- 您的位置:
- 标准下载网 >>
- 标准分类 >>
- 有色金属行业标准(YS) >>
- YS/T 209-1994 硅材料原生缺陷图谱
标准号:
YS/T 209-1994
标准名称:
硅材料原生缺陷图谱
标准类别:
有色金属行业标准(YS)
标准状态:
现行-
发布日期:
1987-06-25 -
实施日期:
1988-03-01 出版语种:
简体中文下载格式:
.rar.pdf下载大小:
14.21 MB
替代情况:
原标准号GBn 266-87

部分标准内容:
669.782:620.191/.192
中华人民共和国国家标准
CBn 26687
yS/T 209 —94
上海市战求益督情研究所
登话号07971909
硅材料原生缺陷图谱
中国有色全属行
工业总公司
最研究
标准资料专用章
1987-06-25发布
1988-03-01实施
国家标准局发布
中华人民共和国国家标准
硅材料原生缺陷图谱
UDC669.782:620
.191/.192
Y5(12-94
优精GBn 266-87
本标准规定了硅多晶、单晶、切磨抛片和外延片等硅材料的各种原生缺陷及其密切相关的某些诱生缺陷的形貌特征。
本标准适用硅多晶、单晶、切磨抛片和外延片等硅材料生产研究中各种缺陷的检验。硅器件、大规模和超大规模集成电路的生产研究也可参考本标准。本标准中所用图(片),请见中国有色金属工业总公司标准计量所所印制的照片。1硅多晶结构的不完整性
1.1多晶的外观形态
由三氯氢硅(SiHCl:)或四氯化硅(SiC1)氢还原法和硅烷(SiH)热分解法生长的硅多晶表面致密度和晶粒大小,因生长条件的差异有所不同(见图1~8)。一般来讲,沉积速率过快,温度过高,易造成颗粒粗大。
1.2温度圈
1.2.1特征
硅多晶横断面上,晶粒呈枝蔓状或径向辐射生长(见图9~11)。但有时可以观察到以硅芯为中心的年轮状结构,称为温度圈(见图12~16)。它是由于结晶致密度(指SiHC13或SiC14氢还原法)、晶粒大小不同或颜色的差异而形成。严重的温度圈易形成疏松的夹层。1.2.2产生原因
氢还原或热分解反应过程中,较大幅度的温度波动,使硅棒表面气相沉积速率不同所致。1.2.3对单晶制备的影响
严重的温度圈因为形成疏松夹层,在其内部容易存在气泡和携带杂质,给单晶制备前多晶料的清洁处理带来困难,并成为单晶中杂质的污染源。特别是生长区熔单晶时,会使熔体产生抖动,严重时还会发生硅跳,影响晶体正常生长。1.2.4消除方法
严格控制硅多晶生长时的反应温度,一般SiHC13、SiC1氢还原和SiH.热分解法的反应温度应分别控制在1050~1150℃、1100~1150℃、800~850℃为宜。温度波动最好不超过±20℃。此外,在SiH热分解反应中,还应控制好气体的流量。1.3氧化夹层
1.3.1,特征
氧化夹层的特征与温度圈相似,呈同心圆层状结构,并以氧化硅为界限。由于氧化程度的不同,氧化硅的颜色可能呈灰白色、棕黄色或深褐色等(见图17~19)。1.3.2产生原因
反应气体或反应系统中,残留有较多的水分或空气,高温下发生氧化反应,生成的氧化硅附着于硅棒表面,随后在被氧化的表面上继续生长硅多晶,形成了氧化夹层。1.3.3对单晶制备的影响
在区熔或直拉法生长硅单晶之前,多晶的酸洗清洁处理,不能彻底将氧化夹层腐蚀掉。晶体生长时,由于氧化硅的熔点高于硅的熔点,因此在硅熔体上易形成浮渣,在区熔法生长单晶时,往往飘浮在固液界面附近的熔硅表面,使单晶生长无法进行。中国有色金属工业总公司1987-01-27批准1988-03-01实施
GBn266-87
1.3.4消除方法
严格控制还原用氢气的含水量,保证使露点低汀-50℃,氢气的含氧量应小于1ppm。反应系统要有良好的气密性,无漏水、渗水现象。开炉前应将系统1燥,把残留空气驱除十净。1.4裂纹
1.4.1特征
硅多晶榨表面或横断面上可以观察到裂纹(见阁20~23)。1.4.2产生原因
还原反应过程中,如果硅棒的心和边缘之间的温度差过大,就会产生较大的热应力而引起裂纹。特别是生长大直径的硅棒时,裂纹现象更容易产生。此外,反应结束时降温速度过快或在反应过程中突然断电都可能引起裂纹。
1.4.3对单晶制备的影响
与温度圈的情况类似,清洁处理时,不易将夹带的杂质彻底清除掉,因此直接影响到硅单晶的质盈。在区熔法生长单晶时,往往导致“掉熔区”,使品体生长过程被追中止。1.4.4消除方法
直径较小的硅多晶棒,只要反应结束时降温速度较,防出中途断电,--般不会发生裂纹。大直径硅棒应考虑反应炉内璧抛光,应用石英钟罩等办法,减小反应系统内的温度梯度,可以防止裂纹现象。
1.5夹杂物
1,5.1·特征
硅多晶中含有非硅元素或化合物的颗粒状物质称为夹杂物。应用电了探针和透射电子显微镜分析,发现硅多晶中有αSiC和β-SiC夹杂物,尺寸从儿个微米到30μm(见图24~28)之间。在SiH法生长的硅多晶中,除SiC夹杂物外,还可能有SisN:夹杂物。1.5.2产生原因
当反应气体中含有CH4、CO、CO2、NH:等杂质气体时,还原反应过程中就可能生成SiC、SisN。等颗粒,成为硅多晶中的夹杂物。1.5.3对单晶制备和晶体质量的影响SiC的熔点高于硅的熔点,在熔硅中不易熔解。在晶体生长时,由丁熔的热对流和旋转对流效应;熔体中的颗稳状SiC被卷带到固液交界面处,如果长人单晶中,成为单晶中的夹杂物,直接影响到硅单晶的质最。
1.5.4、消除和抑制措施
乘取有效的分离提纯技术,去除反应气体中含碳、含氮的杂质气体。1.6断面孔洞
硅多晶横断面上的孔润,多是局部区域温度过高和发热体熔化所致(见图29~31)。2硅单晶晶体缺陷
2.1位错
硅单晶显然已经实现无位错生长,但晶体内仍有-定数量的位错存在。此外,硅片在外延生长和硅器件制备过程中,由于各种原因,也会引人大量位错。因此,位错是硅材料中一-种最常见基本缺陷。
2.1.1位错形态及分布
选择适当的腐蚀剂,对观察表面进行择优腐蚀,在位错表面露头处,可以显示出与晶向有关特定形态的位错蚀坑。典型位错蚀坑在:111面上呈三角形(见图32),1100:面上呈方形(见图41),而1110面上星菱形(见图55)。应当指出,位错蚀坑的形态还与位错线走向、晶向偏离度、腐蚀剂种类、腐蚀时间、腐蚀液的温度等因素有关。实际上观察到的位错蚀坑形态是多种多样的(见图322
GBn.266-87
应用红外显微镜和X射线形貌技术可以更清楚地观察到位错线形态以及它们在晶体内的分布(见图59~63)。
硅单晶横断面位错蚀坑的宏观分布可有下列几种组态:a,-位错均匀分布。
