- 您的位置:
- 标准下载网 >>
- 标准分类 >>
- 铁路运输行业标准(TB) >>
- TB/T 2403-1993 货车高摩擦系数合成闸瓦
标准号:
TB/T 2403-1993
标准名称:
货车高摩擦系数合成闸瓦
标准类别:
铁路运输行业标准(TB)
标准状态:
现行-
发布日期:
1993-12-18 -
实施日期:
1994-07-01 出版语种:
简体中文下载格式:
.rar.pdf下载大小:
2.54 MB

点击下载
标准简介:
标准下载解压密码:www.bzxz.net
本标准规定了铁道货车用高摩擦系数合成闸瓦的技术要求、试验方法、检验规则和标志、包装、运输与贮存等要求。本标准适用于运输速度低于或等于120km/h的铁路货车用高摩擦系数合成闸瓦,以下简称(高摩合成闸瓦)。 TB/T 2403-1993 货车高摩擦系数合成闸瓦 TB/T2403-1993

部分标准内容:
中华人民共和国铁道行业标准
TB/T 2403 — 93
货车高摩擦系数合成闸瓦
1993 12 18发布
199407-01实施
中华人民共和国铁道部
中华人民共和国铁道行业标准
货车高摩擦系数合成闸瓦
1主题内容与适用范围
TB/T2403—93
本标准规定了铁道货车用高摩擦系数合成闸瓦的技术要求、试验方法、检验规则和标志、包装、运输与贮存等要求。
本标准适用于运行速度低于或等于120km/h的铁路货车用高摩擦系数合成闸瓦(以下简称高摔合成闸瓦)。
注,高率合成闸瓦为专用闸瓦,应使用专用钢背。高库合战闸瓦不得与通用闻瓦《中磷铸铁闸瓦、高磷铸铁闸瓦及低摩擦系数合成闸瓦》互换使用。
2引用标准
GB1033
GB1034
GB1041
GB1043
HG2-168
3技术要求
碳素结构钢
塑料密度试验方法
塑料吸水性试验方法
塑料压缩试验方法
塑料冲击试验方法
塑料布氏硬度试验方法
3.1型式与基本尺寸
3.1.1高合成闻瓦的型式与基本尺寸应符合图1规定。3.1.2高摩合成闸瓦应按本标准及经规定程序批准的图样和技术条件制造。3.1.3高摩合成闸瓦由钢背和闸瓦体粘结而成。闸瓦体由粘结剂、填料及其它辅助材料组成。钢背用4mm的钢板制造,其性能应符合GB700中的Q235-A的要求。3.1.4钢背用样板检查时,瓦鼻两侧与样板应至少有四点接触.局部间隙不得大于1.5mm,钢背两端圆弧面与样板的局部间隙不得大于2mm。3.2物理机械性能
高摩合成闻瓦的物理机械性能应符台表1的规定。3.3制动摩擦性能
3.3.1瞬时摩擦系数
常温干燥状态下的瞬时摩擦系数基准值按公式(1)计算:中华人民共和国铁道部1993-12-18批准1994--0701实施
157±075
注:1,重量~4kg
157±0.75
2.标记示例:货车高摩擦系数合或阐瓦TB/T 2403--93
高案合成闸瓦TB/T2403-93
A-A策转
图1高嗪合威阐瓦型式及基本尺寸表1物理机械性能
吸水率
吸油率
布氏硬度
冲击强度
压缩强度
弹性模量
式中:,瞬时摩擦系数;
V瞬时速度,km/h。
性能指标
不超过给定值的士5%
小于1.5
小于1.5
小于16
大于2.0
大于25
小于1.8×10元
2V+150
3V+150
3.3.1.1瞬时摩擦系数变化范围
157±0.75
检验标准
GB1033
GB1034
GB1034
HG2-168
GB1013
G131041
GB1041
常温干燥状态、一次停车制动、高闸瓦压力条件下的瞬时摩擦系数变化范围应符合表2的规定(参见附录图A1)。
基准值
α基准值
基准值
0.272 +0. 03
TB/T2403—93
表2瞬时摩擦系数变化范围
0.270 +0. 03
0.317±0.05
0.306±0.04
0.298±0.04
