- 您的位置:
- 标准下载网 >>
- 标准分类 >>
- 航空工业行业标准(HB) >>
- HB/Z 358-2005 航空钢弹簧制件热处理
标准号:
HB/Z 358-2005
标准名称:
航空钢弹簧制件热处理
标准类别:
航空工业行业标准(HB)
标准状态:
现行-
发布日期:
2005-12-26 -
实施日期:
2006-05-01 出版语种:
简体中文下载格式:
.rar.pdf下载大小:
3.64 MB

点击下载
标准简介:
标准下载解压密码:www.bzxz.net
本指导性技术文件规定了航空钢弹簧制件热处理的常用材料牌号及技术标准、设备、工艺材料、工艺、质量控制和检验等。本指导性技术文件适用于航空钢弹簧制件的热处理。 HB/Z 358-2005 航空钢弹簧制件热处理 HB/Z358-2005

部分标准内容:
中华人民共和国航空行业标准
FL6310
HB/Z358-2005
航空钢弹簧制件热处理
Heat treatment for spring parts of steel for aviation2005-12-26发布
国防科学技术工业委员会发布
2006-05-01实施
本指导性技术文件的附录A、附录B资料性附录。本指导性技术文件由中国航空工业第一集团公司提山。本指导性技术文件由中国航空综合技术研究所、北京航空材料研究院归口。HB/Z358-2005
本指导性技术文件起草单位:庆安集团有限公司、太原航空仪表有限公司、沈阳飞机工业(集团)有限公司。
本指导性技术文件主要起草人:樊世昆、左卫民、刘连生、焦清洋。1范围
航空钢弹簧制件热处理
HB/Z358-2005
本指导性技术文件规定了航空钢弹簧制件热处理的常用材料牌号及技术标准、设备、工艺材料、工艺、质量控制和检验等。
本指导性技术文件适用于航空钢弹簧制件的热处理。2规范性引用文件
下列文件中的条款通过本指导性技术文件的引用而成为本指导性技术文件的条款。凡是注日期的引用文件,其随后所有的修改单(不包含勘误的内容)或修订版均不适用于本指导性技术文件,然而,鼓励根据本指导性技术文件达成协议的各方研究是否可使用这些文件的最新版本。凡是不注日期的引用文件,其最新版本适用于本指导性技术文件。GB/T224
GB/T228
GB/T230
钢的脱碳层深度测定法
金属材料室温拉伸试验方法
金属洛氏硬度试验方法
碳素工具钢技术条件
GB/T1298
GB/T3279
GB/T4231
GB/T4240
GB/T4357
GB/T4358
弹簧钢热轧薄钢板
弹簧用不锈钢冷轧钢带
不锈钢丝
碳素弹簧钢丝
重要用途碳素弹簧钢丝
GB/T5218
合金弹簧钢丝
GJB3320
GJB5259
GJB5260
航空用不锈钢弹簧丝规范
航空用合金弹簧钢丝规范
航空用碳素弹簧钢丝规范
热处理工艺质量控制
HB5354
HB5408
HB5415
HB/Z80
HB/Z136
HB/Z191
航空热处理用盐规范
热处理淬火用油
航空用不锈钢和耐热钢热处理说明书航空结构钢热处理工艺
航空结构钢不锈钢真空热处理说明书YB/T5008
阀门用油淬火一回火铬钒合金弹簧钢丝YB/T5058
弹簧钢、工具钢冷轧钢带
热处理弹簧钢带
YB/T5063
YB/T5103
YB/T5104
YB/T5105
YB/T5136
YB(T)11
油淬火-回火碳素弹簧钢丝
油淬火一回火硅锰合金弹簧钢丝阀门用油淬火一回火铬硅合金弹簧钢丝阀门用铬钒弹簧钢丝
弹簧用不锈钢丝
HB/Z358-2005
常用材料牌号及技术标准
航空钢弹簧制件常用的材料牌号及技术标准见表1。未列入表1的其他牌号钢弹簧制件的热处理可参照本指导性技术文件进行。
表1航空钢弹簧制件常用材料牌号及技术标准材料种类
碳素弹簧钢丝
油淬火-回火弹簧钢丝
热处理弹簧钢带
合金弹簧钢丝
合金弹簧钢带
碳素工具钢
不锈钢
I组、II组
B组、C组、D组
E级、F级、G级
材料牌号
55、60、65、65Mn、70、70Mn
50CrVA
55CrSiA
60Si2MnA
65Mn、60Si2MnA、70Si2CrA
60Si2MnA、65Si2MnWA
50CrVA
65Mn、60Si2MnA、65Si2MnWA、50CrVAT7A、T8A、T9A
1Cr18Ni9
1Cr18Ni9Ti、4Cr13、OCr18Ni11Ti3Cr13
0Cr19Ni10、0Cr17Ni8Al
0Cr12Mn5Ni4Mo3Al
0Cr17Ni7A1
1Cr11Ni23Ti3MoB
GJB5260
GB/T4357
GB/T4358
技术标准
专用技术条件
YB/T5103
YB/T5008
YB/T5105
YB/T5104
YB/T5063
GJB5259、GB/T5218
GJB5259、GB/T5218、YB/T5136
GB/T3279、YB/T5058
GB/T1298
GJB 3320、YB(T) 11
GB/T4240
GJB3320、GB/T4240
YB(T)11
GJB3320
GJB3320、GB/T4231
专用技术条件
碳素弹簧钢丝的I组、I组、II,组、B组、C组、D组、E级、F级、G级为强度级别代号,每种级别在相应材料技术标准中可选用不同的材料牌号。4设备
4.1加热和冷却设备
4.1.1弹簧制件的淬火、正火和退火加热应在盐浴炉、保护气氛炉或真空炉中进行。若使用空气炉进行加热,制件应用木炭或铸铁屑覆盖保护。回火、消除应力和时效加热应在碱浴炉、硝盐炉、真空炉、油浴炉或空气炉中进行。
