- 您的位置:
- 标准下载网 >>
- 标准分类 >>
- 国家标准(GB) >>
- GB/T 5482-2007 金属材料动态撕裂试验方法
标准号:
GB/T 5482-2007
标准名称:
金属材料动态撕裂试验方法
标准类别:
国家标准(GB)
标准状态:
现行-
发布日期:
2007-02-09 -
实施日期:
2007-08-01 出版语种:
简体中文下载格式:
.rar.pdf下载大小:
439.22 KB
标准ICS号:
冶金>>金属材料试验>>77.040.10金属材料力学试验中标分类号:
冶金>>金属理化性能试验方法>>H22金属力学性能试验方法
替代情况:
替代GB/T 5482-1993采标情况:
修改ASTM E 604-1983

点击下载
标准简介:
标准下载解压密码:www.bzxz.net
本标准规定了金属材料动态撕裂试验试样及其设备、实验机、测试方法和实验结果的处理。 GB/T 5482-2007 金属材料动态撕裂试验方法 GB/T5482-2007

部分标准内容:
ICS77.040.10
中华人民共和国国家标准
GB/T 5482--2007
代替GB/T5482--1993
金属材料动态撕裂试验方法
Test method of metallic materials-Dynamic tear2007-02-09发布
中华人民共和国国家质量监督检验检疫总局中国国家标准化管理委员会
2007-08-01实施
GB/T5482—2007
本标准修改采用ASTME604-83(2002年认可)《金属材料动态撕裂试验标准试验方法》,与ASTME604-83相比主要差异如下:
试验机读数盘的规定;
一删除有关计量的内容;
-增加了附录A和附录B。
本标准代替GB/T5482--1993《金属材料动态撕裂试验方法》,本标准与GB/T5482—1993相比主要变化如下:
增加了前言部分;
一在术语和定义中增加了纤维断面率;压制缺口估算公式中的K值由1.8mm士0.5mm改变为2.4mm士0.5mm。本标准的附录A是规范性附录,本标准的附录B、附录C、附录D是资料性附录。本标准由中国船舶重工集团公司提出。本标准由全国海洋船标准化技术委员会船用材料应用工艺分技术委员会归口。本标准起草单位:中国船舶重工集团公司第七二五研究所、武昌造船厂、江南造船厂。本标准主要起草人:叶宏德、杨小敏、沈权、陈庆垒、张欣耀。本标准的历次版本发布情况为:GB/T5482-1985.GB/T5482—1993。1范围
金属材料动态撕裂试验方法
GB/T5482—2007
本标准规定了金属材料动态撕裂试验试样及其制备、试验机、测试方法和试验结果的处理。本标准适用于测定洛氏硬度值小于36HRC的金属材料或焊接接头试样的动态撕裂能和纤维断面率。
2规范性引用文件
下列文件中的条款通过本标准的引用而成为本标准的条款。凡是注日期的引用文件,其随后所有的修改单(不包括勘误的内容)或修订版均不适用于本标准,然而,鼓励根据本标准达成协议的各方研究是否可使用这些文件的最新版本。凡是不注日期的引用文件,其最新版本适用于本标准。GB/T2975钢及钢产品力学性能试验取样位置及试样制备GB/T3808摆锤式冲击试验机的检验GB/T12778金属夏比冲击断口测定方法JJG130
工作用玻璃液体温度计检定规程JJG141
JJG145
JJG351
工作用贵金属热电偶检定规程
摆锤式冲击试验机检定规程
工业用廉金属热电偶检定规程
JJG368
工作用铜-铜镍热电偶检定规程
3术语和定义
下列术语和定义适用于本标准。3.1
动态撕裂(DT)试验
dynamicteartest
在冲击试验机上,将处于简支梁状态下的动态撕裂试样一次冲断,测量其吸收能量和纤维断面率的试验。
