- 您的位置:
- 标准下载网 >>
- 标准分类 >>
- 航空工业行业标准(HB) >>
- HB 5287-1996 金属材料轴向加载疲劳试验方法

【航空工业行业标准(HB)】 金属材料轴向加载疲劳试验方法
本网站 发布时间:
2024-10-18 01:05:51
- HB5287-1996
- 现行
标准号:
HB 5287-1996
标准名称:
金属材料轴向加载疲劳试验方法
标准类别:
航空工业行业标准(HB)
标准状态:
现行-
发布日期:
1996-09-13 -
实施日期:
1996-10-01 出版语种:
简体中文下载格式:
.rar.pdf下载大小:
4.48 MB
替代情况:
HB 5287-84

部分标准内容:
中华人民共和国航空工业标准
HB 5287 - 96
金属材料轴向加载疲劳试验方法1996-09~13发布
中国航空工业总公司
1996-10-01实施
中华人民共和国航空工业标准
金属材料轴向加载疲劳试验方法HB5287-96
代替HB5287-84
1主题内容与适用范围
本标准规定了金属材料承受图1所示的任一类型循环应力的恒幅轴向疲劳试验的试样形状、试验设备、试验程序、试验结果的处理与表达。本标准适用室温空气中控制载荷的恒幅疲劳试验、以测定材料在整个试验过程中弹性应变分量占优势条件下的轴向疲劳强度。试样所受应力随时间关系一般为正弦波,也可以采用其它波形如梯形波、三角波、方波。但必须予以说明。2引用标准
JJG139
拉力、压力和万能材料试验机检定规程+
3符号、名称、定义及单位
图1循环应力的类型
本标准所用的符号、名称、定义及单位见图2及表1、表2。中国航空工业总公司1996—09-13发布oo
1996-1001实施
最大应力
最小应力
平均应力
应力幅
(交变应力)
应力范围
(应力变程)
应力比
循环频率
疲劳寿命bzxZ.net
疲劳极限
HB5287-96
T-应力循环
图2应力一时间关系
t时间
在应力循环中具有最大代数值的应力,以拉应力为正,压应力为负。
在应力循环中具有最小代数值的应力,以拉应力为正,压应力为负。
在应力循环中,最大应力与最小应力的平均值,即为:Om=(omax + omm)/2
在应力循环中最大应力与最小应力差之半,即为:,=(omx - Omin)/2
在应力循环中最大应力与最小应力之差,即OmaxOmin
在应力循环中最小应力与最大应力的比值,即R= Omn/omar
单位时间的应力循环周次
试样失效(出现规定长度裂纹、断裂)的应力循环次数指定循环次数下的中值疲劳强度。若S-N曲线具有水平段循环次数取10°;若S-N曲线无水平段循环次数取10°或>10°。
Hz或周/分
4试样
理论应力
集中系数
疲劳缺口
存活率
HB5287-96
续表1
根据弹性理论计算所得到的应力集中区最大应力与名义应力之比值。
在试验条件和循环周次相同条件下,没有应力集中试样的疲劳强度与有应力集中试样的疲劳强度之比。疲劳寿命高于规定值的概率。
圆形横截面试样夹持部分的直径或夹持部分螺纹的外径圆形横截面试样非工作部分的直径圆形横截面试样工作部分的直径试样工作部分的平行长度
矩形横截面试样工作部分的厚度矩形横截面试样夹持部分的宽度矩形横截面试样非工作部分的宽度矩形横截面试样工作部分的宽度单截面试样两夹持部分之间的圆弧半径4.1设计试样的一般原则
4.1.1设计试样必须满足下列要求,单位
a.圆形横截面试样:D/d=1.5~3.5(带螺纹头的试样尽可能取大者);L.>3d;当试样受压应力时3db.矩形横截面试样:B/b=1.5~4(头部有销孔的试样尽可能取大者);b/a=3~8;ba=9~645mm2;L>3b;当试样受压应力时3b4.2本标准规定下列形状和尺寸的标准试样:a.直径7mm的光滑试样(K,=1),见图3、图4;3
HB5287-96
b.直径10mm的光滑试样(K,=1),见图5、图6;c.直径8.5mm的缺口试样(K=2~5),见图7;d.宽度15mm的板状光滑试样(K,=1),见图8e.具有边缺口的板状试样(K,=2~5)见图9;f.具有中心孔的板状试样(K,=2.5),见图10、图11。注:①如有特殊要求,可采用其它应力集中系数或其它缺口形状的试样,但在试验报告中必须注明。②试样夹头部分的形状和尺寸可极据需要自行设计。③由于材料尺寸和试验条件所限允许采用工作部分直径为5mm的非标准试样,见附录A。④如有特殊需要,允许根据双方协议和其它技术条件确定试样尺寸。?如圆形横截面光滑试样试验结果有争议时,以图4试样为仲裁试样。4.3试样的尺寸、形位公差
4.3.1圆形横截面试样的公差见表3。表3
试样直径,d
最大最小直径差
夹持部分与工作部分中心线不同轴度≤0.02
对于缺口试样,缺口与试样中心线的垂直度为0.02mm,缺口底部半径公差为0.02mmc4.3.2矩形横截面试样的公差见表4。表4
试样宽度,b
最大最小宽度差
夹持部分与工作部分中心线不对称度≤0.02
