- 您的位置:
- 标准下载网 >>
- 标准分类 >>
- 铁路运输行业标准(TB) >>
- TB/T 1818-2009 机车、动车用柴油机零部件 连杆
标准号:
TB/T 1818-2009
标准名称:
机车、动车用柴油机零部件 连杆
标准类别:
铁路运输行业标准(TB)
标准状态:
现行-
发布日期:
2009-11-11 出版语种:
简体中文下载格式:
.rar .pdf下载大小:
2.39 MB
替代情况:
替代TB/T 1818-1987

部分标准内容:
ICS 45.060.10
中华人民共和国铁道行业标准
TB/T1818—2009
代替TB/T1818-1987
机车、动车用柴油机零部件
Components of diesel engine for locomotive and rail carConnectingrod
2009-11-11发布
2010-05-01实施
中华人民共和国铁道部发 布
规范性引用文件
技术要求
检验方法
验收规则
标志、包装和贮存
TB/T1818-2009
TB/T1818-2009
本标准代替TB/T1818-1987《内燃机车用柴油机连杆技术条件》。本标准与TB/T1818一1987相比主要变化如下:-增加了范围、规范性引用文件;-删除了“名词术语”的全部内容;调整了“技术要求”的相关内容;-明确了对连杆原材料、毛坏及成品的检验(测)方法和要求;一增加了数据修约的依据等内容;一取消了保用期条款,增加了贮存期的要求。本标准由铁道行业内燃机车标准化技术委员会提出并归口。本标准起草单位:南车资阳机车有限公司、南车戚墅堰机车有限公司、南车四方机车车辆股份有限公司、中国北车集团大连机车车辆有限公司、北京二七轨道交通装备有限责任公司。本标准主要起草人:杨军、万虎、曾省建、杨林生、王浩、张建平。本标准所代替标准的历次版本发布情况:TB/T1818—1987。
1范围
机车、动车用柴油机零部件连杆TB/T1818-2009
本标准规定了机车、动车用柴油机连杆(包括连杆体和连杆盖,下同)的技术要求、检验方法、验收规则及标志、包装和贮存等。
本标准适用于新造的锻钢连杆的设计、制造与验收。2规范性引用文件
下列文件中的条款通过本标准的引用而成为本标准的条款。凡是注日期的引用文件,其随后所有的修改单(不包括勘误的内容)或修订版均不适用于本标准,然而,鼓励根据本标准达成协议的各方研究是否可使用这些文件的最新版本。凡是不注日期的引用文件,其最新版本适用于本标准。GB/T228—-2002金属材料室温拉伸试验方法(eqvIS06892:1998)GB/T229—2007金属材料夏比摆锤冲击试验方法(IS0148-1:2006,MOD)GB/T230.1金属洛氏硬度试验第1部分:试验方法(A、B、C、D、E、F、G、H、K、N、T标尺)(GB/T230.1—2004,IS06508-1:1999,M0D)GB/T231.1金属布氏硬度试验第1部分:试验方法(GB/T231.1—2002,eqVISO6506-1:1999)GB/T1184-1996形状与位置公差未注明公差值(eqvIS03768-2:1989)GB/T1800.3一1998极限与配合基础第3部分:标准公差和基本偏差数值表(eqvIS0286-1:1988)
