- 您的位置:
- 标准下载网 >>
- 标准分类 >>
- 国家标准(GB) >>
- GB/T 41478-2022生产过程质量控制 系统模型与架构 装配与铸造
标准号:
GB/T 41478-2022
标准名称:
生产过程质量控制 系统模型与架构 装配与铸造
标准类别:
国家标准(GB)
英文名称:
Quality control of production process—System model and architecture—Assembly and casting标准状态:
现行-
发布日期:
2022-04-15 -
实施日期:
2022-11-01 出版语种:
简体中文下载格式:
.pdf .zip下载大小:
7.08 MB
标准ICS号:
机械制造>>工业自动化系统>>25.040.40工业过程的测量与控制中标分类号:
仪器、仪表>>工业自动化仪表与控制装置>>N19其他自动化装置
起草人:
陈玉平、马玉山、王成城、游和平、俞文光、李沨、张凤丽、王凯、宋佳娜、马俊峰、郭伟、彭正红、黄亮、唐霞、王春喜、张镇、刘建胜、王德吉、刘阳、田英明、贾华、张海潮起草单位:
无锡职业技术学院、吴忠仪表有限责任公司、机械工业仪器仪表综合技术经济研究所、东风设计研究院有限公司、浙江中控技术股份有限公司、武汉船用机械有限责任公司、中国石油大学(北京)、中国科学院沈阳自动化研究所、山东省计算中心(国家超级计算济南中心)、南昌大学等归口单位:
全国工业过程测量控制和自动化标准化技术委员会(SAC/TC 124)提出单位:
中国机械工业联合会发布部门:
国家市场监督管理总局 国家标准化管理委员会相关标签:
生产 过程 质量 控制 系统 模型 架构 装配 铸造

点击下载
标准简介:
本标准规定了装配与铸造数字化车间生产过程质量控制的系统模型与架构、装配过程质量控制、铸造过程质量控制等。
本标准适用于装配与铸造数字化车间生产过程质量控制,可用于提高装配与铸造生产过程质量控制能力。

部分标准内容:
ICS25.040.40
CCSN19
中华人民共和国国家标准
GB/T41478—2022
生产过程质量控制
系统模型与架构
装配与铸造
Quality control of productionprocess-System model and architecture-Assembly and casting
2022-04-15发布
国家市场监督管理总局
国家标准化管理委员会
2022-11-01实施
GB/T41478-—2022
规范性引用文件
3术语和定义
缩略语
系统模型与架构
5.1系统结构组成
系统功能及要求
系统模型技术要求
质量分析与评价
质量追溯与改进
装配质量控制
通用要求
事前控制技术要求
事中控制技术要求
事后控制技术要求
7铸造质量控制·
通用要求·
事前控制技术要求
事中控制技术要求
事后控制技术要求
参考文献
GB/T41478—2022
本文件按照GB/T1.1一2020《标准化工作导则第1部分:标准化文件的结构和起草规则》的规定起草。
请注意本文件的某些内容可能涉及专利。本文件的发布机构不承担识别专利的责任。本文件由中国机械工业联合会提出。本文件由全国工业过程测量控制和自动化标准化技术委员会(SAC/TC124)归口。本文件起草单位:无锡职业技术学院、吴忠仪表有限责任公司、机械工业仪器仪表综合技术经济研究所、东风设计研究院有限公司、浙江中控技术股份有限公司、武汉船用机械有限责任公司、中国石油大学(北京)、中国科学院沈阳自动化研究所、山东省计算中心(国家超级计算济南中心)、南昌大学、中国烟草总公司职工进修学院、中信戴卡股份有限公司、绵阳市维博电子有限责任公司、重庆川仪自动化股份有限公司、无锡市贝尔机械股份有限公司。本文件主要起草人:陈玉平、马玉山、王成城、游和平、俞文光、李讽、张凤丽、王凯、宋佳娜、马俊峰、郭伟、彭正红、黄亮、唐霞、王春喜、张镇、刘建胜、王德吉、刘阳、田英明、贾华、张海潮。I
1范围
生产过程质量控制系统模型与架构装配与铸造
GB/T41478—2022
本文件规定了装配与造数字化车间生产过程质量控制的系统模型与架构、装配过程质量控制、铸造过程质量控制等。
本文件适用于装配与铸造数字化车间生产过程质量控制,可用于提高装配与铸造生产过程质量控制能力。
2规范性引用文件
本文件没有规范性引用文件。
3术语和定义
下列术语和定义适用于本文件。3.1
生产过程
productionprocess
将原材料转变为成品的全过程。[来源:GB/T4863—2008,3.1.9]3.2
manufacturing
将材料从原材料或半成品状态转换成进一步完成状态的功能或活动。[来源:GB/T19114.44-2012,3.1.7]3.3
系统system
由一个或多个过程、硬件、软件、设施和人员组成的集合体,具有满足某个已明确的要求或目标的能力。
[来源:GB/T26224-2010,3.26]3.4
以任何方式(包括数学、物理、符号、图形或描述等方式)对现实事务某一方面进行的抽象描述。[来源:GB/T25485—2010,3.32]3.5
装配assembly
将零件或部件进行配合和连接,使之成为半成品或成品的工艺过程。[来源:GB/T51218—2017,12.1.1]3.6
虚拟装配
virtualassembly
对装配建模所形成的装配模型进行装配分析与模拟的过程。包括一次或多次的装配顺序规划、装1
GB/T41478—2022
配路径规划以及装配过程仿真等,可用于装配干涉检查和装配工艺优化等目的。来源:GB/T261012010,3.17
铸造casting
熔炼金属,制造铸型,并将熔融金属浇人铸型,凝固后获得具有一定形状、尺寸和性能的金属铸件的成型方法。
[来源:GB/T51218—2017,3.1.1]3.8
工艺technology
使各种原材料、半成品成为产品的方法和过程。[来源:GB/T51218—2017,2.1.38]3.9
