- 您的位置:
- 标准下载网 >>
- 标准分类 >>
- 国家标准(GB) >>
- GB 9414.4-1988 设备维修性导则 第五部分:设计阶段的维修性研究
标准号:
GB 9414.4-1988
标准名称:
设备维修性导则 第五部分:设计阶段的维修性研究
标准类别:
国家标准(GB)
标准状态:
现行-
发布日期:
1988-06-23 -
实施日期:
1988-12-01 出版语种:
简体中文下载格式:
.rar.pdf下载大小:
342.72 KB

点击下载
标准简介:
标准下载解压密码:www.bzxz.net
本标准概述了初步设计和详细设计阶段的维修性研究以及这些研究工作与本导则其他部分描述的维修性和维修保障工作的关系.描述了选用的维修性和设计研究方法,其中也包括设计评审中维修性的分析。 GB 9414.4-1988 设备维修性导则 第五部分:设计阶段的维修性研究 GB9414.4-1988

部分标准内容:
1引言
中华人民共和国国家标准
设备维修性导则
第五部分:设计阶段的维修性研究Guide on maintainability of equipmentPart 5: Maintainability studies during the design phaseGB 9414.4--- 88
本标准叙述设计过程中维修性研究的各个方面和如何进行这种研究。维修性研究应与设计过程相结合,以满足规定的系统工作要求。为保证满足这些要求,在设计的各个阶段,必须进行维修性研究,其研究结果供设计决策使用。
2范围
本标准概述了初步设计和详细设计阶段的维修性研究以及这些研究工作与本导则其他部分描述的维修性和维修保障工作的关系,描述了选用的维修性和设计研究方法,其中也包括设计评节中维修性的分析。
3目的
维修性研究的日的是:,
为设计决策提供支持;
预计产品定址的维修性特性;
C.确定产品的设计变更和(或)要求的变更,以满足给约束条件下的工作要求。4设计过程中的维修性研究
4.1概述
维修性研究是实施维修性大纲的一个组成部分,旨在确保交付使用的产品满足维修性要求。这项工作应由供货方安排执行,即使合同上未予规定,也应进行。维修性分析是维修性研究的个组成部分·它是·个把工作要求转换成详细的定性和延量的维修性要求及设计准则的过程。维修性分析为设计过程提供信息。其结果应记载在下列文件中:a.设计中具体的维修性要求;
b,设计指南及检查表(确保设计包含所要求的维修性特性);c.基本维修功能及保障要求提要。在选定最佳设计方案之前,要反复进行设计综合权衡研究。维修性分析就包括在综合权衡研究中。维修性分析还可用于评价维修性设计要求的实现程度。为实现最低的寿命周期费用,在优化设计时,应拟订出维修规则。维修规则是对工作环境中系统维修保障计划的概述。它规定了各种维修场所的修理范阐和方法,论证所需人力资源,为产品及其测试设备的设计、配貿及包装提供切实可行的根据。中华人民共和国电子工业部1988-04-26批准1988-12.01实施
GB 9414. 4-88
设计者的责任在时间和费用的约束条件下实现包括维修性要求在内的各种工作要求。为此,从设计过程的开始就必须规定维修性要求,并在设计过程中进行必要的维修性研究。维修性研究是维修性工程师的职责,研究的广度和深度取决于产品复杂性、安全性、有效性及可靠性水平的需要。图1为如何在设计中进行维修性研究及其研究顺序与设计工作的关系示例。设计是·个反复过程,每次工作都为同时进行的其他研究和后继研究提供信息。维修性研究的基本信息来源于本标准未包括的可靠性研究。图1也表明了维修性分析与同时进行维修保障分析之间的关系。维修保障研究在本导则的第八部分《维修与维修保障计划》中详述作要求
应用与环境要求
系统初步设计和研制
设计备择方案
初步设计
系统选择
综合权衡研究
寿命周期费用研究
系统选择
选择最伟的系统设讯
设计评审
详细的系统设计和研制
图纸、规范、技术数据
设计评审
系统制造
制造与功能试验
整体工作试验
性能、有效性、可、
靠性、维修性要手
初步的维修性分析
维修性功能图
维修性分配
维修性可行性评价
初步的维修性分析
详细的维修性分析
维修性设计准则
维修性设计检查表
维修性综合权衡研究
维修性预计
维修性验证实验
维修性
系统约束如进度,费
用、维修策略等
维修保障分析
维修规则
维修保障分析
详细的维修分析
维修计划
维修任务分析
居勤保障
规定和器材
测试与保障设备
人员和培训
技术资料
图1设计过程中的维修性研究
4.2维修性分析
4.2.1前提
维修性研究的重要前提是产品有维修性要求。这些要求成为设计任务的条款之前,或者由用户根据本导则第二部分《规范与合同中的维修性要求》在合同中规定,或者在“工作要求”的条款中规定。“工作要求”应包括具体的功能、性能、可靠性、维修性及安全性的要求。为了恰当地安排计划和进行设计,维修性要求必须用定性和定量的条款明确规定。4.2.2功能分析
在维修性分析的过程中,可借助于功能层次图来描述产品。产品功能层次的分解,是按其下属的各282
GB 9414. 4-88
种结构层次从上到下,直至能够定位故障和更换,修理或调整子产品的层次为止。功能分析提供产品的主要部分的功能说明,并规定设备的排列规则,还为维修性设计作好准备,指出哪些子产品是可以通过更换修复的,哪些是不可以更换的,故障定位、隔离及测试点在功能层次上也应标明。图2为维修性功能层次图示例
了系统子系统
图表符号说明;
定位点,在该点应能确定设备发生故障的部位;隔离点·在该点设备中发生故障的产品能被示别和隔离:测试点在该点测试产品的性能;不需更换产品;
需更换的产品。
4.2.3维修性的可行性估计
图2维修性功能层次图示例bzxz.net
在设计过程中,存在一些决策点,在这些点上必须对各种备用方案进行可行性评价以便选定··个方案。在产品的早期设计阶段,在进行详细设计之前,还缺乏足够的信息来详细地预计和确认设计是否符合规定的维修性要求,因此必须使用基于以往经验的简易方法,对维修性进行粗略的预计,可以使用以往设计的维修性数据,并把这些数据与新的设计特征及维修条件联系起来,这时仅需论证主要的修复性维修及预防维修任务及其持续时间。可行性分析的结果可用于系统设计和其备用方案的评价。可行性研究也可用来证明在规定的约束条件下,若系统的维修性要求不能满足,则必须予以修改。4.2.4维修性分配
把系绕维修性要求转换到较低功能层次的过程称为维修性分配。维修性分配是·个反复的过释在早期设计阶段就必须采用。在早期设计阶段,由于受到信息的限制、维修性分配只能涉及系统的较高层283
GB9414.4—88
次,当有详细的设计时,要再反复进行分配直至更低的功能层次。维修性分配的第步是要将系统分解到适应分配要求深度的功能层次。此工作可用4.2.2条所述的功能层次图来进行。在初始阶段,功能分解不可能做到所要求的深度,一旦可以得到更详细的信息时,功能分解必须继续进行。此过程中的关键是维修性工程师需要得到功能层次图上所示的各组成部分的可靠性估计值。没有这些可靠性估计值,维修性工程师就不能继续进行下一步工作,因此,需要可靠性工程师和维修性工程师·开始就密切合作,使用同一功能层次图。第二步是利用产品设计和环境所能得到的基本信息,对每·个单元进行维修性特性分配。分配可能存在两种情况:
a,对于含有未知固有特性的新设计,分配应以所涉及的单元的相对复杂性为基础。在许多场合,单元的失效率可用来作为衡量复杂性的量度。b。若设计是从过去的设计中演变而来,分配应以以往的经验为基础,并确定需要改进的地方。基本分配参数是:
平均修理实施时间(MART),此参数可进--步细分成诊断时间,修复时间和检验间;平均预防维修实施时间,以及维修工作与工作小时之比。如果需要,也可以对后勤保障时间和管理延迟时间进行分配。第三步是对功能层次图(见图2)中标记的每个单元的维修性分配进行可行性研究,若认为不能满足该分配值,则应开展下述工作:通过重新设计(改进诊断、检测窗口、模块化、维修设施等等)改进维修性特性,在满足整个系统a.