3.3.1.2常温干燥状态、一次停车制动、低闸瓦压力条件下的瞬时摩擦系数的上限值可比表2规定的上限值高10%,但下限值不得低于表2规定的下限值。3.3.2平均摩擦系数
3.3.2.1常温干燥状态下的平均摩擦系数基准值按公式(2)计算:0.175V3
0.75V--37.5V.+2812.5Ln
式中:双,
平均摩擦系数
V。初始速度,km/h。
3.3.2.2常温干燥状态、一次停车制动、高闸瓦压力条件下的平均摩擦系数的变化范围应符合表3的规定(参见附录图A2)。表3平均摩擦系数变化范围
Vekns/h
D,基准值
Vokm/h
必,基准值
0.317±0.04
0.292±0.03
0.310±0.04
0.288±0.03
3.3潮湿状态的瞬时摩擦系数
0.305±0.04
0.285±0.03
0.300±0.03
0.283±0.03
0.295±0.03
0.280±0.03
潮湿状态、一次停车制动、低闸瓦压力条件下的瞬时摩擦系数在各种初始速度下均不得低于0.21。
3.3.4坡道匀速连续制动条件下的摩擦系数坡道匀速连续制动条件下的摩擦系数在规定的制动时间内不得低于0.21。3.3.5静摩擦系数
静摩擦系数不得低于0.30。
3.3.6闸瓦的磨耗量
闸瓦的磨耗量不得超过1cm\/MJ。3.3.7车轮踏面的摩擦温度
TB/T2403--93
在1:1制动动力试验台上进行各种规定程序的试验时,车轮踏面温度均不得大于400℃。
3.4闸瓦体与钢背的粘结
闸瓦体与钢背之间的剪切强度不得小于0.6MPa。在所加载荷下,闸瓦体和钢背之间不得产生裂缝。
3.5外观及使用性能
3.5.1外观
3.5.1.1闻瓦体不得有裂纹、起泡、翘曲、分层和蔬松等缺陷。3.5.1.2钢背不得出现裂纹。钢背冲孔的撕裂尖角的位置不得损害闸瓦的横向强度。3.5.1.3钢背与闸瓦体之间不得有缝隙。3.5.2使用性能
3.5.2.1闸瓦体材料成分要均匀分布,且不得混进有害车轮及摩擦性能的杂质。3.5.2.2高摩合成闸瓦在其正常使用限度内,不得折断、掉块、脱落;钢背不得外露而与车轮踏面接触;闸瓦体摩擦表面材料不得产生局部脱落和凹陷。3.5.2.3对车轮踏面的磨耗
高摩合成闸瓦不得对车轮踏面产生异状磨耗或沟状磨耗。在相同运用条件下,高痒合成闸瓦对车轮踏面的正常磨耗量不应大于使用铸铁阐瓦时对同类车轮的正常磨耗量。3.5.2.4对车轮的热损伤
在相同运用条件下,高摩合成闻瓦不得比铸铁闸瓦对同类车轮产生更严重的热损伤(热斑、热裂纹和热剥离等)。
3.5.2.5金属镶嵌
在正常使用时,高摩合成闸瓦摩擦面不得形成导致车轮损伤、异状磨耗或影响制动摩擦性能的金属镶嵌。
3.5.2.6制动时不允许产生明显的火花和刺耳的噪声。3.5.2.7高摩合成闸瓦不得使轮轨粘着有明显的下降。4试验方法
4.1外观检查
目测。
4.2外形尺寸检查
用样板或精度0.05mm的游标卡尺测量闸瓦的外形尺寸。4.3物理机械性能试验
4.3.1试样制取
试样从闸瓦体上制取。取样位置的间隔应尽量大,但距离不得小于5mm。冲击强度试样沿闸瓦长度方向制取;压缩强度及弹性模量沿闸瓦厚度方向制取。4.3.2试验方法
4.3.2.1密度试验
按GB1033的规定进行。
4.3.2.2吸水性、吸油性试验
TB/T2403-93
按GB1034的规定进行。吸油性试验采用车轴油。4.3.2.3布氏硬度试验
布氏硬度试验方法按HG2-168的规定进行。在闸瓦体的任一侧面至少测试3点(上下两处各3点),取各点测试结果的平均值作为该闻瓦的硬度值。压痕间隔应尽量大,但压痕边缘与闸瓦边缘的距离不得小于10mm。4.3.2.4冲击强度试验
按GB1043的规定进行。试样不带缺口。4.3.2.5压缩强度试验和弹性模量试验按GB1041的规定进行。
