- 您的位置:
- 标准下载网 >>
- 标准分类 >>
- 铁路运输行业标准(TB) >>
- TB/T 2989-2015 机车车辆牵引齿轮
标准号:
TB/T 2989-2015
标准名称:
机车车辆牵引齿轮
标准类别:
铁路运输行业标准(TB)
标准状态:
现行出版语种:
简体中文下载格式:
.zip .pdf下载大小:
5.29 MB

点击下载
标准简介:
TB/T 2989-2015.Gear for railway locomotive and power car.
1范围
TB/T 2989规定了机车车辆用牵引齿轮(以下简称“齿轮")的分类、技术要求检验方法、检验规则、质量保证及标志、包装、运输和储存。
TB/T 2989适用于机车车辆用渐开线直齿圆柱齿轮和斜齿圆柱齿轮。
2规范性引 用文件
下列文件对于本文件的应用是必不可少的。凡是注日期的引用文件,仅注日期的版本适用于本文件。凡是不注日期的引用文件,其最新版本(包括所有的修改单)适用于本文件。
GB/T223钢铁及合金化学分析方法
CB/T225钢淬透性的末端淬 火试验方法( Jominy试验) ( GB/T 225- -2006 , IsO 642 :1999 ,IDT)
GB/T 226钢的低倍组 织及缺陷酸蚀检验法
CB/T228.1金属材料拉伸试验第1 部分:室温试验方法( GB/T 228. 1-2010, ISO 6892-1 : 2009 MOD)
CB/T 229金属材料夏比摆锤冲击试验方法( GB/T 229- -2007 , ISO 148-1 :2006 , MOD)
CB/T230.1金属材料洛氏硬度试验第1 部分:试验方法(A、B、C、D、E、F、G、H、K.N.T标尺)(GB/T 230. 1- -2009 ,ISO 6508-1 :2005 , MOD)
CB/T231.1金属材料布氏硬度试验第 1部分:试验方法( GB/T 231.1- -2009 , ISO 6506-1:2005 , MOD)
CB/T 699优质碳素结构钢
GB/T 1979- 2001 结构钢低倍组织缺陷评级图
CB/T 3077- 1999合金结构钢
GB/T 4336碳素钢和中低合 金钢火花源原子发射光谱分析方法(常规法)
GB/T 5216保证淬透性结构钢

部分标准内容:
中华人民共和国铁道行业标准
TB/T2989—2015
代替TB/T2989—2000
机车车辆牵引齿轮
Gear for railway locomotive and power car2015-07-02发布
国家铁路局发布
2016-01-01实施
规范性引用文件
技术要求
检验方法
检验规则
标志、包装、运输和储存
附录A(资料性附录)
附录B(规范性附录)
机车车辆牵引齿轮常用材料
印模法
TB/T2989—2015