质量管理qualitymanagement
制造执行层的制造设施协调、指导、管理和跟踪质量测量和汇报功能的活动。[来源:GB/T25485—2010,3.45]3.10
追溯tracing
提供资源和产品使用的组织记录的活动,利用跟踪信息从任何结点,向前或向后。[来源:GB/T25485—2010,3.50]3.11
质量控制qualitycontrol
致力于满足质量要求的措施与活动。[来源:GB/T51218—2017.2.5.73.12
数据data
适合于由人或计算机进行通信、解释、或处理的形式化方法的信息表示。[来源GB/T16656.1—20083.2.16]3.13
验证verification
提供客观证据,证明给定项目满足规定要求。[来源:GB/T27025—2019,3.8]3.14
traceability
可追溯性
追溯客体的历史、应用情况或所处位置的能力。[来源GB/T36061—2018,3.1]4
缩略语
下列缩略语适用于本文件。
APS:高级计划与排程(AdvancedPlanningandScheduling)BOM:物料清单(BillofMaterial)CAPP:计算机辅助工艺过程设计(ComputerAidedProcessPlanning)CRM:客户关系管理(CustomerRelationshipManagement)2bzxz.net
ERP:企业资源计划(EnterpriseResourcePlanning)FCS:铸造炉料系统(FoundryChargeSystem)HMI:人机界面(HumanMachineInterface)MES:制造执行系统(ManufacturingExecutionSystem)OA:办公自动化(OfficeAutomation)PDM:产品数据管理(ProductDataManagement)PLC,可编程逻辑控制器(ProgrammableLogicController)SCM:供应链管理(SupplyChainManagement)VR:虚拟现实技术(VirtualReality)系统模型与架构
5.1系统结构组成
GB/T41478—2022
生产过程是指从产品投产前生产技术组织工作开始,直到把合格产品生产出来的全部过程。生产过程始于用户需求,终于生产出合格产品之间的过程,包括根据用户需求下达生产任务、制定生产计划、提出生产资源保障、装配与铸造生产等环节。质量控制是为使产品或服务达到质量要求而采取的技术措施和管理措施方面的活动。质量控制的目标在于确保产品质量满足用户要求生产过程质量控制系统各环节架构关系如下:一根据用户需求制定质量目标数据,质量监控系统利用质量目标数据对生产资源保障的各个环节进行质量控制;
基于产品采集的质量数据与质量目标数据进行比对,对比对结果进行分析与评价,对质量缺陷进行追溯,对影响质量的环节进行改进。生产过程质量控制系统各环节之间关系架构描述如图1所示。装配/铸造数字化车间生产过程质量控制系统是基于现有的数字化车间的建设成果,应用新一代信息技术,提升企业的生产过程质量控制水平。装配/铸造产品是将物料在特定的条件下,通过人员、设备,按照一定的工艺方法经过特定的工序生产手段得到的过程输出。
装配/铸造生产过程质量控制系统是生产过程质量控制中针对装配/铸造环节的信息管理系统。装配/铸造生产过程质量控制系统模型是对装配/铸造过程质量控制的信息集成。3
GB/T41478—2022
用户需求
生产任务
生产计划
生产资源保障
装配/铸造
生产组织
5.2系统功能及要求
生产过程
人力资源
生产设备
生产物料
生产工艺
生产环境
质量数据采集
作业培训
检验与校核
检验与确认
仿真与优化
监测与保证
质量控制
质量追潮与改进
质量分析与评价
质量数据比对
图1装配/铸造系统模型与架构图系统应具备的功能包括以下内容。质量目标数据
质量监控
支持各个数字化工位/智能终端快速获取物料质量数据、工序数据、设备状态数据等,具有工序执行视频监视、基于消息机制的呼叫联络、车间看板数据显示等网络化质量控制信息能力;可按工位/人员标识发送管理信息和收取反馈信息。支持实施生产过程质量数据采集,可辅助人工检查及在线自动测量,以最小的滞后时间获取工艺结果检测数据,使多个并行工位的质量数据及时入库,为生产过程质量数据分析和控制决策提高数字化、网络化环境,从而强化生产过程质量控制的效果。系统应与数字化车间的制造执行、企业数字化设计制造一体化等生产过程质量相关信息系统实现集成应用,且能够客观展示系统必备的软件功能;系统及各个应用软件、各用户端具有统一的时钟控制;系统应具有环境适宜性、数据精确性、网络互操作性和信息安全性。系统应满足的要求:
生产过程中影响产品质量特性的因素主要包括六个方面,即人力、机器、材料、方法、环境和测量,由于这些质量因素的变化,使得产品质量特性之间存在着差异,应将上述六要素加入质量控制范畴;
装配/铸造生产过程质量控制是从工艺执行与管理、装配/铸造工序制造执行与管理,以及贯穿始终的生产过程质量控制,最终输出产品的过程;装配/铸造生产过程质量控制系统是从工序质量数据采集,作用于质量监控,再到质量检测与判定,质量检测与判定的结果可作用于质量分析与评价,对于质量异常的数据,立刻停止加工转人质量追溯,对于质量正常的数据转人质量分析与评价:质量监控和质量检测与判定的结果可用于质量追溯与改进,质量追溯应作用于生产资源保障和装配/铸造生产组织过程质量控制输入环节。5.3系统模型技术要求
5.3.1通用要求
GB/T41478—2022
系统是对金属原材料或零部件转变成产品的过程质量监控,贯穿生产过程始终,是一个具有用户需求输人和产品输出的系统。
系统应遵循以下原则,可靠性、安全性、可扩展性。系统对影响生产过程的人员、设备、工装、材料、方法和环境等因素进行控制,确保其处于受控状态。系统将装配/铸造生产过程所有的质量信息纳人质量控制系统,确保信息传递完整、有效,信息记录清晰、准确,信息输出准确、完整,并用于质量改进和追溯。5.3.2质量数据采集
