- 您的位置:
- 标准下载网 >>
- 标准分类 >>
- 汽车行业标准(QC) >>
- QC/T 637-2000 汽车发动机曲轴弯曲疲劳强度试验方法
标准号:
QC/T 637-2000
标准名称:
汽车发动机曲轴弯曲疲劳强度试验方法
标准类别:
汽车行业标准(QC)
标准状态:
现行-
发布日期:
2000-01-19 -
实施日期:
2000-07-01 出版语种:
简体中文下载格式:
.rar.pdf下载大小:
2.76 MB

点击下载
标准简介:
标准下载解压密码:www.bzxz.net
本标准规定了汽车发动机曲轴曲拐试样的台架疲劳试验方法、数据处理方法和试验精度要求。本标准适用于下列情形,曲轴疲劳强度评估试验、新设计、变更工艺、变更材料、货源鉴定、产品质量抽检及其它认为可能引起疲劳强度显著变化等情况。 QC/T 637-2000 汽车发动机曲轴弯曲疲劳强度试验方法 QC/T637-2000

部分标准内容:
QC/T637-2000(2000-01-19发布,2000=07-01实施)原机械部标准,JB3258-1983《汽车发动机曲轴弯曲疲劳台架试验方法》已于1998年3月12日由机械工业部通知废除。本标准与原JB3258-1983标准的主要区别在于:1)统一规定循环基数N=10;
2)要求试验机精度提高到优于土3%;3)用一定存活率下的承载能力来表达曲轴的可靠性,取消“安全系数”应该≥1.3的规定;
4)用数理统计方法处理疲劳试验数据;5)规定了试验结果的置信度和相对误差。附录A、附录B和附录C都是标准的附录。本标准由国家机械工业局提出。本标准由全国汽车标准化技术委员会归口。本标准起草单位:东风汽车公司工艺研究所。本标准主要起草人,徐家炽
中华人民共和国汽车行业标
汽车发动机曲轴弯曲疲劳试验方法1范围
QC/T 637-2000
本标准规定子汽车发动机曲轴曲拐试样的台架疲劳试验力法、数据处理方法和试验精度要求。
本标准适用于下列情形:曲轴疲劳强度评估试验、新设计、变更工艺、变更材料、货源鉴定、产品质量抽检及其它认为可能引起疲劳强度显著变化等情况。引用标准
下列标准包含的条文,通过在本标准中引用而构成为本标准的条文。本标准出版时所示版本均为有效,所有标准都会被修订,使用本标准的各方应探讨使用下列标准最新版本的可能性。
GB/T10623-1989金属力学性能试验术语3符号、术语及定义
本标准中采用的符号、术语及其定义见表1;疲劳试验有关术语见GB/T10623。
Sti(i=1、
4抽样
术语单位
表1符号、术语及其定义
测定疲劳强度时.人为规定的一个载荷循环次数界限。试样超过该界限即中止试验。对高周疲劳通常规定N=10
通过试验确定的一个试样至疲劳失效时所经受的规定交变载荷次数
寿命曲线上所确定的恰好在N次循环时失从载荷——
效的一个载荷估计值。载荷用弯矩表示在指定循环基数下,母体的中值疲劳承载能力,亦即m母体的50%能经受规定的循环基数而不产生裂纹或断裂的一个载荷估计值
子样总数为n的一组试验中,第i次独立试验所使用的交变载荷幅。试验载荷用弯矩表示在升降法相邻两级试验载荷下,出现相反试验结果(通过和失效)的二个独立试验组成“一对”。所有这些对的总数,称为对子数目
升降法相邻两级载荷的平均值。设第i次试验载荷为Sti,第i+1次试验为Sti+1,则Sri=(St+Sti+)/2按附录A规定方法,计算得到的曲轴工作时承受弯炬的一个理论估计值
4.1试样应是经稳定工艺生产的同一批工业产品,数量不少于30根并经质量检验确认符合产品图样、工艺及材料规定,从中随机抽样。4.2试样数量应能保证试验精度满足本标准6.4。4.3
由曲轴上截取试样的方法,应保证能获得曲轴中疲劳强度最薄弱的部位,并用简图形式作出规定,在以后同类试严重保持不变,4.4
试验开始前,试样应统一编号。试验顺序应按编号随机化处现后进行。5试验装置
疲劳试验装置应通过国家计量器具的型式批准,试验频率及载荷应保证不会导致试样危险截面产生局部发热,频率应控制在20Hz~200Hz范围内。5.2试验采用夹具上某一定点的加速度值作为力载荷控制参数,因为这样引起的载荷系统误差最小。一般采用加速度传感器,也可选用位移或应变传感器。在实际工作中允许通过调节中间放大环节使传感器的电压输出量直接表示成为载荷值(称为归一化处理)。
5.3试验系统采用静标动测法通过试样上的应变值作为中间量对试验载荷进行检定。试验力矩示值得相对误差不应大于士3%,示值的重复性相对误差不应大于3%。计算公式如下:
q-[(e)/]×100%
b=[(eim—E;mn)/e,]X100%
式中:装置试验力矩示值相对误差;b——装置试验力矩重复性相对误差—静标定力矩对应的应变值;
e,一-一装置动态力矩示值与静标定力矩相等时.在试样上动态应变峰值三次读数的平均值;E,s—同-一组动态应变峰值读数中的最大值:e,…——同一组动态应变峰值读数中的最小值。力值检定应使用量程适当的三等标准测力仪。应变测量应使用准确度为1%的电阻应变仪或应变放大器。力臂长度测量精度应优于0.1%。当对系统检定结果产生疑问时,可根据力学惯性原理,计算在一定弯矩下5.4
夹具上某点的加速度值来进行复核,但这时所用的传感器应事先进行检定,确保所得加速度值误差不大于土3%。5.5系统应至少每年检定一次,对传感器归一化值进行修正并作好记录。所用测试仪表需有计量部门定期检验合格证明。根据工作需要,系统也可以在每进行组试验之前检定一次。
6试验方法
6.1试验循环基数取10,并在试验报告中注明。6.2判据
承载能力:曲轴疲劳承载能力以弯矩为判据,但不排除各企业可以采用6.2.1
其它指标(例如:力、应力)作为自己的内控判据。试样开裂:试样产生疲劳裂纹的特征是系统共振频率下降,规定下降量6.2.2
为开始试验时频率的1%作为试样开裂的判据。如果委托试验,双方也可以经过协商量另定规定,但这时的开裂判据应在试验报告中注明。6.3试验程序
曲拐试样S一N曲线的测定是曲轴承载能力评估的基础,可由成组法和升降法两部分试验组成。成组法取三个组,分别获得三个载荷水平下具有50%存活(1)
