- 您的位置:
- 标准下载网 >>
- 标准分类 >>
- 船舶行业标准(CB) >>
- CB/Z 133-74 船体零件加工技术要求
标准号:
CB/Z 133-74
标准名称:
船体零件加工技术要求
标准类别:
船舶行业标准(CB)
标准状态:
现行出版语种:
简体中文下载格式:
.zip .pdf下载大小:
327.88 KB

点击下载
标准简介:
CB/Z 133-74.
CB/Z 133适用于碳素钢和902钢焊接零件的制造。
一矫正
1.在划线前,对于有明显变形的钢板,应进行矫正,矫正时的环境温度不低于- 25°C。
2.矫正后,钢板的表面波纹度不得超过表1数值:
8.型钢经初步矫正后,在每米长度上直线性偏差不应超过2 m m,而在整个长度上不应大于
8mm。
二、划线
4.划线前,应清除钢板表面铁锈、圬垢和检查表面有无缺陷,边缘有无裂纹,夹灰等,并核对钢、
板的牌号、规格是否符合图纸要求。
5.划线时,钢板零件之间,留有最小切割的宽度:
8<25mm-切割宽度为8 m
m;δ≥25mm一切割宽度为4m m。
6,零件划线离钢板边缘的最小距离:
(1)在机械切割时一δ≥10mm时,最小距离<0.58; 8<10mm时,最小距离>5mm,
(2)在气割时一> 5mm。
如果经过机械切割或气割之后,边缘要刨削时,则应留有刨削余量。
7。零件划线时,线的宽度为0.5~ 1mm。
8.热弯曲的零件应留有加工和机械性能试验的取样余量。
9.零件划线后,应对轮廓线,构件的连接线,理论线,错开线、折角线、余量线、开口线,对接缝线,助骨位置线,孔中心线和检查线等加铳点标志。
对铳点要求如下:

部分标准内容:
船体零件加工技术要求
本技术要求适用于碾素钢902钢焊接零件的制造。矫正
CB/ Z 133--74
I,在划綫前,对于行明显变的钢枢,南齿行矫正,矫止时的环境温度不假于-25\C。2,矫正后,钢板的表面被绞度灭得超过表1数慎:mm
被厚度
每采长度上波纹度不大于
8,型钢经初步矫正后,在每来长度上直线性宿差不应超过2且扭,而在整个长度[不应人于8mm
二,划线
4,划线前,虚除前版表面铁锈,均和检查表面有芳龄路,边絲有无裂纹,夹灰等,所核对钢板的牌号、规格是否符合图纸要求。5。姚线时,树版零件之间,留有最小切割的鼠度;8<25m—切割宽度为8m㎡
8>25mm-—切制宽度为4mm。
B,零件剑毁离钢板边缘的最小距离;(1)在机切时8≥10mm,最小距离0,58,g10mm时,最小距离>5m血(2)在气割过一
如果经过机械切剖或气割之后,边缘要创削时,则应留有刨削余量。了,零件划线时,线的宽度为0,5~1。8,热弯曲的需件应留有加工和机性能试验的取样余量。9,零件刘线后,应对轮廓线,构的连接线,理论线,错开线、折角线,余益线、开几线,对接缝线,助骨位置线,孔中心线和检查线等加饶点标志。对镜点要求则下:
第六机被工业部发市
1974年5月1日卖施
共4更第2页
CB/z1S-7
(1)轮率线,切口线镜点闻距为20~50m扭(2)折角线,每纽8个统点:敲在折角端点。毓点应打在考曲的内表面,(8)铆钉、螺栓等孔中心线及沿圆周打上点。10,划过线的全部钢板,要犯产品代号、图号、零件号、在船上按装区城或在使用总段建造时的总段号,应用点标志在钢板另件右上角,并用油漆划成方,用文字或符号说明正轧或反乳方向。对于助骨号、焊接坡口、刨斜边、余盘大小的说明、首尾上下位置等全部说明、在装配时箫要某种开口,可用油漆标志山来,同一批用不同颜色区别。11。没有余量的零件划綫启,其尺寸偏差规定如下:(1)对直线度编差<1 m㎡
(2)山线外形偏差±1.0mm!