4.1.2淬火、回火、时效和消除应力热处理,应选用HB5354规定的I类或I类以上加热炉。预备热处理应选用HB5354规定的IV类或IV类以上加热炉。4.1.3加热炉应配备温度自动调节、记录和报警装置,并应符合HB5354的规定。4.1.4保护气氛炉应能根据热处理工艺要求调节和控制炉内气氛,保护气体不应直接冲刷弹簧。4.1.5盐浴炉应定期用校正剂脱氧,并按有关标准或专用技术文件进行脱氧效果检查。2
4.1.6真空炉应符合HB/Z191的规定。4.1.7油浴炉的使用温度应在所用油的安全使用范围内。HB/Z358-2005
4.1.8硝盐浴或碱浴的成分、配比、熔化温度和使用温度应符合HB/Z136的规定,槽液技术要求应符合HB5354的规定。
4.1.9淬火冷却槽应符合HB5354的规定。4.2清理、清洗设备
4.2.1弹簧制件清理可用喷砂机、喷丸机、酸洗槽等设备,并应根据制件表面状态要求,选用合适的砂、丸的粒度,砂或丸中不应混有对制件产生有害影响的成分。不推荐采用酸洗方法进行清理,若使用酸洗方法,应防止产生脆、过腐蚀等缺陷。4.2.2清洗设备应满足弹簧制件表面质量的要求。4.3工装
4.3.1加热时装载制件的工装夹具不应对制件产生有害影响,并应保证制件放置平稳、变形小以及进出炉方便。
4.3.2制件变形要求严时,可使用专用夹具或模具。5工艺材料
5.1热处理用盐应符合HB5408的要求,碱和校正剂应符合HB5354的要求,盐、碱利校正剂对弹簧制件不应产生超过规定深度的脱碳、增碳、腐蚀及其它有害作用。5.2淬火油应符合HB5415或专用技术文件的要求,使用温度一般在10℃~100℃的范围内。5.3火用水和水溶液不应含有对弹簧制件产生不良影响的物质。水溶液的溶质应符合相应标准的要求,水溶液的成分和浓度应符合弹簧制件淬火的要求。5.4保护用木炭和铸铁屑使用前应烘干,木炭颗粒适中。木炭和铸铁屑不应对弹簧制件产生脱碳、增碳或其它有害影响。
6工艺
6.1冷拉钢丝弹簧制件
6.1.1材料状态和制件热处理作用弹簧制件制造前的材料状态为形变硬化,弹簧制件热处理的目的是为了消除应力。6.1.2摆放
弹簧制件消除应力处理时应注意摆放,避免弹簧制件热处理后变形。6.1.3变形趋势
消除应力后弹簧制件尺寸会略有变化。绕在心轴上的弹簧制件经热处理卸下心轴后,直径方向的尺寸会稍有涨大;自由状态的碳素钢丝弹簧制件热处理后直径有收缩减小趋势,自由状态的不锈钢弹簧制件热处理后直径有涨大趋势。温度越高,涨大或减小的趋势就越明显。6.1.4重复热处理
消除应力处理重复次数不限。
6.1.5热处理制度
冷拉钢丝弹簧制件的消除应力制度见表2。6.2油淬火一回火弹簧钢丝和热处理弹簧钢带弹簧制件6.2.1材料状态和制件热处理作用弹簧制件制造前的材料状态为油淬火一回火的钢丝或已经热处理的钢带,弹簧制件热处理的目的为消除应力。
6.2.2重复热处理
HB/Z358-2005
消除应力处理重复次数不限。
6.2.3热处理制度
油淬火一回火弹簧钢丝和热处理弹簧钢带弹簧制件的消除应力制度见表3。6.3沉淀硬化型不锈钢弹簧制件
6.3.1材料状态和制件热处理作用弹簧制件制造前的材料状态为固溶处理十冷变形,弹簧制件热处理的目的是时效强化。6.3.2重复热处理
时效处理的重复次数不限。
6.3.3热处理制度
沉淀硬化型不锈钢弹簧制件的时效处理制度见表4。表2冷拉钢丝弹簧制件的消除应力制度材料种类
碳素弹簧钢丝
不锈弹簧钢丝
材料牌号
I组、ⅡI组、II,组、B
组、C组、D组、E
级、F级、G级
ICr18Ni9
iCr18Ni9Ti
0Cr19Ni10
OCr18Ni11Ti
260300
260~450b
保温时间
浴炉:(15~~20)min+
5min/mun
空气炉:(20~25)min+
(10~15)min/mm。
1常用温度为280℃
b根据弹簧制件的具体情况,温度可适当调整,常用温度为350℃~450℃。冷却介质
空气或水“
空气或水‘
从浴炉(硝盐炉、碱槽)中取出的弹簧制件立即放入热水中冷却和清洗,然后用流动水清洗,直到硝盐或碱清洗于净为止。最后用压缩空气吹干或在炉中加热至100℃~150℃烘干。表3油淬火一回火弹簧钢丝和热处理弹簧钢带弹簧制件的消除应力制度材料品种
油淬火-回火弹簧钢丝
热处理弹簧钢带
材料牌号
50CrVA
55CrSiA
60Si2MnA
55、60、65、65Mn、
70、70Mn
65Mn、60Si2MnA
70Si2CrA
380~-400
260~300g
300~420
保温时间
浴炉:(15~20)min+
5min/mm。
空气炉:(20~25)min+
(10~15)min/mm。
冷却介质
空气或水。
常用温度为280℃。
。从浴炉(硝盐炉、碱槽)中取出的弹簧制件立即放入热水中冷却和清洗,然后用流动水清洗,直到硝盐或碱清洗干净为止。最后用压缩空气吹干或在炉中加热至100℃~150℃烘干。表4
沉淀硬化型不锈钢弹簧制件的时效处理制度材料牌号
0Cr17Ni8Al
OCr17Ni7A/b
温度:
420500
保温时间
抗拉强度
Rm(og)
R.(o)增加值不小于245
低硬状态(DY)R(og)≥1230
半硬状态(BY)R(%)≥1420
硬状态(Y)Rm(og)≥1720
不同规格按GJB3320的规定
材料牌号
0Cr12Mn5Ni4M03Al
1Cr11Ni23Ti3MoB
温度:
500~540
保温时间
表4(续)
抗拉强度
Rm(og)
不同规格按GJB3320的规定