:(2)
率的对数中值寿命;升降法则用以获取具有50%存活率的条件疲劳极限。用上述4个点组成S一N曲线,然后按三参数幂函数的形式拟合获得具有50%存活率的S一N曲线,并且根据各点的标准差推算出不同失效概率的P一S一N曲线。具体步骤如下:
6.3.1成组试验法
用成组法评估曲轴在过载时的疲劳强度。在一个较高的载荷下,用一组不少于8个的试样,测定它们对数疲劳寿命N.的平均值和标准差,就构成了成组法的试验结果,其精度满足6.4。
成组试验法三组载荷水平的选择应使曲拐断裂的循环次数分别在下列范围内:
S=(0.8~5.2) X105
Sz=(5.2~8.0)X10
Ss=(0.8~5.2)×10°
也可以将试验结果在正态概率纸上检验在该载荷下的失效概率一对数寿命关系是否符合对数正态分布(检验各点是否在一直线上)。在满足所要求的最小相关系数的情况下,计算中值对数寿命和标准差,并通过检验变异系数确定是否已经满足本标准中6.4,最后画出失效溉率一一对数寿命图,见图1。央效摄率P%
对数寿命IgN
图!三组不同载荷下失效概率与对数疲劳寿命之问的美系6.3.2升降法
用升降法测定曲拐的M-确定曲轴的疲劳极限M-1,首批试样数量不得小于18个,试验前应对全部试样编号并随机化处理,以保证获得六对有效数据。弯矩增量△M一般在预计疲劳极限的5%以内,试验可在三至五级弯矩水平下进行。应使第一根试样的试验弯矩水平略高于预计M-1。根据上一根试样的试验结果(失效或通过),决定下一根试样的试验水平个(降低或升高),直至完成全部试验。对第一次出现相反结果(失效和通过;通过和失效)以前的数据,如在以后的试验数据波动范围之外,则予以舍弃;如在上述波动范围之内,则作为有效数据加以利用,即在试验过程中,陆续将它们平移到第一对相反结果之后,作为该试样所弯矩水平下的第一个有效数据。所用计算公式如下:承载弯矩疲劳极限:M-bzxz.net
式中:S,-(S,+S+)/2
S.、S.+分别是出现相反结果的相邻两级试验载荷,-1.2…\—一有效数据的对子数目
子样标准差:
变异系数参照附录B确定是否满足6.4。变异系数
μ=S-1/M_
6.3.3无限寿命疲劳极限估算,S—N曲线及P—SN曲线的拟合将不同载荷下用成组法求得的结果与升降法测得的疲劳极限结合在一起,就组成了这种型号曲轴的S一N曲线,并且将成为今后进行统计推断的依据。按三参数幂函数拟合S—N曲线:
s-c(1-
式中S载荷N—寿命A、a得定常数C—无限寿命下的疲劳极限(存活率P=50%置信度=95%)拟和的方法见附录C。
6.4试验精度要求
试验最小的子样由对(升降法)或八个(成组法)试样构成,试验结果应满足置信度≥95%,相对误差≤5%的要求。如果精度不能满足,应加大子样直至满足要求为止(参见附录B)。
6.5试验结果的分析和说明
6.5.1比较
若试验结果符合6.4有关试验精度的规定,可将结果直接与已有数据或已有的P一S一N曲线相比较,以确定这批试样的优劣。(3)
(5)
6.5.2不同存活率下的疲劳极限
因为试验得到的疲劳极限是存活率50%的中位值,所以有时需要对不同存活率的疲劳极限进行估算。存活率为P的疲劳极限值可按下式计算:M- (P%)=M--aXKXSr-1
式中:S-I—对应M-.的标准差
a——对应概率为P的单侧正态分布分位值K一一与有效数据的对子数目有关的修正系数·(7)
安全疲劳极限的估算精度,可参照附录B计算。(7)式中的K值可由表B2根据n值查出。
6.5.3安全系数
安全系数本身是一个不能被唯一确定的随机值,而且它与所要求曲轴的存活率有关,所以本标准不采用安全系数作为评价曲轴安全性的指标。但如果仍然希望沿用这一概念表述曲轴的可靠性,应按(8)式计算存活率为99.9%时的安全系数。
n=M- (99.9%) /M-......
式中:n——存活率为99.9%的安全系数M-1(99.9%)一一由(7)计算得的疲劳极限M-一一由附录A计算得的名义工作弯矩(8)
在所有的试验报告中,安全系数应明确标示出对应的存活率。每一种型号的曲轴,n值应由各生产企业在承担风险与投资额度之间作出合理的执择。6.6强化检验
本标准适用范围中规定的产品质量抽检,也可以不用升降法测定样品的疲劳极限而代之以用成组法在·个较高的载荷下测定其对数平均疲劳寿命IgN,:若测得的gN,值大于或等于事前用合格产品测得的对数平均寿命IgN,且其标准差小于等于合格产品在同一试验载荷下的标准差,则该批产品可认为合格予以验收。
强化检验中的试样不得少于8个,所选试验载荷应使试样寿命在5×105~5×10°范围,建议试验载荷选用本标准6.3.1中的成组试验法中最低的一个载荷。试验精度应符合本标准中6.4。
强化检验也可以通过作图法进行,具体方法是:将某一载荷下成组法的试验结果按寿命由小至大排列。序号m=1,2,·8,·n;并按小子样计算其失效概率Pi。
Pi=3-1/ 3n+11
(9)
式中:n=子样大小,应大于或等于8。不同的P值与之对应的对数疲劳寿命N组成正态概率坐标上的一个点,如果各点的联线在P-1gN图上位于同一载荷下试样许用界限的右侧,则该批产品可认为合格。许用界限由合格试样在同一载荷下测定。7试验报告
试验报告应包括以下内容:
a)试验日期(自××日起至××日结束)。b)试验目的。
c)试件说明(曲轴零件号,材料,工艺,表面状态,硬度,金相组织等)。d)取样部件(附简图)。
e)夹具型号,力学常数。
f)疲劳失效判据(频率下降限度或其它)。g)升降法及/或成组试验法的数据记录。h)升降图及/或成组试验法的分析结果,并附有关于试验精度的计算说明。必须注明循环基数。
i)强度评估结论。
8原始记录
组独立试验完成后,其原始记录应随同一份报告存档备查。原始记录内容应包括:试验日期、操作者,激振频率,试验弯矩,试样寿命及其它必要的情况说明。若系统在本次试验前进行了新的检定,则应同时附带检定记录。附录A
(标准的附录)
曲轴名义工作弯矩计算
A1曲轴名义工作弯矩计算方法由图A1计算曲轴名义工作弯矩如下:M-=K×R×G=πD\LKGP/4L··