动态撕裂能(DT能)dynamictearenergy动态撕裂试验时试样所吸收的能量,用以表征各特定厚度的金属材料抵抗动态撕裂的能力。3.3
动态撕裂试样断口fracture surfaceofdynamictearspecimen动态撕裂试样冲断后的断裂表面。其宏观形貌一般呈晶状、纤维状(含剪切唇)或混合状。3.4
纤维断面率
percent shear fracture appearance纤维状断口面积与缺口处原始横截面积之比的百分数。4试样及其制备
4.1取样
4.1.1样坏的切取部位和方向应符合GB/T2975或有关技术条件的规定。4.1.2焊接接头试样取样方法按附录A执行。1
GB/T5482—2007
4.2试样
4.2.1厚度为5mm~16mm的样坏,试样应为180mm×40mm×t,保留原轧制表面,其厚度公差执行相应材料的技术条件规定,其他尺寸和公差见图1,厚度t大于16mm的样坏,加工成规格为180mm×40mm×16mm的试样,尺寸和公差见图1。4.2.2对于厚度等于或大于25mm的大型动态撕裂试样及试验机的要求参见附录B。4.3缺口制备
4.3.1试样缺口可用铣削或线切割等方法加工,但一组试样必须采用同一种加工方法。单位为毫米
180±2
全部12
图1动态撕裂试样
4.3.2机加工合格的试样,试验前需用硬度不小于60HRC的压刀压制缺口,压制方法参见附录C。4.3.3试样缺口和缺口项端的压制尺寸及公差见图2和表1压制顶端根部半径
机加工缺口根部半径厂。
图2动态撕裂试样缺口和缺口顶端的压制尺寸2
缺口几何参数
净宽(ba)/mm
机加工缺口宽度ba/mm
机加工缺口根部角度a/()
机加工缺口根部半径r./mm
压制深度D,/mm
压制顶端角度a./(\)
压制项端根部半径r/mm
表1缺口尺寸和公差
压刀的尺寸见图3,刃口应无毛刺和缺陷。4.3.4
图3锐化缺口顶端用的压刀
4.3.5缺口压制深度的测量方法参见附录D4.3.6试样缺口顶端应逐个压制,所需压力可按式(1)估算:p-KXR.Xt
式中:
—压力,单位为牛顿(N);
抗拉强度,单位为兆帕(MPa);Rm
t-试样厚度,单位为毫米(mm);K系数,取K=2.4mm士0.5mm。
5试验机
GB/T5482—2007
其余1.60
40*±5
刃部半轻r≤0.025
5.1动态撕裂试验通常采用摆锤式冲击试验机,其能量应能在一次冲击时将试样打断。也可使用落锤式冲击试验机,试验机有关参数应满足本标准测试要求。注:对大多数钢材进行动态撕裂试验所需能量:16mm厚试样约为3000J。铝合金所需能量比上述能量约低20%。
5.2打击瞬间摆锤的冲击速度应为4.0m/s~8.5m/s3
GB/T5482—2007
5.3摆锤式冲击试验机读数盘的分度应符合表2的规定。表2试验机读数盘
最大冲击能量值
>500~1500
>1500~3000
分度最大值
单位为焦耳
5.4试验机的支座和冲击刀刃的硬度不得小于48HRC,其尺寸及支座跨距应符合图4的规定,5.5由摆锤重量或下落高度引起的动态撕裂能量值的误差不应超过1%,由于风阻和摩擦阻力所造成的能量损失不应超过初始位能的2%。5.6摆锤两个侧面与支座之间的间隙,应不小于51mm。冲击刀中心线的运动平面,应通过支座跨距的中点,偏差不应超过0.8mm。冲击刀刃应垂直于试样的纵轴,其偏差不大于0.01rad。冲击刀刃与试样侧面的平行度不得大于0.005rad。支座的垂直支承面应垂直于水平支承面,偏差在0.025rad之内,支座的垂直支承面、水平支承面的左右面应在同一平面上,其偏差不得大于0.13mm。万刃半径r12.7±0.8
冲击力
支座半径r12.7±0.8
