- 您的位置:
- 标准下载网 >>
- 标准分类 >>
- 国家标准(GB) >>
- GB/T 17744-1999 钻井设备规范

【国家标准(GB)】 钻井设备规范
本网站 发布时间:
2024-08-02 19:32:29
- GB/T17744-1999
- 已作废
标准号:
GB/T 17744-1999
标准名称:
钻井设备规范
标准类别:
国家标准(GB)
标准状态:
已作废-
发布日期:
1999-05-01 -
实施日期:
1999-01-02 -
作废日期:
2009-03-01 出版语种:
简体中文下载格式:
.rar.pdf下载大小:
1.71 MB
替代情况:
被GB/T 17744-2008代替采标情况:
=API Spec 7K-96

点击下载
标准简介:
标准下载解压密码:www.bzxz.net
本标准的目的是为钻井设备及其主要承载件的设计、制造和试验提供统一标准。本标准适用于以下钻井设备:a)转盘;b)转盘补心;c)转盘卡瓦;d)钻井软管;e)钻井泵零部件;f)绞车零部件;g)不用于提升的卡盘;h)吊钳;I)不用于提升的安全卡瓦;j)动力大钳。 GB/T 17744-1999 钻井设备规范 GB/T17744-1999

部分标准内容:
GB/T17744-1999
本标准等效采用美国石油学会标准APISpec7K《钻井设备规范》(1996年2月第二版)。等效采用APISpec7K,为使我国石油钻并设备和主要承载件的设计、制造和试验与国际标准和国外先进标准接轨,以满足国际贸易、技术和经济交流的需要本标准采用了APISpec7K的技术内容,基本保留了其编写格式和方法。本标准删去了APlSpec7K的靡页、特别注释(SpecialNotes)、附录A“API会标使用说明(UseofAPI Monogram)”、附录D“设备不适用章节一览表(Listing of Paragraphs/Sections in API Spec 7Kthat Do Not Apply to Certain Equipment)”和附录F\SI单位(SIUnits)\,并对附录目次作了相应调整。
对APISpec7K引用标准中的MILSTD120,原文中只作为参考内容,在本标准中不作为引用标准。
对APISpec7K中的引用标准ASTMA668、SAEAS-1260、APISpcc8A、APISpec7和参考文献IAI>C《钻井手册》的有关条款已被全部引用,所以这些标准不再列人引用标准中。本标准的附录A、附录B.附录C是标准的附录。本标准的附录D是提示的附录。
本标准由全国石油钻采设备和工具标准化技术委员会提出、归口并负责解释。本标准起草单位:宝鸡石油机械厂。本标准主要起草人:刘玉杰、欧阳晓红、武强、全德祥、马中海、蒲容春。768
GB/T 17744--1999
API前言
本规范归美国石油学会(API)钻井和作业设备标准化委员会管理,本规范包括了由规范7分出的非钻杆类和由规范8A/8C分出的非提升类钻井设备项目。发布API规范,是为了有助于标准设备和材料的采购,引导API规范所涵盖产品的生产厂按规范生产。这些规范既无意排除正确的技术需要,也无意以任何方式限制任何人购买或生产其他规范的产品。
制定、发布API规范和API会标纲要,无意以任何方式限制向未经授权使用API会标的公司购买产品。
标明其设备或材料符合API规范要求的制造厂家,有责任遵守该规范的所有条款。美国石油学会不表示、担保或保证这些产品实际上是否符合其所用的API规范。本规范的生效日期印在封面上,但自发布之日起可自愿采用。任何人只要愿意,都可以使用API标准,API为保证其标准内容的准确性和可靠性作了不懈的努力。本学会对所发布的API规范不代表、担保或保证。这里明确声明,对于因使用API规范造成的损失或损害,或因使用API规范所造成的可能与联邦、州或市法规相抵触的违法行为,本学会不承担任何责任和义务。
1范围
1.1自的
中华人民共和国国家标准
钻井设备规范
Specification for drilling equipmentGB/T 177441999
本标准的目的是为钻井设备及其主要承载件的设计、制造和试验提供统一标准。1.2设备
本标准适用于以下钻井设备:
a)转盘;
b)转盘补心;
c)转盘卡瓦;
d)钻井软管;
e)钻井泵零部件;
f)绞车零部件;
g)不用于提升的卡盘;
h)吊钳;
i)不用丁提升的安全卡瓦;
j)动力大钳,
1.3功能和操作要求
钻井设备的设计、制造和试验应使其达到预定的目的,设备应能安全地传递预定的载荷,且应操作简便、安全可靠。
1.4附加要求
附加要求仅当买方在合同或订单中规定时采用(见附录A)。2引用标准
下列标准所包含的条文,通过在本标准中引用而构成为本标准的条文。本标准出版时,所示版本均为有效。所有标准都会被修订,使用本标准的各方应探讨使用下列标准最新版本的可能性美国齿轮制造商协会(AGMA)
斜齿和人字齿轮齿面耐久性
Std 21l.01:
齿轮材料用钢
Std 241.01
Std 244. 01
球墨铸铁齿轮材料
Std424.01确定油田钻井泵斜齿和人字齿齿轮额定值的标准作法美国国家标准学会(ANSI)
B1.1统-螺纹
B1.2统一-螺纹用量规和测量
量规毛坏(或美国量规设计委员会(CS8)国家质量技术监督局1999-05-17批准770
1999-12-01实施
美国焊接协会(ANSI/AWS)
D1.1钢结构焊接规程
美国石油学会(API)
GB/T 17744 -- 1999
Spec5B套管、油管和管线管螺纹加T、计量和检验规范美国机械工程师协会(ASME)
V无损检测
VI压力容器标准
X焊接和钎焊规范
美国无损检测协会(ASNT)
无损检测人员的资格
美国材料与试验协会(ASTM)
钢产品力学试验的标准方法和说明铸钢件焊接工艺和人员资格推荐作法专用钢板通过厚度测量进行的抗拉试验试验机载荷校准方法
铸铁件缺陷磁痕的标准参考底片渗透检测操作方法
壁厚(51~114mm)铸钢件的参考射线底片壁厚(114~305mm)铸钢件的参考射线底片厚度不大于2英寸(51mm)钢铸件的参考射线底片磁粉检测方法
美国国防部(DOD)
MILSTD6875F钢的热处理-航空器实用工艺GB/T12231-—1989(idtMSSSP-55)阀门铸钢件外观质量要求SY/T6367-1998(eqVAPIRP7K)钻井设备的检验、维护、修理和修复程序注:本标准的附录D提供了以上引用标准的溯源。3定义
本标准采用下列定义。
3.1危险区域 critical area
主要承载件上的高应力区域。
3.2设计载荷 design load
设备产生最大许用应力时静载荷与动载荷之和。3.3设计安全因数 design safety factor设计安全因数等于所用材料的最小屈服强度除以最大许用应力。3.4 设计验证试验 design verification test为证实设计计算的准确性而进行的试验。3.5动载荷dynamic load
由于加速度的影响而加到设备上的载荷。3.6高应力high stress
材料的最小屈服强度
高应力≥1.33X(设计安至因数)3.7最大许用应力maximum allowable stress771
GB/T 177441999
最大许用应力等于最小屈服强度除以设计安全因数。3.8主要载荷primaryload
设备执行其主要设计功能时产生的载荷。3.9主承载件primary load carrying components设备中承受主要载荷的零部件。3.10产品验证载荷试验proof load test为证实设备额定载荷而进行的载荷试验,3.11额定载荷rated load
设备的最大允许载荷,包括静载荷和动载荷,在数值上等于设计载荷。3.12额定速度rated speed
制造广确定的旋转移动速度或速率。3.13修补repair
制造过程中,为消除铸件和焊接件的缺陷而对零部件和焊接件进行的修补。注:本标推述及的修补仅适用于新设备的制造。3.14安全工作载荷 safeworking load安全工作载荷等于设计载荷减去动载荷。3.15.尺寸规格 size class
代表设备的尺寸互换性。
3.16 特殊工艺special process改变或影响设备所用材料的力学性能,包括韧性在内的工艺方法。3.17试验样机test unit