要求的条件下重新分配。
b.通过改进可靠性降低失效率。c.最后一种办法是重新考虑系统要求。维修性分配示例在附录A中描述。4.2.5维修性预计
维修性预计是通过解析的方法评定产品维修性和使用规定的维修性解析模型(包括规的维修保障条件)计算产品定量的维修性特性的过程。维修性预计应在设计过程需要的时候进行,以提供:a。评价分配的维修性要求能否满足,需要的维修保障是否能有效的满足工作要求;b,发现必须改进或修改设计的部位。预计的结果应提供给管理部门,以确保设计的顺利进行和指出需改变的设计方问和需修改的设计区域。
图3给出了每-个预计循环中应遵循的步骤。284
4.2.5.1维修性模型
GB 9414.4—88
提出维修性模型
确定修复性维修
任务及时间间隔
维修任务时间分析
估计维修性参数值
确定预防性维修
在务及时间间障
图3维修性预计基本步骤
应拟定一个恰当的反映维修性特性与产品研究中的关系的分析模型。维修性模型应建文在前而图2所描述的维修性功能层次图的基础上,并应确定数学法则,以综合产品组成部分在给定的约束下维修性数值,通常宜用简单的解析模型,在某些情况下也需采用较复杂的模型。4.2.5.2维修任务及时间间隔
维修性预计应考虑修复性维修和预防性维修.并以其对全部维修费用的影响为依据修复性维修分析的倍息的可靠性分析提供,用FMEA(见4.2.7条)分析可能发生的故障,提出修复的要求。平均修复性维修间隔时间则出相应的失效率决定。预防维修的分析应以维修计划为根据,维修计划确定了维修任务及其相应的以工作次数或周期表示的时间间隔。
维修服务工作,如补给润滑,应按具体情况包括修复性维修和预防性维修工作之中。4.2.5.3维修任务时间分析
4.2.5.2条所确定的维修工作,可分解成实际工作部分、技术延迟及保障工作部分(如测试设备、器材的配置),各部分所需时间应予以估计,估计值是以历史数据或以往经验为基础的,并按照有关的维修任务的内容进行综合,通过这种分析所得到的各部分的维修任务时问应载人文件。4.2.5.4维修性参数估计
根据4.2.5.1~~4.2.5.3条确定的信息、可对设计所达到的维修性进行定量的估计。按照给定的维修性要求,应对所有有关的维修措施分别地或综合地进行维修性预计。预让使用的维修性参数必须与维修性分配参数相同,运用维修性数学模型,即可由有关的任务频数及任务时间的数据计算出维修性参数。4.2.6综合权衡研究
综合权衡研究是一种决策技术,当评价几种备择方案时,在选定最佳方案之前,应系统地和充分地考虑所有有关的主要因素,维修性权衡分析用于确定·一种备择设计方案及其维修规则是否优厂其他方案。在初步设计中,综合评价集注于高层次系统参数,例如性能、有效性、可靠性和寿命周期费用等,在其285
GB9414.488
体的较低层次产品的详细设计中,应该考虑些较低层次的参数,如可达性,测试及保障设备,包装,备件等。
综合权衡研究通常按下述四个步骤进行:。明确问题:说明需要解决的具体问题和需要考虑的具体因素。b.确定可行的备择方案:首先列出所有可能的解决问题的方案,然后从中选择从整个系统着来是可接受的方案。
确定评价准则:选择评价过程中使用的参数,并按其重要程度划分等级,参数可以加权,以利评c
评价过程中包括下列步骤:
获得数据;
建立模型与分析;
决策。
在进行综合权衡研究时必须谨慎小心,以消除个人偏见,验证分析的数据和结果。采用灵敏度分析以确定结果对输入参数变化的敏感程度是非常有用的。寿命周期费用LCC(LifeCycleCos1)是综合权衡研究所娶考虑的最重要的参数之。从维修性角度来看,I(C研究是对系统或产品的购置、维修、保障费用(寿命周期费用)和和应的维修性特性、维修规则的综合评价。在设计评价过程中,用寿命周期费用研究来找出各种特性的最佳组合·使设计能在最低寿命周期费用的条件下满足工作要求。综合权衡研究(包括LCC研究和其他的研究)为系统评价和优化提供了依据,许借以选定晟佳设计方案。
失效模式及效应分析FMEA(FailureModeandEffectAnalysis)4.2.7
FMEA是一种可靠性分析方法,目的是发现产品所有可能出现的故障模式及原因。进行FMEA的步骤是:
明确产品性能要求:
将系统分解成功能单元(部件、元件);b.
