- 您的位置:
- 标准下载网 >>
- 标准分类 >>
- 铁路运输行业标准(TB) >>
- TB/T 2568-1995 机车牵引弓|齿轮齿廓感应强化技术条件
标准号:
TB/T 2568-1995
标准名称:
机车牵引弓|齿轮齿廓感应强化技术条件
标准类别:
铁路运输行业标准(TB)
标准状态:
现行出版语种:
简体中文下载格式:
.zip .pdf下载大小:
6.08 MB

点击下载
标准简介:
TB/T 2568-1995.
1主题内容与适用范围
TB/T 2568规定了机车牵引齿轮齿廓强化的技术要求,包括齿轮材料、冶金质量、单齿感应淬火、喷丸强化,以及质量检验等。
TB/T 2568适用于内燃、电力机车中的中碳合金结构钢牵引从动齿轮齿廓的单齿感应淬火强化工艺。
2引用标准
GB 1979结构钢低倍组织缺陷评级图
GB 4342金属显微维氏硬度试验方法
GB 3077合金结构钢的技术条件
GB 5617钢的感应淬火或火焰淬火后有效硬化层深度的测定
GB 6394金属平均晶粒度测定法
GB 8539齿轮材料及热处理质量检验- -般规定
GB 10095渐开线圆柱齿轮精度
GB/T 10561钢中非金属夹杂物显微测定法
YB 4068热轧环件
TB 1758机车车辆弹簧喷丸技术条件
ZB/T J17004齿轮火焰及感应淬 火工艺及其质量控制
ZB J36009感应淬火零件金相标准
3术语
3.1 齿面硬度
指成品齿轮轮齿工作高度中间部位的齿面硬度.
3.2轮齿心部硬度
齿轮齿宽中部法截面上,在齿轮中心线与齿根圆相交处的硬度。
3.3有效硬化层深度
齿轮经感应加热淬火及回火后,于齿宽中部轮齿法截面上,在半齿高处垂直于齿面方向,自表面测至极限硬度处的深度。极限硬度值:
3.4 硬化层分布
齿轮感应淬火后,于齿宽中部轮齿法截面上,轮齿与其齿槽底面所呈现出的淬硬层分布形式。

部分标准内容:
TB/T2568-1995
