- 您的位置:
- 标准下载网 >>
- 标准分类 >>
- 铁路运输行业标准(TB) >>
- TB/T 1718.3-2018 机车车辆轮对组装第3部分:动车组
标准号:
TB/T 1718.3-2018
标准名称:
机车车辆轮对组装第3部分:动车组
标准类别:
铁路运输行业标准(TB)
标准状态:
现行出版语种:
简体中文下载格式:
.zip .pdf下载大小:
2.90 MB

点击下载
标准简介:
TB/T 1718.3-2018.Wheelsets assembly for locomotive and rolling stock-Part 3: EMU/DMU.
1范围
TB/T 1718.3规定了动车组轮对组装零部件的技术要求,轮对组装的技术要求,检验方法和检验规则,标志、防腐与防护。
TB/T 1718.3适用于动车组新制轮对的压装和注油压装。
2规范性引用文件
下列文件对于本文件的应用是必不可少的。凡是注日期的引用文件,仅注日期的版本适用于本文件。凡是不注日期的引用文件,其最新版本(包括所有的修改单)适用于本文件。
TB/T 1027.2-2015机车车轴 第2 部分:车轴
TB/T 2980机车 车辆用制动盘
3组装零部件的技术要求
3.1总则
车轴、车轮、制动盘应符合按规定程序审批的产品图样的要求。
3.2车轴
3.2.1轮座(盘座)的终加工宜采用磨削工艺。圆柱度公差为0. 015 mm,大端应在轮座内侧。待组装表面粗糙度Ra.上限值为1.6 μm,下限值为0.8 μm。
3.2.2轮座(盘座)部应有一个圆锥形引人段,引人段与轮座(盘座)装配面过渡部分应圆滑。
3.3车轮
3.3.1车轮 的轮毂孔在加工成品后,表面粗糙度Ra上限值为3.2 μm,下限值为0.8 μm;圆柱度公差为0.02mm,大端应在轮毂孔内侧。
3.3.2车轮轮毂孔中的油槽与毂孔过渡部分应圆滑,不应有锐棱尖角,轮毂孔压装引人段的倒圆角应圆滑过渡。
3.4 制动盘
制动盘应符合TB/T 2980的要求。
制动盘油槽与盘毂孔过渡部分应圆滑,不应有锐棱尖角,制动盘毂孔压装引人段的倒圆角应圆滑过渡。

部分标准内容:
中华人民共和国铁道行业标准
TB/T1718.3—2018
机车车辆轮对组装
第3部分:动车组
Wheelsets assembly for locomotive and rolling stock-Part 3:EMU/DMU
2018-07-16发布
国家铁路局
2019-02-01实施
规范性引用文件
组装零部件的技术要求
3.1总则
3.2车轴
3.3车轮
3.4制动盘
4轮对组装的技术要求
4.1基本要求
4.2车轮与车轴的压装
4.3车轮与车轴的注油压装
4.4成品轮对特性
5检验方法和检验规则
6标志、防腐与防护
附录A(规范性附录)轮对压装压装力曲线及说明附录B(规范性附录)
轮对注油压装压装力曲线及说明TB/T1718.3—2018
TB/T1718《机车车辆轮对组装》分为三个部分:—第1部分:机车(TB/T1463—2015):一第2部分:车辆;
一第3部分:动车组。
本部分为TB/T1718的第3部分。
本部分按照GB/T1.1—2009给出的规则起草。本部分由中车戚墅堰机车车辆工艺研究所有限公司提出并归口。TB/T1718.3—2018