鉴别故障模式及效应;
鉴别故障状态;
拟订故障检测措施;
f.拟订排除故障的基本维修措施。FMEA通过鉴别故障模式、故障频次及需要的维修措施。为维修性预计提供信息,也使维修性分配容易进行。FMEA还可用来作为设计和配置状态监控、故障传感装置以及设计自动检测、故障诊断程序的依据,借以减少停工修理的时间。FMEA程序的细节见GB2826《失效模式及效应分析程序》4.2.8其他的维修性分析
除了上述的维修性分析以外,还可进行其他的分析,如编址诊断要求、诊断效率水平,修理部位等。编址维修及维修保障研究与分析(如易维修研究、维修任务分析、技能分析等)在本导则的第八部分《维修与维修保障计划》中详述。
4.3维修性设计保障
4.3.1设计和维修性分析的协调和联系维修性工程师为广不断地为设计提供支援,必须参加下述工作。a.作为顾问参加设计过程,从事维修性的协调工作;提供维修性经验数据和信息;
监督设计,以确保在图纸和设备规范中规定维修性特性;c.
GB9414.4-88
d.监督设计变更,以确保不降低各种维修性要求;e.对与维修性有密切关系的其他工作(可靠性、维修保障及成本效益或价值T程)进行协调4.3.2维修性设计准则及检查表
在中选设计方案中所规定的维修性要求、维修规则及维修性分配的基础上,应拟定出详细的维修性设计准则,这些推则构成具体的维修性目标及设计的各种预期特性:标准化、互换性、模块化、修理与报废,可达性,提升装置等。有些准则可以在通用的设计规范中规定,而另·些则必须按特定丁程专门规定,这些准则可用定性和定量的形式了以说明,并为设计师们实现系统或产品的维修性要求提供指南检查表的制定通常是以维修性的基本原则及过去设计中出现的维修方面的问题为基础。它是设计师的备忘录。有些问题非常简单和实际,但在设计中往往又最容易忽视。标准检查表通常包括在设计部门的设计规范和公开出版的有关文件中检查表也可用来作为设计评审的指南。检查表叫包含如下内容
a、可达性与提升、校准与统调、润滑、支承、连接、液压等系统;b.功能组件包装、快速交付能力、耗损监控、标准化;C.小型化与模块化、电缆与连接器、设备闭锁、操纵台(仪表面板)、支架与组装、控制显示、测试点、可达性,
环境保护、预定的维修要求、保障要求、工作期间的维修、安全保护措施、人机接I1。d.
上述内容仅是使用设计准则和检查表的-些例于。对于新系统或新产品的设计,应鉴别出哪些是会反复出现问题的区域,并拟订出相应的设计准则和检查表。4.3.3设计评审中的维修性考虑
设计评审是对系统(或产品)设计方案的一种正式的、系统的研究,设计评审应形成文件并中不首接参与设计的专家来进行。
设计评审的目的是:
a评价设计是否满足系统的全部要求(包括维修性要求);b.发现有问题的区域,提出解决方法;C.对研制试验、验证试验及检查计划的必要性提供预测;d.增加设计完善的可能性。
维修性估计应在选定设计方案后,与设计评审一道进行。估计的结果可为批准维修性特性及纠节提供依据。为了做好设计评审的准备,每次评审考虑的定性和定量要求,应预先按评价准则及检查表的格式给出。
应子关注的涉及维修性方面的问题有:维修性要求是否明确到了必要的详细程度?a.
b.是否拟订维修规则,维修规则与维修性要求及给定的约束条件是否一-致?维修保障要求是否明确?维修保障要求与维修性要求、维修规则及给定的约束条件是否··致?c
设计规则是否与维修性要求一致?e.
是否进行了包括寿命周期费用研究在内的可行性研究及最优化研究?f、是否对测试和诊断设备规定了要求?以上仪是些需要关注的问题示例,并未包括所有的维修性问题。通过对上述有关问题的评价,可以证明设计是否与维修性要求一致。在不致的情况下,需要进行下列工作:a.
重新分配或重新规定维修性要求;b.
重新分配或重新规定设计要求;c
重新论证设计是否恰当;
d.对确定的特性重新设计;
重新检查维修策略。
GB9414.488
如果上述上作完全无效,尽管设计与维修性要求不致,这时也不得不认可这种偏离,接受设计方在整个设计过程中,从维修性观点来讲,当需要时,应进行不太正式的设计评审。对于正式和非正式的设计评审的结果,都应以文件的形式予以记载,以便为已经完成最终设计的整个设计过程提供说明。288
维修性分配的基本工作如下
GB 9414.4--- 88
附录A
维修性分配示例
(参考件)
…个由K个可更换或可修理的子产品所组成的产品应满足总特性要求表明的某维修性要求。如产品的平均修理实施时间MART,根据4.2.4条,当将MART目标值向各了产品进行分配时,会遇到下列情况:
新设计:分配应以各子产品的相对复杂性为根据,在无其他度量单位情况下,子产品;的相对a.
复杂性可用失效率入,表示。于是,对于了产品1
如渠产品由K个了产品组成.则
b.局部新设计:产品的K个子产品中,只有(K一l)个了产品属于新设计,其余个子产品有过去的资料可供使用,这时对于新设计的子产品:Sn.aM
(K=)na
1+1+ 2、
全部K个子产品都有过去的资料可供使用、即子产品i的MART预期数值为M,,则:M
当M≤M时,符合给定的维修性要求;SMnia
当M≥M时,不符合要求,应根据4.2.4条的规定,作进-*步的改进。例:M=0.5、功能层次图见图A1、分配过程可用类似表A1的分配表产品
广产品
手产品
子产品
图A1功能层次示意图
子产品
子产品类型
情况&:
情况b:
于是:
情况:
GB9414.4-88
表A1分配表
失效率
累积失效率
MA=0.5X2.73
M—0.5X2.73
Me = 0.5 × 2. 73
情况a
MA 0.5 ×2. 73 - (0.5 X 0. 96 + 1. 0 × 0. 06)1.71
根据过去的资料
于是:
附加说明:
Me = 0. 5
情况h
M 0. 4 × 1.71 + 0. 5X 0.96 ± 1. 0 × 0. 062.73
本标准由电子工业部标准化研究所、成都电讯工程学院起草。290
情况。
小提示:此标准内容仅展示完整标准里的部分截取内容,若需要完整标准请到上方自行免费下载完整标准文档。
中华人民共和国国家标准
设备维修性导则
第五部分:设计阶段的维修性研究Guide on maintainability of equipmentPart 5: Maintainability studies during the design phaseGB 9414.4--- 88
本标准叙述设计过程中维修性研究的各个方面和如何进行这种研究。维修性研究应与设计过程相结合,以满足规定的系统工作要求。为保证满足这些要求,在设计的各个阶段,必须进行维修性研究,其研究结果供设计决策使用。
