- 您的位置:
- 标准下载网 >>
- 标准分类 >>
- 铁路运输行业标准(TB) >>
- TB/T 2985-2000 金属材料的动态撕裂试验方法
标准号:
TB/T 2985-2000
标准名称:
金属材料的动态撕裂试验方法
标准类别:
铁路运输行业标准(TB)
标准状态:
现行出版语种:
简体中文下载格式:
.zip .pdf下载大小:
11.38 MB

点击下载
标准简介:
TB/T 2985-2000.
1范围
TB/T 2985规定了金属动态撕裂试验用装置、试样和试验方法。
TB/T 2985适用于最小厚度为5mm的金属材料的动态撕裂试验。
2引用标准
下列标准所包含的条文,通过在本标准中引用而构成为本标准的条文。本标准出版时,所示版本均为有效。所有标准都会被修订,使用本标准的各方应探讨使用下列标准最新版本的可能性。
GB/T 3190-1996 变形 铝及铝合金化学成分
GB/T 3191-1998铝及铝 合金挤压棒材
GB/T 4161-1984金属材料平面应变断裂韧度Kec试验方法
3定义
3.1动态撕裂功 Dynemic Tear Energy
按本试验方法进行试验时使动态撕裂试样断裂所需要的能量。
注:1对于摆锤式试验机,动态撕裂功是 摆锤的初始势能与最终势能之差。
2对于落锤试验机,动态斯裂功是由经标定的测功系统测定的落锤的切始势能与最终势能之差。
3.2剪切面积百 分数PercentShear Fracture Appearanice
剪切面积百分数是指以切变模式断裂的截面占整个截面积的百分比。整个截面积既可以是断裂之前的试样截面面积,也可以是试样断裂面的投影面积。
4概述
动态撕裂试验系以三点弯曲方式对单侧缺口的简支梁施加冲击载荷的一种试验。 试验中应记录断裂过程中损失的总能量。
在对金属材料进行动态撕裂试验时可使用摆锤式或落锤式试验机。
4.1作用与意义
动态撕裂功值是抵抗断裂快速发展的一-种度量。 对于大量的使用场合来说,主要关心的是裂纹从一个尖锐缺口扩展到几乎整个板厚的过程中金属材料是否能够产生足够大的抗力。
在本试验方法中,提供了一条足够 长的断裂路径,以致于试验的结果可以作为该项性能的度量。

部分标准内容:
TB/T2985—2000
金属材料的动态撕裂试验方法
2000-03-29发布
中华人民共和国铁道部发布
2000-11-01实施
TB/T2985—--2000
引用标准
3定义
5装置
6试样
装置的校准
8试验方法
9报告
附录A(提示的附录)
附录B(提示的附录)
附录C(提示的附录)
测量缺口压制尖端的深度
压制缺口尖端
确定剪切面积百分数
TB/T2985—2000
