- 您的位置:
- 标准下载网 >>
- 标准分类 >>
- 机械行业标准(JB) >>
- JB/T 11018-2010 超临界及超超临界机组汽轮机用Cr10型不锈钢铸件 技术条件
标准号:
JB/T 11018-2010
标准名称:
超临界及超超临界机组汽轮机用Cr10型不锈钢铸件 技术条件
标准类别:
机械行业标准(JB)
标准状态:
现行-
发布日期:
2010-02-11 出版语种:
简体中文下载格式:
.rar .pdf下载大小:
5.95 MB

点击下载
标准简介:
标准下载解压密码:www.bzxz.net
本标准规定了超临界及超超临界机组汽轮机用Cr10型不锈钢铸件的订货要求、制造工艺、技术要求、试验方法和检验规则、质量证明书等。本标准适用于超临界及超超临界机组汽轮机中用砂型铸造方法生产的缸体、阀体、阀盖、弯管等铸钢件的订货、制造、检验和验收。 JB/T 11018-2010 超临界及超超临界机组汽轮机用Cr10型不锈钢铸件 技术条件 JB/T11018-2010

部分标准内容:
ICS77.140.80
备案号:28567—2010
中华人民共和国机械行业标准
JB/T11018—2010
超临界及超超临界机组汽轮机用Cr10型不锈钢铸件技术条件
Specification for Cr10 stainless steel casting of steam turbine forsupercriticalandultra-supercritical units2010-02-11发布
2010-07-01实施
中华人民共和国工业和信息化部发布前言,
规范性引用文件
订货要求
制造工艺
热处理
缺陷清除及补焊
5技术要求.
化学成分
力学性能,
显微组织
表面质量.
无损检测,
形状和尺寸公差
重量公差
试验方法和检验规则
化学成分分析
力学性能试验
表面质量检测..
无损检测..
6.5复试和重新热处理
7验收及质量证明书
7.1验收...
质量证明书,
8标识和包装.
附录A(规范性附录)力学性能的补充要求A.1
高温持久性能试验
高温拉伸性能试验
铸件热处理规范(推荐)
化学成分(质量分数)
表3成品化学成分(质量分数)的允许偏差表4气体含量(体积分数)
表5力学性能
高温持久性能试验条件
高温拉伸性能试验条件
JB/T11018—2010
JB/T11018—2010
本标准的附录A为规范性附录。
本标准由中国机械工业联合会提出。前言
本标准由机械工业大型铸锻件标准化技术委员会归口。本标准起草单位:中国第二重型机械集团公司、上海重型机器厂有限公司。本标准主要起草人:肖章玉、吕友清、赵喜林。本标准为首次发布。
JB/T11018-2010
超临界及超超临界机组汽轮机用Cr10型不锈钢铸件技术条件1范围
本标准规定了超临界及超超临界机组汽轮机用Cr10型不锈钢铸件的订货条件、制造工艺、技术要求、试验方法和检验规则、质量证明书等。本标准适用于超临界及超超临界机组汽轮机中用砂型铸造方法生产的缸体、阀体、阀盖、弯管等铸钢件的订货、制造、检验和验收。2规范性引用文件
下列文件中的条款通过本标准的引用而成为本标准的条款。凡是注日期的引用文件,其随后所有的修改单(不包括勘误的内容)或修订版均不适用于本标准,然而,鼓励根据本标准达成协议的各方研究是否可使用这些文件的最新版本。凡是不注日期的引用文件,其最新版本适用于本标准。GB/T223(所有部分)钢铁及合金化学分析方法GB/T228金属材料室温拉伸试验方法(GB/T228—2002,eqvISO6892:1998)GB/T229金属材料夏比摆锤冲击试验方法(GB/T229—2007,ISO148-1:2006,MOD)GB/T231.1金属材料布氏硬度试验第1部分:试验方法(GB/T231.1—2009,ISO6506-1:2005,MOD)
GB/T2039
GB/T4338
金属拉伸螨变及持久试验方法(GB/T2039—1997,eqVISO204:1997)金属材料高温拉伸试验方法(GB/T4338—2006,ISO783:1999,MOD)GB/T6060.1表面粗糙度比较样块铸造表面(GB/T6060.1—1997,eqVISO2632-3:1979)GB/T6414--1999铸件尺寸公差与机械加工余量(eqvISO8062:1994)GB/T9443
铸钢件渗透检测(GB/T9443—2007,ISO4987:1992,IDT)GB/T11351
铸件重量公差
钢和铁化学成分测定用试样的取样和制样方法(GB/T20066—2006,ISO14284:GB/T20066
1996IDT)
JB/T4058—1999汽轮机清洁度
汽轮机铸钢件磁粉探伤及质量分级方法JB/T9630.1
汽轮机铸钢件超声波探伤及质量分级方法JB/T9630.2
3订货要求
供方应有完善的质量保证体系,应具有生产过类似材料、相近尺寸的铸件的业绩3.1
3.2需方应在订货合同或技术协议中注明采用的标准、铸件名称、材料牌号、数量和供货状态、供需双方明确的相应技术要求和检验项目及本标准要求以外的检验项目。3.3需方应提供经双方共同审定的订货图样。3.4需方要求参加现场检验的项目应在订货合同中注明。4制造工艺
4.1治炼
铸件用钢应采用电炉冶炼、钢包精炼工艺。经需方同意,也可采用保证质量的其他冶炼方法。JB/T11018—2010
4.2铸造
在需方无特殊要求时,铸造工艺可由供方自行确定,但不得使用芯撑和内冷铁。4.3热处理
4.3.1铸件应进行热处理。通常情况下,热处理由供方进行。热处理时为保证炉温的均匀性,可在铸件表面上放置外接热电偶。当需方无特殊要求时,在铸件表面上放置外接热电偶的位置、数量可由供方决定。4.3.2推荐的铸件的预备热处理和性能热处理规范见表1。表1铸件热处理规范(推荐)
材料牌号
ZG10Cr9Mo1VNbN
ZG12Cr9Mo1VNbN
ZG12Cr10MoVNbN
ZG11Cr10Mo1NiWVNbN
ZG13Cr11MoVNbN
ZG14Cr10MoVNbN
ZG12Cr10Mo1W1NbN-1
ZG12Cr10Mo1W1NbN-2
ZG12Cr10Mo1W1NbN-3
热处理规范
1)进行预备热处理的铸件加热到≥1050℃,保持足够时间,然后炉冷到300℃以下空冷