图4动态撕裂试验机的支座和冲击刀5.7摆轴中心至摆锤打击中心的距离与摆锤中心至试样中心的距离应一致,两者之差应小于摆轴中心至摆锤打击中心距离的1%。当摆自由悬挂时,从试样缺口背面到冲击刀刃的距离应小于5mm。5.8支座周围应加安全罩,防止断裂试样飞出。5.9本标准未作具体规定的试验机技术参数,应按GB/T3808的有关规定执行,并按JJG145检定。5.10试验机应检定合格,有效期不超过3年。6试验
6.1试验之前,把试样浸没在装有冷却或加热介质的保温槽筛板上,筛板离槽底至少25mm,试样间距至少等于试样厚度。应使槽内温度均匀。介质的温度与试验温度之差,应控制在土1℃范围内,保温时间按1min/mm计算,但至少保温15min。6.2测温使用的玻璃温度计最小分度值应不大于1℃,误差应符合JJG130规定,测温热电偶应符合JJG141、JJG351或JJG368中Ⅱ级热电偶要求;测温仪器的误差应不超过士0.1%,热电偶参考端温度应保持恒定,偏差应不超过士0.5℃。6.3从保温槽内取出试样到冲断,应在10s内究成,如果超过10s而未试验,则应把试样重新放回保4
GB/T5482—2007
温槽内,至少再保温10min。不得采用与试验温度明显不同的夹具在缺[1附近夹持试样。6.4应紧贴支座放置试样,并使冲击刀刃中心线与缺口顶端对中,偏差在士0.8mm之内。6.5打断试样,记录试验温度与动态撕裂能量值。6.6在每一试验温度下,至少试验两个试样。7纤维断面率的测算
7.1晶状区面积的测量
非奥氏体类钢的动态撕裂试样断口的晶状区形状,通常是不规则的,为便于直接测量其面积,需把这些不规则的晶状区归类成矩形、三角形或梯形等使于测量和计算的等效图形,如图5,用分辨力不大于0.1mm的量具测量等效图形的相应尺寸,计算晶状区面积。若一个试样断口上分成几块晶状区,则应分别测量每块晶状区面积,再把几块面积相加。或者采用GB/T12778规定的或其他能保证测量精度的测试方法测量晶状区面积。9.0mm
图5典型动态撕裂试样断口及其晶状区等效归并法示意图7.2纤维断面率的计算
7.2.1用缺口处原始横截面积减去晶状区面积计算出断口纤维状面积。7.2.2用纤维状面积与缺口处原始横截面积之比的百分数计算出纤维断面率。8试验结果处理
试验数据至少应保留两位有效数字。8.2当DT能高于试验机最大量程的80%时,应在试验报告中注明。8.3试验过程中出现下列情况之一时,试验数据无效:a)操作失误;
b)试验时发生卡锤现象。
9试验报告
试验报告一般包括:试验日期、报告缩号、材料名称、牌号、规格、取样方向、试样标识、试验温度、试样厚度和试验结果,焊接接头试样,应注明缺口部位。5
GB/T5482—2007
A.1试板的制备
附录A
(规范性附录)
焊接接头试样取样方法
A,1.1试板用母材及其取向和焊接材料应符合有关技术条件规定试板用母材的宽度应符合表A.1的规定,其长度可根据样坏数量而定,但不得小于400mm。A.12
试板厚度t
>24~50
试板宽度B
≥100
≥150
≥200
单位为毫米
A.1.3在200mm长度内,试板挠度f不应超过板厚的10%,且不得大于4mm。试板错边量h不应超过板厚的15%,且不得大于4mm,见图A.1。单位为毫米
图A.1试板挠度和错边
A.2样坏切取
A.2.1试验用样坏应从焊接试板或焊接结构上切取。切取样坏之前,应将试板两端各截弃50mtn。A.2.2样坏切取,尽量采用机械切削方法。若采用火焰切割方法,应留有足够加工余量,以保证受试金属不受热影响。
A.3试样切取
试样应尽量靠近后焊面切取,如图A.2所示。6
加工线
A4试样缺口位置
后辉面
先焊面
试样切取示意图
GB/T5482--2007
A,4.1焊缝金属试样的缺口轴线应与焊缝表面垂直,并位于焊缝中心处,如图A.3所示。图A.3焊缝金属试样缺口位置示意图A,4.2熔合线及近缝区试样的缺口轴线与焊缝表面垂直。熔合线缺口位置,开在试样二分之一厚度平面与熔合线交界处的M点。近缝区各部位的缺口位置,根据技术条件要求,开在M点以外的H点,如图A.4所示。
