- 您的位置:
- 标准下载网 >>
- 标准分类 >>
- 国家标准(GB) >>
- GB/T 21012-2007 精密加工中心技术条件
标准号:
GB/T 21012-2007
标准名称:
精密加工中心技术条件
标准类别:
国家标准(GB)
标准状态:
现行-
发布日期:
2007-07-17 -
实施日期:
2007-12-01 出版语种:
简体中文下载格式:
.rar.pdf下载大小:
940.79 KB
替代情况:
替代JB/T 8773-1998

点击下载
标准简介:
标准下载解压密码:www.bzxz.net
本标准规定了精密加工中心制造和验收的要求。本标准适用于线性轴线行程至2000mm 的精密加工中心。线性轴线行程超过2000mm 的精密加工中心也可参照使用。 GB/T 21012-2007 精密加工中心技术条件 GB/T21012-2007

部分标准内容:
ICS 25. 040. 10
中华人民共和国国家标准
GB/T21012—2007
技术条件
精密加工中心
Precision machining centers-Specifications2007-07-17发布
中华人民共和国国家质量监督检验检疫总局中国国家标准化管理委员会
2007-12-01实施
GB/T 21012—2007
规范性引用文件
3技术要求
3.1概述
附件和工具
安全卫生
加工和装配质量
检验与验收
4.1概述
一般要求
4.3外观检验
附件和工具
参数检验(抽查)
4.6机床空运转试验
4.7机床连续空运转试验
4.8机床负荷试验
4.9最小设定单位试验
4.10原点返回试验
机床精度检验
5包装和随机文件
与本部分配套便用的标雅有:
GB/T 210122007
GB/T20957.1—2007《精密加工中心检验条件第1部分:卧式和带附加主轴头机床几何精度检验(水乎Z轴)》;
GB/T20957.2:2007《精密加丁中心检验条件第2部分:立式或带垂直主回转轴的万能主轴头机床儿何精度检验(垂育2轴)》;GB/T20957.4一2007精密加1中心检验条件第4部分:线性和回转轴线的定位精度和重复定位精度检验》;
—GH/20957.5—2007《精加工中心检验条件第5部分:工件火持托板的定位精度和重复定位精度检验》;
--GB/T20957.7一2007精密加工中心检验条件:第7部分:精加工试件精度检验》,本部分白实施之起·同时废止JB/T87731998精密加1中心技术条件》。本标准由中国机械工业联合会提出。本标由全国金属切削机床标准化技术委员会(SAC/TC 22)H口本标准起草单位:昆明机床股份有限公司,北京机床研究所,北京铣床研究所。本标主要起草人:唐其寿,张晓毅,李祥文,胡瑞琳,1
1范围
精密加工中心技术条件
本标准规定了精密加工中心制造和验收的要求。本标准用丁线性轴线行程至2000mm的精密加工中心线性轴线行程超过2 00 mm的精密加工中心也可参照使用,2规范性引用文件
GB/T 21012—2007
下列文件中的条款通过本标推的引用近成为本标谁的条款,凡是注期的引用文件,其随后所有的修改单(不包括堪误的内容)或修订版均不适用于本标准,然而,鼓励根据本标准达成协议的各方研究是否可使用这些文件的最新版本。凡是不注明日期的引用文件,其最新版本适用于本标准。GB5226.1-2002机械安全机械电气设备:第1部分:通用技术条件(IEC60204-1:2000,IDT)
GB/T9061—20C6金属切削机床通用技术条件GB15760—2004:金属切削机床安防护通用技术条件GB/T16769-1S97金属切前机床噪声声压级测量方法GB/T1742L.2·-2000机床检验通则第2部分:数控轴线的定位精度和重复定位精度的确定(eqv IS0 230-2: 1997)
GH18568--20C1加工中心安全防护技术条件GB/T20957.1一2007精密加工中心验条件第1部分:卧式和带附加主轴头机床几何精度检验(水 Z轴)(ISO 10791-1:1998,M0D)GB/20957.2--2007精密加工中心检验条件第2部分:式或带垂直主间转轴的方能主轴头机床儿何精度检验(垂直Z轴)(IS0)10791-2:2001.MOD)GB/T20957.4--2007精密加工中心检验条件第4部分:线性和回转轴线的定位精度和重复定位精度检验(150 10791-4:1998,MO0)(H/120957.5一2007精密加工中心检验条件第5部分:7.件夹持托板的霆位精度和重复定位精度检验(IS() 10791-5:1998,MOD)GB/T20957.7-2C07精密加T中心检验条件第7部分:精加工试件精度检验(ISO107917:1998,MOD)
JB/T 5561 -1991
金属切削机床圆锥表面涂色法检验及评定JB/T98721999金属切削机床机械加工件通用技术条件JB/T9873-1999金属切前机床焊接件通用技术条件JB/T9874—1999金属切削机床装配通用技术条件JB/T9875-1999金属切削机床随机技术文件的编制JB/T 9877- 1999
金属切削机床清洁度的测定
JF/T10051—1999金属切削机床液[乐系统通用技术条件3技术要求
3.1概述
本标准是对GB/T9061、JB/T9872、JB/T9874等标推的具体化和补充:按本标推验收机床时,应GB/T 21012—2007
同时对上述标准中未经本标准具体化的有关验收项目进行检验。3. 2附件和工具
3. 2. 1应随机供应表 1 所列的附件和工具,表1
调整垫铁
专用调整工具
安装机床
调整机床
3.2.2扩大机床使用性能的特殊附件,根据用户要求按协议提供。3.3安全卫生
3.3.1机床的安全防护应符合GB15760,GB18568,GB5226.1等有关标准的规定,3.3.2机床的空运转噪声声压级应符合4.6.2的规定。3.4加工和装配质量
3.4.1床身、立柱、工作台、托板、主轴箱、滑座,滑鞍为重要铸件(焊接件),在粗加工后应进行时效处理(包括振动时效处理等)。必要时在半精加工后再进行一次时效处理。3.4.2各进给运动导轨副应采用耐磨铸铁、镶钢导轨,注塑或贴塑导轨以及感应率火等耐磨措施。3.4.3焊接零部件应符合JB/T9873的规定。重要的焊缝应进行探伤检验,不应有裂纹。3.4.4镀镶钢导轨应进行探伤检验,不应有裂纹。3.4.5下列结合面应按“重要固定结合面”的要求考核:滑动导轨压板的固定结合面;
立柱与床身的固定结合面;
前、后床身的固定结合面;
立柱与立柱滑座的周定结合面;d)
主轴箱与主轴箱滑座的固定绪合面;f)
镶钢导轨基面:
安装直线导轨的基面。
下列结合面应按“特别重要固定结合面”的要求考核:3. 4.6
滚珠丝杠托架的固定结合面;
螺母座的固定结合面:
端齿盘的固定结合面。
下列导轨副应按“滑(滚)动导轨”的要求考核:3. 4. 7
各直线运动导轨副:
向转工作台与上滑座环形导轨副。b)