TB/T2989—2015
本标准按照GB/T1.1—2009给出的规则起草。本标准代替TB/T2989--2000《机车车辆用齿轮供货技术条件》。与TB/T2989--2000相比,主要技术变化如下:
修改了分类(见第3章,2000年版的第3章);修改了非金属夹杂物的含量(见4.1.3,2000年版的4.3);增加了带状组织、力学性能要求(见4.1.7、4.1.1);修改了锻造要求(见4.2.1,2000年版的5.1);-删除了第2类齿轮制造方面的相关规定(见2000年版的5.2);修改了热处理要求(见4.2.2,2000年版的5.3);修改了切齿要求(见4.2.3,2000年版的5.5);增加了喷丸强化(见4.2.5);
修改了内部质量要求(见4.3.2,2000年版的6.2);修改了硬度要求(见4.3.3.1,2000年版的6.7);修改了有效硬化层深度(见4.3.3.2,2000年版的6.8);增加了金相组织要求(见4.3.3.3);修改了渗碳层的碳含量要求(见4.3.3.3.1.1,2000年版的6.4);修改了形状、尺寸和公差(见4.3.4,2000年版的6.6):增加了检验方法(见第5章);
修改了检验规则(见第6章,2000年版的第7章);修改了标志、包装、运输和储存(见第7章,2000年版的第8、12、15章);删除了生产质量的控制(见2000年版的第10、11、13、14章);删除了第1类和第2类齿轮认可程序及要求(见2000年版的第9章、附录A);删除了齿轮坏件超声波检查方法(见2000年版的附录B)。本标准由铁道行业内燃机车标准化技术委员会提出并归口。本标准起草单位:南车墅堰机车车辆工艺研究所有限公司、北京南口轨道交通机械有限责任公司、中国北车集团大连机车车辆有限公司、南车戚墅堰机车有限公司。本标准主要起草人:刘忠伟、文超、张银风、唐亮、蒋田芳、张亚光、高小平、李建国、张建平。本标准所代替标准的历次版本发布情况为:TB/T2989--2000。Ⅱ
1范围
机车车辆牵引齿轮
TB/T2989-2015
本标准规定了机车车辆用牵引齿轮(以下简称“齿轮”)的分类、技术要求、检验方法、检验规则、质量保证及标志、包装、运输和储存。本标准适用于机车车辆用渐开线直齿圆柱齿轮和斜齿圆柱齿轮2规范性引用文件
下列文件对于本文件的应用是必不可少的。凡是注日期的引用文件,仅注日期的版本适用于本文件。凡是不注日期的引用文件,其最新版本(包括所有的修改单)适用于本文件。GB/T223钢铁及合金化学分析方法钢辫透性的末端率火试验方法(Jominy试验)(GB/T225—2006,ISO642:1999,IDT)GB/T225
GB/T226
钢的低倍组织及缺陷酸蚀检验法GB/T228.1
2009MOD)
金属材料拉伸试验第1部分:室温试验方法(GB/T228.1-2010,ISO6892-1:GB/T229