2范围
本标准概述了初步设计和详细设计阶段的维修性研究以及这些研究工作与本导则其他部分描述的维修性和维修保障工作的关系,描述了选用的维修性和设计研究方法,其中也包括设计评节中维修性的分析。
3目的
维修性研究的日的是:,
为设计决策提供支持;
预计产品定址的维修性特性;
C.确定产品的设计变更和(或)要求的变更,以满足给约束条件下的工作要求。4设计过程中的维修性研究
4.1概述
维修性研究是实施维修性大纲的一个组成部分,旨在确保交付使用的产品满足维修性要求。这项工作应由供货方安排执行,即使合同上未予规定,也应进行。维修性分析是维修性研究的个组成部分·它是·个把工作要求转换成详细的定性和延量的维修性要求及设计准则的过程。维修性分析为设计过程提供信息。其结果应记载在下列文件中:a.设计中具体的维修性要求;
b,设计指南及检查表(确保设计包含所要求的维修性特性);c.基本维修功能及保障要求提要。在选定最佳设计方案之前,要反复进行设计综合权衡研究。维修性分析就包括在综合权衡研究中。维修性分析还可用于评价维修性设计要求的实现程度。为实现最低的寿命周期费用,在优化设计时,应拟订出维修规则。维修规则是对工作环境中系统维修保障计划的概述。它规定了各种维修场所的修理范阐和方法,论证所需人力资源,为产品及其测试设备的设计、配貿及包装提供切实可行的根据。中华人民共和国电子工业部1988-04-26批准1988-12.01实施
GB 9414. 4-88
设计者的责任在时间和费用的约束条件下实现包括维修性要求在内的各种工作要求。为此,从设计过程的开始就必须规定维修性要求,并在设计过程中进行必要的维修性研究。维修性研究是维修性工程师的职责,研究的广度和深度取决于产品复杂性、安全性、有效性及可靠性水平的需要。图1为如何在设计中进行维修性研究及其研究顺序与设计工作的关系示例。设计是·个反复过程,每次工作都为同时进行的其他研究和后继研究提供信息。维修性研究的基本信息来源于本标准未包括的可靠性研究。图1也表明了维修性分析与同时进行维修保障分析之间的关系。维修保障研究在本导则的第八部分《维修与维修保障计划》中详述作要求
应用与环境要求
系统初步设计和研制
设计备择方案
初步设计
系统选择
综合权衡研究
寿命周期费用研究
系统选择
选择最伟的系统设讯
设计评审
详细的系统设计和研制
图纸、规范、技术数据
设计评审
系统制造
制造与功能试验
整体工作试验
性能、有效性、可、
靠性、维修性要手
初步的维修性分析
维修性功能图
维修性分配
维修性可行性评价
初步的维修性分析
详细的维修性分析
维修性设计准则
维修性设计检查表
维修性综合权衡研究
维修性预计
维修性验证实验
维修性
系统约束如进度,费
用、维修策略等
维修保障分析
维修规则
维修保障分析
详细的维修分析
维修计划
维修任务分析
居勤保障
规定和器材
测试与保障设备
人员和培训
技术资料
图1设计过程中的维修性研究
4.2维修性分析
4.2.1前提
维修性研究的重要前提是产品有维修性要求。这些要求成为设计任务的条款之前,或者由用户根据本导则第二部分《规范与合同中的维修性要求》在合同中规定,或者在“工作要求”的条款中规定。“工作要求”应包括具体的功能、性能、可靠性、维修性及安全性的要求。为了恰当地安排计划和进行设计,维修性要求必须用定性和定量的条款明确规定。4.2.2功能分析
在维修性分析的过程中,可借助于功能层次图来描述产品。产品功能层次的分解,是按其下属的各282
GB 9414. 4-88
种结构层次从上到下,直至能够定位故障和更换,修理或调整子产品的层次为止。功能分析提供产品的主要部分的功能说明,并规定设备的排列规则,还为维修性设计作好准备,指出哪些子产品是可以通过更换修复的,哪些是不可以更换的,故障定位、隔离及测试点在功能层次上也应标明。图2为维修性功能层次图示例
了系统子系统
图表符号说明;
定位点,在该点应能确定设备发生故障的部位;隔离点·在该点设备中发生故障的产品能被示别和隔离:测试点在该点测试产品的性能;不需更换产品;
需更换的产品。
4.2.3维修性的可行性估计
图2维修性功能层次图示例bzxz.net
在设计过程中,存在一些决策点,在这些点上必须对各种备用方案进行可行性评价以便选定··个方案。在产品的早期设计阶段,在进行详细设计之前,还缺乏足够的信息来详细地预计和确认设计是否符合规定的维修性要求,因此必须使用基于以往经验的简易方法,对维修性进行粗略的预计,可以使用以往设计的维修性数据,并把这些数据与新的设计特征及维修条件联系起来,这时仅需论证主要的修复性维修及预防维修任务及其持续时间。可行性分析的结果可用于系统设计和其备用方案的评价。可行性研究也可用来证明在规定的约束条件下,若系统的维修性要求不能满足,则必须予以修改。4.2.4维修性分配
把系绕维修性要求转换到较低功能层次的过程称为维修性分配。维修性分配是·个反复的过释在早期设计阶段就必须采用。在早期设计阶段,由于受到信息的限制、维修性分配只能涉及系统的较高层283
GB9414.4—88
次,当有详细的设计时,要再反复进行分配直至更低的功能层次。维修性分配的第步是要将系统分解到适应分配要求深度的功能层次。此工作可用4.2.2条所述的功能层次图来进行。在初始阶段,功能分解不可能做到所要求的深度,一旦可以得到更详细的信息时,功能分解必须继续进行。此过程中的关键是维修性工程师需要得到功能层次图上所示的各组成部分的可靠性估计值。没有这些可靠性估计值,维修性工程师就不能继续进行下一步工作,因此,需要可靠性工程师和维修性工程师·开始就密切合作,使用同一功能层次图。第二步是利用产品设计和环境所能得到的基本信息,对每·个单元进行维修性特性分配。分配可能存在两种情况:
a,对于含有未知固有特性的新设计,分配应以所涉及的单元的相对复杂性为基础。在许多场合,单元的失效率可用来作为衡量复杂性的量度。b。若设计是从过去的设计中演变而来,分配应以以往的经验为基础,并确定需要改进的地方。基本分配参数是:
平均修理实施时间(MART),此参数可进--步细分成诊断时间,修复时间和检验间;平均预防维修实施时间,以及维修工作与工作小时之比。如果需要,也可以对后勤保障时间和管理延迟时间进行分配。第三步是对功能层次图(见图2)中标记的每个单元的维修性分配进行可行性研究,若认为不能满足该分配值,则应开展下述工作:通过重新设计(改进诊断、检测窗口、模块化、维修设施等等)改进维修性特性,在满足整个系统a.