对具有边缺口的试样,两缺口中心线与试样中心线应垂直,不垂直度小于0.02mm。对具有中心缺口的试样,其缺口中心与试样中心线不对称度小于0.03mm,在试样长度为100~200mm时,夹持部分定位孔的中心线与试样中心线的不对称度为0.05mm。4.3.3光滑试样表面应抛光,表面粗糙度Ra<0.32mm,缺口粗糙度为Ra<0.32mm,试样表面不应有任何划伤或损伤。试样工作部分与过渡圆孤的连接应光滑。4.3.4对于圆形横截面试样工作部分直径的测量精度为0.01mm;对矩形横截面试样工作部分截面尺寸的测量误差,厚度为0.01mm,宽度为0.02mm。测量尺寸时应防止损伤试样表面。4.4试样的制备
HB5287-96
4.4.1试样的取样部位和方向根据有关标准和双方协议执行。4.4.2试样的加工工艺对疲劳试验结果影响很大,因此选择适当的加工工艺并严格遵守是非常重要的。在加工过程中为了避免材料过热和加工硬化,并使表面残余应力减到最小,以及保证试样表面状态尽可能一致,推荐采用附录B规定的加工工艺。4.4.3试样加工完毕应要善保存防止变形、表面损伤和腐蚀。4.4.4用放大20倍的光学仪器检验试样工作表面,不充许有缺陷。4.4.5试样的缺口应在热处理以后进行加工,缺口的形状、尺寸应用不低于50倍的光学仪器检查。
5试验机
5.1试验可在各种类型的疲劳试验机上进行。5.2疲劳试验机应满足下列要求:5.2.1试验机的静载荷按JJG139-74进行校正,动态标定时,平均载荷和载荷变程的误差均不大于载荷循环中最大载荷的土3%,或试验机满量程的0.5%,取其中大者。5.2.2为了确保轴向加载,要求试验机的儿何筒轴度不大于0.1%,同时推荐用贴应变片测量试样弯曲变形的方法,检查试验机连同装夹试样系统的同轴度。采用直径为10土0.02mm,标距为50mm的圆形截面试样,在试样工作部分的中部圆周上平均分布贴4片电阻值相同的应变片,它们的中心精确地保持在试样的同一个横截面上,并采用半桥连接。然后用电桥检查4片应变片的电阻值,各片之间的差值不应大于测量仪器所允许的范围。在试样不承受载荷时予调平衡。注:如有特殊需要,可根据双方协议确定试样表面粗度。从试验机每挡量程的10%起至满量程,在5个载荷水平下(在应力与应变呈线性比例关系范围内)进行测量,并记录4个应变片指示的变形值,然后卸去负荷,照此重复测量3次。弯曲变形率PBS用下式计算:
PBS = (q13)* + (q2)
×100%
式中:9。=9i+++
q13 =[(q - qo) -(qq)1/2
=(qi-Q)/2
q24 =[(qz - qo) -(q4 q。)]/2=(q-q4)/2
91>2v3>94分别是4个应变片三次测量的变形平均值。(1)
然后将试样分别旋转90°、180°、270°在每一个位置同样进行上述测量和计算。在所测定的负荷范围内,弯曲变形率均不应大于10%。5.2.3夹具的设计应保证良好的同心度,如因夹具不满足同心度的要求时应改进设计。5
6试验程序
HB5287-96
6.1装夹试样必须保证施加于试样上的载荷是沿轴向的。6.2施加载荷应平稳,不得超载。试验过程中应经常检测载荷。6.3试验频率
频率的选择取决于试验机的类型、试样的刚度和被试材料的性质。一般在5~200Hz范围内进行试验。对于同一批试样,应在大致相同的频率下进行试验,频率相差过大,可能对试验结果有影响。如需要在不同频率下试验,必须经过试验验证,并在试验报告中予以说明。试验过程中试样工作部分的温度不得超过60℃,否则必须降低试验频率或对试样进行冷却。
6.4试样在规定的应力下连续试验,直至规定的循环次数或试样失效。6.5试样失效发生在非工作部分,试验结果作废。7疲劳极限和S一N曲线的测定
7.1疲劳极限的测定
推荐用升降法测定材料的疲劳极限。有效试样数为15根左右,选择合适的应力增量(或降低量)是升降法试验中一个重要的程序。一般光滑试样的应力增量选择在预计疲劳极限的5%以内。缺口试样的应力增量适当减少。应使第一根试样的试验应力水平略高于预计疲劳极限。根据上一根的试验结果(失效或通过)决定下一根试样的试验应力水平(降低或升高),直至完成全部试验。对第一次出现相反结果以前的试验数据,如在以后试验数据的波动范围之内则有效。升降的应力水平数一般为4级左右。如果试验的目的只要求出中值疲劳极限n,则按下式进行计算:1
式中:n---有效试验总次数:
m—升降应力水平级数;
a;第i级应力水平;
V.一一第i级应力水平下的试验次数。(2)
如果试验还要求出疲劳极限的标准差,则必须将相邻应力水平的各数据点按一个破坏点(×)和一个越出点(0)配成一对,如果升降图是封闭的,则所有试验点都能配成对子,这时中值疲劳强度或疲劳极限的估计量6s为:aso=
式中:n*一配成的对子总数;
m*-配成对子的级数,为升降法级数减1,即m*=m-1;o=(o+gi+1)/2;
V”一相邻两级配成的对子数。
HB5287-96
疲劳极限或疲劳强度的子样标推差S*按下式计算:S
n*(n*- 1)
7.2S-N曲线的测定
获得一条S一N曲线,通常取4~6级或更多的应力水平。用升降法求得的疲劳极限做为S-N曲线最低应力水平,其它应力水平一般用成组试验法进行试验。当成组试验法不能满足要求时,也可以用升降法测定在给定某一长寿命下(如10°)的疲劳强度。成组试验法就是在每一个应力水平做一组试样,每组试样的数量取决于试验数据的分散程度和所要求的置信度,一般随着应力水平的降低逐渐增加,每组应不少于三根试样。成组试验法中值对数疲劳寿命X按下式计算:
1logN;
X = logNso =
式中:N.