GB/T1800.4一1999极限与配合标准公差等级和孔、轴的极限偏差表(eqvIS0286-2:1988)GB/T1958产品几何技术规范(GPS)形状和位置公差检测规定GB/T2828.1计数抽样检验程序第1部分:按接收质量限(AQL)检索的逐批检验抽样计划(GB/T2828.1—2003,ISO2859-1:1999,IDT)GB/T2975钢及钢产品力学性能试验取样位置及试样制备(GB/T2975—1998,eqVISO377:1997)GB/T3077—1999合金结构钢(neqDINEN10083-1:1991)GB/T8170数值修约规则与极限数值的表示和判断GB/T13320—-2007钢质模锻件金相组织评级图及评定方法GB/T17394金属里氏硬度试验方法JB/T6721.2内燃机连杆第2部分:磁粉探伤JB/T8468
锻钢件磁粉检验方法
JB/T9377
JB/T10659
3技术要求
超声硬度计技术条件
无损检测锻钢材料超声检测连杆的检测连杆应按照经规定程序批准的产品图样及技术文件制造,并应符合本标准的规定。3.2材
3.2.1连杆应采用35CrMo、42CrMo等合金结构钢制造,也可采用满足使用要求的其他钢材制造。3.2.2材料应为压力加工用钢,应具有熔炼炉号并带有质量证明书,其化学成分、力学性能、低倍组1
TB/T1818-2009
织、表面质量、脱碳层及非金属夹杂物等,均应符合CB/T3077一1999中的相应规定。各类非金属夹杂物粗系、细系级别均应小于或等于2.0级;锻件正火后的晶粒度应≤5级。3.2.3材料应依据JB/T10659沿两条相互为90°夹角的轨迹作100%超声波探伤检验,并作探伤记录。
3.3锻造和热处理
3.3.1连杆应采用模锻。
3.3.2连杆剖面的金属宏观组织,其纤维方向应沿着连杆中心线,并与外形相符,不得有紊乱及间断。不允许有折叠、裂纹、分层、夹渣等缺陷。3.3.3连杆热处理后的显微组织应符合GB/T13320—2007中的1~4级。如产品图样上有要求,脱碳层深度应符合产品图样的相关规定。3.3.4连杆表面不应有裂纹、折叠、损伤、结疤、氧化坑点及夹渣等缺陷。在符合下列条件时,允许打磨消除局部缺陷。
a)在锻件的非加工表面上,允许存在的凹坑数不应超过3,凹坑最大直径不应超过10mm,最大允许打磨深度不应超过1mm;凹坑边缘应统一倒圆,倒圆半径不小于10mm。b)在待加工表面上,打磨深度应小于机加工余量的1/2。c)打磨方向应平行于连杆的长度方向,打磨区域与周围区域的连接应圆滑过渡。3.3.5锻件不允许过烧。
注:判断过烧与否,可采用1:1:8的硫酸硝酸混合水溶液试剂进行浸蚀并抛光后(反复3次),在100倍金相显微镜下观察,若晶界呈白色网络状且基体为灰黑色时,视为过烧。3.3.6不允许在锻件的任何部位进行焊补及火焰切割。3.3.7连杆应进行调质处理,然后对所有表面进行喷丸处理。喷丸宜采用急冷铸铁丸粒,丸粒大小应均匀,其最大直径为1.2mm。
3.3.8若连杆毛坏有扭曲变形,允许在热态下作矫直处理。矫直后应进行去应力退火处理,退火温度至少应低于回火温度30℃。
3.3.9所有连杆毛坏均应在去氧化皮和允许的粗加工后,按JB/T8468对全部表面进行磁粉探伤检查。探伤后作退磁处理,剩磁强度不大于0.3mT。3.4连杆的力学性能与要求