金属材料夏比摆锤冲击试验方法(GB/T229-2007,ISO148-1:2006,MOD)GB/T230.1
金属材料洛氏硬度试验第1部分:试验方法(A、B、C、D、E、F、G、H、K、N、T标尺)(GB/T230.12009,IS06508-1:2005,M0D)GB/T231.1
2005,MOD)
GB/T699
金属材料布氏硬度试验第1部分:试验方法(GB/T231.1-—2009,IS06506-1:优质碳素结构钢
CB/T1979—2001结构钢低倍组织缺陷评级图GB/T3077-
GB/T4336
GB/T5216
GB/T5617
合金结构钢
碳素钢和中低合金钢火花源原子发射光谱分析方法(常规法)保证淬透性结构钢
钢的感应淬火或火焰淬火后有效硬化层深度的测定GB/T6060.2
表面粗糙度比较样块、磨、车、镗、铣、插及刨加工表面GB/T6394
金属平均晶粒度测定方法
GB/T9450
钢件渗碳淬火有效硬化层深度的测定和校核GB/T10095.1
圆柱齿轮精度制第1部分:轮齿同侧齿面偏差的定义和允许值(CB/T10095.1—2008,ISO1328-1:1995,IDT)GB/T10095.2圆柱齿轮精度制第2部分:径向综合偏差与径向跳动的定义和允许值(GB/T10095.2—2008,ISO1328-2:1997.IDT)GB/T10561—2005钢中非金属夹杂物含量的测定标准评级图显微检验法GB/T11259无损检测超声检测用钢参考试块的制作与检验方法钢的显微组织评定方法
GB/T13299—1991
GB/T15822.1无损检测磁粉检测第1部分:总则(GB/T15822.1—2005,IS09934-1:2001,IDT)
GB/T17394金属里氏硬度试验方法1
TB/T2989—2015
GB/T17879—1999齿轮磨削后表面回火的浸蚀检验HB/Z26-2011航空零件喷丸强化工艺JB/T10061A型脉冲反射式超声探伤仪通用技术条件JB/T9204-—2008钢件感应淬火金相检验TB/T2047.3铁路用无损检测材料技术条件第3部分:超声波检测用探头TB/T2254—1991机车牵引用渗碳率硬齿轮金相检验标准JISGO556钢中发纹宏观试验方法(Methodofmacro-streak-flawtestforsteel)3分
齿轮按其用途分类,分为以下类:a)第1类齿轮:300km/h以下动车组、客运机车和重载货运机车的齿轮:第2类齿轮:300km/h及以上动车组齿轮;b)
第3类齿轮:其他齿轮。
4技术要求
4.1材料要求
4.1.1牌号
齿轮材料的牌号宜在GB/T699、GB/T3077—1999、GB/T5216中选取。经供需双方协商,可采用其他材料。机车牵引齿轮常用材料参见附录A。4.1.2熔