要求的条件下重新分配。
b.通过改进可靠性降低失效率。c.最后一种办法是重新考虑系统要求。维修性分配示例在附录A中描述。4.2.5维修性预计
维修性预计是通过解析的方法评定产品维修性和使用规定的维修性解析模型(包括规的维修保障条件)计算产品定量的维修性特性的过程。维修性预计应在设计过程需要的时候进行,以提供:a。评价分配的维修性要求能否满足,需要的维修保障是否能有效的满足工作要求;b,发现必须改进或修改设计的部位。预计的结果应提供给管理部门,以确保设计的顺利进行和指出需改变的设计方问和需修改的设计区域。
图3给出了每-个预计循环中应遵循的步骤。284
4.2.5.1维修性模型
GB 9414.4—88
提出维修性模型
确定修复性维修
任务及时间间隔
维修任务时间分析
估计维修性参数值
确定预防性维修
在务及时间间障
图3维修性预计基本步骤
应拟定一个恰当的反映维修性特性与产品研究中的关系的分析模型。维修性模型应建文在前而图2所描述的维修性功能层次图的基础上,并应确定数学法则,以综合产品组成部分在给定的约束下维修性数值,通常宜用简单的解析模型,在某些情况下也需采用较复杂的模型。4.2.5.2维修任务及时间间隔
维修性预计应考虑修复性维修和预防性维修.并以其对全部维修费用的影响为依据修复性维修分析的倍息的可靠性分析提供,用FMEA(见4.2.7条)分析可能发生的故障,提出修复的要求。平均修复性维修间隔时间则出相应的失效率决定。预防维修的分析应以维修计划为根据,维修计划确定了维修任务及其相应的以工作次数或周期表示的时间间隔。
维修服务工作,如补给润滑,应按具体情况包括修复性维修和预防性维修工作之中。4.2.5.3维修任务时间分析
4.2.5.2条所确定的维修工作,可分解成实际工作部分、技术延迟及保障工作部分(如测试设备、器材的配置),各部分所需时间应予以估计,估计值是以历史数据或以往经验为基础的,并按照有关的维修任务的内容进行综合,通过这种分析所得到的各部分的维修任务时问应载人文件。4.2.5.4维修性参数估计
根据4.2.5.1~~4.2.5.3条确定的信息、可对设计所达到的维修性进行定量的估计。按照给定的维修性要求,应对所有有关的维修措施分别地或综合地进行维修性预计。预让使用的维修性参数必须与维修性分配参数相同,运用维修性数学模型,即可由有关的任务频数及任务时间的数据计算出维修性参数。4.2.6综合权衡研究
综合权衡研究是一种决策技术,当评价几种备择方案时,在选定最佳方案之前,应系统地和充分地考虑所有有关的主要因素,维修性权衡分析用于确定·一种备择设计方案及其维修规则是否优厂其他方案。在初步设计中,综合评价集注于高层次系统参数,例如性能、有效性、可靠性和寿命周期费用等,在其285
GB9414.488
体的较低层次产品的详细设计中,应该考虑些较低层次的参数,如可达性,测试及保障设备,包装,备件等。
综合权衡研究通常按下述四个步骤进行:。明确问题:说明需要解决的具体问题和需要考虑的具体因素。b.确定可行的备择方案:首先列出所有可能的解决问题的方案,然后从中选择从整个系统着来是可接受的方案。
确定评价准则:选择评价过程中使用的参数,并按其重要程度划分等级,参数可以加权,以利评c
评价过程中包括下列步骤:
获得数据;
建立模型与分析;
决策。
在进行综合权衡研究时必须谨慎小心,以消除个人偏见,验证分析的数据和结果。采用灵敏度分析以确定结果对输入参数变化的敏感程度是非常有用的。寿命周期费用LCC(LifeCycleCos1)是综合权衡研究所娶考虑的最重要的参数之。从维修性角度来看,I(C研究是对系统或产品的购置、维修、保障费用(寿命周期费用)和和应的维修性特性、维修规则的综合评价。在设计评价过程中,用寿命周期费用研究来找出各种特性的最佳组合·使设计能在最低寿命周期费用的条件下满足工作要求。综合权衡研究(包括LCC研究和其他的研究)为系统评价和优化提供了依据,许借以选定晟佳设计方案。
失效模式及效应分析FMEA(FailureModeandEffectAnalysis)4.2.7
FMEA是一种可靠性分析方法,目的是发现产品所有可能出现的故障模式及原因。进行FMEA的步骤是:
明确产品性能要求:
将系统分解成功能单元(部件、元件);b.
鉴别故障模式及效应;
鉴别故障状态;
拟订故障检测措施;
f.拟订排除故障的基本维修措施。FMEA通过鉴别故障模式、故障频次及需要的维修措施。为维修性预计提供信息,也使维修性分配容易进行。FMEA还可用来作为设计和配置状态监控、故障传感装置以及设计自动检测、故障诊断程序的依据,借以减少停工修理的时间。FMEA程序的细节见GB2826《失效模式及效应分析程序》4.2.8其他的维修性分析
除了上述的维修性分析以外,还可进行其他的分析,如编址诊断要求、诊断效率水平,修理部位等。编址维修及维修保障研究与分析(如易维修研究、维修任务分析、技能分析等)在本导则的第八部分《维修与维修保障计划》中详述。
4.3维修性设计保障
4.3.1设计和维修性分析的协调和联系维修性工程师为广不断地为设计提供支援,必须参加下述工作。a.作为顾问参加设计过程,从事维修性的协调工作;提供维修性经验数据和信息;
监督设计,以确保在图纸和设备规范中规定维修性特性;c.
GB9414.4-88
d.监督设计变更,以确保不降低各种维修性要求;e.对与维修性有密切关系的其他工作(可靠性、维修保障及成本效益或价值T程)进行协调4.3.2维修性设计准则及检查表
在中选设计方案中所规定的维修性要求、维修规则及维修性分配的基础上,应拟定出详细的维修性设计准则,这些推则构成具体的维修性目标及设计的各种预期特性:标准化、互换性、模块化、修理与报废,可达性,提升装置等。有些准则可以在通用的设计规范中规定,而另·些则必须按特定丁程专门规定,这些准则可用定性和定量的形式了以说明,并为设计师们实现系统或产品的维修性要求提供指南检查表的制定通常是以维修性的基本原则及过去设计中出现的维修方面的问题为基础。它是设计师的备忘录。有些问题非常简单和实际,但在设计中往往又最容易忽视。标准检查表通常包括在设计部门的设计规范和公开出版的有关文件中检查表也可用来作为设计评审的指南。检查表叫包含如下内容
a、可达性与提升、校准与统调、润滑、支承、连接、液压等系统;b.功能组件包装、快速交付能力、耗损监控、标准化;C.小型化与模块化、电缆与连接器、设备闭锁、操纵台(仪表面板)、支架与组装、控制显示、测试点、可达性,
环境保护、预定的维修要求、保障要求、工作期间的维修、安全保护措施、人机接I1。d.