b.位错排是位错蚀坑的某一边排列在一条直线上的-种位错组态(见图64~73),它是硅单晶在应力作用下,位错滑移、增殖和堆积的结果。硅单晶的滑移面为{111面,滑移方向为110方向。因此,不论在11111面、{100)面还是(110)面上,位错排都沿着110>方向排列。星形结构是由-系列位错排沿<110>方向密集排列而成的。在(111!面上,星形结构星三角形或六角形组态,在11001面上,呈井字形组态(见图74~78)d.硅晶体中相邻区域取向差别在几分之一秒到一分(弧度)的晶粒间界称为小角度晶界。在《111)面上小角晶界呈现为位错蚀坑以角顶底的方式直线排列,而在1100;面上,位错蚀坑则以角顶角方式直线排列(见图79~84)。2.1.2位错产生原因
在硅单晶生长开始,由籽晶中原有位错和籽晶熔接引入的位错,在生长的晶体中会继续延伸,在晶体生长过程中,固液界面附近落入不溶固态颗粒,也易引入位错,尤其当热场温度梯度较大,在晶体中产生较大的热应力时,更容易产生位错并使其增殖。2.1.3无位错硅晶体的生长
实现硅单晶的无位错生长,首先要采用缩颈方法防止籽晶中原有位错和籽晶与熔体熔接引入的位错向晶体中延伸,其次调节热场,选择合理的晶体生长参数,维持恒定的固液界面形状,最后要特别防止不溶固态颗粒落人固液界面等。2.2层错
层错系指晶体内,原子平面的堆垛次序错乱形成的一种面缺陷。硅单晶的层错面为1111)面。2.2.1层错的腐蚀形态
应用化学腐蚀方法显示硅单晶中的层错时,有时可以观察到沿<110>方向腐蚀沟槽,它是层错面与观察表面的交线。在1111;面上,层错线相互平行或成60°、120\分布,(100)面上的层错线相互半行或垂直(见图85~95),在层错线两端为偏位错蚀坑。2.2.2层错产生原因
在目前工艺条件下,原生硅单晶中的层错是不多见的。一般认为,在单晶生长过程中,固态颗粒进入固液界面,单晶体内存在较大热应力,固液界面附近熔体过冷度较大,以及机械振动等都可能成为产生层错的原因。
2.3微缺陷
微缺陷是无位错区熔和直拉硅单晶中常见的一类主要缺陷。因为它们的尺寸很小,一般在微米数量级范围内,故通称为微缺陷。2.3.1微缺陷的形态和分布
硅单晶的微缺陷,经择优化学腐蚀后在横断面上往往呈均匀分布或组成各种形态的宏观旋涡花纹,后者也称旋涡缺陷(见图96~111)。在显微镜下微缺陷的微观腐蚀形态为浅底腐蚀坑或腐蚀小丘(见图112~121)。在硅单晶的纵面上,微缺陷通常呈层状分布(见图122)。CZ硅单晶中的微缺陷,因为它的应力场太小,往往需热氧化处理,使微缺陷缀饰长大或转化为氧化层错或小位错环后,才可用择优腐蚀方法显示(见图123~150)。因此,热氧化是检验CZ硅单晶中微缺陷的标准方法。
扫描电子显微技术、X射线形貌技术、红外显微技术都可以用来研究微缺陷及其空间分布(见图151~165)
GBn266-87
2.3.2微缺陷的结构
区熔单晶中微缺陷通常是尺寸不同的两类缺陷组成,尺寸较大的一类称为A型微缺陷,尺寸较小的一类称为B型微缺陷。TEM观察结果证明,A型微缺陷是由间隙型的位错环、位错环团以及堆垛层错等缺陷构成。在这些缺陷上面,还可能有杂质缀饰着,这些已被确认。B型微缺陷的本质,目前还不十分清楚。
直拉单晶中的微缺陷情况比较复杂。TEM观察到在原生直拉硅单晶中,存在着类似区熔单晶A型微缺陷的间隙位错环、位错环团和小的堆垛层错等构成的微缺陷,以及板片状SiO2沉积物(见图166172),退火CZ硅单晶中的微缺陷为体层错、氧沉淀物及沉淀物-位错-络合物等(见图173~177)。
2.3.3微缺陷产生原因和旋涡缺陷控制措施区熔硅单晶中的微缺陷是在晶体生长冷却过程中,由过饱和的热点缺陷聚集或者它们与杂质的络合物凝聚而成的间隙型位错环、位错环团及层错等。CZ硅单晶中的微缺陷,多数是各种形态的氧化物沉淀,它们是氧和碳等杂质,在晶体冷却过程中,通过均质成核和异质成核机理形成的。通过仔细地调整热场,使之具有良好的轴对称性,控制生长条件,减小热对流影响,就能防止发生回熔现象,有利于消除旋涡缺陷。位错可消除或抑制微缺陷的产生(见图178~181)。2.4雾缺陷
抛光后的硅片经过热氧化处理和化学腐蚀后,其表面上有时会出现一种高密度的微缺陷,由于漫反射,在微缺陷密集的区域呈雾状,故称为雾缺陷。2.4.1雾缺陷的特征
雾缺陷微观上为高密度的浅蚀坑(见图182~186)。宏观上,氧化可能呈较均匀分布或各种旋涡花纹图样分布。雾缺陷是一种近表面缺陷,具有较高的热迁移率和对晶格应力的高敏感性,容易被其他缺陷吸收。所以,氧化雾缺陷的宏观分布将会受到其他晶体缺陷的制约(见图187~189)。2.4.2雾缺陷的产生和消除方法
许多研究证明,雾缺陷的产生是与热处理等工艺过程中重金属杂质(铜、镍、铁、钴等)的污染有直接关系。因此,加强空气净化,避免硅片沾污是消除雾缺陷的主要措施。另外,利用背面损伤等外吸除技术(和氧的本征吸除技术)可有效地防止雾缺陷发生。2.5杂质条纹
杂质条纹是硅单晶中一种常见的宏观缺陷,它表征硅单晶中,不同区域杂质浓度存在明显的差异。2.5.1杂质条纹的形态和特征
杂质条纹有一定的分布规律。在垂直生长轴方向的横断面上,杂质条纹多呈环状或条纹状分布,在半行于生长轴方向的纵剖面上,杂质条纹呈层状分布。杂质条纹的形状反映了固液界面的结晶前沿形状(见图190~201)。
2.5.2杂质条纹产生的原因
晶体生长时,由于种种原因,或引起固液界面附近的温度发生微小的变化,由此导致晶体微观生长速率的起伏,或者引起杂质边界层厚度起伏,以及小平面效应等,均使晶体和熔体之间的杂质有效分凝系数产生波动,引起晶体中的杂质浓度分布发生相应的变化,从而形成了杂质条纹。2.5.3杂质条纹的消除与抑制
调整热场,使之具有良好的轴对称性,并使晶体的旋转轴尽量与热场中心轴同轴,抑制和减弱熔体热对流,可以使晶体中杂质趋于均匀分布。采用磁场拉晶工艺或在无重力作用的太空拉晶有可能完全消除条纹。
2.6硅单晶中杂质富集缺陷
2.6.1管道
a,在硅单晶中,形成贯穿晶体纵向的杂质富集区称为管道(见图202~206)。生长<111>晶向无位错硅单晶时,固液界面处往往会出现(111)小平面。(111)小平面的b.
GBn266-87
出现是由于Jackson因子α>2之故。小平面的具体情况与籽晶取向及固液界面的形状有关。油于(111)小平面和其他部位生长速度的差异,使(111)小平面处杂质有效分凝系数显著变大,在晶体中形成管道。管道多发生在重掺硅单晶中。2.6.2杂质富集.