(8)境度尺寸偏1m㎡
(4)对角线尺寸偏差±1,5m益)(与)长度8m以内偏差<1mm
(6)长度8m以上偏差<2m
(7)防材文骨、人孔、手孔、开口等位移的偏差士1.0mm。12。没有余量的型钢零件应符合型值表(放样问数据)或图纸尺寸、长度偏差规定如下:(1)长度9以内的偏差<1m1
(2)长度8以上偏<2。
13。弯带型钢按样板划线,如没有样和缺少数据进行初步划线时,应按巾和轨计算型钢长度。弯曲形状复杂的型纫零件,划线时要留有余量。14,弯山形状特别复杂的钢板零件划线,成留有30~50起m余虽,冷旁或热弯后,再根据样板作最后划线。
15。已划线的季件。应按图纸、草图或样板进行检查,并做好耐压壳被(包括耐压液舱)的材质登记。
三、下料
16,季件在剪冲谋下料时,刀间劑规定茹下!钢板厚度1.5~4㎡m时,间间为0.125也益!钢板厚度5~12mm时,刀间间隙为0.4mm。17。在剪冲床上切割后不需刨和的钢板容件其直边对鏡点的偏差<± 1m组,见图1。图
18.在剃床上切舒的型缺零件,对统点沿长度的偏差<±1,5m。HTYKAONiKAca-
CB/ZISTT4
共4贡第8
19。钢板在刨之前,用卧定在机床刀架,上划线盘捡查钢板安放在机床上的准确性,将钢板直线边缘刨成直角时,充许偏翌<±0,5扭现(即不超过举个点)并川样板进行检查,见图212
20。将钢板刨成焊接坡,或刨成斜边时的偏差应符合图纸要求,可用纯角样板检查见图3:21,钻头中心对被加工等件表再应保证垂直,钻孔与划线偏差<1.0㎡m。22.夹层板钻孔时,应压紧,二被间除<2m血,下板孔眼对上孔限的位移应<1.0mm。23。型材等件的钻孔要在桁架内或垫板上固定进行。24,销孔验收,应检查孔道轻,孔中心线与划线偏差、孔的垂直度。25,钢板气割前,表面要清除汀泥,铁锈、夹道、漆等。气割后的零件不应有夹层,气泡、砂眼,严重压力氧化铁皮和裂等缺陷。26。为碱少零外在切割时的变形,在工作中应尽虽采用下列规则:(1)在钢板上切下大零片时,应先从短边开始切割。(2)在钢板上切割一系列不同只寸的零件时,庞先切割加工精度娶求较高的零件,先切割小料,后切割大料。
(8)在钢板上切割复杂形状零件时,首先切割较复杂的外形,前且从边上开始。27,按钢扳享度和设备性能选取不同切制规范,参者的数据见表2。裴
代制咀号
氧气力乙
炔压力
正 G/ em2
k G/ cm2
不小于0.5
切割速度
(m/分钟)
400~500
300--400
250~300
28。按镜点切割时,应将点留有--半,并应保持加工边缘和检查线的距离。29,为减少预热焙的发热量损失,从气咀到被切割的钢板表面距离,豌是焰心的长度加1~2,5mm.
30。气翻用的氧气纯度应不低于99.4%。31.零件落料应连续进行,如果临时停额,应在钢扳的不利用处,并且是以后要接着韧割的开始点,
共4页 第4页
CB/Z187--74
32。零件下料后应再次矫正,矫正后钢板应符合下列规定:8=8~8mm,波纹度<3mm
829mm,波纹度<2.0mm。
33,弯业的环境温度不得低于一20℃°34。需要开口祈弯的零件,在开口角顶处,应钻孔或气制吹圆。35。钢校弯山半径R<108附,应在弯部份端缘8R~4R处加工成圆角,<10m时,r=2mm1
8≥10mm,f= 4mm。
见图?
