- 您的位置:
- 标准下载网 >>
- 标准分类 >>
- 机械行业标准(JB) >>
- JB/T 7425-1994 超硬磨具 技术条件

【机械行业标准(JB)】 超硬磨具 技术条件
本网站 发布时间:
2024-07-17 16:15:38
- JB/T7425-1994
- 现行
标准号:
JB/T 7425-1994
标准名称:
超硬磨具 技术条件
标准类别:
机械行业标准(JB)
标准状态:
现行-
发布日期:
1994-09-06 -
实施日期:
1995-07-01 出版语种:
简体中文下载格式:
.rar.pdf下载大小:
361.33 KB
替代情况:
原标准号GB 6409.1-1986采标情况:
非等效ГOCT16181-82

点击下载
标准简介:
标准下载解压密码:www.bzxz.net
本标准规定了超硬磨具的技术要求,试验方法,检验规则和标志、包装、运输及贮存。 JB/T 7425-1994 超硬磨具 技术条件 JB/T7425-1994

部分标准内容:
中华人民共和国机械行业标准
超硬磨具
1主题内容与适用范围
技术条件
JB/T7425
本标准规定了超硬磨具的技术要求,试验方法,验收规则和标志、包装、运输及贮存。本标准适用于树脂结合剂、金属结合剂和陶瓷结合剂人造金刚石或立方氮化硼砂轮、磨盘、油石和磨头。
2引用标准
形状和位置公差未注公差的规定GB 1184
GB 1801
公差与配合尺寸至500mm孔、轴公差带与配合GB6405~6408人造金刚石和立方氮化硼金刚石或立方氮化硼磨具形状代号、标记GB 6409.1
GB 6409. 2
GB 11272
金刚石或立方氮化硼砂轮
金刚石或立方氮化硼油石
JB/T3296
JB/T6355
金刚石磨边砂轮
金刚石简形砂轮
加工铁氧体用金刚石磨盘和砂轮JB/T6356
3技术要求
3.1般要求
3.1.1磨具所使用的超硬磨料,应符合GB6405~6408要求。3.1.2磨具形状和产品标记应符合GB6409.1要求。磨具尺寸应符合GB6409.2、GB11272、JB/T6355、JB/T6356和JB/T3296的要求。3.1.3磨具允许用树脂结合剂、金属结合剂或陶瓷结合剂,其代号应符合GB6409.1的要求。3.1.4磨具基体允许使用金属件和粉末压制件等。3.1.5磨具磨料层与基体之间允许有无磨料的过渡层。1
3.1.6磨具浓度应按25%、50%、75%、100%、125%、150%、175%或200%选择,并符合GB6409.1的规定。
3.2外观要求
3.2.1磨具工作表面不得有原始表皮(不包括不加工磨具)、发泡、氧化层和夹杂,且敲击不得有睡声。3.2.2基体表面应组织均匀、美观,不得有裂纹、毛刺和腐蚀凹坑等现象(如因校正产品形成的凹坑和痕迹,不按缺陷处理)。
3.2.3磨料层、过渡层与基体相互衔接处应均勾一致,不得有起层和裂纹。属于相互粘结的磨具,要牢固、端正和美观。
3.2.4磨具工作表面上的磨料颗粒应出露,且分布均匀。3.2.5磨具工作表面凹坑面积和数量按表1规定。中华人民共和国机械工业部1994-09-06批准1995-07-01实施
磨盘、磨头、油石
3.3边棱损坏
3.3.1砂轮(包括磨盘)
JB/T7425—94
寸,mm2
3.3.1.1沿径向和轴向测量,掉边均不得超过0.5mm。数
量,个/cm2
3.3.1.2砂轮厚度等于或小于10mm者,其掉边累计总长不得超过圆周长的十五分之-砂轮厚度大于10mm者,其掉边累计总长不得超过圆周长的十分之3. 3. 1. 3
3.3.1.4每处掉边的最大长度不得超过圆周长的六十分之一3.3.2下列砂轮形状不得有掉边:1A1R,1E6Q,14E6Q,14EE1,14E1,1DD1,4BT1,12A2/20,12A2/45°,12V1,6A9,11V9,12V9,12V2,1EE1V,1V9,2EEA1V,1DD6Y。3.3.3油石
3.3.3.1磨油石
磨料层部分边棱损坏,沿长、宽、高方向均不得超过0.5mm。基体部分边校损坏按表2规定。表2
沿宽、高方向
沿长方向
沿长方向
3.3.3.2带柄油石
宽度(W)3~6
宽度(W)>6
边棱损坏
掉边各处累计,总长度不得超过规定极限的2倍磨料层部分边棱损坏沿长、宽、高、弧和斜边方向均不得超过1mm。基体部分沿高方向,边棱损坏不得超过2mm。3.3.4切割砂轮
3.3.4.1切割砂轮的锯齿应高于基体端面,如果出现锯齿与基体端面平齐者,其数量不得多于5个,连续出现不得多于3个。
3.3.4.2切割砂轮沿径向断齿尺寸不得大于1mm,其数量不得多于5个,连续出现不得多于3个。3.4形位公差
3.4.1切割、薄片砂轮
3.4.2.无芯磨砂轮
直线度
1A1型、1A1R型、1A6Q型平面度按表3规定。表3
1A1型和9A1型轴向工作面直线度按表4规定。表4
60~100
>200~400
>100~150
3.4.3珩磨油石度按表5规定
宽度或厚度
3.4.4磨盘工作面平面度按表6规定。外
平面度
JB/T7425—94
>50~100
>400~600
磨盘的平行度按GB1184附表3中7级精度,其规定如表7。表7
平行度
>160~250
砂轮圆跳动按表8规定。
1E6Q.14E6Q.14EE1.14E1.1V9.1EE1VIDD1
1A1.14A1.1L1、4BT1、1FF1、1F16A2、11A2.12A2/20°12A2/45°12V1.6A9,11V9,12V9.12V2
9A1、1A1
磨边砂轮
无心磨砂轮
9A1,1A1
2EEA1V
D=125~200
D>200~500
D>500~750
2F2/1、2F2/2.2F2/3
>250~400
径向圆跳动
>400~~630
端面圆跳动
>100~250
>630~1000
斜边圈跳动
注:根据表8规定形状要求,砂轮外径D≥75mm的应进行圆跳动检验,不加工的砂轮不进行圆跳动检验,3.5基本尺寸极限偏差
3.5.1砂轮
3.5.1.1外径(D)极限偏差按表9规定。213
>30~50
>50~80
>80~120
>120~180
>180~250
JB/T 7425-94
限偏差
>250~315
>315~400
>400~500