4.3.2.6闸瓦体和钢背的粘结强度试验按图2所示的试验方法进行。达验载荐=0.6MP
南瓦体。
南瓦铜背
潮瓦饼
图2高障合成闸瓦闸瓦体与钢背粘结强度试验方法4.4制动摩擦性能试验
4.4.1基本原则
a.制动摩擦性能试验以1:1制动动力试验台为基准。定位部件
b.制动摩擦性能试验应在铁道部认可,并经国家技术监督局认证合格的1:1制动动力试验台上进行。
c.制动障擦性能试验的试验条件必须与闸瓦应用的车型条件一致。d。本标准按大型货车、单式制动条件制定。4.4.21:1制动动力试验台的基本条件和要求5
TB/T 2403-93
a,试验台用直径840mm的辊钢整体车轮,直径要测量准确。车轮踏面应保持光洁,消除对试验的影响。车轮与主轴应同心。b.试验台漠拟轴重不应超过实际轴重的10%。c.必须测定试验台加载装置的效率,计算纯闸瓦压力。d必须测定试验台在试验速度范围内的阻力(包括试验台的内阻和风阻)。e.试验台应有潮湿试验喷水装置,水量在踏面上均匀分布。4.4.3试验数据记录
4.4.3.1试验记录应有试验日期、试验室温度和湿度、车型、车重(或轴重)、轮径、制动方式等。
4.4.3.2试验时记录下列数据:
a.制动操作序号;
b.制动初始速度;
c.闸瓦压力;
d.实制动时间;
e.实制动距离;
f.车轮踏面初始温度;
g.制动过程车轮踏面最高温度:h.瞬时摩擦系数;
i.平均摩擦系数;
j.坡道连续制动过程的糜擦系数一时间曲线、车轮踏面温度一时间曲线或最高温度;k,静擦系数。
4.4.3.3记录试验过程中火花的程度,有无热红带,车轮踏面有无热斑或热斑的程度,噪声和烟尘状况,闸瓦摩擦表面状态一一有无裂纹、剥离凹陷、粘结剂渗出、金属镶嵌及其它缺陷,或这些缺陷的程度。
4.4.3.4在高闸瓦压力一次停车制动试验程序前和低闸瓦压力一次停车制动试验程序后,分别测量闸瓦的质量,然后根据已知的密度计算单位制动能量的体积磨耗。计算公式:
W_W,-we
单位制动能量的体积磨耗量,cm/MJ;式中:w-
W,—试前闻瓦重量·g;
W,试后闸瓦重量g;
β闸瓦体密度·g/cm;
A一试验过程总的制动功,MJ。
4.4.41:1制动动力试验台试验程序及方法4.4.4.1磨合试验
a.新闸瓦上机后,首先应进行磨合试验一一初始速度为80km/h.闸瓦压力为19.6kN.连续进行10次一次停车制动试验”(每次停车后不冷却车轮),称为一个制动循环,然后将车轮冷却到50C以下。
TB/T2403-93
b.如果有必要,再进行第二个制动循环,直到闸瓦和车轮踏面接触面积达到70%以上。c.为了节省磨合时间,可按试验车轮的直径旋削闸瓦摩擦表面,旋削深度5mm左右。旋削之后,再进行至少一个循环的磨合试验。4.4.4.2高闸瓦压力,一次停车制动试验a,试验前测定闸瓦的质量。wwW.bzxz.Net
b.闸瓦压力为19.6kN。
c.试验初始速度(km/h)的顺序为:95、75、55.35、35、55、75、95。此试验程序称为一个循环。
d.每闸试验开始前,车轮踏面温度应降至50C以下。e,本试验方法至少做一个循环。必要时可增加半个或一个循环。4.4.4.3低闸瓦压力、一次停车制动试验a.闸瓦压力为9.8kN。
b.试验方法同4.4.4.2中的c、d、e项。c.试验完毕,测定闸瓦的质量,然后计算闻瓦的磨耗量。4.4.4.4静摩擦系数试验
a.闸瓦压力为4.9kN。
b.对车轮施加转矩,测出车轮开始转动瞬间的摩擦系数即为静摩擦系数。c.试验重复5次,取试验结果的平均值,作为该闸瓦的静摩擦系数。4.4.4.5坡道匀速连续制动试验
a.闸瓦压力为4.9kN。
b,车轮线速度为40km/h。
c.匀速连续制动10min。
4.4.4.6潮湿加水试验