a杂质富集常见于重掺杂单晶的尾部,用化学腐蚀法显示的杂质富集如图207~216所示。b.在生长重掺杂硅单晶时,如果杂质在硅中的分凝系数K<1时,在晶体尾部,由于熔体中杂质浓度过高,组分过冷而使杂质局部富集。当晶体中杂质浓度超过其固溶度时,便会发生杂质析出现象。
2.6.3六角网络
.a六角网络是一组封闭的六角环状网络,其外围是杂质富集条纹(见图217~219)。b.·六角网络常出现在重掺杂单晶的尾部,它是杂质富集进一步发展而成的。为了降低其界面能,转变为正六边形,边的取向均为<110>。2.7李晶
2.7.1李晶的构成
李晶是由两部分取向不同,但具有--个共同晶面的双晶体组成。它们共用的晶面称李生面,两部分晶体的取向以李生面为镜面对称,且两部分晶体取向夹角具有特定的值。硅晶体的李生面为《111)面(见图220~229)。
2.7.2李晶生成原因
晶体生长过程中,固液界面处引人固态小颗粒,成为新的结晶中心并不断长大形成李晶。此外,机械振动、拉晶速度过快或拉速突变也可促使李晶的形成。2.8嵌晶
硅晶体内部存在与基体取向不同的小晶体:(晶粒)称为嵌晶(见图230~231)。嵌晶可为单晶或多晶。在一般拉晶工艺条件下,嵌晶很少见。2.9·夹杂物
由外界或多晶引人熔硅中的固态颗粒,在拉晶时被夹带到晶体中形成第二相称为夹杂物。应用电子探针和扫描电子显微镜观察到直拉和区熔硅单晶中,存在α-SiC和β-SiC颗粒,其尺寸由几个微米到十几个微米(见图232~236)。2.10孔洞
硅单晶中存在的近于圆柱形或球形的空洞。在硅单晶机械加工时,硅片上所见到的圆形孔洞,大的孔洞直径有几毫米(见图237~238)。2.11氢致缺陷
氢致缺陷是在氢气或含氢气氛下生长的区熔硅单晶中特有的一种晶体缺陷。在经过600~1000℃热处理后的晶锭中常常观察到这种缺陷。2.11.1氢致缺陷的特征
氢致缺陷是由裂缝及周围的压印棱柱位错所组成。因晶体生长条件和热处理条件等因素不同,氢致缺陷的尺寸和腐蚀形态有很大区别。有的单晶经化学抛光处理后可看到大小不一的蚀坑(见图239~242)。如将单晶进行机械抛光,并用Sirtl腐蚀,显微镜下可观察到双排蚀坑,它们是由裂缝处沿<110>方向发射一系列棱柱位错组成(见图243~248)。尺寸微小的一类氢致缺陷,腐蚀后宏观上呈旋涡条纹或均匀分布(见图249),微观上是小黑点,密度较高。在红外显微镜下,裂缝呈条状或叶片状(见图250~251)。应用X射线形貌技术观察,氢致缺陷呈雪花等形态(见图252~254)2.11.2氢致缺陷的形成原因
在氢或含氢气氛下生长的区熔硅单晶中,溶解有大量的氢,当晶体冷却到室温,硅中氢呈高度过饱和状态,并与硅形成Si-H键。在随后的热处理过程中,Si-H键断裂,氢在硅中脱溶析出,聚集成具有一定尺寸原子团,同时对周围的硅点阵产生压应力导致位错环形成并以氢原子团为中心沿5
<110>方向发射棱柱状位错环。
GBn266-87
2.11.3氢致缺陷的抑制
单晶生长时,采用较快冷却的方法(如加大氢气流量),抑制氢原子聚集成团,使氢原子较均匀地分布于硅晶体中。另外,可采用使硅片快速推进高温区进行预热处理,使微小氢原子团溶解并扩散出硅片表面。经此种工艺处理后的硅片,在随后的器件工艺中不再产生可观察到的氢致缺陷。3硅片加工缺陷
3.1刀痕
刀痕是硅片切割加工时在硅片表面遗留下的切割痕迹。严重的刀痕形成一系列凹凸相间圆弧形沟槽,圆弧的半径与切割刀具半径相同(见图255~257)切片机有较大的机械振动,刀片安装不平整,刀口处金刚石涂层及进刀速度不均勾都会使硅片上留下明显痕迹。
3.2崩边和缺口
崩边是不贯穿硅片前、背表面的局部边缘破损(见图258)。缺口是贯穿硅片前、背表面的局部边缘破损(见图259~260)切片机有较大的机械振动、刀具摆动或研磨时硅片承受压力不均匀以及操作不当等原因都可能造成崩边或缺口。缺口一般沿硅晶体解理面发生,并常伴有裂纹。3.3裂纹
裂纹是硅片上不贯穿整个表面的裂痕。裂纹容易沿晶体解理面产生,故在11111面上裂纹呈“-\字或“Y”字形,(100】面上呈“”字或“十”字形(见图261~263)。磨片过程中,硅片局部受力不均匀,是造成裂纹的主要原因。3.4划道和拉丝(擦伤)
划道系指在研磨和抛光工艺过程中,在硅片表面上出现宏观无规则的浅沟(见图264),它们是由于磨盘质量不佳或磨料和抛光液中混有较大的硬质颗粒造成的。拉丝(擦伤)是指在经过严格清洗处理的抛光面上,所见到的一些无规则轻微的划痕(见图265~266)。拉丝通常是由于抛光环境不够洁净,抛光液中混有微小颗粒造成的。3:5塌边
塌边是抛光工艺中,在硅片边缘区域形成斜坡状加工缺陷(见图267)。它是由于抛光布太软,抛光速度过慢,抛光时间过长以及抛光前的化学腐蚀时边缘减薄量较多等因素所致。3.6亮点
亮点是指研磨或抛光时硅片上可观察到的孤立小亮点(见图268)。亮点的大小、数量不等。亮点是研磨或抛光不充分,残留下来的一些孤立机械损伤点。3.7波纹和平整度
波纹是指硅片抛光表面上遗留下的种宏观波纹状起伏。波纹表征抛光表面不平整,在荧光灯下根据灯影是否平直检查平整度或利用激光干涉条纹来评价硅片表面平整程度(见图269~271)。化学减薄时,腐蚀液定向流动,抛光过程中硅片停转等因素都可能造成波纹。3.8桔皮
在显微镜下观察到抛光表面呈现大面积类似桔皮状粗糙表面称桔皮。桔皮是由于化学减薄不均匀,抛光液pH值不合适,抛光片旋转不均匀等因素引起的。3.9凹坑和小丘
凹坑指硅片抛光表面上的一种凹陷,具有-一定的形状。小丘系指硅片抛光表面存在的不规则突起,又叫做台阶。3.10抛光雾
硅片抛光表面上,如存在高密度的凹坑、小丘和拉丝等缺陷时对强光发生漫反射而呈现出的一种6
GBn266-87
宏观雾状缺陷,称做抛光雾。抛光表面氧化也呈雾状,但进一步抛光可去除(见图272)。3.11残留机械损伤
残留机械损伤是经过切、磨、抛加工之后,在硅片表面残留下来的机械损伤。残留机械损伤与整个硅片加工过程有关,但主要是因抛光不充分,机械损伤层未完全去掉所致。残留机械损伤在高温氧化过程中将诱生出氧化层错等二次缺陷,通常用氧化层错的密度来检测硅片抛光质量(见图273~288)。
3.12.表面沾污
硅片抛光后清洁处理不彻底而在抛光表面残存如水迹、溶剂等有机物质以及外界引入的各种沾污如尘埃、指印等称为表面沾污(见图289~294)。4硅外延缺陷
4.1.外延位错
外延位错是外延工艺中产生的位错,它是外延层中常见的一种缺陷。4.1.1.外延位错的魔蚀形态及分布应用化学腐蚀方法,在显微镜下观察到的外延位错蚀坑形状及分布与原生硅单晶位错类似。a:在显微镜下整个外延层上常常观察到位错蚀坑呈较为均匀分布,并常伴有外延层错(见图295~297)。
