- 您的位置:
- 标准下载网 >>
- 标准分类 >>
- 机械行业标准(JB) >>
- JB/T 8555-2008 热处理技术要求在零件图样上的表示方法

【机械行业标准(JB)】 热处理技术要求在零件图样上的表示方法
本网站 发布时间:
2024-06-30 14:21:25
- JB/T8555-2008
- 现行
标准号:
JB/T 8555-2008
标准名称:
热处理技术要求在零件图样上的表示方法
标准类别:
机械行业标准(JB)
标准状态:
现行-
发布日期:
2008-06-04 -
实施日期:
2008-11-01 出版语种:
简体中文下载格式:
.rar.pdf下载大小:
926.82 KB
替代情况:
替代JB/T 8555-1997

点击下载
标准简介:
标准下载解压密码:www.bzxz.net
本标准规定了钢制零件热处理技术要求在零件图样上的表示方法。本标准适用于各种钢制的机械零件。 JB/T 8555-2008 热处理技术要求在零件图样上的表示方法 JB/T8555-2008

部分标准内容:
ICS25.200
备案号:24496—2008
中华人民共和国机械行业标准
JB/T85552008
代警JB/T85551997
热处理技术要求在零件图样上的表示方法Method of prescribing heat treatment requirements in drawings2008-06-04发布
2008-11-01实施
中华人民共和国国家发展和改革委员会发布前言
2规范性引用文件,
正火、退火及率火回火(含调质)零件4
5表而萍火、回火零件
5.1-般技术要求
5.2表面硬度
5.3心部硬度
5.4有效硬化层深度
5.5标注示例
6渗碳和碳氮共渗零件,
一般技术要求
6.2表面硬度
6.3心部硬度
渗层的有效硬化层深度,
6.5标注示例,
7渗氮零件.
7.1、一般技术要求
7.2表面硬度
7.3心部硬度…
7.4有效渗氮层深度
7.5总渗氟层深度
7.6标注示例
8其他热处理零件
图1硬度测量点符号标注方法
复杂零件热处理技术要求的标注方法目
局部热处理零件技术要求的标注方法局部感应加热率火回火标注方法局部渗碳标注方法.
诊氮零件的标注方法
各种表面热处理零件有效硬化层深度和测定方法JB/T8555—2008
表2以维氏硬度表示时最低表面硬度值、最小有效硬化层深度与试验力之间的关系,表3以表面氏硬度表示时最低表面硬度、最小有效硬化层深度与试验力之间的关系表4以洛氏硬度A标尺或C标尺表示时最低表面硬度、最小有效硬化层深度与试验力之间的关系.5表5表面淬火界限硬度值
表6表面淬火有效硬化层深度分级和相应的上偏差..表7推荐的渗碳后淬火回火或碳氮共渗淬火回火等件有效硬化层深度及上偏差,表8推荐的最小有效渗氮层深度及上偏差.表9技术要求的最小有效渗氮层深度、最低表面硬度与硬度试验力之间的关系表10推荐的化合物层厚度及公差,6
JB/T85552008
本标准代替JB/T8555一1997《热处理技术要求在零件图样上的表示方法》。本标准与JB/T8555—1997相比,主要变化如下:规范并标出了封面的各种信息;调整并填充了“前言”中的相关要素;一将原标准的“2引用标推”改为“2规范性引而文件”,同时又推了原有的引用文件,并对采标项目给予了标识:
完善了相关章中“条”的标题,见5.1、6.1、7.1;删除了已作废的引用文件,规池了相关条口的写法,见5.2、7.2:将原标准的5.5、6.5、7.6的“标注示例”进行了规范了,见第5、6、7章“示例\期除8.1:
本标准由中国机械工业联合会提出。本标准出全国热处理标准化技术委员会(SACTC75)归门本标主要起草单位:爱协林热处埋系统(北京)有限公司、江苏人学本标雅主要起草人:火树鹏、般汉奇。本标准所代替标准的历次版本发布情况:-JB/T 8555--1997
1范围
热处理技术要求在零件图样上的表示方法本标准规定了钢制零件热处理技术要求在零件图样的表示方法。本标准适用于各种钢制的机械零件2规范性引用文件
JB/T 8555--2008
下列文件中的条款通过本标准的引用而成为尽标准的条款,凡是润期的引用文件,其随后所有的修改单(不包括勘误的内容)或修订版均不适用于本标准,然前,鼓励根据本标准达成协议的各方研究是否可使用这些文件的最新版本。凡是不注日期的引用文件,其最新版本适用于本标难,GB/T131机械制图表面粗糙度符号、代号及其注法(GB/T131--2006.ISO1302:2002,DT)GB/T230.1金属洛氏硬度试验第I部分:试验方法(A、B、C、D、E、F、G、H、K、N、T标尺) [ISO 6508-1:1999 (Metallic materiais-Rockwel hardness test-Part l: Test method : scales A,B, C.D、E、F、G、H、K、N、T),MOD:GB231.1金属布沃硬度试验第1部分:试验方法[GB/T231.1--2002,e9ISO6506:1999(E)GB/T4340.1金属维长硬度试验第1部分:试验方法(GB/T4340.1-1999,eqVISO6507:1997)GB/T5617钢的感皮率火或火焰率火后有效硬化层深度测定(GB/T5617—2005,ISO37.54:1976NEQ)
GB/T94.50钢件渗碳火硬化层深度的测定和校核(GB/T9450-2005,ISO2039:2002,MOD)GB/T9451钢件薄表面总硬化层深度或有效硬化深度的测定!GB/T9451--2005,[SO4970:1979(H), MOD)