第1和第2类齿轮应采用电炉熔炼或供需双方商定的钢锭或钢坏制造,且该钢锭或钢坏顶部和底部应有足够余量,并去除有害部位。钢应在炉内或浇包内镇静并进行真空脱气处理。钢应采用底注工艺。在任何情况下,选择浇注设备种类应预先经用户同意。4.1.3非金属夹杂物
第1类齿轮非金属夹杂物的含量应符合表1的规定;第2类齿轮非金属夹杂物的含量应符合表2的规定;第3类齿轮非金属夹杂物的含量应符合表3的规定。表1第1类齿轮用钢的非金属夹杂物含量夹杂物种类
A(硫化物类)
B(氧化铝类)
C(硅酸盐类)
D(球状氧化物类)
以上各类夹杂物总和应小于或等于4.0级。细系级别数(不大于)
纯洁度
粗系级别数(不大于)
表2第2类齿轮用钢的非金属夹杂物含量夹杂物种类
A(硫化物类)
B(氧化铝类)
C(硅酸盐类)
细系级别数(不大于)
纯洁度
粗系级别数(不大于)
夹杂物种类
D(球状氧化物类)
表2第2类齿轮用钢的非金属夹杂物含量(续)纯洁度
细系级别数(不大于)
以上各类夹杂物总和应小于或等于2.5级。表3第3类齿轮用钢的非金属夹杂物含量夹杂物种类
A(硫化物类)
B(氧化铝类)
C(硅酸盐类)
D(球状氧化物类)
以上各类夹杂物总和应小于或等于5.5级。4.1.4低倍组织
细系级别数(不大于)
纯洁度
TB/T2989—2015
粗系级别数(不大于)
粗系级别数(不大于)
4.1.4.1齿轮用钢应进行低倍组织检查和评定。酸浸低倍试片上不应有肉眼可见的缩孔、白点、气泡、翻皮、裂纹和夹杂等。酸浸低倍组织级别按GB/T1979一2001评定时,第1类和第2类齿轮的一般疏松、中心疏松、偏析均应小于或等于1.0级,第3类齿轮的一般疏松、中心疏松和偏析应符合GB/T3077-1999中表4的规定。
4.1.4.2第2类齿轮应进行宏观发纹检查,换算成基准面积(100cm2)后,应满足表4所示的数值。表4第2类齿轮宏观发纹限值
总换算数
4.1.5晶粒度
奥氏体晶粒度级别应大于或等于6级。4.1.6淬透性
宏观发纹总长度
淬透性曲线应符合GB/T5216或者供需双方协商的规定。4.1.7带状组织
最多发纹数
如用户有要求,在原材料上沿轴向取样后,按GB/T13299—1991中B系列进行评级,带状组织应小于或等于2级。
4.2制造要求
4.2.1锻造要求
4.2.1.1齿轮应采用锻坏制造。锻造、冲孔和成形应在去除钢锭或钢坏中不符合4.3.1和4.3.2规定的缺陷部分后进行。
4.2.1.2齿轮的锻造比,在开齿部位或齿根所在部位应满足以下要求:a)钢锭锻造比应大于或等于7;b)圆钢锻造比应大于或等于4。其他部位的锻造比应大于4。
4.2.1.3齿轮锻坏冲孔直径应符合下列要求:3
TB/T2989—2015
当成品齿轮的内孔直径小于或等于50mm时,坏件应锻成实心坏:a)
b)当成品齿轮的内孔直径小于148mm和大于50mm时,齿坏可锻成盲孔,如图1所示;单位为毫米