试验方法同4.4.4.3中的a、b项。制动过程中向车轮踏面均匀酒水,酒水量为14L/h5检验规则
5.1产品出厂前应由制造厂技术检查部门按本标准要求进行检查,合格后签发产品合格证。5.2外观检查
出厂的闻瓦应全部进行外观检查。5.3外形尺寸检查
5.3.1同材质、同规格的闸瓦,每1000块为一批,不足1000块的按一批计。5.3.2检验数量:每批不得少于5块。5.3.3若有一块闸瓦不合格,则应加倍复检;若仍有一块不合格,则应对该批闻瓦逐个进行检查。
5.4物理机械性能检验及闸瓦体和钢背的粘结强度试验5.4.1同材质、同规格的闸瓦,每1000块为一批,不足1000块的也按一批计。5.4.2检查数量:每批不得少于3块。5.4.3任何一项未达到本标准规定的要求时,都应在该批闸瓦中加倍抽样,对不合格项目进行复检,以复检结果为准。若复检结果仍不合格,则该批闸瓦为不合格品。7
5.5制动摩擦性能检验
TB/T2403-93
5.5.1不定期地进行1:1制动动力试验台制动摩擦性能试验(每年至少两次)。5.5.2检验数量:每批不得少于2块。5.5.3任何项末达到本标准规定的要求时,均应重复抽样,对不合格项目进行复检,以复检结果为准。若复检结果仍不合格、则该批阐瓦为不合格品。5.6产品出厂前应由制造厂技术检查部门按本标准要求进行检查,合格后签发产品合格证。5.7质量仲载
供需双方对某项试验结果有争议时,可针对该项进行仲裁试验,以仲裁试验结果为准。承担仲裁试验的单位应由铁道部组织供需双方协商确定。仲裁试验按本标准的规定进行依照本标准的有关规定对仲裁试验的结果进行评价、得出仲裁结论。5.8复查、拒收、退货、赔偿
5.8.1使用单位有权对产品进行复查。5.8.2使用单位对产品进行复查,确认产品不符合本标准规定的要求时,有权提出拒收或退货。
5.8.3高摩合成闸瓦在使用过程中,若确因其质量问题而造成行车事故,应由生产厂家承担事故责任,赔偿经济损失。
6标志、包装、运输与贮存
6.1闸瓦钢背表面须有闸瓦型号、制造厂代号、制造年月的永久标志(闸瓦使用到限时仍能识别)。
6.2闸瓦包装箱上应有闸瓦名称、型号、制造厂名、制造年月等标志,箱内须有检验合格证(含生产批号)。
6.3运输需用包装箱,装卸时严禁摔、扔,防止闸瓦破损和变形。6.4闸瓦应储存在通风、千燥处,防止日晒和雨淋。闸瓦储存期不宜过长。8
附加说明:
TB/T2403--93
附录A
高摩合成闸瓦摩擦系数
(参考件)
上限值
标准像
下限信
图A1高率合成闸瓦瞬时降擦系数标准值及其幅度变化范(常溢、干燥状态)0.45
远、上股值
标准值
多,下限值
0.353V+150
2V+150
V(km/b)
2V。+150
0.75V.-37.3V.+2812.5ln
图A?简率合成闸瓦瞬时障爆系数标准值及其幅度变化范围(常温、干燥状态)本标准由铁道部四方车辆研究所提出并归口。foo
本标准由铁道部科学研究院金属及化学研究所、机车车辆研究所起草。本标准主要起草人张玉心、汪志洋、鞠传珍、王京波、彭明翔。110
V(km/b)
小提示:此标准内容仅展示完整标准里的部分截取内容,若需要完整标准请到上方自行免费下载完整标准文档。
TB/T 2403 — 93
货车高摩擦系数合成闸瓦
1993 12 18发布
199407-01实施
中华人民共和国铁道部
中华人民共和国铁道行业标准
货车高摩擦系数合成闸瓦
1主题内容与适用范围
TB/T2403—93
本标准规定了铁道货车用高摩擦系数合成闸瓦的技术要求、试验方法、检验规则和标志、包装、运输与贮存等要求。
本标准适用于运行速度低于或等于120km/h的铁路货车用高摩擦系数合成闸瓦(以下简称高摔合成闸瓦)。