>500~630
>630~800
2磨料层深度(X)、环宽(W)和厚度(U)基本尺寸极限偏差按表10规定。表10
X、W、U
极限偏差
3. 5. 1. 3
孔径(H)按H7规定:
>6~10
无心磨砂轮磨料层深度(X)极限偏差按表11规定。3.5.1.4
极限偏差
M(金属结合剂)
B(树脂结合剂)
3.5.1.5无心磨砂轮孔径(H)按H7规定6
3.5.1.6薄片砂轮基本尺寸(T、X、H)极限偏差按表12规定。表12
>6~10
3. 5. 1. 7
极限偏差
0.3~~0. 8
切割砂轮基本尺寸极限偏差按表13规定。表13
基本尺寸
磨盘基本尺寸极限偏差规定
极限偏差
极限偏差
>10~~15
>6~~10
粉末基体
>10~15
JB/T7425-94
磨料层深度(X)极限偏差按表10规定。孔径(H)按H9规定。
小砂轮及磨头基本尺寸极限偏差按表14规定。表14
>6~10
>10~18
3.5.3油石
极限偏差
>6~10
>10~18
>18~30
极限偏差
>3~6
极限偏差
3.5.3.1磨油石(HMA/1、HMA/2、HMH、2HMA)基本尺寸极限偏差按表15规定。表15
16~250
极限偏差
极限偏差
磨油石(HMA/S)基本尺寸极限偏差按表16规定。表16
】极限偏差
极限偏差
极限偏差
带柄油石基本尺寸极限偏差按表17规定。表17
极限偏差
基体粗糙度(R)按下列规定:
配合孔和支承端面粗糙度值R。不大于1.6μm。其余表面粗糙度值R。不大于3.2pm。极限偏差
极限偏差
极限偏差
极限偏差
极限偏差
极限偏差
3.7外径等于或大于100mm及每片质量等于或大于250g的金属、树脂和瓷结合剂平行系列砂轮(不包括薄片和切割砂轮),应进行静平衡检验或动态静平衡检验,其检验方法及不平衡值,按附录A(补充件)或附录B(补充件)规定。4试验方法
4.1一般要求检查
交检产品时,其施工文件应与产品及产品上的标志相符,并按一般要求(3.1.1-~3.1.6条)逐条以目力检查。
4.2外观检查
4.2.1·磨具工作表面上的原始表皮、发泡、氧化层和夹杂用目力查。4.2.2凹坑、裂纹、起层等均用带刻度的10倍放大镜检查。4.2.3磨料层、过渡层、基体(粉末基体)组织不均及磨料颗粒出露等外观要求均以目力检查。4.3边棱损坏
4.3.1砂轮沿周边、沿高度和沿直径方向,油石沿长、宽、高和弧等方向均用带刻度的10倍放大镜检215
JB/T7425—94
4.3.2切割砂轮断齿和端面缺陷均用精度0.02mm的游标卡尺检测。4.4形位公差
4.4.1平面度:将薄片砂轮、切割砂轮平放在平板上,用平尺和塞尺配合测量。4.4.2直线度:用刀口尺和塞尺测量。4.4.3圆跳动:将砂轮穿在芯轴上夹紧后,在圆跳动检查仪上用百分表检验。芯轴技术要求按GB1801公差带为g5配合公差要求,硬度要求不低于50HRC,表面粗糙度R值不大于0.80μm。
4.5基本尺寸
4.5.1外径、厚度及磨料层(深度、厚度和环宽)均用精度0.02mm的游标卡尺测量。4.5.2孔径用塞规、内径量表或内径千分尺测量。4.5.3角度(孤度)用角度尺或样板检查。4.5.4其他尺寸均用游标卡尺测量。4.5.5粗糙度以目力对照标准样块检查。4.6平衡检查
按本标准附录 A和附录 B检查。5验收规则
5.1产品必须按本标准技术要求检验,合格者附合格证。5.2使用单位收到产品后,按本标准和相关标准检验。5.3库存产品应定期进行自检,每年不得少于2次,一次性抽取数量每种不得少于5片。具体要求按附录D(参考件)规定。
6标志、包装、运输与贮存
6.1标志
6.1.1磨具标志
制造厂名、商标;
磨料牌号;
磨料粒度;
浓度代号;
结合剂代号;
f、,产品编号;
制造年、月。
无法标志者,只填写合格证。
磨具标志要字迹清晰、整洁、美观和牢固,同时应符合运输、贮存保管要求。6.1.2外包装标志:
制造厂名、商标;
产品名称;
安全标志;
厂广址。
6.1.3内包装内应附有合格证、说明书和装箱单等。合格证标志:
、产品型号:
磨料牌号;下载标准就来标准下载网
磨料粒度;
浓度代号:
结合剂代号;
规格尺寸;
检验年、月;
检验印章。
6.2包装
JB/T7425-94
6.2.1内包装:应根据产品规格尺寸和形状不同,应分别单装或多片装箱,箱内应填村软质材料,以筋串动碰坏,但包装要牢固、美观。6.2.2外包装应做到安全可靠,符合运输有关规定。6.2.3出口产品按合同要求。
6.3运输
产品装卸和搬运应按安全标志要求。6.4贮存
6.4.1产品人库后,应分类存放。6.4.2薄片砂轮多片存放时,应夹在表面平整光滑的金属圆板中间,以防变形。6.4.3产品存放处应通风干燥。
6.4.4产品存放期,树脂结合剂磨具为一年,金属和陶瓷结合剂磨具为二年,逾期产品,必须进行质量检验后方可使用。
A1准备
JB/T 7425-94
附录A
金刚石磨边砂轮动态静平衡检验方法(补充件)
A1.1仪器:BLWy-100B型闪光式动平衡机或同等性能的动平衡机。A1.2平衡检验用芯轴的技术要求A1.2.1轴颈、带轴、套砂轮的带锥度轴颈的同心度小于或等于0.005mm。A1.2.2硬度不低于50HRC,表面粗度R。值不大于0.40μm。A1.2.3套砂轮位置的轴头端面上应标上均分数为1、2、3、4…以确定不平衡相位。A1.2.4芯轴应预先在平衡机上将其平衡至最佳精度,即重心偏移量小于或等于0.001mm。A1.2.5芯轴与砂轮的总重量应大于平衡机可测重量的下限。A1.3按BLwy-100B型动平衡机的要求做好准备:A1. 3. 1
设备转数:2400r/min。
A1.3.2将平衡芯轴放置于V形槽上,套上传动带,调整垂直拉紧强度以使芯轴稳定旅转为宜。A1.3.3将各旋钮调整到以下位置:“左量”“右量”旋转指10”位置;a。
“左面”、“左面\旋转指“5”位置;“左”、“静”“右”旋转指“静”位置;“轻”、“重”旋转指“重”位置(按去重选择)。A1.3.4
砂轮在去重前后与芯轴的相对位置应保持不变,应该从相对180°的位置测两次。A1.3.5
通电预热1~2min。
A2操作
先开动电动机;
将“输人衰减”开关调至1档,若电表超过满刻度,可按\3”、“10”“30”“100”顺序衰减下去,使b.