3.4.8重要固定结合面、特别重要固定结合面应紧密贴合,并按下列规定进行检验a)重要固定结合面紧周后用 0.03 mm塞尺检验不应插入;b)特别重要固定结合面除按JB/T9874一1999的I级精度做涂色法检验外,紧固前、后用0.03mm塞尺检验不应插人(与水平面垂直或倾斜的结合面只在紧固后检验);c)用塞尺检验时,允计局部插人深度、插人长度应符合JB/T9874-1999中5.4.4的规定。3.4.9滑动导轨表面除按JB/T 9874—1999的V级精度做涂色法检验外,还应用 0.04 mm塞尺对其相配的导轨、镶条、压板端部的滑动面进行检验,其插人深度不应大于表2的规定。2
机床重蛋/t
塞尺痛人深度/rmm
GB/T 21012—2007
3. 4, 10 拼接的键钢导轨、床身导轨其接合处留有 0. 02 1r1 ~-0. 04 m 缝隙,相邻接合处导轨导向面错位量不应大于表3的规定。
机术重量/
导就导向面错立量/mm
3.4.11直线导轨安装基面应符合设计文件的规定.纽装后运动应轻便、灵活、无阻滞现象3.4.12各运动坐标的滚珠丝杠副、数控回转工作台,组装后按设计文件的规定进行运转:其反向间隙不宜大于表4的推荐值。
直线坐标反向间隙/mm
向转坐标反向问隙/(\)
3.4.13拉刀机构及其他主要机构所用蝶形弹簧,组装后应按图样或技术文件规定进行压力试验。3. 4. 14重要的压力油缸组装后应按系统压力的 1. 5倍迹行不少十0.5 h 的保压试验。3.4.15高速旋转的主轴组件,装配后应进行动平衡试验,平衡品质等级:允许剩余不平衡的不确定值应符合设计文件的规定:带轮的平衡应符合设计文件的规定。3.4.16正轴箱、滚珠丝杠支承座和螺母座等重要的定位销,其接触长度不应少于维销T.作长度的70%,并应均布在接继的两侧,
3.4.17机床主轴装配后,其锥孔应按J13/T5561用量规做涂色法检查,锥孔的接触应靠近天端,实际接触长度与工作长度的比值不应低于80收。3.4.1B按JB/T9877抽查机床总装后的清洁度,其主轴箱和液压箱内部清洁度按重量法进行检验。其单位体积中脏物的重量;主轴箱不应超过 400 m1g/I;液压箱不应超过150 mg/L。其他部位用日测,手感法进行检查,不应有明显脏物。4检验与验收
4.1概述
每台机床应在制造厂经检验合格后出厂。特殊情况下,经用广同意可在使用处进行检验,4.1.1
机床的检验与验收一般宜包括下列内容:a)
外观检验;
附件和工具检验;
参数检验;
d)机床的空运转试验;
机床的负荷试验;
机床的精度检验;
g)其他。
4.2一般要求
检验时,应防止气流,光线热辐射的干扰对坏境温度变化的影响,并应在相应精度标准规定的3
GB/T21012—2007
温度条件下进行检验和验收。
4.2.2检验与验收时,应按照制造广所规定的安装要求调平机床,4.2.3检验过程中,不应调整影响机床精度和性能的机构和零件。用地脚螺栓紧固的机床,在检验过程中不应重新调整安装水平,确需重新调整时,应复检调整后受影响的有关项耳,不宜紧固地脚螺栓的机床,负荷试验后可重新调整安装水平。4.2.4检验过程中,因特殊原闷需拆卸某些零部件才能进行检验时,可按制造厂的规定进行,但这被拆卸的零部件不应对机床的精度造成影响。4.3外观检验
4.3.1按GB/T9061一2006中3.2评定机床的布局和造型(仪在型式试验时进行)。4.3.2按GB/T9061—2006中3.15及设计文件检验机床的外观质量。4.4附件和工具
按3.2检验随机供应的附件和工其应符合技术文件的规定。4.5参数检验(抽查)
按设计文件规定的主要技术参数检验。4.6机床空运转试验
4.6.1温升试验和主运动、进给运动检验4.6.1.1机床的主运动机构应从最低转速起,依次运转。无级变速的机床应不少于10级转速,有级变速的机床应从最低到最高逐级进行空运转试验,各级转速的运转时间不应少于2mil,最高转速运转时间不少于1h,使主轴轴承达到稳定温度,并在靠近轴承处检验其温度和温升,其温度不应超过55℃,温升不应超过35℃。
4.6.1.2液压系统在额定工作压力下使系统连续运行,至油液达到热平衡后,检验油液的温度和温升,其温度和温升应不超过JB/T10051—1999中4,3的规定。4.6.1.3在空运转条件下,有级传动的各级主轴转速的实际偏差,应不超过公称值的一2%~-6%,无级传动的各级主轴转速的实际偏差,应不超过公称值的土10%。4.6.1.4对机床直线和间转坐标上的运动部件,分别以低、中、高进给速度和快速移动进行空运转试验,同时抽检各级进给速度的实际偏差,应不超过公称值的一2%~十6%。当运动部件高速进给和快速移动时,只在除行程两端之外的2/3全行程上进行检验,试验时运动部件移动应平稳、灵活,无明显爬行和振动,限位应可靠。4.6.2噪声检验
机床运转时不应有不正常的尖叫声和冲击声。在空运转条件下,机床的噪声声压级应不超过GB18568的规定。
机床噪声的测量方法按GB/T16769。4.6.3空运转功率试验(插查)
主传动系统的空运转功率按设计文件的规定检验。4.6.4机床的功能试验
4.6.4.1用按键、开关人工操作机床各部位进行试验(即:手动功能试验):a)对主轴连续进行不少于5次的锁刀、松刀和吹气的动作试验,动作应灵活、可靠、准确,b)对主轴在中速时连续进行10次正、反转的启动、停止(包括制动)和定向的操作试验,动作应灵活、可靠。
c)对无级变速的主轴至少应包括低、中、高在内的转速,对有级变速的主轴在各级转速进行变速操作试验,动作应灵活,可靠。
GB/T21012-—2007
d)对各坐标(包括直线坐标和向转坐标)上的运动部件,在中等进给速度连续进行各10饮的正负向启动,停止的操作试验·并选择适应的增量进给进行正,负向操作试验,动作应灵活、靠、谁确,
对进给系统进行包括低,中,高进给速度和快速在内的10种变速操作试验,动作应灵活.可靠。e
对分度回转工作台或数控回转工作台连续进行10次的分度,定位试验,动作应灵活,可靠、f)
雅确。
对托板连续进行5次的交换试验,动作应灵活,可靠。g
h)对刀库、机械手以任选方式进行换刀试验:刀库L.刀具配置应包括设计规定的最大重量,最大长度和最大直径的刀具。换刀动作应灵活、可靠、准确,机械手的承载重量和换刀时间应符合设计规定。
i)对机床数字控制的各种指示灯,控制按钮,DNC通讯传输和风扇等进行空运转试验,动作应灵活、可靠。
j)对液压、气动、润滑,冷却系统进行密封、润滑、冷却性能试验,功能应可靠,动作应灵活、准确,各系统虚无渗(泄)漏现象。
k)对机床的安全、保险、防护装置以及电气系统的控制,联锁,保护功能进行试验,功能应靠,动作应灵活、准确。
1)对机床的各附属装置进行试验,动作应灵活、可靠4.6.4.2用数控程序操作机床各部位进行试验(即:白动功能试验,可与4.7连续空运转试验合并进行):
a)对主轴在中速时,连续进行10次的正、反转启动、停止(包括制动)和定向的操作试验,动作应灵活、而靠:
b对无级变速的主轴至少应包括低,中,高在内的转速,对有级变速的主轴在各级转速进行变速操作试验,动作应灵活、可靠,c)对各坐标(包括直线坐标和回转坐标)上的运动部件,在中等进给速度连续进行正,负向的启动、停止和增量进给的操作试验,动作应灵活、可靠、准确d)对进给系统至少进行低、中、高进给速度和快速的变速操作试验,动作应灵活、可靠:e)对分度回转二作台或数控回转工作台连续进行10次的分度、定位操作试验,动作应灵活,运转应平稳,可靠、准确;