本标准等效采用美国ASTME604—83(1994复审)《StandardTestMethordForDynamicTearTestingofMetallicMaterials》(金属材料的动态撕裂试验方法)。本标准与ASTME604—83(1994复审)的主要差别如下:1引用标准均引用我国的相应标准。2考虑到手动液压机在国内使用不多,本标准在附录B中删去了用手动液压机压制缺口尖端的内容。
本标准的附录A、附录B和附录C均是提示的附录。本标准系首次发布。
本标准由贼墅堰机车车辆工艺研究所提出并归口。本标准起草单位:戚墅堰机车车辆工艺研究所、戚墅堰机车车辆厂。本标准主要起草人:未忠明、王法度、蒋田方、谢兴年。1
中华人民共和国铁道行业标准
TB/T2985-2000
金属材料的动态撕裂试验方法
本标准规定了金属动态撕裂试验用装置代样和试验方法
本标准适用于最小厚度为5mh的金属材料的动态撕裂试验2引用标准
下列标准所包含的条文,通过在本标准中引用而构成为本标准的条文。本标准出版时,所示版本均为有效。所有标准都会被修订,使用本标准的各方应探讨使用卡列标准最新版本的可能性。
GB/T 3190--1996
变形铝及铝合金化学成分
GB/T3191-1998
GB/T4161-1984
3定义
铝及铝合金挤压棒材
金属材料平面应变断裂韧度K北试验方法动态撕裂功
Dynanic
TearEnergy
按本试验方法进行试验时使动态撕裂试样断裂所需要的能量。注:1对于摆锤式试验机,勃态斯裂功是摆锤的初始势能与最终势能之差。2对于落锤试验机,动态斯裂功是由经标定的测功系统测定的落锤的初始势能与最终势能之差。剪切面积百分数 Percentshear.Fracture Appearance3.2
剪切面积百分数是指以切变模式断裂的截面占整个截面积的百分比。整个截面积既可以是断裂之前的试样截面面积,也可以是试样断裂面的投影面积。4概述
动态撕裂试验系以三点弯曲方式对单侧缺口的简支梁施加冲击载荷的一种试验。试验中应记录断裂过程中损失的总能量。在对金属材料进行动态撕裂试验时可使用摆锤式或落锤式试验机。4.1作用与意义
动态撕裂功值是抵抗断裂快速发展的一种度量。对于大量的使用场合来说,主要关心的中华人民共和国铁道部2000-03-29批准2000-11-01实施
TB/T2985-2000
是裂纹从一个尖锐缺口扩展到几乎整个板厚的过程中金属材料是否能够产生足够大的抗力。在本试验方法中,提供了一条足够长的断裂路径,以致于试验的结果可以作为该项性能的度量。4.2用途