进行设计验证试验的样机。
3.18等效圆equivalent round
把各种形状的截面用等效的圆截面表示以便在热处理低合金钢或马氏体不锈钢时确定硬度特性。4设计
设计条件
设备的设计工作环境温度为20C(-4F),除第9章另有规定外。4.2强度分析
设备的强度应着重考虑屈服、疲劳或扭曲等失效形式4.2.15
强度分析以弹性理论为基础,在设计文件认为合理的地方,也可采用极限强度(塑性)分析。4.2.2
与设计有关的力都应纳人计算。对危险区域的不同受力方向的每个截面都应进行计算。应力分布和应力集中的简化可采用假设假设应符合常规作法、经验或试验。4.2.3
没有可靠的分析方法时,设备和零部件的承载能力应由试验来确定(见第5章)。4.2.5疲劳寿命应不少于20年。
4.2.6疲劳分析应按常规理论进行。4.3尺寸规格设计
设备的尺寸规格应满足第9章所要求的尺互换性。4.4额定值的确定
4.4.1转盘、卡盘、吊钳和动力大钳如按本标准供货,应按本标准的要求进行计算。4.4.2所有主要承载部位轴承的静载荷值应满足或超过设备的额定载荷。:4.4.3制造厂应注明动力大钳和吊钳的扭矩额定值。4.5额定载荷计算依据
a)4.6规定的设计安全因数;
GB/T 17744 --1999
b)主承载件所用材料的最小屈服强度:c)设计计算和(或)根据第5章中设计验证载荷试验收集的数据面确定的应力分布。4.6设计安全因数
4.6.1卡盘的设计安全因数应按表1确定。表1
卡盘的设计安全因数
额定载荷
1 350~4 500
150~500
1)原文的设计安全因数为\SF,\。(t)
136~454
2)额定载荷Pmx为 ton时,公式为 3.000.75(Pnax150)/350额定载荷Pmx为t时,公试为3.00-0.75(max136)/318转盘主要承载结构件的最小设计安全因数应为1.67。4.6.2
设计安全因数ns
8. 00-- 0. 75(Pmx — 1 350)/3 1502)2.25
吊钳、动力大钳的颚板、大钳尾绳附件的最小设计安全因数应按表2确定:表2
额定扭矩Panx.kN·m(kit·lb)
41(30)
41(30)~136(100)
136(100)
1)额定扭矩Pmx为kft·1b时,公式为3.00--0.75(Pmx-30)/70
4.7剪切强度
设计安全因数
3. 00-- 0. 75(Pmx—41)/951)
设计计算时应考虑到剪切强度,剪切屈服强度与抗拉属服强度的比值应取0.58。4.8设备
见第9章。
4.9设计文件
设计文件应包括方法、假设、计算和设计要求。设计要求应包括API规范要求的尺寸、试验、工作压力、材料、环境以及其他有关的内容。设计变更文件也应包括这些要求。5设计验证
5.1总则
为确保设计和计算的准确性,应对设备进行设计验证试验。5.1.1设计验证试验应按程序文件进行。5.1.2设计验证试验应由对产品设计和制造不负直接责任,且具有该项工作资格的人员进行。5.1.3设计验证试验可由本标准有关章节要求的试验项月组成:a)功能试验;
b)压力试验;
c)载荷试验。
5.2设计验证功能试验
5.2.1试验取样
GB/T17744—1999
如果机器利用零件的连续运动传递力、运动或能量,应从每种型号中选-一台进行功能试验5.2.2试验程序
制造厂应制定试验时间、试验载荷和试验速度的程序文件。连续运转的设备,试验样机应在额定速度下最少试运转2h:间断运转或周期运转的设备,除第9章规定外·应在额定速度下最少试运转2h或10个工作周期(取时间长者)。5.2.3合格条件
设备运行时应没有额外的动力损失,轴承和润滑油的温度在设计文件规定的范围内5.3设计验证压力试验
5.3.1试验取样
承压部件设计及第9章的主承压件应进行设计验证静水压试验,但不包括传递液压动力的零部件。5.3.2试验程序
试验压力应为最大额定工作压力的1.5倍,冷水、加人添加剂的水和通常在实际1.作中使用的液体可作为试验液体,应在油漆前对已完工的零件或组件进行试验。静水压试验应进行2次,每次由4步组成:a)初始保压期;
b)降压至零;
c)试验件外表面应完全干燥;
d)二次保压期。
保压期应从达到试验压力,且设备和压力测试仪表同压力源切断时开始计时,保压期不应少于3min。
5.3.3合格条件
每次试验循环后无渗漏或永久性变形。不满足要求或过早失效,应重新试验,重新进行评价。5.3.4单个零件
若组件中的单个零件适用于加载的试验装置,这些零件可单独进行试验。5.4设计验证载荷试验
5.4.1设计验证载荷试验
当第9章所列设备有要求时,设备应进行设计验证载荷试验。5.4.2试验取样
具有相同设计原理,不同规格和额定值的同系列设备的设计应力计算值的验证,应采用下列方法:a)最少选三台样机进行设计验证载荷试验,额定载荷的取值应从低端、中间和高端选取;b)另一种方法是,试验样机的数量以每台样机可验证高于和低于它的一种额定载荷为原则来确定(这种方法通常用于有限的产品额定值范围)。5.4.3试验程序
a)对安装好的试验样机应加载到额定载荷。在卸载后,检查设计功能,所有部件的功能都不应受到本次载荷的损伤;
b)试验样机上应力较高的地方应用应变仪(应变片),在适合应变片使用的位置也推荐使用有限元分析、模拟、涂脆性膜等方法。在危险截面处推荐采用三维应变仪以确定应力大小和方向;c)施加在设计验证试验样机上的载荷应按以下方法确定:设计验证试验载荷P,=0.8·Pmaxns,但不小于2Pmax,式中Pmax为额定载荷或额定扭矩,n:为1.6规定的设计安全因数:
d)试验载荷应逐渐增加,直至达到设计验证试验载荷,同时记录应变仪读数并观察变形情况。加载次数以取得足够的数据而决定:e)根据应变仪读数计算出的应力值不应超过依据设计验证试验载荷计算出的应力值,试验仪器的774
GB/T 17744-1999
误差不超出5.4.6的规定。样机不能满足要求或过早失效,应按原要求以相同数目的试验样机(与失效样机具有相同的额定值)再次试验,重新进行评价;f)设计验证载荷试验完成后拆开试验样机,检查主承载件的尺寸足否变化;g)如果试验装置的加载情况适用于组件中的单个零件,这些零件可单独进行试验。5.4.4额定载荷的确定
额定载荷应根据5.1设计验证试验的结果或应力分布计算值来确定。应力分布计算值不应超过最大许用应力。样机试验后除接触区域外,采用应变仪或其他方法测得水久变形不应超过0.2%。允许接触区有局部变形。如果应力分布计算值超过最大许用应力,受影响的零部件必须重新设计,直至达到所需额定值。如果用分析法确定的应力值不小于试验期间观测到的应力值应力分布计算值可用于设备额定载荷的计算。
5.4.5另-一种设计验证试验程序和计算方法样机的破坏性试验可用来提供设备所用材料的屈服强度和抗拉强度,试验可采用与所代表零件经相同热处理并属同一批次的抗拉试样进行,且应满足ASTMA370的要求。Pmaxi)=LX
式中:L—破坏载荷,kN;
as—最小屈服强度,MPa:
Qu-极限抗拉强度,MPa;
n.设计安全因数(见4.6);
Pmax—额定载荷,kN。
由于这种方法不依据应力计算,因此仅限于规定的型号、规格和试验计算。5.4.6设计验证试验装置
用丁模拟T作载荷的试验装置应按ASTME4校准,以确保试验载荷的准确性。超过3560kN(400ton、363t)的试验装置由A级校准仪器检验,误差应小于2.5%。试验装置应采用与实际工作情况相同的方式,在与实际工况相同的承载表面加载。所有加载设备的试验能力应予以确认。
5.5设计变更
因设计或制造的改变而变更设计载荷时,应根据本章要求进行设计验证试验。制造厂应评价所有设计或制造方面的改变,以确定是否影响额定载荷。这种评价应形成文件。5.6记录
设计验证记录和数据应按11.1的规定加以控制。6材料要求
6.1总则
本章叙述主承载件和承压件所用材料的验收准则、性能和加工要求。6.2书面规定
用于制造本标准涉及产品的材料应满足或超过设计要求的书面规定。6.3力学性能
6.3.1冲击韧度
6.3.1.1按ASTMA370的要求进行冲击试验。6.3.1.2必要时使用非标准冲击试样,验收准则应乘上表3所列的校正因数。非标准冲击试样宽度不-psi.o---- psi.I'max -ton.