3.4.1连杆的力学性能及硬度由连杆产品图样技术要求给出。3.4.2最终热处理后,连杆的力学性能和硬度应达到产品设计的技术要求,而且同一连杆体或连杆盖上的硬度差应小于30HBW或小于25HLD。3.5连杆加工部位的主要线性尺寸公差和形状位置公差3.5.1连杆大头孔的线性尺寸公差不低于GB/T1800.4一1999规定的H6级精度,小头孔的线性尺寸公差不低于GB/T1800.4一1999规定的H7级精度。3.5.2连杆大、小头孔中心距的尺寸公差不低于GB/T1800.3-1998规定的IT8级精度。3.5.3连杆大头孔的圆柱度公差不低于GB/T1184一1996规定的7级精度,小头孔的圆柱度公差不低于GB/T1184—1996规定的8级精度。3.5.4连杆小头孔轴线对大头孔轴线的平行度公差不低于GB/T1184一1996规定的7级精度。3.5.5连杆螺栓孔支承面对螺孔轴线的垂直度公差不低于CB/T1184一1996规定的9级精度。3.6连杆主要加工表面的粗糙度
3.6.1连杆大小头孔表面粗糙度MRRR.1.6μm。3.6.2连杆大头分开面粗糙度MRRR.1.6μm。3.6.3连杆螺栓孔支承面粗糙度MRRR.3.2μm。2
4检验方法
4.1产品实物硬度检验
4.1.1检测部位
连杆大头和小头加工面A处,检测点距边缘距离不小于10mm。如图1所示。图1连杆硬度检测部位
4.1.2检测方法
机械法按GB/T17394进行检测。
TB/T 1818—2009
无损硬度法可使用超声硬度计进行检测,超声硬度计应符合JB/T9377要求,也可用其他无损硬度检测法进行。
4.2力学性能检验
4.2.1试样的截取
4.2.1.1依照GB/T2975,从同一熔炼炉号、同批锻造、同炉热处理的连杆中取其一(包括体和盖),截作力学性能试验的试样,试样应沿连杆的纤维方向截取。4.2.1.2允许用与实物同一熔炼炉号、同批锻造、同炉热处理的模拟试棒代替实物的取样。连杆体的模拟试棒应与其对应的连杆体杆身具有相同的截面;连杆盖的模拟试棒应是与其对应的连杆盖具有相近截面积的矩形试棒,模拟试棒的有效长度均不应小于200mm,且应打上与所代表的实物相同的标识。同一热处理炉次应具备一组(根)模拟试棒。新产品、定期抽检或质量不稳定时,同一热处理炉次应具备三组(根)模拟试棒。截取试样应沿模拟试棒的纤维方向。4.2.2拉伸检验
按GB/T228一2002附录B表B1所列R4号样制作试样;也可根据连杆尺寸或技术要求选用板形试样。允许采用非标准试样。依据GB/T228一2002进行Rm、R.0.2、A、Z等项目试验,试验结果按GB/T8170进行数值修约。
4.2.3冲击检验
按GB/T229--2007中U形缺口深度为2mm的试样要求制作试样。依据GB/T229进行冲击试验。冲击吸收能量KU,至少应保留两位有效数字,修约按GB/T8170执行。4.2.4硬度检验(试样检验)
试样由紧靠拉伸试样余料或拉伸试样残样端部截取,也可使用冲击试样。依据GB/T230.1或GB/T231.1之要求制作。依据GB/T230.1或GB/T231.1进行硬度试验,并按GB/T8170进行数值修约。
复式检验
如果力学性能和硬度试验(试样检验)有一项指标不能满足图样要求时,应取双倍试样进行复试,若有一个试样试验结果仍然不能满足要求时,该批连杆应重新热处理,热处理后重新进行所有各项试验。重复热处理的次数不应多于3次。3
TB/T1818-2009
4.3金相显微组织检验
采用硬度试样或拉伸试样残样端部作为金相试样,用500倍金相显微镜观测显微组织级别,用100倍或更高倍数金相显微镜测量脱碳层深度。4.4表面粗糙度检测
表面粗糙度检测采用表面粗糙度检查仪,测量规定位置的表面粗糙度参数值,也可用其他方法测量。
4.5尺寸检测
4.5.1连杆大小头孔用内径千分表或其他测量仪进行测量。4.5.2大小头孔中心距在平板上用游标高度尺、杠杆千分表和四等量块进行测量,也可用其他方法测量。
