- 您的位置:
- 标准下载网 >>
- 标准分类 >>
- 石油天然气行业标准(SY) >>
- SY/T 6477-2000 含缺陷油气输送管道剩余强度评价方法第1部分:体积型缺陷
标准号:
SY/T 6477-2000
标准名称:
含缺陷油气输送管道剩余强度评价方法第1部分:体积型缺陷
标准类别:
石油天然气行业标准(SY)
标准状态:
现行-
发布日期:
2000-03-14 -
实施日期:
2000-10-01 出版语种:
简体中文下载格式:
.rar.pdf下载大小:
19.49 MB
标准ICS号:
石油及相关技术>>石油和天然气工业设备>>75.180.30容积测量和容积设备中标分类号:
石油>>石油勘探、开发、集输设备>>E98油、气集输设备

点击下载
标准简介:
标准下载解压密码:www.bzxz.net
本标准规定了含体积型缺陷油气输送管道的剩余强度评价方法。本标准适用于原设计标准与GB 50251《输气管道工程设计规范》或GB 50253.《输油管道工程设计规范》相一致的在役油气输送管道。 SY/T 6477-2000 含缺陷油气输送管道剩余强度评价方法第1部分:体积型缺陷 SY/T6477-2000

部分标准内容:
ICS75.180.30
备案号:6805—2000
石油工业标准化技术委员会CPSCSY
中华人民共和国石油天然气行业标准SY/T6477--2000
含缺陷油气输送管道剩余强度评价方法第1部分:体积型缺陷
The evaluation method of remaining strength of theoil & gas transmission pipeline with the flawPart 1: The volumetric type flaw.2000-03-14发布
国家石油和化学工业局
2000-10-01实施
SY/T6477—2000
引用标准
均匀腐蚀缺陷评价
局部金属损失评价
业标准化技不安员
附录A(标准的附录)管子壁厚、MAWP和应力计算公式附录B(标准的附录)
管道许用压缩应力计算
1范围
石油工业标准化技术委员会CPSC中华人民共和国石油天然气行业标准含缺陷油气输送管道剩余强度评价方法第1部分:体积型缺陷
The evaluation method of remaining strength ofthe oil & gas transmission pipeline with the flawPart 1: The volumetric type flaw本标准规定了含体积型缺陷油气输送管道的剩余强度评价方法。SY/T6477—2000Www.bzxZ.net
本标准适用于原设计标准与GB50251《输气管道工程设计规范》或GB50253《输油管道工程设计规范》相一致的在役油气输送管道。2引用标准
下列标准所包含的条文,通过在本标准中引用而构成为本标准的条文。本标准出版时,所示版本均为有效。所有标准都会被修订,使用本标准的各方应探讨使用下列标准最新版本的可能性。GB50251一1994输气管道工程设计规范GB50253—1994输油管道工程设计规范3定义
本标准采用如下定义。
3.1术语
3.1.1均匀腐蚀generalcorrosion金属表面以大体相同的腐蚀速率进行腐蚀,其腐蚀程度可以用平均腐蚀深度来表示。3.1.2局部金属损失localizedmetal loss在金属表面由于局部腐蚀或机械损伤造成的局部壁厚减薄。3.1.3局部腐蚀localcorrosion
腐蚀主要集中在金属表面某一区域,而表面其它部位腐蚀程度相对较小,或者几乎未被腐蚀。3.1.4金属损失量degreeofmetalloss金属因腐蚀或(和)机械损伤造成的厚度减小量。3.1.5剩余强度remainingstrength腐蚀或(和)机械损伤管道剩余承压能力。3.1.6设计压力designed pressure按设计规范确定的管道最大安全工作压力。3.1.7最大允许工作压力MAWPmaximumallowedworkingpressure管道允许工作的最大压力。对于未损伤管道,最大允许工作压力等于设计压力;对于损伤管道,最大允许工作压力用本标准确定。3.2符号及单位
LDx一含缺陷管道的极限载荷或塑性崩溃载荷,MPa;国家石油和化学工业局2000-03-14批准2000-10-01实施
SY/T6477-2000
Luc一完整管道的极限载荷或塑性崩溃载荷,MPa;MAWP一含缺陷管道降级后的最大允许工作压力,MPa;MAWP一管道未损伤前的最大允许工作压力(等于管道设计压力),MPa;RSF一剩余强度因子;
RSF。一许用剩余强度因子,本标准规定取0.9;L,一推荐的检测截面间距,mm;L一均厚长度,mm;
t一管子公称壁厚,mm;
p一内压,MPa;
tmin最小要求壁厚,mm;
tmm一最小测试壁厚,mm;
LOSS-t-tmm,mm;
FCA一未来腐蚀裕量,mm;
t-t-LOSS-FCA,mm;
tam—平均测试壁厚,mm;
tm一依轴向CTP得到的平均厚度,mm;tm一依环向CTP得到的平均厚度,mmCTP一危险厚度截面;
s一由轴向CTP和tmin确定的轴向金属损失长度,mm;c一由环向CTP和tmin确定的环向金属损失长度,mm;D;一管子内径,mm;
D。一管子外径,mm;
D-D;+2(LOSS+FCA),mm;
FS一设计系数,按GB50251和GB50253的规定取值;S一许用应力(S=oysFS),MPa;R一由tmm和tmin计算的剩余厚度比;Q一由R,确定的用于计算L的系数;tmin一依环向应力计算得到的最小要求壁厚,mm;thin一依轴向应力计算得到的最小要求壁厚,mm;ts一承受附加载荷增加的管子壁厚,mm;trg一未来操作要求壁厚,mm;
gr一对于轴向和环向沟槽状缺陷,表示缺陷的轴向尺寸;对于与轴向夹角为β的沟槽状缺陷,表示沿β方向尺寸。gl由CTP和tm确定,mm;gw一表示沟槽状缺陷的环向尺寸,mm;gr一表示沟槽状缺陷根部曲率半径,mm;β一沟槽状缺陷与轴向夹角,(°);gi一沟槽状缺陷根部临界曲率半径,mm;M一傅立叶因子;
入一壳体参数;
E一焊缝系数,按GB50251和GB50253规定取值;0y一材料最低屈服强度,MPa;
SY/T6477—2000
si一将CTP划分为若干子截面,s表示第i个子截面的金属损失长度(见图12),mm;A一基于s计算的金属损失面积(见图12),mm2;A一基于s计算的原始金属面积(见图12),mm2;入\一基于5计算的壳体参数;
M一基于入\计算的傅立叶因子;A一管道横截面积,mm2;
Aa一管道横截面的内孔面积,mm2;Am一管道横截面白的金属面积,mm?;Ix一管子截面惯性矩,mm;
A一横截面上金属损失所占面积,mm2;A,一用于计算剪应力的无金属损失区平均面积,mm2;A一用于计算剪应力的含金属损失区平均面积,mm2;Aw一内压作用的有效面积,mm?;a一中性轴到最大应力点的距离,mm;b一Aw的重心位置,mm;
