- 您的位置:
- 标准下载网 >>
- 标准分类 >>
- 煤炭行业标准(MT) >>
- MT/T 689.2-1997 刨煤机 型式检验规范
标准号:
MT/T 689.2-1997
标准名称:
刨煤机 型式检验规范
标准类别:
煤炭行业标准(MT)
标准状态:
现行-
发布日期:
1997-12-30 -
实施日期:
1998-06-01 出版语种:
简体中文下载格式:
.rar.pdf下载大小:
335.31 KB

点击下载
标准简介:
标准下载解压密码:www.bzxz.net
本标准规定了煤矿地下开采长壁采煤工作面用静力式刨煤机的型式试验方法和检验规则。本标准适用于长壁采煤工作面使用的静力式刨煤机(以下简称“刨煤机”)的地面整机、刨煤部减速器型式检验。 MT/T 689.2-1997 刨煤机 型式检验规范 MT/T689.2-1997

部分标准内容:
MT/T689.2—1997
参照MT/T410一95《刨煤机型式和基本参数》,考虑到我国目前生产和使用的均为静力式刨煤机,因此,本标准只规定了静力式刨煤机的型式试验方法和检验规则。本标准的附录A、附录B和附录C都是提示的附录本标准由煤炭工业部科技教育司提出。本标准由煤炭工业部煤矿专用设备标准化技术委员会归口。本标准起草单位:煤炭科学研究总院上海分院。本标准主要起草人:周志春、周国庆、华元钦。本标准委托煤炭科学研究总院上海分院负责解释。85
1范围
中华人民共和国煤炭行业标准
刨煤机型式检验规范
Plough--Specification of type inspectionMT/T 689.2—1997
本标准规定了煤矿地下开采长壁采煤工作面用静力式刨煤机的型式试验方法和检验规则。本标准适用于长壁采煤工作面使用的静力式刨煤机(以下简称“刨煤机”)的地面整机、刨煤部减速器型式检验。
2引用标准
下列标准所包含的条文,通过在本标准中引用而构成为本标准的条文。本标准出版时,所示版本均为有效。所有标准都会被修订,使用本标准的各方应探讨使用下列标准最新版本的可能性。GB/T6404--86齿轮装置噪声声功率级测定方法MT/T101—93刮板输送机用减速器检验规范煤矿安全规程(1992年版)
3型式检验对象
符合下述情况之一的刨煤机及其减速器,应进行型式检验。a)总体结构新颖的试制新产品;b)正式生产后,当产品的总体结构有重大改变,足以影响产品性能时;c)国家质量监督机构提出进行型式检验的要求时。4应符合的规定
4.1产品附有的电气设备,须经防爆送审检验合格。4.2产品应满足《煤矿安全规程》的有关规定。4.3送型式检验的产品必须经出厂检验合格,并应附有完整的出厂检验报告。5
刨煤机地面整机试验
刨煤机地面整机试验,参考了附录A提示的附录)中提及的标准。5.1刨煤机整机(以下简称“整机”)空运转试验刨煤机装上除刨链外所有的零部件。在水泥地面水平直线铺设,铺设长度不应少于60m。按设计要求的油质和数量加油,接通电源。如装有冷却系统,应按设计要求的水压和流量接上冷却水。5.1.1整机空运转试验
5.1.1.1试验方法
刨煤机刨煤部的传动装置正、反向空运转各0.5h,测录刨煤部电动机的输入功率。5.1.1.2试验要求
运转时应无异常声响和强烈振动。不应出现异常温升。中华人民共和国煤炭工业部1997-12-30批准86
1998-06-01实施
MT/T 689. 2—1997
5.1.2刨煤部的传动装置密封性能试验5.1.2.1试验方法
与5.1.1试验同时进行。
5.1.2.2试验要求
刨煤机传动装置各密封处应密封性能良好,没有渗漏现象。5.1.3操作系统试验
5.1.3.1机械操作机构试验
对紧链器、调高油缸、推进油缸、喷雾阀等操纵机构(手把、按钮等)进行动作试验。各操作20次。要求动作灵活、准确可靠。
5.1.3.2电控系统手把、按钮试验对电器控制箱的手把、按钮和紧急停车断电开关,以及刨煤机的各个紧急停车开关等进行动作试验。每个手把和按钮各操作20次。应能准确可靠地正、反向启动、停止刨煤部电动机,准确可靠地启动、停止输送部电动机,正确地控制音响或灯光讯号。
5.2整机空载试验
在整机空运转试验合格后,接上刨链,并予以张紧,使刨链预张力达到设计要求。5.2.1刨煤机各部分相关尺寸检测5.2.1.1检查刨链和链道的配合尺寸,链道与链道间的错位量。5.2.1.2检查刨头与滑架或中部槽的配合尺寸及滑架与滑架(或导护链装置与导护链装置)、中部槽与中部槽间的错位量,以及机头架各部分的相对位置。5.2.1.3检查刨头往返运行至终端极限位置时,刨头左、右端底刨刀刀尖至输送部链轮中心线的距离。5.2.1.4检查其他各部分的相关尺寸。5.2.2刨削深度及底刀位置检测
5.2.2.1拖钩刨煤机:测量左、右底刨刀刀尖至不同厚度限位块前沿平面的距离;滑行刨煤机:测量不同刨削深度的左、右底刨刀刀尖至铲板前沿的距离。5.2.2.2测量不同刨削深度的左、右底刨刀在不同刀位时,刀尖至刨煤机底平面的垂直距离。5.2.3让刀机构让刀量捡测
