- 您的位置:
- 标准下载网 >>
- 标准分类 >>
- 机械行业标准(JB) >>
- JB/T 7280-2008 拖拉机制动系统 台架试验方法
标准号:
JB/T 7280-2008
标准名称:
拖拉机制动系统 台架试验方法
标准类别:
机械行业标准(JB)
标准状态:
现行-
发布日期:
2008-02-01 -
实施日期:
2008-07-01 出版语种:
简体中文下载格式:
.rar.pdf下载大小:
738.21 KB
替代情况:
替代JB/T 7280-1994

点击下载
标准简介:
标准下载解压密码:www.bzxz.net
本标准规定了拖拉机行车制动器及其操纵机构的台架试验方法和程序。本标准适用于农业轮式和履带拖拉机上的制动系统。 JB/T 7280-2008 拖拉机制动系统 台架试验方法 JB/T7280-2008

部分标准内容:
ICS65.060.10
备案号:23155—2008
中华人民共和国机械行业标准
JB/T7280—2008
代替JB/T7280-1994
拖拉机制动系统
台架试验方法
Testmethodof brakesystemfortractor2008-02-01发布
2008-07-01实施
中华人民共和国国家发展和改革委员会发布前言
1范围
2术语和定义
3试验项目
4试验条件
一般要求
试验设备
试验台的转动惯量
测量允差
摩擦表面温度的测量
4.6冷却条件.
制动器驱动力的测量
试验备,
试验方法和程序
第一次冷态制动效能试验.
第一次制动效能热衰退试验
6.4制动效能恢复试验
第二次冷态制动效能试验,
第二次制动效能热衰退试验
第二次磨合
6.8第三次冷态制动效能试验
6.9制动器耐久试验,
6.10操纵机构耐久试验
附录A(规范性附录)记录格式及绘制曲线格式图A.1第一、二、三次冷态制动效能试验图A.2第一、二次热衰退试验和恢复试验表A.1整车及其制动系统主要参数次
表A.2第一、二次磨合
表A.3冷态制动效能试验、第一次热衰退试验、恢复试验.表A.4第二次热衰退试验
表A.5制动器耐久试验..
表A.6摩擦衬片(衬块)磨损量
表A.7操纵机构耐久试验
JB/T7280—-2008
本标准代替JB/T7280—1994《拖拉机制动系统台架试验方法》。本标准与JB/T7280—1994相比,主要变化如下:JB/T7280—2008
-第2章定义中增加了制动周期、拖磨、制动器初温、制动时间、制动减速度、制动驱动力增加了5.8、5.9试验准备要求。-6.1.2中磨合时规定制动减速度的控制偏差在土5%以内:6.1.4中技术内容改为“按上述条件刹停磨合150次,每10次按表A.2记录一次数据。”:在6.1中第一次磨合次数改为150次,取消80%磨合面积的检查:一将6.2.2和6.2.3合并后改为:以设计规定的最大制动驱动力的六分之一为第一次制动驱动力F,按F、2F、3F、每级制动三次,每级间隔F,直至达到设计规定的制动器最大制动力矩为止:
在6.3第一次制动效能热衰退试验和6.4恢复试验规定从第一次冷态制动效能试验结果中,确定0.3g制动减速度对应的制动驱动力,以此制动驱动力进行制动:-在6.6第二次制动效能热衰退试验规定从第二次冷态制动效能试验结果中,确定0.1g制动减速度对应的制动驱动力,以此制动驱动力进行拖磨制动;6.9.2中的内容改为“耐久试验以给定的最大制动驱动力矩制动,每10次制动中的最大制动力矩控制在0.95倍~1倍给定值范围”;冷态制动效能试验图横坐标由原来的减速度改为制动驱动力;试验数据记录格式作为规范性附录放到附录A中。本标准的附录A为规范性附录。
本标准由中国机械工业联合会提出。本标准由全国拖拉机标准化技术委员会(SAC/TC140)归口。本标准起草单位:国家拖拉机质量监督检验中心、洛阳拖拉机研究所。本标准主要起草人:岳倩、张晓丹、齐劲峰、徐惠娟。本标准所代替标准的历次版本发布情况:JB/T7280—1994。
1范围
拖拉机制动系统台架试验方法
本标准规定了拖拉机行车制动器及其操纵机构的台架试验方法和程序。本标准适用于农业轮式和履带拖拉机上的制动系统。2术语和定义
下列术语和定义适用于本标准。2.1
JB/T7280—2008
maximalbrakingtorgue
最大制动力矩
指一次制动过程中,在以制动力矩为纵坐标,时间为横坐标的曲线图上,持续制动过程段纵坐标的最大值。如图1中的MBmax。
最小制动力矩minimalbrakingtorque指一次制动过程中,在以制动力矩为纵坐标,时间为横坐标的曲线图上,持续制动过程段纵坐标的最小值。如图1中的MBmin。
averagebrakingtorque
平均制动力矩
指一次制动过程中持续制动过程段,制动力矩与制动时间所包围的面积除以持续制动过程的时间所得值。
制动时间!