d一金属损失最大深度,mm;
D一局部金属损失缺陷根部直径,mm;ILx一A,面的惯性矩,mm;
Ix一含金属损失缺陷的管子惯性矩,mm;R一局部金属损失缺陷根部半径,mm;y一Ar面的中性轴位置,mm;
—缺陷长度半角度(见图13和图14),rad;F一轴向作用力,N;
M一弯矩,N·mm;
Mr一扭矩,Nmm;
E一弹性模量,MPa;
om一薄膜应力,MPa;
0m一金属损失处的最大轴向薄膜应力,MPa;acm金属损失处的最大环向薄膜应力,MPa;t一金属损失处的最大剪应力,MPa;lu一无支撑段管段长度,mm;
M一壳体参数;
V一剪切力,N;
W一截面模量,mm2;
axa一发生局部鼓胀的临界压缩应力,MPa;Cca一发生整体鼓胀的临界压缩应力,MPa;Oba一承受内压和弯矩作用的管道许用压缩应力,MPa;tva一承受内压和剪切力作用的管道许用压缩应力,MPa。4总论
4.1总则
石油工业标准化技术委员会CPSCSY/T6477—2000
含有缺陷管道剩余强度评价是在缺陷检测基础上,对管道剩余承压能力的定量评价。若剩余强度评价结果表明损伤管道适用于目前的工作条件,则只要建立合适的监测(检测)程序,管道可以在目前工作条件下继续安全运行。若评价结果表明损伤管道不适合目前操作条件,则宜对该管道降级使用,也就是降低管道最大允许工作压力MAWP,本标准给出了最大允许工作压力的计算方法。本标准提供了含均匀腐蚀和局部金属损失两种体积型缺陷管道的剩余强度评价方法。本标准提供的剩余强度评价程序按缺陷类型分章编写。均匀腐蚀和局部金属损失两种体积型缺陷的评价分别按第5章和第6章提供的方法进行。有时如果主导损伤类型不明显,则可能需要同时采用上述两章的评价程序(例如管道上同时存在均匀腐蚀和局部金属损失缺陷)。含体积型腐蚀缺陷管道剩余强度评价一般包括以下程序;a)缺陷类型识别:推荐在面积为L·L[L的计算按5.4.1.1中c)】的腐蚀区域内至少选取15个厚度测试点,若测试数据的标准偏差与平均值之比小于20%,定为均匀腐蚀缺陷,否则定为局部金属损失。
b)选择评价方法:缺陷类型一且确定,就从本标准中选择相应的方法进行评价。c)资料、数据收集:管道剩余强度评价所需数据取决于缺陷类型。4.2给出了两种体积型缺陷评价共同需要的数据。
d)运用所选择的评价方法进行剩余强度评价。4.2所需资料和数据
4.2.1管道设计、制造及施工资料管道设计、制造及施工资料包括:a)材质及管子制造检测记录;
b)几何尺寸,包括管径和壁厚;c)设计压力和设计温度;
d)设计计算公式;
e)管道制造和防腐标准;
f)管道建造时的质量检验记录;g)材料性能数据;
h)水压试验记录,包括试验压力和温度。4.2.2管道运行和维修的历史记录管道运行和维修记录包括:
a)管道运行压力和温度记录;
b)管道维修记录;
c)管道在线检测记录,包括壁厚测量结果和其它无损检测结果;d)水压试验记录,包括试验压力和温度;e)管线巡视记录(如非法压线、开挖、地质情况等);f)误操作记录。
4.2.3金属损失定量化
4.23,1对每一种体积型缺陷,本标准均提供了金属损失定量化方法。4.2.3.2根据所期望的管道运行周期,建立管道未来腐蚀裕量FCA。FCA由腐蚀速率乘以所期望的管道运行周期计算得到。腐蚀速率可以基于以下三个方面得到:以往的腐蚀缺陷检测数据;
现场挂片试验数据;
一已报道的该管道材料在类似腐蚀环境下的腐蚀速率。4.2.4推荐的缺陷检测技术
石油工业标准化技术委员会CPSCSY/T6477—2000
在第5章和第6章中分别推荐了均匀腐蚀和局部金属损失缺陷的无损检测技术。4.3评价技术和判据
第5章和第6章都提供了两个级别的评价程序,图1示出了两个评价级别的逻辑关系。总体上,每个评价级别都在保守度、评价所需数据量、评价人员的技能水平、分析过程的复杂性四者之间达到了平衡。-级评价最为保守,但最容易使用。评价一般由一级评价到二级评价的顺序执行。4.3.1级评价
一级评价使用的检测数据和管道数据最少,提供了计算过程简单而评价结果偏于保守的筛选判据。获得评价所需数据
势桥程擎
按一级评价准则,
缺陷可以接受吗?
按一级评价准则,
确定MAWP,
降压使用吗?
热行三级评价
程序吗?
接二级评价准则:
缺陷可以接受吗?
降压使用吗?
进行维修或换管处理
继续使用
按二级评价准则,
确定MAWP,
图1含体积型缺陷管道剩余强度评价流程图SY/T6477-2000
4.3.2二级评价
二级评价提供了更为详尽的评价程序。与一级评价相比,二级评价结果更为准确。4.3.3剩余强度因子RSF及评价判据本标准以RSF作为含体积型腐蚀缺陷管道剩余强度的评价判据。RSF定义如下:RSF
式中:Lpc——含缺陷管道的极限载荷或塑性崩溃载荷,MPa;Luc——完整管道的极限载荷或塑性崩溃载荷,MPa。 (1)
RSF可以利用弹塑性分析、极限载荷理论和传统的计算公式计算得出。本标准在均匀腐蚀和局部金属损失缺陷评价程序中均提供了RSF的计算公式。若RSF计算值大于推荐的RSF下限值,则管道可以继续在目前压力下继续运行,否则应降级使用。降级后的最大允许工作压力计算方法如下:RSFRSF≥RSF,时:
MAWP,=MAWP(RSF
MAWP.=MAWP
式中:MAWP一一含缺陷管道降级后的最大允许工作压力,MPa;MAWP一—管道未损伤前的最大允许工作压力(等于管道设计压力),MPa;RSF——含缺陷管道剩余强度因子计算值;RSF。——许用剩余强度因子,本标准规定取0.9。5均匀腐蚀缺陷评价
(2)
5.1概述
本章的评价程序可以用来评价含均匀腐蚀缺陷的管道,均匀腐蚀缺陷可以在管道外表面,也可以在管道内表面。对于均匀腐蚀缺陷,本章提供了点测厚法或厚度截面法两种金属损失定量方法。图2给出了均匀腐蚀缺陷评价的流程图。5.2适用性
只有满足下述条件的管道才能应用本章提供的剩余强度评价程序:a)管道材料是延性的,且在运行过程中不会因为温度或其它工艺环境发生脆化b)管道不含裂纹型缺陷;
c)用本方法评价的管段可以是直管段,也可以是弯头。5.3所需资料和数据
5.3.1管道设计、制造及施工资料需要搜集的管道设计、制造及施工资料见4.2.1。5.3.2管道运行和维修历史记录
需要搜集的管道以往运行和维修记录见4.2.2。5.3.3金属损失定量化
5.3.3.1为了评价均匀腐蚀缺陷,必须测量金属损失区域的剩余壁厚,即对金属损失定量化。获得金属损失数据有两种方法可供选择。如果最小剩余壁厚与最小要求壁厚【见附录A(标准的附录】之比大于0.7,宜用点测厚法对金属损失进行定量化;反之,宜采用厚度截面法。5.3.3.2若采用点测厚法对金属损失区域进行定量化,其测试点的数量依金属损失区域面积而定,推荐在面积为L·L[L的计算按5.4.1.1中c)】的腐蚀区域内至少选取15个厚度测试点。5.3.3.3若采用厚度截面法来对金属损失进行定量化,按以下步骤确定检测截面和危险厚度截面6
CTP:
求平均厚度吗?