上述内容仅是使用设计准则和检查表的-些例于。对于新系统或新产品的设计,应鉴别出哪些是会反复出现问题的区域,并拟订出相应的设计准则和检查表。4.3.3设计评审中的维修性考虑
设计评审是对系统(或产品)设计方案的一种正式的、系统的研究,设计评审应形成文件并中不首接参与设计的专家来进行。
设计评审的目的是:
a评价设计是否满足系统的全部要求(包括维修性要求);b.发现有问题的区域,提出解决方法;C.对研制试验、验证试验及检查计划的必要性提供预测;d.增加设计完善的可能性。
维修性估计应在选定设计方案后,与设计评审一道进行。估计的结果可为批准维修性特性及纠节提供依据。为了做好设计评审的准备,每次评审考虑的定性和定量要求,应预先按评价准则及检查表的格式给出。
应子关注的涉及维修性方面的问题有:维修性要求是否明确到了必要的详细程度?a.
b.是否拟订维修规则,维修规则与维修性要求及给定的约束条件是否一-致?维修保障要求是否明确?维修保障要求与维修性要求、维修规则及给定的约束条件是否··致?c
设计规则是否与维修性要求一致?e.
是否进行了包括寿命周期费用研究在内的可行性研究及最优化研究?f、是否对测试和诊断设备规定了要求?以上仪是些需要关注的问题示例,并未包括所有的维修性问题。通过对上述有关问题的评价,可以证明设计是否与维修性要求一致。在不致的情况下,需要进行下列工作:a.
重新分配或重新规定维修性要求;b.
重新分配或重新规定设计要求;c
重新论证设计是否恰当;
d.对确定的特性重新设计;
重新检查维修策略。
GB9414.488
如果上述上作完全无效,尽管设计与维修性要求不致,这时也不得不认可这种偏离,接受设计方在整个设计过程中,从维修性观点来讲,当需要时,应进行不太正式的设计评审。对于正式和非正式的设计评审的结果,都应以文件的形式予以记载,以便为已经完成最终设计的整个设计过程提供说明。288
维修性分配的基本工作如下