对托板进行5次交换试验,动作应灵活,可靠;f
g)对刀床总容量中包括最大重量刀具在内的每把刀具,以任选方式进行不少于2次的自动换刀动作试验,动作应灵活、可靠;对机床的坐标联动、坐标选择、机械定、定位、自线和圆弧插补,螺距、间隙、刀具补偿,程序h)
暂停、急停等指令,刀具的夹紧、松开等数控功能逐··进行试验,其功能应可靠,动作应灵活、准确;
i)有类紧机构的运动部件应分别在各自全部运动范围内的任意工作位置上(一般选3个~5个位置)进行夹紧试验,动作应可靠,稳定,4.7机床连续空运转试验
4.7.1用包括机床主要加工功能的数控程序,模拟工作状态做不切削的连续空运转,整机连续空运转时间为48h。每次循环时间不大于15 trnin,各次循环之间的休止时间不超过1 min.4.7.2连续空运转的整个过程巾,机床运转应正常,平稳、可靠,不应发生故障,否则必须重新进行运转。
GB/T 21012—2007
4.7.3连续空运转程序中应包括下列内容:a)主轴包括低、中、高转速的正、反向运动和定位,其中高速运转时间一般不少丁每个循环程序所用时问的10%,
b)各坐标上的运动部件应包括低、中,高进给速度和快速的正,负向运动,运行应在接近全行程范围内,并可选任意点进行定位。运行中不允许使用倍率开关。高速进给速度和快速进给时间一般不少于每个循环程序所用时间的10%。c)刀库中各刀位上的具不少于2次自动换刀。d)分度回转工作台或数控回转工作台的白动分度、定位。e)各联动坐标的联动,
f)各托板不少于5次的自动交换。4.8机床负荷试验
4.8.1工作台承载工件最大童量的运转试验(抽查,可用与设计规定的承载工件最大重量相当的重物作为工件置于工作台上,使其载荷均匀,分别以最抵、最高进给速度和快速运转。在最低进给速度运转时,一般应在接近行程的两端和中间往复进行,每处移动距离应不少于20mm.在最高进给速度和快速运转时,应在除行程两端之外的2/3全行程上进行,分别往复1次和5次。
运转时应平稳、可靠低速运转时应无明显的爬行现象。4.8.2主传动系统最大扭矩的试验在机床计算转速范围内,选用一适当的主轴转速,采用铣削或镗削方法按设计规定的切削范围进行试验
在进行主传动系统最大扭矩的切削试验时,机床工作应正常稳,运动应推确,各传动元、部件和变速机构应正常、可靠。
4.8.3主传动系统最大切削抗力的试验在机床计算转速范围内,选一适当的主轴转速,采用镗削或钻削的方法按设计规定的切削规范进行试验。
在最大切削抗力的试验时,机床工作应正带,各运动机构应灵活、可靠,过载保险装置应正常,可靠。4.8.4主传动系统达到最大功率试验(抽查)在主轴恒功率的调速范围内,选用一适当的主轴转速,采用铣削方法按设计规定的切削规范进行试验。
在主传动系统达到最大功率的切削试验时,机床工作应正常,无明显额抖现象。4.9最小设定单位试验
4.9.1直线坐标最小设定单位试验4. 9. 1. 1试验方法
先以快速使直线坐标上的运动部件向正(或负)向移动一定距离,停止后,向同方向给出数个最小设定单位的指令,再停止,以此位置作为基准位置,每次给出1个,共给出20个最小设定单位的指令,向同方向移动(要注意实际移动方向),测量各指令的停止位置。从上述的最终位置,连续向同方向给出数个最小设定单位的指令,停止后,向负(或正向给出数个最小设定单位的指令,药返回到上述的最终测量位置,这些正向和负向的数个最小设定单位指令的停止位置不作测量。然后从上述最终位置开始,每欲给出1个,共给出20个最小设定单位的指令,继续向负(或正)向移动,测量各指令停至位置,见图1,各直线坐标均需至少在行程的中间两端3个位置分别迹行试验。按4.9.1.2的规定计算误差,6
以3个位置上的最大误差值作为该项的误差其备距误差、间隙补偿装置的机床,应在使用这些装置的情况下进行试验。数·个量小设定单位
指令的停山:位置不作测量
测母范围
4.9. 1.2误差计算方法
GB/T21012——2007
30823890
实际移动距离
4. 9. 1. 2. 1 最小设定单位误差 S,按式(1)计算:图1
S, =II.,--m Imin
武中:
L;某个最小设定单位指令的实际位移,单位为毫米(mm):注:实际位移的方向与给出的方向相反,其位移应为负值-1个最小设定单位指令的理论位移,单位为毫米(mm)。4.9.1.2.2最小设定单位相对误差5%按式(2)计算:S
式中:
×100%
20个最小设定单位指令的实际位移的总和,单位为毫米(mm)。4.9.1.3允差
根据机床具体情况,由制造厂规定。4.9.1.4检验工具
激光1涉仪或读数显微镜和金属线纹尺。4.9.2回转坐标最小设定单位试验4.9.2.1试验方法
最小段定单位
-(1)
先以快速使回转坐标上的运动部件向正(或负)向转动定角度,停止后间同力向给出数个最小设定单位的指令,再停止,以此位置作为基准位置,每次给出1个,共给出20个最小设定单位的指令,向同方向转动(要注意实际转动的方向),测量各指令的停止位置。从上述的最终位置,连续向问方向给出数个最小设定单位的指令,停止后,向负(或正)向给出数个最小设定单位的指令,约返回到上述的最终测量位置,这些正向和负向的数个最小设定单位指令的停止位置不作测量。然后从上述最终位置开始,衔次给出1个,共给出20个最小设定单位的指令继续向负(或正)向转动,测量各指令停置位置,见图2。GB/T 21012—2007
各回转坐标均需在回转范围内的任意3个位置进行试验。按4.9.2.2的规定计算误差,以3个位置上的最大误差值作为该项的误差。具备螺距误差、补偿装置的机床,应在使用这些装置的情况下进行试验。要个最小设定单位
指令的停止位置不作测至
严津范围
4. 9.2.2误差计算方法
实际转动角控
最小设定单位
4.9.2.2.1最小设定单位误差,按式(3)计算:w, = I B, -- ma I
式中:免费标准bzxz.net
6.【个最小设定单位指令的实际角位移,单位为秒(\),注:实际角位移的方向与给出的方向相反,其角位移应为负值。n
-1个最小设定单位指令的理论角位移,单位为秒(\)。4. 9. 2. 2. 2 最小设定单位相对误差 按式(4)计算:20
20maImx
式中:
×100%
20个最小设定单位指令的实际角位移的总和,单位为秒(\)。4.9.2.3允差
根据机床其体情况,由制造厂规定。4.9.2.4检验工具
白准直仪和多面体。
4.10原点返回试验
4.10.1直线坐标原点返回试验
4.10.1.1试验方法
·(4)
各首线坐标上的运动部件,从行程上的任意点按相同的移动方向,以快速进行5次返回原点的试验。测量每次实际位置P与原点理论位置P。的偏差X(一1,2,,5),见图3。各直线坐标至少在行程的中间及靠近两端的任意3个位置进行试验,按4.10.1.2的规定计算误差,以3个位置上的最大误差值作为该项的误差。8
设有向原点自动返回功能的机床,才进行本项试验:具备螺距误差,间隙补偿装置的机床,应在使用这些装置的情说下进行试验。Pa
4.10.1.2误差计算方法
GB/T 21012—2007
各自线坐标中,原点返问试验时的4倍标准偏差的最大值,即为原点返回误差,按式(5)计算:Ra = 4S.