b.滑移线是外延层表面上,沿<110>滑移方向延伸的直线,它多为贯穿整个表面的直线(见图298)。滑移线是由位错源在应力作用下产生大量位错并不断沿<110方向滑移出硅片表面而形成的。在显微镜下,它的微观结构是由许多台阶组成的滑移带。外延片上的位错排是位错蚀坑的某一边沿<110>方向排列在一条直线的一种位错分布组态(见图299)。它是因为由同一位错源产生的位错滑移运动受阻,位错堆积而成。c.外延片上的星形结构是由大量位错排组成的一种位错宏观分布,多数是由于衬底的残留机械损伤和较大的热应力引起的。
4.1.2外延位错产生原因
外延位错一般是由于衬底内位错向外延层延伸,或由衬底表面机械损伤等硅片加工缺陷,在热应力的作用下产生大量滑移位错。另外,因外延层与衬底界面处的晶格失配,也可产生失配位错。4.1.3·外延位错抑制方法
选用无位错硅单晶制备衬底,提高衬底加工质量,避免一切可能的加工缺陷,合理控制外延生长的升降温速率,减小衬底径向温度梯度等,都可减少或抑制外延位错的产生。4.2外延层错
外延工艺中产生的层错称为外延层错。外延层错是本征层错,柏格斯失量为号<111>。外延层错是外延层中主要缺陷之一
4.2.1外延层错的形态
经择优化学腐蚀后,在显微镜下可观察到各种形态的外延层错。在(111)外延片上,外延层错呈正三角形、V字形、一字形或多边形的腐蚀槽(见图300~304)。而在(100)外延片上,外延层错为正方形、L字形、一字形或多边形的腐蚀槽(见图305~306)。如用干涉相衬显微镜,不需化学腐蚀,可直接看到外延层错。
4.2.2外延层错产生原因
外延层错多成核于衬底表面。衬底中的各种晶体缺陷,衬底表面机核损伤以及外来沾污等都可能成为外延层错成核中心(见图307~311)。此外,当外延生长温度偏低,生长速率过快或温度起伏较大而产生热应力等因素都将促使外延层错密度的增加。外延层错随着外延层的生长而长大。GBn266—87
4.2.3减少和消除外延层错的方法消除外延层错最根本的方法是提高衬底表面的抛光质量,减少残存的机械损伤和避免外来沾污。在工艺上,外延生长前对衬底表面进行HC1或HBr气相腐蚀抛光,是减少外延层错的有效方法。另外,提高反应剂和氢气的纯度以及反应系统的洁净度,都有助于减少外延层错。4.3棱锥
棱锥又称角锥,为外延层表面的一种突起物。在(111)面外延层上,一个棱锥一般由三个李晶四面体组成,并常与一个外延层错相联系,两者相对转过60°角(见图312~322)。棱锥一般认为是由外延层与衬底界面处各种不完整性引起的。衬底表面存在杂质沾污或反应系统漏气等导致外延各向异性生长,形成棱锥。外延生长速率过快或衬底晶向偏离度很小(<0.5°),也容易形成棱锥。高密度的棱锥形成所谓棱脉状缺陷(见图323~325)。为了避免棱锥,首先是保证外延系统和衬底表面无任何沾污。此外,适当提高外延温度,使衬底晶向朝最近的<110>方向偏离<111>3~5°等措施都可减少棱锥的产生。4.4乳突
乳突为外延表面上一种尺寸较大的突起物。在乳突的顶端多为一棱锥(见图326~327)。可见,乳突的形成是由棱锥生长引起的。乳突的产生原因和消除方法同棱锥。4.5层错阴影(月芽、鱼尾等)
当外延生长表面偏离(111)面较多时,在沿着外延层错一定方向的表面上,产生形如月芽、鱼尾等形状的凹沟,统称层错阴影。这种缺陷有许多变态,都是由于外延层错妨碍生长前沿(二维)推进而产生的。层错阴影的方向、形状与衬底取向有密切关系。沟深与外延层厚度成正比,晶向偏离<111>角度越大,阴影越长,衬底接近正(111)面时,阴影即会消失。4.6·多晶点
多晶点是由外延层表面上形成的多晶颗粒构成的一种外延缺陷(见图328~330)。它是由衬底表面的杂质颗粒或外延生长时发生氧化而生成的。加强衬底洁净处理,防止氧化气氛进人反应系统,可防止多晶点产生。
4.7氧化白雾
氧化白雾是指外延层表面不经化学腐蚀,直接观察到的一种白雾状宏观缺陷。在显微镜下是由高密度的棱锥、乳突、多晶点等缺陷组成的(见图331~340)。产生原因和消除方法与棱锥、乳突、多晶点等相同。
4.8雾缺陷
外延层表面经择优腐蚀后,有时可观察到宏观上呈云雾状的缺陷,在显微镜下是由密度极高的小浅蚀坑组成,故称为雾缺陷(见图341~343)。一般认为雾缺陷主要是因为高温外延生长时外来金属杂质污染引起的。污染可能来自反应系统、石墨基座、反应气体和环境等。因此,消除外界杂质污染源或采用吸除技术,可以有效地减少或消除雾缺陷。4.9取向平台
取向平台为一种平台状的凸起,多发生在<111>取向外延片的边缘。由于1111]面腐蚀速度最慢,在化学气相腐蚀时,如果在衬底边缘处出现正(111)面,祖露区就会因腐蚀慢而成为凸起的平台,外延生长后发展成取向平台。
4.10雪球和钉
外延生长时,由于球形杂质颗粒在外延层上滚动而形成的缺陷称为雪球。它包括杂质颗粒及其滚动的痕迹(见图344)。
钉是外延层表面一种浅凹陷沟。它是在外延反应下,液态杂质在表面运动留下的痕迹。雪球和钉在外延生长时很少见,只要严格工艺操作均可避免。4.11桔皮
GBn266-87
桔皮系指外延表面粗糙不平整的一种表面缺陷。桔皮与衬底表面的桔皮缺陷有关。4.12麻坑
外延层表面局部温度过高而形成的小凹坑称为麻坑(见图345~346)。4.13沾污
不洁净工艺操作,在外延层表面引人各种杂质沾污(见图347~348)GBn266-87bzxz.net
附录A
部分缺陷的彩色照片
(补充件)
照片见有色金属上业总公司标准计量所所制照片(图A1~图A94)
小提示:此标准内容仅展示完整标准里的部分截取内容,若需要完整标准请到上方自行免费下载完整标准文档。
中华人民共和国国家标准
CBn 26687
yS/T 209 —94
上海市战求益督情研究所
登话号07971909
硅材料原生缺陷图谱
中国有色全属行
工业总公司
最研究
标准资料专用章
1987-06-25发布
1988-03-01实施
国家标准局发布
中华人民共和国国家标准
硅材料原生缺陷图谱
UDC669.782:620
.191/.192
Y5(12-94
优精GBn 266-87
本标准规定了硅多晶、单晶、切磨抛片和外延片等硅材料的各种原生缺陷及其密切相关的某些诱生缺陷的形貌特征。
本标准适用硅多晶、单晶、切磨抛片和外延片等硅材料生产研究中各种缺陷的检验。硅器件、大规模和超大规模集成电路的生产研究也可参考本标准。本标准中所用图(片),请见中国有色金属工业总公司标准计量所所印制的照片。1硅多晶结构的不完整性
1.1多晶的外观形态