制动力矩增长时间
制动周期brakingcycle
持续制动时间
放松时间
在连续制动过程中,从本次制动开始到下一次制动开始所经过的时间。2.5
拖磨continuousbraking
在不切断输人动力的情况下进行制动。JB/T7280—2008
制动器初温initialtemperatareofbrake开始制动时制动鼓(盘)或制动衬片(衬块)的温度。2.7
制动时间brakingtime
包括制动力矩增长时间、持续制动时间、放松时间。2.8
制动减速度brakingdeceleration开始制动时的拖拉机初速度与制动终了时的拖拉机末速度之差除以制动时间。2.9
制动驱动力drivingforceofbrake油压或气压驱动制动的为管路的压力,机械踏板力驱动制动的为踏板力或相应杆件的力。3试验项目
制动器冷态制动效能试验。
3.2制动器热衰退试验和恢复试验。3.3制动器耐久试验。
3.4操纵机构耐久试验。
4试验条件
一般要求
被试制系统应符合按规定程序批准的图样和技术文件,按表A.1填写试样及配套主机的有关技术参4.2试验设备
试验设备采用惯性式试验台。
4.3试验台的转动惯量
试验台的转动惯量应根据动能相等的原则,按拖拉机的最大使用质量加上旋转部分的当量修正值计算。旋转部分的当量修正值取最大使用质量的7%。试验台上所选飞轮片的转动惯量与试验台其他旋转件的转动惯量之和应与计算值一致,允差为5%。当超过该允差时,允许按动能相等的原则调整安装制动器的驱动轴转速。
4.4测遥充差
试验台上安装被试制动器的驱动轴转速应与规定的试验车速确定的相应转速一致,允差为3%。4.5摩擦表面温度的测量
试验时应对被试制动器摩擦副表面的动态温度进行测量。当采用热电偶作为测温传感器时,热电偶丝直径为?0.3mm~?0.5mm,长度不超过1.0m,热端焊点直径不大于2mm。测温传感器可以埋设在被试制动器的旋转件或非旋转件上,位于摩擦表面工作宽度的正中处或有效工作半径处及接近单位分布压力的最大处,其感温触点距摩擦表面1.0mm。4.6冷却条件
试验在室温条件下进行,采用通风机对制动器进行冷却。4.7制动器驱动力的测量
4.7.1机械驱动的制动器,应测量制动器踏板的操纵力。4.7.2液压或气压驱动的制动器,应测量制动油(气)缸内工作介质的压力。5试验准备
JB/T7280—2008
5.1检查被试制动系统是否符合出厂的技术条件、各部分有无异常,用溶剂洗净摩擦副的摩擦表面。5.2在制动器的旋转部件或非旋转部件上安装测摩擦表面温度的传感器,在液压操纵的制动油缸内以及在湿式制动器的油池中安装测油温传感器。5.3机械驱动的制动器,应安装测量制动器踏板力的传感器。5.4对液压或气压驱动的制动器应在制动油(气)缸处安装测量压力的传感器。5.5为测量摩擦衬面的磨损量,应根据不同的制动器型式,预先标明并测量至少两个测点位置的摩擦面厚度,其中应包括单位压力最大处。选定点厚度的测量精度为0.01mm。5.6根据要求的试验车速,计算出试验台安装制动器的驱动轴计算转速,以便在试验过程中能调整和控制该轴的转速,见式(1):
式中:
制动器轴计算转速,单位为r/min:一规定的试验车速,单位为km/h;拖拉机驱动轮滚动半径,单位为m:m
一制动器轴与驱动轮间的转速比。5.7按式(2)计算被试制动器所承担的计算惯量负荷:1=mmax(1+0.07)r
式中:
被试制动器承担的计算转动惯量,单位为kg·m2-该拖拉机的最大使用质量,单位为kg;mmax
-拖拉机驱动轮滚动半径,单位为m;一该拖拉机行车制动器个数,一般为2m
一制动器轴与驱动轮间的转速比。(1)
(2)
5.8当施加的转动惯量超出计算惯量的允差5%时,按动能相等的原则调整安装制动器的驱动轴转速,见式(3):
式中:
n'——调整后的制动器轴转速,单位为r/min;一制动器轴计算转速,单位为r/min;I被试制动器承担的计算转动惯量,单位为kg·m2所施加转动惯量,单位为kg·m
5.9有些试验需控制制动减速度,可以通过控制制动时间达到此项要求,见式(4):3.6a
式中:
控制制动时间,单位为s;
规定的试验车速,单位为km/h;试验要求的减速度,单位为m/s2。(4)
5.10将被试制动器及操纵机构安装在试验台上,按设计要求调整好制动器总成的制动间隙。机械式操3
JB/T7280—2008
纵机构可用液压缸代替,液压式和气压式操纵机构的连接方式应与实车一致,将装上的油(气)管路和制动油缸中的空气放净,并检查管路各接点处密封情况。5.11按设计要求检查湿式制动器所在油池的油面高度,并检查试验用液压泵站的工作是否正常。5.12根据所需测量的参数及其变化范围,选择并调整好测试仪器,并把需要重新标定的测试量标定好。6试验方法和程序
6.1磨合
6.1.1制动初速度取最高设计车速的80%,即制动轴初转速为0.8n,制动末速度为零。6.1.2制动减速度为0.2g,制动减速度的偏差在5%以内。注:g为重力加速度,下同。
6.1.3打开通风机并调整制动间隔时间,使每次制动前制动器摩擦表面的初温控制在100℃以下。6.1.4按上述条件刹停磨合150次,每10次按表A.2记录一次数据。6.1.5检查制动器及操纵机构有无异常状况,按表A.2填写检查结果。6.2第一次冷态制动效能试验
6.2.1制动初速度为最高设计车速,即制动轴初转速n,制动末速度为零。6.2.2以设计规定的最大制动驱动力的六分之一为第一次制动驱动力F,按F、2F、3F、每级制动3次,每级间隔F,直至达到设计规定的制动器最大制动力矩为止。6.2.3每次制动前制动器摩擦副表面的初温控制在65℃5℃。6.2.4按表A.3记录每次制动数据,按图A.1绘制曲线,备注记录试验过程中的异常和声响。6.3第一次制动效能热衰退试验
6.3.1制动初速度为最高设计车速,即制动轴初转速n,制动末速度为零。6.3.2从第一次冷态制动效能试验结果中,确定0.3g制动减速度对应的制动驱动力,以此制动驱动力进行制动。
6.3.3第一次制动的摩擦副表面初温为65℃土5℃。试验过程中关闭通风机。干式制动器从制动初速度刹停15次,湿式制动器从制动初速度刹停25次。制动周期为60s。6.3.4
湿式制动器在试验过程中,当油池中油温低于85℃时,应禁止油液循环,以防制动器降温。6.3.5
每次试验按表A.3记录数据,最后按图A.2绘制曲线。6.3.6
6.3.7热衰退试验结束后,使制动器驱动轴以相当于15km/h车速的转速运转,同时打开通风机,以8m/s的风速冷却3min后开始恢复试验。6.4制动效能恢复试验
6.4.1试验要求按6.3.1~6.3.6的规定,但是在整个试验过程,以8m/s的风速冷却被试制动器。6.4.2按表A.3和图A.2记录数据和绘制曲线。6.5第二次冷态制动效能试验
试验要求按6.2的规定。
6.6第二次制动效能热衰退试验