金属损失可以接受
简单评价
t运用第4
章提供的级和
级评价判据
SY/T6477—2000
计算最小要求壁厚tain
找出金属损失区域
采用厚度截面法吗?
确定检测截面
沿检测裁面测量和记录剩余壁厚基于检测数据建立轴向和环向
危险裁面CTP
确定s,C,tL和t
利用厚度截面吗?
S≤L吗?
选择评价方法
厚度法
确定t运用第
4章提供的一级和
级评价判据
采用直接测厚法:增加
NDE以证实金属损失为
均匀腐蚀缺陷
由金属损失区域壁厚
测试结果确定t_和L
局部金属
损失评价
作为局部金属损
失,按第5章提
供的方法评价
图2均匀腐蚀缺陷评价流程图
a)第1步:找出金属损失区域,确定检测截面的方向和长度。如果内压产生的环向应力起主导作用,检测截面定为轴向;如果内压和附加载荷产生的轴向应力起主导作用,检测截面定为环向(如图3所示)。注意检测截面的长度应足以表征金属损失区域。b)第2步:沿每一个检测截面间隔测量剩余壁厚,并确定每个检测截面的最小测量壁厚tmm。7
石油工业标准化技术委员会CPSOSY/T6477—2000
金属损失区
(a)直管段
外缘线-
金属损失区
内缘线
(b)弯头
图3金属损失区域的检测截面示意图测量过程中测量点间距应根据缺陷的具体情况随时调整,以保证获得准确的剩余厚度截面。式(4)给出了推荐的检测截面间距,每个检测截面至少测量5个点的厚度。表1给出了检测数据的记录格式。
Ls=max[0.18/D;tmin,12.7mm]
式中:Ls—推荐的检测截面间距,mm;8
石油工业标准化技术委员会CPSOSY/T 6477-2000
管子内径,mm;
未来腐蚀裕量:
管子外径:
名义壁厚:
最小要求壁厚:
-基于管道设计压力计算的管道最小要求壁厚【见附录A(标准的附录)],mm。表1均匀腐蚀缺陷检测数据记录格式缺陷尺寸(s和c):
每个检测截面的厚度测试结果以下列格式记录:检测截面编号:
检测截面编号:
检测截面编号:
检测截面编号:
c)第3步:建立危险厚度截面CTP。将所有的平行检测截面上每个测量位置最小厚度向同一平面投影得到CTP(如图4所示)。1)将C~Cs各检测截面的最小厚度向同一个平行于轴向的平面投影,得到轴向CTP。轴向金属损失长度s用CTP和tmin来确定(如图4所示)。2)将M,~Ms检测截面的最小厚度向同一个平行于环向的平面投影,得到环向CTP。环向金属损失长度用CTP和t来确定(如图4所示)。3)如果金属损失面积比较大,仅采用个危险截面来评价往往导致评价结果过份保守,宜采用几个轴向或环向CTP来评价金属损失:CTP的个数可以通过限定建立每个CTP的检测截面数量最多不超过5个来确定。9
小提示:此标准内容仅展示完整标准里的部分截取内容,若需要完整标准请到上方自行免费下载完整标准文档。
备案号:6805—2000
石油工业标准化技术委员会CPSCSY
中华人民共和国石油天然气行业标准SY/T6477--2000
含缺陷油气输送管道剩余强度评价方法第1部分:体积型缺陷
The evaluation method of remaining strength of theoil & gas transmission pipeline with the flawPart 1: The volumetric type flaw.2000-03-14发布
国家石油和化学工业局
2000-10-01实施
SY/T6477—2000
引用标准
均匀腐蚀缺陷评价
局部金属损失评价
业标准化技不安员
附录A(标准的附录)管子壁厚、MAWP和应力计算公式附录B(标准的附录)
管道许用压缩应力计算
1范围
石油工业标准化技术委员会CPSC中华人民共和国石油天然气行业标准含缺陷油气输送管道剩余强度评价方法第1部分:体积型缺陷
The evaluation method of remaining strength ofthe oil & gas transmission pipeline with the flawPart 1: The volumetric type flaw本标准规定了含体积型缺陷油气输送管道的剩余强度评价方法。SY/T6477—2000Www.bzxZ.net
本标准适用于原设计标准与GB50251《输气管道工程设计规范》或GB50253《输油管道工程设计规范》相一致的在役油气输送管道。2引用标准
下列标准所包含的条文,通过在本标准中引用而构成为本标准的条文。本标准出版时,所示版本均为有效。所有标准都会被修订,使用本标准的各方应探讨使用下列标准最新版本的可能性。GB50251一1994输气管道工程设计规范GB50253—1994输油管道工程设计规范3定义
本标准采用如下定义。
3.1术语
3.1.1均匀腐蚀generalcorrosion金属表面以大体相同的腐蚀速率进行腐蚀,其腐蚀程度可以用平均腐蚀深度来表示。3.1.2局部金属损失localizedmetal loss在金属表面由于局部腐蚀或机械损伤造成的局部壁厚减薄。3.1.3局部腐蚀localcorrosion
腐蚀主要集中在金属表面某一区域,而表面其它部位腐蚀程度相对较小,或者几乎未被腐蚀。3.1.4金属损失量degreeofmetalloss金属因腐蚀或(和)机械损伤造成的厚度减小量。3.1.5剩余强度remainingstrength腐蚀或(和)机械损伤管道剩余承压能力。3.1.6设计压力designed pressure按设计规范确定的管道最大安全工作压力。3.1.7最大允许工作压力MAWPmaximumallowedworkingpressure管道允许工作的最大压力。对于未损伤管道,最大允许工作压力等于设计压力;对于损伤管道,最大允许工作压力用本标准确定。3.2符号及单位
LDx一含缺陷管道的极限载荷或塑性崩溃载荷,MPa;国家石油和化学工业局2000-03-14批准2000-10-01实施
SY/T6477-2000
Luc一完整管道的极限载荷或塑性崩溃载荷,MPa;MAWP一含缺陷管道降级后的最大允许工作压力,MPa;MAWP一管道未损伤前的最大允许工作压力(等于管道设计压力),MPa;RSF一剩余强度因子;
RSF。一许用剩余强度因子,本标准规定取0.9;L,一推荐的检测截面间距,mm;L一均厚长度,mm;
t一管子公称壁厚,mm;
p一内压,MPa;
tmin最小要求壁厚,mm;