2)进行性能热处理的铸件加热到1040℃,保持足够时间,风冷或空冷+一次或二次间火(加热温度在Ac,点以下)1)进行预备热处理的铸件加热到≥1050℃,保持足够时间,然后炉冷到300℃以下空冷
2)进行性能热处理的铸件加热到1010℃,保持足够时间,风冷或空冷+一次或二次回火(加热温度在Ac,点以下)1)进行性能热处理的铸件加热到≥】050℃C,保持足够时间,然后炉冷到300℃以下空冷
2)进行性能热处理的铸件加热到1010℃,保持足够时间,风冷或空冷+二次回火(加热温度≥700℃)
1)进行性能热处理的铸件加热到≥1080℃,保持足够时间,然后炉冷到300℃以下空冷
2)进行性能热处理的铸件加热到≥1080℃,保持足够时间,风冷或空冷+二次回火(加热温度≥720℃)
4.3.3铸件在粗加工、焊接及补焊后均应进行消除应力热处理。最终消除应力热处理应在大于或等于690℃的温度下进行。
4.3.4除预备热处理和性能热处理外,通常铸件的回火温度应高于消除应力温度10℃以上。4.4缺陷清除及补焊
4.4.1铸件应在软化退火后清除表面可见缺陷。缺陷清除可采用机械加工、打磨或电弧气刨等方式。4.4.2允许对铸件中的超标缺陷进行补焊修复,补焊前应将缺陷全部清除干净,并应经无损检测确认清除结果。
4.4.3补焊应在性能热处理后,最终热处理之前进行,补焊应使用与铸件材料相同或相近[Cr含量(质量分数)应为9%~14%1的焊接材料进行。4.4.4最终热处理后原则上不应再进行补焊,如果有少量缺陷必须补焊,则焊后应进行局部消除应力热处理并作记录。
4.4.5供方进行焊接或补焊操作时,应对缺陷部位予以记录。焊工应具有资格证书。补焊工艺应经过焊接工艺评定。
5技术要求
5.1化学成分
5.1.1供方应对每炉钢水进行熔炼分析,分析结果应符合表2的规定。5.1.2当需方有要求时,可以进行成品化学成分分析。铸件的成品化学成分分析结果应符合表2的规定,但允许存在表3规定的偏差,5.1.3供方应进行气体含量分析。当无特殊要求时,气体含量的分析结果应符合表4的规定。2
材料牌号
ZG10Cr9MoIVNbN
ZG12Cr9Mo1VNbN
ZG11Cr10MoVNbN
ZG13Cr11IMoVNbN
ZG14Cr10MoVNbN
ZG11Cr10Mo1NiWVNbN
ZG12Cr10Mo1W1VNbN-1
ZG12Cr10MoIW1VNbN-2
ZG12Cr10Mo/W1VNbN-3
注1:ZG11Cr10MoINiWVNbN的铬当益为7.5~10.5,注2:ZG13CrIIMoVNbN的铬当量为8~10,Cr
化学成分(质量分数)
铬当量=Cr40C-2Mn-4Ni+6Si+4Mo+1IV+SNb30N+1.5W。络当量-C
40C2Mn4Ni+6Si+4Mo+1IV+5Nb30N,注3:ZG14CrI0MoVNbN的铬当量为<9,铬当量Cr-40C2Mn4Ni+6Si+4Mo+11V+5Nb30N。注4:残余元素含量的测定,露方无要求时,仅作参考。
(目标)
残金元素
记录记录
JB/T11018—2010
JB/T11018—2010
材料牌号
ZG10Cr9Mo1VNbN
ZG12Cr9Mo1VNbN
ZG11Cr10MoVNbN
ZG13Cr11MoVNbN
ZG14Cr10MoVNbN
成品化学成分
质量分数
0.10~0.15
8.00~11.50
0.60~1.30
0.02~0.07
ZG11Cr11Mo1NiWVNbN
ZG12Cr10Mo!W1VNbN-!
ZG12Cr1GMo1W1VNbN-2
ZG12Cr10Mo1W1VNbN-3
(质量分数)自
的允许偏差
超出上限或低于下限的极限偏差值-0.005
气体含量(体积分数)
≤3×10-(目标值)
≤7×10
力学性能
经最终热处理后的铸件的力学性能应符合表5的规定。5.2.1
力学性能
材料牌号
ZG10Cr9Mo1VNbN
ZG12Cr9Mo1VNbN
ZG11Cr10MoVNbN
ZG13Cr11MoVNbN
ZG14Cr10MoVNbN
ZG11Cr10Mo1NiWVNbN
ZG12Cr10Mo1W1VNbN-1
ZG12Cr10Mo1W1VNbN-2
ZG12Cr10Mo1WIVNbN-3
585~760
630~750
≥680
≥689
≥700
≥685
680~850
680~850
680~850
≥500
≥516(Ro0.02)
≥500(Rp0.02)
≥490(Rpo.02)
≥520
≥>17
≤70×10-(目标值)
90×10
≥65(Aku)
≥30(Aku)
FATTso
《121
≤260
≤260
≤260
≤260
≤260
JB/T11018-2010
5.2.2焊后最终消应热处理后应再次进行力学性能试验,试验结果应符合表5的要求。5.2.3当需方有要求,并且在铸件首件生产或热处理.1.艺发生重大变化时可以做高温持久性能试验和高温拉伸性能试验
5.2.4铸件首件制造时应进行韧脆转变温度试验,试验结果仅作为参考。5.3显微组织
铸件在热处理合格后应进行金相分析,显微组织中的铁素体含量应在5%以下。5.4表面质量
5.4.1铸件的表面质量应符合订货图样规定。如图样未作规定,则铸件的表面粗糙度Ra值应达到100μm。
5.4.2需作无损检测的铸件加工面的表面粗糙度Ra值应达到6.3um,非加工面的表面粗糙度Ra值应达到12.5μm。下载标准就来标准下载网
5.4.3铸件表面不允许存在裂纹、冷隔、气孔和粘砂等铸造缺陷。5.4.4铸件的表面清洁度应符合订货图样规定。当图样中未对表面清洁度作出规定时,高中压气缸内缸、阀体的内壁应符合JB/T4058一1999中洁-2的要求。5.5无损检测
5.5.1铸件应进行无损检测。检测的标准、部位和验收的质量等级由供需双方在订货时协商决定。5.5.2铸件不允许存在的缺陷应予以记录。5.5.3铸件的补焊处仍应按本体规定的质量要求进行无损检测。5.6形状和尺寸公差
5.6.1铸件的尺寸公差应符合订货图样规定,如图样中未作规定,则应符合GB/T6414一1999中CT14级的规定。
5.6.2铸件的壁厚应符合订货图样规定。如图样中未作规定,则应符合GB/T6414一1999中CT15级的规定。
5.7重量公差