式中:名义弯矩M-1,N·m
支承反力R,N
曲拐总作用力P=P×元D/4,N
爆发压力P,kPa
气缸直径D,cm
支承反力臂长G=(H十L)/2,m(A1)
(对于某些曲轴,两相邻主轴颈宽度可能不同,分别为L1及Lz2,计算G时,L取Lz及Lz2两者中的较大值,使计算得的M-较大)。曲柄臂厚度H,m
主轴颈宽度Lz,m
相邻两主轴颈中心距离L=Lz1/2+2H+L:+Lz2/2,mB1
连杆轴颈宽度Li,m
血拐中心至主轴颈中心距离Li=L/2+H+L./2,m(计算L时,取Lz及Lz两者中的较小值)支承系数K:全支承K取0.75;非全支承K取0.85;滚动轴承K取0.90。图AI
曲轴名义工作弯矩计算图
附录B
(标准的附录)
安全疲劳极限的计算
用升降队分析求得的“极限”,都是母体中值估计量;即存活率50%,它的精度,或在一定精度与误差允许范围下所需的最少子样数n,可由它的变异系数大小来判定。适用于升降法的数据列于表B1,其中n是有效子样的对子数目。表B1子样大小与变异系数的关系最少子样(n)
变异系数最大
值S-/M
注:置信度≥95%
最少子样(n)
相对误差≤5%
变异系数最大
值Sm-/ML-
由M-估算其它的存活率,例如99.9%,如果是正态分布,则应减去3.09倍的Sn-1。同时,考虑到子样大小n不是无限大值,因而S-1还要可乘以一个大于1的修正值K。K值可以通过表B2查得。表B2
标准差修正系数K值
1.0181.017
51.0141.0141.0091.0061.005
般情况下,变异系数应满足下列条件:S.--/M-,s
式中:相对误差:
#一一子样大小;
t,xV(1/n+up(k=-1))-oxupxk
,分布值.取决于置信度及自由度一!:\p正态分布的百分位值,与存活客有关:K—标准差修正系数。
由(B1)N式可见,变异系数的界限,除与误差百分数、置信度及子样大小有关外,还同所要求的存活率有关,估计的存活率越高,要求的子样就越大。表B3列出了置信度90%、相对误差限度10%时为了估计99.9%存活率所需的最低限度试样量。
表B3子样大小与变异系数的关系最少子样(n)
变异系数最大值
Sn-/M-
最少子样(n)
注:置信度90%;存活率99.9%;相对误差10%。附录
(标准的附录)
变异系数最大值
(BI)
拟合方法
将公式(6)变换为
式中:
则公式C1为:
S—N曲线及P—S—N曲线的拟和方法YalgN-IgA
Y--Ig(S/C-1)
6=-IgA
Y=ux+b
先设定一个必然小于条件疲劳极限M-,的C值,将该C值代人公式(C2),求得对应成组法和升降法4级载荷S的Y值及与之对应公式(C3)的X值,根据最小二乘法求出公式(C5)的斜率a、截距b及相关系数。通过不断的设定、试算,找出能使公式(C5)的线性相关系数达到最大的C。这时的C值即为无限寿命下具有50%的存活率、置信度为95%的疲劳极限值。同时,确定了这时的A和。据公式(6)得到描述曲轴疲劳性能的S-N曲线。
P-S-N曲线的拟合与S-N曲线相同.例如当要求存活率P=99.9%时Y,-lg(S/C,-1)
.为寿命标准差
X-X,-3.090
α-1-0-1-3.09S.-S.-1为条件疲劳极限的标准差,只要设定一个C,值就能用最小二乘法求得当线性相关系数Y最大时的A,和a,:这时的P-S一N曲线方程为:S,-C,(1+A,/N)
C,即为具有99.9%存活率、置信度为95%无限寿命下的疲劳极限。(C6)
小提示:此标准内容仅展示完整标准里的部分截取内容,若需要完整标准请到上方自行免费下载完整标准文档。
2)要求试验机精度提高到优于土3%;3)用一定存活率下的承载能力来表达曲轴的可靠性,取消“安全系数”应该≥1.3的规定;
4)用数理统计方法处理疲劳试验数据;5)规定了试验结果的置信度和相对误差。附录A、附录B和附录C都是标准的附录。本标准由国家机械工业局提出。本标准由全国汽车标准化技术委员会归口。本标准起草单位:东风汽车公司工艺研究所。本标准主要起草人,徐家炽
中华人民共和国汽车行业标
汽车发动机曲轴弯曲疲劳试验方法1范围
QC/T 637-2000
本标准规定子汽车发动机曲轴曲拐试样的台架疲劳试验力法、数据处理方法和试验精度要求。
本标准适用于下列情形:曲轴疲劳强度评估试验、新设计、变更工艺、变更材料、货源鉴定、产品质量抽检及其它认为可能引起疲劳强度显著变化等情况。引用标准
下列标准包含的条文,通过在本标准中引用而构成为本标准的条文。本标准出版时所示版本均为有效,所有标准都会被修订,使用本标准的各方应探讨使用下列标准最新版本的可能性。
GB/T10623-1989金属力学性能试验术语3符号、术语及定义
本标准中采用的符号、术语及其定义见表1;疲劳试验有关术语见GB/T10623。
Sti(i=1、
4抽样
术语单位
表1符号、术语及其定义
测定疲劳强度时.人为规定的一个载荷循环次数界限。试样超过该界限即中止试验。对高周疲劳通常规定N=10
通过试验确定的一个试样至疲劳失效时所经受的规定交变载荷次数
寿命曲线上所确定的恰好在N次循环时失从载荷——
效的一个载荷估计值。载荷用弯矩表示在指定循环基数下,母体的中值疲劳承载能力,亦即m母体的50%能经受规定的循环基数而不产生裂纹或断裂的一个载荷估计值
子样总数为n的一组试验中,第i次独立试验所使用的交变载荷幅。试验载荷用弯矩表示在升降法相邻两级试验载荷下,出现相反试验结果(通过和失效)的二个独立试验组成“一对”。所有这些对的总数,称为对子数目
升降法相邻两级载荷的平均值。设第i次试验载荷为Sti,第i+1次试验为Sti+1,则Sri=(St+Sti+)/2按附录A规定方法,计算得到的曲轴工作时承受弯炬的一个理论估计值
4.1试样应是经稳定工艺生产的同一批工业产品,数量不少于30根并经质量检验确认符合产品图样、工艺及材料规定,从中随机抽样。4.2试样数量应能保证试验精度满足本标准6.4。4.3
由曲轴上截取试样的方法,应保证能获得曲轴中疲劳强度最薄弱的部位,并用简图形式作出规定,在以后同类试严重保持不变,4.4