6.6.1制动初速度为最高设计车速的70%,即制动轴初转速0.7n。6.6.2从第二次冷态制动效能试验结果中,确定0.1g制动减速度对应的制动驱动力,以此制动驱动力进行拖磨制动。
6.6.3第一次制动时被试制动器摩擦副表面的初温为65℃土5℃。6.6.4试验过程中关闭通风机。湿式制动器油池中油温低于85℃时,禁止其油液循环。6.6.5每次拖磨40s(机械式和液压式)、15s(气压式)、80s(湿式),拖磨间断时间60s(机械式和液压式)、20s(气压式)、30s(湿式),试验总时间为30min。6.6.6观察并记录摩擦衬片(衬块)在第几次拖磨时发出烧焦味、冒烟:第几次出现气阻与气阻时的4
摩擦副表面温度。
6.6.7每次制动按表A.4记录数据,最后按图A.2绘制曲线。JB/T7280—2008
6.6.8拖磨试验结束后打开通风机,使被试制动器以相当于车速为15km/h的转速运转并冷却至室温。拆开被试制动器,检查摩擦衬片(衬块)的龟裂、积炭与烧焦状况,以及摩擦材料表面有无亮膜等,并作记录。
6.6.9对液压操纵式制动器或湿式制动器,应在试验停止后冷却过程中,继续记录制动油缸内的油温上升值,直至达到最高温度为止,并记录从试验停止至达到最高温度值的时间。6.7第二次磨合
磨合要求按6.1的规定。但刹停50次。6.8第三次冷态制动效能试验
试验要求按6.2的规定。
6.9制动器耐久试验
6.9.1制动初速度为最高设计车速,即制动轴初转速n,制动末速度为零。6.9.2试验中施加表A.1给定的最大制动力矩,每10次制动中最大的制动力矩范围控制在0.95倍~1倍的最大制动力矩之间。
6.9.3第一次制动摩擦副表面的初温低于100℃。6.9.4试验过程中打开通风机,以8m/s的风速冷却被试制动器。湿式制动器还应使制动器中的油液循环流动。
6.9.5以40s的制动周期连续刹停100次。6.9.6按表A.5记录第1次、第50次和第100次制动时的数据,备注记录试验过程中的异常现象。6.9.7刹停100次以后,让试验台上制动器的驱动轴以相当于15km/h车速的转速运转,直至摩擦副表面温度低于100℃。
6.9.8按6.9.16.9.7的要求共进行50个重复试验(总共制动5000次)。6.9.9记录已完成的制动总次数、制动器摩擦副表面的最高温度,并按表A.5填人数据。6.9.10拆开制动器,仔细检查并记录制动器各零部件的状况,测定摩擦衬片(衬块)指定点的厚度,计算摩擦衬片(衬块)的总磨损量。将其结果记人表A.6。6.10操纵机构耐久试验
将被试制动系统安装在台架上,并按使用说明书的要求调整好。6.10.1
6.10.2试验过程中,使安装制动器的驱动轴低速运转。6.10.3以最大制动力矩相应的制动驱动力进行制动驱动。6.10.4以4s的制动周期连续制动25×10次。6.10.5在试验过程中,如制动部件温度超过250℃(干式制动器)或150℃(湿式制动器),应降低制动频率或打开通风机以8m/s的风速进行冷却。6.10.6按表A.7记录试验中的故障、完成的制动次数、操纵机构的工作状态。试验结束后,解体检查并记录被试操纵机构各元件磨损、变形、裂纹或油(气)管路、接头的漏损等现象。5
JB/T7280—2008
最大设计车速vkm/h
整车最大使用质量mmaxkg
附录A
(规范性附录)
记录格式及绘制曲线格式
整车及其制动系统主要参数
生产企业
制动器驱动轴与驱动轮轴间转速比制动器所在轮胎滚动半径或版带驱动轮节圆半径rm制动器使用个数5
制动器旋向及所在部位
制动器型式
制动器驱动力型式
制动器摩擦材料
制动器摩擦副总间隙
制动器制动液牌号
制动器设计的最大操纵力N,或最大油(气)压力kPa制动器设计的最大制动力矩N·m表A.2第一、二次磨合
样品编号
试验车速
制动次数
检查结果
样品编号
试验车速
制动驱动力
MPa或N
制动驱动力
MPa或N
试验日期
制动初转速
制动力矩
出厂日期
操作者
制动时间
恢复试验
第一次热衰退试验、
冷态制动效能试验、
试验日期
制动初转速
制动时间
制动力矩
操作者
摩擦副表面最
高温度
最大最小平均
制动油最
高温度
制动减速度
制动减速度
样品编号
试验车速
制动次数
检查结果
制动驱动力
MPa或N
制动驱动力 kPa或N
图A.1第一、二、三次冷态制动效能试验pbZxz.net
试验次数
第一、二次热衰退试验和恢复试验图A.2
表A.4第二次热衰退试验
试验日期
制动初转速
制动力矩
摩擦副表面最高温度
操作者
制动油最高温度
JB/T7280—2008
累计试验时间
JB/T7280—2008
样品编号
试验车速
制动总次数
第1次
第50次
第100次
第101次
制动驱动力
MPa或N
样品编号
摩擦材料
测量点
磨损量
样品编号
试验开始日期
操纵机构型式
完成的试验次数
操纵机构工作状态
表A.5制动器耐久试验
试验开始日期
试验结束日期
试验台驱动轴转速
摩擦副表面最高温度
操作者
第一、二、三、…、五十个100次制动试验制动力矩
制动时间
最小平均
摩擦副表面
表A.6摩擦衬片(衬块)磨损量
生产企业
制动前摩擦副初温
操纵机构耐久试验
试验结束日期
操作者
制动减速度
中华人民共和国
机械行业标准
拖拉机制动系统
台架试验方法
JB/T7280—2008
机械工业出版社出版发行
北京市百万庄大街22号
邮政编码:100037
210mm×297mm?0.75印张·21千字2008年7月第1版第1次印刷
书号:15111:9080
网址:http:1/cmpbook.com编辑部电话:(010)88379778
(010)88379693
直销中心电话:
封面无防伪标均为盗版
版权专有侵权必究
小提示:此标准内容仅展示完整标准里的部分截取内容,若需要完整标准请到上方自行免费下载完整标准文档。
备案号:23155—2008
中华人民共和国机械行业标准
JB/T7280—2008
代替JB/T7280-1994
拖拉机制动系统
台架试验方法
Testmethodof brakesystemfortractor2008-02-01发布
2008-07-01实施
中华人民共和国国家发展和改革委员会发布前言
1范围
2术语和定义
3试验项目
4试验条件
一般要求
试验设备
试验台的转动惯量
测量允差
摩擦表面温度的测量
4.6冷却条件.
制动器驱动力的测量
试验备,
试验方法和程序
第一次冷态制动效能试验.
第一次制动效能热衰退试验
6.4制动效能恢复试验
第二次冷态制动效能试验,
第二次制动效能热衰退试验
第二次磨合
6.8第三次冷态制动效能试验
6.9制动器耐久试验,
6.10操纵机构耐久试验
附录A(规范性附录)记录格式及绘制曲线格式图A.1第一、二、三次冷态制动效能试验图A.2第一、二次热衰退试验和恢复试验表A.1整车及其制动系统主要参数次
表A.2第一、二次磨合
表A.3冷态制动效能试验、第一次热衰退试验、恢复试验.表A.4第二次热衰退试验
表A.5制动器耐久试验..