-组试验中第i个试样的疲劳寿命;组试样的总数:
Nso—具有50%存活率的疲劳寿命即中值疲劳寿命。对数疲劳寿命标准差S按下式计算:n Z(logN,)2
变异系数Cv按下式计算:
n(n -1)
以试验应力为纵坐标,以疲劳寿命为横坐标拟合成的应力-寿命曲线为某材料的S-N曲线。用上述方法画出的S-N曲线即为中值S-N曲线。具有50%的存活率。如果需要提供具有某置信度(如95%)和在一定误差条件的中值S-N曲线时,必须保证每组最少试样个数。见附录C。
8试验结果的表示法
8.1列表法
表中应包括试样号、试样形式、应力集中系数、试验顺序、材料基本状况、试验条件、循环次数等基本数据。可以根据需要给出原始记录形式的表格或经整理的表格。见附录D。8.2解析法
推荐用下列方程表达S-N曲线。
logN = A, + A20mz
logN = A, + Azlogomux
HB5287-96
logN = A, + A2(omr -A)
logN = A; + A2log(omx - A3)
式中:A1、A2、A3—待定常数。8.3图示法
8.3.1S-N曲线
这是最常用的一种疲劳试验结果的表示方法,绘制S一N曲线时,疲劳寿命采用对数坐标,应力可采用线性坐标或对数坐标。在曲线图上应注明必要的试验参数。见图12和图13。8.3.2等寿命曲线
等寿命曲线是由同批试样至少3条S一N曲线转换绘制而成的。它表示在给定疲劳寿命下的最大应力、最小应力、应力幅、平均应力和应力比之间的关系,见图14。无论用哪种方法表示试验结果,都应注明被试材料、试样状况和试验条件等。9试验报告
9.1试验报告包括下述内容:
a.被试材料的名称、产物、炉号、状态、规格、冶炼方法、制造及热处理工艺、化学成分、力学性能等;
b.取样方向、试样的形状尺寸应力集中系数、表面状态等;C.试样的主要制造工艺;
d.试验机的型号、试验频率、加载方式、应力比、平均应力、应力幅、波形等;e.试验环境:试验温度、湿度及其变化范围;f.试验结果:按第8章规定形式报告试验结果;g.其它。
@00.03A-B
GB145-59
HB 5287-96
图3直径7mm的光滑试样(k=1)
HB5287-96
GB145-59
?00.03A-B
图4直径7mm的光滑试样(k=1)
89-1 ×2E-2
图5直径10mm的光滑试样(k.=1)其余
GB145-59
小提示:此标准内容仅展示完整标准里的部分截取内容,若需要完整标准请到上方自行免费下载完整标准文档。
HB 5287 - 96
金属材料轴向加载疲劳试验方法1996-09~13发布
中国航空工业总公司
1996-10-01实施
中华人民共和国航空工业标准
金属材料轴向加载疲劳试验方法HB5287-96
代替HB5287-84
1主题内容与适用范围
本标准规定了金属材料承受图1所示的任一类型循环应力的恒幅轴向疲劳试验的试样形状、试验设备、试验程序、试验结果的处理与表达。本标准适用室温空气中控制载荷的恒幅疲劳试验、以测定材料在整个试验过程中弹性应变分量占优势条件下的轴向疲劳强度。试样所受应力随时间关系一般为正弦波,也可以采用其它波形如梯形波、三角波、方波。但必须予以说明。2引用标准
JJG139
拉力、压力和万能材料试验机检定规程+
3符号、名称、定义及单位
图1循环应力的类型
本标准所用的符号、名称、定义及单位见图2及表1、表2。中国航空工业总公司1996—09-13发布oo
1996-1001实施
最大应力
最小应力
平均应力
应力幅
(交变应力)
应力范围
(应力变程)
应力比
循环频率
疲劳寿命bzxZ.net
疲劳极限
HB5287-96
T-应力循环
图2应力一时间关系
t时间
在应力循环中具有最大代数值的应力,以拉应力为正,压应力为负。
在应力循环中具有最小代数值的应力,以拉应力为正,压应力为负。
在应力循环中,最大应力与最小应力的平均值,即为:Om=(omax + omm)/2
在应力循环中最大应力与最小应力差之半,即为:,=(omx - Omin)/2
在应力循环中最大应力与最小应力之差,即OmaxOmin
在应力循环中最小应力与最大应力的比值,即R= Omn/omar
单位时间的应力循环周次
试样失效(出现规定长度裂纹、断裂)的应力循环次数指定循环次数下的中值疲劳强度。若S-N曲线具有水平段循环次数取10°;若S-N曲线无水平段循环次数取10°或>10°。
Hz或周/分
4试样
理论应力
集中系数
疲劳缺口
存活率
HB5287-96
续表1
根据弹性理论计算所得到的应力集中区最大应力与名义应力之比值。
在试验条件和循环周次相同条件下,没有应力集中试样的疲劳强度与有应力集中试样的疲劳强度之比。疲劳寿命高于规定值的概率。
圆形横截面试样夹持部分的直径或夹持部分螺纹的外径圆形横截面试样非工作部分的直径圆形横截面试样工作部分的直径试样工作部分的平行长度
矩形横截面试样工作部分的厚度矩形横截面试样夹持部分的宽度矩形横截面试样非工作部分的宽度矩形横截面试样工作部分的宽度单截面试样两夹持部分之间的圆弧半径4.1设计试样的一般原则
4.1.1设计试样必须满足下列要求,单位
a.圆形横截面试样:D/d=1.5~3.5(带螺纹头的试样尽可能取大者);L.>3d;当试样受压应力时3d
HB5287-96
b.直径10mm的光滑试样(K,=1),见图5、图6;c.直径8.5mm的缺口试样(K=2~5),见图7;d.宽度15mm的板状光滑试样(K,=1),见图8e.具有边缺口的板状试样(K,=2~5)见图9;f.具有中心孔的板状试样(K,=2.5),见图10、图11。注:①如有特殊要求,可采用其它应力集中系数或其它缺口形状的试样,但在试验报告中必须注明。②试样夹头部分的形状和尺寸可极据需要自行设计。③由于材料尺寸和试验条件所限允许采用工作部分直径为5mm的非标准试样,见附录A。④如有特殊需要,允许根据双方协议和其它技术条件确定试样尺寸。?如圆形横截面光滑试样试验结果有争议时,以图4试样为仲裁试样。4.3试样的尺寸、形位公差