试验开始前,试样应统一编号。试验顺序应按编号随机化处现后进行。5试验装置
疲劳试验装置应通过国家计量器具的型式批准,试验频率及载荷应保证不会导致试样危险截面产生局部发热,频率应控制在20Hz~200Hz范围内。5.2试验采用夹具上某一定点的加速度值作为力载荷控制参数,因为这样引起的载荷系统误差最小。一般采用加速度传感器,也可选用位移或应变传感器。在实际工作中允许通过调节中间放大环节使传感器的电压输出量直接表示成为载荷值(称为归一化处理)。
5.3试验系统采用静标动测法通过试样上的应变值作为中间量对试验载荷进行检定。试验力矩示值得相对误差不应大于士3%,示值的重复性相对误差不应大于3%。计算公式如下:
q-[(e)/]×100%
b=[(eim—E;mn)/e,]X100%
式中:装置试验力矩示值相对误差;b——装置试验力矩重复性相对误差—静标定力矩对应的应变值;
e,一-一装置动态力矩示值与静标定力矩相等时.在试样上动态应变峰值三次读数的平均值;E,s—同-一组动态应变峰值读数中的最大值:e,…——同一组动态应变峰值读数中的最小值。力值检定应使用量程适当的三等标准测力仪。应变测量应使用准确度为1%的电阻应变仪或应变放大器。力臂长度测量精度应优于0.1%。当对系统检定结果产生疑问时,可根据力学惯性原理,计算在一定弯矩下5.4
夹具上某点的加速度值来进行复核,但这时所用的传感器应事先进行检定,确保所得加速度值误差不大于土3%。5.5系统应至少每年检定一次,对传感器归一化值进行修正并作好记录。所用测试仪表需有计量部门定期检验合格证明。根据工作需要,系统也可以在每进行组试验之前检定一次。
6试验方法
6.1试验循环基数取10,并在试验报告中注明。6.2判据
承载能力:曲轴疲劳承载能力以弯矩为判据,但不排除各企业可以采用6.2.1
其它指标(例如:力、应力)作为自己的内控判据。试样开裂:试样产生疲劳裂纹的特征是系统共振频率下降,规定下降量6.2.2
为开始试验时频率的1%作为试样开裂的判据。如果委托试验,双方也可以经过协商量另定规定,但这时的开裂判据应在试验报告中注明。6.3试验程序
曲拐试样S一N曲线的测定是曲轴承载能力评估的基础,可由成组法和升降法两部分试验组成。成组法取三个组,分别获得三个载荷水平下具有50%存活(1)
:(2)
率的对数中值寿命;升降法则用以获取具有50%存活率的条件疲劳极限。用上述4个点组成S一N曲线,然后按三参数幂函数的形式拟合获得具有50%存活率的S一N曲线,并且根据各点的标准差推算出不同失效概率的P一S一N曲线。具体步骤如下:
6.3.1成组试验法
用成组法评估曲轴在过载时的疲劳强度。在一个较高的载荷下,用一组不少于8个的试样,测定它们对数疲劳寿命N.的平均值和标准差,就构成了成组法的试验结果,其精度满足6.4。
成组试验法三组载荷水平的选择应使曲拐断裂的循环次数分别在下列范围内:
S=(0.8~5.2) X105
Sz=(5.2~8.0)X10
Ss=(0.8~5.2)×10°
也可以将试验结果在正态概率纸上检验在该载荷下的失效概率一对数寿命关系是否符合对数正态分布(检验各点是否在一直线上)。在满足所要求的最小相关系数的情况下,计算中值对数寿命和标准差,并通过检验变异系数确定是否已经满足本标准中6.4,最后画出失效溉率一一对数寿命图,见图1。央效摄率P%
对数寿命IgN
图!三组不同载荷下失效概率与对数疲劳寿命之问的美系6.3.2升降法
用升降法测定曲拐的M-确定曲轴的疲劳极限M-1,首批试样数量不得小于18个,试验前应对全部试样编号并随机化处理,以保证获得六对有效数据。弯矩增量△M一般在预计疲劳极限的5%以内,试验可在三至五级弯矩水平下进行。应使第一根试样的试验弯矩水平略高于预计M-1。根据上一根试样的试验结果(失效或通过),决定下一根试样的试验水平个(降低或升高),直至完成全部试验。对第一次出现相反结果(失效和通过;通过和失效)以前的数据,如在以后的试验数据波动范围之外,则予以舍弃;如在上述波动范围之内,则作为有效数据加以利用,即在试验过程中,陆续将它们平移到第一对相反结果之后,作为该试样所弯矩水平下的第一个有效数据。所用计算公式如下:承载弯矩疲劳极限:M-bzxz.net
式中:S,-(S,+S+)/2
S.、S.+分别是出现相反结果的相邻两级试验载荷,-1.2…\—一有效数据的对子数目
子样标准差:
变异系数参照附录B确定是否满足6.4。变异系数
μ=S-1/M_
6.3.3无限寿命疲劳极限估算,S—N曲线及P—SN曲线的拟合将不同载荷下用成组法求得的结果与升降法测得的疲劳极限结合在一起,就组成了这种型号曲轴的S一N曲线,并且将成为今后进行统计推断的依据。按三参数幂函数拟合S—N曲线:
s-c(1-
式中S载荷N—寿命A、a得定常数C—无限寿命下的疲劳极限(存活率P=50%置信度=95%)拟和的方法见附录C。
6.4试验精度要求
试验最小的子样由对(升降法)或八个(成组法)试样构成,试验结果应满足置信度≥95%,相对误差≤5%的要求。如果精度不能满足,应加大子样直至满足要求为止(参见附录B)。
6.5试验结果的分析和说明
6.5.1比较
若试验结果符合6.4有关试验精度的规定,可将结果直接与已有数据或已有的P一S一N曲线相比较,以确定这批试样的优劣。(3)
(5)
6.5.2不同存活率下的疲劳极限
因为试验得到的疲劳极限是存活率50%的中位值,所以有时需要对不同存活率的疲劳极限进行估算。存活率为P的疲劳极限值可按下式计算:M- (P%)=M--aXKXSr-1
式中:S-I—对应M-.的标准差
a——对应概率为P的单侧正态分布分位值K一一与有效数据的对子数目有关的修正系数·(7)
安全疲劳极限的估算精度,可参照附录B计算。(7)式中的K值可由表B2根据n值查出。
6.5.3安全系数
安全系数本身是一个不能被唯一确定的随机值,而且它与所要求曲轴的存活率有关,所以本标准不采用安全系数作为评价曲轴安全性的指标。但如果仍然希望沿用这一概念表述曲轴的可靠性,应按(8)式计算存活率为99.9%时的安全系数。
n=M- (99.9%) /M-......