50
一成品齿轮的内孔直径:
h齿轮锻坏育孔深度;
一齿轮锻坏厚度。
w号和号
图1齿轮盲孔锻坏
当齿圈坏件重量大于或等于200kg时,其通孔直径至少应为150mm;重量小于200kg时,其c
通孔直径至少应为100mm。
4.2.1.4齿坏锻造后,应进行正火或正火+回火或调质处理。4.2.2热处理要求
4.2.2.1齿轮应进行热处理,如正火,调质和表面硬化处理。4.2.2.2表面硬化处理时应采取必要的措施保护不应被表面硬化的部位。4.2.2.3热处理用试棒或齿块应符合下列要求:对于热处理检验试棒,制造商应根据标准或合同的要求制造,且试棒应与产品同时进行热处理;
对于热处理齿块,建议采用5齿试块,且齿块应与产品同时进行热处理。4.2.3切齿要求
4.2.3.1齿轮的轮齿一般应来用滚齿加工,精滚时要求连续加工不应有接刀痕迹。4.2.3.2齿根过渡曲线应光滑连接,不应有滚切刀痕、加工棱楞等跳变缺陷的存在。4.2.4轮齿精加工
4.2.4.1当齿的精加工方式为磨削时,应对所有的齿面磨削。砂轮的成形应确保切削部分和磨削部分之间光滑过渡,且不应小于120°见图2和图3。4.2.4.2如采用凸角留磨滚刀加工齿坏,则在渗碳和淬火后,不应磨削过渡区和根部圆柱面。4.2.4.3如采用标准刀具加工齿坏,齿槽规定磨削,则在齿槽磨削后应进行电解抛光或采用喷丸处理。
4.2.4.4如用户有要求,磨齿后表面回火等级应符合GB/T17879—1999中FB2的规定。4.2.5喷丸强化
4.2.5.1齿轮应按产品图样规定喷丸,其中第1类齿轮宜全齿廓喷丸,第2类齿轮宜齿根喷丸。4.2.5.2第1类齿轮推荐采用复合喷丸T艺。次喷丸强度0.5~0.6A,二次喷丸强度约为一次喷丸强度的三分之一。一次表面覆盖率应大于或等于200%,二次表面覆盖率应大于或等于100%。4
实际完成情况中
磨削极限中
磨削前借助刀具切出的毛坏齿面1209
凸角滚刀
理想的完成情况
磨削极限电
磨削前借助刀具切出的毛坏齿面120
图3标准刀具
TB/T2989—2015
4.2.5.3喷丸后,齿面的粗糙度充许比原有精加工表面降低1/2级,推荐粗糙度范围Ra0.6~Ra1.6。4.2.5.4喷丸后应进行如下处理:a)喷后用25倍的放大镜观察覆盖率是否均匀。b)喷丸后,应及时清理零件表面,并上防锈油防锈。4.2.5.5其他要求宜按HB/Z26—2011的规定。4.3质量要求
4.3.1表面质量
齿轮不应有裂纹、折叠、缺肉和凹坑等任何影响使用的缺陷。特别是轮齿,应无淬火裂纹或磨削裂纹,无毛刺或拉伤等任何缺陷,齿的过渡棱都应倒角。4.3.2内部质量www.bzxz.net
4.3.2.1齿轮的所有部位都应完好,不应有任何影响使用的缺陷。特别是齿区或临近齿区,不应有夹杂、气孔、偏析。
TB/T2989—2015