机车牵引齿轮齿廓感应强化技术条件1996-05—27发布
1997—01—01实施
中华人民共和国铁道部
中华人民共和国铁道行业标准
机车牵引齿轮齿廓感应强化技术条件1主题内容与适用范围
TB/T2568-1995
本标准规定了机车牵引齿轮齿廓强化的技术要求,包括齿轮材料、冶金质量、单齿感应淬火、喷丸强化,以及质量检验等,本标准适用于内燃、电力机车中的中碳合金结构钢牵引从动齿轮齿廊的单齿感应淬火强化工艺。
2引用标准
GB1979
GB4342
GB3077
GB5617
GB6394
GB8539
GB10095
GB/T10561
YB4068
TB1758
ZB/TJ17004
ZBJ36009
3术语
3.1齿面硬度
结构钢低倍组织缺陷评级图
金属显微维氏硬度试验方法
合金结构钢的技术条件
钢的感应淬火或火焰淬火后有效硬化层深度的测定金属平均晶粒度测定法
齿轮材料及热处理质量检验一般规定渐开线圆柱齿轮精度
钢中非金属夹杂物显微测定法
热轧环件
机车车辆弹簧喷丸技术条件
齿轮火焰及感应淬火工艺及其质量控制感应淬火零件金相标准
指成品齿轮轮齿工作高度中间部位的齿面硬度。3.2轮齿心部硬度
齿轮齿宽中部法截面上,在齿轮中心线与齿根圆相交处的硬度。3.3有效硬化层深度
齿轮经感应加热痒火及回火后,于齿宽中部轮齿法截面上,在半齿高处垂直于齿面方向,自表面测至极限硬度处的深度。极限硬度值:HVHt=0.8×HVMS
中华人民共和国铁道部1996—05—27批准1997-01--01实施
式中:HVH极限硬度,
TB/T2568-—1995
HVMs-设计要求的最低表面硬度。3.4硬化层分布
齿轮感应淬火后,于齿宽中部轮齿法截面上,轮齿与其齿槽底面所呈现出的淬硬层分布形式。
4齿轮材料
4.1机车牵引从动齿轮带用材料
42CrMo50CrMoA45CrNi40CrNiMoA4.2冶金质量