注,高率合成闸瓦为专用闸瓦,应使用专用钢背。高库合战闸瓦不得与通用闻瓦《中磷铸铁闸瓦、高磷铸铁闸瓦及低摩擦系数合成闸瓦》互换使用。
2引用标准
GB1033
GB1034
GB1041
GB1043
HG2-168
3技术要求
碳素结构钢
塑料密度试验方法
塑料吸水性试验方法
塑料压缩试验方法
塑料冲击试验方法
塑料布氏硬度试验方法
3.1型式与基本尺寸
3.1.1高合成闻瓦的型式与基本尺寸应符合图1规定。3.1.2高摩合成闸瓦应按本标准及经规定程序批准的图样和技术条件制造。3.1.3高摩合成闸瓦由钢背和闸瓦体粘结而成。闸瓦体由粘结剂、填料及其它辅助材料组成。钢背用4mm的钢板制造,其性能应符合GB700中的Q235-A的要求。3.1.4钢背用样板检查时,瓦鼻两侧与样板应至少有四点接触.局部间隙不得大于1.5mm,钢背两端圆弧面与样板的局部间隙不得大于2mm。3.2物理机械性能
高摩合成闻瓦的物理机械性能应符台表1的规定。3.3制动摩擦性能
3.3.1瞬时摩擦系数
常温干燥状态下的瞬时摩擦系数基准值按公式(1)计算:中华人民共和国铁道部1993-12-18批准1994--0701实施
157±075
注:1,重量~4kg
157±0.75
2.标记示例:货车高摩擦系数合或阐瓦TB/T 2403--93
高案合成闸瓦TB/T2403-93
A-A策转
图1高嗪合威阐瓦型式及基本尺寸表1物理机械性能
吸水率
吸油率
布氏硬度
冲击强度
压缩强度
弹性模量
式中:,瞬时摩擦系数;
V瞬时速度,km/h。
性能指标
不超过给定值的士5%
小于1.5
小于1.5
小于16
大于2.0
大于25
小于1.8×10元
2V+150
3V+150
3.3.1.1瞬时摩擦系数变化范围
157±0.75
检验标准
GB1033
GB1034
GB1034
HG2-168
GB1013
G131041
GB1041
常温干燥状态、一次停车制动、高闸瓦压力条件下的瞬时摩擦系数变化范围应符合表2的规定(参见附录图A1)。
基准值
α基准值
基准值
0.272 +0. 03
TB/T2403—93
表2瞬时摩擦系数变化范围
0.270 +0. 03
0.317±0.05
0.306±0.04
0.298±0.04
3.3.1.2常温干燥状态、一次停车制动、低闸瓦压力条件下的瞬时摩擦系数的上限值可比表2规定的上限值高10%,但下限值不得低于表2规定的下限值。3.3.2平均摩擦系数
3.3.2.1常温干燥状态下的平均摩擦系数基准值按公式(2)计算:0.175V3
0.75V--37.5V.+2812.5Ln
式中:双,
平均摩擦系数
V。初始速度,km/h。
3.3.2.2常温干燥状态、一次停车制动、高闸瓦压力条件下的平均摩擦系数的变化范围应符合表3的规定(参见附录图A2)。表3平均摩擦系数变化范围
Vekns/h
D,基准值
Vokm/h
必,基准值
0.317±0.04
0.292±0.03
0.310±0.04
0.288±0.03
3.3潮湿状态的瞬时摩擦系数
0.305±0.04
0.285±0.03
0.300±0.03
0.283±0.03
0.295±0.03
0.280±0.03
潮湿状态、一次停车制动、低闸瓦压力条件下的瞬时摩擦系数在各种初始速度下均不得低于0.21。
3.3.4坡道匀速连续制动条件下的摩擦系数坡道匀速连续制动条件下的摩擦系数在规定的制动时间内不得低于0.21。3.3.5静摩擦系数
静摩擦系数不得低于0.30。
3.3.6闸瓦的磨耗量
闸瓦的磨耗量不得超过1cm\/MJ。3.3.7车轮踏面的摩擦温度
TB/T2403--93
在1:1制动动力试验台上进行各种规定程序的试验时,车轮踏面温度均不得大于400℃。
3.4闸瓦体与钢背的粘结