齿坏开齿部位2倍齿高或齿根以下25mm处的无损检测质量要求应符合表5的规定,其余4.3.2.21
部位按3mm平底孔当量进行检测。表5不同缺陷类型的质量要求
起始记录
缺陷类别
当量值中
单个缺陷最大
允许当量值中
缺陷任一方向上延伸
的最大长度
不允许
缺陷处底波降低
量的最大允许值
密集区缺陷最大
充许范围”
125×103
由于超声波检测存在局限性和不足,除了从生产工艺、缺陷产生的部位及其大致走向和分布能对缺陷性质进行估判外,纯粹从超声波检测技术上是无法对缺陷进行定性的。因此,在使用时,最好用其他有效方法对缺陷定性进行辅助说明,如缺陷已露出表面、金相检验等方法。用户有特殊要求时,其质量验收条款也可由供需双方具体协商制定。密集区缺陷范围的计算是以密集区最大长度范围×最大宽度范围×最大深度范围。相邻密集区间的间距不应小于150mm,否则,应视为一个密集区。存在多个密集区时,应分别计算其密集区范围,然后累计求和,按累积值评定。若密集区深度范围小于或等于50mm时,则按50mm计算其深度范围;若密集区长度范围小于或等于50mm时,则按50mm计算其长度范围。
4.3.3热处理质量
4.3.3.1硬
4.3.3.1.1非表面硬化部位热处理后的硬度热处理后(正火+国火、淬火+低温回火、调质等)的硬度应符合有关技术文件的规定。4.3.3.1.2硬化层表面硬度
硬化层表面硬度应为:
a)渗碳淬火齿轮硬度为58HRC~64HRC;b)感应淬火齿轮硬度为52HRC~60HRC。4.3.3.1.3渗碳淬火齿轮表面硬化处理的均匀性在同一齿轮的轮齿面上测得的表面硬度值之差不应大于3HRC。4.3.3.1.4表面硬化范围
感应火齿轮硬化层范围包括轮齿所有的工作齿面,齿面过渡区和齿根圆柱表面。渗碳淬火齿轮的轮齿的下列表面应有硬化层:a)工作齿面、齿根圆柱表面和齿项圆柱表面、过渡区表面:b)侧表面,高度从齿顶圆直径开始至少为齿高的1.5倍。4.3.3.2有效硬化层深度
4.3.3.2.1
齿轮各部有效硬化层深度应符合表6的规定。表6齿轮各部有效硬化层深度
齿轮状态
渗碳淬火齿轮
感应淬火齿轮
注:m为齿轮模数。
4.3.3.2.2如无特别规定,渗碳淬火界限硬度为550HV1。有效硬化层深度CHD
CHD≥(m +1)/10
CHD≥0.2m
4.3.3.2.3第2类齿轮有效硬化层深度的均勾性应符合标准或合同的规定。4.3.3.2.4感应淬火齿轮有效硬化层深度应符合下列规定:6
TB/T2989—2015
应检查轮齿齿廊全齿宽范围内半齿高及齿根处有效硬化层深度,沿齿廓分布的硬化层,应能达到图样规定的要求;
b)齿根处有效硬化层深度不低于半齿高处有效硬化层深度的60%,且均应不小于图样规定的最小值;
c)齿顶硬化层不应重叠。
4.3.3.3金相组织
4.3.3.3.1渗碳火组织
4.3.3.3.1.1表层含碳量
表层含碳量应为0.6%~1.0%。