测量左、右刨刀的让刀距离。
5.2.4刨头最高高度和最低高度检测将刨头分别调整至最高高度和最低高度,并分别测量其相应的高度值。5.2.5上述5.2.1至5.2.4各项检测的测量值均应符合设计要求。而且:a)5.2.1项中,零部件应能互换安装。b)5.2.3项中,让刀机构应灵活可靠。5.2.6空载运转时,刨煤部电动机功率及刨头牵引力测试5.2.6.1试验方法
刨煤机空载运转,按下列三种情况,测录刨煤部电动机功率及刨头牵引力。a)刨头沿直线、水平铺设的输送部往返运行各3次。同时测录刨头运行速度。b)刨煤机按水平弯曲铺设,按照输送部设计允许的最大水平弯曲量铺设至少一个弯曲区段,刨头往返运行各3次。
c)刨煤机按垂直弯曲铺设,按照输送部设计允许的最大垂直弯曲量铺设至少一个弯曲区段,刨头往返运行各3次。
5.2.6.2试验要求
各项试验时,刨头应运行平稳,无卡滞现象。87
MT/T 689. 2—1997
试验时,测录的刨煤部电动机功率,拖钩刨煤机不应超过额定功率的40%,滑行刨煤机不应超过额定功率的30%。测录的刨头运行速度和刨头牵引力,应符合设计要求。5.2.7刨头惯性试验
5.2.7.1试验方法
刨煤机按直线、水平铺设,启动刨头,8s后停机。双速刨煤机试验时,低速起动,转为高速并达到额定速度后停机。
5.2.7.2试验要求
测量刨头惯性行程,往返各测量3次。5.2.8缓冲器试验
5.2.8.1试验方法
去掉限位开关,将刨头置于距缓冲器10m处,启动刨煤部电动机,刨头在不停机情况下撞击缓冲器。双速刨煤机,以高速运行进行试验。左、右缓冲器各试验3次。5.2.8.2试验要求
缓冲器若装有电动机停机开关,电动机停机开关应动作及时、安全可靠。缓冲器试验时,若缓冲器及其固定机构出现漏油、漏气或变形、损坏现象,允许修复或更换后继续试验。刨煤机的其他部分,不允许出现变形或损坏现象。5.2.9电控系统试验
5.2.9.1电压波动情况下操作试验按刨煤机要求的电控系统接线,在75%和110%额定电压情况下,分别空载启动和停止刨煤部及输送部电动机,各动作试验20次。应能准确可靠地启动和停止刨煤部和输送部电动机。5.2.9.2紧急停车开关试验
操作工作面上的紧急停车开关,每个各操作20次。应能准确可靠地停止刨煤部电动机(或刨煤部和输送部电动机)。5.2.10电控安全保护系统试验
5.2.10.1刨头行程限位装置试验对机头、机尾限位开关各进行动作试验50次。应能准确可靠地停止刨头。
5.2.10.2行程指示器试验
用行程指示器发出的信号,控制刨煤部电动机停机,上、下行各试验50次。同时观察行程指示器的显示情况。
行程显示应准确可靠,应能在上、下行预定位置,准确可靠地停止刨头。5.2.10.3具有双速功能的刨煤机速度切换试验刨煤部电动机设置为自动运行方式(启动→低速-→高速→低速→停止→换向启动),上、下行各运行50次。与5.2.10.1同时试验。
刨煤部电动机应能准确可靠地完成启动至低速、低速与高速的相互转换、低速至停止及换向启动等自动切换功能。
5.3模拟煤壁刨削试验
刨削试验用模拟煤壁的可截割性(可刨性)、形状尺寸等参数,应符合刨煤机的设计性能参数。刨煤机安装在模拟煤壁一侧,按直线、水平铺设,启动刨煤机进行刨削模拟煤壁试验,5.3.1不同刨削深度时的刨削试验,并测定相应的电动机功率、刨头牵引力和实际刨削深度,计算比能耗。比较给定的刨削深度与实际的刨削深度之间的差别。5.3.1.1选定一种刨头设计高度不变。每种刨削深度时的底刨刀均调整在水平零位,刨头往返各刨削88
3次。
MT/T 689. 2 - 1997
5.3.1.2测录刨煤部左、右两个电动机的输入功率,刨头牵引力,刨削深度,推进油缸的压力。5.3.1.3绘制刨削深度和刨煤部电动机功率及刨头牵引力的相关曲线。5.3.1.4计算比能耗。
5.3.1.5推进部分各液压件应无渗漏液现象。5.3.2刨头不同设计高度时的刨削试验,并测定刨头相应高度时的电动机功率,刨头牵引力和刨削深度。
按刨头最低、中间、最高三种刨头高度进行刨削,对每种刨头高度按选定的一种符合设计要求5.3.2.1
的刨削深度,往返各刨削3次。
5.3.2.2测录刨煤部左、右电动机的输入功率,刨头牵引力,刨削深度和推进油缸的压力。5.3.2.3绘制刨头高度和刨煤部电动机功率及刨头牵引力的相关曲线。5.3.3刨头调向装置试验
安装最大刨削深度的左、右底刨力。5.3.3.1调整底刀试验
5.3.3.1.1把左、右底刨刀调整至零位以上的最高位置,往返各刨削3次。5.3.3.1.2把左、右底刨刀调整至零位以下的最低位置,往返各刨削3次。前述5.3.3.1.1和5.3.3.1.2分别完成后,各测量一次刨削的深度及底刨刀刀尖的水平位置。同时观察刨头在零位以上最高位置和零位以下最低位置时的刨削效果。5.3.3.2刨头调向机构试验