1)用英制单位计算Pnux时,式中各单位为:L—ton、o.--775
小于5mm。
GB/T17744—1999
表3非标准冲击试样的校正系数
试样尺寸,mmXmm
10.0×7.5
10,0×5.0
校正系数
6.3.1.3设计工作环境温度低于-20℃时,采用附加冲击韧度要求。见附录A的附加要求SR26.3.2厚度方向的性能试验
设计对厚度方向性能要求时,应根据ASTMA770对材料进行厚度方向断面收缩试验。最小收缩率应为25%。
6.4材料验证
本标准要求的力学性能试验,应在与所代表零件经相同热处理且属同一批次的试棒上进行。试验应按ASTMA370或等效的国家标准,在材料最终热处理状态下进行。为了材料验证试验的目的,焊后消除应力处理不看作热处理,材料试验可在不改变热处理状态的应力处理之前进行。零件的试棒尺寸用等效圆(ER)法确定。确定简单形状实体和空心零件等效圆的基本模型如图1所示,所示形状均可用于试验试棒。确定复杂截面形状等效圆的步骤如图2所述。根据热处理条件下零件的实际尺寸来确定其等效圆尺寸。验证试棒的等效圆应不小于零件的等效圆尺寸,要求等效圆不超过127mm(5in)的验证试棒除外。确定ASTMA370基尔试块尺寸的步骤如图3所述:试棒可与所代表的零部件是一体或分体,也可是解剖零件的一部分。试棒应与所代表的零件经相同的热处理且属同一批次。
试样切取部位,对于实体试棒,在距表面1/4厚度内切取;对于空心试棒,在距试棒表面3mm(%in)的最厚截面处切取。拉伸试样的计量长度和冲击试样的切口应距试棒端面至少1/4个试棒厚度。bZxz.net
解剖产品零件取样应在距零件表面1/4厚度内的最厚截面处切取。6.5制造
制造工艺应确保零部件重复生产时符合本标推的要求。锻造材料应保证零部件内部组织结构的同-性。热处理应在制造厂或工艺员认可的设备内进行。热处理炉内任一零件应不影响同批次中其他零件的热处理特性。热处理的温度和时间应符合制造厂或工艺员的书面规范。实际热处理温度和时间应有记录,记录应对零部件具有追踪性。注:本标准的附录B提供了热处理设备验收准则的推荐作法。6.6化学成分
应对制造厂书面规定的材料逐炉进行化学成分分析。776
两端开口
正六边形
GB/T 17744 1999
ER= 1. 25 7
当L管(任意截面)
注:当L1)等效圆直径。
2)当厚度不相等时计算使用最大厚度。2.5R
长方形或平板
-端或两端封口
注:当D≤63.5mm(2.5in)时,ER=2.57当 D≥63.5mm(2.5 in)时,ER=3.5 T距表面1/4 厚度切取试棒
等效圆模型
简单截面
ER一等效圆摔直径
采用以下步骤确定复杂截面的等效圆:1简化零部件为简单截面;
GB/T 17744—1999
LER-12
交叉构件的ER计算值
可用交叉点处的测绘值代替
2换算简单截面为ER值,交叉构件的ER值等于与ER交叉面外切且垂直较大ER截面圆的直径,如右上图所示,
简单零部件和交叉构件的最大ER值,应作为复杂截面的ER值。3
图2复杂形状的等效圆
单位:mm(in)
2. 5R 69. 02(2. 7)
给定:ER=63.5mm(2/%in);
由图1:ER-2.3R得出:
(62880521
7焊接要求
7.1总则
$30.48(1.2)
R27. 94(1.1)
R-ER/2.3=27.61 mm(1.007 in)
1. 7 R=1. 75×27. 61 48. 32 mm(1. 902 in)2.5 R2.5X27.61=69.02 mm(2.718 in)3.5 R=3.5X27.6196.63mm(3.805 in)构成基尔试块
图3基尔试块尺寸展开图
本章叙述主承载件和承压件的焊接和补焊要求,包括对辅助焊接的要求。7.2焊接限定条件
GB/T 17744 --1999
所有零部件的焊接应按ASMEIX、ANSI/AWSD1.1或ASTMA488的焊接工艺进行,应由本标规定的鉴定合格的焊接操作者和焊机进行。非上述标准所列母材的焊接工艺应以可焊性、拉伸性能或成分为基础单独或作为一组进行评定,延展性不能满足ASMEIX中弯曲试验要求的母材,弯曲试验应按下列方式进行:母材热处理后有延伸和强度要求的弯曲试棒,应试验至破坏。弯曲试棒的边缘弯曲应不大于5°。7.3书面规定
焊接应按书面焊接工艺规程进行,并按有关标准进行评定。爆接工艺规程应包括相关标准所列的基本因素、次要因素和补充因素(如要求,见ASMEIX)。工艺评定记录应记录评定试验焊接工艺的基本因素和补充因素(如要求)。焊接工艺规程和工艺评定记录应按本标准第11章的要求保存。7.4焊料控制
焊料应符合美国焊接协会或焊料生产厂的规定,制造厂应具有贮存和检验焊料的书面规程。低氢型材料应按生产厂的建议贮存和使用,以保持其原有的低氢性能。
7.5焊接性能
工艺评定试验确定的焊缝力学性能应满足设计规定的最低力学性能。要求母材作冲击试验时,也应作为工艺评定的要求。焊缝和母材热影响区的试验结果应符合对母材的最低要求。辅助焊缝仅要求做冲击试验材料的热影响区满足上述要求。焊接试验应在焊后热处理状态下进行。7.6焊后热处理
零部件的焊后热处理应按焊接工艺规程进行。7.7质量控制要求
焊接质量控制应符合本标准第8章的要求。7.8组焊的特殊要求
焊接型式和焊缝尺寸应满足制造厂的设计要求,并应在制造厂焊接工艺规程中作出书面规定。7.9补焊的特殊要求
除7.2~~7.7的规定外,下列要求也适用。7.9.1方法
应有适当的方法评定、消除和检验补焊后的不合格品。7.9.2熔合
选定的焊接工艺规程(WPS)和补焊方法,应能保证母材完全熔合。7.9.3锻件和铸件
补焊应按制造厂的书面焊接工艺进行。补焊工艺应按用户的要求形成文件。补焊前制造厂应有下列允许补焊的文件:
a)缺陷类型;
b)缺陷尺寸限制;
c)主/次修补的定义。
焊前坡口和随后的补焊应满足本标准第8章的质量控制要求。7.9.4热处理
补焊工艺规程应确定补焊的实际顺序和焊后热处理。8质量控制
8.1总则
小提示:此标准内容仅展示完整标准里的部分截取内容,若需要完整标准请到上方自行免费下载完整标准文档。
本标准等效采用美国石油学会标准APISpec7K《钻井设备规范》(1996年2月第二版)。等效采用APISpec7K,为使我国石油钻并设备和主要承载件的设计、制造和试验与国际标准和国外先进标准接轨,以满足国际贸易、技术和经济交流的需要本标准采用了APISpec7K的技术内容,基本保留了其编写格式和方法。本标准删去了APlSpec7K的靡页、特别注释(SpecialNotes)、附录A“API会标使用说明(UseofAPI Monogram)”、附录D“设备不适用章节一览表(Listing of Paragraphs/Sections in API Spec 7Kthat Do Not Apply to Certain Equipment)”和附录F\SI单位(SIUnits)\,并对附录目次作了相应调整。
对APISpec7K引用标准中的MILSTD120,原文中只作为参考内容,在本标准中不作为引用标准。