铸件的重量公差应符合GB/T11351的规定。除订货合同有要求外,铸件的重量公差不作考核。6试验方法和检验规则
6.1化学成分分析
6.1.1供需双方没有特别约定时,化学成分分析试样应以钢包熔炼试样为准。6.1.2化学成分分析的取样方法按GB/T20066的规定进行,化学成分分析的分析方法按GB/T223的规定进行。
6.2力学性能试验
6.2.1力学性能试验的试样应从附铸试块制取,试样形状和尺寸应符合GB/T228的规定。6.2.2附铸试块的部位和形状由供方自行决定,当需方有特殊要求时,由供需双方协商决定。6.2.3力学性能试验用附铸试块应随其所代表的铸件同炉热处理。在没有特殊规定时,铸件重量小于1000kg时,每一熔炼炉次和每一热处理炉次至少取一个拉伸试样,三个冲击试样;铸件重量大于1000kg时,每个铸件都要取一个拉伸试样和三个冲击试样单独进行试验。6.2.4拉伸试验应按GB/T228的规定进行,冲击试验应按GB/T229的规定进行。对于冲击试验,一组三个冲击试验结果的平均值应符合表5的规定,最多允许其中一个试验结果低于规定值,但不应低于规定值的70%(另有规定的除外)。6.2.5硬度试验应按GB/T231.1的规定执行,无特殊说明时,硬度为试样测定值。6.2.6韧脆转变温度试验中,冲击试样断口上各区所占面积的评定应按GB/T229的规定执行。6.2.7高温持久性能试验应按附录A的规定进行。5
JB/T11018—2010
3高温拉伸性能试验应按附录A的规定进行。6.2.8
6.3表面质量检测
表面粗糙度的评定应按GB/T6060.1的规定进行。6.4无损检测
6.4.1一般要求
铸件在无损检测之前应按规定做好表面准备,对超标缺陷应予以记录。6.4.2超声检测
铸件超声检测应按JB/T9630.2的规定进行,或供需双方另行协商。6.4.3磁粉检测
铸件表面磁粉检测应按JB/T9630.1的规定进行,或供需双方另行协商。6.4.4渗透检测
铸件表面渗透检测应按GB/T9443的规定进行,或供需双方另行协商。6.5复试和重新热处理
6.5.1当力学性能试验结果不合格时,允许进行复试。复试应按以下要求进行:a)拉伸试验的复试应从靠近不合格试样的相邻位置取双倍试样重新做不合格项目的试验,重新试验的结果应满足表5的规定要求。若复试中有一个结果仍不合格,则其所代表的铸件连同备用试料应重新进行热处理;
b)冲击试验复试应从靠近不合格试样的相邻位置取样制备三个冲击试样进行,每个复试结果都应等于或超过表5的规定值。否则其所代表的铸件连同备用试料应重新进行热处理。6.5.2显微组织检验结果不合格时,则其所代表的铸件连同备用附铸试块应重新进行热处理。重新热处理后,按6.2.1~6.3的规定重新试验、重新验收6.5.3不包括回火在内的重新热处理次数不得超过两次。7验收及质量证明书
7.1验收
7.1.1供方应为需方验收人员提供必要的条件,以便于需方验收人员进行现场检验工作。需方检验人员不应对供方的生产造成不必要的妨碍7.1.2需方有权选择铸件的某些试验项目进行验收。在验收以后的加工或检验中,发现铸件不符合本标准和订货合同中规定的补充技术要求条款时,需方应及时通知供方,双方协商解决。7.2质量证明书
7.2.1交货时,供方必须向需方提供质量证明书。质量证明书应包括下列内容:a)订货合同号;
b)图号;
c)铸件名称;
d)重量;
e)材料牌号;
f)铸件识别号或熔炼炉号;
g)化学成分分析试验报告和力学性能试验报告等;h)热处理状态、热处理曲线记录、热处理炉批号:i)无损检测报告;
j)尺寸检验记录:
k)合同和技术协议有要求的其他检验报告。7.2.2质量证明书应有供方质量部门和负责人的签章。6
标识和包装
铸件应有供方标识、订货合同号、图号等标识内容。供方应根据运输条件要求进行包装。JB/T11018—2010
小提示:此标准内容仅展示完整标准里的部分截取内容,若需要完整标准请到上方自行免费下载完整标准文档。
备案号:28567—2010
中华人民共和国机械行业标准
JB/T11018—2010
超临界及超超临界机组汽轮机用Cr10型不锈钢铸件技术条件
Specification for Cr10 stainless steel casting of steam turbine forsupercriticalandultra-supercritical units2010-02-11发布
2010-07-01实施
中华人民共和国工业和信息化部发布前言,
规范性引用文件
订货要求
制造工艺
热处理
缺陷清除及补焊
5技术要求.
化学成分
力学性能,
显微组织
表面质量.
无损检测,
形状和尺寸公差
重量公差
试验方法和检验规则
化学成分分析
力学性能试验
表面质量检测..
无损检测..
6.5复试和重新热处理
7验收及质量证明书
7.1验收...
质量证明书,
8标识和包装.
附录A(规范性附录)力学性能的补充要求A.1
高温持久性能试验
高温拉伸性能试验
铸件热处理规范(推荐)
化学成分(质量分数)
表3成品化学成分(质量分数)的允许偏差表4气体含量(体积分数)
表5力学性能
高温持久性能试验条件
高温拉伸性能试验条件
JB/T11018—2010
JB/T11018—2010
本标准的附录A为规范性附录。
本标准由中国机械工业联合会提出。前言
本标准由机械工业大型铸锻件标准化技术委员会归口。本标准起草单位:中国第二重型机械集团公司、上海重型机器厂有限公司。本标准主要起草人:肖章玉、吕友清、赵喜林。本标准为首次发布。
JB/T11018-2010
超临界及超超临界机组汽轮机用Cr10型不锈钢铸件技术条件1范围
本标准规定了超临界及超超临界机组汽轮机用Cr10型不锈钢铸件的订货条件、制造工艺、技术要求、试验方法和检验规则、质量证明书等。本标准适用于超临界及超超临界机组汽轮机中用砂型铸造方法生产的缸体、阀体、阀盖、弯管等铸钢件的订货、制造、检验和验收。2规范性引用文件
下列文件中的条款通过本标准的引用而成为本标准的条款。凡是注日期的引用文件,其随后所有的修改单(不包括勘误的内容)或修订版均不适用于本标准,然而,鼓励根据本标准达成协议的各方研究是否可使用这些文件的最新版本。凡是不注日期的引用文件,其最新版本适用于本标准。GB/T223(所有部分)钢铁及合金化学分析方法GB/T228金属材料室温拉伸试验方法(GB/T228—2002,eqvISO6892:1998)GB/T229金属材料夏比摆锤冲击试验方法(GB/T229—2007,ISO148-1:2006,MOD)GB/T231.1金属材料布氏硬度试验第1部分:试验方法(GB/T231.1—2009,ISO6506-1:2005,MOD)