HB/Z358-2005
≥980(直径2mm5mm丝材,冷作硬化20%)≥1080(直径2mm~5mm丝材,冷作硬化40%)≥1130(直径1mm2mm丝材,冷作硬化20%)≥1320(直径1mm~2mm丝材,冷作硬化40%)≥1370(直径<1mm丝材,冷作硬化40%~60%)\未给出范围的温度,调整范围为土10℃。b0Cr17Ni7A1弹簧制件的固溶处理十调整处理+时效处理按HB/Z80进行。6.4淬火加回火钢弹簧制件
6.4.1材料状态和制件热处理作用弹簧制件制造前的材料为退火状态或轧制状态。材料预备热处理是为制造弹簧制件做组织和性能准备,弹簧制件最终热处理的日的是通过火或等温淬火后加回火,达到弹性要求。6.4.2重复热处理
6.4.2.1弹簧制件允许进行重复热处理,重复淬火前应进行600℃~680℃的低温退火。重复淬火次数应符合如下规定:
a)对于直径或厚度不大于1mm的弹簧制件,重复淬火次数不超过1次:b)对于直径或厚度大于1mm的弹簧制件,重复淬火次数不超过2次。6.4.2.2弹簧制件回火次数不限。6.4.3·热处理制度
弹簧制件制造前的材料预备热处理制度见表5。弹簧制件淬火和回火的热处理制度及推荐的硬度见表6。表5
预备热处理制度
材料牌号
T7A、T8A、T9A
50CrVA
60Si2MnA
65Si2MnWA
65Mn、70Mn
3Cr13、4Cr13
加热温度
850~870
850~870
850~870
800~820
冷却方式
完全退火或不完全退火
加热温度
760~780
850~870
850~870
850~870
800~820
870~900
冷却方式
低温退火
加热温度
690~710
680~700
680~700
680~700
680700
730~780
3Cr13、4Cr13钢的保温时间按HB/Z80的规定,其它牌号钢的保温时间按HB/Z136的规定。淬火和回火的热处理制度和推荐硬度值表6
材料牌号
T7A、T8A、T9A
50CrVA
60Si2MnA
加热温度
770~790
840870
800830
850~870
冷却介质
油或低温碱浴
油或低溢碱浴
加热温度
360~4003
370~4203
360~410
390~-440
410470此内容来自标准下载网
冷却介质
水或空气
水或空气
热水或油
水或油
冷却方式
推荐硬度值
47~51
HB/Z358-2005
材料牌号
65Si2MnWA
3Cr13、4Cr13
加热温度
840~860
1020~1050b
表6(续)
冷却介质
加热溢度
420470
450~550c
250~350
冷却介质
水或油
水或油
推荐硬度值
直径小于2.8mm的50CrVA钢丝弹簧制件和厚度小于0.5mm的T7A、T8A、T9A钢带弹簧制件,在保证硬度的条件下允许将回火温度降至350℃。b3Cr13、4Cr13可采用960℃~980℃进行痒火,此时问火温度可适当降低。。选择回火温度时,应注意避免回火脆性的不良影响。6.4.3.3钢丝弹簧制件推荐的淬火、回火加热保温时间见表7,钢板、钢带弹簧制件推荐的淬火、回火加热保温时间见表8。65Si2MnWA钢弹簧制件淬火保温时间可按表7、表8推荐的时间延长一倍。根据弹簧制件的具体要求,保温时间可适当调整。当弹簧制件装心轴热处理时,淬火和回火的保温时间根据心轴尺寸的大小应适当延长。采用真空炉进行淬火加热时,保温时间按HB/Z191的规定。表7钢丝弹簧制件淬火、回火加热保温时间热处理类型
热处理类型
炉子类型
盐浴炉
空气炉
空气炉
不同钢丝直径弹簧制件的保温时间min
>1mm~2mm
>2mm~4mm
10~12
>4mm~8mm
30~40
表8钢板、
钢带弹簧制件淬火、回火加热保温时间炉子类型
盐浴炉
空气炉
空气炉
保温时间
(3~5)min+(0.5~1)min/mm条件厚度(1015)min+1min/mm条件厚度
(10~20)min+(0.5~1)min/mm条件厚度(20~40)min+(1~2)min/mm条件厚度>8mm~10mm
6.4.3.4采用真空炉进行小弹簧制件的油淬时,由于制件的热容量较小,转移过程中温度降低较多容易产生淬火效果差的问题,可采取增大热容量的措施来解决。6.4.3.5弹簧制件火至回火之间的间隔时间一般不应超过2h。6.4.3.6为了提高弹簧制件的强韧性和使用寿命,减少热处理变形,可采用等温淬火或分级淬火代替油淬,但在高温应力松弛或变条件下工作的弹簧制件,不应进行等温淬火或分级淬火。常用钢弹簧制件的等温或分级淬火制度见表9。表9:
常用钢弹簧制件的等温或分级淬火制度制件的厚度
材料牌号
S或直径D
等温或分级淬火
加热温度
等温制度
340~360
320~360
320~370
加热温度
抗拉强度
Rm(op)
硬度值
45.5~49.5
45.5~49.5
材料牌号
60Si2MnA
65Si2MnWA
50CrVA
制件的厚度
S或直径D
表9(续)
等温或分级火
加热温度
等温制度b
300340
300~340
280~320
350~400
加热温度
300~340°
300~340°
280~320°
250~300
HB/Z358-2005
抗拉强度
Rm(op)
1420~1810
1520~1810
1520~1760
15201810
硬度值
45.5~50.5
45.5~50.5
45.5~51.5
温度调整范围为士10℃。3Cr13钢的淬火加热保温时间按HB/Z80的规定,其它牌号钢的淬火加热保温时间按HB/Z136的规定。