tmm一最小测试壁厚,mm;
LOSS-t-tmm,mm;
FCA一未来腐蚀裕量,mm;
t-t-LOSS-FCA,mm;
tam—平均测试壁厚,mm;
tm一依轴向CTP得到的平均厚度,mm;tm一依环向CTP得到的平均厚度,mmCTP一危险厚度截面;
s一由轴向CTP和tmin确定的轴向金属损失长度,mm;c一由环向CTP和tmin确定的环向金属损失长度,mm;D;一管子内径,mm;
D。一管子外径,mm;
D-D;+2(LOSS+FCA),mm;
FS一设计系数,按GB50251和GB50253的规定取值;S一许用应力(S=oysFS),MPa;R一由tmm和tmin计算的剩余厚度比;Q一由R,确定的用于计算L的系数;tmin一依环向应力计算得到的最小要求壁厚,mm;thin一依轴向应力计算得到的最小要求壁厚,mm;ts一承受附加载荷增加的管子壁厚,mm;trg一未来操作要求壁厚,mm;
gr一对于轴向和环向沟槽状缺陷,表示缺陷的轴向尺寸;对于与轴向夹角为β的沟槽状缺陷,表示沿β方向尺寸。gl由CTP和tm确定,mm;gw一表示沟槽状缺陷的环向尺寸,mm;gr一表示沟槽状缺陷根部曲率半径,mm;β一沟槽状缺陷与轴向夹角,(°);gi一沟槽状缺陷根部临界曲率半径,mm;M一傅立叶因子;
入一壳体参数;
E一焊缝系数,按GB50251和GB50253规定取值;0y一材料最低屈服强度,MPa;
SY/T6477—2000
si一将CTP划分为若干子截面,s表示第i个子截面的金属损失长度(见图12),mm;A一基于s计算的金属损失面积(见图12),mm2;A一基于s计算的原始金属面积(见图12),mm2;入\一基于5计算的壳体参数;
M一基于入\计算的傅立叶因子;A一管道横截面积,mm2;
Aa一管道横截面的内孔面积,mm2;Am一管道横截面白的金属面积,mm?;Ix一管子截面惯性矩,mm;
A一横截面上金属损失所占面积,mm2;A,一用于计算剪应力的无金属损失区平均面积,mm2;A一用于计算剪应力的含金属损失区平均面积,mm2;Aw一内压作用的有效面积,mm?;a一中性轴到最大应力点的距离,mm;b一Aw的重心位置,mm;
d一金属损失最大深度,mm;
D一局部金属损失缺陷根部直径,mm;ILx一A,面的惯性矩,mm;
Ix一含金属损失缺陷的管子惯性矩,mm;R一局部金属损失缺陷根部半径,mm;y一Ar面的中性轴位置,mm;
—缺陷长度半角度(见图13和图14),rad;F一轴向作用力,N;
M一弯矩,N·mm;
Mr一扭矩,Nmm;
E一弹性模量,MPa;
om一薄膜应力,MPa;
0m一金属损失处的最大轴向薄膜应力,MPa;acm金属损失处的最大环向薄膜应力,MPa;t一金属损失处的最大剪应力,MPa;lu一无支撑段管段长度,mm;
M一壳体参数;
V一剪切力,N;
W一截面模量,mm2;
axa一发生局部鼓胀的临界压缩应力,MPa;Cca一发生整体鼓胀的临界压缩应力,MPa;Oba一承受内压和弯矩作用的管道许用压缩应力,MPa;tva一承受内压和剪切力作用的管道许用压缩应力,MPa。4总论
4.1总则
石油工业标准化技术委员会CPSCSY/T6477—2000
含有缺陷管道剩余强度评价是在缺陷检测基础上,对管道剩余承压能力的定量评价。若剩余强度评价结果表明损伤管道适用于目前的工作条件,则只要建立合适的监测(检测)程序,管道可以在目前工作条件下继续安全运行。若评价结果表明损伤管道不适合目前操作条件,则宜对该管道降级使用,也就是降低管道最大允许工作压力MAWP,本标准给出了最大允许工作压力的计算方法。本标准提供了含均匀腐蚀和局部金属损失两种体积型缺陷管道的剩余强度评价方法。本标准提供的剩余强度评价程序按缺陷类型分章编写。均匀腐蚀和局部金属损失两种体积型缺陷的评价分别按第5章和第6章提供的方法进行。有时如果主导损伤类型不明显,则可能需要同时采用上述两章的评价程序(例如管道上同时存在均匀腐蚀和局部金属损失缺陷)。含体积型腐蚀缺陷管道剩余强度评价一般包括以下程序;a)缺陷类型识别:推荐在面积为L·L[L的计算按5.4.1.1中c)】的腐蚀区域内至少选取15个厚度测试点,若测试数据的标准偏差与平均值之比小于20%,定为均匀腐蚀缺陷,否则定为局部金属损失。
b)选择评价方法:缺陷类型一且确定,就从本标准中选择相应的方法进行评价。c)资料、数据收集:管道剩余强度评价所需数据取决于缺陷类型。4.2给出了两种体积型缺陷评价共同需要的数据。
d)运用所选择的评价方法进行剩余强度评价。4.2所需资料和数据
4.2.1管道设计、制造及施工资料管道设计、制造及施工资料包括:a)材质及管子制造检测记录;
b)几何尺寸,包括管径和壁厚;c)设计压力和设计温度;
d)设计计算公式;
e)管道制造和防腐标准;
f)管道建造时的质量检验记录;g)材料性能数据;
h)水压试验记录,包括试验压力和温度。4.2.2管道运行和维修的历史记录管道运行和维修记录包括:
a)管道运行压力和温度记录;
b)管道维修记录;
c)管道在线检测记录,包括壁厚测量结果和其它无损检测结果;d)水压试验记录,包括试验压力和温度;e)管线巡视记录(如非法压线、开挖、地质情况等);f)误操作记录。
4.2.3金属损失定量化
4.23,1对每一种体积型缺陷,本标准均提供了金属损失定量化方法。4.2.3.2根据所期望的管道运行周期,建立管道未来腐蚀裕量FCA。FCA由腐蚀速率乘以所期望的管道运行周期计算得到。腐蚀速率可以基于以下三个方面得到:以往的腐蚀缺陷检测数据;
现场挂片试验数据;
一已报道的该管道材料在类似腐蚀环境下的腐蚀速率。4.2.4推荐的缺陷检测技术
石油工业标准化技术委员会CPSCSY/T6477—2000
在第5章和第6章中分别推荐了均匀腐蚀和局部金属损失缺陷的无损检测技术。4.3评价技术和判据
第5章和第6章都提供了两个级别的评价程序,图1示出了两个评价级别的逻辑关系。总体上,每个评价级别都在保守度、评价所需数据量、评价人员的技能水平、分析过程的复杂性四者之间达到了平衡。-级评价最为保守,但最容易使用。评价一般由一级评价到二级评价的顺序执行。4.3.1级评价
一级评价使用的检测数据和管道数据最少,提供了计算过程简单而评价结果偏于保守的筛选判据。获得评价所需数据
势桥程擎
按一级评价准则,
缺陷可以接受吗?