GB 9414.4--- 88
附录A
维修性分配示例
(参考件)
…个由K个可更换或可修理的子产品所组成的产品应满足总特性要求表明的某维修性要求。如产品的平均修理实施时间MART,根据4.2.4条,当将MART目标值向各了产品进行分配时,会遇到下列情况:
新设计:分配应以各子产品的相对复杂性为根据,在无其他度量单位情况下,子产品;的相对a.
复杂性可用失效率入,表示。于是,对于了产品1
如渠产品由K个了产品组成.则
b.局部新设计:产品的K个子产品中,只有(K一l)个了产品属于新设计,其余个子产品有过去的资料可供使用,这时对于新设计的子产品:Sn.aM
(K=)na
1+1+ 2、
全部K个子产品都有过去的资料可供使用、即子产品i的MART预期数值为M,,则:M
当M≤M时,符合给定的维修性要求;SMnia
当M≥M时,不符合要求,应根据4.2.4条的规定,作进-*步的改进。例:M=0.5、功能层次图见图A1、分配过程可用类似表A1的分配表产品
广产品
手产品
子产品
图A1功能层次示意图
子产品
子产品类型
情况&:
情况b:
于是:
情况:
GB9414.4-88
表A1分配表
失效率
累积失效率
MA=0.5X2.73
M—0.5X2.73
Me = 0.5 × 2. 73
情况a
MA 0.5 ×2. 73 - (0.5 X 0. 96 + 1. 0 × 0. 06)1.71
根据过去的资料
于是:
附加说明:
Me = 0. 5
情况h
M 0. 4 × 1.71 + 0. 5X 0.96 ± 1. 0 × 0. 062.73
本标准由电子工业部标准化研究所、成都电讯工程学院起草。290
情况。
小提示:此标准内容仅展示完整标准里的部分截取内容,若需要完整标准请到上方自行免费下载完整标准文档。

标准图片预览:
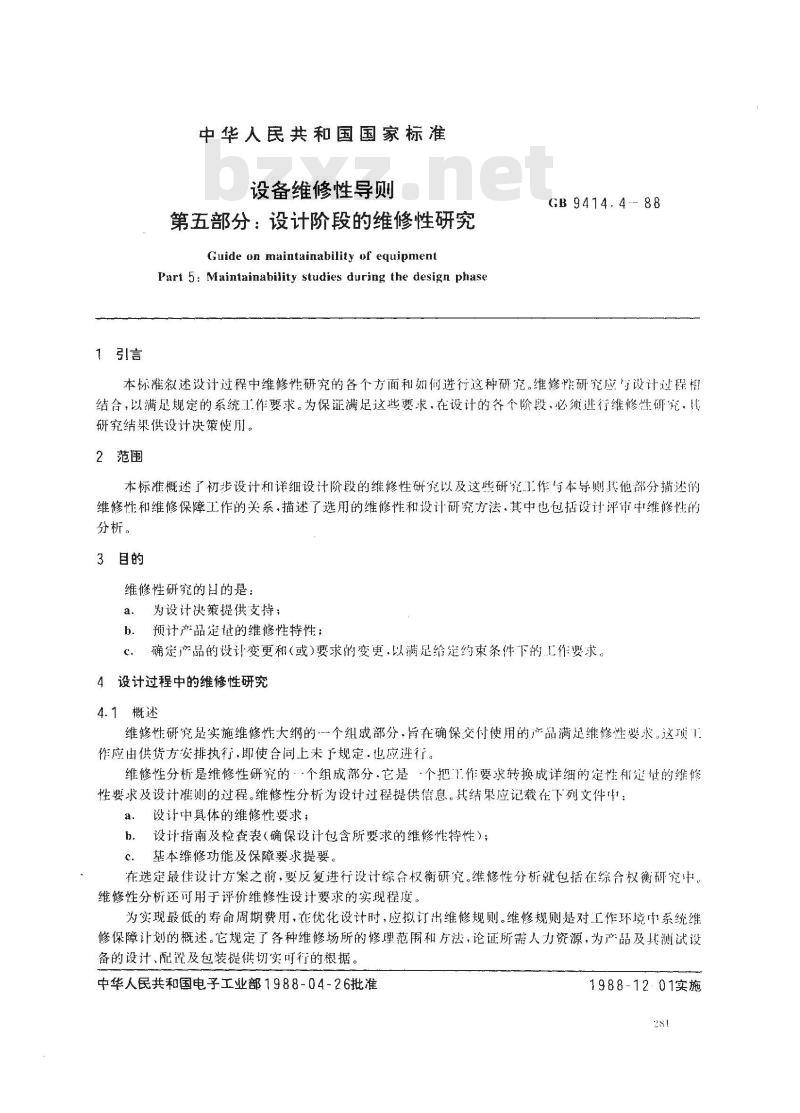