GB/T11354钢铁零件渗氮层深度测定和金剂纠织检验JB/T6050~~2006钢铁热处理零件硬度测试通则JR/T6956离子渗氮
3总则
3.1零件图样1的热处理技术要求(以下简称技术要求)是制成品零件热处理最终状态(以下简称最终状态)应达到的技术指标:
3.2热处理技术要求可以用已标准化的符号、代号标注,也可以文字说明,文字说明--般写在图面右下角标题栏上方,与其他工艺的技术要求写在起。特殊情况允许写在图而其他部位的守白处。能在图形上标注的,尽量避免用文说明。3.3技术要求标注必须简明、谁确、完整,合理。如策技术内穿要求较多,日.另有技术标难或技术规范时,除标注主要内容外,可写明按某标雅战某技术规范执行。3.4技术要求的指标值,-般采用范用表示法标出上,下限,如60HRC~65HRC;TDC=0.8-1.2。也可用偏差表示法以技术要求的下限名义值下偏差零加1:上偏差表示,如60HRC:DC-0,84。特殊情况也可只标注下限值或上限值,如不小于50HRC:不大于299HBW,在同…产品的所有零件图样上,应来用统-·的表达形武。3.5各种表面热处理零件均应注有效硬化深度,其代号、定义和测定方法见表1:JB/T85552008
表面热处理方法
表面淬火回火
表1各种表面热处理零件有效硬化层深度和测定方法有效硬化层深度代号
渗碳或碳氮共渗萍火回火
注:标注时单位(mm)可省略:DC
定义和测量方法标雅
深度>U.3mm时按GB/T5617
深度≥.0.3mum时按GB/T9451
深度>0.3mm时按GB/T9450
深度≥0.3mm时按GB/T9451
按GB/T11354
3.6局部热处理零件需将有硬化要求的部位按GB/T131的规定,在图形上用粗点画线框出。如果是轴对称零件或在不致引起误会情况下,也可用一条粗点面线画在热处理部位外侧表示,其他部位即硬化与不硬化均可的过渡部位用虚线表示,不允许硬化或不要硬化的部位则不必标注。3.7要求零件硬度检测必须在指定点(部位)时,用图1符号表示,其尺寸大小应与GB/T131规定的局部热处理指示符号一致指定硬度测量点位置时,应符合JB/F6050一2006中第6章的规定。图1硬度测量点符号标注方法
3.8如零件形状复杂或儿他原四(如与其他工艺标注容易混淆)热处理技术要求难以标注,用文字说明又不易表达时,可另加附图表示,此时附图上与热处理无关的内容均可省略,见图2。a)零件热处理标注图
表面硬度测量点
DS 测至点
b)Y部热处理技术要求的标注递30*
DS测量点
表面硬度测盘点
c2部热处理技术要求的窃注图
复杂零件热处理技术要求的标注方法图2
JB/T85552008
3.9标注除硬度以外的其他力学性能要求时(如强度、冲击韧度等),应在零件图样上注明具体技术指标和取样方法。
3.10零件热处理的外观质量或者无法用量值表达的要求,可用文字说明。4正火、退火及淬火回火(含调质)零件4.1以正火、退火或淬火回火(含调质)作为最终热处理状态的零件一般标注硬度要求:通常以布氏硬度(GB/T231.1)或洛氏硬度(GB/T230.1)表示。也可以用其他硬度表示。4.2同一零件的不同部位有不同热处理技术要求时,应在零件图样上分别注明。4.3局部热处理零件必须在技术要求的文字说明中写明局部热处理。并在图样上按3.4和3.6的规定标出需热处理的部位和技术要求,见图3。不大于30HRC
a)范围表示法
b)偏差表示法
56HRC-62HRC
35'HRC下载标准就来标准下载网
图3局部热处理零件技术要求的标注方法5表面淬火、回火零件
5.1一般技术要求
感应加热萍火回火和火焰加热痒火回火零件标注的主要技术要求是表面硬度、心部硬度和有效硬化层深度。
5.2表面硬度
表面硬度的标注包括两部分,即要求硬度值和相应的试验力,而试验力的选取又与要求的最小有效硬化层深度有关。表面硬度的测量应符合GB/T230.1、GB/T4340.1的规定。以维氏硬度表示时,最低表面硬度、最小有效硬化层深度与硬度试验力之间的关系见表2。表内试验力为最大允许值,也可以用较低的试验力代替表中所列值,如用HV10代替HV30。3
JB/T85552008
表2以维氏硬度表示时最低表面硬度值、最小有效硬化层深度与试验力之间的关系最小有效诬化层深度
400-~500
最低表面硬度HV
>500--600
>600--700
以洛氏硬度表示时,最低表面硬度、最小有效硬化层深度与试验力之间的关系见表3和表4。5.3心部硬度
对表面辫火零件的心部硬度有要求时,应予标注。经有关各方协商同意,允许以预备热处理后的硬度值为溅。
最小有效硬
化层深度
以表面洛氏硬度表示时最低表面硬度、最小有效硬化层深度与试验力之间的关系最低表面硬度(以HR\N表示)
82--85
>85~88
60~6868--73]73-~78
1:NR30N
>54--61
HR45NHR45N
JB/T8555--2008
表 4以洛氏硬度 标尺或 C标尺表示时最低表面硬度、最小有效硬化层深度与试验力之间的关系最小有效硬
化层深度
70~-75
5.4有效硬化层深度
75--78
278--81
最低表面硬度
40~-49
55~-60
表面率火零件有效硬化层深度的标注包括三个部分,即硬化展深度代号(见表1)、界限硬度值和要求的深度。在图样上的标注方法见5.5界限硬度值可振据最低表面硬度按表5选取。特殊情况,也可采用其他界限硬度值,但此时在DS后必须注明商定的界限硬度值。
零件的有效硬化尽深度分级及1:偏差可参照表6。火焰率火的有效硬化层深度通常不应小于1.6nm.