b等温保温后在40℃~100℃水中或空气中冷却。推荐在与等温淬火相同的温度下进行回火。6.5尺寸稳定化处理
根据弹簧设计要求,螺旋弹簧制件热处理后可进行尺寸稳定化处理。螺旋弹簧制件尺寸稳定化处理是预先通过加载或加温加载的方法使弹簧制件尺寸稳定,尺寸稳定化处理的具体方法参见附录A。7质量控制和检验
7.1质量控制
7.1.1弹簧制件热处理过程应实行全面质量控制,并进行检验,以确保热处理质量。7.1.2热处理原始记录应认真填写并妥善保存,按HB5354有关要求建立完整的热处理质量档案。7.1.3弹簧制件的硬度、抗拉强度应符合图样、本指导性技术文件或专用技术文件的规定。7.1.4弹簧制件的表面质量和尺寸应符合图样或专用技术文件的要求。7.1.5弹簧制件的弹力(载荷)应符合图样或专用技术条件的规定。7.1.6弹簧制件的脱碳和金相组织按HB5354或专用技术文件进行控制。7.1.7弹簧制件热处理常见的缺陷及防止措施参见附录B。7.2检验
7.2.1弹簧制件的脱碳层试验按GB/T224进行。7.2.2弹簧制件的硬度试验按GB/T230进行。7.2.3钢丝直径小至一定尺寸的弹簧制件允许用拉伸试验代替硬度试验。拉伸试验按GB/T228进行。7.2.4弹簧制件的表面质量和尺寸检验、金相组织检验及弹力试验按相应标准或专用技术文件进行。HB/Z358-2005
A.1立定处理
附录A
(资料性附录)
螺旋弹簧制件尺寸稳定化处理方法立定处理方法是将压缩弹簧压并圈或压至一定高度岩干次,或将拉伸弹簧拉伸至最大工作距离1.2倍的长度若干次,一般为10次。A.2强压处理(加荷时效)
强压处理是将弹簧压缩至并圈或压至--定高度保持12h~48h,具体时间由设计人员确定或根据生产经验决定。
A.3加温加荷时效
A.3.1弹簧的加温加荷时效处理一般要经过两次。第一次是在热处理后进行,将弹簧压缩(或拉伸)至最大.T作载荷下的高度,温度按表A.1的规定,保持时间为:65Si2MnWA弹簧不少于7h;50CrVA和ⅡI,、E、F、G组的弹簧不少于2h。第::次是在表面处理后进行,将弹簧压缩(或拉伸)至最大工作载荷下的高度,温度按表A.1的规定,保持时间为:65Si2MnWA弹簧不少于5h;50CrVA和II、E、F、G组的弹簧不少于2h。
A.3.2弹簧经加温加荷时效处理后,为了保持弹簧尺寸稳定,可将弹簧用夹具保持一定长度入库保存。
弹簧的工作温度
>60~100
>100~150
>150~180
表A.1加温加荷时效处理的温度
第一次加温加荷时效处理的温度℃
120±10
200±10
250±10
>180~230
注:允许采用高于工作温度20℃土10℃作为第一次加温加荷时效处理。A.4预疲劳处理(循环稳定处理)第二次加温加荷时效处理的温度℃
100±10
150±10
180±10
230±10
预疲劳处理是将弹簧在工作高(长)度先进行一定次数的加载循环,一般为100~2000次。附录B
(资料性附录)
弹簧制件热处理常见的缺陷及防止措施弹簧制件热处理常见的缺陷及防止措施见表B.1。表B.1
弹簧制件热处理常见的缺陷及防止措施缺陷类型
表面脱碳或元素贫化
硬度不足
变形过大
表面腐蚀
淬火后开裂
脆性大
弹力低
弹力高
产生原因
1、淬火加热盐浴炉脱氧不充分
2、保护气氛未调整好
3、真空炉真空度过高过低,或漏气率太高。1、火转移速度过慢
2、淬火加热表面脱碳
3、淬火温度过高,残余奥氏体过多1、应力过大
2、心轴或夹具设计不合理
3、装炉方式不合理
4、加温加荷时效处理时压缩过分1、盐浴内腐蚀性杂质过高
2、没有及时清理残盐
3、零件表面不洁净
1、原材料有缺陷
2、加热速度过快,没有预热或预热不当3、淬火剂选择不当
4、火加热温度过高,保温时间过长1、在脆性区回火
2、硬度过高
3、过热
1、设计不合理
2、硬度不足
3、表面脱碳或元紫贫化
4、热处理后,材料尺寸变小或弹簧外径变大设计不合理
2、硬度高
3、热处理后,弹簧螺距不均匀或弹簧外径变小
充分脱氧
把气氛调整好
HB/Z358-2005
防止措施
选择适当的真空热处理参数
加快淬火转移速度
盐浴炉充分脱氧,或使用气氛炉、真空炉进行冷处理
充分消除应方
设计合适的心轴或夹具
合理摆放
选用合适的加温加荷时效处理温度和压缩量及时充分脱氧
及时清理残盐
热处理前后加强清洗
加强原材料检验
进行合适的预热
选用合适的淬火剂
选用合适的淬火溢度和保温时间回火时快冷或避免在脆性区回火选用合适的回火温度
选用合适的淬火温度
设计重新计算
按硬度不足原因采取措施
按表面脱碳或元素贫化采取措施热处理时采用合适丁装和减少材料尺寸变小的措施
设计重新计算
提高回火温度
热处理时采用合适工装和减少嫌距不均匀的措施
小提示:此标准内容仅展示完整标准里的部分截取内容,若需要完整标准请到上方自行免费下载完整标准文档。
FL6310
HB/Z358-2005
航空钢弹簧制件热处理
Heat treatment for spring parts of steel for aviation2005-12-26发布
国防科学技术工业委员会发布
2006-05-01实施
本指导性技术文件的附录A、附录B资料性附录。本指导性技术文件由中国航空工业第一集团公司提山。本指导性技术文件由中国航空综合技术研究所、北京航空材料研究院归口。HB/Z358-2005
本指导性技术文件起草单位:庆安集团有限公司、太原航空仪表有限公司、沈阳飞机工业(集团)有限公司。