对APISpec7K中的引用标准ASTMA668、SAEAS-1260、APISpcc8A、APISpec7和参考文献IAI>C《钻井手册》的有关条款已被全部引用,所以这些标准不再列人引用标准中。本标准的附录A、附录B.附录C是标准的附录。本标准的附录D是提示的附录。
本标准由全国石油钻采设备和工具标准化技术委员会提出、归口并负责解释。本标准起草单位:宝鸡石油机械厂。本标准主要起草人:刘玉杰、欧阳晓红、武强、全德祥、马中海、蒲容春。768
GB/T 17744--1999
API前言
本规范归美国石油学会(API)钻井和作业设备标准化委员会管理,本规范包括了由规范7分出的非钻杆类和由规范8A/8C分出的非提升类钻井设备项目。发布API规范,是为了有助于标准设备和材料的采购,引导API规范所涵盖产品的生产厂按规范生产。这些规范既无意排除正确的技术需要,也无意以任何方式限制任何人购买或生产其他规范的产品。
制定、发布API规范和API会标纲要,无意以任何方式限制向未经授权使用API会标的公司购买产品。
标明其设备或材料符合API规范要求的制造厂家,有责任遵守该规范的所有条款。美国石油学会不表示、担保或保证这些产品实际上是否符合其所用的API规范。本规范的生效日期印在封面上,但自发布之日起可自愿采用。任何人只要愿意,都可以使用API标准,API为保证其标准内容的准确性和可靠性作了不懈的努力。本学会对所发布的API规范不代表、担保或保证。这里明确声明,对于因使用API规范造成的损失或损害,或因使用API规范所造成的可能与联邦、州或市法规相抵触的违法行为,本学会不承担任何责任和义务。
1范围
1.1自的
中华人民共和国国家标准
钻井设备规范
Specification for drilling equipmentGB/T 177441999
本标准的目的是为钻井设备及其主要承载件的设计、制造和试验提供统一标准。1.2设备
本标准适用于以下钻井设备:
a)转盘;
b)转盘补心;
c)转盘卡瓦;
d)钻井软管;
e)钻井泵零部件;
f)绞车零部件;
g)不用于提升的卡盘;
h)吊钳;
i)不用丁提升的安全卡瓦;
j)动力大钳,
1.3功能和操作要求
钻井设备的设计、制造和试验应使其达到预定的目的,设备应能安全地传递预定的载荷,且应操作简便、安全可靠。
1.4附加要求
附加要求仅当买方在合同或订单中规定时采用(见附录A)。2引用标准
下列标准所包含的条文,通过在本标准中引用而构成为本标准的条文。本标准出版时,所示版本均为有效。所有标准都会被修订,使用本标准的各方应探讨使用下列标准最新版本的可能性美国齿轮制造商协会(AGMA)
斜齿和人字齿轮齿面耐久性
Std 21l.01:
齿轮材料用钢
Std 241.01
Std 244. 01
球墨铸铁齿轮材料
Std424.01确定油田钻井泵斜齿和人字齿齿轮额定值的标准作法美国国家标准学会(ANSI)
B1.1统-螺纹
B1.2统一-螺纹用量规和测量
量规毛坏(或美国量规设计委员会(CS8)国家质量技术监督局1999-05-17批准770
1999-12-01实施
美国焊接协会(ANSI/AWS)
D1.1钢结构焊接规程
美国石油学会(API)
GB/T 17744 -- 1999
Spec5B套管、油管和管线管螺纹加T、计量和检验规范美国机械工程师协会(ASME)
V无损检测
VI压力容器标准
X焊接和钎焊规范
美国无损检测协会(ASNT)
无损检测人员的资格
美国材料与试验协会(ASTM)
钢产品力学试验的标准方法和说明铸钢件焊接工艺和人员资格推荐作法专用钢板通过厚度测量进行的抗拉试验试验机载荷校准方法
铸铁件缺陷磁痕的标准参考底片渗透检测操作方法
壁厚(51~114mm)铸钢件的参考射线底片壁厚(114~305mm)铸钢件的参考射线底片厚度不大于2英寸(51mm)钢铸件的参考射线底片磁粉检测方法
美国国防部(DOD)
MILSTD6875F钢的热处理-航空器实用工艺GB/T12231-—1989(idtMSSSP-55)阀门铸钢件外观质量要求SY/T6367-1998(eqVAPIRP7K)钻井设备的检验、维护、修理和修复程序注:本标准的附录D提供了以上引用标准的溯源。3定义
本标准采用下列定义。
3.1危险区域 critical area
主要承载件上的高应力区域。
3.2设计载荷 design load
设备产生最大许用应力时静载荷与动载荷之和。3.3设计安全因数 design safety factor设计安全因数等于所用材料的最小屈服强度除以最大许用应力。3.4 设计验证试验 design verification test为证实设计计算的准确性而进行的试验。3.5动载荷dynamic load
由于加速度的影响而加到设备上的载荷。3.6高应力high stress
材料的最小屈服强度
高应力≥1.33X(设计安至因数)3.7最大许用应力maximum allowable stress771
GB/T 177441999
最大许用应力等于最小屈服强度除以设计安全因数。3.8主要载荷primaryload
设备执行其主要设计功能时产生的载荷。3.9主承载件primary load carrying components设备中承受主要载荷的零部件。3.10产品验证载荷试验proof load test为证实设备额定载荷而进行的载荷试验,3.11额定载荷rated load
设备的最大允许载荷,包括静载荷和动载荷,在数值上等于设计载荷。3.12额定速度rated speed
制造广确定的旋转移动速度或速率。3.13修补repair
制造过程中,为消除铸件和焊接件的缺陷而对零部件和焊接件进行的修补。注:本标推述及的修补仅适用于新设备的制造。3.14安全工作载荷 safeworking load安全工作载荷等于设计载荷减去动载荷。3.15.尺寸规格 size class
代表设备的尺寸互换性。
3.16 特殊工艺special process改变或影响设备所用材料的力学性能,包括韧性在内的工艺方法。3.17试验样机test unit
进行设计验证试验的样机。
3.18等效圆equivalent round
把各种形状的截面用等效的圆截面表示以便在热处理低合金钢或马氏体不锈钢时确定硬度特性。4设计
设计条件
设备的设计工作环境温度为20C(-4F),除第9章另有规定外。4.2强度分析
设备的强度应着重考虑屈服、疲劳或扭曲等失效形式4.2.15
强度分析以弹性理论为基础,在设计文件认为合理的地方,也可采用极限强度(塑性)分析。4.2.2
与设计有关的力都应纳人计算。对危险区域的不同受力方向的每个截面都应进行计算。应力分布和应力集中的简化可采用假设假设应符合常规作法、经验或试验。4.2.3
没有可靠的分析方法时,设备和零部件的承载能力应由试验来确定(见第5章)。4.2.5疲劳寿命应不少于20年。
4.2.6疲劳分析应按常规理论进行。4.3尺寸规格设计
设备的尺寸规格应满足第9章所要求的尺互换性。4.4额定值的确定
4.4.1转盘、卡盘、吊钳和动力大钳如按本标准供货,应按本标准的要求进行计算。4.4.2所有主要承载部位轴承的静载荷值应满足或超过设备的额定载荷。:4.4.3制造厂应注明动力大钳和吊钳的扭矩额定值。4.5额定载荷计算依据