表5表面淬火界限硬度值
界限硬度值
69·70
75--76
80-- 81
最低表面硬度
54~-55
56--58
59 -- 62
69·70
72 --73
36~-38
39~ 41
50--52
55 --57
60~~61
62 -- 63
66-·67
71--72
300-330
335~355
360--385
390~:420
425 --.455
460)--480
485--515
520-545
550-575
580--605
610635
670705
710--730
735765
770 ·795
800$35
840 -865
40--42
46 --47
48 -- 49
50--51
52--53
55--56
JB/T85552008
表6表面淬火有效硬化层深度分级和相应的上偏差最小有效硬化层深度DS
5.5标注示例
感应济火
上偏差
单位:mm
火焰淬火
示例:图4所示为局部感应加热萍火同火标注方法,该例表示:离轴端15mm土5mm处F始,在长30*mm一段内感应热率火回火,表面硬度620HV30780HV30,有效硬化层深度0.8mm-1.6mrm。hXHV70-780HV30
[35300=0.8~1.6
al范围表示法
125=0.8+*.620-gHV30
h)编差表示法
图4局部感应加热淬火回火标注方法6渗碳和碳氮共渗零件
6.1—一般技术要求
渗碳后淬火回火和碳氮渗眉淬火可火零件标注的主要技术要求是表面硬度,心部硬度利有效硬化层深度。共他技术要求(如渗尽金相组织、诊么碳液虑或硬度分布、心部力学性能等;按3.3的规定执行
6.2表面硬度
渗碳后率火回火和碳氮共渗压萍火问火零件的表面硬度要求,通常以维氏硬度或洛氏硬度表示,对应的段小有效硬化层深度和试验力与表面淬火零件相同6.3心部硬度
对渗碳后率火回火或碳氮共渗后浒火回火零件的心部硬度有要求时,应予标注:6.4渗层的有效硬化层深度
JB/T 8555—2008
渗碳后率火[叫火或碳氮共渗后淬火回火零件的有效砾化层深度(DC)在图样1的表示方法,与表恒率火有效硬化层深度DS基本相同,在图样上的标注方法见6.5渗俄后济火回火或碳氮共渗后淬火间火的界限硬度值是低定的,通常取550HV1,标注时一般可省略,特殊情况下可以不采用550HV1作界限硬度值,此时DC后必须注明商定的界限硬度值和试验力。推荐的渗碳后济火回火或碳氮共渗后淬火回火零件有效硬化层深度(DC)及上偏差见表7表7推荐的渗碳后淬火回火或碳氮共渗淬火回火零件有效硬化层深度及上偏差单位:mm
有效硬化层深度
6.5标注示例
上偏差
示:图5所示为而部渗碳标注方法,对零件不同部份有不同的要求,要求渗饿后火同火部位用粗点画战润出;有的部位色许同时渗碳济硬也可以不渗碳济硬,视工艺上是否有利而定,用虚绒表示:末标出部位:啡不犯许渗氮也不允许率便。
局部渗碳泽火回火
57HRC-63HRC
DC -1.2 -- 1.7
图5局部渗碳标注方法
7渗氮零件
7.1 一般技术要求
气体渗氮或离了渗氮零件的主要技术要求是表面硬度、心部硬度和有效渗氮层深度果些零件还有渗氮层脆性要求,其他技术要求(如渗氮层金、渗氮层硬度分布,心部力学性能等)按33的就行7.2表面硬度
零件诊氮旨的表面硬度与零件材质和预备热处理有密切关系、在正营工艺条件下,营月渗氮材料能达到的硬度范封可参照JB/T6956。JB/T8555—2008
表面链度因有效氮层深度不回而有差异,标注足应准确选择。表面硬度值的测量应衍合GB/4340.1的有关规定。
有效渗氮层深度不大于0.3mm时按GB/T9451执行,人F0.3mm时按GB/T11354执行,经协商同意,也可以采用拉他硬度检测方法表示:7.3心部硬按
对渗氨零件心部硬度有要求时,应特别注意,心部砸度通常允许以预备热处理后的检测结果为准:以维長硬度、布氏硬度或洛氏硬度表示。7.4有效渗氮层深度
图样上标注渗氮层深度,除非另有说明,般均措有效渗氮层深度(见3.5)。其表示方式与DS、DC基本相同,在图样上的标方式见7.6..来用2.94N(0.3玉gf)的维氏硬度试验力测量行效渗氮层深度DN时,DN后不标注界限硬度值:采用其他试验力时,成在DN后加试验力值,如DNHV0.5一0.3·0.4.一般零件推荐的最小有效渗氮层深度(DN)及1偏兰见表8:表8推荐的最小有效渗氮层深度及上偏差辛位:rmm
有效渗氮层深度DY
上诵差
有效渗氮层深度DN
上偏差
技术要求的最小有效渗氮爆深度、最低面续追与碘度试验力之间的关系见衣9:表内检验方法国场是指允许采用最大试验力,允许用较低的试验力代替表中规定的试验力,如IV10代替HV30,表9技术要求的最小有效渗氮层深度、最低表面硬度与硬度试验力之间的关系最小有效
渗氮展深度
2()~300
300---40
2 400...50m
最低志面碑
2- ---70
700 --800
7.5总渗氨层深度
JB/T8555—2008
总渗氮层深度是氮渗人的总深度,一般指从表面测基到与基体的硬度或组织无差别处的垂直距离(单位mm)。
总渗氮层深度包括化合物层和散层两部分。零件以化合物层深度代替DN要求时,应特别说明,厚度要求随零件服役条件不同而改变,一般零件推荐的化合物层厚度及公差值见表10。7.6标注示例
示例:图6所示为诊氮零件的标注方法,渗氮部位边缘以粗点面线子以标注,并规定了硬度测定点位置。虚线部位允许渗氮或不充许渗氮是对工艺是否有利而决定。未标法部位不允许渗氮,如器防,必须说期。表10推荐的化合物层厚度及公差单位:mm
化合物层厚度
8、其他热处理零件
局部渗氮硬度不小于800HV30
DN=0.4~0.6,脆性不大了3级
图6渗氮零件的标注方法
上俯差
其他热处理零件的热处理技术要求在零件图样上的表示方法可参照第3章的规定执行
小提示:此标准内容仅展示完整标准里的部分截取内容,若需要完整标准请到上方自行免费下载完整标准文档。
备案号:24496—2008
中华人民共和国机械行业标准
JB/T85552008
代警JB/T85551997
热处理技术要求在零件图样上的表示方法Method of prescribing heat treatment requirements in drawings2008-06-04发布
2008-11-01实施
中华人民共和国国家发展和改革委员会发布前言
2规范性引用文件,
正火、退火及率火回火(含调质)零件4
5表而萍火、回火零件
5.1-般技术要求
5.2表面硬度
5.3心部硬度
5.4有效硬化层深度
5.5标注示例
6渗碳和碳氮共渗零件,
一般技术要求
6.2表面硬度
6.3心部硬度
渗层的有效硬化层深度,
6.5标注示例,
7渗氮零件.
7.1、一般技术要求
7.2表面硬度
7.3心部硬度…
7.4有效渗氮层深度
7.5总渗氟层深度
7.6标注示例
8其他热处理零件
图1硬度测量点符号标注方法
复杂零件热处理技术要求的标注方法目
局部热处理零件技术要求的标注方法局部感应加热率火回火标注方法局部渗碳标注方法.