GB/T2039
GB/T4338
金属拉伸螨变及持久试验方法(GB/T2039—1997,eqVISO204:1997)金属材料高温拉伸试验方法(GB/T4338—2006,ISO783:1999,MOD)GB/T6060.1表面粗糙度比较样块铸造表面(GB/T6060.1—1997,eqVISO2632-3:1979)GB/T6414--1999铸件尺寸公差与机械加工余量(eqvISO8062:1994)GB/T9443
铸钢件渗透检测(GB/T9443—2007,ISO4987:1992,IDT)GB/T11351
铸件重量公差
钢和铁化学成分测定用试样的取样和制样方法(GB/T20066—2006,ISO14284:GB/T20066
1996IDT)
JB/T4058—1999汽轮机清洁度
汽轮机铸钢件磁粉探伤及质量分级方法JB/T9630.1
汽轮机铸钢件超声波探伤及质量分级方法JB/T9630.2
3订货要求
供方应有完善的质量保证体系,应具有生产过类似材料、相近尺寸的铸件的业绩3.1
3.2需方应在订货合同或技术协议中注明采用的标准、铸件名称、材料牌号、数量和供货状态、供需双方明确的相应技术要求和检验项目及本标准要求以外的检验项目。3.3需方应提供经双方共同审定的订货图样。3.4需方要求参加现场检验的项目应在订货合同中注明。4制造工艺
4.1治炼
铸件用钢应采用电炉冶炼、钢包精炼工艺。经需方同意,也可采用保证质量的其他冶炼方法。JB/T11018—2010
4.2铸造
在需方无特殊要求时,铸造工艺可由供方自行确定,但不得使用芯撑和内冷铁。4.3热处理
4.3.1铸件应进行热处理。通常情况下,热处理由供方进行。热处理时为保证炉温的均匀性,可在铸件表面上放置外接热电偶。当需方无特殊要求时,在铸件表面上放置外接热电偶的位置、数量可由供方决定。4.3.2推荐的铸件的预备热处理和性能热处理规范见表1。表1铸件热处理规范(推荐)
材料牌号
ZG10Cr9Mo1VNbN
ZG12Cr9Mo1VNbN
ZG12Cr10MoVNbN
ZG11Cr10Mo1NiWVNbN
ZG13Cr11MoVNbN
ZG14Cr10MoVNbN
ZG12Cr10Mo1W1NbN-1
ZG12Cr10Mo1W1NbN-2
ZG12Cr10Mo1W1NbN-3
热处理规范
1)进行预备热处理的铸件加热到≥1050℃,保持足够时间,然后炉冷到300℃以下空冷
2)进行性能热处理的铸件加热到1040℃,保持足够时间,风冷或空冷+一次或二次间火(加热温度在Ac,点以下)1)进行预备热处理的铸件加热到≥1050℃,保持足够时间,然后炉冷到300℃以下空冷
2)进行性能热处理的铸件加热到1010℃,保持足够时间,风冷或空冷+一次或二次回火(加热温度在Ac,点以下)1)进行性能热处理的铸件加热到≥】050℃C,保持足够时间,然后炉冷到300℃以下空冷
2)进行性能热处理的铸件加热到1010℃,保持足够时间,风冷或空冷+二次回火(加热温度≥700℃)
1)进行性能热处理的铸件加热到≥1080℃,保持足够时间,然后炉冷到300℃以下空冷
2)进行性能热处理的铸件加热到≥1080℃,保持足够时间,风冷或空冷+二次回火(加热温度≥720℃)
4.3.3铸件在粗加工、焊接及补焊后均应进行消除应力热处理。最终消除应力热处理应在大于或等于690℃的温度下进行。
4.3.4除预备热处理和性能热处理外,通常铸件的回火温度应高于消除应力温度10℃以上。4.4缺陷清除及补焊
4.4.1铸件应在软化退火后清除表面可见缺陷。缺陷清除可采用机械加工、打磨或电弧气刨等方式。4.4.2允许对铸件中的超标缺陷进行补焊修复,补焊前应将缺陷全部清除干净,并应经无损检测确认清除结果。
4.4.3补焊应在性能热处理后,最终热处理之前进行,补焊应使用与铸件材料相同或相近[Cr含量(质量分数)应为9%~14%1的焊接材料进行。4.4.4最终热处理后原则上不应再进行补焊,如果有少量缺陷必须补焊,则焊后应进行局部消除应力热处理并作记录。
4.4.5供方进行焊接或补焊操作时,应对缺陷部位予以记录。焊工应具有资格证书。补焊工艺应经过焊接工艺评定。
5技术要求
5.1化学成分
5.1.1供方应对每炉钢水进行熔炼分析,分析结果应符合表2的规定。5.1.2当需方有要求时,可以进行成品化学成分分析。铸件的成品化学成分分析结果应符合表2的规定,但允许存在表3规定的偏差,5.1.3供方应进行气体含量分析。当无特殊要求时,气体含量的分析结果应符合表4的规定。2
材料牌号
ZG10Cr9MoIVNbN
ZG12Cr9Mo1VNbN
ZG11Cr10MoVNbN
ZG13Cr11IMoVNbN
ZG14Cr10MoVNbN
ZG11Cr10Mo1NiWVNbN
ZG12Cr10Mo1W1VNbN-1
ZG12Cr10MoIW1VNbN-2
ZG12Cr10Mo/W1VNbN-3
注1:ZG11Cr10MoINiWVNbN的铬当益为7.5~10.5,注2:ZG13CrIIMoVNbN的铬当量为8~10,Cr
化学成分(质量分数)
铬当量=Cr40C-2Mn-4Ni+6Si+4Mo+1IV+SNb30N+1.5W。络当量-C
40C2Mn4Ni+6Si+4Mo+1IV+5Nb30N,注3:ZG14CrI0MoVNbN的铬当量为<9,铬当量Cr-40C2Mn4Ni+6Si+4Mo+11V+5Nb30N。注4:残余元素含量的测定,露方无要求时,仅作参考。
(目标)
残金元素
记录记录
JB/T11018—2010
JB/T11018—2010
材料牌号
ZG10Cr9Mo1VNbN
ZG12Cr9Mo1VNbN
ZG11Cr10MoVNbN
ZG13Cr11MoVNbN
ZG14Cr10MoVNbN
成品化学成分
质量分数
0.10~0.15
8.00~11.50
0.60~1.30
0.02~0.07
ZG11Cr11Mo1NiWVNbN
ZG12Cr10Mo!W1VNbN-!