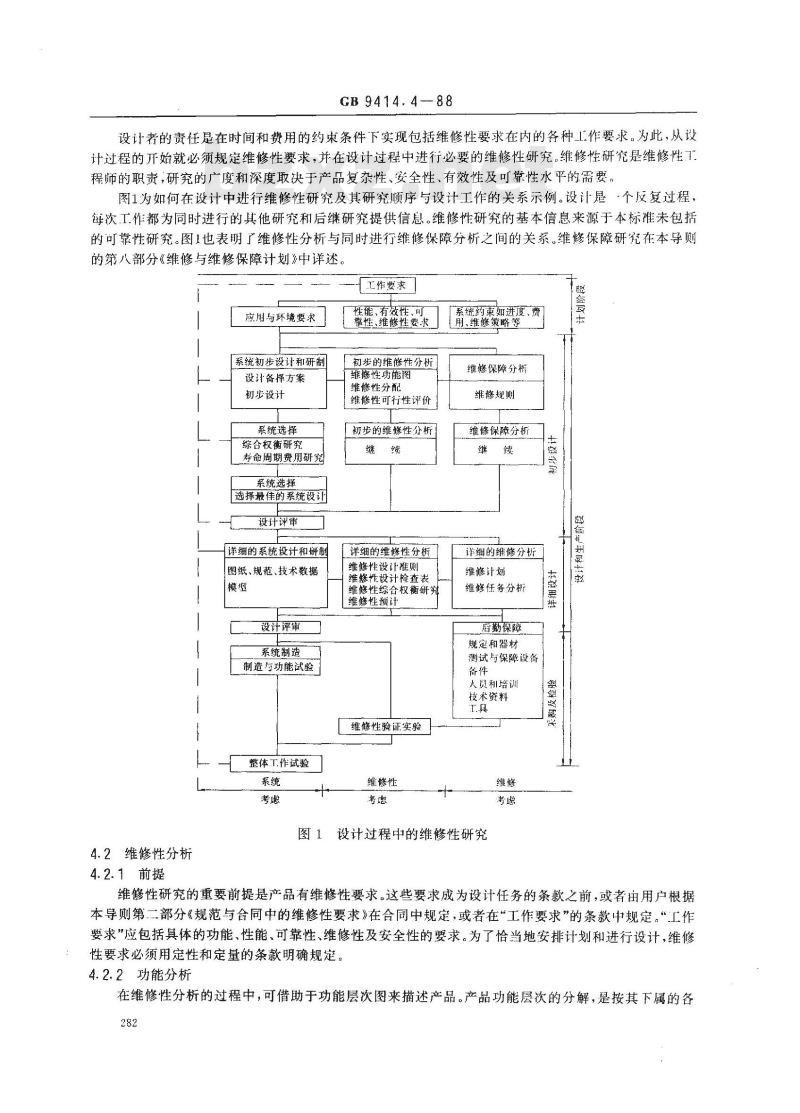
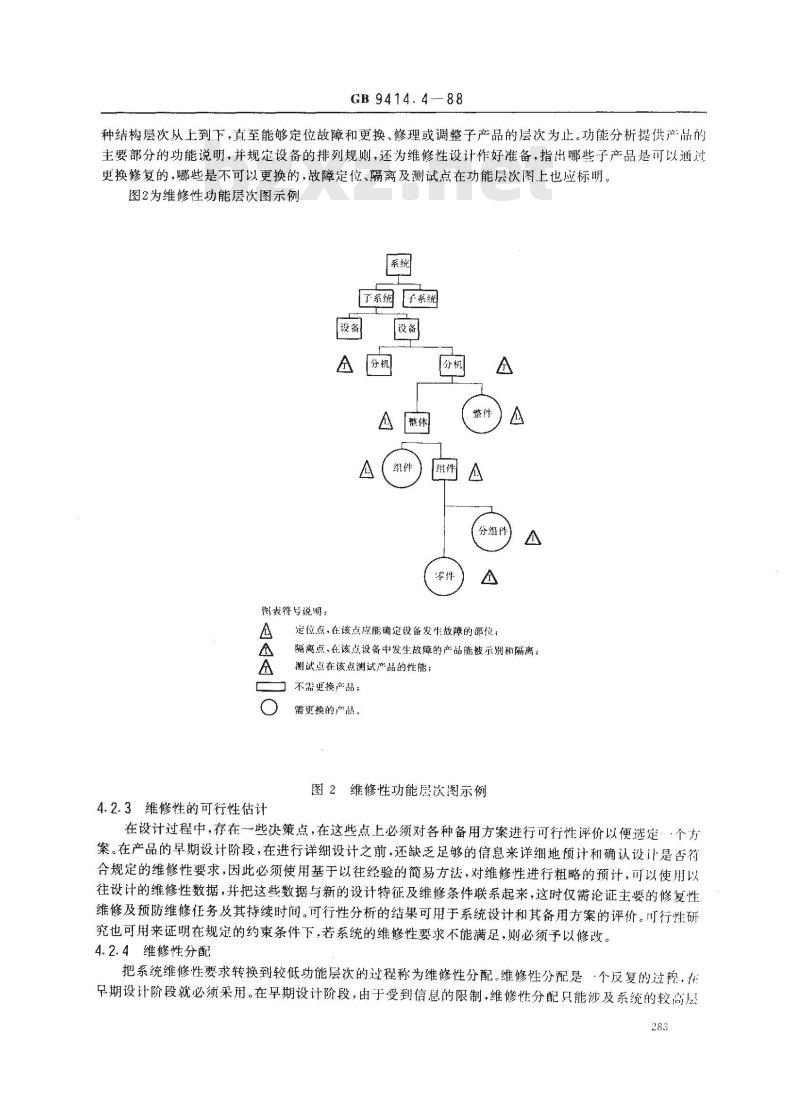
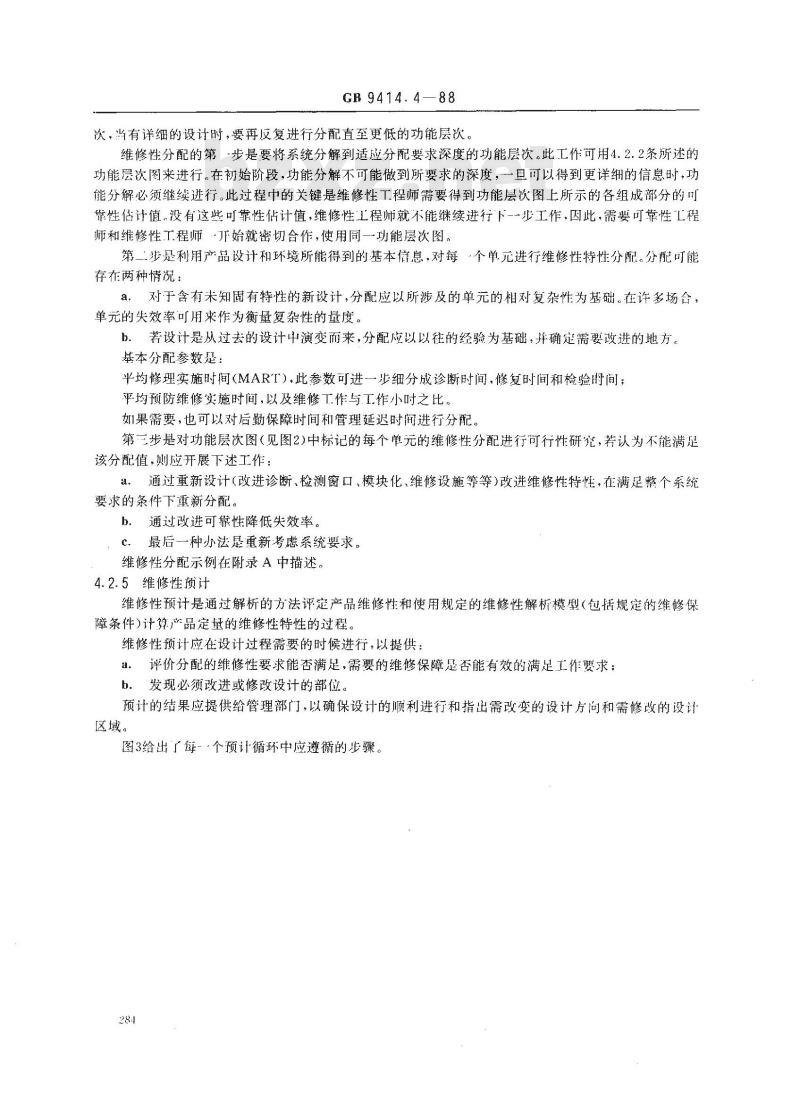
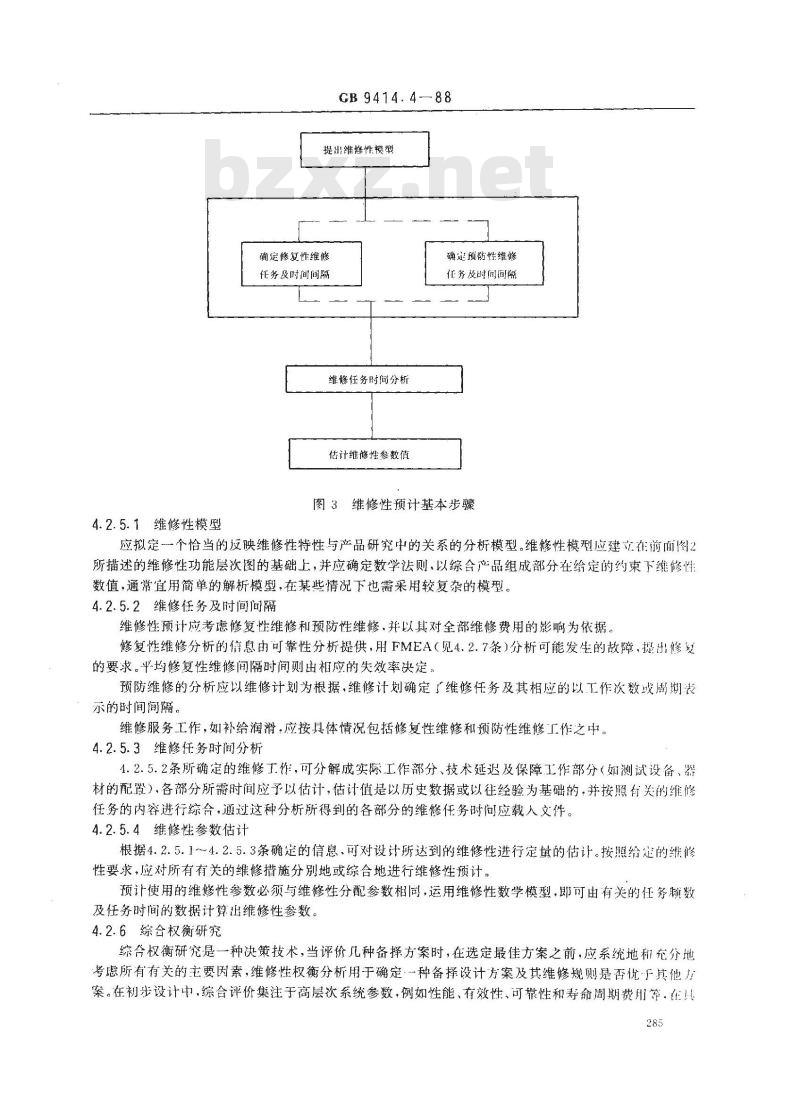
- 热门标准
- 国家标准(GB)
- GB/T14946-2002 全国干部、人事管理信息系统指标体系分类与代码
- GB/T12810-2021 实验室玻璃仪器玻璃量器的容量校准和使用方法
- GB/T51435-2021 农村生活垃圾收运和处理技术标准
- GB/T38670-2020 智能制造 射频识别系统 标签数据格式
- GB50777-2012 ±800KV及以下换流站构支架施工及验收规范
- GB7521—1987 多个控制器在一CA MAC机箱中
- GB/T43542-2023 机关办公区域物业服务监管和评价规范
- GB/T13477.19-2017 建筑密封材料试验方法 第19部分:质量与体积变化的测定
- GB/T6002.6-2003 纺织机械术语第6部分:卷纬机
- GB4623-1994 环形预应力混凝土电杆
- GB12838-1999 大芯腔轮胎气门芯
- GB/T1567-2003 薄型 平键
- GB/T18664-2002 呼吸防护用品的选择、使用与维护
- GB917.2—2000 公路路线标识规则国道名称和编号
- GB/T20290-2024 家用电动洗碗机 性能测试方法
请牢记:“bzxz.net”即是“标准下载”四个汉字汉语拼音首字母与国际顶级域名“.net”的组合。 ©2009 标准下载网 www.bzxz.net 本站邮件:bzxznet@163.com
网站备案号:湘ICP备2023016450号-1
网站备案号:湘ICP备2023016450号-1