底刨刀调整至水平零位。
5.3.3.2.1调向机构调整至刨头向上的最大设计位置,往返各刨削3次。5.3.3.2.2调向机构调整至刨头向下的最大设计位置,往返各刨削3次。前述5.3.3.2.1和5.3.3.2.2分别完成后,各测量一次刨削的深度及底刨刀刀尖的水平位置。同时观察刨头在最大向上和最大向下设计位置时的刨削效果。调向机构各液压件应无渗漏液现象。5.3.4喷雾装置试验
5.3.4.1试验方法
在上述刨削过程中,进行人工控制或自动控制喷雾。5.3.4.2·试验要求
喷雾效果良好,动作可靠。
5.3.5,刨头行程限位装置试验
5.3.5.1试验方法
与模拟煤壁刨削试验同时进行。5.3.5.2试验要求
应能准确可靠地停止刨头。
5.3.6电控系统操作试验
5.3.6.1试验方法
与模拟煤壁刨削试验同时进行。5.3.6.2试验要求
动作应准确可靠,各指示仪表应显示正常。5.3.7让刀机构让刀量的再检测
模拟煤壁刨削试验完成后进行。检测方法和检测要求同5.2.3及5.2.5中有关内容。5.4过载保护系统试验
5.4.1试验方法
MT/T 689.2-1997
刨头运行过程中使过载保护系统动作3次。测录刨煤部电动机功率和刨头牵引力。5.4.2试验要求
过载保护系统应在设计的范围内产生保护作用。6刨煤部减速器试验
刨煤部减速器(以下简称“减速器”)试验,参考了附录A(提示的附录)中提及的标准。6.1试验准备
每台减速器组装后,水平置于试验台位上,注入设计要求的油质和油量,接通电源。如装有冷却系统,应按设计要求的水压和流量接上冷却水。6.2轻载跑合试验
6.2.1试验方法
减速器按额定功率的25%跑合1h(正、反向各0.5h)。每15min测定一次油池温度、各轴承温度和机壳温度。试验时,外循环油池可通以冷却水。跑合后允许换油和清洗油池。
6.2.2试验要求
6.2.2.1运转平稳,无异常响声、冲击和强烈振动。6.2.2.2各接合面密封处不允许有渗漏现象。6.2.2.3各部分无异常温升。
6.2.2.4各连接处应紧固可靠,不应松动。6.3温升试验
6.3.1试验方法
减速器分别进行正、反向连续加载试验,各个方向加载顺序和负荷分配按表1规定(双速电动机以高速,减速器按最大传动比进行试验)。记录油池温度、轴承部位温度和环境温度,并绘制温升曲线图。表1加载负荷的分配
加载顺序
6.3.2试验要求
负荷(占额定负荷的百分率)
运转时间,h
6.3.2.1齿轮箱油池和轴承的温升均不应大于80℃,最高温度不应大于100℃。6.3.2.2运转过程中,应无异常噪声,无渗漏现象。6.4耐久试验
6.4.1试验方法
减速器水平置于台位上,以最低输出转速(双速电动机用高速,减速器用最大传动比),以减速器的额定功率加载,正、反向各连续运转300h,共计600h。6.4.1.1试验时,允许采用外循环润滑油,控制其油温低于80℃。6.4.1.2在试验过程中,当试验时间在300h时,进行阶段停机检查。若齿轮、轴承、轴及其他零部件没有失效,则继续进行试验。
6.4.1.3在试验过程中,若发生意外停机现象,但减速器运转无异常情况,则仍可继续进行试验,试验90
时间可累计
MT/T 689. 2 --- 1997
6.4.1.4在试验过程中,允许换油2次。6.4.1.5在试验过程中,由记录仪随时描绘温度曲线。试验初始阶段,每隔1h记录--次油温,达到热平衡后,每隔4h记录一次油温。6.4.1.6600h试验结束后,将其解体全面检查,对齿轮、轴、轴承等主要零部件作全面测量检查。6.4.2试验要求
6.4.2.1在试验过程中,不允许更换重要零件,否则重新试验。6.4.2.2600h试验结束后,减速器的零部件不允许损坏,轮齿不允许失效,齿轮检查项目及要求应符合表2规定。
表2刨煤部减速器齿轮轮齿失效判别标准序号
项目名称
塑性变形
干涉损伤
6.5超载试验
6.5.1试验方法
判别标推
轮齿允许出现轻微磨损现象或中等磨损现象,其磨损量不应超过以下规定:
a)硬齿面轮齿任一齿面磨损量不应大于0.13mm。b)磨损不均匀的轮齿齿面,齿面两端相差不应大于0.08mm
轮齿齿面允许发生轻微胶合,胶合区域不应大于齿高的1/4,齿宽的1/3
轮齿齿面允许出现非扩展性点蚀,但麻点的大小及点蚀坑面积不应超过以下规定:
a)模数6mm以下的齿轮,麻点的平均直径不应大于1mm,模数6mm以上的齿轮麻点的平均直径不应大于2 mm。
b)点蚀坑面积为下述情况时为失效:1)点蚀区占齿高的80%时;
2)点蚀区占齿高的30%,点蚀区占齿长的40%时;3)点蚀区占齿高的60%,点蚀区占齿长的10%时轮齿齿面不应产生剥落
硬齿面轮齿不应出现塑性变形
轮齿不应出现折断现象
齿轮的任何部位不应出现裂纹
轮齿齿面不应出现干涉损伤