4.3.1圆形横截面试样的公差见表3。表3
试样直径,d
最大最小直径差
夹持部分与工作部分中心线不同轴度≤0.02
对于缺口试样,缺口与试样中心线的垂直度为0.02mm,缺口底部半径公差为0.02mmc4.3.2矩形横截面试样的公差见表4。表4
试样宽度,b
最大最小宽度差
夹持部分与工作部分中心线不对称度≤0.02
对具有边缺口的试样,两缺口中心线与试样中心线应垂直,不垂直度小于0.02mm。对具有中心缺口的试样,其缺口中心与试样中心线不对称度小于0.03mm,在试样长度为100~200mm时,夹持部分定位孔的中心线与试样中心线的不对称度为0.05mm。4.3.3光滑试样表面应抛光,表面粗糙度Ra<0.32mm,缺口粗糙度为Ra<0.32mm,试样表面不应有任何划伤或损伤。试样工作部分与过渡圆孤的连接应光滑。4.3.4对于圆形横截面试样工作部分直径的测量精度为0.01mm;对矩形横截面试样工作部分截面尺寸的测量误差,厚度为0.01mm,宽度为0.02mm。测量尺寸时应防止损伤试样表面。4.4试样的制备
HB5287-96
4.4.1试样的取样部位和方向根据有关标准和双方协议执行。4.4.2试样的加工工艺对疲劳试验结果影响很大,因此选择适当的加工工艺并严格遵守是非常重要的。在加工过程中为了避免材料过热和加工硬化,并使表面残余应力减到最小,以及保证试样表面状态尽可能一致,推荐采用附录B规定的加工工艺。4.4.3试样加工完毕应要善保存防止变形、表面损伤和腐蚀。4.4.4用放大20倍的光学仪器检验试样工作表面,不充许有缺陷。4.4.5试样的缺口应在热处理以后进行加工,缺口的形状、尺寸应用不低于50倍的光学仪器检查。
5试验机
5.1试验可在各种类型的疲劳试验机上进行。5.2疲劳试验机应满足下列要求:5.2.1试验机的静载荷按JJG139-74进行校正,动态标定时,平均载荷和载荷变程的误差均不大于载荷循环中最大载荷的土3%,或试验机满量程的0.5%,取其中大者。5.2.2为了确保轴向加载,要求试验机的儿何筒轴度不大于0.1%,同时推荐用贴应变片测量试样弯曲变形的方法,检查试验机连同装夹试样系统的同轴度。采用直径为10土0.02mm,标距为50mm的圆形截面试样,在试样工作部分的中部圆周上平均分布贴4片电阻值相同的应变片,它们的中心精确地保持在试样的同一个横截面上,并采用半桥连接。然后用电桥检查4片应变片的电阻值,各片之间的差值不应大于测量仪器所允许的范围。在试样不承受载荷时予调平衡。注:如有特殊需要,可根据双方协议确定试样表面粗度。从试验机每挡量程的10%起至满量程,在5个载荷水平下(在应力与应变呈线性比例关系范围内)进行测量,并记录4个应变片指示的变形值,然后卸去负荷,照此重复测量3次。弯曲变形率PBS用下式计算:
PBS = (q13)* + (q2)
×100%
式中:9。=9i+++
q13 =[(q - qo) -(qq)1/2
=(qi-Q)/2
q24 =[(qz - qo) -(q4 q。)]/2=(q-q4)/2
91>2v3>94分别是4个应变片三次测量的变形平均值。(1)
然后将试样分别旋转90°、180°、270°在每一个位置同样进行上述测量和计算。在所测定的负荷范围内,弯曲变形率均不应大于10%。5.2.3夹具的设计应保证良好的同心度,如因夹具不满足同心度的要求时应改进设计。5
6试验程序
HB5287-96
6.1装夹试样必须保证施加于试样上的载荷是沿轴向的。6.2施加载荷应平稳,不得超载。试验过程中应经常检测载荷。6.3试验频率
频率的选择取决于试验机的类型、试样的刚度和被试材料的性质。一般在5~200Hz范围内进行试验。对于同一批试样,应在大致相同的频率下进行试验,频率相差过大,可能对试验结果有影响。如需要在不同频率下试验,必须经过试验验证,并在试验报告中予以说明。试验过程中试样工作部分的温度不得超过60℃,否则必须降低试验频率或对试样进行冷却。
6.4试样在规定的应力下连续试验,直至规定的循环次数或试样失效。6.5试样失效发生在非工作部分,试验结果作废。7疲劳极限和S一N曲线的测定
7.1疲劳极限的测定
推荐用升降法测定材料的疲劳极限。有效试样数为15根左右,选择合适的应力增量(或降低量)是升降法试验中一个重要的程序。一般光滑试样的应力增量选择在预计疲劳极限的5%以内。缺口试样的应力增量适当减少。应使第一根试样的试验应力水平略高于预计疲劳极限。根据上一根的试验结果(失效或通过)决定下一根试样的试验应力水平(降低或升高),直至完成全部试验。对第一次出现相反结果以前的试验数据,如在以后试验数据的波动范围之内则有效。升降的应力水平数一般为4级左右。如果试验的目的只要求出中值疲劳极限n,则按下式进行计算:1
式中:n---有效试验总次数:
m—升降应力水平级数;
a;第i级应力水平;
V.一一第i级应力水平下的试验次数。(2)
如果试验还要求出疲劳极限的标准差,则必须将相邻应力水平的各数据点按一个破坏点(×)和一个越出点(0)配成一对,如果升降图是封闭的,则所有试验点都能配成对子,这时中值疲劳强度或疲劳极限的估计量6s为:aso=
式中:n*一配成的对子总数;
m*-配成对子的级数,为升降法级数减1,即m*=m-1;o=(o+gi+1)/2;
V”一相邻两级配成的对子数。
HB5287-96
疲劳极限或疲劳强度的子样标推差S*按下式计算:S
n*(n*- 1)
7.2S-N曲线的测定
获得一条S一N曲线,通常取4~6级或更多的应力水平。用升降法求得的疲劳极限做为S-N曲线最低应力水平,其它应力水平一般用成组试验法进行试验。当成组试验法不能满足要求时,也可以用升降法测定在给定某一长寿命下(如10°)的疲劳强度。成组试验法就是在每一个应力水平做一组试样,每组试样的数量取决于试验数据的分散程度和所要求的置信度,一般随着应力水平的降低逐渐增加,每组应不少于三根试样。成组试验法中值对数疲劳寿命X按下式计算:
1logN;
X = logNso =
式中:N.