表A.6摩擦衬片(衬块)磨损量
表A.7操纵机构耐久试验
JB/T7280—-2008
本标准代替JB/T7280—1994《拖拉机制动系统台架试验方法》。本标准与JB/T7280—1994相比,主要变化如下:JB/T7280—2008
-第2章定义中增加了制动周期、拖磨、制动器初温、制动时间、制动减速度、制动驱动力增加了5.8、5.9试验准备要求。-6.1.2中磨合时规定制动减速度的控制偏差在土5%以内:6.1.4中技术内容改为“按上述条件刹停磨合150次,每10次按表A.2记录一次数据。”:在6.1中第一次磨合次数改为150次,取消80%磨合面积的检查:一将6.2.2和6.2.3合并后改为:以设计规定的最大制动驱动力的六分之一为第一次制动驱动力F,按F、2F、3F、每级制动三次,每级间隔F,直至达到设计规定的制动器最大制动力矩为止:
在6.3第一次制动效能热衰退试验和6.4恢复试验规定从第一次冷态制动效能试验结果中,确定0.3g制动减速度对应的制动驱动力,以此制动驱动力进行制动:-在6.6第二次制动效能热衰退试验规定从第二次冷态制动效能试验结果中,确定0.1g制动减速度对应的制动驱动力,以此制动驱动力进行拖磨制动;6.9.2中的内容改为“耐久试验以给定的最大制动驱动力矩制动,每10次制动中的最大制动力矩控制在0.95倍~1倍给定值范围”;冷态制动效能试验图横坐标由原来的减速度改为制动驱动力;试验数据记录格式作为规范性附录放到附录A中。本标准的附录A为规范性附录。
本标准由中国机械工业联合会提出。本标准由全国拖拉机标准化技术委员会(SAC/TC140)归口。本标准起草单位:国家拖拉机质量监督检验中心、洛阳拖拉机研究所。本标准主要起草人:岳倩、张晓丹、齐劲峰、徐惠娟。本标准所代替标准的历次版本发布情况:JB/T7280—1994。
1范围
拖拉机制动系统台架试验方法
本标准规定了拖拉机行车制动器及其操纵机构的台架试验方法和程序。本标准适用于农业轮式和履带拖拉机上的制动系统。2术语和定义
下列术语和定义适用于本标准。2.1
JB/T7280—2008
maximalbrakingtorgue
最大制动力矩
指一次制动过程中,在以制动力矩为纵坐标,时间为横坐标的曲线图上,持续制动过程段纵坐标的最大值。如图1中的MBmax。
最小制动力矩minimalbrakingtorque指一次制动过程中,在以制动力矩为纵坐标,时间为横坐标的曲线图上,持续制动过程段纵坐标的最小值。如图1中的MBmin。
averagebrakingtorque
平均制动力矩
指一次制动过程中持续制动过程段,制动力矩与制动时间所包围的面积除以持续制动过程的时间所得值。
制动时间!
制动力矩增长时间
制动周期brakingcycle
持续制动时间
放松时间
在连续制动过程中,从本次制动开始到下一次制动开始所经过的时间。2.5
拖磨continuousbraking
在不切断输人动力的情况下进行制动。JB/T7280—2008
制动器初温initialtemperatareofbrake开始制动时制动鼓(盘)或制动衬片(衬块)的温度。2.7
制动时间brakingtime
包括制动力矩增长时间、持续制动时间、放松时间。2.8
制动减速度brakingdeceleration开始制动时的拖拉机初速度与制动终了时的拖拉机末速度之差除以制动时间。2.9
制动驱动力drivingforceofbrake油压或气压驱动制动的为管路的压力,机械踏板力驱动制动的为踏板力或相应杆件的力。3试验项目