式中:n——存活率为99.9%的安全系数M-1(99.9%)一一由(7)计算得的疲劳极限M-一一由附录A计算得的名义工作弯矩(8)
在所有的试验报告中,安全系数应明确标示出对应的存活率。每一种型号的曲轴,n值应由各生产企业在承担风险与投资额度之间作出合理的执择。6.6强化检验
本标准适用范围中规定的产品质量抽检,也可以不用升降法测定样品的疲劳极限而代之以用成组法在·个较高的载荷下测定其对数平均疲劳寿命IgN,:若测得的gN,值大于或等于事前用合格产品测得的对数平均寿命IgN,且其标准差小于等于合格产品在同一试验载荷下的标准差,则该批产品可认为合格予以验收。
强化检验中的试样不得少于8个,所选试验载荷应使试样寿命在5×105~5×10°范围,建议试验载荷选用本标准6.3.1中的成组试验法中最低的一个载荷。试验精度应符合本标准中6.4。
强化检验也可以通过作图法进行,具体方法是:将某一载荷下成组法的试验结果按寿命由小至大排列。序号m=1,2,·8,·n;并按小子样计算其失效概率Pi。
Pi=3-1/ 3n+11
(9)
式中:n=子样大小,应大于或等于8。不同的P值与之对应的对数疲劳寿命N组成正态概率坐标上的一个点,如果各点的联线在P-1gN图上位于同一载荷下试样许用界限的右侧,则该批产品可认为合格。许用界限由合格试样在同一载荷下测定。7试验报告
试验报告应包括以下内容:
a)试验日期(自××日起至××日结束)。b)试验目的。
c)试件说明(曲轴零件号,材料,工艺,表面状态,硬度,金相组织等)。d)取样部件(附简图)。
e)夹具型号,力学常数。
f)疲劳失效判据(频率下降限度或其它)。g)升降法及/或成组试验法的数据记录。h)升降图及/或成组试验法的分析结果,并附有关于试验精度的计算说明。必须注明循环基数。
i)强度评估结论。
8原始记录
组独立试验完成后,其原始记录应随同一份报告存档备查。原始记录内容应包括:试验日期、操作者,激振频率,试验弯矩,试样寿命及其它必要的情况说明。若系统在本次试验前进行了新的检定,则应同时附带检定记录。附录A