指针处于“0\与满刻度之间;
调节频率调节”旋钮,使指针达最大值;c
旋亮闪光灯”移近砂轮,观察水平位置的数字,记下位置及电表读数,d
停机取下砂轮进行去重,直至达到和标准值相对应的衰减档数和电表读数。A3衰减档数和电表读数的确定
A3.1当首次检验同规格的一批砂轮时,第一片砂轮应平衡至本机最佳精度,即用闪光灯照射,字迹不清,且电表读数最小。
可按说明书中“工作物精度的测量方法”去测定这片砂轮的剩余不平衡值,若测定出剩余不平衡值的重心偏移小于或等于0.001mm时,即已达到本机最高精度。然后按式(A1)计算出与标准规定值相对应的加重质量。(Wr+W2)e
式中:G与标准允许值相对应加重质量g;W--砂轮质量-g,
W2芯轴质量gs
JB/T7425—94
e——标准规定的重心偏移量,mm;例如:金刚石磨边砂轮重心偏移量 e(标准) 0. 006 mm一加重位置的半径。
按砂轮规格自行选择,按算出的重量称取橡皮泥粘附于所选择的加重半径处;再按前述方法检验,此时闪光灯照射应清晰看见加重物位于水平位置。记下衰减档数及电表读数,此数即为与标准值允许相对应的档数及电表读数。
检验其砂轮时,若档数和电表读数小于该档数和电表读数,即表示重心偏移未超过标准允许值,砂轮为合格不需去重,若大于该档数及电表读数,可去重使其小于该值,即为合格。A3.2若第一次检验经去重后,闪光位置转移,这是去重之重量及位置未找准,允许在新的位置去重,但钻孔去重最多不得超过三处。为使去重位置准确,需正确调整“频率调节”旋钮,并力求准确地确定闪光水平位置。附录B
砂轮静平衡检验方法及不平衡数值(补充件)
B1本标准适用于外径等于或大于100mm及每片质量等于或大于250g的金属、树脂和陶瓷结合剂金刚石或立方氮化硼砂轮(包括电镀砂轮)。砂轮检验质量范围为0.250~50kg。所规定的不平衡数值仅指砂轮本身而与砂轮轴及安装中出现的平衡误差无关。B2不平衡:砂轮在旋转时由于砂轮的质量中心与它旋转中心不相重合而引起的振动。其造成原因是:
a。砂轮组织不均勾(图B1);
砂轮两个端面不平行(图B2)
孔径与外径不同心(图B3);
组装体质量不等或不对称(图B4)。图B1
B3放置砂轮周边某一选择位置为使其平衡而去重的质量,即为砂轮的静不平衡数值。B4按砂轮的单片质量不同,不平衡数值不应超过表B1的规定。图B4
砂轮质量
0.25~0.28
≥>0. 28~0. 31
>0. 31 ~0. 34
≥0. 34~0. 37
>0. 37~0. 40
≥0. 40~D. 45
>0. 45~0.50
>0. 50~0. 55
>0. 55~0. 60
>0. 60~0. 65
>0. 65~0. 70
>0.70~0.75
>0.75~0.80
>0. 80~0. 85
>0. 85~ 0. 90
>0. 90~0. 95
≥0. 95 ~~1. 00
>1. 00~1. 10
>1. 10~1. 20
>1. 20~1. 30
≥1.30~1. 40
>1.40~1.50
>1.50~1.60
>1. 60~1. 70
≥1. 70~~1. 80
>1.80~1.90
>1. 90~2. 00
>2. 00~2. 10
>2. 10~~2. 20
>2. 20~~2. 30
B5静平衡检验方法
B5.1测量装置
不平衡值
JB/T 7425--94
砂轮质量
>2. 30~~ 2. 40
>2. 40~~2. 50
>2. 50~2. 60
>2. 60 ~ 2. 70
>2. 70~2. 80
>2. 80~2. 90
≥ 2. 90~3. 00
>3. 00 ~~3. 50
>3. 50~4. 00
>4.00~4.50
>4. 50~5. 00
>5. 00~~5. 50
>5. 50~~6. 00
>6. 00~6. 50
>6. 50~7. 00
≥7. 00~7. 50
>7. 50~-8. 00
>8. 00~8. 50
>8. 50~9. 00
>9. 00~~9. 50
>9. 50~10. 00
>10. 00~11. 00
>11. 00~12. 00
≥12. 00~13. 00
≥13. 00~~14. 00
>14. 00~15. 00
>15. 00~16. 00
>16. 00~17. 00
>17. 00~18. 00
>18. 00~19. 00
不平衡值
砂轮质量
>19. 00~~20. 00
>20. 00~ 22. 00
22. 00~-23. 00
>23. 00~24. 00
>24. 00~25. 00
>25. 00~26. 00
>26, 00-~27. 00
>27. 00~ 28. 00
>28. 00~~ 29. 00
>29. 00-~30. 00
> 30. 00~31. 00
>31. 00~ 32. 00
>32. 00-- 33. 00
≥33. 0034. 00
≥34. 00~~35. 00
>35. 00~36. 00
>36. 00 -~ 37. 00
>37. 00~ 38. 00
>38. 00~39. 00
>39.00~40.00
>40. 00~41. 00
>41.00~42.00
>42.00~43.00
≥43. 00~44. 00
>44. 00-45. 00
>45. 00~46.00
46. 00~47. 00
≥47. 00~48. 00
>48.00~49.00
>49. 00~50. 00
不平衡值
静平衡检验在轴辊式平衡上进行。平衡器的两根钢轴直径应相等,其表面粗糙度R。值应不大于0.40μm,硬度大于或等于50HRC。两根轴应处于同一水平面上。检验用的芯轴表面粗糙度R,值应不大220
JB/T 7425-94
于0.80um,硬度大于或等于50HRC,并预先经过平衡。B5.2操作要点
将装有平衡轴的砂轮对称地置于平衡器的钢轴之间,并使平衡轴中心线与水平钢轴垂直。缓慢地转动砂轮,当砂轮自动停止时,在砂轮的适当位置贴上橡皮泥,使其重心靠近圆心,然后使砂轮转动90°,如砂轮在这个荷重作用下,可停于任意位置,则该荷重即为该砂轮的静不平衡数值。B5.3砂轮不平衡值超差去重钻孔规定取下橡皮泥称重,超过表B1对应不平衡数值者,应在贴橡皮泥处的对称基体端面距磨料层10~20mm处钻孔去重,所去质量应等于或小于橡皮泥重量。去重钻孔要求:
a。砂轮外径D≤400mm、厚度T≤40mm,根据静不平衡数值大小,应选用直径7~12mm的钻头取重;外径D>400mm,厚度T>40mm,应视其静不平衡数值大小,选用直径10~15mm的钻头取重。
取重钻孔部位处与基体铆钉、螺孔等不当部位重合时,可另选适当部位钻孔去重。附录C
超硬磨具标准有关技术术语说明(参考件)
C1夹杂:除结合剂(包括填料)和超硬材料之外,用目力能分辨出来的其他异物均为夹杂。C2凹坑:磨料层表面的凹陷部分,称为凹坑。因磨加工,造成磨料层表面磨料颗粒脱落,形成的凹坑,或基体因取重钻孔等,均不作凹坑处理。C3掉边:因碰撞、撞击外力作用下,造成磨料层边棱损坏,称为掉边。因磨加工,造成磨料层表面磨料颗粒脱落,形成的边棱缺口,不按边棱缺陷处理。C4原始表皮:未经加工的磨料层表皮,称为原始表皮。C5发泡:磨料层表面出现的鼓泡,称为发泡。C6氧化:金属结合剂磨具经烧结后,磨料层表面无光泽和异色现象。附录D
产品质量抽查办法及评定规定
(参考件)
D1产品质量抽查办法
D1.1库存产品应定期进行抽样检验,·次性抽取的数量,每种产品不得少于5片。D1.2产品检验所用的量具、检具、检测仪器和设备等,应具备有效合格证。D1.3产品技术缺陷类别应按表D1规定。221
重缺陷
一般缺陷
轻缺陷
JB/T7425-94
径向或端面圆跳动(指工作面方向)、直线度、平面度、平行度、挠度、组织不均、发泡、氧化、裂纹、睡声、不平衡、边棱损坏(指本标准中3.3.2条)和孔径偏差等径向或端面圆跳动(指非工作面方向)、磨料层(X、W、U)基本尺寸极限偏差、凹坑、边被摄坏(指本标准中3.3.1条)和断齿(包括端向脱层齿)非主要基本尺寸(T、TI、E、K、J、L、L2等)极限偏差和基体外观缺陷等D1.4抽样产品判定等级按表D2规定。表 D2
重缺陷
一般缺陷
轻缺陷
D2产品质量等级的评定
合格品
优等品
D2.1产品全面达到表D1、表D2及质量分等标准的各项要求,方能判定相应的质量等级。判定时,先按表D1、表D2及产品质量分等标准中不同等级的质量要求,对每项检查结果做出单项结论(合格项、一等项,优等项),然后按单项结论综合评定每份试样质量等级。如有些项达到较高等级,有些项达到较低等级,在综合评定时应按表D2规定。例如:在十项考核项中,有二项一般缺陷或有三项轻缺陷确定不合格项,其他各项均达到合格项以上的水平时,该试样仍确定为“不合格品”,有一项一般缺陷或有二项轻缺陷确定不合格项,其他各项均达到合格项或以上水平时,该试样确定为“合格品”;该试样有一项轻缺陷确定为不合格项,其他各项达到一等品项或以上项水平时,该试样确定为“一等品”,十项均达到优等品项,该试样才能判定为“优等品”。D2.2成品批产品质量等级评定是在抽样判定的基础上,按其试样抽查合格率、一等品率、优等品率来评定批(或规格段)等级,按如下公式计算:试样合格品数、
试样合格品率——
X100%...........