4.2.1在作研究开发时,用于评价诸如化学成分、加工方法、热处理或者象成形或焊接之类的加工工艺对新材料或现有材料的抗动态撕裂性能的影响。4.2.2在作使用评价时,只有在建立了动态撕裂功与使用性能之间的关系后,才可以确定某一种材料对某一具体使用场合的适用性。4.2.3对于需要最小动态撕裂功的场合,本试验可供作参考资料,制订验收标准,以及在制造过程中进行质量控制之用。本试验方法标准不涉及某一具体应用场合下应规定多大的动态撕裂功的最小值问题。
5装置
5.1一般要求
试验机应是摆锤式或落锤式的其能量应施加一次打击即足以打断试样。当动态撕裂功大于一次打击的初始能量的80%以上时,该试验值无效。当试样厚度为16mm时,对大多数钢材进行动态撕裂试验所需的能量为2-700-当试样厚度为5mm射为00J。对铸铁和铝合金进行动态撕裂试验所需的能量可比上述对大多数钢材试验时所规定的能量值小20%。5.1.1速度限制
动态撕裂试验可在4.0~8.5m/s的速度(指锤头打击到试样时的速度)范围内进行。这个速度范围相当于锤实从高度0.8~3.7m落下时的速度范围。5.1.2试验机应真有校准的标度、图表或直接可读出初始能量值和最终能量值读数或其差值的仪表。标度、图表或直接可读数的仪表,其分度值应为:动态撕裂功值
54~800J
分度值
动态撕裂功的5%
由于摆锤或落锤的重量误差或由于下落高度的误差而造成的动态撕裂功值的误差应不超过1%。空气阻力和摩擦阻力可以通过增加落锤高度来补偿。此时,超过名义值的高度不应大于2%。5.1.3试验机支座和锤头应由萍硬至最小硬度为48HRC的钢制造,且应符合图1中的尺寸要求。落锤侧面与支座之间的间隙应不小于51mm。在下落过程中,落锤刃口中心线应通过支座跨距的中点,偏差应不大于0.80mm落锤刃口应垂直于试样的纵向轴线,允许偏差为0.01rad。当落锤刃口接触试样时,刃口应同置于支座上的试样的长方形平面平行,允许偏差为0.005rad。对摆锤式试验机,支座垂直支承面应与水平支承面垂直,允许偏差为0.0025rad。两支座的垂直支承面与水平支承面应分别共面,允许偏差为0.125mm,并且互相之间应平行,允许偏差为0.002rad。5.2中心距确定
摆锤式冲击试验机的摆轴中心至摆锤打击中心的距离应与摆轴中心至试样中心的距离一致,允许偏差为摆轴中心至摆锤打击中心距离的1%。当摆锤自由悬挂时,其打击刃口离试样侧面的距离应小于5mm。
5.2.1打击中心的位置可以根据如下方法来确定:使用能读出0.2s的秒表或其他适用的计2
TB/T2985-2000
时器,将摆锤提起,使其提起的总角度不大于15°,随后记录摆锤往返100次的时间,按下式决定打击中心
g=0.2485p2
式中[-—摆轴到打击中心的距离,mp—摆锤往返一次的时间,s;
g-重力加速度,9.81m/s2。
5.2.2对于双摆锤试验机,每一个摆锤的打击中心应分别决定。5.3防护