平均直径一(最大直径十
最小直径)/2
以减速器的最低输出转速,减速器额定功率的125%加载运行,正、反向各运转5min。记录输入转速,输出扭矩、齿轮箱的油温及各轴承的温度。6.5.2试验要求下载标准就来标准下载网
减速器的零部件不允许损坏,轮齿不允许失效,齿轮检查项目及要求应符合表2的规定。6.6效率试验
6.6.1试验方法
6.6.1.1减速器以最低输出转速(双速电动机用高速,减速器用最大传动比),以减速器的额定功率正、反向分别运转。
MT/T 689.2—1997
6.6.1.2分别记录减速器正、反向运转时的输入扭矩、转速和输出扭矩、转速。6.6:1.3本试验可以与耐久试验同时进行。6.6.2试验要求
减速器在附设外循环冷却的条件下,以额定负荷运转,当达到热平衡温度后,其机械效率应符合下列要求:
a)90kW及以下的减速器的机械效率不应低于90%;b)90kW以上的减速器的机械效率不应低于92%。6.7噪声测量
6.7.1测量方法
6.7.1.1按额定负荷运转时进行综合噪声测量(可以在耐久试验的同时进行)。6.7.1.2噪声测量方法按GB/T6404的规定进行。6.7.1.3将拾音器放置在与减速器同一水平距其周边为1m的位置,共测4点。6.7.1.4:记录噪声测量值。噪声测量数据的记录表,可参考附录B(提示的附录)。6.7.2测量要求
减速器的最大综合噪声值不应超过92dB(A)。6.8试验设备及仪器
6.8.1试验台位
6.8.1.1试验台位需经有关部门验收后方可使用。6.8.1.2试验台架应保证安全运转,加载装置应能可靠施加载荷。6.8.1.3减速器在试验台架上的安装应符合其工况及紧固方式。6.8.1.4试验装置系统可参照附录C(提示的附录)。6.8.2检验用仪器仪表
检验用各种传感器、传输线、测量仪表、记录仪表等均应按有关标准和规定进行定期校准、检定,并具有有效期内的检定合格证书、测试报告。6.9试验用润滑油
试验用润滑油应符合设计要求。6.10试验条件
6.10.1型式检验的减速器每次至少-台。6.10.2型式检验的产品,其制造、加工工艺应与出厂检验的产品一致,不应故意改动制造工艺或作附加准备。
6.11检验报告
6.11.1全部试验结束后,应根据试验结果写出详细的检验报告,所有技术文件应归档妥善保存。6.11.2记录测量结果,绘制特性曲线及图表并附在检验报告之后。6.11.3型式检验报告由检验单位提出。7刨煤机输送部试验
刨煤机输送部试验应按刮板输送机有关标准的规定进行。输送部减速器试验应按MT/T101中型式检验部分的规定进行。
整机检验时,可以按生产及设计单位的要求,参照4.1的要求,对输送部的技术参数(主要是与刨煤机其他部分的相关性能)进行检验。8判定规则
8.1刨煤机经过整机型式检验、减速器型式检验,并且在所有试验项目中均符合试验要求的则为合格品92
MT/T 689. 2-1997
8.2刨煤机属下列情况之一者为不合格品:a)未完成所需的试验项目,且不能继续进行试验时;b)试验中发生故障,主要零部件损坏时;c)虽经整机试验、减速器试验,但试验结果不符合试验要求时。9检验用仪器、仪表测量误差的规定压力:±1%。
扭矩:±2%。
转速:转速≥100r/min时,士2%,转速<100r/min时,±3%。
温度:±2℃。
噪声:±1 dB(A)。
位移:±2.5%。
9.7功率:±2%。
9.8流量:±2%。
9拉力:±3%。
MT/T 689.2--1997
附录A
(提示的附录)
参考标准
为了与已有的相关国家标准、行业标准相协调,本标准制订过程中,参考了下列标准。JB/T5077—91通用齿轮装置型式试验方法JJG1001—91通用计量名词及定义MT81一84滚简式采煤机型式试验规范附录B
(提示的附录)
噪声测量记录表
委托单位
测量地点
被测设备名称、型号、主要参数测
测量噪声平面布置图:
检测者
声级dB(A)
测量目的
MT/T 689. 2—1997
附录C
(提示的附录)
创煤部减速器试验系统示意图
1—冷却器;2一被试减速器,3联轴节4一扭矩传感器;5一加载装置;6—联轴节;7—截止阀;8-齿轮油泵9—扭矩传感器10—电动机图C1创刨煤部减速器试验系统示意图95
小提示:此标准内容仅展示完整标准里的部分截取内容,若需要完整标准请到上方自行免费下载完整标准文档。
参照MT/T410一95《刨煤机型式和基本参数》,考虑到我国目前生产和使用的均为静力式刨煤机,因此,本标准只规定了静力式刨煤机的型式试验方法和检验规则。本标准的附录A、附录B和附录C都是提示的附录本标准由煤炭工业部科技教育司提出。本标准由煤炭工业部煤矿专用设备标准化技术委员会归口。本标准起草单位:煤炭科学研究总院上海分院。本标准主要起草人:周志春、周国庆、华元钦。本标准委托煤炭科学研究总院上海分院负责解释。85
1范围
中华人民共和国煤炭行业标准