诊氮零件的标注方法
各种表面热处理零件有效硬化层深度和测定方法JB/T8555—2008
表2以维氏硬度表示时最低表面硬度值、最小有效硬化层深度与试验力之间的关系,表3以表面氏硬度表示时最低表面硬度、最小有效硬化层深度与试验力之间的关系表4以洛氏硬度A标尺或C标尺表示时最低表面硬度、最小有效硬化层深度与试验力之间的关系.5表5表面淬火界限硬度值
表6表面淬火有效硬化层深度分级和相应的上偏差..表7推荐的渗碳后淬火回火或碳氮共渗淬火回火等件有效硬化层深度及上偏差,表8推荐的最小有效渗氮层深度及上偏差.表9技术要求的最小有效渗氮层深度、最低表面硬度与硬度试验力之间的关系表10推荐的化合物层厚度及公差,6
JB/T85552008
本标准代替JB/T8555一1997《热处理技术要求在零件图样上的表示方法》。本标准与JB/T8555—1997相比,主要变化如下:规范并标出了封面的各种信息;调整并填充了“前言”中的相关要素;一将原标准的“2引用标推”改为“2规范性引而文件”,同时又推了原有的引用文件,并对采标项目给予了标识:
完善了相关章中“条”的标题,见5.1、6.1、7.1;删除了已作废的引用文件,规池了相关条口的写法,见5.2、7.2:将原标准的5.5、6.5、7.6的“标注示例”进行了规范了,见第5、6、7章“示例\期除8.1:
本标准由中国机械工业联合会提出。本标准出全国热处理标准化技术委员会(SACTC75)归门本标主要起草单位:爱协林热处埋系统(北京)有限公司、江苏人学本标雅主要起草人:火树鹏、般汉奇。本标准所代替标准的历次版本发布情况:-JB/T 8555--1997
1范围
热处理技术要求在零件图样上的表示方法本标准规定了钢制零件热处理技术要求在零件图样的表示方法。本标准适用于各种钢制的机械零件2规范性引用文件
JB/T 8555--2008
下列文件中的条款通过本标准的引用而成为尽标准的条款,凡是润期的引用文件,其随后所有的修改单(不包括勘误的内容)或修订版均不适用于本标准,然前,鼓励根据本标准达成协议的各方研究是否可使用这些文件的最新版本。凡是不注日期的引用文件,其最新版本适用于本标难,GB/T131机械制图表面粗糙度符号、代号及其注法(GB/T131--2006.ISO1302:2002,DT)GB/T230.1金属洛氏硬度试验第I部分:试验方法(A、B、C、D、E、F、G、H、K、N、T标尺) [ISO 6508-1:1999 (Metallic materiais-Rockwel hardness test-Part l: Test method : scales A,B, C.D、E、F、G、H、K、N、T),MOD:GB231.1金属布沃硬度试验第1部分:试验方法[GB/T231.1--2002,e9ISO6506:1999(E)GB/T4340.1金属维长硬度试验第1部分:试验方法(GB/T4340.1-1999,eqVISO6507:1997)GB/T5617钢的感皮率火或火焰率火后有效硬化层深度测定(GB/T5617—2005,ISO37.54:1976NEQ)
GB/T94.50钢件渗碳火硬化层深度的测定和校核(GB/T9450-2005,ISO2039:2002,MOD)GB/T9451钢件薄表面总硬化层深度或有效硬化深度的测定!GB/T9451--2005,[SO4970:1979(H), MOD)
GB/T11354钢铁零件渗氮层深度测定和金剂纠织检验JB/T6050~~2006钢铁热处理零件硬度测试通则JR/T6956离子渗氮
3总则
3.1零件图样1的热处理技术要求(以下简称技术要求)是制成品零件热处理最终状态(以下简称最终状态)应达到的技术指标:
3.2热处理技术要求可以用已标准化的符号、代号标注,也可以文字说明,文字说明--般写在图面右下角标题栏上方,与其他工艺的技术要求写在起。特殊情况允许写在图而其他部位的守白处。能在图形上标注的,尽量避免用文说明。3.3技术要求标注必须简明、谁确、完整,合理。如策技术内穿要求较多,日.另有技术标难或技术规范时,除标注主要内容外,可写明按某标雅战某技术规范执行。3.4技术要求的指标值,-般采用范用表示法标出上,下限,如60HRC~65HRC;TDC=0.8-1.2。也可用偏差表示法以技术要求的下限名义值下偏差零加1:上偏差表示,如60HRC:DC-0,84。特殊情况也可只标注下限值或上限值,如不小于50HRC:不大于299HBW,在同…产品的所有零件图样上,应来用统-·的表达形武。3.5各种表面热处理零件均应注有效硬化深度,其代号、定义和测定方法见表1:JB/T85552008
表面热处理方法
表面淬火回火
表1各种表面热处理零件有效硬化层深度和测定方法有效硬化层深度代号
渗碳或碳氮共渗萍火回火
注:标注时单位(mm)可省略:DC
定义和测量方法标雅
深度>U.3mm时按GB/T5617
深度≥.0.3mum时按GB/T9451
深度>0.3mm时按GB/T9450
深度≥0.3mm时按GB/T9451
按GB/T11354
3.6局部热处理零件需将有硬化要求的部位按GB/T131的规定,在图形上用粗点画线框出。如果是轴对称零件或在不致引起误会情况下,也可用一条粗点面线画在热处理部位外侧表示,其他部位即硬化与不硬化均可的过渡部位用虚线表示,不允许硬化或不要硬化的部位则不必标注。3.7要求零件硬度检测必须在指定点(部位)时,用图1符号表示,其尺寸大小应与GB/T131规定的局部热处理指示符号一致指定硬度测量点位置时,应符合JB/F6050一2006中第6章的规定。图1硬度测量点符号标注方法
3.8如零件形状复杂或儿他原四(如与其他工艺标注容易混淆)热处理技术要求难以标注,用文字说明又不易表达时,可另加附图表示,此时附图上与热处理无关的内容均可省略,见图2。a)零件热处理标注图
表面硬度测量点
DS 测至点
b)Y部热处理技术要求的标注递30*
DS测量点
表面硬度测盘点
c2部热处理技术要求的窃注图
复杂零件热处理技术要求的标注方法图2
JB/T85552008
3.9标注除硬度以外的其他力学性能要求时(如强度、冲击韧度等),应在零件图样上注明具体技术指标和取样方法。
3.10零件热处理的外观质量或者无法用量值表达的要求,可用文字说明。4正火、退火及淬火回火(含调质)零件4.1以正火、退火或淬火回火(含调质)作为最终热处理状态的零件一般标注硬度要求:通常以布氏硬度(GB/T231.1)或洛氏硬度(GB/T230.1)表示。也可以用其他硬度表示。4.2同一零件的不同部位有不同热处理技术要求时,应在零件图样上分别注明。4.3局部热处理零件必须在技术要求的文字说明中写明局部热处理。并在图样上按3.4和3.6的规定标出需热处理的部位和技术要求,见图3。不大于30HRC
a)范围表示法
b)偏差表示法
56HRC-62HRC
35'HRC下载标准就来标准下载网
图3局部热处理零件技术要求的标注方法5表面淬火、回火零件
5.1一般技术要求
感应加热萍火回火和火焰加热痒火回火零件标注的主要技术要求是表面硬度、心部硬度和有效硬化层深度。
5.2表面硬度