制动器冷态制动效能试验。
3.2制动器热衰退试验和恢复试验。3.3制动器耐久试验。
3.4操纵机构耐久试验。
4试验条件
一般要求
被试制系统应符合按规定程序批准的图样和技术文件,按表A.1填写试样及配套主机的有关技术参4.2试验设备
试验设备采用惯性式试验台。
4.3试验台的转动惯量
试验台的转动惯量应根据动能相等的原则,按拖拉机的最大使用质量加上旋转部分的当量修正值计算。旋转部分的当量修正值取最大使用质量的7%。试验台上所选飞轮片的转动惯量与试验台其他旋转件的转动惯量之和应与计算值一致,允差为5%。当超过该允差时,允许按动能相等的原则调整安装制动器的驱动轴转速。
4.4测遥充差
试验台上安装被试制动器的驱动轴转速应与规定的试验车速确定的相应转速一致,允差为3%。4.5摩擦表面温度的测量
试验时应对被试制动器摩擦副表面的动态温度进行测量。当采用热电偶作为测温传感器时,热电偶丝直径为?0.3mm~?0.5mm,长度不超过1.0m,热端焊点直径不大于2mm。测温传感器可以埋设在被试制动器的旋转件或非旋转件上,位于摩擦表面工作宽度的正中处或有效工作半径处及接近单位分布压力的最大处,其感温触点距摩擦表面1.0mm。4.6冷却条件
试验在室温条件下进行,采用通风机对制动器进行冷却。4.7制动器驱动力的测量
4.7.1机械驱动的制动器,应测量制动器踏板的操纵力。4.7.2液压或气压驱动的制动器,应测量制动油(气)缸内工作介质的压力。5试验准备
JB/T7280—2008
5.1检查被试制动系统是否符合出厂的技术条件、各部分有无异常,用溶剂洗净摩擦副的摩擦表面。5.2在制动器的旋转部件或非旋转部件上安装测摩擦表面温度的传感器,在液压操纵的制动油缸内以及在湿式制动器的油池中安装测油温传感器。5.3机械驱动的制动器,应安装测量制动器踏板力的传感器。5.4对液压或气压驱动的制动器应在制动油(气)缸处安装测量压力的传感器。5.5为测量摩擦衬面的磨损量,应根据不同的制动器型式,预先标明并测量至少两个测点位置的摩擦面厚度,其中应包括单位压力最大处。选定点厚度的测量精度为0.01mm。5.6根据要求的试验车速,计算出试验台安装制动器的驱动轴计算转速,以便在试验过程中能调整和控制该轴的转速,见式(1):
式中:
制动器轴计算转速,单位为r/min:一规定的试验车速,单位为km/h;拖拉机驱动轮滚动半径,单位为m:m
一制动器轴与驱动轮间的转速比。5.7按式(2)计算被试制动器所承担的计算惯量负荷:1=mmax(1+0.07)r
式中:
被试制动器承担的计算转动惯量,单位为kg·m2-该拖拉机的最大使用质量,单位为kg;mmax
-拖拉机驱动轮滚动半径,单位为m;一该拖拉机行车制动器个数,一般为2m
一制动器轴与驱动轮间的转速比。(1)
(2)
5.8当施加的转动惯量超出计算惯量的允差5%时,按动能相等的原则调整安装制动器的驱动轴转速,见式(3):
式中:
n'——调整后的制动器轴转速,单位为r/min;一制动器轴计算转速,单位为r/min;I被试制动器承担的计算转动惯量,单位为kg·m2所施加转动惯量,单位为kg·m
5.9有些试验需控制制动减速度,可以通过控制制动时间达到此项要求,见式(4):3.6a
式中:
控制制动时间,单位为s;
规定的试验车速,单位为km/h;试验要求的减速度,单位为m/s2。(4)