刨煤机型式检验规范
Plough--Specification of type inspectionMT/T 689.2—1997
本标准规定了煤矿地下开采长壁采煤工作面用静力式刨煤机的型式试验方法和检验规则。本标准适用于长壁采煤工作面使用的静力式刨煤机(以下简称“刨煤机”)的地面整机、刨煤部减速器型式检验。
2引用标准
下列标准所包含的条文,通过在本标准中引用而构成为本标准的条文。本标准出版时,所示版本均为有效。所有标准都会被修订,使用本标准的各方应探讨使用下列标准最新版本的可能性。GB/T6404--86齿轮装置噪声声功率级测定方法MT/T101—93刮板输送机用减速器检验规范煤矿安全规程(1992年版)
3型式检验对象
符合下述情况之一的刨煤机及其减速器,应进行型式检验。a)总体结构新颖的试制新产品;b)正式生产后,当产品的总体结构有重大改变,足以影响产品性能时;c)国家质量监督机构提出进行型式检验的要求时。4应符合的规定
4.1产品附有的电气设备,须经防爆送审检验合格。4.2产品应满足《煤矿安全规程》的有关规定。4.3送型式检验的产品必须经出厂检验合格,并应附有完整的出厂检验报告。5
刨煤机地面整机试验
刨煤机地面整机试验,参考了附录A提示的附录)中提及的标准。5.1刨煤机整机(以下简称“整机”)空运转试验刨煤机装上除刨链外所有的零部件。在水泥地面水平直线铺设,铺设长度不应少于60m。按设计要求的油质和数量加油,接通电源。如装有冷却系统,应按设计要求的水压和流量接上冷却水。5.1.1整机空运转试验
5.1.1.1试验方法
刨煤机刨煤部的传动装置正、反向空运转各0.5h,测录刨煤部电动机的输入功率。5.1.1.2试验要求
运转时应无异常声响和强烈振动。不应出现异常温升。中华人民共和国煤炭工业部1997-12-30批准86
1998-06-01实施
MT/T 689. 2—1997
5.1.2刨煤部的传动装置密封性能试验5.1.2.1试验方法
与5.1.1试验同时进行。
5.1.2.2试验要求
刨煤机传动装置各密封处应密封性能良好,没有渗漏现象。5.1.3操作系统试验
5.1.3.1机械操作机构试验
对紧链器、调高油缸、推进油缸、喷雾阀等操纵机构(手把、按钮等)进行动作试验。各操作20次。要求动作灵活、准确可靠。
5.1.3.2电控系统手把、按钮试验对电器控制箱的手把、按钮和紧急停车断电开关,以及刨煤机的各个紧急停车开关等进行动作试验。每个手把和按钮各操作20次。应能准确可靠地正、反向启动、停止刨煤部电动机,准确可靠地启动、停止输送部电动机,正确地控制音响或灯光讯号。
5.2整机空载试验
在整机空运转试验合格后,接上刨链,并予以张紧,使刨链预张力达到设计要求。5.2.1刨煤机各部分相关尺寸检测5.2.1.1检查刨链和链道的配合尺寸,链道与链道间的错位量。5.2.1.2检查刨头与滑架或中部槽的配合尺寸及滑架与滑架(或导护链装置与导护链装置)、中部槽与中部槽间的错位量,以及机头架各部分的相对位置。5.2.1.3检查刨头往返运行至终端极限位置时,刨头左、右端底刨刀刀尖至输送部链轮中心线的距离。5.2.1.4检查其他各部分的相关尺寸。5.2.2刨削深度及底刀位置检测
5.2.2.1拖钩刨煤机:测量左、右底刨刀刀尖至不同厚度限位块前沿平面的距离;滑行刨煤机:测量不同刨削深度的左、右底刨刀刀尖至铲板前沿的距离。5.2.2.2测量不同刨削深度的左、右底刨刀在不同刀位时,刀尖至刨煤机底平面的垂直距离。5.2.3让刀机构让刀量捡测
测量左、右刨刀的让刀距离。
5.2.4刨头最高高度和最低高度检测将刨头分别调整至最高高度和最低高度,并分别测量其相应的高度值。5.2.5上述5.2.1至5.2.4各项检测的测量值均应符合设计要求。而且:a)5.2.1项中,零部件应能互换安装。b)5.2.3项中,让刀机构应灵活可靠。5.2.6空载运转时,刨煤部电动机功率及刨头牵引力测试5.2.6.1试验方法
刨煤机空载运转,按下列三种情况,测录刨煤部电动机功率及刨头牵引力。a)刨头沿直线、水平铺设的输送部往返运行各3次。同时测录刨头运行速度。b)刨煤机按水平弯曲铺设,按照输送部设计允许的最大水平弯曲量铺设至少一个弯曲区段,刨头往返运行各3次。
c)刨煤机按垂直弯曲铺设,按照输送部设计允许的最大垂直弯曲量铺设至少一个弯曲区段,刨头往返运行各3次。
5.2.6.2试验要求
各项试验时,刨头应运行平稳,无卡滞现象。87
MT/T 689. 2—1997
试验时,测录的刨煤部电动机功率,拖钩刨煤机不应超过额定功率的40%,滑行刨煤机不应超过额定功率的30%。测录的刨头运行速度和刨头牵引力,应符合设计要求。5.2.7刨头惯性试验
5.2.7.1试验方法
刨煤机按直线、水平铺设,启动刨头,8s后停机。双速刨煤机试验时,低速起动,转为高速并达到额定速度后停机。
5.2.7.2试验要求