ZG12Cr1GMo1W1VNbN-2
ZG12Cr10Mo1W1VNbN-3
(质量分数)自
的允许偏差
超出上限或低于下限的极限偏差值-0.005
气体含量(体积分数)
≤3×10-(目标值)
≤7×10
力学性能
经最终热处理后的铸件的力学性能应符合表5的规定。5.2.1
力学性能
材料牌号
ZG10Cr9Mo1VNbN
ZG12Cr9Mo1VNbN
ZG11Cr10MoVNbN
ZG13Cr11MoVNbN
ZG14Cr10MoVNbN
ZG11Cr10Mo1NiWVNbN
ZG12Cr10Mo1W1VNbN-1
ZG12Cr10Mo1W1VNbN-2
ZG12Cr10Mo1WIVNbN-3
585~760
630~750
≥680
≥689
≥700
≥685
680~850
680~850
680~850
≥500
≥516(Ro0.02)
≥500(Rp0.02)
≥490(Rpo.02)
≥520
≥>17
≤70×10-(目标值)
90×10
≥65(Aku)
≥30(Aku)
FATTso
《121
≤260
≤260
≤260
≤260
≤260
JB/T11018-2010
5.2.2焊后最终消应热处理后应再次进行力学性能试验,试验结果应符合表5的要求。5.2.3当需方有要求,并且在铸件首件生产或热处理.1.艺发生重大变化时可以做高温持久性能试验和高温拉伸性能试验
5.2.4铸件首件制造时应进行韧脆转变温度试验,试验结果仅作为参考。5.3显微组织
铸件在热处理合格后应进行金相分析,显微组织中的铁素体含量应在5%以下。5.4表面质量
5.4.1铸件的表面质量应符合订货图样规定。如图样未作规定,则铸件的表面粗糙度Ra值应达到100μm。
5.4.2需作无损检测的铸件加工面的表面粗糙度Ra值应达到6.3um,非加工面的表面粗糙度Ra值应达到12.5μm。下载标准就来标准下载网
5.4.3铸件表面不允许存在裂纹、冷隔、气孔和粘砂等铸造缺陷。5.4.4铸件的表面清洁度应符合订货图样规定。当图样中未对表面清洁度作出规定时,高中压气缸内缸、阀体的内壁应符合JB/T4058一1999中洁-2的要求。5.5无损检测