式中:
R。—原点返回误差,单位为毫米(mm);S。一原点返回时的标准偏差,单位为毫米(mIn)。注:S,根据 GR/T17421.2—200G 的有关公式进行计算。4.10.1.3允差
根据机床具体情况,由制造」规定,4.10.1.4检验工具
激光干涉仪或读数显微镜和金属线纹尺,4.10.2回转坐标原点返回试验
4.10.2.1试验方法
各同转坐标上的运动部件,从行程上的征意点按相同的转动方向,以快速进行5次返回原点P.的试验。测量每次实际位置 P与原点理论位置 P能的偏差0,(i=1,2,,5),见图4:F'g
各回转坐标均需至少在转范用内的征意 3个位置进行试验,按4.1C.2.2的规定计算误差,以 3个位置1的最大误差值作为该项的误差,设有向原点自动返回功能的机床,才进行本项试验。具备爆距误差,简隙补偿装置的机床,成在使用这些装置的情况下进行试验。9
小提示:此标准内容仅展示完整标准里的部分截取内容,若需要完整标准请到上方自行免费下载完整标准文档。
中华人民共和国国家标准
GB/T21012—2007
技术条件
精密加工中心
Precision machining centers-Specifications2007-07-17发布
中华人民共和国国家质量监督检验检疫总局中国国家标准化管理委员会
2007-12-01实施
GB/T 21012—2007
规范性引用文件
3技术要求
3.1概述
附件和工具
安全卫生
加工和装配质量
检验与验收
4.1概述
一般要求
4.3外观检验
附件和工具
参数检验(抽查)
4.6机床空运转试验
4.7机床连续空运转试验
4.8机床负荷试验
4.9最小设定单位试验
4.10原点返回试验
机床精度检验
5包装和随机文件
与本部分配套便用的标雅有:
GB/T 210122007
GB/T20957.1—2007《精密加工中心检验条件第1部分:卧式和带附加主轴头机床几何精度检验(水乎Z轴)》;
GB/T20957.2:2007《精密加丁中心检验条件第2部分:立式或带垂直主回转轴的万能主轴头机床儿何精度检验(垂育2轴)》;GB/T20957.4一2007精密加1中心检验条件第4部分:线性和回转轴线的定位精度和重复定位精度检验》;
—GH/20957.5—2007《精加工中心检验条件第5部分:工件火持托板的定位精度和重复定位精度检验》;
--GB/T20957.7一2007精密加工中心检验条件:第7部分:精加工试件精度检验》,本部分白实施之起·同时废止JB/T87731998精密加1中心技术条件》。本标准由中国机械工业联合会提出。本标由全国金属切削机床标准化技术委员会(SAC/TC 22)H口本标准起草单位:昆明机床股份有限公司,北京机床研究所,北京铣床研究所。本标主要起草人:唐其寿,张晓毅,李祥文,胡瑞琳,1
1范围
精密加工中心技术条件
本标准规定了精密加工中心制造和验收的要求。本标准用丁线性轴线行程至2000mm的精密加工中心线性轴线行程超过2 00 mm的精密加工中心也可参照使用,2规范性引用文件
GB/T 21012—2007
下列文件中的条款通过本标推的引用近成为本标谁的条款,凡是注期的引用文件,其随后所有的修改单(不包括堪误的内容)或修订版均不适用于本标准,然而,鼓励根据本标准达成协议的各方研究是否可使用这些文件的最新版本。凡是不注明日期的引用文件,其最新版本适用于本标准。GB5226.1-2002机械安全机械电气设备:第1部分:通用技术条件(IEC60204-1:2000,IDT)
GB/T9061—20C6金属切削机床通用技术条件GB15760—2004:金属切削机床安防护通用技术条件GB/T16769-1S97金属切前机床噪声声压级测量方法GB/T1742L.2·-2000机床检验通则第2部分:数控轴线的定位精度和重复定位精度的确定(eqv IS0 230-2: 1997)
GH18568--20C1加工中心安全防护技术条件GB/T20957.1一2007精密加工中心验条件第1部分:卧式和带附加主轴头机床几何精度检验(水 Z轴)(ISO 10791-1:1998,M0D)GB/20957.2--2007精密加工中心检验条件第2部分:式或带垂直主间转轴的方能主轴头机床儿何精度检验(垂直Z轴)(IS0)10791-2:2001.MOD)GB/T20957.4--2007精密加工中心检验条件第4部分:线性和回转轴线的定位精度和重复定位精度检验(150 10791-4:1998,MO0)(H/120957.5一2007精密加工中心检验条件第5部分:7.件夹持托板的霆位精度和重复定位精度检验(IS() 10791-5:1998,MOD)GB/T20957.7-2C07精密加T中心检验条件第7部分:精加工试件精度检验(ISO107917:1998,MOD)
JB/T 5561 -1991
金属切削机床圆锥表面涂色法检验及评定JB/T98721999金属切削机床机械加工件通用技术条件JB/T9873-1999金属切前机床焊接件通用技术条件JB/T9874—1999金属切削机床装配通用技术条件JB/T9875-1999金属切削机床随机技术文件的编制JB/T 9877- 1999
金属切削机床清洁度的测定
JF/T10051—1999金属切削机床液[乐系统通用技术条件3技术要求
3.1概述
本标准是对GB/T9061、JB/T9872、JB/T9874等标推的具体化和补充:按本标推验收机床时,应GB/T 21012—2007
同时对上述标准中未经本标准具体化的有关验收项目进行检验。3. 2附件和工具
3. 2. 1应随机供应表 1 所列的附件和工具,表1
调整垫铁
专用调整工具
安装机床
调整机床
3.2.2扩大机床使用性能的特殊附件,根据用户要求按协议提供。3.3安全卫生
3.3.1机床的安全防护应符合GB15760,GB18568,GB5226.1等有关标准的规定,3.3.2机床的空运转噪声声压级应符合4.6.2的规定。3.4加工和装配质量
3.4.1床身、立柱、工作台、托板、主轴箱、滑座,滑鞍为重要铸件(焊接件),在粗加工后应进行时效处理(包括振动时效处理等)。必要时在半精加工后再进行一次时效处理。3.4.2各进给运动导轨副应采用耐磨铸铁、镶钢导轨,注塑或贴塑导轨以及感应率火等耐磨措施。3.4.3焊接零部件应符合JB/T9873的规定。重要的焊缝应进行探伤检验,不应有裂纹。3.4.4镀镶钢导轨应进行探伤检验,不应有裂纹。3.4.5下列结合面应按“重要固定结合面”的要求考核:滑动导轨压板的固定结合面;
立柱与床身的固定结合面;
前、后床身的固定结合面;
立柱与立柱滑座的周定结合面;d)
主轴箱与主轴箱滑座的固定绪合面;f)
镶钢导轨基面:
安装直线导轨的基面。
下列结合面应按“特别重要固定结合面”的要求考核:3. 4.6
滚珠丝杠托架的固定结合面;
螺母座的固定结合面:
端齿盘的固定结合面。
下列导轨副应按“滑(滚)动导轨”的要求考核:3. 4. 7
各直线运动导轨副:
向转工作台与上滑座环形导轨副。b)