4.6形状与位置公差检测
连杆上各主要加工部位的形状和位置公差按GB/T1958进行检测。4.7表面质量检查
连杆的表面质量采用目测方式检查。4.8磁粉探伤检验
连杆应逐根进行磁粉探伤,按JB/T6721.2的规定执行。5验收规则
每根连杆需经制造单位的质量检验部门检查合格后方能流入下道工序或向订货方供货。每根连杆应提供检查记录表,记载材料牌号、熔炼炉号、热处理炉号、成品探伤记录、主要尺寸记录、连杆装配质量及生产编号等。5.2批次检验Www.bzxZ.net
制造单位应按4.1、4.2、4.3等规定的方法,对连杆按照热处理炉号批次进行产品实物硬度、力学性能、金相组织等项目的检验。制造单位应按4.4规定的方法,对连杆按照加工批次进行表面粗糙度检验。5.3成品检验
制造单位应按4.5、4.6、4.7、4.8等规定的方法,对每根连杆的尺寸、形状与位置公差、表面质量、磁粉探伤等项目进行检验。
5.4用户抽检
用户可按照GB/T2828.1的规定对连杆进行抽检,抽检项目及要求由供需双方协商确定。6标志、包装和购存
连杆应按产品图样的要求,在规定部位打印如下标志:a)制造单位代码或标记、生产编号:连杆体和盖的配对号;
c)探伤合格标记;
d)连杆组的重量。
6.2包装
6.2.1连杆体和连杆盖应配对包装,在包装前应仔细清洗并作防锈处理,用结实不透水的中性纸或塑料薄膜包好,再装入衬有防水纸的干燥包装箱内,保证在正常运输过程中不致损伤零件。6.2.2包装箱内应附有制造单位提供的装箱清单、技术证件和检验部门出具的产品质量合格证。4
TB/T·1818—2009
包装箱上应注明制造单位名称、地址、产品型号、名称、数量、总重量、装箱日期,并书写“小心6.2.3
轻放”、“防潮”、“防磁”、“防雨”和堆放层数等字样。6.3贮
连杆应存放在清洁、干燥、无酸碱等腐蚀性物质、通风良好的仓库内。在正常保管情况下,12个月内不致锈蚀。
中华人民共和国
铁道行业标准
机车、动车用柴油机零部件
Components of diesel engine for locomotive and rail carConnecting rod
TB/T1818--2009
中国铁道出版社出版、发行
(100054,北京市宣武区右安门西街8号)读者服务部电话:市电(010)51873174,路电(021)73174中国铁道出版社印刷厂印刷
版权专有侵权必究
开本:880mm×1230mm
印张:0.75字数:10千字
2010年3月第1次印刷
2010年3月第1版
统一书号:15113·.3110
小提示:此标准内容仅展示完整标准里的部分截取内容,若需要完整标准请到上方自行免费下载完整标准文档。
中华人民共和国铁道行业标准
TB/T1818—2009
代替TB/T1818-1987
机车、动车用柴油机零部件
Components of diesel engine for locomotive and rail carConnectingrod
2009-11-11发布
2010-05-01实施
中华人民共和国铁道部发 布
规范性引用文件
技术要求
检验方法
验收规则
标志、包装和贮存
TB/T1818-2009
TB/T1818-2009