本部分起草单位:中车青岛四方机车车辆股份有限公司、中车长春轨道客车股份有限公司、中车戚墅堰机车车辆工艺研究所有限公司、中国铁道科学研究院集团有限公司标准计量研究所、中车青岛四方车辆研究所有限公司、智奇铁路设备有限公司。本部分主要起草人:张峰、朱崇飞、徐世东、蒋田芳、高俊莉、徐芳、刁克军、袁博、王锐、马作为。H
1范围
机车车辆轮对组装
第3部分:动车组
TB/T1718.3-2018
TB/T1718的本部分规定了动车组轮对组装零部件的技术要求,轮对组装的技术要求,检验方法和检验规则标志、防腐与防护。
本部分适用于动车组新制轮对的压装和注油压装。2规范性引用文件
下列文件对于本文件的应用是必不可少的。凡是注日期的引用文件,仅注日期的版本适用于本文件。凡是不注日期的引用文件,其最新版本(包括所有的修改单)适用于本文件。TB/T1027.2-2015机车车轴第2部分:车轴TB/T2980机车车辆用制动盘
3组装零部件的技术要求
3.1总则
车轴、车轮、制动盘应符合按规定程序审批的产品图样的要求。3.2车轴
3.2.1轮座(盘座)的终加工宜采用磨削工艺。圆柱度公差为0.015mm,大端应在轮座内侧。待组装表面粗糙度Ra上限值为1.6μm,下限值为0.8μm。3.2.2轮座(盘座)部应有一个圆锥形引人段,引人段与轮座(盘座)装配面过渡部分应圆滑。3.3车轮
3.3.1车轮的轮毂孔在加工成品后,表面粗糙度Ra上限值为3.2μm,下限值为0.8μm;圆柱度公差为0.02mm,大端应在轮毂孔内侧。3.3.2车轮轮毂孔中的油槽与毂孔过渡部分应圆滑,不应有锐棱尖角,轮毂孔压装引人段的倒圆角应圆滑过渡。
3.4制动盘
制动盘应符合TB/T2980的要求。制动盘油槽与盘毂孔过渡部分应圆滑,不应有锐棱尖角,制动盘毂孔压装引人段的倒圆角应圆滑过渡。
4轮对组装的技术要求
4.1基本要求
4.1.1同一车轴上应组装同型号、同材质、同厂家生产的车轮及同型号、同材质、同厂家生产的制动盘。
4.1.2同一车轴上组装的两个车轮轮辆宽度差不应大于2mm。4.1.3同一车轴上车轮和制动盘的静不平衡位置应符合下列方法中的一种规定:两车轮残余静不平衡位置相位差为180°±5°,制动盘残余静不平衡位置相位差为180°±5°,同a)
TB/T1718.3-2018
侧车轮与制动盘残余不平衡相位差为180°±5°,制动盘静不平衡位置与车轮静不平衡位置应位于通过车轴中心线的同一平面。b)两车轮的残余静不平衡位置应位于通过车轴中心线的同一平面,且在车轴中心线的同一侧。制动盘残余静不平衡位置应与车轮残余静不平衡位置位于通过车轴中心线的同一平面。制动盘与车轮的残余静不平衡位置应分别位于车轴中心线的两侧。4.1.4车轴、车轮(制动盘)及量具宜在相同环境温度下同温8h后进行测量和组装。4.1.5轮对组装采用的压力机应配有压力一位移曲线的自动记录系统。压力一位移曲线中表示位移的横坐标长度不应小于压装长度实际值的1/2。纵坐标应能达到25kN的读数精度。压力传感器的精确度应达到10kN。
4.1.6轮座与轮毂孔应采取过盈配合,如无特殊规定,过盈量s应符合公式(1)的要求。0.0010d≤s≤0.0015d.+0.06
式中:
s一过盈量,单位为毫米(mm):d—车轴轮座直径的名义值,单位为毫米(mm)。.·++··.+++(1)
4.1.7组装前,轮座(盘座)表面、轮毂孔(盘毂孔)内径面应清洁,均勾涂抹二硫化钼或其他规定的压装介质。