3.4.8重要固定结合面、特别重要固定结合面应紧密贴合,并按下列规定进行检验a)重要固定结合面紧周后用 0.03 mm塞尺检验不应插入;b)特别重要固定结合面除按JB/T9874一1999的I级精度做涂色法检验外,紧固前、后用0.03mm塞尺检验不应插人(与水平面垂直或倾斜的结合面只在紧固后检验);c)用塞尺检验时,允计局部插人深度、插人长度应符合JB/T9874-1999中5.4.4的规定。3.4.9滑动导轨表面除按JB/T 9874—1999的V级精度做涂色法检验外,还应用 0.04 mm塞尺对其相配的导轨、镶条、压板端部的滑动面进行检验,其插人深度不应大于表2的规定。2
机床重蛋/t
塞尺痛人深度/rmm
GB/T 21012—2007
3. 4, 10 拼接的键钢导轨、床身导轨其接合处留有 0. 02 1r1 ~-0. 04 m 缝隙,相邻接合处导轨导向面错位量不应大于表3的规定。
机术重量/
导就导向面错立量/mm
3.4.11直线导轨安装基面应符合设计文件的规定.纽装后运动应轻便、灵活、无阻滞现象3.4.12各运动坐标的滚珠丝杠副、数控回转工作台,组装后按设计文件的规定进行运转:其反向间隙不宜大于表4的推荐值。
直线坐标反向间隙/mm
向转坐标反向问隙/(\)
3.4.13拉刀机构及其他主要机构所用蝶形弹簧,组装后应按图样或技术文件规定进行压力试验。3. 4. 14重要的压力油缸组装后应按系统压力的 1. 5倍迹行不少十0.5 h 的保压试验。3.4.15高速旋转的主轴组件,装配后应进行动平衡试验,平衡品质等级:允许剩余不平衡的不确定值应符合设计文件的规定:带轮的平衡应符合设计文件的规定。3.4.16正轴箱、滚珠丝杠支承座和螺母座等重要的定位销,其接触长度不应少于维销T.作长度的70%,并应均布在接继的两侧,
3.4.17机床主轴装配后,其锥孔应按J13/T5561用量规做涂色法检查,锥孔的接触应靠近天端,实际接触长度与工作长度的比值不应低于80收。3.4.1B按JB/T9877抽查机床总装后的清洁度,其主轴箱和液压箱内部清洁度按重量法进行检验。其单位体积中脏物的重量;主轴箱不应超过 400 m1g/I;液压箱不应超过150 mg/L。其他部位用日测,手感法进行检查,不应有明显脏物。4检验与验收
4.1概述
每台机床应在制造厂经检验合格后出厂。特殊情况下,经用广同意可在使用处进行检验,4.1.1
机床的检验与验收一般宜包括下列内容:a)
外观检验;
附件和工具检验;
参数检验;
d)机床的空运转试验;
机床的负荷试验;
机床的精度检验;
g)其他。
4.2一般要求
检验时,应防止气流,光线热辐射的干扰对坏境温度变化的影响,并应在相应精度标准规定的3
GB/T21012—2007
温度条件下进行检验和验收。
4.2.2检验与验收时,应按照制造广所规定的安装要求调平机床,4.2.3检验过程中,不应调整影响机床精度和性能的机构和零件。用地脚螺栓紧固的机床,在检验过程中不应重新调整安装水平,确需重新调整时,应复检调整后受影响的有关项耳,不宜紧固地脚螺栓的机床,负荷试验后可重新调整安装水平。4.2.4检验过程中,因特殊原闷需拆卸某些零部件才能进行检验时,可按制造厂的规定进行,但这被拆卸的零部件不应对机床的精度造成影响。4.3外观检验
4.3.1按GB/T9061一2006中3.2评定机床的布局和造型(仪在型式试验时进行)。4.3.2按GB/T9061—2006中3.15及设计文件检验机床的外观质量。4.4附件和工具
按3.2检验随机供应的附件和工其应符合技术文件的规定。4.5参数检验(抽查)
按设计文件规定的主要技术参数检验。4.6机床空运转试验
4.6.1温升试验和主运动、进给运动检验4.6.1.1机床的主运动机构应从最低转速起,依次运转。无级变速的机床应不少于10级转速,有级变速的机床应从最低到最高逐级进行空运转试验,各级转速的运转时间不应少于2mil,最高转速运转时间不少于1h,使主轴轴承达到稳定温度,并在靠近轴承处检验其温度和温升,其温度不应超过55℃,温升不应超过35℃。
4.6.1.2液压系统在额定工作压力下使系统连续运行,至油液达到热平衡后,检验油液的温度和温升,其温度和温升应不超过JB/T10051—1999中4,3的规定。4.6.1.3在空运转条件下,有级传动的各级主轴转速的实际偏差,应不超过公称值的一2%~-6%,无级传动的各级主轴转速的实际偏差,应不超过公称值的土10%。4.6.1.4对机床直线和间转坐标上的运动部件,分别以低、中、高进给速度和快速移动进行空运转试验,同时抽检各级进给速度的实际偏差,应不超过公称值的一2%~十6%。当运动部件高速进给和快速移动时,只在除行程两端之外的2/3全行程上进行检验,试验时运动部件移动应平稳、灵活,无明显爬行和振动,限位应可靠。4.6.2噪声检验
机床运转时不应有不正常的尖叫声和冲击声。在空运转条件下,机床的噪声声压级应不超过GB18568的规定。
机床噪声的测量方法按GB/T16769。4.6.3空运转功率试验(插查)
主传动系统的空运转功率按设计文件的规定检验。4.6.4机床的功能试验
4.6.4.1用按键、开关人工操作机床各部位进行试验(即:手动功能试验):a)对主轴连续进行不少于5次的锁刀、松刀和吹气的动作试验,动作应灵活、可靠、准确,b)对主轴在中速时连续进行10次正、反转的启动、停止(包括制动)和定向的操作试验,动作应灵活、可靠。
c)对无级变速的主轴至少应包括低、中、高在内的转速,对有级变速的主轴在各级转速进行变速操作试验,动作应灵活,可靠。
GB/T21012-—2007
d)对各坐标(包括直线坐标和向转坐标)上的运动部件,在中等进给速度连续进行各10饮的正负向启动,停止的操作试验·并选择适应的增量进给进行正,负向操作试验,动作应灵活、靠、谁确,
对进给系统进行包括低,中,高进给速度和快速在内的10种变速操作试验,动作应灵活.可靠。e
对分度回转工作台或数控回转工作台连续进行10次的分度,定位试验,动作应灵活,可靠、f)
雅确。
对托板连续进行5次的交换试验,动作应灵活,可靠。g
h)对刀库、机械手以任选方式进行换刀试验:刀库L.刀具配置应包括设计规定的最大重量,最大长度和最大直径的刀具。换刀动作应灵活、可靠、准确,机械手的承载重量和换刀时间应符合设计规定。
i)对机床数字控制的各种指示灯,控制按钮,DNC通讯传输和风扇等进行空运转试验,动作应灵活、可靠。
j)对液压、气动、润滑,冷却系统进行密封、润滑、冷却性能试验,功能应可靠,动作应灵活、准确,各系统虚无渗(泄)漏现象。
k)对机床的安全、保险、防护装置以及电气系统的控制,联锁,保护功能进行试验,功能应靠,动作应灵活、准确。
1)对机床的各附属装置进行试验,动作应灵活、可靠4.6.4.2用数控程序操作机床各部位进行试验(即:白动功能试验,可与4.7连续空运转试验合并进行):
a)对主轴在中速时,连续进行10次的正、反转启动、停止(包括制动)和定向的操作试验,动作应灵活、而靠:
b对无级变速的主轴至少应包括低,中,高在内的转速,对有级变速的主轴在各级转速进行变速操作试验,动作应灵活、可靠,c)对各坐标(包括直线坐标和回转坐标)上的运动部件,在中等进给速度连续进行正,负向的启动、停止和增量进给的操作试验,动作应灵活、可靠、准确d)对进给系统至少进行低、中、高进给速度和快速的变速操作试验,动作应灵活、可靠:e)对分度回转二作台或数控回转工作台连续进行10次的分度、定位操作试验,动作应灵活,运转应平稳,可靠、准确;