质量数据采集对象包括产品的信息(名称、件号、材料牌号、产品状态、条码、生产数量等)、质量检测结果(设备检测结果、人工检测结果等)。系统应提供质量数据的全面采集,对质量控制过程的关键停检点应在指导性工艺文件中标明,并有系统控制停检,关键质量数据应能够实现在线自动测量,以保证产品质量档案的准确与完整。系统应满足数据监控所需的网络通信,提供多种工序质量数据的采集方法,支持各种异构数据源的数据集成,支持各类质量数据的集中存储与初步处理。5.3.3质量监控
5.3.3.1通则
根据产品标准要求,对生产过程中的产品特性进行监控。质量监控应通过质量控制系统记录生产过程质量数据,以满足为产品生产过程符合性以及质量管理体系运行有效性提供证据的要求。质量记录类型(包括电子表格)一般包括:检验报告、试验数据、鉴定报告、确认报告、考察和审核报告、不合格品审理报告、校准报告、纠正措施和改进报告等。质量控制系统应确认质量记录的标识、贮存、保护、检索、保存期限和处置的控制情况,确认质量记录有效、完整、准确、连续、易于识别和检索。定期随机抽查质量记录,验证质量记录与产品实物的符合性。装配/铸造生产过程质量监控主要包括对生产资源保障、装配/铸造生产组织两大环节进行质量监控,其中生产资源保障监控包括对人力资源、生产设备、生产物料、生产工艺、生产环境等生产要素进行质量控制,确认其符合相关规定。5.3.3.2人力资源质量控制
人力资源质量控制应满足以下内容。生产人员及其要求,配备足够数量的生产工人和辅助人员,以满足产品的生产过程及各工种工序的要求。生产人员应经过专业培训,持证上岗。检验员及其要求,检验员数量以能完成检验工作任务,并能有力配合生产检验为宜。检验人员应经过专业培训,持证上岗。
技术和管理人员要求,人员数量应保证能够有效地管理生产现场,保证整个生产过程有效进行为宜。技术和管理人员工作能力应能够及时高效地解决分管领域内发生的各种问题,确保自已的工作不影响生产。
生产设备质量控制
生产设备质量控制应满足以下内容。5
GB/T41478—2022
一按工艺文件要求配齐生产设施,生产设备应符合生产工艺文件要求。一生产设备应处于随时能启动状态,具有操作和保养规定。一生产设备信息(名称、型号、系统参数、设备状况、维修保养记录等)应处于受控制状态。一生产设备、工艺装备、监视和测量装置应满足规定要求。5.3.3.4生产物料质量控制
生产物料质量控制应满足以下内容。生产物料采购应符合采购流程要求、物料供应方应是具备相应资质的合格供方;外购产品的数量、质量要满足物料质量标准要求;对外购产品的人厂检验、人库、贮存和发放实施有效控制。一通过质量控制系统检查,确认批次管理、质量记录与产品实物一致,并符合有关规定;批次管理的产品应做到批次清、质量状态清、原始记录清、数量清、批(炉)号清及分批投料、分批装配/铸造、分批转移、分批入库、分批出厂。一一工序生产过程质量控制系统应能按批次建立随工流动信息,随机抽查确认其详细记录投料、加工、检验的数量、质量、操作者和检验者等数据信息,并按规定进行保存。转人本工序的器材(原材料、毛坏、半成品、元器件、零件、部件、组件、外购成品件及主要辅助材料)应具有合格证明文件或标识。5.3.3.5
生产工艺质量控制
生产工艺质量控制应满足以下内容。生产现场使用的文件包括产品设计图样和有关技术文件应能满足批量生产需要;生产用设计图样应通过定型,且完整、准确、协调、统一、清晰。一生产产品的工艺方案,经过生产部、技术部、质检部评审并合格。一一关键或特殊过程的质量控制方法,经过评审应纳人工艺规程,对生产过程进行标识管理。一一工艺方案、关键件和重要件的工艺应经过评审。一对产品制造、检验和试验所用计算机软件应经过鉴定,并确保满足生产要求。一一各种作业指导书和技术文件的质量和数量应能满足批量生产要求。5.3.3.6生产环境质量控制
生产环境质量控制应满足以下内容。控制对象包括温度、湿度、清洁度、照明、防静电等,环境条件符合工艺文件要求。生产过程对环境有特殊要求时,应满足要求,并有相应控制手段。如有些测量仪器和测量过程要求恒温恒湿,对光强度、清洁度、振动、电磁等也有要求。一一外购产品的贮存条件应满足规定要求。5.3.3.7生产检测质量控制
生产检测质量控制应满足以下内容。一对产品实现的全过程实施监视和测量,并形成文件。一有外购产品人厂检验的文件。一有过程检验、最终检验的文件。一一有计量器具的检定、修理、发放等各种文件;计量器具的不确定度应满足生产产品的要求。一检验、测量和试验设备应按生产计划配备齐全;对检验与生产共用的工艺装备,应具有控制文件,保证按规定进行检验和校准。6
5.4质量分析与评价
质量分析与评价应满足以下内容。GB/T41478—2022
一系统对质量数据趋势进行监控,并对综合指标进行统计分析。基于实时采集质量数据所呈现出的总体趋势,利用质量预测和控制方法对潜在的质量问题进行警告。一对不合格品信息进行统计,分析产品质量实际状况,查找质量控制中的薄弱环节。对于质量异常的数据应进一步分析质量异常原因,对于质量正常的数据提供统计分析和趋势分析。采集产品的质量数据与质量目标数据库进行比对,对数据差异进行评价,评价结论用于指导产品生产过程质量控制。
5.5质量追溯与改进
质量追溯与改进应满足以下内容。系统应支持以产品标识作为追溯载体,基于产品质量档案,追溯产品装配/铸造生产过程中的关键信息,如作业人员、作业地点、加工工艺、加工设备、作业时间、质量检测结果、不合格品处理过程等。
一系统应对质量数据执行追溯,质量追溯结果应能转入质量分析和质量改进,形成质量闭环控制。
一系统应能抽查并确认每个或每批产品都有符合要求标识和记录;当产品或零部件质量需要追溯时,确保产品的识别具备可追溯性。针对生产过程中发现的质量缺陷,基于“计划-执行-检查-处理”(PDCA)循环原则构建质量持续改进机制,固化质量改进流程,提供质量异常原因分析工具,不断积累形成完备的质量改进经验库。质量改进目标和手段应反馈至工艺系统,从源头进行改进。6装配质量控制