4.2.1化学成分应符合GB3077的规定。50CrMoA按YB4068规定。碳含量上、下限差应小于0.05%。
4.2.2在横向酸漫试片上检查低倍组织时,不得有肉眼可见的白点、夹杂和翻皮。一般疏松、中心疏松和偏析按GB1979评定,按GB3077规定判定。4.2.3钢的非金属夹杂物按GB/T10561测定,氧化物和硫化物的最高级别各不超过3级,两者之和不超过5.5级。
4.2.4机车牵引齿轮用钢为细晶粒钢,晶粒度为5~8级,按GB6394评定。4.3锻坏质量与机械性能
4.3.1齿坏由钢锭锻辗而成,锻造比不小于3。4.3.2齿坏晶粒度不得低于原材料的晶粒度。4.3.3经粗加工之后的齿轮坏表面残留的缺陷深度不得侵入精加工尺寸。4.3.4齿坏经正火、调质处理后测定机械性能。每一熔炼炉号的齿坏取样时,检验项目应包括:抗拉强度,屈服强度の,伸长率os,冲击韧性Ax(a)。硬度HB作参考。对每一热处理炉次检验齿坏时,应做硬度HB测定。各性能指标应符合设计图样规定的要求。4.4取样部位及数量
4.4.1取样部位
拉伸、高倍、晶粒度、常温冲击试样均取自相当于齿轮心部部位、圆周方向。低倍试样自轮缘横向切取。也允许用等效试块轴向取样。试块的横截面与齿坏相同,长度应为拉伸试样的23倍,材料与齿坏同一熔炼炉号。硬度试验在齿轮端面中部进行,4.4.2试样数量
每一熔炼炉号取样数量:拉伸2个,常温冲击2个,高倍试样1个,低倍试样1个,晶粒度试样1个。硬度试验:热处理每炉齿坏做1个。5齿轮感应淬火预备处理
5.1滚齿后齿糜面上不允许有毛刺,铁屑、污垢、铁锈及其它杂物。5.2齿轮加工精度,按GB10095不低于8级。5.3齿面不允许磁伤,齿端倒角及齿面的表面粗糙度应符合图样和技术条件的规定。按GB10095齿槽及齿面的表面粗糙度为Ra3.2。2
TB/T2568—1995