测量刨头惯性行程,往返各测量3次。5.2.8缓冲器试验
5.2.8.1试验方法
去掉限位开关,将刨头置于距缓冲器10m处,启动刨煤部电动机,刨头在不停机情况下撞击缓冲器。双速刨煤机,以高速运行进行试验。左、右缓冲器各试验3次。5.2.8.2试验要求
缓冲器若装有电动机停机开关,电动机停机开关应动作及时、安全可靠。缓冲器试验时,若缓冲器及其固定机构出现漏油、漏气或变形、损坏现象,允许修复或更换后继续试验。刨煤机的其他部分,不允许出现变形或损坏现象。5.2.9电控系统试验
5.2.9.1电压波动情况下操作试验按刨煤机要求的电控系统接线,在75%和110%额定电压情况下,分别空载启动和停止刨煤部及输送部电动机,各动作试验20次。应能准确可靠地启动和停止刨煤部和输送部电动机。5.2.9.2紧急停车开关试验
操作工作面上的紧急停车开关,每个各操作20次。应能准确可靠地停止刨煤部电动机(或刨煤部和输送部电动机)。5.2.10电控安全保护系统试验
5.2.10.1刨头行程限位装置试验对机头、机尾限位开关各进行动作试验50次。应能准确可靠地停止刨头。
5.2.10.2行程指示器试验
用行程指示器发出的信号,控制刨煤部电动机停机,上、下行各试验50次。同时观察行程指示器的显示情况。
行程显示应准确可靠,应能在上、下行预定位置,准确可靠地停止刨头。5.2.10.3具有双速功能的刨煤机速度切换试验刨煤部电动机设置为自动运行方式(启动→低速-→高速→低速→停止→换向启动),上、下行各运行50次。与5.2.10.1同时试验。
刨煤部电动机应能准确可靠地完成启动至低速、低速与高速的相互转换、低速至停止及换向启动等自动切换功能。
5.3模拟煤壁刨削试验
刨削试验用模拟煤壁的可截割性(可刨性)、形状尺寸等参数,应符合刨煤机的设计性能参数。刨煤机安装在模拟煤壁一侧,按直线、水平铺设,启动刨煤机进行刨削模拟煤壁试验,5.3.1不同刨削深度时的刨削试验,并测定相应的电动机功率、刨头牵引力和实际刨削深度,计算比能耗。比较给定的刨削深度与实际的刨削深度之间的差别。5.3.1.1选定一种刨头设计高度不变。每种刨削深度时的底刨刀均调整在水平零位,刨头往返各刨削88
3次。
MT/T 689. 2 - 1997
5.3.1.2测录刨煤部左、右两个电动机的输入功率,刨头牵引力,刨削深度,推进油缸的压力。5.3.1.3绘制刨削深度和刨煤部电动机功率及刨头牵引力的相关曲线。5.3.1.4计算比能耗。
5.3.1.5推进部分各液压件应无渗漏液现象。5.3.2刨头不同设计高度时的刨削试验,并测定刨头相应高度时的电动机功率,刨头牵引力和刨削深度。
按刨头最低、中间、最高三种刨头高度进行刨削,对每种刨头高度按选定的一种符合设计要求5.3.2.1
的刨削深度,往返各刨削3次。
5.3.2.2测录刨煤部左、右电动机的输入功率,刨头牵引力,刨削深度和推进油缸的压力。5.3.2.3绘制刨头高度和刨煤部电动机功率及刨头牵引力的相关曲线。5.3.3刨头调向装置试验
安装最大刨削深度的左、右底刨力。5.3.3.1调整底刀试验
5.3.3.1.1把左、右底刨刀调整至零位以上的最高位置,往返各刨削3次。5.3.3.1.2把左、右底刨刀调整至零位以下的最低位置,往返各刨削3次。前述5.3.3.1.1和5.3.3.1.2分别完成后,各测量一次刨削的深度及底刨刀刀尖的水平位置。同时观察刨头在零位以上最高位置和零位以下最低位置时的刨削效果。5.3.3.2刨头调向机构试验
底刨刀调整至水平零位。
5.3.3.2.1调向机构调整至刨头向上的最大设计位置,往返各刨削3次。5.3.3.2.2调向机构调整至刨头向下的最大设计位置,往返各刨削3次。前述5.3.3.2.1和5.3.3.2.2分别完成后,各测量一次刨削的深度及底刨刀刀尖的水平位置。同时观察刨头在最大向上和最大向下设计位置时的刨削效果。调向机构各液压件应无渗漏液现象。5.3.4喷雾装置试验
5.3.4.1试验方法
在上述刨削过程中,进行人工控制或自动控制喷雾。5.3.4.2·试验要求
喷雾效果良好,动作可靠。
5.3.5,刨头行程限位装置试验
5.3.5.1试验方法
与模拟煤壁刨削试验同时进行。5.3.5.2试验要求
应能准确可靠地停止刨头。
5.3.6电控系统操作试验
5.3.6.1试验方法
与模拟煤壁刨削试验同时进行。5.3.6.2试验要求
动作应准确可靠,各指示仪表应显示正常。5.3.7让刀机构让刀量的再检测
模拟煤壁刨削试验完成后进行。检测方法和检测要求同5.2.3及5.2.5中有关内容。5.4过载保护系统试验
5.4.1试验方法
MT/T 689.2-1997
刨头运行过程中使过载保护系统动作3次。测录刨煤部电动机功率和刨头牵引力。5.4.2试验要求
过载保护系统应在设计的范围内产生保护作用。6刨煤部减速器试验