本标准代替TB/T1818-1987《内燃机车用柴油机连杆技术条件》。本标准与TB/T1818一1987相比主要变化如下:-增加了范围、规范性引用文件;-删除了“名词术语”的全部内容;调整了“技术要求”的相关内容;-明确了对连杆原材料、毛坏及成品的检验(测)方法和要求;一增加了数据修约的依据等内容;一取消了保用期条款,增加了贮存期的要求。本标准由铁道行业内燃机车标准化技术委员会提出并归口。本标准起草单位:南车资阳机车有限公司、南车戚墅堰机车有限公司、南车四方机车车辆股份有限公司、中国北车集团大连机车车辆有限公司、北京二七轨道交通装备有限责任公司。本标准主要起草人:杨军、万虎、曾省建、杨林生、王浩、张建平。本标准所代替标准的历次版本发布情况:TB/T1818—1987。
1范围
机车、动车用柴油机零部件连杆TB/T1818-2009
本标准规定了机车、动车用柴油机连杆(包括连杆体和连杆盖,下同)的技术要求、检验方法、验收规则及标志、包装和贮存等。
本标准适用于新造的锻钢连杆的设计、制造与验收。2规范性引用文件
下列文件中的条款通过本标准的引用而成为本标准的条款。凡是注日期的引用文件,其随后所有的修改单(不包括勘误的内容)或修订版均不适用于本标准,然而,鼓励根据本标准达成协议的各方研究是否可使用这些文件的最新版本。凡是不注日期的引用文件,其最新版本适用于本标准。GB/T228—-2002金属材料室温拉伸试验方法(eqvIS06892:1998)GB/T229—2007金属材料夏比摆锤冲击试验方法(IS0148-1:2006,MOD)GB/T230.1金属洛氏硬度试验第1部分:试验方法(A、B、C、D、E、F、G、H、K、N、T标尺)(GB/T230.1—2004,IS06508-1:1999,M0D)GB/T231.1金属布氏硬度试验第1部分:试验方法(GB/T231.1—2002,eqVISO6506-1:1999)GB/T1184-1996形状与位置公差未注明公差值(eqvIS03768-2:1989)GB/T1800.3一1998极限与配合基础第3部分:标准公差和基本偏差数值表(eqvIS0286-1:1988)
GB/T1800.4一1999极限与配合标准公差等级和孔、轴的极限偏差表(eqvIS0286-2:1988)GB/T1958产品几何技术规范(GPS)形状和位置公差检测规定GB/T2828.1计数抽样检验程序第1部分:按接收质量限(AQL)检索的逐批检验抽样计划(GB/T2828.1—2003,ISO2859-1:1999,IDT)GB/T2975钢及钢产品力学性能试验取样位置及试样制备(GB/T2975—1998,eqVISO377:1997)GB/T3077—1999合金结构钢(neqDINEN10083-1:1991)GB/T8170数值修约规则与极限数值的表示和判断GB/T13320—-2007钢质模锻件金相组织评级图及评定方法GB/T17394金属里氏硬度试验方法JB/T6721.2内燃机连杆第2部分:磁粉探伤JB/T8468
锻钢件磁粉检验方法
JB/T9377
JB/T10659
3技术要求
超声硬度计技术条件
无损检测锻钢材料超声检测连杆的检测连杆应按照经规定程序批准的产品图样及技术文件制造,并应符合本标准的规定。3.2材
3.2.1连杆应采用35CrMo、42CrMo等合金结构钢制造,也可采用满足使用要求的其他钢材制造。3.2.2材料应为压力加工用钢,应具有熔炼炉号并带有质量证明书,其化学成分、力学性能、低倍组1
TB/T1818-2009
织、表面质量、脱碳层及非金属夹杂物等,均应符合CB/T3077一1999中的相应规定。各类非金属夹杂物粗系、细系级别均应小于或等于2.0级;锻件正火后的晶粒度应≤5级。3.2.3材料应依据JB/T10659沿两条相互为90°夹角的轨迹作100%超声波探伤检验,并作探伤记录。