本指导性技术文件主要起草人:樊世昆、左卫民、刘连生、焦清洋。1范围
航空钢弹簧制件热处理
HB/Z358-2005
本指导性技术文件规定了航空钢弹簧制件热处理的常用材料牌号及技术标准、设备、工艺材料、工艺、质量控制和检验等。
本指导性技术文件适用于航空钢弹簧制件的热处理。2规范性引用文件
下列文件中的条款通过本指导性技术文件的引用而成为本指导性技术文件的条款。凡是注日期的引用文件,其随后所有的修改单(不包含勘误的内容)或修订版均不适用于本指导性技术文件,然而,鼓励根据本指导性技术文件达成协议的各方研究是否可使用这些文件的最新版本。凡是不注日期的引用文件,其最新版本适用于本指导性技术文件。GB/T224
GB/T228
GB/T230
钢的脱碳层深度测定法
金属材料室温拉伸试验方法
金属洛氏硬度试验方法
碳素工具钢技术条件
GB/T1298
GB/T3279
GB/T4231
GB/T4240
GB/T4357
GB/T4358
弹簧钢热轧薄钢板
弹簧用不锈钢冷轧钢带
不锈钢丝
碳素弹簧钢丝
重要用途碳素弹簧钢丝
GB/T5218
合金弹簧钢丝
GJB3320
GJB5259
GJB5260
航空用不锈钢弹簧丝规范
航空用合金弹簧钢丝规范
航空用碳素弹簧钢丝规范
热处理工艺质量控制
HB5354
HB5408
HB5415
HB/Z80
HB/Z136
HB/Z191
航空热处理用盐规范
热处理淬火用油
航空用不锈钢和耐热钢热处理说明书航空结构钢热处理工艺
航空结构钢不锈钢真空热处理说明书YB/T5008
阀门用油淬火一回火铬钒合金弹簧钢丝YB/T5058
弹簧钢、工具钢冷轧钢带
热处理弹簧钢带
YB/T5063
YB/T5103
YB/T5104
YB/T5105
YB/T5136
YB(T)11
油淬火-回火碳素弹簧钢丝
油淬火一回火硅锰合金弹簧钢丝阀门用油淬火一回火铬硅合金弹簧钢丝阀门用铬钒弹簧钢丝
弹簧用不锈钢丝
HB/Z358-2005
常用材料牌号及技术标准
航空钢弹簧制件常用的材料牌号及技术标准见表1。未列入表1的其他牌号钢弹簧制件的热处理可参照本指导性技术文件进行。
表1航空钢弹簧制件常用材料牌号及技术标准材料种类
碳素弹簧钢丝
油淬火-回火弹簧钢丝
热处理弹簧钢带
合金弹簧钢丝
合金弹簧钢带
碳素工具钢
不锈钢
I组、II组
B组、C组、D组
E级、F级、G级
材料牌号
55、60、65、65Mn、70、70Mn
50CrVA
55CrSiA
60Si2MnA
65Mn、60Si2MnA、70Si2CrA
60Si2MnA、65Si2MnWA
50CrVA
65Mn、60Si2MnA、65Si2MnWA、50CrVAT7A、T8A、T9A
1Cr18Ni9
1Cr18Ni9Ti、4Cr13、OCr18Ni11Ti3Cr13
0Cr19Ni10、0Cr17Ni8Al
0Cr12Mn5Ni4Mo3Al
0Cr17Ni7A1
1Cr11Ni23Ti3MoB
GJB5260
GB/T4357
GB/T4358
技术标准
专用技术条件
YB/T5103
YB/T5008
YB/T5105
YB/T5104
YB/T5063
GJB5259、GB/T5218
GJB5259、GB/T5218、YB/T5136
GB/T3279、YB/T5058
GB/T1298
GJB 3320、YB(T) 11
GB/T4240
GJB3320、GB/T4240
YB(T)11
GJB3320
GJB3320、GB/T4231
专用技术条件
碳素弹簧钢丝的I组、I组、II,组、B组、C组、D组、E级、F级、G级为强度级别代号,每种级别在相应材料技术标准中可选用不同的材料牌号。4设备
4.1加热和冷却设备
4.1.1弹簧制件的淬火、正火和退火加热应在盐浴炉、保护气氛炉或真空炉中进行。若使用空气炉进行加热,制件应用木炭或铸铁屑覆盖保护。回火、消除应力和时效加热应在碱浴炉、硝盐炉、真空炉、油浴炉或空气炉中进行。
4.1.2淬火、回火、时效和消除应力热处理,应选用HB5354规定的I类或I类以上加热炉。预备热处理应选用HB5354规定的IV类或IV类以上加热炉。4.1.3加热炉应配备温度自动调节、记录和报警装置,并应符合HB5354的规定。4.1.4保护气氛炉应能根据热处理工艺要求调节和控制炉内气氛,保护气体不应直接冲刷弹簧。4.1.5盐浴炉应定期用校正剂脱氧,并按有关标准或专用技术文件进行脱氧效果检查。2
4.1.6真空炉应符合HB/Z191的规定。4.1.7油浴炉的使用温度应在所用油的安全使用范围内。HB/Z358-2005
4.1.8硝盐浴或碱浴的成分、配比、熔化温度和使用温度应符合HB/Z136的规定,槽液技术要求应符合HB5354的规定。
4.1.9淬火冷却槽应符合HB5354的规定。4.2清理、清洗设备
4.2.1弹簧制件清理可用喷砂机、喷丸机、酸洗槽等设备,并应根据制件表面状态要求,选用合适的砂、丸的粒度,砂或丸中不应混有对制件产生有害影响的成分。不推荐采用酸洗方法进行清理,若使用酸洗方法,应防止产生脆、过腐蚀等缺陷。4.2.2清洗设备应满足弹簧制件表面质量的要求。4.3工装
4.3.1加热时装载制件的工装夹具不应对制件产生有害影响,并应保证制件放置平稳、变形小以及进出炉方便。
4.3.2制件变形要求严时,可使用专用夹具或模具。5工艺材料