-组试验中第i个试样的疲劳寿命;组试样的总数:
Nso—具有50%存活率的疲劳寿命即中值疲劳寿命。对数疲劳寿命标准差S按下式计算:n Z(logN,)2
变异系数Cv按下式计算:
n(n -1)
以试验应力为纵坐标,以疲劳寿命为横坐标拟合成的应力-寿命曲线为某材料的S-N曲线。用上述方法画出的S-N曲线即为中值S-N曲线。具有50%的存活率。如果需要提供具有某置信度(如95%)和在一定误差条件的中值S-N曲线时,必须保证每组最少试样个数。见附录C。
8试验结果的表示法
8.1列表法
表中应包括试样号、试样形式、应力集中系数、试验顺序、材料基本状况、试验条件、循环次数等基本数据。可以根据需要给出原始记录形式的表格或经整理的表格。见附录D。8.2解析法
推荐用下列方程表达S-N曲线。
logN = A, + A20mz
logN = A, + Azlogomux
HB5287-96
logN = A, + A2(omr -A)
logN = A; + A2log(omx - A3)
式中:A1、A2、A3—待定常数。8.3图示法
8.3.1S-N曲线
这是最常用的一种疲劳试验结果的表示方法,绘制S一N曲线时,疲劳寿命采用对数坐标,应力可采用线性坐标或对数坐标。在曲线图上应注明必要的试验参数。见图12和图13。8.3.2等寿命曲线