刨煤部减速器(以下简称“减速器”)试验,参考了附录A(提示的附录)中提及的标准。6.1试验准备
每台减速器组装后,水平置于试验台位上,注入设计要求的油质和油量,接通电源。如装有冷却系统,应按设计要求的水压和流量接上冷却水。6.2轻载跑合试验
6.2.1试验方法
减速器按额定功率的25%跑合1h(正、反向各0.5h)。每15min测定一次油池温度、各轴承温度和机壳温度。试验时,外循环油池可通以冷却水。跑合后允许换油和清洗油池。
6.2.2试验要求
6.2.2.1运转平稳,无异常响声、冲击和强烈振动。6.2.2.2各接合面密封处不允许有渗漏现象。6.2.2.3各部分无异常温升。
6.2.2.4各连接处应紧固可靠,不应松动。6.3温升试验
6.3.1试验方法
减速器分别进行正、反向连续加载试验,各个方向加载顺序和负荷分配按表1规定(双速电动机以高速,减速器按最大传动比进行试验)。记录油池温度、轴承部位温度和环境温度,并绘制温升曲线图。表1加载负荷的分配
加载顺序
6.3.2试验要求
负荷(占额定负荷的百分率)
运转时间,h
6.3.2.1齿轮箱油池和轴承的温升均不应大于80℃,最高温度不应大于100℃。6.3.2.2运转过程中,应无异常噪声,无渗漏现象。6.4耐久试验
6.4.1试验方法
减速器水平置于台位上,以最低输出转速(双速电动机用高速,减速器用最大传动比),以减速器的额定功率加载,正、反向各连续运转300h,共计600h。6.4.1.1试验时,允许采用外循环润滑油,控制其油温低于80℃。6.4.1.2在试验过程中,当试验时间在300h时,进行阶段停机检查。若齿轮、轴承、轴及其他零部件没有失效,则继续进行试验。
6.4.1.3在试验过程中,若发生意外停机现象,但减速器运转无异常情况,则仍可继续进行试验,试验90
时间可累计
MT/T 689. 2 --- 1997
6.4.1.4在试验过程中,允许换油2次。6.4.1.5在试验过程中,由记录仪随时描绘温度曲线。试验初始阶段,每隔1h记录--次油温,达到热平衡后,每隔4h记录一次油温。6.4.1.6600h试验结束后,将其解体全面检查,对齿轮、轴、轴承等主要零部件作全面测量检查。6.4.2试验要求
6.4.2.1在试验过程中,不允许更换重要零件,否则重新试验。6.4.2.2600h试验结束后,减速器的零部件不允许损坏,轮齿不允许失效,齿轮检查项目及要求应符合表2规定。
表2刨煤部减速器齿轮轮齿失效判别标准序号
项目名称
塑性变形
干涉损伤
6.5超载试验
6.5.1试验方法
判别标推
轮齿允许出现轻微磨损现象或中等磨损现象,其磨损量不应超过以下规定:
a)硬齿面轮齿任一齿面磨损量不应大于0.13mm。b)磨损不均匀的轮齿齿面,齿面两端相差不应大于0.08mm
轮齿齿面允许发生轻微胶合,胶合区域不应大于齿高的1/4,齿宽的1/3
轮齿齿面允许出现非扩展性点蚀,但麻点的大小及点蚀坑面积不应超过以下规定:
a)模数6mm以下的齿轮,麻点的平均直径不应大于1mm,模数6mm以上的齿轮麻点的平均直径不应大于2 mm。
b)点蚀坑面积为下述情况时为失效:1)点蚀区占齿高的80%时;
2)点蚀区占齿高的30%,点蚀区占齿长的40%时;3)点蚀区占齿高的60%,点蚀区占齿长的10%时轮齿齿面不应产生剥落
硬齿面轮齿不应出现塑性变形
轮齿不应出现折断现象
齿轮的任何部位不应出现裂纹
轮齿齿面不应出现干涉损伤
平均直径一(最大直径十
最小直径)/2
以减速器的最低输出转速,减速器额定功率的125%加载运行,正、反向各运转5min。记录输入转速,输出扭矩、齿轮箱的油温及各轴承的温度。6.5.2试验要求下载标准就来标准下载网
减速器的零部件不允许损坏,轮齿不允许失效,齿轮检查项目及要求应符合表2的规定。6.6效率试验
6.6.1试验方法
6.6.1.1减速器以最低输出转速(双速电动机用高速,减速器用最大传动比),以减速器的额定功率正、反向分别运转。
MT/T 689.2—1997
6.6.1.2分别记录减速器正、反向运转时的输入扭矩、转速和输出扭矩、转速。6.6:1.3本试验可以与耐久试验同时进行。6.6.2试验要求
减速器在附设外循环冷却的条件下,以额定负荷运转,当达到热平衡温度后,其机械效率应符合下列要求:
a)90kW及以下的减速器的机械效率不应低于90%;b)90kW以上的减速器的机械效率不应低于92%。6.7噪声测量
6.7.1测量方法
6.7.1.1按额定负荷运转时进行综合噪声测量(可以在耐久试验的同时进行)。6.7.1.2噪声测量方法按GB/T6404的规定进行。6.7.1.3将拾音器放置在与减速器同一水平距其周边为1m的位置,共测4点。6.7.1.4:记录噪声测量值。噪声测量数据的记录表,可参考附录B(提示的附录)。6.7.2测量要求
减速器的最大综合噪声值不应超过92dB(A)。6.8试验设备及仪器
6.8.1试验台位