6.1通用要求
装配过程中采集到的数据与CAPP、ERP、MES等信息化管理系统对接,形成基于生产任务包括生产计划、人力资源、生产工艺、生产设备、检测设备、工序作业指导、质量追溯管理的装配质量保障管理系统。采用HMI+PLC自动控制技术、通信技术、传感技术等,系统具有虚拟装配、三维信息处理、监视、视觉识别检测等自我诊断的功能,系统具有采集产品的质量数据并加以分析、比对、研判、控制等质量控制技术。主要包括事前控制、事中控制和事后控制。其装配过程质量控制架构图如图2所示。事前控制是基于装配任务,完成对人、机、料、物、环的质量保证工作,建立装配质量管理系统和确定质量目标数据,为装配过程采集的数据比对做准备,事前控制为装配过程质量控制提供资源保障。事中控制是基于生产过程中采集到质量数据与质量目标数据进行比对、分析、研判,实时反馈信息,确保装配过程中产生的问题及时发现、及时解决以及预防纠偏。事后控制是在总装配工作完成以后,利用测试、验证等手段完成对整机的数据采集,对采集的数据进行分析和评价,找出采集数据与质量目标数据差异,分析差异产生的原因,并对引起装配质量缺陷的环节进行追溯,提出保障措施,以及利用数据进行装配质量缺陷预测。7
GB/T41478—2022
事前控制
生产任务
装配资源保障
6.2事前控制技术要求
事中控制
质量目标数据库
质量数据采集
那件装配
总装配
图2装配质量控制示意图
事后控制
质量追潮
事前控制是基于生产任务对生产计划、人力资源、生产工艺、生产设备、生产物料、检测设备、工序作业指导等生产资源保障环节的质量控制。常规要求包括以下内容:
装配任务作业资料核对:包括BOM、零件图、部件装配图、总装配图等,应保证图纸的完整性、正确性和整洁性:
实施生产过程现场检验,即对将要开始的工艺过程保障条件进行全面系统的检查,包括作业人员、设备、工具、工装、检验人员及器具以及工件、标识、齐套、信息系统状态、工艺执行依据的所有相关文件;
装配零件的核对:包括零件的制造质量,如零件的制造精度符合图纸要求,不符合要求的不得启用;
对检查装配工艺操作人员和质量检验人员进行培训,掌握装配工艺规程及了解装配质量目标数据:
对装配工艺文件里涉及的装配用设备和检测用设备进行试操作和校核;零部件原材料和生产设备在装配过程中处于受控状态,并具有可追溯性;根据装配任务和装配质量控制要求,对装配对象进行分析,结合装配车间的实际生产能力,制定装配计划;
质量控制作业应与企业现有生产条件紧密结合;事先设计出符合用户需求的装配质量检验标准。数字化要求包括以下内容:
通过样机的虚拟装配验证装配过程或装配工艺的正确性,并建立工艺过程数据库和质量目标数据库,对装配过程实施风险点分析用于装配工艺规程的改进8
GB/T41478—2022
基于APS排产调度的准时化,应保障装配过程质量控制作业的同步化和准时化。6.3事中控制技术要求
事中控制是基于装配过程对零件装配成部件、部件到总装的各个环节进行数据采集,并与质量目标数据进行实时比对、分析和研判,及时发现质量问题并预警和反馈。常规要求包括以下内容。
实施装配线运行监视,获取各装配工位的作业情况,判断装配过程稳定性和连续性,监视产品装配过程中的运行情况。
装配流程集成检查,基于虚拟装配流程,制定零部件质量文件和装配工艺规程,对零部件装配过程或环节进行检验,防止对下部工序的影响。一结合装配件、装配工序规程和关键设备情况,设置关键检验点,并将其在产品质量检验报告等质量文件中明确出来。
一质量信息员应熟悉装配工艺及装配质量数据、知识和工艺过程,贯彻企业的质量文件内容和要求,确保上述文件内容得到实施。各项质量信息如检验、试验记录等应齐全,数据采集应准确,并妥善保管,具有可追溯性。与工序控制有关的各项质量信息,按规定的程序进行分类、统计、分析和处理,并上传至车间看板。装配工艺流程进人关键工序(或关键过程)时,应在下部工序不可逆或下部工序完成后,且产品难以拆卸或对前面的工序无法检验之前,实施对该工艺作业质量进行检验。一面向产品再制造工程,基于产品装配过程质量情况,对既有的故障数据实施重点检验,反向改进产品结构、装配工艺和装配过程,形成基于数据反馈的产品闭环制造模式。只有在质量向题发现并可快速解决的情况下,才能继续执行当前的生产过程。数字化要求包括以下内容:
装配前对合格零件进行数据采集、排序、身份标识、数据人库,以便根据配合性质进行选配;—基于数字化的三维模型实施虚拟装配,获取装配生产过程的图片、视频、VR体验场景等;装配过程质量数据的采集包括零件、部件、组件的编号与批次、装配人员、检验人员、完成时间及装配质量数据;
一基于装配工艺过程监视,实时获取装配过程的数据,并以质量数据识别质量偏差,经分析后实时反馈,形成装配作业流程的闭环控制模式;一装配过程中关键设备的控制数据、关键工艺的质量数据等,要求能追溯到零件、部件、组件的编号与批次、装配人员、检验人员、完成时间及装配质量数据记录等,能在生产管理系统中与质量目标数据比对:
一一装配过程中实施产品质量状态跟踪,采集产品状态数据、实时获取各装配工作的作业情况。6.4事后控制技术要求
事后控制是基于装配结果对完成装配的整机进行测试、验证,进行数据采集;与质量目标数据库进行比对,实施分析、研判和评价;根据评价结论对影响装配质量事前和事中的各个环节进行追溯;利用数据分析出规律对质量缺陷进行预测,并根据产品质量装配预测对装配资源进行优化。常规要求包括以下内容。
在产品装配工艺文件或其他相关的研制文件中,设置关键检验点的检验项目、指标、合格判据、检验方法、检验记录等。结合产品研制过程进行具体细化,作为关键检验点现场实施的依据。必要时,上述有关内容应经过评审。一关键检验点检验结果由检验、工艺和产品设计人员共同确认并签署,对检验状态应进行标识,以表明检验合格与否;装配质量检验过程应按表格化的要求及时填写检验记录,检验记录应完9
小提示:此标准内容仅展示完整标准里的部分截取内容,若需要完整标准请到上方自行免费下载完整标准文档。
CCSN19
中华人民共和国国家标准