6齿轮感应淬火、回火设备及技术要求6.1机车牵引齿轮建议采用沿齿槽单齿连续感应淬火强化齿,中频电源的输出频率为8000~10000Hz,中频变频装置的输出功率变动量控制在士5%之内。6.2采用专用单齿齿轮淬火机床。机床不允许有爬行现象。机床精度应符合表1的规定。表1
机床检验项目
主轴锥孔径向题脱动
回转工作台面跳动
滑板(杆)移动的平行度
工件进给速度变化遗
将检验棒插入主轴锥孔,在距主轴端面300mm处测量,
装上直径大于300mm的圆盘,在半径150mm处测量
测量滑板(杆)300mm行程的平行度。测量工作行程300mm的平均速度,齿轮感应淬火时的定位装置与拨齿装置应精确、可靠,齿轮定位和拔齿装置的精度应不低于被处理齿轮的加工精度。
6.3单齿加热感应器的设计必须保证沿齿扇均匀加热。感应器冷却水通道应畅通,冷却水出口温度不大于60℃。冷却水应有过滤装置,防止异物堵塞。6.4淬火介质及冷却装置
6.4.1合金钢齿轮单齿感应火,推荐采用埋液冷却,淬火介质为10号机械油或冷却性能更佳的介质。淬火介质应定期检查,保持足够的冷却能力。火介质必须循环冷却,温度不超过60℃。
6.4.2单齿感应加热火时,对已火的相邻齿槽的齿面应适当冷却保护,以防止已硬化齿廓的回火。冷却液流量及压力应可以调节,以适应不同模数齿轮的冷却需要。6.5回火设备
齿轮应在有循环气流的回火电炉或有搅拌装置的油浴炉中进行回火。回火设备的有效加热区温度均匀,低温回火时温度偏差应为士10℃。回火设备应配备有自动记录仪表,热电偶应定期校对,有效加热区的温度必须定期检测,保持规定的控温精度。6.6技术要求
6.6.1应根据工艺试验确定感应器尺寸及电压、电流、功率、感应器或工件的移动速度,冷却保护液的压力等参数。
6.6.2齿轮感应淬火时,电参数、感应器或工件的移动速度、感应器与齿廓的间隙应保持恒定,以免加热不足、加热不均匀,过热或过烧等缺陷。6.6.3淬火介质种类及温度控制按本标准6.4.1的规定。6.6.4单齿感应痒火时,相邻齿面应喷液冷却,按本标准6.4.2的规定。6.6.5感应器或工件的移动速度应根据感应器的结构、硬化层深度、生产效率而定。6.6.6回火