等寿命曲线是由同批试样至少3条S一N曲线转换绘制而成的。它表示在给定疲劳寿命下的最大应力、最小应力、应力幅、平均应力和应力比之间的关系,见图14。无论用哪种方法表示试验结果,都应注明被试材料、试样状况和试验条件等。9试验报告
9.1试验报告包括下述内容:
a.被试材料的名称、产物、炉号、状态、规格、冶炼方法、制造及热处理工艺、化学成分、力学性能等;
b.取样方向、试样的形状尺寸应力集中系数、表面状态等;C.试样的主要制造工艺;
d.试验机的型号、试验频率、加载方式、应力比、平均应力、应力幅、波形等;e.试验环境:试验温度、湿度及其变化范围;f.试验结果:按第8章规定形式报告试验结果;g.其它。
@00.03A-B
GB145-59
HB 5287-96
图3直径7mm的光滑试样(k=1)
HB5287-96
GB145-59
?00.03A-B
图4直径7mm的光滑试样(k=1)
89-1 ×2E-2
图5直径10mm的光滑试样(k.=1)其余
GB145-59
小提示:此标准内容仅展示完整标准里的部分截取内容,若需要完整标准请到上方自行免费下载完整标准文档。

标准图片预览:
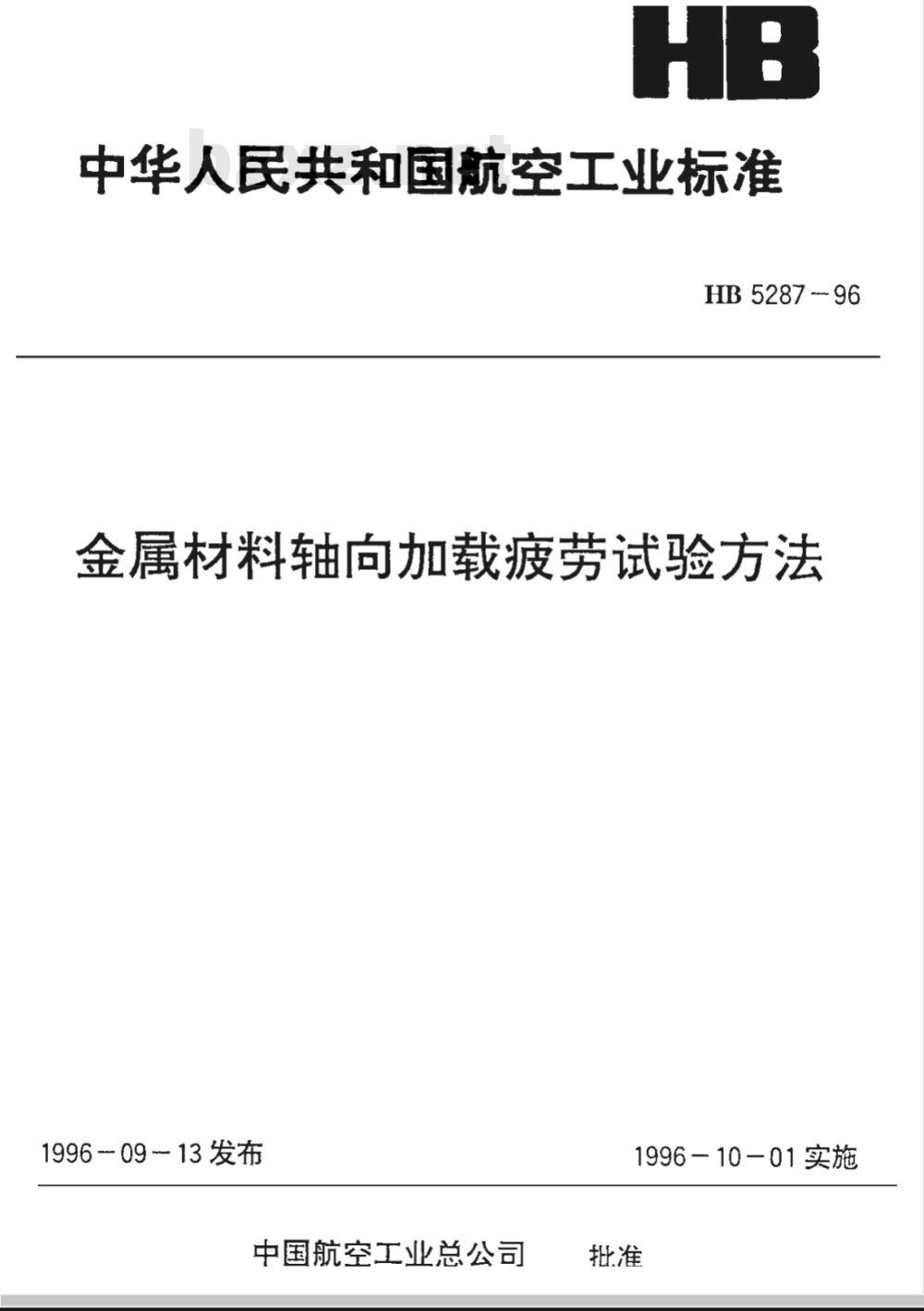

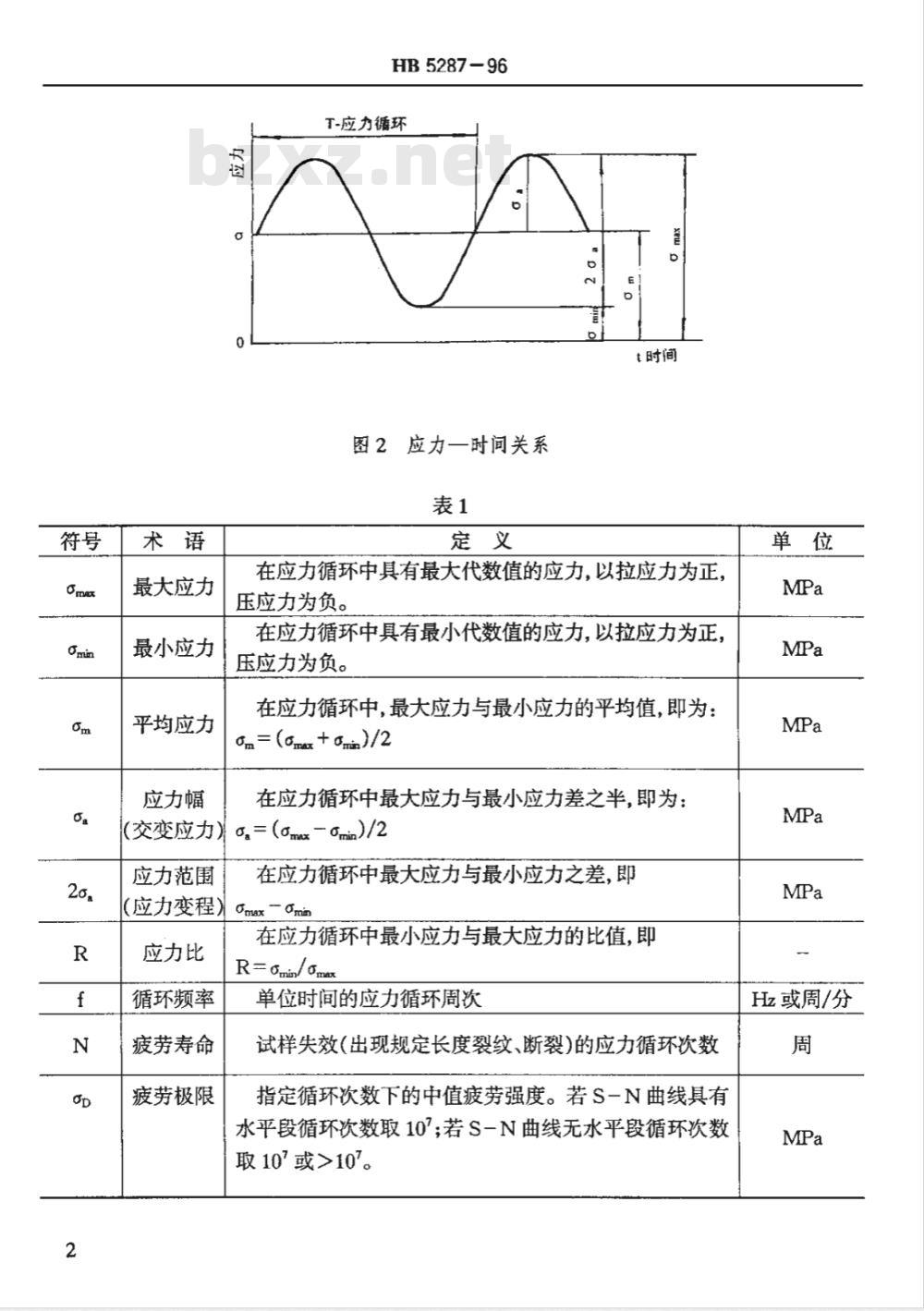
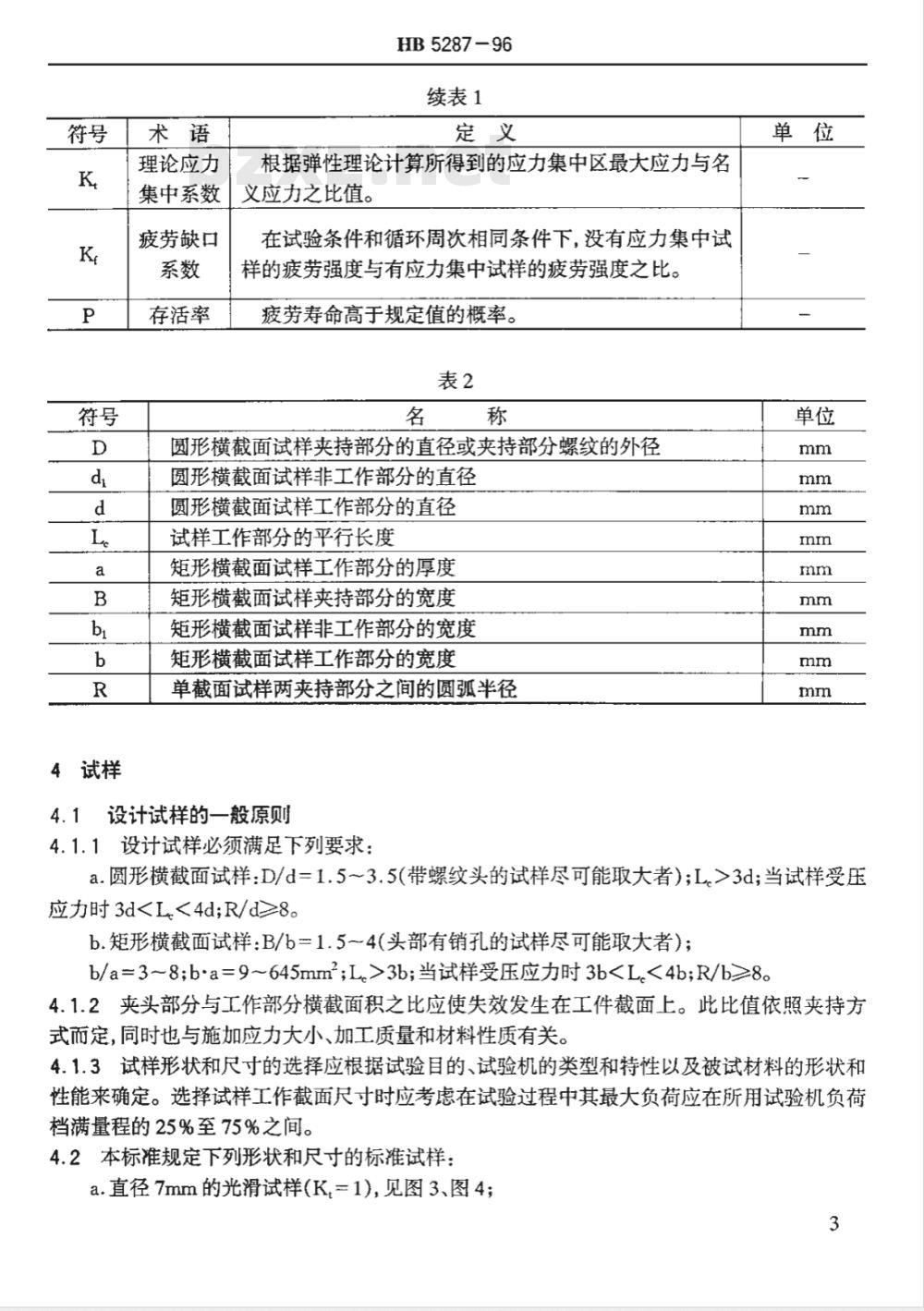