对托板进行5次交换试验,动作应灵活,可靠;f
g)对刀床总容量中包括最大重量刀具在内的每把刀具,以任选方式进行不少于2次的自动换刀动作试验,动作应灵活、可靠;对机床的坐标联动、坐标选择、机械定、定位、自线和圆弧插补,螺距、间隙、刀具补偿,程序h)
暂停、急停等指令,刀具的夹紧、松开等数控功能逐··进行试验,其功能应可靠,动作应灵活、准确;
i)有类紧机构的运动部件应分别在各自全部运动范围内的任意工作位置上(一般选3个~5个位置)进行夹紧试验,动作应可靠,稳定,4.7机床连续空运转试验
4.7.1用包括机床主要加工功能的数控程序,模拟工作状态做不切削的连续空运转,整机连续空运转时间为48h。每次循环时间不大于15 trnin,各次循环之间的休止时间不超过1 min.4.7.2连续空运转的整个过程巾,机床运转应正常,平稳、可靠,不应发生故障,否则必须重新进行运转。
GB/T 21012—2007
4.7.3连续空运转程序中应包括下列内容:a)主轴包括低、中、高转速的正、反向运动和定位,其中高速运转时间一般不少丁每个循环程序所用时问的10%,
b)各坐标上的运动部件应包括低、中,高进给速度和快速的正,负向运动,运行应在接近全行程范围内,并可选任意点进行定位。运行中不允许使用倍率开关。高速进给速度和快速进给时间一般不少于每个循环程序所用时间的10%。c)刀库中各刀位上的具不少于2次自动换刀。d)分度回转工作台或数控回转工作台的白动分度、定位。e)各联动坐标的联动,
f)各托板不少于5次的自动交换。4.8机床负荷试验
4.8.1工作台承载工件最大童量的运转试验(抽查,可用与设计规定的承载工件最大重量相当的重物作为工件置于工作台上,使其载荷均匀,分别以最抵、最高进给速度和快速运转。在最低进给速度运转时,一般应在接近行程的两端和中间往复进行,每处移动距离应不少于20mm.在最高进给速度和快速运转时,应在除行程两端之外的2/3全行程上进行,分别往复1次和5次。
运转时应平稳、可靠低速运转时应无明显的爬行现象。4.8.2主传动系统最大扭矩的试验在机床计算转速范围内,选用一适当的主轴转速,采用铣削或镗削方法按设计规定的切削范围进行试验
在进行主传动系统最大扭矩的切削试验时,机床工作应正常稳,运动应推确,各传动元、部件和变速机构应正常、可靠。
4.8.3主传动系统最大切削抗力的试验在机床计算转速范围内,选一适当的主轴转速,采用镗削或钻削的方法按设计规定的切削规范进行试验。
在最大切削抗力的试验时,机床工作应正带,各运动机构应灵活、可靠,过载保险装置应正常,可靠。4.8.4主传动系统达到最大功率试验(抽查)在主轴恒功率的调速范围内,选用一适当的主轴转速,采用铣削方法按设计规定的切削规范进行试验。
在主传动系统达到最大功率的切削试验时,机床工作应正常,无明显额抖现象。4.9最小设定单位试验
4.9.1直线坐标最小设定单位试验4. 9. 1. 1试验方法
先以快速使直线坐标上的运动部件向正(或负)向移动一定距离,停止后,向同方向给出数个最小设定单位的指令,再停止,以此位置作为基准位置,每次给出1个,共给出20个最小设定单位的指令,向同方向移动(要注意实际移动方向),测量各指令的停止位置。从上述的最终位置,连续向同方向给出数个最小设定单位的指令,停止后,向负(或正向给出数个最小设定单位的指令,药返回到上述的最终测量位置,这些正向和负向的数个最小设定单位指令的停止位置不作测量。然后从上述最终位置开始,每欲给出1个,共给出20个最小设定单位的指令,继续向负(或正)向移动,测量各指令停至位置,见图1,各直线坐标均需至少在行程的中间两端3个位置分别迹行试验。按4.9.1.2的规定计算误差,6
以3个位置上的最大误差值作为该项的误差其备距误差、间隙补偿装置的机床,应在使用这些装置的情况下进行试验。数·个量小设定单位
指令的停山:位置不作测量
测母范围
4.9. 1.2误差计算方法
GB/T21012——2007
30823890
实际移动距离
4. 9. 1. 2. 1 最小设定单位误差 S,按式(1)计算:图1
S, =II.,--m Imin
武中:
L;某个最小设定单位指令的实际位移,单位为毫米(mm):注:实际位移的方向与给出的方向相反,其位移应为负值-1个最小设定单位指令的理论位移,单位为毫米(mm)。4.9.1.2.2最小设定单位相对误差5%按式(2)计算:S
式中:
×100%
20个最小设定单位指令的实际位移的总和,单位为毫米(mm)。4.9.1.3允差
根据机床具体情况,由制造厂规定。4.9.1.4检验工具
激光1涉仪或读数显微镜和金属线纹尺。4.9.2回转坐标最小设定单位试验4.9.2.1试验方法
最小段定单位
-(1)
先以快速使回转坐标上的运动部件向正(或负)向转动定角度,停止后间同力向给出数个最小设定单位的指令,再停止,以此位置作为基准位置,每次给出1个,共给出20个最小设定单位的指令,向同方向转动(要注意实际转动的方向),测量各指令的停止位置。从上述的最终位置,连续向问方向给出数个最小设定单位的指令,停止后,向负(或正)向给出数个最小设定单位的指令,约返回到上述的最终测量位置,这些正向和负向的数个最小设定单位指令的停止位置不作测量。然后从上述最终位置开始,衔次给出1个,共给出20个最小设定单位的指令继续向负(或正)向转动,测量各指令停置位置,见图2。GB/T 21012—2007
各回转坐标均需在回转范围内的任意3个位置进行试验。按4.9.2.2的规定计算误差,以3个位置上的最大误差值作为该项的误差。具备螺距误差、补偿装置的机床,应在使用这些装置的情况下进行试验。要个最小设定单位
指令的停止位置不作测至
严津范围
4. 9.2.2误差计算方法
实际转动角控
最小设定单位
4.9.2.2.1最小设定单位误差,按式(3)计算:w, = I B, -- ma I
式中:免费标准bzxz.net
6.【个最小设定单位指令的实际角位移,单位为秒(\),注:实际角位移的方向与给出的方向相反,其角位移应为负值。n
-1个最小设定单位指令的理论角位移,单位为秒(\)。4. 9. 2. 2. 2 最小设定单位相对误差 按式(4)计算:20
20maImx
式中:
×100%
20个最小设定单位指令的实际角位移的总和,单位为秒(\)。4.9.2.3允差
根据机床其体情况,由制造厂规定。4.9.2.4检验工具
白准直仪和多面体。
4.10原点返回试验
4.10.1直线坐标原点返回试验
4.10.1.1试验方法
·(4)
各首线坐标上的运动部件,从行程上的任意点按相同的移动方向,以快速进行5次返回原点的试验。测量每次实际位置P与原点理论位置P。的偏差X(一1,2,,5),见图3。各直线坐标至少在行程的中间及靠近两端的任意3个位置进行试验,按4.10.1.2的规定计算误差,以3个位置上的最大误差值作为该项的误差。8
设有向原点自动返回功能的机床,才进行本项试验:具备螺距误差,间隙补偿装置的机床,应在使用这些装置的情说下进行试验。Pa
4.10.1.2误差计算方法
GB/T 21012—2007
各自线坐标中,原点返问试验时的4倍标准偏差的最大值,即为原点返回误差,按式(5)计算:Ra = 4S.