表面硬度的标注包括两部分,即要求硬度值和相应的试验力,而试验力的选取又与要求的最小有效硬化层深度有关。表面硬度的测量应符合GB/T230.1、GB/T4340.1的规定。以维氏硬度表示时,最低表面硬度、最小有效硬化层深度与硬度试验力之间的关系见表2。表内试验力为最大允许值,也可以用较低的试验力代替表中所列值,如用HV10代替HV30。3
JB/T85552008
表2以维氏硬度表示时最低表面硬度值、最小有效硬化层深度与试验力之间的关系最小有效诬化层深度
400-~500
最低表面硬度HV
>500--600
>600--700
以洛氏硬度表示时,最低表面硬度、最小有效硬化层深度与试验力之间的关系见表3和表4。5.3心部硬度
对表面辫火零件的心部硬度有要求时,应予标注。经有关各方协商同意,允许以预备热处理后的硬度值为溅。
最小有效硬
化层深度
以表面洛氏硬度表示时最低表面硬度、最小有效硬化层深度与试验力之间的关系最低表面硬度(以HR\N表示)
82--85
>85~88
60~6868--73]73-~78
1:NR30N
>54--61
HR45NHR45N
JB/T8555--2008
表 4以洛氏硬度 标尺或 C标尺表示时最低表面硬度、最小有效硬化层深度与试验力之间的关系最小有效硬
化层深度
70~-75
5.4有效硬化层深度
75--78
278--81
最低表面硬度
40~-49
55~-60
表面率火零件有效硬化层深度的标注包括三个部分,即硬化展深度代号(见表1)、界限硬度值和要求的深度。在图样上的标注方法见5.5界限硬度值可振据最低表面硬度按表5选取。特殊情况,也可采用其他界限硬度值,但此时在DS后必须注明商定的界限硬度值。
零件的有效硬化尽深度分级及1:偏差可参照表6。火焰率火的有效硬化层深度通常不应小于1.6nm.
表5表面淬火界限硬度值
界限硬度值
69·70
75--76
80-- 81
最低表面硬度
54~-55
56--58
59 -- 62
69·70
72 --73
36~-38
39~ 41
50--52
55 --57
60~~61
62 -- 63
66-·67
71--72
300-330
335~355
360--385
390~:420
425 --.455
460)--480
485--515
520-545
550-575
580--605
610635
670705
710--730
735765
770 ·795
800$35
840 -865
40--42
46 --47
48 -- 49
50--51
52--53
55--56
JB/T85552008
表6表面淬火有效硬化层深度分级和相应的上偏差最小有效硬化层深度DS
5.5标注示例
感应济火
上偏差
单位:mm
火焰淬火
示例:图4所示为局部感应加热萍火同火标注方法,该例表示:离轴端15mm土5mm处F始,在长30*mm一段内感应热率火回火,表面硬度620HV30780HV30,有效硬化层深度0.8mm-1.6mrm。hXHV70-780HV30
[35300=0.8~1.6
al范围表示法
125=0.8+*.620-gHV30
h)编差表示法
图4局部感应加热淬火回火标注方法6渗碳和碳氮共渗零件
6.1—一般技术要求
渗碳后淬火回火和碳氮渗眉淬火可火零件标注的主要技术要求是表面硬度,心部硬度利有效硬化层深度。共他技术要求(如渗尽金相组织、诊么碳液虑或硬度分布、心部力学性能等;按3.3的规定执行
6.2表面硬度
渗碳后率火回火和碳氮共渗压萍火问火零件的表面硬度要求,通常以维氏硬度或洛氏硬度表示,对应的段小有效硬化层深度和试验力与表面淬火零件相同6.3心部硬度
对渗碳后率火回火或碳氮共渗后浒火回火零件的心部硬度有要求时,应予标注:6.4渗层的有效硬化层深度
JB/T 8555—2008