齿轮感应淬火后应及时进行回火,时间间隔应不超过4h。回火处理在空气炉或油浴炉内进行,回火温度应满足图样规定的硬度要求,保温3h以上。3
7喷丸强化
喷丸强化处理按附录A的要求进行。8质量检验
8.1外观
TB/T2568—1995
齿轮经感应淬火后,经目测齿廓上不得有裂纹、烧伤、烧熔、剥落等缺陷。齿面不得碰伤。8.2齿面硬度
8.2.1齿轮在感应火时,操作人员应使用标准挫刀或其它方法对每个齿轮检查齿面及齿槽的萍火硬度。
8.2.2经感应淬火后的成品齿轮,每批抽取2件检验硬度。8.2.3在齿宽方向的有效硬化区内(见本标准8.2.5条)用手提式齿面硬度计或其它硬度计检验齿廊两侧节圆齿面硬度,每侧齿面任意检验1~2点,在相隔180°处再检验一个齿廓的两侧齿面硬度。检测处的表面粗糙度应为Ra3.2um。需磨齿的齿轮,在齿面磨削后测定齿面硬度。
8.2.4所检测的硬度值不取平均值,其最低硬度应符合设计要求。齿面硬度的允许偏差按表2的规定。免费标准bzxz.net
洛氏硬度
同一件
齿面硬度偏差值
同一批
注:同一批指用同一批材料、在相同工艺条件下处理的一批齿轮工件。同一批处理件的最大量由技术条件规定。8.2.5有效齿宽硬化区应不小于齿宽的80%,齿宽两端各10%齿宽范围不作检验。8.3有效淬硬层深度
有效淬硬层测定方法按GB5617的规定。测定结果应符合设计要求。同一件齿轮的有效淬硬层深度偏差应在技术条件中值的士20%范围内。8.4硬化层分布
8.4.1批量生产时,每半年抽验一件实物齿轮,取样检验。8.4.2沿齿廊分布的硬化层应能达到技术条件要求,齿槽部分的淬硬层深度应不低于节圆处有效率硬层深度的60%,但不能低于技术条件规定的下限。8.5金相检验