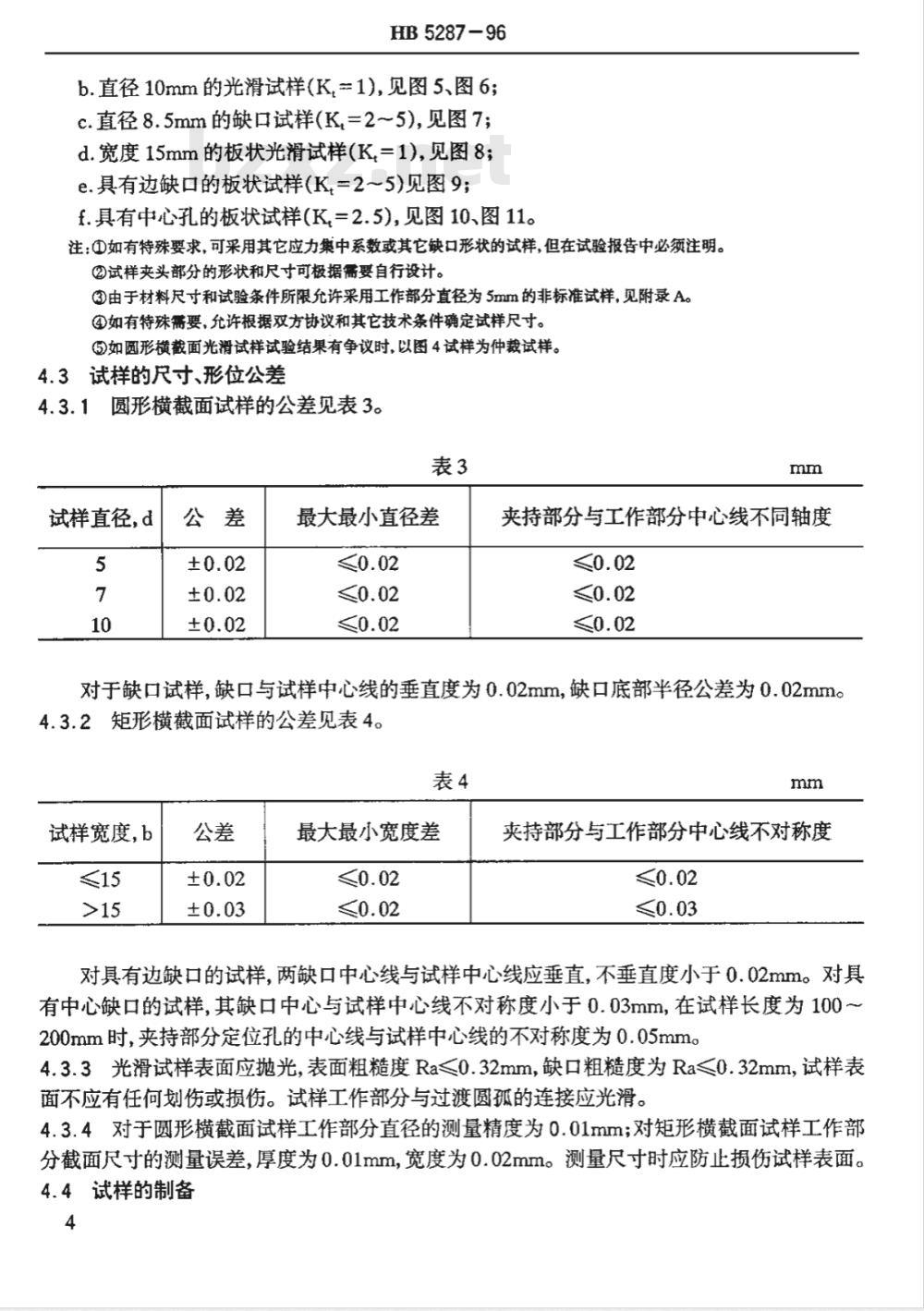
- 其它标准
- 热门标准
- 航空工业行业标准(HB)
- HB4267-2004 钢丝螺套用标准螺孔环的校通-通螺纹塞规 T—T
- HB5453-2004 铝合金化学铣切保护涂料规范
- HB6911-1994 数控铣床加工铝合金用三齿削平型直柄粗加工立铣刀 d=25~45mm
- HB7546-1997 加工钛合金用焊硬质合金螺旋刀片的二齿削平型直柄数控立铣刀 d=16~32mm
- HB5220.5-2008 高温合金化学分析方法 第5部分:碘酸钾容量法测定硫含量
- HB2-1972-1983 双盘快卸锁
- HB2654-1976 板牙夹头用转接套
- HB2779-1976 立式车床用短转接衬套
- HB2661-1976 钻头及车刀转接刀座
- HB5483-1991 飞机整体油箱及燃油舱用聚硫密封剂通用规范
- HB2664-1976 转接刀座用切向车刀刀杆
- HB7559-1997 加工钛合金用焊硬质合金螺旋刀片的二齿端刃过中心莫氏圆锥柄数控立铣刀 d=16~32mm
- HB2753-1976 转接刀座
- HB2790-1976 转接衬套d=12~34
- HB5289-1997 XM16室温硫化聚硫密封剂
- 行业新闻
- Republic称:您现在可以通过Solana上的Mirror代币投资SpaceX