(标准的附录)
曲轴名义工作弯矩计算
A1曲轴名义工作弯矩计算方法由图A1计算曲轴名义工作弯矩如下:M-=K×R×G=πD\LKGP/4L··
式中:名义弯矩M-1,N·m
支承反力R,N
曲拐总作用力P=P×元D/4,N
爆发压力P,kPa
气缸直径D,cm
支承反力臂长G=(H十L)/2,m(A1)
(对于某些曲轴,两相邻主轴颈宽度可能不同,分别为L1及Lz2,计算G时,L取Lz及Lz2两者中的较大值,使计算得的M-较大)。曲柄臂厚度H,m
主轴颈宽度Lz,m
相邻两主轴颈中心距离L=Lz1/2+2H+L:+Lz2/2,mB1
连杆轴颈宽度Li,m
血拐中心至主轴颈中心距离Li=L/2+H+L./2,m(计算L时,取Lz及Lz两者中的较小值)支承系数K:全支承K取0.75;非全支承K取0.85;滚动轴承K取0.90。图AI
曲轴名义工作弯矩计算图
附录B
(标准的附录)
安全疲劳极限的计算
用升降队分析求得的“极限”,都是母体中值估计量;即存活率50%,它的精度,或在一定精度与误差允许范围下所需的最少子样数n,可由它的变异系数大小来判定。适用于升降法的数据列于表B1,其中n是有效子样的对子数目。表B1子样大小与变异系数的关系最少子样(n)
变异系数最大
值S-/M
注:置信度≥95%
最少子样(n)
相对误差≤5%
变异系数最大
值Sm-/ML-
由M-估算其它的存活率,例如99.9%,如果是正态分布,则应减去3.09倍的Sn-1。同时,考虑到子样大小n不是无限大值,因而S-1还要可乘以一个大于1的修正值K。K值可以通过表B2查得。表B2
标准差修正系数K值
1.0181.017
51.0141.0141.0091.0061.005
般情况下,变异系数应满足下列条件:S.--/M-,s
式中:相对误差:
#一一子样大小;
t,xV(1/n+up(k=-1))-oxupxk