GB/T41478—2022
生产过程质量控制
系统模型与架构
装配与铸造
Quality control of productionprocess-System model and architecture-Assembly and casting
2022-04-15发布
国家市场监督管理总局
国家标准化管理委员会
2022-11-01实施
GB/T41478-—2022
规范性引用文件
3术语和定义
缩略语
系统模型与架构
5.1系统结构组成
系统功能及要求
系统模型技术要求
质量分析与评价
质量追溯与改进
装配质量控制
通用要求
事前控制技术要求
事中控制技术要求
事后控制技术要求
7铸造质量控制·
通用要求·
事前控制技术要求
事中控制技术要求
事后控制技术要求
参考文献
GB/T41478—2022
本文件按照GB/T1.1一2020《标准化工作导则第1部分:标准化文件的结构和起草规则》的规定起草。
请注意本文件的某些内容可能涉及专利。本文件的发布机构不承担识别专利的责任。本文件由中国机械工业联合会提出。本文件由全国工业过程测量控制和自动化标准化技术委员会(SAC/TC124)归口。本文件起草单位:无锡职业技术学院、吴忠仪表有限责任公司、机械工业仪器仪表综合技术经济研究所、东风设计研究院有限公司、浙江中控技术股份有限公司、武汉船用机械有限责任公司、中国石油大学(北京)、中国科学院沈阳自动化研究所、山东省计算中心(国家超级计算济南中心)、南昌大学、中国烟草总公司职工进修学院、中信戴卡股份有限公司、绵阳市维博电子有限责任公司、重庆川仪自动化股份有限公司、无锡市贝尔机械股份有限公司。本文件主要起草人:陈玉平、马玉山、王成城、游和平、俞文光、李讽、张凤丽、王凯、宋佳娜、马俊峰、郭伟、彭正红、黄亮、唐霞、王春喜、张镇、刘建胜、王德吉、刘阳、田英明、贾华、张海潮。I
1范围
生产过程质量控制系统模型与架构装配与铸造
GB/T41478—2022
本文件规定了装配与造数字化车间生产过程质量控制的系统模型与架构、装配过程质量控制、铸造过程质量控制等。
本文件适用于装配与铸造数字化车间生产过程质量控制,可用于提高装配与铸造生产过程质量控制能力。
2规范性引用文件
本文件没有规范性引用文件。
3术语和定义
下列术语和定义适用于本文件。3.1
生产过程
productionprocess
将原材料转变为成品的全过程。[来源:GB/T4863—2008,3.1.9]3.2
manufacturing
将材料从原材料或半成品状态转换成进一步完成状态的功能或活动。[来源:GB/T19114.44-2012,3.1.7]3.3
系统system
由一个或多个过程、硬件、软件、设施和人员组成的集合体,具有满足某个已明确的要求或目标的能力。
[来源:GB/T26224-2010,3.26]3.4
以任何方式(包括数学、物理、符号、图形或描述等方式)对现实事务某一方面进行的抽象描述。[来源:GB/T25485—2010,3.32]3.5
装配assembly
将零件或部件进行配合和连接,使之成为半成品或成品的工艺过程。[来源:GB/T51218—2017,12.1.1]3.6
虚拟装配
virtualassembly
对装配建模所形成的装配模型进行装配分析与模拟的过程。包括一次或多次的装配顺序规划、装1
GB/T41478—2022
配路径规划以及装配过程仿真等,可用于装配干涉检查和装配工艺优化等目的。来源:GB/T261012010,3.17
铸造casting
熔炼金属,制造铸型,并将熔融金属浇人铸型,凝固后获得具有一定形状、尺寸和性能的金属铸件的成型方法。
[来源:GB/T51218—2017,3.1.1]3.8
工艺technology
使各种原材料、半成品成为产品的方法和过程。[来源:GB/T51218—2017,2.1.38]3.9
质量管理qualitymanagement
制造执行层的制造设施协调、指导、管理和跟踪质量测量和汇报功能的活动。[来源:GB/T25485—2010,3.45]3.10
追溯tracing
提供资源和产品使用的组织记录的活动,利用跟踪信息从任何结点,向前或向后。[来源:GB/T25485—2010,3.50]3.11
质量控制qualitycontrol
致力于满足质量要求的措施与活动。[来源:GB/T51218—2017.2.5.73.12
数据data
适合于由人或计算机进行通信、解释、或处理的形式化方法的信息表示。[来源GB/T16656.1—20083.2.16]3.13
验证verification
提供客观证据,证明给定项目满足规定要求。[来源:GB/T27025—2019,3.8]3.14
traceability
可追溯性
追溯客体的历史、应用情况或所处位置的能力。[来源GB/T36061—2018,3.1]4
缩略语
下列缩略语适用于本文件。
APS:高级计划与排程(AdvancedPlanningandScheduling)BOM:物料清单(BillofMaterial)CAPP:计算机辅助工艺过程设计(ComputerAidedProcessPlanning)CRM:客户关系管理(CustomerRelationshipManagement)2bzxz.net
ERP:企业资源计划(EnterpriseResourcePlanning)FCS:铸造炉料系统(FoundryChargeSystem)HMI:人机界面(HumanMachineInterface)MES:制造执行系统(ManufacturingExecutionSystem)OA:办公自动化(OfficeAutomation)PDM:产品数据管理(ProductDataManagement)PLC,可编程逻辑控制器(ProgrammableLogicController)SCM:供应链管理(SupplyChainManagement)VR:虚拟现实技术(VirtualReality)系统模型与架构