渗碳后率火[叫火或碳氮共渗后淬火回火零件的有效砾化层深度(DC)在图样1的表示方法,与表恒率火有效硬化层深度DS基本相同,在图样上的标注方法见6.5渗俄后济火回火或碳氮共渗后淬火间火的界限硬度值是低定的,通常取550HV1,标注时一般可省略,特殊情况下可以不采用550HV1作界限硬度值,此时DC后必须注明商定的界限硬度值和试验力。推荐的渗碳后济火回火或碳氮共渗后淬火回火零件有效硬化层深度(DC)及上偏差见表7表7推荐的渗碳后淬火回火或碳氮共渗淬火回火零件有效硬化层深度及上偏差单位:mm
有效硬化层深度
6.5标注示例
上偏差
示:图5所示为而部渗碳标注方法,对零件不同部份有不同的要求,要求渗饿后火同火部位用粗点画战润出;有的部位色许同时渗碳济硬也可以不渗碳济硬,视工艺上是否有利而定,用虚绒表示:末标出部位:啡不犯许渗氮也不允许率便。
局部渗碳泽火回火
57HRC-63HRC
DC -1.2 -- 1.7
图5局部渗碳标注方法
7渗氮零件
7.1 一般技术要求
气体渗氮或离了渗氮零件的主要技术要求是表面硬度、心部硬度和有效渗氮层深度果些零件还有渗氮层脆性要求,其他技术要求(如渗氮层金、渗氮层硬度分布,心部力学性能等)按33的就行7.2表面硬度
零件诊氮旨的表面硬度与零件材质和预备热处理有密切关系、在正营工艺条件下,营月渗氮材料能达到的硬度范封可参照JB/T6956。JB/T8555—2008
表面链度因有效氮层深度不回而有差异,标注足应准确选择。表面硬度值的测量应衍合GB/4340.1的有关规定。
有效渗氮层深度不大于0.3mm时按GB/T9451执行,人F0.3mm时按GB/T11354执行,经协商同意,也可以采用拉他硬度检测方法表示:7.3心部硬按
对渗氨零件心部硬度有要求时,应特别注意,心部砸度通常允许以预备热处理后的检测结果为准:以维長硬度、布氏硬度或洛氏硬度表示。7.4有效渗氮层深度
图样上标注渗氮层深度,除非另有说明,般均措有效渗氮层深度(见3.5)。其表示方式与DS、DC基本相同,在图样上的标方式见7.6..来用2.94N(0.3玉gf)的维氏硬度试验力测量行效渗氮层深度DN时,DN后不标注界限硬度值:采用其他试验力时,成在DN后加试验力值,如DNHV0.5一0.3·0.4.一般零件推荐的最小有效渗氮层深度(DN)及1偏兰见表8:表8推荐的最小有效渗氮层深度及上偏差辛位:rmm
有效渗氮层深度DY
上诵差
有效渗氮层深度DN
上偏差
技术要求的最小有效渗氮爆深度、最低面续追与碘度试验力之间的关系见衣9:表内检验方法国场是指允许采用最大试验力,允许用较低的试验力代替表中规定的试验力,如IV10代替HV30,表9技术要求的最小有效渗氮层深度、最低表面硬度与硬度试验力之间的关系最小有效
渗氮展深度
2()~300
300---40
2 400...50m
最低志面碑
2- ---70
700 --800
7.5总渗氨层深度
JB/T8555—2008
总渗氮层深度是氮渗人的总深度,一般指从表面测基到与基体的硬度或组织无差别处的垂直距离(单位mm)。
总渗氮层深度包括化合物层和散层两部分。零件以化合物层深度代替DN要求时,应特别说明,厚度要求随零件服役条件不同而改变,一般零件推荐的化合物层厚度及公差值见表10。7.6标注示例
示例:图6所示为诊氮零件的标注方法,渗氮部位边缘以粗点面线子以标注,并规定了硬度测定点位置。虚线部位允许渗氮或不充许渗氮是对工艺是否有利而决定。未标法部位不允许渗氮,如器防,必须说期。表10推荐的化合物层厚度及公差单位:mm
化合物层厚度
8、其他热处理零件
局部渗氮硬度不小于800HV30