图A,4熔合线及近缝区试样缺口位置示意图GB/T5482—2007
B.1试样
附录B
(资料性附录)
厚度大于或等于25mm的动态撕裂试样及试验机的要求B.1.1厚度为25mm,32mm和40mm的动态撕裂试样取样按4.1.1的规定,尺寸如图B.1和表B.1所示。取自板厚为25mm、32mm和40mm的试样,保留原轧制表面,其他厚度尺寸的样坏,可加工成与上述相应尺寸的试样。
B.1.2缺口宽度b.=3mm,压制顶端深度D,=1.0mm士0.15mm,缺口其余尺寸和公差同表1。压制缺口所需压力力按4.3.6中公式估算,但K一3.6mm士0.5mm。L/2
试样尺寸参数
大于或等于25mm动态撕裂试样
表B.1试样尺寸
试样厚度
460±5
120±1
550±5
160±1
压刀的长度和厚度分别为50mm和2.5mm,其余要求见图3。B.2试验机
试验机的容量应不小于7500J,其读数盘的分度最大值为50J~100J。试验机的冲击刀刃半径、支座半径和支座跨距应符合表B.2的规定。表B.2试验参数表
试验参数
支座跨距
支座半径
冲击刀刃半径
试样厚度
单位为毫米
650±5
200±1
单位为毫米wwW.bzxz.Net
C,1总则
附录C
(资料性附录)
缺口顶端的压制
GB/T5482-—2007
本标准采用位移控制法或载荷控制法完成缺口顶端的压制。压制缺口可用压力机或万能材料试验机。只要压制深度能达到表1的要求,也可采用其他方法压制缺口项端。C.2位移控制法
C.2.1每次压制之前,检查压刀。压刀应符合4.3.4的规定,还应仔细清除试样缺口中的金属屑和缺口边缘的毛刺。
C.2.2对缺口预加载荷,并把千分表的表盘对准零。厚度为10mm~16mm的钢试样可预加400N,10mm以下的钢试样和其他较软的金属试样,可预加200N。C.2.3采用千分表控制压下量,千分表读数应大于表1规定的压制深度,超过量与试验材料和试样厚度等有关,应按附录D通过实测确定。c.3载荷控制法
C.3.1压制前的要求同C.2.1。
C.3.2按照4.3.6中压力公式估算出的载荷压制缺口,记录载荷,并按附录D测量压制深度。若试样的压制深度都符合表1的规定,则同批号、同厚度的其余试样可按此载荷压制。C.3.3若测得压制深度不符合要求,应调整压力,重新压制,直到获得稳定、合格的压制深度为止。C.3.4压制过程中应抽检压制深度。GB/T5482—2007
D.1一般要求
附录D
(资料性附录)
缺口压制深度的测量
建议采用以下方法测量缺口压制深度,只要测量分辨力能够达到0.01mm,也可采用其他方法测量压制缺口的深度。
D.2测量步骤
D.2.1在试样两面离机加工顶端约2mn处,画一条基准线,或以试样棱边作为基准线,并分别做出识别标记。
D.2.2用工具显微镜或分辨力不大于0.01mm的读数显微镜测量未压试样两面机加工缺口顶端与基准线之间的距离。
D.2.3按附录C中任意一种方法压制缺口顶端。D.2.4测量试样两面压制缺口顶端与基准线之间的距离。D.2.5D.2.2和D.2.4所得结果之差,即为缺口的压制深度。10
小提示:此标准内容仅展示完整标准里的部分截取内容,若需要完整标准请到上方自行免费下载完整标准文档。
中华人民共和国国家标准
GB/T 5482--2007
代替GB/T5482--1993
金属材料动态撕裂试验方法
Test method of metallic materials-Dynamic tear2007-02-09发布
中华人民共和国国家质量监督检验检疫总局中国国家标准化管理委员会
2007-08-01实施
GB/T5482—2007
本标准修改采用ASTME604-83(2002年认可)《金属材料动态撕裂试验标准试验方法》,与ASTME604-83相比主要差异如下:
试验机读数盘的规定;
一删除有关计量的内容;
-增加了附录A和附录B。
本标准代替GB/T5482--1993《金属材料动态撕裂试验方法》,本标准与GB/T5482—1993相比主要变化如下:
增加了前言部分;
一在术语和定义中增加了纤维断面率;压制缺口估算公式中的K值由1.8mm士0.5mm改变为2.4mm士0.5mm。本标准的附录A是规范性附录,本标准的附录B、附录C、附录D是资料性附录。本标准由中国船舶重工集团公司提出。本标准由全国海洋船标准化技术委员会船用材料应用工艺分技术委员会归口。本标准起草单位:中国船舶重工集团公司第七二五研究所、武昌造船厂、江南造船厂。本标准主要起草人:叶宏德、杨小敏、沈权、陈庆垒、张欣耀。本标准的历次版本发布情况为:GB/T5482-1985.GB/T5482—1993。1范围
金属材料动态撕裂试验方法
GB/T5482—2007
本标准规定了金属材料动态撕裂试验试样及其制备、试验机、测试方法和试验结果的处理。本标准适用于测定洛氏硬度值小于36HRC的金属材料或焊接接头试样的动态撕裂能和纤维断面率。
2规范性引用文件
下列文件中的条款通过本标准的引用而成为本标准的条款。凡是注日期的引用文件,其随后所有的修改单(不包括勘误的内容)或修订版均不适用于本标准,然而,鼓励根据本标准达成协议的各方研究是否可使用这些文件的最新版本。凡是不注日期的引用文件,其最新版本适用于本标准。GB/T2975钢及钢产品力学性能试验取样位置及试样制备GB/T3808摆锤式冲击试验机的检验GB/T12778金属夏比冲击断口测定方法JJG130
工作用玻璃液体温度计检定规程JJG141
JJG145
JJG351
工作用贵金属热电偶检定规程
摆锤式冲击试验机检定规程
工业用廉金属热电偶检定规程
JJG368
工作用铜-铜镍热电偶检定规程
3术语和定义
下列术语和定义适用于本标准。3.1
动态撕裂(DT)试验
dynamicteartest
在冲击试验机上,将处于简支梁状态下的动态撕裂试样一次冲断,测量其吸收能量和纤维断面率的试验。
动态撕裂能(DT能)dynamictearenergy动态撕裂试验时试样所吸收的能量,用以表征各特定厚度的金属材料抵抗动态撕裂的能力。3.3
动态撕裂试样断口fracture surfaceofdynamictearspecimen动态撕裂试样冲断后的断裂表面。其宏观形貌一般呈晶状、纤维状(含剪切唇)或混合状。3.4
纤维断面率
percent shear fracture appearance纤维状断口面积与缺口处原始横截面积之比的百分数。4试样及其制备
4.1取样
4.1.1样坏的切取部位和方向应符合GB/T2975或有关技术条件的规定。4.1.2焊接接头试样取样方法按附录A执行。1
GB/T5482—2007
4.2试样
4.2.1厚度为5mm~16mm的样坏,试样应为180mm×40mm×t,保留原轧制表面,其厚度公差执行相应材料的技术条件规定,其他尺寸和公差见图1,厚度t大于16mm的样坏,加工成规格为180mm×40mm×16mm的试样,尺寸和公差见图1。4.2.2对于厚度等于或大于25mm的大型动态撕裂试样及试验机的要求参见附录B。4.3缺口制备
4.3.1试样缺口可用铣削或线切割等方法加工,但一组试样必须采用同一种加工方法。单位为毫米
180±2
全部12
图1动态撕裂试样
4.3.2机加工合格的试样,试验前需用硬度不小于60HRC的压刀压制缺口,压制方法参见附录C。4.3.3试样缺口和缺口项端的压制尺寸及公差见图2和表1压制顶端根部半径
机加工缺口根部半径厂。
图2动态撕裂试样缺口和缺口顶端的压制尺寸2
缺口几何参数
净宽(ba)/mm
机加工缺口宽度ba/mm