36。弯曲比较简单的零件,在弯法过翟中,成型后月样板检查,包可直接月肩钢弯成样板检查。37。湾曲圆柱泥钢极用一个祥板,在零件岩下截面土检查,弯出夙锥形板,最少乃二个样板,在零件截面的二端检查。
38。弯曲后的圆柱和圆锥形零件偏差规定如下:10
8210mm
样被与零件的高部问隙<\4m
样披与零件的部间琐<。
,弯曲双函形状的零件时,应在每挡助肾位置进行检查,检意偏差1~2mn并检查当:8<10mm
8≥10mm
-样板与零件的局部随<1
祥板与等件的高部问隙<'么血血。弯曲后的钢扳零件,叫周边缘线型应利顺。40。弯曲形决复杂的零件时,用箱子样板捡查翁了上的对角线在交双处的问距8扭:并检查当容<10mm
样被与零作的局部间隙<5
8 210mm-
样板与零件的局部间膜<4 m。Www.bzxZ.net
弯出后的钢板零件,四周边缘线型应和厕。41,有折角或招边的零件,用样板成分度规进行检查,板边端部与样板开尺的间隧<土2血m在整个长度上检查数量不少于8处。弯曲成型后,在每米长度上局部不平度不应超过3mm,在全长上对样板或直线的偏差不应超过长度的0.001。42.碳素钢和8≤3Umm的;902钢的不重要零件,弯半径不受限制。HTYKADNIKAca-
小提示:此标准内容仅展示完整标准里的部分截取内容,若需要完整标准请到上方自行免费下载完整标准文档。

标准图片预览:
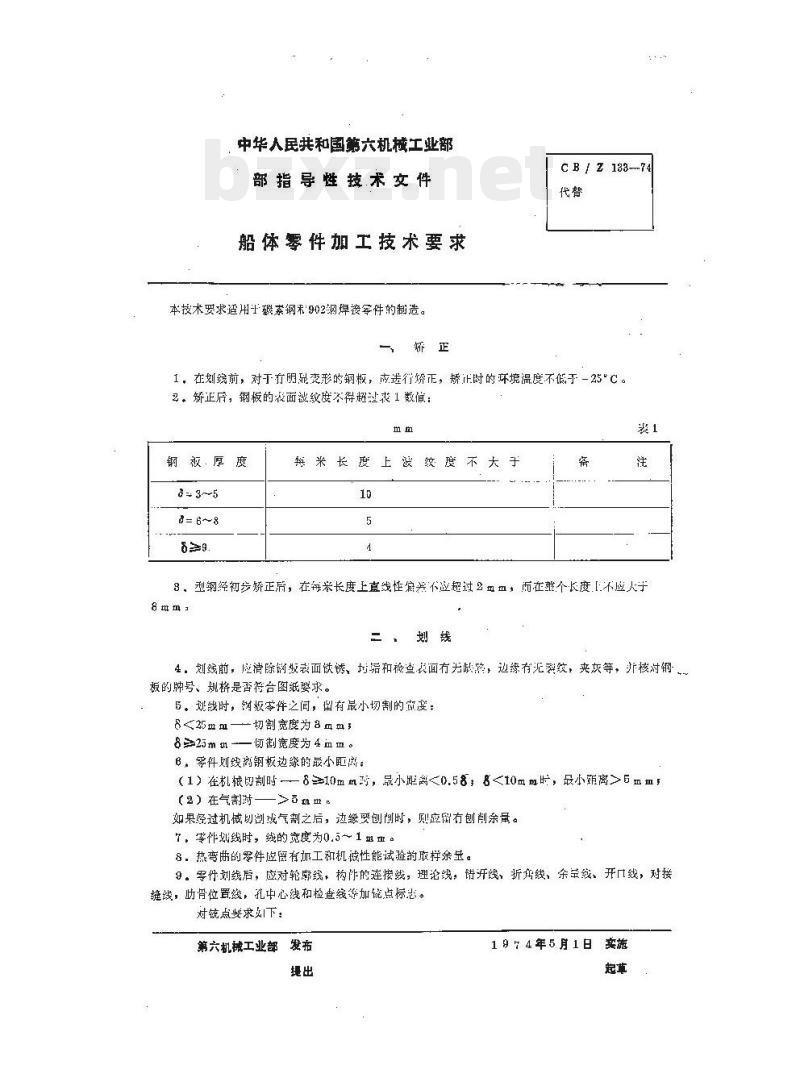
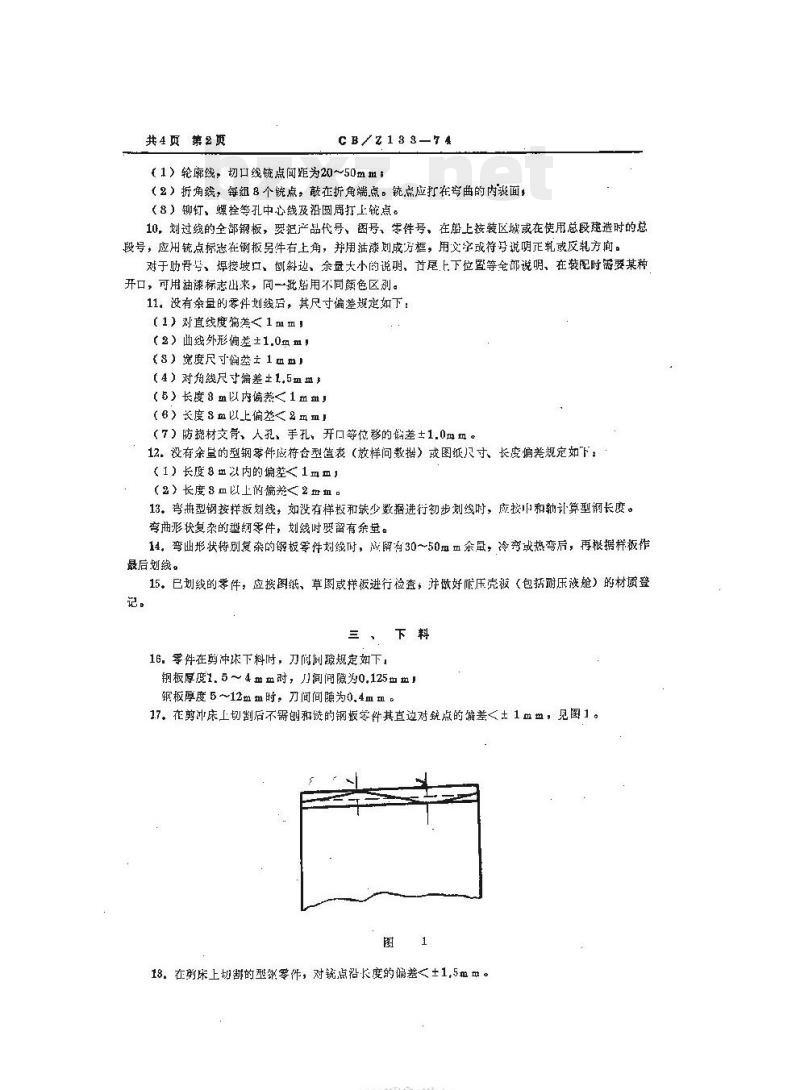
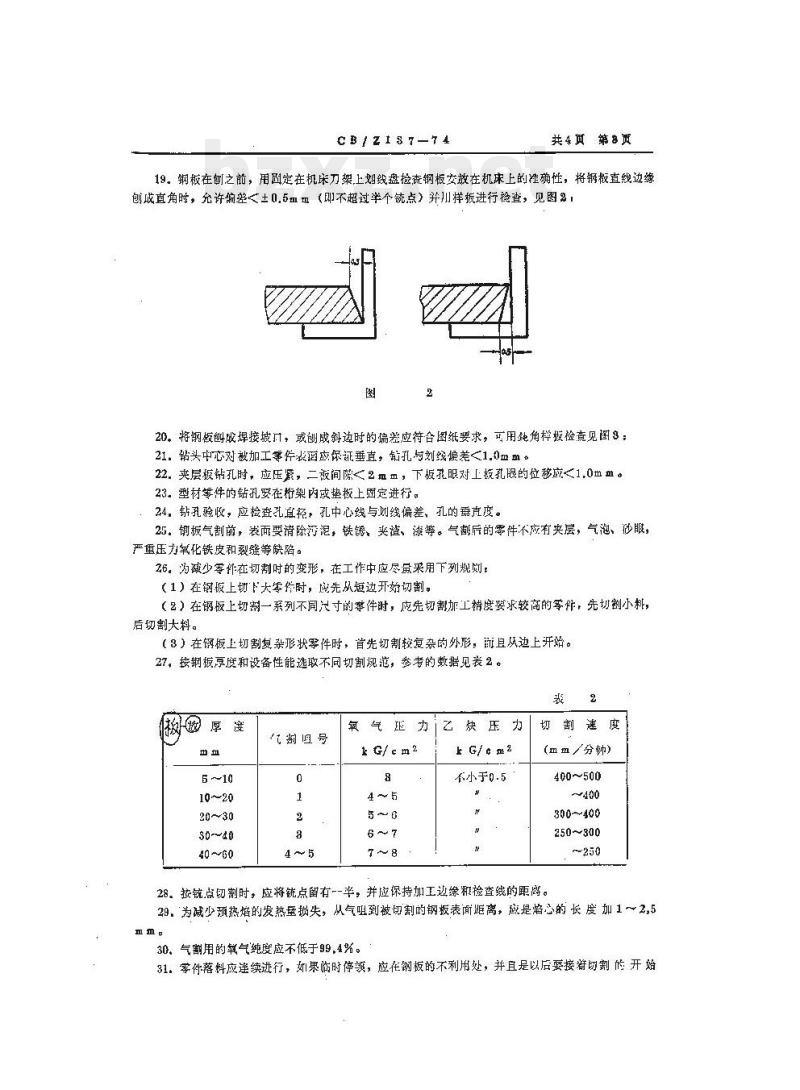
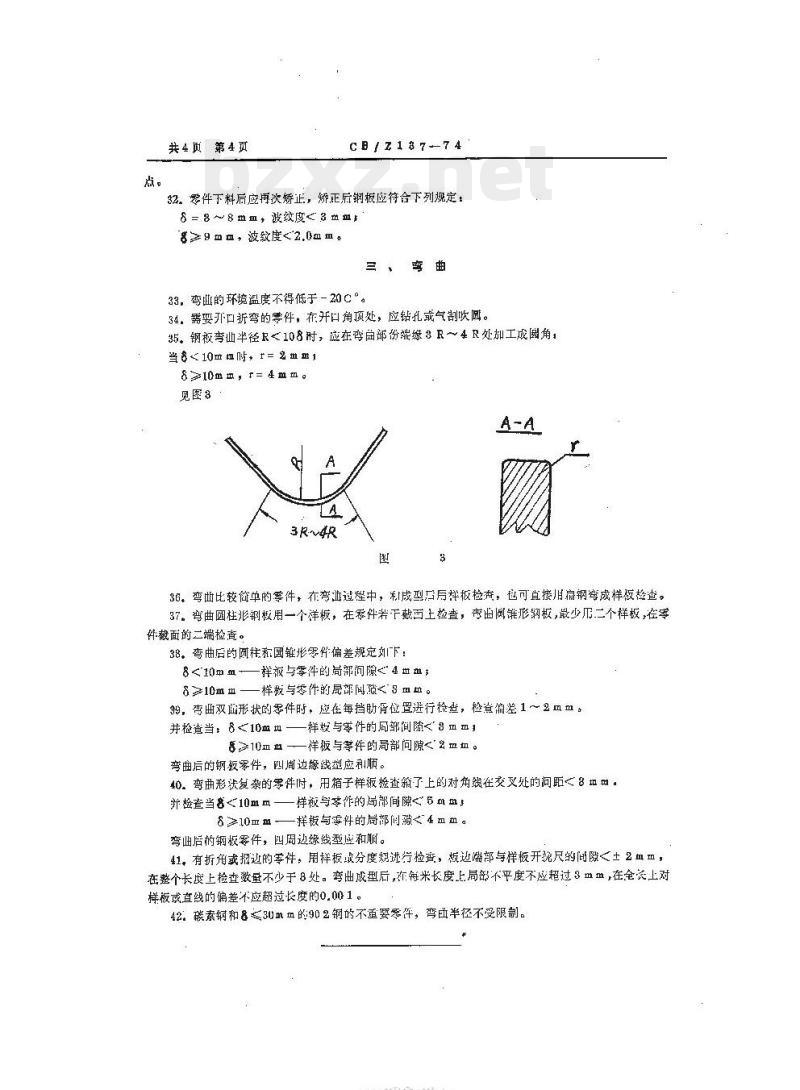
- 其它标准
- 热门标准
- CB船舶标准
- CB/T3543-94 船用柴油机活塞修理技术要求
- CB776-2004 升降式带缆桩规范
- CB/T4032-2005 J类法兰青铜消防栓
- CB1092-88 船舶家具、附件修理工时定额
- CB/T352-93 保护式隔振器
- CB/T3799-1997 船舶液压系统修理清洗技术要求
- CB/T3528-93 海洋平台变压器
- CB/T3476-92 立式防浪阀
- CB/Z243-88 木作修理技术要求
- CB/Z245-1988 单桨潜艇伴流与推力减额分数的估算
- CB/T3570-93 船用气动马达技术条件
- CB1307-98 鱼雷末弹道测量设备规范
- CB1060.8-87 钢质船体制造工时定额批凿碳刨
- CB1060.7-87 钢质船体制造工时定额电焊
- CB*3348-1988 船用锅壳式辅锅炉本体总装技术条件
- 行业新闻
网站备案号:湘ICP备2023016450号-1