抽样试样数
试样等品数×100%…
试样一等品率—!
抽样试样数
试样优等品数,
试样优等品率=
X100%:
抽样试样数
.... (D2)
......(D3)
当试样合格品率≥90%,该抽检批的产品可判为合格品。试样合格率达100%,其试样一、优等品率≥70%时,该抽样批产品可判为一等品,当试样优等品率≥70%时,该抽样批产品可为优等品。附加说明:
本标准由全国磨料磨具标准化技术委员会提出。本标雅由郑州磨料磨具磨削研究所归口。本标准由第六砂轮厂负责起草。本标准主要起草人刘建邦、李黔湘、范松振。222
小提示:此标准内容仅展示完整标准里的部分截取内容,若需要完整标准请到上方自行免费下载完整标准文档。
超硬磨具
1主题内容与适用范围
技术条件
JB/T7425
本标准规定了超硬磨具的技术要求,试验方法,验收规则和标志、包装、运输及贮存。本标准适用于树脂结合剂、金属结合剂和陶瓷结合剂人造金刚石或立方氮化硼砂轮、磨盘、油石和磨头。
2引用标准
形状和位置公差未注公差的规定GB 1184
GB 1801
公差与配合尺寸至500mm孔、轴公差带与配合GB6405~6408人造金刚石和立方氮化硼金刚石或立方氮化硼磨具形状代号、标记GB 6409.1
GB 6409. 2
GB 11272
金刚石或立方氮化硼砂轮
金刚石或立方氮化硼油石
JB/T3296
JB/T6355
金刚石磨边砂轮
金刚石简形砂轮
加工铁氧体用金刚石磨盘和砂轮JB/T6356
3技术要求
3.1般要求
3.1.1磨具所使用的超硬磨料,应符合GB6405~6408要求。3.1.2磨具形状和产品标记应符合GB6409.1要求。磨具尺寸应符合GB6409.2、GB11272、JB/T6355、JB/T6356和JB/T3296的要求。3.1.3磨具允许用树脂结合剂、金属结合剂或陶瓷结合剂,其代号应符合GB6409.1的要求。3.1.4磨具基体允许使用金属件和粉末压制件等。3.1.5磨具磨料层与基体之间允许有无磨料的过渡层。1
3.1.6磨具浓度应按25%、50%、75%、100%、125%、150%、175%或200%选择,并符合GB6409.1的规定。
3.2外观要求
3.2.1磨具工作表面不得有原始表皮(不包括不加工磨具)、发泡、氧化层和夹杂,且敲击不得有睡声。3.2.2基体表面应组织均匀、美观,不得有裂纹、毛刺和腐蚀凹坑等现象(如因校正产品形成的凹坑和痕迹,不按缺陷处理)。
3.2.3磨料层、过渡层与基体相互衔接处应均勾一致,不得有起层和裂纹。属于相互粘结的磨具,要牢固、端正和美观。
3.2.4磨具工作表面上的磨料颗粒应出露,且分布均匀。3.2.5磨具工作表面凹坑面积和数量按表1规定。中华人民共和国机械工业部1994-09-06批准1995-07-01实施
磨盘、磨头、油石
3.3边棱损坏
3.3.1砂轮(包括磨盘)
JB/T7425—94
寸,mm2
3.3.1.1沿径向和轴向测量,掉边均不得超过0.5mm。数
量,个/cm2
3.3.1.2砂轮厚度等于或小于10mm者,其掉边累计总长不得超过圆周长的十五分之-砂轮厚度大于10mm者,其掉边累计总长不得超过圆周长的十分之3. 3. 1. 3
3.3.1.4每处掉边的最大长度不得超过圆周长的六十分之一3.3.2下列砂轮形状不得有掉边:1A1R,1E6Q,14E6Q,14EE1,14E1,1DD1,4BT1,12A2/20,12A2/45°,12V1,6A9,11V9,12V9,12V2,1EE1V,1V9,2EEA1V,1DD6Y。3.3.3油石
3.3.3.1磨油石
磨料层部分边棱损坏,沿长、宽、高方向均不得超过0.5mm。基体部分边校损坏按表2规定。表2
沿宽、高方向
沿长方向
沿长方向
3.3.3.2带柄油石
宽度(W)3~6
宽度(W)>6
边棱损坏
掉边各处累计,总长度不得超过规定极限的2倍磨料层部分边棱损坏沿长、宽、高、弧和斜边方向均不得超过1mm。基体部分沿高方向,边棱损坏不得超过2mm。3.3.4切割砂轮
3.3.4.1切割砂轮的锯齿应高于基体端面,如果出现锯齿与基体端面平齐者,其数量不得多于5个,连续出现不得多于3个。
3.3.4.2切割砂轮沿径向断齿尺寸不得大于1mm,其数量不得多于5个,连续出现不得多于3个。3.4形位公差
3.4.1切割、薄片砂轮
3.4.2.无芯磨砂轮
直线度
1A1型、1A1R型、1A6Q型平面度按表3规定。表3
1A1型和9A1型轴向工作面直线度按表4规定。表4
60~100
>200~400
>100~150
3.4.3珩磨油石度按表5规定
宽度或厚度
3.4.4磨盘工作面平面度按表6规定。外
平面度
JB/T7425—94
>50~100
>400~600
磨盘的平行度按GB1184附表3中7级精度,其规定如表7。表7
平行度
>160~250
砂轮圆跳动按表8规定。
1E6Q.14E6Q.14EE1.14E1.1V9.1EE1VIDD1
1A1.14A1.1L1、4BT1、1FF1、1F16A2、11A2.12A2/20°12A2/45°12V1.6A9,11V9,12V9.12V2
9A1、1A1
磨边砂轮
无心磨砂轮
9A1,1A1
2EEA1V
D=125~200
D>200~500
D>500~750
2F2/1、2F2/2.2F2/3
>250~400
径向圆跳动
>400~~630
端面圆跳动
>100~250
>630~1000
斜边圈跳动
注:根据表8规定形状要求,砂轮外径D≥75mm的应进行圆跳动检验,不加工的砂轮不进行圆跳动检验,3.5基本尺寸极限偏差
3.5.1砂轮
3.5.1.1外径(D)极限偏差按表9规定。213
>30~50
>50~80
>80~120
>120~180
>180~250
JB/T 7425-94
限偏差
>250~315
>315~400
>400~500
>500~630
>630~800
2磨料层深度(X)、环宽(W)和厚度(U)基本尺寸极限偏差按表10规定。表10
X、W、U
极限偏差
3. 5. 1. 3