4.1.8组装时,车轴纵向中心线与压力机活塞中心线一致,并平行压入,压装速度宜为0.5mm/s~5mm/s
4.1.9制动盘毂孔与盘座的压装过盈量及压装力应符合产品图样的要求。制动盘压装压力曲线和过盈量记录应保存。
4.1.10每个车轮(制动盘)压力曲线图上应填写:轴号、车轮号(制动盘号)、轮毂孔(盘毂孔)直径、轮座(盘座)直径、最大压装力、最终压装力、压装年月日。车轮压力曲线和过盈量记录应保存。4.2车轮与车轴的压装
4.2.1车轮与车轴压装的最终压装力F。应符合公式(2)的要求。3.4×d
F—最终压装力的数值,单位为千牛(kN)。4.2.2车轮与车轴的压装力曲线及说明见附录A。+(2)
4.2.3轮对压装后,如压装力曲线、压装尺寸不合格,应注油退卸,注油压力应符合技术文件要求。不应将退下的原车轮与原车轴原位压装,在原车轴,车轮表面无损伤的情况下,可重新选配其他车轮,车轴进行压装。分解后有损伤的车轮、车轴,清除缺陷符合新造要求后方可使用。4.3车轮与车轴的注油压装
4.3.1车轮与车轴注油压装最大压装力按车轴轮座直径的名义值计算,每100mm的压装力应符合表1的规定。
表1每100mm的压装力
动车车轮
拖车车轮
4.3.2车轮与车轴的压装力曲线及说明见附录B。压装力
单位为千牛下载标准就来标准下载网
4.3.3轮对注油压装时,注油油压应在110MPa~180MPa范围内,油压在规定范围内可波动。注油2
TB/T1718.3-2018
压装过程中,压力机中途可停顿。注油压装后,不限停顿时间,在注油状态下可自由调整内侧距和相位角,调整时注油油压应在110MPa~180MPa范围内。4.3.4轮对注油压装后如压力曲线不合格.应注油退卸.注油压力应符合技术文件要求。退卸后原车轴、车轮在表面无损伤的情况下,可再次选配组装。分解后有损伤的车轮、车轴,清除缺陷符合新造要求后方可使用。
4.4成品轮对特性
4.4.1尺寸
轮对组装后尺寸应符合表2的规定。轮对尺寸检测示意见图1。表2轮对尺寸参数
同一轮对两车轮滚动圆直径差
轮位差
盘摩擦面与轴肩距离公差”
盘位差
轮对内侧距。
盘内侧面间距公差
车轮踏面径向跳动
车轮内侧面跳动。
制动盘摩擦面跳动
适用于一个或三个制动盘的轮对。适用于两个制动盘的轮对。
在轮缘项部以下60mm处测量。
f或或f
a)组装单个制动盘的轮对
图1轮对尺寸检测示意
单位为毫米
TB/T1718.3—2018
4.4.2轮对动不平衡
b)组装两个制动盘的轮对
c)组装三个制动盘的轮对
图1轮对尺寸检测示意(续)
4.4.2.1轮对组装后的动不平衡应符合表3的规定。表3轮对的最大动不平衡值
120200
轮对的最大动不平衡值
4.4.2.2压装轮对的动不平衡值超限时,应在轮辋内侧去重调整,去重部位最大深度不应大于4mm(从新造尺寸开始计算,如需在轮辋外侧去重调整,去重部位最大深度应符合设计规定),去重表面应圆滑过渡到相邻表面。注油压装轮对的动不平衡值超限时,可在注油状态下调整车轮或制动盘相位,调4
整时注油油压应在110MPa~180MPa范围内。4.4.3电阻
TB/T1718.3-2018
轮对应在绝缘状态下,测量两个车轮踏面间的电阻值,电阻值不应大于0.01Q。4.4.4压力试验
4.4.4.1压装轮对
车轮与车轴压装48h后,应进行压力试验,轮对应能经得住30s的轴向力F。当装配长度符合公式(3)时,试验压力F见公式(4)。0.8d.