,分布值.取决于置信度及自由度一!:\p正态分布的百分位值,与存活客有关:K—标准差修正系数。
由(B1)N式可见,变异系数的界限,除与误差百分数、置信度及子样大小有关外,还同所要求的存活率有关,估计的存活率越高,要求的子样就越大。表B3列出了置信度90%、相对误差限度10%时为了估计99.9%存活率所需的最低限度试样量。
表B3子样大小与变异系数的关系最少子样(n)
变异系数最大值
Sn-/M-
最少子样(n)
注:置信度90%;存活率99.9%;相对误差10%。附录
(标准的附录)
变异系数最大值
(BI)
拟合方法
将公式(6)变换为
式中:
则公式C1为:
S—N曲线及P—S—N曲线的拟和方法YalgN-IgA
Y--Ig(S/C-1)
6=-IgA
Y=ux+b
先设定一个必然小于条件疲劳极限M-,的C值,将该C值代人公式(C2),求得对应成组法和升降法4级载荷S的Y值及与之对应公式(C3)的X值,根据最小二乘法求出公式(C5)的斜率a、截距b及相关系数。通过不断的设定、试算,找出能使公式(C5)的线性相关系数达到最大的C。这时的C值即为无限寿命下具有50%的存活率、置信度为95%的疲劳极限值。同时,确定了这时的A和。据公式(6)得到描述曲轴疲劳性能的S-N曲线。
P-S-N曲线的拟合与S-N曲线相同.例如当要求存活率P=99.9%时Y,-lg(S/C,-1)
.为寿命标准差
X-X,-3.090
α-1-0-1-3.09S.-S.-1为条件疲劳极限的标准差,只要设定一个C,值就能用最小二乘法求得当线性相关系数Y最大时的A,和a,:这时的P-S一N曲线方程为:S,-C,(1+A,/N)
C,即为具有99.9%存活率、置信度为95%无限寿命下的疲劳极限。(C6)
小提示:此标准内容仅展示完整标准里的部分截取内容,若需要完整标准请到上方自行免费下载完整标准文档。

标准图片预览:
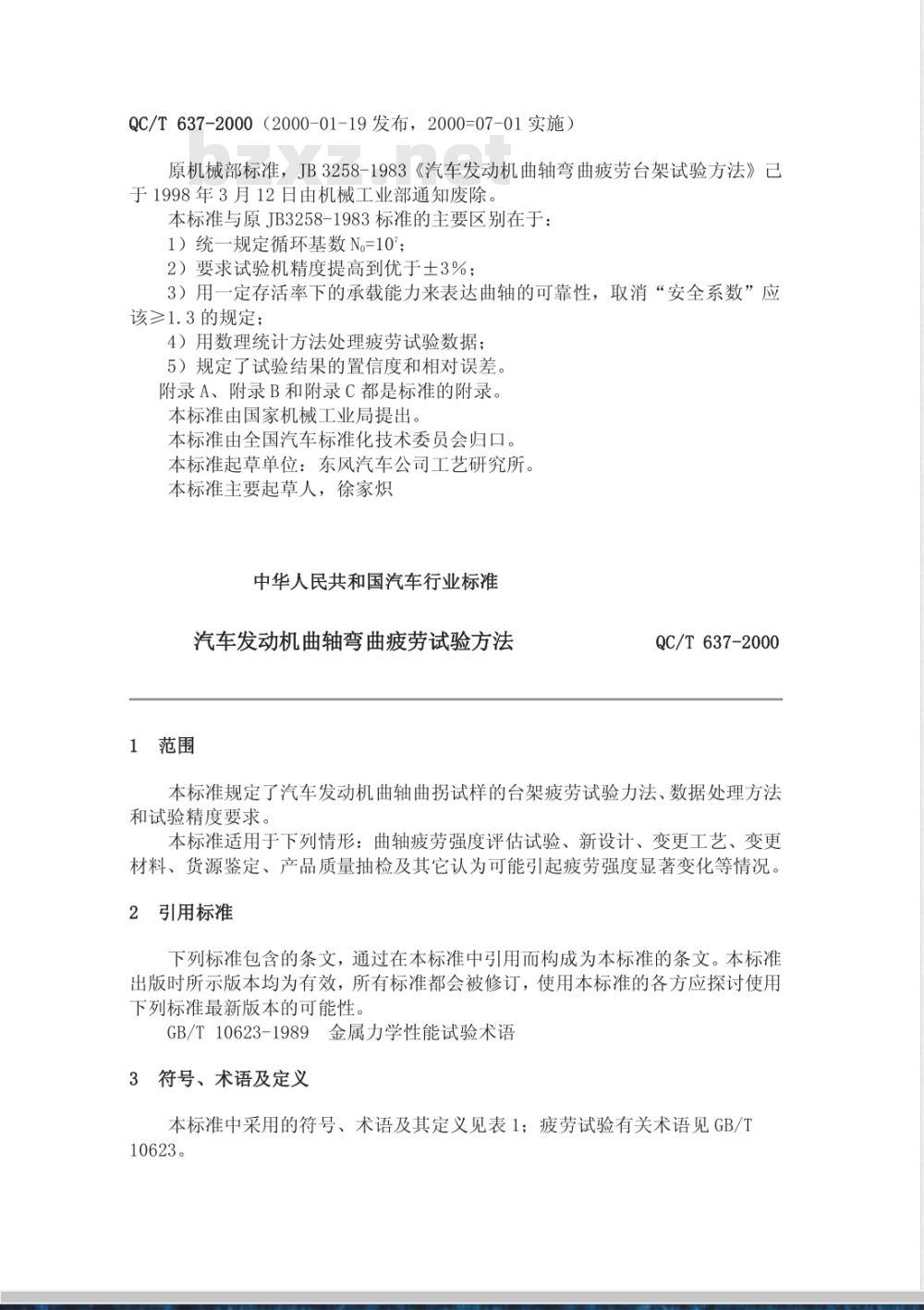