5.3.1支座周围应设置安全护网,以防止断裂的试样飞出。(1)
5.3.2必须小心保护工作人员免受悬空的摆锤、落锤和飞出的试样的伤害,以及由于试样加热和冷却引起的伤害。
6试样
6.1试样选取
应按照GB/T411984规定的方法对试样在基本金属中的取向作出说明。如果产品的厚度天手16mm,购16mm厚的试样应是标准试样6.2试样制备
6.2.1试样尺寸
试样的尺寸及允许偏差应符合图1的规定。但试样的厚度B可从5mm到16mm。AOM
长度L(rmm)
宽度W(rmm)
厚度B(mm)
角度α
支座半径为12.7±0.8
允许偏差
图1动态撕裂试验用试样的尺寸、允许偏差及支座间距3
TB/T2985—2000
6.2.2应采用加工方法制出缺口,以便在试样上造成28.5mm的断裂路径。缺口尖端应认为是名义断面的一部分。缺口的形状与尺寸由图2规定。(D-M)
净宽度(W
加工的缺口宽
(mm)
加工的缺口银部角度
加工的缺口根部圆角半径
尖端深度
压制的全
压制的类端角度
压制的尖端圆角半径
6.3缺口的制备法
6.3.1粗加工
(mm)
(mm)
图2动态撕裂试样缺口的形状与尺寸允许偏差
将缺口加工到图2所示的尺寸。缺口的顶角部分,特别是根据圆弧的最终切割应该采用精密砂轮、刀具和电花痴工,或其他任何一种能确保最后的圆角半径小于0.13mm的方法加工。这些加工作业通常奇以对一组试样同时进行。6.3.2压制缺口尖端bzxZ.net
将缺口尖端压成图所宗尽寸的作业应该对试样一个个地进行。可以用磨到图3所示尺寸的高速钢(硬度最小为品,HR)刀片来压制缺口尖端,随后再打磨掉毛刺和尖锐的边缘。27±0.025
40*±5°
尖端圆角
R≤0.025
图3压制动态撕裂试样缺口尖端用的刀片4
TB/T2985-—2000
可以使用任何一种能使刀片压出规定深度的加载装置。为完成这一压制作业所需的力同试样的硬度和厚度有关。
所需的力可用下列公式近似得出F=2.9ah-B
式中F一压制缺口尖端所需的力,Nab被试材料的抗拉强度,MPa;
B-试样的厚度,mm。
注:1为作出缺口尖端而规定的刀片压制法通常只限用手硬度低于36HRC的金属材料。2测定压制尖端的深度和压制缺口尖端的推荐做法在附录A和附录B中规定。7装置的校准
7.1单摆锤试验机
在某个最能与诸如磅称失平或测力传感器这类称重装置起作用的一点上将摆锤支在水平位置(离静止位置90主),测定其重量,精度要求为0.4%操作时要小心,务使承载支承和称重支承处的摩擦妇减至最小。测定力壁的长度(即摆轴中心与通过支承点的垂直线之间的水平距离),精度要求为0.1%。任何一个确度时的势能可按下式计算S
式中E势能;
f—测出的摆锤重量,N;
L—力臂长度m;