由三氯氢硅(SiHCl:)或四氯化硅(SiC1)氢还原法和硅烷(SiH)热分解法生长的硅多晶表面致密度和晶粒大小,因生长条件的差异有所不同(见图1~8)。一般来讲,沉积速率过快,温度过高,易造成颗粒粗大。
1.2温度圈
1.2.1特征
硅多晶横断面上,晶粒呈枝蔓状或径向辐射生长(见图9~11)。但有时可以观察到以硅芯为中心的年轮状结构,称为温度圈(见图12~16)。它是由于结晶致密度(指SiHC13或SiC14氢还原法)、晶粒大小不同或颜色的差异而形成。严重的温度圈易形成疏松的夹层。1.2.2产生原因
氢还原或热分解反应过程中,较大幅度的温度波动,使硅棒表面气相沉积速率不同所致。1.2.3对单晶制备的影响
严重的温度圈因为形成疏松夹层,在其内部容易存在气泡和携带杂质,给单晶制备前多晶料的清洁处理带来困难,并成为单晶中杂质的污染源。特别是生长区熔单晶时,会使熔体产生抖动,严重时还会发生硅跳,影响晶体正常生长。1.2.4消除方法
严格控制硅多晶生长时的反应温度,一般SiHC13、SiC1氢还原和SiH.热分解法的反应温度应分别控制在1050~1150℃、1100~1150℃、800~850℃为宜。温度波动最好不超过±20℃。此外,在SiH热分解反应中,还应控制好气体的流量。1.3氧化夹层
1.3.1,特征
氧化夹层的特征与温度圈相似,呈同心圆层状结构,并以氧化硅为界限。由于氧化程度的不同,氧化硅的颜色可能呈灰白色、棕黄色或深褐色等(见图17~19)。1.3.2产生原因
反应气体或反应系统中,残留有较多的水分或空气,高温下发生氧化反应,生成的氧化硅附着于硅棒表面,随后在被氧化的表面上继续生长硅多晶,形成了氧化夹层。1.3.3对单晶制备的影响
在区熔或直拉法生长硅单晶之前,多晶的酸洗清洁处理,不能彻底将氧化夹层腐蚀掉。晶体生长时,由于氧化硅的熔点高于硅的熔点,因此在硅熔体上易形成浮渣,在区熔法生长单晶时,往往飘浮在固液界面附近的熔硅表面,使单晶生长无法进行。中国有色金属工业总公司1987-01-27批准1988-03-01实施
GBn266-87
1.3.4消除方法
严格控制还原用氢气的含水量,保证使露点低汀-50℃,氢气的含氧量应小于1ppm。反应系统要有良好的气密性,无漏水、渗水现象。开炉前应将系统1燥,把残留空气驱除十净。1.4裂纹
1.4.1特征
硅多晶榨表面或横断面上可以观察到裂纹(见阁20~23)。1.4.2产生原因
还原反应过程中,如果硅棒的心和边缘之间的温度差过大,就会产生较大的热应力而引起裂纹。特别是生长大直径的硅棒时,裂纹现象更容易产生。此外,反应结束时降温速度过快或在反应过程中突然断电都可能引起裂纹。
1.4.3对单晶制备的影响
与温度圈的情况类似,清洁处理时,不易将夹带的杂质彻底清除掉,因此直接影响到硅单晶的质盈。在区熔法生长单晶时,往往导致“掉熔区”,使品体生长过程被追中止。1.4.4消除方法
直径较小的硅多晶棒,只要反应结束时降温速度较,防出中途断电,--般不会发生裂纹。大直径硅棒应考虑反应炉内璧抛光,应用石英钟罩等办法,减小反应系统内的温度梯度,可以防止裂纹现象。
1.5夹杂物
1,5.1·特征
硅多晶中含有非硅元素或化合物的颗粒状物质称为夹杂物。应用电了探针和透射电子显微镜分析,发现硅多晶中有αSiC和β-SiC夹杂物,尺寸从儿个微米到30μm(见图24~28)之间。在SiH法生长的硅多晶中,除SiC夹杂物外,还可能有SisN:夹杂物。1.5.2产生原因
当反应气体中含有CH4、CO、CO2、NH:等杂质气体时,还原反应过程中就可能生成SiC、SisN。等颗粒,成为硅多晶中的夹杂物。1.5.3对单晶制备和晶体质量的影响SiC的熔点高于硅的熔点,在熔硅中不易熔解。在晶体生长时,由丁熔的热对流和旋转对流效应;熔体中的颗稳状SiC被卷带到固液交界面处,如果长人单晶中,成为单晶中的夹杂物,直接影响到硅单晶的质最。
1.5.4、消除和抑制措施
乘取有效的分离提纯技术,去除反应气体中含碳、含氮的杂质气体。1.6断面孔洞
硅多晶横断面上的孔润,多是局部区域温度过高和发热体熔化所致(见图29~31)。2硅单晶晶体缺陷
2.1位错
硅单晶显然已经实现无位错生长,但晶体内仍有-定数量的位错存在。此外,硅片在外延生长和硅器件制备过程中,由于各种原因,也会引人大量位错。因此,位错是硅材料中一-种最常见基本缺陷。
2.1.1位错形态及分布
选择适当的腐蚀剂,对观察表面进行择优腐蚀,在位错表面露头处,可以显示出与晶向有关特定形态的位错蚀坑。典型位错蚀坑在:111面上呈三角形(见图32),1100:面上呈方形(见图41),而1110面上星菱形(见图55)。应当指出,位错蚀坑的形态还与位错线走向、晶向偏离度、腐蚀剂种类、腐蚀时间、腐蚀液的温度等因素有关。实际上观察到的位错蚀坑形态是多种多样的(见图322
GBn.266-87
应用红外显微镜和X射线形貌技术可以更清楚地观察到位错线形态以及它们在晶体内的分布(见图59~63)。
硅单晶横断面位错蚀坑的宏观分布可有下列几种组态:a,-位错均匀分布。
b.位错排是位错蚀坑的某一边排列在一条直线上的-种位错组态(见图64~73),它是硅单晶在应力作用下,位错滑移、增殖和堆积的结果。硅单晶的滑移面为{111面,滑移方向为110方向。因此,不论在11111面、{100)面还是(110)面上,位错排都沿着110>方向排列。星形结构是由-系列位错排沿<110>方向密集排列而成的。在(111!面上,星形结构星三角形或六角形组态,在11001面上,呈井字形组态(见图74~78)d.硅晶体中相邻区域取向差别在几分之一秒到一分(弧度)的晶粒间界称为小角度晶界。在《111)面上小角晶界呈现为位错蚀坑以角顶底的方式直线排列,而在1100;面上,位错蚀坑则以角顶角方式直线排列(见图79~84)。2.1.2位错产生原因
在硅单晶生长开始,由籽晶中原有位错和籽晶熔接引入的位错,在生长的晶体中会继续延伸,在晶体生长过程中,固液界面附近落入不溶固态颗粒,也易引入位错,尤其当热场温度梯度较大,在晶体中产生较大的热应力时,更容易产生位错并使其增殖。2.1.3无位错硅晶体的生长
实现硅单晶的无位错生长,首先要采用缩颈方法防止籽晶中原有位错和籽晶与熔体熔接引入的位错向晶体中延伸,其次调节热场,选择合理的晶体生长参数,维持恒定的固液界面形状,最后要特别防止不溶固态颗粒落人固液界面等。2.2层错
层错系指晶体内,原子平面的堆垛次序错乱形成的一种面缺陷。硅单晶的层错面为1111)面。2.2.1层错的腐蚀形态