L一装配长度的数值,单位为毫米(mm);F一压力试验的轴向力的数值,单位为千牛(kN)。4.4.4.2注油压装轮对
***(3
车轮与车轴注油压装或注油调整至少2h后方可进行压力试验,轮对应能经得住不小于5s的试验压力。试验压力按车轴轮座直径的名义值计算,每100mm的试验压力应符合表4的规定。表4每100mm的试验压力
动车车轮
拖车车轮
4.4.5轮座疲劳特性
试验压力
单位为千牛
对于不同车轴材料的轮对,其轮座疲劳极限值应符合相关技术文件。在疲劳极限下,经10°次循环下,不应产生裂纹。
受车轴内孔对应力分布影响,实心轴和空心轴疲劳特性有所不同。对于实心轴,轮座疲劳极限为F3。对于空心轴,轮座疲劳极限为F4。注:当车轴轴颈直径与轴孔直径比大于3或轮座直径与轴孔直径比大于4时,可按照实心车轴评估。5检验方法和检验规则
5.1轮对动不平衡检测在轮对动平衡设备上进行。检测时,将轮对两侧轴颈放置在轮对动平衡设备的水平支撑面上,均速旋转轮对,旋转速度不应低于235r/min。在车轮平面内测量轮对的最大动不平衡值。
5.2轮对需在绝缘状态下进行检验,用轮对电阻检测仪测量轮对两踏面间的电阻。5.3轮对组装后应在压力机或专用设备上进行压力试验。压力试验时压力应逐渐平稳地增加到规定数值,压力作用在车轮轮毂处,并保压一定时间,车轮不应在车轴上产生任何位移,并记录压力试验曲线。