8.5.1批量生产时,每半年抽验一件实物齿轮,取样检验。8.5.2淬硬层组织应为较细马氏体或隐晶马氏体,按ZBJ36009评定。心部组织为回火索氏体或屈氏体。
8.6裂纹检验
齿轮感应淬火后应100%进行裂纹检验。表面不允许有淬火裂纹。4
9报告单
报告单应包括下列内容
TB/T2568—1995
a)齿轮件号、材料、内径、外径、齿宽、模数、技术要求;b)数量及重量;
c)质量检验结果;
d)操作者、检验者姓名或代号;e)处理日期。
TB/T2568--1995
附录A
喷丸强化
(补充件)
建议对于负荷较大、速度较高的机车牵引齿轮,或经齿形修复后的齿轮,进行喷丸强化处A1设备
推荐采用喷管式喷丸设备,设备应自动化。齿轮作转动及平移运动,使齿廓达到均匀一致的喷丸强度与所需要的复盖率。A2喷丸前的准备工作
A2.1对无需喷丸的内孔及某些精加工部位应加以屏蔽。A2.2除齿面研磨、齿、抛光外,所有齿廓机加工必须在喷丸前完成。A2.3所有热处理工艺应在喷丸前完成。A2.4齿轮的磁粉探伤应在喷丸前(磨齿后)进行。A2.5
齿廓表面不应有影响喷丸效果的碰伤、切口、裂纹等表面缺陷。喷丸前齿轮应保持干燥。
A3喷丸工艺要求
A3.1应根据图样技术要求,对齿轮进行喷丸强化处理。齿轮喷丸强化区,若无明确规定,是指全部齿廓。
A3.2喷丸丸粒的材料、尺寸、质量要求应符合TB1758及有关企业标准的规定。感应淬火齿轮的喷丸钢丸硬度推荐为HRC5060。允许用铸铁丸作喷丸丸粒。A3.3喷丸强度应符合图样及有关技术文件的规定,其测试方法及一般要求按TB1758中第5章、第6章的规定。
A3.4喷丸复盖率应符合图样及有关技术文件的规定,其测试方法按TB1758中的第6.2条的规定。若无明确规定时,齿廓喷丸复盖率应为200%。A4喷丸质量捡验应符合TB1758中第6章的规定。喷丸后的处理推荐采用TB1758中7.27.3条的规定。
附加说明:
本标准由铁道部戚墅堰机车车辆工艺研究所提出并归口。本标准由铁道部戚墅堰机车车辆工艺研究所负责起草。6