5.5.1铸件应进行无损检测。检测的标准、部位和验收的质量等级由供需双方在订货时协商决定。5.5.2铸件不允许存在的缺陷应予以记录。5.5.3铸件的补焊处仍应按本体规定的质量要求进行无损检测。5.6形状和尺寸公差
5.6.1铸件的尺寸公差应符合订货图样规定,如图样中未作规定,则应符合GB/T6414一1999中CT14级的规定。
5.6.2铸件的壁厚应符合订货图样规定。如图样中未作规定,则应符合GB/T6414一1999中CT15级的规定。
5.7重量公差
铸件的重量公差应符合GB/T11351的规定。除订货合同有要求外,铸件的重量公差不作考核。6试验方法和检验规则
6.1化学成分分析
6.1.1供需双方没有特别约定时,化学成分分析试样应以钢包熔炼试样为准。6.1.2化学成分分析的取样方法按GB/T20066的规定进行,化学成分分析的分析方法按GB/T223的规定进行。
6.2力学性能试验
6.2.1力学性能试验的试样应从附铸试块制取,试样形状和尺寸应符合GB/T228的规定。6.2.2附铸试块的部位和形状由供方自行决定,当需方有特殊要求时,由供需双方协商决定。6.2.3力学性能试验用附铸试块应随其所代表的铸件同炉热处理。在没有特殊规定时,铸件重量小于1000kg时,每一熔炼炉次和每一热处理炉次至少取一个拉伸试样,三个冲击试样;铸件重量大于1000kg时,每个铸件都要取一个拉伸试样和三个冲击试样单独进行试验。6.2.4拉伸试验应按GB/T228的规定进行,冲击试验应按GB/T229的规定进行。对于冲击试验,一组三个冲击试验结果的平均值应符合表5的规定,最多允许其中一个试验结果低于规定值,但不应低于规定值的70%(另有规定的除外)。6.2.5硬度试验应按GB/T231.1的规定执行,无特殊说明时,硬度为试样测定值。6.2.6韧脆转变温度试验中,冲击试样断口上各区所占面积的评定应按GB/T229的规定执行。6.2.7高温持久性能试验应按附录A的规定进行。5
JB/T11018—2010
3高温拉伸性能试验应按附录A的规定进行。6.2.8
6.3表面质量检测
表面粗糙度的评定应按GB/T6060.1的规定进行。6.4无损检测