闸瓦体与钢背之间的剪切强度不得小于0.6MPa。在所加载荷下,闸瓦体和钢背之间不得产生裂缝。
3.5外观及使用性能
3.5.1外观
3.5.1.1闻瓦体不得有裂纹、起泡、翘曲、分层和蔬松等缺陷。3.5.1.2钢背不得出现裂纹。钢背冲孔的撕裂尖角的位置不得损害闸瓦的横向强度。3.5.1.3钢背与闸瓦体之间不得有缝隙。3.5.2使用性能
3.5.2.1闸瓦体材料成分要均匀分布,且不得混进有害车轮及摩擦性能的杂质。3.5.2.2高摩合成闸瓦在其正常使用限度内,不得折断、掉块、脱落;钢背不得外露而与车轮踏面接触;闸瓦体摩擦表面材料不得产生局部脱落和凹陷。3.5.2.3对车轮踏面的磨耗
高摩合成闸瓦不得对车轮踏面产生异状磨耗或沟状磨耗。在相同运用条件下,高痒合成闸瓦对车轮踏面的正常磨耗量不应大于使用铸铁阐瓦时对同类车轮的正常磨耗量。3.5.2.4对车轮的热损伤
在相同运用条件下,高摩合成闻瓦不得比铸铁闸瓦对同类车轮产生更严重的热损伤(热斑、热裂纹和热剥离等)。
3.5.2.5金属镶嵌
在正常使用时,高摩合成闸瓦摩擦面不得形成导致车轮损伤、异状磨耗或影响制动摩擦性能的金属镶嵌。
3.5.2.6制动时不允许产生明显的火花和刺耳的噪声。3.5.2.7高摩合成闸瓦不得使轮轨粘着有明显的下降。4试验方法
4.1外观检查
目测。
4.2外形尺寸检查
用样板或精度0.05mm的游标卡尺测量闸瓦的外形尺寸。4.3物理机械性能试验
4.3.1试样制取
试样从闸瓦体上制取。取样位置的间隔应尽量大,但距离不得小于5mm。冲击强度试样沿闸瓦长度方向制取;压缩强度及弹性模量沿闸瓦厚度方向制取。4.3.2试验方法
4.3.2.1密度试验
按GB1033的规定进行。
4.3.2.2吸水性、吸油性试验
TB/T2403-93
按GB1034的规定进行。吸油性试验采用车轴油。4.3.2.3布氏硬度试验
布氏硬度试验方法按HG2-168的规定进行。在闸瓦体的任一侧面至少测试3点(上下两处各3点),取各点测试结果的平均值作为该闻瓦的硬度值。压痕间隔应尽量大,但压痕边缘与闸瓦边缘的距离不得小于10mm。4.3.2.4冲击强度试验
按GB1043的规定进行。试样不带缺口。4.3.2.5压缩强度试验和弹性模量试验按GB1041的规定进行。
4.3.2.6闸瓦体和钢背的粘结强度试验按图2所示的试验方法进行。达验载荐=0.6MP
南瓦体。
南瓦铜背
潮瓦饼
图2高障合成闸瓦闸瓦体与钢背粘结强度试验方法4.4制动摩擦性能试验
4.4.1基本原则
a.制动摩擦性能试验以1:1制动动力试验台为基准。定位部件
b.制动摩擦性能试验应在铁道部认可,并经国家技术监督局认证合格的1:1制动动力试验台上进行。
c.制动障擦性能试验的试验条件必须与闸瓦应用的车型条件一致。d。本标准按大型货车、单式制动条件制定。4.4.21:1制动动力试验台的基本条件和要求5
TB/T 2403-93
a,试验台用直径840mm的辊钢整体车轮,直径要测量准确。车轮踏面应保持光洁,消除对试验的影响。车轮与主轴应同心。b.试验台漠拟轴重不应超过实际轴重的10%。c.必须测定试验台加载装置的效率,计算纯闸瓦压力。d必须测定试验台在试验速度范围内的阻力(包括试验台的内阻和风阻)。e.试验台应有潮湿试验喷水装置,水量在踏面上均匀分布。4.4.3试验数据记录
4.4.3.1试验记录应有试验日期、试验室温度和湿度、车型、车重(或轴重)、轮径、制动方式等。
4.4.3.2试验时记录下列数据:
a.制动操作序号;
b.制动初始速度;
c.闸瓦压力;
d.实制动时间;
e.实制动距离;
f.车轮踏面初始温度;
g.制动过程车轮踏面最高温度:h.瞬时摩擦系数;
i.平均摩擦系数;
j.坡道连续制动过程的糜擦系数一时间曲线、车轮踏面温度一时间曲线或最高温度;k,静擦系数。