5.1系统结构组成
GB/T41478—2022
生产过程是指从产品投产前生产技术组织工作开始,直到把合格产品生产出来的全部过程。生产过程始于用户需求,终于生产出合格产品之间的过程,包括根据用户需求下达生产任务、制定生产计划、提出生产资源保障、装配与铸造生产等环节。质量控制是为使产品或服务达到质量要求而采取的技术措施和管理措施方面的活动。质量控制的目标在于确保产品质量满足用户要求生产过程质量控制系统各环节架构关系如下:一根据用户需求制定质量目标数据,质量监控系统利用质量目标数据对生产资源保障的各个环节进行质量控制;
基于产品采集的质量数据与质量目标数据进行比对,对比对结果进行分析与评价,对质量缺陷进行追溯,对影响质量的环节进行改进。生产过程质量控制系统各环节之间关系架构描述如图1所示。装配/铸造数字化车间生产过程质量控制系统是基于现有的数字化车间的建设成果,应用新一代信息技术,提升企业的生产过程质量控制水平。装配/铸造产品是将物料在特定的条件下,通过人员、设备,按照一定的工艺方法经过特定的工序生产手段得到的过程输出。
装配/铸造生产过程质量控制系统是生产过程质量控制中针对装配/铸造环节的信息管理系统。装配/铸造生产过程质量控制系统模型是对装配/铸造过程质量控制的信息集成。3
GB/T41478—2022
用户需求
生产任务
生产计划
生产资源保障
装配/铸造
生产组织
5.2系统功能及要求
生产过程
人力资源
生产设备
生产物料
生产工艺
生产环境
质量数据采集
作业培训
检验与校核
检验与确认
仿真与优化
监测与保证
质量控制
质量追潮与改进
质量分析与评价
质量数据比对
图1装配/铸造系统模型与架构图系统应具备的功能包括以下内容。质量目标数据
质量监控
支持各个数字化工位/智能终端快速获取物料质量数据、工序数据、设备状态数据等,具有工序执行视频监视、基于消息机制的呼叫联络、车间看板数据显示等网络化质量控制信息能力;可按工位/人员标识发送管理信息和收取反馈信息。支持实施生产过程质量数据采集,可辅助人工检查及在线自动测量,以最小的滞后时间获取工艺结果检测数据,使多个并行工位的质量数据及时入库,为生产过程质量数据分析和控制决策提高数字化、网络化环境,从而强化生产过程质量控制的效果。系统应与数字化车间的制造执行、企业数字化设计制造一体化等生产过程质量相关信息系统实现集成应用,且能够客观展示系统必备的软件功能;系统及各个应用软件、各用户端具有统一的时钟控制;系统应具有环境适宜性、数据精确性、网络互操作性和信息安全性。系统应满足的要求:
生产过程中影响产品质量特性的因素主要包括六个方面,即人力、机器、材料、方法、环境和测量,由于这些质量因素的变化,使得产品质量特性之间存在着差异,应将上述六要素加入质量控制范畴;
装配/铸造生产过程质量控制是从工艺执行与管理、装配/铸造工序制造执行与管理,以及贯穿始终的生产过程质量控制,最终输出产品的过程;装配/铸造生产过程质量控制系统是从工序质量数据采集,作用于质量监控,再到质量检测与判定,质量检测与判定的结果可作用于质量分析与评价,对于质量异常的数据,立刻停止加工转人质量追溯,对于质量正常的数据转人质量分析与评价:质量监控和质量检测与判定的结果可用于质量追溯与改进,质量追溯应作用于生产资源保障和装配/铸造生产组织过程质量控制输入环节。5.3系统模型技术要求
5.3.1通用要求
GB/T41478—2022
系统是对金属原材料或零部件转变成产品的过程质量监控,贯穿生产过程始终,是一个具有用户需求输人和产品输出的系统。
系统应遵循以下原则,可靠性、安全性、可扩展性。系统对影响生产过程的人员、设备、工装、材料、方法和环境等因素进行控制,确保其处于受控状态。系统将装配/铸造生产过程所有的质量信息纳人质量控制系统,确保信息传递完整、有效,信息记录清晰、准确,信息输出准确、完整,并用于质量改进和追溯。5.3.2质量数据采集
质量数据采集对象包括产品的信息(名称、件号、材料牌号、产品状态、条码、生产数量等)、质量检测结果(设备检测结果、人工检测结果等)。系统应提供质量数据的全面采集,对质量控制过程的关键停检点应在指导性工艺文件中标明,并有系统控制停检,关键质量数据应能够实现在线自动测量,以保证产品质量档案的准确与完整。系统应满足数据监控所需的网络通信,提供多种工序质量数据的采集方法,支持各种异构数据源的数据集成,支持各类质量数据的集中存储与初步处理。5.3.3质量监控
5.3.3.1通则
根据产品标准要求,对生产过程中的产品特性进行监控。质量监控应通过质量控制系统记录生产过程质量数据,以满足为产品生产过程符合性以及质量管理体系运行有效性提供证据的要求。质量记录类型(包括电子表格)一般包括:检验报告、试验数据、鉴定报告、确认报告、考察和审核报告、不合格品审理报告、校准报告、纠正措施和改进报告等。质量控制系统应确认质量记录的标识、贮存、保护、检索、保存期限和处置的控制情况,确认质量记录有效、完整、准确、连续、易于识别和检索。定期随机抽查质量记录,验证质量记录与产品实物的符合性。装配/铸造生产过程质量监控主要包括对生产资源保障、装配/铸造生产组织两大环节进行质量监控,其中生产资源保障监控包括对人力资源、生产设备、生产物料、生产工艺、生产环境等生产要素进行质量控制,确认其符合相关规定。5.3.3.2人力资源质量控制
人力资源质量控制应满足以下内容。生产人员及其要求,配备足够数量的生产工人和辅助人员,以满足产品的生产过程及各工种工序的要求。生产人员应经过专业培训,持证上岗。检验员及其要求,检验员数量以能完成检验工作任务,并能有力配合生产检验为宜。检验人员应经过专业培训,持证上岗。
技术和管理人员要求,人员数量应保证能够有效地管理生产现场,保证整个生产过程有效进行为宜。技术和管理人员工作能力应能够及时高效地解决分管领域内发生的各种问题,确保自已的工作不影响生产。
生产设备质量控制
生产设备质量控制应满足以下内容。5
GB/T41478—2022