孔径(H)按H7规定:
>6~10
无心磨砂轮磨料层深度(X)极限偏差按表11规定。3.5.1.4
极限偏差
M(金属结合剂)
B(树脂结合剂)
3.5.1.5无心磨砂轮孔径(H)按H7规定6
3.5.1.6薄片砂轮基本尺寸(T、X、H)极限偏差按表12规定。表12
>6~10
3. 5. 1. 7
极限偏差
0.3~~0. 8
切割砂轮基本尺寸极限偏差按表13规定。表13
基本尺寸
磨盘基本尺寸极限偏差规定
极限偏差
极限偏差
>10~~15
>6~~10
粉末基体
>10~15
JB/T7425-94
磨料层深度(X)极限偏差按表10规定。孔径(H)按H9规定。
小砂轮及磨头基本尺寸极限偏差按表14规定。表14
>6~10
>10~18
3.5.3油石
极限偏差
>6~10
>10~18
>18~30
极限偏差
>3~6
极限偏差
3.5.3.1磨油石(HMA/1、HMA/2、HMH、2HMA)基本尺寸极限偏差按表15规定。表15
16~250
极限偏差
极限偏差
磨油石(HMA/S)基本尺寸极限偏差按表16规定。表16
】极限偏差
极限偏差
极限偏差
带柄油石基本尺寸极限偏差按表17规定。表17
极限偏差
基体粗糙度(R)按下列规定:
配合孔和支承端面粗糙度值R。不大于1.6μm。其余表面粗糙度值R。不大于3.2pm。极限偏差
极限偏差
极限偏差
极限偏差
极限偏差
极限偏差
3.7外径等于或大于100mm及每片质量等于或大于250g的金属、树脂和瓷结合剂平行系列砂轮(不包括薄片和切割砂轮),应进行静平衡检验或动态静平衡检验,其检验方法及不平衡值,按附录A(补充件)或附录B(补充件)规定。4试验方法
4.1一般要求检查
交检产品时,其施工文件应与产品及产品上的标志相符,并按一般要求(3.1.1-~3.1.6条)逐条以目力检查。
4.2外观检查
4.2.1·磨具工作表面上的原始表皮、发泡、氧化层和夹杂用目力查。4.2.2凹坑、裂纹、起层等均用带刻度的10倍放大镜检查。4.2.3磨料层、过渡层、基体(粉末基体)组织不均及磨料颗粒出露等外观要求均以目力检查。4.3边棱损坏
4.3.1砂轮沿周边、沿高度和沿直径方向,油石沿长、宽、高和弧等方向均用带刻度的10倍放大镜检215
JB/T7425—94
4.3.2切割砂轮断齿和端面缺陷均用精度0.02mm的游标卡尺检测。4.4形位公差
4.4.1平面度:将薄片砂轮、切割砂轮平放在平板上,用平尺和塞尺配合测量。4.4.2直线度:用刀口尺和塞尺测量。4.4.3圆跳动:将砂轮穿在芯轴上夹紧后,在圆跳动检查仪上用百分表检验。芯轴技术要求按GB1801公差带为g5配合公差要求,硬度要求不低于50HRC,表面粗糙度R值不大于0.80μm。
4.5基本尺寸
4.5.1外径、厚度及磨料层(深度、厚度和环宽)均用精度0.02mm的游标卡尺测量。4.5.2孔径用塞规、内径量表或内径千分尺测量。4.5.3角度(孤度)用角度尺或样板检查。4.5.4其他尺寸均用游标卡尺测量。4.5.5粗糙度以目力对照标准样块检查。4.6平衡检查
按本标准附录 A和附录 B检查。5验收规则
5.1产品必须按本标准技术要求检验,合格者附合格证。5.2使用单位收到产品后,按本标准和相关标准检验。5.3库存产品应定期进行自检,每年不得少于2次,一次性抽取数量每种不得少于5片。具体要求按附录D(参考件)规定。
6标志、包装、运输与贮存
6.1标志
6.1.1磨具标志
制造厂名、商标;
磨料牌号;
磨料粒度;
浓度代号;
结合剂代号;
f、,产品编号;
制造年、月。
无法标志者,只填写合格证。
磨具标志要字迹清晰、整洁、美观和牢固,同时应符合运输、贮存保管要求。6.1.2外包装标志:
制造厂名、商标;
产品名称;
安全标志;
厂广址。
6.1.3内包装内应附有合格证、说明书和装箱单等。合格证标志:
、产品型号:
磨料牌号;下载标准就来标准下载网
磨料粒度;
浓度代号:
结合剂代号;
规格尺寸;
检验年、月;
检验印章。
6.2包装
JB/T7425-94
6.2.1内包装:应根据产品规格尺寸和形状不同,应分别单装或多片装箱,箱内应填村软质材料,以筋串动碰坏,但包装要牢固、美观。6.2.2外包装应做到安全可靠,符合运输有关规定。6.2.3出口产品按合同要求。
6.3运输
产品装卸和搬运应按安全标志要求。6.4贮存
6.4.1产品人库后,应分类存放。6.4.2薄片砂轮多片存放时,应夹在表面平整光滑的金属圆板中间,以防变形。6.4.3产品存放处应通风干燥。
6.4.4产品存放期,树脂结合剂磨具为一年,金属和陶瓷结合剂磨具为二年,逾期产品,必须进行质量检验后方可使用。
A1准备
JB/T 7425-94
附录A
金刚石磨边砂轮动态静平衡检验方法(补充件)
A1.1仪器:BLWy-100B型闪光式动平衡机或同等性能的动平衡机。A1.2平衡检验用芯轴的技术要求A1.2.1轴颈、带轴、套砂轮的带锥度轴颈的同心度小于或等于0.005mm。A1.2.2硬度不低于50HRC,表面粗度R。值不大于0.40μm。A1.2.3套砂轮位置的轴头端面上应标上均分数为1、2、3、4…以确定不平衡相位。A1.2.4芯轴应预先在平衡机上将其平衡至最佳精度,即重心偏移量小于或等于0.001mm。A1.2.5芯轴与砂轮的总重量应大于平衡机可测重量的下限。A1.3按BLwy-100B型动平衡机的要求做好准备:A1. 3. 1
设备转数:2400r/min。
A1.3.2将平衡芯轴放置于V形槽上,套上传动带,调整垂直拉紧强度以使芯轴稳定旅转为宜。A1.3.3将各旋钮调整到以下位置:“左量”“右量”旋转指10”位置;a。
“左面”、“左面\旋转指“5”位置;“左”、“静”“右”旋转指“静”位置;“轻”、“重”旋转指“重”位置(按去重选择)。A1.3.4
砂轮在去重前后与芯轴的相对位置应保持不变,应该从相对180°的位置测两次。A1.3.5
通电预热1~2min。
A2操作
先开动电动机;
将“输人衰减”开关调至1档,若电表超过满刻度,可按\3”、“10”“30”“100”顺序衰减下去,使b.