a)4.6规定的设计安全因数;
GB/T 17744 --1999
b)主承载件所用材料的最小屈服强度:c)设计计算和(或)根据第5章中设计验证载荷试验收集的数据面确定的应力分布。4.6设计安全因数
4.6.1卡盘的设计安全因数应按表1确定。表1
卡盘的设计安全因数
额定载荷
1 350~4 500
150~500
1)原文的设计安全因数为\SF,\。(t)
136~454
2)额定载荷Pmx为 ton时,公式为 3.000.75(Pnax150)/350额定载荷Pmx为t时,公试为3.00-0.75(max136)/318转盘主要承载结构件的最小设计安全因数应为1.67。4.6.2
设计安全因数ns
8. 00-- 0. 75(Pmx — 1 350)/3 1502)2.25
吊钳、动力大钳的颚板、大钳尾绳附件的最小设计安全因数应按表2确定:表2
额定扭矩Panx.kN·m(kit·lb)
41(30)
41(30)~136(100)
136(100)
1)额定扭矩Pmx为kft·1b时,公式为3.00--0.75(Pmx-30)/70
4.7剪切强度
设计安全因数
3. 00-- 0. 75(Pmx—41)/951)
设计计算时应考虑到剪切强度,剪切屈服强度与抗拉属服强度的比值应取0.58。4.8设备
见第9章。
4.9设计文件
设计文件应包括方法、假设、计算和设计要求。设计要求应包括API规范要求的尺寸、试验、工作压力、材料、环境以及其他有关的内容。设计变更文件也应包括这些要求。5设计验证
5.1总则
为确保设计和计算的准确性,应对设备进行设计验证试验。5.1.1设计验证试验应按程序文件进行。5.1.2设计验证试验应由对产品设计和制造不负直接责任,且具有该项工作资格的人员进行。5.1.3设计验证试验可由本标准有关章节要求的试验项月组成:a)功能试验;
b)压力试验;
c)载荷试验。
5.2设计验证功能试验
5.2.1试验取样
GB/T17744—1999
如果机器利用零件的连续运动传递力、运动或能量,应从每种型号中选-一台进行功能试验5.2.2试验程序
制造厂应制定试验时间、试验载荷和试验速度的程序文件。连续运转的设备,试验样机应在额定速度下最少试运转2h:间断运转或周期运转的设备,除第9章规定外·应在额定速度下最少试运转2h或10个工作周期(取时间长者)。5.2.3合格条件
设备运行时应没有额外的动力损失,轴承和润滑油的温度在设计文件规定的范围内5.3设计验证压力试验
5.3.1试验取样
承压部件设计及第9章的主承压件应进行设计验证静水压试验,但不包括传递液压动力的零部件。5.3.2试验程序
试验压力应为最大额定工作压力的1.5倍,冷水、加人添加剂的水和通常在实际1.作中使用的液体可作为试验液体,应在油漆前对已完工的零件或组件进行试验。静水压试验应进行2次,每次由4步组成:a)初始保压期;
b)降压至零;
c)试验件外表面应完全干燥;
d)二次保压期。
保压期应从达到试验压力,且设备和压力测试仪表同压力源切断时开始计时,保压期不应少于3min。
5.3.3合格条件
每次试验循环后无渗漏或永久性变形。不满足要求或过早失效,应重新试验,重新进行评价。5.3.4单个零件
若组件中的单个零件适用于加载的试验装置,这些零件可单独进行试验。5.4设计验证载荷试验
5.4.1设计验证载荷试验
当第9章所列设备有要求时,设备应进行设计验证载荷试验。5.4.2试验取样
具有相同设计原理,不同规格和额定值的同系列设备的设计应力计算值的验证,应采用下列方法:a)最少选三台样机进行设计验证载荷试验,额定载荷的取值应从低端、中间和高端选取;b)另一种方法是,试验样机的数量以每台样机可验证高于和低于它的一种额定载荷为原则来确定(这种方法通常用于有限的产品额定值范围)。5.4.3试验程序
a)对安装好的试验样机应加载到额定载荷。在卸载后,检查设计功能,所有部件的功能都不应受到本次载荷的损伤;
b)试验样机上应力较高的地方应用应变仪(应变片),在适合应变片使用的位置也推荐使用有限元分析、模拟、涂脆性膜等方法。在危险截面处推荐采用三维应变仪以确定应力大小和方向;c)施加在设计验证试验样机上的载荷应按以下方法确定:设计验证试验载荷P,=0.8·Pmaxns,但不小于2Pmax,式中Pmax为额定载荷或额定扭矩,n:为1.6规定的设计安全因数:
d)试验载荷应逐渐增加,直至达到设计验证试验载荷,同时记录应变仪读数并观察变形情况。加载次数以取得足够的数据而决定:e)根据应变仪读数计算出的应力值不应超过依据设计验证试验载荷计算出的应力值,试验仪器的774
GB/T 17744-1999
误差不超出5.4.6的规定。样机不能满足要求或过早失效,应按原要求以相同数目的试验样机(与失效样机具有相同的额定值)再次试验,重新进行评价;f)设计验证载荷试验完成后拆开试验样机,检查主承载件的尺寸足否变化;g)如果试验装置的加载情况适用于组件中的单个零件,这些零件可单独进行试验。5.4.4额定载荷的确定
额定载荷应根据5.1设计验证试验的结果或应力分布计算值来确定。应力分布计算值不应超过最大许用应力。样机试验后除接触区域外,采用应变仪或其他方法测得水久变形不应超过0.2%。允许接触区有局部变形。如果应力分布计算值超过最大许用应力,受影响的零部件必须重新设计,直至达到所需额定值。如果用分析法确定的应力值不小于试验期间观测到的应力值应力分布计算值可用于设备额定载荷的计算。
5.4.5另-一种设计验证试验程序和计算方法样机的破坏性试验可用来提供设备所用材料的屈服强度和抗拉强度,试验可采用与所代表零件经相同热处理并属同一批次的抗拉试样进行,且应满足ASTMA370的要求。Pmaxi)=LX
式中:L—破坏载荷,kN;
as—最小屈服强度,MPa:
Qu-极限抗拉强度,MPa;
n.设计安全因数(见4.6);
Pmax—额定载荷,kN。
由于这种方法不依据应力计算,因此仅限于规定的型号、规格和试验计算。5.4.6设计验证试验装置
用丁模拟T作载荷的试验装置应按ASTME4校准,以确保试验载荷的准确性。超过3560kN(400ton、363t)的试验装置由A级校准仪器检验,误差应小于2.5%。试验装置应采用与实际工作情况相同的方式,在与实际工况相同的承载表面加载。所有加载设备的试验能力应予以确认。
5.5设计变更
因设计或制造的改变而变更设计载荷时,应根据本章要求进行设计验证试验。制造厂应评价所有设计或制造方面的改变,以确定是否影响额定载荷。这种评价应形成文件。5.6记录
设计验证记录和数据应按11.1的规定加以控制。6材料要求
6.1总则
本章叙述主承载件和承压件所用材料的验收准则、性能和加工要求。6.2书面规定
用于制造本标准涉及产品的材料应满足或超过设计要求的书面规定。6.3力学性能
6.3.1冲击韧度
6.3.1.1按ASTMA370的要求进行冲击试验。6.3.1.2必要时使用非标准冲击试样,验收准则应乘上表3所列的校正因数。非标准冲击试样宽度不-psi.o---- psi.I'max -ton.