按一级评价准则,
确定MAWP,
降压使用吗?
热行三级评价
程序吗?
接二级评价准则:
缺陷可以接受吗?
降压使用吗?
进行维修或换管处理
继续使用
按二级评价准则,
确定MAWP,
图1含体积型缺陷管道剩余强度评价流程图SY/T6477-2000
4.3.2二级评价
二级评价提供了更为详尽的评价程序。与一级评价相比,二级评价结果更为准确。4.3.3剩余强度因子RSF及评价判据本标准以RSF作为含体积型腐蚀缺陷管道剩余强度的评价判据。RSF定义如下:RSF
式中:Lpc——含缺陷管道的极限载荷或塑性崩溃载荷,MPa;Luc——完整管道的极限载荷或塑性崩溃载荷,MPa。 (1)
RSF可以利用弹塑性分析、极限载荷理论和传统的计算公式计算得出。本标准在均匀腐蚀和局部金属损失缺陷评价程序中均提供了RSF的计算公式。若RSF计算值大于推荐的RSF下限值,则管道可以继续在目前压力下继续运行,否则应降级使用。降级后的最大允许工作压力计算方法如下:RSF
MAWP,=MAWP(RSF
MAWP.=MAWP
式中:MAWP一一含缺陷管道降级后的最大允许工作压力,MPa;MAWP一—管道未损伤前的最大允许工作压力(等于管道设计压力),MPa;RSF——含缺陷管道剩余强度因子计算值;RSF。——许用剩余强度因子,本标准规定取0.9。5均匀腐蚀缺陷评价
(2)
5.1概述
本章的评价程序可以用来评价含均匀腐蚀缺陷的管道,均匀腐蚀缺陷可以在管道外表面,也可以在管道内表面。对于均匀腐蚀缺陷,本章提供了点测厚法或厚度截面法两种金属损失定量方法。图2给出了均匀腐蚀缺陷评价的流程图。5.2适用性
只有满足下述条件的管道才能应用本章提供的剩余强度评价程序:a)管道材料是延性的,且在运行过程中不会因为温度或其它工艺环境发生脆化b)管道不含裂纹型缺陷;
c)用本方法评价的管段可以是直管段,也可以是弯头。5.3所需资料和数据