6.4.1一般要求
铸件在无损检测之前应按规定做好表面准备,对超标缺陷应予以记录。6.4.2超声检测
铸件超声检测应按JB/T9630.2的规定进行,或供需双方另行协商。6.4.3磁粉检测
铸件表面磁粉检测应按JB/T9630.1的规定进行,或供需双方另行协商。6.4.4渗透检测
铸件表面渗透检测应按GB/T9443的规定进行,或供需双方另行协商。6.5复试和重新热处理
6.5.1当力学性能试验结果不合格时,允许进行复试。复试应按以下要求进行:a)拉伸试验的复试应从靠近不合格试样的相邻位置取双倍试样重新做不合格项目的试验,重新试验的结果应满足表5的规定要求。若复试中有一个结果仍不合格,则其所代表的铸件连同备用试料应重新进行热处理;
b)冲击试验复试应从靠近不合格试样的相邻位置取样制备三个冲击试样进行,每个复试结果都应等于或超过表5的规定值。否则其所代表的铸件连同备用试料应重新进行热处理。6.5.2显微组织检验结果不合格时,则其所代表的铸件连同备用附铸试块应重新进行热处理。重新热处理后,按6.2.1~6.3的规定重新试验、重新验收6.5.3不包括回火在内的重新热处理次数不得超过两次。7验收及质量证明书
7.1验收
7.1.1供方应为需方验收人员提供必要的条件,以便于需方验收人员进行现场检验工作。需方检验人员不应对供方的生产造成不必要的妨碍7.1.2需方有权选择铸件的某些试验项目进行验收。在验收以后的加工或检验中,发现铸件不符合本标准和订货合同中规定的补充技术要求条款时,需方应及时通知供方,双方协商解决。7.2质量证明书
7.2.1交货时,供方必须向需方提供质量证明书。质量证明书应包括下列内容:a)订货合同号;
b)图号;
c)铸件名称;
d)重量;
e)材料牌号;
f)铸件识别号或熔炼炉号;
g)化学成分分析试验报告和力学性能试验报告等;h)热处理状态、热处理曲线记录、热处理炉批号:i)无损检测报告;
j)尺寸检验记录:
k)合同和技术协议有要求的其他检验报告。7.2.2质量证明书应有供方质量部门和负责人的签章。6
标识和包装
铸件应有供方标识、订货合同号、图号等标识内容。供方应根据运输条件要求进行包装。JB/T11018—2010