小提示:此标准内容仅展示完整标准里的部分截取内容,若需要完整标准请到上方自行免费下载完整标准文档。

标准图片预览:
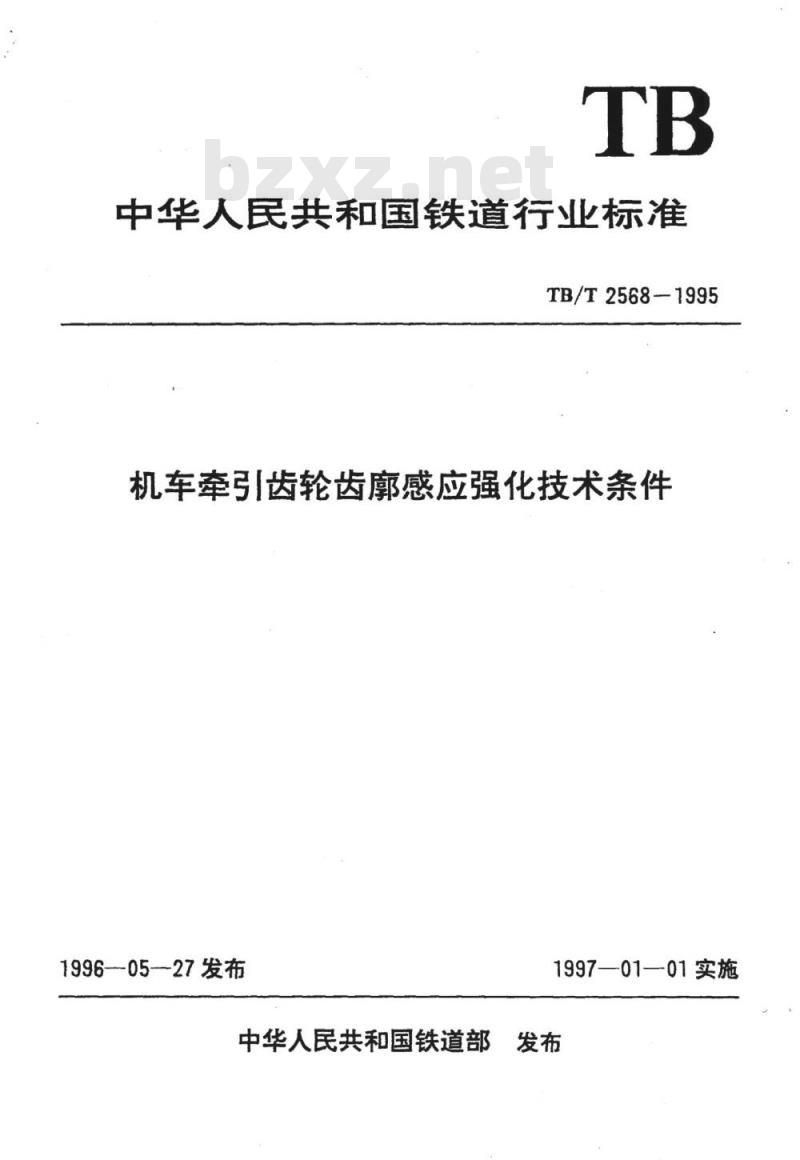
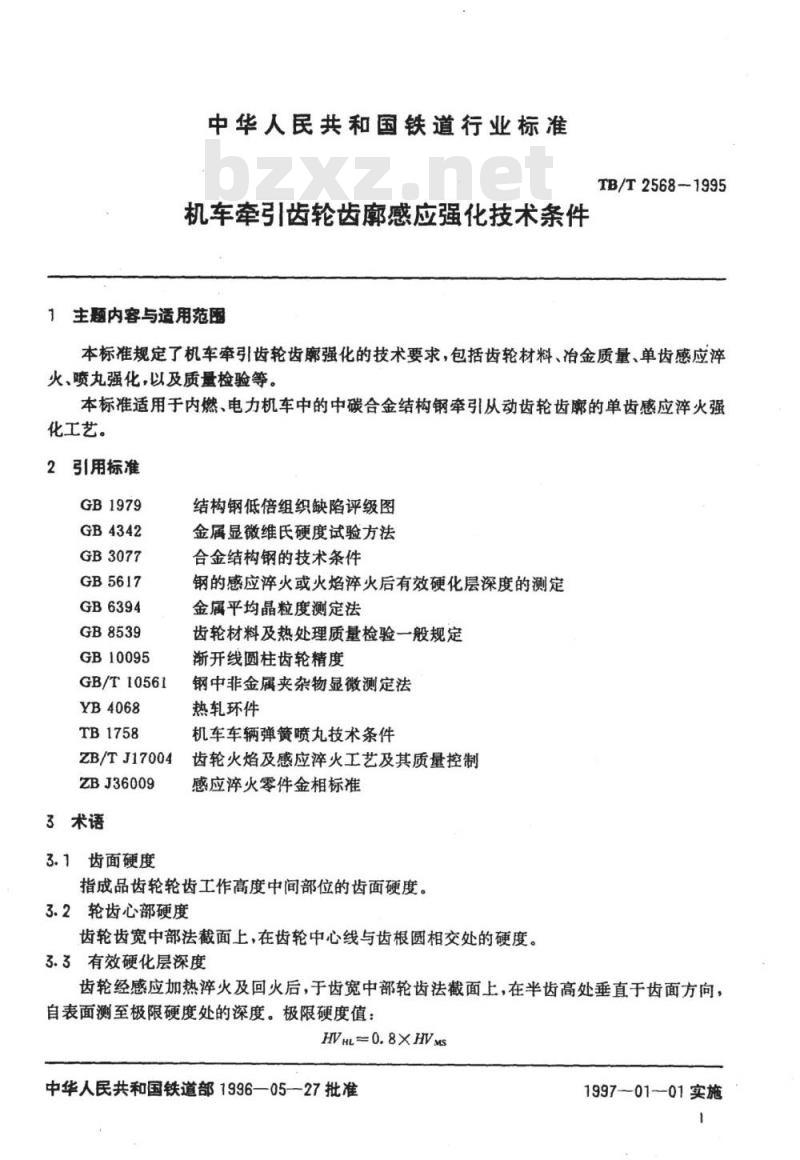
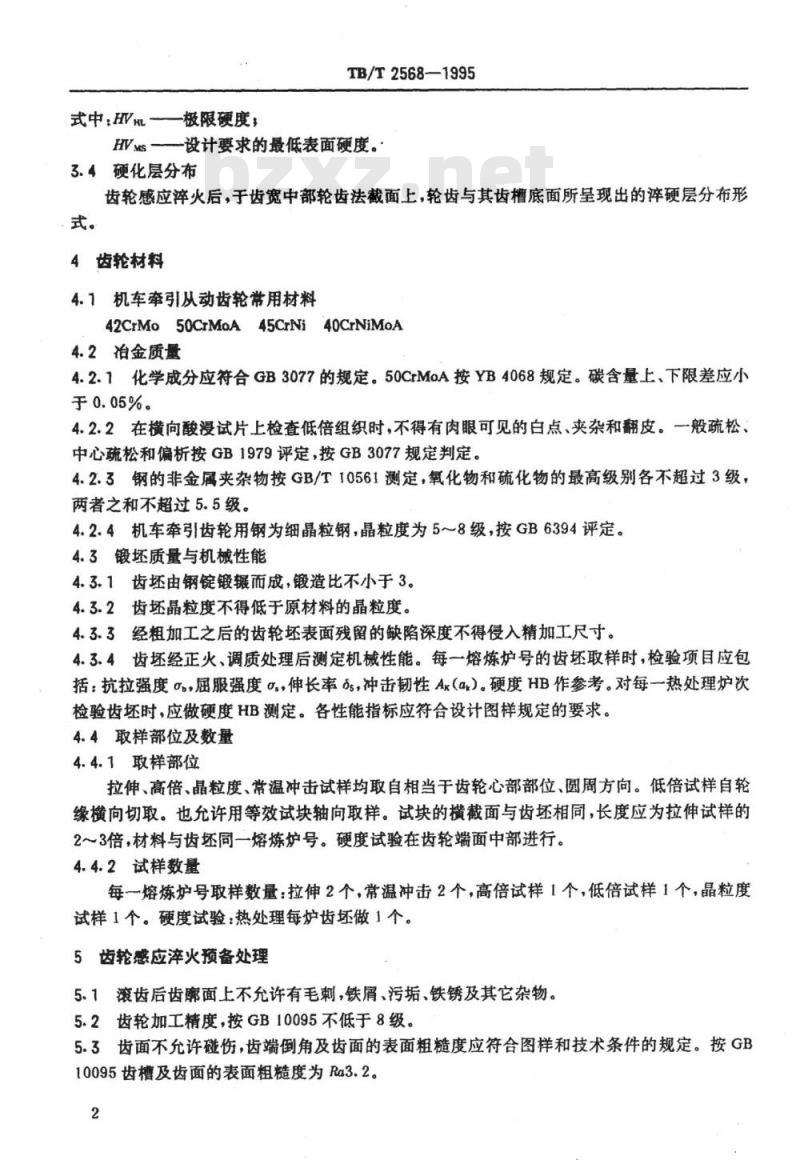
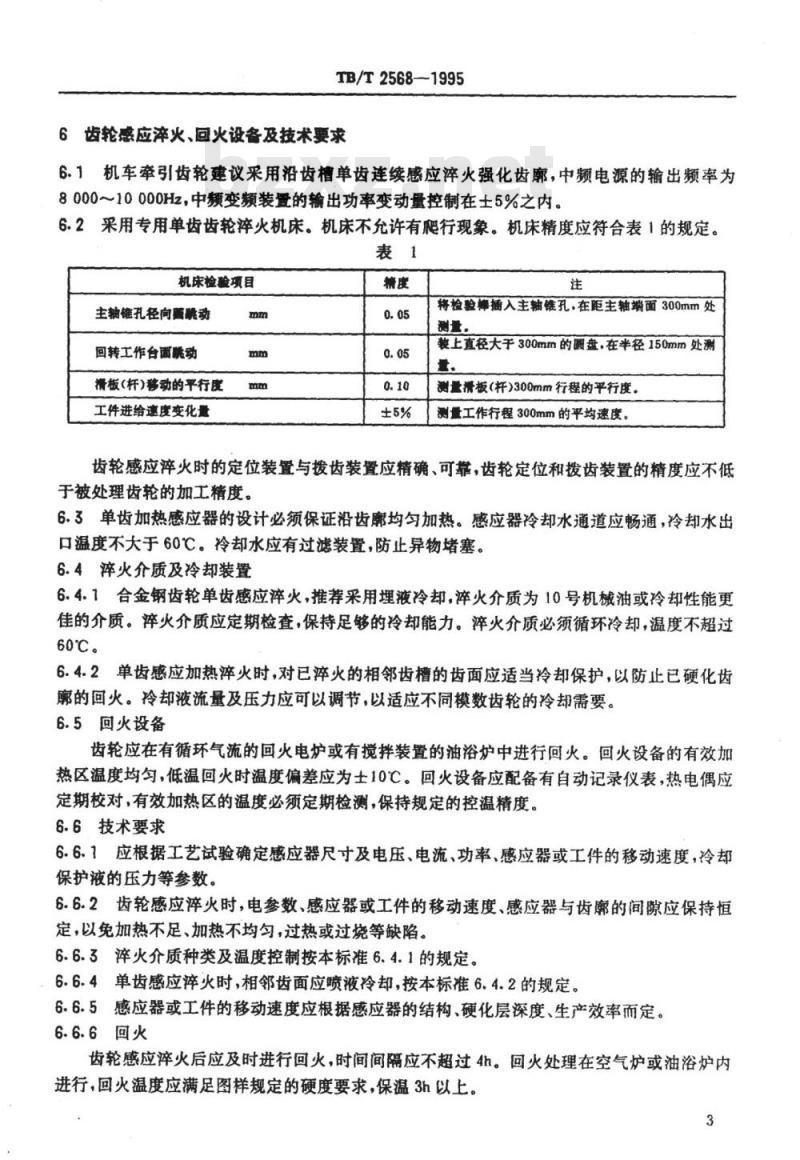
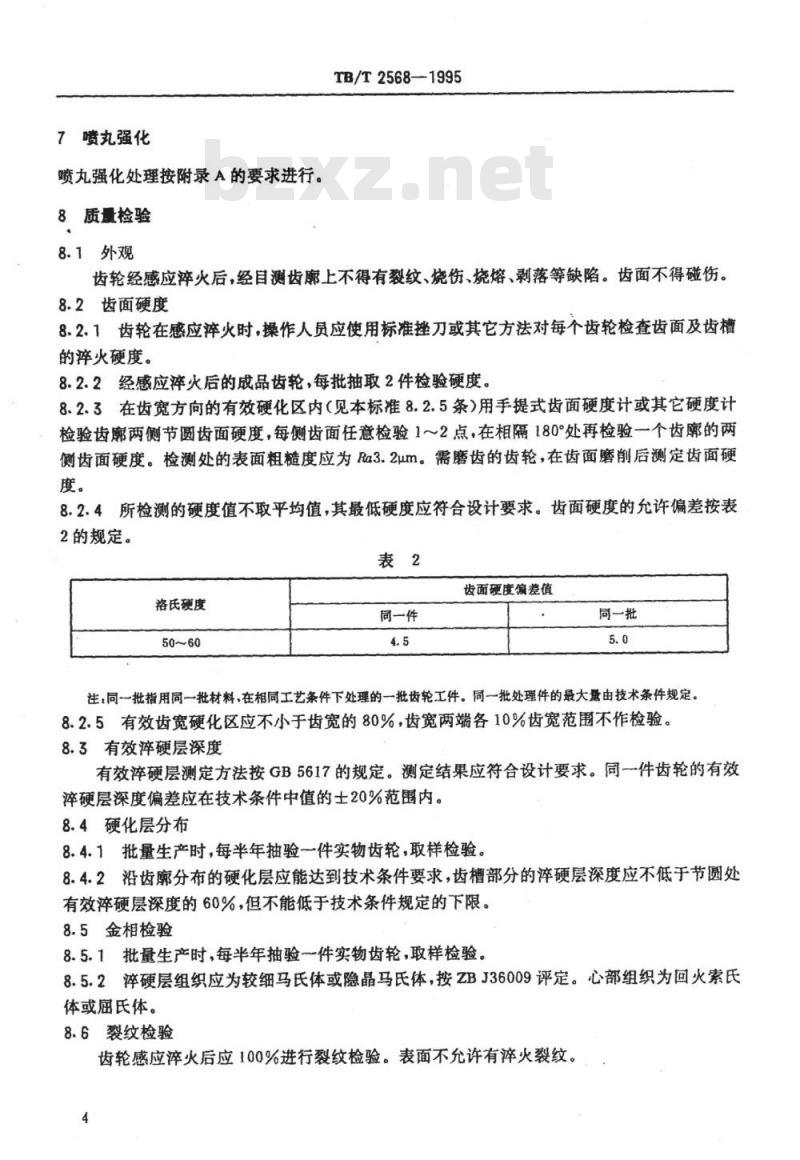
- 热门标准
- TB铁路运输标准
- TB/T3568.1-2021 铁路无损检测材料 第1部分:磁粉检测材料
- TB/T30002-2020 铁路调车作业
- TB/T3567—2021 铁路车辆轴承塑料保持架
- TB/T1760-1986 客车门锁技术条件
- TB/T2563-1995 内燃机车用柴油机机体清洁度测定方法
- TB/T3523.2-2018 交流传动电力机车试验方法第2部分:输入特性试验
- TB/T1632.4-2005 钢轨焊接 第4部分:气压焊接
- TB/T2769.9-1997 重型轨道车试验方法动力学性能试验方法及评定标准
- TB2034-88铁 轨道强度检算法
- TB/T2820.1-1997 铁路桥隧建筑物劣化评定标准钢梁
- TB/T2658.7-1995 工务作业标准林业作业
- TB/T2686-1995 铁路高温作业人员健康检查规范
- TB/T2599-1996 细长钢管内壁涂塑技术条件
- TB/T2521-1995 电力机车平波电抗器装车后温升与电感值试验计算方法
- TB/T3416.3-2015 动车组编码标识系统第3部分:安装地点与位置的标识
网站备案号:湘ICP备2023016450号-1