6.8.1.1试验台位需经有关部门验收后方可使用。6.8.1.2试验台架应保证安全运转,加载装置应能可靠施加载荷。6.8.1.3减速器在试验台架上的安装应符合其工况及紧固方式。6.8.1.4试验装置系统可参照附录C(提示的附录)。6.8.2检验用仪器仪表
检验用各种传感器、传输线、测量仪表、记录仪表等均应按有关标准和规定进行定期校准、检定,并具有有效期内的检定合格证书、测试报告。6.9试验用润滑油
试验用润滑油应符合设计要求。6.10试验条件
6.10.1型式检验的减速器每次至少-台。6.10.2型式检验的产品,其制造、加工工艺应与出厂检验的产品一致,不应故意改动制造工艺或作附加准备。
6.11检验报告
6.11.1全部试验结束后,应根据试验结果写出详细的检验报告,所有技术文件应归档妥善保存。6.11.2记录测量结果,绘制特性曲线及图表并附在检验报告之后。6.11.3型式检验报告由检验单位提出。7刨煤机输送部试验
刨煤机输送部试验应按刮板输送机有关标准的规定进行。输送部减速器试验应按MT/T101中型式检验部分的规定进行。
整机检验时,可以按生产及设计单位的要求,参照4.1的要求,对输送部的技术参数(主要是与刨煤机其他部分的相关性能)进行检验。8判定规则
8.1刨煤机经过整机型式检验、减速器型式检验,并且在所有试验项目中均符合试验要求的则为合格品92
MT/T 689. 2-1997
8.2刨煤机属下列情况之一者为不合格品:a)未完成所需的试验项目,且不能继续进行试验时;b)试验中发生故障,主要零部件损坏时;c)虽经整机试验、减速器试验,但试验结果不符合试验要求时。9检验用仪器、仪表测量误差的规定压力:±1%。
扭矩:±2%。
转速:转速≥100r/min时,士2%,转速<100r/min时,±3%。
温度:±2℃。
噪声:±1 dB(A)。
位移:±2.5%。
9.7功率:±2%。
9.8流量:±2%。
9拉力:±3%。
MT/T 689.2--1997
附录A
(提示的附录)
参考标准
为了与已有的相关国家标准、行业标准相协调,本标准制订过程中,参考了下列标准。JB/T5077—91通用齿轮装置型式试验方法JJG1001—91通用计量名词及定义MT81一84滚简式采煤机型式试验规范附录B
(提示的附录)
噪声测量记录表
委托单位
测量地点
被测设备名称、型号、主要参数测
测量噪声平面布置图:
检测者
声级dB(A)
测量目的
MT/T 689. 2—1997
附录C
(提示的附录)
创煤部减速器试验系统示意图
1—冷却器;2一被试减速器,3联轴节4一扭矩传感器;5一加载装置;6—联轴节;7—截止阀;8-齿轮油泵9—扭矩传感器10—电动机图C1创刨煤部减速器试验系统示意图95
小提示:此标准内容仅展示完整标准里的部分截取内容,若需要完整标准请到上方自行免费下载完整标准文档。

标准图片预览:
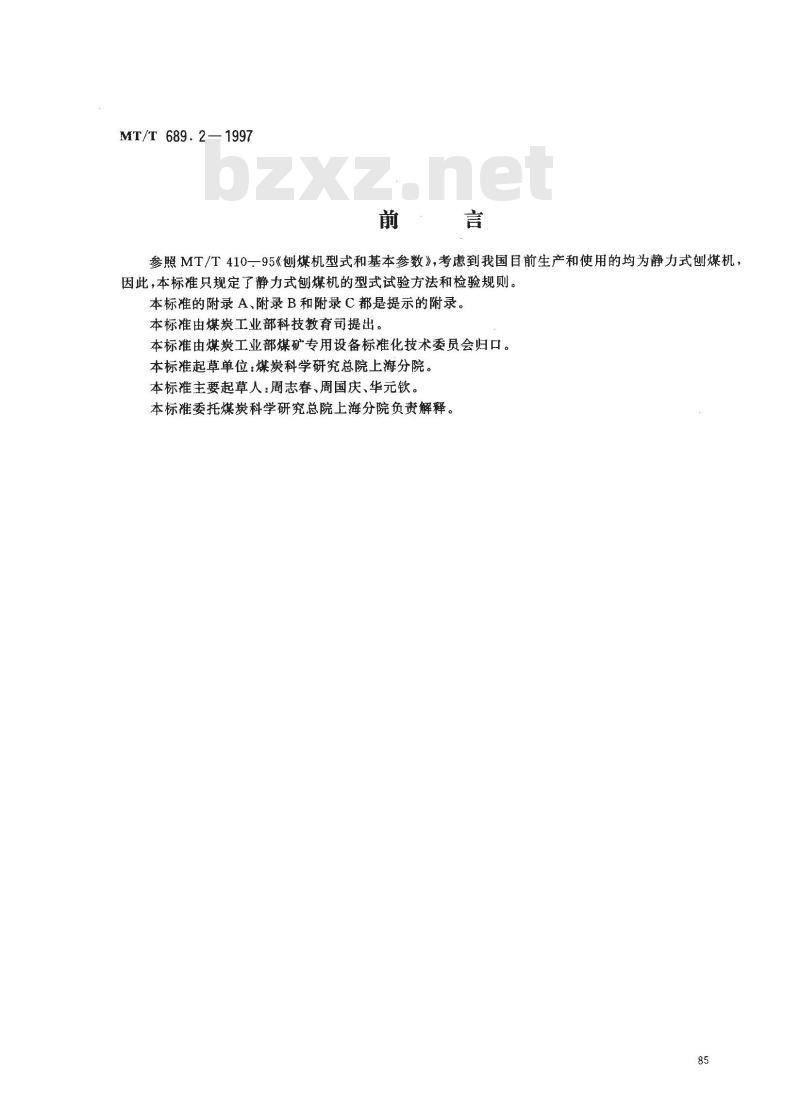
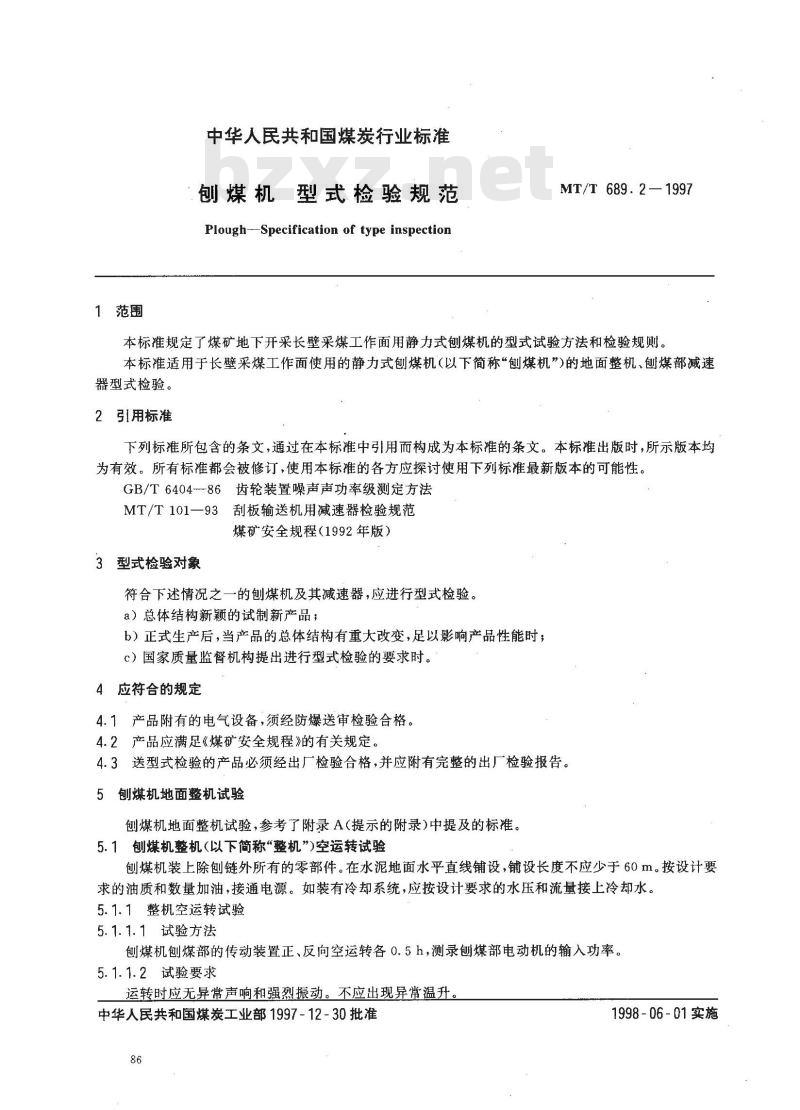
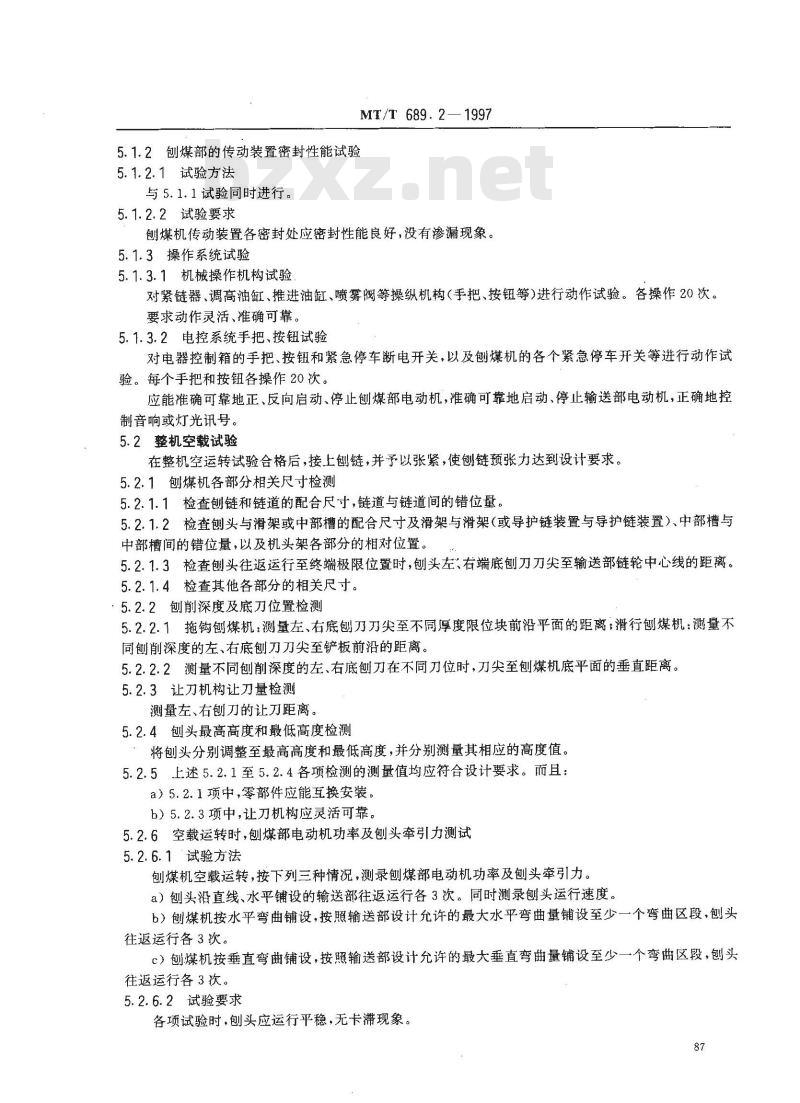
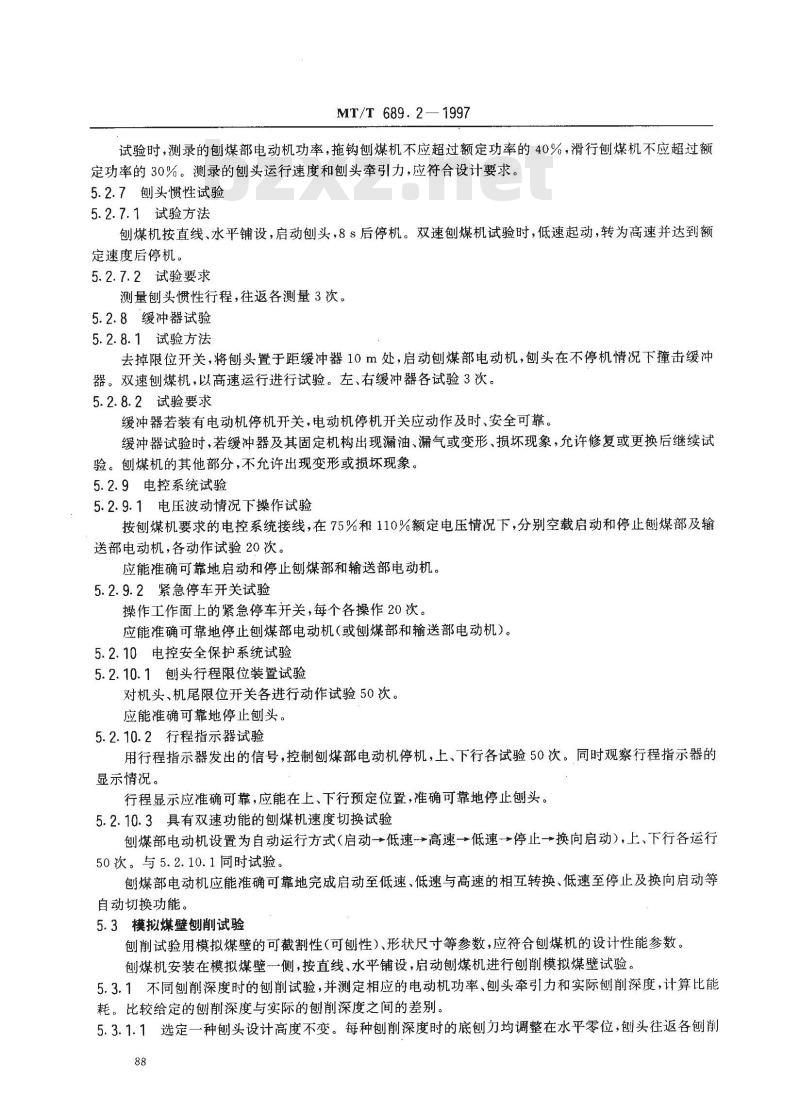
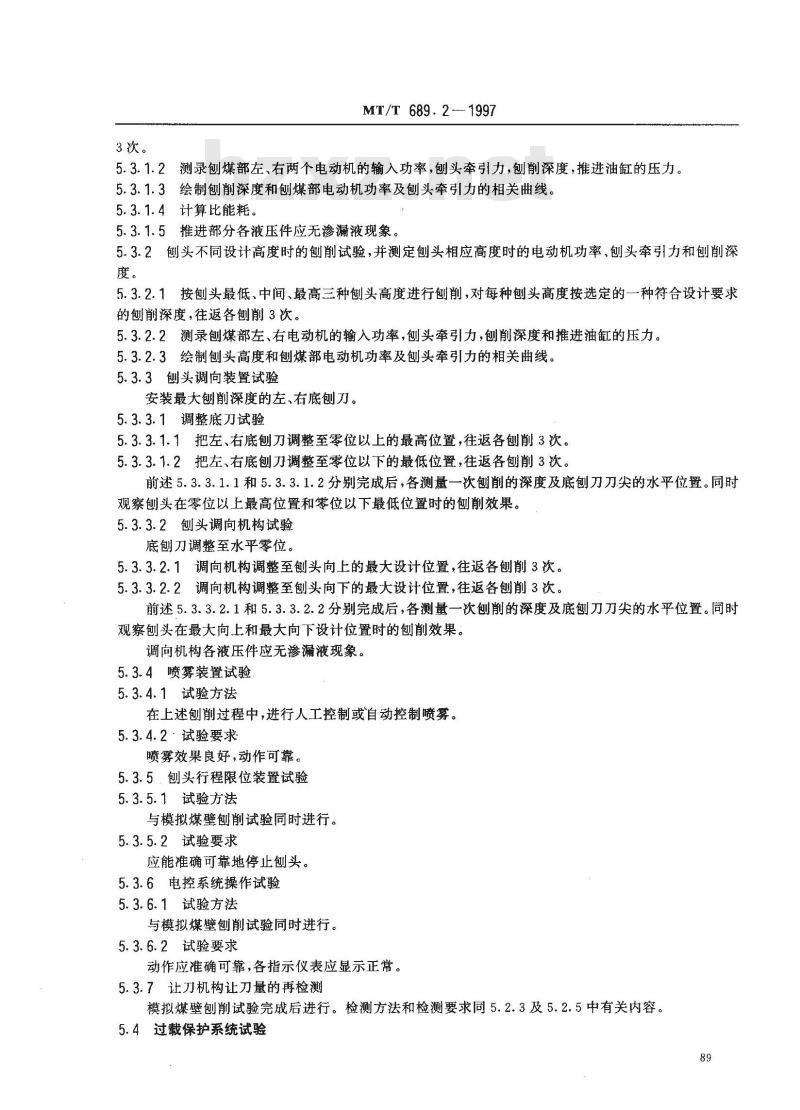
- 其它标准
- 热门标准
- 煤炭行业标准(MT)
- MT/T839-1999 石门揭穿煤层煤与瓦斯突出危险性的测定方法
- MT254-1991 煤矿水中铵离子的测定方法
- MT/T432.2-1995 蒸汽机车用靖远矿务局煤矿技术条件
- MT/T524-1995 防爆水压记录仪
- MT26-1998 KS型矿灯
- MT/T435.1-1995 冶金焦用通化矿务局煤技术条件
- MT238-1991 悬臂式掘进机通用技术条件
- MT297.3-1992 常压固定床煤气发生炉用阳泉矿务局煤技术条件
- MT/T510.3-1995 蒸汽机车用乌达矿务局煤技术条件
- MT333-1993 煤矿机车产品型号编制方法和管理办法
- MT/T618.1-1996 冶金焦用汾西矿务局煤技术条件
- MT/T348.1-1994 冶金焦用萍乡矿务局煤技术条件
- MT/T510.2-1995 冶金焦用乌达矿务局煤技术条件
- MT/T514.3-1995 蒸汽机车用徐州矿务局煤技术条件
- MT/T367-2007 煤矿水中浸蚀性二氧化碳的测定
- 行业新闻
请牢记:“bzxz.net”即是“标准下载”四个汉字汉语拼音首字母与国际顶级域名“.net”的组合。 ©2009 标准下载网 www.bzxz.net 本站邮件:bzxznet@163.com
网站备案号:湘ICP备2023016450号-1
网站备案号:湘ICP备2023016450号-1