5.3.1管道设计、制造及施工资料需要搜集的管道设计、制造及施工资料见4.2.1。5.3.2管道运行和维修历史记录
需要搜集的管道以往运行和维修记录见4.2.2。5.3.3金属损失定量化
5.3.3.1为了评价均匀腐蚀缺陷,必须测量金属损失区域的剩余壁厚,即对金属损失定量化。获得金属损失数据有两种方法可供选择。如果最小剩余壁厚与最小要求壁厚【见附录A(标准的附录】之比大于0.7,宜用点测厚法对金属损失进行定量化;反之,宜采用厚度截面法。5.3.3.2若采用点测厚法对金属损失区域进行定量化,其测试点的数量依金属损失区域面积而定,推荐在面积为L·L[L的计算按5.4.1.1中c)】的腐蚀区域内至少选取15个厚度测试点。5.3.3.3若采用厚度截面法来对金属损失进行定量化,按以下步骤确定检测截面和危险厚度截面6
CTP:
求平均厚度吗?
金属损失可以接受
简单评价
t运用第4
章提供的级和
级评价判据
SY/T6477—2000
计算最小要求壁厚tain
找出金属损失区域
采用厚度截面法吗?
确定检测截面
沿检测裁面测量和记录剩余壁厚基于检测数据建立轴向和环向
危险裁面CTP
确定s,C,tL和t
利用厚度截面吗?
S≤L吗?
选择评价方法
厚度法
确定t运用第
4章提供的一级和
级评价判据
采用直接测厚法:增加
NDE以证实金属损失为
均匀腐蚀缺陷
由金属损失区域壁厚
测试结果确定t_和L
局部金属
损失评价
作为局部金属损
失,按第5章提
供的方法评价
图2均匀腐蚀缺陷评价流程图
a)第1步:找出金属损失区域,确定检测截面的方向和长度。如果内压产生的环向应力起主导作用,检测截面定为轴向;如果内压和附加载荷产生的轴向应力起主导作用,检测截面定为环向(如图3所示)。注意检测截面的长度应足以表征金属损失区域。b)第2步:沿每一个检测截面间隔测量剩余壁厚,并确定每个检测截面的最小测量壁厚tmm。7