5.4对于轮对的疲劳试验,应当把一个车轮或具有相同尺寸(特别是轮毂处尺寸)的试件压装或者注油压装到轮座上,过盈量应当满足4.1.6的要求。试件产生裂纹的区域应当与被考察车轴具有相同的几何、环境和表面条件。轮对疲劳特性试验应在能产生周期性弯曲应力的试验装置上进行,试验装置应符合TB/T1027.2一2015中附录B的规定。对于各极限值,F、F。应在3个试样上进行验证。通过梁理论进行换算,使轮座上的应力(不考虑装配应力)达到技术文件规定的疲劳极限。5.5轮对组装前及组装过程中应按第3章和4.1~4.3的规定进行逐件检查。5.6轮对组装后应按4.4.1、4.4.2和4.4.3的规定进行逐件检查。5.7轮对组装后,注油压装的轮对逐件进行压力试验;首次压装的轮对,制造厂家应对至少前10条轮5
TB/T1718.3—2018
对均进行压力试验,若压力试验均合格,后续可按照5%比例进行抽检5.8轮对疲劳特性试验仅在新产品研制或首次生产时进行。5.9各项检验中,任何一项不符合规定要求时,均为不合格品。标志、防腐与防护
6.1标志
轮对组装后,轮对至少应当有以下标志:a)轮对组装厂家代码:
b)轮对型号;
c)轮对顺序号;
d)轮对组装年,月。
新造轮对的组装标志刻打在车轴的制造标记端,标志字符高5mm,并应保留到车轴报废为止。标志刻打采用冷打印方式,深度不超过0.5mm,钢印不应有尖锐边缘,字迹应清晰可见。6.2防腐