4.3.3.3.1.2渗碳层碳化物
渗碳层应以不连续、弥散状碳化物组织形态为主,无块状或网状的碳化物组织形态存在,满足TB/T2254—1991中第一评级图的1~5级要求。4.3.3.3.1.3渗碳层表层组织和残余奥氏体含量渗碳层表层组织应以细针状马氏体为主,残余奥氏体含量应符合TB/T2254一1991中第二评级图的1~4级,且细小弥散。
4.3.3.3.1.4渗碳层晶界内氧化深度和非马氏体深度渗碳层晶界内氧化深度和非马氏体深度应满足表7的要求。表7渗碳层晶界内氧化深度和非马氏体深度有效硬化层深度CHD
CHD≤0.75
0.75≤CHD≤1.50
1.50
心部组织为马氏体、贝氏体,游离铁素体不应超过10%。4.3.3.3.2感应痒火组织
4.3.3.3.2.1表层组织
内氧化深度和非马氏体深度
感应率火齿轮淬硬层组织应为较细马氏体或隐晶马氏体,应满足JB/T9204—2008的4级~7级要求。
4.3.3.3.2.2心部组织
心部组织应为回火索氏体或回火届氏体。4.3.4形状、尺寸和公差
齿轮的形状、尺寸和公差应满足图纸或技术文件的规定,齿轮的轮齿精度等级应符合GB/T10095.1、GB/T10095.2的相关规定。4.3.5表面粗糙度
4.3.5.1齿轮过渡区和齿根圆柱面粗糙度宜按表8的规定。7
TB/T2989—2015
表8过渡区和齿根圆柱面粗糙度
工作齿面的粗糙度Ra
1
5.1化学成分
过渡区和齿根圆柱表面的粗糙度Ra2.5
5.1.1钢的化学成分分析按照GB/T223或GB/T4336的规定进行。对化学成分检验结果有争议时,应按GB/T223执行。
5.1.2化学成分分析试样应在锻坏或锻造试样上取样,并应通过冷切割取得,如需要,可通过钻削取得(钻屑)。
5.2非金属夹杂物
非金属夹杂物检验按照GB/T10561-2005中A法的规定进行评定。5.3低倍组织
5.3.1酸浸低倍组织检验按照GB/T226的规定进行。5.3.2宏观发纹检验按照JISG0556的规定进行。5.3.3检查应在钢坏端部的横截面上或切头后有代表性的钢锭头部横截面上进行。5.4晶粒度
晶粒度检验按照GB/T6394的规定进行。5.5淬透性
淬透性检验按照GB/T225的规定进行。5.6带状组织
带状组织检验按照GB/T13299—1991的规定进行。5.7力学性能
5.7.1拉伸试验方法按照GB/T228.1的规定进行。拉伸试样的尺寸和加工质量应符合GB/T228.1的规定。
冲击试验方法按照GB/T229的规定进行。冲击试样的尺寸和加工质量应符合CB/T229的规定。
5.8齿轮磨削后表面回火(磨削烧伤)齿轮磨削后表面回火(磨前烧伤)检查按GB/T17879—1999的规定进行。5.9表面质量