4.4.3.3记录试验过程中火花的程度,有无热红带,车轮踏面有无热斑或热斑的程度,噪声和烟尘状况,闸瓦摩擦表面状态一一有无裂纹、剥离凹陷、粘结剂渗出、金属镶嵌及其它缺陷,或这些缺陷的程度。
4.4.3.4在高闸瓦压力一次停车制动试验程序前和低闸瓦压力一次停车制动试验程序后,分别测量闸瓦的质量,然后根据已知的密度计算单位制动能量的体积磨耗。计算公式:
W_W,-we
单位制动能量的体积磨耗量,cm/MJ;式中:w-
W,—试前闻瓦重量·g;
W,试后闸瓦重量g;
β闸瓦体密度·g/cm;
A一试验过程总的制动功,MJ。
4.4.41:1制动动力试验台试验程序及方法4.4.4.1磨合试验
a.新闸瓦上机后,首先应进行磨合试验一一初始速度为80km/h.闸瓦压力为19.6kN.连续进行10次一次停车制动试验”(每次停车后不冷却车轮),称为一个制动循环,然后将车轮冷却到50C以下。
TB/T2403-93
b.如果有必要,再进行第二个制动循环,直到闸瓦和车轮踏面接触面积达到70%以上。c.为了节省磨合时间,可按试验车轮的直径旋削闸瓦摩擦表面,旋削深度5mm左右。旋削之后,再进行至少一个循环的磨合试验。4.4.4.2高闸瓦压力,一次停车制动试验a,试验前测定闸瓦的质量。wwW.bzxz.Net
b.闸瓦压力为19.6kN。
c.试验初始速度(km/h)的顺序为:95、75、55.35、35、55、75、95。此试验程序称为一个循环。
d.每闸试验开始前,车轮踏面温度应降至50C以下。e,本试验方法至少做一个循环。必要时可增加半个或一个循环。4.4.4.3低闸瓦压力、一次停车制动试验a.闸瓦压力为9.8kN。
b.试验方法同4.4.4.2中的c、d、e项。c.试验完毕,测定闸瓦的质量,然后计算闻瓦的磨耗量。4.4.4.4静摩擦系数试验
a.闸瓦压力为4.9kN。
b.对车轮施加转矩,测出车轮开始转动瞬间的摩擦系数即为静摩擦系数。c.试验重复5次,取试验结果的平均值,作为该闸瓦的静摩擦系数。4.4.4.5坡道匀速连续制动试验
a.闸瓦压力为4.9kN。
b,车轮线速度为40km/h。
c.匀速连续制动10min。
4.4.4.6潮湿加水试验
试验方法同4.4.4.3中的a、b项。制动过程中向车轮踏面均匀酒水,酒水量为14L/h5检验规则
5.1产品出厂前应由制造厂技术检查部门按本标准要求进行检查,合格后签发产品合格证。5.2外观检查
出厂的闻瓦应全部进行外观检查。5.3外形尺寸检查
5.3.1同材质、同规格的闸瓦,每1000块为一批,不足1000块的按一批计。5.3.2检验数量:每批不得少于5块。5.3.3若有一块闸瓦不合格,则应加倍复检;若仍有一块不合格,则应对该批闻瓦逐个进行检查。
5.4物理机械性能检验及闸瓦体和钢背的粘结强度试验5.4.1同材质、同规格的闸瓦,每1000块为一批,不足1000块的也按一批计。5.4.2检查数量:每批不得少于3块。5.4.3任何一项未达到本标准规定的要求时,都应在该批闸瓦中加倍抽样,对不合格项目进行复检,以复检结果为准。若复检结果仍不合格,则该批闸瓦为不合格品。7
5.5制动摩擦性能检验
TB/T2403-93
5.5.1不定期地进行1:1制动动力试验台制动摩擦性能试验(每年至少两次)。5.5.2检验数量:每批不得少于2块。5.5.3任何项末达到本标准规定的要求时,均应重复抽样,对不合格项目进行复检,以复检结果为准。若复检结果仍不合格、则该批阐瓦为不合格品。5.6产品出厂前应由制造厂技术检查部门按本标准要求进行检查,合格后签发产品合格证。5.7质量仲载
供需双方对某项试验结果有争议时,可针对该项进行仲裁试验,以仲裁试验结果为准。承担仲裁试验的单位应由铁道部组织供需双方协商确定。仲裁试验按本标准的规定进行依照本标准的有关规定对仲裁试验的结果进行评价、得出仲裁结论。5.8复查、拒收、退货、赔偿