E = f-L(1- cosβ)
β—摆锤从首由悬挂状态的静止位置向上回转所转动的角度。如果摆轴中心与摆锤重力中心之间的距离已知且误差在0.1%套内时,可以使用一种代用方法。在与重力护心成一条线的某一点土水平地支起摆锤,测定摆锤的重量,允许偏差为0.4%。此时,任一点的势能即等于重量乘以摆锤的重力中心从静此位置抬起的高度。7.1.1试验机势能因摩擦和空气阻力造成的损失不应超过原势能的2.0%。摩擦和空气阻力损失即是摆锤开始位置时的势能与摆锤莞成一次无试样时的摆动后的势能之差。补偿摩擦和空气阻力损失,使摆锤无试样释放时指示出零势能。7.1.2打击速度
不考虑摩擦时,按如下公式确定试验机的打击速度p(2gh)1n
式中g——重力加速度,m/s;
锤头刃边的起始升高量,m;
一打击速度,m/s。
7.2双锤头试验机
应按7.1规定的方法校准摆锤和砧摆。应在没有试样的情况下校准贴摆。按7.1.1规定的方法确定和补偿因摩擦与空气阻力而损失的能量。7.3立式落锤试验机
试验机的尺寸应该使落锤在碰到试样后,最终能量测量前有一最小为51rmm的垂直行程,以及在如图4所示的止动块被触及之前有70mm的垂直行程。7.3.1需要对每一组由同一根棒料加工的铝块进行标定。对由每-根棒料制取的铝块加以5
TB/T2985—2000
分开,并作出识别标记。一批中的铝块的原始横断面积之差不应大于0.2%。在试验前后测定铝块的平均高度,并记录测定结果,误差不应大于0.013mm。在标定范围内,在高度增量不超过305mm且不用试样的情况下通过重复试验,画出吸收能量与铝块变形量之间的关系图。将每一一次试验的两个铝块的变形量加以平均;多次试验时,每一高度位置的变形量平均值靶块
光束传感器
W.=12.7mm
之差不应超过0.075mm。计算吸收能量,即锤头重量乘以铝块顶面到锤头上打击铝块的表面之间的高度。在标定范围内将各数据点连成光滑曲线,以表示吸收功与铝块爱形量之间的关系。铝块的尺寸应这样来快定,即应使一块铝块在标定范围内的任一点工的刚度如下动态撕裂功
≤74J
每一铝块的刚度
136/mn
止动块
止动块
图4.垂直落锂式动态断裂试验机的锤头、黏座、铝块、无束传感器的位置关系要达到这样的敏度,当两铝块的吸收能量小于1400了时,可以使用两块原始高度为40mm和原始直径为13mm的铝块。铝块的材料可以是GB3190—1996标准中的1060、1100和6061,其状态为:0,即43℃退火后炉冷。动态撕裂试样的试验应同锦块一起在与标定时同样的温度(允许偏差为60)下进行。7.3.2摩擦和空气阻力损失不应使打击速度降低1%(按7.1.2计算的打击速度)。可以通过调整吸收功与铝块变形之间的标定曲线,或增加落锤高度以达到按7.12计算的无摩擦条件下的速度的办法来补偿摩擦和空气的阻力损失。7.3.3光束传感器速度测量装置的校准动态撕裂功可以通过测定打击前与试样断裂后的速度的办法来取得。通过测定已知宽度的目标靶遮断一束窄光束所需的时间来确定锤头的速度。在试验机标定范围内锤头的指示速度或计算速度应等于按考1计算得出的速度,两者之差应在1%范闺内。8试验方法