指针处于“0\与满刻度之间;
调节频率调节”旋钮,使指针达最大值;c
旋亮闪光灯”移近砂轮,观察水平位置的数字,记下位置及电表读数,d
停机取下砂轮进行去重,直至达到和标准值相对应的衰减档数和电表读数。A3衰减档数和电表读数的确定
A3.1当首次检验同规格的一批砂轮时,第一片砂轮应平衡至本机最佳精度,即用闪光灯照射,字迹不清,且电表读数最小。
可按说明书中“工作物精度的测量方法”去测定这片砂轮的剩余不平衡值,若测定出剩余不平衡值的重心偏移小于或等于0.001mm时,即已达到本机最高精度。然后按式(A1)计算出与标准规定值相对应的加重质量。(Wr+W2)e
式中:G与标准允许值相对应加重质量g;W--砂轮质量-g,
W2芯轴质量gs
JB/T7425—94
e——标准规定的重心偏移量,mm;例如:金刚石磨边砂轮重心偏移量 e(标准) 0. 006 mm一加重位置的半径。
按砂轮规格自行选择,按算出的重量称取橡皮泥粘附于所选择的加重半径处;再按前述方法检验,此时闪光灯照射应清晰看见加重物位于水平位置。记下衰减档数及电表读数,此数即为与标准值允许相对应的档数及电表读数。
检验其砂轮时,若档数和电表读数小于该档数和电表读数,即表示重心偏移未超过标准允许值,砂轮为合格不需去重,若大于该档数及电表读数,可去重使其小于该值,即为合格。A3.2若第一次检验经去重后,闪光位置转移,这是去重之重量及位置未找准,允许在新的位置去重,但钻孔去重最多不得超过三处。为使去重位置准确,需正确调整“频率调节”旋钮,并力求准确地确定闪光水平位置。附录B
砂轮静平衡检验方法及不平衡数值(补充件)
B1本标准适用于外径等于或大于100mm及每片质量等于或大于250g的金属、树脂和陶瓷结合剂金刚石或立方氮化硼砂轮(包括电镀砂轮)。砂轮检验质量范围为0.250~50kg。所规定的不平衡数值仅指砂轮本身而与砂轮轴及安装中出现的平衡误差无关。B2不平衡:砂轮在旋转时由于砂轮的质量中心与它旋转中心不相重合而引起的振动。其造成原因是:
a。砂轮组织不均勾(图B1);
砂轮两个端面不平行(图B2)
孔径与外径不同心(图B3);
组装体质量不等或不对称(图B4)。图B1
B3放置砂轮周边某一选择位置为使其平衡而去重的质量,即为砂轮的静不平衡数值。B4按砂轮的单片质量不同,不平衡数值不应超过表B1的规定。图B4
砂轮质量
0.25~0.28
≥>0. 28~0. 31
>0. 31 ~0. 34
≥0. 34~0. 37
>0. 37~0. 40
≥0. 40~D. 45
>0. 45~0.50
>0. 50~0. 55
>0. 55~0. 60
>0. 60~0. 65
>0. 65~0. 70
>0.70~0.75
>0.75~0.80
>0. 80~0. 85
>0. 85~ 0. 90
>0. 90~0. 95
≥0. 95 ~~1. 00
>1. 00~1. 10
>1. 10~1. 20
>1. 20~1. 30
≥1.30~1. 40
>1.40~1.50
>1.50~1.60
>1. 60~1. 70
≥1. 70~~1. 80
>1.80~1.90
>1. 90~2. 00
>2. 00~2. 10
>2. 10~~2. 20
>2. 20~~2. 30
B5静平衡检验方法
B5.1测量装置
不平衡值
JB/T 7425--94
砂轮质量
>2. 30~~ 2. 40
>2. 40~~2. 50
>2. 50~2. 60
>2. 60 ~ 2. 70
>2. 70~2. 80
>2. 80~2. 90
≥ 2. 90~3. 00
>3. 00 ~~3. 50
>3. 50~4. 00
>4.00~4.50
>4. 50~5. 00
>5. 00~~5. 50
>5. 50~~6. 00
>6. 00~6. 50
>6. 50~7. 00
≥7. 00~7. 50
>7. 50~-8. 00
>8. 00~8. 50
>8. 50~9. 00
>9. 00~~9. 50
>9. 50~10. 00
>10. 00~11. 00
>11. 00~12. 00
≥12. 00~13. 00
≥13. 00~~14. 00
>14. 00~15. 00
>15. 00~16. 00
>16. 00~17. 00
>17. 00~18. 00
>18. 00~19. 00
不平衡值
砂轮质量
>19. 00~~20. 00
>20. 00~ 22. 00
22. 00~-23. 00
>23. 00~24. 00
>24. 00~25. 00
>25. 00~26. 00
>26, 00-~27. 00
>27. 00~ 28. 00
>28. 00~~ 29. 00
>29. 00-~30. 00
> 30. 00~31. 00
>31. 00~ 32. 00
>32. 00-- 33. 00
≥33. 0034. 00
≥34. 00~~35. 00
>35. 00~36. 00
>36. 00 -~ 37. 00
>37. 00~ 38. 00
>38. 00~39. 00
>39.00~40.00
>40. 00~41. 00
>41.00~42.00
>42.00~43.00
≥43. 00~44. 00
>44. 00-45. 00
>45. 00~46.00
46. 00~47. 00
≥47. 00~48. 00
>48.00~49.00
>49. 00~50. 00
不平衡值
静平衡检验在轴辊式平衡上进行。平衡器的两根钢轴直径应相等,其表面粗糙度R。值应不大于0.40μm,硬度大于或等于50HRC。两根轴应处于同一水平面上。检验用的芯轴表面粗糙度R,值应不大220
JB/T 7425-94
于0.80um,硬度大于或等于50HRC,并预先经过平衡。B5.2操作要点
将装有平衡轴的砂轮对称地置于平衡器的钢轴之间,并使平衡轴中心线与水平钢轴垂直。缓慢地转动砂轮,当砂轮自动停止时,在砂轮的适当位置贴上橡皮泥,使其重心靠近圆心,然后使砂轮转动90°,如砂轮在这个荷重作用下,可停于任意位置,则该荷重即为该砂轮的静不平衡数值。B5.3砂轮不平衡值超差去重钻孔规定取下橡皮泥称重,超过表B1对应不平衡数值者,应在贴橡皮泥处的对称基体端面距磨料层10~20mm处钻孔去重,所去质量应等于或小于橡皮泥重量。去重钻孔要求:
a。砂轮外径D≤400mm、厚度T≤40mm,根据静不平衡数值大小,应选用直径7~12mm的钻头取重;外径D>400mm,厚度T>40mm,应视其静不平衡数值大小,选用直径10~15mm的钻头取重。
取重钻孔部位处与基体铆钉、螺孔等不当部位重合时,可另选适当部位钻孔去重。附录C
超硬磨具标准有关技术术语说明(参考件)
C1夹杂:除结合剂(包括填料)和超硬材料之外,用目力能分辨出来的其他异物均为夹杂。C2凹坑:磨料层表面的凹陷部分,称为凹坑。因磨加工,造成磨料层表面磨料颗粒脱落,形成的凹坑,或基体因取重钻孔等,均不作凹坑处理。C3掉边:因碰撞、撞击外力作用下,造成磨料层边棱损坏,称为掉边。因磨加工,造成磨料层表面磨料颗粒脱落,形成的边棱缺口,不按边棱缺陷处理。C4原始表皮:未经加工的磨料层表皮,称为原始表皮。C5发泡:磨料层表面出现的鼓泡,称为发泡。C6氧化:金属结合剂磨具经烧结后,磨料层表面无光泽和异色现象。附录D
产品质量抽查办法及评定规定
(参考件)
D1产品质量抽查办法
D1.1库存产品应定期进行抽样检验,·次性抽取的数量,每种产品不得少于5片。D1.2产品检验所用的量具、检具、检测仪器和设备等,应具备有效合格证。D1.3产品技术缺陷类别应按表D1规定。221
重缺陷
一般缺陷
轻缺陷
JB/T7425-94
径向或端面圆跳动(指工作面方向)、直线度、平面度、平行度、挠度、组织不均、发泡、氧化、裂纹、睡声、不平衡、边棱损坏(指本标准中3.3.2条)和孔径偏差等径向或端面圆跳动(指非工作面方向)、磨料层(X、W、U)基本尺寸极限偏差、凹坑、边被摄坏(指本标准中3.3.1条)和断齿(包括端向脱层齿)非主要基本尺寸(T、TI、E、K、J、L、L2等)极限偏差和基体外观缺陷等D1.4抽样产品判定等级按表D2规定。表 D2
重缺陷
一般缺陷
轻缺陷
D2产品质量等级的评定
合格品
优等品
D2.1产品全面达到表D1、表D2及质量分等标准的各项要求,方能判定相应的质量等级。判定时,先按表D1、表D2及产品质量分等标准中不同等级的质量要求,对每项检查结果做出单项结论(合格项、一等项,优等项),然后按单项结论综合评定每份试样质量等级。如有些项达到较高等级,有些项达到较低等级,在综合评定时应按表D2规定。例如:在十项考核项中,有二项一般缺陷或有三项轻缺陷确定不合格项,其他各项均达到合格项以上的水平时,该试样仍确定为“不合格品”,有一项一般缺陷或有二项轻缺陷确定不合格项,其他各项均达到合格项或以上水平时,该试样确定为“合格品”;该试样有一项轻缺陷确定为不合格项,其他各项达到一等品项或以上项水平时,该试样确定为“一等品”,十项均达到优等品项,该试样才能判定为“优等品”。D2.2成品批产品质量等级评定是在抽样判定的基础上,按其试样抽查合格率、一等品率、优等品率来评定批(或规格段)等级,按如下公式计算:试样合格品数、
试样合格品率——
X100%...........