应用化学腐蚀方法显示硅单晶中的层错时,有时可以观察到沿<110>方向腐蚀沟槽,它是层错面与观察表面的交线。在1111;面上,层错线相互平行或成60°、120\分布,(100)面上的层错线相互半行或垂直(见图85~95),在层错线两端为偏位错蚀坑。2.2.2层错产生原因
在目前工艺条件下,原生硅单晶中的层错是不多见的。一般认为,在单晶生长过程中,固态颗粒进入固液界面,单晶体内存在较大热应力,固液界面附近熔体过冷度较大,以及机械振动等都可能成为产生层错的原因。
2.3微缺陷
微缺陷是无位错区熔和直拉硅单晶中常见的一类主要缺陷。因为它们的尺寸很小,一般在微米数量级范围内,故通称为微缺陷。2.3.1微缺陷的形态和分布
硅单晶的微缺陷,经择优化学腐蚀后在横断面上往往呈均匀分布或组成各种形态的宏观旋涡花纹,后者也称旋涡缺陷(见图96~111)。在显微镜下微缺陷的微观腐蚀形态为浅底腐蚀坑或腐蚀小丘(见图112~121)。在硅单晶的纵面上,微缺陷通常呈层状分布(见图122)。CZ硅单晶中的微缺陷,因为它的应力场太小,往往需热氧化处理,使微缺陷缀饰长大或转化为氧化层错或小位错环后,才可用择优腐蚀方法显示(见图123~150)。因此,热氧化是检验CZ硅单晶中微缺陷的标准方法。
扫描电子显微技术、X射线形貌技术、红外显微技术都可以用来研究微缺陷及其空间分布(见图151~165)
GBn266-87
2.3.2微缺陷的结构
区熔单晶中微缺陷通常是尺寸不同的两类缺陷组成,尺寸较大的一类称为A型微缺陷,尺寸较小的一类称为B型微缺陷。TEM观察结果证明,A型微缺陷是由间隙型的位错环、位错环团以及堆垛层错等缺陷构成。在这些缺陷上面,还可能有杂质缀饰着,这些已被确认。B型微缺陷的本质,目前还不十分清楚。
直拉单晶中的微缺陷情况比较复杂。TEM观察到在原生直拉硅单晶中,存在着类似区熔单晶A型微缺陷的间隙位错环、位错环团和小的堆垛层错等构成的微缺陷,以及板片状SiO2沉积物(见图166172),退火CZ硅单晶中的微缺陷为体层错、氧沉淀物及沉淀物-位错-络合物等(见图173~177)。
2.3.3微缺陷产生原因和旋涡缺陷控制措施区熔硅单晶中的微缺陷是在晶体生长冷却过程中,由过饱和的热点缺陷聚集或者它们与杂质的络合物凝聚而成的间隙型位错环、位错环团及层错等。CZ硅单晶中的微缺陷,多数是各种形态的氧化物沉淀,它们是氧和碳等杂质,在晶体冷却过程中,通过均质成核和异质成核机理形成的。通过仔细地调整热场,使之具有良好的轴对称性,控制生长条件,减小热对流影响,就能防止发生回熔现象,有利于消除旋涡缺陷。位错可消除或抑制微缺陷的产生(见图178~181)。2.4雾缺陷
抛光后的硅片经过热氧化处理和化学腐蚀后,其表面上有时会出现一种高密度的微缺陷,由于漫反射,在微缺陷密集的区域呈雾状,故称为雾缺陷。2.4.1雾缺陷的特征
雾缺陷微观上为高密度的浅蚀坑(见图182~186)。宏观上,氧化可能呈较均匀分布或各种旋涡花纹图样分布。雾缺陷是一种近表面缺陷,具有较高的热迁移率和对晶格应力的高敏感性,容易被其他缺陷吸收。所以,氧化雾缺陷的宏观分布将会受到其他晶体缺陷的制约(见图187~189)。2.4.2雾缺陷的产生和消除方法
许多研究证明,雾缺陷的产生是与热处理等工艺过程中重金属杂质(铜、镍、铁、钴等)的污染有直接关系。因此,加强空气净化,避免硅片沾污是消除雾缺陷的主要措施。另外,利用背面损伤等外吸除技术(和氧的本征吸除技术)可有效地防止雾缺陷发生。2.5杂质条纹
杂质条纹是硅单晶中一种常见的宏观缺陷,它表征硅单晶中,不同区域杂质浓度存在明显的差异。2.5.1杂质条纹的形态和特征
杂质条纹有一定的分布规律。在垂直生长轴方向的横断面上,杂质条纹多呈环状或条纹状分布,在半行于生长轴方向的纵剖面上,杂质条纹呈层状分布。杂质条纹的形状反映了固液界面的结晶前沿形状(见图190~201)。
2.5.2杂质条纹产生的原因
晶体生长时,由于种种原因,或引起固液界面附近的温度发生微小的变化,由此导致晶体微观生长速率的起伏,或者引起杂质边界层厚度起伏,以及小平面效应等,均使晶体和熔体之间的杂质有效分凝系数产生波动,引起晶体中的杂质浓度分布发生相应的变化,从而形成了杂质条纹。2.5.3杂质条纹的消除与抑制
调整热场,使之具有良好的轴对称性,并使晶体的旋转轴尽量与热场中心轴同轴,抑制和减弱熔体热对流,可以使晶体中杂质趋于均匀分布。采用磁场拉晶工艺或在无重力作用的太空拉晶有可能完全消除条纹。
2.6硅单晶中杂质富集缺陷
2.6.1管道
a,在硅单晶中,形成贯穿晶体纵向的杂质富集区称为管道(见图202~206)。生长<111>晶向无位错硅单晶时,固液界面处往往会出现(111)小平面。(111)小平面的b.
GBn266-87
出现是由于Jackson因子α>2之故。小平面的具体情况与籽晶取向及固液界面的形状有关。油于(111)小平面和其他部位生长速度的差异,使(111)小平面处杂质有效分凝系数显著变大,在晶体中形成管道。管道多发生在重掺硅单晶中。2.6.2杂质富集.
a杂质富集常见于重掺杂单晶的尾部,用化学腐蚀法显示的杂质富集如图207~216所示。b.在生长重掺杂硅单晶时,如果杂质在硅中的分凝系数K<1时,在晶体尾部,由于熔体中杂质浓度过高,组分过冷而使杂质局部富集。当晶体中杂质浓度超过其固溶度时,便会发生杂质析出现象。
2.6.3六角网络
.a六角网络是一组封闭的六角环状网络,其外围是杂质富集条纹(见图217~219)。b.·六角网络常出现在重掺杂单晶的尾部,它是杂质富集进一步发展而成的。为了降低其界面能,转变为正六边形,边的取向均为<110>。2.7李晶
2.7.1李晶的构成
李晶是由两部分取向不同,但具有--个共同晶面的双晶体组成。它们共用的晶面称李生面,两部分晶体的取向以李生面为镜面对称,且两部分晶体取向夹角具有特定的值。硅晶体的李生面为《111)面(见图220~229)。
2.7.2李晶生成原因
晶体生长过程中,固液界面处引人固态小颗粒,成为新的结晶中心并不断长大形成李晶。此外,机械振动、拉晶速度过快或拉速突变也可促使李晶的形成。2.8嵌晶
硅晶体内部存在与基体取向不同的小晶体:(晶粒)称为嵌晶(见图230~231)。嵌晶可为单晶或多晶。在一般拉晶工艺条件下,嵌晶很少见。2.9·夹杂物
由外界或多晶引人熔硅中的固态颗粒,在拉晶时被夹带到晶体中形成第二相称为夹杂物。应用电子探针和扫描电子显微镜观察到直拉和区熔硅单晶中,存在α-SiC和β-SiC颗粒,其尺寸由几个微米到十几个微米(见图232~236)。2.10孔洞