1)用英制单位计算Pnux时,式中各单位为:L—ton、o.--775
小于5mm。
GB/T17744—1999
表3非标准冲击试样的校正系数
试样尺寸,mmXmm
10.0×7.5
10,0×5.0
校正系数
6.3.1.3设计工作环境温度低于-20℃时,采用附加冲击韧度要求。见附录A的附加要求SR26.3.2厚度方向的性能试验
设计对厚度方向性能要求时,应根据ASTMA770对材料进行厚度方向断面收缩试验。最小收缩率应为25%。
6.4材料验证
本标准要求的力学性能试验,应在与所代表零件经相同热处理且属同一批次的试棒上进行。试验应按ASTMA370或等效的国家标准,在材料最终热处理状态下进行。为了材料验证试验的目的,焊后消除应力处理不看作热处理,材料试验可在不改变热处理状态的应力处理之前进行。零件的试棒尺寸用等效圆(ER)法确定。确定简单形状实体和空心零件等效圆的基本模型如图1所示,所示形状均可用于试验试棒。确定复杂截面形状等效圆的步骤如图2所述。根据热处理条件下零件的实际尺寸来确定其等效圆尺寸。验证试棒的等效圆应不小于零件的等效圆尺寸,要求等效圆不超过127mm(5in)的验证试棒除外。确定ASTMA370基尔试块尺寸的步骤如图3所述:试棒可与所代表的零部件是一体或分体,也可是解剖零件的一部分。试棒应与所代表的零件经相同的热处理且属同一批次。
试样切取部位,对于实体试棒,在距表面1/4厚度内切取;对于空心试棒,在距试棒表面3mm(%in)的最厚截面处切取。拉伸试样的计量长度和冲击试样的切口应距试棒端面至少1/4个试棒厚度。bZxz.net
解剖产品零件取样应在距零件表面1/4厚度内的最厚截面处切取。6.5制造
制造工艺应确保零部件重复生产时符合本标推的要求。锻造材料应保证零部件内部组织结构的同-性。热处理应在制造厂或工艺员认可的设备内进行。热处理炉内任一零件应不影响同批次中其他零件的热处理特性。热处理的温度和时间应符合制造厂或工艺员的书面规范。实际热处理温度和时间应有记录,记录应对零部件具有追踪性。注:本标准的附录B提供了热处理设备验收准则的推荐作法。6.6化学成分
应对制造厂书面规定的材料逐炉进行化学成分分析。776
两端开口
正六边形
GB/T 17744 1999
ER= 1. 25 7
当L
注:当L
2)当厚度不相等时计算使用最大厚度。2.5R
长方形或平板
-端或两端封口
注:当D≤63.5mm(2.5in)时,ER=2.57当 D≥63.5mm(2.5 in)时,ER=3.5 T距表面1/4 厚度切取试棒
等效圆模型
简单截面
ER一等效圆摔直径
采用以下步骤确定复杂截面的等效圆:1简化零部件为简单截面;
GB/T 17744—1999
LER-12
交叉构件的ER计算值
可用交叉点处的测绘值代替
2换算简单截面为ER值,交叉构件的ER值等于与ER交叉面外切且垂直较大ER截面圆的直径,如右上图所示,
简单零部件和交叉构件的最大ER值,应作为复杂截面的ER值。3
图2复杂形状的等效圆
单位:mm(in)
2. 5R 69. 02(2. 7)
给定:ER=63.5mm(2/%in);