抽样试样数
试样等品数×100%…
试样一等品率—!
抽样试样数
试样优等品数,
试样优等品率=
X100%:
抽样试样数
.... (D2)
......(D3)
当试样合格品率≥90%,该抽检批的产品可判为合格品。试样合格率达100%,其试样一、优等品率≥70%时,该抽样批产品可判为一等品,当试样优等品率≥70%时,该抽样批产品可为优等品。附加说明:
本标准由全国磨料磨具标准化技术委员会提出。本标雅由郑州磨料磨具磨削研究所归口。本标准由第六砂轮厂负责起草。本标准主要起草人刘建邦、李黔湘、范松振。222
小提示:此标准内容仅展示完整标准里的部分截取内容,若需要完整标准请到上方自行免费下载完整标准文档。

标准图片预览:
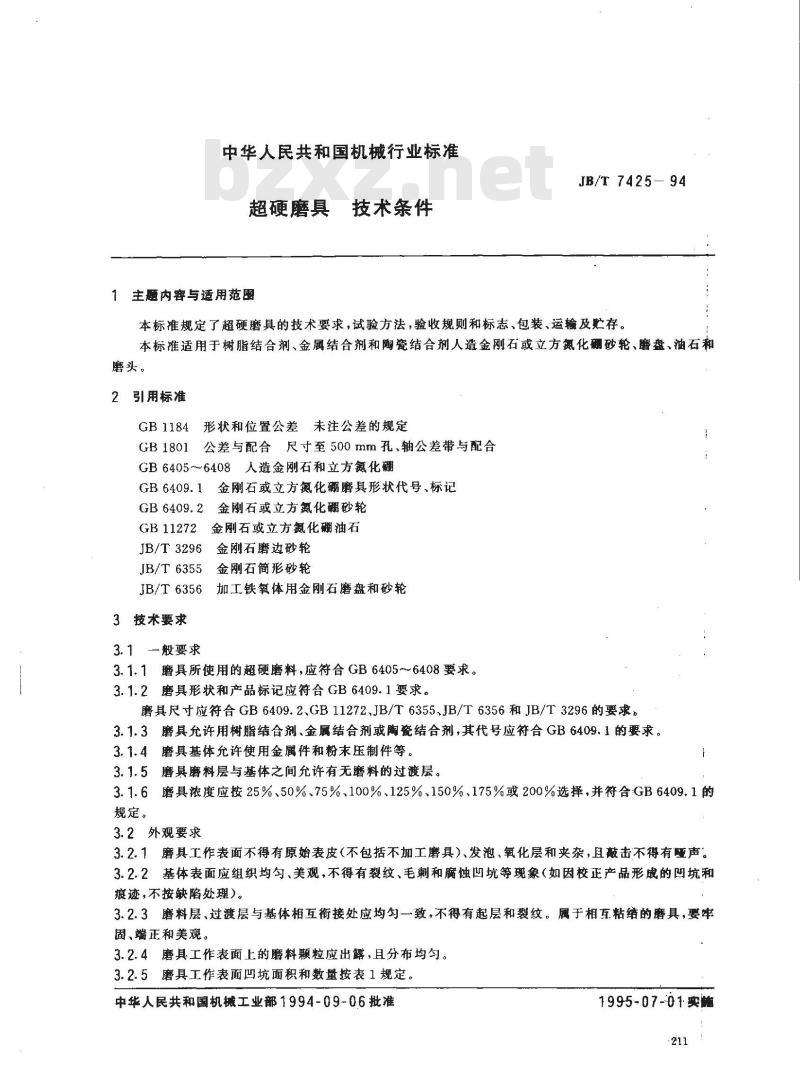
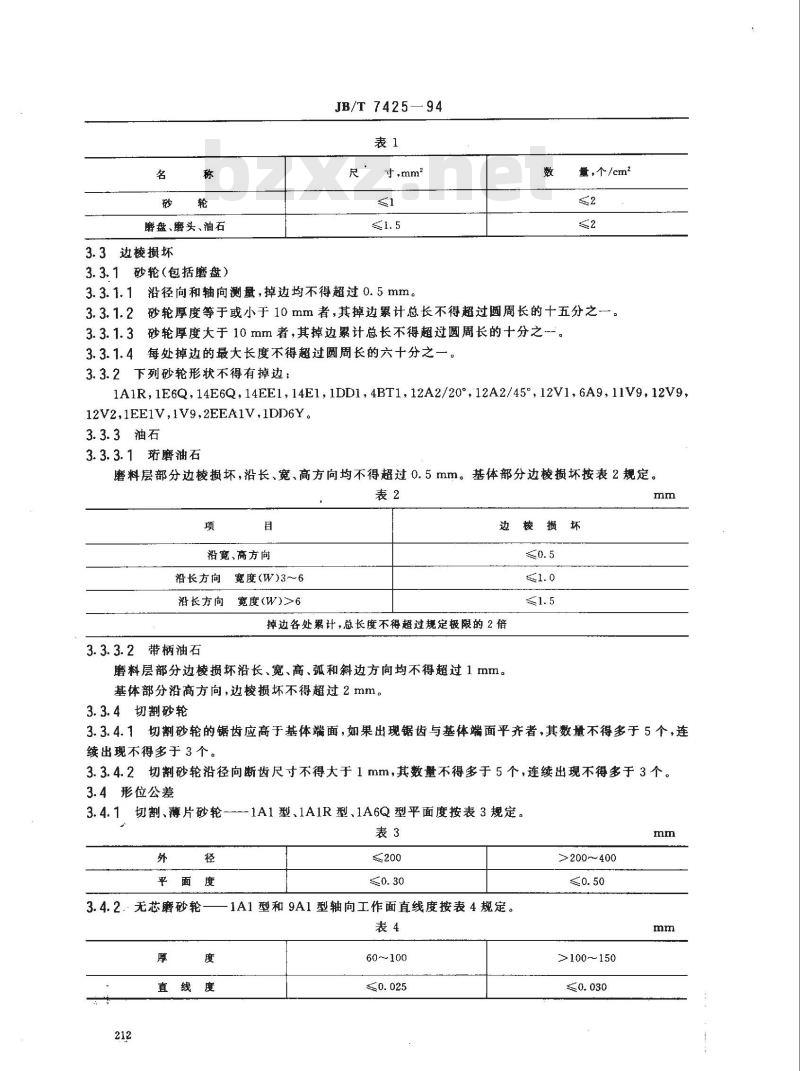

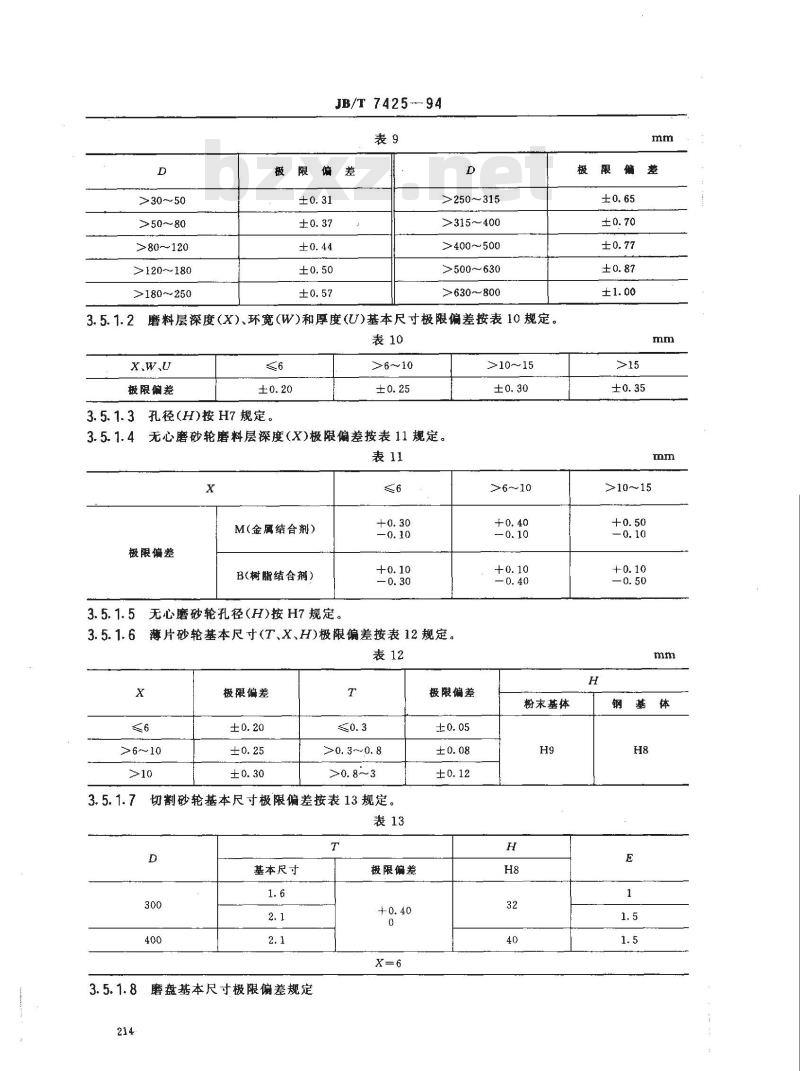
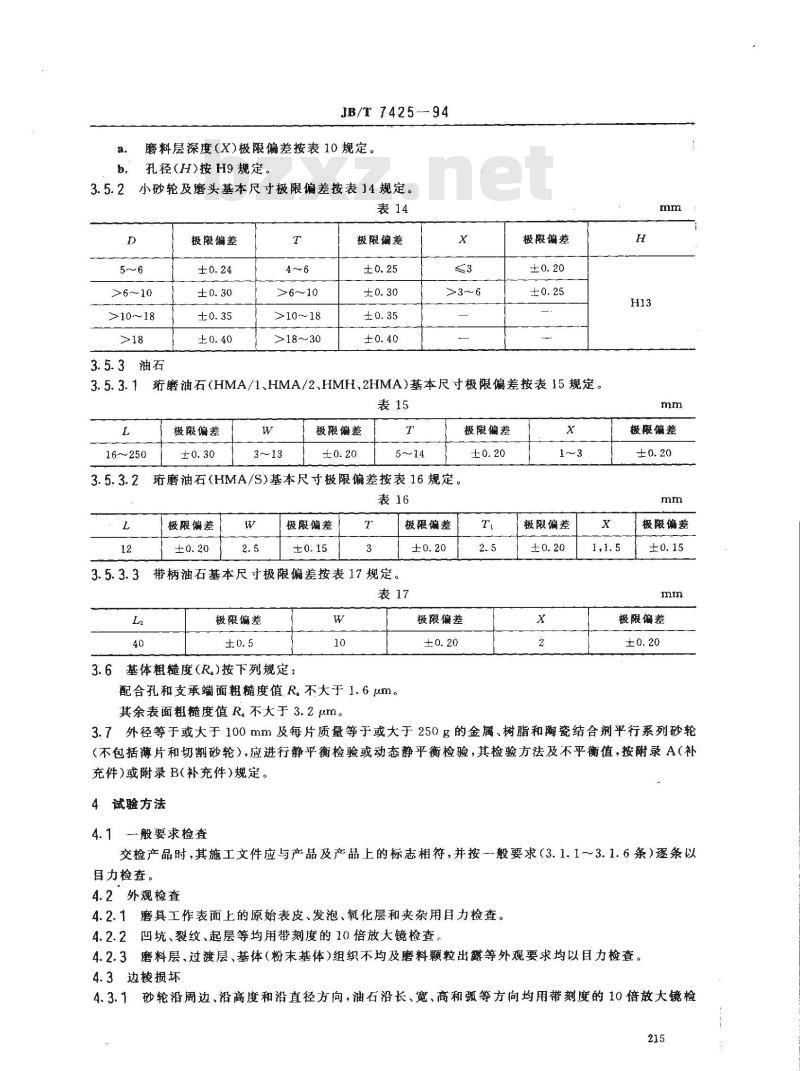
- 其它标准
- 热门标准
- 机械行业标准(JB)
- JB/T5762.2-2006 转塔车床 第2部分:精度
- JB/T10723-2007 焊接聚晶金刚石或立方氮化硼镗刀
- JB/T3103.2-2010 锯条开齿机 第2部分:精度
- JB/T10565-2006 工业过程测量和控制系统用动圈式指示仪性能评定方法
- JB/T2965-1992 溅射离子泵 性能测试方法
- JB/T10596-2006 磁阻式步进电动机通用技术条件
- JB/T10725-2007 天然金刚石车刀
- JB/T10767-2007 装载机铜基湿式粉末冶金摩擦片 技术条件
- JB/T7775.2-2008 铜钨碳化钨真空触头材料化学分析方法 第2部分:气体容量法测定碳量
- JB/T10579-2006 腐蚀数据统计分析标准方法
- JB/T2841-1993 控制气体发生装置 基本技术条件