DN=0.4~0.6,脆性不大了3级
图6渗氮零件的标注方法
上俯差
其他热处理零件的热处理技术要求在零件图样上的表示方法可参照第3章的规定执行
小提示:此标准内容仅展示完整标准里的部分截取内容,若需要完整标准请到上方自行免费下载完整标准文档。

标准图片预览:
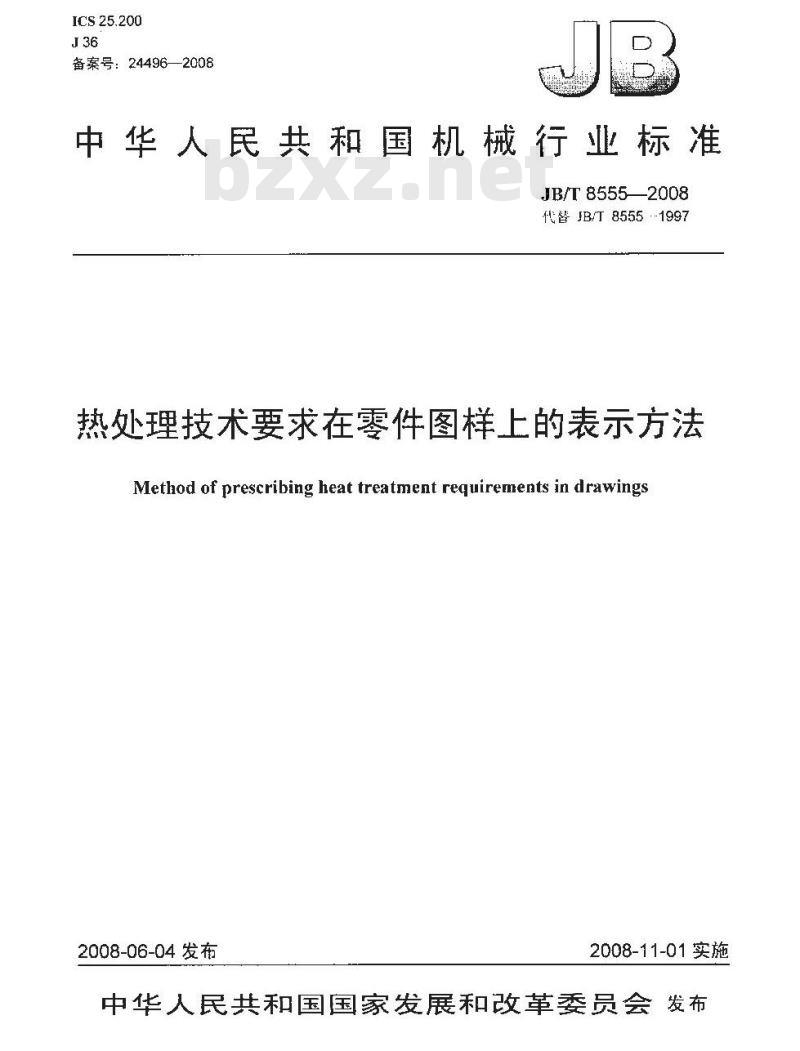
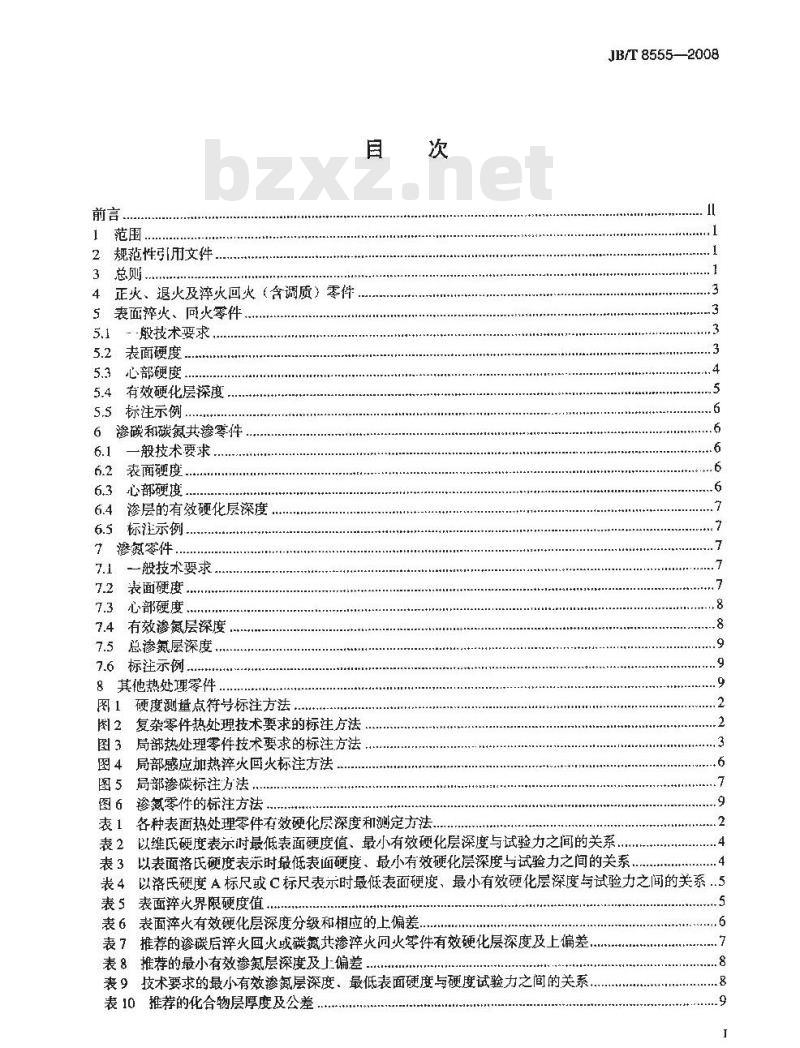
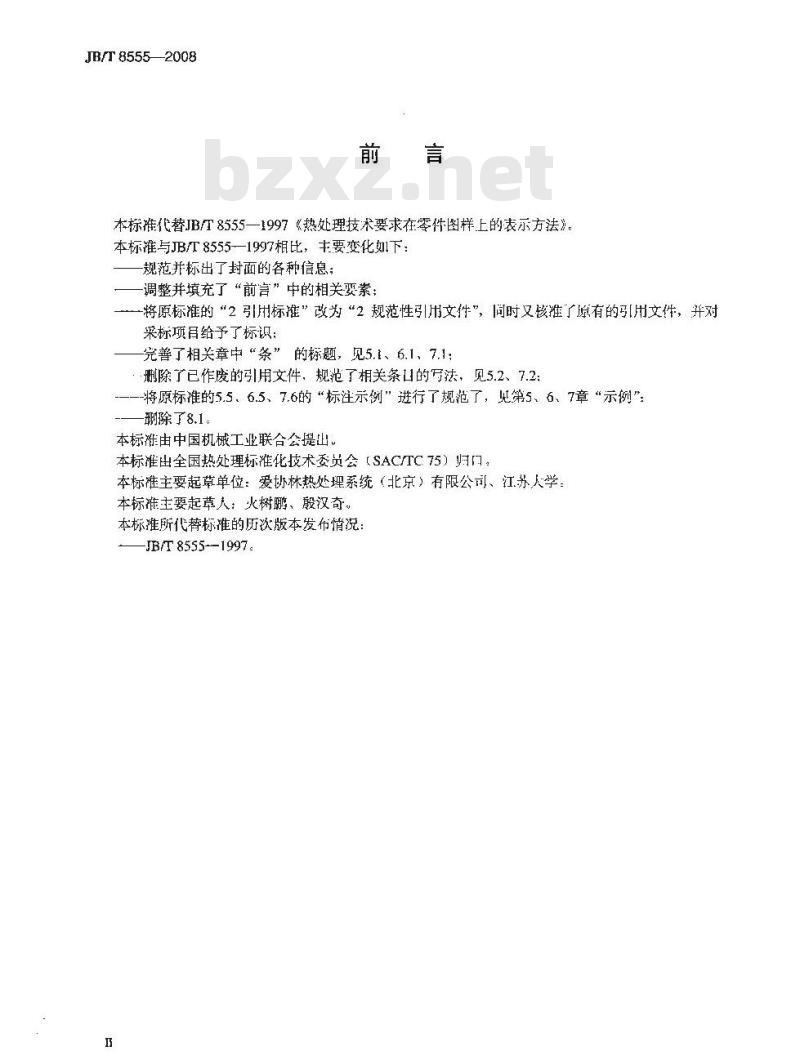
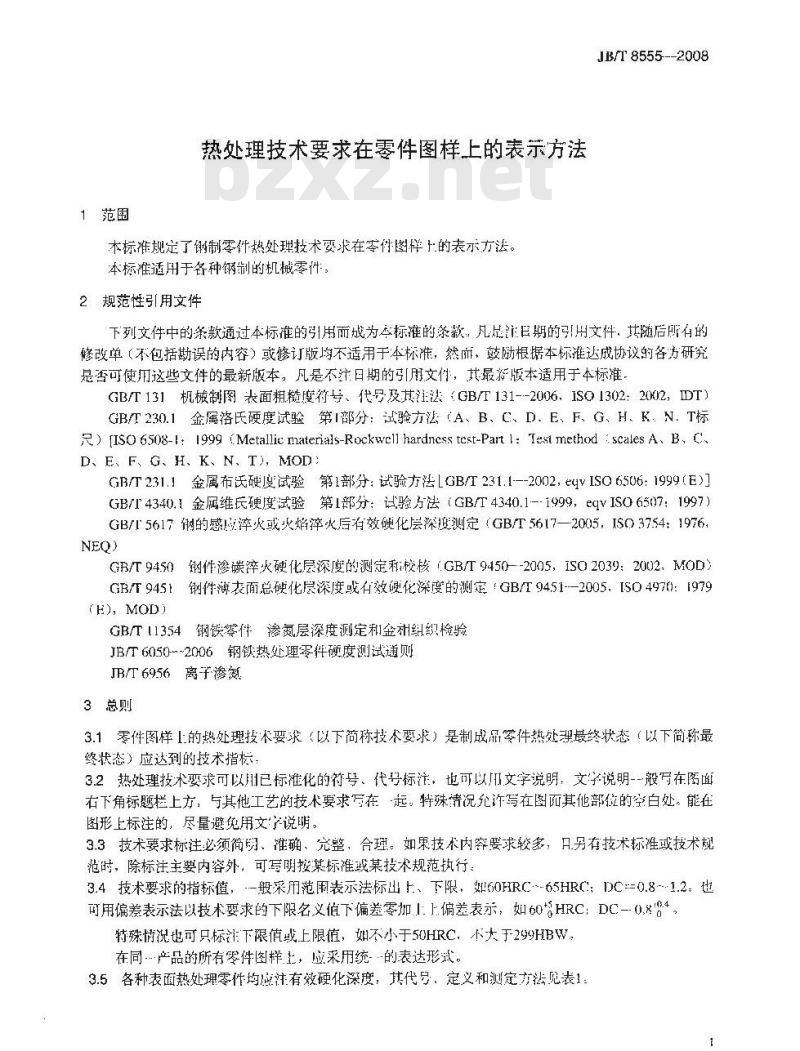
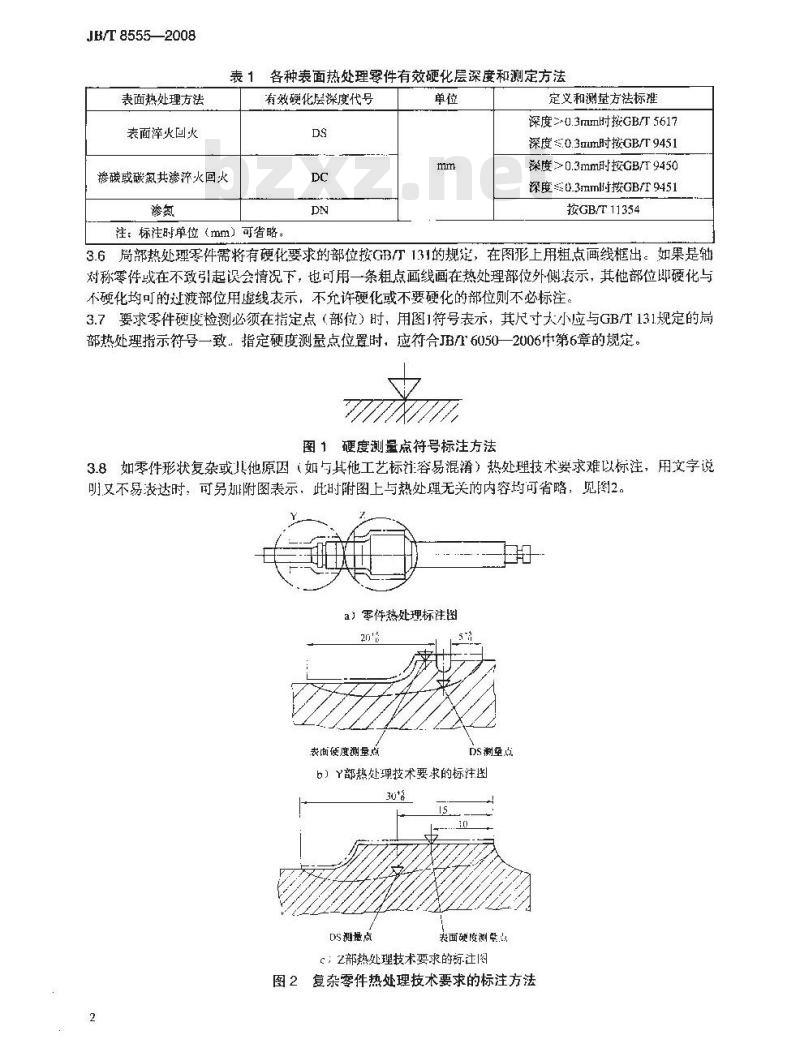
- 其它标准
- 热门标准
- 机械行业标准(JB)
- JB/T3103.2-2010 锯条开齿机 第2部分:精度
- JB3228-1983 闭式机械压力机 紧固模具用槽打(顶)杆孔的分布形式与尺寸
- JB/T6342.1-2006 数控插齿机 第1部分:精度检验
- JB/T7810-2007 幻灯片 24mm×36mm
- JB/T5532-2007 静电复印干式色调剂流动性测定方法
- JB/T7895-2008 永磁筒式磁选机
- JB/T2936.1-1999 闭式冷挤压压力机 型式与基本参数
- JB2513-1978 组合机床通用部件 底座名义尺寸、互换尺寸
- JB/T5448-2007 静电复印干式双组份显影剂用色调剂
- JB2506-1978 组合机床通用部件 多轴攻丝动力头名义尺寸、参数、互换尺寸
- JB2509-1978 组合机床通用部件 圆盘底座参数、互换尺寸
- JB2516-1978 组合机床通用部件 立柱(长台面滑台用)名义尺寸、互换尺寸
- JB/T6237.4-2008 电触头材料用银粉化学分析方法 第4部分:火焰原子吸收光谱法测定镍量
- JB2511-1978 组合机床通用部件 侧支架(辐射型)名义尺寸、互换尺寸
- JB2518-1978 组合机床通用部件 风动动力头参数、互换尺寸
- 行业新闻
- 华盛顿斯波坎市因诈骗损失增加禁止加密货币ATM
- 香港《稳定币条例》全解读:从定义、监管架构、申请资格到市场影响
- 战争危机中的加密货币?比特币除外——看看BTC如何挺住
- 柏克莱教授警告:名校毕业生也没得挑工作!AI再5年斩掉一半基层职位
- 加拿大XRP ETF的推出在美国引发FOMO情绪
- Pi Network在Pi2Day前夕推出新同步功能以优化KYC流程
- 贝莱德的BUIDL被Deribit和Crypto.com接受为抵押品
- 伊朗在Nobitex交易所1亿美元黑客攻击后限制加密货币交易时间
- 朝鲜黑客瞄准印度加密货币求职者
- 美联储、恐惧与错失恐惧症:山寨币等待下一次大动作
- 贝莱德IBIT比特币ETF资金流入创纪录,比特币冲击10.9万美元大关 | ETF动态
- 财政部长贝森特表示:稳定币或有助于削减美国债务
- ZachXBT预警:2025年黑客攻击升级,加密货币犯罪进入超级循环
- Semler Scientific 计划购买 105,000 枚比特币
- 尽管市场喧嚣不断,比特币仍在横盘整理:或将突破至11.4万美元
请牢记:“bzxz.net”即是“标准下载”四个汉字汉语拼音首字母与国际顶级域名“.net”的组合。 ©2009 标准下载网 www.bzxz.net 本站邮件:bzxznet@163.com
网站备案号:湘ICP备2023016450号-1
网站备案号:湘ICP备2023016450号-1