5.10将被试制动器及操纵机构安装在试验台上,按设计要求调整好制动器总成的制动间隙。机械式操3
JB/T7280—2008
纵机构可用液压缸代替,液压式和气压式操纵机构的连接方式应与实车一致,将装上的油(气)管路和制动油缸中的空气放净,并检查管路各接点处密封情况。5.11按设计要求检查湿式制动器所在油池的油面高度,并检查试验用液压泵站的工作是否正常。5.12根据所需测量的参数及其变化范围,选择并调整好测试仪器,并把需要重新标定的测试量标定好。6试验方法和程序
6.1磨合
6.1.1制动初速度取最高设计车速的80%,即制动轴初转速为0.8n,制动末速度为零。6.1.2制动减速度为0.2g,制动减速度的偏差在5%以内。注:g为重力加速度,下同。
6.1.3打开通风机并调整制动间隔时间,使每次制动前制动器摩擦表面的初温控制在100℃以下。6.1.4按上述条件刹停磨合150次,每10次按表A.2记录一次数据。6.1.5检查制动器及操纵机构有无异常状况,按表A.2填写检查结果。6.2第一次冷态制动效能试验
6.2.1制动初速度为最高设计车速,即制动轴初转速n,制动末速度为零。6.2.2以设计规定的最大制动驱动力的六分之一为第一次制动驱动力F,按F、2F、3F、每级制动3次,每级间隔F,直至达到设计规定的制动器最大制动力矩为止。6.2.3每次制动前制动器摩擦副表面的初温控制在65℃5℃。6.2.4按表A.3记录每次制动数据,按图A.1绘制曲线,备注记录试验过程中的异常和声响。6.3第一次制动效能热衰退试验
6.3.1制动初速度为最高设计车速,即制动轴初转速n,制动末速度为零。6.3.2从第一次冷态制动效能试验结果中,确定0.3g制动减速度对应的制动驱动力,以此制动驱动力进行制动。
6.3.3第一次制动的摩擦副表面初温为65℃土5℃。试验过程中关闭通风机。干式制动器从制动初速度刹停15次,湿式制动器从制动初速度刹停25次。制动周期为60s。6.3.4
湿式制动器在试验过程中,当油池中油温低于85℃时,应禁止油液循环,以防制动器降温。6.3.5
每次试验按表A.3记录数据,最后按图A.2绘制曲线。6.3.6
6.3.7热衰退试验结束后,使制动器驱动轴以相当于15km/h车速的转速运转,同时打开通风机,以8m/s的风速冷却3min后开始恢复试验。6.4制动效能恢复试验
6.4.1试验要求按6.3.1~6.3.6的规定,但是在整个试验过程,以8m/s的风速冷却被试制动器。6.4.2按表A.3和图A.2记录数据和绘制曲线。6.5第二次冷态制动效能试验
试验要求按6.2的规定。
6.6第二次制动效能热衰退试验
6.6.1制动初速度为最高设计车速的70%,即制动轴初转速0.7n。6.6.2从第二次冷态制动效能试验结果中,确定0.1g制动减速度对应的制动驱动力,以此制动驱动力进行拖磨制动。
6.6.3第一次制动时被试制动器摩擦副表面的初温为65℃土5℃。6.6.4试验过程中关闭通风机。湿式制动器油池中油温低于85℃时,禁止其油液循环。6.6.5每次拖磨40s(机械式和液压式)、15s(气压式)、80s(湿式),拖磨间断时间60s(机械式和液压式)、20s(气压式)、30s(湿式),试验总时间为30min。6.6.6观察并记录摩擦衬片(衬块)在第几次拖磨时发出烧焦味、冒烟:第几次出现气阻与气阻时的4
摩擦副表面温度。
6.6.7每次制动按表A.4记录数据,最后按图A.2绘制曲线。JB/T7280—2008