- JB/T2936.1-1999 闭式冷挤压压力机 型式与基本参数
- JB/T5532-2007 静电复印干式色调剂流动性测定方法
- JB/T7810-2007 幻灯片 24mm×36mm
- JB/T5448-2007 静电复印干式双组份显影剂用色调剂
- 行业新闻
- 比特币在10.8万美元阻力位回落,但仍守住关键支撑位,分析师建议本季度保持谨慎
- OKX 视角:BONK 在 Solana 币生态中的角色与发展机会
- 专家称忽视XRP将错失史上最大的财富转移
- Pi Network价格不会跌破0.40美元,原因如下
- Ripple首席技术官谈EVM侧链如何为XRP账本创造价值
- Bonk 币是什么?解读背景、官网、白皮书与社区生态
- 深扒 xStocks 开发商 Backed:“归零”团队二次创业,音乐生管项目增长
- BOB 宣布在BitVM测试网将原生BTC引入DeFi系统,Lombard、Solv Protocol、Fiamma等十家机构提供支持
- 突发:纳斯达克上市公司Nano Labs购入5000万美元BNB成立金库
- Solaxy 与 Axie Infinity AXS 对比:P2E 与 Layer‑2 扩容路径的反思
- 如果XRP今年能匹配USDT 2920亿美元的峰值日交易量,它可能值这个价
- XRP、Solana、Cardano遭冰封——SEC冻结灰度ETF上市计划
- 海耶斯的预警信号:华尔街推动的繁荣之前,比特币或将暴跌至9万美元
- 比特币的“诺克斯堡”进军英超联赛:Xapo银行与阿斯顿维拉达成赞助协议
- DDC为其企业比特币累积策略筹集了5.28亿美元
请牢记:“bzxz.net”即是“标准下载”四个汉字汉语拼音首字母与国际顶级域名“.net”的组合。 ©2009 标准下载网 www.bzxz.net 本站邮件:bzxznet@163.com
网站备案号:湘ICP备2023016450号-1
网站备案号:湘ICP备2023016450号-1