8.1在-75℃~+100℃的温度范围内,试验应用8.1.1和8.1.2规定的方法。8.1.1试验前,将试样完全浸在温度为所需试验温度主i℃的适当保温槽中最少15min。试样间距至少应等于试样的厚度。应将水平放置在保温槽中的试样置于离槽底至少25mm的网框中或筛板上。应采取措施使槽内介质循环流动,以确保槽内温度均勾一致。注:也可以使用其他的加热和冷却方法,只要这些方法能用相同的时间使试样达到所需的温度。8.1.2从保温槽中取出试样,此动作应在10s内完成。如果试样在保温槽外停留的时间超过10s而未能进行试验,则应将未损伤的试样重新放入保温槽内至少10min。切勿用与试验温度明显不同的装置来处理试样上的缺口处。8.2对于超出8.1规定范围的温度,应将试样在打击时的温度维持在所需试验温度±1℃的范围内。
8.3将试样放置在支座的支承面上使锤头的中心线与试样缺口的项端对准,允许偏差为0.86
TB/T29852000
8.4如果试样在试验机里卡住,则试验结果不算。此时应彻底检查试验机的标定精度。8.5如有需要,断裂表面应用目视或使用仪器通过确定切变断裂断面所占的比例来评定“切变断裂断面的百分比率”。为确定切变断裂断面的百分比率所用的方法应由用户与生产方商定。附录C即是一种确定切变断裂断面的百分比率的方法。9报告
试验报告应包括材料标识、试验温度试样厚度以及动态撕裂功。如有需要,试验报告还应包括:试样在产品中的取向、产品的厚度、熔炼炉号以及剪切面积百分数。HOUSE
A1引言
TB/T2985--2000
附录A
(提示的附录)
测量缺口压制尖端的深度
在动态撕裂试样上缺口压制尖端的深度会减小试样的宽度尺寸。16mm的动态撕裂试样的名义净宽度在加工出缺口后,在压出尖端之前为28.5.mm。压制尖端会减小净断面约1%,或者名义值为0.25mm。由于压痕深度的公差很严,需要对选取的试样精确测量压制缺口的深度,这样的测量可以用精度为0.013mm的光学仪器进行。必须小心除去加工好的缺口上的所有毛刺,以便得到精确的压制尖端的基准点。用以测量缺口尖端的另-一个基准点既可以是试样上的某一条边,世可以是刻在试样上的一条细线。A2