6.6.8拖磨试验结束后打开通风机,使被试制动器以相当于车速为15km/h的转速运转并冷却至室温。拆开被试制动器,检查摩擦衬片(衬块)的龟裂、积炭与烧焦状况,以及摩擦材料表面有无亮膜等,并作记录。
6.6.9对液压操纵式制动器或湿式制动器,应在试验停止后冷却过程中,继续记录制动油缸内的油温上升值,直至达到最高温度为止,并记录从试验停止至达到最高温度值的时间。6.7第二次磨合
磨合要求按6.1的规定。但刹停50次。6.8第三次冷态制动效能试验
试验要求按6.2的规定。
6.9制动器耐久试验
6.9.1制动初速度为最高设计车速,即制动轴初转速n,制动末速度为零。6.9.2试验中施加表A.1给定的最大制动力矩,每10次制动中最大的制动力矩范围控制在0.95倍~1倍的最大制动力矩之间。
6.9.3第一次制动摩擦副表面的初温低于100℃。6.9.4试验过程中打开通风机,以8m/s的风速冷却被试制动器。湿式制动器还应使制动器中的油液循环流动。
6.9.5以40s的制动周期连续刹停100次。6.9.6按表A.5记录第1次、第50次和第100次制动时的数据,备注记录试验过程中的异常现象。6.9.7刹停100次以后,让试验台上制动器的驱动轴以相当于15km/h车速的转速运转,直至摩擦副表面温度低于100℃。
6.9.8按6.9.16.9.7的要求共进行50个重复试验(总共制动5000次)。6.9.9记录已完成的制动总次数、制动器摩擦副表面的最高温度,并按表A.5填人数据。6.9.10拆开制动器,仔细检查并记录制动器各零部件的状况,测定摩擦衬片(衬块)指定点的厚度,计算摩擦衬片(衬块)的总磨损量。将其结果记人表A.6。6.10操纵机构耐久试验
将被试制动系统安装在台架上,并按使用说明书的要求调整好。6.10.1
6.10.2试验过程中,使安装制动器的驱动轴低速运转。6.10.3以最大制动力矩相应的制动驱动力进行制动驱动。6.10.4以4s的制动周期连续制动25×10次。6.10.5在试验过程中,如制动部件温度超过250℃(干式制动器)或150℃(湿式制动器),应降低制动频率或打开通风机以8m/s的风速进行冷却。6.10.6按表A.7记录试验中的故障、完成的制动次数、操纵机构的工作状态。试验结束后,解体检查并记录被试操纵机构各元件磨损、变形、裂纹或油(气)管路、接头的漏损等现象。5
JB/T7280—2008
最大设计车速vkm/h
整车最大使用质量mmaxkg
附录A
(规范性附录)
记录格式及绘制曲线格式
整车及其制动系统主要参数
生产企业
制动器驱动轴与驱动轮轴间转速比制动器所在轮胎滚动半径或版带驱动轮节圆半径rm制动器使用个数5
制动器旋向及所在部位
制动器型式
制动器驱动力型式
制动器摩擦材料
制动器摩擦副总间隙
制动器制动液牌号
制动器设计的最大操纵力N,或最大油(气)压力kPa制动器设计的最大制动力矩N·m表A.2第一、二次磨合
样品编号
试验车速
制动次数
检查结果
样品编号
试验车速
制动驱动力
MPa或N
制动驱动力
MPa或N
试验日期
制动初转速
制动力矩
出厂日期
操作者
制动时间
恢复试验
第一次热衰退试验、
冷态制动效能试验、
试验日期
制动初转速
制动时间
制动力矩
操作者
摩擦副表面最
高温度
最大最小平均
制动油最
高温度
制动减速度
制动减速度
样品编号
试验车速
制动次数
检查结果
制动驱动力
MPa或N
制动驱动力 kPa或N
图A.1第一、二、三次冷态制动效能试验pbZxz.net
试验次数
第一、二次热衰退试验和恢复试验图A.2