式中:
R。—原点返回误差,单位为毫米(mm);S。一原点返回时的标准偏差,单位为毫米(mIn)。注:S,根据 GR/T17421.2—200G 的有关公式进行计算。4.10.1.3允差
根据机床具体情况,由制造」规定,4.10.1.4检验工具
激光干涉仪或读数显微镜和金属线纹尺,4.10.2回转坐标原点返回试验
4.10.2.1试验方法
各同转坐标上的运动部件,从行程上的征意点按相同的转动方向,以快速进行5次返回原点P.的试验。测量每次实际位置 P与原点理论位置 P能的偏差0,(i=1,2,,5),见图4:F'g
各回转坐标均需至少在转范用内的征意 3个位置进行试验,按4.1C.2.2的规定计算误差,以 3个位置1的最大误差值作为该项的误差,设有向原点自动返回功能的机床,才进行本项试验。具备爆距误差,简隙补偿装置的机床,成在使用这些装置的情况下进行试验。9
小提示:此标准内容仅展示完整标准里的部分截取内容,若需要完整标准请到上方自行免费下载完整标准文档。

标准图片预览:

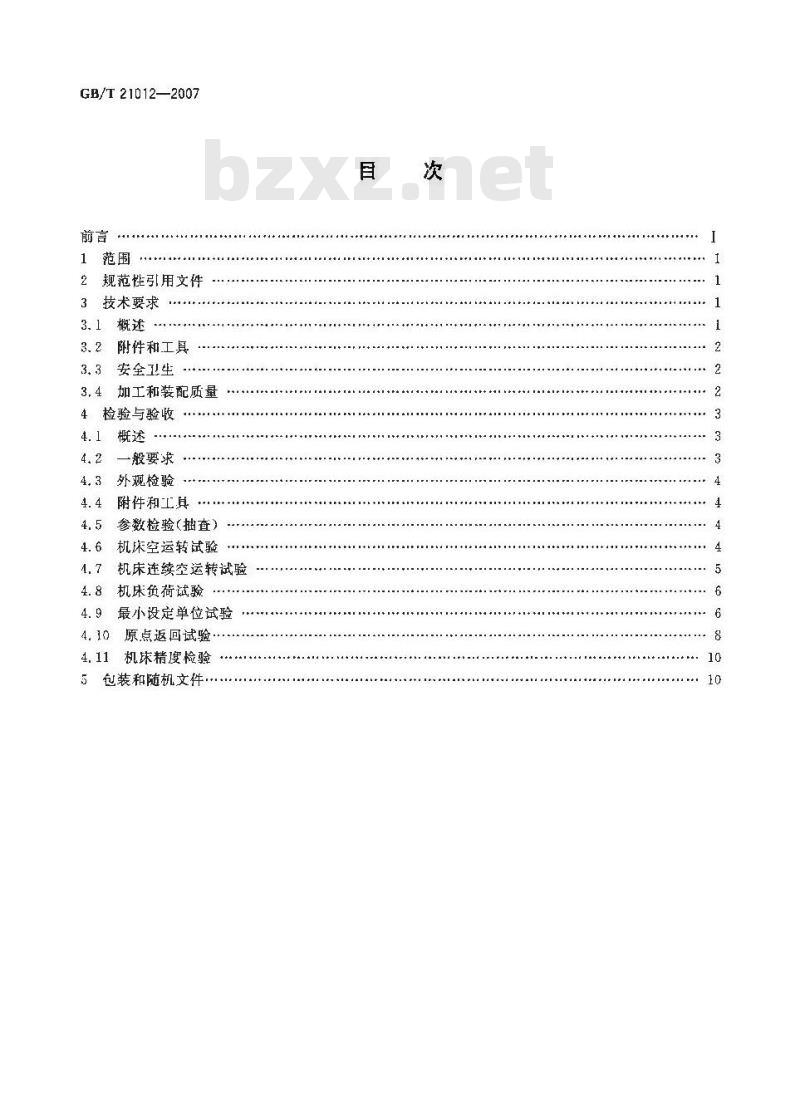
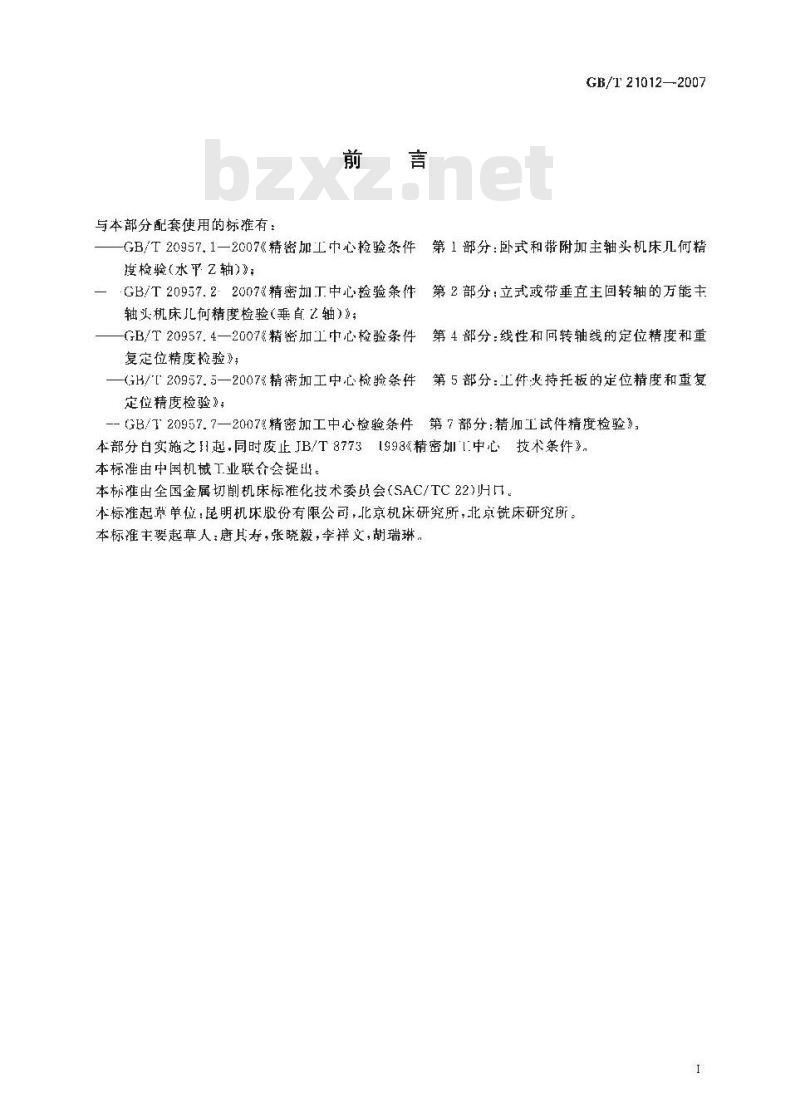
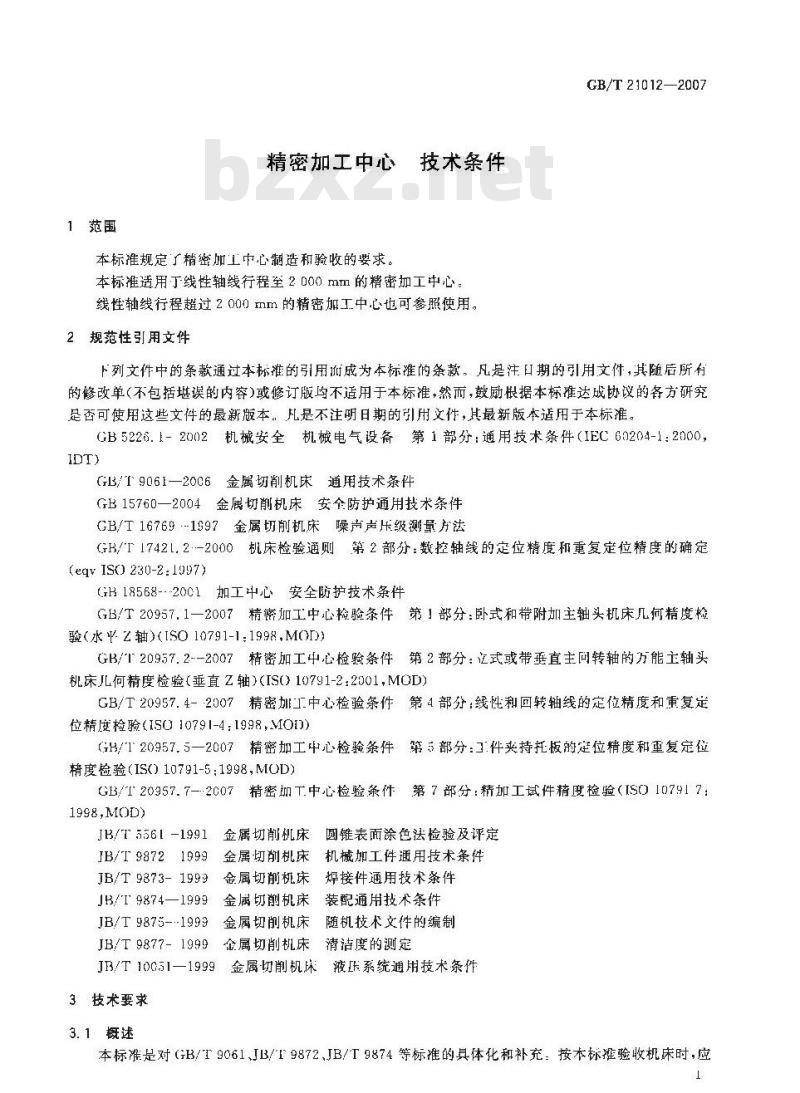
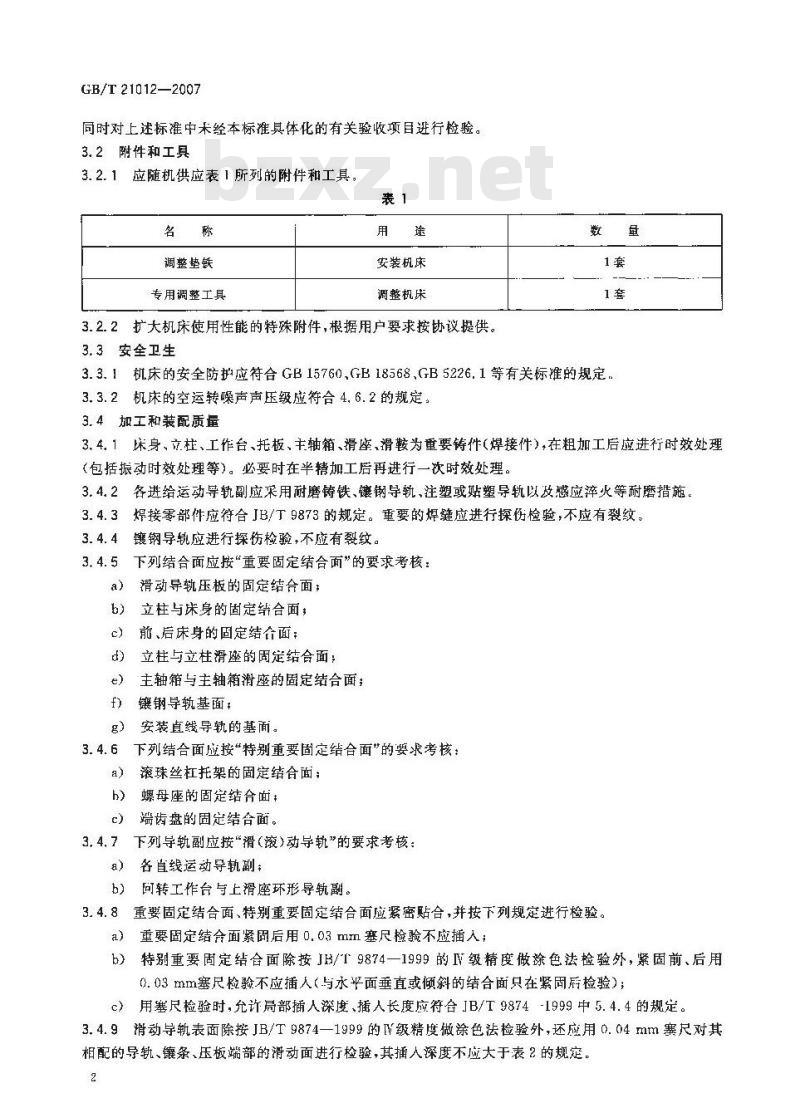
- 热门标准
- 国家标准(GB)
- GB/T28784.5-2022 机械振动 船舶振动测量 第5部分:客船和商船适居性振动测量、评价和报告准则