由图1:ER-2.3R得出:
(62880521
7焊接要求
7.1总则
$30.48(1.2)
R27. 94(1.1)
R-ER/2.3=27.61 mm(1.007 in)
1. 7 R=1. 75×27. 61 48. 32 mm(1. 902 in)2.5 R2.5X27.61=69.02 mm(2.718 in)3.5 R=3.5X27.6196.63mm(3.805 in)构成基尔试块
图3基尔试块尺寸展开图
本章叙述主承载件和承压件的焊接和补焊要求,包括对辅助焊接的要求。7.2焊接限定条件
GB/T 17744 --1999
所有零部件的焊接应按ASMEIX、ANSI/AWSD1.1或ASTMA488的焊接工艺进行,应由本标规定的鉴定合格的焊接操作者和焊机进行。非上述标准所列母材的焊接工艺应以可焊性、拉伸性能或成分为基础单独或作为一组进行评定,延展性不能满足ASMEIX中弯曲试验要求的母材,弯曲试验应按下列方式进行:母材热处理后有延伸和强度要求的弯曲试棒,应试验至破坏。弯曲试棒的边缘弯曲应不大于5°。7.3书面规定
焊接应按书面焊接工艺规程进行,并按有关标准进行评定。爆接工艺规程应包括相关标准所列的基本因素、次要因素和补充因素(如要求,见ASMEIX)。工艺评定记录应记录评定试验焊接工艺的基本因素和补充因素(如要求)。焊接工艺规程和工艺评定记录应按本标准第11章的要求保存。7.4焊料控制
焊料应符合美国焊接协会或焊料生产厂的规定,制造厂应具有贮存和检验焊料的书面规程。低氢型材料应按生产厂的建议贮存和使用,以保持其原有的低氢性能。
7.5焊接性能
工艺评定试验确定的焊缝力学性能应满足设计规定的最低力学性能。要求母材作冲击试验时,也应作为工艺评定的要求。焊缝和母材热影响区的试验结果应符合对母材的最低要求。辅助焊缝仅要求做冲击试验材料的热影响区满足上述要求。焊接试验应在焊后热处理状态下进行。7.6焊后热处理
零部件的焊后热处理应按焊接工艺规程进行。7.7质量控制要求
焊接质量控制应符合本标准第8章的要求。7.8组焊的特殊要求
焊接型式和焊缝尺寸应满足制造厂的设计要求,并应在制造厂焊接工艺规程中作出书面规定。7.9补焊的特殊要求
除7.2~~7.7的规定外,下列要求也适用。7.9.1方法
应有适当的方法评定、消除和检验补焊后的不合格品。7.9.2熔合
选定的焊接工艺规程(WPS)和补焊方法,应能保证母材完全熔合。7.9.3锻件和铸件
补焊应按制造厂的书面焊接工艺进行。补焊工艺应按用户的要求形成文件。补焊前制造厂应有下列允许补焊的文件:
a)缺陷类型;
b)缺陷尺寸限制;
c)主/次修补的定义。
焊前坡口和随后的补焊应满足本标准第8章的质量控制要求。7.9.4热处理
补焊工艺规程应确定补焊的实际顺序和焊后热处理。8质量控制
8.1总则
小提示:此标准内容仅展示完整标准里的部分截取内容,若需要完整标准请到上方自行免费下载完整标准文档。

标准图片预览:
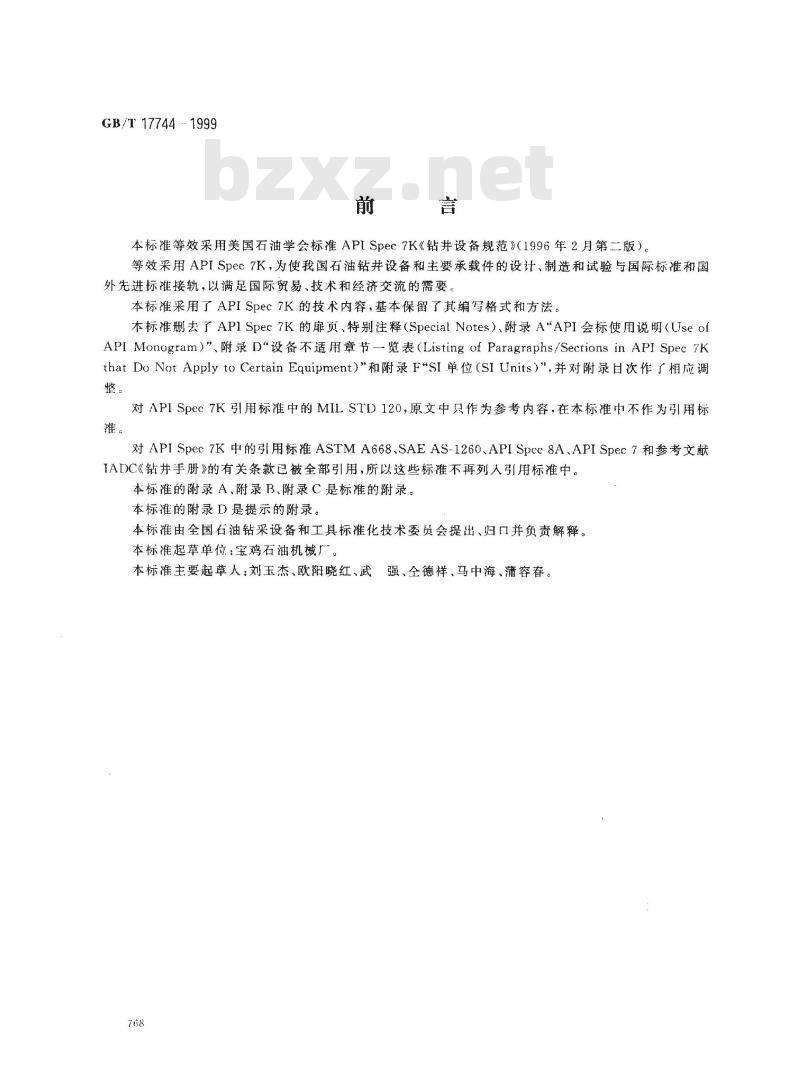