硅单晶中存在的近于圆柱形或球形的空洞。在硅单晶机械加工时,硅片上所见到的圆形孔洞,大的孔洞直径有几毫米(见图237~238)。2.11氢致缺陷
氢致缺陷是在氢气或含氢气氛下生长的区熔硅单晶中特有的一种晶体缺陷。在经过600~1000℃热处理后的晶锭中常常观察到这种缺陷。2.11.1氢致缺陷的特征
氢致缺陷是由裂缝及周围的压印棱柱位错所组成。因晶体生长条件和热处理条件等因素不同,氢致缺陷的尺寸和腐蚀形态有很大区别。有的单晶经化学抛光处理后可看到大小不一的蚀坑(见图239~242)。如将单晶进行机械抛光,并用Sirtl腐蚀,显微镜下可观察到双排蚀坑,它们是由裂缝处沿<110>方向发射一系列棱柱位错组成(见图243~248)。尺寸微小的一类氢致缺陷,腐蚀后宏观上呈旋涡条纹或均匀分布(见图249),微观上是小黑点,密度较高。在红外显微镜下,裂缝呈条状或叶片状(见图250~251)。应用X射线形貌技术观察,氢致缺陷呈雪花等形态(见图252~254)2.11.2氢致缺陷的形成原因
在氢或含氢气氛下生长的区熔硅单晶中,溶解有大量的氢,当晶体冷却到室温,硅中氢呈高度过饱和状态,并与硅形成Si-H键。在随后的热处理过程中,Si-H键断裂,氢在硅中脱溶析出,聚集成具有一定尺寸原子团,同时对周围的硅点阵产生压应力导致位错环形成并以氢原子团为中心沿5
<110>方向发射棱柱状位错环。
GBn266-87
2.11.3氢致缺陷的抑制
单晶生长时,采用较快冷却的方法(如加大氢气流量),抑制氢原子聚集成团,使氢原子较均匀地分布于硅晶体中。另外,可采用使硅片快速推进高温区进行预热处理,使微小氢原子团溶解并扩散出硅片表面。经此种工艺处理后的硅片,在随后的器件工艺中不再产生可观察到的氢致缺陷。3硅片加工缺陷
3.1刀痕
刀痕是硅片切割加工时在硅片表面遗留下的切割痕迹。严重的刀痕形成一系列凹凸相间圆弧形沟槽,圆弧的半径与切割刀具半径相同(见图255~257)切片机有较大的机械振动,刀片安装不平整,刀口处金刚石涂层及进刀速度不均勾都会使硅片上留下明显痕迹。
3.2崩边和缺口
崩边是不贯穿硅片前、背表面的局部边缘破损(见图258)。缺口是贯穿硅片前、背表面的局部边缘破损(见图259~260)切片机有较大的机械振动、刀具摆动或研磨时硅片承受压力不均匀以及操作不当等原因都可能造成崩边或缺口。缺口一般沿硅晶体解理面发生,并常伴有裂纹。3.3裂纹
裂纹是硅片上不贯穿整个表面的裂痕。裂纹容易沿晶体解理面产生,故在11111面上裂纹呈“-\字或“Y”字形,(100】面上呈“”字或“十”字形(见图261~263)。磨片过程中,硅片局部受力不均匀,是造成裂纹的主要原因。3.4划道和拉丝(擦伤)
划道系指在研磨和抛光工艺过程中,在硅片表面上出现宏观无规则的浅沟(见图264),它们是由于磨盘质量不佳或磨料和抛光液中混有较大的硬质颗粒造成的。拉丝(擦伤)是指在经过严格清洗处理的抛光面上,所见到的一些无规则轻微的划痕(见图265~266)。拉丝通常是由于抛光环境不够洁净,抛光液中混有微小颗粒造成的。3:5塌边
塌边是抛光工艺中,在硅片边缘区域形成斜坡状加工缺陷(见图267)。它是由于抛光布太软,抛光速度过慢,抛光时间过长以及抛光前的化学腐蚀时边缘减薄量较多等因素所致。3.6亮点
亮点是指研磨或抛光时硅片上可观察到的孤立小亮点(见图268)。亮点的大小、数量不等。亮点是研磨或抛光不充分,残留下来的一些孤立机械损伤点。3.7波纹和平整度
波纹是指硅片抛光表面上遗留下的种宏观波纹状起伏。波纹表征抛光表面不平整,在荧光灯下根据灯影是否平直检查平整度或利用激光干涉条纹来评价硅片表面平整程度(见图269~271)。化学减薄时,腐蚀液定向流动,抛光过程中硅片停转等因素都可能造成波纹。3.8桔皮
在显微镜下观察到抛光表面呈现大面积类似桔皮状粗糙表面称桔皮。桔皮是由于化学减薄不均匀,抛光液pH值不合适,抛光片旋转不均匀等因素引起的。3.9凹坑和小丘
凹坑指硅片抛光表面上的一种凹陷,具有-一定的形状。小丘系指硅片抛光表面存在的不规则突起,又叫做台阶。3.10抛光雾
硅片抛光表面上,如存在高密度的凹坑、小丘和拉丝等缺陷时对强光发生漫反射而呈现出的一种6
GBn266-87
宏观雾状缺陷,称做抛光雾。抛光表面氧化也呈雾状,但进一步抛光可去除(见图272)。3.11残留机械损伤
残留机械损伤是经过切、磨、抛加工之后,在硅片表面残留下来的机械损伤。残留机械损伤与整个硅片加工过程有关,但主要是因抛光不充分,机械损伤层未完全去掉所致。残留机械损伤在高温氧化过程中将诱生出氧化层错等二次缺陷,通常用氧化层错的密度来检测硅片抛光质量(见图273~288)。
3.12.表面沾污
硅片抛光后清洁处理不彻底而在抛光表面残存如水迹、溶剂等有机物质以及外界引入的各种沾污如尘埃、指印等称为表面沾污(见图289~294)。4硅外延缺陷
4.1.外延位错
外延位错是外延工艺中产生的位错,它是外延层中常见的一种缺陷。4.1.1.外延位错的魔蚀形态及分布应用化学腐蚀方法,在显微镜下观察到的外延位错蚀坑形状及分布与原生硅单晶位错类似。a:在显微镜下整个外延层上常常观察到位错蚀坑呈较为均匀分布,并常伴有外延层错(见图295~297)。
b.滑移线是外延层表面上,沿<110>滑移方向延伸的直线,它多为贯穿整个表面的直线(见图298)。滑移线是由位错源在应力作用下产生大量位错并不断沿<110方向滑移出硅片表面而形成的。在显微镜下,它的微观结构是由许多台阶组成的滑移带。外延片上的位错排是位错蚀坑的某一边沿<110>方向排列在一条直线的一种位错分布组态(见图299)。它是因为由同一位错源产生的位错滑移运动受阻,位错堆积而成。c.外延片上的星形结构是由大量位错排组成的一种位错宏观分布,多数是由于衬底的残留机械损伤和较大的热应力引起的。
4.1.2外延位错产生原因
外延位错一般是由于衬底内位错向外延层延伸,或由衬底表面机械损伤等硅片加工缺陷,在热应力的作用下产生大量滑移位错。另外,因外延层与衬底界面处的晶格失配,也可产生失配位错。4.1.3·外延位错抑制方法
选用无位错硅单晶制备衬底,提高衬底加工质量,避免一切可能的加工缺陷,合理控制外延生长的升降温速率,减小衬底径向温度梯度等,都可减少或抑制外延位错的产生。4.2外延层错
外延工艺中产生的层错称为外延层错。外延层错是本征层错,柏格斯失量为号<111>。外延层错是外延层中主要缺陷之一
4.2.1外延层错的形态
经择优化学腐蚀后,在显微镜下可观察到各种形态的外延层错。在(111)外延片上,外延层错呈正三角形、V字形、一字形或多边形的腐蚀槽(见图300~304)。而在(100)外延片上,外延层错为正方形、L字形、一字形或多边形的腐蚀槽(见图305~306)。如用干涉相衬显微镜,不需化学腐蚀,可直接看到外延层错。