石油工业标准化技术委员会CPSOSY/T6477—2000
金属损失区
(a)直管段
外缘线-
金属损失区
内缘线
(b)弯头
图3金属损失区域的检测截面示意图测量过程中测量点间距应根据缺陷的具体情况随时调整,以保证获得准确的剩余厚度截面。式(4)给出了推荐的检测截面间距,每个检测截面至少测量5个点的厚度。表1给出了检测数据的记录格式。
Ls=max[0.18/D;tmin,12.7mm]
式中:Ls—推荐的检测截面间距,mm;8
石油工业标准化技术委员会CPSOSY/T 6477-2000
管子内径,mm;
未来腐蚀裕量:
管子外径:
名义壁厚:
最小要求壁厚:
-基于管道设计压力计算的管道最小要求壁厚【见附录A(标准的附录)],mm。表1均匀腐蚀缺陷检测数据记录格式缺陷尺寸(s和c):
每个检测截面的厚度测试结果以下列格式记录:检测截面编号:
检测截面编号:
检测截面编号:
检测截面编号:
c)第3步:建立危险厚度截面CTP。将所有的平行检测截面上每个测量位置最小厚度向同一平面投影得到CTP(如图4所示)。1)将C~Cs各检测截面的最小厚度向同一个平行于轴向的平面投影,得到轴向CTP。轴向金属损失长度s用CTP和tmin来确定(如图4所示)。2)将M,~Ms检测截面的最小厚度向同一个平行于环向的平面投影,得到环向CTP。环向金属损失长度用CTP和t来确定(如图4所示)。3)如果金属损失面积比较大,仅采用个危险截面来评价往往导致评价结果过份保守,宜采用几个轴向或环向CTP来评价金属损失:CTP的个数可以通过限定建立每个CTP的检测截面数量最多不超过5个来确定。9
小提示:此标准内容仅展示完整标准里的部分截取内容,若需要完整标准请到上方自行免费下载完整标准文档。

标准图片预览:
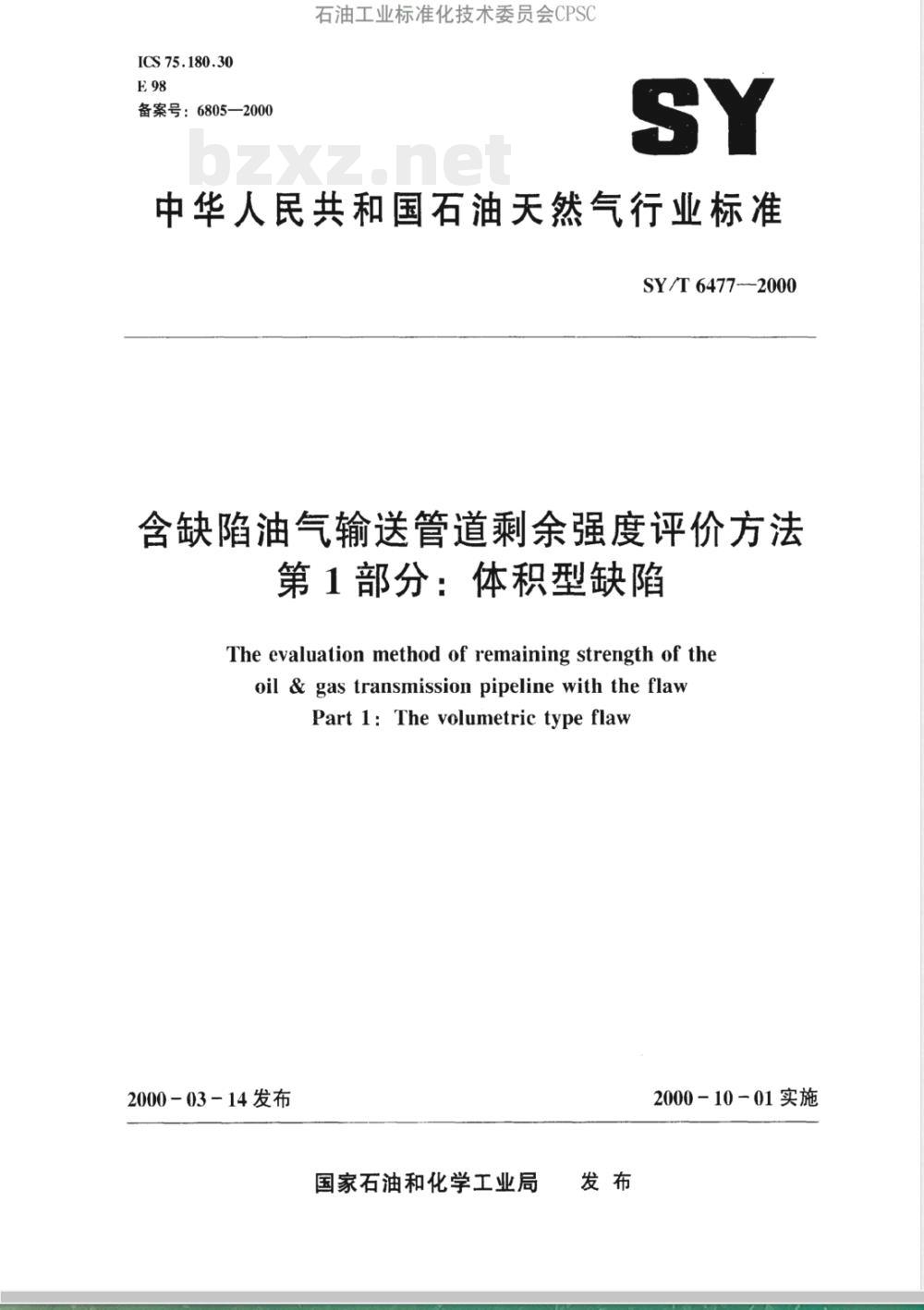