3.3锻造和热处理
3.3.1连杆应采用模锻。
3.3.2连杆剖面的金属宏观组织,其纤维方向应沿着连杆中心线,并与外形相符,不得有紊乱及间断。不允许有折叠、裂纹、分层、夹渣等缺陷。3.3.3连杆热处理后的显微组织应符合GB/T13320—2007中的1~4级。如产品图样上有要求,脱碳层深度应符合产品图样的相关规定。3.3.4连杆表面不应有裂纹、折叠、损伤、结疤、氧化坑点及夹渣等缺陷。在符合下列条件时,允许打磨消除局部缺陷。
a)在锻件的非加工表面上,允许存在的凹坑数不应超过3,凹坑最大直径不应超过10mm,最大允许打磨深度不应超过1mm;凹坑边缘应统一倒圆,倒圆半径不小于10mm。b)在待加工表面上,打磨深度应小于机加工余量的1/2。c)打磨方向应平行于连杆的长度方向,打磨区域与周围区域的连接应圆滑过渡。3.3.5锻件不允许过烧。
注:判断过烧与否,可采用1:1:8的硫酸硝酸混合水溶液试剂进行浸蚀并抛光后(反复3次),在100倍金相显微镜下观察,若晶界呈白色网络状且基体为灰黑色时,视为过烧。3.3.6不允许在锻件的任何部位进行焊补及火焰切割。3.3.7连杆应进行调质处理,然后对所有表面进行喷丸处理。喷丸宜采用急冷铸铁丸粒,丸粒大小应均匀,其最大直径为1.2mm。
3.3.8若连杆毛坏有扭曲变形,允许在热态下作矫直处理。矫直后应进行去应力退火处理,退火温度至少应低于回火温度30℃。
3.3.9所有连杆毛坏均应在去氧化皮和允许的粗加工后,按JB/T8468对全部表面进行磁粉探伤检查。探伤后作退磁处理,剩磁强度不大于0.3mT。3.4连杆的力学性能与要求
3.4.1连杆的力学性能及硬度由连杆产品图样技术要求给出。3.4.2最终热处理后,连杆的力学性能和硬度应达到产品设计的技术要求,而且同一连杆体或连杆盖上的硬度差应小于30HBW或小于25HLD。3.5连杆加工部位的主要线性尺寸公差和形状位置公差3.5.1连杆大头孔的线性尺寸公差不低于GB/T1800.4一1999规定的H6级精度,小头孔的线性尺寸公差不低于GB/T1800.4一1999规定的H7级精度。3.5.2连杆大、小头孔中心距的尺寸公差不低于GB/T1800.3-1998规定的IT8级精度。3.5.3连杆大头孔的圆柱度公差不低于GB/T1184一1996规定的7级精度,小头孔的圆柱度公差不低于GB/T1184—1996规定的8级精度。3.5.4连杆小头孔轴线对大头孔轴线的平行度公差不低于GB/T1184一1996规定的7级精度。3.5.5连杆螺栓孔支承面对螺孔轴线的垂直度公差不低于CB/T1184一1996规定的9级精度。3.6连杆主要加工表面的粗糙度
3.6.1连杆大小头孔表面粗糙度MRRR.1.6μm。3.6.2连杆大头分开面粗糙度MRRR.1.6μm。3.6.3连杆螺栓孔支承面粗糙度MRRR.3.2μm。2
4检验方法
4.1产品实物硬度检验
4.1.1检测部位
连杆大头和小头加工面A处,检测点距边缘距离不小于10mm。如图1所示。图1连杆硬度检测部位
4.1.2检测方法
机械法按GB/T17394进行检测。
TB/T 1818—2009
无损硬度法可使用超声硬度计进行检测,超声硬度计应符合JB/T9377要求,也可用其他无损硬度检测法进行。
4.2力学性能检验
4.2.1试样的截取