表A.4第二次热衰退试验
试验日期
制动初转速
制动力矩
摩擦副表面最高温度
操作者
制动油最高温度
JB/T7280—2008
累计试验时间
JB/T7280—2008
样品编号
试验车速
制动总次数
第1次
第50次
第100次
第101次
制动驱动力
MPa或N
样品编号
摩擦材料
测量点
磨损量
样品编号
试验开始日期
操纵机构型式
完成的试验次数
操纵机构工作状态
表A.5制动器耐久试验
试验开始日期
试验结束日期
试验台驱动轴转速
摩擦副表面最高温度
操作者
第一、二、三、…、五十个100次制动试验制动力矩
制动时间
最小平均
摩擦副表面
表A.6摩擦衬片(衬块)磨损量
生产企业
制动前摩擦副初温
操纵机构耐久试验
试验结束日期
操作者
制动减速度
中华人民共和国
机械行业标准
拖拉机制动系统
台架试验方法
JB/T7280—2008
机械工业出版社出版发行
北京市百万庄大街22号
邮政编码:100037
210mm×297mm?0.75印张·21千字2008年7月第1版第1次印刷
书号:15111:9080
网址:http:1/cmpbook.com编辑部电话:(010)88379778
(010)88379693
直销中心电话:
封面无防伪标均为盗版
版权专有侵权必究
小提示:此标准内容仅展示完整标准里的部分截取内容,若需要完整标准请到上方自行免费下载完整标准文档。

标准图片预览:
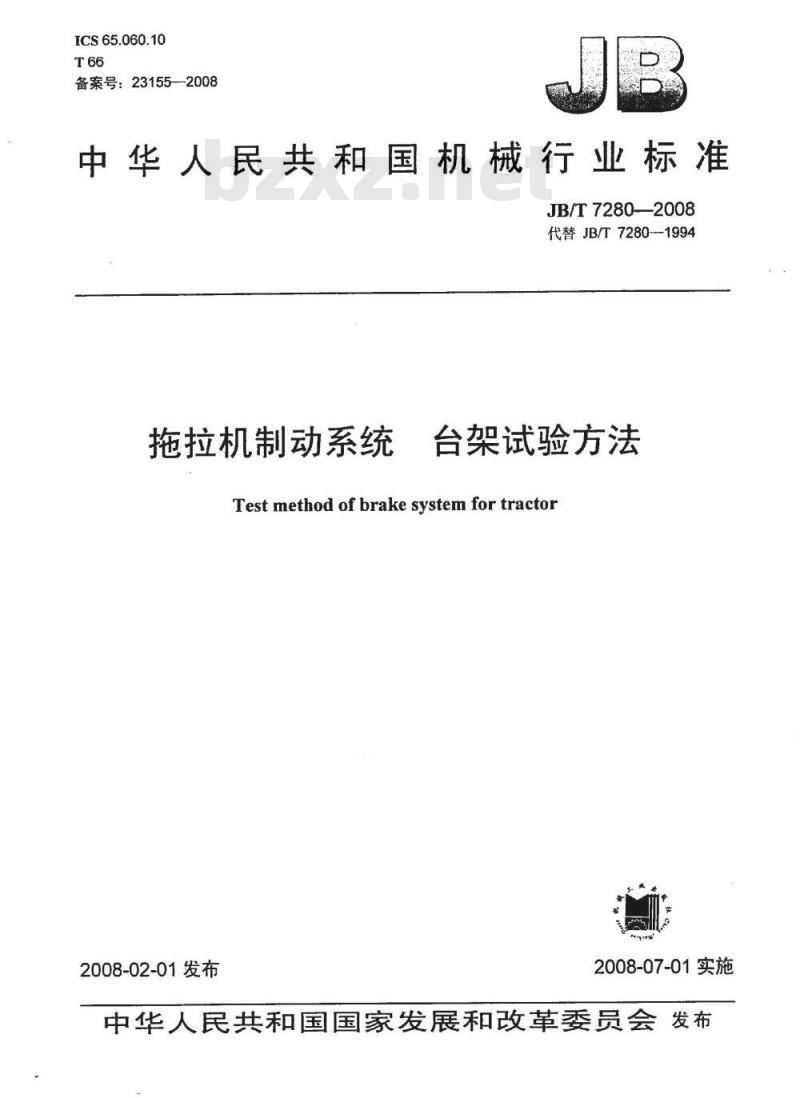
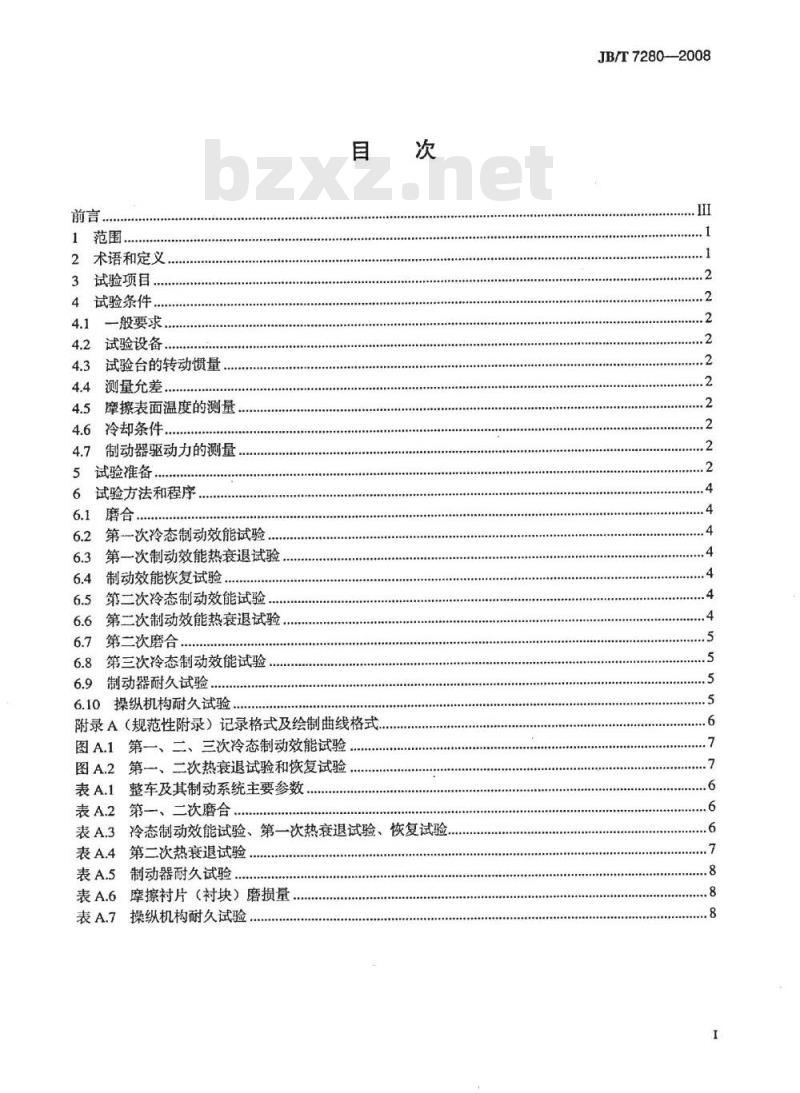
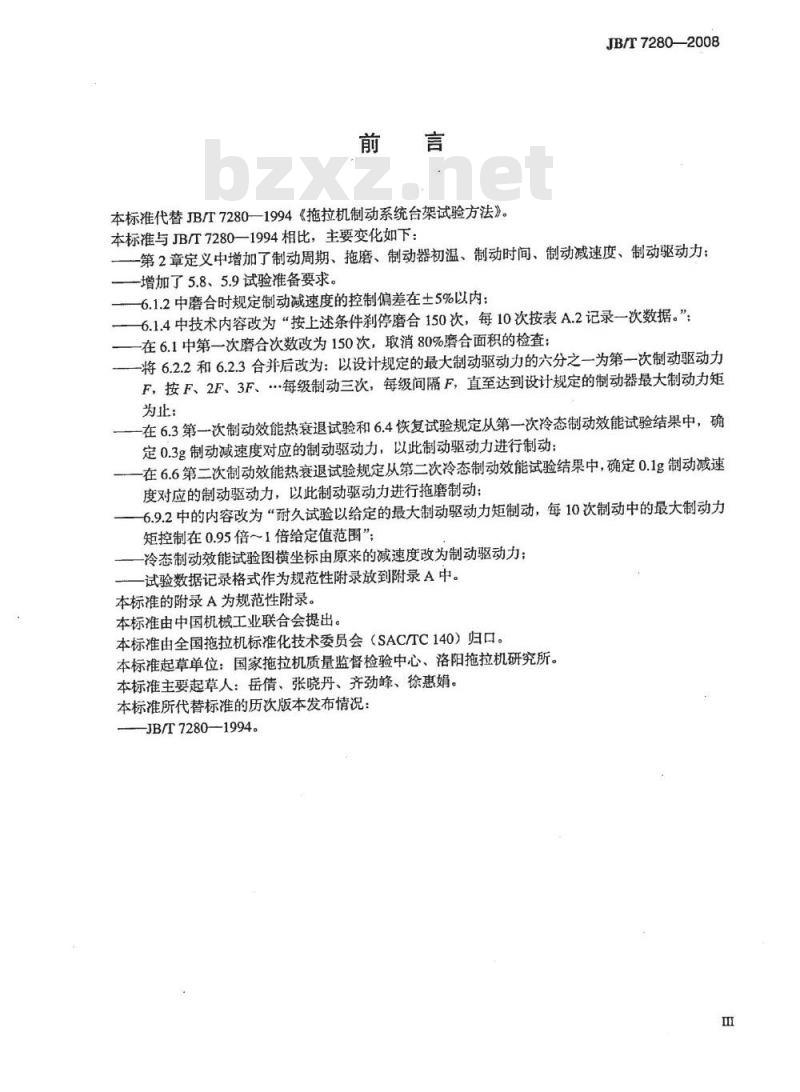
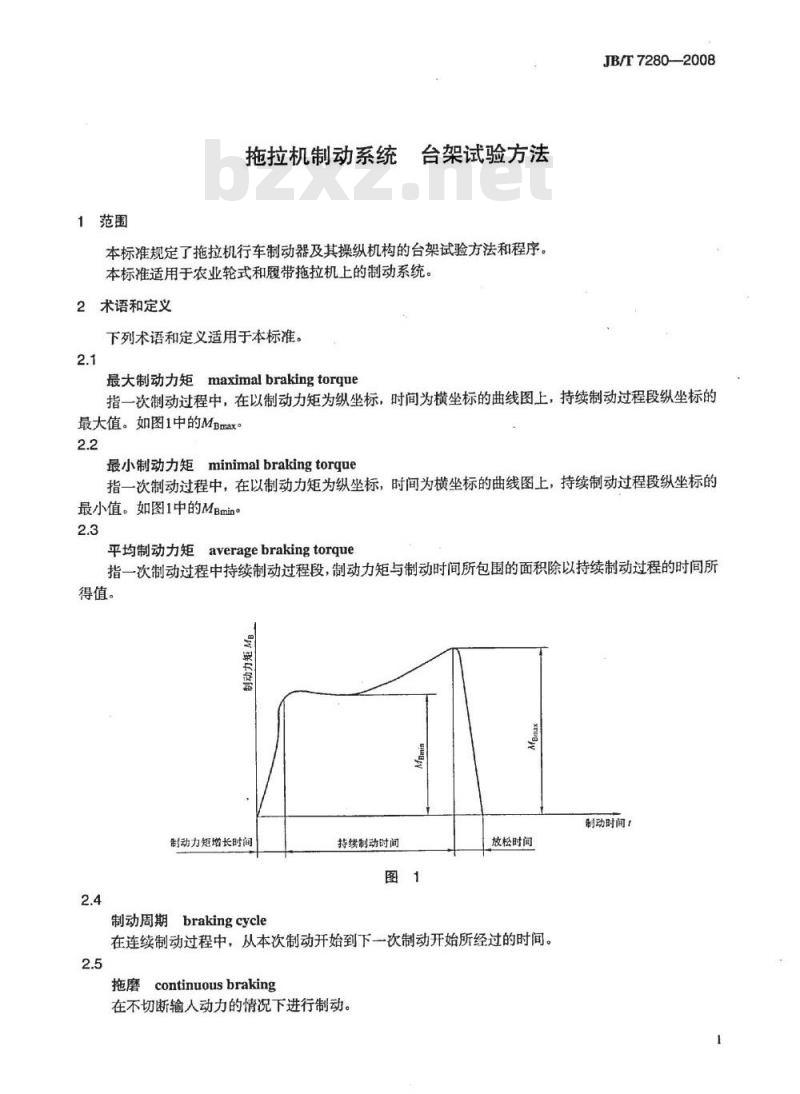
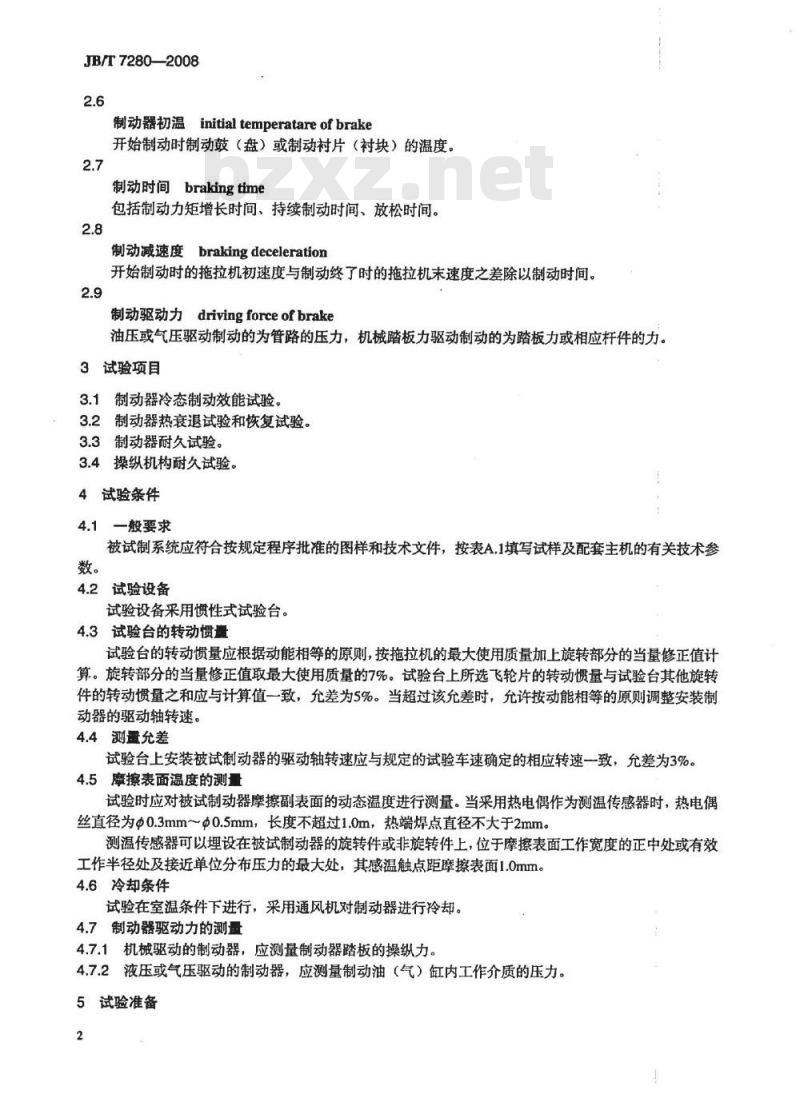
- 热门标准
- 机械行业标准(JB)
- JB/T5762.2-2006 转塔车床 第2部分:精度
- JB/T10719-2007 焊接聚晶金刚石或立方氮化硼槽刀
- JB/T10725-2007 天然金刚石车刀
- JB/T10596-2006 磁阻式步进电动机通用技术条件
- JB/T10723-2007 焊接聚晶金刚石或立方氮化硼镗刀
- JB/T7144.1-1993 青饲料切碎机 技术条件
- JB/T5372.6-1991 8mm槽系组合夹具其他件 鳞齿支承螺母
- JB/T5742.1-2010 单排多轴木工钻床 第1部分:参数
- JB/T9162.8-1999 表柱 尺寸
- JB/T5368.18-1991 8mm槽系组合夹具定位件 V形板
- JB/T5368.16-1991 8mm槽系组合夹具定位件 定位板
- JB/T7712-2007 高温合金热处理
- JB3930.58-1985 U形角铁
- JB/T5371.12-1991 8mm槽系组合夹具压紧件 V形压板
- JB/T8746.5-2008 塑料异型材挤出模零件 第5部分:定型块
- 行业新闻
请牢记:“bzxz.net”即是“标准下载”四个汉字汉语拼音首字母与国际顶级域名“.net”的组合。 ©2009 标准下载网 www.bzxz.net 本站邮件:bzxznet@163.com
网站备案号:湘ICP备2023016450号-1
网站备案号:湘ICP备2023016450号-1