小提示:此标准内容仅展示完整标准里的部分截取内容,若需要完整标准请到上方自行免费下载完整标准文档。

标准图片预览:
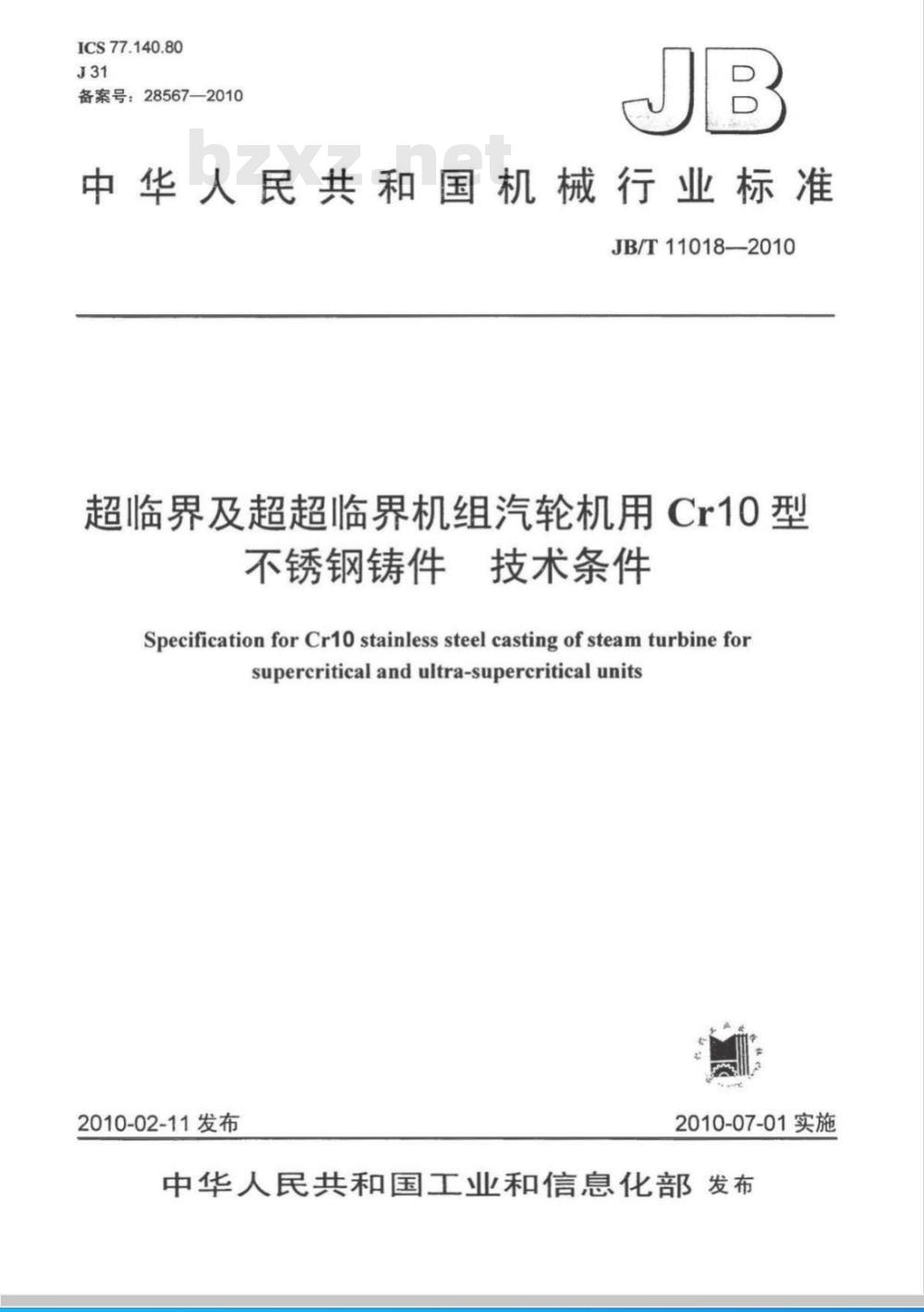
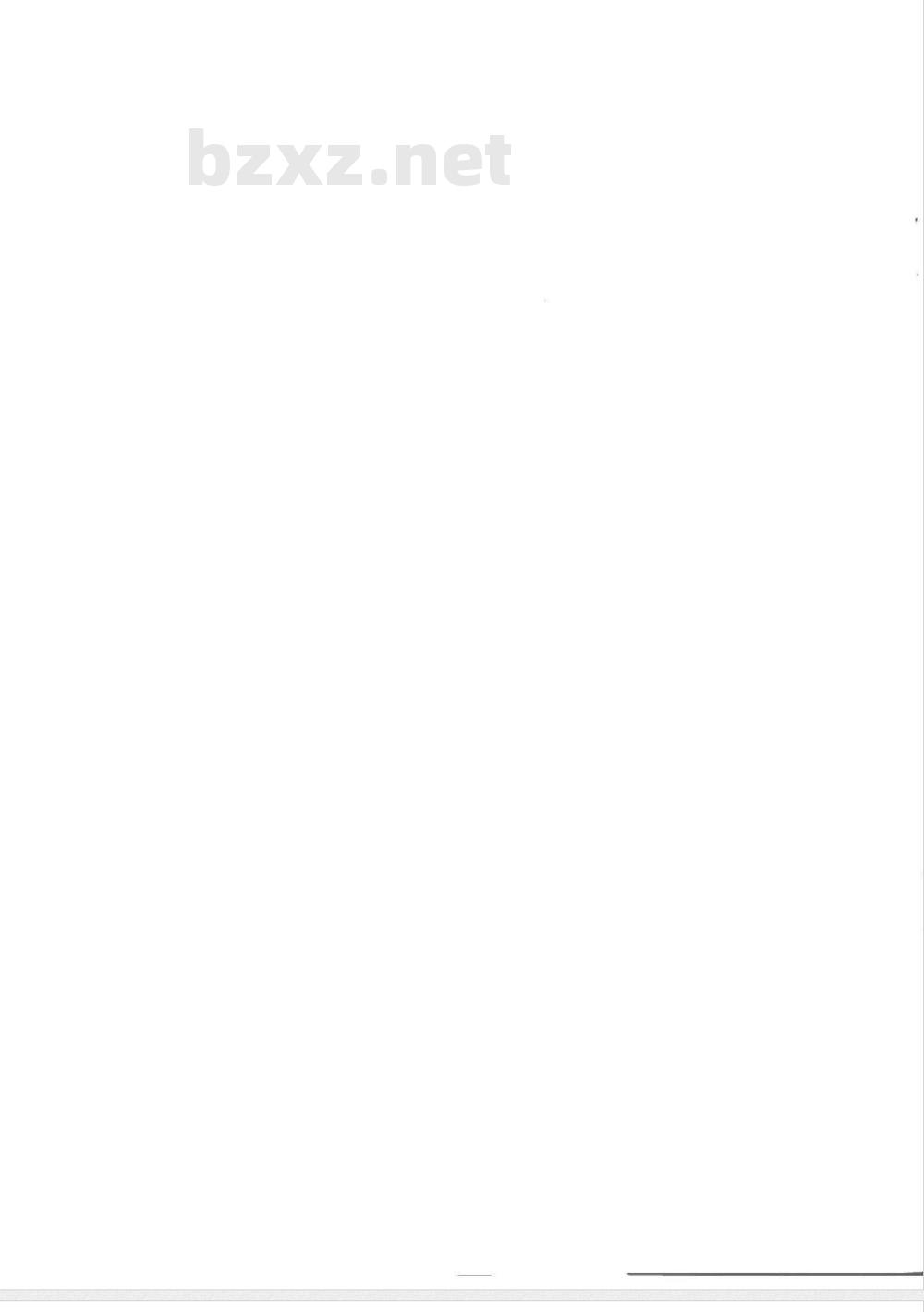
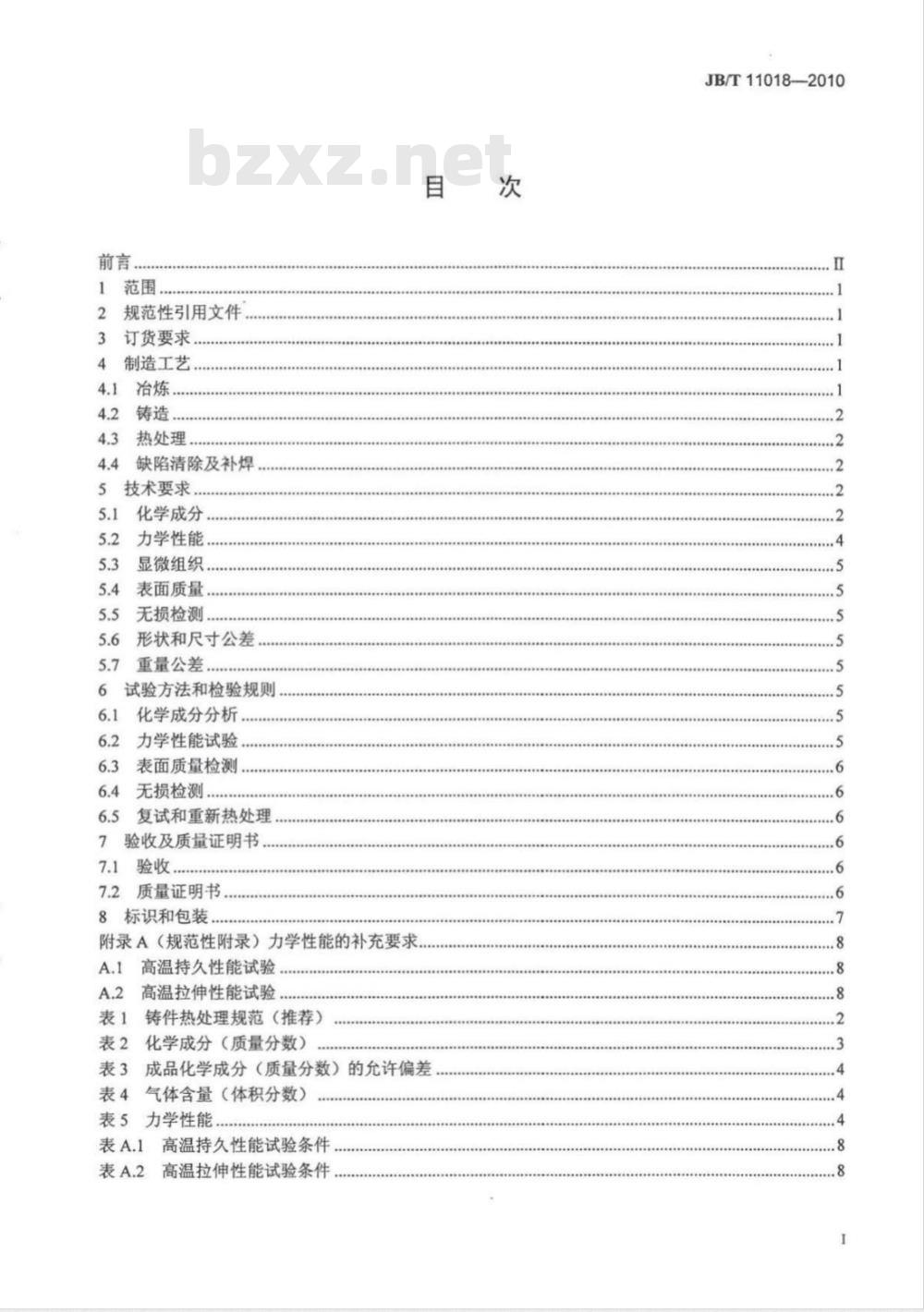
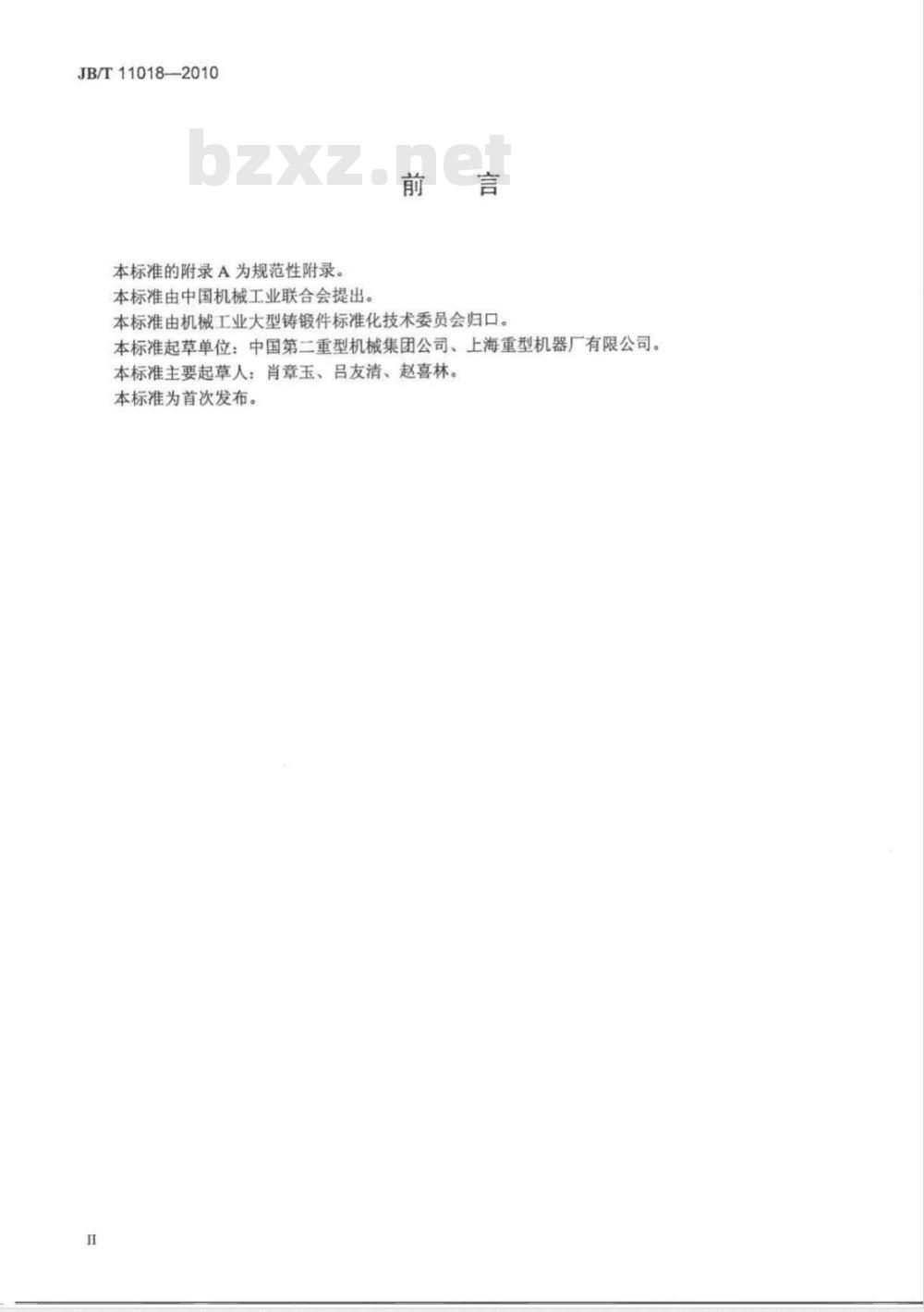
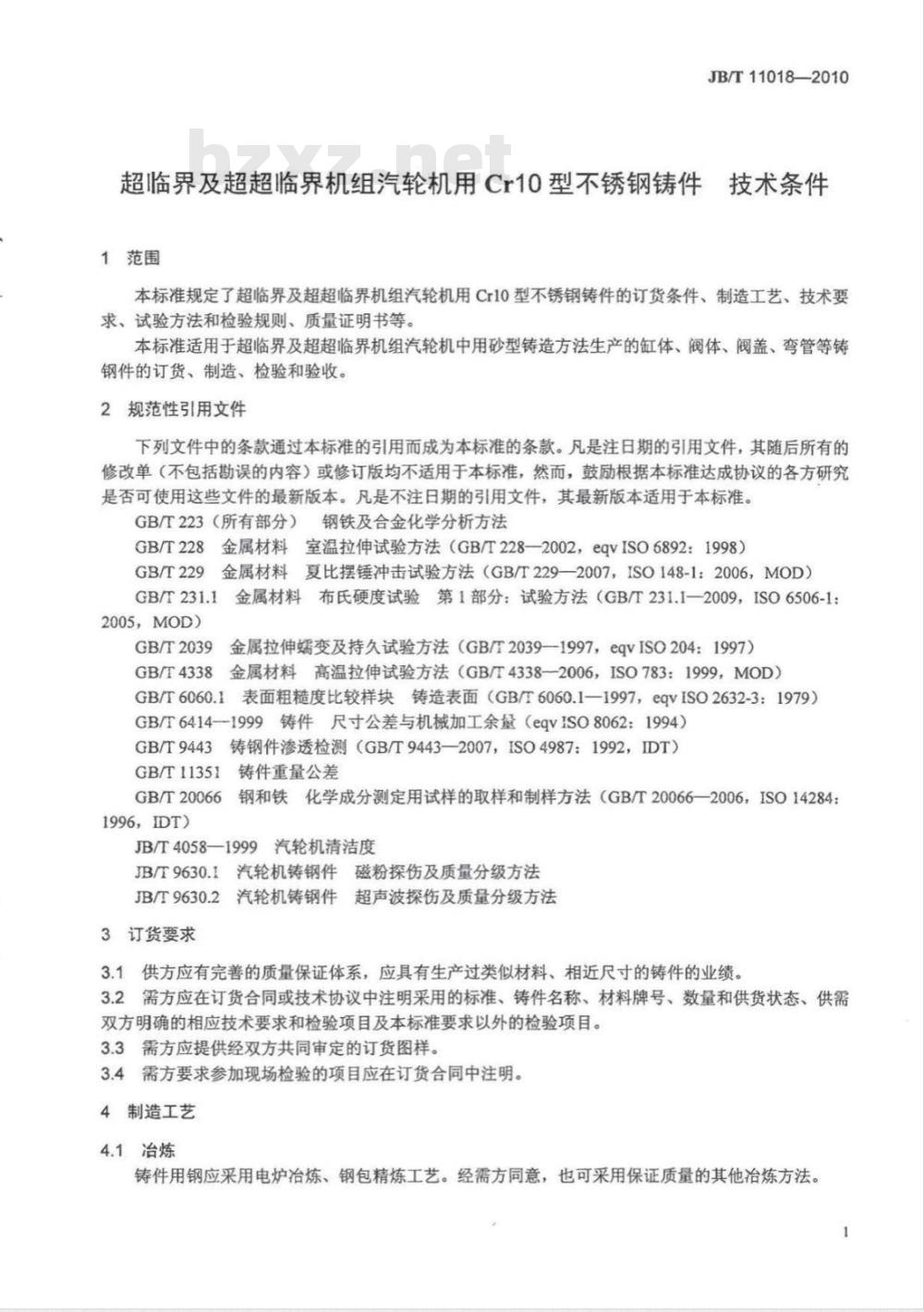
- 热门标准
- 机械行业标准(JB)
- JB/T5762.2-2006 转塔车床 第2部分:精度
- JB/T10719-2007 焊接聚晶金刚石或立方氮化硼槽刀
- JB/T10725-2007 天然金刚石车刀
- JB/T10723-2007 焊接聚晶金刚石或立方氮化硼镗刀
- JB/T8521.1-2007 编织吊索 安全性 第1部分:一般用途合成纤维扁平吊装带
- JB/T5372.6-1991 8mm槽系组合夹具其他件 鳞齿支承螺母
- JB/T7712-2007 高温合金热处理
- JB/T9162.8-1999 表柱 尺寸
- JB/T5371.12-1991 8mm槽系组合夹具压紧件 V形压板
- JB/T5368.18-1991 8mm槽系组合夹具定位件 V形板
- JB/T8746.5-2008 塑料异型材挤出模零件 第5部分:定型块
- JB20024-2004 中药自动制丸机
- JB3930.58-1985 U形角铁
- JB/T5368.16-1991 8mm槽系组合夹具定位件 定位板
- JB1006-1984 汽车燃油箱用槽型盖加注头及连接尺寸
- 行业新闻
请牢记:“bzxz.net”即是“标准下载”四个汉字汉语拼音首字母与国际顶级域名“.net”的组合。 ©2009 标准下载网 www.bzxz.net 本站邮件:bzxznet@163.com
网站备案号:湘ICP备2023016450号-1
网站备案号:湘ICP备2023016450号-1