- GB/T2828.1-2012 计数抽样检验程序 第1部分:按接收质量限(AQL)检索的逐批检验抽样计划
- GB/T15329.1-2003 橡胶软管及软管组合件 织物增强液压型 第1部分: 油基流体用
- GB/T42403-2023 激光器和激光相关设备 激光光谱特性测量方法
- GB/T4100-2015 陶瓷砖
- GB30441.1-2013 信息技术通用多八位编码字符集满文名义字符与变形显现字符16点阵字型第1部分:铅印白体
- GB11554-2008 机动车和挂车用后雾灯配光性能
- GB/T26949.10-2011 工业车辆 稳定性验证 第10部分:在由动力装置侧移载荷条件下堆垛作业的附加稳定性试验
- GB/T32070-2022 土方机械 物体监测系统及其可视辅助装置 性能要求和试验
- GB/T22395-2022 锅炉钢结构设计规范
- GB4623-1994 环形预应力混凝土电杆
- GB/T14993-1994 转动部件用高温合金热轧棒材
- GB/T5286-2001 螺栓、螺钉和螺母用平垫圈 总方案
- GB/T24681-2009 植物保护机械 喷雾飘移的田间测量方法
- GB/T38142-2019 ISO 4918:2016 弹性、纺织和层压铺地物脚轮椅测试
- 行业新闻
请牢记:“bzxz.net”即是“标准下载”四个汉字汉语拼音首字母与国际顶级域名“.net”的组合。 ©2009 标准下载网 www.bzxz.net 本站邮件:bzxznet@163.com
网站备案号:湘ICP备2023016450号-1
网站备案号:湘ICP备2023016450号-1