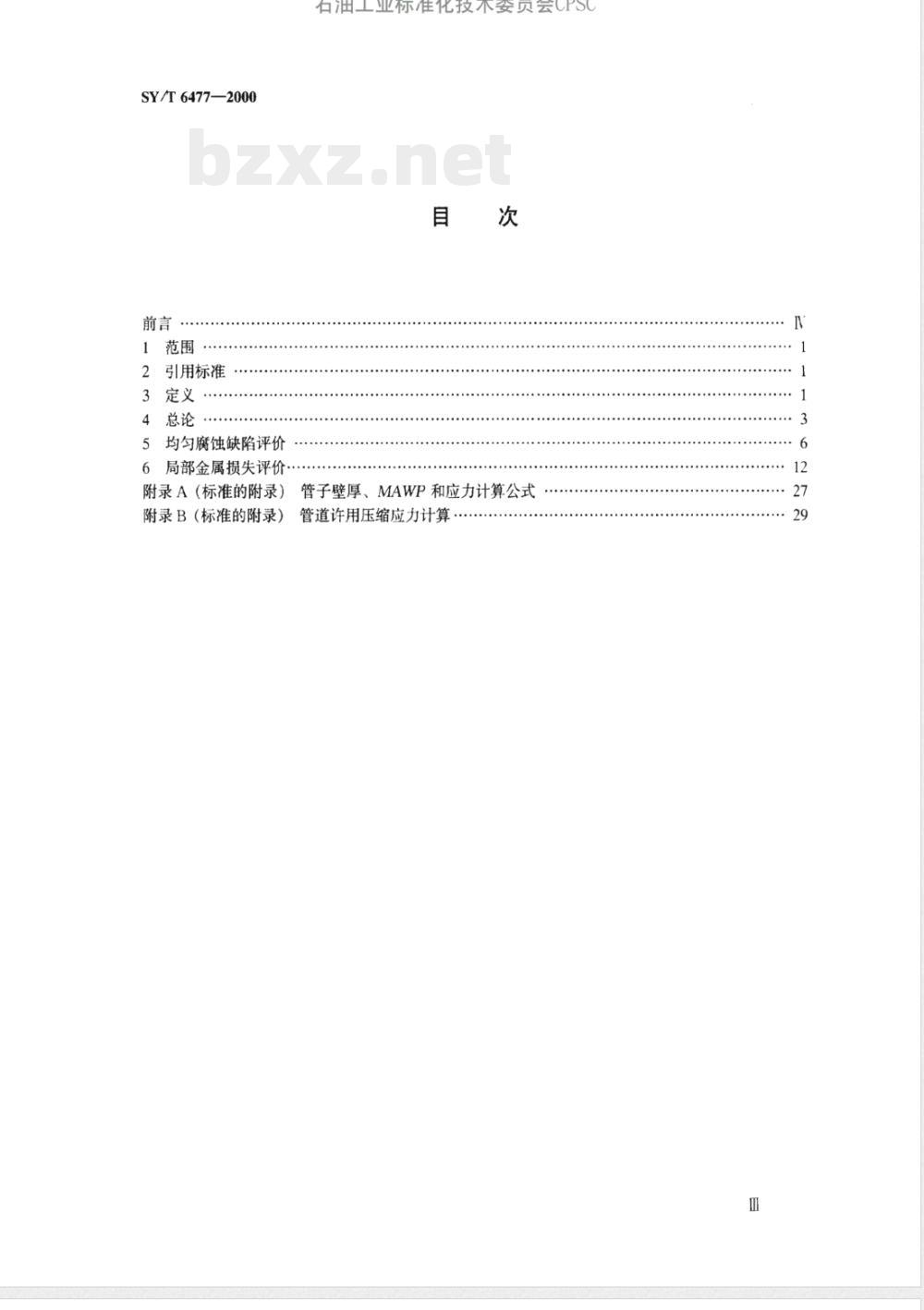
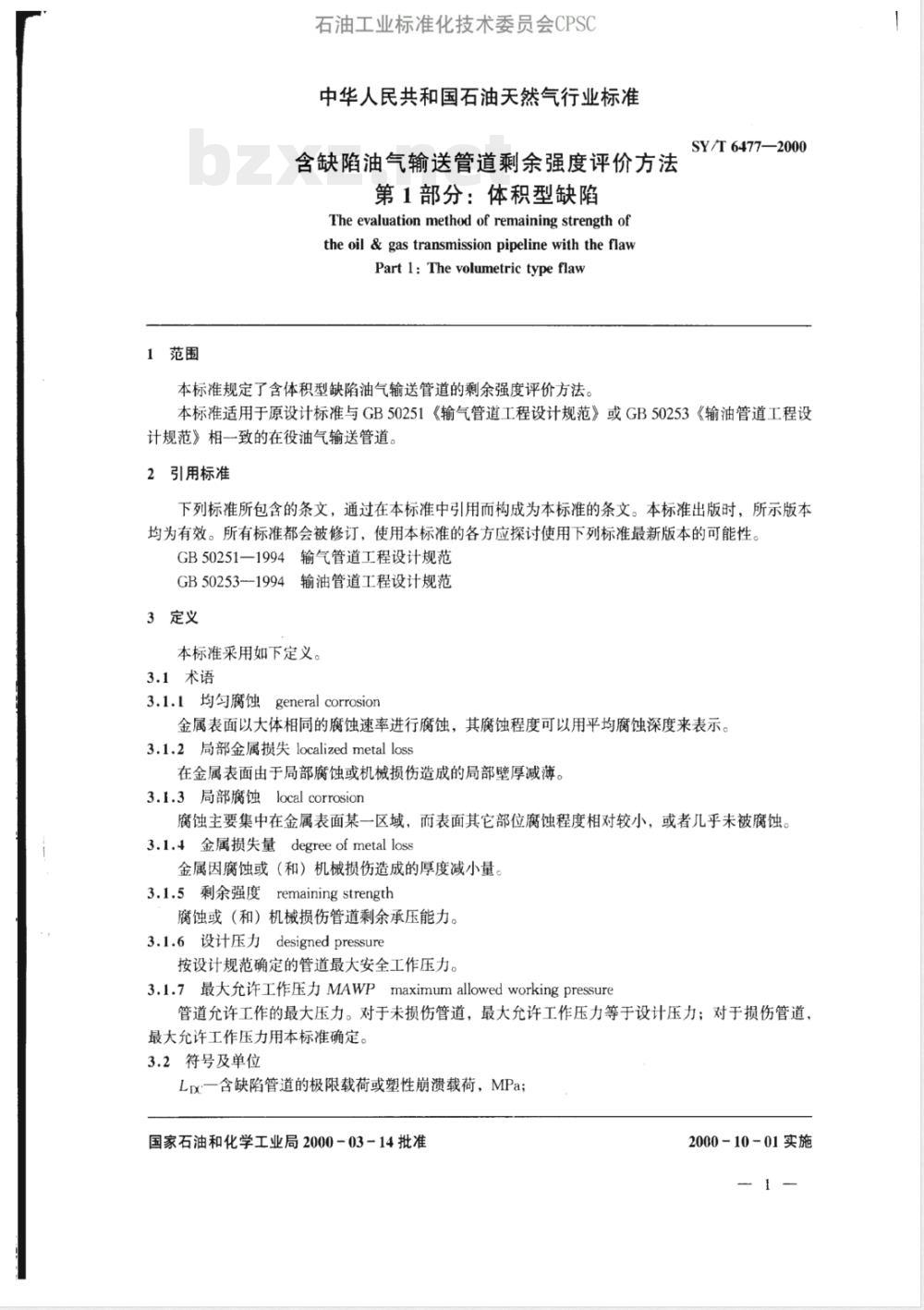
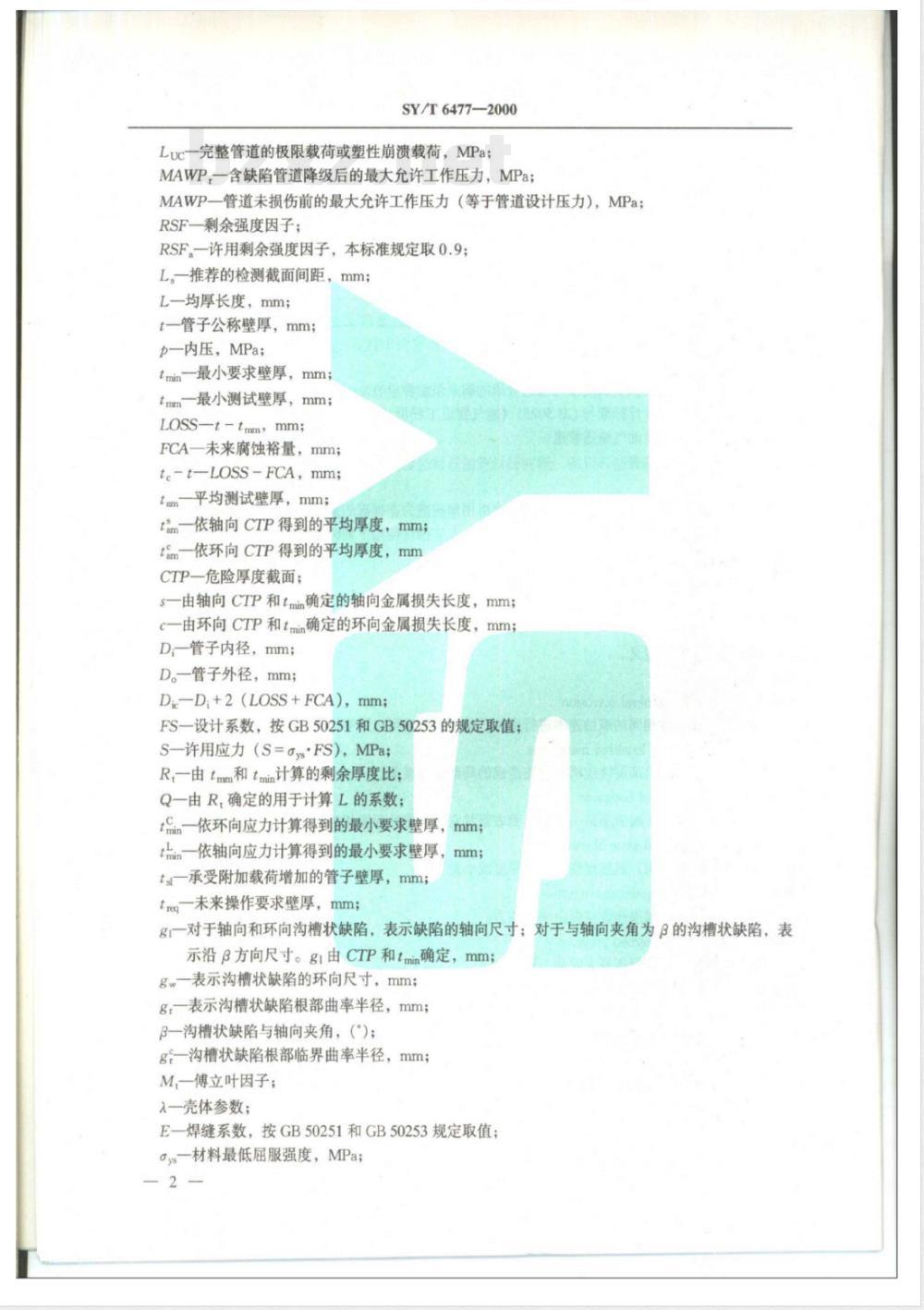
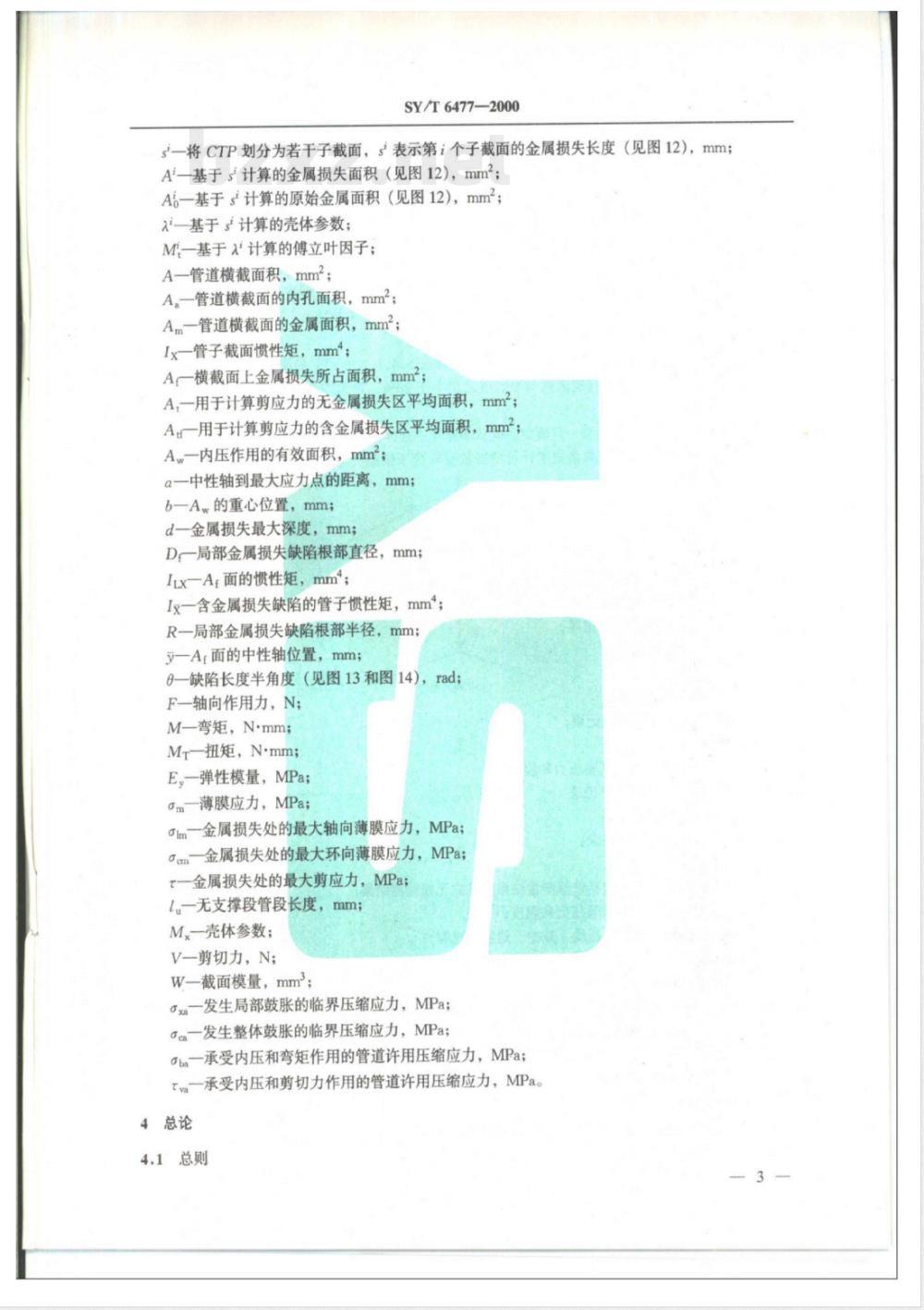
- 其它标准
- 热门标准
- 石油天然气行业标准(SY)
- SY4025-1993 石油建设工程质量检验评定标准 建筑工程
- SY/T0612-2008 高含硫化氢气田地面集输系统设计规范
- SY/T5778-2008 岩石热解录井规范
- SY/T5262-2009 火简式加热炉规范
- SY/T5619-2009 定向井下部钻具组合设计方法
- SY/T6578-2009 输油管道减阻剂减阻效果室内测试方法
- SY/T10006-2000 海上井口地面安全阀和水下安全阀规范
- SY/T0005-1999 油田注水设计规范
- SY0470-2000 石油天然气管道跨越工程施工及验收规范
- SY/T0535-1994 火筒式加热炉热力与阻力计算方法
- SY1523-1982 特75号精密仪表脂
- SY/T5712-1995 压控式测试器性能检验
- SY/T5768-2006 一般结构用焊接钢管
- SY/T6031-2006 井温、井径、井斜测井仪刻度
- SY/T6161-2009 天然气测井资料处理及解释规范
- 行业新闻
请牢记:“bzxz.net”即是“标准下载”四个汉字汉语拼音首字母与国际顶级域名“.net”的组合。 ©2009 标准下载网 www.bzxz.net 本站邮件:bzxznet@163.com
网站备案号:湘ICP备2023016450号-1
网站备案号:湘ICP备2023016450号-1