用光学比较仪测量压制尖端的深度该法使用一放大20或50×的反射图象和试样两侧面上的识别标记。方法如下:A2.1将一块1~2nm厚的薄板定位于工作台上作为试样测量面的可重复使用的基准挡块。A2.2将试样贴靠挡块,将工作台定位好,使挡块的边与观察屏幕上的基准线对齐,然后将工作台上的干分表置零位。挡板上的尖角是定位试样边的一个很方便的基准。A2.3通过使用一适当的量块以补偿工作台的大部分位移,测量基准边与加工好的缺口顶端之间的距离。
A2.4记录加工好的缺口顶端到基准线之间的初始距离。A2.5将试样翻身,重复A2.2,A2.3和A2.4。A2.6使用附录B中介绍的方法之一,将刀片压进试样里。A2.7按A2.2的做法将试样放置在工作台上,并测量基推线与压制缺口尖端之间的距离。该项测量要在试样的两侧进行。A2.8压制缺口尖端的深度即是按A2.3和A2.7所得测量结果之差。试样两面上的压制缺口尖端深度应处于图2所示的尽封范围内。A3,用带刻度的显微镜测量压制缺口尖端的深度使用滑标千分尺、工具显微镜或首镜千分尺在放大倍率为20×~50×下进行测量。方法如下:
A3.1在试样的两面离加工缺口的项端约2.5mm处刻一条细线。可使用尖头刀或镶嵌金刚石的刻刀来刻出细线。
A3.2在试样上作出标记,使得试样的两个面都能得到识别。A3.3试样的两个面上测量从加工缺口顶端到刻线之间的距离。A3.4
按附录B中所述的任何一种方法压制缺口尖端。A3.5
测量试样的两个面上压出的缺口尖端到刻线之间的距离。压制缺口尖端的深度即是按A3.3和A3.5所得测量结果之差。压制尖端的深度应处A3.6
在图2规定的尺寸范围内。
B1.引言
TB/T2985—2000
附录B
(提示的附录)
压制缺口尖端
应使用能控制载荷或控制位移的液压加载机或机截加载机在动态撕裂试样上压制如图2所示几何形状和尺寸的缺口尖端。在钢试样上压出缺口尖端所必需的力取决于材料的届服强度和应变硬化特性处在13kN至36KN之间。加载机头部的位移或移动的头部与试样之间的位移可以用作压制缺口的控制参数,但是加载机的卖部行程与缺口的深度是没有直接关系的。因此,当测量实际的缺口深度蔚,应便用附录A中介绍的方法多一在加压前后对试样进行测定。
使用大吨位压力机和能控制缺口深度的定尺寸的刀片和试样来压出缺口尖端可以使用最小吨位为36kN或更大吨位的液压机,并按本方法压制缺口尖端。该法要求试样加工到比图1规定的更为严格的宽度尺寸公差。B2.1试样缺口深度多的允许偏差为主0.025mm。将刀片磨到比缺口的深度长0.25mm。B2.2将刀片放人缺口,并压进试样,直到刀片与试样齐平。当压制工作完成时加载压力会急剧提高,这时不需要记录位移和加载读数。B2.3每次加压后,检查刀片的锐利程度,以确保符合图的尺寸。用万能试验机和刻出的基准线来压制缺口尖端B3