4.2.1.1依照GB/T2975,从同一熔炼炉号、同批锻造、同炉热处理的连杆中取其一(包括体和盖),截作力学性能试验的试样,试样应沿连杆的纤维方向截取。4.2.1.2允许用与实物同一熔炼炉号、同批锻造、同炉热处理的模拟试棒代替实物的取样。连杆体的模拟试棒应与其对应的连杆体杆身具有相同的截面;连杆盖的模拟试棒应是与其对应的连杆盖具有相近截面积的矩形试棒,模拟试棒的有效长度均不应小于200mm,且应打上与所代表的实物相同的标识。同一热处理炉次应具备一组(根)模拟试棒。新产品、定期抽检或质量不稳定时,同一热处理炉次应具备三组(根)模拟试棒。截取试样应沿模拟试棒的纤维方向。4.2.2拉伸检验
按GB/T228一2002附录B表B1所列R4号样制作试样;也可根据连杆尺寸或技术要求选用板形试样。允许采用非标准试样。依据GB/T228一2002进行Rm、R.0.2、A、Z等项目试验,试验结果按GB/T8170进行数值修约。
4.2.3冲击检验
按GB/T229--2007中U形缺口深度为2mm的试样要求制作试样。依据GB/T229进行冲击试验。冲击吸收能量KU,至少应保留两位有效数字,修约按GB/T8170执行。4.2.4硬度检验(试样检验)
试样由紧靠拉伸试样余料或拉伸试样残样端部截取,也可使用冲击试样。依据GB/T230.1或GB/T231.1之要求制作。依据GB/T230.1或GB/T231.1进行硬度试验,并按GB/T8170进行数值修约。
复式检验
如果力学性能和硬度试验(试样检验)有一项指标不能满足图样要求时,应取双倍试样进行复试,若有一个试样试验结果仍然不能满足要求时,该批连杆应重新热处理,热处理后重新进行所有各项试验。重复热处理的次数不应多于3次。3
TB/T1818-2009
4.3金相显微组织检验
采用硬度试样或拉伸试样残样端部作为金相试样,用500倍金相显微镜观测显微组织级别,用100倍或更高倍数金相显微镜测量脱碳层深度。4.4表面粗糙度检测
表面粗糙度检测采用表面粗糙度检查仪,测量规定位置的表面粗糙度参数值,也可用其他方法测量。
4.5尺寸检测
4.5.1连杆大小头孔用内径千分表或其他测量仪进行测量。4.5.2大小头孔中心距在平板上用游标高度尺、杠杆千分表和四等量块进行测量,也可用其他方法测量。
4.6形状与位置公差检测
连杆上各主要加工部位的形状和位置公差按GB/T1958进行检测。4.7表面质量检查
连杆的表面质量采用目测方式检查。4.8磁粉探伤检验
连杆应逐根进行磁粉探伤,按JB/T6721.2的规定执行。5验收规则
每根连杆需经制造单位的质量检验部门检查合格后方能流入下道工序或向订货方供货。每根连杆应提供检查记录表,记载材料牌号、熔炼炉号、热处理炉号、成品探伤记录、主要尺寸记录、连杆装配质量及生产编号等。5.2批次检验Www.bzxZ.net
制造单位应按4.1、4.2、4.3等规定的方法,对连杆按照热处理炉号批次进行产品实物硬度、力学性能、金相组织等项目的检验。制造单位应按4.4规定的方法,对连杆按照加工批次进行表面粗糙度检验。5.3成品检验
制造单位应按4.5、4.6、4.7、4.8等规定的方法,对每根连杆的尺寸、形状与位置公差、表面质量、磁粉探伤等项目进行检验。
5.4用户抽检
用户可按照GB/T2828.1的规定对连杆进行抽检,抽检项目及要求由供需双方协商确定。6标志、包装和购存
连杆应按产品图样的要求,在规定部位打印如下标志:a)制造单位代码或标记、生产编号:连杆体和盖的配对号;
c)探伤合格标记;
d)连杆组的重量。
6.2包装