- 特朗普高喊建立“比特币强国”,矿企却快挺不住了?
- Tether 執行長喊今年要成「全球最大」比特幣礦企:挖礦才可保 BTC 安全
- 比特币重回107,000美元高位,但MVRV指标显露牛市疲态
- XRP将获黄金支持并触及2000美元;XRP大军梦想的现实检验
- Sahara AI为币安上市铺路,推出8%空投
- 比特币主导地位创新高,山寨币季希望渐消
- 香港《穩定幣法》8/1生效,金管局總裁余偉文:穩定幣不是投機工具,三大門檻構成港元護城河
- Verasity突破下降楔形形态——多头重掌控制权,目标涨幅46%
- 从CoinDCX到CoinSwitch:探索印度顶级加密货币应用
- WazirX迈向重组之路,新加坡法院最新批准
- 本周最佳加密货币:SUI、TRX和ONDO展现价格强势
- 目标1美元:随着HYPE飙升和DOGE疲软,为何Unstaked成为加密货币购买清单榜首
- 卡尔达诺考虑设立主权财富基金以应对稳定币流动性缺口
- 治理失效、空投乱象、价值错配:加密行业需要什么样的代币?
请牢记:“bzxz.net”即是“标准下载”四个汉字汉语拼音首字母与国际顶级域名“.net”的组合。 ©2009 标准下载网 www.bzxz.net 本站邮件:bzxznet@163.com
网站备案号:湘ICP备2023016450号-1
网站备案号:湘ICP备2023016450号-1