5.1热处理用盐应符合HB5408的要求,碱和校正剂应符合HB5354的要求,盐、碱利校正剂对弹簧制件不应产生超过规定深度的脱碳、增碳、腐蚀及其它有害作用。5.2淬火油应符合HB5415或专用技术文件的要求,使用温度一般在10℃~100℃的范围内。5.3火用水和水溶液不应含有对弹簧制件产生不良影响的物质。水溶液的溶质应符合相应标准的要求,水溶液的成分和浓度应符合弹簧制件淬火的要求。5.4保护用木炭和铸铁屑使用前应烘干,木炭颗粒适中。木炭和铸铁屑不应对弹簧制件产生脱碳、增碳或其它有害影响。
6工艺
6.1冷拉钢丝弹簧制件
6.1.1材料状态和制件热处理作用弹簧制件制造前的材料状态为形变硬化,弹簧制件热处理的目的是为了消除应力。6.1.2摆放
弹簧制件消除应力处理时应注意摆放,避免弹簧制件热处理后变形。6.1.3变形趋势
消除应力后弹簧制件尺寸会略有变化。绕在心轴上的弹簧制件经热处理卸下心轴后,直径方向的尺寸会稍有涨大;自由状态的碳素钢丝弹簧制件热处理后直径有收缩减小趋势,自由状态的不锈钢弹簧制件热处理后直径有涨大趋势。温度越高,涨大或减小的趋势就越明显。6.1.4重复热处理
消除应力处理重复次数不限。
6.1.5热处理制度
冷拉钢丝弹簧制件的消除应力制度见表2。6.2油淬火一回火弹簧钢丝和热处理弹簧钢带弹簧制件6.2.1材料状态和制件热处理作用弹簧制件制造前的材料状态为油淬火一回火的钢丝或已经热处理的钢带,弹簧制件热处理的目的为消除应力。
6.2.2重复热处理
HB/Z358-2005
消除应力处理重复次数不限。
6.2.3热处理制度
油淬火一回火弹簧钢丝和热处理弹簧钢带弹簧制件的消除应力制度见表3。6.3沉淀硬化型不锈钢弹簧制件
6.3.1材料状态和制件热处理作用弹簧制件制造前的材料状态为固溶处理十冷变形,弹簧制件热处理的目的是时效强化。6.3.2重复热处理
时效处理的重复次数不限。
6.3.3热处理制度
沉淀硬化型不锈钢弹簧制件的时效处理制度见表4。表2冷拉钢丝弹簧制件的消除应力制度材料种类
碳素弹簧钢丝
不锈弹簧钢丝
材料牌号
I组、ⅡI组、II,组、B
组、C组、D组、E
级、F级、G级
ICr18Ni9
iCr18Ni9Ti
0Cr19Ni10
OCr18Ni11Ti
260300
260~450b
保温时间
浴炉:(15~~20)min+
5min/mun
空气炉:(20~25)min+
(10~15)min/mm。
1常用温度为280℃
b根据弹簧制件的具体情况,温度可适当调整,常用温度为350℃~450℃。冷却介质
空气或水“
空气或水‘
从浴炉(硝盐炉、碱槽)中取出的弹簧制件立即放入热水中冷却和清洗,然后用流动水清洗,直到硝盐或碱清洗于净为止。最后用压缩空气吹干或在炉中加热至100℃~150℃烘干。表3油淬火一回火弹簧钢丝和热处理弹簧钢带弹簧制件的消除应力制度材料品种
油淬火-回火弹簧钢丝
热处理弹簧钢带
材料牌号
50CrVA
55CrSiA
60Si2MnA
55、60、65、65Mn、
70、70Mn
65Mn、60Si2MnA
70Si2CrA
380~-400
260~300g
300~420
保温时间
浴炉:(15~20)min+
5min/mm。
空气炉:(20~25)min+
(10~15)min/mm。
冷却介质
空气或水。
常用温度为280℃。
。从浴炉(硝盐炉、碱槽)中取出的弹簧制件立即放入热水中冷却和清洗,然后用流动水清洗,直到硝盐或碱清洗干净为止。最后用压缩空气吹干或在炉中加热至100℃~150℃烘干。表4
沉淀硬化型不锈钢弹簧制件的时效处理制度材料牌号
0Cr17Ni8Al
OCr17Ni7A/b
温度:
420500
保温时间
抗拉强度
Rm(og)
R.(o)增加值不小于245
低硬状态(DY)R(og)≥1230
半硬状态(BY)R(%)≥1420
硬状态(Y)Rm(og)≥1720
不同规格按GJB3320的规定
材料牌号
0Cr12Mn5Ni4M03Al
1Cr11Ni23Ti3MoB
温度:
500~540
保温时间
表4(续)
抗拉强度
Rm(og)
不同规格按GJB3320的规定
HB/Z358-2005
≥980(直径2mm5mm丝材,冷作硬化20%)≥1080(直径2mm~5mm丝材,冷作硬化40%)≥1130(直径1mm2mm丝材,冷作硬化20%)≥1320(直径1mm~2mm丝材,冷作硬化40%)≥1370(直径<1mm丝材,冷作硬化40%~60%)\未给出范围的温度,调整范围为土10℃。b0Cr17Ni7A1弹簧制件的固溶处理十调整处理+时效处理按HB/Z80进行。6.4淬火加回火钢弹簧制件
6.4.1材料状态和制件热处理作用弹簧制件制造前的材料为退火状态或轧制状态。材料预备热处理是为制造弹簧制件做组织和性能准备,弹簧制件最终热处理的日的是通过火或等温淬火后加回火,达到弹性要求。6.4.2重复热处理
6.4.2.1弹簧制件允许进行重复热处理,重复淬火前应进行600℃~680℃的低温退火。重复淬火次数应符合如下规定:
a)对于直径或厚度不大于1mm的弹簧制件,重复淬火次数不超过1次:b)对于直径或厚度大于1mm的弹簧制件,重复淬火次数不超过2次。6.4.2.2弹簧制件回火次数不限。6.4.3·热处理制度
弹簧制件制造前的材料预备热处理制度见表5。弹簧制件淬火和回火的热处理制度及推荐的硬度见表6。表5
预备热处理制度
材料牌号
T7A、T8A、T9A
50CrVA
60Si2MnA
65Si2MnWA
65Mn、70Mn
3Cr13、4Cr13
加热温度
850~870
850~870
850~870
800~820
冷却方式
完全退火或不完全退火