B3.1从所有同级别钢的一组试样中选取三根试样,在已加工好的缺下面0.25mm处刻出根短细线(2.5mm长)。线可在、10倍的放大镜下用锋利的刀片来刻划。可用钳工的蓝色染料来改善刻线的可见度
B3.2将刀片安装在试验机的上横梁里,将试样放在下平面上,试样的缺口向上。B3.3将刀片刃口压入加工好的缺口里,直到刃口碰到刻线。刃口的移动可用10×的放大镜观察。
B3.4记录将刀片压到刻线所需的力。B3.5按附录A规定的方法测定实际压出的缺口深度。B3.6对第二根试样重复B3.3,B3.4和B3.5。如果两根试样的压出的尖端深度符合图2规定的尺寸要求,则进行B3.7;否则,对第三根试样重复B3.6。B3.7使用按B3.4得出的力对余下的试样压制缺口尖端。每一次施压后,检查刀片的锋利程度。对低强度钢(屈服强度约为280MPa)每10根施压后检查缺口深度,对高强度钢则检查频次应增多。
小提示:此标准内容仅展示完整标准里的部分截取内容,若需要完整标准请到上方自行免费下载完整标准文档。

标准图片预览:
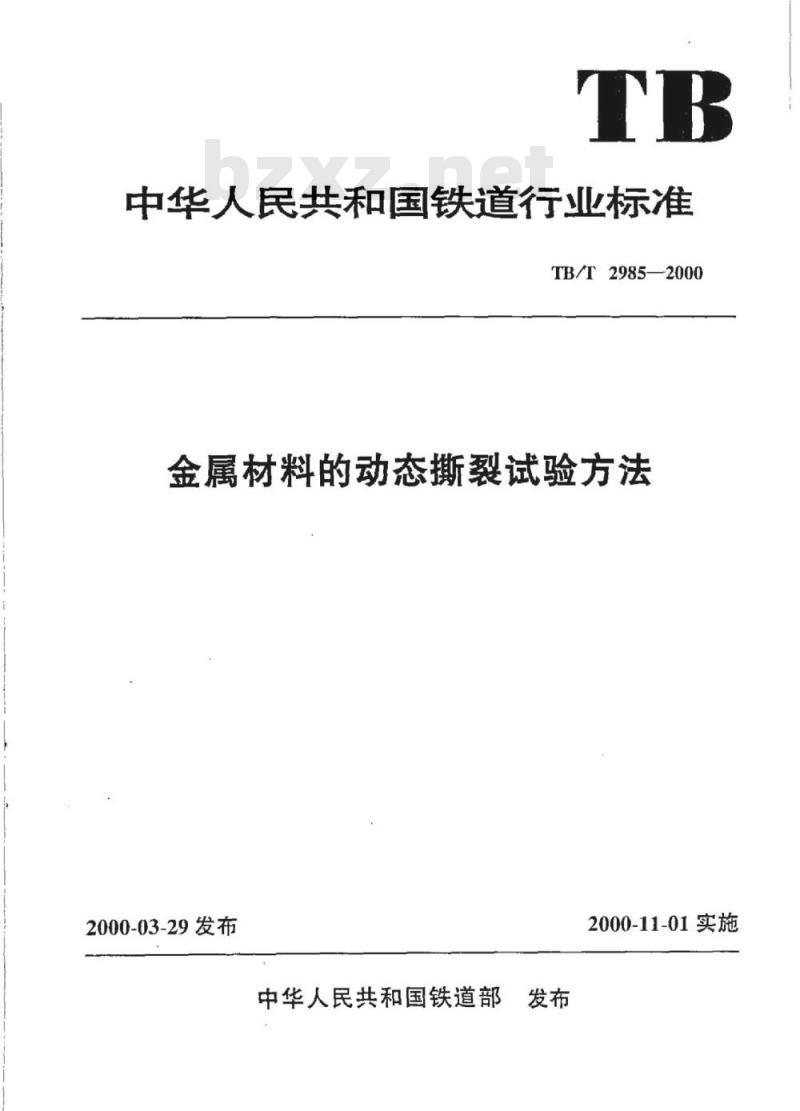
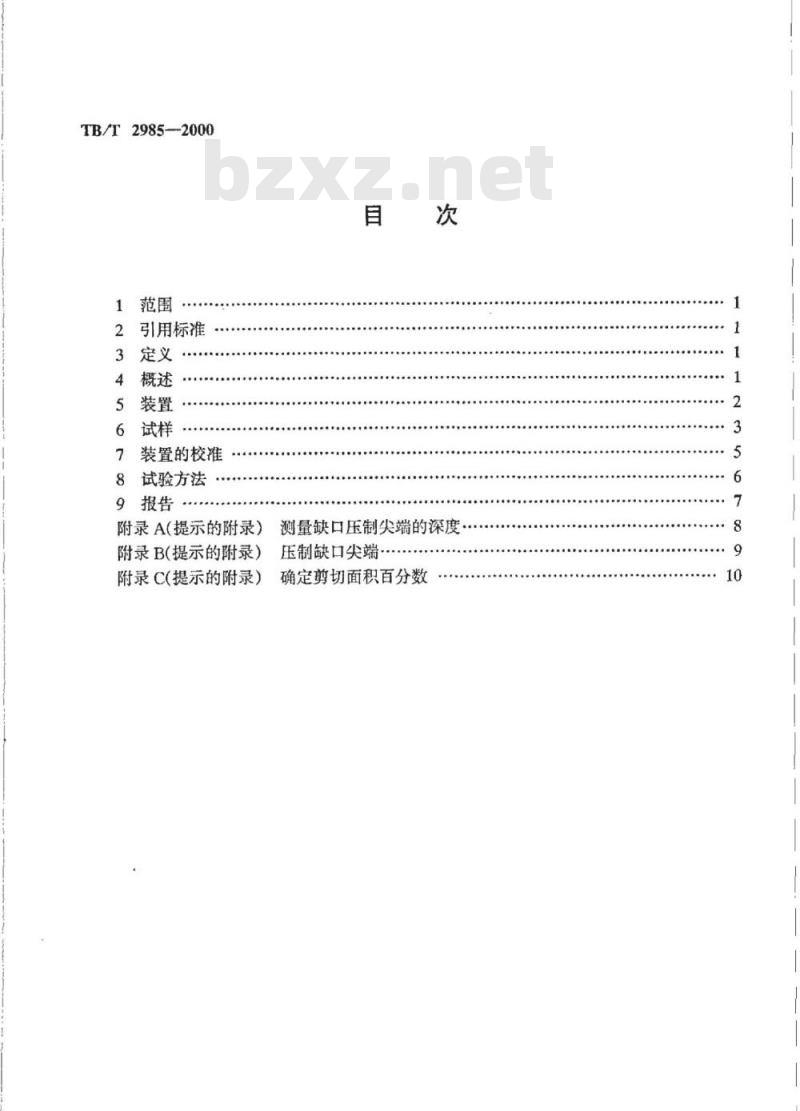
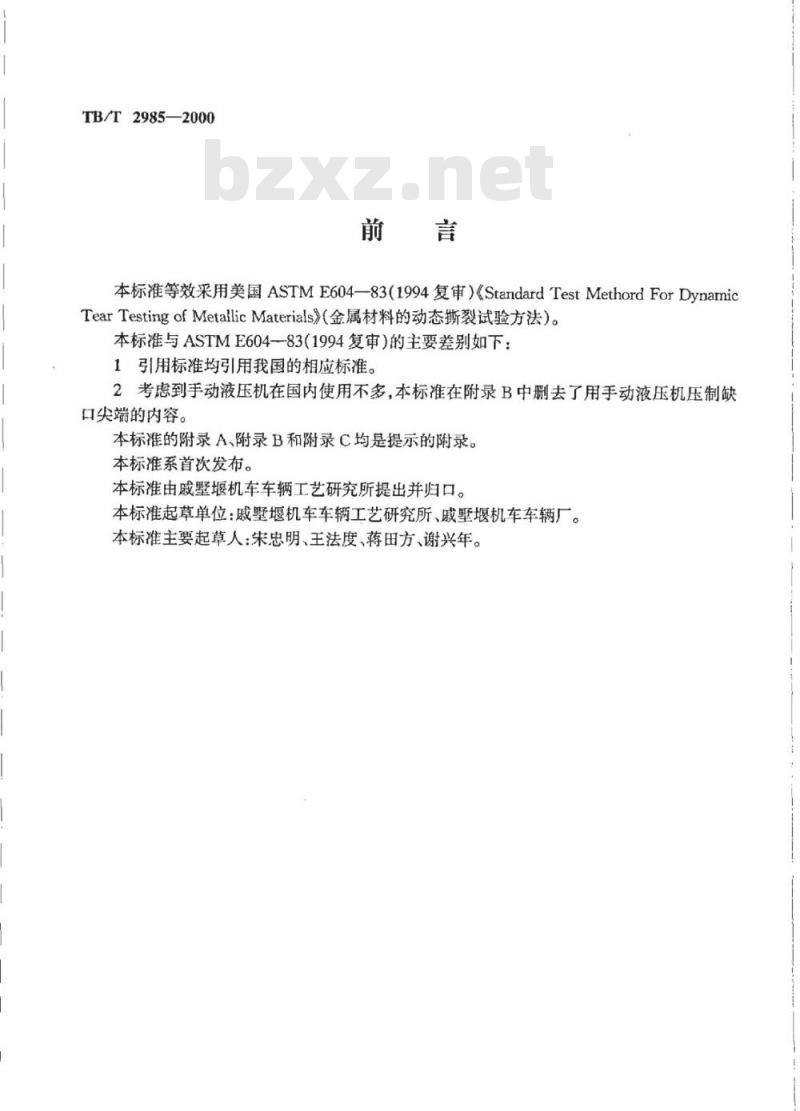
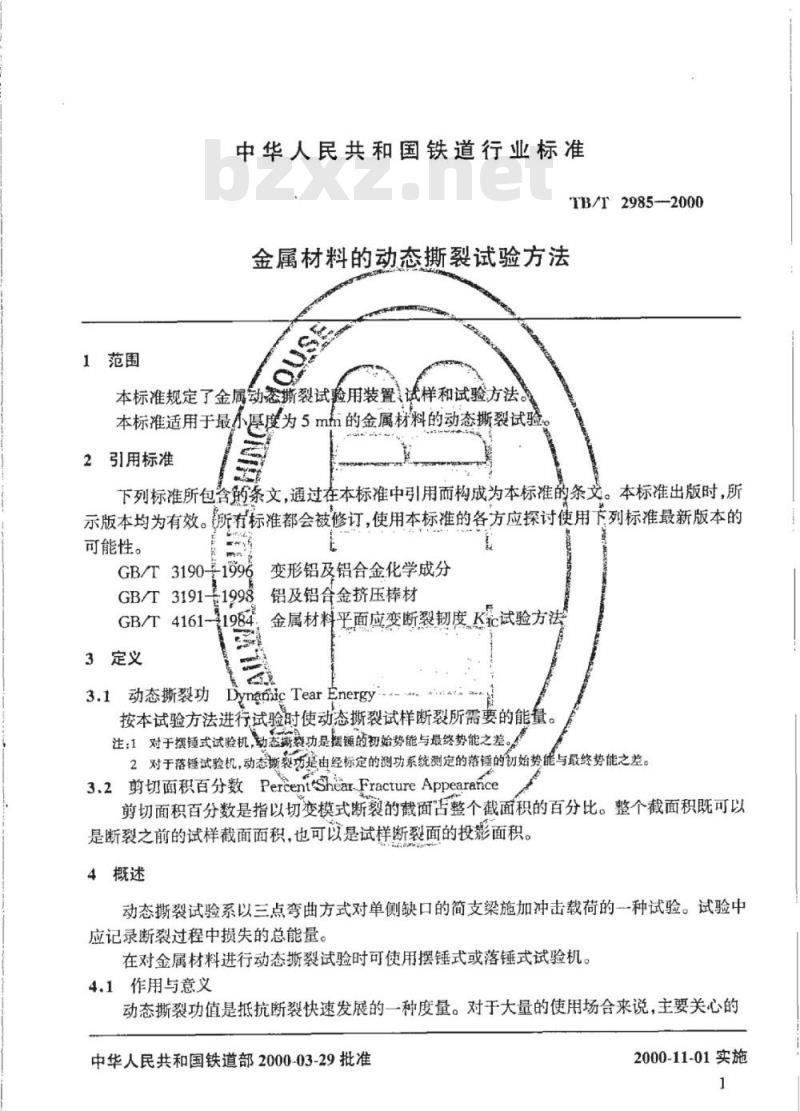
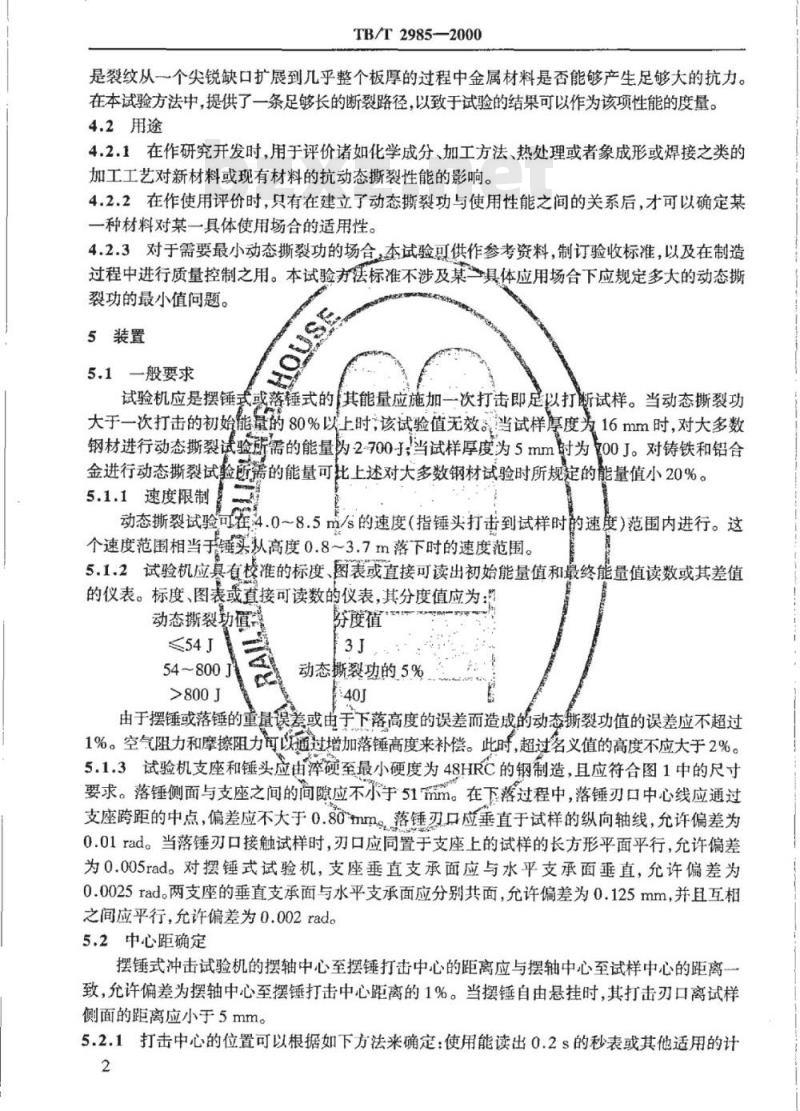
- 热门标准
- TB铁路运输标准
- TB/T3568.1-2021 铁路无损检测材料 第1部分:磁粉检测材料
- TB/T30002-2020 铁路调车作业
- TB/T1760-1986 客车门锁技术条件
- TB/T3567—2021 铁路车辆轴承塑料保持架
- TB/T2563-1995 内燃机车用柴油机机体清洁度测定方法
- TB/T2769.9-1997 重型轨道车试验方法动力学性能试验方法及评定标准
- TB/T3523.2-2018 交流传动电力机车试验方法第2部分:输入特性试验
- TB/T3522-2018 铁路线路防护栅栏
- TB/T3416.3-2015 动车组编码标识系统第3部分:安装地点与位置的标识
- TB/T1632.4-2005 钢轨焊接 第4部分:气压焊接
- TB/T2658.7-1995 工务作业标准林业作业
- TB/T2686-1995 铁路高温作业人员健康检查规范
- TB/T3170-2007 货车车钩、钩尾框采购和验收技术条件
- TB/T2599-1996 细长钢管内壁涂塑技术条件
- TB/T3269-2011 铁道货车弹性旁承
网站备案号:湘ICP备2023016450号-1