一按工艺文件要求配齐生产设施,生产设备应符合生产工艺文件要求。一生产设备应处于随时能启动状态,具有操作和保养规定。一生产设备信息(名称、型号、系统参数、设备状况、维修保养记录等)应处于受控制状态。一生产设备、工艺装备、监视和测量装置应满足规定要求。5.3.3.4生产物料质量控制
生产物料质量控制应满足以下内容。生产物料采购应符合采购流程要求、物料供应方应是具备相应资质的合格供方;外购产品的数量、质量要满足物料质量标准要求;对外购产品的人厂检验、人库、贮存和发放实施有效控制。一通过质量控制系统检查,确认批次管理、质量记录与产品实物一致,并符合有关规定;批次管理的产品应做到批次清、质量状态清、原始记录清、数量清、批(炉)号清及分批投料、分批装配/铸造、分批转移、分批入库、分批出厂。一一工序生产过程质量控制系统应能按批次建立随工流动信息,随机抽查确认其详细记录投料、加工、检验的数量、质量、操作者和检验者等数据信息,并按规定进行保存。转人本工序的器材(原材料、毛坏、半成品、元器件、零件、部件、组件、外购成品件及主要辅助材料)应具有合格证明文件或标识。5.3.3.5
生产工艺质量控制
生产工艺质量控制应满足以下内容。生产现场使用的文件包括产品设计图样和有关技术文件应能满足批量生产需要;生产用设计图样应通过定型,且完整、准确、协调、统一、清晰。一生产产品的工艺方案,经过生产部、技术部、质检部评审并合格。一一关键或特殊过程的质量控制方法,经过评审应纳人工艺规程,对生产过程进行标识管理。一一工艺方案、关键件和重要件的工艺应经过评审。一对产品制造、检验和试验所用计算机软件应经过鉴定,并确保满足生产要求。一一各种作业指导书和技术文件的质量和数量应能满足批量生产要求。5.3.3.6生产环境质量控制
生产环境质量控制应满足以下内容。控制对象包括温度、湿度、清洁度、照明、防静电等,环境条件符合工艺文件要求。生产过程对环境有特殊要求时,应满足要求,并有相应控制手段。如有些测量仪器和测量过程要求恒温恒湿,对光强度、清洁度、振动、电磁等也有要求。一一外购产品的贮存条件应满足规定要求。5.3.3.7生产检测质量控制
生产检测质量控制应满足以下内容。一对产品实现的全过程实施监视和测量,并形成文件。一有外购产品人厂检验的文件。一有过程检验、最终检验的文件。一一有计量器具的检定、修理、发放等各种文件;计量器具的不确定度应满足生产产品的要求。一检验、测量和试验设备应按生产计划配备齐全;对检验与生产共用的工艺装备,应具有控制文件,保证按规定进行检验和校准。6
5.4质量分析与评价
质量分析与评价应满足以下内容。GB/T41478—2022
一系统对质量数据趋势进行监控,并对综合指标进行统计分析。基于实时采集质量数据所呈现出的总体趋势,利用质量预测和控制方法对潜在的质量问题进行警告。一对不合格品信息进行统计,分析产品质量实际状况,查找质量控制中的薄弱环节。对于质量异常的数据应进一步分析质量异常原因,对于质量正常的数据提供统计分析和趋势分析。采集产品的质量数据与质量目标数据库进行比对,对数据差异进行评价,评价结论用于指导产品生产过程质量控制。
5.5质量追溯与改进
质量追溯与改进应满足以下内容。系统应支持以产品标识作为追溯载体,基于产品质量档案,追溯产品装配/铸造生产过程中的关键信息,如作业人员、作业地点、加工工艺、加工设备、作业时间、质量检测结果、不合格品处理过程等。
一系统应对质量数据执行追溯,质量追溯结果应能转入质量分析和质量改进,形成质量闭环控制。
一系统应能抽查并确认每个或每批产品都有符合要求标识和记录;当产品或零部件质量需要追溯时,确保产品的识别具备可追溯性。针对生产过程中发现的质量缺陷,基于“计划-执行-检查-处理”(PDCA)循环原则构建质量持续改进机制,固化质量改进流程,提供质量异常原因分析工具,不断积累形成完备的质量改进经验库。质量改进目标和手段应反馈至工艺系统,从源头进行改进。6装配质量控制
6.1通用要求
装配过程中采集到的数据与CAPP、ERP、MES等信息化管理系统对接,形成基于生产任务包括生产计划、人力资源、生产工艺、生产设备、检测设备、工序作业指导、质量追溯管理的装配质量保障管理系统。采用HMI+PLC自动控制技术、通信技术、传感技术等,系统具有虚拟装配、三维信息处理、监视、视觉识别检测等自我诊断的功能,系统具有采集产品的质量数据并加以分析、比对、研判、控制等质量控制技术。主要包括事前控制、事中控制和事后控制。其装配过程质量控制架构图如图2所示。事前控制是基于装配任务,完成对人、机、料、物、环的质量保证工作,建立装配质量管理系统和确定质量目标数据,为装配过程采集的数据比对做准备,事前控制为装配过程质量控制提供资源保障。事中控制是基于生产过程中采集到质量数据与质量目标数据进行比对、分析、研判,实时反馈信息,确保装配过程中产生的问题及时发现、及时解决以及预防纠偏。事后控制是在总装配工作完成以后,利用测试、验证等手段完成对整机的数据采集,对采集的数据进行分析和评价,找出采集数据与质量目标数据差异,分析差异产生的原因,并对引起装配质量缺陷的环节进行追溯,提出保障措施,以及利用数据进行装配质量缺陷预测。7
GB/T41478—2022
事前控制
生产任务
装配资源保障
6.2事前控制技术要求
事中控制
质量目标数据库
质量数据采集
那件装配
总装配
图2装配质量控制示意图
事后控制
质量追潮
事前控制是基于生产任务对生产计划、人力资源、生产工艺、生产设备、生产物料、检测设备、工序作业指导等生产资源保障环节的质量控制。常规要求包括以下内容:
装配任务作业资料核对:包括BOM、零件图、部件装配图、总装配图等,应保证图纸的完整性、正确性和整洁性:
实施生产过程现场检验,即对将要开始的工艺过程保障条件进行全面系统的检查,包括作业人员、设备、工具、工装、检验人员及器具以及工件、标识、齐套、信息系统状态、工艺执行依据的所有相关文件;
装配零件的核对:包括零件的制造质量,如零件的制造精度符合图纸要求,不符合要求的不得启用;