5.8.1使用单位有权对产品进行复查。5.8.2使用单位对产品进行复查,确认产品不符合本标准规定的要求时,有权提出拒收或退货。
5.8.3高摩合成闸瓦在使用过程中,若确因其质量问题而造成行车事故,应由生产厂家承担事故责任,赔偿经济损失。
6标志、包装、运输与贮存
6.1闸瓦钢背表面须有闸瓦型号、制造厂代号、制造年月的永久标志(闸瓦使用到限时仍能识别)。
6.2闸瓦包装箱上应有闸瓦名称、型号、制造厂名、制造年月等标志,箱内须有检验合格证(含生产批号)。
6.3运输需用包装箱,装卸时严禁摔、扔,防止闸瓦破损和变形。6.4闸瓦应储存在通风、千燥处,防止日晒和雨淋。闸瓦储存期不宜过长。8
附加说明:
TB/T2403--93
附录A
高摩合成闸瓦摩擦系数
(参考件)
上限值
标准像
下限信
图A1高率合成闸瓦瞬时降擦系数标准值及其幅度变化范(常溢、干燥状态)0.45
远、上股值
标准值
多,下限值
0.353V+150
2V+150
V(km/b)
2V。+150
0.75V.-37.3V.+2812.5ln
图A?简率合成闸瓦瞬时障爆系数标准值及其幅度变化范围(常温、干燥状态)本标准由铁道部四方车辆研究所提出并归口。foo
本标准由铁道部科学研究院金属及化学研究所、机车车辆研究所起草。本标准主要起草人张玉心、汪志洋、鞠传珍、王京波、彭明翔。110
V(km/b)
小提示:此标准内容仅展示完整标准里的部分截取内容,若需要完整标准请到上方自行免费下载完整标准文档。

标准图片预览:
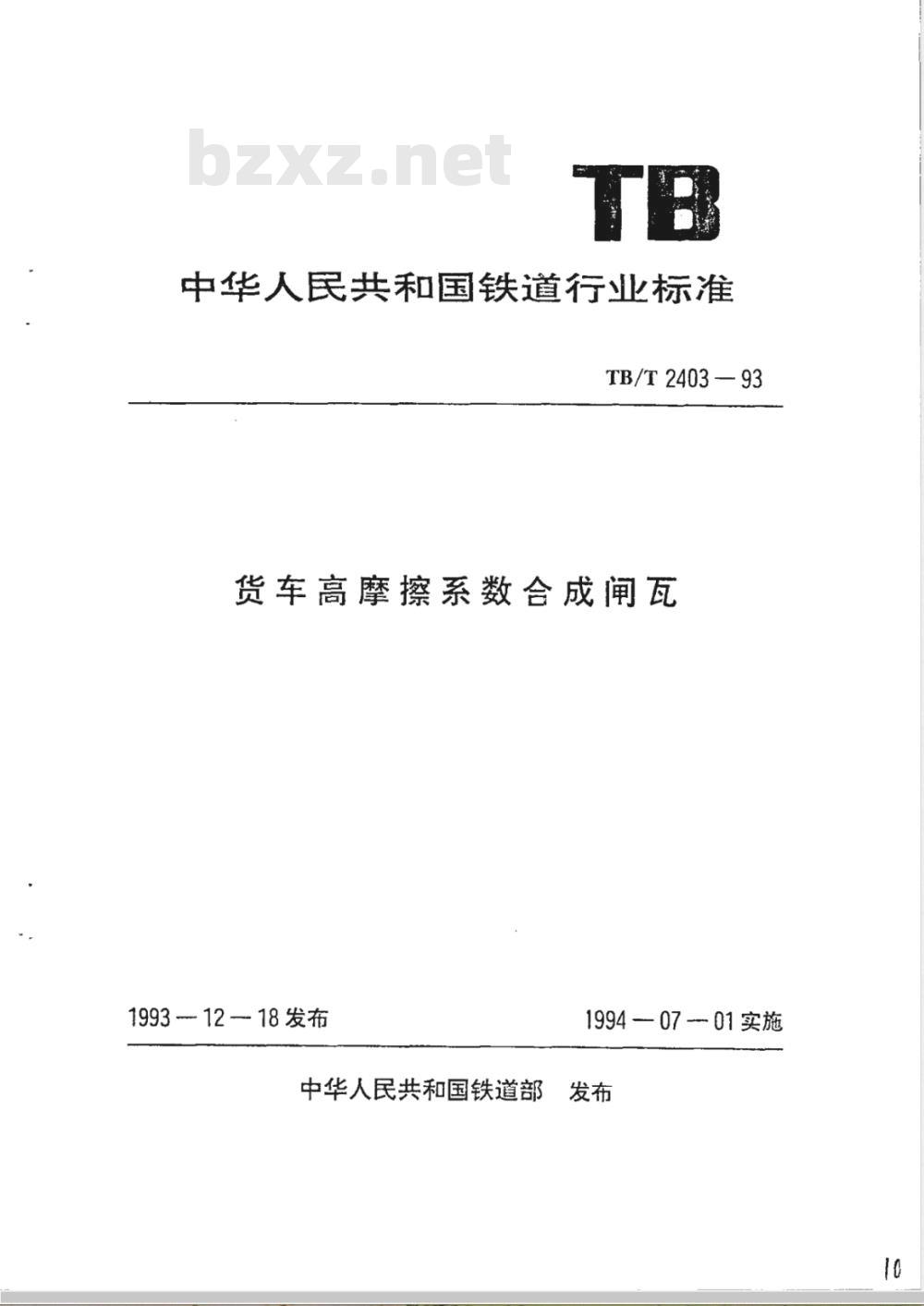
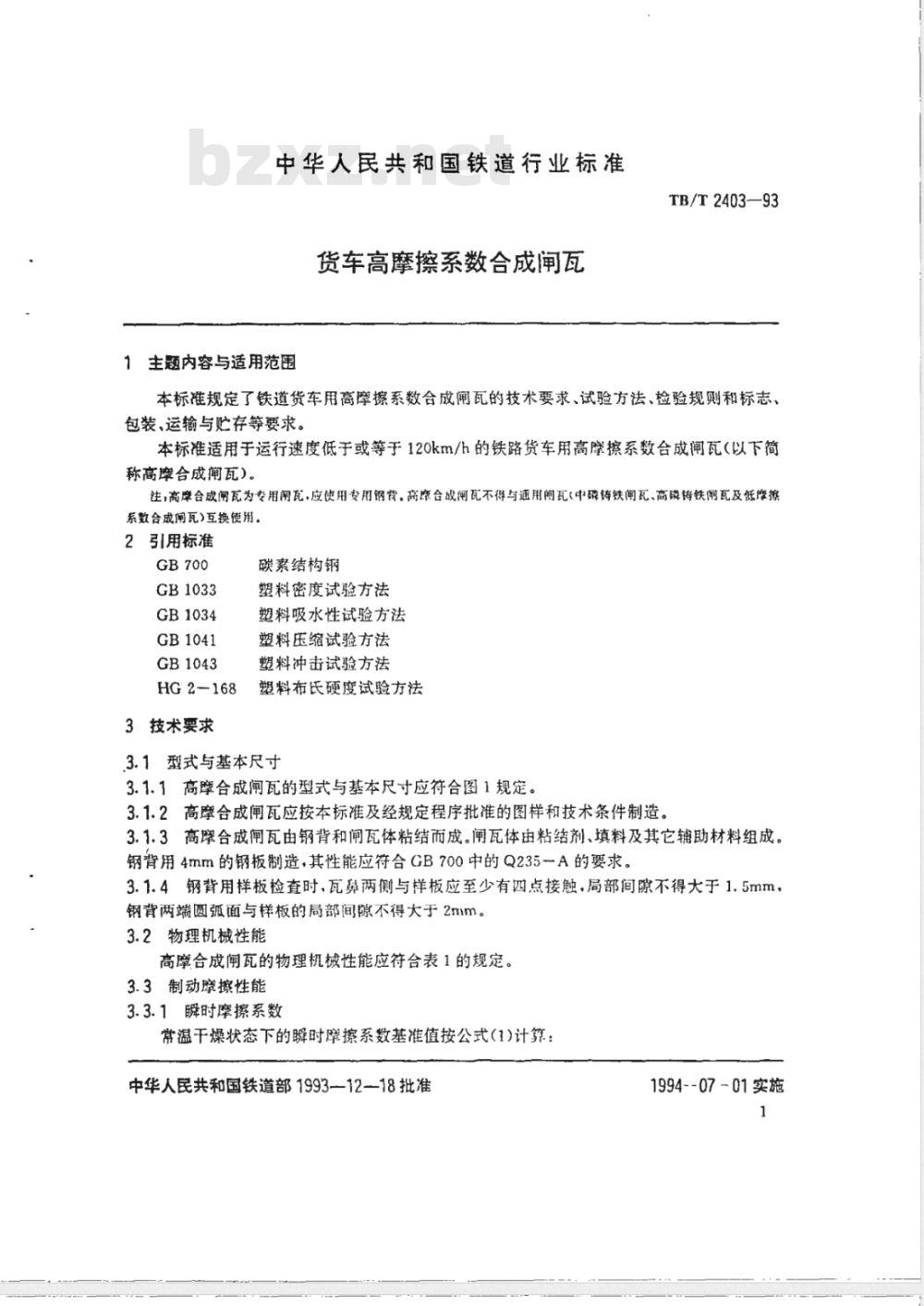
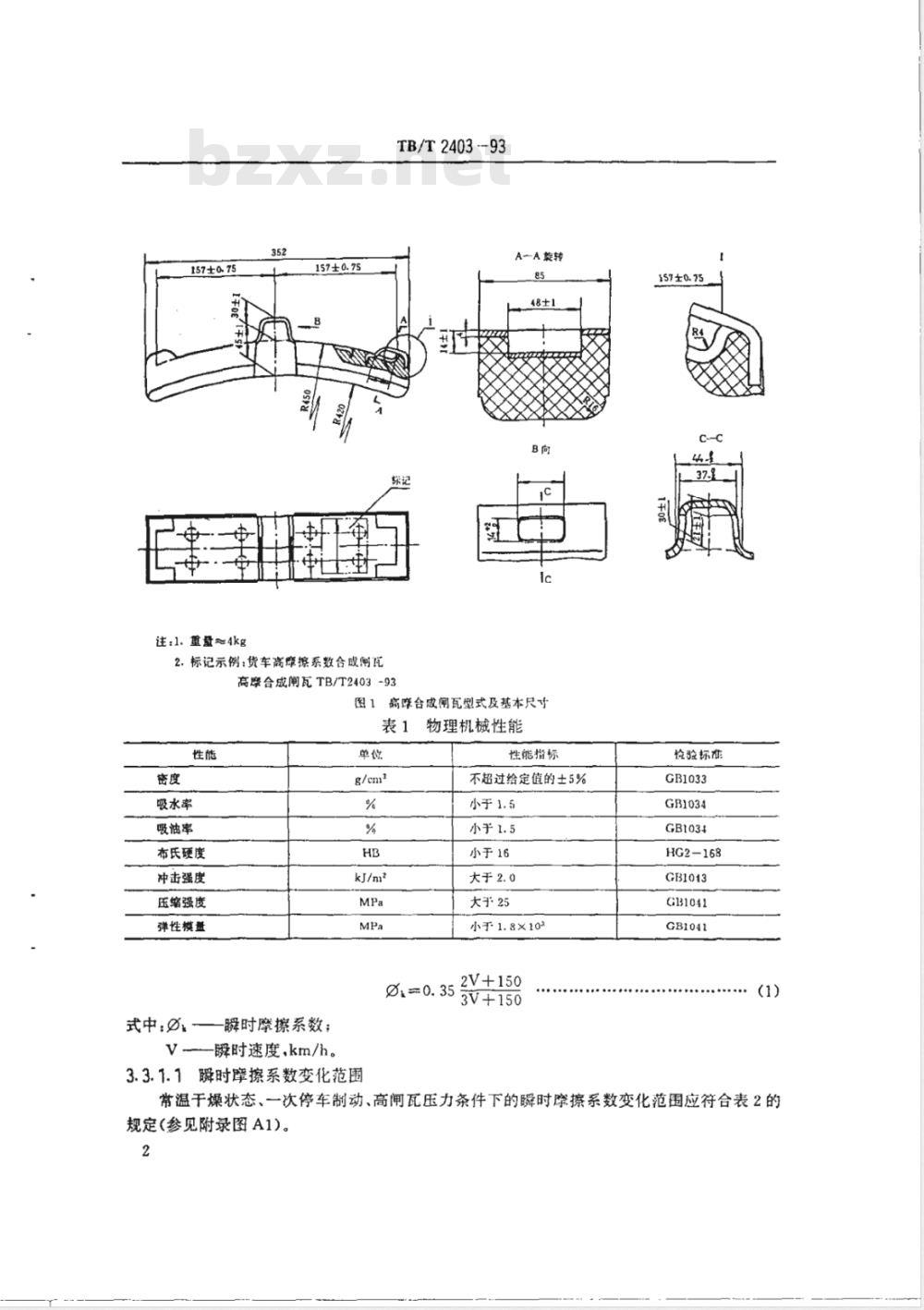
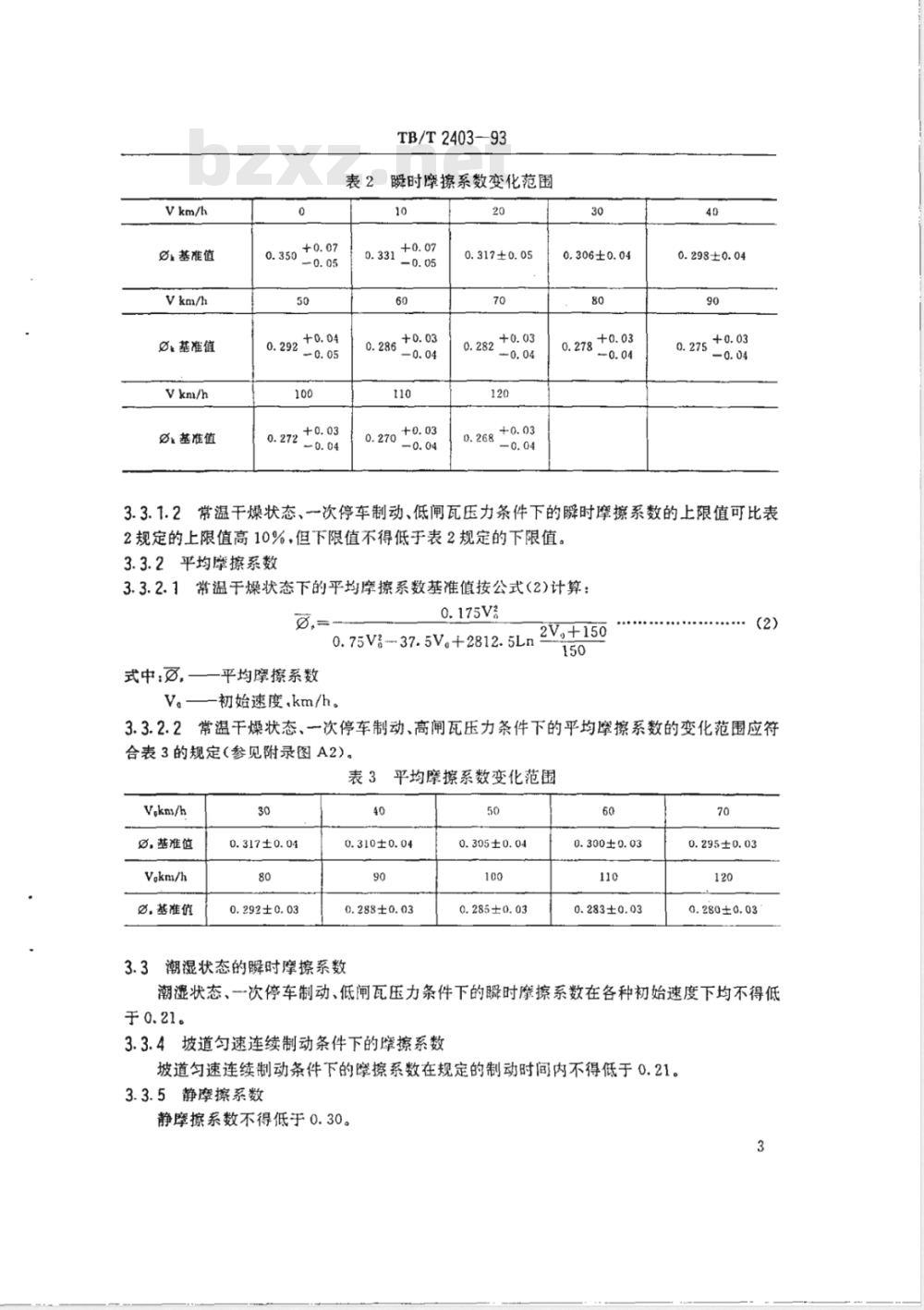
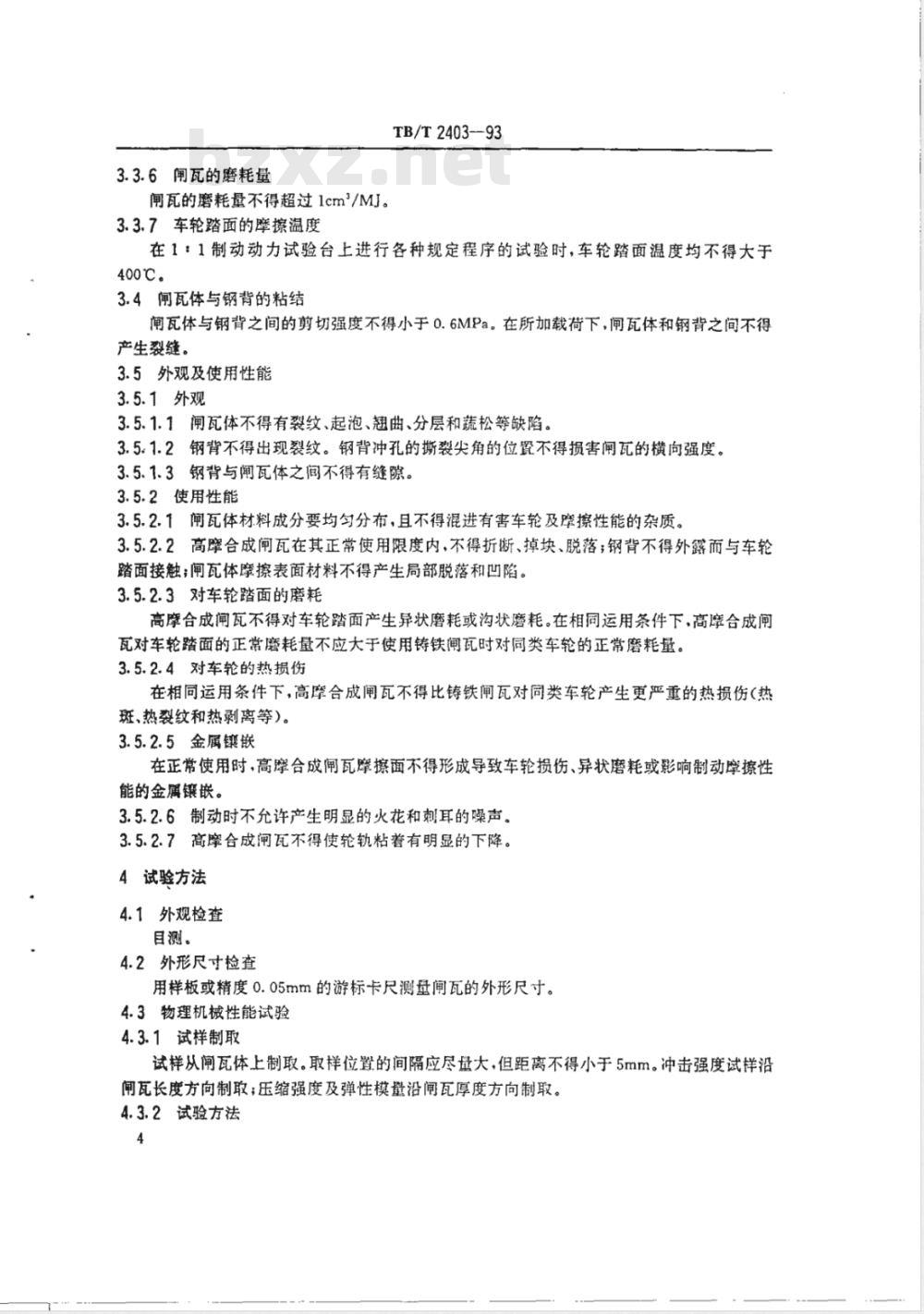
- 其它标准
- 热门标准
- 铁路运输行业标准(TB)
- TB/T3391-2015 机车车辆隔离变压器
- TB/T3263-2011 动车组乘客座椅
- TB/T2152.27-1990 铁路工人技术标准 机务 接触网工
- TB/T2365-93 机车最大牵引|力、起动加速能力试验方法
- TB10421-2018 铁路电力牵引供电工程施工质量验收标准
- TB/T2685.1-1995 铁路环境监测质量控制环境监测指标体系及体系表
- TB/T2993.5-2016 铁路通信电源第5部分:交流配电设备
- TB/T3416.3-2015 动车组编码标识系统第3部分:安装地点与位置的标识
- TB/T1824-1987 蒸汽机车铸钢轮心技术条件
- TB/T2262-1991 上游型蒸汽机车
- TB/T2152.28-1990 铁路工人技术标准 机务 继电保护工
- TB/T2152.29-1990 铁路工人技术标准 机务 高压试验工
- TB/T3032.6-2002 D08-32型自动整平捣固车技术条件 制动系统
- TB/T2353-2018 铁路信号灯光发光强度
- TB/T2794-1997 超速停车装置试验台技术条件
- 行业新闻
请牢记:“bzxz.net”即是“标准下载”四个汉字汉语拼音首字母与国际顶级域名“.net”的组合。 ©2009 标准下载网 www.bzxz.net 本站邮件:bzxznet@163.com
网站备案号:湘ICP备2023016450号-1
网站备案号:湘ICP备2023016450号-1