车轮轮毂(制动盘盘毂)位于车轴轮座(盘座)上的凸悬缝隙处应用防腐产品保护或填充。车轮、制动盘上的注油孔内应采取防锈措施,并安装防松油堵。空心车轴轮对内孔应采取防锈措施。轮对应进行防腐处理,避免锈蚀、雨淋、水浸。6.3防护
轮对生产、装卸和运输过程中应采取有效防止机械损伤或损坏的措施,轴颈等配合面应使用有效的防护措施,确保不发生碰伤。在吊运过程中,不应使用磁性吊具进行吊装。6
A.1轮对压装压装力曲线特性
附录A
(规范性附录)
轮对压装压装力曲线及说明
车轮和车轴的压装曲线特性见图A.1。TB/T1718.3—2018
在图A.1中,AB、BC、HE和ED是直线的一部分,AG等于轮座的长度。对于车轮,各点的位置如下:
Yh=1.3d.iyc=3.4dmyp=yg=5.8dmos
说明:
一距离,单位为毫米(mm);
一压装力,单位为千牛(kN)。≤25
图A.1车轮和车轴的压装曲线特性A.2轮对压装压装力曲线说明
图A.1中描述了车轮和车轴的压装曲线特性。压装力应当在轮毂相对于轮座的位移达到30mm之前开始增加,然后该压装力应当持续增加,压装曲线应在图A.1规定的ABCDEH曲线范围内。但可出现以下情况:
注油槽处压装力减小。但在此后25mm移动位移范围内,压装力应当恢复至到达油槽之前的最大值。在压装力减小的过程中,压装力的值可超出图A.1中曲线规定的下限。在最后的25mm位移范围内,压装力的减小量不超过50kN。一如客户和供货商此前已就此情况或产品达成协议,允许曲线出现局部偏离。TB/T1718.3-2018