对检查装配工艺操作人员和质量检验人员进行培训,掌握装配工艺规程及了解装配质量目标数据:
对装配工艺文件里涉及的装配用设备和检测用设备进行试操作和校核;零部件原材料和生产设备在装配过程中处于受控状态,并具有可追溯性;根据装配任务和装配质量控制要求,对装配对象进行分析,结合装配车间的实际生产能力,制定装配计划;
质量控制作业应与企业现有生产条件紧密结合;事先设计出符合用户需求的装配质量检验标准。数字化要求包括以下内容:
通过样机的虚拟装配验证装配过程或装配工艺的正确性,并建立工艺过程数据库和质量目标数据库,对装配过程实施风险点分析用于装配工艺规程的改进8
GB/T41478—2022
基于APS排产调度的准时化,应保障装配过程质量控制作业的同步化和准时化。6.3事中控制技术要求
事中控制是基于装配过程对零件装配成部件、部件到总装的各个环节进行数据采集,并与质量目标数据进行实时比对、分析和研判,及时发现质量问题并预警和反馈。常规要求包括以下内容。
实施装配线运行监视,获取各装配工位的作业情况,判断装配过程稳定性和连续性,监视产品装配过程中的运行情况。
装配流程集成检查,基于虚拟装配流程,制定零部件质量文件和装配工艺规程,对零部件装配过程或环节进行检验,防止对下部工序的影响。一结合装配件、装配工序规程和关键设备情况,设置关键检验点,并将其在产品质量检验报告等质量文件中明确出来。
一质量信息员应熟悉装配工艺及装配质量数据、知识和工艺过程,贯彻企业的质量文件内容和要求,确保上述文件内容得到实施。各项质量信息如检验、试验记录等应齐全,数据采集应准确,并妥善保管,具有可追溯性。与工序控制有关的各项质量信息,按规定的程序进行分类、统计、分析和处理,并上传至车间看板。装配工艺流程进人关键工序(或关键过程)时,应在下部工序不可逆或下部工序完成后,且产品难以拆卸或对前面的工序无法检验之前,实施对该工艺作业质量进行检验。一面向产品再制造工程,基于产品装配过程质量情况,对既有的故障数据实施重点检验,反向改进产品结构、装配工艺和装配过程,形成基于数据反馈的产品闭环制造模式。只有在质量向题发现并可快速解决的情况下,才能继续执行当前的生产过程。数字化要求包括以下内容:
装配前对合格零件进行数据采集、排序、身份标识、数据人库,以便根据配合性质进行选配;—基于数字化的三维模型实施虚拟装配,获取装配生产过程的图片、视频、VR体验场景等;装配过程质量数据的采集包括零件、部件、组件的编号与批次、装配人员、检验人员、完成时间及装配质量数据;
一基于装配工艺过程监视,实时获取装配过程的数据,并以质量数据识别质量偏差,经分析后实时反馈,形成装配作业流程的闭环控制模式;一装配过程中关键设备的控制数据、关键工艺的质量数据等,要求能追溯到零件、部件、组件的编号与批次、装配人员、检验人员、完成时间及装配质量数据记录等,能在生产管理系统中与质量目标数据比对:
一一装配过程中实施产品质量状态跟踪,采集产品状态数据、实时获取各装配工作的作业情况。6.4事后控制技术要求
事后控制是基于装配结果对完成装配的整机进行测试、验证,进行数据采集;与质量目标数据库进行比对,实施分析、研判和评价;根据评价结论对影响装配质量事前和事中的各个环节进行追溯;利用数据分析出规律对质量缺陷进行预测,并根据产品质量装配预测对装配资源进行优化。常规要求包括以下内容。
在产品装配工艺文件或其他相关的研制文件中,设置关键检验点的检验项目、指标、合格判据、检验方法、检验记录等。结合产品研制过程进行具体细化,作为关键检验点现场实施的依据。必要时,上述有关内容应经过评审。一关键检验点检验结果由检验、工艺和产品设计人员共同确认并签署,对检验状态应进行标识,以表明检验合格与否;装配质量检验过程应按表格化的要求及时填写检验记录,检验记录应完9
小提示:此标准内容仅展示完整标准里的部分截取内容,若需要完整标准请到上方自行免费下载完整标准文档。

标准图片预览:
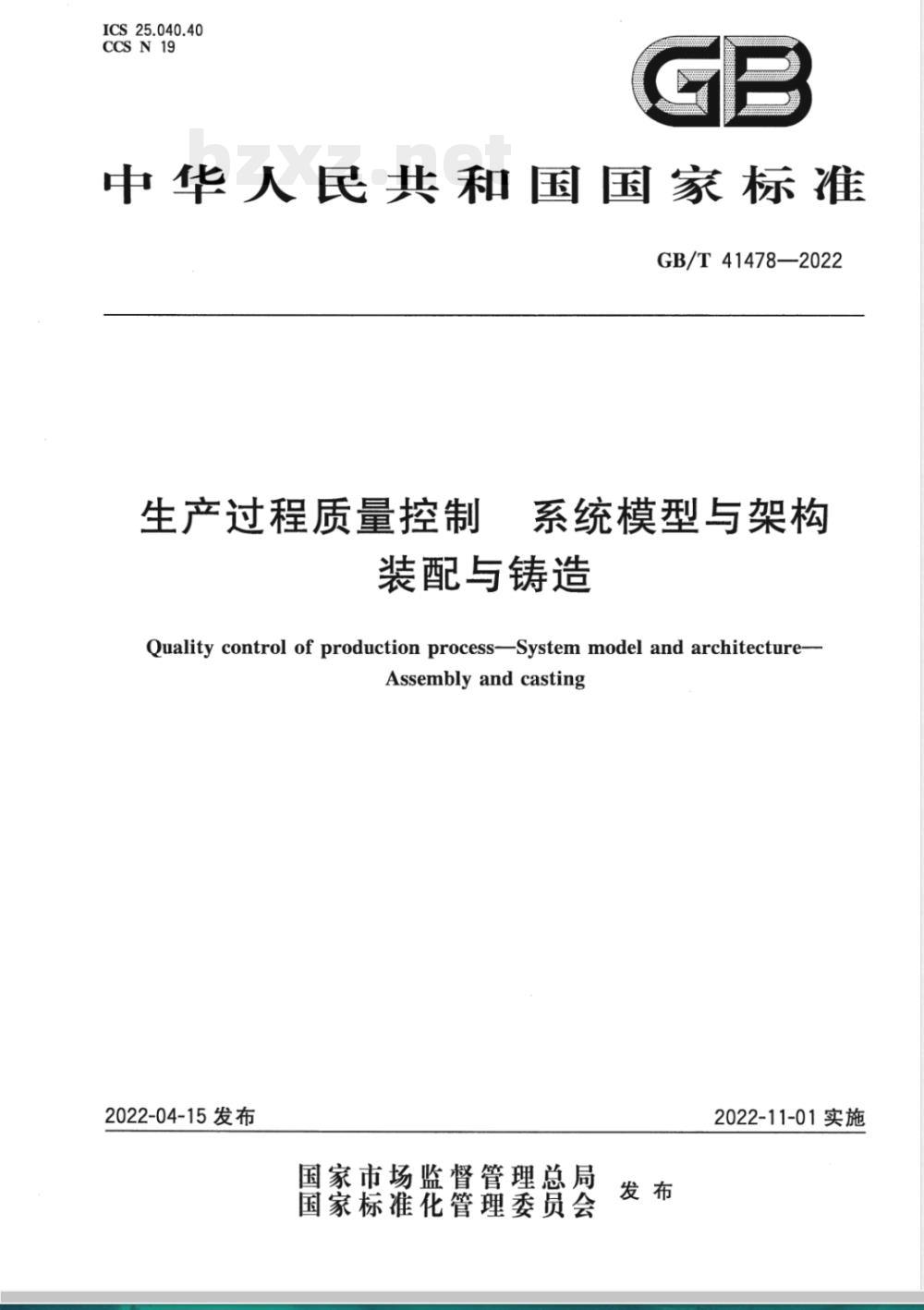
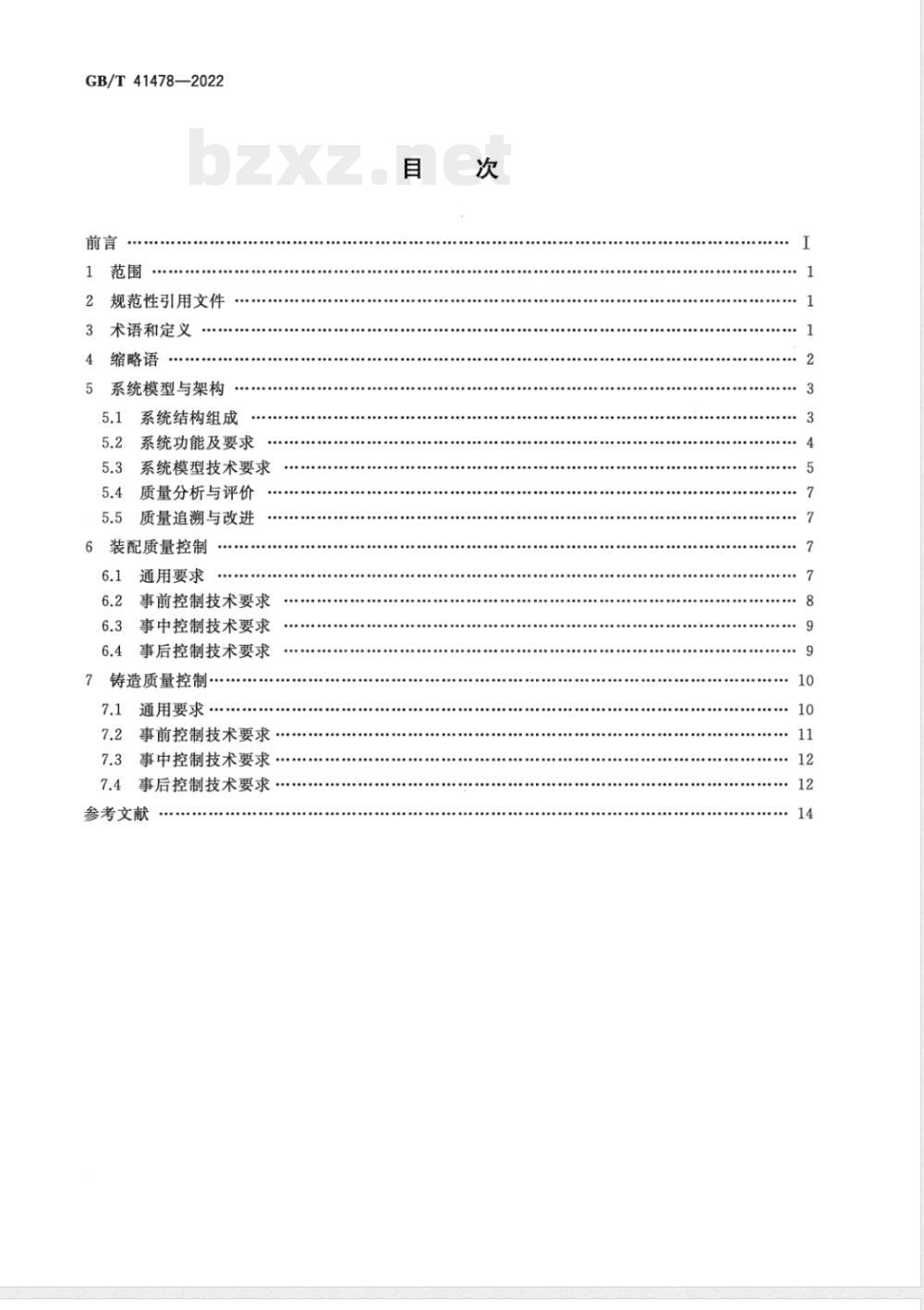
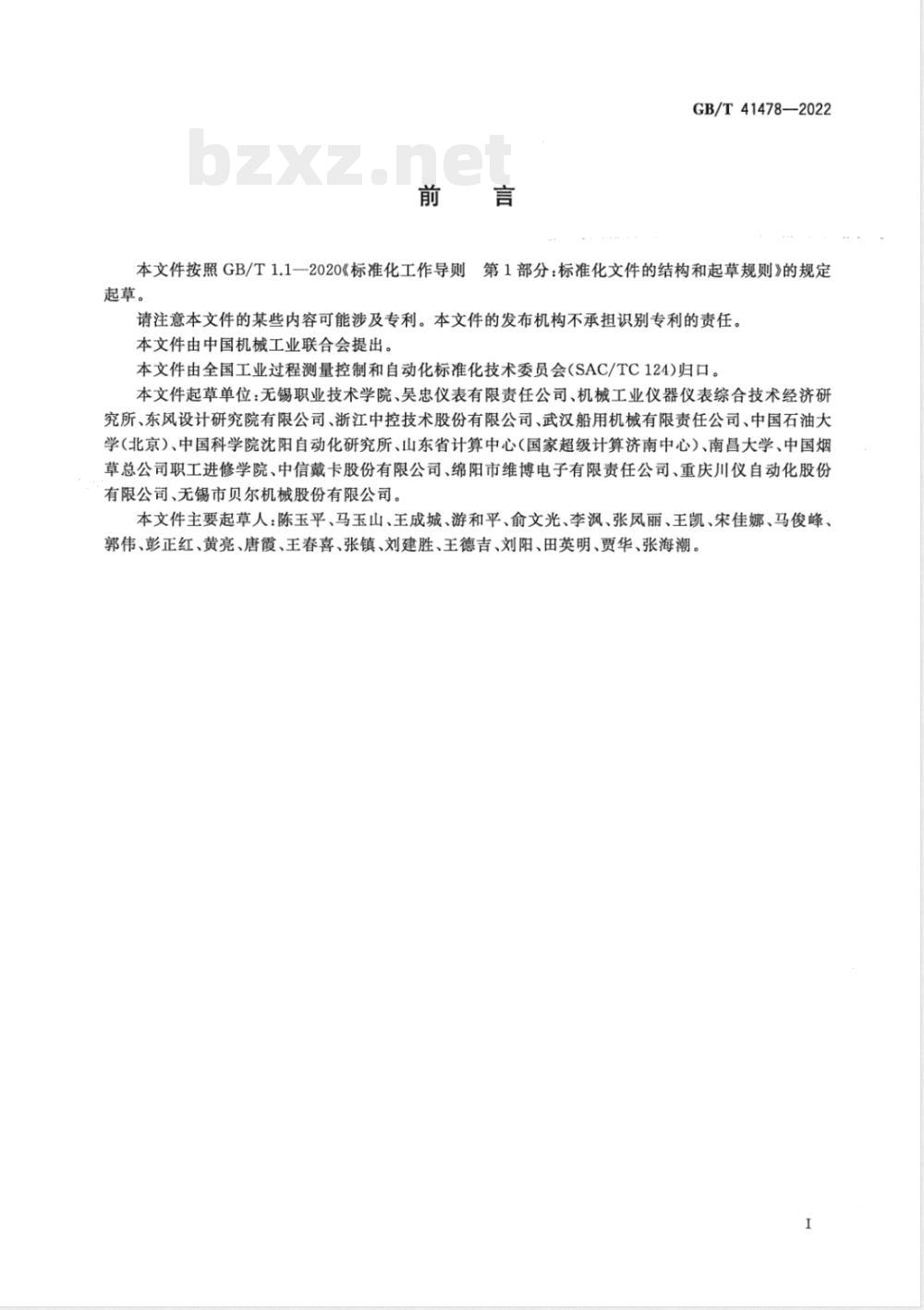
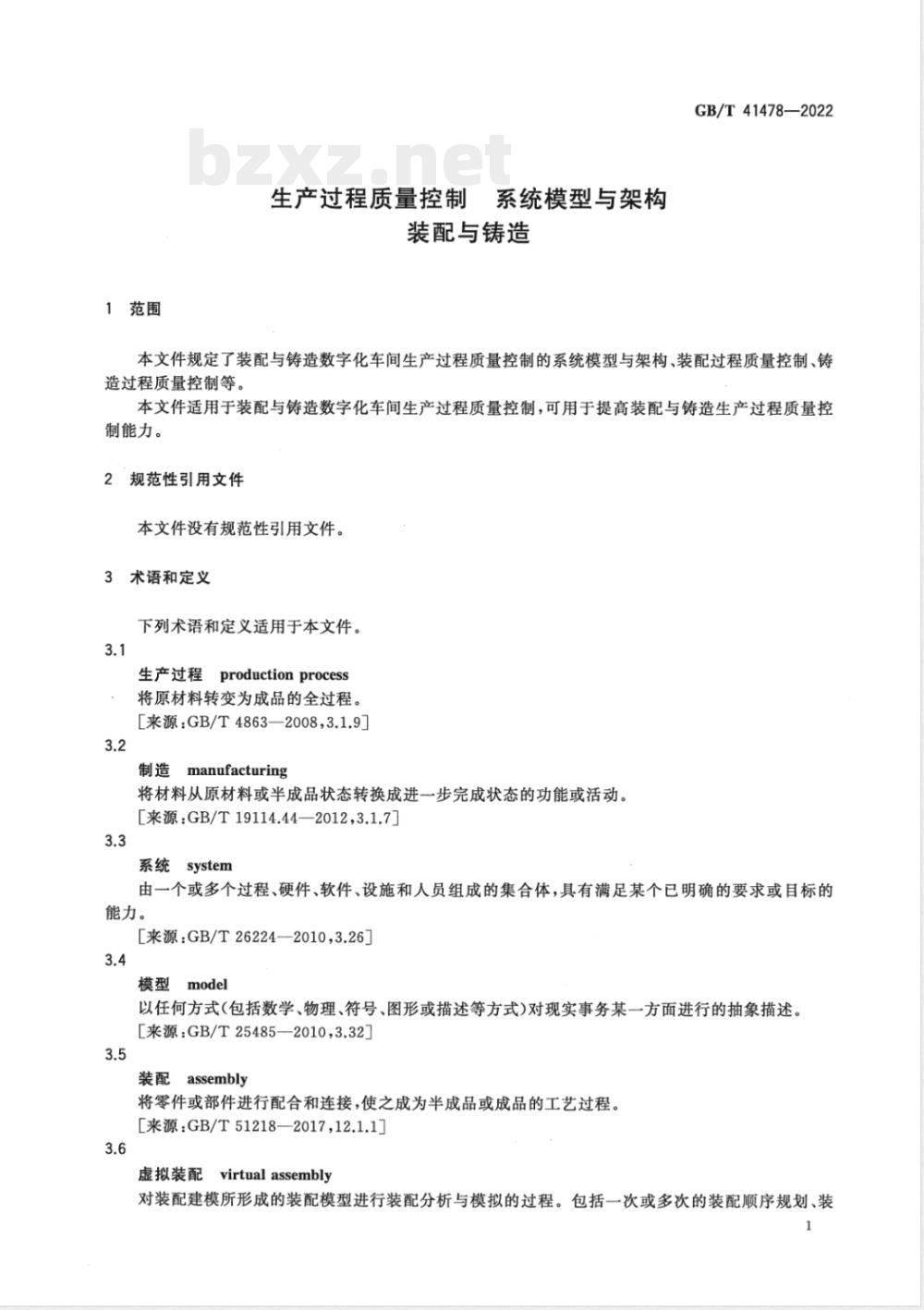
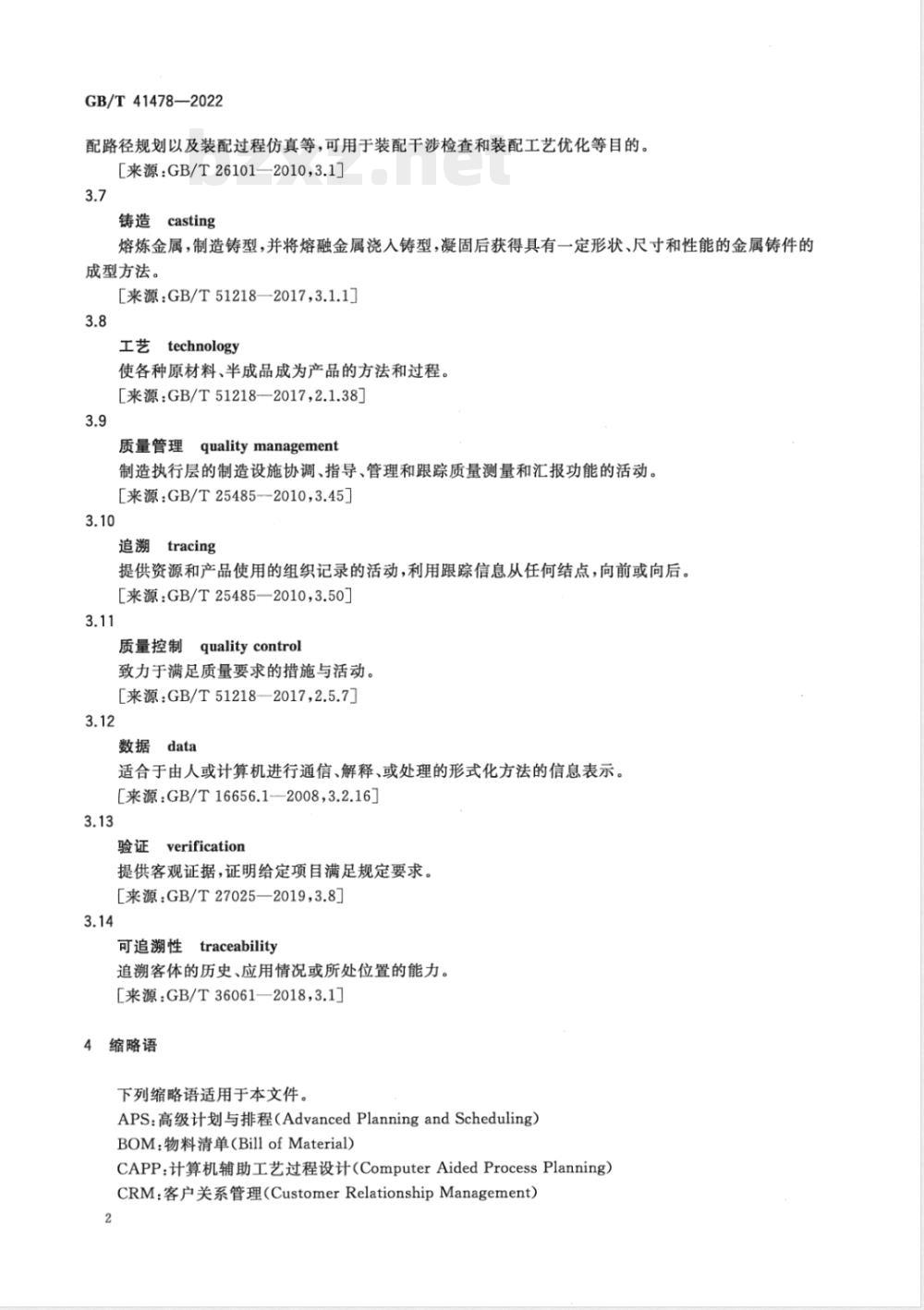
- 其它标准
- 热门标准
- 国家标准
- GB2761—2005 食品中真菌毒素限量
- GB7521—1987 多个控制器在一CA MAC机箱中
- GB/T90.2-2002 紧固件 标志与包装
- GB13690-2009 化学品分类和危险性公示 通则
- GB/T2988—2004 高铝砖
- GB3033.1—2005 /ISO 14726-1 : 1999 船舶与海上技术管路系统内含物的识别颜色第1部分:主颜色和介质
- GB/T80-2007 内六角凹端紧定螺钉
- GB13077-2004 铝合金无缝气瓶定期检验与评定
- GB/T2951.11-2008 电缆和光缆绝缘和护套材料通用试验方法 第11部分:通用试验方法 厚度和外形尺寸测量 机械性能试验
- GB/T4789.4-2003 食品卫生微生物学检验沙门氏菌检验
- GB917.2—2000 公路路线标识规则国道名称和编号
- GB/T14652.1-2001 小艇耐火燃油软管
- GB/T155—2006 原木缺陷
- GB9116.5-1988 PN1.6MPa(16bar)凸面带颈平焊钢制管法兰
- GB/T21485-2008 船舶和海上技术 船上消防、救生设备及逃生路线布置图
- 行业新闻
请牢记:“bzxz.net”即是“标准下载”四个汉字汉语拼音首字母与国际顶级域名“.net”的组合。 ©2009 标准下载网 www.bzxz.net 本站邮件:bzxznet@163.com
网站备案号:湘ICP备2023016450号-1
网站备案号:湘ICP备2023016450号-1