机加工缺口根部角度a/()
机加工缺口根部半径r./mm
压制深度D,/mm
压制顶端角度a./(\)
压制项端根部半径r/mm
表1缺口尺寸和公差
压刀的尺寸见图3,刃口应无毛刺和缺陷。4.3.4
图3锐化缺口顶端用的压刀
4.3.5缺口压制深度的测量方法参见附录D4.3.6试样缺口顶端应逐个压制,所需压力可按式(1)估算:p-KXR.Xt
式中:
—压力,单位为牛顿(N);
抗拉强度,单位为兆帕(MPa);Rm
t-试样厚度,单位为毫米(mm);K系数,取K=2.4mm士0.5mm。
5试验机
GB/T5482—2007
其余1.60
40*±5
刃部半轻r≤0.025
5.1动态撕裂试验通常采用摆锤式冲击试验机,其能量应能在一次冲击时将试样打断。也可使用落锤式冲击试验机,试验机有关参数应满足本标准测试要求。注:对大多数钢材进行动态撕裂试验所需能量:16mm厚试样约为3000J。铝合金所需能量比上述能量约低20%。
5.2打击瞬间摆锤的冲击速度应为4.0m/s~8.5m/s3
GB/T5482—2007
5.3摆锤式冲击试验机读数盘的分度应符合表2的规定。表2试验机读数盘
最大冲击能量值
>500~1500
>1500~3000
分度最大值
单位为焦耳
5.4试验机的支座和冲击刀刃的硬度不得小于48HRC,其尺寸及支座跨距应符合图4的规定,5.5由摆锤重量或下落高度引起的动态撕裂能量值的误差不应超过1%,由于风阻和摩擦阻力所造成的能量损失不应超过初始位能的2%。5.6摆锤两个侧面与支座之间的间隙,应不小于51mm。冲击刀中心线的运动平面,应通过支座跨距的中点,偏差不应超过0.8mm。冲击刀刃应垂直于试样的纵轴,其偏差不大于0.01rad。冲击刀刃与试样侧面的平行度不得大于0.005rad。支座的垂直支承面应垂直于水平支承面,偏差在0.025rad之内,支座的垂直支承面、水平支承面的左右面应在同一平面上,其偏差不得大于0.13mm。万刃半径r12.7±0.8
冲击力
支座半径r12.7±0.8
图4动态撕裂试验机的支座和冲击刀5.7摆轴中心至摆锤打击中心的距离与摆锤中心至试样中心的距离应一致,两者之差应小于摆轴中心至摆锤打击中心距离的1%。当摆自由悬挂时,从试样缺口背面到冲击刀刃的距离应小于5mm。5.8支座周围应加安全罩,防止断裂试样飞出。5.9本标准未作具体规定的试验机技术参数,应按GB/T3808的有关规定执行,并按JJG145检定。5.10试验机应检定合格,有效期不超过3年。6试验
6.1试验之前,把试样浸没在装有冷却或加热介质的保温槽筛板上,筛板离槽底至少25mm,试样间距至少等于试样厚度。应使槽内温度均匀。介质的温度与试验温度之差,应控制在土1℃范围内,保温时间按1min/mm计算,但至少保温15min。6.2测温使用的玻璃温度计最小分度值应不大于1℃,误差应符合JJG130规定,测温热电偶应符合JJG141、JJG351或JJG368中Ⅱ级热电偶要求;测温仪器的误差应不超过士0.1%,热电偶参考端温度应保持恒定,偏差应不超过士0.5℃。6.3从保温槽内取出试样到冲断,应在10s内究成,如果超过10s而未试验,则应把试样重新放回保4
GB/T5482—2007
温槽内,至少再保温10min。不得采用与试验温度明显不同的夹具在缺[1附近夹持试样。6.4应紧贴支座放置试样,并使冲击刀刃中心线与缺口顶端对中,偏差在士0.8mm之内。6.5打断试样,记录试验温度与动态撕裂能量值。6.6在每一试验温度下,至少试验两个试样。7纤维断面率的测算
7.1晶状区面积的测量
非奥氏体类钢的动态撕裂试样断口的晶状区形状,通常是不规则的,为便于直接测量其面积,需把这些不规则的晶状区归类成矩形、三角形或梯形等使于测量和计算的等效图形,如图5,用分辨力不大于0.1mm的量具测量等效图形的相应尺寸,计算晶状区面积。若一个试样断口上分成几块晶状区,则应分别测量每块晶状区面积,再把几块面积相加。或者采用GB/T12778规定的或其他能保证测量精度的测试方法测量晶状区面积。9.0mm