附录B
(规范性附录)
轮对注油压装压装力曲线及说明1轮对注油压装压装力曲线特性
车轮与车轴的注油压装曲线特性见图B.1。说明:
x——距离,单位为毫米(mm);y——压装力,单位为千牛(kN)。图B.1车轮和车轴的注油压装曲线特性B.2轮对注油压装压装力曲线说明图B.1中描述了车轮和车轴的注油压装曲线特性。未注油时的压装力曲线应均勾成比例平稳上升,曲线中部不应有压力下降(在注油沟区允许存在压力下降)。注油后压装力曲线应平稳变化,注油后压装力允许高于注油前压装力,但不应高于注油前压装力最大值的2倍,注油压装曲线不应超过该装配部件设计人员提供的极限曲线,注油压装曲线终止时的压装力最小。8
小提示:此标准内容仅展示完整标准里的部分截取内容,若需要完整标准请到上方自行免费下载完整标准文档。

标准图片预览:
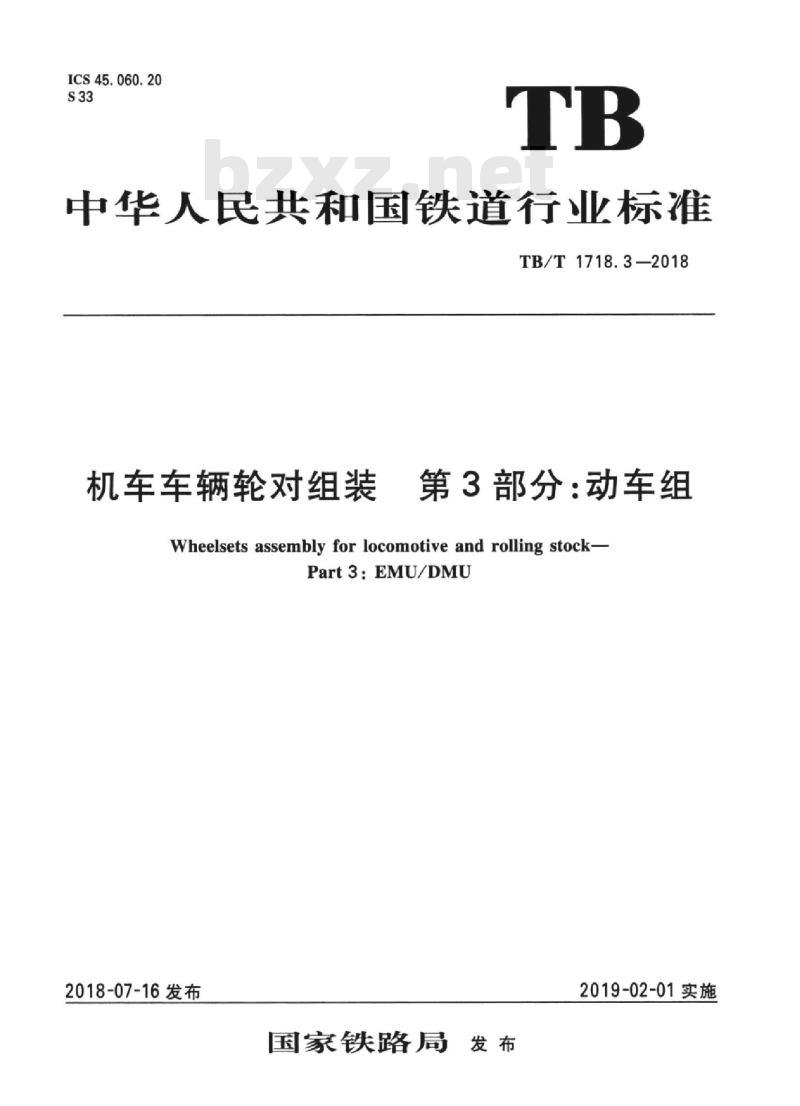
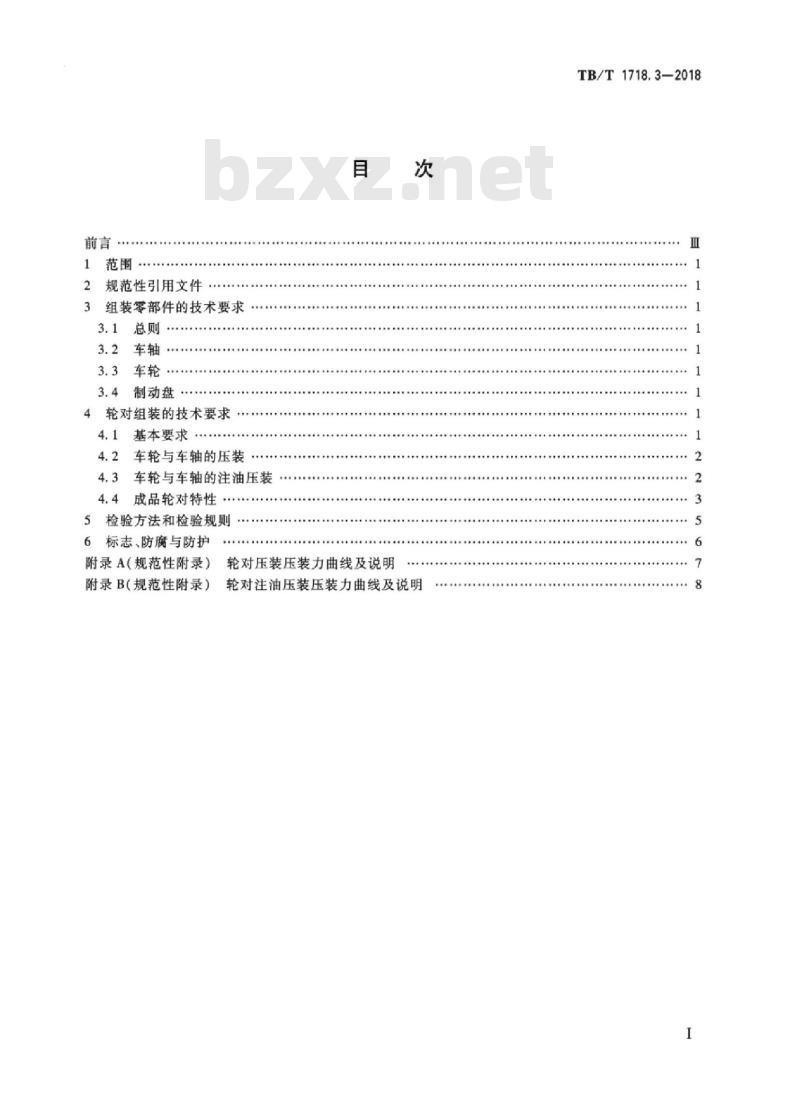
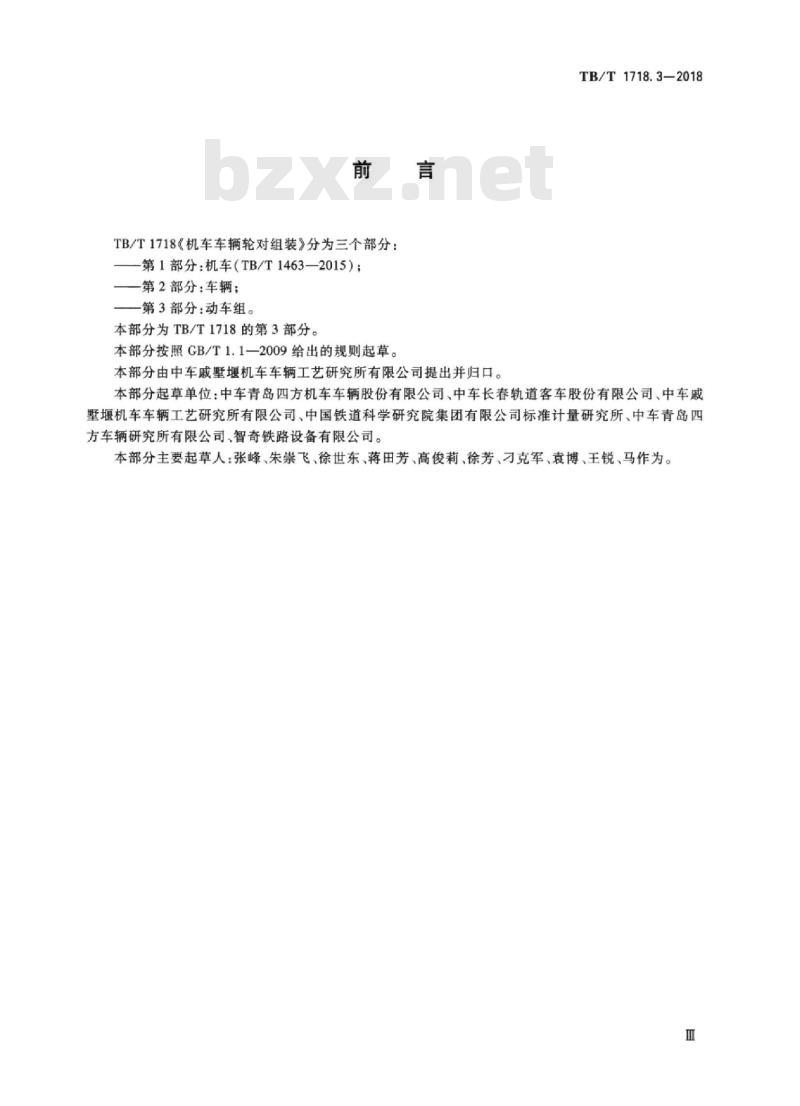
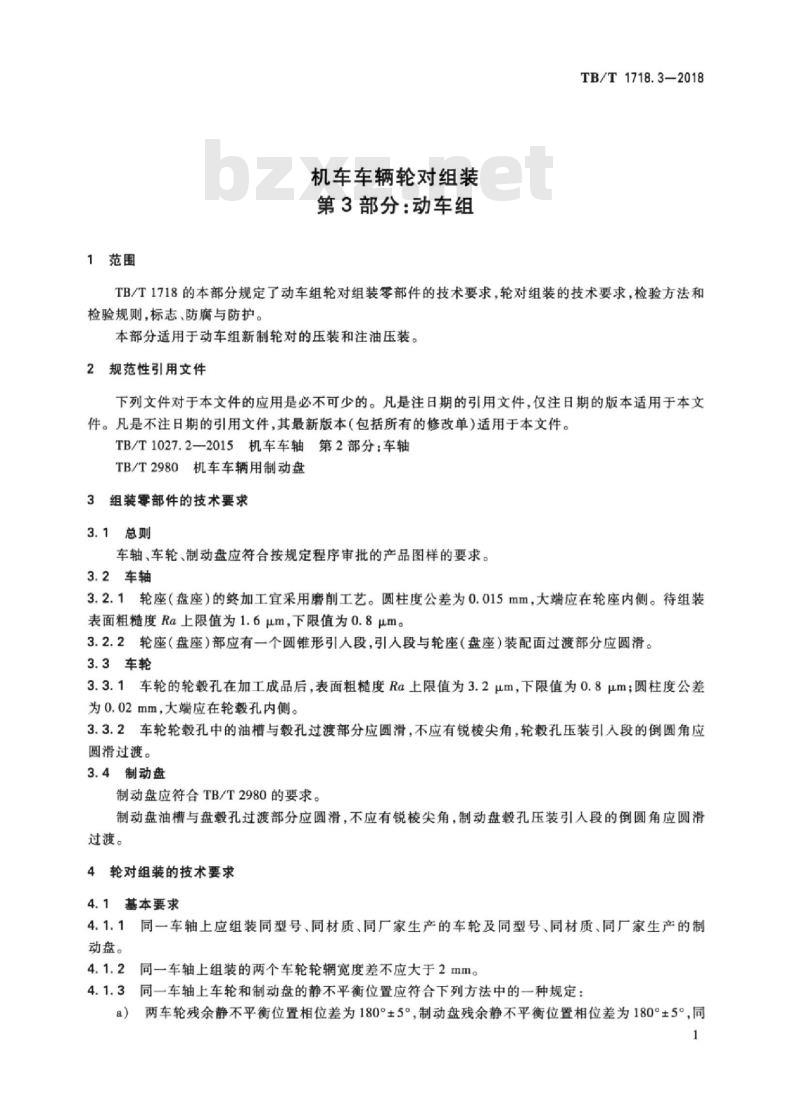
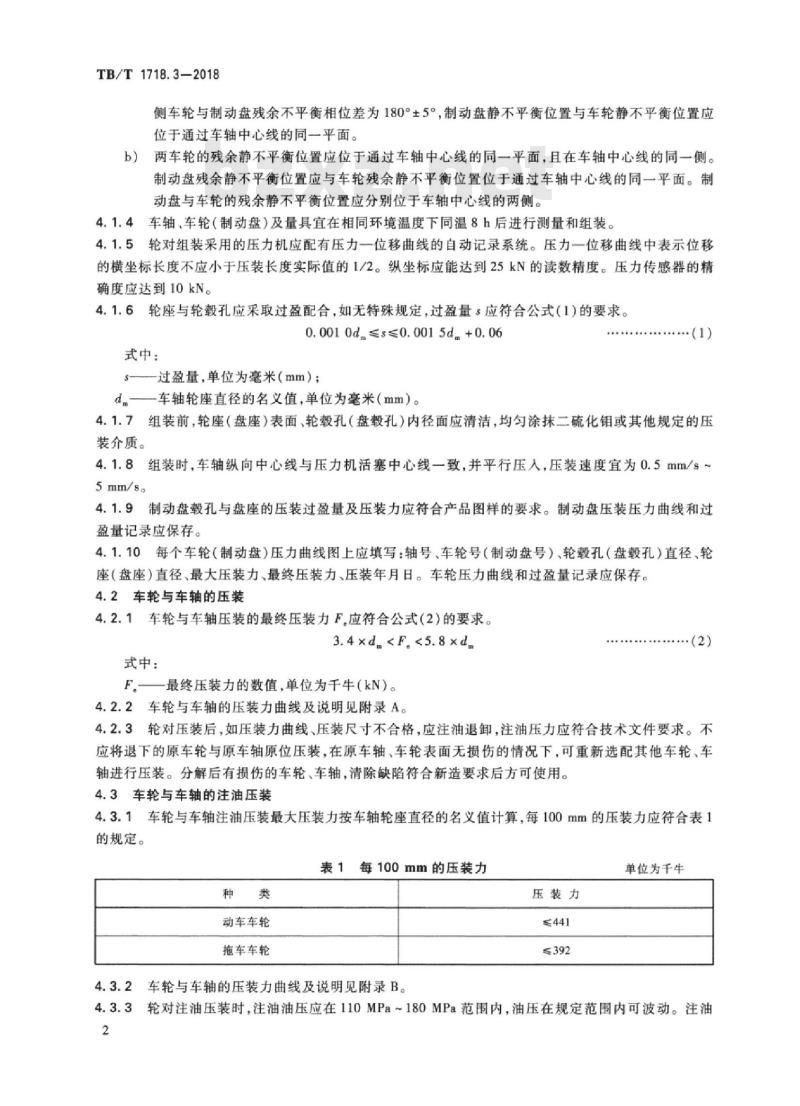