4.2.2外延层错产生原因
外延层错多成核于衬底表面。衬底中的各种晶体缺陷,衬底表面机核损伤以及外来沾污等都可能成为外延层错成核中心(见图307~311)。此外,当外延生长温度偏低,生长速率过快或温度起伏较大而产生热应力等因素都将促使外延层错密度的增加。外延层错随着外延层的生长而长大。GBn266—87
4.2.3减少和消除外延层错的方法消除外延层错最根本的方法是提高衬底表面的抛光质量,减少残存的机械损伤和避免外来沾污。在工艺上,外延生长前对衬底表面进行HC1或HBr气相腐蚀抛光,是减少外延层错的有效方法。另外,提高反应剂和氢气的纯度以及反应系统的洁净度,都有助于减少外延层错。4.3棱锥
棱锥又称角锥,为外延层表面的一种突起物。在(111)面外延层上,一个棱锥一般由三个李晶四面体组成,并常与一个外延层错相联系,两者相对转过60°角(见图312~322)。棱锥一般认为是由外延层与衬底界面处各种不完整性引起的。衬底表面存在杂质沾污或反应系统漏气等导致外延各向异性生长,形成棱锥。外延生长速率过快或衬底晶向偏离度很小(<0.5°),也容易形成棱锥。高密度的棱锥形成所谓棱脉状缺陷(见图323~325)。为了避免棱锥,首先是保证外延系统和衬底表面无任何沾污。此外,适当提高外延温度,使衬底晶向朝最近的<110>方向偏离<111>3~5°等措施都可减少棱锥的产生。4.4乳突
乳突为外延表面上一种尺寸较大的突起物。在乳突的顶端多为一棱锥(见图326~327)。可见,乳突的形成是由棱锥生长引起的。乳突的产生原因和消除方法同棱锥。4.5层错阴影(月芽、鱼尾等)
当外延生长表面偏离(111)面较多时,在沿着外延层错一定方向的表面上,产生形如月芽、鱼尾等形状的凹沟,统称层错阴影。这种缺陷有许多变态,都是由于外延层错妨碍生长前沿(二维)推进而产生的。层错阴影的方向、形状与衬底取向有密切关系。沟深与外延层厚度成正比,晶向偏离<111>角度越大,阴影越长,衬底接近正(111)面时,阴影即会消失。4.6·多晶点
多晶点是由外延层表面上形成的多晶颗粒构成的一种外延缺陷(见图328~330)。它是由衬底表面的杂质颗粒或外延生长时发生氧化而生成的。加强衬底洁净处理,防止氧化气氛进人反应系统,可防止多晶点产生。
4.7氧化白雾
氧化白雾是指外延层表面不经化学腐蚀,直接观察到的一种白雾状宏观缺陷。在显微镜下是由高密度的棱锥、乳突、多晶点等缺陷组成的(见图331~340)。产生原因和消除方法与棱锥、乳突、多晶点等相同。
4.8雾缺陷
外延层表面经择优腐蚀后,有时可观察到宏观上呈云雾状的缺陷,在显微镜下是由密度极高的小浅蚀坑组成,故称为雾缺陷(见图341~343)。一般认为雾缺陷主要是因为高温外延生长时外来金属杂质污染引起的。污染可能来自反应系统、石墨基座、反应气体和环境等。因此,消除外界杂质污染源或采用吸除技术,可以有效地减少或消除雾缺陷。4.9取向平台
取向平台为一种平台状的凸起,多发生在<111>取向外延片的边缘。由于1111]面腐蚀速度最慢,在化学气相腐蚀时,如果在衬底边缘处出现正(111)面,祖露区就会因腐蚀慢而成为凸起的平台,外延生长后发展成取向平台。
4.10雪球和钉
外延生长时,由于球形杂质颗粒在外延层上滚动而形成的缺陷称为雪球。它包括杂质颗粒及其滚动的痕迹(见图344)。
钉是外延层表面一种浅凹陷沟。它是在外延反应下,液态杂质在表面运动留下的痕迹。雪球和钉在外延生长时很少见,只要严格工艺操作均可避免。4.11桔皮
GBn266-87
桔皮系指外延表面粗糙不平整的一种表面缺陷。桔皮与衬底表面的桔皮缺陷有关。4.12麻坑
外延层表面局部温度过高而形成的小凹坑称为麻坑(见图345~346)。4.13沾污
不洁净工艺操作,在外延层表面引人各种杂质沾污(见图347~348)GBn266-87bzxz.net
附录A
部分缺陷的彩色照片
(补充件)
照片见有色金属上业总公司标准计量所所制照片(图A1~图A94)
小提示:此标准内容仅展示完整标准里的部分截取内容,若需要完整标准请到上方自行免费下载完整标准文档。

标准图片预览:
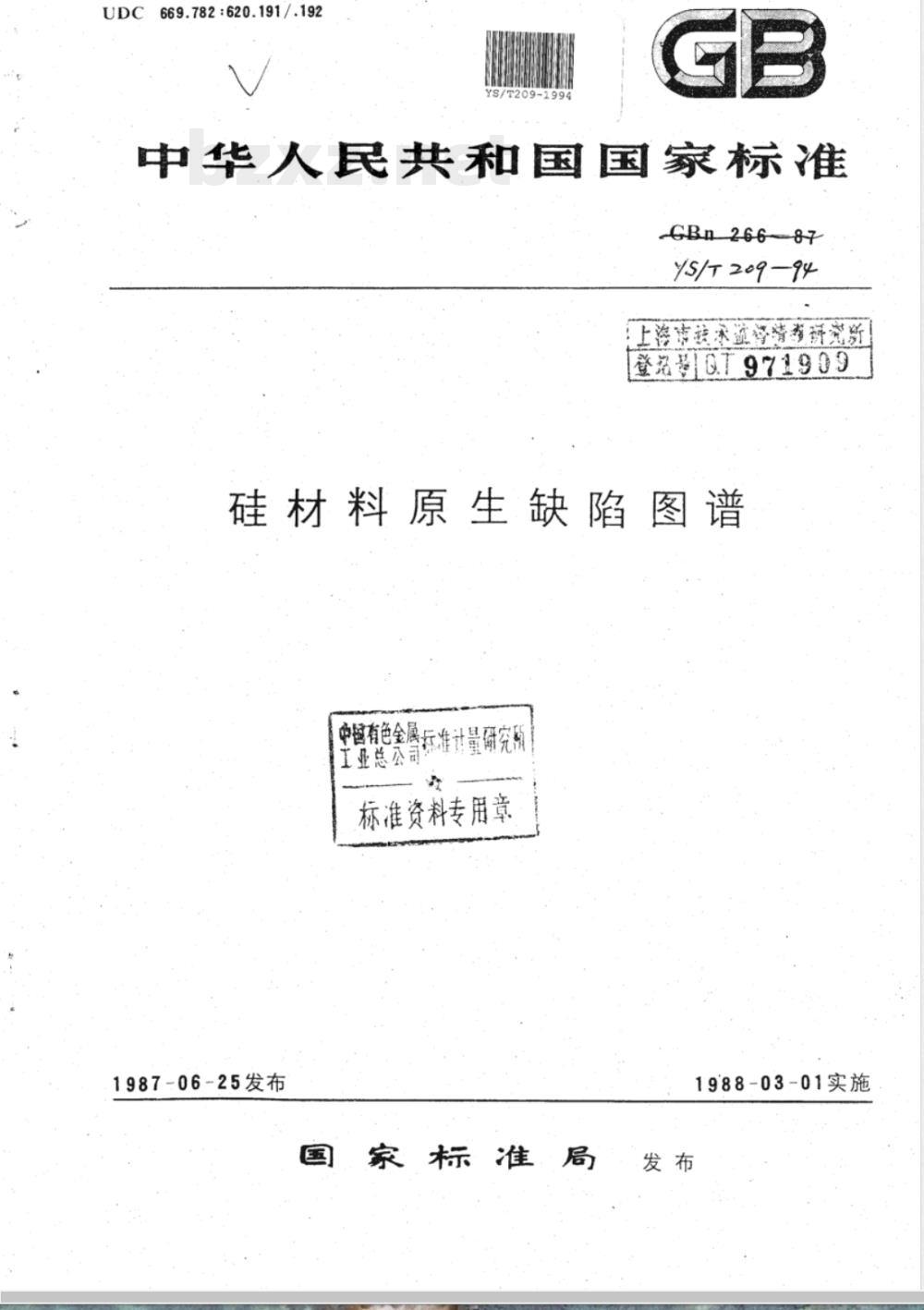
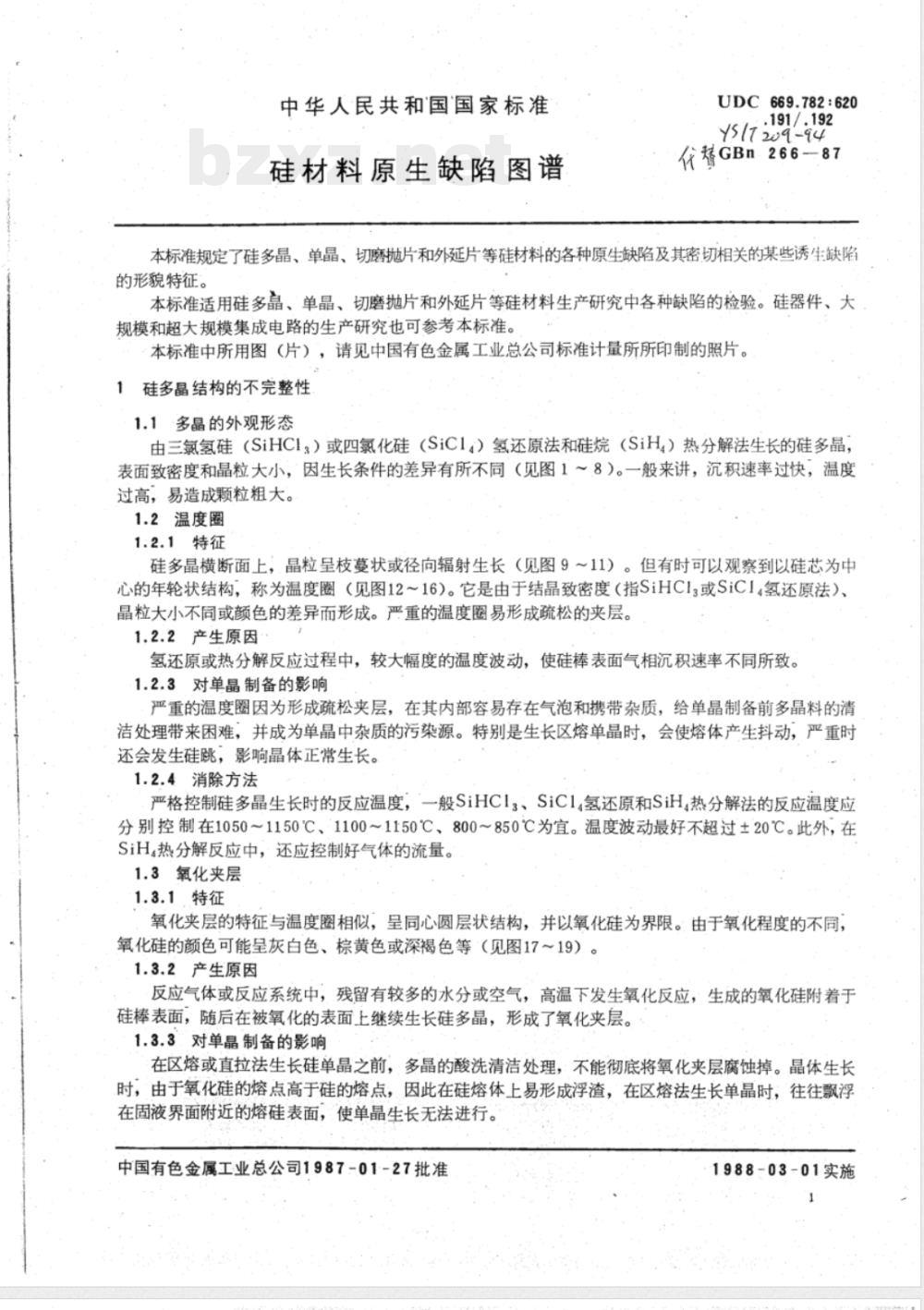
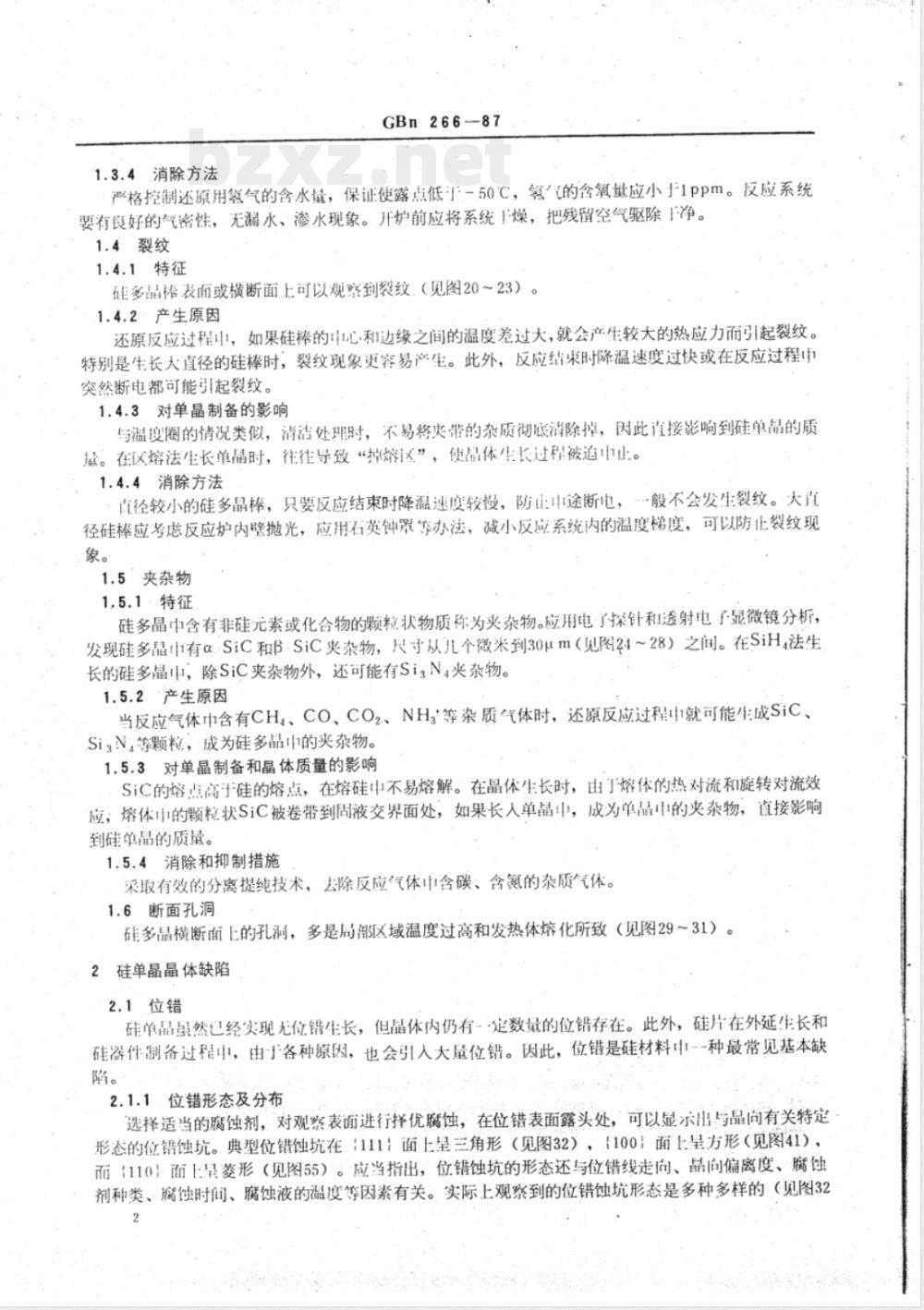
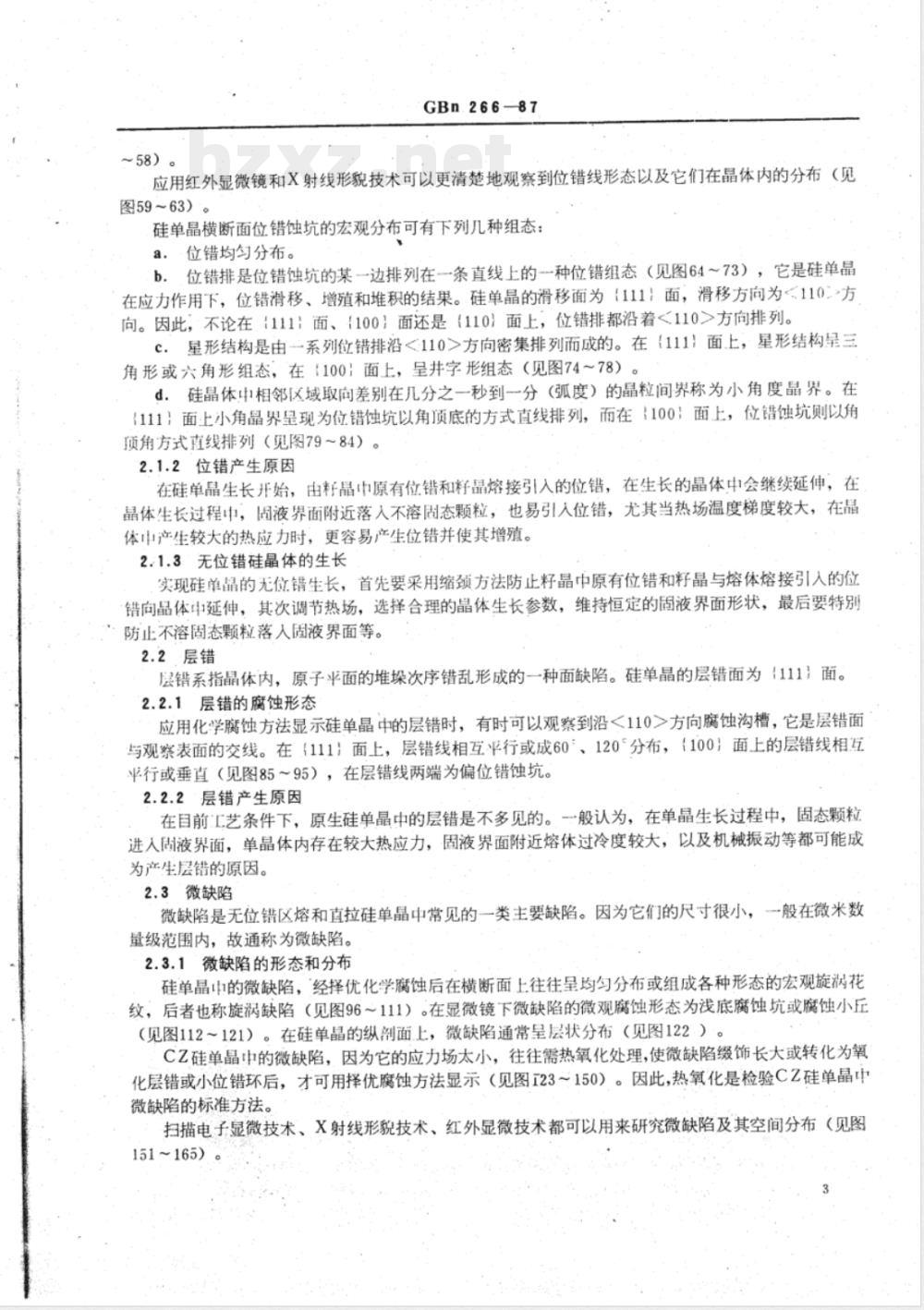
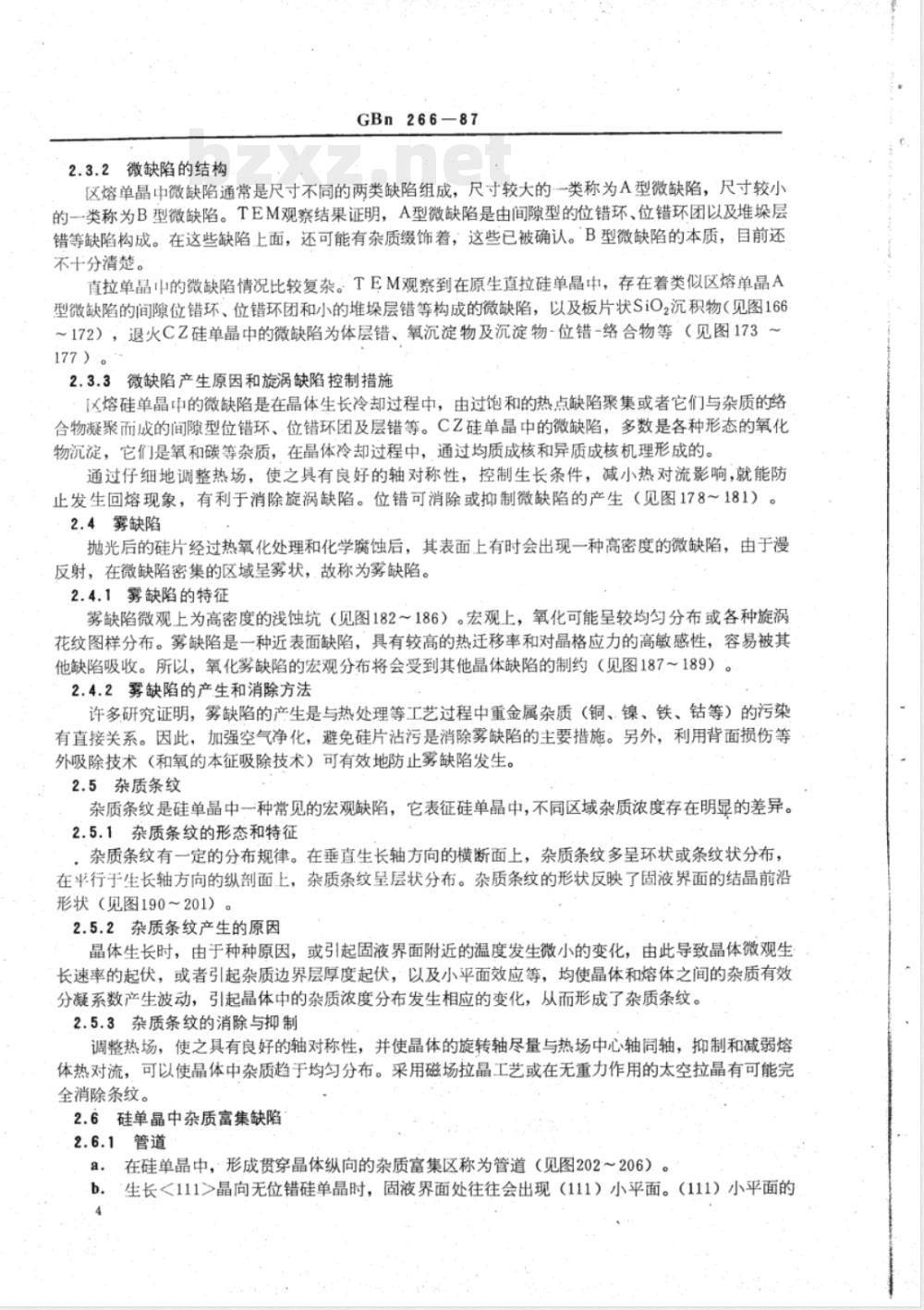
- 其它标准
- 热门标准
- 有色金属行业标准(YS)
- YS/T568.7-2006 氧化锆 氧化铪中磷量的测定(锑盐-抗坏血酸钼蓝吸光光度法)
- YS/T568.2-2006 氧化锆 氧化铪中铁量的测定(磺基水杨酸吸光光度法)
- YS/T523-2006 锡、铅及其合金箔和锌箔
- YS/T539.13-2006 镍基合金粉化学分析方法 脉冲加热惰性气熔融库仑滴定法测定氧量
- YS/T534.4-2006 氢氧化铝化学分析方法 邻二氮杂菲光度法测定三氧化二铁含量
- YS/T575.21-2006 铝土矿石化学分析方法 滴定法测定有机碳量
- YS/T568.6-2006 氧化锆 氧化铪中钛量的测定(二安替吡啉甲烷吸光光度法)
- YS/T572-2006 工业纯氧化铍粉末技术条件
- YS/T574.6-2009 电真空用锆粉化学分析方法 铬天青S分光光度法测定铝量
- YS/T509.10-2006 锂辉石、锂云母精矿化学分析方法 离子选择电极法测定锂云母中氟量
- YS/T520.2-2006 镓化学分析方法 4-(2-吡啶偶氮)-间苯二酚光度法测定铅量
- YS/T569.6-2006 铊中铅量的测定(双硫腙苯萃取吸光光度法)
- YS/T520.8-2006 镓化学分析方法 乙基紫光度法测定铟量
- YS/T535.2-2006 氟化钠化学分析方法 蒸馏 硝酸钍容量法测定氟量
- YS/T95.2-2009 空调器散热片用铝箔 第2部分 涂层铝箔
请牢记:“bzxz.net”即是“标准下载”四个汉字汉语拼音首字母与国际顶级域名“.net”的组合。 ©2009 标准下载网 www.bzxz.net 本站邮件:bzxznet@163.com
网站备案号:湘ICP备2023016450号-1
网站备案号:湘ICP备2023016450号-1