外观采用目视检查或借助小于或等于3倍的放大镜进行检查。表面缺陷采用磁粉探伤方法,表面磁粉探伤方法按GB/T15822.1的规定进行。表面磁粉探伤应在齿轮轮齿磨齿后喷丸前进行。5.10内部质量
超声波检测按GB/T11259、JB/T10061和TB/T2047.3的规定进行。超声波检测应在开齿部位精车后切齿前进行。超声波检测应尽可能在两个相互垂直的方向上对齿轮坏料的所有截面实行扫查;对于盘形齿轮坏料,除至少从一个平面扫查外,还应尽可能从圆周面进行径向扫查;对于轴类齿轮坏料,除应从径向进行扫查外,还应从轴向进行辅助扫查。5.11硬
5.11.1非表面硬化部位硬度
非表面硬化部位硬度的检验按照GB/T230.1或GB/T17394或GB/T231.1的规定进行。8
小提示:此标准内容仅展示完整标准里的部分截取内容,若需要完整标准请到上方自行免费下载完整标准文档。

标准图片预览:
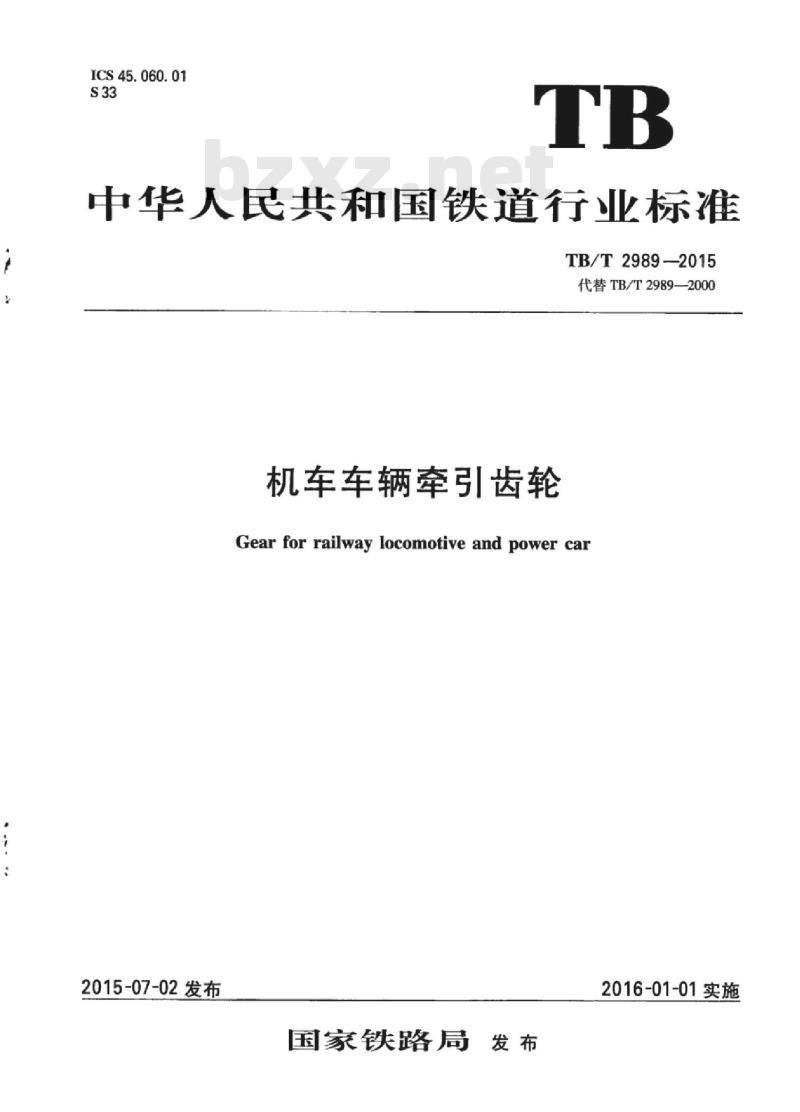
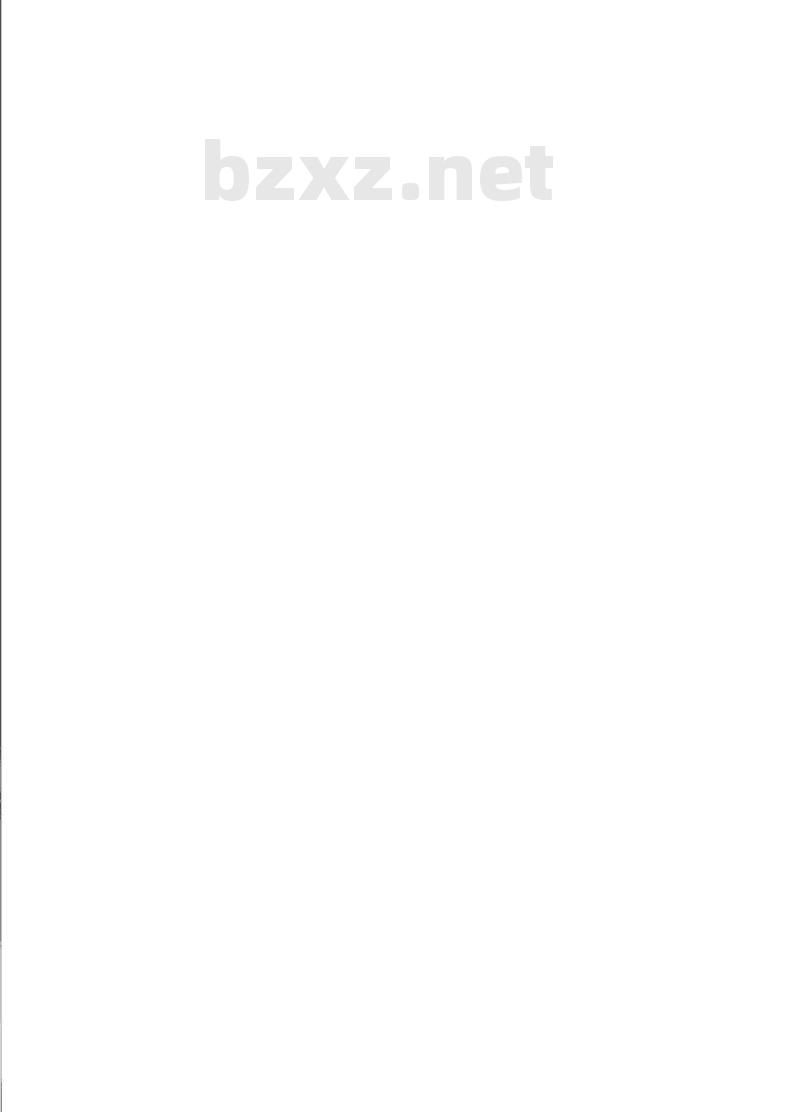
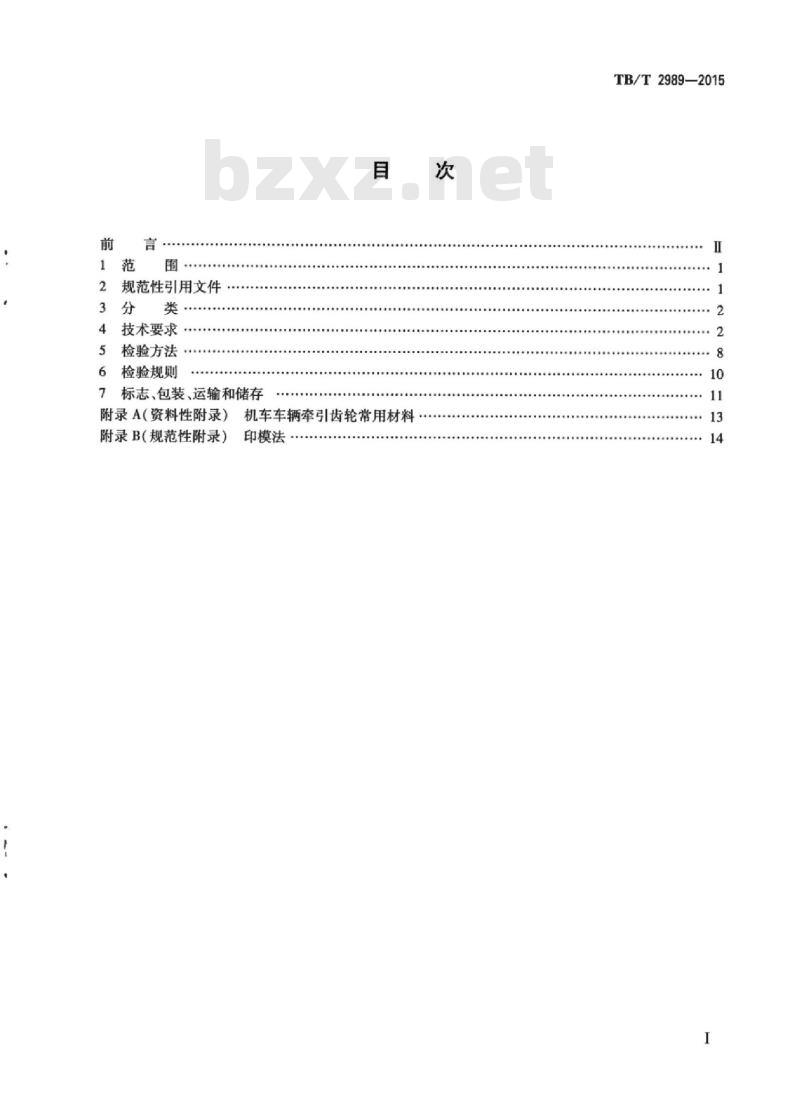
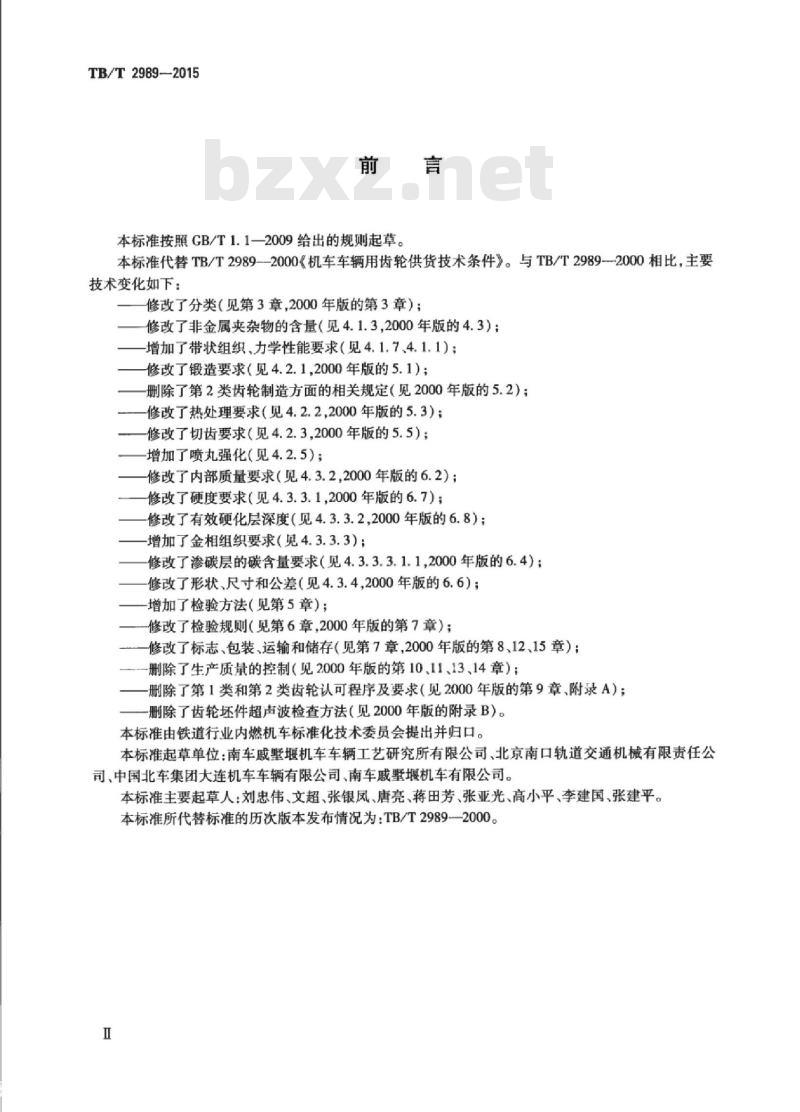
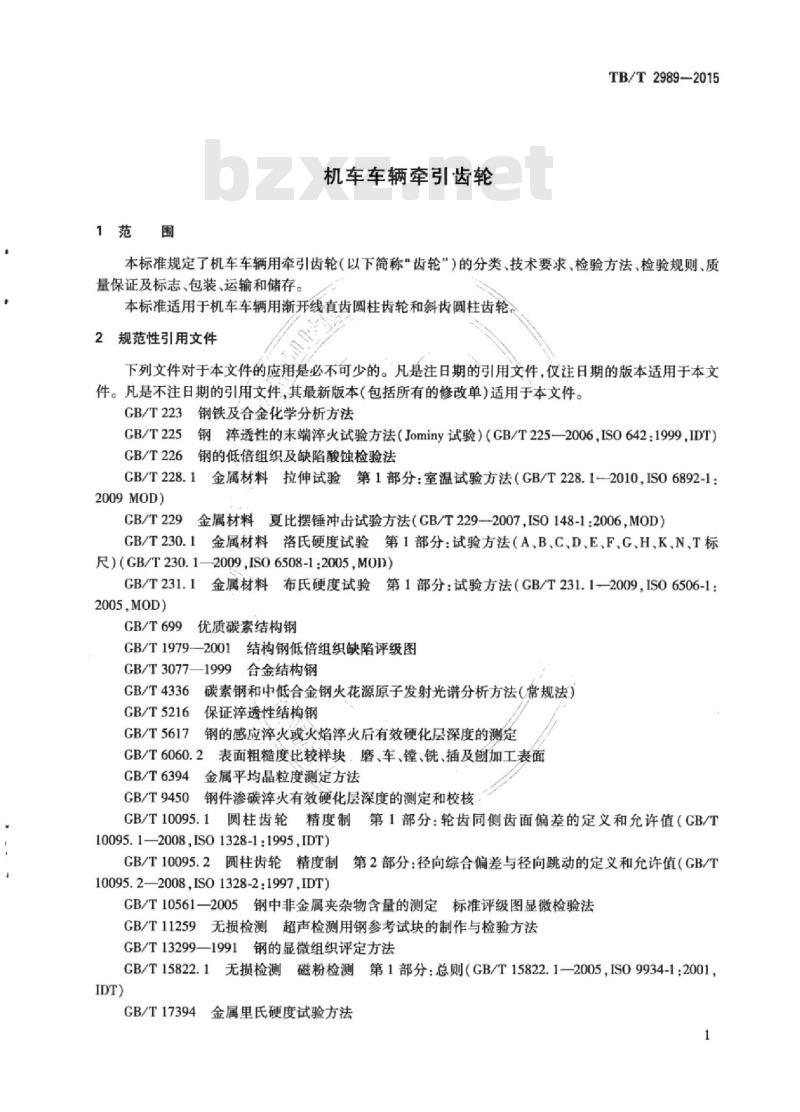
- 其它标准
- 上一篇: HG 3628-1999 氯氰菊酯乳油
- 下一篇: HG 3629-1999 高效氯氰菊酯原药
- 热门标准
- TB铁路运输标准
- TB/T3199.2-2018 电气化铁路接触网用绝缘子第2部分:棒形复合绝缘子
- TB/T2685.1-1995 铁路环境监测质量控制环境监测指标体系及体系表
- TB10038-2012 铁路工程特殊岩土勘察规程
- TB/T2152.27-1990 铁路工人技术标准 机务 接触网工
- TB/T122-2001 机车车辆产品图样及设计文件编号原则
- TB/T2342.4-1993 75kg/m钢轨用接头夹板型式尺寸
- TB/T1670.4-1985 15号车钩钩体上牵引台样板
- TB/T2152.36-1990 铁路工人技术标准 机务 油脂发放工
- TB1017-1982 蒸汽机车闸瓦托技术条件
- TB/T3103.16-2005 机车车辆用锥面卡套式管接头 第16部分:管锥直通管接头体
- TB/T2794-1997 超速停车装置试验台技术条件
- TB/T2835-1997 铁道重载列车用货车的基本要求
- TB/T2365-93 机车最大牵引|力、起动加速能力试验方法
- TB/T3246.6-2010 机车车辆及其零部件设计准则螺栓连接第6部分:连接尺寸
- TB/T3375-2018 铁路数字移动通信系统(GSM-R)机车综合无线通信设备
- 行业新闻
网站备案号:湘ICP备2023016450号-1