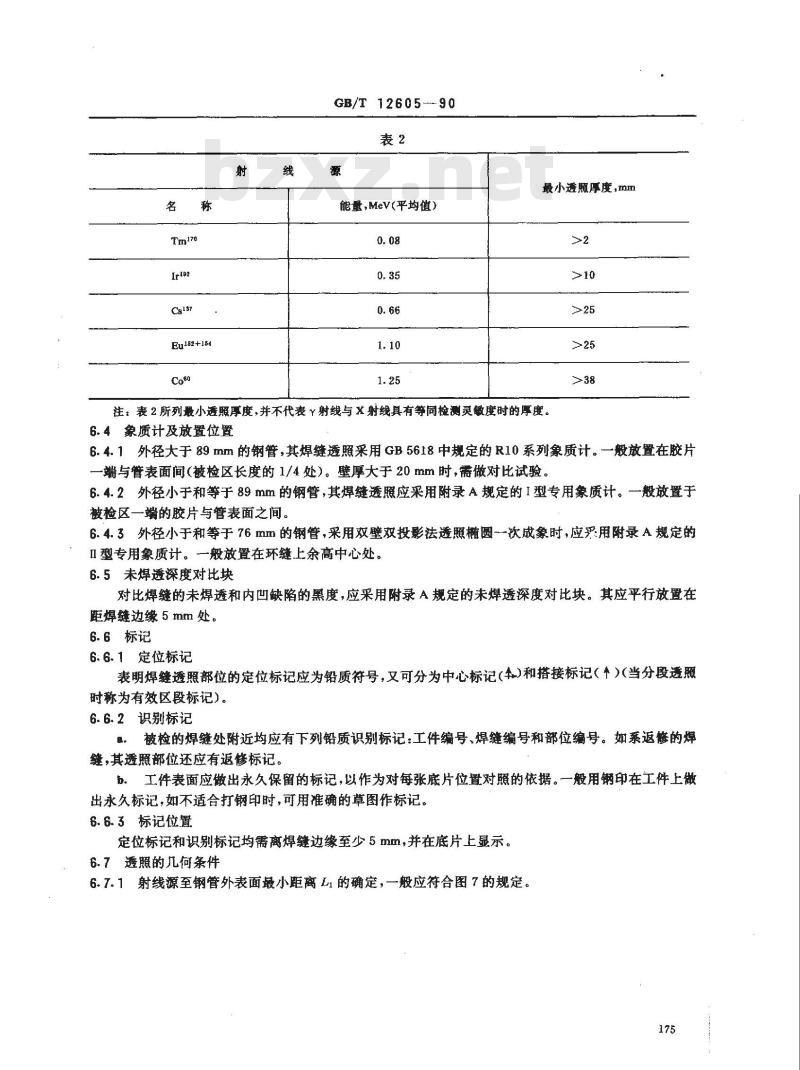
- 其它标准
- 热门标准
- 国家标准(GB)
- GB/T2828.1-2012 计数抽样检验程序 第1部分:按接收质量限(AQL)检索的逐批检验抽样计划
- GB/T6002.6-2003 纺织机械术语第6部分:卷纬机
- GB/T41251-2022 生产过程质量控制 生产装备全生命周期管理
- GB/T7251.1-2023 低压成套开关设备和控制设备 第1部分:总则
- GB5226.1-2019 机械电气安全 机械电气设备 第1部分:通用技术条件
- GB50268-2008 给水排水管道工程施工及验收规范
- GB/T3098.1-2010 紧固件机械性能 螺栓、螺钉和螺柱
- GB/T51435-2021 农村生活垃圾收运和处理技术标准
- GB/T12706.1-2020 额定电压1 kV(Um=1.2 kV)到35 kV(Um=40.5 kV)挤包绝缘电力电缆及附件第1部分:额定电压1 kV(Um=1.2 kV)和3 kV(Um=3.6 kV)电缆
- GB50235-2010 工业金属管道工程施工规范
- GB4943.1-2022 音视频、信息技术和通信技术设备 第1部分:安全要求
- GB/T3836.1-2021 爆炸性环境 第1部分:设备 通用要求
- GB7521—1987 多个控制器在一CA MAC机箱中
- GB50777-2012 ±800KV及以下换流站构支架施工及验收规范
- GB/T35024-2018 常见畜禽动物成分检测方法 液相芯片法
请牢记:“bzxz.net”即是“标准下载”四个汉字汉语拼音首字母与国际顶级域名“.net”的组合。 ©2009 标准下载网 www.bzxz.net 本站邮件:bzxznet@163.com
网站备案号:湘ICP备2023016450号-1
网站备案号:湘ICP备2023016450号-1