加热温度
760~780
850~870
850~870
850~870
800~820
870~900
冷却方式
低温退火
加热温度
690~710
680~700
680~700
680~700
680700
730~780
3Cr13、4Cr13钢的保温时间按HB/Z80的规定,其它牌号钢的保温时间按HB/Z136的规定。淬火和回火的热处理制度和推荐硬度值表6
材料牌号
T7A、T8A、T9A
50CrVA
60Si2MnA
加热温度
770~790
840870
800830
850~870
冷却介质
油或低温碱浴
油或低溢碱浴
加热温度
360~4003
370~4203
360~410
390~-440
410470此内容来自标准下载网
冷却介质
水或空气
水或空气
热水或油
水或油
冷却方式
推荐硬度值
47~51
HB/Z358-2005
材料牌号
65Si2MnWA
3Cr13、4Cr13
加热温度
840~860
1020~1050b
表6(续)
冷却介质
加热溢度
420470
450~550c
250~350
冷却介质
水或油
水或油
推荐硬度值
直径小于2.8mm的50CrVA钢丝弹簧制件和厚度小于0.5mm的T7A、T8A、T9A钢带弹簧制件,在保证硬度的条件下允许将回火温度降至350℃。b3Cr13、4Cr13可采用960℃~980℃进行痒火,此时问火温度可适当降低。。选择回火温度时,应注意避免回火脆性的不良影响。6.4.3.3钢丝弹簧制件推荐的淬火、回火加热保温时间见表7,钢板、钢带弹簧制件推荐的淬火、回火加热保温时间见表8。65Si2MnWA钢弹簧制件淬火保温时间可按表7、表8推荐的时间延长一倍。根据弹簧制件的具体要求,保温时间可适当调整。当弹簧制件装心轴热处理时,淬火和回火的保温时间根据心轴尺寸的大小应适当延长。采用真空炉进行淬火加热时,保温时间按HB/Z191的规定。表7钢丝弹簧制件淬火、回火加热保温时间热处理类型
热处理类型
炉子类型
盐浴炉
空气炉
空气炉
不同钢丝直径弹簧制件的保温时间min
>1mm~2mm
>2mm~4mm
10~12
>4mm~8mm
30~40
表8钢板、
钢带弹簧制件淬火、回火加热保温时间炉子类型
盐浴炉
空气炉
空气炉
保温时间
(3~5)min+(0.5~1)min/mm条件厚度(1015)min+1min/mm条件厚度
(10~20)min+(0.5~1)min/mm条件厚度(20~40)min+(1~2)min/mm条件厚度>8mm~10mm
6.4.3.4采用真空炉进行小弹簧制件的油淬时,由于制件的热容量较小,转移过程中温度降低较多容易产生淬火效果差的问题,可采取增大热容量的措施来解决。6.4.3.5弹簧制件火至回火之间的间隔时间一般不应超过2h。6.4.3.6为了提高弹簧制件的强韧性和使用寿命,减少热处理变形,可采用等温淬火或分级淬火代替油淬,但在高温应力松弛或变条件下工作的弹簧制件,不应进行等温淬火或分级淬火。常用钢弹簧制件的等温或分级淬火制度见表9。表9:
常用钢弹簧制件的等温或分级淬火制度制件的厚度
材料牌号
S或直径D
等温或分级淬火
加热温度
等温制度
340~360
320~360
320~370
加热温度
抗拉强度
Rm(op)
硬度值
45.5~49.5
45.5~49.5
材料牌号
60Si2MnA
65Si2MnWA
50CrVA
制件的厚度
S或直径D
表9(续)
等温或分级火
加热温度
等温制度b
300340
300~340
280~320
350~400
加热温度
300~340°
300~340°
280~320°
250~300
HB/Z358-2005
抗拉强度
Rm(op)
1420~1810
1520~1810
1520~1760
15201810
硬度值
45.5~50.5
45.5~50.5
45.5~51.5
温度调整范围为士10℃。3Cr13钢的淬火加热保温时间按HB/Z80的规定,其它牌号钢的淬火加热保温时间按HB/Z136的规定。
b等温保温后在40℃~100℃水中或空气中冷却。推荐在与等温淬火相同的温度下进行回火。6.5尺寸稳定化处理
根据弹簧设计要求,螺旋弹簧制件热处理后可进行尺寸稳定化处理。螺旋弹簧制件尺寸稳定化处理是预先通过加载或加温加载的方法使弹簧制件尺寸稳定,尺寸稳定化处理的具体方法参见附录A。7质量控制和检验
7.1质量控制
7.1.1弹簧制件热处理过程应实行全面质量控制,并进行检验,以确保热处理质量。7.1.2热处理原始记录应认真填写并妥善保存,按HB5354有关要求建立完整的热处理质量档案。7.1.3弹簧制件的硬度、抗拉强度应符合图样、本指导性技术文件或专用技术文件的规定。7.1.4弹簧制件的表面质量和尺寸应符合图样或专用技术文件的要求。7.1.5弹簧制件的弹力(载荷)应符合图样或专用技术条件的规定。7.1.6弹簧制件的脱碳和金相组织按HB5354或专用技术文件进行控制。7.1.7弹簧制件热处理常见的缺陷及防止措施参见附录B。7.2检验
7.2.1弹簧制件的脱碳层试验按GB/T224进行。7.2.2弹簧制件的硬度试验按GB/T230进行。7.2.3钢丝直径小至一定尺寸的弹簧制件允许用拉伸试验代替硬度试验。拉伸试验按GB/T228进行。7.2.4弹簧制件的表面质量和尺寸检验、金相组织检验及弹力试验按相应标准或专用技术文件进行。HB/Z358-2005
A.1立定处理
附录A
(资料性附录)