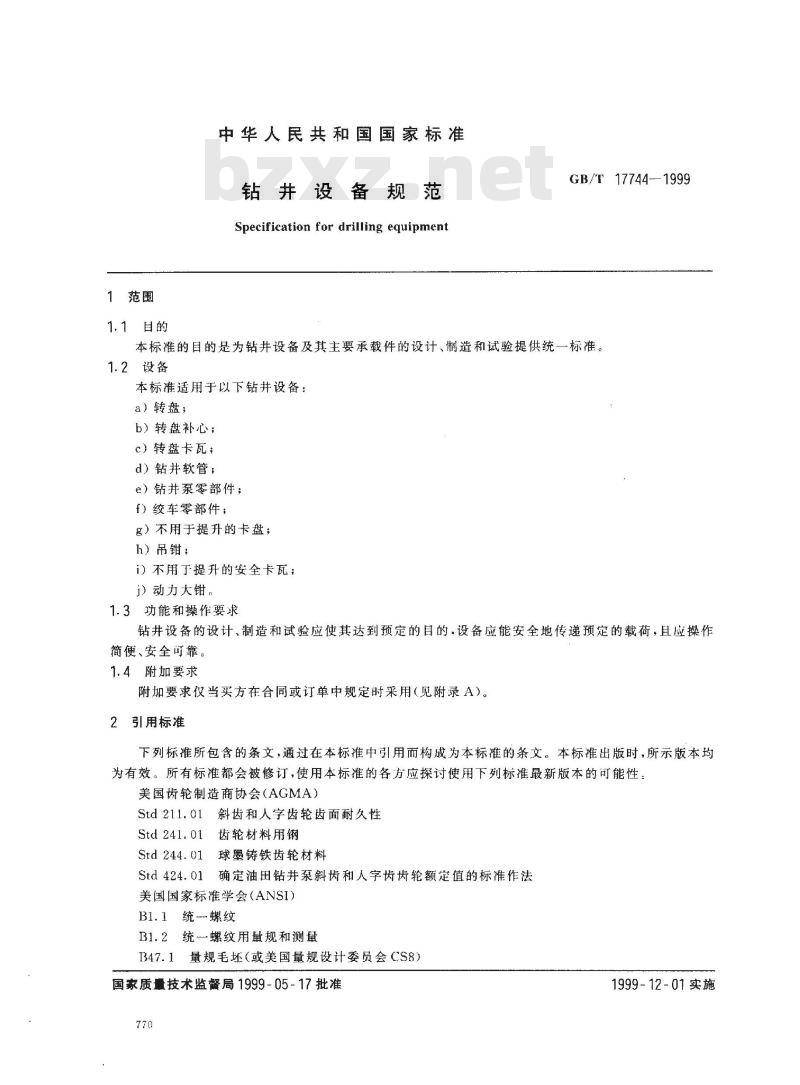
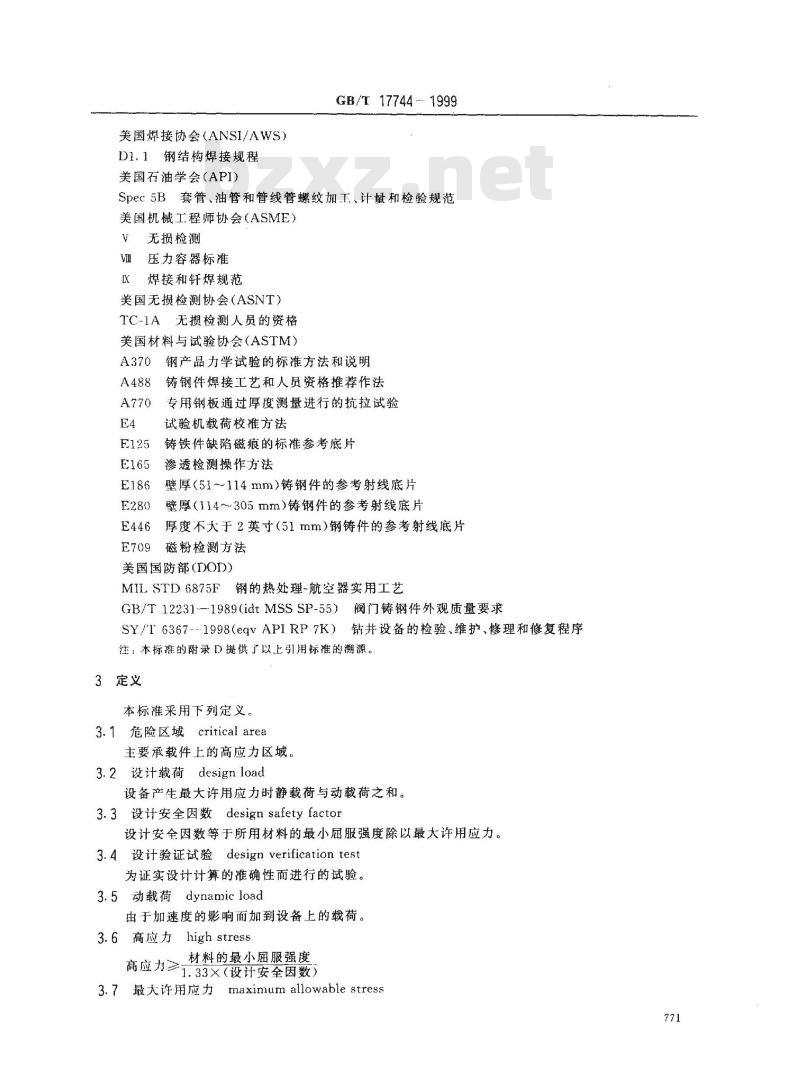
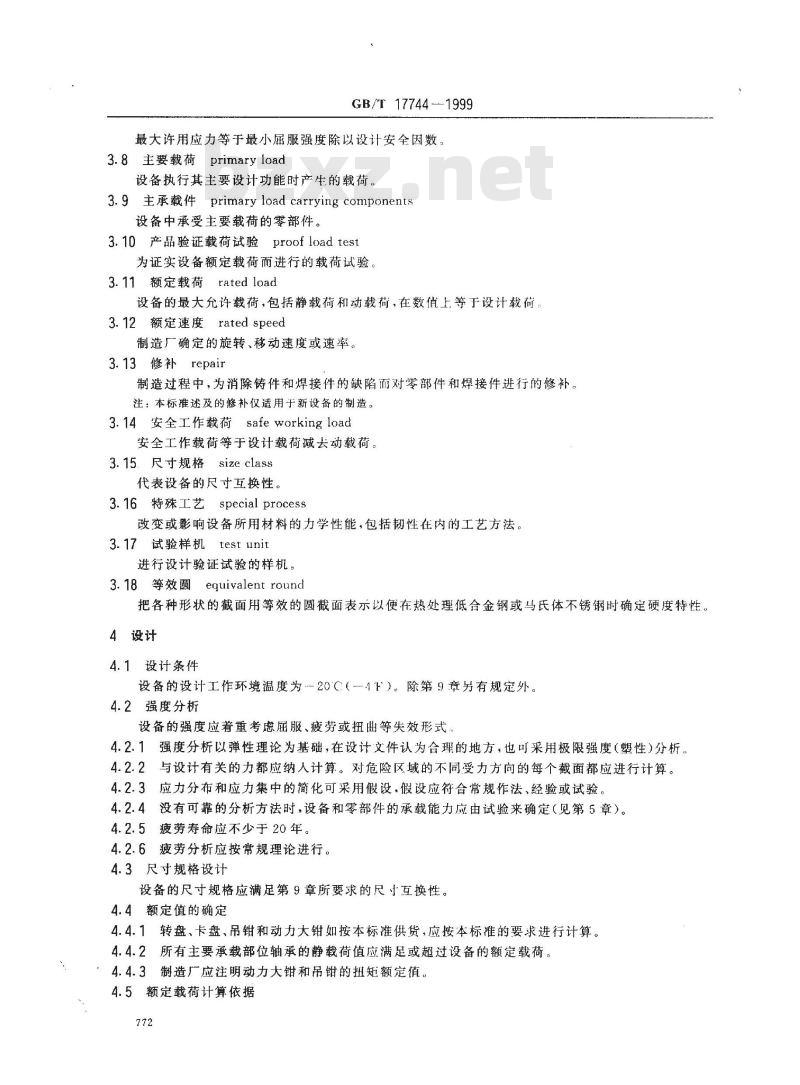
- 其它标准
- 热门标准
- 国家标准(GB)
- GB/T16739.2-2014 汽车维修业开业条件 第2部分 汽车综合小修及专项维修业户
- GB50067-2014 汽车库 、修车库 、停车场设计防火规范
- GB/T15456-2019 工业循环冷却水中化学需氧量(COD)的测定 高锰酸盐指数法
- GB/T4208-2017 外壳防护等级(IP代码)
- GB13851-2022 内河交通安全标志
- GB2894-2008 安全标志及其使用导则
- GB16327-1996 肉干、肉脯卫生标准
- GB/T5009.70-2003 食品容器内壁聚酰胺环氧树脂涂料卫生标准的分析方法
- GB/T38130-2019 铂合金首饰铂含量的测定钇内标ICP光谱法
- GB/T14643.5-1993 工业循环冷却水中硫酸盐还原菌的测定 MPN法
- GB15558.1-2003 燃气用埋地聚乙烯(PE)管道系统第1部分:管材
- GB/T5564-1994 橡胶、塑料软管低温曲挠试验
- GB/T13869-2017 用电安全导则
- GB/T50010-2010 混凝土结构设计标准(2024年版)
- FZ/T01057.9-2012 纺织纤维鉴别试验方法 第9部分:双折射率法
- 行业新闻
- 专家称忽视XRP将错失史上最大的财富转移
- Bonk 币最新行情:价格飙涨、空头回补与技术面揭秘
- 加密货币大佬预测比特币价格将跌破10万美元,山寨币将面临末日
- 在市场低迷之际,PENGU暴涨10%——但回调可能即将来临的原因如下
- 2025年7月6日Celestia(TIA)价格预测:再度跌破后多头能否守住1.45美元?
- XRP面临2.38美元关键阻力位,27.5亿代币蓄势待发
- 比特币突破10.9万美元关口 下一阻力位剑指11.2万美元
- 等待仍在继续:SEC暂停灰度ETF为加密货币敞口带来新不确定性
- Ripple首席技术官打破沉默,解释Ripple命名的选择
- OKX支持BONK交易吗?平台热点与操作指南
- 分析师预测,由于成功通过审计,Ruvi AI(RUVI)将比预期更快达到1美元,币安币(BNB)能跟上吗?
- Chainlink价格预测:LINK突破200日均线,有望冲击18美元
- 为什么比特币向历史新高冲刺可能还有更多上涨空间
- ChatGPT预测2025年7月31日XRP价格
- 2025年最佳加密货币:今年迄今表现最佳的加密货币
请牢记:“bzxz.net”即是“标准下载”四个汉字汉语拼音首字母与国际顶级域名“.net”的组合。 ©2009 标准下载网 www.bzxz.net 本站邮件:bzxznet@163.com
网站备案号:湘ICP备2023016450号-1
网站备案号:湘ICP备2023016450号-1