图5典型动态撕裂试样断口及其晶状区等效归并法示意图7.2纤维断面率的计算
7.2.1用缺口处原始横截面积减去晶状区面积计算出断口纤维状面积。7.2.2用纤维状面积与缺口处原始横截面积之比的百分数计算出纤维断面率。8试验结果处理
试验数据至少应保留两位有效数字。8.2当DT能高于试验机最大量程的80%时,应在试验报告中注明。8.3试验过程中出现下列情况之一时,试验数据无效:a)操作失误;
b)试验时发生卡锤现象。
9试验报告
试验报告一般包括:试验日期、报告缩号、材料名称、牌号、规格、取样方向、试样标识、试验温度、试样厚度和试验结果,焊接接头试样,应注明缺口部位。5
GB/T5482—2007
A.1试板的制备
附录A
(规范性附录)
焊接接头试样取样方法
A,1.1试板用母材及其取向和焊接材料应符合有关技术条件规定试板用母材的宽度应符合表A.1的规定,其长度可根据样坏数量而定,但不得小于400mm。A.12
试板厚度t
>24~50
试板宽度B
≥100
≥150
≥200
单位为毫米
A.1.3在200mm长度内,试板挠度f不应超过板厚的10%,且不得大于4mm。试板错边量h不应超过板厚的15%,且不得大于4mm,见图A.1。单位为毫米
图A.1试板挠度和错边
A.2样坏切取
A.2.1试验用样坏应从焊接试板或焊接结构上切取。切取样坏之前,应将试板两端各截弃50mtn。A.2.2样坏切取,尽量采用机械切削方法。若采用火焰切割方法,应留有足够加工余量,以保证受试金属不受热影响。
A.3试样切取
试样应尽量靠近后焊面切取,如图A.2所示。6
加工线
A4试样缺口位置
后辉面
先焊面
试样切取示意图
GB/T5482--2007
A,4.1焊缝金属试样的缺口轴线应与焊缝表面垂直,并位于焊缝中心处,如图A.3所示。图A.3焊缝金属试样缺口位置示意图A,4.2熔合线及近缝区试样的缺口轴线与焊缝表面垂直。熔合线缺口位置,开在试样二分之一厚度平面与熔合线交界处的M点。近缝区各部位的缺口位置,根据技术条件要求,开在M点以外的H点,如图A.4所示。
图A,4熔合线及近缝区试样缺口位置示意图GB/T5482—2007
B.1试样
附录B
(资料性附录)
厚度大于或等于25mm的动态撕裂试样及试验机的要求B.1.1厚度为25mm,32mm和40mm的动态撕裂试样取样按4.1.1的规定,尺寸如图B.1和表B.1所示。取自板厚为25mm、32mm和40mm的试样,保留原轧制表面,其他厚度尺寸的样坏,可加工成与上述相应尺寸的试样。
B.1.2缺口宽度b.=3mm,压制顶端深度D,=1.0mm士0.15mm,缺口其余尺寸和公差同表1。压制缺口所需压力力按4.3.6中公式估算,但K一3.6mm士0.5mm。L/2
试样尺寸参数
大于或等于25mm动态撕裂试样
表B.1试样尺寸
试样厚度
460±5
120±1
550±5
160±1
压刀的长度和厚度分别为50mm和2.5mm,其余要求见图3。B.2试验机
试验机的容量应不小于7500J,其读数盘的分度最大值为50J~100J。试验机的冲击刀刃半径、支座半径和支座跨距应符合表B.2的规定。表B.2试验参数表
试验参数
支座跨距
支座半径
冲击刀刃半径
试样厚度
单位为毫米
650±5
200±1
单位为毫米wwW.bzxz.Net
C,1总则
附录C
(资料性附录)
缺口顶端的压制
GB/T5482-—2007
本标准采用位移控制法或载荷控制法完成缺口顶端的压制。压制缺口可用压力机或万能材料试验机。只要压制深度能达到表1的要求,也可采用其他方法压制缺口项端。C.2位移控制法