6.2.1连杆体和连杆盖应配对包装,在包装前应仔细清洗并作防锈处理,用结实不透水的中性纸或塑料薄膜包好,再装入衬有防水纸的干燥包装箱内,保证在正常运输过程中不致损伤零件。6.2.2包装箱内应附有制造单位提供的装箱清单、技术证件和检验部门出具的产品质量合格证。4
TB/T·1818—2009
包装箱上应注明制造单位名称、地址、产品型号、名称、数量、总重量、装箱日期,并书写“小心6.2.3
轻放”、“防潮”、“防磁”、“防雨”和堆放层数等字样。6.3贮
连杆应存放在清洁、干燥、无酸碱等腐蚀性物质、通风良好的仓库内。在正常保管情况下,12个月内不致锈蚀。
中华人民共和国
铁道行业标准
机车、动车用柴油机零部件
Components of diesel engine for locomotive and rail carConnecting rod
TB/T1818--2009
中国铁道出版社出版、发行
(100054,北京市宣武区右安门西街8号)读者服务部电话:市电(010)51873174,路电(021)73174中国铁道出版社印刷厂印刷
版权专有侵权必究
开本:880mm×1230mm
印张:0.75字数:10千字
2010年3月第1次印刷
2010年3月第1版
统一书号:15113·.3110
小提示:此标准内容仅展示完整标准里的部分截取内容,若需要完整标准请到上方自行免费下载完整标准文档。

标准图片预览:
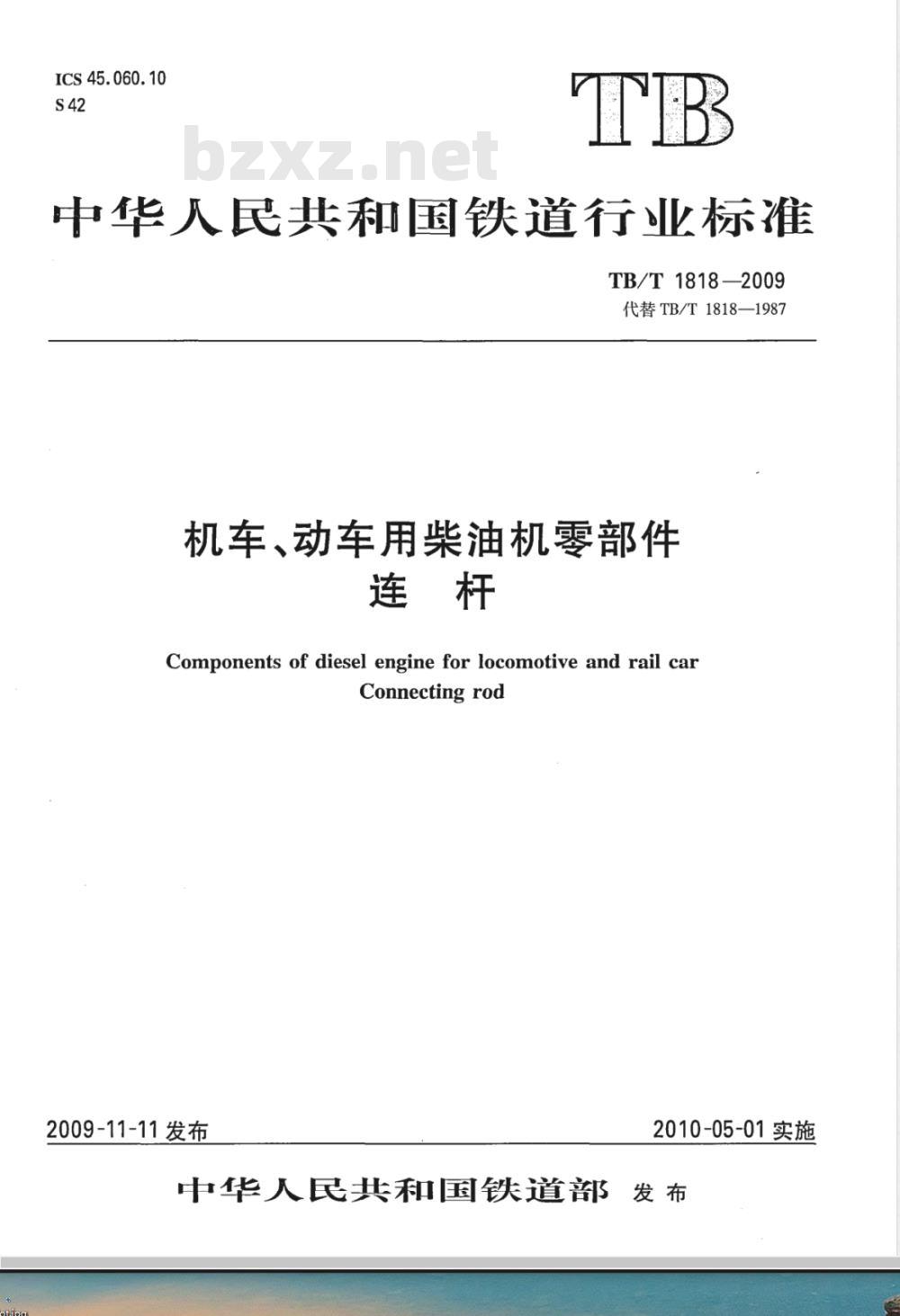
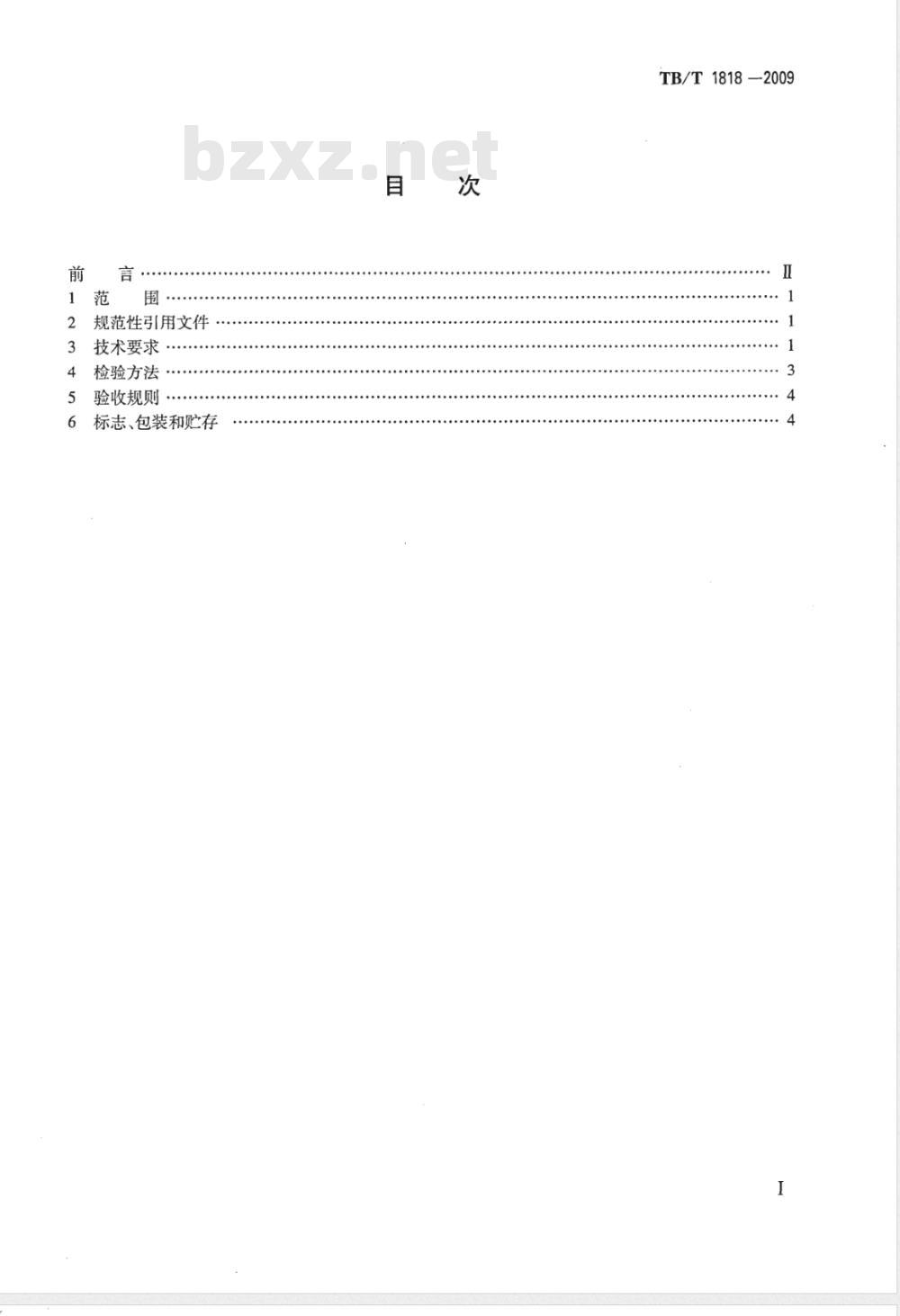
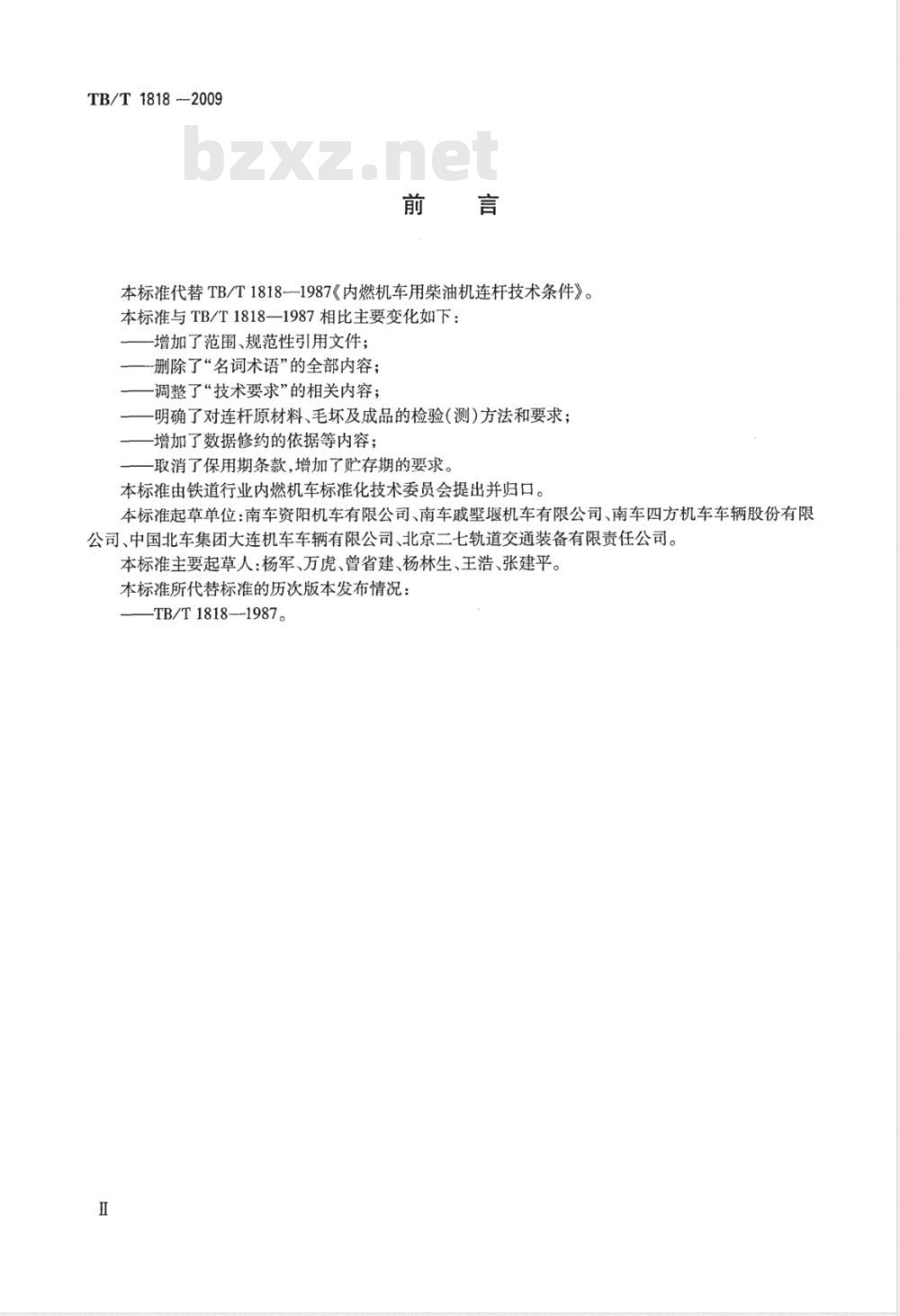
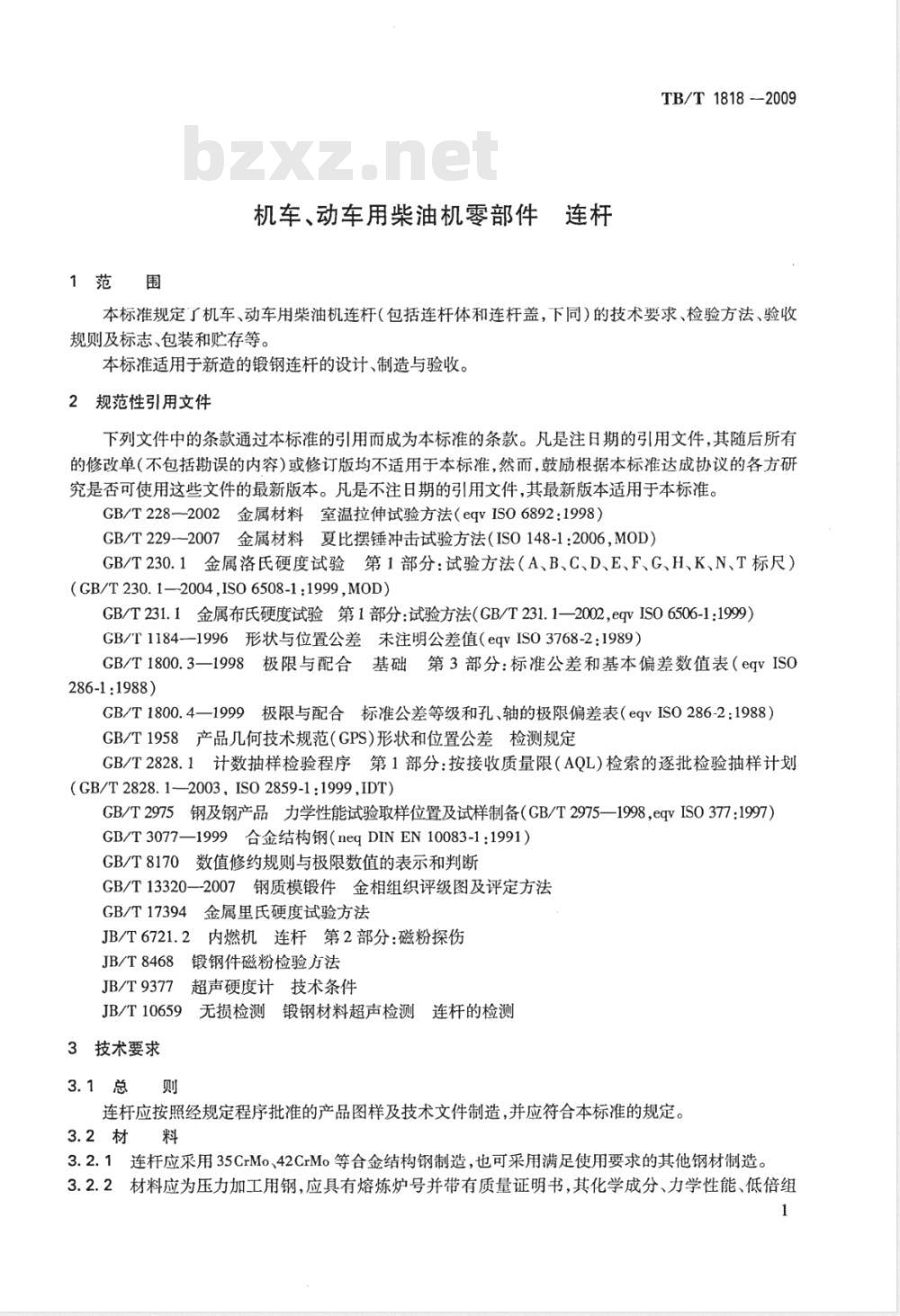
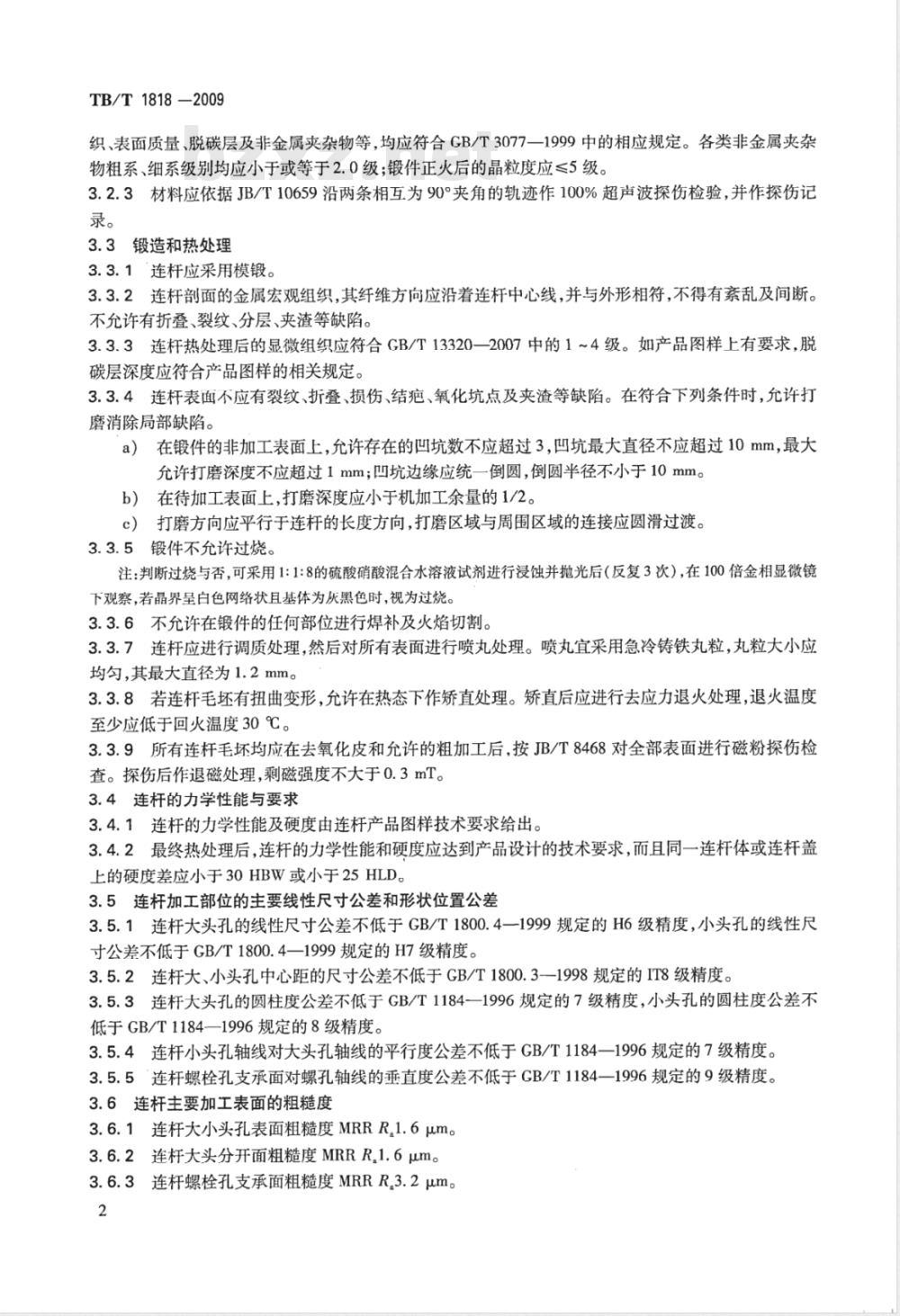
- 热门标准
- 铁路运输行业标准(TB)
- TB10122-2008 铁路路堑边坡光面(预裂)爆破技术规程
- TB/T1760-1986 客车门锁技术条件
- TB/T1632.4-2005 钢轨焊接 第4部分:气压焊接
- TB/T2563-1995 内燃机车用柴油机机体清洁度测定方法
- TB/T3523.2-2018 交流传动电力机车试验方法第2部分:输入特性试验
- TB/T2599-1996 细长钢管内壁涂塑技术条件
- TB/T2769.9-1997 重型轨道车试验方法动力学性能试验方法及评定标准
- TB/T2521-1995 电力机车平波电抗器装车后温升与电感值试验计算方法
- TB/T2820.1-1997 铁路桥隧建筑物劣化评定标准钢梁
- TB/T3416.3-2015 动车组编码标识系统第3部分:安装地点与位置的标识
- TB/T1932-2009 旅客列车卫生及监测技术规定
- TB/T3170-2007 货车车钩、钩尾框采购和验收技术条件
- TB/T1869.4-2013 铁路信号用变压器第4部分:25 Hz系列轨道变压器
- TB/T2472-93D ●S型道口闪光器
- TB/T2658.15-1998 工务作业标准小型线路机械作业
- 行业新闻
请牢记:“bzxz.net”即是“标准下载”四个汉字汉语拼音首字母与国际顶级域名“.net”的组合。 ©2009 标准下载网 www.bzxz.net 本站邮件:bzxznet@163.com
网站备案号:湘ICP备2023016450号-1
网站备案号:湘ICP备2023016450号-1