螺旋弹簧制件尺寸稳定化处理方法立定处理方法是将压缩弹簧压并圈或压至一定高度岩干次,或将拉伸弹簧拉伸至最大工作距离1.2倍的长度若干次,一般为10次。A.2强压处理(加荷时效)
强压处理是将弹簧压缩至并圈或压至--定高度保持12h~48h,具体时间由设计人员确定或根据生产经验决定。
A.3加温加荷时效
A.3.1弹簧的加温加荷时效处理一般要经过两次。第一次是在热处理后进行,将弹簧压缩(或拉伸)至最大.T作载荷下的高度,温度按表A.1的规定,保持时间为:65Si2MnWA弹簧不少于7h;50CrVA和ⅡI,、E、F、G组的弹簧不少于2h。第::次是在表面处理后进行,将弹簧压缩(或拉伸)至最大工作载荷下的高度,温度按表A.1的规定,保持时间为:65Si2MnWA弹簧不少于5h;50CrVA和II、E、F、G组的弹簧不少于2h。
A.3.2弹簧经加温加荷时效处理后,为了保持弹簧尺寸稳定,可将弹簧用夹具保持一定长度入库保存。
弹簧的工作温度
>60~100
>100~150
>150~180
表A.1加温加荷时效处理的温度
第一次加温加荷时效处理的温度℃
120±10
200±10
250±10
>180~230
注:允许采用高于工作温度20℃土10℃作为第一次加温加荷时效处理。A.4预疲劳处理(循环稳定处理)第二次加温加荷时效处理的温度℃
100±10
150±10
180±10
230±10
预疲劳处理是将弹簧在工作高(长)度先进行一定次数的加载循环,一般为100~2000次。附录B
(资料性附录)
弹簧制件热处理常见的缺陷及防止措施弹簧制件热处理常见的缺陷及防止措施见表B.1。表B.1
弹簧制件热处理常见的缺陷及防止措施缺陷类型
表面脱碳或元素贫化
硬度不足
变形过大
表面腐蚀
淬火后开裂
脆性大
弹力低
弹力高
产生原因
1、淬火加热盐浴炉脱氧不充分
2、保护气氛未调整好
3、真空炉真空度过高过低,或漏气率太高。1、火转移速度过慢
2、淬火加热表面脱碳
3、淬火温度过高,残余奥氏体过多1、应力过大
2、心轴或夹具设计不合理
3、装炉方式不合理
4、加温加荷时效处理时压缩过分1、盐浴内腐蚀性杂质过高
2、没有及时清理残盐
3、零件表面不洁净
1、原材料有缺陷
2、加热速度过快,没有预热或预热不当3、淬火剂选择不当
4、火加热温度过高,保温时间过长1、在脆性区回火
2、硬度过高
3、过热
1、设计不合理
2、硬度不足
3、表面脱碳或元紫贫化
4、热处理后,材料尺寸变小或弹簧外径变大设计不合理
2、硬度高
3、热处理后,弹簧螺距不均匀或弹簧外径变小
充分脱氧
把气氛调整好
HB/Z358-2005
防止措施
选择适当的真空热处理参数
加快淬火转移速度
盐浴炉充分脱氧,或使用气氛炉、真空炉进行冷处理
充分消除应方
设计合适的心轴或夹具
合理摆放
选用合适的加温加荷时效处理温度和压缩量及时充分脱氧
及时清理残盐
热处理前后加强清洗
加强原材料检验
进行合适的预热
选用合适的淬火剂
选用合适的淬火溢度和保温时间回火时快冷或避免在脆性区回火选用合适的回火温度
选用合适的淬火温度
设计重新计算
按硬度不足原因采取措施
按表面脱碳或元素贫化采取措施热处理时采用合适丁装和减少材料尺寸变小的措施
设计重新计算
提高回火温度
热处理时采用合适工装和减少嫌距不均匀的措施
小提示:此标准内容仅展示完整标准里的部分截取内容,若需要完整标准请到上方自行免费下载完整标准文档。

标准图片预览:
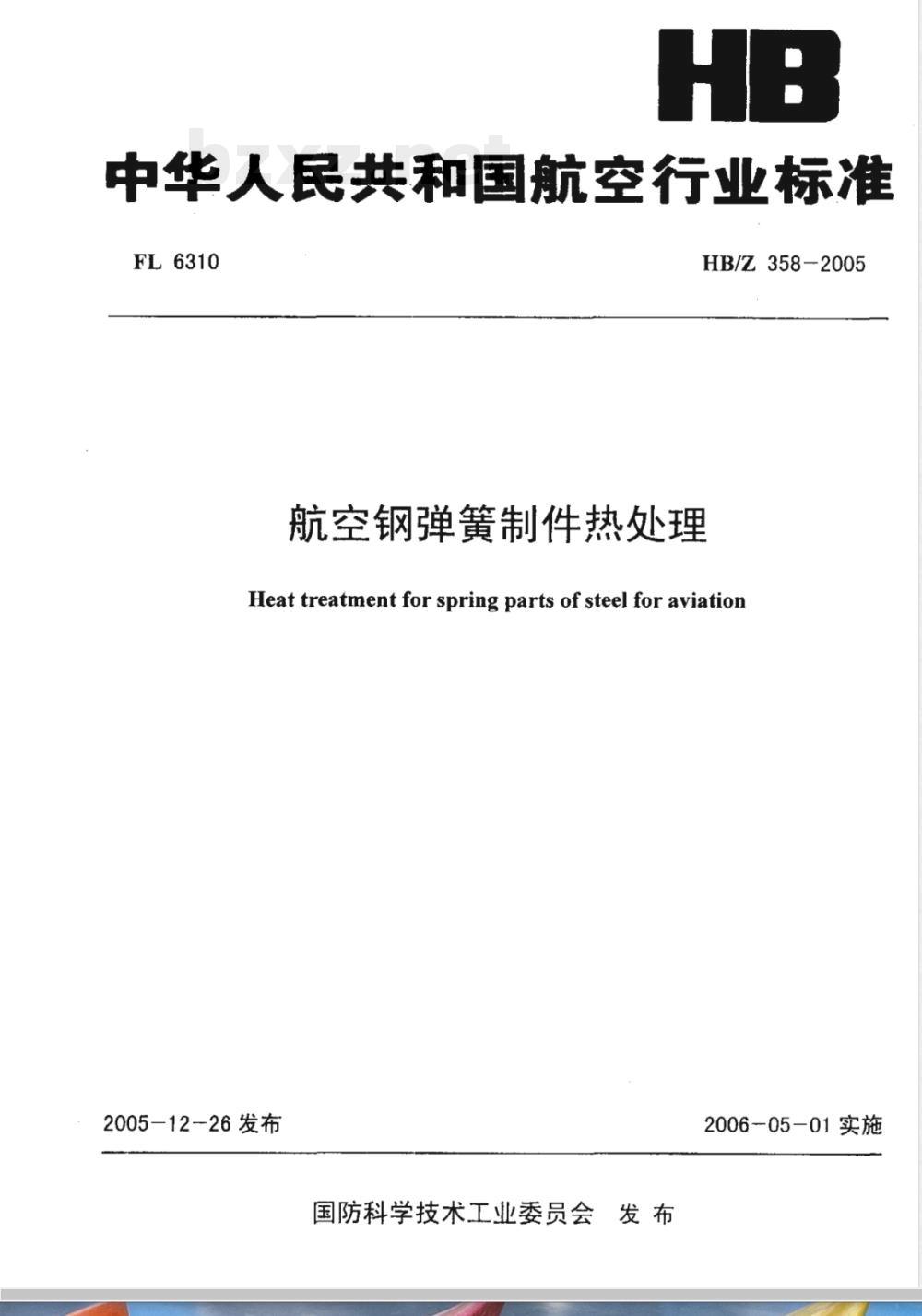
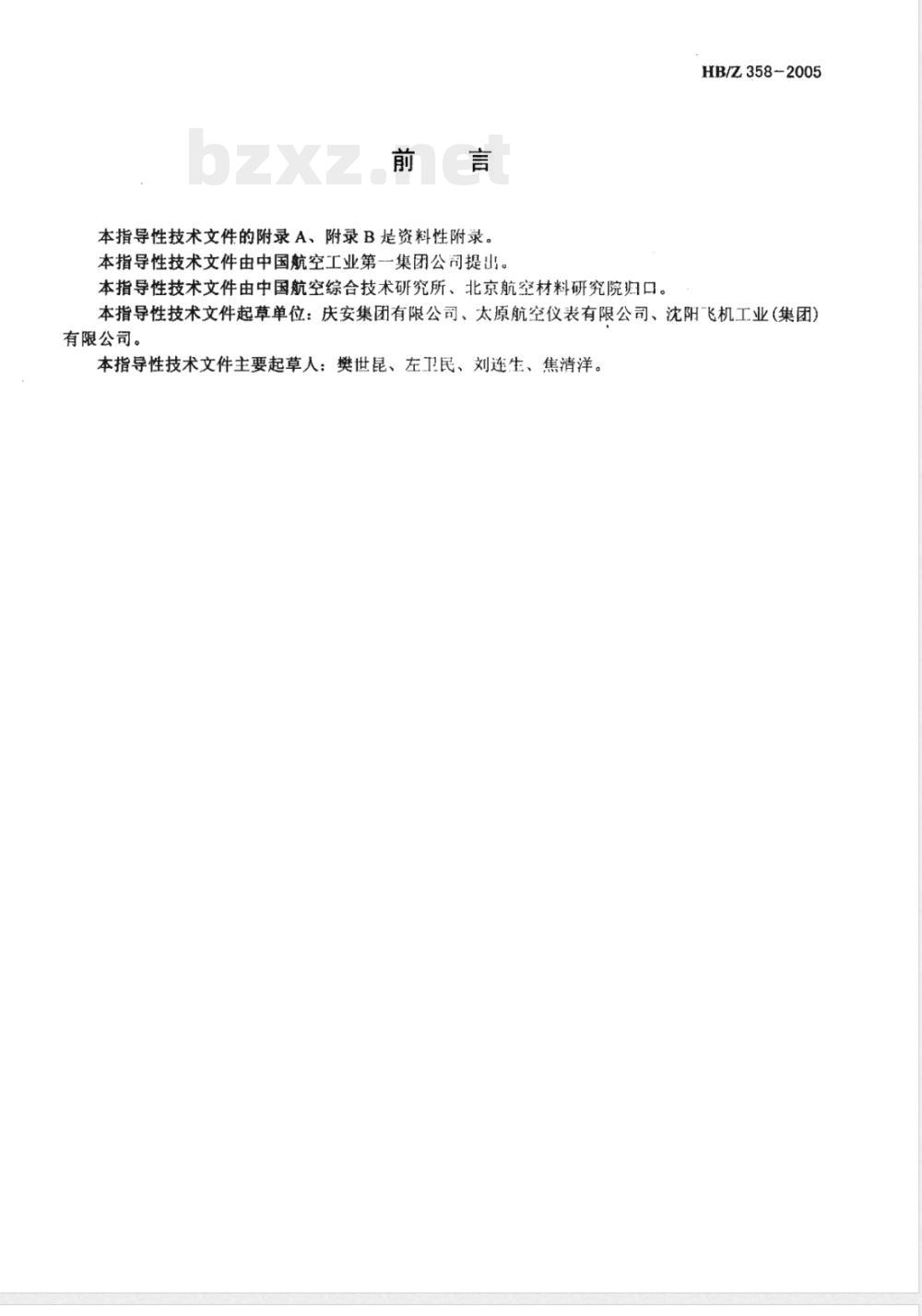
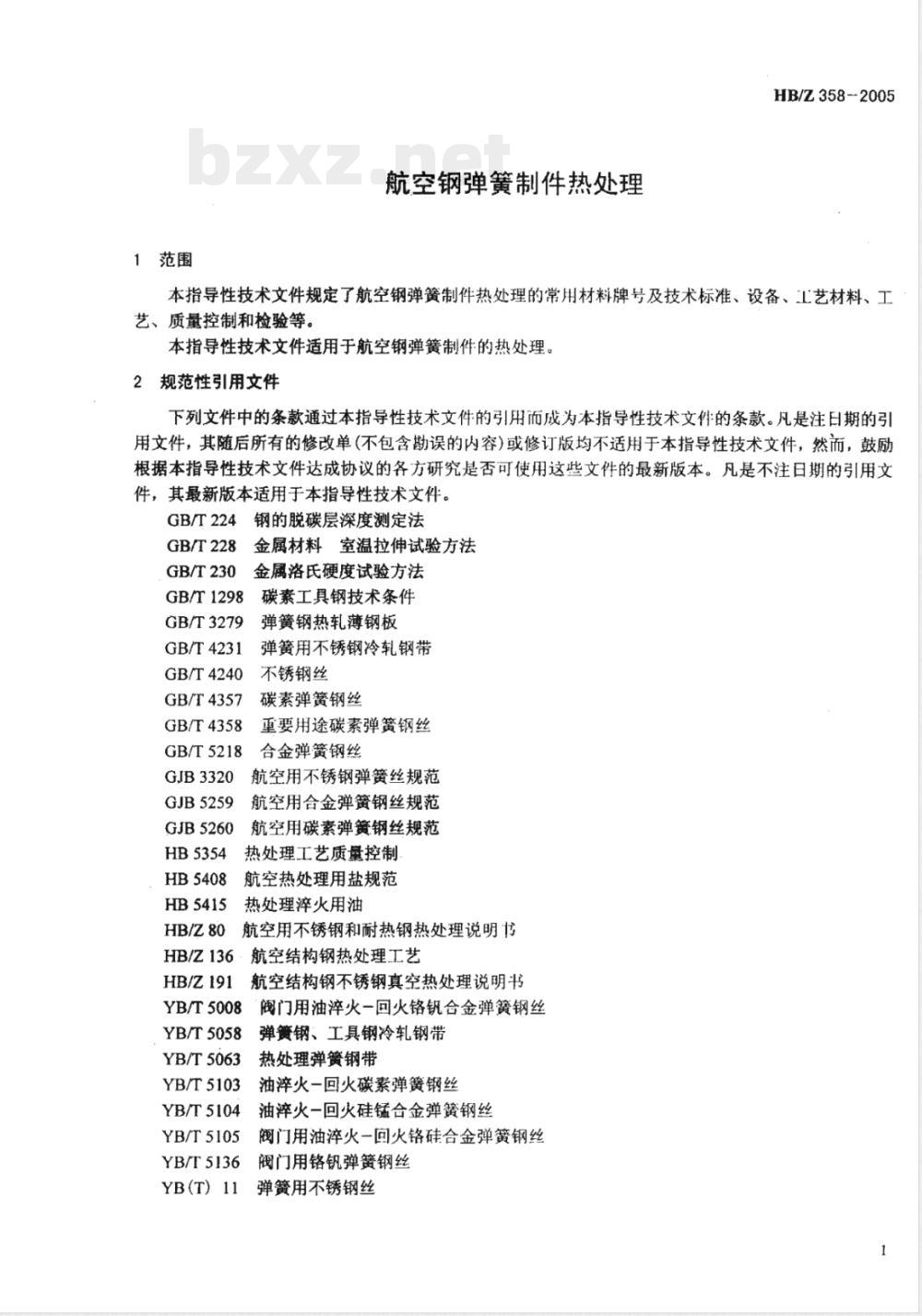
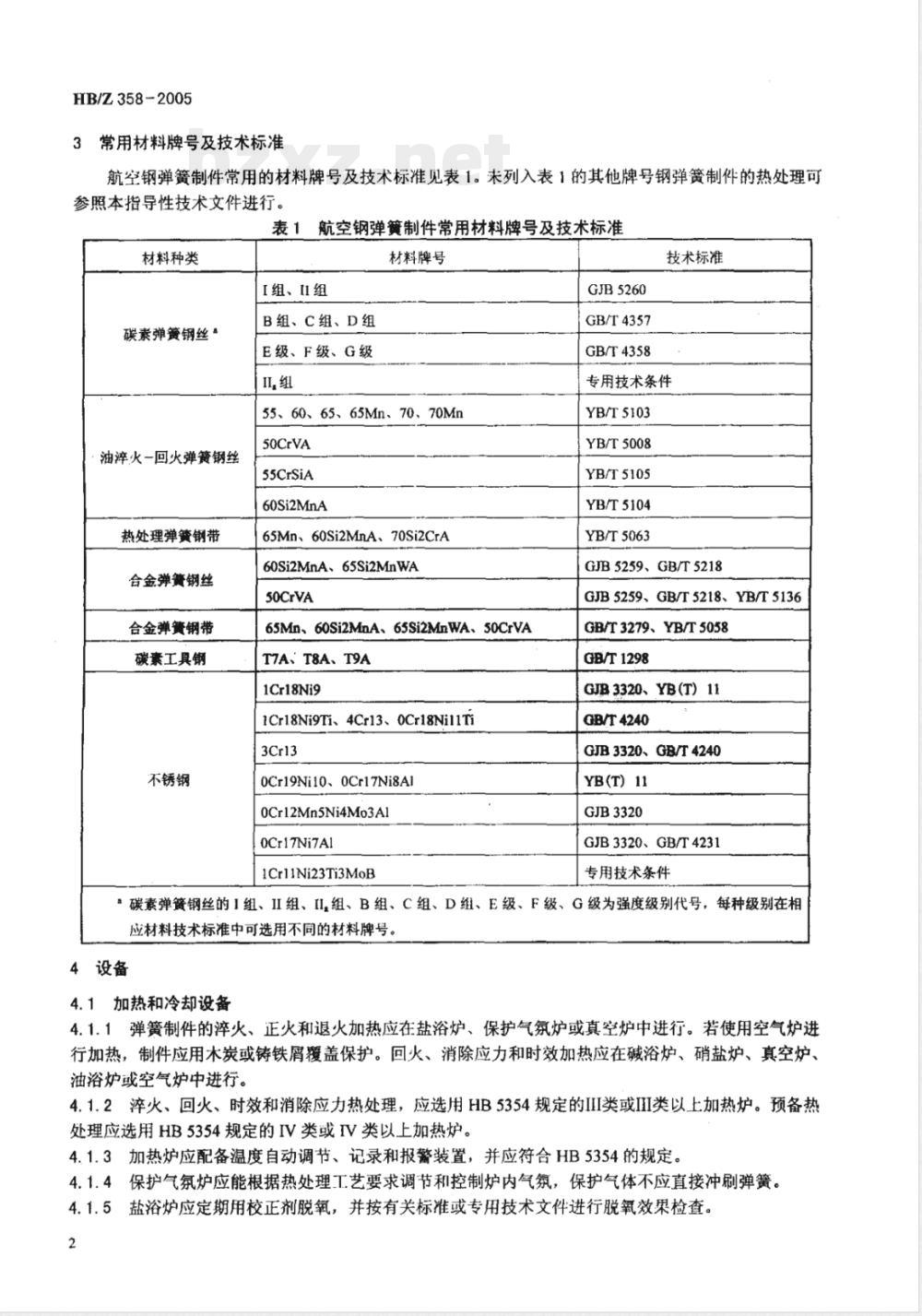
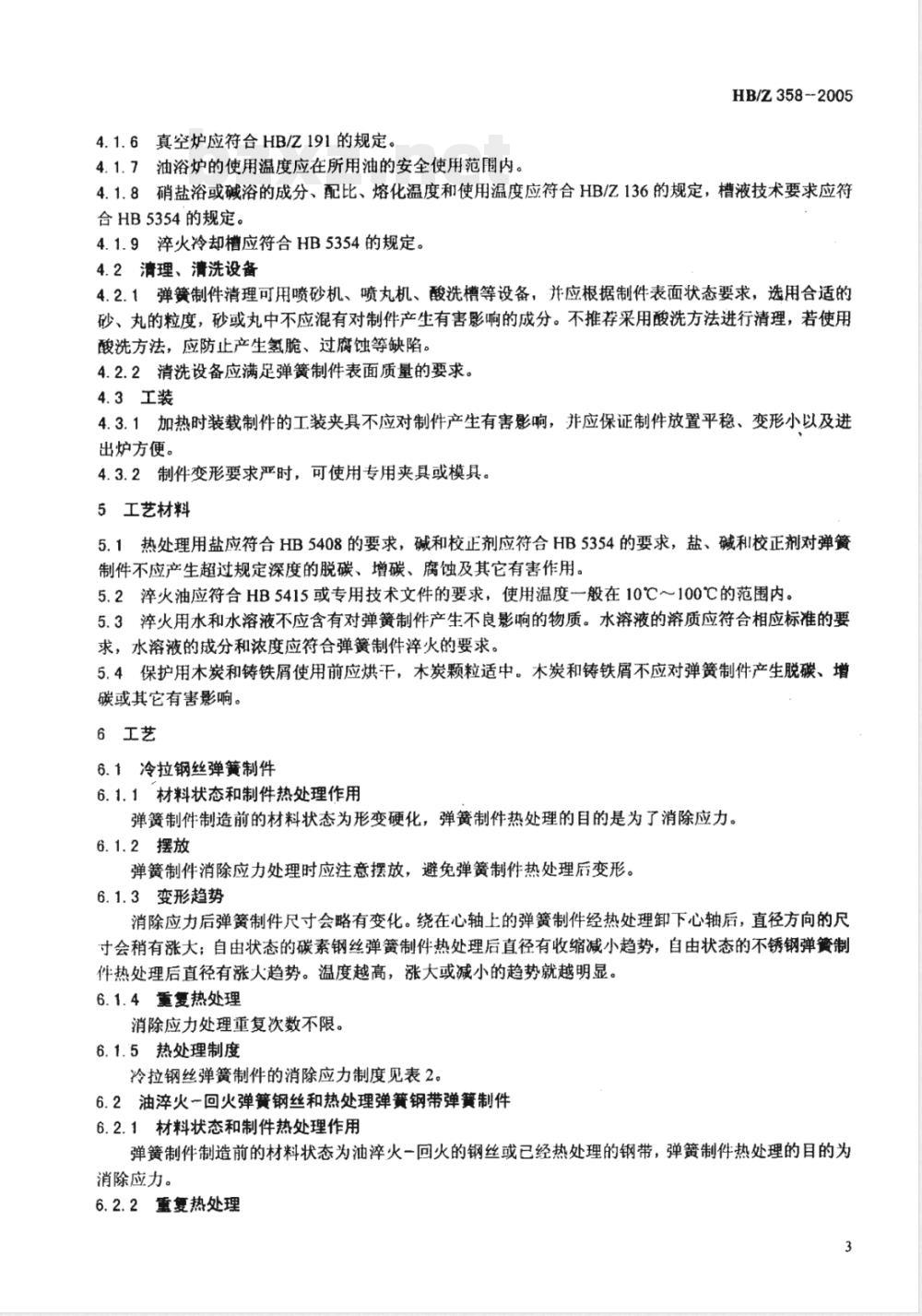
- 其它标准
- 热门标准
- 航空工业行业标准(HB)
- HB4530.13-1991 H型孔系组合夹具压板类件 偏心轮夹紧组件
- HB1426-1987 侧向压紧器
- HB3733-1986 手提压铆机用窝头(用于GB 867-76)
- HB4529.34-1991 H型孔系组合夹具定位件 固定顶尖
- HB2-25-1983 挤压型材合页片
- HB7852-2008 28MPa无扩口过隔板带密封垫圈45°弯管接头
- HB4535.14-1991 K型孔系组合夹具件 圆柱定位支承
- HB7344.38-1996 数控机床用夹具件 大型齿面侧向压紧器
- HB3716-1986 手用窝头(用于HB 1-609,610-83)
- HB2393-1977 HB 242-70螺纹通端环规d=105~150mm
- HBM65.7-1988 微型汽车 机械式变速器台架试验方法
- HB4532.9-1991 H型孔系组合夹具紧固件 活节螺栓
- HB6934-1994 数控铣床用六齿莫氏锥柄球头立铣刀 d=32~63mm
- HB7144.11-1995 大型系列组合夹具支承件 左角铁
- HB4007-1987 气瓶专用锥螺纹中径螺纹环规
- 行业新闻
请牢记:“bzxz.net”即是“标准下载”四个汉字汉语拼音首字母与国际顶级域名“.net”的组合。 ©2009 标准下载网 www.bzxz.net 本站邮件:bzxznet@163.com
网站备案号:湘ICP备2023016450号-1
网站备案号:湘ICP备2023016450号-1