C.2.1每次压制之前,检查压刀。压刀应符合4.3.4的规定,还应仔细清除试样缺口中的金属屑和缺口边缘的毛刺。
C.2.2对缺口预加载荷,并把千分表的表盘对准零。厚度为10mm~16mm的钢试样可预加400N,10mm以下的钢试样和其他较软的金属试样,可预加200N。C.2.3采用千分表控制压下量,千分表读数应大于表1规定的压制深度,超过量与试验材料和试样厚度等有关,应按附录D通过实测确定。c.3载荷控制法
C.3.1压制前的要求同C.2.1。
C.3.2按照4.3.6中压力公式估算出的载荷压制缺口,记录载荷,并按附录D测量压制深度。若试样的压制深度都符合表1的规定,则同批号、同厚度的其余试样可按此载荷压制。C.3.3若测得压制深度不符合要求,应调整压力,重新压制,直到获得稳定、合格的压制深度为止。C.3.4压制过程中应抽检压制深度。GB/T5482—2007
D.1一般要求
附录D
(资料性附录)
缺口压制深度的测量
建议采用以下方法测量缺口压制深度,只要测量分辨力能够达到0.01mm,也可采用其他方法测量压制缺口的深度。
D.2测量步骤
D.2.1在试样两面离机加工顶端约2mn处,画一条基准线,或以试样棱边作为基准线,并分别做出识别标记。
D.2.2用工具显微镜或分辨力不大于0.01mm的读数显微镜测量未压试样两面机加工缺口顶端与基准线之间的距离。
D.2.3按附录C中任意一种方法压制缺口顶端。D.2.4测量试样两面压制缺口顶端与基准线之间的距离。D.2.5D.2.2和D.2.4所得结果之差,即为缺口的压制深度。10
小提示:此标准内容仅展示完整标准里的部分截取内容,若需要完整标准请到上方自行免费下载完整标准文档。

标准图片预览:
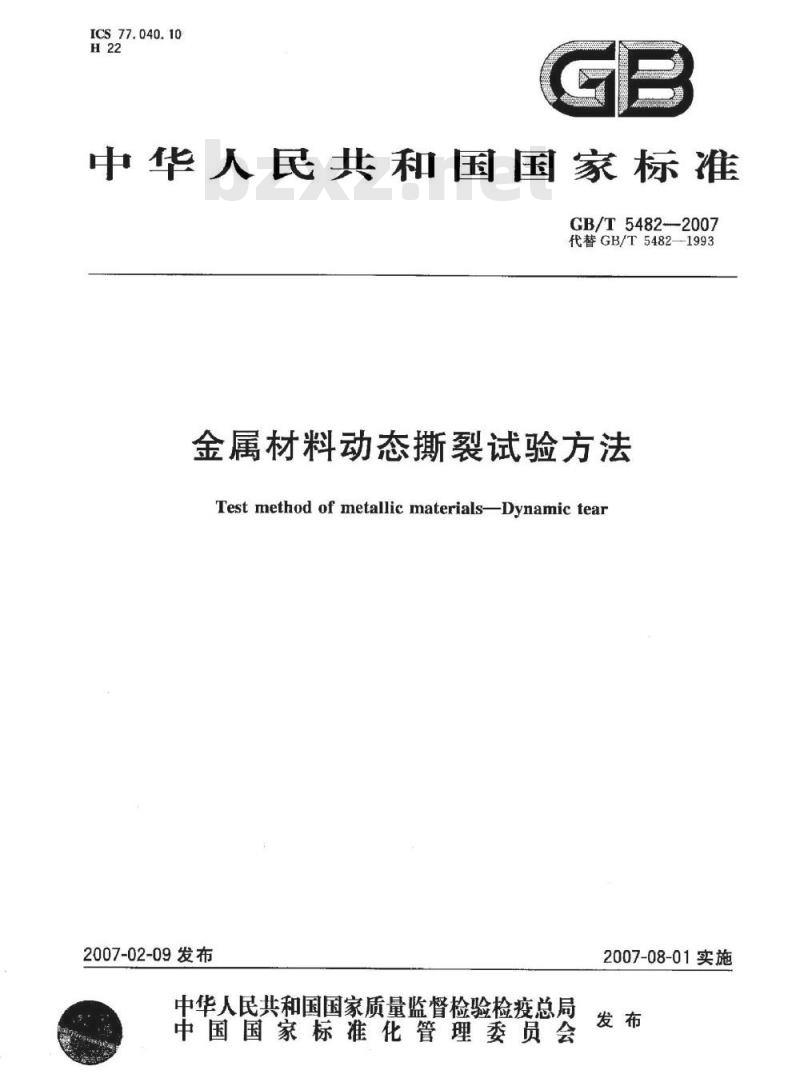
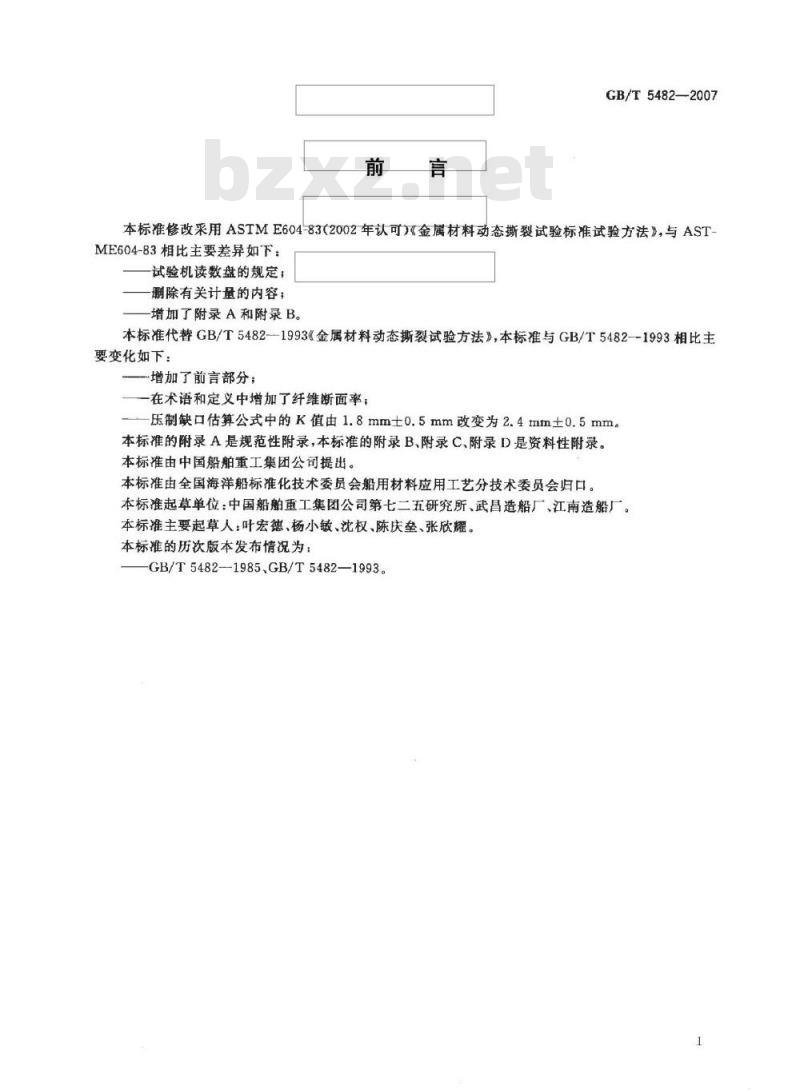
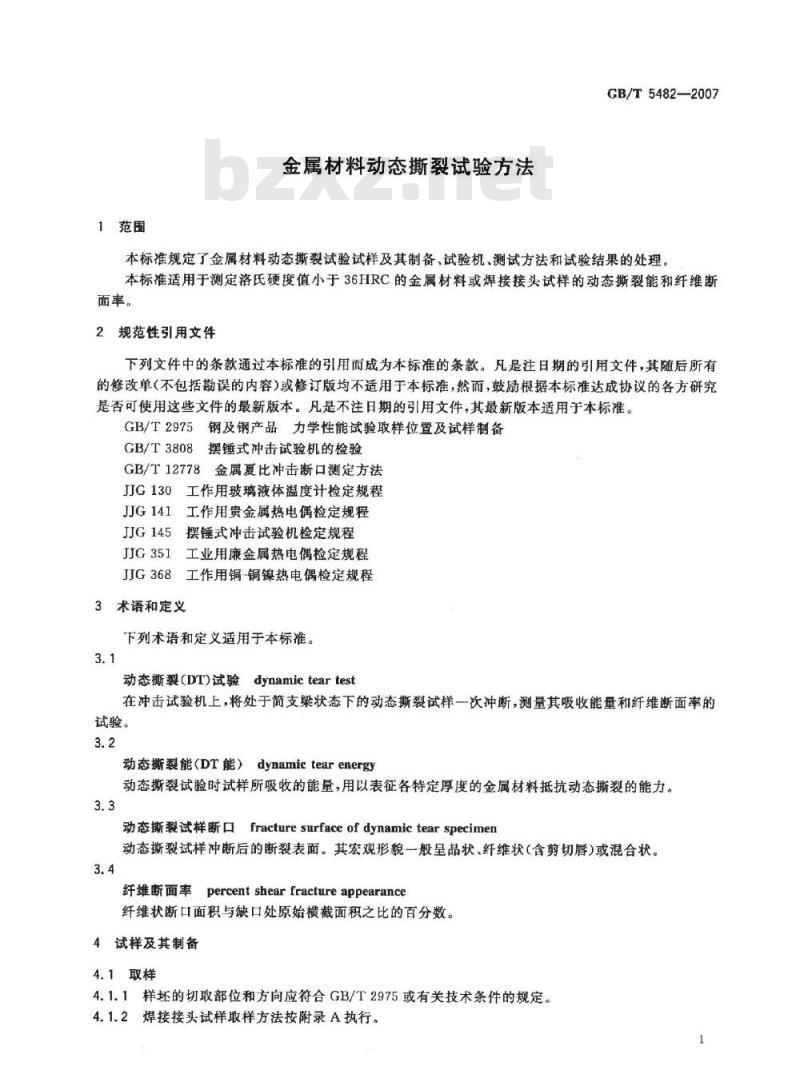
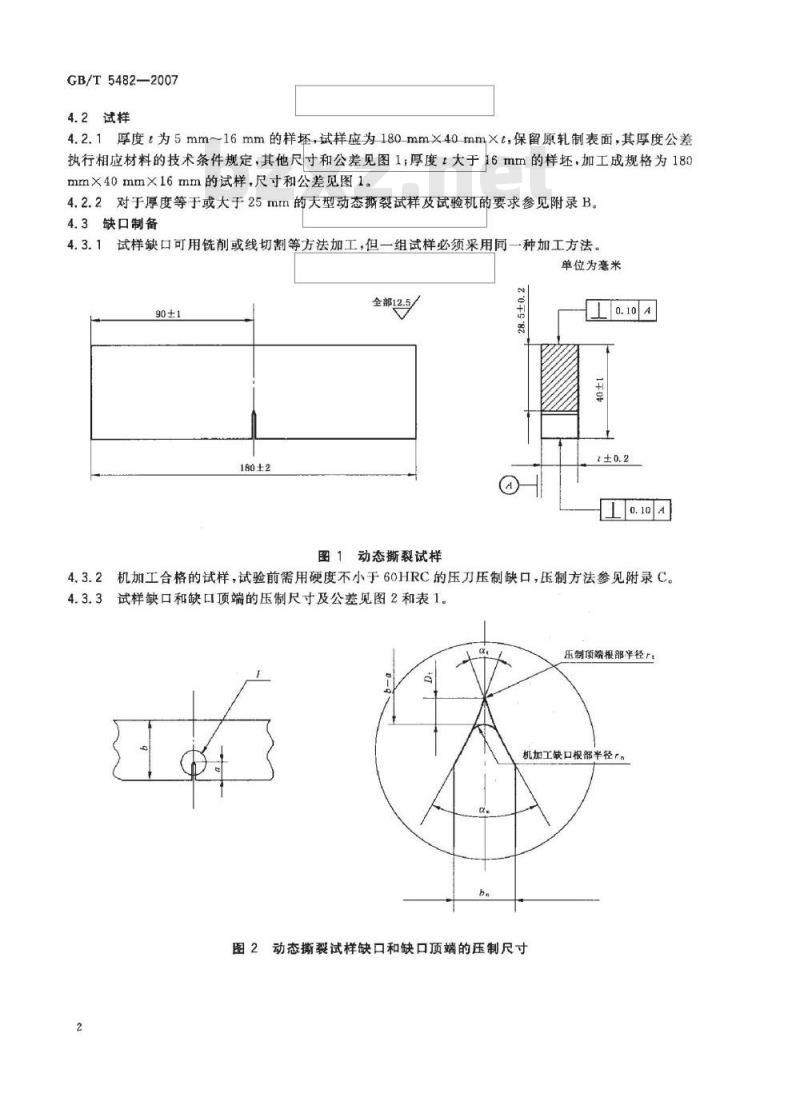
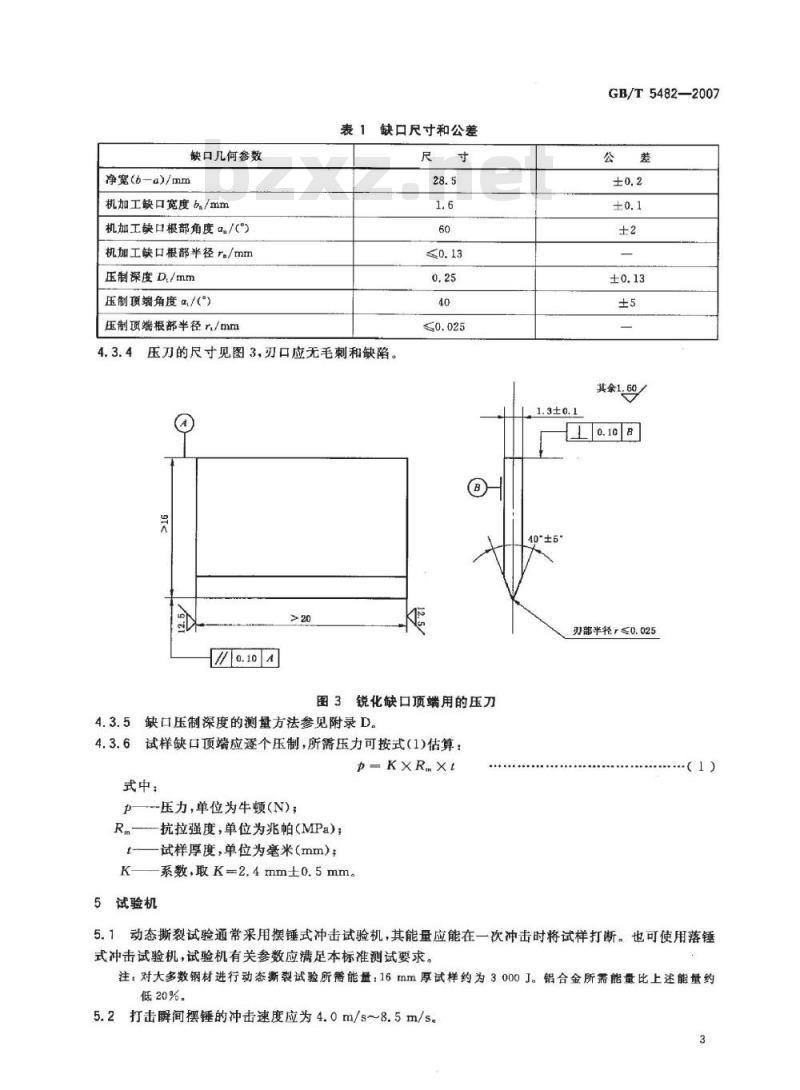
- 其它标准
- 热门标准
- 国家标准(GB)
- GB/T15310.3-1994 外贸出口单证格式 装运声明
- GB/T2828.1-2012 计数抽样检验程序 第1部分:按接收质量限(AQL)检索的逐批检验抽样计划
- GB2761—2005 食品中真菌毒素限量
- GB7521—1987 多个控制器在一CA MAC机箱中
- GB/T2988—2004 高铝砖
- GB3033.1—2005 /ISO 14726-1 : 1999 船舶与海上技术管路系统内含物的识别颜色第1部分:主颜色和介质
- GB/T80-2007 内六角凹端紧定螺钉
- GB13077-2004 铝合金无缝气瓶定期检验与评定
- GB/T4789.4-2003 食品卫生微生物学检验沙门氏菌检验
- GB917.2—2000 公路路线标识规则国道名称和编号
- GB/T14652.1-2001 小艇耐火燃油软管
- GB/T155—2006 原木缺陷
- GB9116.5-1988 PN1.6MPa(16bar)凸面带颈平焊钢制管法兰
- GB/T21485-2008 船舶和海上技术 船上消防、救生设备及逃生路线布置图
- GB/T13612-2006 人工煤气
- 行业新闻
请牢记:“bzxz.net”即是“标准下载”四个汉字汉语拼音首字母与国际顶级域名“.net”的组合。 ©2009 标准下载网 www.bzxz.net 本站邮件:bzxznet@163.com
网站备案号:湘ICP备2023016450号-1
网站备案号:湘ICP备2023016450号-1