- 其它标准
- 热门标准
- TB铁路运输标准
- TB/T3199.2-2018 电气化铁路接触网用绝缘子第2部分:棒形复合绝缘子
- TB/T2152.27-1990 铁路工人技术标准 机务 接触网工
- TB/T2685.1-1995 铁路环境监测质量控制环境监测指标体系及体系表
- TB10038-2012 铁路工程特殊岩土勘察规程
- TB/T122-2001 机车车辆产品图样及设计文件编号原则
- TB/T2342.4-1993 75kg/m钢轨用接头夹板型式尺寸
- TB/T1670.4-1985 15号车钩钩体上牵引台样板
- TB/T2152.28-1990 铁路工人技术标准 机务 继电保护工
- TB/T2152.29-1990 铁路工人技术标准 机务 高压试验工
- TB/T2152.36-1990 铁路工人技术标准 机务 油脂发放工
- TB1017-1982 蒸汽机车闸瓦托技术条件
- TB/T3103.16-2005 机车车辆用锥面卡套式管接头 第16部分:管锥直通管接头体
- TB/T2794-1997 超速停车装置试验台技术条件
- TB/T2835-1997 铁道重载列车用货车的基本要求
- TB/T2365-93 机车最大牵引|力、起动加速能力试验方法
- 行业新闻
网站备案号:湘ICP备2023016450号-1