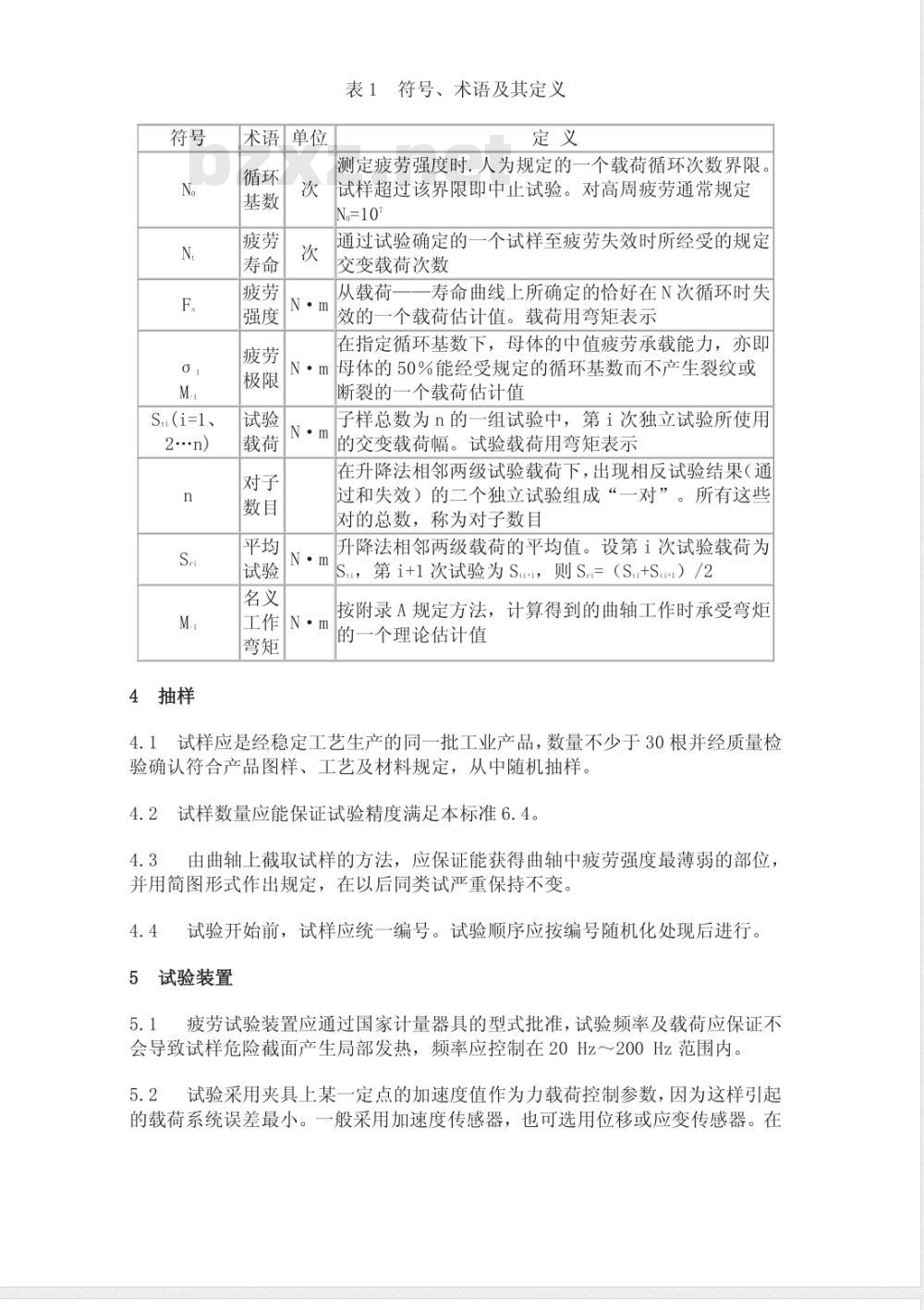
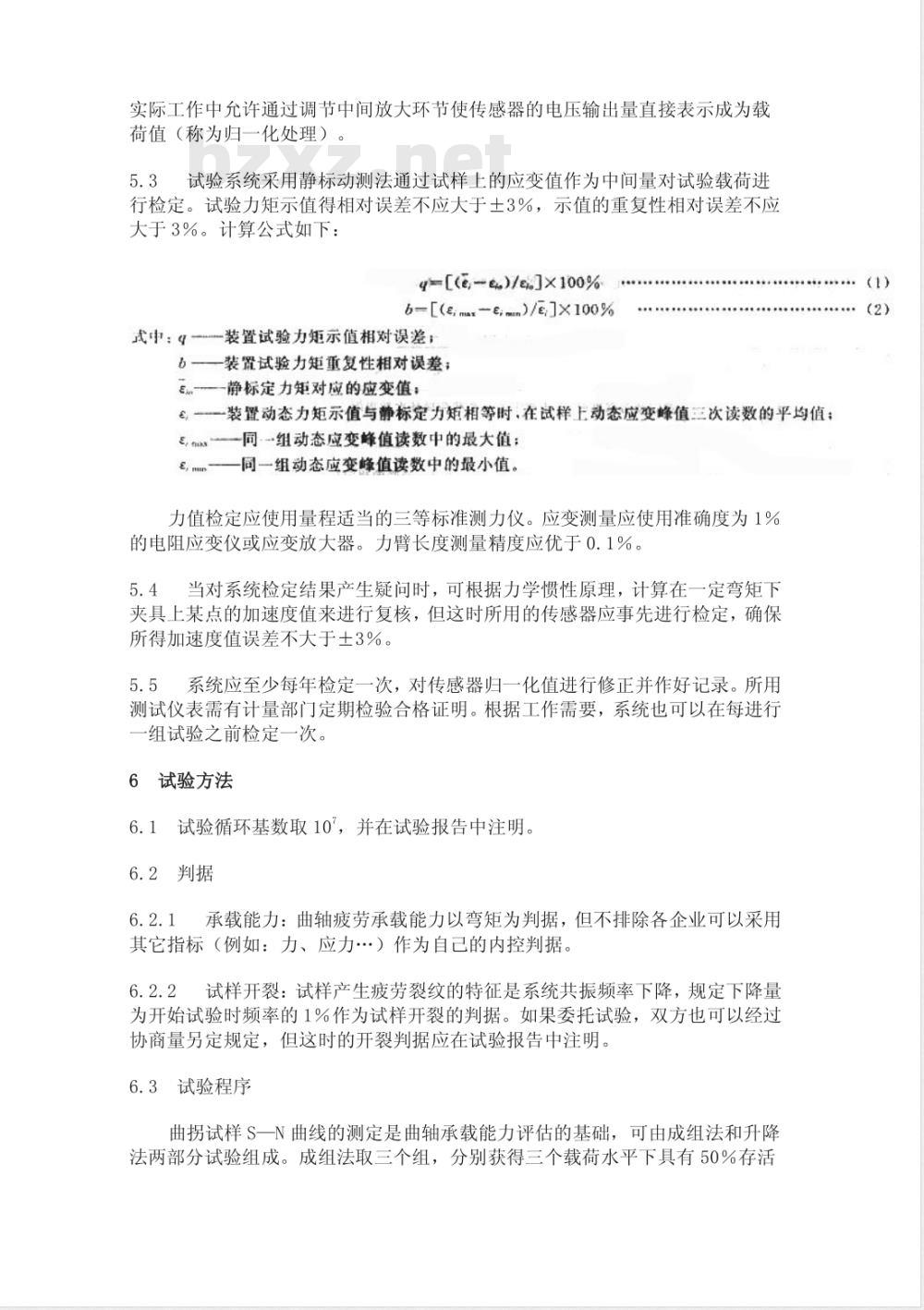
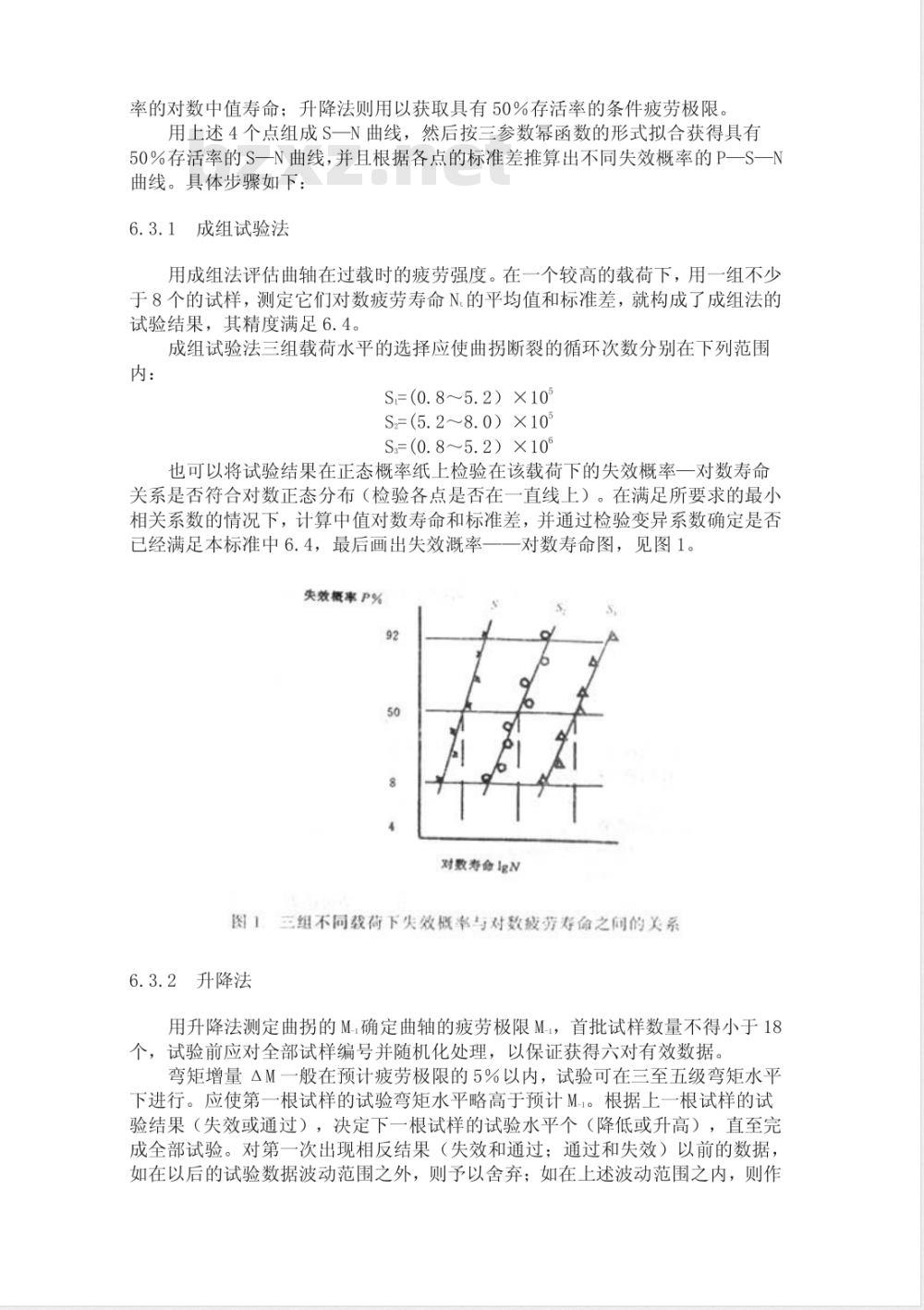
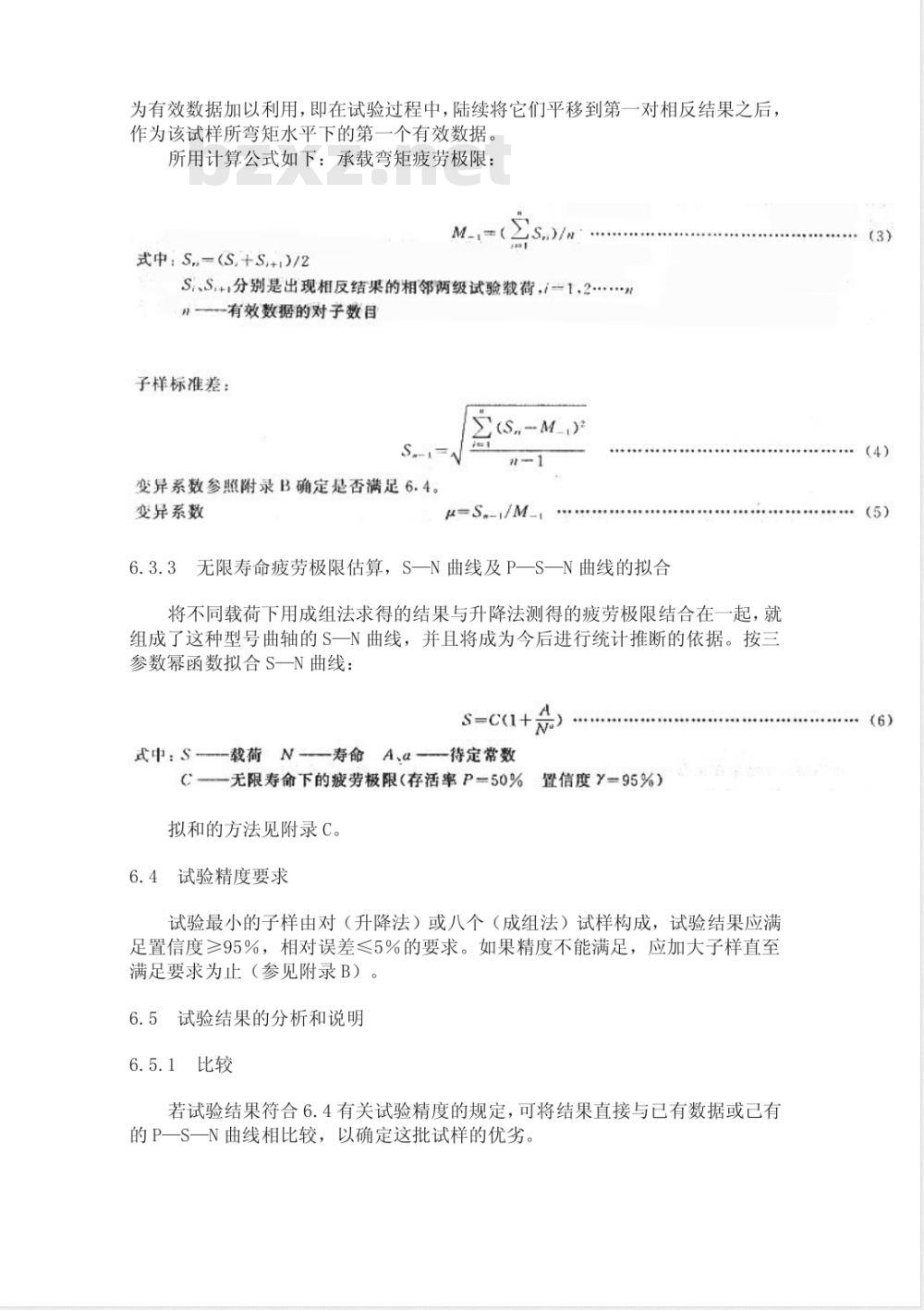
- 其它标准
- 上一篇: QC/T 636-2000 汽车电动玻璃升降器
- 下一篇: QC/T 638-2000 密封垫圈
- 热门标准
- 汽车行业标准(QC)
- QC/T29106-2014 汽车电线束技术条件
- QC/T882-2011 开口夹
- QC/T323-2007 汽车门锁和车门保持件
- QC/T1068-2017 电动汽车用异步驱动电机系统
- QC/T772-2006 汽车用柴油滤清器试验方法
- QC/T35-1992 汽车与挂车气压控制装置台架试验方法
- QC/T439-2013 摆臂式自装卸汽车
- QC/T853-2011 六角法兰面自排屑螺栓
- QC/T29102-92 汽车化油器质量分等
- QC/T824-2009 汽车用转速传感器
- QC/T875-2011 内六角花形盘头自钻自攻螺钉
- QC/T881-2011 塑料用焊接螺柱
- QC/T228.2-1997 摩托车和轻便摩托车操纵拉索钢丝绳
- QC/T932-2012 道路运输液体危险货物罐式车辆紧急切断阀
- QC/T29115-2013 摩托车和轻便摩托车产品质量检验规程
- 行业新闻
请牢记:“bzxz.net”即是“标准下载”四个汉字汉语拼音首字母与国际顶级域名“.net”的组合。 ©2009 标准下载网 www.bzxz.net 本站邮件:bzxznet@163.com
网站备案号:湘ICP备2023016450号-1
网站备案号:湘ICP备2023016450号-1